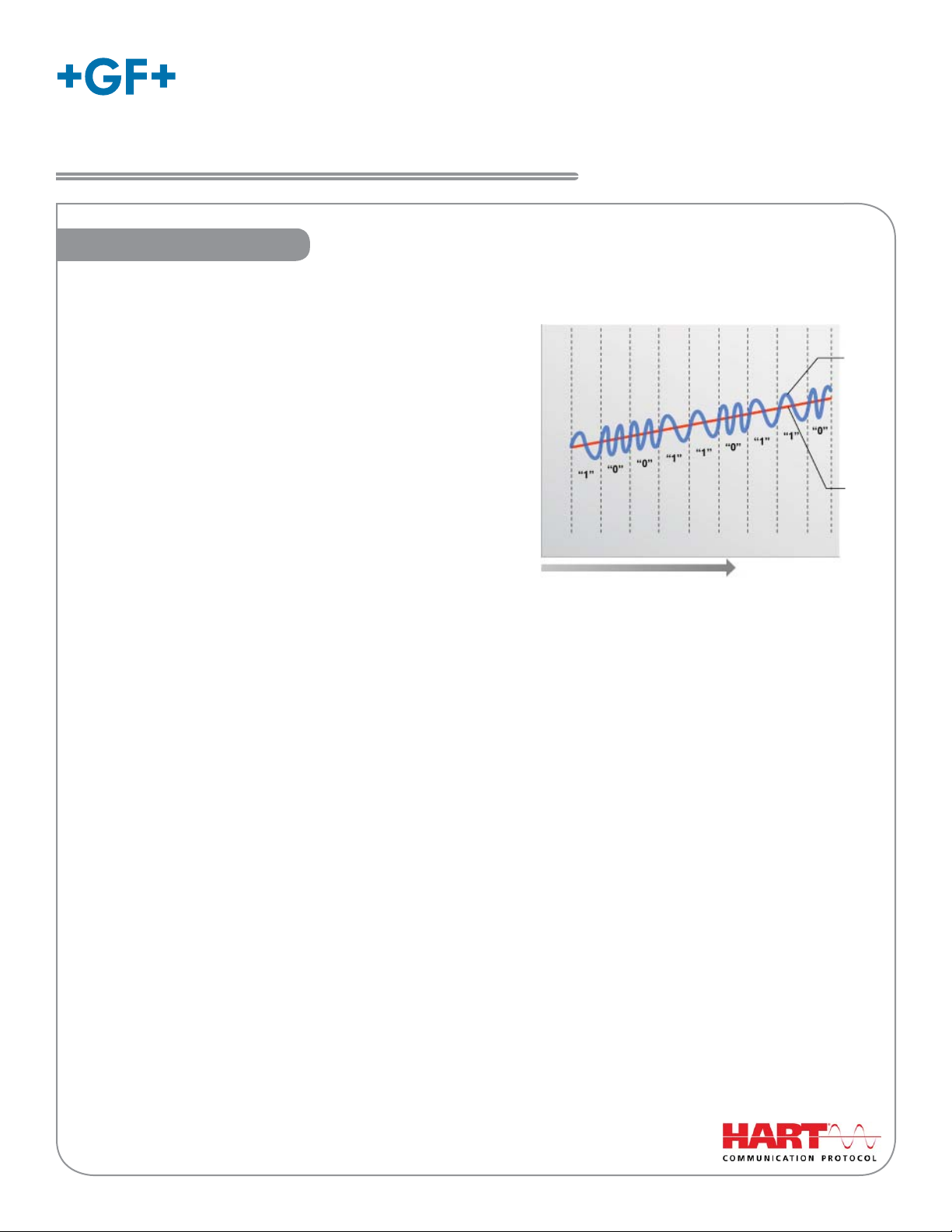
Signet 9900 H COMM Module
*3-9900.094*
3-9900.094 Rev. C 03/13 English
Introduction
How HART® Works
The HART® (Highway Addressable Remote Transducer)
Protocol uses Frequency Shift Keying (FSK) to superimpose
digital signals on top of the analog 4 to 20 mA current loop.
This allows two-way digital communication to occur and
allows additional information beyond the normal process
data to be communicated to the 9900. This digital signal
can contain data such as device status, diagnostics, etc.
20 mA -
Instruction Sheet
English
Digital
Signal
The HART protocol provides two simultaneous communication
channels: a 4 to 20 mA analog signal and a digital signal.
The analog signal communicates the primary measured
value using the 4 to 20 mA current loop.
Additional information is communicated using a digital
signal superimposed on the 4 to 20 mA signal.
Communication occurs between two HART -enabled devices,
4 mA -
Time
Note: Drawing not to scale
Frequency Shift Keying
Digital over Analog
Time
Analog
Signal
in this application a Signet 9900 Transmitter and a PLC or
handheld device, using standard wiring and termination practices. The HART Protocol communicates at 1200 bits per second without interfering with the 4 to 20 mA signal and allows the PLC or handheld device to communicate two or
more updates per second to and from the 9900.
The HART protocol operates according to the master-slave method. Any communication activity is initiated by the
master, usually a programmable logic controller (PLC) or a data acquisition system. HART accepts two masters: the
primary master - usually the control system (PLC) - and the secondary master - a PC laptop or handheld terminal
used in the fi eld.
HART fi eld devices - the slaves - never send without being requested to do so. They respond only when they have
received a command message from the master. Once a transaction (i.e., a data exchange between the control station and the fi eld device) is complete, the master will pause for a fi xed time period before sending another command,
allowing the other master to break in. The two masters observe a fi xed time frame when taking turns communicating
with the slave devices.
As deployed in the 9900 application, HART allows remote verifying, testing, adjusting and monitoring of primary and
secondary device variables. Features available in the 9900 Transmitter with H COMM Module installed:
• Adjust 4 mA: Allows fi ne-tuning to compensate for errors in other equipment connected to the 9900.
Adjust the minimum and maximum current output.
• Adjust 20 mA: Allows fi ne-tuning to compensate for errors in other equipment connected to the 9900.
Adjust the minimum and maximum current output.
• Supports Multi-Drop Mode: Allows up to four 9900 Transmitters be installed in Multidrop mode.
• Supports all Universal HART Protocol Revision 7.2 commands
• Supports many Common Practice Commands
• Makes Primary and Secondary values available at PLC. Secondary values are sensor-dependent and are
available with pH, Conductivity, Resistivity, Salinity and Level sensors.
HART® is a registered trademark of the HART Communication Foundation, Austin, Texas, USA.
Any use of the term HART hereafter in this document implies the registered trademark.
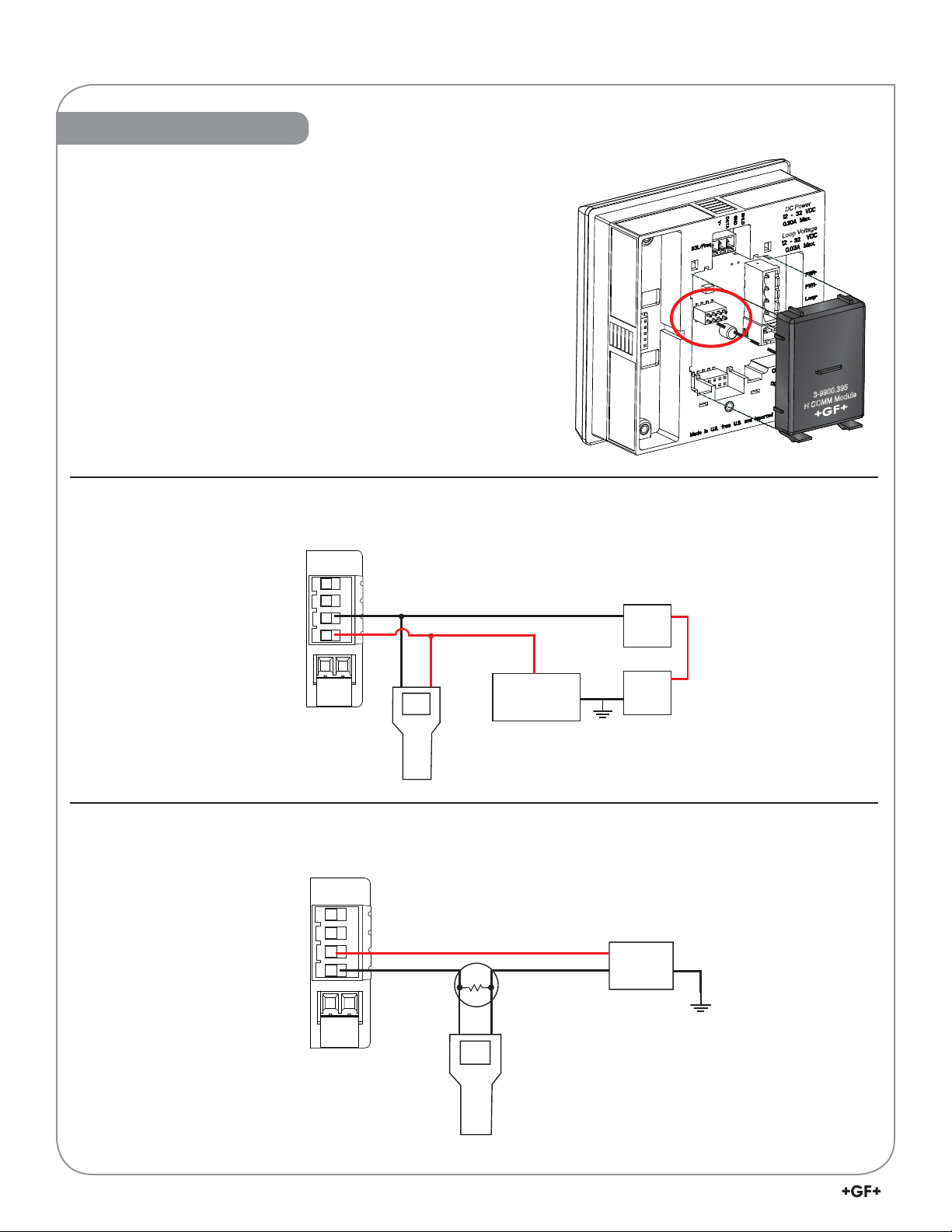
Installation
If the 9900 Base Unit will be mounted in a panel, plug-in modules may
be installed either before or after the base unit is mounted. If the 9900
Base Unit will be mounted using the accessory wall mount bracket,
install plug-in modules fi rst. If the Direct Conductivity/Resistivity
Module will be included in your unit, install the H COMM module fi rst
and then install Conductivity/Resistivity Module over the H COMM
Module.
To install the H COMM module, carefully align the module pins into its
plug (see illustration) and push the module straight in until the tabs on
the bottom edge snap into place.
DC Power
Loop Voltage
To uninstall, squeeze tabs, grasp the module and pull straight out.
Be careful not to bend the pins when installing or removing the
module to or from the base unit.
Connecting HART with a Loop-powered sensor
9900 Device
Loop +
Loop –
Connections
Black
Red
Optional ammeter
(recommended for
4 to 20 mA trim only)
Hand-held device
(Secondary HART Master)
(Typical installation)
Connecting HART to a Hand-Held Master Device
(Primary HART Master)
–
PLC
Device
+
+
Power
–
Supply
3-9900.395
H COMM Module
(Typical installation)
2
9900 H COMM Module Instruction Sheet
Loop +
Loop –
9900 Device
Connections
Red
Black
+
250
Load Resistor
Hand-held device
(HART Master)
–
Power
Supply
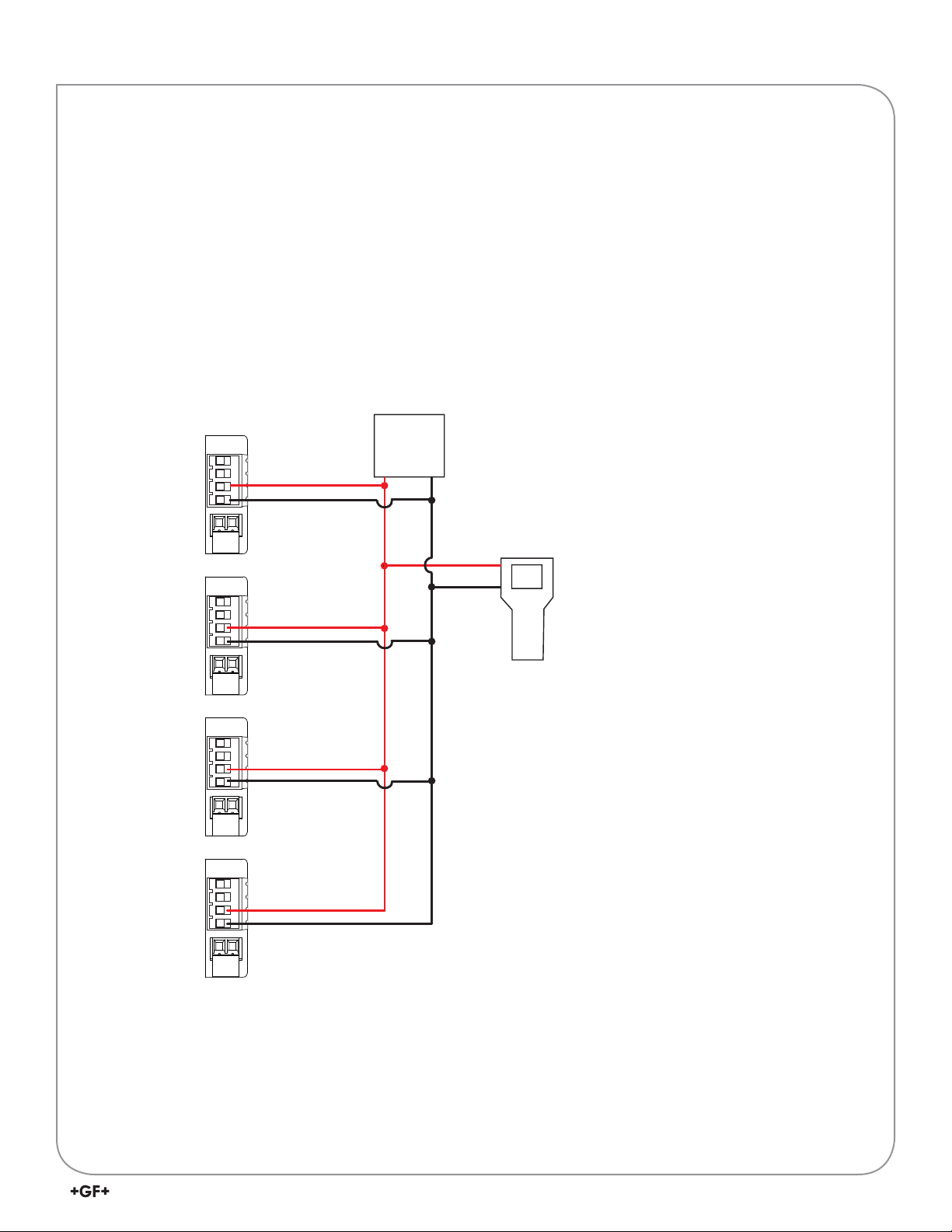
NOTE: From this point forward the term “9900 Transmitter” or “Transmitter” will assume the H COMM Module
is installed unless otherwise noted.
Multi-Drop Mode
Up to four 9900 Transmitters can be connected in Multi-Drop mode using the H COMM Module.
To ensure proper operation in Multi-Drop mode, confi gure each 9900 Transmitter with its own poll address using a
confi guration tool (laptop or hand-held device).
After confi guring the 9900 Transmitter for multi-drop function, reset the Transmitter (remove power for fi ve seconds
then apply power) before use.
Connecting HART in Multi-Drop mode
Device 1
Loop +
Loop –
Device 2
Loop +
Loop –
Device 3
Loop +
Loop –
9900
Connections
Red
Black
Red
Black
Red
Black
(HART Master)
PLC
Device
+
–
(Typical four-unit installation)
Red
Black
Hand-held device
(Secondary HART Master)
Device 4
Loop +
Loop –
Red
Black
39900 H COMM Module Instruction Sheet