
INSTALLATION INSTRUCTIONS
These instructions apply to the external field installation of
the Siemens, GND Series, actuators on Greenheck models
VCD (Control Dampers).
These models are direct drive actuators that rotate to their
energized position when power is applied, and spring
return to their fail position when power is disconnected.
Part number 473723
GND Series Actuators
Models GND-121, GND-221, & GND-321
Tools Required:
Wrenches: (1) 1⁄2 in., (1) 7⁄16 in.,
3
⁄8 in., (1) 10 mm
(1)
Item Part No. Qty Description
1 1 GND actuator
2 723092 1 Anti-rotation bracket
3 815027 1 Standoff bracket
4 415475 4 1/4 -20 x 1/2" bolt
5 415455 4 1/4-20 spinlock nut
6 415586 4 #14 TEK screw
7 416122 1 Anti-rotation pin
8 415385 1 Keps hex nut zp.
Figure 1: Siemens GND Series external mount (exploded view).
WARNING
!
Equipment Damage or Electrical Power Hazard. Line voltage can cause death or serious injury and short equipment
circuitry. Disconnect power supply before installation.
CAUTION
!
Device Malfunction Hazard. Improper set screw tightening causes device malfunction. Tighten set screws with proper
torque to prevent damper shaft slippage.
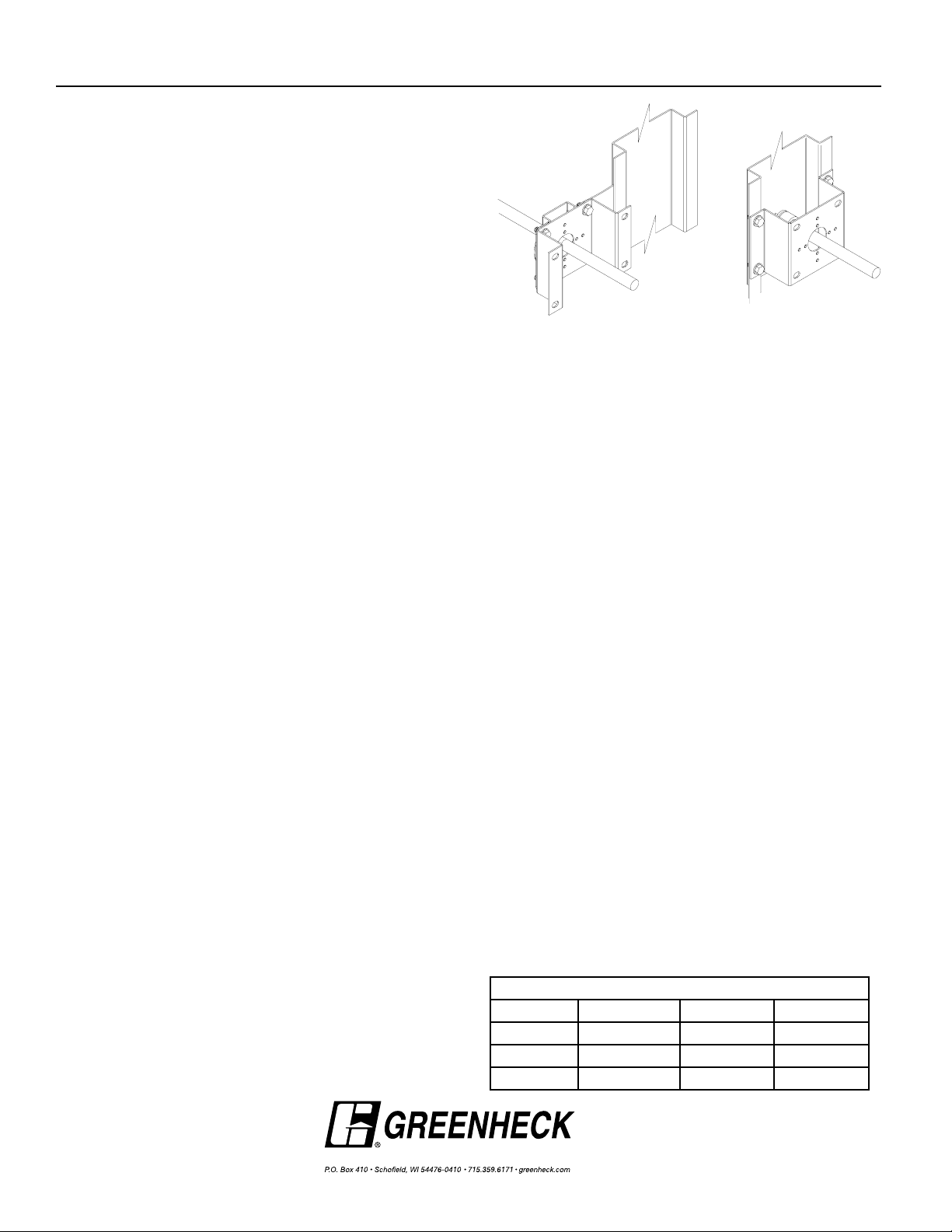
These installation instructions assume the damper is already
mounted in a duct or sleeve with the damper shaft extending
beyond the duct or sleeve 6 inches (152mm).
1. Install the stand off bracket.
Dampers with a jackshaft
1a. Mount the stand off bracket (item 3) onto the jackshaft
bracket with [4] 1/4 - 20 x 1/2 in. bolts (item 4) and [4]
1/4 - 20 spinlock nut (item 5) Orient the anchor bracket
perpendicular to the damper on the duct or sleeve so that
the bracket shaft hole is centered on the jackshaft.
Dampers without a jackshaft (Shaft Extension)
1b. Mount the stand off bracket (item 3) and extension pin, as
detailed in extension pin kit instructions, spanning across
the damper frame flanges. Orient the anchor bracket perpendicular to the damper on the duct or sleeve so that
the bracket shaft hole is centered on the shaft extension.
Fasten to the damper frame with (4) #14 Tek screws or
equal (item 6), supplied by others. Be sure not to run the
screws into the damper linkage, which is between the
flanges.
2. If the fail rotation of the damper is counter clockwise, this is a
Left Hand installation and the universal clamp should be on
the side labeled CCW on the actuator (usually shipped in this
orientation). If the fail rotation of the damper is clockwise, this
is a Right Hand installation and the universal clamp should be
on the side labeled CW on the actuator.
To change the universal clamp from one side to the other side,
remove the retaining clamp and then the universal clamp from
the actuator. Replace the universal clamp on the correct side of
the actuator making sure that the corresponding tab is pointing
to 0° and fits onto the actuator. Slip the clamp on and then lock
in place using the retaining clamp.
Note: All fail rotations refer to the damper shaft rotation needed
to achieve the desire blade fail position. If fail position is closed,
make sure damper blades are fully close and ensure blade seals
are compressed prior to tightening the actuator clamp to the
damper extension pin or jackshaft. Inspect the damper blades
and the damper shaft to determine the proper damper shaft
rotation for the desired blade fail position.
3. Slide the actuator and the mounting bracket (item 2) onto the
damper shaft. Mount the mounting bracket (item 2) to the
stand off bracket (item 3) using (4)
4), and (4)
holes of the mounting bracket for jackshafted models and the
inner four holes for directly driven models.
Note: The mounting bracket (item 2) may be attached in three
positions: parallel with the duct, perpendicular up from the duct,
or perpendicular down from the duct. Choose a position that
offers the most clearance for the application.
4. Verify that the damper is in its fail position. Tighten the universal
clamp to the damper shaft.
5. The wiring illustration is located on the face of the actuator.
Wiring should be per an approved project or job wiring diagram
and must comply with all applicable electrical codes.
6. Apply power to the actuator. The damper blades should fully
open or close. No adjustments are required.
1
/4 in. - 20 Spinlock nuts (item 5). Use the outer four
1
/4 in.-20 x 1/2 in. bolts (item
GND DIRECT DRIVE SERIESINSTRUCTIONS
Orientation of Stand Off
Bracket for a jackshaft
driven damper
Actuator Weight
4 lb (1.8 kg).
Temperature Ratings
Ambient: 0°F to 140°F (-18°C to 60°C)
One Time 350°F (177°C) for 1/2 Hour (per UL 555S)
Shipping and Storage: -40°F to 158°F (-40°C to 70°C)
Humidity Ratings
Maximum 95% RH, Non-condensing
Environmental Protection Ratings
NEMA 1.
Approvals
Underwriters Laboratories Inc. UL 873 plenum rating,
and C-UL Certified to Canadian standard C22.2 No.
24-93.
Australian EMC Framework (C-tick) with the limits per
AS/NZS 2064 1/2:1997.
Conforms to CE requirements for the EMC and low
voltage directives.
Australian Electromagnetic Compatibility (EMC) per
AS/NZS 4251.1/2:1999 (C-tick)
Direction of Spring Return
Reversible Fail-Safe Spring Return
Actuator Timing (Under Load)
Drive Open: 15 seconds.
Spring Close: 15 seconds.
Power Consumption
Model Volts Running Holding
GND-321 230 VAC 20 VA 9 VA
GND-221 120 VAC 20 VA 9 VA
GND-121 24VAC/VDC 20 VA 8 VA
Orientation of Stand Off
Bracket for a directly driven
damper
Copyright © 2010 Greenheck Fan Corporation
473723 GND IOM Rev. 1 May 2010