
Installation Instructions
Electro_ux Front_Load Gas _ E_ectric Dryer
Instructions d'installation
S_cheuse _ gaz et _ P4Jectridt4 _ chargement fTontal E]ectrolux
lnstrucciones de |nstalaci6n
Secadora d4ctr_ca y _ gas de carga frontaJ EJec_'oJux
137396000A(lolo)
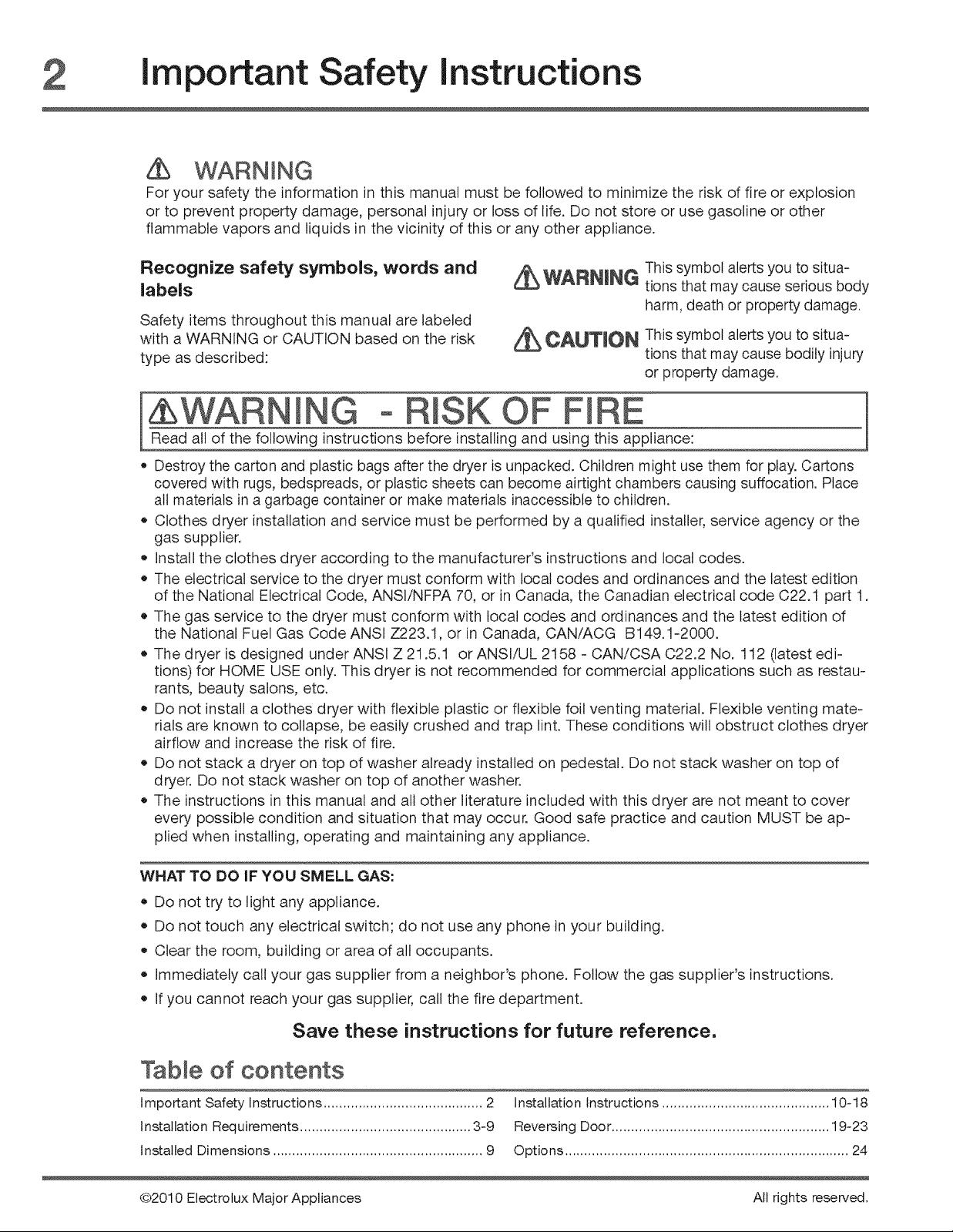
2 important Safety Instructions
For your safety the information in this manual must be followed to minimize the risk of fire or explosion
or to prevent property damage, personal injury or loss of life. Do not store or use gasoline or other
flammable vapors and liquids in the vicinity of this or any other appliance.
Recognize safety symbols, words and
labels
Safety items throughout this manual are labeled
with a WARNING or CAUTION based on the risk
type as described:
_VA_N|NG tions that may cause serious body
CAUTION This symbol alerts you to situa-
This symbol alerts you to situa-
harm death or property damage.
tions that may cause bodily injury
or property damage.
I G - IS OF F!
Read all of the following instructions before installing and using this appliance:
• Destroy the carton and plastic bags after the dryer is unpacked. Children might use them for play. Cartons
covered with rugs, bedspreads, or plastic sheets can become airtight chambers causing suffocation. Place
all materials in agarbage container or make materials inaccessible to children.
o Clothes dryer installation and service must be performed by a qualified installer, service agency or the
gas supplier.
• Install the clothes dryer according to the manufacturer's instructions and local codes.
• The electrical service to the dryer must conform with local codes and ordinances and the latest edition
of the National Electrical Code, ANSI/NFPA 70, or in Canada, the Canadian electrical code C22.1 part t.
• The gas service to the dryer must conform with local codes and ordinances and the latest edition of
the National Fuel Gas Code ANSI Z223.1, or in Canada, CAN/ACG B149.1-2000.
• The dryer is designed under ANSI Z 21.5.1 or ANSI/UL 2158 - CAN/CSA C22.2 No. 112 (latest edi-
tions) for HOME USE only. This dryer is not recommended for commercial applications such as restau-
rants, beauty salons, etc.
o Do not install a clothes dryer with flexible plastic or flexible foil venting material. Flexible venting mate-
rials are known to collapse, be easily crushed and trap lint. These conditions will obstruct clothes dryer
airflow and increase the risk of fire.
O
Do not stack a dryer on top of washer already installed on pedestal. Do not stack washer on top of
dryer. Do not stack washer on top of another washer.
o
The instructions in this manual and all other literature included with this dryer are not meant to cover
every possible condition and situation that may occur. Good safe practice and caution MUST be ap=
plied when installing, operating and maintaining any appliance.
WHAT TO DO IF YOU SMELL GAS:
Do not try to light any appliance.
,, Do not touch any electrical switch; do not use any phone in your building.
,, Clear the room, building or area of all occupants.
• Immediately call your gas supplier from a neighbor's phone. Follow the gas supplier's instructions.
If you cannot reach your gas supplier, call the fire department.
Save these instructions for future reference.
Table of contents
Important Safety Instructions ......................................... 2
Installation Requirements ............................................ 3-9
Installed Dimensions ...................................................... 9
O2010 Electrotux Major Appliances All rights reserved,
Installation Instructions ........................................... 10-18
Reversing Door ........................................................ 19-23
Options ......................................................................... 24

Installation Requirements 3
Please read and save this guide
Thank you for choosing Eiectrolux, the new
premium brand in home appliances. These
Installation Instructions are part of our commitment
to customer satisfaction and product quality
throughout the life of your new appliance.
lnstaJmation Checklist
Exhaust Venting
[] Free-flowing, clear of lint buildup
[] 4 inch (102 mm) rigid or semi=rigid ducting
of minimal length and turns
[] NO foil or plastic venting material
[] Approved vent hood exhausted to outdoors
Leveling
r] Dryer is level, side-to-side and front-to-back
[] Cabinet is setting solid on all corners
Gas Supply (Gas Dryer)
I_1 Manual shutoff valve present in supply
[] All connections sealed with approved sealer
and wrench tight
[] Conversion kit for LP system
r] Gas supply turned on
[] No leaks present at all connections -
check with soapy water, NEVER check with
flame
For toll-free telephone support in the U.S. and
Canada: 1-877-4ELECTROLUX (1-877-435-3287).
For online support and product information visit
http:/iwww.electroluxappliances.com.
240v Electric Supply (Electric Dryer)
[] Approved NEMA 10-30R or 14-30R service
cord with all screws tight on terminal block
[] Approved strain relief installed
[] Terminal access cover installed before initial
operation
Door Reversal
[] Follow detailed instructions in this guide
Cl Test hinge and latch for function
Electrical Power
[] House power turned on
[] Dryer plugged in
Final Checks
[] Installation Instructions and Use and Care
Guide read thoroughly
[] Door latches and drum tumbles when cycle
starts
[] Registration card sent in
Pre4nstaHation requirements
Tools and materials needed for installation:
tt_5_ "
,¢ ,% -¢
Adjustak le Phillips, straight, & Adjustable
pliers square bit screwdrivers wrenc, h
4 inch, rigid metal or
semi-rigid metal exhaust duct work
Universal wrench Pipewrench LP-resJstant Carpenter's bvel
supplied with for gas thread tape
matching washer supply (for natural gas _
240volt cord kit (10.2 ore) shutoff valve flexible gas supply line
(electric dryer) clamp (gas dryer) (gas dryer)
ar
External
vent hood
or LP supply) _Et
_ Y/' NPT union flare
or 4-wire 4 in. gas line adapters (x2) and
Metal foil tape
(net duct tape)
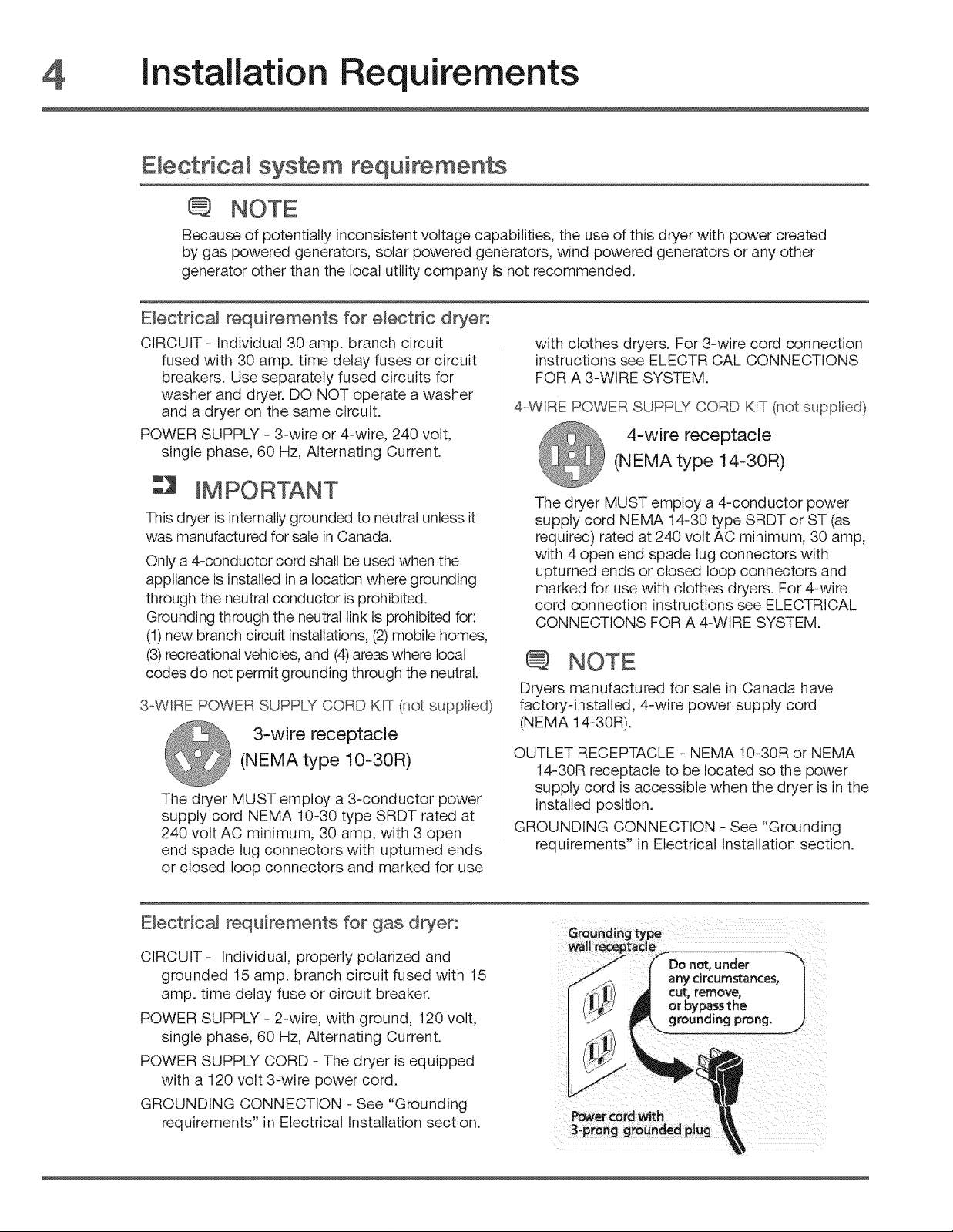
4 Installation Requirements
Electrical system requirements
NOTE
Because of potentially inconsistent voltage capabilities, the use of this dryer with power created
by gas powered generators, solar powered generators, wind powered generators or any other
generator other than the local utility company is not recommended.
Electrical requirements for electric d_er:
CIRCUIT- Individual 30 amp. branch circuit
fused with 30 amp. time delay fuses or circuit
breakers. Use separately fused circuits for
washer and dryer. DO NOT operate a washer
and a dryer on the same circuit.
POWER SUPPLY - 3-wire or 4-wire, 240 volt,
single phase, 60 Hz, Alternating Current.
4-WIRE POWER SUPPLY CORD KIT (not supplied)
with clothes dryers. For 3-wire cord connection
instructions see ELECTRICAL CONNECTIONS
FOR A 3-WIRE SYSTEM.
4-wire receptacle
(NEMA type 14-30R)
iMPORTANT
This dryer is internally grounded to neutral unless it
was manufactured for sale in Canada.
Only a 4-conductor cord shall be used when the
appliance is installed in a location where grounding
through the neutral conductor is prohibited.
Grounding through the neutral link is prohibited for:
(1)new branch circuit installations, (2) mobile homes,
(3)recreational vehicles, and (4)areas where local
codes do not permit grounding through the neutral.
3-WIRE POWER SUPPLY CORD KiT (not supplied)
3-wire receptacle
(NEMA type 10-30R)
The dryer MUST employ a 3-conductor power
supply cord NEMA 10-30 type SRDT rated at
240 volt AC minimum, 30 amp, with 3 open
end spade tug connectors with upturned ends
or closed loop connectors and marked for use
Electrical requirements for gas dryer:
The dryer MUST employ a 4-conductor power
supply cord NEMA 14-30 type SRDT or ST (as
required) rated at 240 volt AC minimum, 30 amp,
with 4 open end spade lug connectors with
upturned ends or closed loop connectors and
marked for use with clothes dryers. For 4-wire
cord connection instructions see ELECTRICAL
CONNECTIONS FOR A 4-WIRE SYSTEM.
NOTE
Dryers manufactured for sale in Canada have
factory-installed, 4-wire power supply cord
(NEMA 14-30R).
OUTLET RECEPTACLE - NEMA 10-30R or NEMA
14-30R receptacle to be located so the power
supply cord is accessible when the dryer is in the
installed position.
GROUNDING CONNECTION - See "Grounding
requirements" in Electrical Installation section.
CIRCUIT- Individual, properly polarized and
grounded 15 amp. branch circuit fused with 15
amp. time delay fuse or circuit breaker.
POWER SUPPLY - 2-wire, with ground, 120 volt,
single phase, 60 Hz, Alternating Current.
POWER SUPPLY CORD - The dryer isequipped
with a 120 volt 3-wire power cord.
GROUNDING CONNECTION - See "Grounding
requirements" in Electrical Installation section.
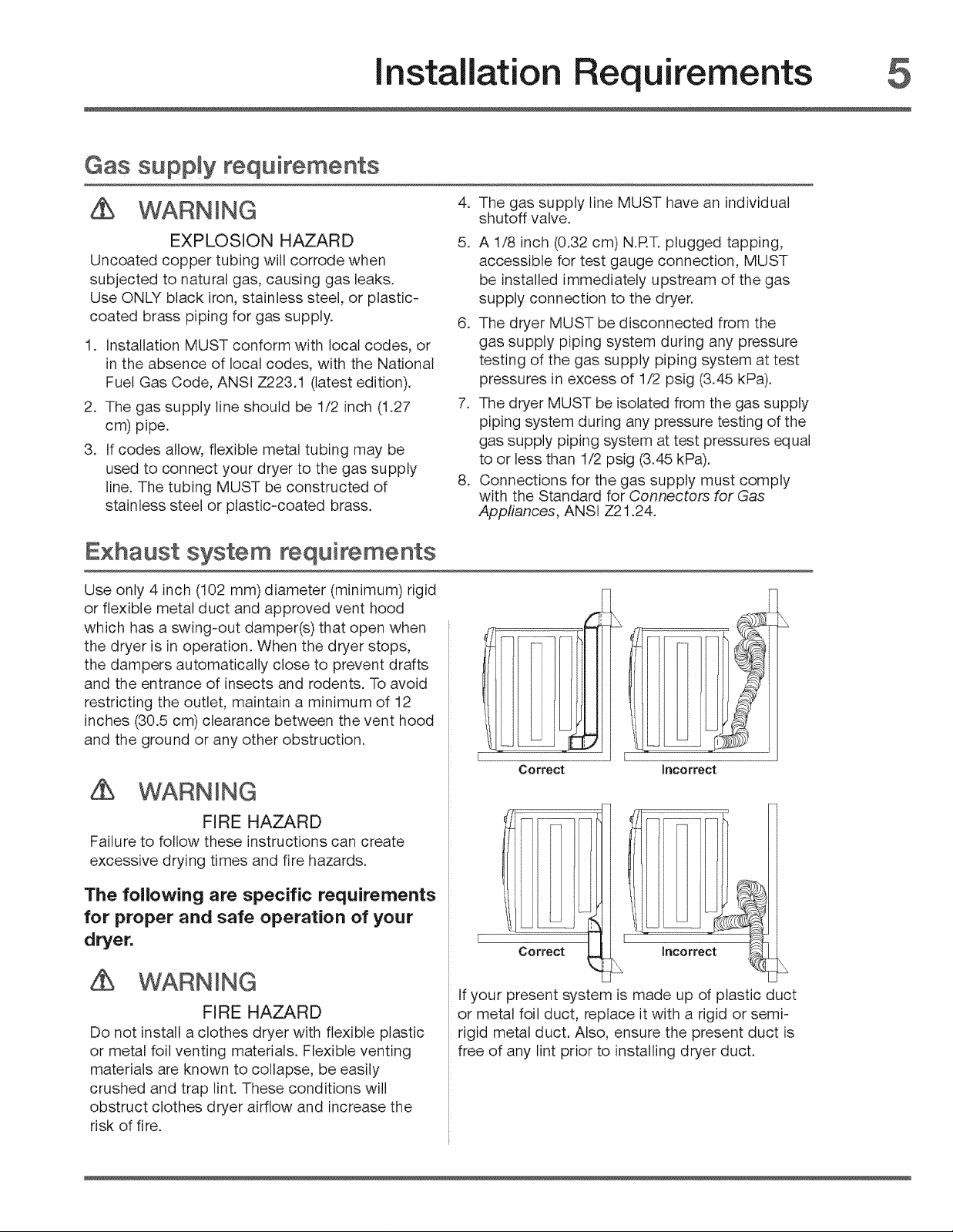
Gas suppJy requirements
Installation Requirements 5
WARNING 4.
EXPLOSION HAZARD 5.
Uncoated copper tubing will corrode when
subjected to natural gas, causing gas leaks.
Use ONLY black iron, stainless steel, or plastic-
coated brass piping for gas supply.
1. installation MUST conform with local codes, or
in the absence of Iocai codes, with the National
Fuel Gas Code, ANSI Z223.1 (latest edition).
2. The gas supply line should be 1/2 inch (1.27
cm) pipe.
3. If codes allow, flexible metal tubing may be
used to connect your dryer to the gas supply
line. The tubing MUST be constructed of
stain less steel or plastic-coated brass.
Exhaust system requirements
Use only 4 inch (102 mm) diameter (minimum) rigid
or flexible metal duct and approved vent hood
which has a swing-out damper(s) that open when
the dryer is in operation. When the dryer stops,
the dampers automatically close to prevent drafts
and the entrance of insects and rodents. To avoid
restricting the outlet, maintain a minimum of 12
inches (30.5 cm) clearance between the vent hood
and the ground or any other obstruction.
WARNING
The gas supply line MUST have an individual
shutoff valve.
A 1/8 inch (0.32 cm) N.RT. plugged tapping,
accessible for test gauge connection, MUST
be installed immediately upstream of the gas
supply connection to the dryer.
6. The dryer MUST be disconnected from the
gas supply piping system during any pressure
testing of the gas supply piping system at test
pressures in excess of 1/2 psig (3.45 kPa).
7. The dryer MUST be isolated from the gas supply
piping system during any pressure testing of the
gas supply piping system at test pressures equal
to or less than 1/2 psig (3.45 kPa).
8. Connections for the gas supply must comply
with the Standard for Connectors for Gas
Appliances, ANSI Z21.24.
Correct Incorrect
FIRE HAZARD
Failure to follow these instructions can create
excessive drying times and fire hazards.
The following are specific requirements
for proper and safe operation of your
dryer.
WARNING
FIRE HAZARD
Do not install a clothes dryer with flexible plastic
or metal foil venting materials. Flexible venting
materials are known to collapse, be easily
crushed and trap lint. These conditions will
obstruct clothes dryer airflow and increase the
risk of fire.
Ill
Correct
If your present system is made up of plastic duct
or metal foil duct, replace it with a rigid or semi-
rigid metal duct. Also, ensure the present duct is
free of any tint prior to installing dryer duct.

6 Installation Requirements
Exhaust system requirements, continued
WARNING
FIRE HAZARD
A clothes dryer must be exhausted outdoors.
Do not exhaust dryer into a chimney, a wall, a
ceiling, an attic, a crawl space or any concealed
space of a building. A clothes dryer produces
combustible tint. If the dryer is not exhausted
outdoors, some fine lint will be expelled into the
laundry area. An accumulation of lint in any area
of the home can create a health and fire hazard.
The dryer must be connected to an exhaust
outdoors. Regularly inspect the outdoor exhaust
opening and remove any accumulation of lint
around the outdoor exhaust opening and in the
surrounding area.
FIRE HAZARD
Do not allow combustible materials (for
example: clothing, draperies!curtains, paper)
to come in contact with exhaust system. The
dryer MUST NOT be exhausted into a chimney,
a wall, a ceiling, or any concealed space of a
building which can accumulate tint, resulting in
a fire hazard.
Do not screen the exhaust ends of the vent
system, or use any screws, rivets or other
fasteners that extend into the duct to assemble
the exhaust system. Lint can become caught
in the screen, on the screws or rivets, clogging
the duct work and creating a fire hazard as well
as increasing drying times. Use an approved
vent hood to terminate the duct outdoors, and
seal all joints with metal foil tape. All male duct
pipe fittings MUST be installed downstream
with the flow of air.
MAXIMUM LENGTH
Z
t-
3
ET
e.
of 4" (102mm) Rigid Metal Duct
VENT HOOD TYPE
(Preferred)
o
E_
4"
(10,2cm)
0 125 ft. (38.10m)
1 115 ft. (35.05m)
2 105 ft. (32.00m) 90 ft, (27A3m)
3 95 ft. (28.96m) 80 ft, (24.38m)
4 85 ft. (25.91 m) 70 ft. (21.34m)
Iouvered
2,5"
(6.35cm)
110 ft. (33.53m)
100 ft. (30.48m)
WARNING
FIRE HAZARD
Do not install flexible plastic or flexible foil
venting material.
• if installing semi-rigid venting, do not exceed 8
ft. (2.4 m) duct length.
Exhaust direction
Directional exhausting can be accomplished by
installing a quick-turn 90 ° dryer vent elbow directly
to exhaust outlet of dryer. Dryer vent elbow's are
available through your local parts distributor or
hardware store.
J
J
FIRE HAZARD
Exceeding the length of duct pipe or number
of elbows allowed in the "MAXIMUM LENGTH"
charts can cause an accumulation of lint in the
exhaust system. Plugging the system could
create a fire hazard, as well as increase drying
times.
See also CLEARANCE REQUIREMENTS on the
next page.
NOTE
Use of 90 ° quick-turn elbow required to meet
minimum installation depth.

Installation Requirements 7
Exhaust system requirements, continued
WARNING
EXPLOSION HAZARD
Do not install the dryer where gasoline or other
flammables are kept or stored. If the dryer is
installed in a garage, it must be a minimum of 18
inches (45.7 cm) above the floor. Failure to do so
can result in death, explosion, fire or burns.
In installations where the exhaust system is not
described in the charts, the following method must
be used to determine if the exhaust system is
acceptable:
1. Connect an inclined or digital manometer
between the dryer and the point the exhaust
connects to the dryer.
2. Set the dryer timer and temperature to air fluff
(coot down) and start the dryer.
3. Read the measurement on the manometer.
4. The system back pressure MUST NOT be
higher than 1.0 inch of water column. If the
system back pressure is less than 1.0 inch of
water column, the system is acceptable. If the
manometer reading is higher than 1.0 inch of
water column, the system is too restrictive and
the installation is unacceptable.
Install male fittings in correct direction:
CORRECT INCORRECT
Although vertical orientation of the exhaust system
is acceptable, certain extenuating circumstances
could affect the performance of the dryer:
Only the rigid metal duct work should be used.
,, Venting vertically through a roof may expose
the exhaust system to down drafts causing an
increase in vent restriction.
Running the exhaust system through an
uninsulated area may cause condensation and
faster accumulation of lint.
o Compression or crimping of the exhaust system
will cause an increase in vent restriction.
The exhaust system should be inspected and
cleaned a minimum of every 18 months with
normal usage. The more the dryer is used,
the more often you should check the exhaust
system and vent hood for proper operation.
Manufactured or mobile home installation
1. Installation MUST conform to current
Manufactured Home Construction & Safety
Standard, Title 24 CFR, Part 32-80 (formerly the
Federal Standard for Mobile Home Construction
and Safety, Title 24, HUD Part 280) or Standard
CAN/CSAZ240 MH.
2. Dryer MUST be exhausted outside (outdoors, not
beneath the mobile home) using metal ducting
that will not support combustion. Metal ducting
must be 4 inches (10.16 cm)in diameter with no
obstructions. Rigid metal duct is preferred.
3. If dryer is exhausted through the floor and
area beneath the mobile home is enclosed,
the exhaust system MUST terminate outside
the enclosure with the termination securely
fastened to the mobile home structure.
4. Refer to previous sections in this guide for other
important exhaust venting system requirements.
5. When installing a gas dryer into a mobile home,
a provision must be made for outside make up
air. This provision is to be not less than twice
the area of the dryer exhaust outlet.
6. Installer MUST anchor this (1) dryer or (2) dryer
mounted on pedestal to the floor with approved
Mobile Home Installation Kit - P/N 137067200.

Installation Requirements
iMPORTANT
DO NOT INSTALL YOUR DRYER:
1. In an area exposed to dripping water or outside
weather conditions.
2. In an area where it will come in contact with
curtains, drapes, or anything that wilt obstruct
the flow of combustion and ventilation air.
3. On carpet. Floor MUST be solid with a maximum
slope of 1 inch (2.54 cm).
INSTALLATION IN A RECESS OR CLOSET
1. A dryer installed in a bedroom, bathroom,
recess or closet, MUST be exhausted outdoors.
2. No other fuel burning appliance shall be
installed in the same closet as the gas dryer.
3. Your dryer needs the space around it for proper
ventilation.
DO NOT install your dryer in a closet with a solid
door.
.
Closet door ventilation required: A minimum
of 120 square inches (774.2 cm 2)of opening,
equally divided at the top and bottom of the
door, is required. Openings should be located
3 inches (7.6 cm) from bottom and top of door.
Openings are required to be unobstructed
when a door is installed. A Iouvered door with
equivalent air openings for the full length of the
door is acceptable.
MINIMUM INSTALLATIONCLEARANCES - Inches (cm)
SIDES REAR TOP FRONT
Alcove 0" (0 cm) 0" (0 cm)* 0" (0cm) nia
Under-
Counter
0" (0 cm) 0" (0 cm)* 0" (0 cm) nia
Closet 0" (0 cm) 0" (0 cm)* 0" (0cm) 1" (2.54cm)
* For other than straight back venting, a quick-turn 90°
dryer vent elbow must be installed to achieve 0" (0 cm)
installation.
,,,,
tl
i
ii
I
k 3_!
closet door
NOTE
To achieve an installation with 0" (0 cm) clearance
for the back of the dryer (for other than straight
back venting), a quick-turn 90° dryer vent elbow
must be installed as described previously in this
man ual.

Installed dryer dimensions
50.6" (t28,50m) *
to clear open door
fl oar line
3t .50" (80am)*
to front of closed dear
Installation Requirements
(6&5era)
53.00"
(t34.5cm)
centerline
t
gag aupply
pipe on rear
height for
dryer mounted on
optional pedestal
floor line
* Toobtain these minimal depth dimensions, dryer must either be vented ab'aight back or
with a quick-taro _)° elbow, Connection of water inlet hoae on Steam Modela adda 3/4 in,
(2 ore) to h_atMlation depth, Upward venting of exh auat on pedestal=mounted or freestanding
dryer adds approximately 4 in, (t0.2 am) to inateltation depth. Downward ven6ng of exhauat
on pedestal-mounted dryer adds approximately 1,7 in. (4.3 am) to installation depth.
50.6" (128.5cm)*
to clear open door
75. 75"
(tg2.5cm)
t 6.25"
(4t .5era)
(g.5em)
T
gas supply
pipe on rear
of gag unit
(34.5am)
to center of rear vent
27,0C
(6&5am)
18.25"
(46.5cm)
centerline
height for
rear vent
41.00"
(104am)
To obtain theae minimal depth dimensions, dryer must either be vented a_aight back or with a quick-t_rn 90 _ elbow,
Connection of water inlet hoee on Steam Mo_ela a_a.314 in (2 era) to inatallation depth, Upward or downward venting
of exhaust on etacked dr_'er a_ls approximately 4 in. (10.2 am) to installation depth.

Installation instructions
Eiectricai installation
The following are specific requirements for proper
and safe electrical installation of your dryer. Failure
to follow these instructions can create electrical
shock and/or a fire hazard.
ELECTRICAL SHOCK HAZARD
This appliance MUST be properly grounded.
Electrical shock can result if the dryer is not
properly grounded. Follow the instructions in
this manual for proper grounding.
Do not use an extension cord with this dryer.
Some extension cords are not designed to
withstand the amounts of electrical current this
dryer utilizes and can melt, creating electrical
shock and/or fire hazard. Locate the dryer
within reach of the receptacle for the length
power cord to be purchased, allowing some
slack in the cord. Refer to the pre-installation
requirements in this manual for the proper
power cord to be purchased.
WARNING
ELECTRICAL SHOCK HAZARD
A U.L-approved strain relief must be installed
onto power cord. Ifthe strain relief is not
attached, the cord can be pulled out of the
dryer and can be cut by any movement of the
cord, resulting in electrical shock.
Do not use an aluminum wired receptacle with
a copper wired power cord and plug (or vice
versa). A chemical reaction occurs between
copper and aluminum and can cause electrical
shorts. The proper wiring and receptacle is a
copper wired power cord with a copper wired
receptacle.
NOTE
Dryers operating on 208 volt power supply will
have longer drying times than dryers operating
on 240 volt power supply.
Grounding requirements - Electric dryer (USA}
For a grounded, cord-connected dryer:
1. The dryer MUST be grounded. In the event of
ELECTRICAL SHOCK HAZARD
Improper connection of the equipment grounding
conductor can result in a risk of electrical shock.
Check with a licensed electrician if you are in
doubt as to whether the appliance is properly
grounded.
a malfunction or breakdown, grounding will
reduce the risk of electrical shock by a path of
least resistance for electrical current.
2. After you purchase and install a 3 wire or 4
wire power supply cord having an equipment-
grounding conductor and a grounding plug
that matches your wiring system, the plug
MUST be plugged into an appropriate, copper
wired receptacle that is properly installed and
grounded in accordance with all local codes and
ordinances. If in doubt, call a licensed electrician.
3. DO NOT modify the plug you've installed on
this appliance. If it wilt not fit the outlet, have a
proper outlet installed by a qualified electrician.
For a permanently connected dryer:
1. The dryer MUST be connected to a grounded
metal, permanent wiring system; or an
equipment grounding conductor must be run
with the circuit conductors and connected to
the equipment-grounding terminal or lead on
the appliance.
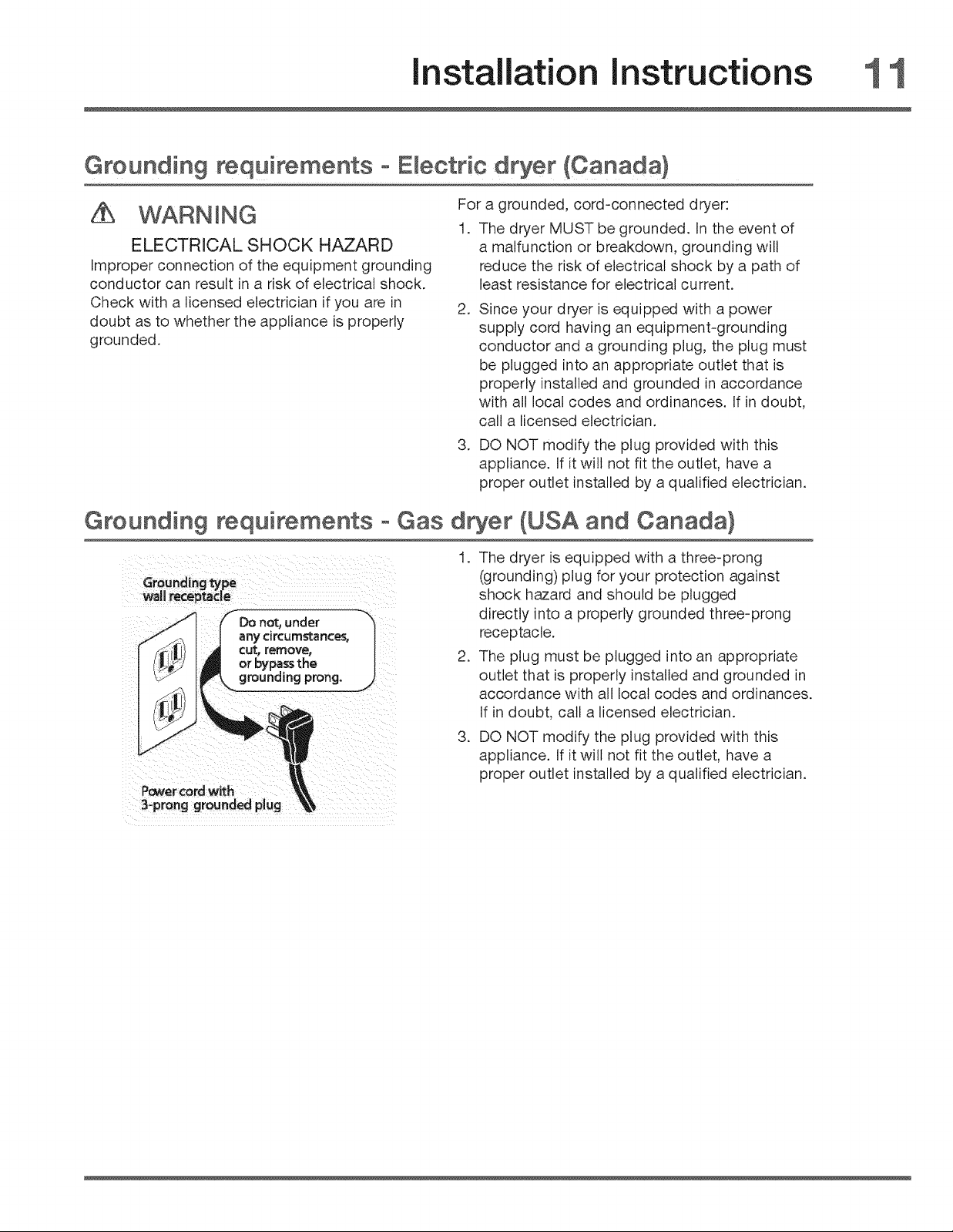
Installation instructions 1
Groundin 9 requirements o Electric dryer (Canada)
WARNING
ELECTRICAL SHOCK HAZARD
Improper connection of the equipment grounding
conductor can result in a risk of electrical shock.
Check with a licensed electrician if you are in
doubt as to whether the appliance is properly
grounded.
For a grounded, cord-connected dryer:
1. The dryer MUST be grounded. In the event of
a malfunction or breakdown, grounding will
reduce the risk of electrical shock by a path of
least resistance for electrical current.
,
Since your dryer is equipped with a power
supply cord having an equipment-grounding
conductor and a grounding plug, the plug must
be plugged into an appropriate outlet that is
properly installed and grounded in accordance
with all local codes and ordinances. If in doubt,
call a licensed electrician.
,
DO NOT modify the plug provided with this
appliance. If it will not fit the outlet have a
proper outlet installed by a qualified electrician.
Grounding requirements o Gas dryer (USA and Canada}
1. The dryer is equipped with a three-prong
Groundingtype
wallreceptacle
Do not, under
anycircumstances,
cut,remove,
orbypassthe
grounding prong.
Paver cordwith
3-prong grounded plug
J
(grounding) plug for your protection against
shock hazard and should be plugged
directly into a properly grounded three-prong
receptacle.
2. The plug must be plugged into an appropriate
outlet that is properly installed and grounded in
accordance with all local codes and ordinances.
If in doubt, call a licensed electrician.
3. DO NOT modify the plug provided with this
appliance. If it will not fit the outlet, have a
proper outlet installed by a qualified electrician.

Installation Instructions
Electrical connection (non-Canada) o3 wire cord
3-wire receptacle
(NEMA type 10-30R)
WARNING
ELECTRICAL SHOCK HAZARD
Failure to disconnect power source before servicing
could result in personal injury or even death.
.
Turn off power supply to outlet.
2.
Remove the screw securing the terminal block
access cover in the lower corner on the back of
the dryer.
,
Install a UL-approved strain relief according
to the power cord/strain relief manufacturer's
instructions in the power cord entry hole below
the access panel. At this time, the strain relief
should be loosely in place.
,
Thread an UNPLUGGED, UL=approved, 30 amp.
power cord, NEMA 10-30 type SRDT, through the
strain relief.
.
Attach the power cord neutral (center wire)
conductor to the SILVER colored center
terminal on the terminal block. Tighten the
screw securely.
.
Attach the remaining two power cord outer
conductors to the outer, BRASS colored
terminals on the terminal block. Tighten both
screws secu rely.
ELECTRICAL SHOCK HAZARD
Do not make a sharp bend or crimp wiring/
conductor at connections.
7. Follow manufacturer's guidelines for firmly
securing the strain relief and power cord.
8. Reinstall the terminal block cover.
=l IMPORTANT
install
UL-approved
strain relief here
Terminal screw
recovery slot
@ NOTE
If a terminal screw falls during cord installation,
it can be retrieved in the terminal screw recovery
slot below the access panel.
DO NOT remove
internal ground in
a3-wire rtstem!!
Neutral
terminal
If moving dryer from a 4-wire system and
installing it in a 3-wire system, move the internal
ground from the center terminal back to the
GREEN screw next to the terminal block.

installation instructions 3
EJectrical connection (non-Canada} o4 wire cord
4-wire receptacle
(NEMA type 14-30R)
WARNING
ELECTRICAL SHOCK HAZARD
Failure to disconnect power source before servicing
could result in personal injuryor even death.
1. Turn off power supply to outlet.
2. Remove the screw securing the terminal block
access cover in the lower corner on the back of
the dryer.
3. Install a UL-approved strain relief according
to the power cord/strain relief manufacturer's
instructions Anthe power cord entry hole below
the access panel. At this time, the strain relief
should be loosely in place.
4. Thread an UNPLUGGED, UL-approved, 30
amp. power cord, NEMA 14-30 type ST or
SRDT, through the strain relief.
5. Disconnect the internal (WHITE) dryer harness
ground wire from the (GREEN) ground screw
next to the terminal block.
6. Attach the ground (GREEN) power cord wire
to the cabinet with the ground (GREEN) screw.
Tighten the screw securely.
7. Move the internal dryer harness ground
(WHtTE) wire to the terminal block and attach
it along with the neutral (WHITE) power cord
wire conductor to the center, SILVER colored
terminal on the terminal block. Tighten the
screw securely.
8. Attach the RED and BLACK power cord
conductors to the outer, BRASS colored
terminals on the terminal block. Tighten both
screws secu rely.
If a terminal screw falls during cord installation,
it can be retrieved in the terminal screw recovery
slot below the access panel.
NOTE
Move internal ground (WHITE)
wiretoneutral(SILVER) ,_
terminal for4-wire system. -_,_
-- Neutral
IWHITEwire)
blod<
Une2
(BP_L_$terminal)
Neutral
{SILVERterminal)
Install
UL-approved
strain relief here
Terminal screw
recovery slot
Neutral
terminal
ELECTRICAL SHOCK HAZARD
Do not make a sharp bend or crimp wiring!
conductor at connections.
9. Fotlow manufacturer's guidelines for firmly
securing the strain relief and power cord.
10. Reinstall the terminal block cover.
GREEN
ground screw
ground wi_
GREEN
REDpower wire
BLACK
or RED
powerwire
BLACKer

Installation instructions
Gas connection
1. Remove the shipping cap from gas pipe at the
rear of the dryer.
IMPORTANT
DO NOT connect the dryer to L.R gas service
without converting the gas valve. An L.R
conversion kit must be installed by a qualified
gas technician.
,
Connect a 1/2 inch (1.27 cm) I.D. semi-rigid or
approved pipe from gas supply line to the 3/8
inch (0.96 cm) pipe located on the back of the
dryer. Use a t/2 inch to 3/8 inch (1.27 cm to
0.96 cm) reducer for the connection. Apply an
approved thread sealer that is resistant to the
corrosive action of liquefied gases on all pipe
connections.
Manual GAS FLOW
Shutoff Flare _ Flare
Valve Union Union
"._ Nipple Flexible Inlet Pipeon
O pen Connector Back of Dryer
All connections must be wrench-tightened
3. Open the shutoff valve in the gas supply line to
allow gas to flow through the pipe. Wait a few
minutes for gas to move through the gas line.
Shutoff Valve-
Open position
.
Check for gas system leaks with a manometer.
If a manometer is not available, test all
connections by brushing on a soapy water
solution.
WARNING
EXPLOSION HAZARD
NEVER test for gas leaks with an open flame.
IMPORTANT
The supply line must be equipped with an
approved manual shutoff valve. This valve
should be located in the same room as the dryer
and should be in a location that allows ease of
opening and closing. Do not block access to the
gas shutoff valve.

installation instructions 5
Water connection (Steam Model on y}
WATER SUPPLY REQUIREMENTS
Cold water faucet MUST be instaHled within 42
inches (107 cm) of your dryer's water inlet. The
faucet MUST be 3/4 inch (1.9 cm) with thread-
ing for laundry hose connection. Water pressure
MUST be between 30 and 120 psi. Your water
department can advise you of your water pressure.
,
Turn off COLD water supply to washer,
2.
Remove COLD inlet hose from COLD water
supply and inspect for rubber washer. Replace
washer if it is torn or worn out.
RUBBER WASHER
MUST BE PRESENT
AND UNDAMAGED
COLD INLET HOSE
TO WASHER
3. Momentarily turn on COLD supply and run
some water into a bucket or container to clear
any contaminants in the line.
4. Remove hose kit from dryer drum and inspect
hose couplings for proper placement of rubber
washers.
RUBBER WASHERS
MUST BE PRESENT

6 Installation instructions
Water connection, con't (Steam Model only}
,
If your installation has room for the COLD
water supply to accept the "Y" connector
directly, thread tile "Y" connector to the COLD
water supply and snug it by hand; then tighten
it another 2/3 turn with pliers.
NOTE
If you were able to install the "Y" connector directly
to the COLD water supply, please skip to step 8.
6. Ifthere is not room to install the "Y" connector
directly, thread the short extension hose on to
the COLD water supply and snug it by hand;
then tighten it another 2/3 turn with pliers.
7. Thread the "Y" connector to the short
extension hose and snug it by hand; then
tighten it another 2/3 turn with pliers.
8. Connect the COLD inlet hose for the washer
to the "Y" connector and snug it by hand; then
tighten it another 2/3 turn with pliers.
9. Connect the straight end of the long hose from
the kit to the other outlet on the "Y" connector
and snug it by hand. Connect the hose's 90 °
coupling to the brass water inlet on the back
of the dryer and snug it by hand. Tighten each
connection of the dryer inlet hose another 2/3
turn with pliers.
10. Turn on the water and check for leaks at all
connections.
DIREOT OONNEOTION
OR WiTH EXTENSION
WATER INLET ON DRYER
OOLD WATER SUPPL"f_
L OHOoE TO WASHER

General installation
,
Connect the exhaust duct to the outside exhaust
system (see pages 5 through 7). Use of a 4" (102
mm) clamp (item A) is recommended to connect
the dpjer to the exhaust vent system. Use metal
foil tape to seal all other joints.
,
Carefully slide the dryer to its final position.
Adjust one or more of the legs until the dryer is
resting solidly on all four legs. Place a level on
top of the dryer. The dryer MUST be level and
resting solidly on all four legs. Rock alternating
corners to check for stability. Remove and
discard door tape.
IMPORTANT
Be sure the power is off at a circuit breaker/fuse
box before plugging the power cord into an outlet.
installation instructions 7
3. Plug the power cord into a grounded outlet.
4. Turn on the power at the circuit breaker/fuse
box.
5. Read the Use & Care Guide provided with
the dryer. It contains valuable and helpful
information that will save you time and money.
6. See the next page about performing a brief,
helpful "installation Cycle" for your new dryer.
7. If you have any questions during initial
operation, please review the "Avoid Service
Checklist" in your Use & Care Guide before
calling for service.
8. Place these instructions in a location near the
dryer for future reference.
NOTE
A wiring diagram and technical data sheet are
located inside the dryer console.

Installation instructions
Performing lnstalJation Cycle
NOTE
FIRE HAZARD
Before operating the dryer, make sure the dryer
area is clear and free of combustible materials,
gasoline, and other flammable vapors. Also
see that nothing (such as boxes, clothing, etc.)
obstructs the flow of combustion and ventilation air.
With your dryer in final location, perform an installation Cycle to assist in proper installation.
If your dryer has this console:
On gas dryers, before the burner wilt light, it is
necessary for the gas line to be bled of air. If the
burner does not light within 45 seconds the first
time the dryer is turned on, the safety switch will
shut the burner off. If this happens, press cancel
and wait 5 minutes before making another
attempt to light.
2a 2b
1.
Empty dryer's drum and close door.
2,
After you plug inthe dryer the first time: wake up the dryer by pressing any button, rotate cycle knob to cycle one
up from lower right position (1), press the 8tart button (3) and then the cancel button (4).
3.Wake up the dryer again by pressing any button, then immediately and simultaneously press and hold buttons 2a
and 2b for 5 seconds, or until the LCD display changes.
4. The LCD window will display II1STRLCYCLEand show estimated time of cycle completion. Press the start button.
The Installation Cycle will automatically perform various diagnostic routines. At cycle completion, the LCD window
may display ItfSTRLPRSS_,meaning your new dryer is properly installed and ready for use. If it prompts an action
such as SER_JICECORD,NB 5RS or CRLLSE_JtCE877 ff35 32B7, review the installation steps and make the necessary
corrections before you attempt to use the dryer.
5,Your dryer will exit the Installation Cycle and return to normal operation the next time you wake it up,
3 4
Dryer will stay awake for 3 minutes after the Installation Cycle. tf you wish to immediately run the
dryer through adrying cycle, press the cancel button to put the unit to sleep and then rewake it
immediately to continue the normal operating mode.
6. Please read the Use & Care Guide and enjoy your new premium dryer!
If your dryer has this console:
__O
1.After you plug in the dryer the first time: wake up the dryer by pressing any button and follow the prompts on the
LCD User Interface, including language selection.
2.The Installation Cycle will automatically test for correct cord connection (on electric models), presence of gas sup-
ply (on gas models) and free flow of exhaust vent. At cycle completion, the LCD user interface may display INSTRL
PRSSI,meaning your new dryer is properly installed and ready for use. If it prompts an action such as SE_:_JfCECORD;
fro 6RSor CRLLSERI21CE877 ff35 3287, review the installation steps and make the necessary corrections before you
attempt to use the dryer,
3.Your dryer will exit the Installation Cycle and return to normal operation the next time you wake it up,
NOTE
Dryer will stay awake for 3 minutes after the Installation Cycle. tf you 'wish to immediately run the
dryer through a drying cycle, press the cancel button to put the unit to sleep and then rewake it
immediately to continue the normal operating mode.
4. Please read the Use & Care Guide and enjoy your new premium dryer!
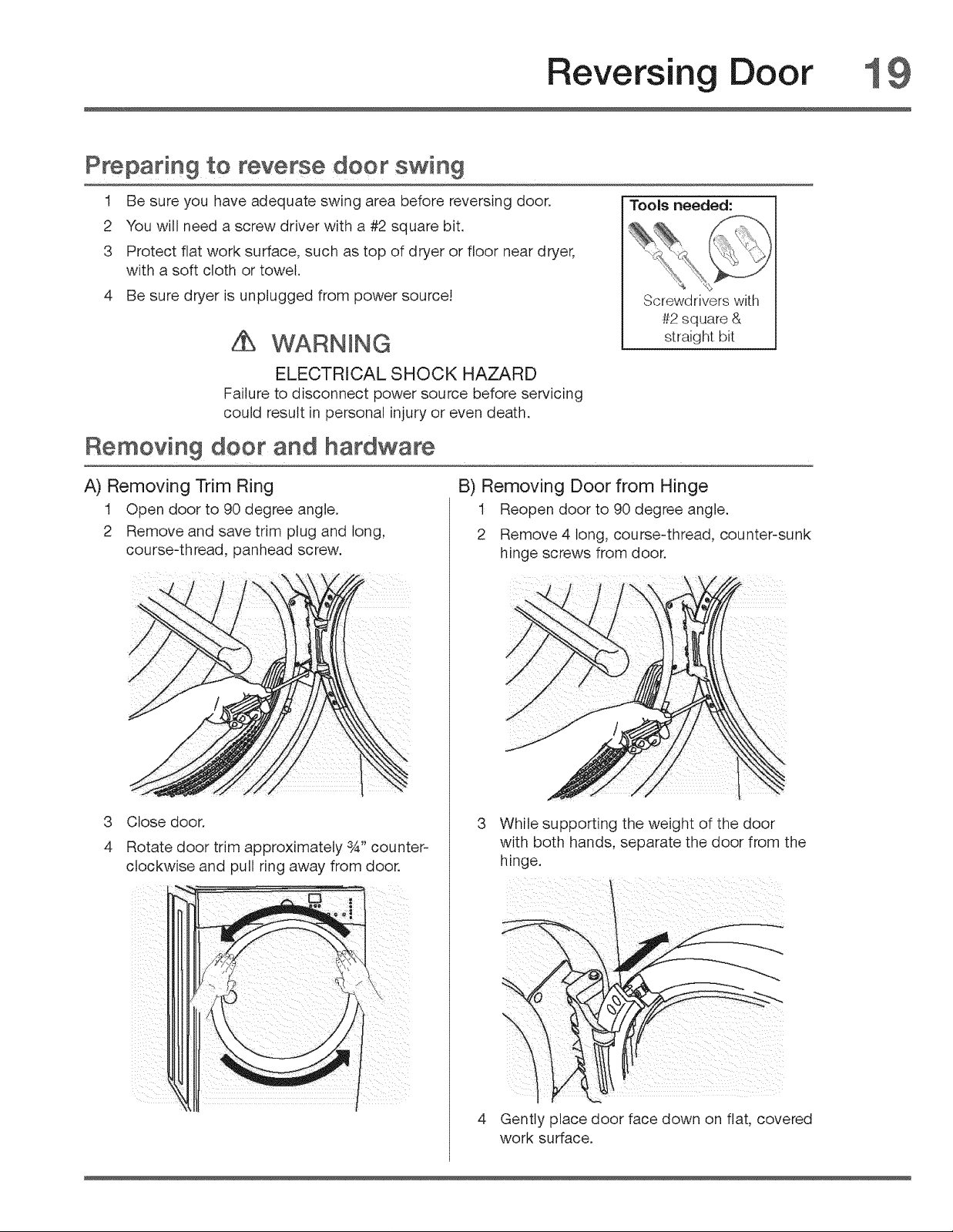
Preparing to reverse door swing
Reversing Door 9
1 Be sure you have adequate swing area before reversing door.
2 You will need a screw driver with a #2 square bit.
3 Protect flat work surface, such as top of dryer or floor near dryer,
with a soft cloth or towel.
4 Be sure dryer is unplugged from power source!
WARNING
ELECTRICAL SHOCK HAZARD
Failure to disconnect power source before servicing
could result in personal injury or even death.
Removing door and hardware
A) Removing Trim Ring
1 Open door to 90 degree angle.
2 Remove and save trim plug and long,
course-thread, panhead screw.
B) Removing Door from Hinge
1 Reopen door to 90 degree angle.
2 Remove 4 tong, course-thread, counter-sunk
hinge screws from door.
Tools needed:
Screwdrivers with
#2 square &
straight bit
34Close door.
Rotate door trim approximately 3A"counter-
clockwise and pull ring away from door.
While supporting the weight of the door
with both hands separate the door from the
hinge.
\
\
\
4 Gently place door face down on flat, covered
work surface.

Reversing Door
Reversin9 door and hardware
C) Removing Hinge from Front Panel
1 With the hinge in open position, remove 2
short, course-thread, panhead screws on
hinge plate.
Remove 3 short, fine-thread, counter-sunk
screws in hinge side.
Rotate striker and move to opposite
opening. Attach with 2 short, course-thread,
panhead screws.
3 Install plastic hole plugs.
E) Reattaching Hinge to Front Panel
1 Rotate the hinge and move it to the opposite
opening. Use the side locating pins to align the
hinge and install 1 short, fine-thread, counter-
sunk screw inthe center hole of hinge side.
D) Reversing Hardware on Front Panel
1 Remove 2 short, course-thread, panhead
screws from striker and 2 plastic hole plugs.
2 Install the other 2 short, fine-thread, counter-
sunk screws in the upper and lower holes of
hinge side.
3 Install 2 short, course-thread, panhead
screws through hinge plate.

Reversing Door 21
F) Removing Striker Plate
1 Remove 2 long, course-thread, counter-sunk
screws and latch plate.
2 Set the latch plate to the side for later.
G) Removing Latch Indicator
H) Removing Hole Plug
1 Insert flat blade screwdriver into open slot of
hole plug.
2 Gently pry upward to release tab.
insert flat blade screwdriver into open slot of
latch indicator.
2 Gently pry upward to release tab.
3 Pull the indicator out and set it aside.
3 Pull the hole plug out and set it aside.

22 Reversing Door
I) Reinserting Latch Indicator
1 Rotate the latch indicator and move it to the
opposite hole in the door.
/
insertindicator
through slot
2 Firmly insert the two small tabs on either
side of the latch indicator into the two slots
on either side of the hole in the door.
J) Reattaching Latch Plate
1 Rotate latch plate and move to opposite side
of door above indicator.
2 Reattach with 2 long, course-thread,
counter-sunk screws.
K) Reinserting Hole Plug
1 Rotate the hole plug and move it to the
opposite hole in the door.
2 Firmly insert the two small tabs on either
side of the hole plug into the two slots on
either side of the hole in the door.
!
inserttab
3 Firmly press downward on the indicator until
the tab snaps in place.
J
pressdown
andsnap
insertta5
inserttab
3 Firmly press downward on the hole plug until
the tab snaps in place.

Reattaching door and hardware
Reversing Door 23
L) Reattaching Door Assembly
1 Open the hinge to a 90 degree angle.
2 Install the door onto the hinge locating pins.
3 Secure the door with 4 long, course-thread,
counter-sunk screws.
\
N) Reinstalling Trim Ring
1 Close door.
2 Orient trim so UP position is approximately
3A"to the left of top center. Opening in ring
should be on the hinge side.
3 Insert trim ring in slots and rotate clockwise
approximately 3A".
O) Reinstalling Trim Plug
1 Open door to 90 degree angle.
2 Install trim plug with 1 long, course-thread,
panhead screw.
4 Close the door and test the operation of the
latch.
M) Reversing Trim Ring
1 Trim ring orientation is marked on the back.
2 Remove trim ring cover plate. To remove
plate from left, pivot point is down. To
remove plate from right, pivot point is up.
3 Rotate and move trim ring cover plate to
opposite opening in trim and reinsert.
P) Plug in dryer and continue operation.