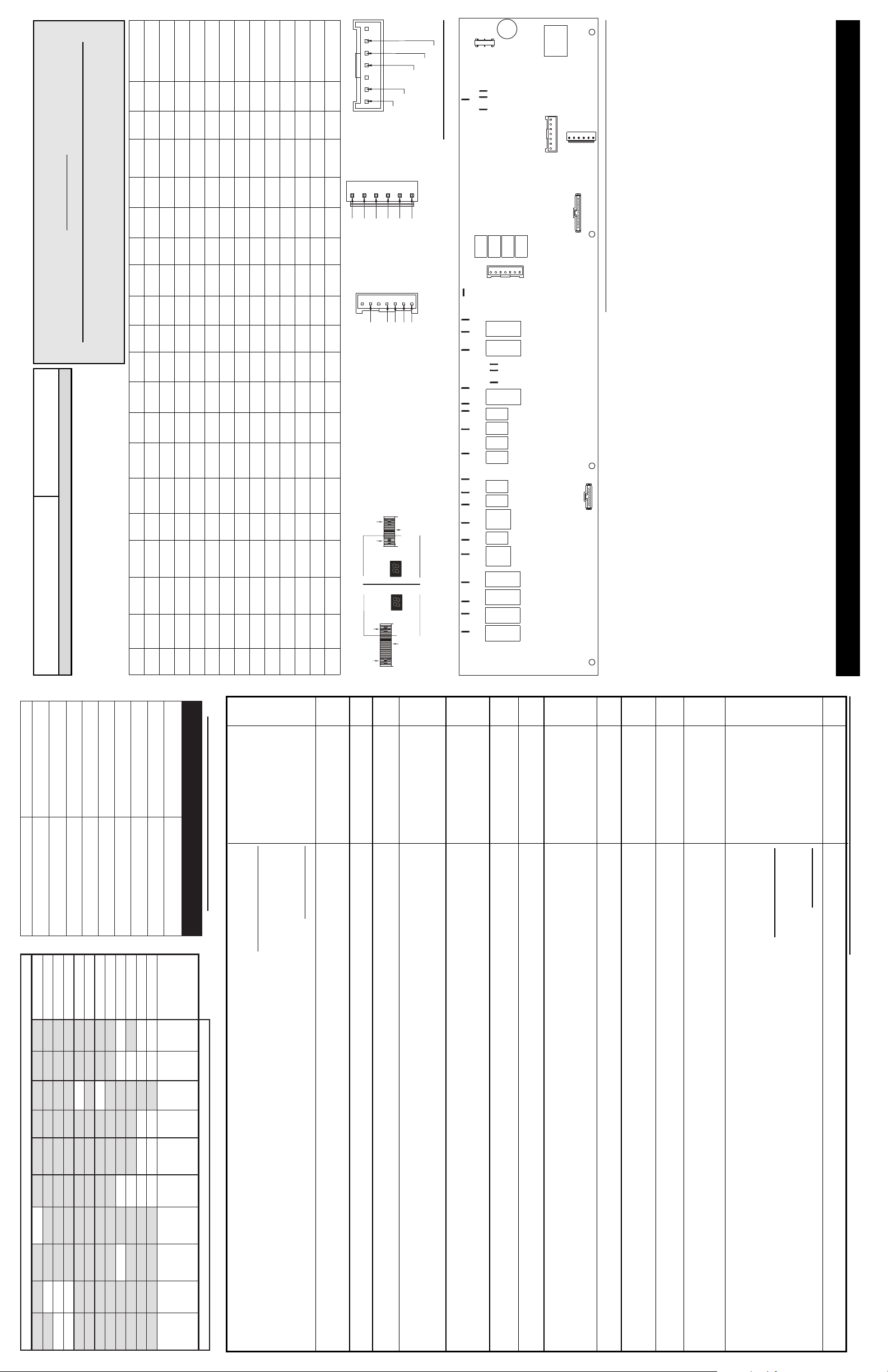
PN 316904479 EN (1206)
WIRING DIAGRAMS AND SERVICE INFORMATION ENCLOSED
DO NOT REMOVE THIS BAG OR DESTROY THE
REPLACE CONTENTS IN BAG
-
-
IMPORTANT
CONTENTS
EOC = Electronic Oven Control
VSC = Variable Speed Control
PS = Power Supply board (PS1, PS2, etc.)
Tech Sheet Abbreviations and Terminology
RTD = Resistance temperature device (Temp. probe/sensor)
TCO = Thermal cut out, also "thermo disc" or "thermal limiter"
PS = Power Supply board (PS1, PS2, etc.)
and P11; test the Warmer Zone Medium on connector PIN 31 with P1 and P10.
-
-
-
-
-
-
-
-
To test keypad function, check for continuity between indicated pin locations while
pressing the keypad. EXAMPLE: test the BAKE key on connector PIN15 with the P2
-
LOOP
-
-
-
-
-
-
-
(UNUSED)
P36-11
P36-12
-
-
-
-
-
-
-
-
-
-
-
CONNECT
-
-
-
-
-
-
-
-
P36-10
P36-9
-
-
-
-
-
-----
-
-
-
-
-
-
-
-
-
-
-
-
(BOTTOM)
WZ MED
WZ ON
MED HIGH
(LOWEST)
WZ_LOW
WZ
(HIGHEST)
WZ HIGH
MED LOW
WZ
-
-
LF1 SIZE
(BOTTOM)
RR2 SIZE
(TOP)
RF1 SIZE
(BOTTOM)
LF2 SIZE
(TOP)
RR1 SIZE
(BOTTOM)
RF2 SIZE
(TOP)
-
-
P15-20 CONNECT
LOOP
-------
-- -
-
-
-
-
-
-
-
-
P15-17 RF
ON/OFF
LOW
RF
MED
RF
HIGH
RF
ON/OFF
RR
LOW
RR
-
MED
RR
HIGH
RR
CONNECT
LOOP
-
-
-
-
-
-
-
-
-
P15-16 LF
P15-15
ON/OFF
CANCEL
BROIL
CONV
LOW
LF
PREHEAT
RAPID
MED
LF
CLEAN
HIGH
SELF
LF
ON/OFF
LR
85
LOW
LR
CONNECT
LOOP
-
MED
LR
HIGH
SIZE
LR
RF
-
-
CONNECT
LOOP
-
-
-
-
-
-
-
-
-
-
-
-
-
-
-
-
-
P15-12
P15-13
P15-14
START
4 BROIL
7
CONV
BAKE
SLOW
COOK
FAVORITES
ROAST
KEEP
WARM
CONV
MY
ON/OFF
TIMER
CLOCK
TIME
SET
END
COOKTOP
LIGHT
LOCK
OVEN
02
6
3
-
-
-
SELECT
WZ
-
-
SIZE
SIZE
LF
RR
-
-
-
-
-
-
-
-
-
-
-
-
-
-
-
-
-
-
-
-
-
-
-
-
-
--
-
-
-
-
P15-11
LOOP
1 BAKE
CONVERT
CONV
COOK
TIME
CONTROL
LOCK
9
-
ON/OFF
WZ
-
-
-
-
-
-
-
-
-
-
-
CONNECTOR-PIN # P15-1 P15-2 P15-3 P15-4 P15-5 P15-6 P15-8 P15-9 P15-10 P15-18 P15-19
P15-7 CONNECT
-
PIN 1-COMMON
PIN 3-HS LR
PIN 2-HS LF
------
PIN 6-OVEN LAMP
-
-
-
P21 - L1 IN
P23 - L2 OUT
P24 - L2 IN
P36-1 P36-2 P36-3 P36-4 P36-5 P36-6 P36-7 P36-8
-
-
-
-
VIEW FROM FRONT OF DISPLAY
LEFT SIDE RIGHT SIDE
PIN 12PIN 1
-
-
-
-
PIN 1
PIN 20
P7
EOC jumper connections
PIN 6-LOCK SWITCH
PIN 5-DOOR SWITCH
PIN 4-COMMON
PIN 2-OVEN PROBE
PIN 1-OVEN PROBE
P8
PIN 6-WARM ZONE
PIN 4-HS RF
PIN 5-HS RR
P16
1
PIN 1-MDL
PIN 3-FAN MOTOR
PIN 2-CATALYST/CLEAN
PIN 4-CONV ELEMENT
P3 - N
P4 - L2
P5 - L1
P19 - BAKE
P20 - BROIL
RIBBON TAIL
12 PIN
P36
(ELECTRIC MODELS ONLY)
RIBBON CONNECTIONS
RIBBON TAIL
20 PIN
P15
P17
P4
P18 P19 P20
P24 P25 P26 P28 P30
P33 P34 P35 P38 P40 P41
P42 P43 P44 P46
K13
P21
P23
P5P2 P3
K12
K17
K18
P22
K19
K20
K21
K22
K23
K25
K26
K27
K28
K29
K30
K31
K32
K33
K11
K10
1
P16
1
P7
Electronic oven control (EOC) & jumper connection locations
1
P8
MEMBRANE KEY
1
P15
MEMBRANE LED
1
P36
4. Prior to returning the product to service, ensure that:
will create a potential safety hazard.
• All electric connections are correct and secure.
• All electrical leads are properly dressed and secured away from sharp edges, high-
temperature components, and moving parts.
3. GROUNDING: The standard color coding for safety ground wires is GREEN or
trip circuit breaker to OFF, or remove fuse.
GREEN WITH YELLOW STRIPES. Ground leads are not to be used as current
carrying conductors. It is extremely important that the service technician
reestablish all safety grounds prior to completion of service. Failure to do so
NOTICE - This service data sheet is intended for use by persons having electrical
and mechanical training and a level of knowledge of these subjects generally
considered acceptable in the appliance repair trade. The manufacturer cannot be
responsible, nor assume any liability for injury or damage of any kind arising from
the use of this data sheet.
Safe servicing practices
To avoid the possibility of personal injury and/or property damage, it is important that safe
servicing practices be observed. The following are examples, but without limitation, of
such practices.
1. Before servicing or moving an appliance, remove power cord from electrical outlet,
2. Never interfere with the proper installation of any safety device.
SERVICE DATA SHEET - Electric Range with ES 1030 Electronic Oven Control
Oven Calibration
Set the electronic oven control for normal baking at 350°F. Obtain an average oven
temperature after a minimum of 5 cycles. Press cancel key to end bake mode.
Temperature Adjustment
1. While in a non-cooking mode, press and hold the bake key for 6 seconds.
2. The current calibration offset (temperature adjustment) should appear in the
3. Use the number keypad (0-9) to enter the desired amount of adjustment (up to
4. Press the bake key to change the sign of the adjustment to a (-) if necessary. A
5. Once the desired adjustment (-35° to 35° F) has been entered, press the start
NOTE: Changing calibration affects all baking modes. The adjustments made will not
change the self-cleaning temperature.
• All uninsulated electrical terminals, connectors, heaters, etc. are adequately
spaced away from all metal parts and panels.
• All safety grounds (both internal and external) are correctly and securely
temperature display.
35°F).
positive adjustment will not display a sign.
key to accept the change or the cancel key to reject the change.
reassembled.
Probe circuit to case ground
900 ± 13.6 (482 ±7.5)
550 ± 8.2 (288 ± 4.5)
650 ± 9.6 (343 ± 5.3)
250 ± 4.4 (121 ± 2.4)
350 ± 5.4 (177 ± 3.0)
450 ± 6.9 (232 ± 3.8)
Open circuit/infinite resistance
2697 ± 24.4
2237 ± 18.5
NOTE:
Door Closed
Oven Lamps ON
Warming Drawer
X=Circuit
Contacts Closed
Door Open XO
1654 ± 10.8
1852 ± 13.5
2047 ± 15.8
Unlocked
Locked
1453 ± 8.9
Clean
Temperature °F (°C)
75 ± 2.5 (24 ± 1.3)
32 ± 1.9 (0 ± 1.0)
RTD SCALE
Resistance (ohms)
1000 ± 4.0
1091 ± 5.3
Conv Bake
Bake/Time Bake
orB
F95
F91
F90
F68
F66
F65
F64
F60
F51
F50
F42
F31
F17
F18
F30
Resistance Temperature Detector Scale
Open oven sensor probe
circuit.
Shorted oven sensor probe
circuit.
EOC internal software
Keyboard short circuit or
High voltage condition. L1 or
L2 may be crossed with
Neutral on incoming PS.
Door lock motor or latch
circuit failure.
If lock motor runs:
1. Test continuity of wiring between EOC and lock switch on lock motor assy. Repair if needed.
2. Advance motor until cam depresses the plunger on lock motor switch. Test continuity of switch contacts. If switch is open replace
lock motor assembly.
3. If motor runs and switch contacts and wiring harness test correctly, replace the EOC.
If lock motor does not run:
1. Test continuity of lock motor windings. Replace lock motor assembly if windings are open.
2. Test lock motor operation by using a test cord to apply voltage. If motor does not operate, replace lock motor assy.
3. If motor runs with test cord, check continuity of wire harness to lock motor terminals. If harness is good replace the EOC.
1. Verify proper incoming line voltage and polarity of L1, L2 and Neutral power supply connections at range terminal block.
2. If power supply voltage and polarity are correct, replace EOC.
internal EOC failure.
EOC internal power supply
failure.
1. Test keyboard circuits using test matrix. Replace touch panel if defective.
2. If keyboard circuits check correctly, replace the EOC
Disconnect power, wait 30 seconds and reapply power. If fault returns upon power-up, replace EOC.
Time Base failure. The EOC
cannot determine if
connected to 50Hz or 60Hz
power supply.
Confirm that range is connected to proper power source (50Hz or 60Hz). Generators or other portable power supplies and solar grids, etc.,
may not provide proper power supply. If power source is correct, replace the EOC.
EOC oven temperature.
Higher than normal
temperature detected on the
EOC board.
1. Verify proper assembly of backguard panel. Check for damaged or loose panels, brackets, endcaps, etc.
2. Check for blocked ventilation slots in control panel rear cover.
3. Inspect oven vent for proper assembly and air flow.
4. Verify operation of cooling fan (if present).
configuration error.
Internal signal voltage error.
Display communication error.
Disconnect power, wait 30 seconds and reapply power. If fault returns when power is reapplied, replace EOC.
Usually this failure code would only appear if the EOC has been replaced with an incorrect version. Verify that the correct replacement
part number is being used.
resistance does not match the RTD chart, replace RTD sensor probe. Check sensor wiring harness between EOC and sensor probe
connector.
2. (F31) Check resistance at room temperature. If less than 500 ohms, replace RTD sensor probe. Check for shorted sensor probe
harness between EOC and probe connector. If resistance is correct, replace the EOC.
EOC Internal hardware error
of failure.
3. If keyboard circuits check correctly, replace EOC.
Disconnect power, wait 30 seconds and reapply power. If fault returns upon power-up, replace EOC.
1. (F30) Check resistance at room temperature and compare to RTD Sensor resistance chart. If resistance is correct replace the EOC. If
Electronic Oven Control Fault Code Descriptions
Fault
F12
F13
F14
Keyboard tail failure.
EOC Internal software error
or failure.
Disconnect power, wait 30 seconds and reapply power. If fault returns upon power-up, replace EOC.
1. Check/reseat ribbon harness connections between keyboard touch panel and EOC.
2. Test keyboard circuits using test matrix (below). Replace touch panel if defective.
F11
Shorted keypad or selector
switch.
1. Reset power supply to range - Disconnect power, wait 30 seconds and reapply power.
2. Check/reseat ribbon harness connections between touch panel and EOC.
3. Test keyboard circuits using test matrix. Replace touch panel if defective.
4. If keyboard circuits check correctly, replace the EOC.
cavity.
2. Disconnect power from the range, wait 30 seconds and reapply power. If oven continues to heat when the power is reapplied, replace
the EOC. NOTE: Severe overheating may require the entire oven to be replaced should damage be extensive.
3. If temperature sensor probe circuit is good but fault code remains when oven is cold replace the EOC.
If Oven is overheating:
1. If oven is severely overheating/heating when no cook cycle is programmed, test oven temperature sensor probe circuit resistance
using the RTD scale found in the service tech sheet. Also verify that the temperature sensor probe in properly installed in the oven
Code
F10
Runaway temperature.
Oven heats when no cook
cycle is programmed.
2. Replace probe or repair wiring connections if defective.
Likely failure
condition/cause
If Oven is cold:
1. If fault code is present with cold oven, test oven temperature sensor probe circuit resistance. Use RTD scale found in the tech sheet.
O =
Circuit
Contacts
Open
*
=
Alternates
with Bake Element
†
= During Preheat ◊ = Cycles as Needed
X◊
OX
X
X◊
◊
L1 to
Broil
X*
X* X X X
Motor
Latch
L1 to
Fan
X† X†
Element
L2 Out
X
Drawer
Element
Lamps
COM-NO
Door
EOC Relays - ES1030 Oven Control
Conv
L1 to
Bake
Heang
Conv.
L1 to
L2 In to
Warming
L1 to
(Electric)
Catalyst
L1 to
Oven
L1 to
Contacts
Switch
Door
XgnikcolnU
XgnikcoL
XXli
XX*X
Suggested Corrective Action
L1 to
Bake
X
X◊