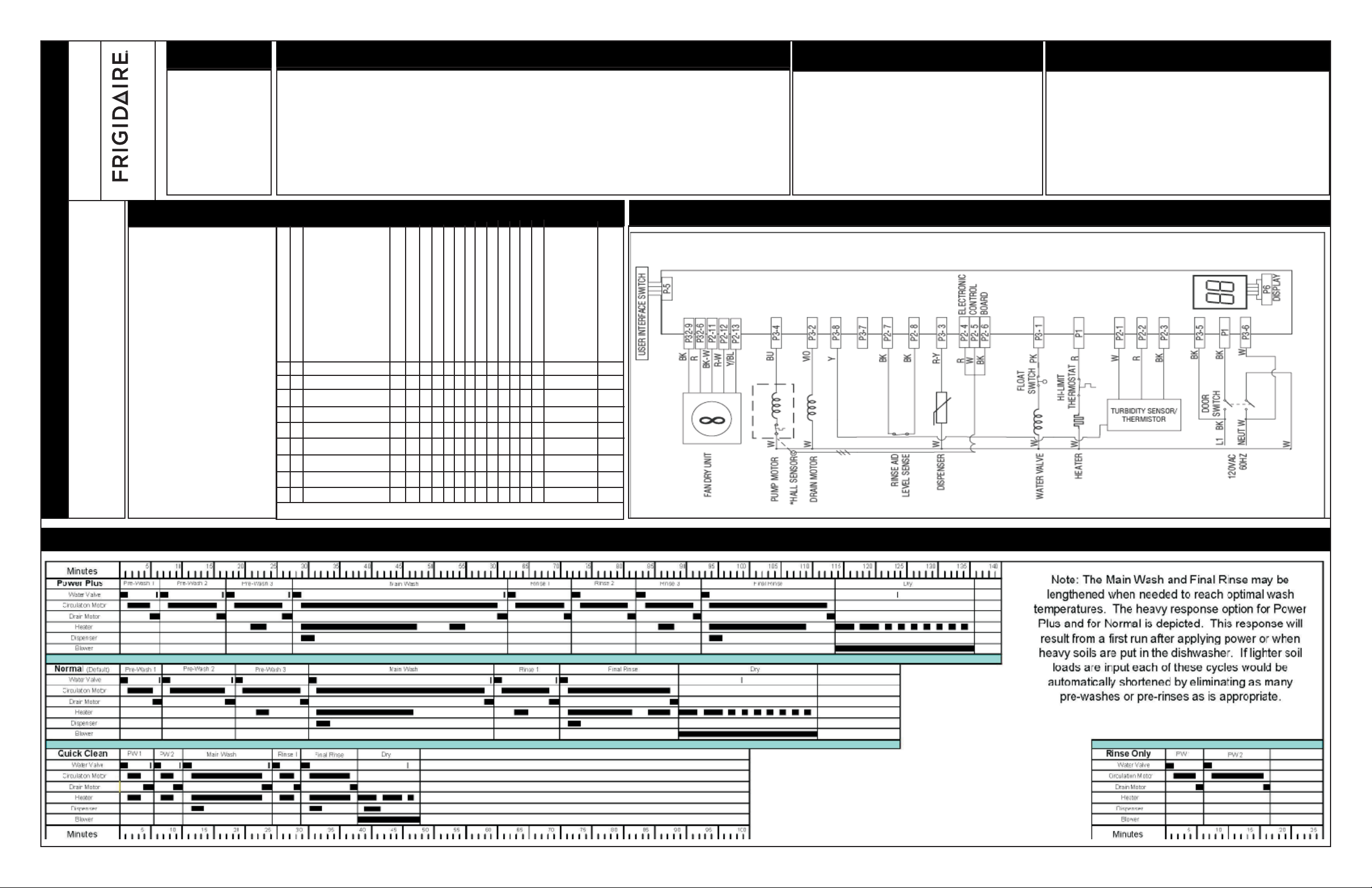
COLOR CODE
BK............Black
BU............Blue
PK............Pink
R..............Red
Viol..........Violet
W.............White
Y-BK.........Yellow/BK
Electronic Series
R-Y............Red/Yellow
BK-W........Black/White
R-W...........R ed/White
P/N: 154889701 Rev.C
Artwork: 154889701 Rev.003
To activate the Water/
Service Test, cycle the
circuit breaker to put the
unit in Power F ailure Mode.
Simultaneously press “DRY”
and START/CANCEL for 3
seconds.
The dishwasher will then
step through the test cycle
per the chart. If START/
SERVICE DATA SHEET
This information is intended for use by persons having electrical and
mechanical training and a level of knowledge of these subjects generally
considered acceptable in the appliance repair trade. Electrolux Home
CANCEL is pressed during
the test the current step
is terminated and the test
advances to the next cycle
step.
Products North America cannot be responsible, nor assume any liability,
for injury or damage of any kind arising from the use of this Service
Data Sheet.
OPERATION
The dishwasher responds to user inputs only when its door is open.
To select a new
cycle or option: Press to select desired cycle and/or option (indicator lights will change).
To delay start : Press DELAY START repeatedly until the desired delay time is displayed.
For controls
lock: Press and hold DELAY START for 3 seconds (its LED will illuminate when lock is
set)
To start: Press START/CANCEL and close the door.
WATER/SERVICE TEST
Fill Number
Interval Number
1
1
Fill/Det. Dispenser
Fill
1
2
Wash/Heat/Det.Disp.
3
1
Pause
41
5
Wash/Heat
1
Wash/Heat/Det.Disp.
61
71
Drain
Dry
81
End State
91
Description
Water V a vle
Interval Duration Sec.
1
60
1
27
45
0
0
0.4
0
75
60
0
90
00
90
00
Circulation Motor
Drain Motor
0
0
0
0
0000
0
1
1
0
0
1
0
1
1
0
1
1
0
1
1000
1
Heater
Blower
Dispenser
1
1
0
0
0
0
0
000
1
1
1
Washing LED
0
1
1
0
1
0
1
0
0
0
0
11
Note: End State remains in effect until door is opened
Sensing LED
Drying LED
Sanitize LED
Clean LED
1
0
0
0
0
0
1
0
1
0
0
0
0
1
1
0
0
0
0
1
0
1
0
0
0
0
000 0 0
0
1
0
0
0
0
0
Rinse LED
Monitored Device
fan damper
turbidity
hall sensor
thermistor
fan speed
fan damper
On display upon detection of
failure
uo
tu
hS
th
uF
uC
DISPLAY CODES (READOUT)
PF------- A Power failure has occurred
Hd------- Water heating delay
CL------- Close and Latch the door
ER/ER--- Switch failure
ER/CE--- Confi guration Error
ER/uo--- Vent will not close
ER/uF--- Fan not running
‘01-24’--Hour(s) delay before Start
WIRING DIAGRAM
(some models)
DISPLAY CODES (LED)
SENSING---Turbidity sensor is checking the condition of the wash/
rinse water. No sensing for LIGHT WASH(Upper Rack), LIGHT W ASH
(Lower Rack) and CHINA/CRYSTAL.
WASHING---Washing portion of cycle.
SANITIZED---The SANITIZED criteria has been met. Indicator light
will switch off when door is opened.
DRYING---Drying portion of cycle.
CLEAN---Shows completion of cycle, Indicator light will switch off
when door is opened.
OPTION LED’s FLASHING --HI-TEMP WASH and NO HEAT DRY/
POWER DRY OFF LED’s fl ashing indicates power failure has occurred.
Press START/CANCEL pad and reselect desired options and cy cles.
(Some Models)
CYCLE SELECTION OPTIONS
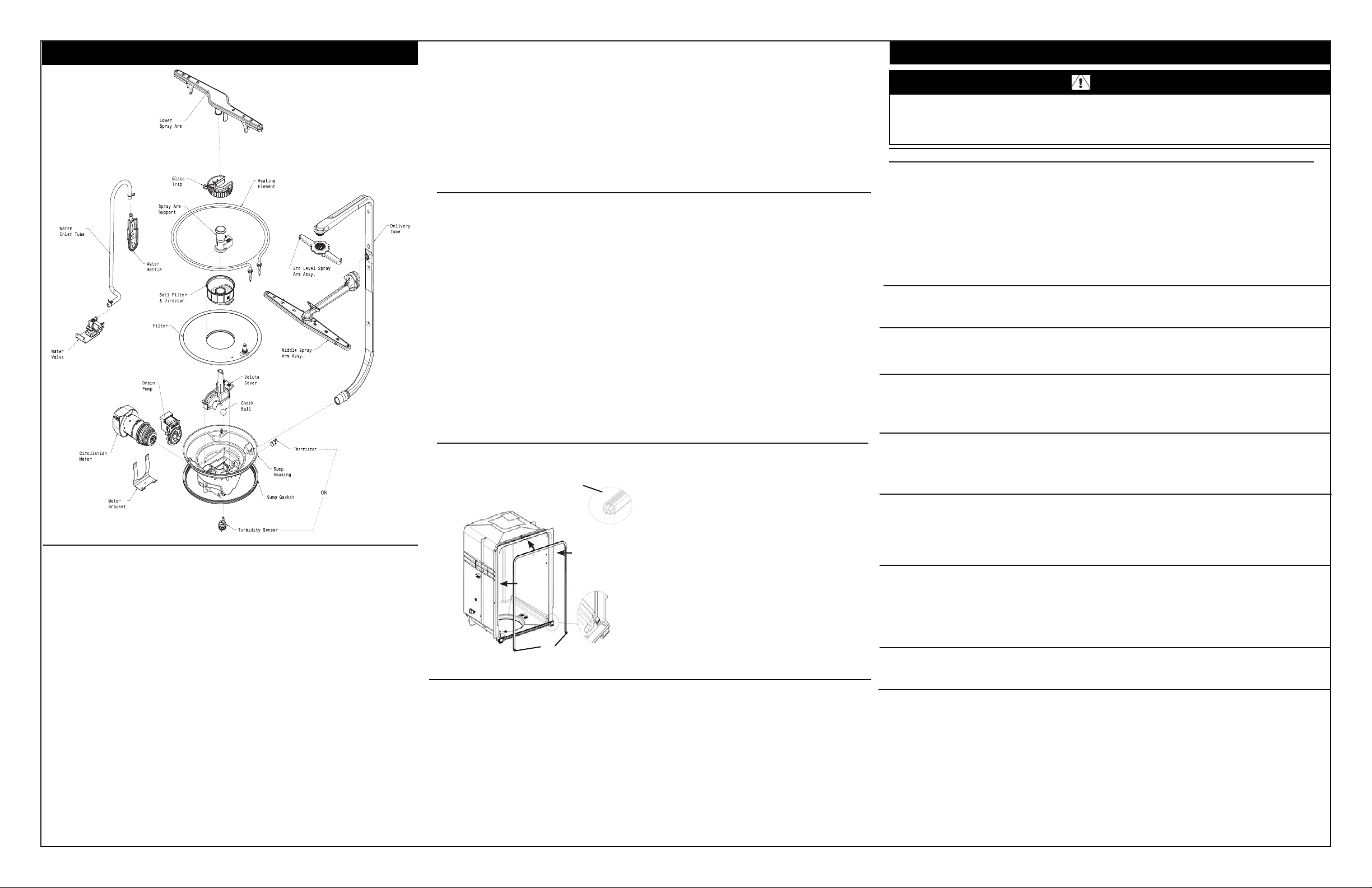
EXPLODED VIEW OF WASH SYSTEM
Standard Dry Air Flow
TROUBLE SHOOTING TIPS
The heating element at the bottom
of the tub and the vent assembly in
the top right rear of the tub are used
to dry dishware. During the “dry”
portion of the cycle the heater, the
solenoid that opens the vent’s damper
and the vent fan are energized. The
vent fan draws in cooler, drier air from
outside the tub and pushes it down
into the tub. Hot moist air rises to
Detergent and Rinse
The detergent and rinse aid dispenser
is a one piece component consisting
of a molded detergent cup and a
built-in rinse aid dispenser.
The detergent cup has a spring
loaded cover and the rinse aid
dispenser has a removeable cover.
To re-fi ll, remove the cap and poor
rinse aid in until the level shows
above the bottom of the cylindrical
opening and the sight gauge changes
appearance. If any is spilled wipe
it up before starting the cycle. The
amount of rinse aid released
the duct inlet near the top of the door.
At the duct exit near the bottom of the
door drier air escapes into the kitchen
and the condensed water runs into the
drain portion of the dishwasher. Energy
from the heating element warms the
incoming air and augments the energy
stored in the dishware. Together their
energy causes the water on the dishware
to evaporate.
can be adjusted by turning the arrow
indicator from one, being the least
amount, to four, being the greatest
amount.
To replace dispenser:
• shut off electricity to dishwasher,
• remover outer door panel assembly,
• disconnect wiring to the actuator,
• remove the six screws,
• remove the dispenser,
• replace and reinstall screws,
• rewire actuator.
WARNING
Personal Injury Hazard
Always disconnect the dishwasher from the electrical power source before adjusting or
replacing components.
Symptom
Dishwasher will not operate
when turned on.
Motor hums but will not
start or run.
Motor trips out on internal
thermal overload protector.
Dishwasher runs but will
not heat.
Check the Following
1. Fuse (blown or tripped).
2. 120 VAC supply wiring
connection faulty.
3. Electronic control board
defective.
4. No 12 VAC power to control.
5. Motor (inoperative).
6. Door Switch (open contacts).
7. Door latch not making contact
with door switch
8. Touch pad circuit defective.
9. No indicator lamps illuminate
when START or OPTIONS are
pressed.
1. Motor (bad bearings).
2. Motor stuck due to prolonged
non-use.
1. Improper voltage.
2. Motor windings shorted.
3. Glass or foreign items in pump.
1. Heater element (open).
2. Electronic control board
defective.
3. Wiring or terminal defective.
4. Hi-Limit thermostate defective.
5. Thermistor failure.
Remedy
1. Replace fuse or reset breaker.
2. Repair or replace wire
fasteners at dishwasher
junction box.
3. Replace control board.
4. Replace control board.
5. Replace motor/impeller
assembly.
6. Replace latch assembly.
7. Replace latch assembly.
8. Replace console assembly.
9. Replace console assembly.
1. Replace motor assembly.
2. Rotate motor impeller.
1. Check voltage.
2. Replace motor/impeller
assembly.
3. Clean and clear blockage.
1. Replace heater element.
2. Replace control board.
3. Repair or replace.
4. Replace thermostat.
5. Replace turbidity sensor.
Pump Assembly
The pump assembly is driven by a
synchronous motor. Rotation is in the
counterclockwise direction at up to
3600 RPM. The motor drives a pump
which supplies 100 percent fi ltered
water at a rate of approximately 12
GPM to one spray arm at a time. The
spray arm’s operation is alternated by
small “pauses” of the motor during
the wash cycle.
Draining is accomplished by using
a small seperate synchronous drain
pump mounted to the side of the
sump. The drain check valve is
located at the discharge end of
the drain pump. The drain hose is
attached by a worm gear clamp to the
discharge end of the drain pump.
The drain hose must have a loop at
a minimum height of 32 inches
in order to insure proper drainage.
To remove the main circulation
(circ) pump do the following in
sequence: Shut off electricity to the
dishwasher. Disconnect the wiring
harness connections located at the
circ pump’s motor. Remove the two
screws that hold the motor bracket.
Slide the motor bracket away from
the sump. The motor and pump,
now held only by friction against
O-rings, can be pulled out of the
sump.
Tub and Door Seal
Mounting Rib
Tub Interior
Short Turn
Line up the center mark on the back of the
seal with the tub top center and press it
into the channel. Move along the channel
left and right periodically pressing the seal
into place without bunching or stretching it
until going around the corners at the top.
Next, place the free ends into the channel
at the bottom left and right by creating
a short turn at the bottom of the tub
channel and ensuring the seal extends to
the locator ridge at the bottom of the tub
(see enlarged portion of the image at left).
Then, press the seal periodically into place.
Finally slide your fi ngers over the seal to
press it fully in place. When complete a
single face of the seal should be visible
and fl ush with the edge of the channel.
Product Specifi cations
Electrical
Rating......................................120 Volts, 60Hz
Separate Circuit..15 amp min......- 20 amp max.
Motor (Amps)............................................1.8
Heater Wattage.........................................900
Total Amps (load rated).............................10.0
TempAssure......................................140
(60
TempBoost........................................145
(63
Sanitize.............................1500F+50F (660C+30C)
0C+30
-
C) [with outer door in place]
0C+30
-
C) Heated Wash/Heated Rinse
-
Hi-Limit Thermostat .......................2000F (930C)
0F+50
0F+50
Water Supply
Suggested minimum incoming water
temperature...........................120
Pressure (PSI) min./max...................20/120
Connection..............................3/8” NPT or
3/4” Hose Thread
-
-
Consumption (Normal Cycle).......................
F
4.9 - 9.7 U.S. gal., 18.5 - 36.7
Water valve fl ow rate (U.S.GPM)..............83
-
F
Water recirculation (U.S. GPM)....................
approx. 12
Water fi ll time........................................87
0
F (49
Detergent cover will not
latch or open.
Dishwasher will not pump
out.
Dishwasher will not fi ll with
water.
Dishwasher water siphons
out.
Detergent left in dispenser. 1. Detergent allowed to stand too
0
C)
1. Latch mechanism defective.
2. Electronic control board
defective.
3. Wiring or terminal defective.
4. Broken spring (s).
5. Defective actuator.
1. Drain restricted.
2. Electronic control board
defective.
3. Defective drain pump.
4. Blocked impeller.
5. Open windings.
6. Wiring or terminal defective.
1. Water supply turned off.
2. Defective water inlet fi ll valve.
3. Check fi ll valve screen for
obstructions.
4. Defective fl oat switch.
5. Electronic control board
defective.
6. Wiring or terminal defective.
7. Float stuck in “UP” position.
1. Drain hose (high) loop too
low.
2. Drain line connected to a fl oor
drain not vented.
long in dispenser.
2. Dispenser wet when detergent
was added.
3. Detergent cover held closed or
blocked by large dishes.
4. Improper incoming water
temperature to properly
dissolve detergent.
5. See “Detergent cover will not
open”.
1. Replace dispenser.
2. Replace control board.
3. Repair or replace.
4. Replace dispenser.
5. Replace dispenser.
1. Clear restrictions.
2. Replace control board.
3. Replace pump.
4. Check for blockage, clear.
5. Replace pump assembly.
6. Repair or replace.
1. Turn water supply on.
2. Replace water inlet fi ll valve.
3. Disassemble and clean
screen.
4. Repair or replace.
5. Replace control board.
6. Repair or replace.
7. Clean fl oat.
1. Repair to proper 32-inch
minimum height.
2. Connect to a vented drain.
1. Instruct customer/user
2. Instruct customer/user
3. Instruct customer/user on
proper loading of dishes.
4. Incoming water temperature
of 1200F is required to
properly dissolve dishwashing
detergents.