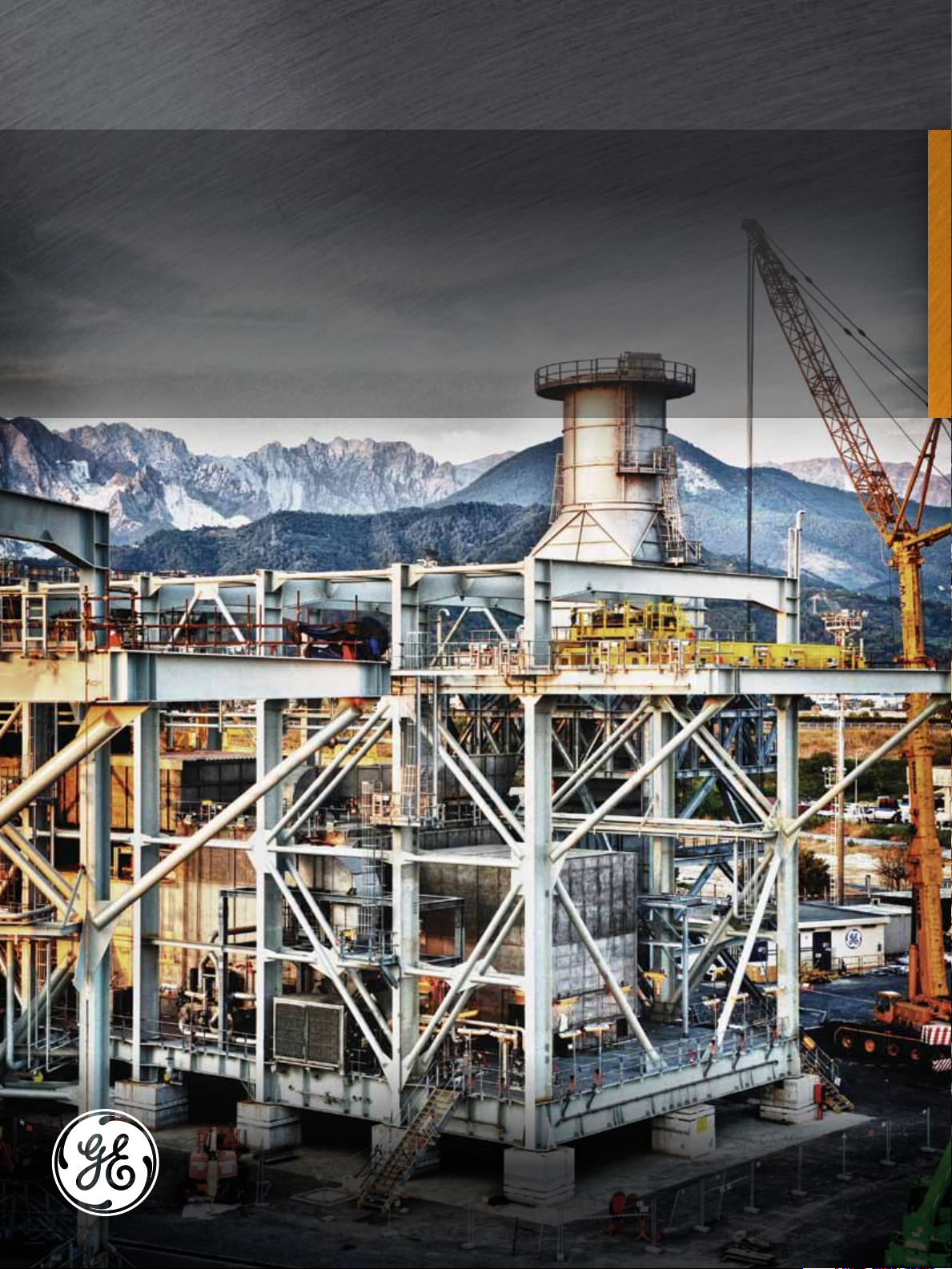
GE Oil & Gas
Module Solutions
Plug & play power-generation and compression solutions
to increase efficiency, reliability and power
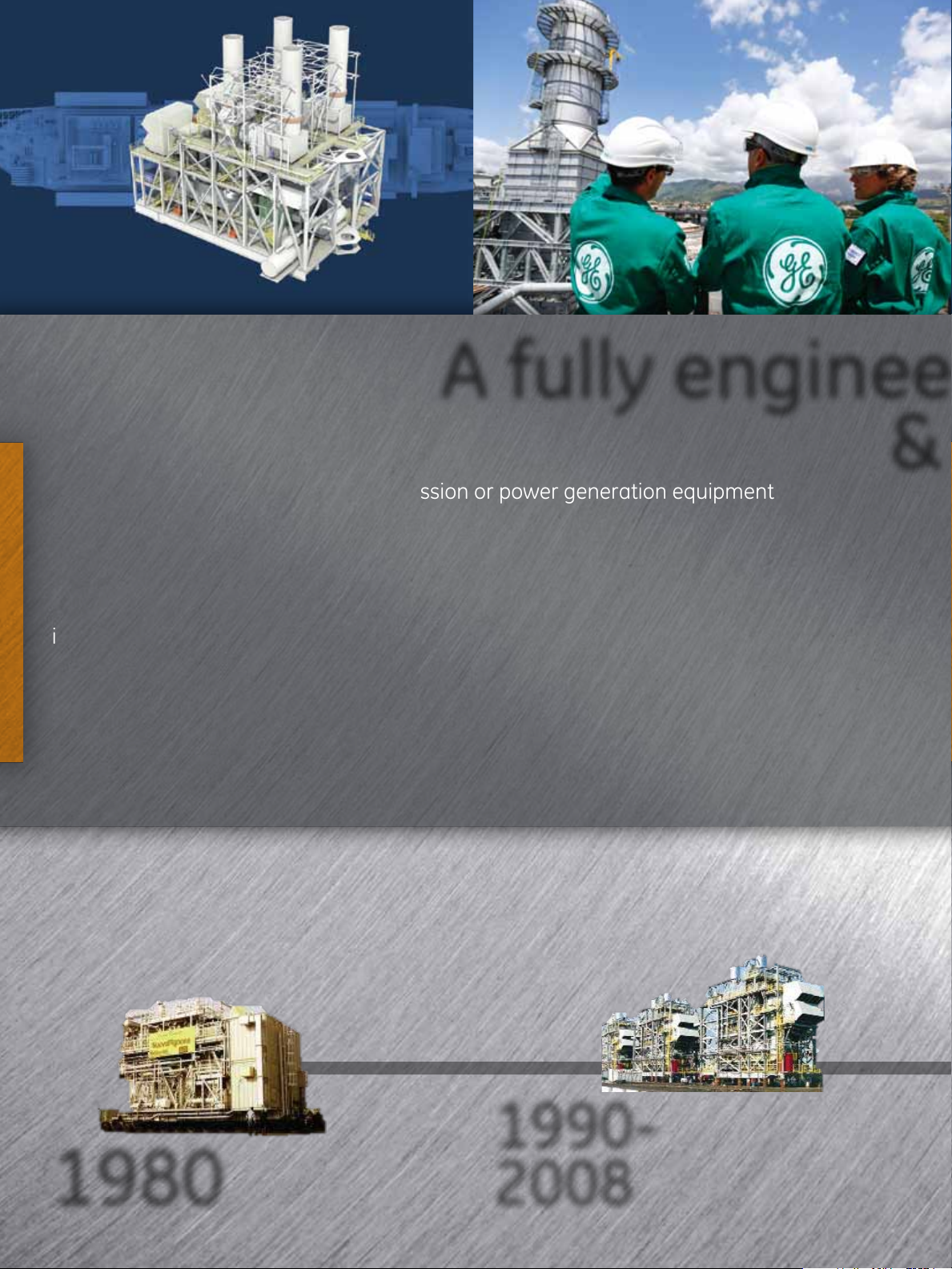
A fully engineered
Customized design
Optimized configuration of gas compression or power generation equipment
and auxiliaries, 100% tailored to customer needs
Integrated assembly
A fully transportable single package available with a dedicated control room
installed – ready for single lift or roll on/off
Complete testing
Fully engineered and tested solution designed to minimize risk during the installation
phase and enable cycle time reduction
Continuous evolution of proven technologies
& tested solution
and innovative processes
Buchan Field
1980
Gas lift
19902008
Brazilian Modules
Campos Basin system:
PG & EMC modules
assembled in Brazil
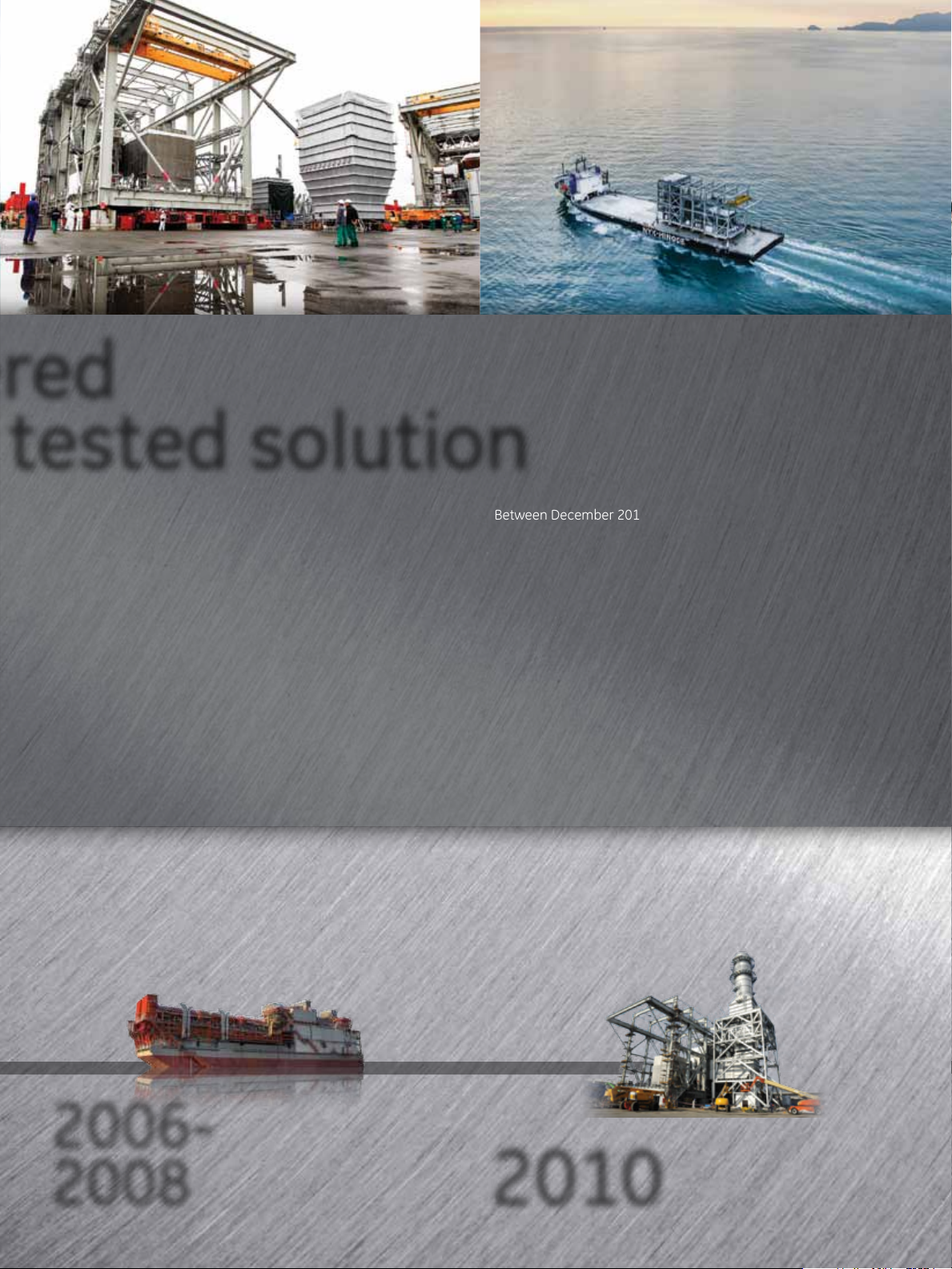
There are three equally important parts to delivering
truly successful modular solutions. First, is the crossfunctional engineering expertise to design them using
the most advanced technologies available. Second,
is the capacity and project management strength to
assemble them. Finally, is the crucial ability to test
them and ensure they will perform as designed.
GE Oil & Gas has been systematically evolving the modular
approach to turbomachinery design since 1985. In that time,
we have supplied over 40 pre-assembled power generation and
compression modules, customized to meet the specific needs of
their increasingly challenging projects around the world.
Between December 2012 and the end of 2013, we will deliver
seven of the industry’s most advanced modules ever, five for
Australia and two for the North Sea. And we have the capacity to
produce more.
We continually invest significant resources in materials,
aerodynamics and every other conceivable area – including
perhaps the most important one of testing and qualification. We
also work closely with key industry-leading clients to ensure that
our direction is always true to their needs and where the industry
overall is moving.
As a result, GE’s latest modular solutions make the difference between
‘gathering acceptable parts’ and ‘creating an exceptional whole’.
20062008
Kashagan
The highest pressure
compressor ever built
2010
Gorgon
5 x MS9001E GTG
modules fully tested
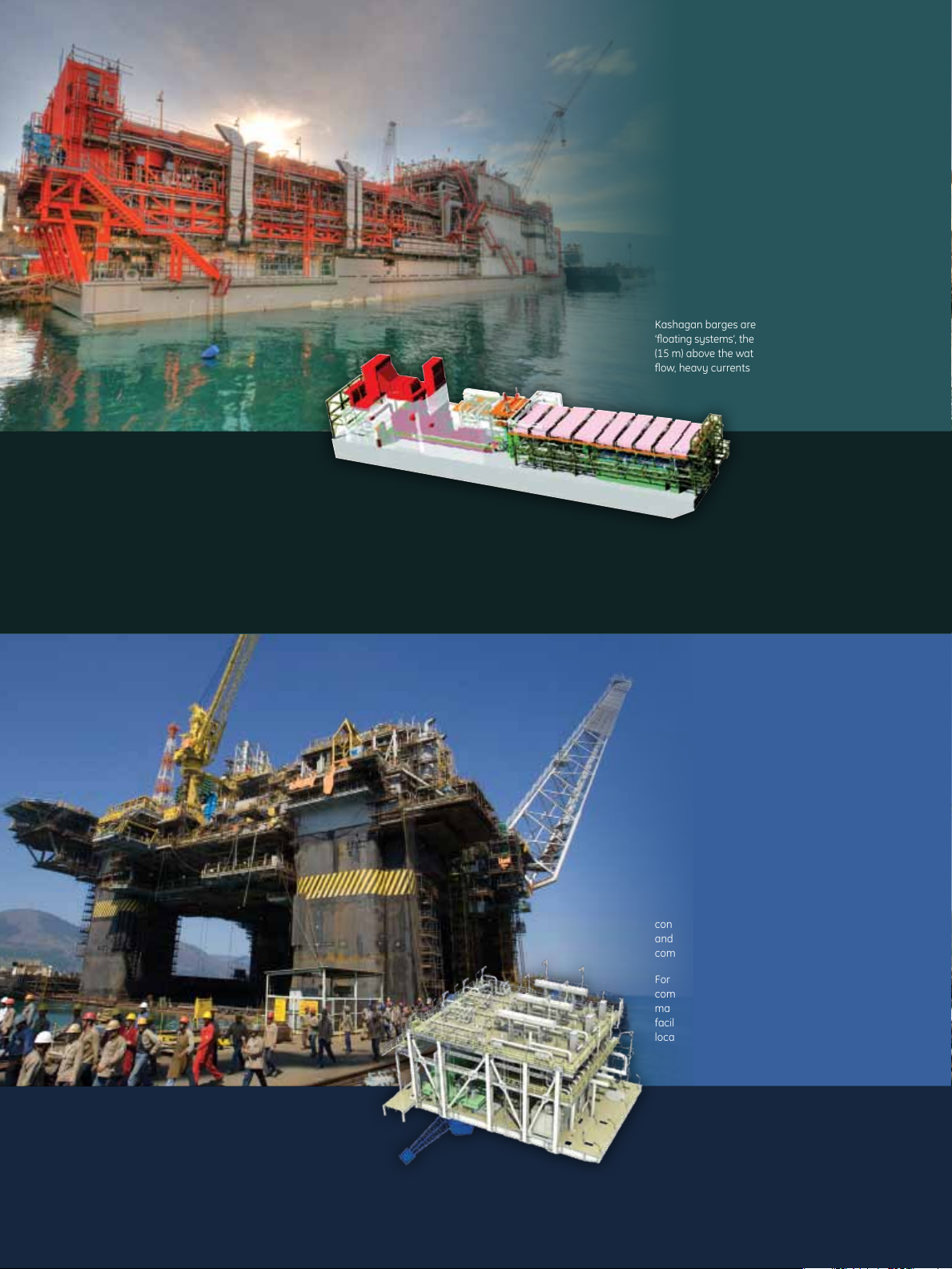
Kashagan gas compression system
• 2 full process floating modules
• 820 bar compression system
• Zero leakage technology for 33% H
• 95 x 16 x 25 m each barge
• 4,000 tons each barge
• 19,757 welded joints, 150 km of wires, 7 km of piping
S
2
With 18% H2S and pressures of 760 bar, Kashagan
is the most advanced project of its kind. The
modular gas compression system we designed for
it, is the highest-pressure re-injection train ever
built—capable of 820 bar and 33% H
The two trains were mounted on barges specially
designed for transport along the winding Volga
canal system. For improved maneuverability and
installation, our designs were about 500 tons lighter
than other existing barges for similar operations.
To pass under many bridges and other obstacles
during transport, all topside structures above 36 ft
were dismantled at our yard in La Spezia and
reassembled at the Caspian yard.
The barges then went 60 km into the Caspian Sea
in depths of just 3 m—each one carrying a full
32-MW/820-bar compression island. Although our
Kashagan barges are commonly referred to as
‘floating systems’, they are actually suspended 49 ft
(15 m) above the water to avoid damage by ice
flow, heavy currents and storms.
S.
2
Floating production modules
• 2 compression modules for P51
• 2 compression modules for P52
• 2 power generation modules for P54
• 2 compression modules for P56
To help Petrobras develop the 8 billion barrels
of oil in the Bay of Santos, our solution went far
beyond the usual capabilities of our own facilities
in Italy. We worked closely with Petrobras and local
contractors to design, build and operate a worldclass assembly yard in Brazil, developing the local
workforce and infrastructure in keeping with the
Petrobras vision.
We began in 2004 with two compression modules
for the P51 floating production unit (FPU) to be
deployed in the deepwater Marlim Sul Field. As
progress continued, we simultaneously built two
larger compression trains for P52 and two powergeneration modules for P54—so that there were
six modules under parallel construction using local
contractors for steel work, fabrication, engineering
and other activities. In 2010, we delivered two
compression modules for the P56 FPU.
For all these modules, core equipment (motorcompressor units and turbogenerator trains) was
manufactured and tested at the GE Oil & Gas
facilities in Massa, Italy and shipped to Brazil for
local assembly and construction.