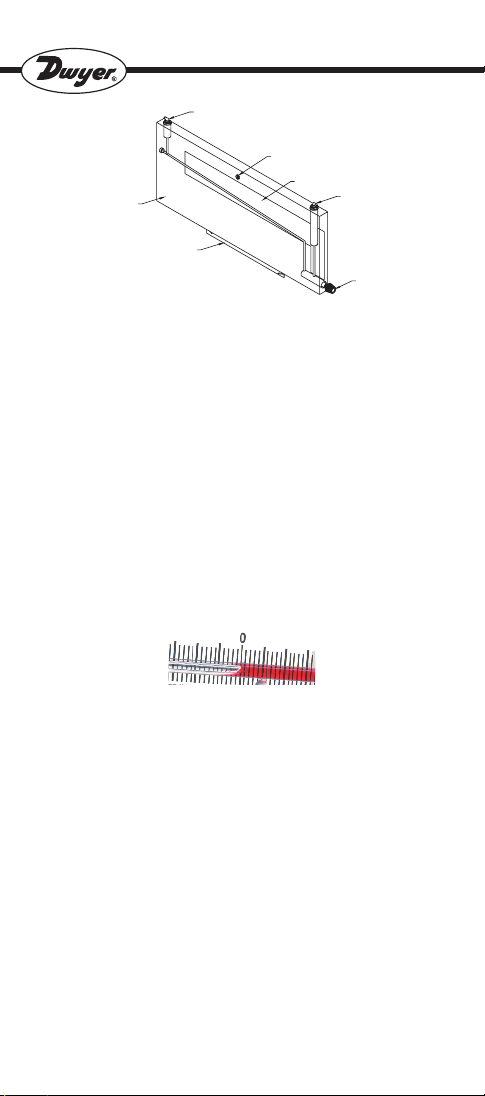
ulletin D-4
B
Series 424 Stationary Gage
perating Instructions and Parts List
O
Parts list. Contact factory for ordering information.
1) Gage body, 5˝ or 10˝ range
2) Molded Nylon Connector –
Rapid shut off type
3) Scale, 5˝ or 10˝ range
4) Mounting
5) Fluid level adjustment
assembly
1. Mount Gage securely on a vertical surface, avoiding excessive heat.
(Temperatures over 150ºF (66ºC), will damage gage). Level gage
approximately by swinging gage about top center mounting screw
and locate bottom bracket screws in center of slot.
2. Turn connectors counter clockwise 1/2 to 3/4 turns, thus venting gage
to atmosphere.
3. Center bubble between guide lines on spirit level by swinging about
top center mounting screw and tighten bottom bracket screws.
4. Turn fluid level adjustment knob to set the meniscus of the fluid
column at zero, as shown below.
Align fluid meniscus and the reflected image to eliminate parallax error.
6) Gage leveling bracket
7) Vinyl tubing 3/16˝ I.D. 3 ft. (not
shown)
8) 1/8˝ NPT Tube Adapter
(not shown)
9) 1 oz. bottle gage fluid
(not shown)
5. Add or remove fluid as necessary.
6. Use left hand gage connection for plus (above atmospheric)
pressures. Connect to right side for minus (below atmospheric)
pressures. Connect to both sides for differential pressures, as with a
Pitot tube.
CAUTION:
Use only Dwyer gage fluid. See gage scale plate for proper specific
gravity. Clean only with mild soap and water. Strong liquid soaps and other
fluids or cleaning agents may damage the gage. Maximum pressure 100
psi.
AIR VELOCITY
The total pressure of an air stream flowing in a duct is the sum of the static
or bursting pressure exerted upon the sidewalls of the duct and the impact
or velocity pressure of the moving air. Through the use of a Pitot tube
connected differentially to a manometer, the velocity pressure alone is
indicated and the corresponding air velocity determined.
DWYER INSTRUMENTS INC.
MICHIGAN CITY, IN 46360 U.S.A.
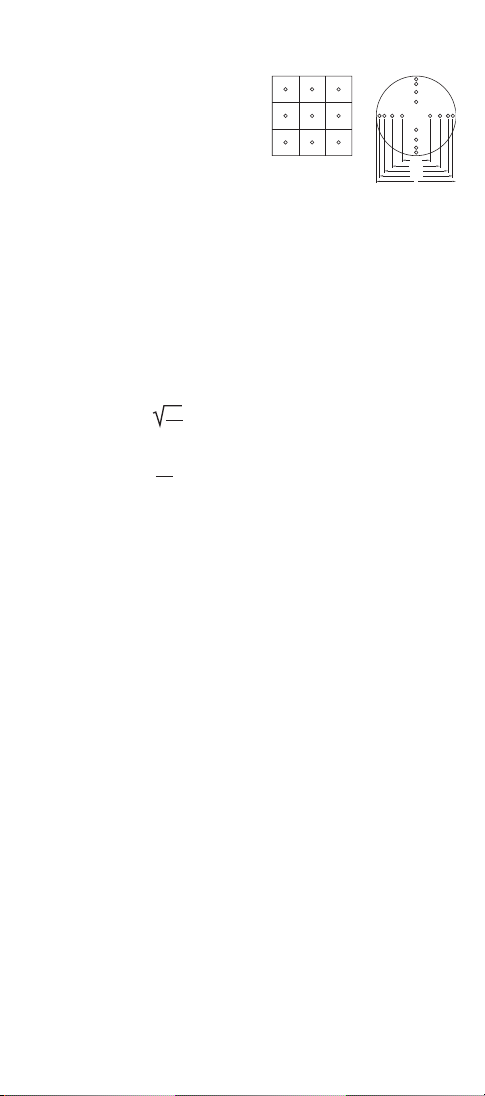
For accuracy of plus or minus 2%, as in laboratory applications, extreme
are is required and the following precautions should be observed:
c
1. Duct diameter 4˝ (8.64 mm) or greater.
2. Make an accurate traverse per sketch
at right and average the readings.
3. Provide smooth, straight duct sections
0 diameters in length both upstream
1
and downstream from the Pitot tube.
. Provide an egg crate type straightener
4
upstream from the Pitot tube.
n making an air velocity check, select a location as suggested above,
I
connect tubing leads from both Pitot tube connections to the manometer
nd insert in the duct with the tip directed into the air stream. If the
a
manometer shows a minus indication reverse the tubes. With a direct
reading manometer, air velocities will now be shown in feet per minute. In
other types, the manometer will read velocity pressure in inches of water
and the corresponding velocity will be found from the curves on the Dwyer
website or Dwyer catalog. If circumstances do not permit an accurate
traverse, center the Pitot tube in the duct, determine the center velocity
and multiply by a factor of .9 for the approximate average velocity. Field
tests run in this manner should be accurate within plus or minus 5%.
The velocity indicated is for dry air at 70°F (21.3°C), 29.9” Barometric
Pressure and a resulting density of .075#/cu. ft. For other variations from
these conditions, corrections may be based upon the following data:
Air Velocity = 1096.2 P
V
= velocity pressure in inches of water; D= Air density in #/cu. ft.
where P
Air Density = 1.325 x P
where P
B
Temperature (indicated temperature °F plus 460)
Flow in cu. ft. per min. = Duct area in square feet x air velocity in ft. per
minute.
STATIC PRESSURE
In checking inlet and discharge fan and blower pressures, balancing
ventilation and dust collection systems, checking exhaust systems and
similar installations, air velocities above 700 ft. per min. (12.81 kms/hr)
can cause an appreciable error. It is recommended that the static
connection of the Pitot tube or a static pressure tip be used. In using the
static pressure tip or Pitot tube, the tip should be directed into the air
stream. For permanent installation, static pressure tips are recommended.
If not available, make connections enter the duct perpendicular to the air
stream and finish off flush and smooth on the inside.
FURNACE DRAFT
Connect the terminal tube to the minus pressure gage opening and insert
it into the combustion chamber for over fire draft reading. If a drilled port
is not available insert through fire door but seal the crack. For last pass or
smoke pipe draft, connect into the breeching on the furnace side of any
draft control or damper. To determine draft loss through the furnace, make
connection as indicated for smoke pipe draft and add a second tube,
connecting the manometer differentially to the combustion chamber.
AIR FILTER TEST
To determine the pressure drop across an air filter, connect the
manometer differentially with one tubing from the downstream or blower
side of the filter to the right hand or minus pressure gage connection. Run
the second tubing from the upstream side of the filter to the other gage
connection. Use static pressure tips if available, with the tips directed into
the air stream, to eliminate possibility of error due to air velocity. Read the
pressure drop across the filter in inches of water and follow the filter
manufacturer’s recommendations for filter cleaning or replacement.
= Barometric Pressure in inches of mercury; T = Absolute
V
D
B
T
DWYER INSTRUMENTS INC.
MICHIGAN CITY, IN 46360 U.S.A.
©Copyright 2013 Dwyer Instruments Inc. Printed in U.S.A. 5/13 FR# 34-440184-00 Rev. 5