
1.3.1.3. Fitting the Connecting Rod Bearing Shells
If the bearings show shallow scratches, remove them
with a very fine oil stone. If the scratches are deep, t he
bearing shells must be replaced, since th e layer of bearing
metal does n ot allow them to be re-worked.
Fig. 16. — Piston ring clamp to pushthe piston rings into their
grooves whe n fitting the pistons.
To check the clearance between bearing shells an d crankpin, use "Plastigage" calibrated wire, and proceed as
follows:
Clean the crankpin surfaces and f it th e connecting rod/
piston assembly t o th e crankpin. Place a calibrated wire
on the crankpin over the full width of the crankpin
as shown in Fig. 1.17.
Install the caps an d tighten the securing nuts to a torque
of 3.5 kgm (25 Ib.ft.). Do not move th e connecting rod
at this stage. Remove the caps a n d measure t he flattened
section of the wire with the scale, supplied with the
"Plastigage" (Fig. 1.18.). If the clearance is between
0.011 - 0.061 mm (0.0004 - 0.0024 in.) on earlier cars o r
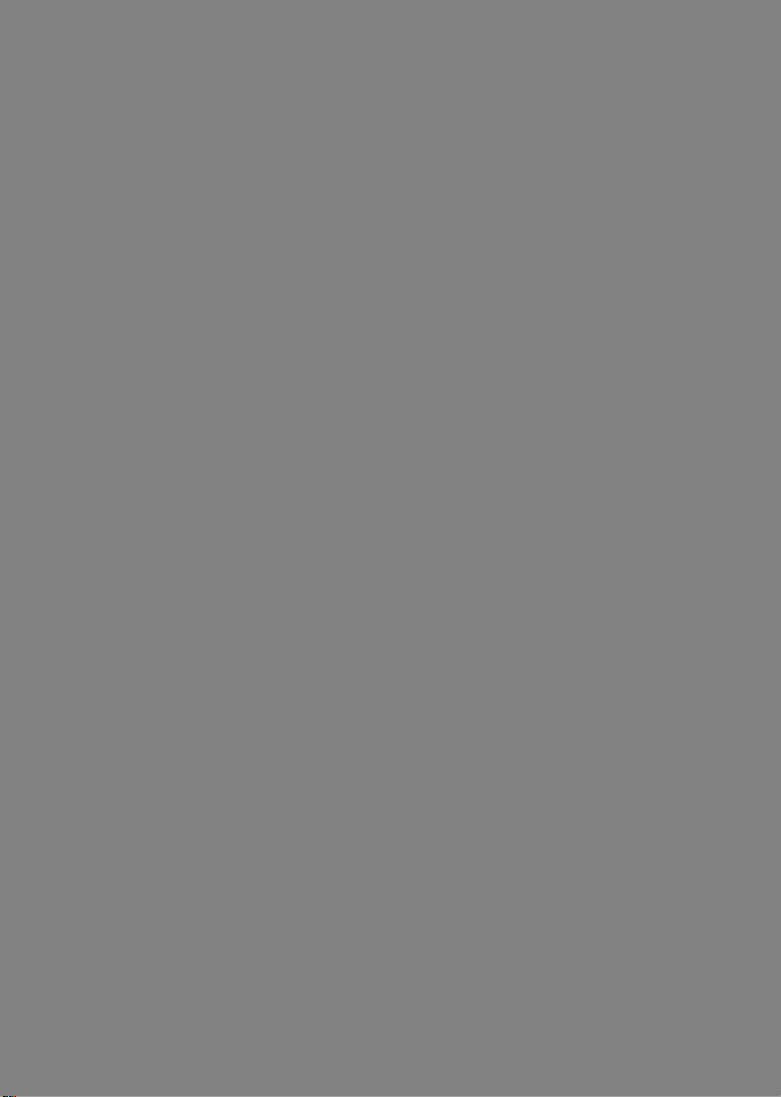
Fig. 17. — When checking the running clearance of the connecting rod bearings, insert the Plastigage strip as shown into the
bearing shell or place it across t he bearing journal. Then f i t the
bearing cap to the crankshaft and tighten the nuts to the
specified torque reading.
Fig. 18. — After the bearing cap has been removed, measure the
width of the now flattened Plastigage s t ri p b y means o f t h e scale
provided in the kit.
0.024 - 0.074 mm (0.0009 - 0.0029 in.) on c ar s after N ov .
1974, the bearing shells can be re-used.
Check the crankpin for wear or ovali ty (see S ect io n o n
Crankshaft).

1.3.2. CRANKSHAFT
1.3.2.0. Technical Data
Main bearing journal
standard diameter:
Inner diameter of main
bearing shells (f it ted):
Main bearing shell undersizes
available:
Crankpin standard diameter:
Pre Nov. 1974:
After Nov. 1974:
Big end bearing shell standard
thickness:
Big end bearing shell undersize
available:
Bearing running clearances:
Main bearings:
Big end bearings:
Pre Nov. 1974:
After Nov. 1974:
Max. out-of-round of crankpins
and main journals after
grinding:
Max. taper of crank pins and
main journals after grinding:
Concentricity of flywheel in
relation to the crankshaft,
measured 25 mm ( 1 in.)
fr om shaft centre:
53.970 - 53.990 mm
(2.1248-2.1256 in.)
54.035 - 54.050 mm
(2.1274-2.1279 in.)
0.2, 0.4, 0.6, 0.8, 1 . 0 m m
(0.008, 0.016, 0.024,
0.031, 0.04 in.)
44.013-44.033 mm
(1.7328- 1.7336 in.)
44.000 - 44.020 mm
(1.7323- 1.7330 in.)
1.534- 1.543 mm
(0.0604-0.0607 in.)
0.254, 0.508, 0.762,
1.016 mm (0.01,0.02,
0.03, 0.04 in.)
0.045 - 0.080 mm
(0.0018-0.0031 in.)
0.011 -0.061 mm
(0.0004-0.0024 in.)
0.024 - 0.074 mm
(0.0009-0.0029 in.)
0.005 mm (0.0002 in.)
0.005 mm (0.0002 in.)
0.025 mm (0.001 in.)
1.3.2.1. Checking and Re-Grinding Journals and
Crankpins
Using a micrometer, measure th e taper and ovality of the
crankpins and main bearing journals (Fig. 1.19 and 1.20),
checking visually at the same time for scoring, before regrinding the crankshaft. Check, using " V " Blocks and a
dial test indicator for bow or twist. If the crankshaft
shows signs of twist it is advisable to replace i t , if bowed