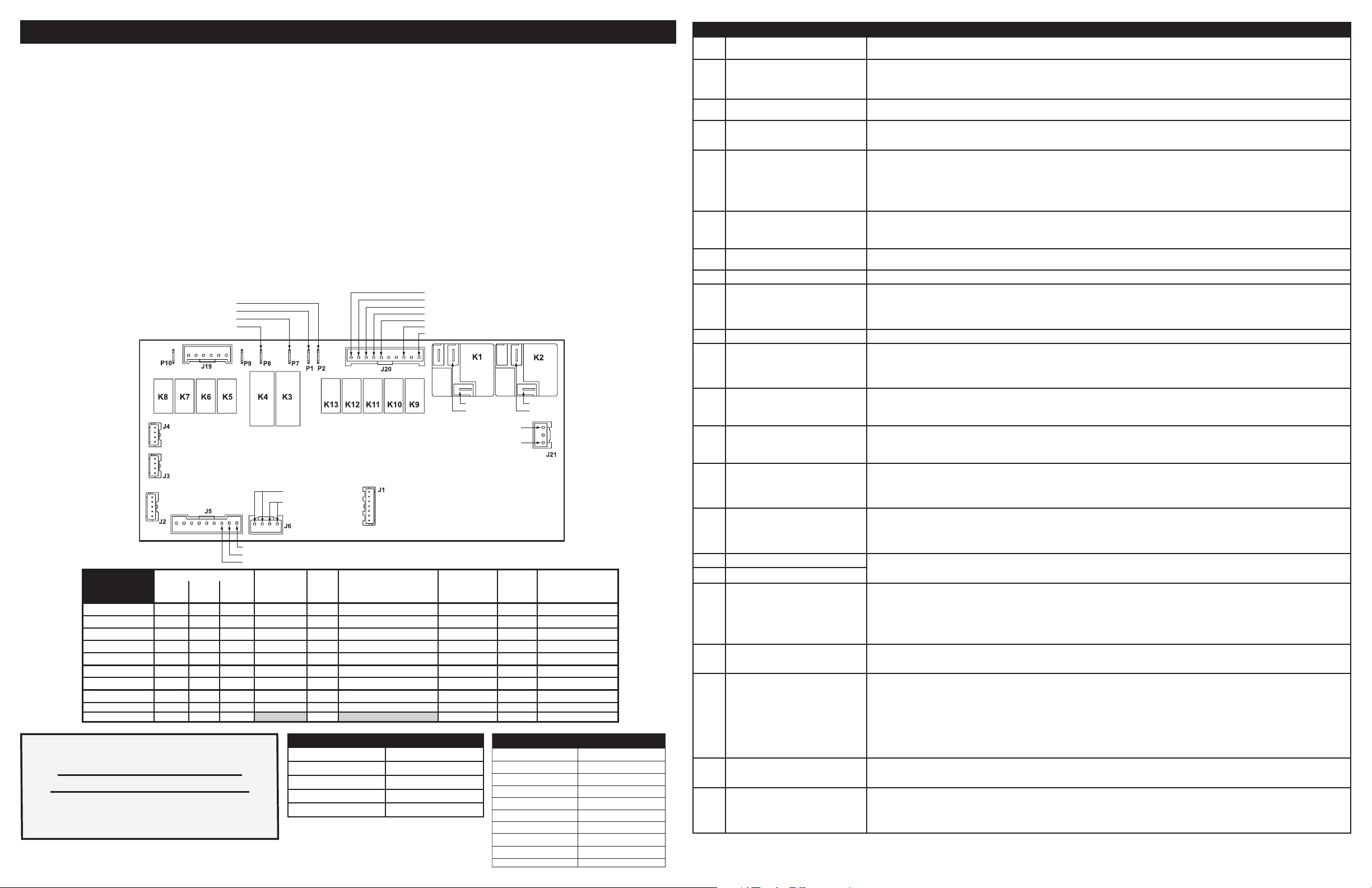
IMPORTANT
DO NOT REMOVE THIS BAG
OR DESTROY THE CONTENTS
WIRING DIAGRAMS AND SERVICE
INFORMATION ENCLOSED
REPLACE CONTENTS IN BAG
ELECTRIC RANGES WITH MODULAR OVEN CONTROLS
Open circuit/infinite resistance
Probe circuit to case ground
NOTICE: This service data sheet is intended for use by persons having electrical and mechanical training and a level of knowledge of these subjects generally considered acceptable in the appliance repair
trade. The manufacturer cannot be responsible, nor assume any liability, for injury or damage of any kind
arising from the use of this data sheet.
IMPORTANT NOTE: This unit includes an EOC (electronic oven control). This board is not eld-repair-
able.
Safe Servicing Practices
To avoid the possibility of personal injury and/or property damage, it is important that safe servicing
practices be observed. The following are some, but not all, examples of safe practices.
1. Do not attempt a product repair if you have any doubts as to your ability to complete it in a safe
and satisfactory manner.
2. Before servicing or moving an appliance, remove power cord from electric outlet, trip circuit
breaker to Off, or remove fuse.
3. Never interfere with the proper installation of any safety device.
4. Use only replacement parts specied for this appliance. Substitutions may not comply with safety
standards set for home appliances.
5. Grounding: The standard color coding for safety ground wires is green or green with yellow
stripes. Ground leads are not to be used as current carrying conductors. It is extremely important
that the service technician reestablish all safety grounds prior to completion of service. Failure to
do so will create a potential hazard.
6. Prior to returning the product to service, ensure that:
• All electric connections are correct and secure.
• All electrical leads are properly dressed and secured away from sharp edges, high-tem-
perature components, and moving parts.
• All uninsulated electrical terminals, connectors, heaters, etc. are adequately spaced away
from all metal parts and panels.
• All safety grounds (both internal and external) are correctly and securely reassembled.
• All panels are properly and securely reassembled.
BAKE ELEMENT
CONVECTION ELEMENT
1
J3 OR J4
TO USER INTERFACE BOARD (MARS BOARD)
VOLTAGES:
1. DC GRD
1
2. MACS DATA
3. +5V DC
4. +13V DC
1
1
CIRCUIT
ANALYSIS
MATRIX
Bake X X X X X X
Broil X X X
Conv. Bake X X X X X X
Conv. Roast X X X X X X
Clean X X X X
Locking X
Unlocking X
Light X
Door Open X
Door Closed X
Elements
BakeP7BroilK2Conv.
L1
L1
1 1
MEAT PROBE
TEMPERATURE PROBE
1
MOTOR DOOR LATCH SWITCH
COMMON
Door Motor
P8
J20-10
SERVICE DATA SHEET
p/n A00980632 Rev A (17/01)
Temperature Adjustment
1. While in a non-cooking mode, press and hold the Bake key for 3 seconds until UPO appears in the
display.
2. Use the number keys (0-9) to enter the desired adjustments (-35° to 35° F).
3. Press the Self Clean key to change the sign of the adjustment to a (-), if necessary. A positive adjust-
ment will not display a sign.
4. Once the desired adjustment (-35° to 35° F) has been entered, press START to accept the change or
the STOP key to reject the change.
Note: Changing calibration affects all baking modes. The adjustments made will not change the self-cleaning
temperature.
Modular Control Systems
This appliance is equipped with a modular system of controls. The modular system consists of various boards
which communicate with one another to drive cooking functions. Oven functions, if available, operate through
an oven user interface (UI or UIB) and an oven relay board. Cooktop functions, if available, operate through
a cooktop UI/UIB and a cooktop relay board. There may be additional boards which work within the system
to drive specic functions (refer to the schematics and diagrams and this sheet). Low voltage operating
and communications power for the modular boards is provided through the wiring schemes. The boards
that generate low voltage operating and communications power depend upon the individual control system
(refer to the schematics and diagrams on this sheet). These voltages are only the operational voltages.
Do not use these voltages as conrmation of communication between the boards. Communication occurs
through software programming on each board. This communication is not detectable by volt ohmmeters. The
programming is self-monitored and the UI displays will show error codes based on detected failures. The
individual boards are not eld repairable. See the schematics and diagrams included on this sheet for more
unit-specic details.
CONVECTION FAN HIGH
CONVECTION FAN LOW
COOLING FAN & FAN THERMOSTAT
OVEN LIGHT
L1
NEUTRAL
PROGRAMMING HEADER
1
Light
J20-6
MEAT PROBE TEMPERATURE VS RESISTANCE
Temperature °F (°C) Resistance (Kohm)
77 (25) 50.0 ± 7%
122 (50) 18.0 ± 4.9%
176 (80) 6.3 ± 3.3%
212 (100) 3.4 ± 4.6%
Conv. Fan
Low Speed J20-8
High Speed J20-9
J5-7, J5-8
DLB BROIL
COM L2 OUT
NO:L2 IN
L1
NEUTRAL
Door
Switch
DLB L2
out K1
Temperature °F (°C)
32 ± 1.9 (0 ± 1.0)
75 ± 2.5 (24 ± 1.3)
250 ± 4.4 (121 ± 2.4)
350 ± 5.4 (177 ± 3.0)
450 ± 6.9 (232 ± 3.8)
550 ± 8.2 (288 ± 4.5)
650 ± 9.6 (343 ± 5.3)
900 ± 13.6 (482 ±7.5)
COM L1
NO:BROIL
1
Cooling Fan
J20-7
RTD SCALE
Resistance (ohms)
1000 ± 4.0
1091 ± 5.3
1453 ± 8.9
1654 ± 10.8
1852 ± 13.5
2047 ± 15.8
2237 ± 18.5
2697 ± 24.4
ELECTRONIC OVEN CONTROL (EOC) FAULT CODE DESCRIPTIONS
Fault
Description of Error Code Suggested Corrective Action
Code
F001
Touch panel failure Disconnect power, wait 30 seconds and reapply power. If fault returns upon power-up replace the touch panel.
F002
F004
F005
F003 The oven user interface board is incorrectly
congured.
F010 Oven temperature runaway: the cavity
temperature has been detected in excess
of the maximum safe operating temperature.
F011 Stuck key: a key has been detected has
pressed continuously for 30 seconds or
more.
F012 Keyboard conguration alarm: the oven
user interface board received from the touch
panel a key code that does not match the
key map.
F013 Data written to non-volatile memory has
failed verication
F015 Keyboard error Disconnect power, wait 30 seconds and reapply power. If fault returns upon power-up replace the touch panel.
F017 The oven user interface board is unable to
congure the touch panel.
F018 Oven relay board failure (wiggler) Replace the oven relay board.
F019 The oven user interface board is unable to
congure the oven relay board
F022 Communication failure between the oven
user interface board and the oven relay
board
F023 Communication failure between the oven
user interface board and the glass touch
panel
F025
The communication between the over user
F027
interface and the oven relay board cannot
be initiated.
F028
The communication between the over user
F029
interface and the touch panel cannot be
initiated.
F030 Open oven temperature sensor (RTD) 1. Check probe circuit wiring for possible open or short condition.
F031 Shorted oven temperature probe (RTD)
F033 Meat probe temperature sensor shorted
or too hot
F050 A/D Out of Range: the oven relay board is
unable to read the status of the switches
(door, MDL)
F090 Motor Door Lock mechanism failure. The
oven control does not see the Motor Door
Lock running.
F095 Motor Door Lock mechanism failure. The
Motor Door Lock does not stop running or
the Lock Switch sends an invalid signal.
F096 The oven door has been detected open
during a Self Clean cycle.
Replace the oven user interface board. Make sure you install the latest revision available for this model.
1. If oven is overheating, disconnect power. Check oven temperature probe (RTD) and replace if necessary.
2. If the oven temperature probe is good and if oven continues to overheat when power is reapplied, replace the oven relay board.
1. If a key was pressed inadvertently for a long time this error code will be displayed. Make sure there is nothing (water, utensils) in contact with the
keyboard. The fault code should go away once the key is released and the Stop key is pressed. If the F011 error comes back when a key is pressed it
means the error condition is still there. If the F011 error does not come back it means the error condition is gone and the oven can be used.
2. If the fault code cannot be cleared, test the wiring harness between oven user interface board (connector I2C1 or I2C2) and touch panel (connector I2C1
or I2C2).
3. If the fault code cannot be cleared and the wiring is good, the touch panel is most likely defective: replace the touch panel.
4. If changing the touch panel did not x the problem replace the oven user interface board.
1. Verify the unit has the proper oven user interface board and touch panel, based on the model number and parts catalog.
2. Replace the oven user interface board.
3. If the problem persists replace the touch panel.
Disconnect power, wait 30 seconds and reapply power. If fault returns upon power-up replace the oven user interface.
1. Disconnect power to the unit, wait 30 seconds, then reapply power.
2. If fault returns, verify harness going to I2C1 or I2C2 connector of the touch panel.
3. Verify the unit has the proper oven user interface board and touch panel, based on the model number and parts catalog.
4. If fault persists, replace the oven user interface.
5. If fault persists, replace the touch panel.
1. Disconnect power to the unit, wait 30 seconds, then reapply power.
2. If fault returns, verify connection between the oven user interface board (MACS1 or MACS2 connector) and the oven relay board (connector J3 or J4).
3. Verify the unit has the proper oven user interface board and oven relay board, based on the model number and parts catalog.
4. If fault persists, replace oven user interface board.
5. If fault persists, replace the relay board.
1. Disconnect power, wait 30 seconds and reapply power. Check if error condition is still there.
2. Test wiring harness between oven user interface board (connector MACS1 or MACS2) and oven relay board (connector J3 or J4).
3. If wiring harness is good replace oven relay board.
4. If the problem persists replace the oven user interface.
1. Disconnect power, wait 30 seconds and reapply power. Check if error condition is still there.
2. Test wiring harness between oven user interface board (connector I2C1 or I2C2) and touch panel (connector I2C1 or I2C2).
3. If wiring harness is good replace touch panel.
4. If the problem persists replace the oven user interface.
1. Disconnect power to the unit, wait 30 seconds, then reapply power.
2. If fault returns, verify connection between the oven user interface board (MACS1 or MACS2 connector) and the oven relay board (connector J3 or J4).
3. Verify the unit has the proper oven user interface board and oven relay board, based on the model number and parts catalog.
4. If fault persists, replace relay board.
5. If fault persists, replace the oven user interface board.
1. Disconnect power to the unit, wait 30 seconds, then reapply power.
2. If fault returns, verify touch panel is connected (verify harness going to I2C1 or I2C2 connector) and is getting power from the oven user interface.
3. Verify the unit has the proper oven user interface board and touch panel, based on the model number and parts catalog.
4. If fault persists, replace the touch panel.
5. If fault persists, replace the oven user interface.
2. Verify RTD resistance at room temperature (compare to probe resistance chart). If resistance does not match the chart, replace the RTD probe.
3. If the problem persists replace the oven relay board.
1. The error is triggered if the meat probe sees a temperature in excess of 392°F. Make sure the meat probe was not used in such way that it could have
seen such temperature. If the tip of the probe is not inserted in the meat it will see the cavity temperature, which can be higher than 392°F (depending on
the setpoint) and trigger the alarm.
2. When the meat probe is connected to the socket inside the oven cavity, if the meat probe is not fully inserted into the socket it may short the contacts and
cause the error. Make sure the probe is inserted as much as it can.
3. Verify meat probe resistance at room temperature. Compare to meat probe resistance chart. If the meat probe does not match the chart, replace it.
4. If the above steps failed to correct the problem, replace the oven relay board.
1. Check to ensure that the connections between the door switch, MDL and temp probes are properly connected. This includes all splices and junctions.
2. If the above step failed to correct the problem, replace the oven relay board.
1. Disconnect power to the unit, wait 30 seconds, then reapply power. Try again to make the door lock or unlock (ex: initiate a Lockout or a Clean cycle).
2. Check if the Lock Motor is running or not. If it is not running, test the wiring between the Lock Motor and the oven relay board. If the wiring is good, check
if there is 120VAC at the motor when it is expected to run to see if the failure originates from a bad motor (120VAC present but not turning) or a problem
with the relay board (J20 pin 10 on the oven relay board is the output to the Lock Motor). The Lock Motor can also be tested by applying 120VAC directly
to the motor (unplug it from the relay board rst). If the Lock Motor does not run when 120VAC is applied replace the Lock Motor Assembly. If it is the
relay board that does not provide 120VAC to the Lock Motor replace the oven relay board.
3. If the Lock Motor is running but the oven control cannot nd the locked or unlocked position (ex: motor turns continuously until F90 fault code is gener-
ated) the Lock Switch needs to be veried. Check wiring between Lock Switch and oven relay board. Verify with ohmmeter if the switch makes contact
properly (verify continuity with ohmmeter when the switch is pressed). If the Lock Switch is defective replace the Motor Lock Assembly.
4. If all above steps failed to correct the situation, replace the oven relay board.
1. The problem can be caused by a faulty Lock Switch or by a defective oven relay board. If the Motor Door Lock is always running (as if the relay controlling it is stuck closed) replace the oven relay board.
2. If the motor is not always running replace the Motor Lock Assembly.
1. This error occurs if the door switch has lost its contact during a Self Clean cycle. Make sure the oven door closes well and fully presses on the door
switch plunger when the door is locked, and no one attempted to pull on the oven door during the Self Clean cycle.
2. Test continuity of wiring between the door switch and the oven relay board, make sure the door switch is well connected. With an ohmmeter, verify the
switch is closed when the plunger is pressed. If the door switch is found to be defective replace the door switch.
3. If the switch and wiring are good and the problem persists, replace the oven relay board.