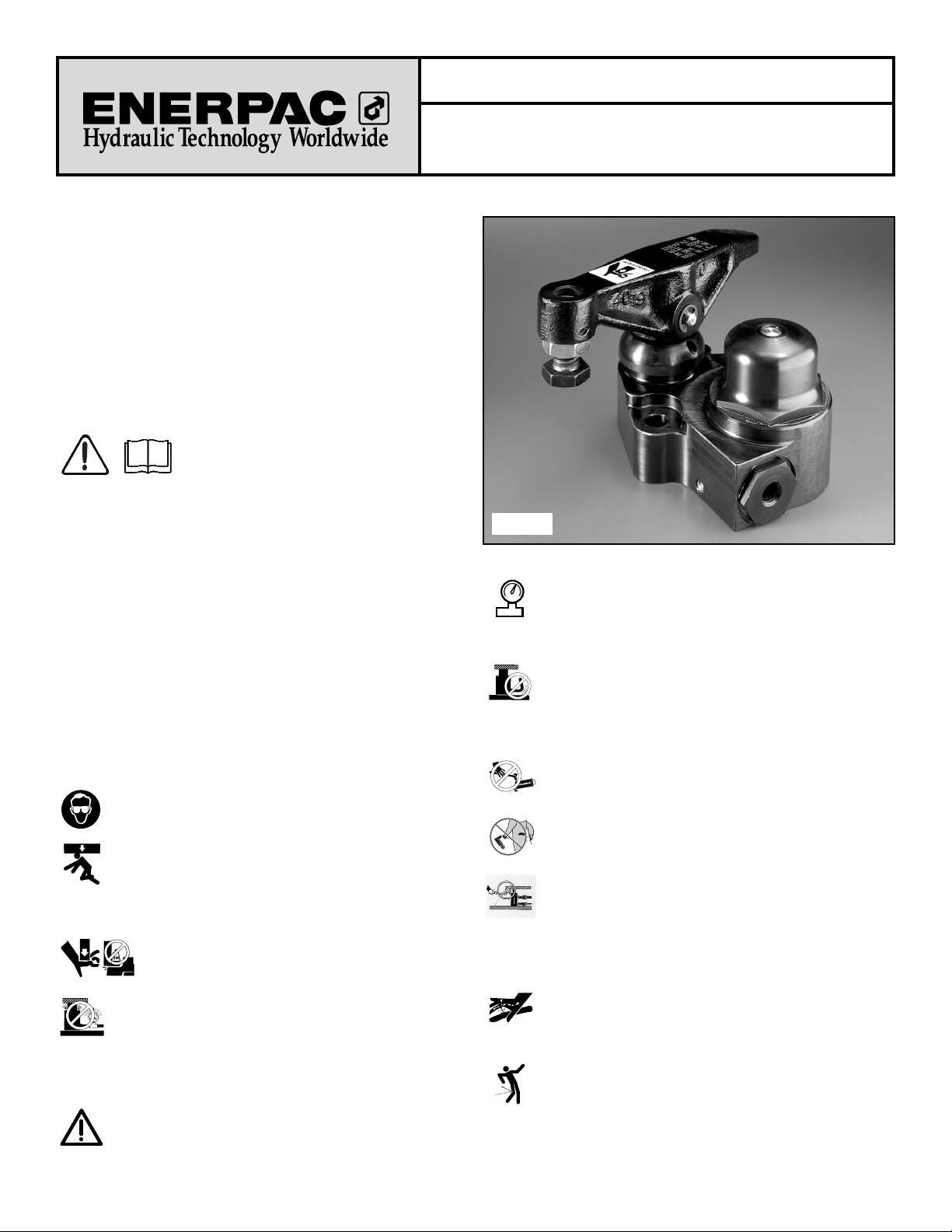
Repair Parts Sheets for this product are available from the Enerpac
web site at www.enerpac.com, or from your nearest Authorized
Enerpac Service Center or Enerpac Sales office.
1.0 IMPORTANT RECEIVING INSTRUCTIONS
Visually inspect all components for shipping damage. Shipping
damage is not covered by warranty. If shipping damage is found,
notify carrier at once. The carrier is responsible for all repair and
replacement costs resulting from damage in shipment.
SAFETY FIRST
2.0 SAFETY ISSUES
Read all instructions, warnings and cautions
carefully. Follow all safety precautions to
avoid personal injury or property damage
during system operation. Enerpac cannot be responsible for
damage or injury resulting from unsafe product use, lack of
maintenance or incorrect product and/or system operation.
Contact Enerpac when in doubt as to the safety precautions and
operations. If you have never been trained on high-pressure
hydraulic safety, consult your distribution or service center for a
free Enerpac Hydraulic safety course.
Failure to comply with the following cautions and warnings could
cause equipment damage and personal injury.
A CAUTION is used to indicate correct operating or maintenance
procedures and practices to prevent damage to, or destruction of
equipment or other property.
A WARNING indicates a potential danger that requires correct
procedures or practices to avoid personal injury.
A DANGER is only used when your action or lack of action may
cause serious injury or even death.
WARNING: Wear proper personal protective gear when
operating hydraulic equipment.
WARNING: Stay clear of loads supported by
hydraulics. A cylinder, when used as a load lifting device,
should never be used as a load holding device. After the
load has been raised or lowered, it must always be blocked
mechanically.
DANGER: To avoid personal injury keep hands and
feet away from cylinder and workpiece during
operation.
WARNING: Do not exceed equipment ratings. Never
attempt to lift a load weighing more than the capacity of
the cylinder. Overloading causes equipment failure and
possible personal injury. The cylinders are designed for a max.
pressure of 350 bar [5,000 psi]. Do not connect a jack or cylinder
to a pump with a higher pressure rating.
Never set the relief valve to a higher pressure than the
maximum rated pressure of the pump. Higher settings
may result in equipment damage and/or personal injury.
WARNING: The system operating pressure must not
exceed the pressure rating of the lowest rated component
in the system. Install pressure gauges in the system to
monitor operating pressure. It is your window to what is
happening in the system.
CAUTION: Avoid damaging hydraulic hose. Avoid sharp
bends and kinks when routing hydraulic hoses. Using a
bent or kinked hose will cause severe back-pressure.
Sharp bends and kinks will internally damage the hose leading to
premature hose failure.
Do not drop heavy objects on hose. A sharp impact may
cause internal damage to hose wire strands. Applying
pressure to a damaged hose may cause it to rupture.
IMPORTANT: Do not lift hydraulic equipment by the
hoses or swivel couplers. Use the carrying handle or other
means of safe transport.
CAUTION: Keep hydraulic equipment away from
flames and heat. Excessive heat will soften packings and
seals, resulting in fluid leaks. Heat also weakens hose
materials and packings. For optimum performance do not expose
equipment to temperatures of 65 °C [150 °F] or higher. Protect
hoses and cylinders from weld spatter.
DANGER: Do not handle pressurized hoses. Escaping
oil under pressure can penetrate the skin, causing serious
injury. If oil is injected under the skin, see a doctor
immediately.
WARNING: Only use hydraulic cylinders in a coupled
system. Never use a cylinder with unconnected couplers. If
the cylinder becomes extremely overloaded, components
can fail catastrophically causing severe personal injury.
Instruction Sheet
ASC-30 / ASC-100
Swing Clamps
L1678 Rev. O 03/03
ASC-30
®
®
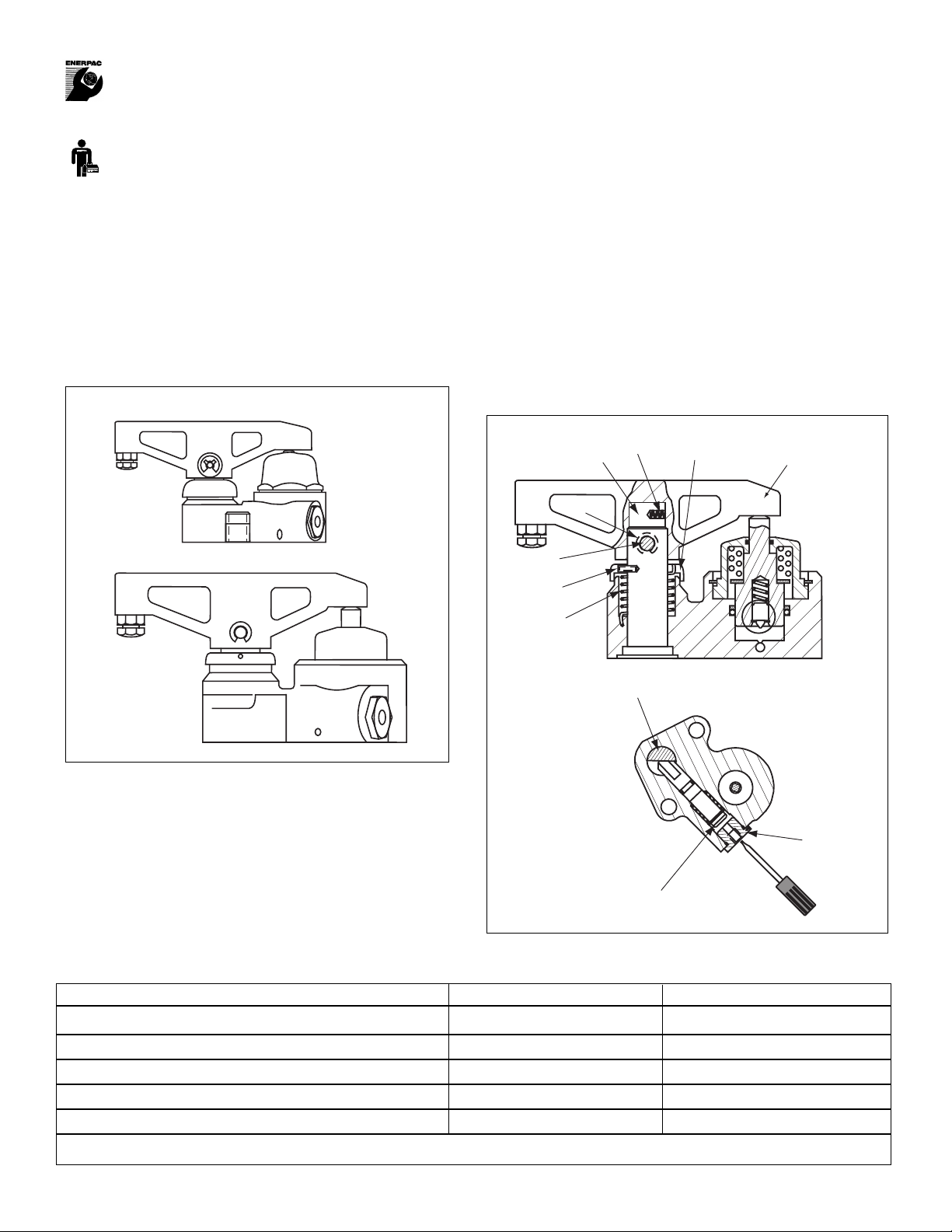
2
IMPORTANT: Hydraulic equipment must only be
serviced by a qualified hydraulic technician. For repair
service, contact the Authorized ENERPAC Service Center
in your area. To protect your warranty, use only ENERPAC oil.
WARNING: Immediately replace worn or damaged parts by
genuine ENERPAC parts. Standard grade parts will break
causing personal injury and property damage. ENERPAC
parts are designed to fit properly and withstand high loads.
3.0 DESCRIPTION
Enerpac ASC Swing Clamps have a clamping arm that swings in
a clockwise (R.H.) rotation 97° to position itself over the
workpiece. Then, a vertical plunger exerts an upward thrust on the
back end of the swing arm providing a powerful downward
pressure to clamp the workpiece. Swing clamp arm direction can
be changed to counter-clockwise (L.H.) rotation. See section 4.1.
Figure 1
4.0 INSTALLATION
4.1 Changing Rotation Direction
All Enerpac ASC Swing Clamps are assembled to swing
clockwise (R.H.). Follow instructions below to change rotation to
counter-clockwise (L.H.) and refer to Figure 2.
1. Remove retaining ring (1) and fulcrum pin (2) and lift off
clamping arm (3).
2. Remove arm spring (4). Mark the position of the spring on the
fulcrum (5).
3. Unscrew set screw (6) and remove cover (7).
4. Remove R.H. torsion spring (8) and replace with L.H. torsion
spring (supplied with cylinder).
5. Replace cover (7) making sure the top tongue of the torsion
spring (8) locates in the hole in the cover.
6. Turn cover (7) counter-clockwise 90° to load spring (8).
7. Tighten set screw (6) making sure the point engages the hole
in the swivel fulcrum (5).
8. Loosen inlet plug three turns (9). Insert a screwdriver through
the inlet bushing (9) and rotate the plunger (10) 180°.
9. Retighten inlet plug (9).
10. Use screwdriver to push plunger (10) to bottom to rotate the
swivel fulcrum (5) and check for proper rotation direction.
11. Replace arm spring (4) in clamping hole at 90° from original
position.
12. Place clamping arm (3) in opposite "at rest" position.
13. Insert fulcrum pin (2) and replace retaining ring (1).
Figure 2
Specifications ASC-30 ASC-100
Rated capacity (lbs.) 1,375 4,375
Rated operating pressure (psi) 1,200 to 2,500 max. 1,200 to 2,500 max.
Hydraulic port 0.125-27 NPT 0.125-27 NPT
Hydraulic Plunger Stroke (in) 0.25 0.43
Clamping volt length (in) 0.75 min.* 0.73 min.*
* Clamping bolt length can be changed to accommodate lower clamping height.
ASC-30
ASC-100
2
6
8
Top View
4
5
1
5
10
7
3
9
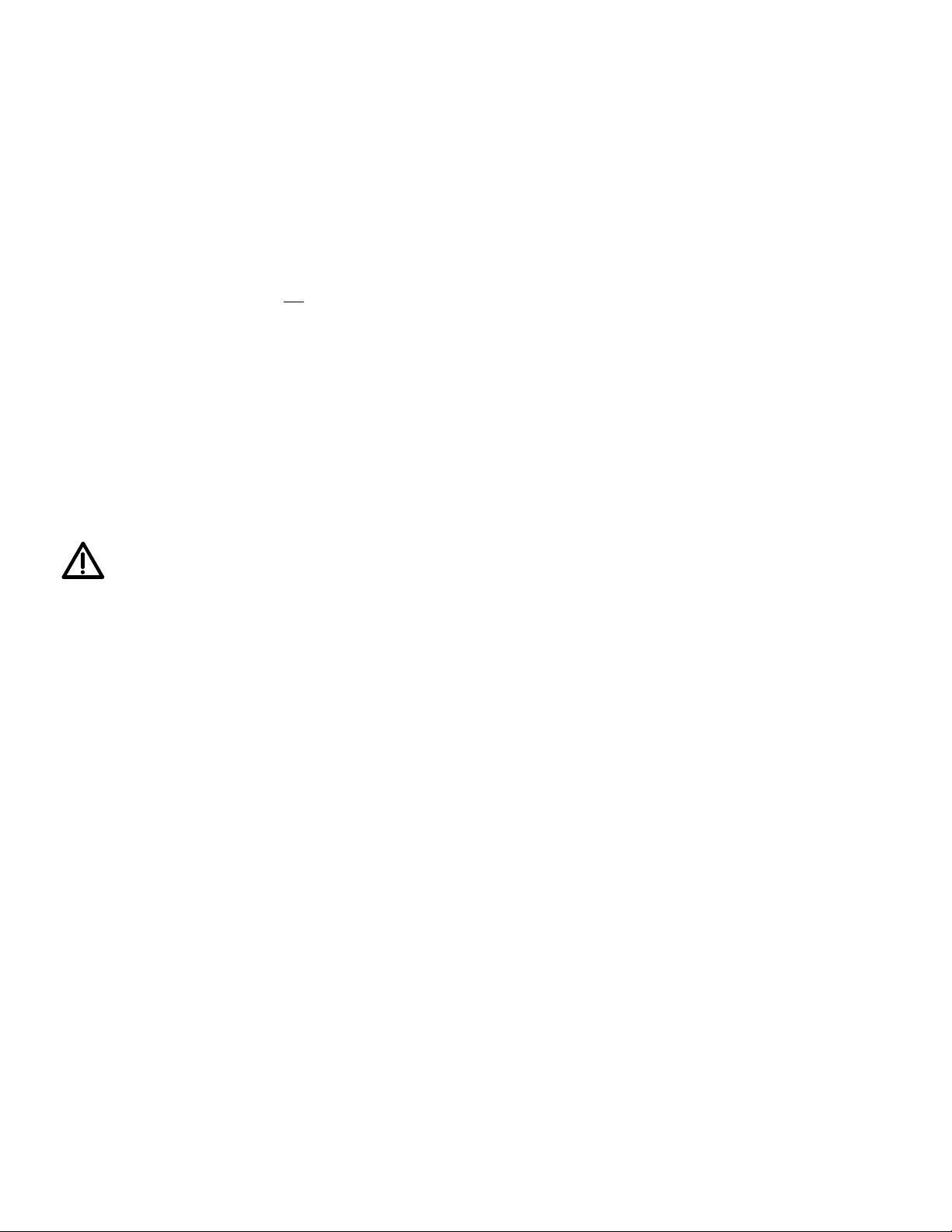
3
4.2 Changing Clamping Bolt
1. To replace clamping bolt, loosen jam nut and unscrew bolt
from clamping arm.
2. Replace with new bolt or toggle pad having 1/2-13 UNC 2A
threads.
3. Tighten jam nut.
4.3 Mounting the Swing Cylinder
Mount cylinder to fixture using two bolts. Attach hydraulic supply
line to hydraulic pressure port.
NOTE: Avoid contaminants in your hydraulic system. Tubing
should be flushed prior to assembly. Solvent may be used as long
as each piece is dry prior to assembly. After system has been
assembled, flush with hydraulic oil – not
solvent. Solvents can and
will cause premature seal failure.
5.0 OPERATION
Trapped air will result in erratic swing clamp operation. Remove
air from system for smooth operation.
1. Apply low hydraulic pressure to system (approximately 5 to
10 psi).
2. Loosen the attachment fitting at pressure port.
3. Tighten fitting after air is expelled and only hydraulic fluid is
expelled from fitting.
4. Swing clamp can new be operated up to full rated pressure
of 2,500 psi.
Never exceed 2,500 psi hydraulic pressure or rated
load capacity. Exceeding the rated limits of your
swing clamp will result in personal injury and/or
equipment damage.
6.0 MAINTENANCE
Perform maintenance regularly to keep swing clamps in good
operating condition.
1. Keep all moving parts free of debris and coolant. Coolant
may damage seals.
2. Keep system full of Enerpac hydraulic oil. Be sure cylinders
are fully retracted when adding oil to system. Use of other
fluids in not recommended. Other fluids may damage seals
and void the warranty.
3. Check that fittings and mountings are tight. Loose fittings
permit dirt to enter your system as well as allowing oil to leak
out. Loose mountings can cause damage to parts or fixtures.
4. Check for oil leaking from swing clamp. Leaks are usually
caused by damaged or worn seals. Seals are available in the
Repair Parts Kit for your swing clamp.
5. Refer to Repair Parts Sheet L1679 to order parts and perform
service work.
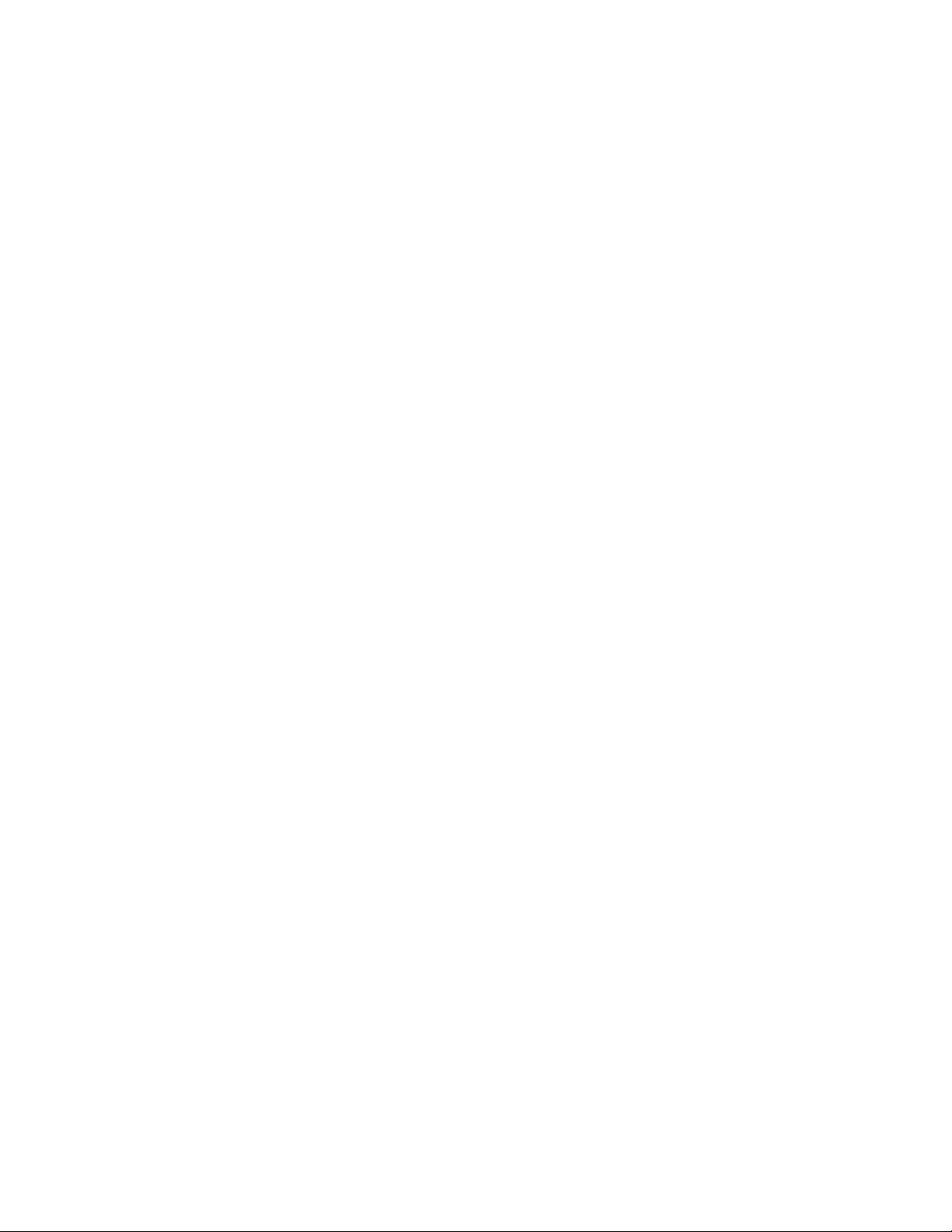
✦
Enerpac Worldwide Locations
Australia
ENERPAC, Applied Power
Australia Ltd.
Block V Unit 3
Regents Park Estate
391 Park Road
Regents Park NSW 2143
(P.O. Box 261) Australia
Tel: +61 297 438 988
Fax: +61 297 438 648
Brazil
Power Packer do Brasil Ltda.
Rua dos Inocentes, 587
04764-050 - Sao Paulo (SP)
Tel: +55 11 5687 2211
Fax: +55 11 5686 5583
Toll Free in Brazil:
Tel: 000 817 200 6718
vendasbrasil@enerpac.com
Canada
Actuant Canada Corporation
6615 Ordan Drive, Unit 14-15
Mississauga, Ontario L5T 1X2
Tel: +1 905 564 5749
Fax: +1 905 564 0305
Toll Free:
Tel: +1 800 268 4987
Fax: +1 800 461 2456
Technical Inquiries:
techservices@enerpac.com
China
Actuant China Ltd.
1F, 269 Fute N. Road
Waigaoqiao Free Trade Zone
Pudong New District
Shanghai, 200 131 China
Tel: +86 21 5866 9099
Fax: +86 21 5866 7156
Actuant China Ltd. (Beijing)
709A Xin No. 2
Diyang Building
Dong San Huan North Rd.
Beijing City, 100028 China
Tel: +86 10 845 36166
Fax: +86 10 845 36220
Eastern Europe
Applied Power International S.A.
Case postale 130
CH-1213 Onex-Genéva
Switzerland
Tel: +49 (211) 47149 44
Fax: +49 (211) 47149 40
France, Greece, Africa
ENERPAC S.A.
B.P. 200
Parc d’Activités
du Moulin de Massy
F-91882 Massy CEDEX
(Paris) France
Tel: +33 1 601 368 68
Fax: +33 1 692 037 50
Germany, Austria
ENERPAC
Applied Power GmbH
P. O. Box 300113
D-40401 Düsseldorf
Germany
Tel: +49 211 471 490
Fax: +49 211 471 49 28
India
ENERPAC Hydraulics
(India) Pvt. Ltd.
Plot No. A/571
MIDC, TTC Industrial Area
Mahape-400 701
Navi Mumbai, India
Tel: +91 22 778 1779
Fax: +91 22 778 1473
Italy
ENERPAC
Applied Power Italiana S.p.A.
Via Canova 4
20094 Corsico (Milano)
Tel: +39 02 4861 111
Fax: +39 02 4860 1288
Japan
Applied Power Japan Ltd.
1-1-11, Shimomae
Toda-shi
Saitama Pref.
Japan 335-0016
Tel: +81 48 430 2311
Fax: +81 48 430 1117
e-mail: info@enerpac.com
Mexico
ENERPAC Applied Power
Mexico S. de R.L. de C.V.
Avenida Principal
La Paz #100
Fracc. Industrial La Paz
42092 Pachuca, Hidalgo
Tel: +52 771 71851 60
+52 771 71870 22
Fax: +52 771 71352 32
Toll Free in Mexico:
Tel: 001 800 590 0130
The Netherlands, Belgium, Luxembourg,
Sweden, Denmark, Norway, Finland
ENERPAC B.V.
Storkstraat 25
P. O. Box 269, 3900 AG Veenendaal
The Netherlands
Tel: +31 318 535 911
Fax: +31 318 525 613
+31 318 535 848
Russia and CIS
(excl. Caspian Sea Countries)
ENERPAC
Leninsky Prospect 95A
117313, Moscow, Russia.
Tel/Fax: +7(095) 936-2005
Tel/Fax: +7(095) 198-3094
Tel/Fax: +7(095) 938-4655
Mobil: +7(903) 731-9558
Singapore
Actuant Asia Pte. Ltd.
25 Serangoon North Ave. 5
#03-01 Keppel Digihub
Singapore 554914
Thomson Road
P. O . Box 114
Singapore 915704
Tel: +65 64 84 5108
+65 64 84 3737
Fax: +65 64 84 5669
South Korea
ENERPAC
Applied Power Korea Ltd.
163-12 Dodang-Dong
Wonmi-Ku, Buchun-shi
Kyunggi-Do
Republic of Korea
Tel: +82 32 675 08 36
Fax: +82 32 675 30 02/73
All Enerpac products are guaranteed against defects in workmanship and materials for as long as you own them.
For your nearest authorized Enerpac Service Center, visit us at www.enerpac.com
✦
internet: www.enerpac.com
Spain, Portugal
ENERPAC
C/San JoséArtesano 8
Pol. Ind.
28108 Alcobendas
(Madrid) Spain
Tel: +34 91 661 11 25
Fax: +34 91 661 47 89
Middle East, Turkey
and Caspian Sea
ENERPAC Middle East FZE
P.O. Box 18004
Jebel Ali, Dubai
United Arab Emirates
Tel: +971 (0)4 8872686
Fax: +971 (0)4 8872687
United Kingdom, Ireland
ENERPAC Ltd., P.O. Box 33
New Romney, TN28 8QF
United Kingdom
Tel: +44 01527 598 900
Fax: +44 01527 585 900
USA, Latin America
and Caribbean
ENERPAC
P. O. Box 3241
6100 N. Baker Road
Milwaukee, WI 53209 USA
Tel: +1 262 781 6600
Fax: +1 262 783 9562
User inquiries:
+1 800 433 2766
Distributor inquiries/orders:
+1 800 558 0530
Technical Inquiries:
techservices@enerpac.com
10/30/02