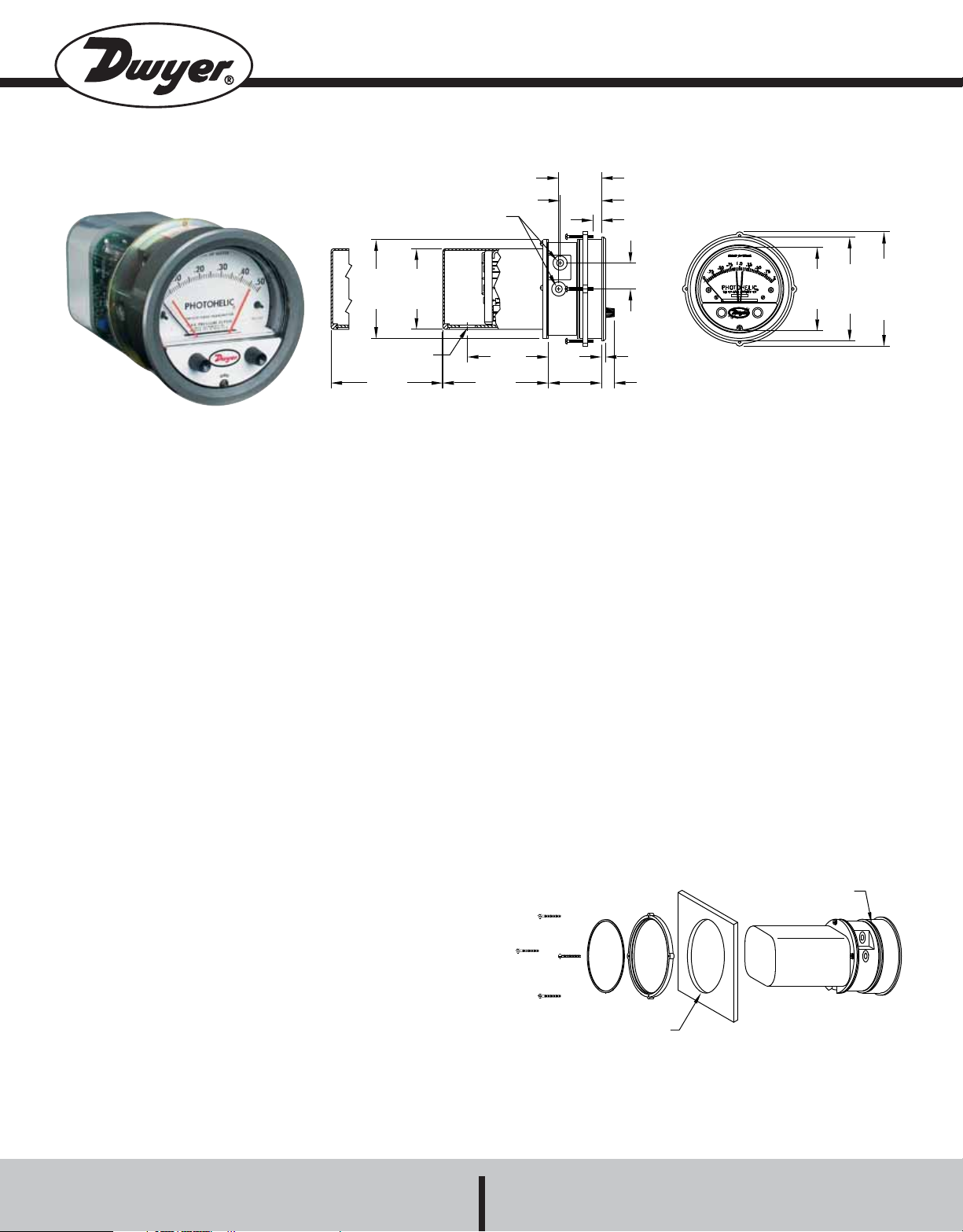
SERIES 3000 SGT PHOTOHELIC
1/8 NPT FEMALE PNEUMATIC TAPS
2-1/16
[52.39]
2
[50.80]
PANEL 5/8 [15.88] MAX
1-1/4
[31.75]
3/16
[4.76]
5/8
[15.88]
2-1/2
[63.50]
3-7/8
[98.43]
5-1/8
[130.18]
4-3/8
[111 .13 ]
HOUSING REMOVAL
3/4 [19.05]
CONDUIT OPENING
Ø4-3/4
[120.65]
FLANGE
3-7/8
[98.43] SQ
HOUSING
Ø4
[101.60]
FACE
5
[127.00]
0.D.
BEZEL
5-1/2
[139.70]
O.D.
MOUNTING
RING
SNAP RING GROOVE
Ø4-3/4 [120.65]
MOUNTING HOLE
®
Bulletin B-36A
DIFFERENTIAL PRESSURE SWITCH/GAGE TRANSMITTER
Specifications – Installation and Operating Instructions
Figure A
The Series 3000 PHOTOHELIC®SGT is a versatile 3-in-1 instrument combining a
time-proven Magnehelic
switches and a 4-20 mA pressure transmitter. It is designed to measure and control
positive, negative or differential pressure of air or other non-combustible, noncorrosive gases. Gage reading is unaffected by switch or transmitter operation.
Switch set points are easily adjusted with knobs located on gage face. Applied
pressure and switch set points are fully visible at all times. Deadband is one pointer
width, less than 1% of full scale. Each set point controls a DPDT relay and both can
be interlocked to provide variable deadband control. The 2-wire transmitter
operates independently, driven by a separate external 10-35 VDC power supply.
Separate zero and span potentiometers are provided inside the rear electronics
package for easy field adjustment.
PHYSICAL DATA
Ambient Temperature Range: 20 to 120˚F (-6.7to 49˚C).
Maximum Pressure: 2 psi (13.8 kPa) for ranges up to 5˝ w.c.; 5 psi (35 kPa) for
ranges 6, 10˝ w.c.; 10 psi (69 kPa) for ranges 20, 30˝ w.c.; 25 psi (170 kPa) for
above ranges.
Accuracy: ±2% of full scale at 70˚F (21.1˚C) (3% on -0).
Pressure Connections: 1/8˝ NPT(F).
Case Finish: Baked dark gray epoxy enamel.
Conduit Opening: 3/4˝.
Standard Accessories: (2) 3/16˝ tubing to 1/8˝ NPT brass adapters for rubber or
vinyl tubing, (1) mounting ring. (1) snap ring, (4) 6-32 x 2˝ mounting screws,
instructions.
Compatibility: Use only with air or other non-combustible, non-corrosive gases.
Weight: 4 lb, 12oz (2.15 kg).
ELECTRICAL SPECIFICATIONS (Switches)
Power Supply: 117 VAC.
Current Consumption: 5 watts average.
Contact Rating: 10A @ 24 VDC or 120 VAC, 6A @ 240 VAC.
®
differential pressure gage, low/high limit pressure
INSTALLATION
1. Location: Select a clean, dry, vibration-free location where ambient
temperatures will be between 20 and 120˚F (-6.7 and 49˚C). Tubing supplying
pressure to the instrument can be practically any length but long runs will
increase response time slightly.
2. Position: The PHOTOHELIC
vertical plane. Operation at other angles may affect accuracy and/or require
zero adjustment. Most models can be specially calibrated at the factory for
other positions if specified at time of ordering. Ranges below 1˝ w.c. must be
used only with scale vertical.
3. Mounting: Normal mounting is flush or through panel as shown in Figure B.
Allow 4-3/8˝ space behind the unit for electrical enclosure removal. Make 4-3/4˝
diameter hole in panel. When installing multiple units, it may be preferred to
obtain a Model 730E, 120 mm chassis punch as manufactured by Greenlee
Tool Co. and available from your machine tool distributor.
Insert PHOTOHELIC
case from rear and seat the snap ring in its groove. Thread the (4) 6-32x2˝
machine screws into mounting ring, back it against snap ring and tighten
screws to back of panel. An alternative to flush mounting is the optional A-371
Surface Mounting Bracket. Unit is mounted in this bracket as described above
and bracket is then surface mounted. Contact factory for details.
®
SGT is factory calibrated for use with scale in a
®
SGT from front of panel, slip the mounting ring over the
ELECTRICAL SPECIFICATIONS (Transmitter)
Power Supply: 10.0 to 35 VDC.
Output Signal: 4-20 mA DC, 2-wire (limited at 38 mA).
Loop Resistance: 0-1250 ohms.
Current Consumption: 38 mA DC, maximum.
Span and Zero Adjustment: Multi-turn potentiometers, internally accessible
Thermal Errors: ±1% per 50˚F typical
Warm-Up Time: 10 minutes.
DWYER INSTRUMENTS, INC.
P.O. BOX 373 • MICHIGAN CITY, INDIANA 46361 U.S.A.
Figure B
Phone: 219/879-8000 www.dwyer-inst.com
Fax: 219/872-9057 e-mail: info@dwyer-inst.com
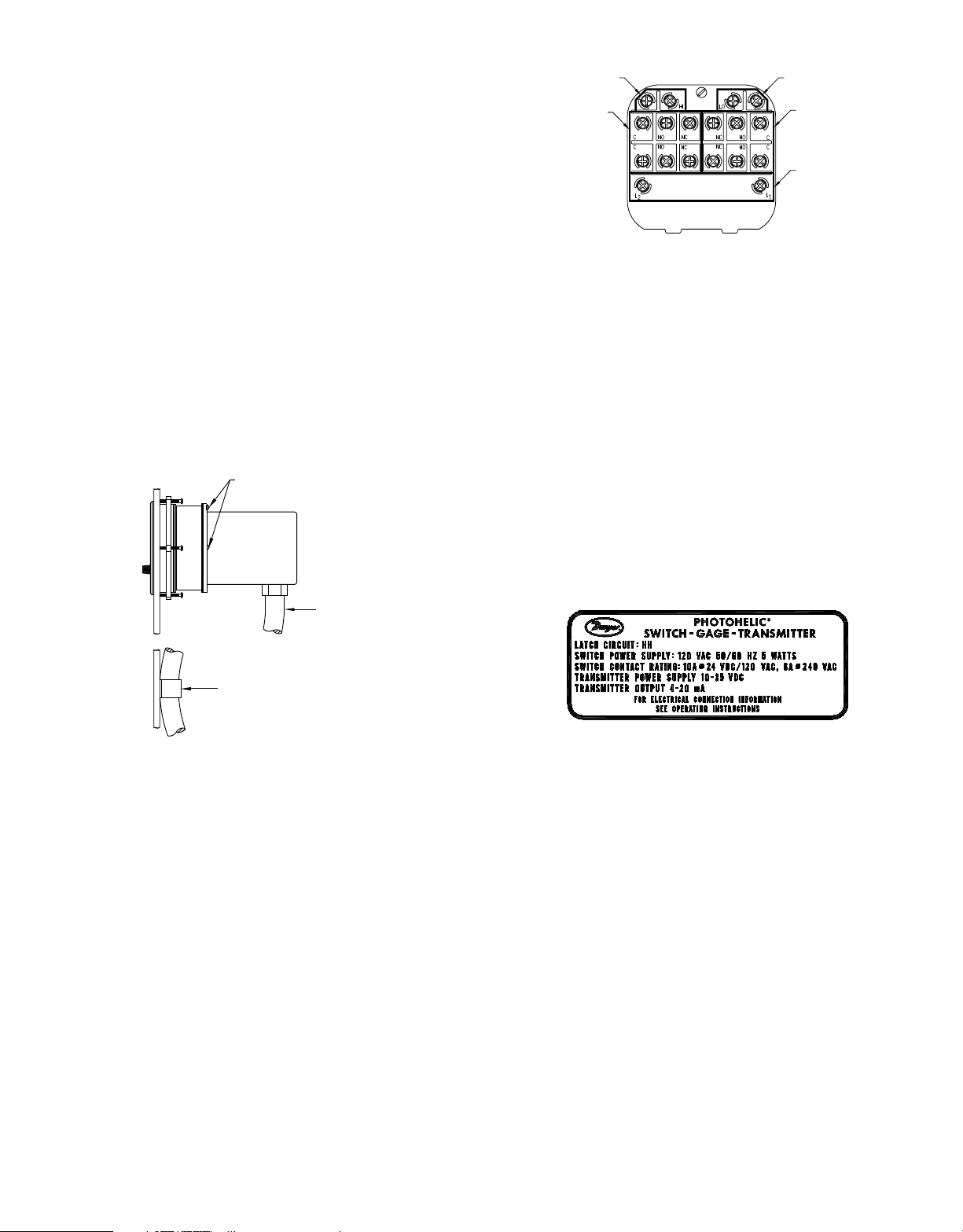
4. Zeroing & Pneumatic Connections: After unit is installed in its final mounting
COVER MOUNTING
SCREWS
FLEXIBLE CONDUIT
SUPPORT CONDUIT
FROM PANEL
SECTION B
SECTION A
SECTION C
SECTION D
SECTION E
position, use the screw at bottom of front cover to adjust pointer for exact zero
reading. This must be done with both pressure ports open and vented to
atmosphere.
(A) For positive pressure, connect tubing to HIGH PRESSURE port and vent LOW
PRESSURE port to atmosphere.
(B) For negative pressure (vacuum), connect tubing to LOW PRESSURE port and
vent HIGH PRESSURE port to atmosphere.
When either port will be left open to atmosphere, we suggest installation of
optional A-331 Filter Vent Plug to keep gage interior clean.
(C) For differential pressure, connect higher pressure to HIGH PRESSURE port
and lower pressure to LOW PRESSURE PORT.
NOTE: If the PHOTOHELIC
®
SGT is on over-pressured beyond its full scale
range, pointer could jump from full scale back to zero and remain there until the
excess pressure condition is relieved. Users should be aware that this condition
would cause a false indication of zero pressure and subsequently affect setpoints and transmitter output signal.
SWITCH/GAGE WIRING CONNECTIONS
To make electrical connections, remove the (3) cover screws and slide cover off. All
wiring should be fed through flexible conduit attached to conduit opening at bottom
of electrical package. Conduit should be attached to the panel of other suitable
support to avoid excess strain on the instrument. See Figure C.
Figure D
CAUTION: Do not apply electrical current to terminals in Sections B and C.
Separate Ground Wire attachment is provided for by a No. 6-32 screw on the
mounting bracket near the conduit opening.
Single Set-Point instruments are furnished with the right or high set-point
components and circuitry in place. These are connected to Sections A and B of
the terminal board. The left or low set-point components are omitted.
2. Circuit Style: The PHOTOHELIC
®
is available with several factory installed
optional internal circuits. They are identified as to style by a label shown in
Figure E. This label is mounted prominently on the terminal board of each
instrument. The letter H denotes a circuit in which the relay can be made to
latch or remain energized after pressure increase to its set-point.
The letter L denotes a circuit in which the relay can be made to latch or remain
de-energized after pressure decreases to its set-point. Two letters are required
to fully identify a dual set-point. Two letters are required to fully identify a dual
set-point unit. Thus, circuit style HH, which is standard, is a dual set-point circuit
which has provisions for latching on pressure increase to either set-point.
Single relay units are identified by the letters SR followed by H for the standard
unit or L for the special low latch unit. Units for use with other than standard 117
VAC will be so indicated on the label.
Figure C
1. Low/High Set-Point Wiring Connections
The rear terminal board contains connections for low and high set-points,
holding coil circuits and line power supply. Transmitter connections are located
behind this terminal board. See TRANSMITTER WIRING CONNECTIONS for
complete information.
Section A contains DPDT connections for the right or high set-point and Section
D contains identical connections for the left or low set-point.
Terminals in Section B are for control of the holding coil circuit for the right, high
set-point and Section C contains identical connections for the left, low set-point.
These holding coil circuits are typically used to allow latching set-points with
manual reset or for adjustable deadband operation with one set-point wired to
reset the other. See paragraphs 3 and 4 for details. Do Not Connect Line
Current to Sections B or C. Section E (L1 and L2) contains power supply
connections for the control unit transformer primary. The transformer in turn
supplies reduced voltage power for the LED, phototransistor, amplifier unit,
load relay pull-in and holding coils. Connections must always be made to this
section for the unit to operate. Standard units require 117 VAC but options are
available for other power sources. See label on terminal board for correct
voltage and circuit style.
2
Figure E
3. Dual Set Point Automatic Reset: Circuit Style HH is used for simple on-off
switching applications. To place in service, connect load circuits to the
appropriate terminals in Section A (Figure D) for the right set-point and Section
D for the left set-point. Note that the N.O. contacts are open when the gage
pressure pointer is to the left of the set-pointers. No connections are necessary
in Sections B and C. Make external ground connections as required and
connect power to Section E for the control unit. To use circuit style LL for
automatic reset, a jumper wire must be installed between the upper and lower
terminals in Sections B and/or C.
4. Dual Set Point Manual Reset: Circuit Style HH may also be
used for manual reset applications where it is desired to have maintained
contact on either relay following pressure increase above its set-point. Load or
signal connections are made to the appropriate terminals in Sections A and D
(as in paragraph 3 above). Connect terminals in Sections B and C through
normally closed switches or push buttons as shown in Figure F. Use of “drycircuit” type switches such as Dwyer Instruments, Inc. Part No. A-601 with
palladium, gold, etc. or rotary wiping action type contacts is recommended.
Make external ground connections as required and connect power to Section
E for the control unit.
Circuit style LL is used for manual reset applications which require that contact
be maintained following pressure decrease below the set-point. Load
connections are made to the appropriate terminals in Sections A and D. A
normally open type manual reset switch such as Dwyer Instruments, Inc. Part
No. A-601 is connected to the terminals in Sections B and C. The circuit must
be reset or “armed” by momentarily closing the switch while the black pointer is
to the right of the set-point. From that point on, the circuit will latch on pressure
decrease below the set-point and remain latched on pressure increase until
manually reset with the optional switch.