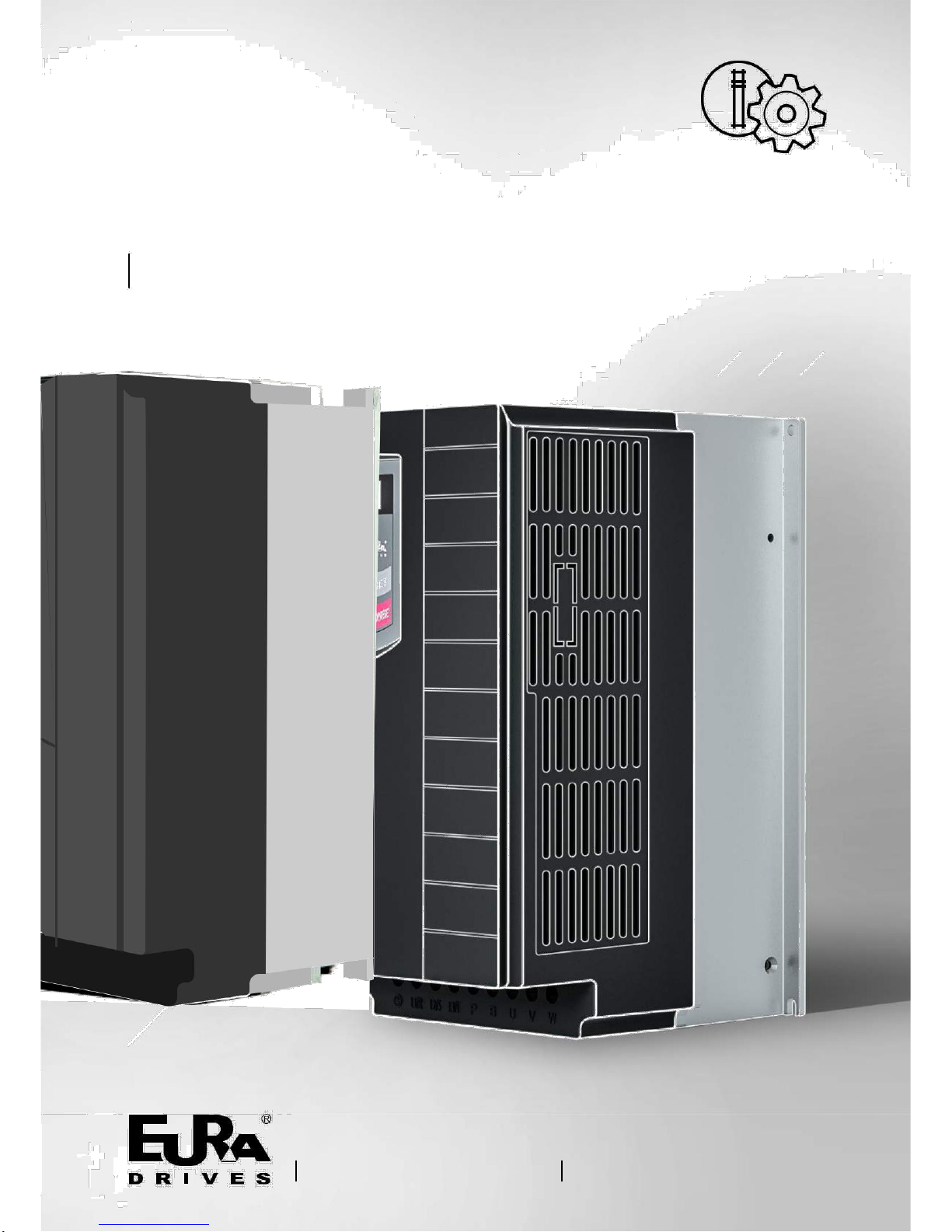
FREQUENCY INVERTER
E2000
0,4kW – 400kW (IP20)
Safety instructions Installation
& operating manual
w w w. e u r a d r i v e s . e u
E2000_Rev.02 -EN- SOFT Rev. 5.09
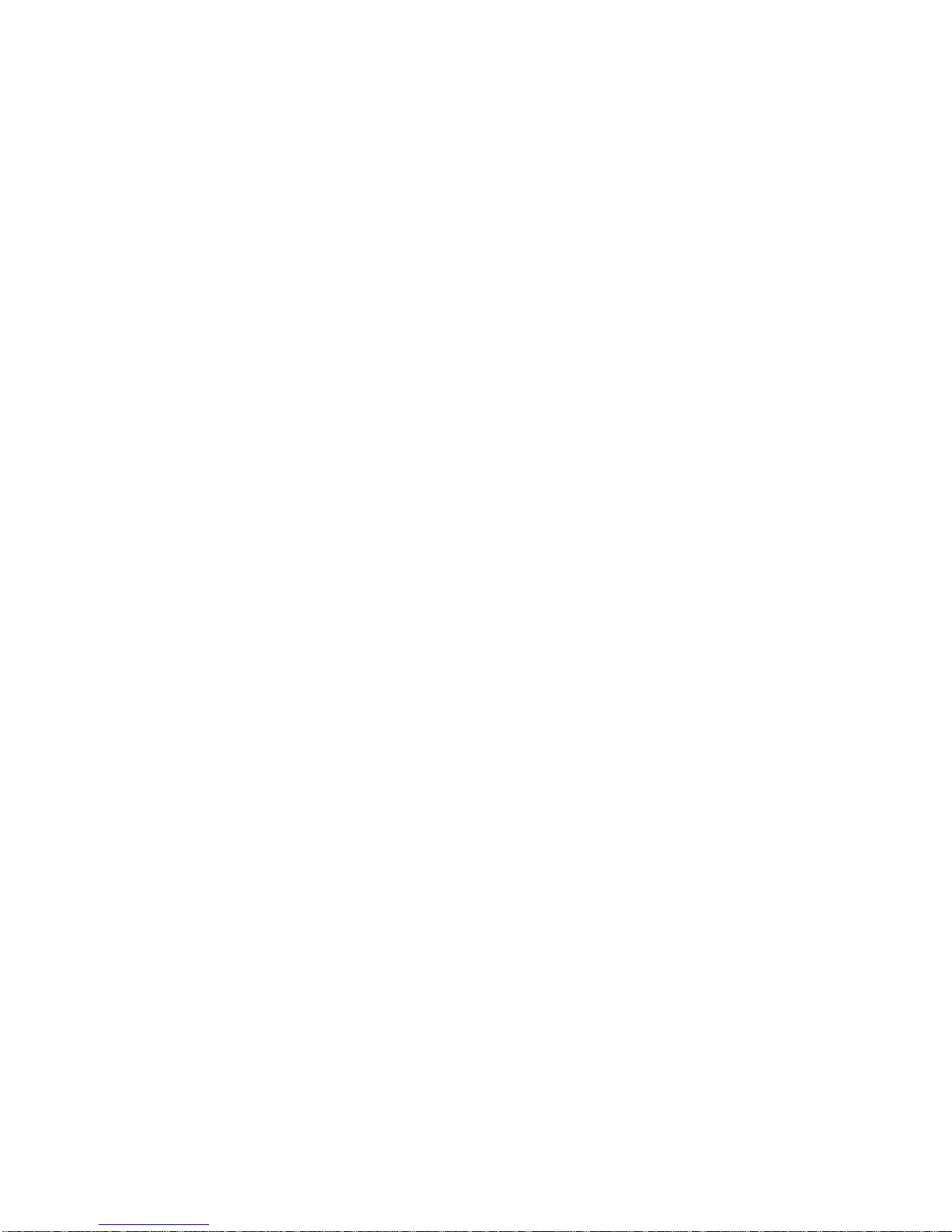
Common installation- and safety rules for series E2000+ inverters
Product data / product power range
Electrical connection of E2000+ Inverters
Control-board – hardware and I/O channel configuration
Inverter parameter setting
Parameter group 100: Basic parameter
Parameter group 200: Inverter control
Parameter group 300: Digital I/O configuration
Parameter group 400: Analogue I/O channel configuration
Parameter group 500: Fixed-frequency, automatic cycling frequencies
Parameter group 600: DC-Bake control / Aux. functions
Parameter group 700: Error handling and protection functions
Parameter group 800: Autotuning – Motor data programming
Parameter group 900: RS485 Hardware and interface parameters
Parameter group A00: PID controller parameter
Parameter group C00: Speed / Torque control
Rev. 02-EN-2016-06-KPP
Software revision: 5.09
E2000+_Rev.02 -E- SOFT Rev. 5.09
© 2016-06-KPP-EURADRIVES EUROPE GmbH

1) Common installation rules and safety information regarding EURA E2000+ inverters
1) Common installation- and safety rules for EURA DRIVES inverters,
series E2000+
IMPORTANT!!
This instruction manual explains rules for correct installation and safe operation of
frequency inverters, series E2000+ (denominated inverter, or drive in the following guidance).
It is mandatory to follow exactly, what reported in this instruction manual.
This instruction manual must be read and fully understood before any action of installation or
placing in operation of the inverter.
Anybody, who operates the inverter, or the machine, equipped with inverter, must have
access to this operation manual, and must become familiar with drives technology, especially
regarding safety and warning issues
All instructions in this manual must be observed, to:
Guarantee safety for humans and machinery
Allow safe function and reliable operation
Permit approvals and certifications
Keep manufacturers warranty in force
Following pictograms are used in this instruction manual:
DANGER-WARNING-CAUTION
ATTENTION: Life or health of the user
are endangered or substantial damage to
property may occur.
ATTENTION – OBSERVE
Measures, necessary for safe and
trouble-free operation
E2000+_ Rev.02 -E- SOFT Rev. 5.09
© 2016-06-KPP-EURADRIVES EUROPE GmbH
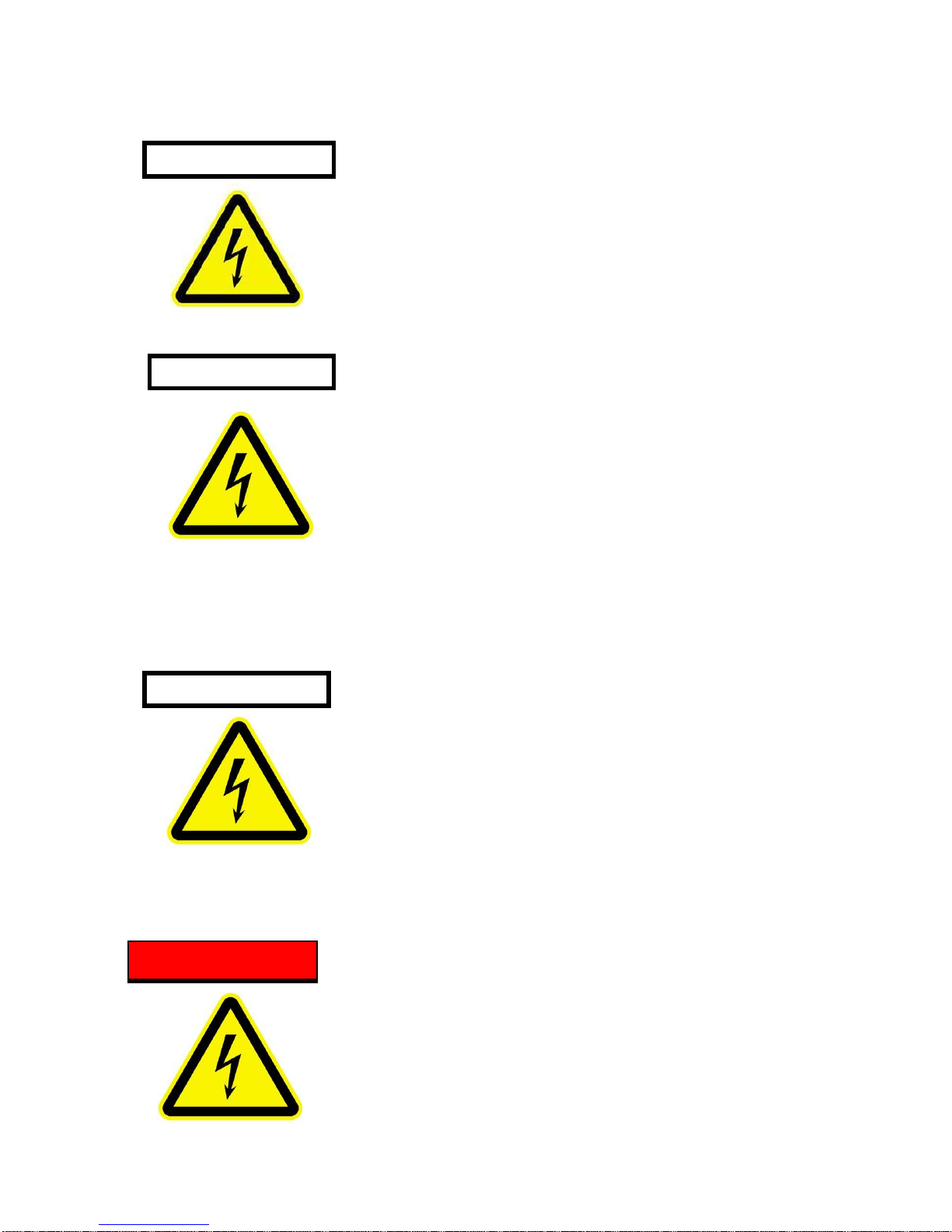
1) Common installation rules and safety information regarding EURA E2000+ inverters
Common:
DANGER
Frequency inverters operate with voltages, hazardous
to humans
Depending on inverters protection degree (IP class) and mounting
conditions, life parts may be accessible.
During heavy duty operation, and especially in case of
malfunction, parts/surfaces of inverters or accessory may reach
dangerous temperatures, which may result in personnel injury.
Inadmissible removal of covers or other parts of the inverter, improper
use, and not qualified mounting or operation may result in high risk
for personnel injury and/or machinery damage
All activity for mounting, cabling, placing into operation and operation
DANGER of the inverter must be done exclusively by proper educated and
trained people.
The standards IEC 364 and/or CENELEC HD384, DIN VDE 0100
and all other national safety standards are to observe.
Trained people has specific professional training, knowledge of all
relevant standards and safety rules and experience in application
of electrical/electronic drive systems.
These professionals are in condition to judge assigned duties, and
resulting risks.
Specified application of frequency inverters
.
DANGER
The inverters, reported in this manual are components of
electrical/electronic drive systems and determinate for integration
in machines and plants only.
The E2000+ inverter serves exclusively for the control and
regulation of three phase motors (asynchronus / synchronus motors)
The connection of loads, other than above listed, may result in
damage of the machinery, destruction of the inverter or connected
equipment, and serious risk of personnel injury.
Observe specific standards and rules
It is not allowed, to place in operation the plant, before the
compliance with all standards of the machinery safety regulation
(89/392/EWG) and the EMC rules (89/336/EWG) has been checked
Inverters are conformal with low voltage directive (73/231/EWG).
Harmonized standards EN50178 (VDE160) and EN60439-1
(VDE0660, T. 500) are applied.
EURA DRIVES E2000+ is a product with limited availability (in sense
of IEC 61800-3). Frequency inverters may create high frequency
noise, in case the operator is responsible for proper
E2000+_ Rev.02 -E- SOFT Rev. 5.09
© 2016-06-KPP-EURADRIVES EUROPE GmbH

1) Common installation rules and safety information regarding EURA E2000+ inverters
Handling, transportation and storage
Inverter components may become damaged and insulating distances
DANGER may be reduced, as a result of improper transportation, handling or
storage of the drive.
In this case, the inverter does not anymore comply with product
specific standards and rules, and it is not allowed to place it into
operation.
Therefore it is mandatory, to check the inverter for mechanical
integrity, before installation and operation.
The inverter may contain components, sensitive to
electrostatic discharge. Therefore avoid, touch components
inside the drive. It is recommended to store the inverter, using
the original box. If inverters are stored or out of use for more
then one year, DC capacitors may lose their capacity. Please
contact the inverter manufacturer for reformatting procedure
Installation of the inverter
DANGER
Frequency inverters must be installed in a proper cabinet.
Only fixed installation is permitted.
Follow all effective standards and rules for correct grounding!!
All minimum distances to other inverters or equipment in the cabinet
are to respect. Minimum distances are reported later on this manual.
Allow adequate air circulating, especially, in case of vertical
mounting, one on top of the other.
Use proper shielded cables, for inverter control signals and feed back
signals
Intrusion of dust, liquids, water, steam and aggressive gases must
be excluded
Attention on adequate heat exchange of the cabinet
Use of the inverter in explosion risky area is not allowed
E2000+_ Rev.02 -E- SOFT Rev. 5.09
© 2016-06-KPP-EURADRIVES EUROPE GmbH

1) Common installation rules and safety information regarding EURA E2000+ inverters
Electrical wiring of frequency inverters
The entire plant must be disconnected from power, crosschecked for
DANGER HAZARDOUS loss of voltage and locked before starting any work
CAPACITOR CHARGE
LVD – DOUBLE
INSULATON
The discharge time of the internal DC-LINK
capacitors may take up to 5 minutes, it is not allowed
to open the enclosures or to do any maintenance
work during discharge cycle!!
All connection terminals for control and feed-back are single insulated
in sense of EN50178.
In case of connection to external equipment with double insulation,
the user has to provide proper arrangement, to guarantee double
insulation in sense of EN50178 for the whole system
E2000+ inverters are designed for steady state installation, using
GROUNDING
fixed wiring. It is not allowed, to use power plug or similar mobile
connection.
Depending on different EMC filter arrangements, the leakage
current to ground may exceed 3,5 mA. Therefore it is recommended
to use earth connection wiring, with minimum section of 10mm2
(copper) or use double wiring (in sense of EN50178)
All grounding connections must be as short as possible, all leading to
one common central point (star arrangement).
Long motor leads
A motor cable lenght, exceeding 30m, may result in over-voltage
spikes on the motor side. These peaks may damage the internal
insulation of the motor.
The use of motor chokes, sinus filter or dV/dt limiting filters may
prevent from risk of motor damage.
Generally it is recommended, to use inverter duty motors In
case of any doubt, please contact the manufacturer
All output filter components must have
inverter manufactures approval
E2000+_ Rev.02 -E- SOFT Rev. 5.09
© 2016-06-KPP-EURADRIVES EUROPE GmbH
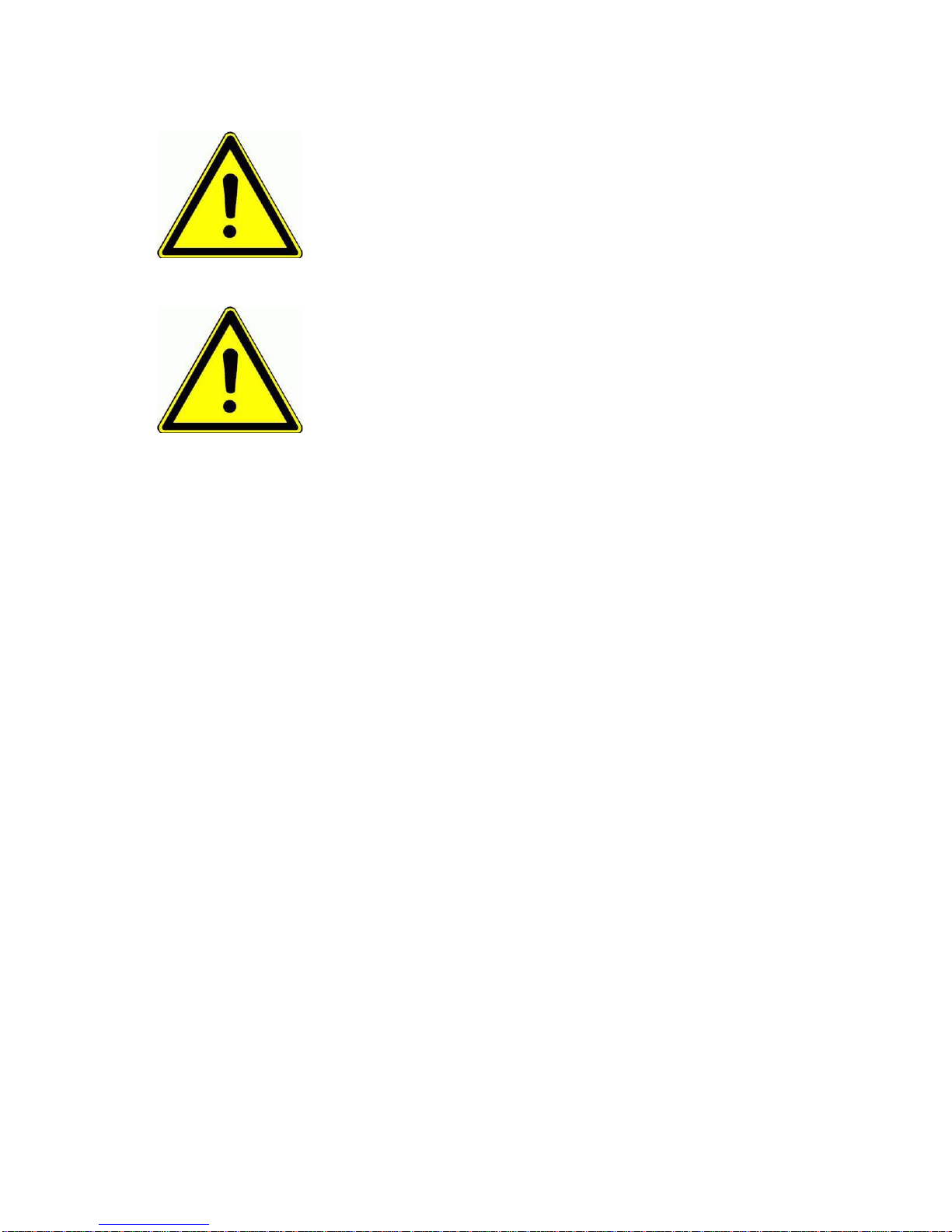
1) Common installation rules and safety information regarding EURA E2000+ inverters
Insulation testing
In case of insulation testing of the whole network, it is recommended
to disconnect the inverter and all optionally mounted filter
components. Some components, used inside the inverter may
impact measurement accuracy, o may become destroyed
All EURA inverters have to pass the insulation test, according to
EN15178, during the final test procedure on the production line.
Potential equalization
If components with no galvanic insulation are used and connected to
the inverter, proper measures are necessary, to guarantee potential
equalization.
E2000+_ Rev.02 -E- SOFT Rev. 5.09
© 2016-06-KPP-EURADRIVES EUROPE GmbH
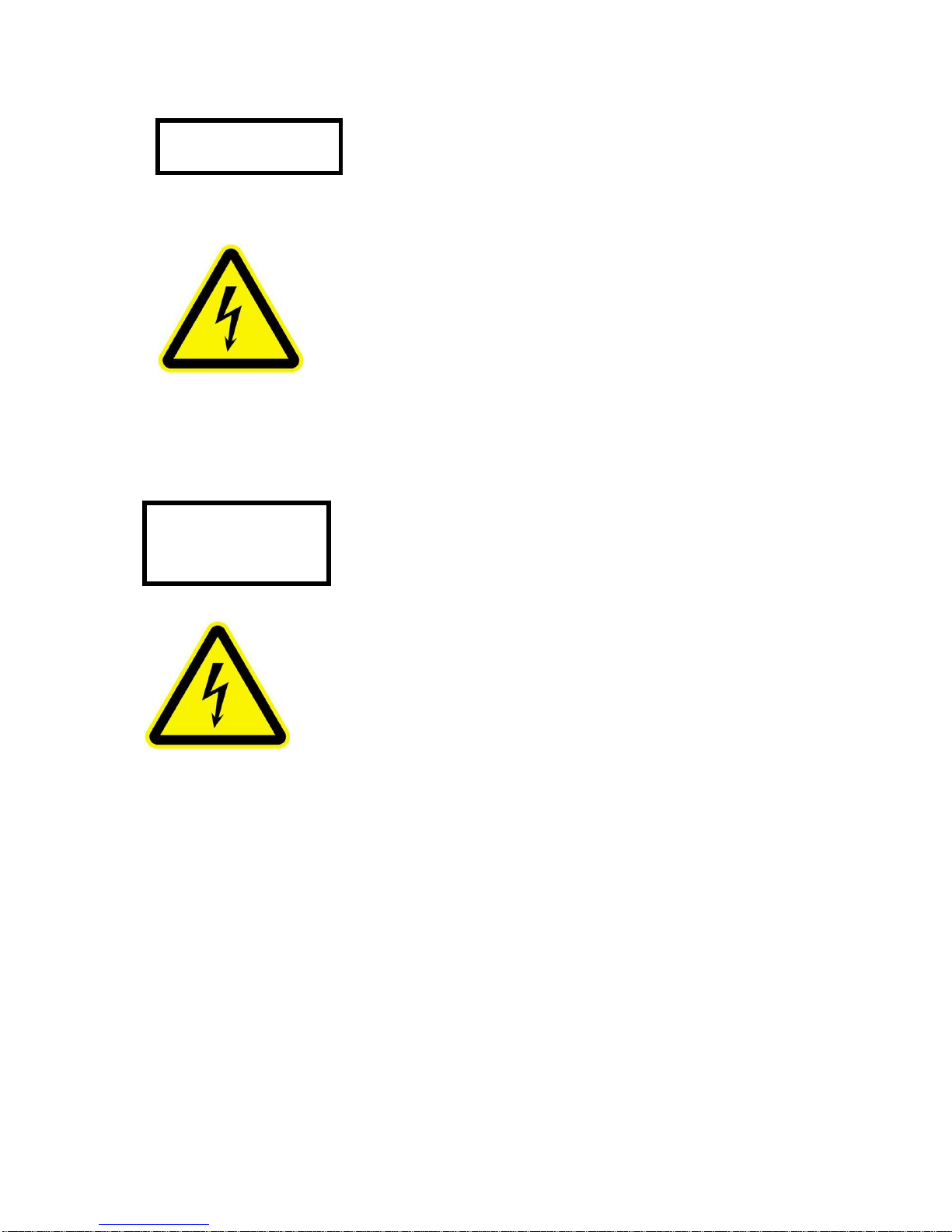
1) Common installation rules and safety information regarding EURA E2000+ inverters
DANGER OF FIRE
BURNS
Braking resistors
All kinetic energy of the system converts to heat, during braking
cycle. This energy dissipates in the braking resistor.
Improper dimensioning of the braking resistor or insufficient
heat exchange may result in high risk if fire
Also over-voltage on the input power supply my lead to high risk
of fire
Therefore all braking resistor must have two thermistors, series
connected, which contacts open in case of over-temperature,
disconnecting the whole power supply, on inverters input terminals
Braking resistors surface may become very hot, even
during normal operation. Therefore it is necessary to
mount the resistor in a save location, using proper
protecting cages.
IMPACT ON
DIFFERENTAL
CURRENT
BRAKERS
Differential current breaker (FI)
The use of frequency inverters may delay or even inhibit the
trigger of differential current breakers.
For life protection, all plant with inverters must have following:
Input wiring protection: Fuses or automatic over-current breaker
(Dimensioning: see tables).
Differential current protection: "All-sensitive"
protectors (breaker), minimum requirement type „B“ ,
mounted on all inverter power lines.
It is not permitted to connect other equipment on inverter
power lines.
For single phase inverters (230V class) the use of differential
current breaker type "A" or "F" is allowed.
The trigger current of the differential current breaker depends on
the operating frequency, motor type, PWM frequency and the length
of the motor cable
It is recommended, to use differential current breaker with 300
mA threshold (for industrial environment).
E2000+_ Rev.02 -E- SOFT Rev. 5.09
© 2016-06-KPP-EURADRIVES EUROPE GmbH
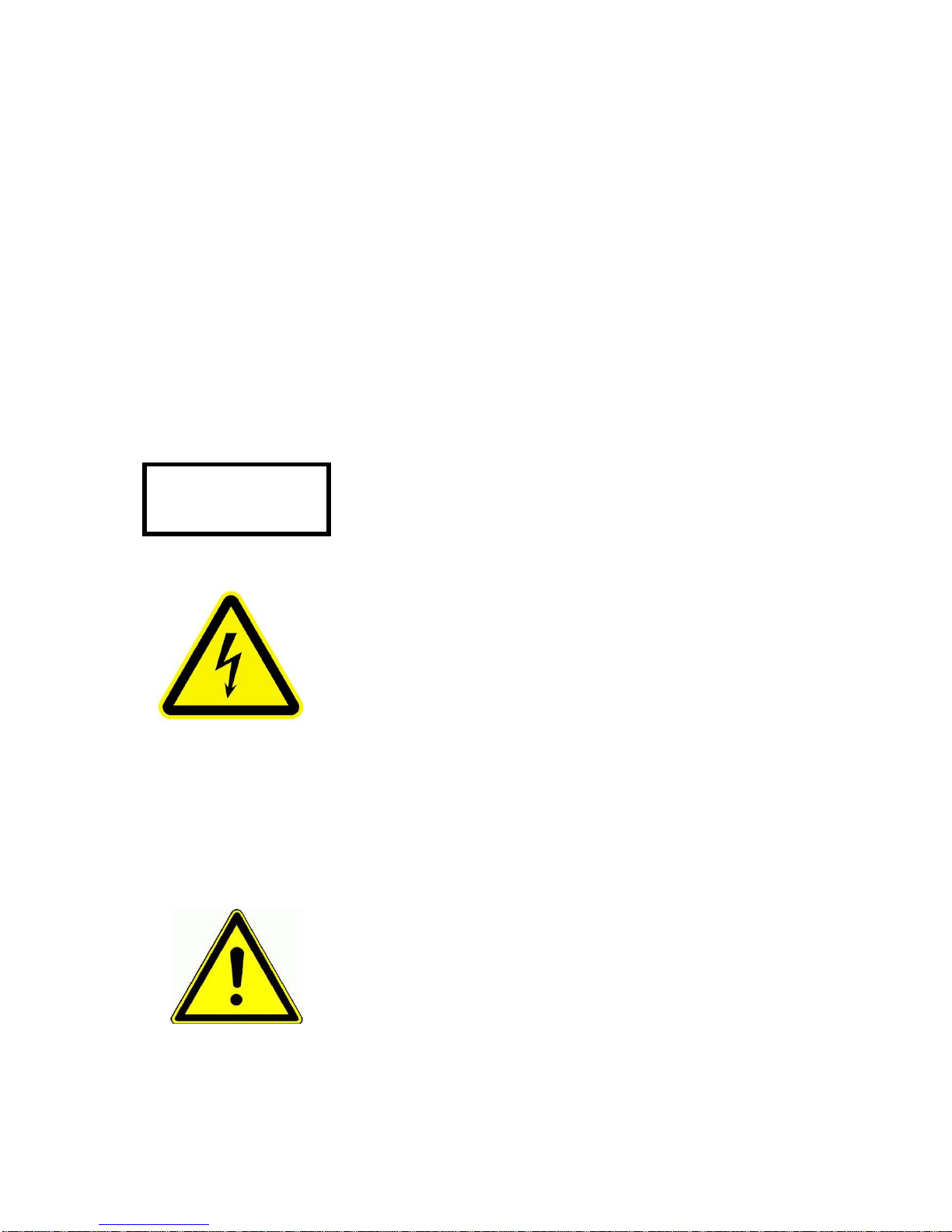
1) Common installation rules and safety information regarding EURA E2000+ inverters
Basic rules for reliable and safe operation
-Proper dimensioning of the system (motor, inverter, mechanical elements).
-Check for correct inverters rated voltage, consider tolerances too
-Review all inverter and motor cabling, including correct terminal tightening
torque (torque values: see table).
-Use proper cable for all control wiring, separate control cable from power cable, min. 15 cm
distance. Use shielded cable for all control connections, exceeding 1 meter
-Twist wires to braking resistors or use shielded cables
-Shielded cables are recommended for motor connection too, especially with distances, exceeding 30
meters.
-Avoid earth loops, all earth connections should have large contact areas, all leading to one
central grounding point (star connected)
IMPORTANT FOR
SAVE INVERTER
OPERATION
One separate circuit breaker is recommended for each inverter
– allowing separate switch off of single inverters.
CHECK FOR PROPER INVERTER PROGRAMMING
Improper programming of the inverter may result in
unpredictable behavior of the system and subsequent high
risk of damage and/or personnel injury.
The inverter may be enabled for multiple automatic restart
attempts in case of fault – delayed restart is possible.
Unpredictable systems reactions may become the result
of internal inverter defects.
The inverter may ignore commands, speed, STOP instructions,
or signals originated from external components.
The braking function of the inverter may fail.
Depending on the application, external safety
components, working independently from the inverter, are
required, to guarantee the safety of the whole system
Inverter protection-functions
Although the inverter is equipped with intelligent protections
functions, the repetitive triggering of those functions may result in
inverter damage.
The inverter is protected against output short circuit and earth fault,
each displayed by a specific code on the display.
Repetitive earth faults and short circuits may damage the
power stage of the inverter.
The motor must be fixed connected, in case, where interruption of the
motor line is required (for safety reason), the circuit should
open/close with inverter in STOP condition only (final stage disabled).
It is recommended, to keep the inverter powered on at all time, if
for application reason repetitive power on cycling is required, it
should not exceed one cycles every 5 minutes – otherwise contact
the manufacturer.
E2000+_ Rev.02 -E- SOFT Rev. 5.09
© 2016-06-KPP-EURADRIVES EUROPE GmbH

1) Common installation rules and safety information regarding EURA E2000+ inverters
Power-grid specification:
The inverter is build for symmetric three phase power supply
systems, with voltage phase to earth/neutral not exceeding 300V. A
transformer can be used for adaptation to higher voltages.
For single phase inverters the maximum input voltage is 240V +15%,
400V class thee phase inverters can work up to 460V +15%. Contact
the inverter manufacturer, before connecting to unbalanced, floating,
or unsymmetrical power systems.
Power supply – short circuit capability
Input chokes (Uk=4%) are recommended to connect the inverter on
a power grid with high short circuit capability, this especially for
continuous full load operation.
If the power supply capability exceeds by 20 times the inverter power,
the use of chokes is mandatory.
Measurements on inverter input and output:
Current and voltage may have no sinus shaped waveform on inverters input/output side.
If improper testing instruments are used, the result may become inaccurate, or in worst case, the
inverter and/or the test instrument may become destroyed.
On input side, the current waveform is composed by fundamental and harmonics, while on output side
the voltage waveform is PWM modulated.
The used instruments must be able to handle the various signal waveforms. For
simple measurements, a high quality moving iron instrument could be suitable.
FOR ANY QUESTION –
CONTACT THE
MANUFACTURER
The inverter manufacturer must be contacted in
case of any question, regarding this
safety/instruction manual, or if some parts have
not been fully understood.
Please ask before installing or placing
on operation the system.
This is mandatory, to avoid any risk for
machinery damage and/or personnel injury.
E2000+_ Rev.02 -E- SOFT Rev. 5.09
© 2016-06-KPP-EURADRIVES EUROPE GmbH
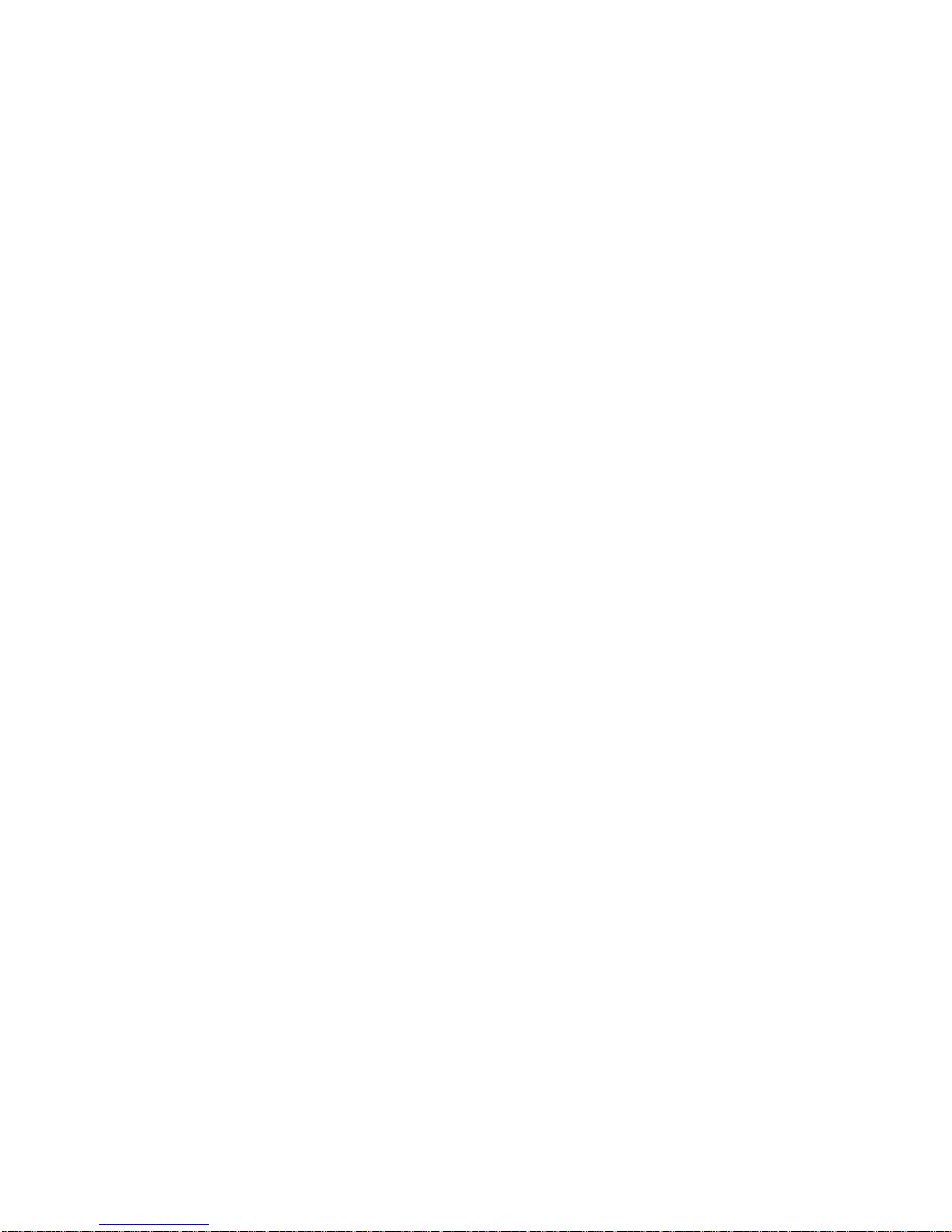
1) Common installation rules and safety information regarding EURA E2000+ inverters
EMC: Basics and recommendations for installation
The E2000+ series inverters are electrical devices, designed for installation in industrial area.
E2000+ inverters are not designed to work stand alone, these inverters are considered as part of
a complex system, for this reason, no separate EMC marking is applied on the inverter.
The machine builder / system integrator is obligated to prove the compliance with actual EMC
standards for the whole system.
Normally, the inverter integrated EMC filters are sufficient, to meet the actual EMC limits (this has
been confirmed by measurements, performed by independent body).
Inverters E2000+ are designed for use in "second environment", (in sense of EN61800-3).
This means installation in industrial area, where power supply is done via separate
transformer.
Fore installation in "first environment" (residential area – public low voltage power
grid), additional filter components may become necessary, to meet EMC rules.
EMC - adequate installation
Mounting in metal cabinet, if possible, the cabinet should be divided into power and control area,
using metal shielding barrier, or similar
Connect all metal parts, grounding cables, cable shields on one central point, using the blank
mounting plate as contact area.
Use 10mm2 cables for potential equalization, "star" connected on one central point.
Please consider, that inverters and filters may have more than 3,5 mA leakage current, therefore
use proper earth/ground conductors:
Grounding conductor min. 10 mm² (copper)
Grounding connection with separate monitoring system, which
disconnects automatically in case of fault.
Dual grounding, using separate cable and terminals.
Use shielded cables, wherever possible, with copper mesh, common cable steel protection is
not working as shield.
Connect shields on large blank areas with potential equalization bars. Use special cable glands,
with integrated contact brushes.
It is not allowed to extend cable shield, using single wire.
Mount all external filter components as close as possible to the noise source (inverter) – get
perfect contact, mounting directly on the blank cabinet plate.
Keep all wiring as short as possible, separate different networks, min. 15 cm distance.
Different networks are: power supply, motor cable (incl. brake resistor), low voltage control wiring
(control signals, feed back, data line).
Twist all unshielded cables
Unused wires in cables should be connected to ground
E2000+_ Rev.02 -E- SOFT Rev. 5.09
© 2016-06-KPP-EURADRIVES EUROPE GmbH
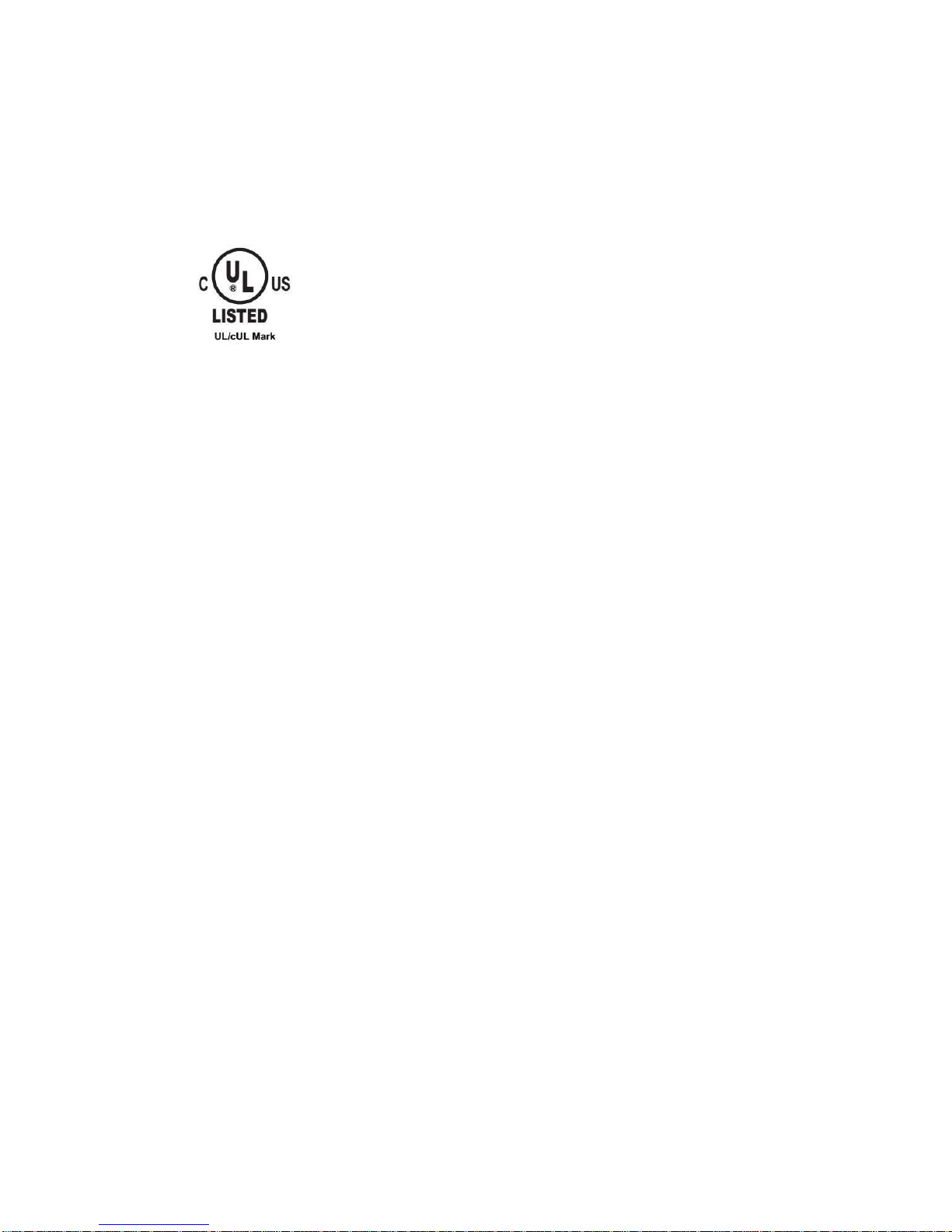
1) Common installation rules and safety information regarding EURA E2000+ inverters
Inverters with UL mark: Additional information
Following information are valid for inverters, designed for use in countries, which require UL approval.
All information below must be available to all who are responsible for commercialization, installation and place in
operation.
UL Standards
The UL/cUL mark applies to products in the United States and Canada and it means that UL has performed product testing and
evaluation and determined that their stringent standards for product safety have been met. For a product to receive UL certification, all
components inside that product must also receive UL certification.
UL Standards Compliance
This drive has been tested in accordance with UL standard UL508C, File No. E363934 and complies with UL requirements. To
ensure continued compliance when using this drive in combination with other equipment, meet the following conditions:
1)Do not install the drive to an area greater than pollution severity 2 (UL standard)
2)Installation and operating instructions shall be provided with each device.
The following markings shall appear in one of the following locations: shipped separately with the device; on a separable, self-adhesive
permanent label that is shipped with the device; or anywhere on the device itself.
a) Designation markings for each wiring diagram;
b) Markings for proper wiring connections.
c) “Maximum Surrounding Air Temperature 40ºC.” or equivalent;
d) “Solid State motor overload protection reacts when reaches 150% of FLA” or equivalent;
e) “Install device in pollution degree 2 environment.” or equivalent;
f) For Models of Frame Size(E2000-0007T3UBR;E2000-0011T3 UBR;E2000-0015T3 UBR;E2000-0022T3UBR): “Suitable For Use On A
Circuit Capable Of Delivering Not More Than 5,000 rms Symmetrical Amperes, 480 Volts Maximum When Protected By made by
COOPER BUSSMANN L L C Class T Fuse: JJS-15.” or equivalent.
For Models of Frame Size (E2000-0030T3UBR;E2000-0037T3UBR;E2000-0040T3UBR): “Suitable For Use On A Circuit Capable Of
Delivering Not More Than 5,000 rms Symmetrical Amperes, 480 Volts Maximum When Protected By made by COOPER BUSSMANN L L C
Class T Fuse: JJS-25.” or equivalent.
For Models of Frame Size (E2000-0055T3UBR;E2000-0075T3UBR): “Suitable For Use On A Circuit Capable Of Delivering Not More Than
5,000 rms Symmetrical Amperes, 480 Volts Maximum When Protected By made by COOPER BUSSMANN L L C Class T Fuse: JJS-35.” or
equivalent..
g) “Integral solid state short circuit protection does not provide branch circuit protection. Branch circuit protection must be provided in
accordance with the National Electrical Code and any additional local codes” or the equivalent;
h) “CAUTION – Risk of Electric Shock” should be provided, followed by instructions to discharge the Bus Capacitor or indicating the
time required (5 minutes) for Bus Capacitor to discharge to a level below 50 Vdc;
i) “Drives have no provision for motor over temperature protection” or equivalent;
j) For used in Canada only: “TRANSIENT SURGE SUPPRESSION SHALL BE I NSTALLED ON THE LINE SIDE OF THIS EQUIPMENT
AND SHALL BE RATED __480_ V (PHASE TO GROUND), 480 V (PHASE TO PHASE), SUITABLE FOR OVERVOLTAGE
CATEGORY _III_, AND SHALL PROVIDE PROTECTION FOR A RATED IMPULSE WITHSTAND VOLTAGE PEAK OF _6 kV” or
equivalent.
Field Wiring Terminal Markings – Wiring terminals shall be marked to indicate the proper connections for power supply and load, or a
wiring diagram coded to the terminal marking shall be securely attached to the device:
a.“Use 60/75°C CU wire” or equivalent;
b. Required wire torque, type and range listed: see chapter 4) Empfohlene Leitungsquerschnitte – Sicherungen Leistungsklemmen
Grounding – The wire connector intended for ground connection for field installed equipment, shall be clearily identified such as being
marked “G”, “GRD”, “Ground”, “Grounding”, or equivalent or with the grounding symbol (IEC 417, Symbol 5019).
Tightening torque and wire section for field grounding wiring are marked adjacent to the terminal or on the EMV: Grundlagen und
ire section for field grounding wiring are marked adjacent to the terminal or on the wiring diagram.
E2000+_ Rev.02 -E- SOFT Rev. 5.09
© 2016-06-KPP-EURADRIVES EUROPE GmbH
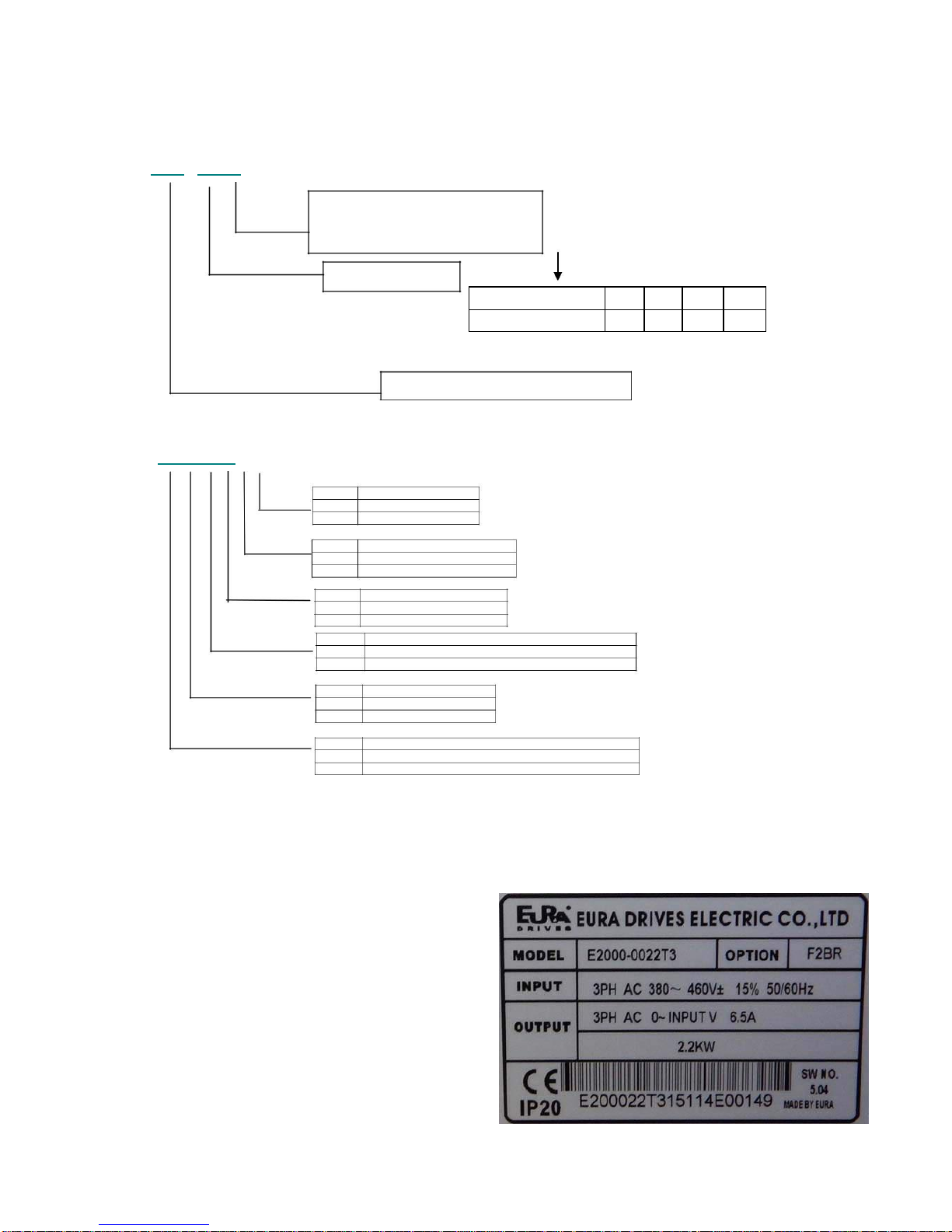
2) Product data – product power range
2) Product data / product power range
Product naming convention
E2000 – 0007 S2
Power supply:
S2 single phase 220/230 VAC +/-15%
T3 three phase 400/460 VAC +/-15%
Codierung-siehe Typenübersicht
Motor rated power
Type-serial-class (E2000+)
Options identifier
D F 1 Y K B R
Keypad without potentiometer
Keypad with potentiometer
Fix integrated, not removable
Removable, inverter has remote control function
Wallmount (inside cabinet)
Inverter integrated in cabinet
Nameplate
The adjacent picture shows a typical nameplate of an series
E2000+, three phase, 400V 2,2 kW inverter, 6,5A rated current,
including following options: F2 (MODBUS), B (Brake-chopper) R
(integrated EMC-Filter)
E2000+_Rev.02 -E- SOFT Rev. 5.09
© 2016-06-KPP- EURADRIVES EUROPE GmbH
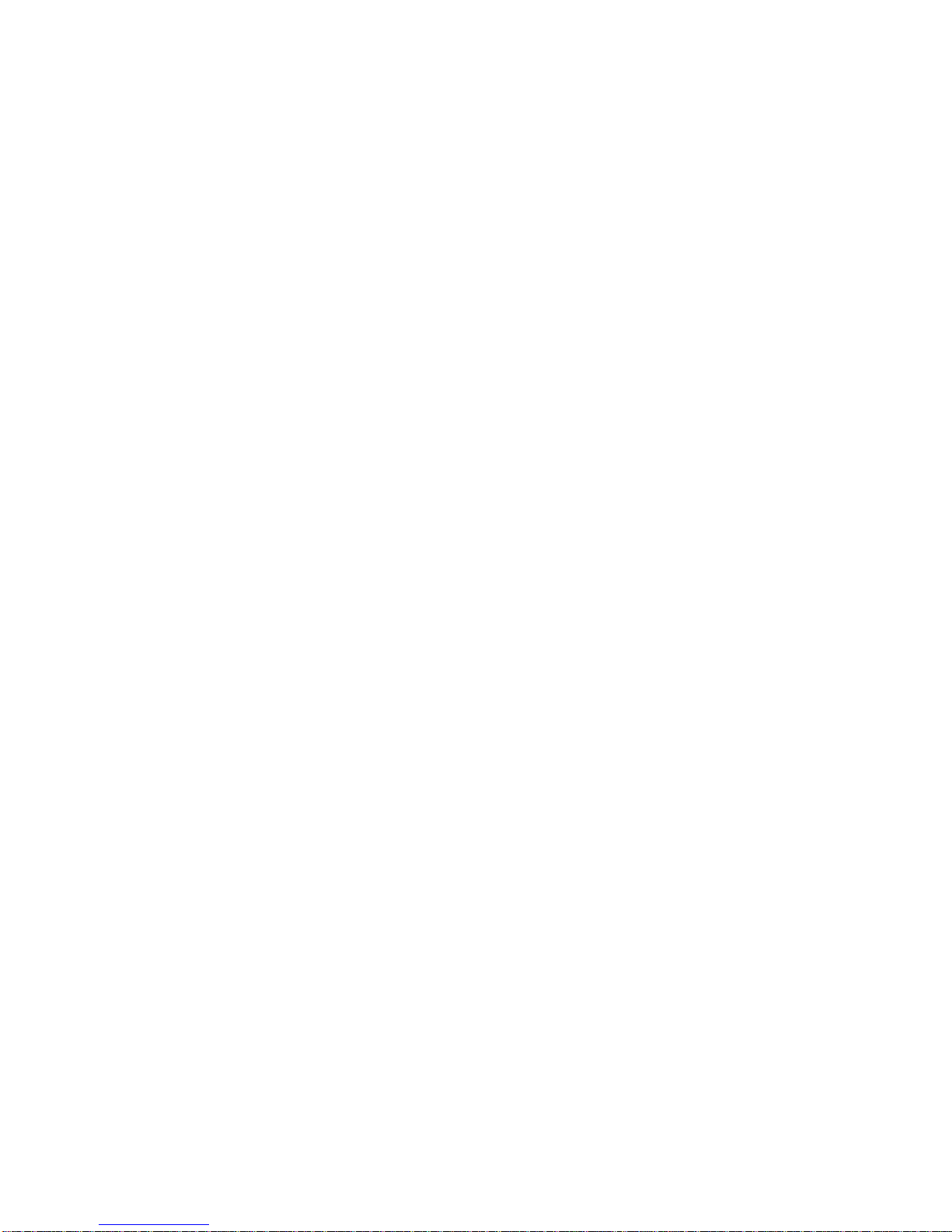
2) Product data – product power range
E2000+_Rev.02 -E- SOFT Rev. 5.09
© 2016-06-KPP- EURADRIVES EUROPE GmbH
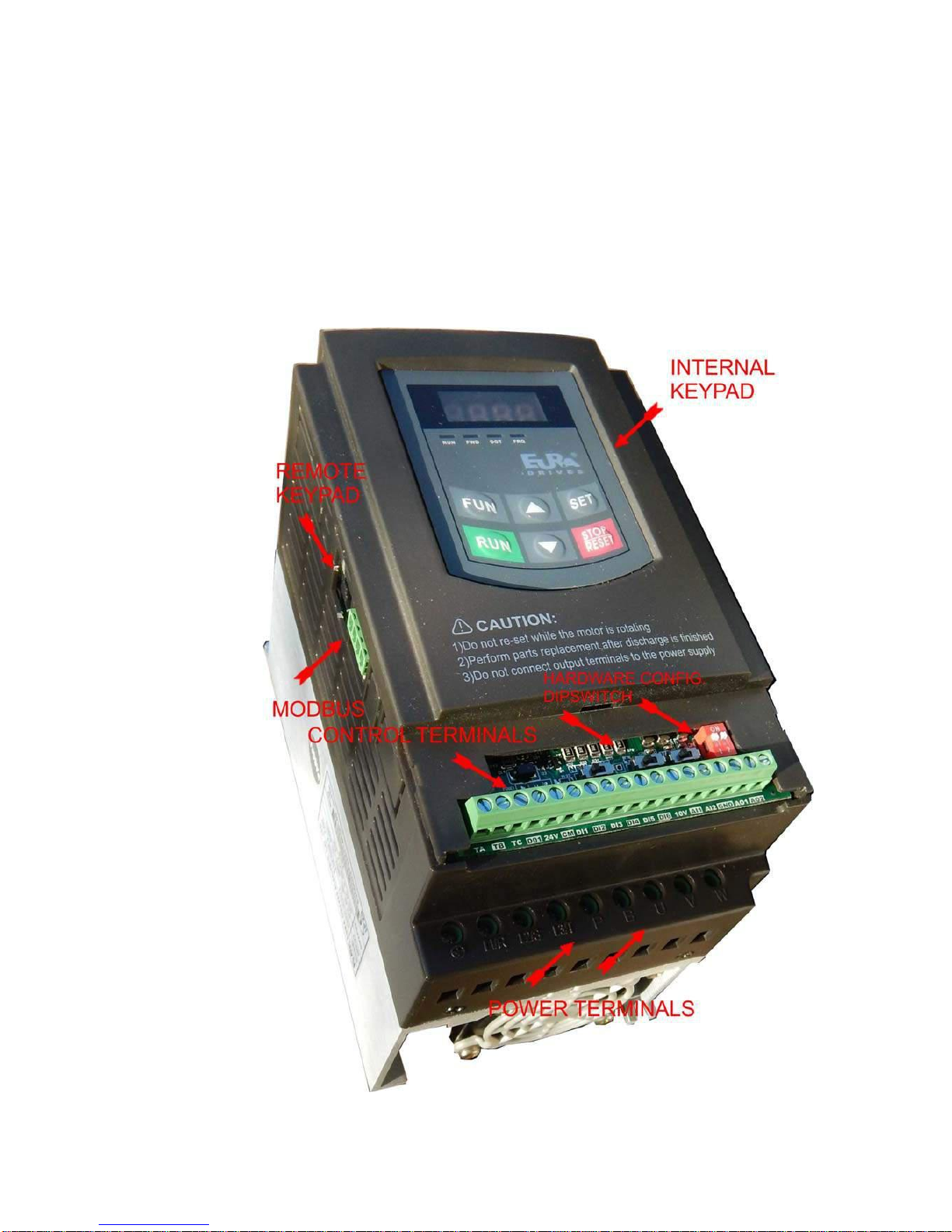
2) Product data – product power range
Mechanical construction
There are two different basic concepts:
Inverter with power range from 0,2 to 22 kW: POLYCARBONATE enclosure, build on a constructional base (heatsink) with
the keypad integrated on the cover (not removable) – framesize E1 – E6
Inverter with power range from 30 to 400 kW: Steel panel, power and control terminals inside, with the keypad integrated in
the cover and removable - framesize C3 – C6
Appearance of an E2000+ Size E2 inverter
E2000+_Rev.02 -E- SOFT Rev. 5.09
© 2016-06-KPP- EURADRIVES EUROPE GmbH
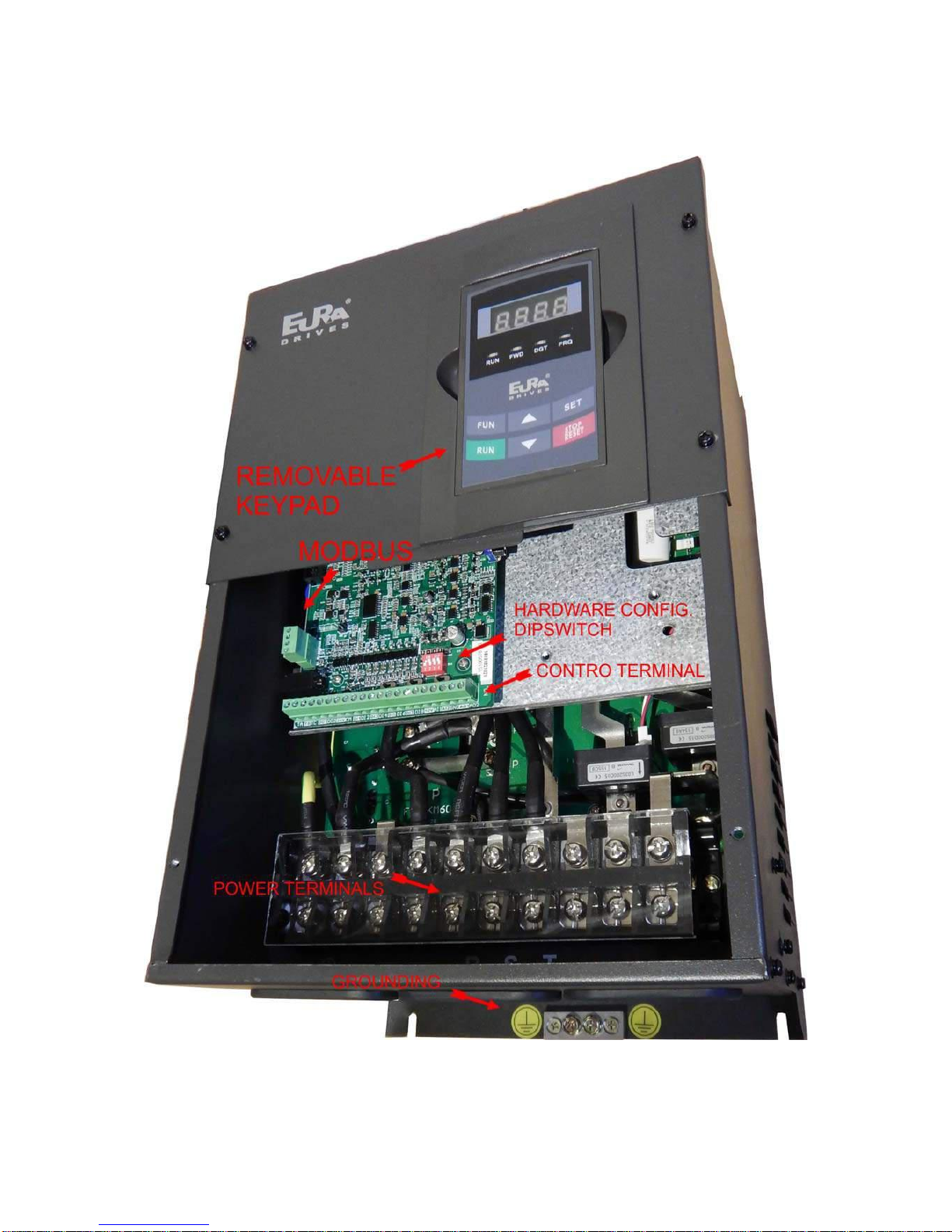
2) Product data – product power range
Appearance of an E2000+ Size C3 inverter
E2000+_Rev.02 -E- SOFT Rev. 5.09
© 2016-06-KPP- EURADRIVES EUROPE GmbH
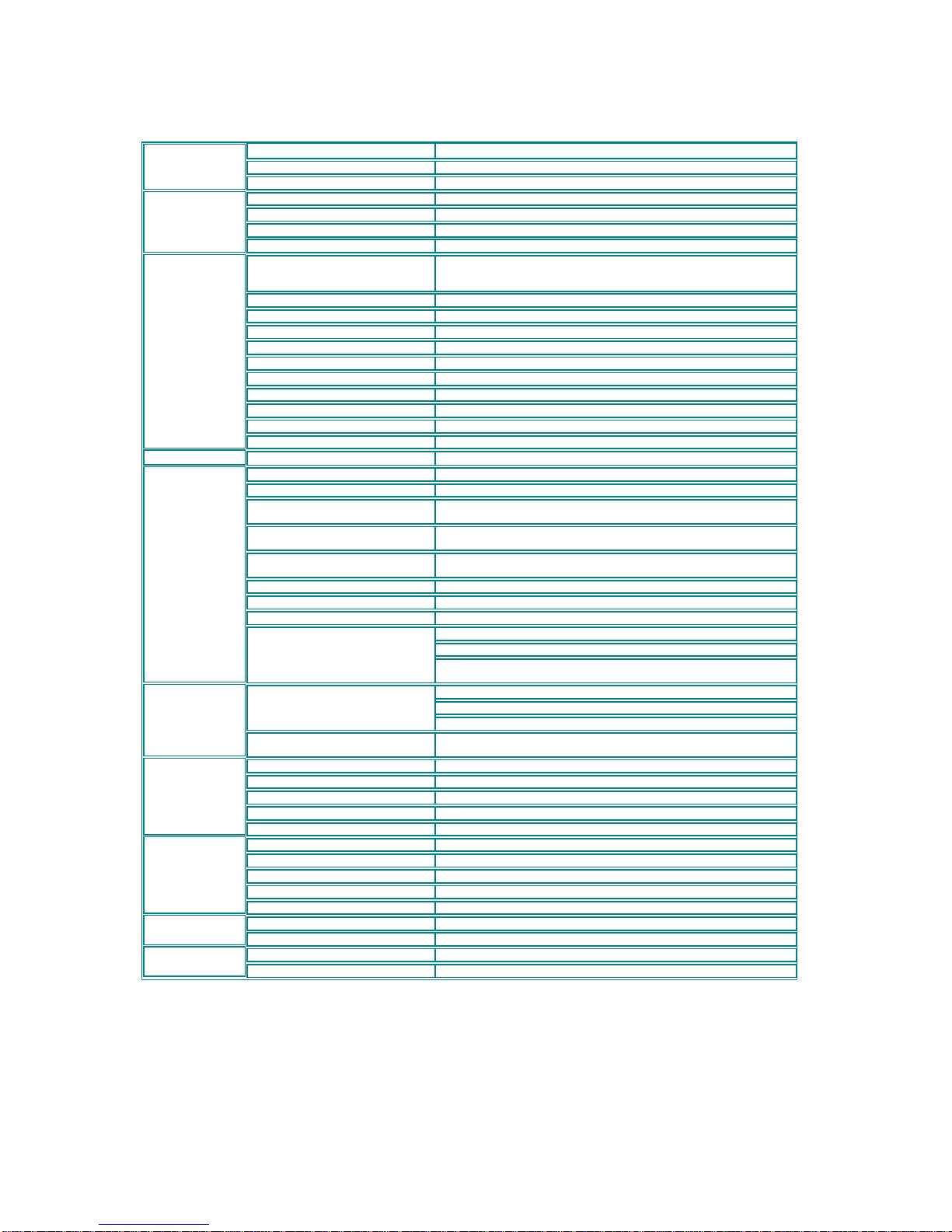
2) Product data – product power range
Technical data - inverter series E2000+
Power supply
Output
Control mode
Display
I/O Channels,
control
functions
Protection
functions, incl.
fault memory
Optionals
Environmental
conditions
Power range
Standards
3-phase 380…460V +/- 15% - 1phase 230V +/- 15%
Integrated for 2. environment (up to 90 kW)
Resolution of output frequency
SENSORLESS VECTOR (SLV) – Speed / torque control
Permanentmagnet Synchronus Motor PMM control
Linear, quadratic, and user-programmable curve – Voltage setpoint
150% rated torque at 0,5 Hz (in SLV mode)
Manual input / intelligent AUTOTUNING function
Freq. threshold, duration and intensity programmable – DC injection
Integrated chopper transistor (Brake resistors – see product table)
7 Segment LED display -4- digit
For programming and visualization of different operating parameters
Inverter control - Start/Stop
To configure: terminals / operation panel / serial link
8 (6) digital inputs (HIGH/LOW configurable), pulse input
Speed / torque reference signal
Potentiometer (on operating panel / Extern), analogue input (terminals),
operating panel keys, pulse input, serial link
Reference analogue channels
2 Analogue channels 0…10V, -10V/+10V, 0..(4)20 mA (with programmable
offset, gain – to concatenate mathematically each other)
2 analogue output channels, both programmable in gain, different functions to
2 digital outputs (different functions to assign)
1 switchover contact 5 A 230 V (programmable for different functions)
Serial link (MODBUS – ASCI/RTU)
Jog mode, 12V / 50 mA auxiliary power supply on terminals
Special function - control options
PI-control / Pump control, Master/Slave control
Fixed frequency control, programmable cycling frequency sequence
"Catch on the fly function", AUTORESET/RESTART function
Overvoltage, Undervoltage
Electrical protection functions
Overcurrent, Overload, Motor-Overload, Output-short
Phaseloss, Motor-Phase imbalance
Thermal protection functions
Heatsink overtemperature – Motor overtemperature (PTC/KLIXON),
Remote keypad / programming tool
High power resistors for heavy duty operation
PFC chokes – dv/dt limiting output filter - sinusfilter
USB Stick with parameter dublication function – USB/RS485 converter
PC-Link Software (via MODBUS)
Special tool for programming, control and diagnostic (parameter set memory)
Max. 90 % not condensing, no corrosion
1000 m - 1% derating / 100m above
E2000+_Rev.02 -E- SOFT Rev. 5.09
© 2016-06-KPP- EURADRIVES EUROPE GmbH
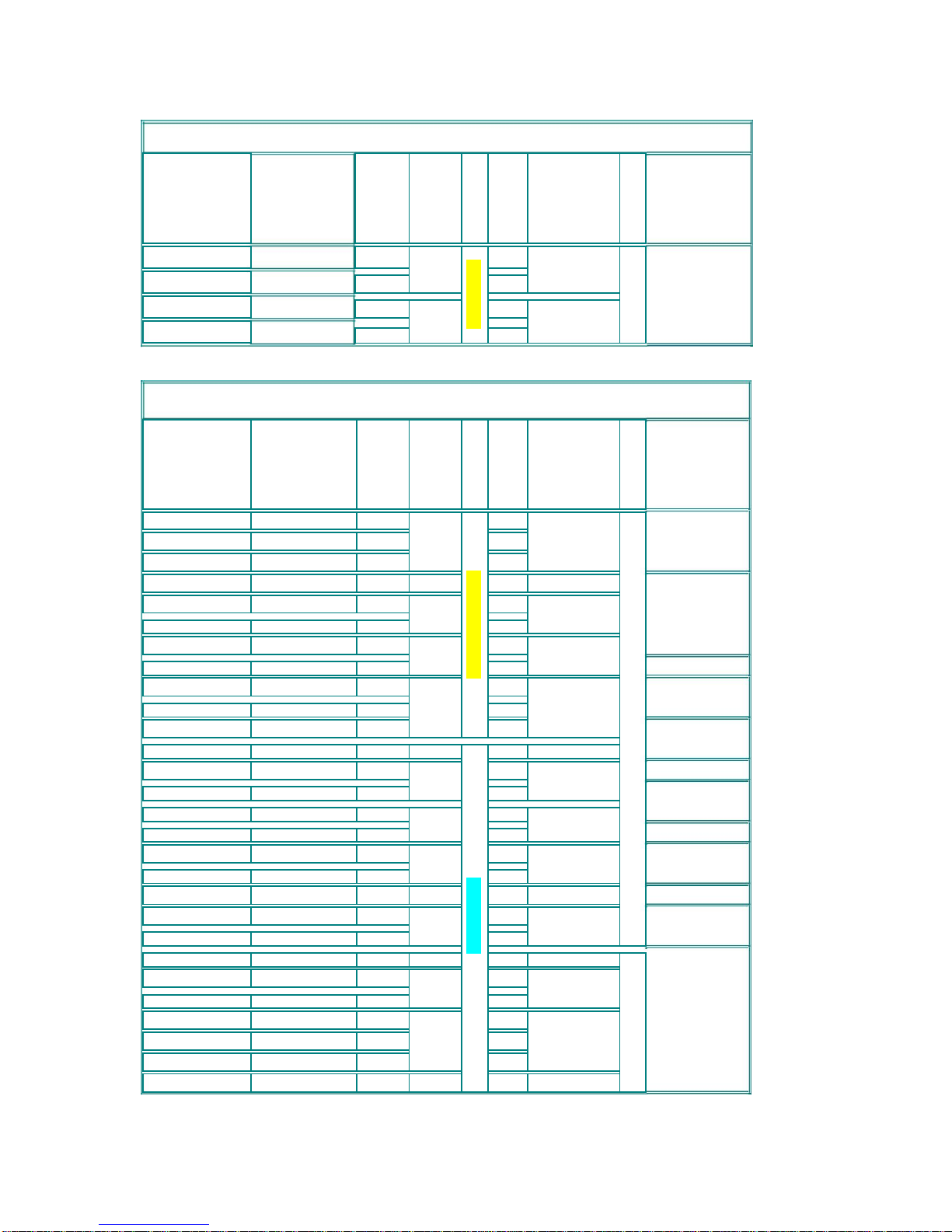
2) Product data – product power range
Inverter 230V
valueresistancebra
ke.Min
valueresistancebra
ke.Min
Note: The indicated RMS input current is approximated for direct connection to a power grid, having a short
circuit capability of 20kA – use adequate input chokes (5% choke) to reduce the RMS current
E2000+_Rev.02 -E- SOFT Rev. 5.09
© 2016-06-KPP- EURADRIVES EUROPE GmbH
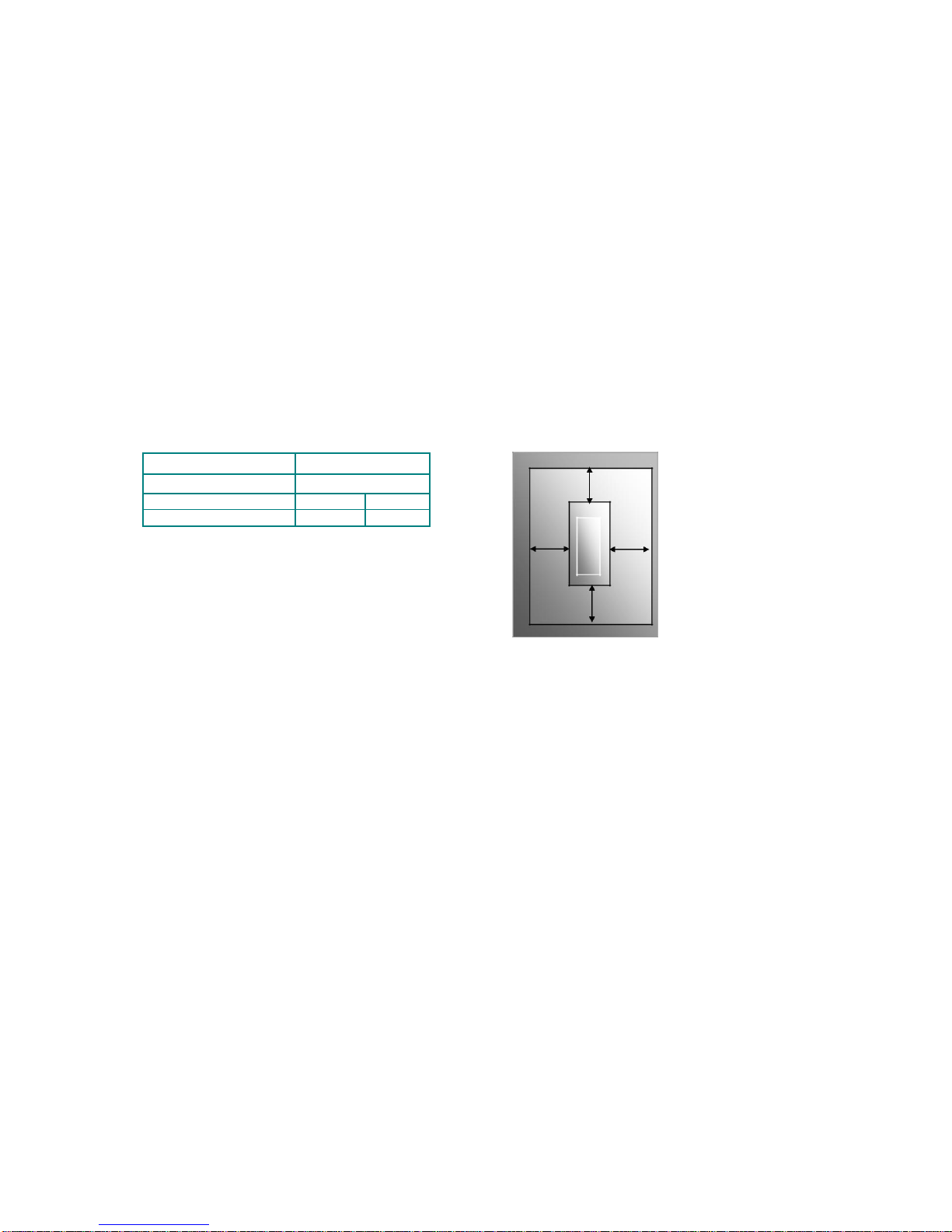
3) Inverter mounting
3) Inverter mounting
Please read all, what reported on chapter 1) Common installation- and safety rules for EURA DRIVES inverters, series
E2000+ before proceeding with inverter mounting, cabinet wiring, and putting into service the system.
Mounting in cabinet
Accordingly to the protection degree class (IP20/21), the inverter must be placed in a proper cabinet.
The inverter should be mounted vertically, using all available mounting holes.
Avoid mounting of more inverters in vertical array. If absolutely necessary, keep double mounting distances
The table below, shows the minimum mounting distances in vertical and horizontal direction
Sufficient heat exchange of the cabinet must be guaranteed, to keep all operating conditions within the specified limits.
Distances for mounting
in cabinet
Fans: All inverters out of the E2000+ series are forced ventilated. Specific parameters are used to set various fan operating
modes: Always ON (F702=2), ON with inverter in running mode (F702=1), or temperature controlled (F702=0) (F703=Temp.
threshold)
see 14) Parameter group 700: Error handling and protection functions (F702-F703)
Maintenance and service:
Provided that the inverter is working in respect of specified environmental conditions, provided that the inverter is
used for proper application, and all instructions have been exactly followed for installation, putting in service and
operation, the inverter does not need any specific maintenance.
E2000+_Rev.02 -E- SOFT Rev. 5.09
© 2016-06-KPP-EURADRIVES EUROPE GmbH
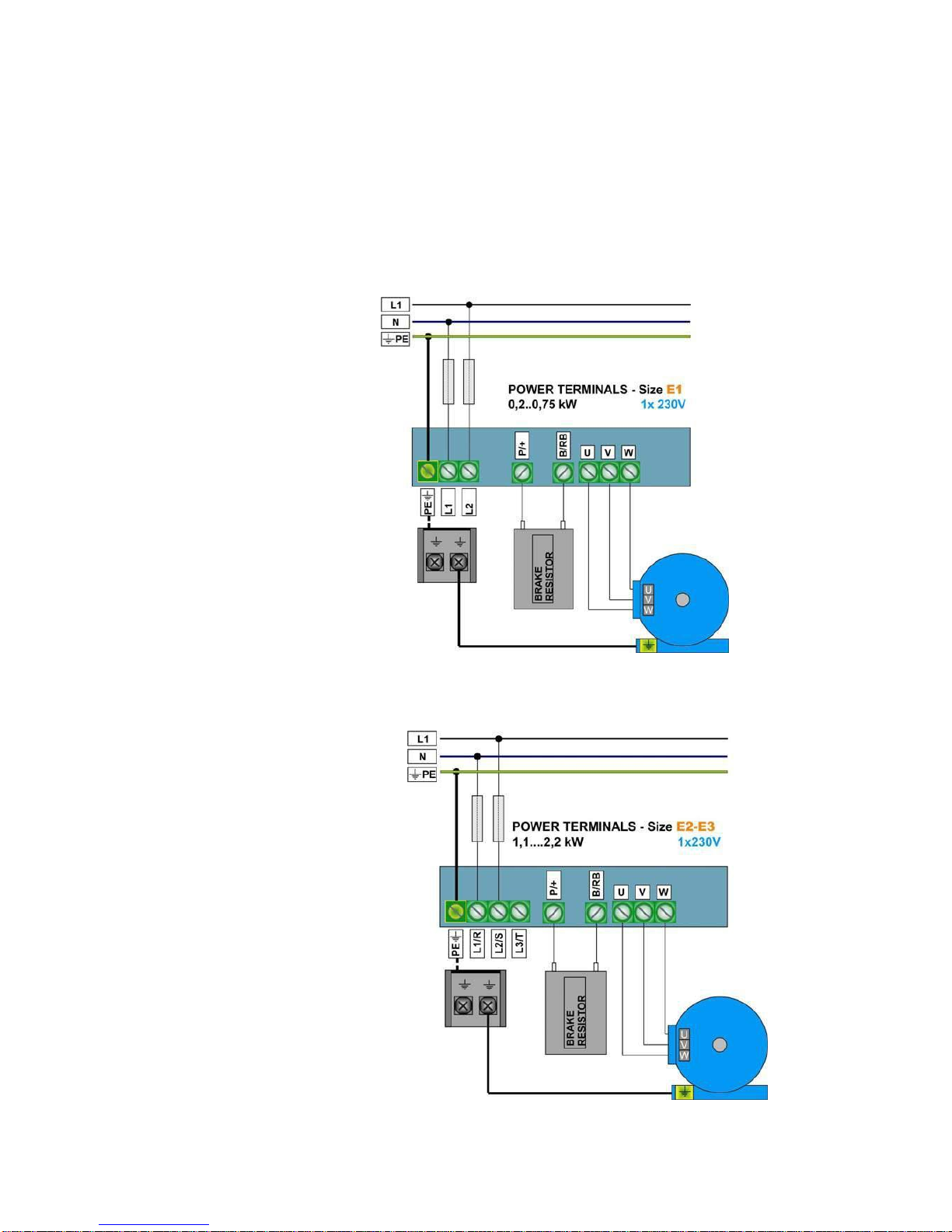
4) Electrical connections of E2000+ inverters
4) Electrical connection of E2000+ Inverters
E2000+ inverters have separate terminals for power- and control-connection. Adequate cables are requested for wiring
the inverter, all safety rules, reported in the first chapter of this manual are to observe.
Power terminals:
There are different arrangements for power terminals, depending on inverter size and number of input phases.
230V Singlephase inverter 0.2 – 0,75 kW – framesize E1
230 V Singlephase inverter 1,5 - 2,2 kW - framsize E2, E3
E2000+_Rev.02 -D- SOFT Rev. 5.09
© 2016-06-KPP-EURADRIVES EUROPE GmbH
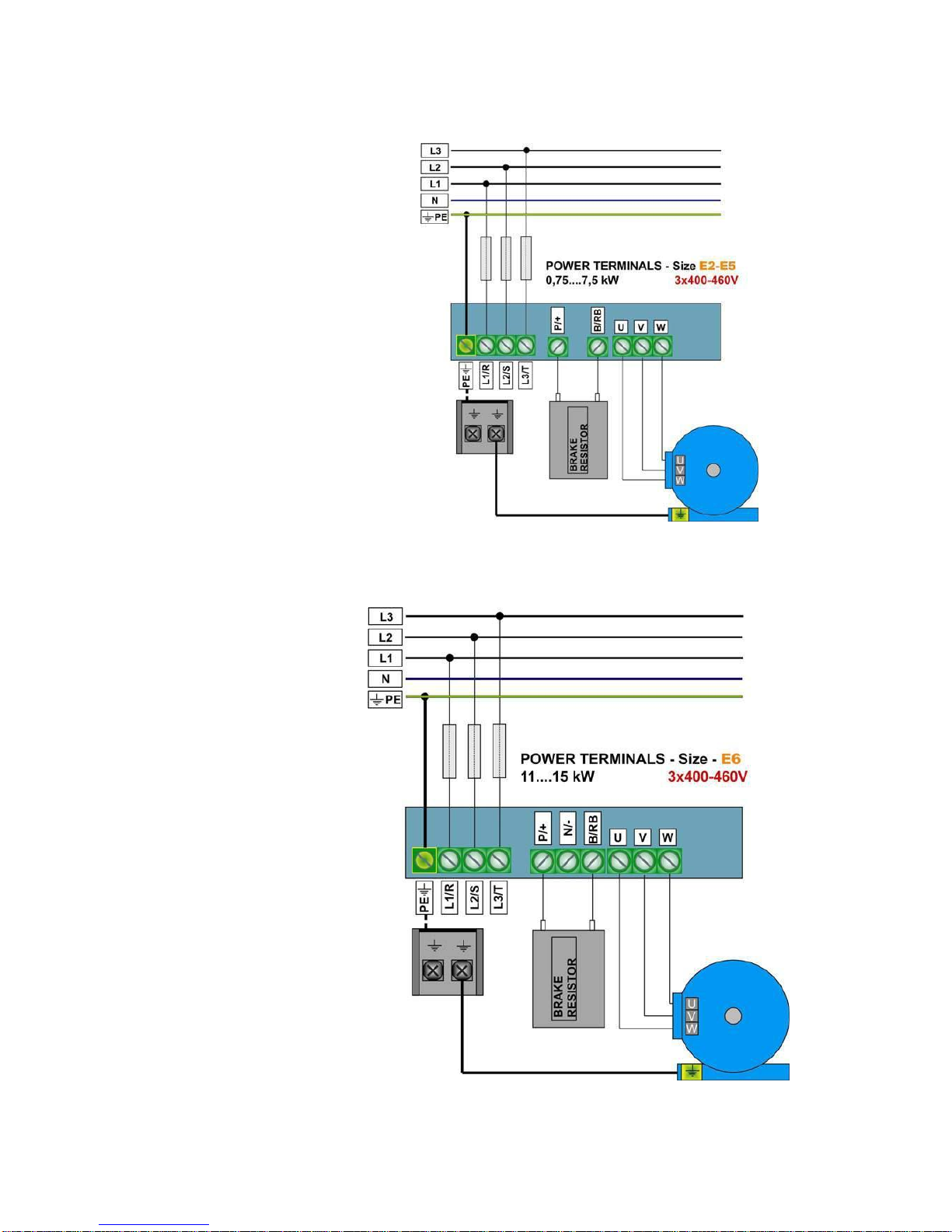
4) Electrical connections of E2000+ inverters
400V Threephase inverter 0.75 – 11 kW – framesize E2, E3, E4, E5
400V Threephase inverter 15 – 22 kW – framesize E6
E2000+_Rev.02 -D- SOFT Rev. 5.09
© 2016-06-KPP-EURADRIVES EUROPE GmbH
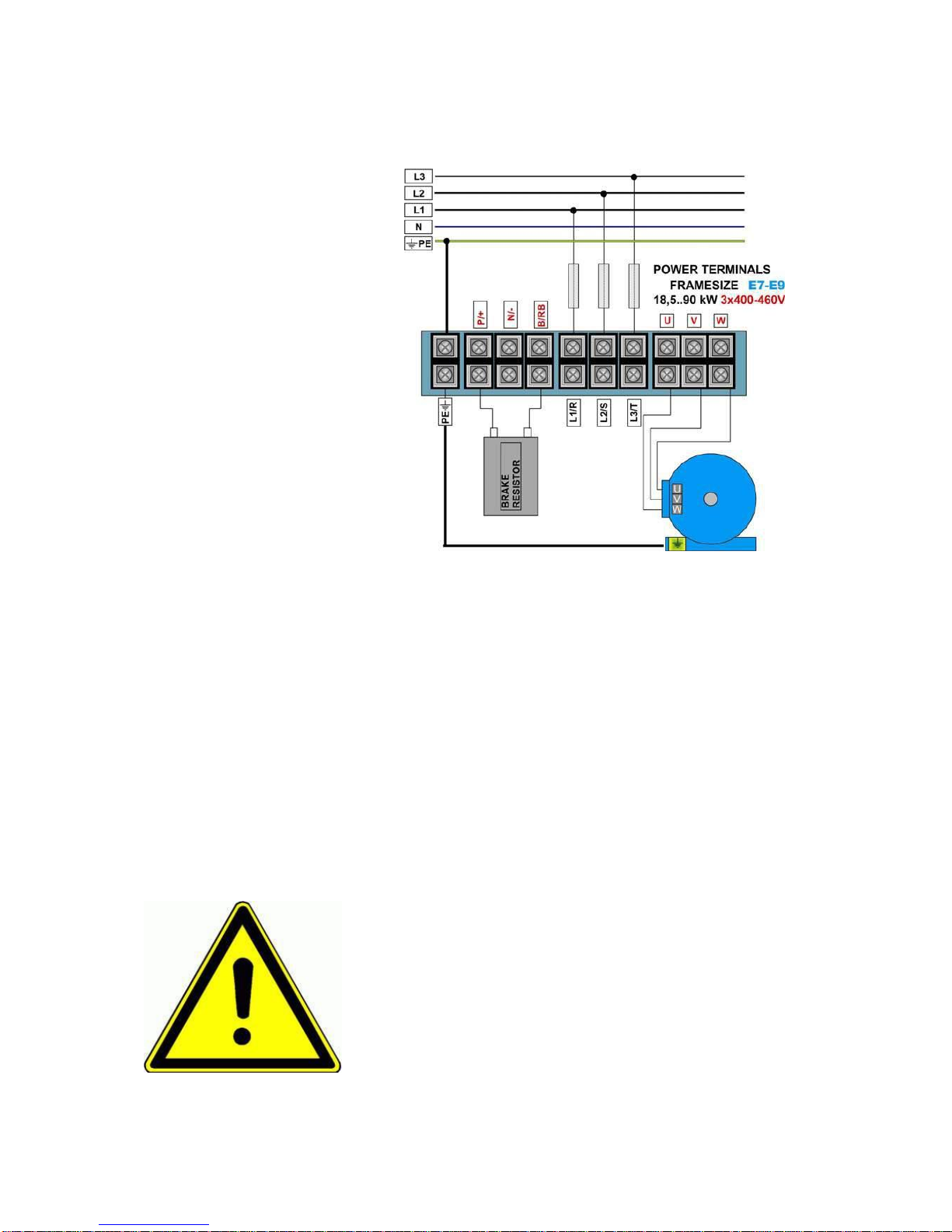
4) Electrical connections of E2000+ inverters
400V Threephase inverter - above 22 kW C3 – C6
Brake resistor:
E2000+ inverters have build in chopper transistor as standard. An adequate brake resistor can be connected externaly. The
maximus lenght of the cable is 2mt, crossection depends on the current through the resistor, calculated, considering the
brake switch on voltage of 800V and the resistor value.
The minimum resistor value for single inverter power ranges is reported in table on chapter: 2) Product overview / Product data
– the value in the table is the absolute minimum value – resistors with up to three times higher resistance value
are allowed.
Right dimensioning of the resistor, especially in sense of continuous power and peak power depends on the application
(inertia, speed, brake cycle rate).
EURADRIVES accessories program offers special resistors for all kind of application.
ATTENTION!! All stored dynamic energy of the system is converted in heat,
during the brake process - heat, dissipated in the brake resistor.
Overheating of the resistor, risk of burning and fire may be the consequence of
improper dimensioning, wrong parameter setting, inverter fault or power
supply over-voltage.
It is necessary to provide suitable electrical and mechanical protection of the
brake resistor
The rules in chapter 1) Common installation and safety rules are to observe.
EURADRIVES does not take any responsibility for any damage or risk, if
improper brake resistors are used.
E2000+_Rev.02 -D- SOFT Rev. 5.09
© 2016-06-KPP-EURADRIVES EUROPE GmbH
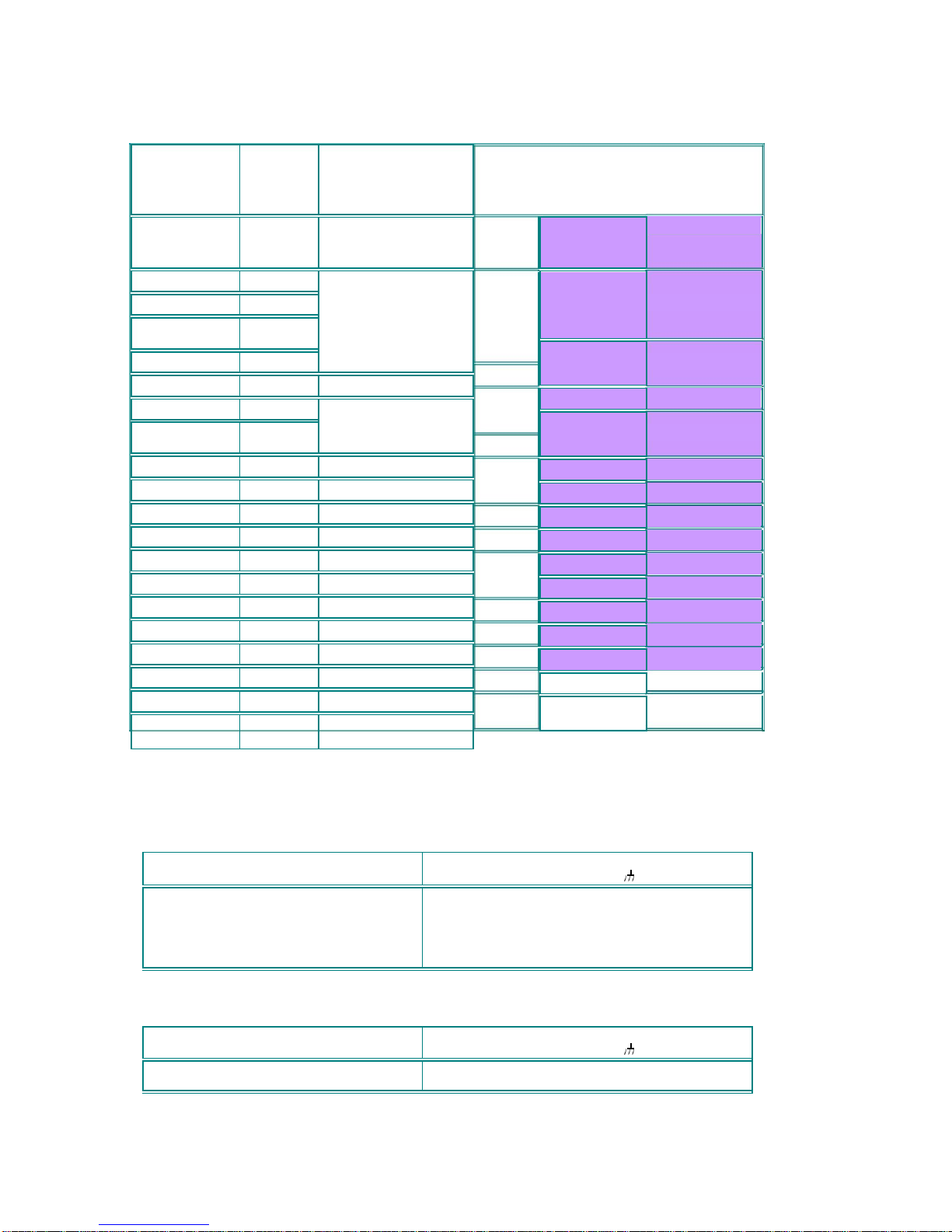
4) Electrical connections of E2000+ inverters
Recommended cable cross sections, fuses, terminal tightening torque
Earth/ground connection
Minimum earth/ground wiring cross section – for terminal connection
Motor wiring section: S (mm2)
Minimum earth wiring cross ection
Minimum earth/ground wiring cross section – for chassis connection (on designed "G"
"GND" "GROUND" connection points)
Motor wiring section: S (mm2)
Minimum earth wiring cross ection
E2000+_Rev.02 -D- SOFT Rev. 5.09
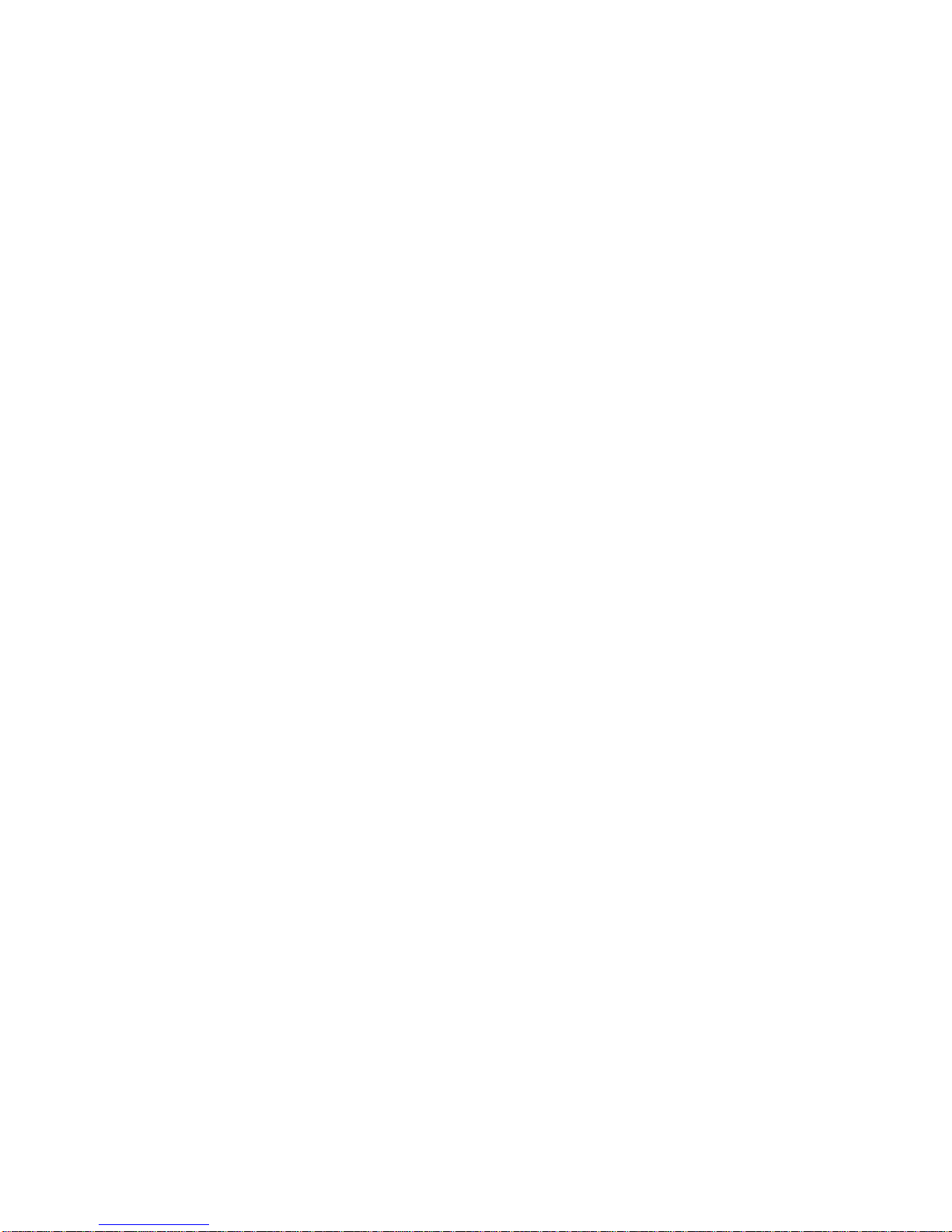
© 2016-06-KPP-EURADRIVES EUROPE GmbH
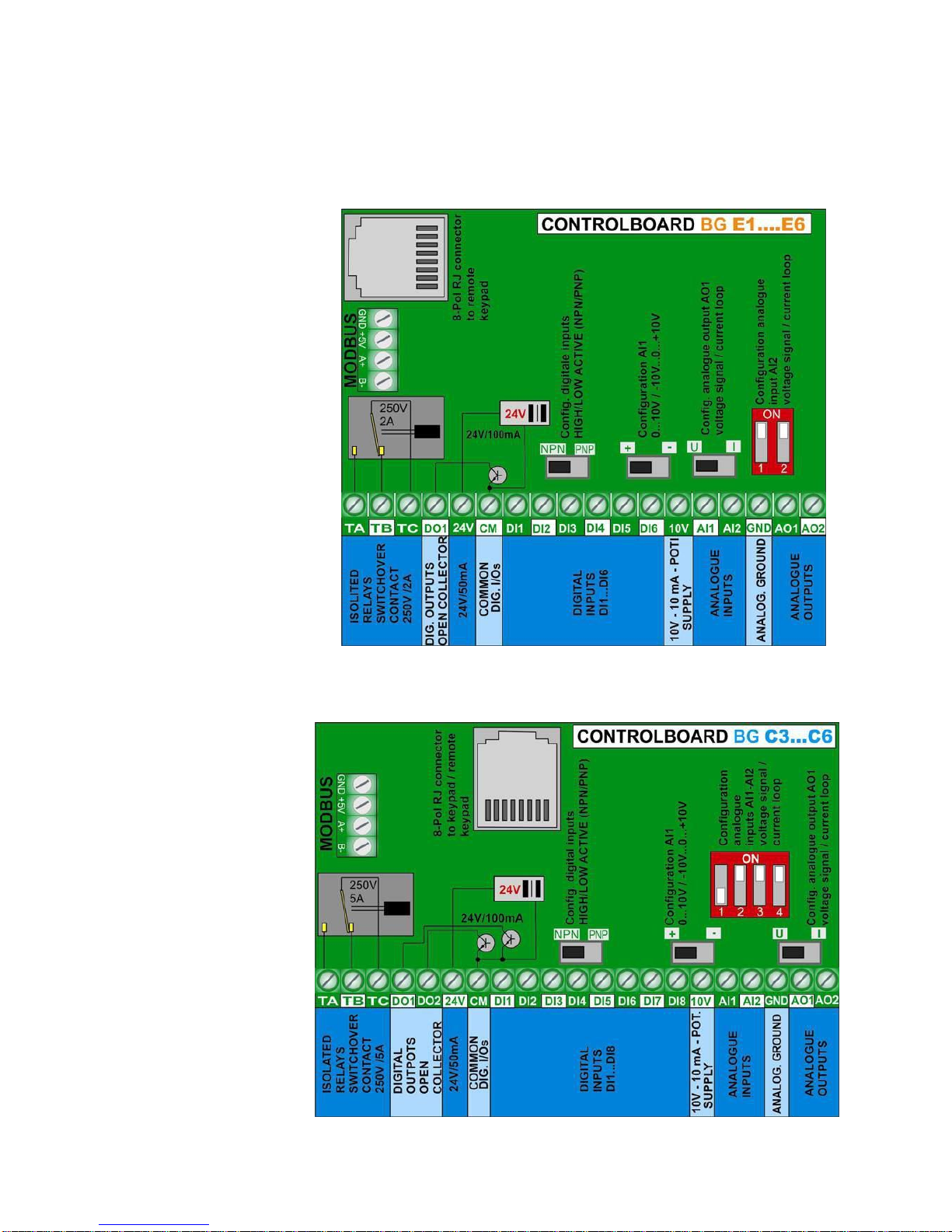
4) Electrical connections of E2000+ inverters
Control terminals – control board
Two different configurations of control terminals and control boards are available, depending
on inverter frame size
Inverter size E1 – E6
0,20...22 kW
Inverter size C3 – C6
30….400 kW
E2000+_Rev.02 -D- SOFT Rev. 5.09
© 2016-06-KPP-EURADRIVES EUROPE GmbH