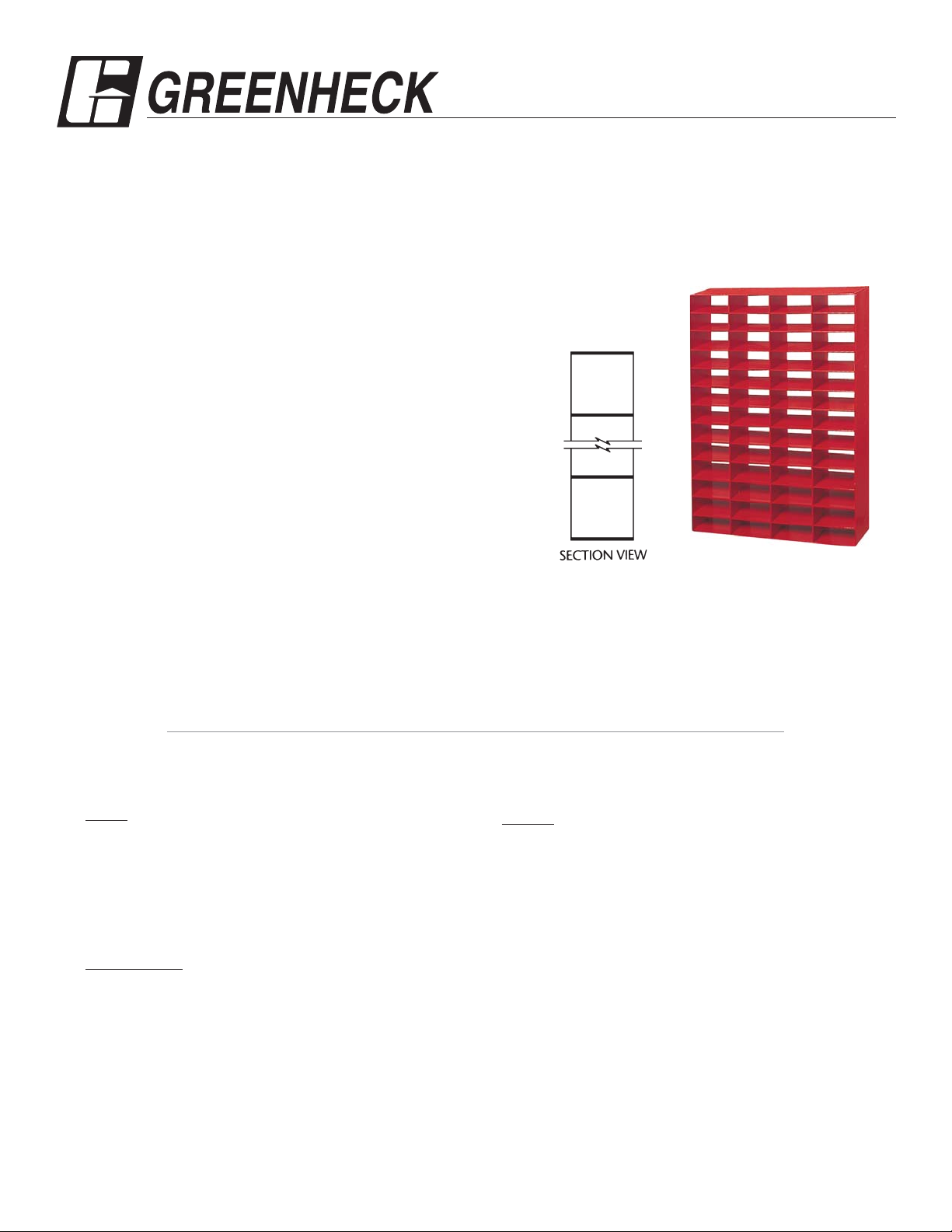
Grille
®
Application and Design
Greenheck Bar Grilles are custom designed and manufactured to function as
architectural accents or as entire facades to prevent sight or serve as solar screens
or security barriers. Bar Grilles are manufactured in configurations from 2 in. (50.88
mm) to 6 in. (152.4 mm) deep and with extruded aluminum members that range in
thicknesses from 0.081 in. (2.06 mm) to 0.250 in. (6.35 mm). Horizontal and vertical
bar spacing can be configured from 2 in. (50.8 mm) minimum to 12 in. (304.8 mm)
maximum center spacing to yield desired sightlines.
Standard Construction
Material . . . . . . . . . . . . . . . . .Extruded Aluminum, Alloy 6063T5
Material Thickness . . . . . . . .0.081 to 0.250 in. (2.06 to 6.35 mm)
Grille Depth . . . . . . . . . . . . . .2 to 6 in. (50.8 to 152.4 mm)
Perimeter Frame . . . . . . . . . .Aluminum Bar, Channel or Tube
Horizontal Bar Spacing . . . . . .2 to 12 in. (50.8 to 304.8 mm)
Vertical Bar Spacing . . . . . . . .2 to 12 in. (50.8 to 304.8 mm)
Minimum Dimension . . . . . . .10 in. (254 mm)
Maximum Dimension . . . . . . .120 in. (3048 mm)
One dimension not to exceed 72 in.
Options
• Anchor clips
• A variety of bird and insect screens
• A variety of architectural finishes including:
(at additional cost)
Clear anodize
Integral color anodize
Baked enamel paint
Kynar paint
BAR
Recommended Specifications
General
Where indicated on plan drawings or described in schedules, furnish
and install Bar Grilles as designed and manufactured by Greenheck
Fan Corporation, Schofield, WI. Grilles shall be furnished in the
configurations represented on the plan drawings and shall include
installation hardware and finishes as specified and required for a
complete installation.
Welded Assembly
All horizontal, vertical and perimeter frame members shall be joined
with slotted or tabbed connections. Where possible, connections
shall be secured with fillet welds concealed from view, unless the
size of the grille makes bolted connections between grille sections
necessary. Each weld shall be manufactured with the Pulsed Gas
Metal Arc Welding (GMAW Mig) process. Intermediate connections
shall be intermittently joined with a 1 in. (25.4 mm) long fillet weld
with a minimum 3/16 in. (4.76 mm) leg. Frames shall be joined at
each corner with a full-length GMAW fillet weld with a minimum 3/16
in. (4.76 mm) throat.
Products
Architectural grilles shall be Greenheck Bar Grilles as follows:
• Material: Extruded Aluminum, Alloy 6063T5
• Material Thickness: Specify 0.081 in. (2.06 mm) to 0.250 in.
(6.35 mm), or as indicated.
• Grille Depth: Specify 2 in. (50.8 mm) to 6 in. (152. 4 mm), or
as indicated.
• Perimeter Frame: Specify Bar, Channel or Tube, or as
indicated.
• Horizontal Bar Spacing: Specify 2 in. (50.8 mm) to 12 in.
(304.8 mm), or as indicated.
• Vertical Bar Spacing: Specify 2 in. (50.8 mm) to 12 in. (304.8
mm), or as indicated.

A - Horizontal Bar Spacing
Specify horizontal members on minimum 2 in. (50.8 mm) to maximum 12 in. (304.8 mm) center spacing.
B - Vertical Bar Spacing
Specify vertical members on minimum 2 in. (50.8 mm) to maximum
12 in. (304.8 mm) center spacing.
C - Grille Depth
Specify minimum 2 in. (50.8 mm) to maximum 6 in. (152.4 mm)
depth.
D - Aluminum Thickness
Specify minimum 0.081 in. (2.06 mm) to maximum 0.250 in. (6.35
mm) Extruded Aluminum (alloy 6063T5) wall thickness.
Grille
BARDETAIL DRAWINGS
FINISHES
Finish Type Description/Application Color Selection
2-coat 70% KYNAR 500®/HYLAR 5000® AAMA 2605 –
Dry fi lm thickness 1.2 mil. (AKA: Duranar®, Fluoropon®,
Trinar®, Flouropolymer, Polyvinylidene Fluoride, PVDF2)
2-coat 50% KYNAR 500®/HYLAR 5000® AAMA 2604
– Dry fi lm thickness 1.2 mil. (AKA: Acrofl ur®, Acrynar®)
Baked Enamel AAMA 2603 – Dry fi lm thickness 0.8 mil.
(AKA: Acrabond Plus®, Duracron®)
Integral Color Anodize AA-M10C22A42 (>0.7 mil)
Clear Anodize 215 R-1 AA-M10C22A41 (>0.7 mil)
Clear Anodize 204 R-1 AA-M10C22A31 (0.4-0.7 mil)
Industrial coatings
Mill
Finishes meet or exceed AAMA 2605, AAMA 2604, and AAMA 2603 requirements. Please consult www.greenheck.com for complete information on standard and
extended paint warranties. Paint fi nish warranties are not applicable to steel products.
“Best.” The premier fi nish for extruded aluminum. Tough,
long-lasting coating has superior color retention and
abrasive properties. Resists chalking, fading, chemical
abrasion and weathering.
“Better.” Tough, long-lasting coating has excellent color
retention and abrasive properties. Resists chalking, fading,
chemical abrasion and weathering.
“Good.” Provides good adhesion and resistance to
weathering, corrosion and chemical stain.
“Two-step” anodizing is produced by following the normal
anodizing step with a second, colorfast process.
Clear, colorless and hard oxide aluminum coating that resists
weathering and chemical attack.
Clear, colorless and hard oxide aluminum coating that resists
weathering and chemical attack.
Greenheck offers a number of industrial coatings such as Hi-Pro Polyester, Epoxy, and Permatector®.
Consult a Greenheck Product Specialist for complete color and application information.
Materials may be supplied in natural aluminum or galvanized steel fi nish when normal weathering is
acceptable and there is no concern for color or color change.
Standard Colors: Any of the 24
standard colors shown can be
furnished in 70% or 50% KYNAR
500®/HYLAR 5000® or Baked Enamel.
2-Coat Mica:
Greenheck offers 9 standard 2coat Mica colors. Other colors are
available. Consult Greenheck for
possible extra cost when selecting
non-standard colors or special
fi nishes.
Light, Medium or Dark Bronze;
Champagne; Black
Clear 5 years
Clear 1 Year
Standard Warranty
(Aluminum)
10 Years
(Consult Greenheck for
availability of extended
warranty)
5 Years
1 Year
5 years
Consult Greenheck
n/a
Copyright © 2007 Greenheck Fan Corporation
Bar Grille March 2007
Greenheck Fan Corporation reserves the right
to make product changes without notice.