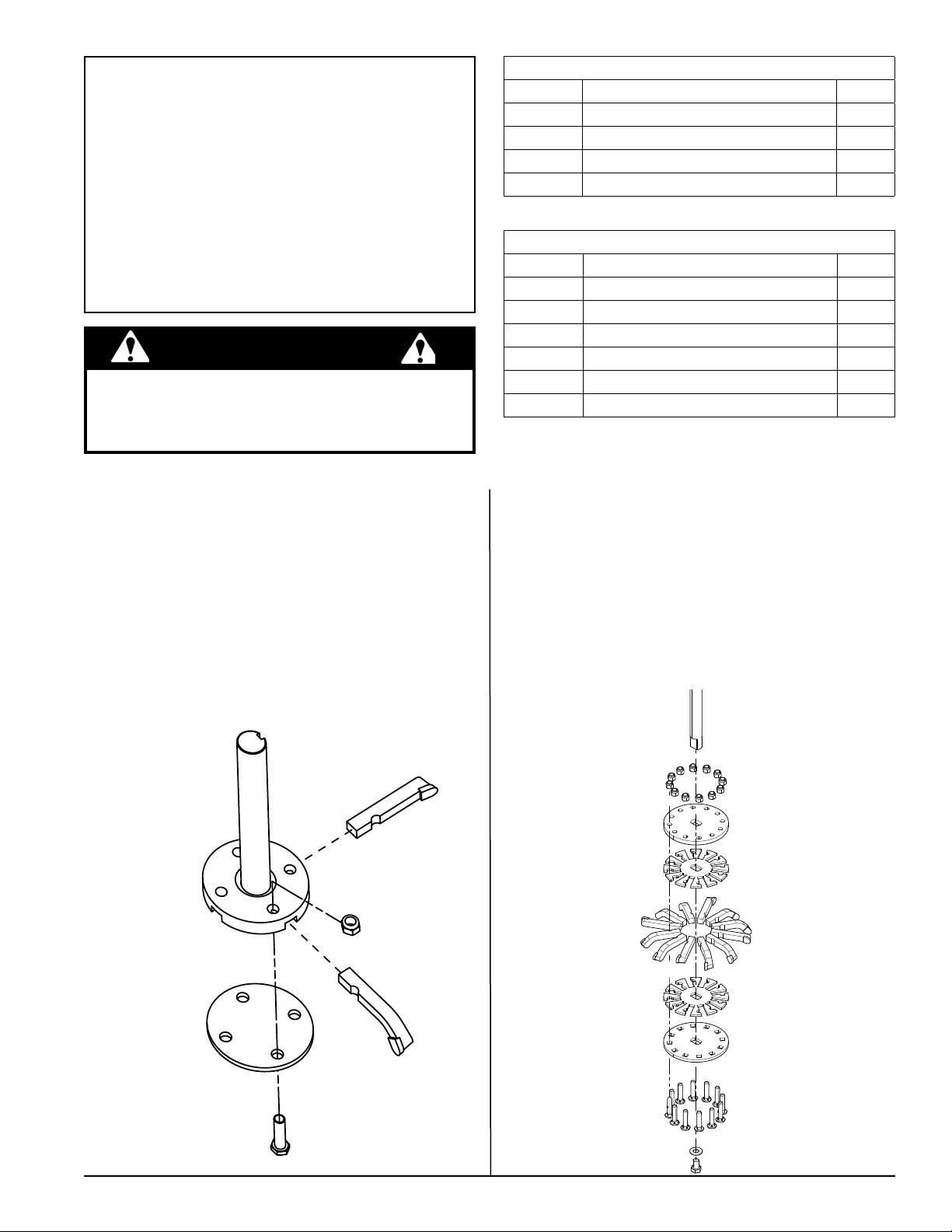
Instructions
SUBJECT: CUTTER TEETH
REPLACEMENT KITS, #71445 AND
4 BLADE CUTTER REPLACEMENT KIT (PN 71445)
PART NO. DESCRIPTION QTY
16687 STUMP CUTTER TEETH, STRAIGHT 2
16688 STUMP CUTTER TEETH, RH 2
15141 BOLT, 3/8 X 1-3/4 GR5 HCS ZP 4
15047 NUT, 3/8” CENTERLOCK ZP 4
#76292-00
FITS MODELS: STUMPGRINDERS
WARNING
Before inspecting or servicing any part of this machine,
shut off power source, remove key, disconnect the
battery cables and make sure all moving parts have
come to a complete stop.
These instructions will describe how to replace cutter teeth on a stumpgrinder.
SERIAL NUMBERS: 0 - 805549
(4 TEETh)
Remove cutting teeth from spindle by removing the 1.
bottom disk and the four (4) 3/8" nylock nuts. Refer to
diagram below.
Replace teeth with new teeth from the kit, using the 2.
new hardware.
12 BLADE CUTTER REPLACEMENT KIT (PN 76292-00)
PART NO. DESCRIPTION QTY
16687 STUMP CUTTER TEETH, STRAIGHT 4
16688 STUMP CUTTER TEETH, RH 8
15059 BOLT, 3/8 X 1-3/4 GR5 CARR BLT ZP 12
15388 NUT, 3/8” NE NYLOCK ZP 12
15762-00 WASHER, 1/2 HI-STRENGTH SAE ZP
15413 BOLT, 1/2-20 X 3/4” GR5 HHCS NF ZP
SERIAL NUMBERS: 810639 - CURRENT
(12 TEETh)
Remove cutting teeth from spindle by removing the 1.
bottom disk, the twelve (12) 3/8" nylock nuts, and the
bottom 1/2" bolt. Refer to diagram below.
Replace teeth with new teeth from the kit, using the 2.
new hardware. Install the four (4) straight cutter teeth
in every third slot (90º apart) and the eight (8) curved
teeth between them.
1
1
Instruction Sheet
PN 71665
Rev. 092110
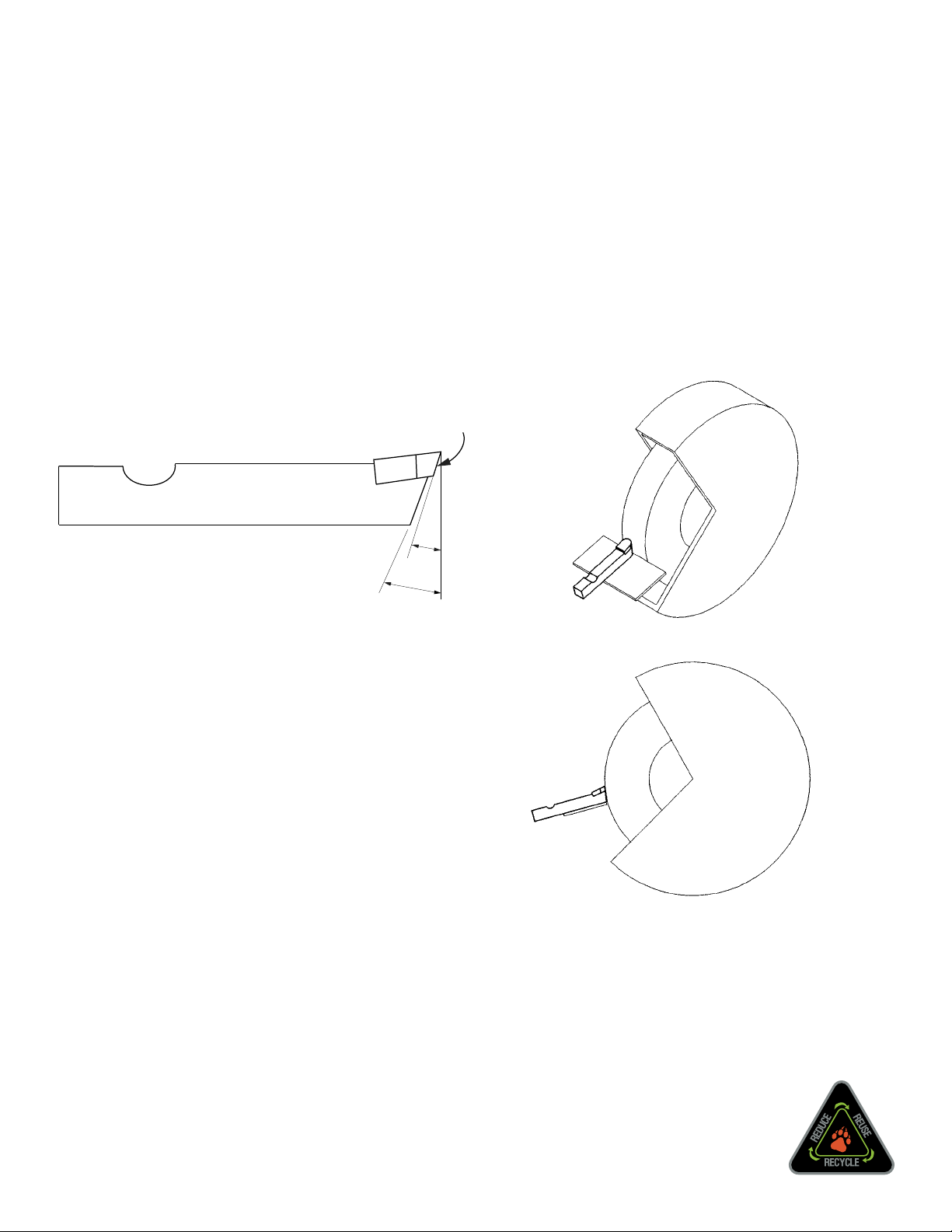
15°
11 °
Sharpen
this surface
CUTTING TEETh MAINTENANCE
The carbide cutting teeth stay sharp for approximately two to
eight hours of operation. A person familiar with sharpening
carbide should use the following instructions to sharpen the
cutting teeth when they become dull.
Grind teeth to sharpen, maintaining original angles. •
Duplicate all clearance and relief angles. The cutting
teeth last longer if the original contour of the tip is
maintained as closely as possible during grinding. Be
sure to leave adequate steel to support the carbide (see
below).
Dry grinding is suggested when sharpening to reduce •
the chance of cracking from insufficient coolants. Dry
grinding also allows better visibility and longer wheel life
due to better grinding action control.
Use a silicon carbide grinding wheel for the carbide •
portions of the teeth. Grinding the steel portions of the
teeth with a carbide wheel is possible, but the wheel
lasts longer if an aluminum oxide wheel is used for the
steel portions. The following wheels are recommended:
- Silicon carbide 60 grit for carbide.
- Aluminum oxide 24 grit for steel.
Move cutting teeth constantly when in contact with the •
grinding wheel surface to reduce heat concentration,
which may damage the teeth. This method will reduce
uneven wheel wear. Refer to diagram below.
Never place the cutting teeth in water immediately after •
grinding; the carbide tip may crack. Carbide is many
times harder than steel, but does not have the same
thermal characteristics.
EChO BEAR CAT
www.bearcatproducts.com
237 NW 12th Street, West Fargo, ND 58078-0849
Phone:701.282.5520•TollFree:800.247.7335•Fax:701.282.9522
E-mail:service@bearcatproducts.com•sales@bearcatproducts.com