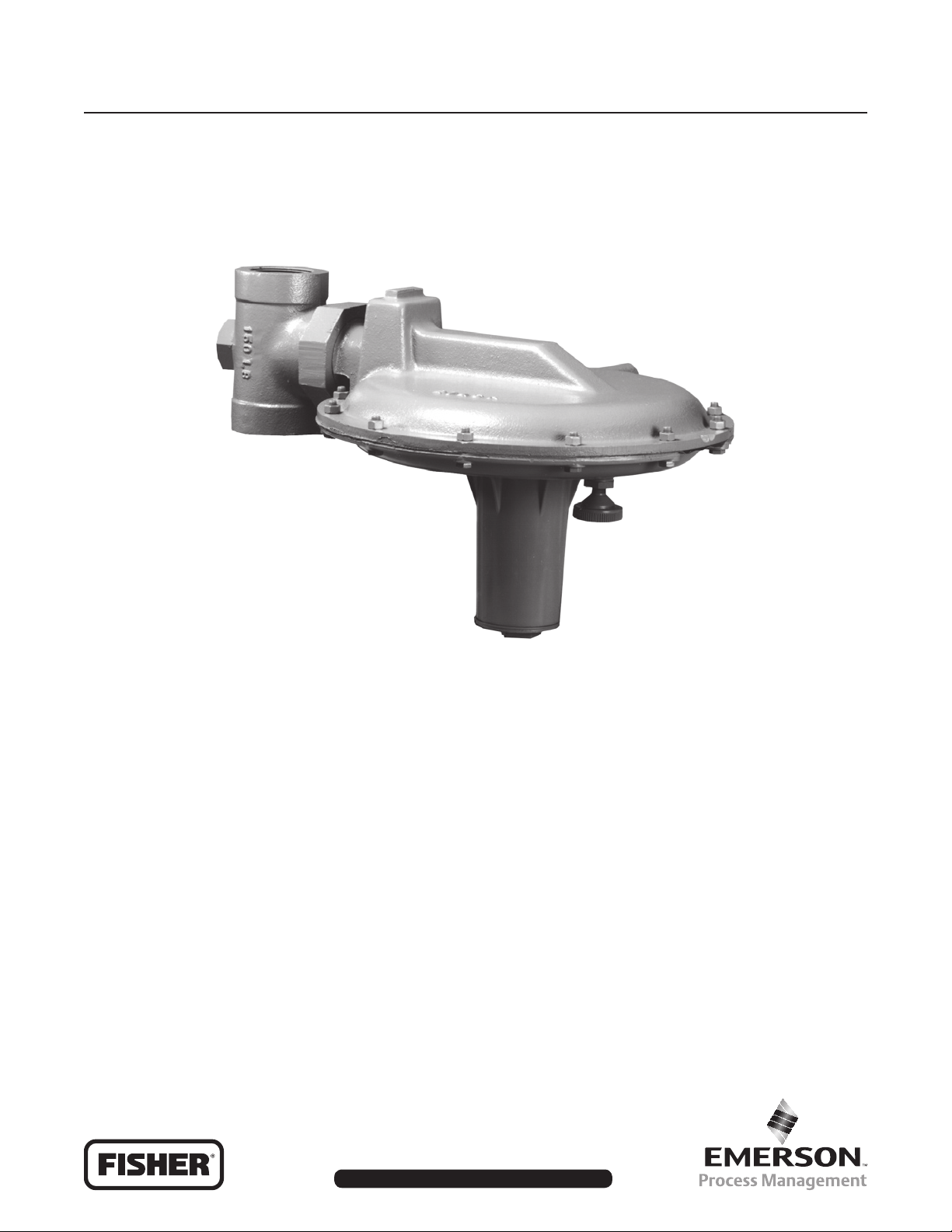
Instruction Manual
Form 5312
January 2009
Type Y696 Vapor Recovery Regulator
Type Y696
W5996
Figure 1. Type Y696 Vapor Recovery Regulator
Introduction
Scope of Manual
This instruction manual includes installation, startup,
maintenance, and parts information for the Type Y696
vapor recovery regulator.
Product Description
The Type Y696 vapor recovery regulator is a directoperated regulator with internal registration requiring
no downstream control line. It is used to sense
increase in vessel pressure and vent excessive
internal vessel pressure to an appropriate vapor
recovery disposal or reclamations system.
Specications
The Specications section lists maximum pressures,
temperatures, and other specications. Specications
for a given regulator as it originally comes from the
factory are stamped on the spring case nameplate.
Principle of Operation
The Type Y696 is used to maintain a constant inlet
(blanket) pressure with the outlet owing to a system
whose pressure is lower than that at the inlet.
When vessel pressure increases above the setpoint
of the regulator due to pumping in or thermal heating,
the force of the control spring is overcome by
www.emersonprocess.com/regulators
D101770X012
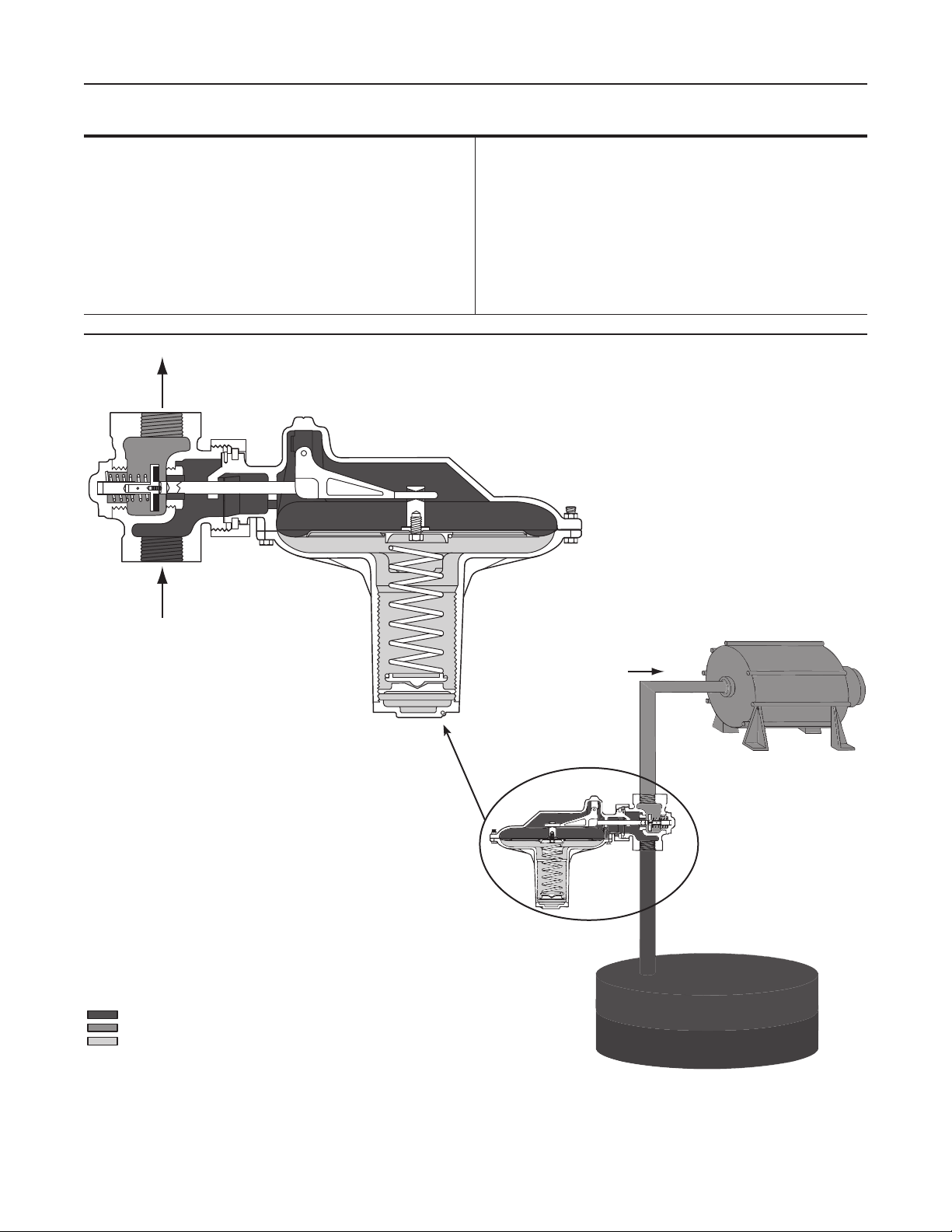
Type Y696
Specications
Body Size and End Connection Style
See Table 1
Maximum Allowable Inlet and Outlet Pressure
15 psig (1,0 bar)
Control Pressure Ranges
See Table 2
1. The pressure/temperature limits in this instruction manual or any applicable standard limitation should not be exceeded.
(1)
Pressure Registration
Internal
(2)
Spring Case and Vent Connections
1/4-inch NPT
Maximum Temperature Capabilities
Nitrile (NBR): -20° to 180°F (-29° to 82°C)
Fluorocarbon (FKM): 0° to 300°F (-18° to 149°C)
(2)
INLET PRESSURE
OUTLET PRESSURE
ATMOSPHERIC PRESSURE
M1058
Figure 2. Type Y696 Vapor Recovery Operational Schematic
VAPOR PRESSURE
LIQUID
VAPOR RECOVERY
VACUUM SOURCE
2
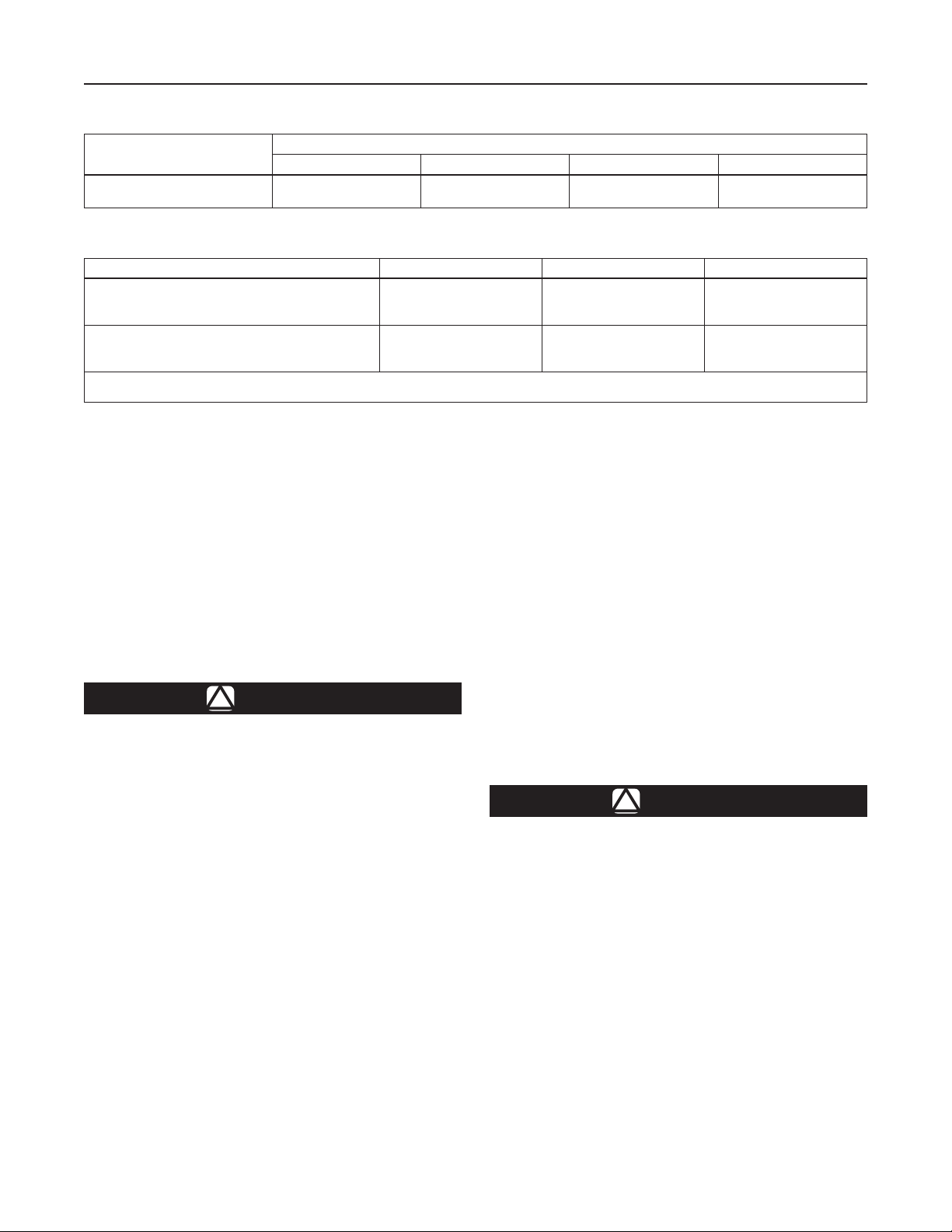
Table 1. Body Sizes and End Connection Styles
Type Y696
BODY SIZE,
INCHES (DN)
1-1/2 and 2 (40 and 50) NPT
CONTROL PRESSURE RANGE SPRING PART NUMBER SPRING COLOR WIRE DIAMETER
2 to 5-inches w.c.
5 to 15-inches w.c.
0.3 to 1 psig
1 to 2.8 psig
2 to 3.5 psig
4 to 7 psig
1. Spring ranges based on spring case installed pointed down. When installed pointed up, spring range increases 2-inches w.c. (5 mbar).
2. Do not use Fluorocarbon (FKM) diaphragm with these springs at diaphragm temperatures lower than 60°F (16°C).
(5 to 12 mbar)
(12 to 37 mbar)
(0,02 to 0,07 bar)
(0,07 to 0,19 bar)
(0,14 to 0,24 bar)
(0,28 to 0,48 bar)
Cast Iron Steel Stainless Steel Hastelloy® C
NPT, SWE, CL150 RF,
CL300, PN 16/25/40
Table 2. Control Pressure Ranges
(1)(2)
(1)(2)
1A200127022
1B577727062
0B019427052
0A081127202
0Y066427022
1H8024000A2
pressure acting on the diaphragm. This moves the
disk away from the orice allowing gas to ow from
the vessel to the vapor recovery system.
As vessel pressure is reduced, the force of the
control spring causes the disk to move toward the
orice decreasing the ow of gas out of the vessel.
As vessel pressure drops below the setpoint of the
regulator, the disk will seat against the orice shutting
off the ow of gas.
BODY MATERIAL
NPT, SWE, CL150 RF,
CL300, PN 16/25/40
Red
Gray
Green
Orange
Green stripe
Silver
1. Use qualied personnel when installing, operating,
and maintaining the regulator. Before installing,
inspect the regulator for any shipment damage or
foreign material that may have collected during
crating and shipment. Make certain the body
interior is clean and the pipelines are free of
foreign material. Apply pipe compound only to the
male pipe threads.
2. Install the regulator using a straight run of pipe the
same size or larger as the regulator body (as
shown in Figure 2). Flow through the regulator
Installation
body is indicated by the ow arrow cast on the
body. If a block valve is required, install a full
WARNING
!
ow valve between the regulator and the
blanketed vessel. For proper operation, the
regulator should be installed with the spring case
Personal injury, equipment damage, or
leakage due to escaping accumulated gas
barrel pointed down. Key numbers referenced in
this section are shown in Figure 3.
or bursting of pressure-containing parts
may result if the vapor recovery regulator
!
is overpressured or installed where
service conditions could exceed the limits
given in the Specications section, or
where conditions exceed any ratings of
the adjacent piping or piping connections.
To avoid such injury or damage, provide
pressure-relieving or pressure-limiting
devices to prevent service conditions from
exceeding those limits.
Additionally, physical damage to the
vapor recovery regulator could result
in personal injury and property damage
due to escaping accumulated gas. To
avoid such injury and damage, install
the vapor recovery regulator in a safe
and well ventilated location.
A regulator may vent some gas to
the atmosphere. In hazardous or
ammable gas service, vented gas may
accumulate, and cause personal injury,
death, or property damage due to re or
explosion. Vent a regulator in hazardous
gas service to a remote, safe location
away from air intakes or any hazardous
location. The vent line or stack opening
must be protected against condensation
or clogging.
3. To keep the spring case vent from being plugged
or the spring case from collecting moisture,
corrosive chemicals, or other foreign material,
point the vent down or otherwise protect it.
CL150 RF
0.135-inches (3,43 mm)
0.156-inches (3,96 mm)
0.187-inches (4,75 mm)
0.250-inches (6,35 mm)
0.363-inches (9,22 mm)
0.406-inches (10,3 mm)
WARNING
3