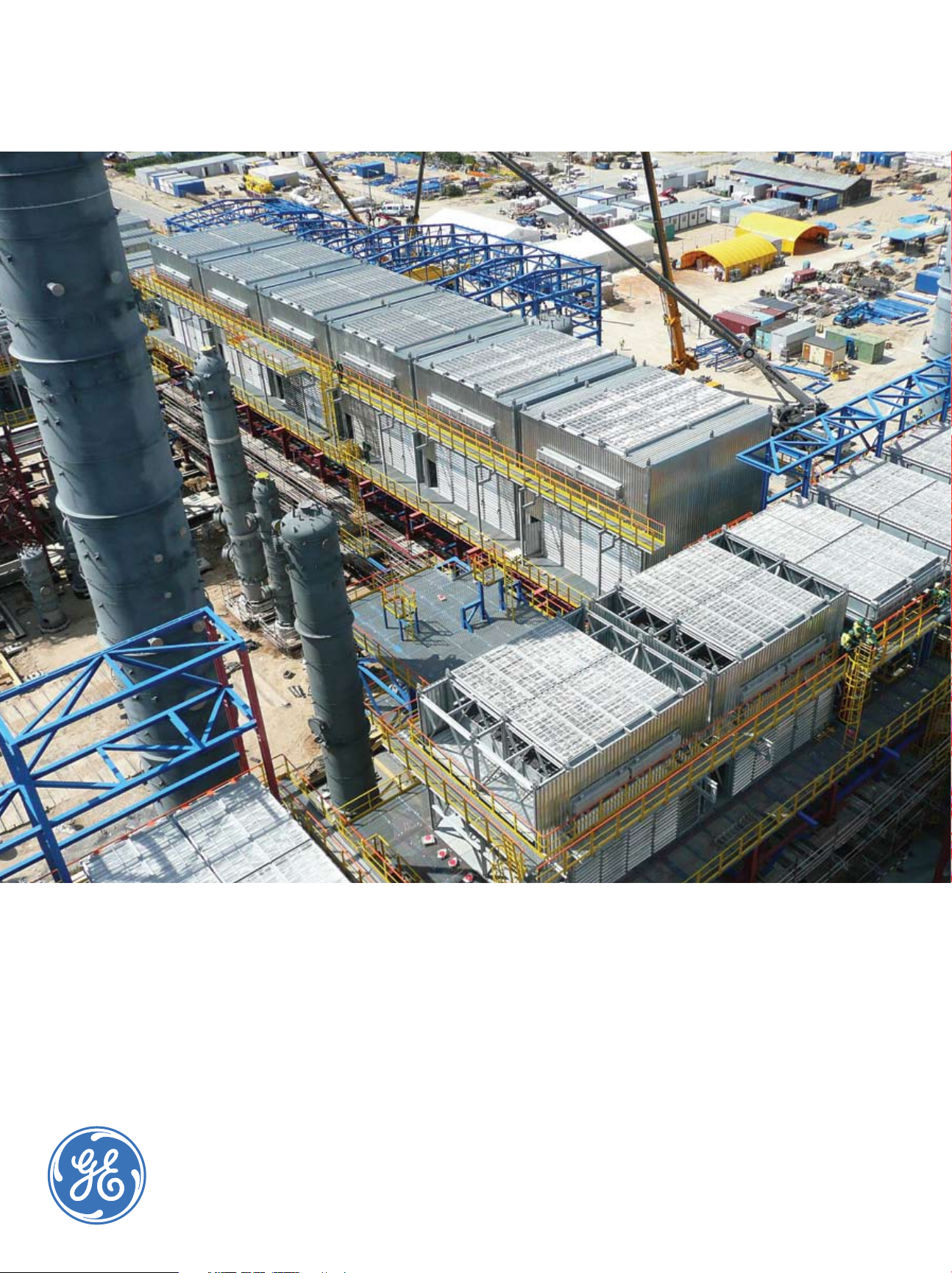
GE Oil & Gas
Air cooled heat exchangers
Robust and reliable for all loads and applications
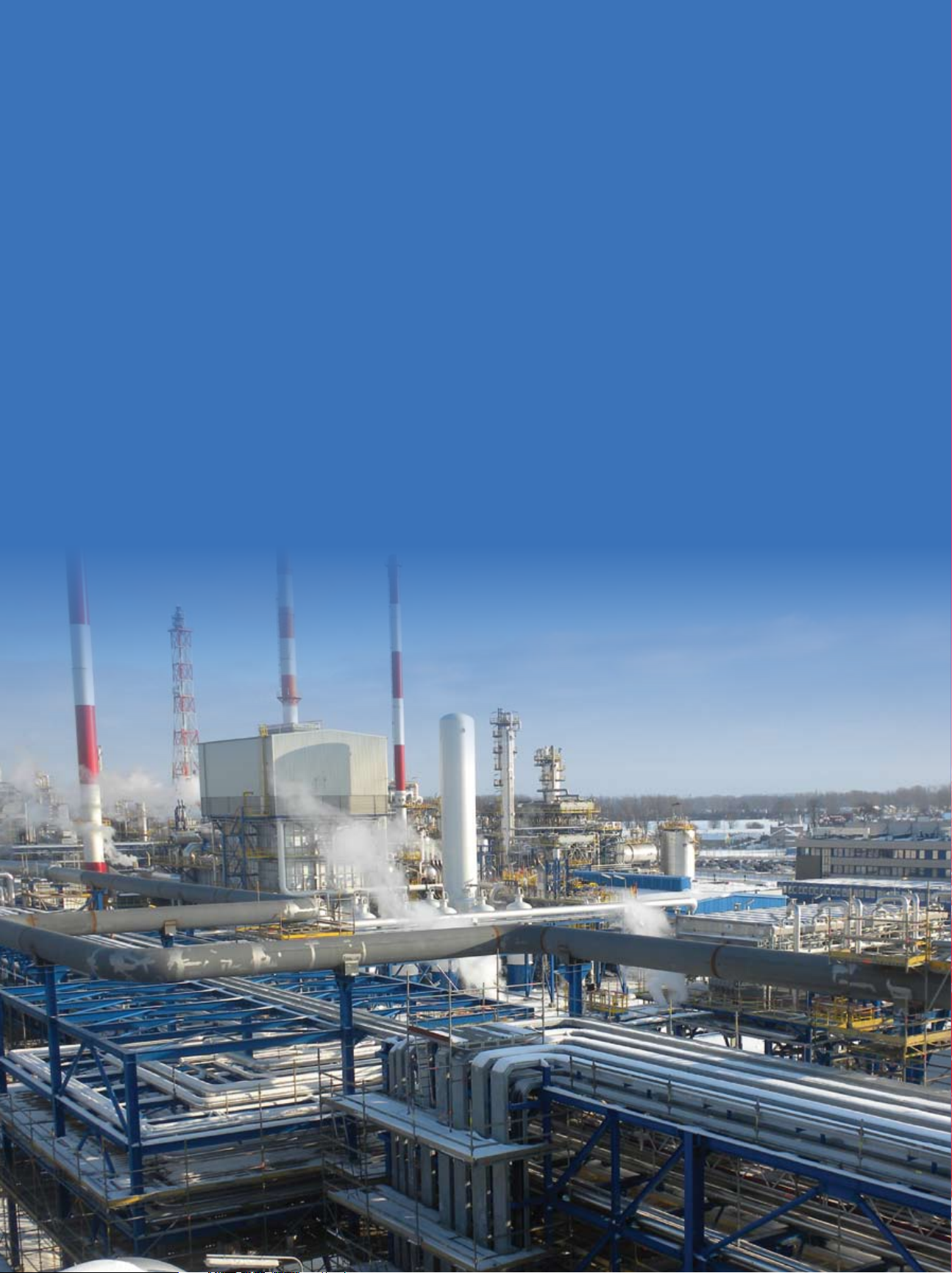
What it is
Air cooled heat exchangers are commonly used in industrial applications
where a reliable source of water is not available as a cooling medium. Air cooled
steam condensers are a special type of heat exchanger employed to condense
steam at the exhaust end of a steam turbine for both power generation and
mechanical drive applications.
How it works
The hot process fluid to be cooled flows through finned tubes while the cooling
air flows across the outer surface to remove heat. The cooling air is propelled by
fans in either a forced draft or induced draft configuration.
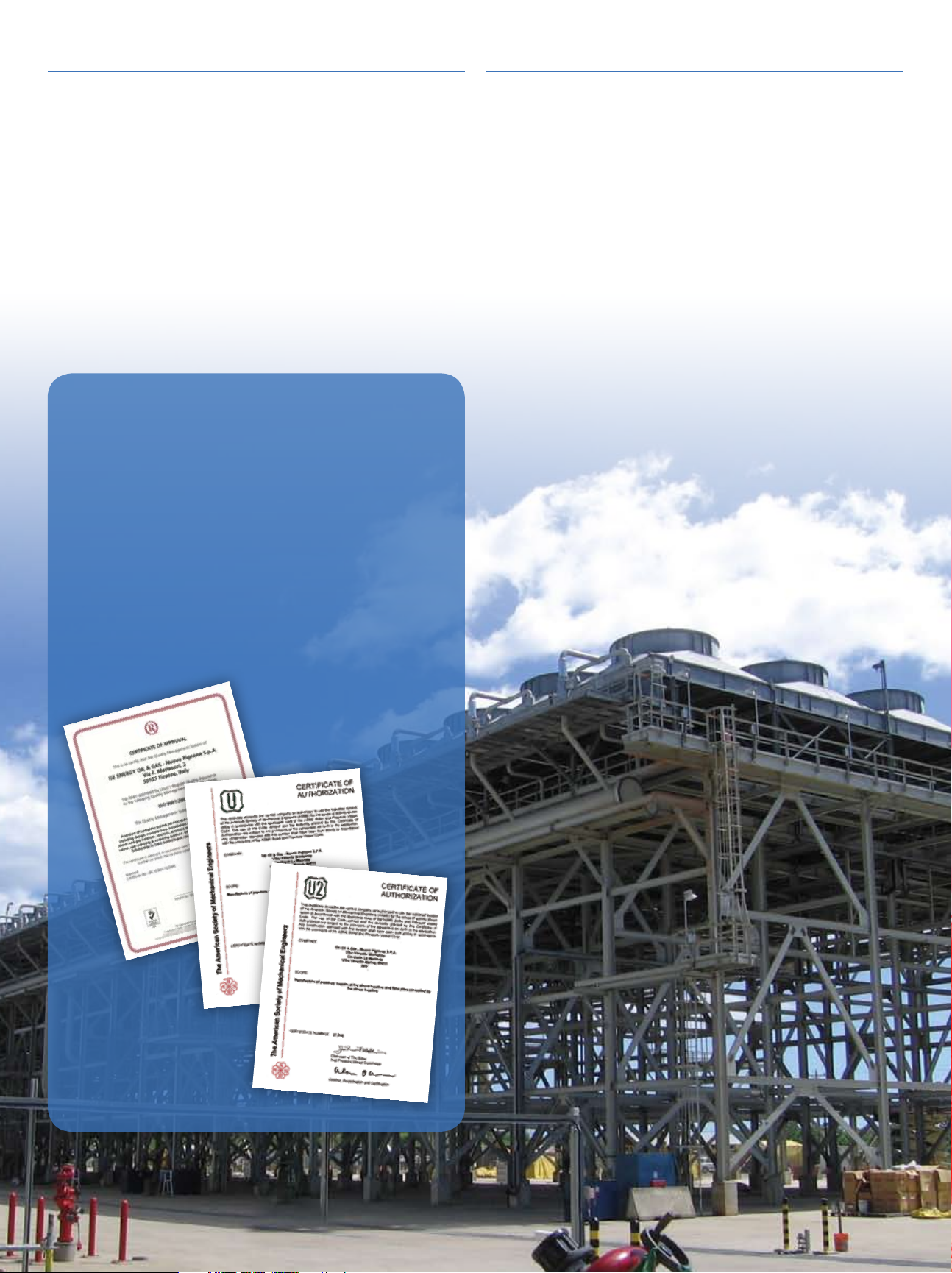
Worldwide presence
Experience makes the difference
GE’s Oil & Gas business has more than 100 years of industry
experience and 5,500 employees worldwide. Our Air Cooled Heat
Exchanger team is centered in Vibo Valentia, Italy, and is an
integral part of the larger Oil & Gas organization headquartered in
Florence. Together, we provide complete solutions to all industry
segments – with a broad and expanding portfolio of advanced
technologies, plant equipment and services.
We are a global company with a local touch. Our highly
experienced personnel offer comprehensive customer support
backed by immediate access to all of GE’s broad resources. Our
people understand the local customs and regulations, and can
help you identify and track growth opportunities.
All our manufacturing processes are implemented in strict
accordance with GE’s world-class Six-Sigma quality system,
which conforms to all major international quality assurance
standards including ISO9001, BS5750 and UNI EN 29001.
Compliance of the QA system with these standards is
certified by LLRR.
We have been a global leader in the fabrication of air cooled heat
exchangers and steam condensers since the late 1960s. The first
high tech pipe and bend air cooled heat exchanger we supplied in
the early 1970s was for sweet gas with pressure slightly over 300 bar.
Our latest applications are for more than 650 bar with H2S content
as high as 18%. We have supplied more than 10,000 bundles
for applications throughout the industry from upstream to
hydrocarbon processing. Our investment in technology continues
in an effort to meet even more extreme conditions.
The quality of our exchangers is a result of advanced design
techniques employing the latest software, world-class fabrication
facilities and capabilities, Six-Sigma quality methodology and
extensive experience in both manufacturing and in-field service.
Focused on
quality
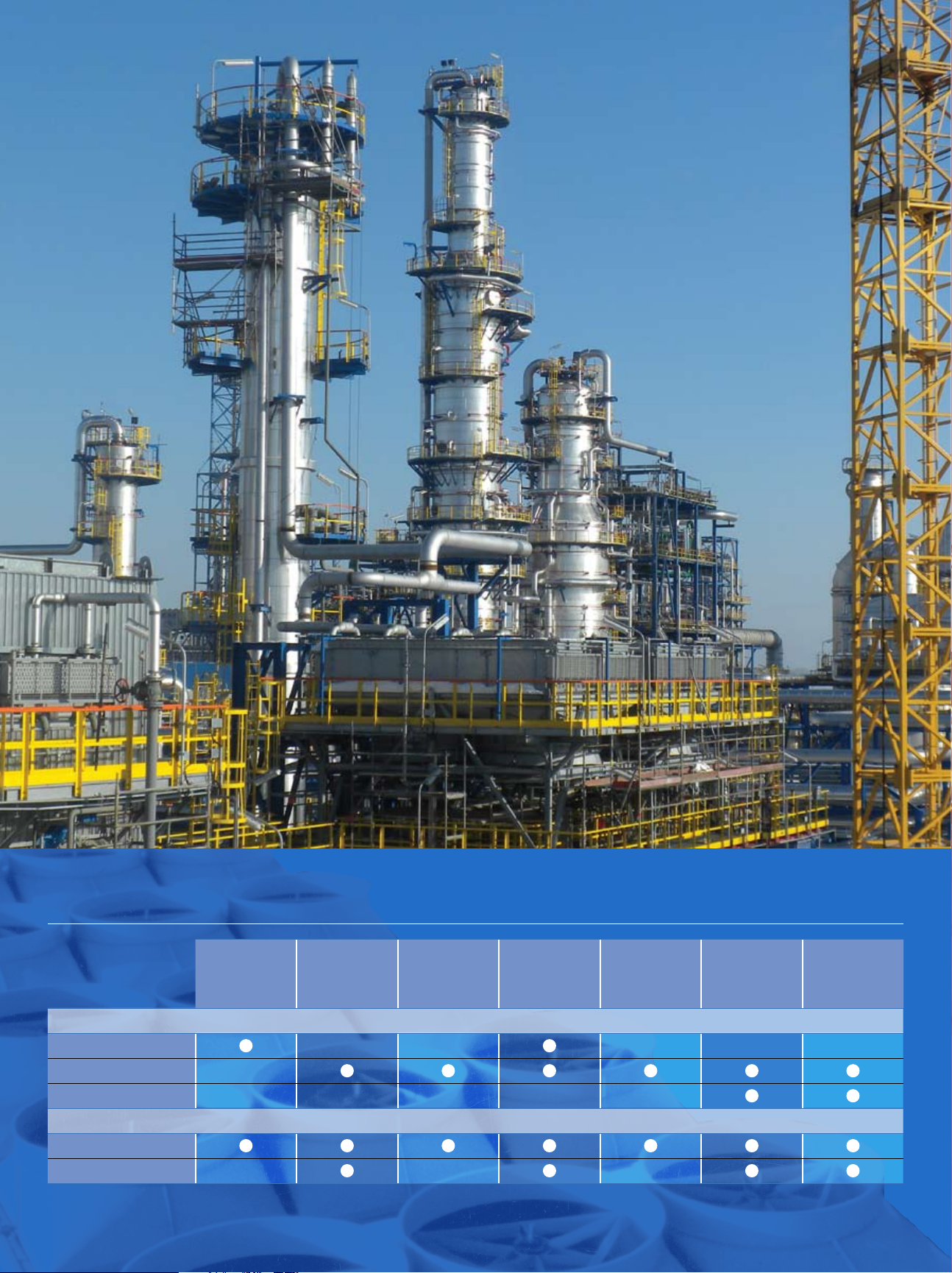
A complete range of products
Header configuration
Pipe & bend
Plug box
Cover plate
Finning type
Extruded/Embedded
L-footed
Gas
re-injection
Gas
compression
& gathering
gas lift
Liquefied
natural gas
Gas pipelines &
storage
Gas-to-liquids
Refineries &
petrochemicals
Machinery lube
oil cooling