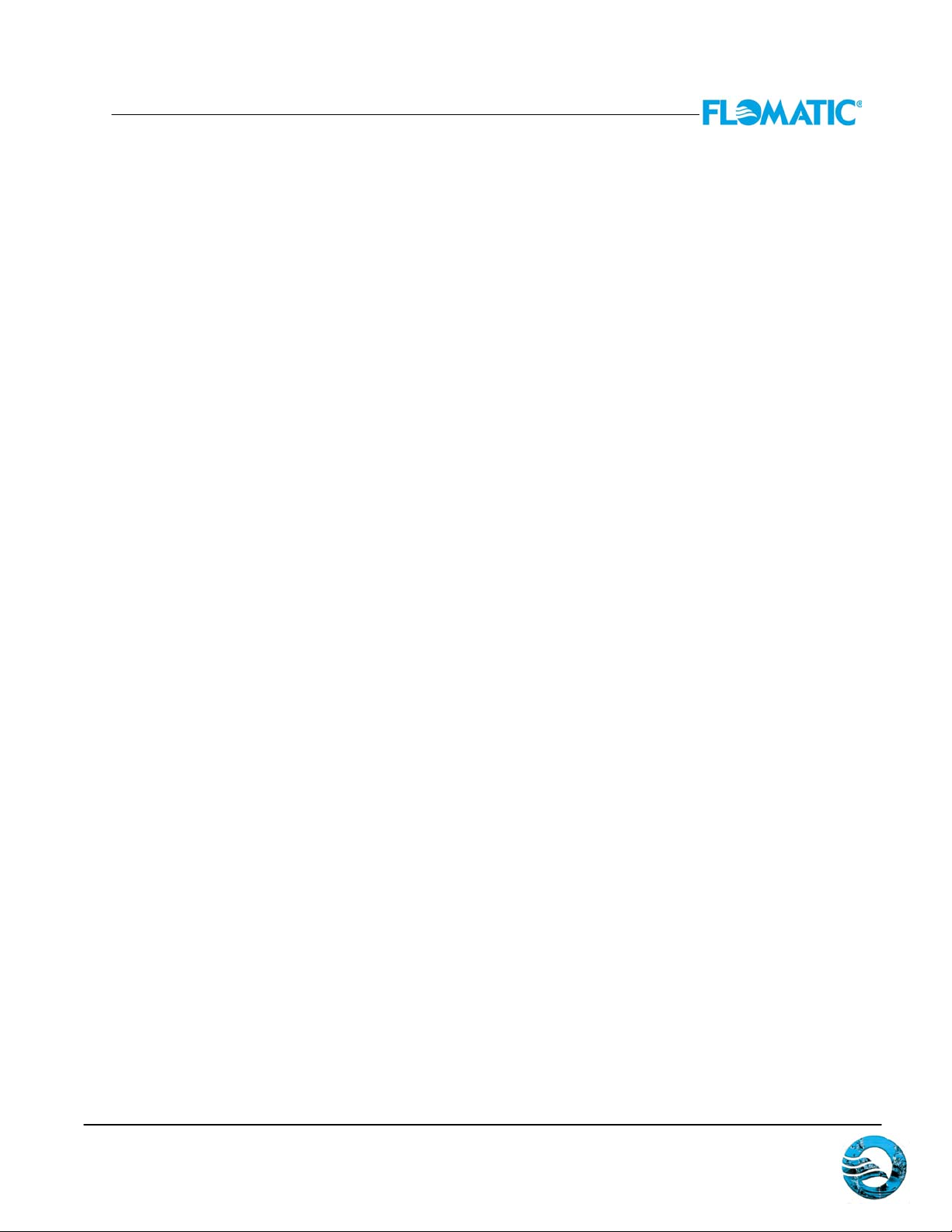
Automatic Control Valve
Written Specification (Purchase Specs)
Flomatic Corporation
Model C104/CA104
CS104 (Global EU Model)
Pressure Reducing, Back Pressure (Sustaining) Valve
FULL PORTED
Sizes:
Globe: 1 1/2" - 30" (DN 40 - DN750)
Angle: 1 1/2" - 12" (DN40 - DN300)
Function:
The Pressure Reducing and Back Pressure (sustaining) valve shall maintain a preset constant
downstream outlet pressure regardless of variations in the flow rate and/or inlet upstream
pressure. When the upstream inlet pressure becomes equal to the spring setting of the pressure
reducing control, the main valve modulates to maintain a constant inlet pressure.
Main Valve Body:
The main valve shall be self contained hydraulically operated, single diaphragm-actuated globe or
angled body valve with no pistons operating the valve or pilot controls. The valve shall have three
major components: the body with seat installed, the cover with bushing installed, and the
diaphragm assembly. The diaphragm assembly shall be the only moving part. It shall form a
sealed chamber above the diaphragm to separate operating pressure from line pressure. Packing
glands and stuffing boxes are not permitted. The valve is designed for use with various types of
pressure and/or electric controls to provide the desired control of pressure or flow for a variety of
water system applications.
Description:
No separate chambers shall be allowed between the valve cover and body. The valve body and
cover shall be of cast material (Ductile Iron) with no fabrication or welding used in the
manufacturing process.
The valve shall contain a resilient, synthetic rubber seat seal, with a rectangular cross-section
contained on three and one half sides by the spool and seat plate, and form a tight seal against a
single removable seat ring. No O-ring type seal (circular, square or quad type) shall be permitted
as the seating surface. The seat plate shall be contoured to permit the smooth transition of flow
and hold the seat seal firmly in place.
The spool shall be of a sturdy one piece design (sizes 1 1/2" thru 4") capable of withstanding
opening and closing shocks. It must have straight sides and radius top to prevent excessive wear
to the diaphragm were it flexes across this surface. The spool shall be of a sturdy one piece design
(sizes 6" thru 24") capable of withstanding opening and closing shocks and having straight sides.
The diaphragm assembly contains a non-magnetic 304 stainless steel stem of sufficient diameter
to withstand the high hydraulic pressure. It shall be fully guided at both ends and for the entire
range of travel, in the cover by a removable bushing and in the valve by an integral bearing in the
valve seat ring. No center guides shall be permitted. The stem shall be drilled and tapped in the
Flomatic Corporation
Glens Falls, NY 12801
Phone (518) 761-9797
Fax (518) 761-9798
C104 Rev A (10/11)
March 30, 2003
1 of 3
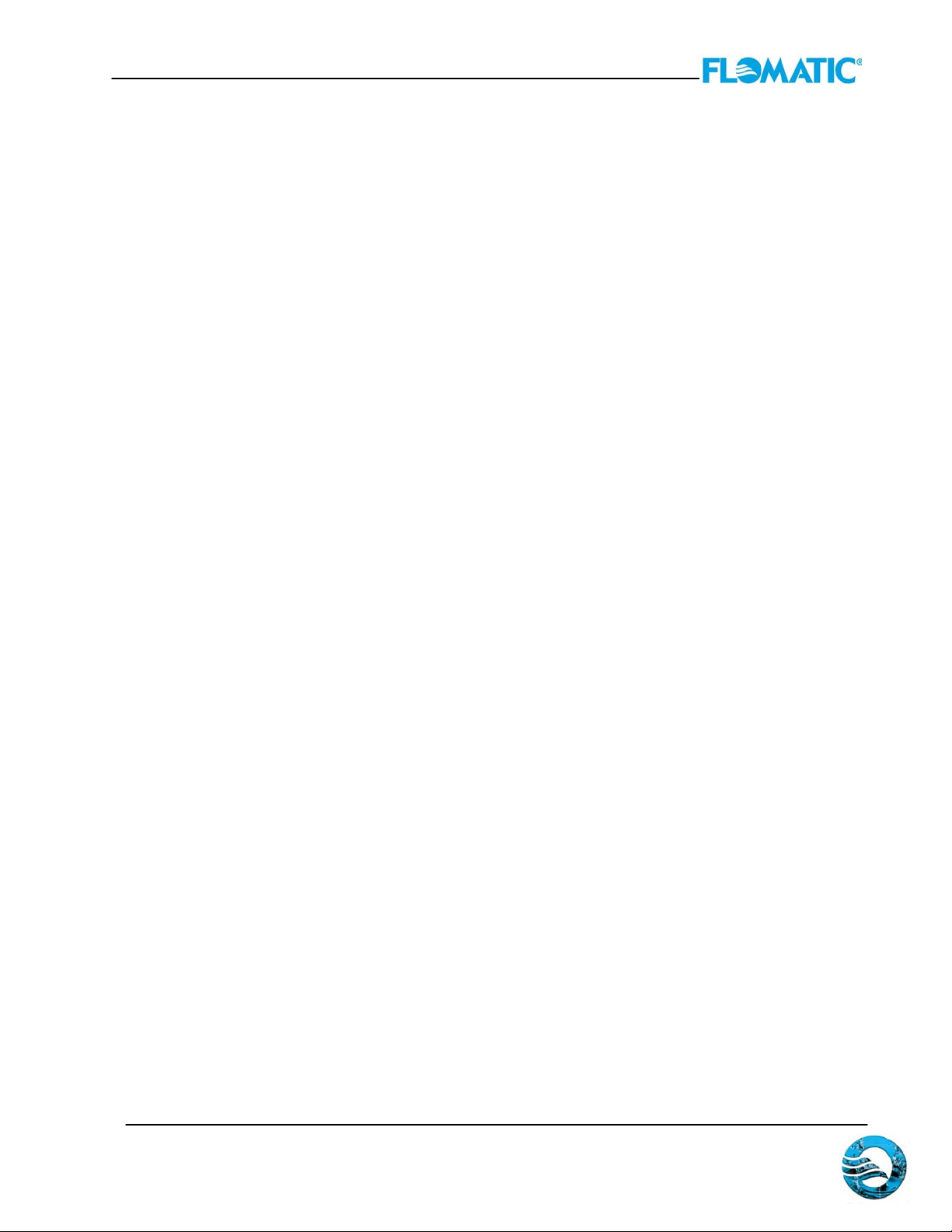
cover end to receive and affix such accessories as may be necessary. The diaphragm assembly
shall be the only moving part and shall form a sealed power chamber in the upper portion of the
valve, separating operating pressure from line pressure. The non-wicking, flexible, FDA approved
diaphragm shall consist of nylon fabric bonded with synthetic rubber compatible with the operating
fluid. The diaphragm must withstand a Mullins Burst Test of a minimum 600 psi per layer of nylon
fabric. It shall be tested 100,000 times to insure longevity. The diaphragm shall be fully supported
in the valve body and cover by machined surfaces with radius edges to prevent excessive wear as
the diaphragm flexes. The support must be no less than one-half of the total surface area of the
diaphragm in either the fully open or fully closed position.
The seat ring with integral bearing shall be a one-piece solid design and shall have a minimum of a
4° taper on the seating surface for a positive drip-tight shut off. The seat ring in 4" and smaller size
valves shall be threaded into the body. The valve seat ring in 6" and larger sizes shall be retained
by hex head bolts for ease of maintenance. The lower bearing of the valve stem shall be
contained concentrically within the seat ring and be exposed to the flow on all sides to avoid
deposits. Locating the valve body and cover shall be by a machined locating lip to insure proper
alignment of the valve stem. Pinning of the cover to the valve body shall not be permitted.
All necessary repairs and/or modifications other than replacement of the main valve body shall be
made possible without removing the valve from the pipeline. The valve manufacturer shall warrant
the valve to be free of defects in material and workmanship for a one year period from date of
shipment, provided the valve is installed and used in accordance with all applicable instructions.
The valve manufacturer shall be able to supply a complete line of equipment from 1-1/2" through
30" sizes and a complete selection of complementary equipment. The valve manufacturer shall
also provide a cavitation chart which shows flow rate, differential pressure, percentage of valve
opening, Cv factor, system velocity and if there will be cavitation damage.
Material Specification
Valve size:
Main Valve Body and Cover:
Main Valve Trim:
Connection:
Pressure Rating:
Temperature Range:
Rubber Material:
Coating:
Desired Options:
Flomatic Corporation
Glens Falls, NY 12801
Phone (518) 761-9797
Fax (518) 761-9798
C104 Rev A (10/11)
March 30, 2003
2 of 3

Pilot Control System:
The pressure reducing pilot control shall be a direct-acting, adjustable, spring-loaded, normally
open, diaphragm valve designed to permit flow when controlled pressure is less than the spring
setting. The pilot control is held open by the force of the compression on the spring above the
diaphragm. It closes when the delivery pressure acting on the underside of the diaphragm
exceeds the spring setting. The pilot control system shall include a fixed orifice. No variable orifices
shall be permitted. The pilot system shall include an opening speed control on all valves 1 ½ - 30”
as standard equipment. The pilot control shall have an optional second downstream sensing port
which can be utilized to install a pressure gauge.
The back pressure (sustaining) pilot control shall be a direct-acting, adjustable, spring-loaded,
diaphragm valve designed to permit flow when inlet (upstream) controlled pressure is greater than
the spring setting on the pilot. A full range of spring settings shall be available in ranges of 0 to 400
psi. A direct factory representative shall be made available for start-up service, inspection and
necessary adjustments.
Material Specification for Pilot Control:
Pressure Rating:
Trim:
Rubber Material:
Tubing and Fittings:
Adjustment Range:
Operating Fluids:
Desired Options:
This valve shall be a Flomatic Model C104/CA104/CS104 Control Valve, as manufactured by
Flomatic Corporation, Glens Falls, NY 12801.
Flomatic Corporation
Glens Falls, NY 12801
Phone (518) 761-9797
Fax (518) 761-9798
C104 Rev A (10/11)
March 30, 2003
3 of 3