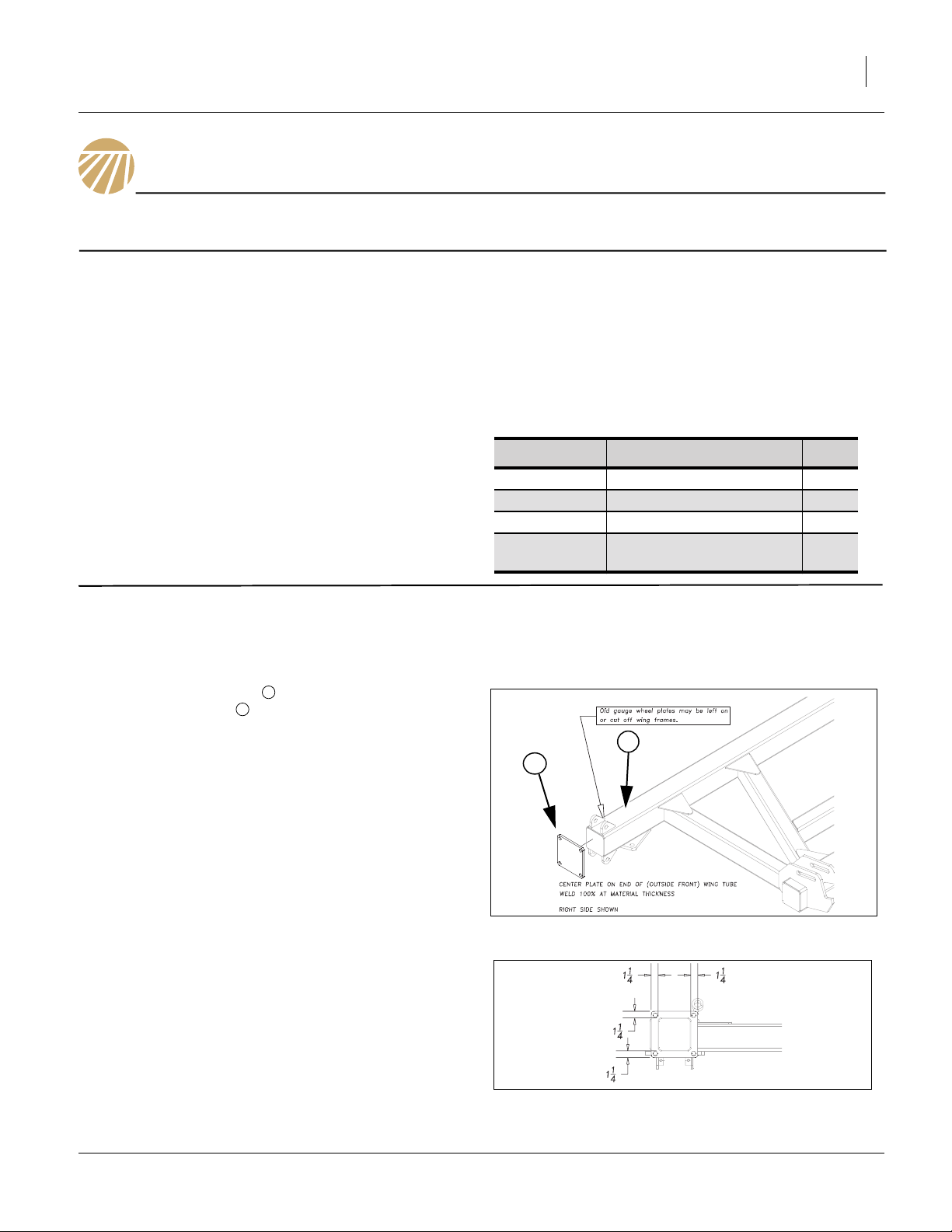
Great Plains Manufacturing, Inc. 1
Disk Harrow Update
Gauge Wheel Update
General Information
These Instructions explain how to install the gauge wheel
kit update. These instructions apply to kit number: 558185A GAUGE WHEEL DISK UPDATE KIT. The gauge
MetaData: of <Safety Topics>Introduction
Tools Required
• Basic Hand Tools
Manual Update
Refer to the Disk Harrow operator’s manual for detailed
safety and maintaining of machine. Refer to parts manual for part identification.
556-100M Operator Manual
556-100P Parts Manual
Assembly Instructions
Move machine to level ground, near a welder and unfold
wings. Remove old gauge wheel assemblies from wing
Refer to Figure 1
1. Center the 556-474D over the end of the outer tube
of the wing frame .
1
2
wheel will come completely assembled. The plates will
have to be welded on to wing frame.
• Torque Wrench
• Welder
558-185A Kit
Part Number
Description Qty.
556-220K GAUGE WHEEL ASY RH 1
556-221K GAUGE WHEEL ASY LH 1
556-474D PLATE - TORCHED 2
821-001C
PAINT GP GREEN
SPRAY CAN
1
frame. The old gauge wheel plates may stay on or may
be cut off.
2
1
FigureSpacer:
Refer to Figure 2
Figure 1
Plate Assembly
2. Position the plate as shown.
3. Weld the back side of the plate to the tube
FigureSpacer:
Figure 2
Plate Location
08/23/2010 558-185M
41867
41869
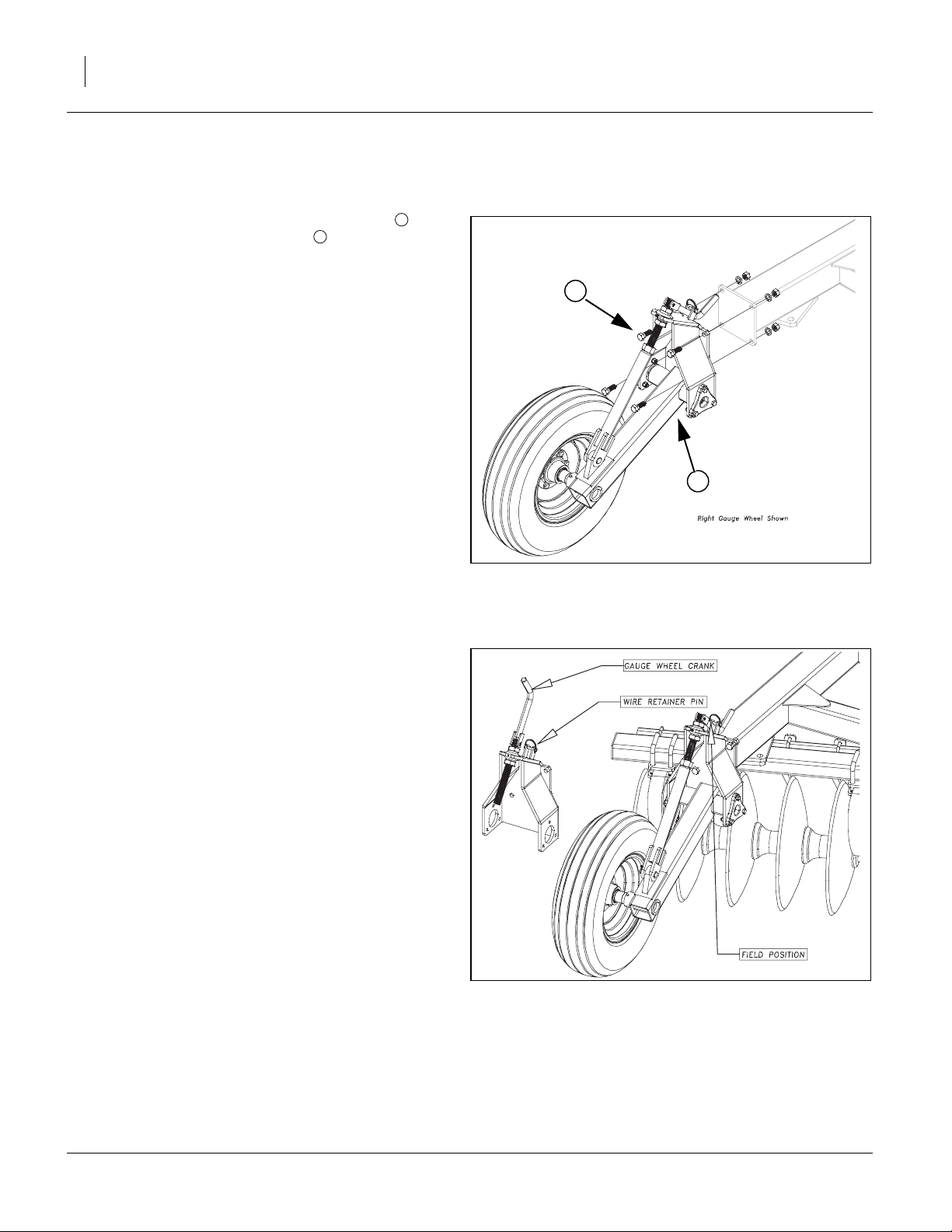
2 Disk Guage Wheel Update Great Plains Manufacturing, Inc.
Refer to Figure 3
Note: There is a RH (right hand) and LH (left hand)
assembly. The RH is shown.
4. Now the 556-220K gauge wheel assembly may be
installed using the 3/4 x 2 hex bolts , 3/4 lock washers
2
1
and 3/4 nuts.
5. Torque the bolts to 265 ft-lb.
6. Repeat the same procedure for the left hand side.
2
1
Refer to Figure 4.
7. To change the gauge wheel setting, remove the wire
retaining pin and fold gauge wheel crank up to adjust.
Lower or raise the gauge wheel by turning the gauge
wheel crank. Raise the wheels up until you have the disk
adjusted in the fore-and-aft, side to side and the desired
working depth you desire. Fold the gauge wheel crank
back down in the field position and reinstall the wire retaining pin. As you are running the disk through the field, stop
the tractor leaving the disk in the ground. Now you can
adjust the gauge wheels 1/2” to 1-1/2” above the ground.
After initial adjustment you can turn gauge wheel crank the
same amount as the depth stop crank (if changed, but
crank turns opposite way than depth control crank to keep
initial setting). This position should be maintained to prevent excessive wear to gauge wheel parts.
FigureSpacer:
FigureSpacer:
Figure 3
Gauge Wheel Assembly
Figure 4
Gauge Wheel Adjustment
41868
41870
558-185M 08/23/2010