
INSTRUCTION MANUAL
for
DODGE® USAF 200 Series
Direct Mount Pillow Blocks
WARNING: Because of the possible danger to persons( s) or property from accidents which may result from the improper
use of products, it is important that correct procedures be followed. Products must be used in accordance with the
engineering information specified in the catalog. Proper installation, maintenance and operation procedures must be
observed. The instructions in the instruction manuals must be followed. In spections should b e made as necessary to a ssure
safe operation under prevailing conditions. Proper guards and other suitable safety devices or procedures as may be
desirable or as may be specified in safety codes should b e provided, and are neither provided by Baldor Electric Company
nor are the responsibility of Baldor Electric Company. This unit and its ass ociated equi pment must be installed, adj usted and
maintained by qualified personnel who are familiar with the construction and operation of all equipment in the system and the
potential hazards involved. When risk to persons or property may be involved, a fails afe device must be an integral part of
the driven equipment beyond the speed reducer output shaft.
1
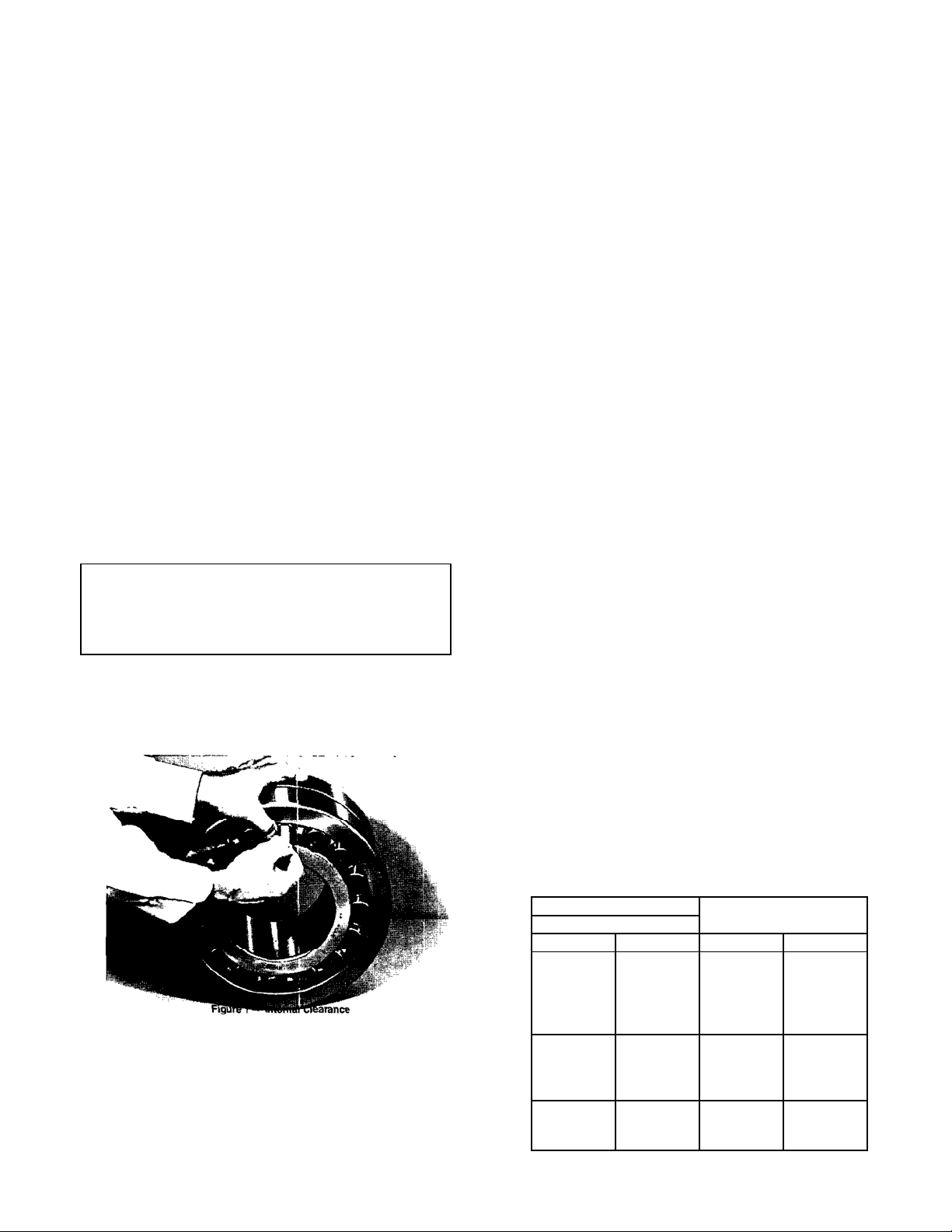
GENERAL INFORMATION
DODGE USAF bearings conform with all appropriate
AFBMA standards. They are available in either adapter or
direct mounting styles for 17/16" through 8”, and up to 220
mm diameter shafts. A wide variety of seals is available
including metallic LER, TRIPLE-TECT non-metallic with vring, Drop-in TRIPLE-TECT with neoprene v-ring, Auxiliary
Taconite, or Split non-metallic. TRIPLE-TECT is provided
as standard on complete assemblies. DODGE USAF
housings provide you with maximum application flexibility.
Cast-in dimples allow for easy field modification for vents,
lube ports and sensors. Oversized drains and an oil
equalization hole make USAF ready for circulating oil
systems off the shelf. For hostile environments, USAF
offers optional cast-closed end housings, stainless
hardware kits, and nylon coating. Complete installation,
maintenance, and modification instructions for direct
mounted units are provided in this manual. Modification
instructions are shown on Table 7.
INSPECTION
Inspect shaft. Ensure that the shaft is smooth, straight,
clean, and within commercial tolerances.
Inspect bearing. Do not allow bearing to be exposed t o
any dirt or moisture. Do not remove slushing compound as
it acts as both a protectant and lubricant and is also
compatible with standard greases.
WARNING
To ensure that drive is not unexpectedly started, turn off
and lock out or tag power source before proceeding.
Failure to observe these precautions could result in bodily
injury.
INSTALLATION
NOTE: Housing caps and bases are not
interchangeable; they must be matched with mating
half. Install non-expansion bearing first.
DIRECT MOUNTED BEARINGS
1. Measure the internal clearance of the bearing
before mounting. Place the bearing in a upright position
as shown in Figure 1. Seat the inner ring and roller
elements by pressing down firmly on the inner ring bore
while rotating the inner ring a few times. Position the roller
assemblies so that a roller is at the top-most position on
both sides. For bore sizes above 6½” only, press these top
rollers inward ensuring contact with center guide flange.
Using a feeler gauge measure the cleara nce for both sides
by inserting as far as possible and sliding ove r top of roller
(Figure 1). Write down the measured clearance and
compare with specifications (Table A). NOTE: Do not
rotate bearing when moving feeler between roller and
outer ring.
NOTE: TRIPLE TECT™ seals are standard seals up to 10
(220 mm) bore. For assistance in installing seals use seal
instruction manual 499665 supplied with the seals.
2. Install the bearing parts in the following sequence:
(refer to the replacement parts drawing and table.)
a) V-ring Seal – Slide one of the V-ri ng seals onto the
shaft, making sure lip is toward the bearing. (NOTE:
Do not install V-ring seal on seal ring until housing cap
has been set in place and tightened.)
b) Seal Ring – Install a seal ring on shaft with largest
O.D. toward bearing.
c) Bearing – Make sure that the internal clearance has
been written down. Install bearing. Bearings with
cylindrical bore up to 2¾ (70 mm) may be cold
mounted on the shaft. Apply coat of light oil to the shaft
and bearing bore, then press the bearing o n by usi ng a
mechanical or hydraulic device or use the mounting
nut to drive the bearing onto the shaft.
Bearings with cylindrical bore above 2¾ (70 mm) are
heated for mounting on shaft. Bearings, heated in oil
between 200°F - 215°F, when still in a heated
condition, should have the bore wiped dry with a clean
cloth. The bearing should be rapidly pushed on the
shaft and positioned squarely against the shoulder. A
slight screwing motion during fitting facilitates the
mounting. It is advisable to use gloves. Large bearings
are generally handled with a hoist or crane.
For cylindrical bore direct mounted bearings, it is not
necessary to check internal clearance after mounting.
It is, however, important to verify the shaft diameters
(Tables 1 & 2) and to measure the unmounted internal
clearance to ensure conformance to specifications
(Table A).
Table A.
Radial Internal Clearance in Self-Aligning Roller
Bearings (Values in .0000 inches)
Bore Diameter
MM
Over Incl. Low High
14 24 14 18
24 30 16 22
30 40 18 24
40 50 22 30
50 65 26 36
65 80 32 44
80 100 39 53
120 140 57 75
140 160 65 87
160 180 71 95
180 200 79 103
200 225 87 114
With Cylindrical Bore
2

TABLE 1 – SHAFT B
EARING SEAT DIAMETERS FOR
CYLINDRICAL BORE MOUNTED PILLOW BLOCKS
Bearing Bore
Diameter
MM Inches Shaft Diameter (S-1) MEAN Shaft Diameter (S-1) MEAN
Nom. Max. Min. Max. Min. FIT Max. Min. FIT
75 2.9528 2.9522 2.9540 2.9532 .0011T 2.9543 2.9536 .0014T
80 3.1496 3.1490 3.1508 3.1500 3.1511 3.1504 .0015T
85 3.3464 3.3457 3.3179 3.3470 3.3484 3.3475
90 3.5433 3.5425 3.5447 3.5438 3.5452 3.5443
95 3.7402 3.7394 3.7416 3.7407 .0014T 3.7421 3.7412 .0019T
100 3.9370 3.9362 3.9384 3.9375 3.9389 3.9380
105 4.1338 4.1331 4.1353 4.1344 4.1358 4.1349
110 4.3307 4.3299 4.3321 4.3312 4.3326 4.3317
120 4.7244 4.7236 4.7258 4.7249 4.7263 4.7254
125 4.9212 4.9203 4.9229 4.9219 4.9235 4.9225
130 5.1181 5.1171 5.1197 5.1187 5.1203 5.1193
140 5.5118 5.5108 5.5134 5.5124 5.5140 5.5130
150 5.9055 5.9045 5.9071 5.9061 .0016T 5.9077 5.9067 .0022T
160 6.2992 6.2982 6.3008 6.2998 6.3014 6.3004
170 6.6929 6.6919 6.6945 6.6935 6.6951 6.6941
180 7.0866 7.0856 7.0882 7.0872 7.0888 7.0878
190 7.4803 7.4791 7.4821 7.4809 7.4829 7.4817 .0026T
200 7.8740 7.8728 7.8758 7.8746 .0019T 7.8772 7.8760 .0032T
220 8.6614 8.6602 8.6632 8.6620 8.6646 8.6634
These fits apply to roller bearings with inner ring rotation under radial and thrust loads.
Bearing Bore Diameter Normal Load High Load
Up to 220 mm P/C = 0.10 to 0.15 P/C>0.15
Where
P = Equivalent Dynamic Load on the Bearing (lbs.)
C = Basic Dynamic Load Rating of Bearing (lbs.)
TABLE 2 – TOLERANCE
Shaft Diameter (S-2 & S3)
Over Including Tolerance
2" (50 mm) 4" (100 mm) +.000" to -.004"
4" (100 mm) 6" (150 mm) +.000" to -.005"
Over 6" (150 mm) +.000" to -.006"
d. Lockwasher and Lo cknut – Install the lock-washer
with inner prong located in the keyway of the shaft and
pointing towards the bearing. Install locknut,
chamfered face toward bearing. Tighten locknut using
a spanner wrench.
Locate a lockwasher tab that aligns with a locknut slot
and bend tab into slot. If slot is past tab, then tighten,
not loosen, locknut to meet a washer tab.
Normal Load High Load
e. Seal Ring – Install second seal ring with large O.D.
toward locknut.
f. V-ring Seal – Slide second V-ring seal onto the
shaft, again making certain lip is toward bearing.
NOTE: Do not install V–ring seal on seal ring until
housing cap has been set in place and tightened.
Steps e. and f. are not necessary if pillow block
housing is a "cast closed end" style.
3. Remove any paint, dirt or burrs from the mating
surfaces of the housing halves. Thoroughly clean seal
grooves on both sides. Set lower half of housing on base
and apply oil to the bearing seats.
4. Apply grease to the bearing and seal rings. The
lubricant should be smeared between the rolling elements.
(See Grease Lubrication Section below.) This step and th e
first sentence of Step 8 do not apply for oil lubricated
bearings.
3