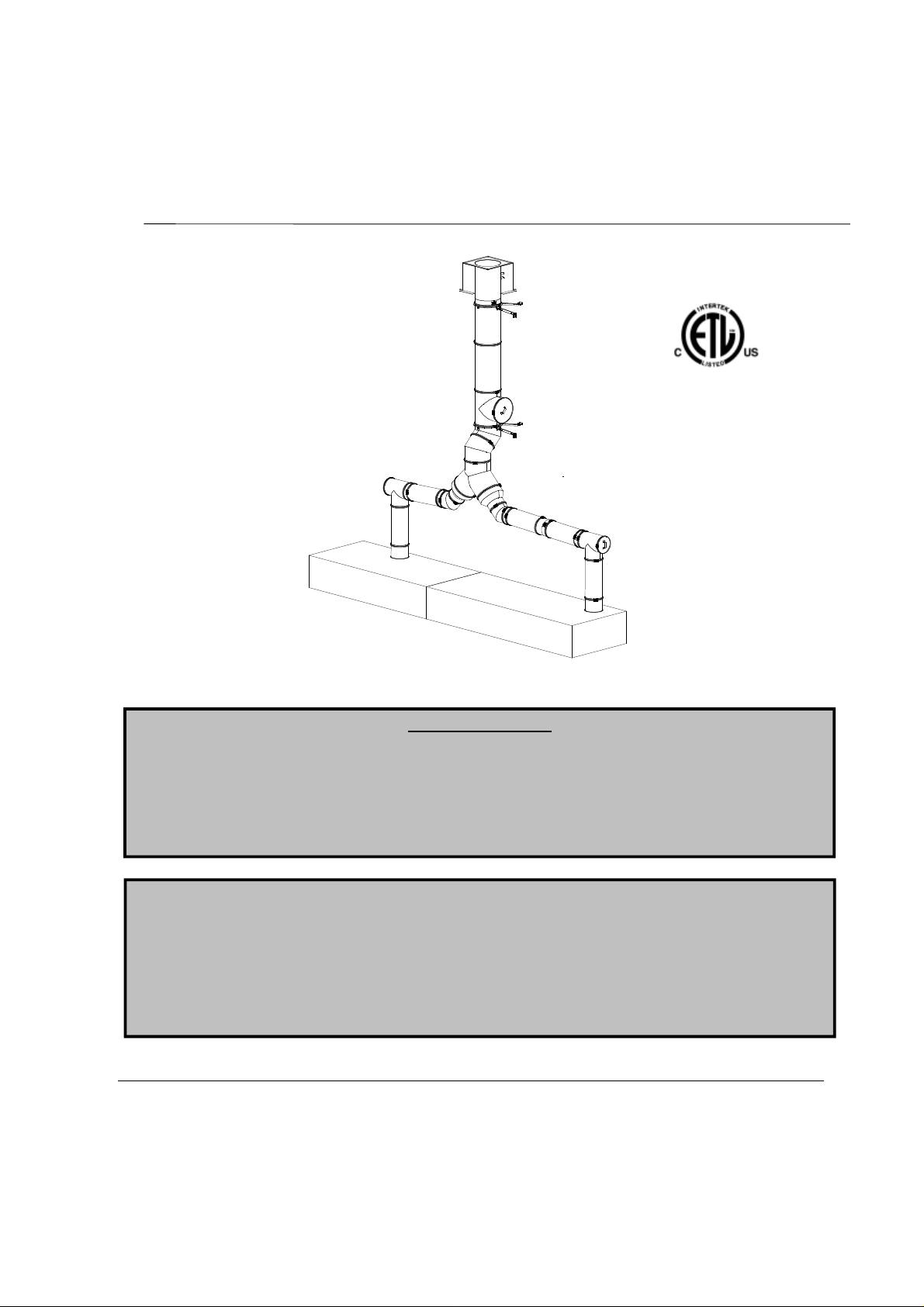
This grease duct is ETL listed to standard UL
1978 and does not have to be
Welded Grease Duct Systems
Installation, Operation, and Maintenance Manual
TWO MAJOR CAUSES OF GREASE DUCT RELATED FIRES: (1) FAILURE TO MAINTAIN
REQUIRED CLEARANCE (AIR SPACE) TO COMBUSTIBLE MATERIALS AND (2) FAILURE TO
CLEAN GREASE LADEN DUCTS. IT IS OF UTMOST IMPORTANCE THAT THIS GREASE DUCT
BE INSTALLED ONLY IN ACCORDANCE WITH THESE INSTRUCTIONS. DO NOT INSTALL
GREASE DUCT WITHOUT FIRST READING THESE INSTRUCTIONS VERY CAREFULLY.
Grease duct installed in accordance with these installation instructions will comply with
national safety standards and building codes.
This booklet contains complete information on details concerning dimensions, installation and
clearances to combustibles. For any additional construction information, refer to Duct Work
Catalog.
February 2014 Rev. 20
A0011047
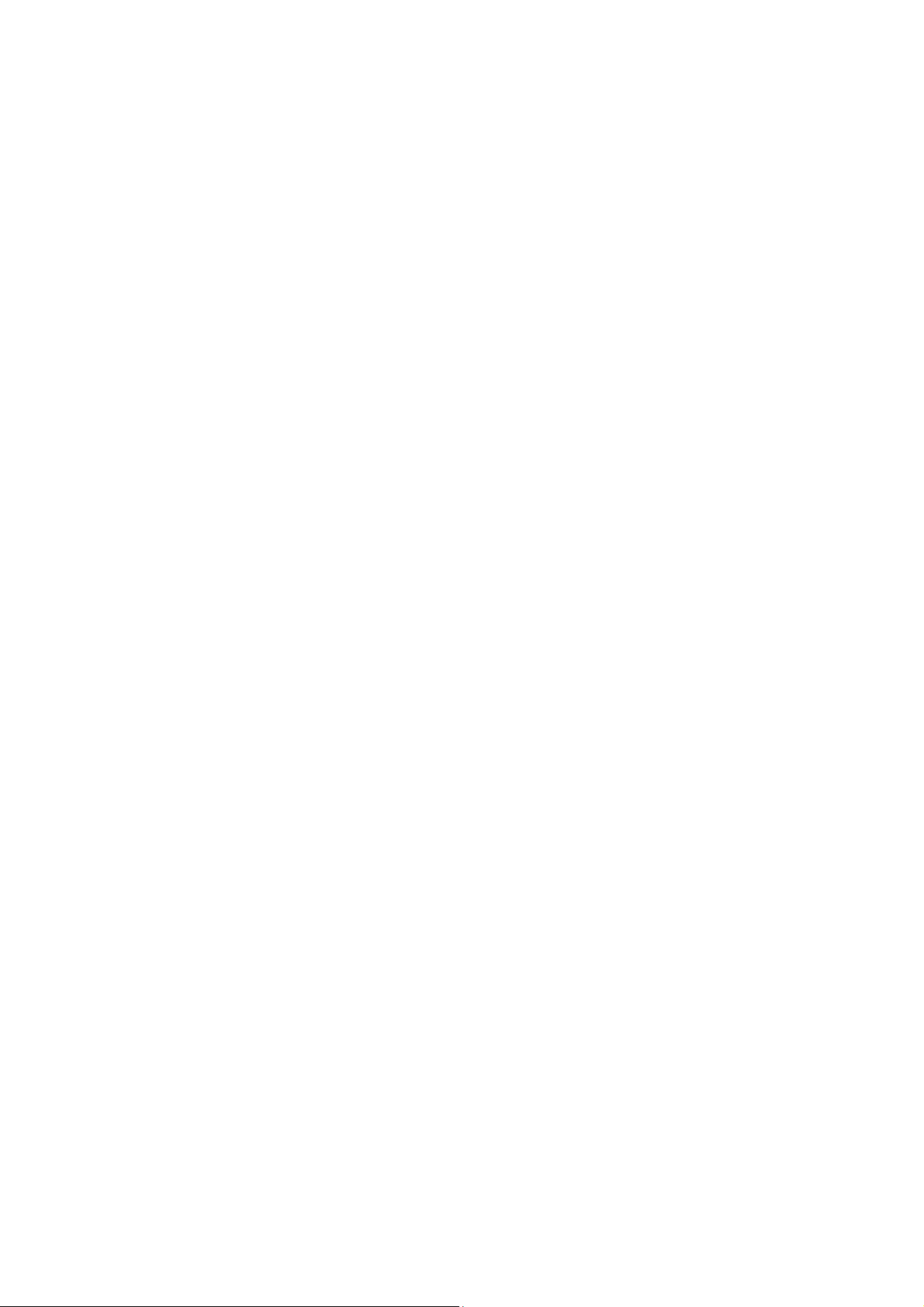
TABLE OF CONTENTS
WARRANTY ............................................................................................................................................ 3
LISTINGS ................................................................................................................................................ 4
APPLICATION ......................................................................................................................................... 4
MECHANICAL ......................................................................................................................................... 5
Joint Sealant ....................................................................................................................................... 5
Sealant Features ............................................................................................................................. 5
Table 1 – Sealant Usage Chart ....................................................................................................... 5
Grease Duct Standard Connection ...................................................................................................... 6
Fig.1 – Joint Assembly .................................................................................................................... 6
Collar & Adjustable Duct Connections ................................................................................................. 7
Fig. 2 – Adjustable Duct Overlap ..................................................................................................... 7
Collar & Adjustable Duct Vertical Installation ........................................................................................ 7
Table 2 – Minimum Overlap ............................................................................................................. 7
Fig. 2a – Adjustable Duct Overlap ................................................................................................... 7
Fig. 2b – Collar & Adjustable Duct Installation.................................................................................. 8
Risers – Factory & Field (Bolted & Welded) Risers .............................................................................. 8
Fig. 3 – Field Installed Riser - Bolted ............................................................................................... 9
Fig. 4 – Duct Drain .......................................................................................................................... 9
Duct Drains ......................................................................................................................................... 9
Grease Manifold Tee ........................................................................................................................... 9
Fig. 5 - Grease Manifold Tee Position .............................................................................................. 9
Access Door (Tee Cap) Assembly ..................................................................................................... 10
Fig. 6 – Access Door Assembly ..................................................................................................... 10
Fan Adapter Plate ............................................................................................................................. 11
Fig. 7 – Fan Adapter Plate ............................................................................................................. 11
Prevention of Grease Accumulation in Horizontal Grease Duct .......................................................... 11
Alignment & Bracing of Grease Duct .................................................................................................. 11
Table 3 – Horizontal Support Spacing ........................................................................................... 11
Horizontal Support & Support Spacing .......................................................................................... 11
Fig. 8 – Horizontal Support Details ................................................................................................ 12
Wall Guide Support & Support Vertical Spacing ............................................................................. 12
Table 4 – Vertical Support Spacing................................................................................................ 12
Fig. 9 – Vertical Support Details .................................................................................................... 13
Grease Duct Assembly Examples ...................................................................................................... 14
Fig. 10 - Grease Duct Installation Guide ........................................................................................ 14
Fig. 11 - Grease Duct Installation Guide ........................................................................................ 15
Fig. 12 - Grease Duct Installation Guide ........................................................................................ 16
CLEARANCES ...................................................................................................................................... 17
Table 5 – Clearance – Grease Duct ................................................................................................... 17
Zero Clearances to Combustibles ...................................................................................................... 18
METHODS USED TO TEST DUCT AFTER ASSEMBLY ....................................................................... 18
Method 1 – Light Test per IMC 506.3.3.1 ........................................................................................... 18
Method 2 – Smoke Test .................................................................................................................... 18
GENERAL DUCT WEIGHT ................................................................................................................... 18
Formula 1 – 20 Gauge Duct............................................................................................................... 18
Formula 2 – 18 Gauge Duct............................................................................................................... 18
NOTES .................................................................................................................................................. 19
CLEANING & MAINTENANCE RECORD .............................................................................................. 20
2
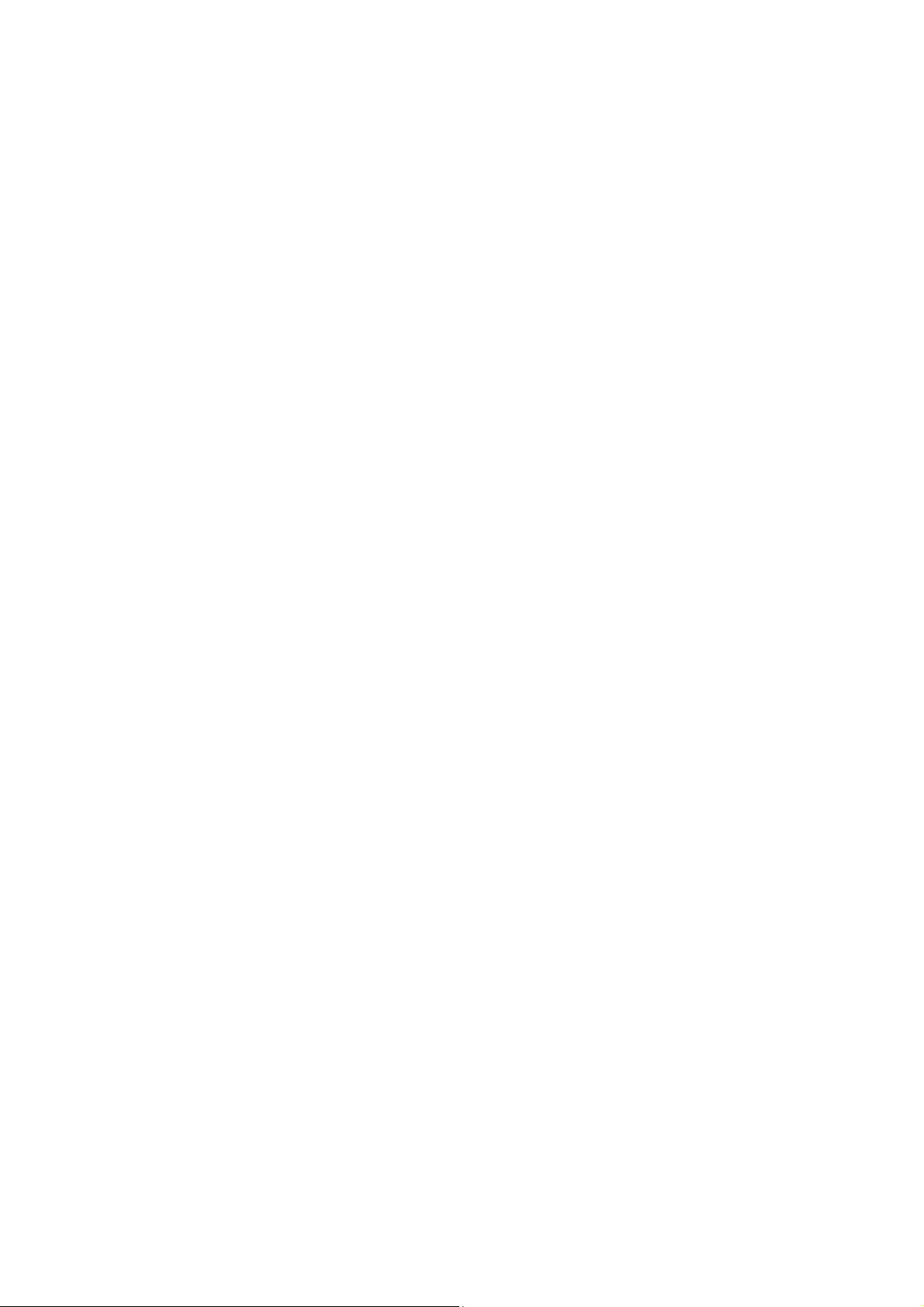
WARRANTY
This duct work system is warranted to be free from defects in material and workmanship, under normal
use and service, for a period of 12 months from the date of shipment. This warranty shall not apply if:
1. The equipment is not installed by a qualified installer per this installation guide, this guide should
be kept with the equipment once installation is complete.
2. The equipment is not installed in accordance with federal, state and local codes and regulations.
3. The equipment is misused or neglected.
4. The equipment is not operated within its published capacity.
5. The invoice is not paid within the terms of the sales agreement.
The MANUFACTURER shall not be liable for incidental and consequential losses and damages
potentially attributable to malfunctioning equipment. Should any part of the equipment prove to be
defective in material or workmanship within the 12-month warranty period, upon examination by the
MANUFACTURER, such parts will be repaired or replaced by the MANUFACTURER at no charge. The
BUYER shall pay all labor costs incurred in connection with such repair or replacement. Equipment shall
not be returned without MANUFACTURER’S prior authorization and all returned equipment shall be
shipped by the BUYER, freight prepaid to a destination determined by the MANUFACTURER.
3
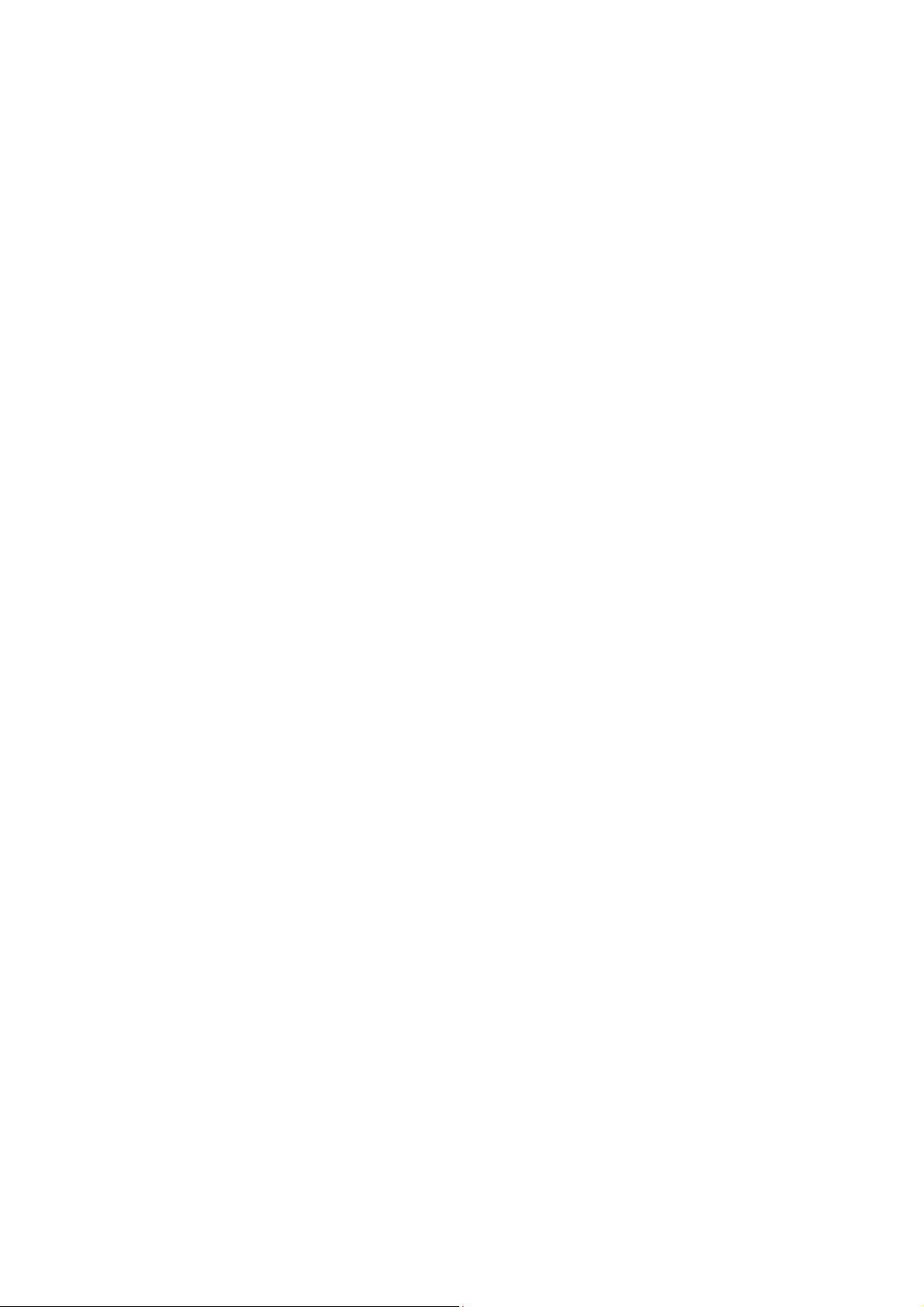
LISTINGS
This grease duct is ETL listed to standard UL-1978 when installed in accordance with these installation
instructions and National Fire Protection Association Standard “NFPA 96, Standard for Ventilation Control
and Fire Protection of Commercial Cooking Operations”.
APPLICATION
The listed grease duct is suitable for use in commercial cooking installations for the removal of smoke
and grease laden vapors. The grease duct system includes all components for a complete exhaust
system from the hood to the exhaust fan inlet.
Grease duct installations require provisions for cleaning the interior of the duct. NFPA 96 cleanout
requirements are as follows:
1. A cleanout must be provided at each change of direction except where the entire length of duct
can be inspected and cleaned from either the hood or the discharge end.
2. On horizontal duct runs, at least one (1) 20” diameter opening must be provided. Where the
opening is smaller than 20” diameter, openings large enough to permit cleaning must be provided
at intervals of no more than 12’.
3. Openings must be at the side or the top, whichever is more accessible. When the opening is on
the side of the duct, the lower edge of the opening must be at least 1 ½” above the bottom of the
duct. For the listed grease duct, this is accomplished by the use of the grease manifold tee and
cleanout cap.
4. On vertical duct runs where personnel entry is possible, access must be from the top of the riser.
Where entry is not possible, access must be provided at each floor.
NOTE: ACCESS REQUIREMENTS ARE SUBJECT TO CHANGE IN ACCORDANCE WITH LOCAL
CODE. LOCAL AUTHORITIES SHOULD BE CONSULTED FOR EXACT REQUIRMENTS. GREASE
DUCT MAY BE CONNECTED ONLY TO HOODS IN A SINGLE FIRE ZONE ON ONE FLOOR. DO
NOT CONNECT GREASE DUCTS TO ANY OTHER PART OF THE BUILDING VENTILATION OR
EXHAUST SYSTEM.
When grease duct is installed in accordance with these installation instructions and the joints are sealed
properly with the recommended sealant, the system will contain a grease fire within the duct. A grease
fire can burn at extremely high temperatures. This system should be dismantled and inspected after any
exposure to a grease fire. Any section that is distorted or discolored should be replaced. All joints in the
system should be examined. Because the sealant expands to assure a positive seal in the case of a fire,
any sealant that has been exposed to high temperature must be replaced. This will ensure that the
system maintains its integrity against fire conditions in the future. The manufacturer of this grease duct
can not be responsible for grease duct systems that are not properly maintained or have been subjected
to one or more grease fires.
Grease duct systems size and capacity information may be obtained from the “ASHRAE Handbook –
Fundamentals” or from the “Air Pollution Engineering Manual” of the “US Environmental Protection
Agency”. Refer to the grease duct systems catalog for descriptions and dimensional data of parts.
4
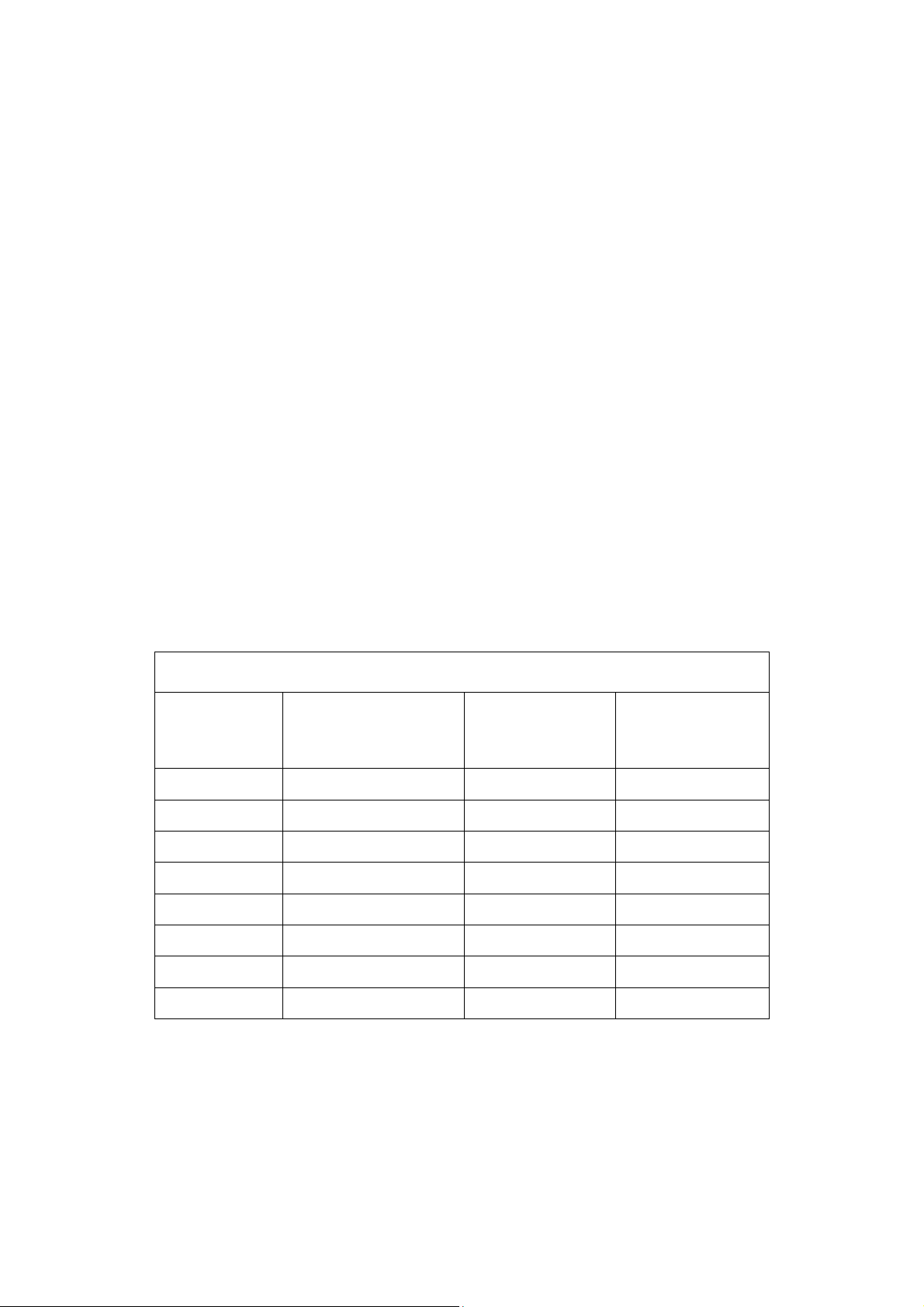
MECHANICAL
Joint Sealant
The joint sealant used to seal all joint assemblies is a 3M product. 3M Fire Barrier 2000 + Silicone
Sealant is a ready-to-use, gun-grade, one-component silicone elastomer that cures upon exposure to
atmospheric humidity to form a flexible seal. 3M Fire Barrier 2000 + Silicone Sealant, when installed
properly, will control the spread of fire before, during and after exposure to open flames. It will stop the
spread of noxious gas, smoke and water and maintain the integrity of fire rated assemblies and
construction. NO SEALANT SUBSTITUTES MAY BE USED.
Sealant Features
1. Superior adhesion.
2. Capable of withstanding 2000 °F + temperatures.
3. Class 25 sealant, per ASTM 920.
4. Re-enterable/repairable.
5. Provides up to 4-hours fire-rating.
6. Cures upon exposure to atmospheric humidity.
7. Working time 30 minutes.
8. Cure time 14 to 21 days.
9. Applied with a standard caulk gun.
Table 1 – Sealant Usage Chart
DIAMETER DUCT PERIMETER FT
8" 2.16 30 7
10" 2.68 30 6
12" 3.21 30 5
14" 3.73 30 4
16" 4.25 30 3.5
18" 4.78 30 3
20" 5.30 30 3
24" 6.35 30 2.5
3M FIRE BARRIER 2000 PLUS USAGE
AVERAGE FEET
PER TUBE
NUMBER OF
JOINTS PER TUBE
5
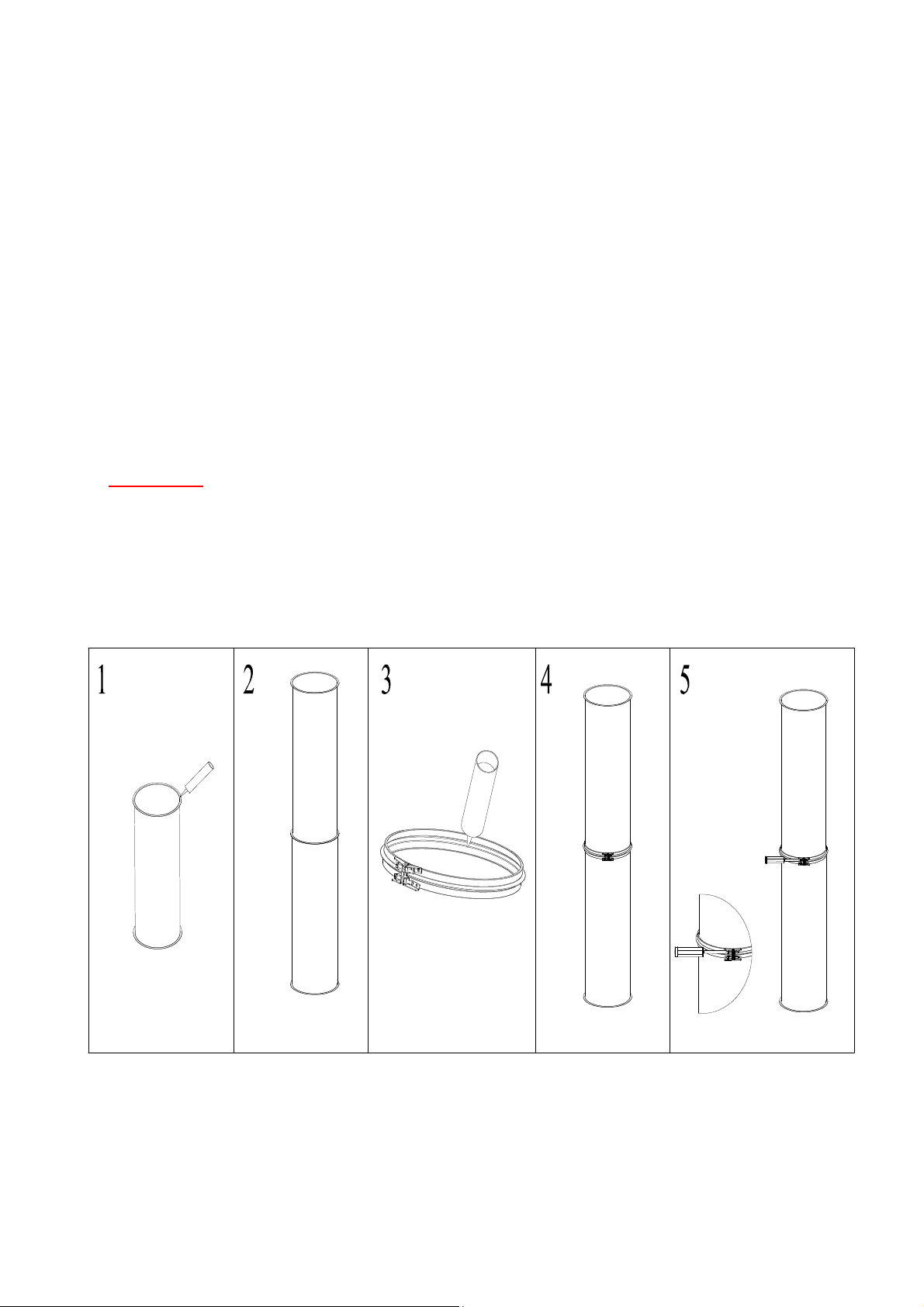
Grease Duct Standard Connection
1. Apply a continuous bead of proper sealant around the flange to be joined. The bead should be
¼” thick and continuous.
2. Join the two flanged ends of the duct section together.
3. Fill the “V” clamp with the proper sealant. The bead should be inside the “V”.
4. Install the “V” clamp around the duct sections. Both duct flanges should be inside the “V”.
5. For horizontal duct runs, the “V” clamp hardware should be located on the top side of the duct
and be orientated between the 3 and 9 o’clock position on the duct.
6. NEVER install the “V” clamp with the hardware orientated on the bottom side of the duct on
horizontal runs.
7. Secure the “V” clamp around the duct by tightening the ¼-20 hardware to 85 in-lbs.
8. See Fig. 1 below for details.
9. Remove any excess sealant from the inside of the duct surface.
IMPORTANT: THE HARDWARE USED TO ASSEMBLE THIS DUCTWORK IS SPECIFICALLY
DESIGNED FOR THIS APPLICATION. NO SUBSTITUTE HARDWARE IS ALLOWED. ALL
REPLACEMENT HARDWARE MUST BE PURCHASED FROM THE DUCTWORK FACTORY.
Fig.1 – Joint Assembly
6