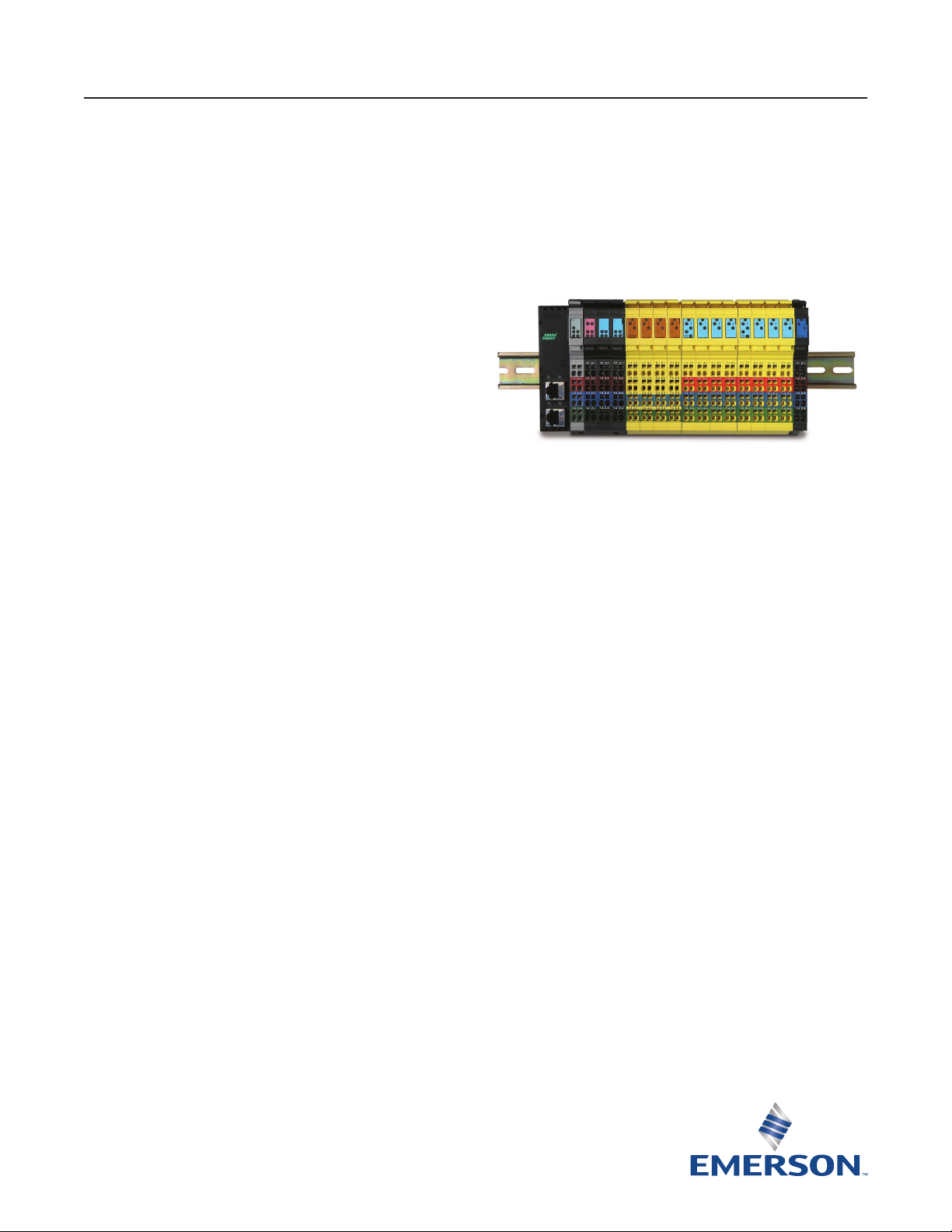
PACSystems VersaSafe
00813-0100-0110
PACSystems VersaSafe
Distributed Safety System with High Availability
At Emerson, we understand that production has
to become more efficient by enabling the operator to work closer to the process without compromising operator safety.
VersaSafe adds SIL3 machine safety capabilities
to our high performance platforms strategy.
By combining secure network connectivity,
certified safety function blocks and an easy to
use graphical programming environment,
customers can efficiently integrate standardscompliant safety capabilities to their equipment
while meeting increasingly stringent regulatory
requirements.
In addition to enabling safety functionality,
VersaSafe provides enhanced I/O control
capabilities suitable for optimization of high-end
machines.
Higher Availability
The VersaSafe distributed safety system provides a
TÜV-certified SIL3 machine safety solution that focuses on the
critical control requirements of the production environment:
safe operation and greater uptime of the manufacturing
equipment.
High availability is delivered by integrating industry-proven
PROFINET with optional media redundant protocol (MRP)
and multiple cable media options. Machine repair times are
reduced by the ability to put a machine in a safe state without
fully
powering down the equipment, enabling faster start-up after
a repair.
Simplified Architecture
VersaSafe is a member of the PACSystems control family that
delivers increased performance, greater uptime and lower total
cost of ownership. Leveraging PACSystems’ distributed I/O
architecture and single point of connect capabilities, VersaSafe
enables efficient development of high-performance
modular machines.
A single network carries standard and safety I/O; this simplifies
wiring without compromising safety.
Simplified Engineering
To minimize engineering efforts, Emerson provides a
comprehensive set of tools and services as part of the
VersaSafe solution, including a library of certified safety
function blocks, the ability to seamlessly integrate safety and
standard capabilities and a robust set of integrated
development and commissioning diagnostic utilities.
Best-in-Class Scalability
We have eliminated the need for a separate safety CPU,
enabling a highly distributed safety I/O configuration that is
both cost effective and maintains highest levels of
performance as the system grows. Emerson has also addressed
customers’ needs to make online changes to safety logic.
Large production lines, in particular, will realize considerable
benefit in the ability to update a portion of the safety logic
witout stopping the controller. Smaller machines benefit from
right-sizing the safety I/O needs without bearing the overhead
of a separate safety controller.
Data Sheet
January 2020
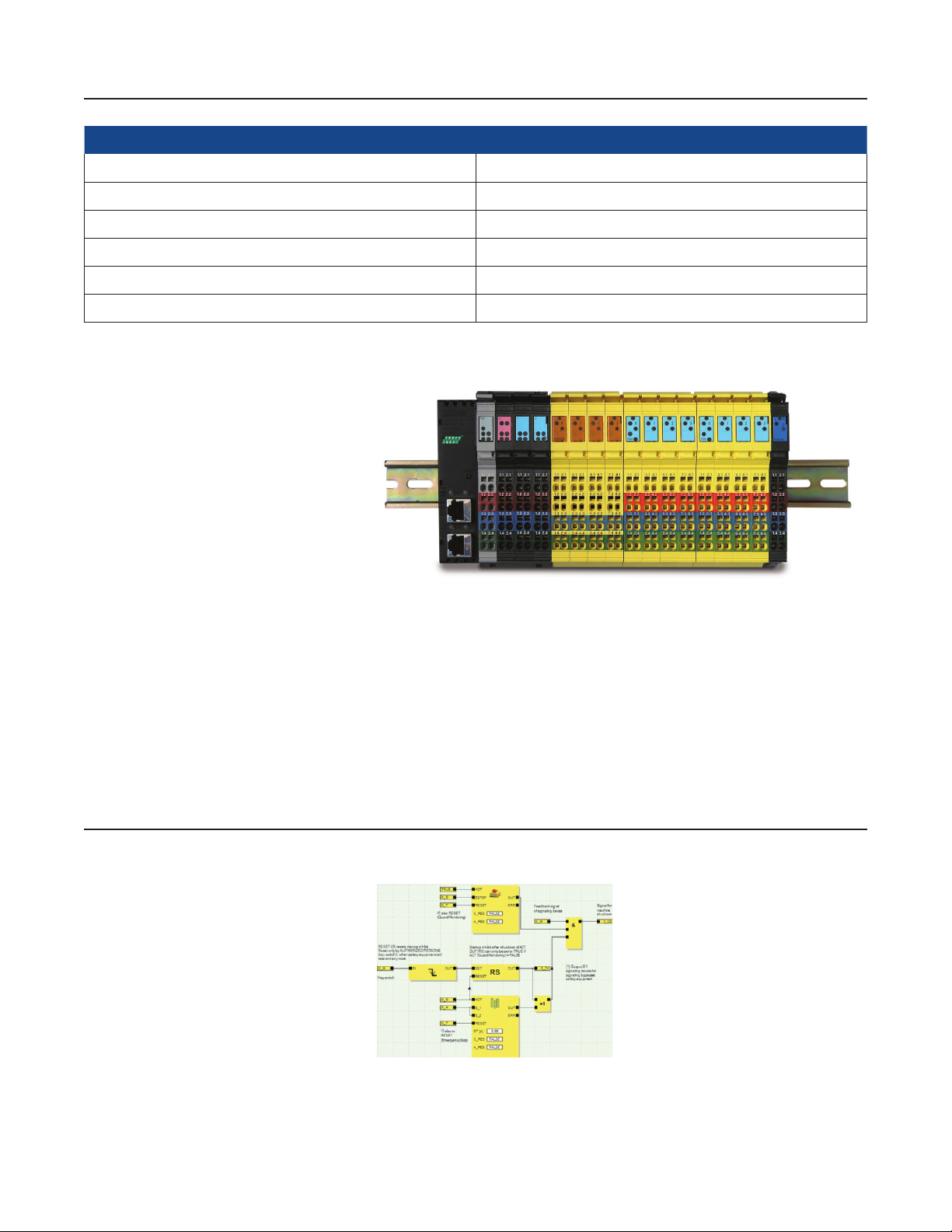
PACSystems VersaSafe
January 2020
Feature Benefit
Powerful integration tools Faster engineering, commissioning, and reduced training
Complete library of safety function blocks Simplified safety engineering due to pre-certified safety logic
Extensive safety diagnostics Shorter time-to-market
Distributed safety architecture “One solution fits all” scalability
PROFINET/PROFIBUS connectivity Distributed safe communication via an open standard network
Redundant fiber network (MRP) High availability in harsh industrial environments
Comprehensive module range
Flexible Network Interfaces
n PROFINET: 100Mbit
n Copper, fiber, cable redundancy
n PROFIBUS DP V1
Flexible Network Interfaces
n Integrated pulse output
n Configurable pulse generation
n Integrated configurable timer
n Safe digital input, 24 VDC
n Safe digital output, 24 VDC, 2 A
n Safe digital output, 24 VDC, sink/source
n Safe output, relay 4 A, 2 contacts
n Configuration of dual channel or
single channel
Standard I/O (VersaPoint)
VersaSafe also provides a wide range
of discrete, analog and special purpose
standard I/O.
Integrated Tools Enable Simplified
Creation of Safety Logic
n Extensive list of pre-certified safety function
blocks
n Simulation of safety logic
n Combination of safe logic and standard logic
n Easy-to-use and flexible configuration
n Tools to validate and document the safety
project
n Graphical BOM configurator
Easy Programming with Graphics
Tools
Global Standards
n CE, UL, CUL approved
n Maximum Safety Levels:
– IEC 61508: SIL 2, SIL 3
– IEC62061: SIL CL 3
– ISO 13849-1: PL d, PL e
– Category: Cat 2, Cat. 4
n Safety level depends on configura-
tion
and wiring
n Operation temperature: -25°C to
+55°C
www.Emerson.com2

PACSystems VersaSafe
00813-0100-0110
Data Sheet
January 2020
United States Office
Emerson Automation Solutions
Intelligent Platforms, LLC
2500 Austin Dr
Charlottesville, VA
China Office:
Emerson Automation Solutions Intelligent
Platforms (Shanghai) Co., Ltd
No.1277, Xin Jin Qiao Rd, Pudong,
Shanghai, China, 201206
Singapore Office
Emerson Automation Solutions Intelligent
Platforms Asia Pacific Pte. Ltd.
1 Pandan Cres,
Singapore, 128461
Germany Office
Emerson Automation Solutions
ICC Intelligent Platforms
GmbH
Memminger Straße 14
Augsburg, DE 86159
Brazil Office:
Emerson Automation Solutions
Rua Irmã Gabriela, 51 – Cidade Monções
São Paulo – SP, 04571-130
India Office
Emerson Automation Solutions
Intelligent Platforms Pvt. Ltd.,
Building No.8, Ground Floor Velankani Tech Park, No.43
Electronics City Phase I, Hosur Rd
Bangalore-560100
©2020 Emerson. All rights reserved.
The Emerson logo is a trademark and service mark of Emerson Electric Co. All other marks are
property of their respective owners.
The contents of this publication are presented for information purposes only, and while
effort has been made to ensure their accuracy, they are not to be construed as warranties or
guarantees, express or implied, regarding the products or services describe herein or their
use or applicability. All sales are governed by our terms and conditions, which are available
on request, We reserve the right to modify or improve the designs or specifications of our
products an any time without notice.