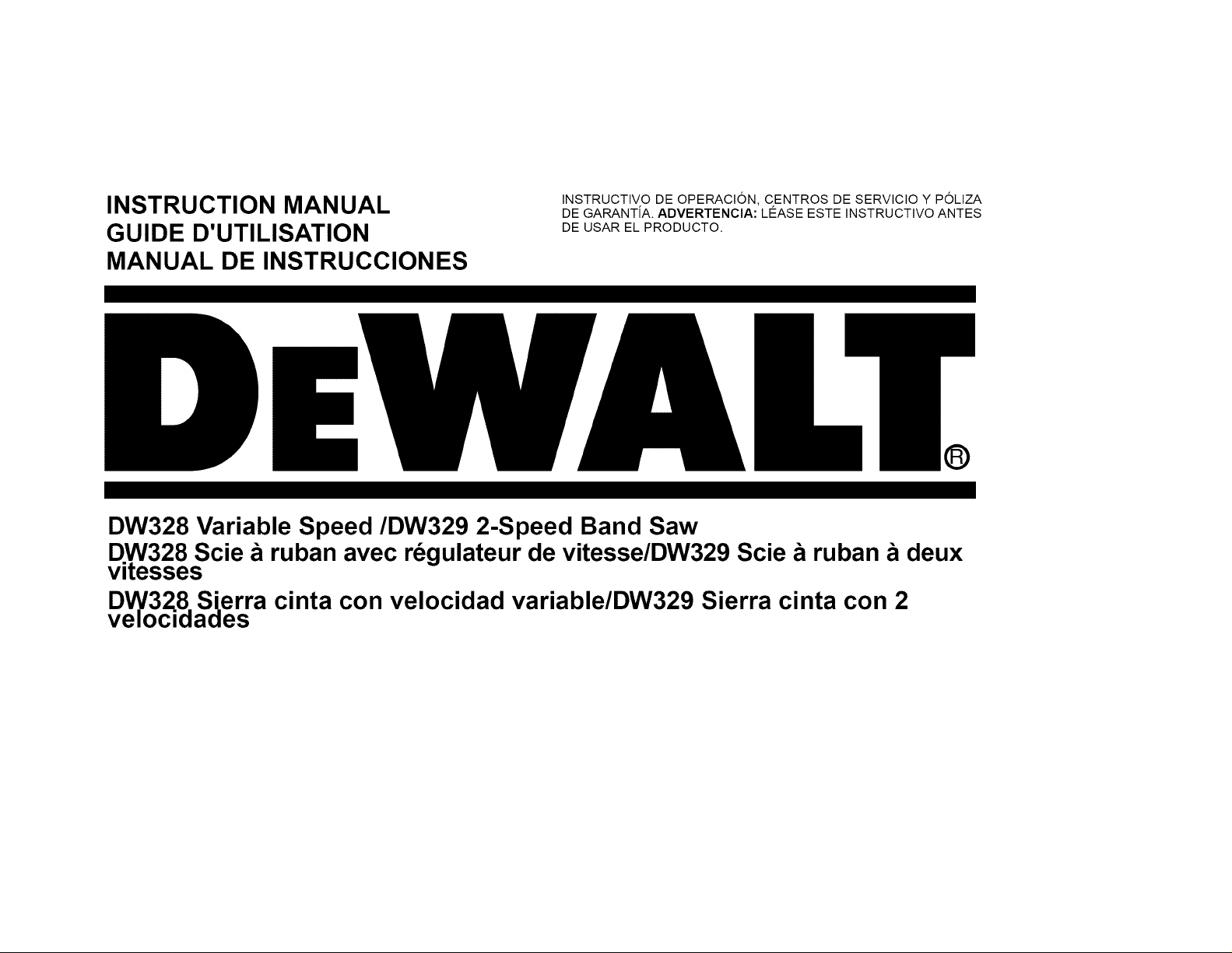
INSTRUCTION MANUAL
GUIDE D'UTILISATION
INSTRUCTIVO DE OPERACION, CENTROS DE SERVIClO Y POLIZA
DE GARANTiA. ADVERTENClA: LEASE ESTE INSTRUCTIVO ANTES
DE USAR EL PRODUCTO.
MANUAL DE INSTRUCCIONES
DW328 Variable Speed/DW329 2-Speed Band Saw
DW328 Scie _ ruban avec r_gulateur de vitesse/DW329 Scie _ ruban _ deux
vitesses
DW328 Sierra cinta con velocidad variable/DW329 Sierra cinta con 2
velocidades
®
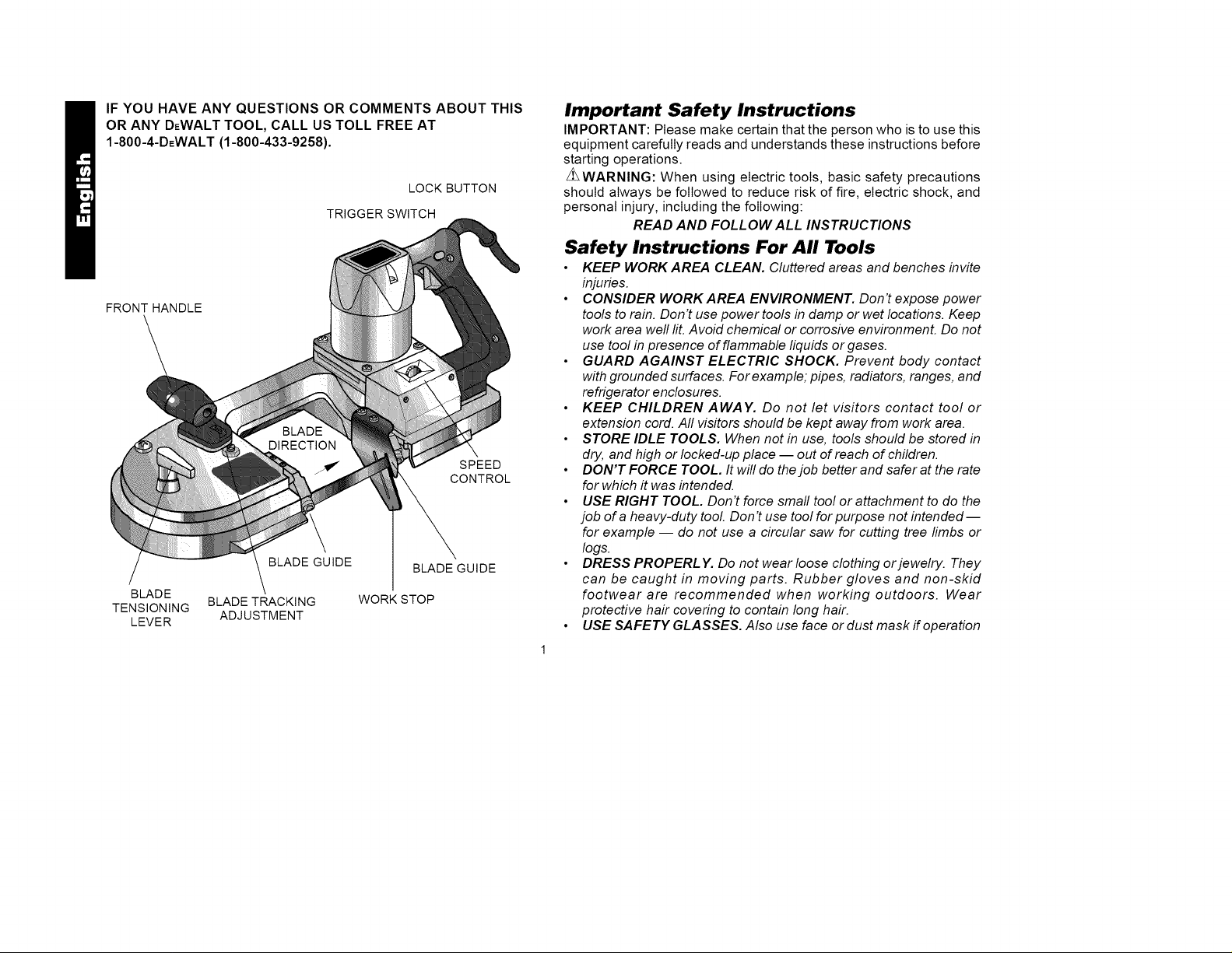
IF YOU HAVE ANY QUESTIONS OR COMMENTS ABOUT THIS
OR ANY DEWALT TOOL, CALL US TOLL FREE AT
1-800-4-DEWALT (1-800-433-9258).
LOCK BUTTON
TRIGGER SWITCH
FRONT HANDLE
SPEED
CONTROL
BLADE
TENSIONING
LEVER
BLADE GUIDE
BLADE TRACKING
ADJUSTMENT
WORK STOP
BLADE GUIDE
Important Safety Instructions
IMPORTANT: Please make certain that the person who is to use this
equipment carefully reads and understands these instructions before
starting operations.
Z_WARNING: When using electric tools, basic safety precautions
should always be followed to reduce risk of fire, electric shock, and
personal injury, including the following:
READ AND FOLLOW ALL INSTRUCTIONS
Safety Instructions For All Tools
• KEEP WORK AREA CLEAN. Cluttered areas and benches invite
injuries.
• CONSIDER WORK AREA ENVIRONMENT. Don't expose power
tools to rain. Don't use power tools in damp or wet locations. Keep
work area well lit. Avoid chemical or corrosive environment. Do not
use tool in presence of flammable liquids or gases.
• GUARD AGAINST ELECTRIC SHOCK. Prevent body contact
with grounded surfaces. For example; pipes, radiators, ranges, and
refrigerator enclosures.
• KEEP CHILDREN AWAY. Do not let visitors contact tool or
extension cord. All visitors should be kept away from work area.
• STORE IDLE TOOLS. When not in use, tools should be stored in
dry, and high or locked-up place -- out of reach of children.
• DON'T FORCE TOOL. It will do the job better and safer at the rate
for which it was intended.
• USE RIGHT TOOL. Don't force small tool or attachment to do the
job of a heavy-duty tooL Don't use tool for purpose not intended--
for example -- do not use a circular saw for cutting tree limbs or
logs.
• DRESS PROPERLY. Do not wear loose clothing or jewelry. They
can be caught in moving parts. Rubber gloves and non-skid
footwear are recommended when working outdoors. Wear
protective hair covering to contain long hair.
• USE SAFETY GLASSES. Also use face or dust mask if operation
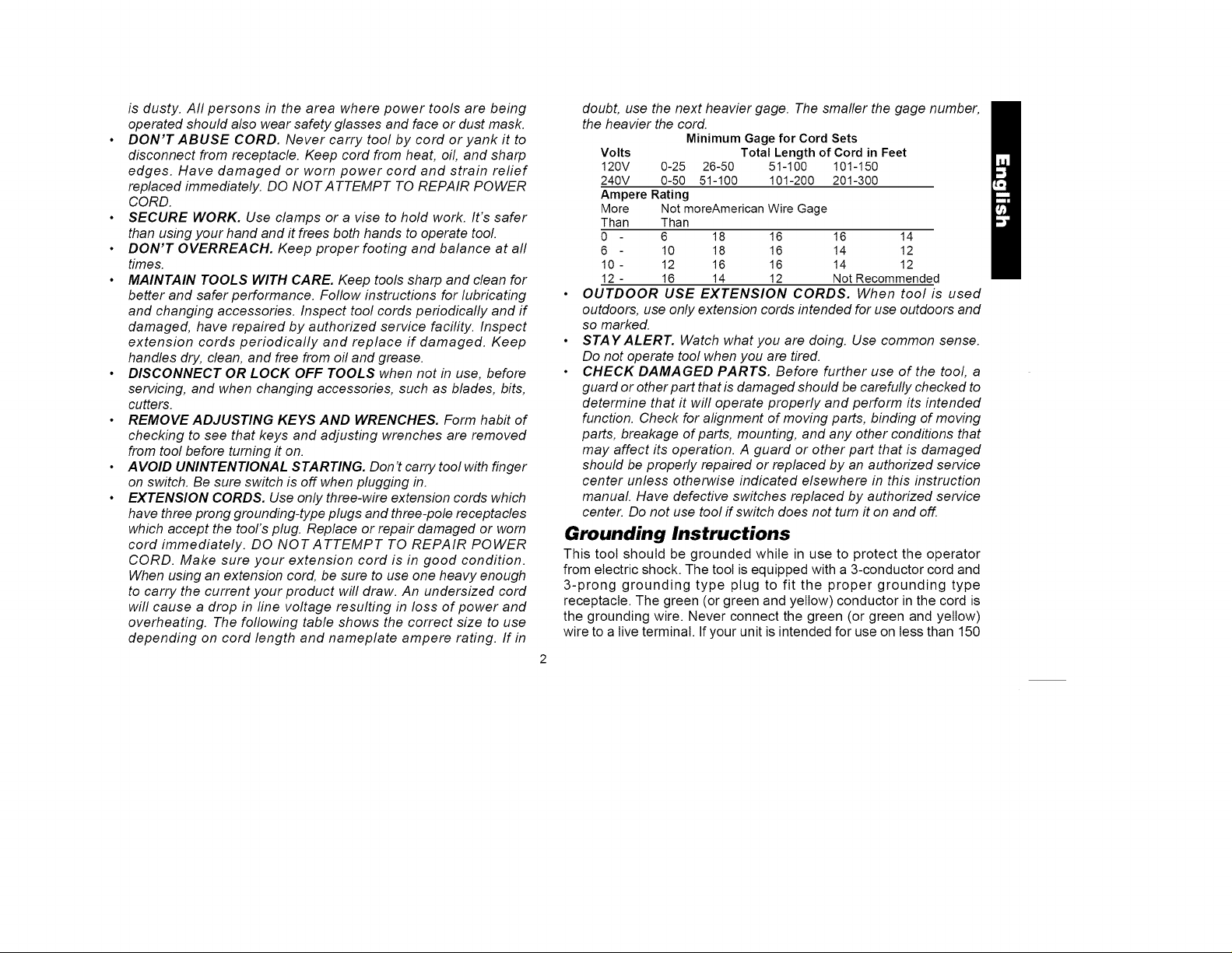
isdusty.Allpersonsintheareawherepowertoolsarebeing
operatedshouldalsowearsafetyglassesandfaceordustmask.
• DON'T ABUSE CORD. Never carry tool by cord or yank it to
disconnect from receptacle. Keep cord from heat, oil, and sharp
edges. Have damaged or worn power cord and strain relief
replaced immediately. DO NO TA TTEMPT TO REPAIR POWER
CORD.
• SECURE WORK. Use clamps or a vise to hold work. It's safer
than using your hand and it frees both hands to operate tool
• DON'T OVERREACH. Keep proper footing and balance at all
times.
• MAINTAIN TOOLS WITH CARE. Keep tools sharp and clean for
better and safer performance. Follow instructions for lubricating
and changing accessories. Inspect tool cords periodically and if
damaged, have repaired by authorized service facility. Inspect
extension cords periodically and replace if damaged. Keep
handles dry, clean, and free from oil and grease.
• DISCONNECT OR LOCK OFF TOOLS when not in use, before
servicing, and when changing accessories, such as blades, bits,
cutters.
• REMOVE ADJUSTING KEYS AND WRENCHES. Form habit of
checking to see that keys and adjusting wrenches are removed
from tool before turning it on.
• AVOID UNINTENTIONAL STARTING. Don't carry tool with finger
on switch. Be sure switch is off when plugging in.
• EXTENSION CORDS. Use only three-wire extension cords which
have three prong grounding-type plugs and three-pole receptacles
which accept the tool's plug. Replace or repair damaged or worn
cord immediately. DO NOT ATTEMPT TO REPAIR POWER
CORD. Make sure your extension cord is in good condition.
When using an extension cord, be sure to use one heavy enough
to carry the current your product will draw. An undersized cord
will cause a drop in line voltage resulting in loss of power and
overheating. The following table shows the correct size to use
depending on cord length and nameplate ampere rating. If in
doubt, use the next heavier gage. The smaller the gage number,
the heavier the cord.
Volts Total Lengthof Cord in Feet
120V 0-25 26-50 51-100 101-150
240V 0-50 51-100 101-200 201-300
Ampere Rating
More NotmoreAmerican Wire Gage
Than Than
0 - 6 18 16 16 14
6 - 10 18 16 14 12
10 - 12 16 16 14 12
12 - 16 14 12 Not Recommended
• OUTDOOR USE EXTENSION CORDS. When tool is used
outdoors, use only extension cords intended for use outdoors and
so marked.
• STAYALERT. Watch what you are doing. Use common sense.
Do not operate tool when you are tired.
• CHECK DAMAGED PARTS. Before further use of the tool, a
guard or other part that is damaged should be carefully checked to
determine that it will operate properly and perform its intended
function. Check for alignment of moving parts, binding of moving
parts, breakage of parts, mounting, and any other conditions that
may affect its operation. A guard or other part that is damaged
should be properly repaired or replaced by an authorized service
center unless otherwise indicated elsewhere in this instruction
manual Have defective switches replaced by authorized service
center. Do not use tool if switch does not turn it on and off.
Minimum Gage for Cord Sets
Grounding Instructions
This tool should be grounded while in use to protect the operator
from electric shock. The tool is equipped with a 3-conductor cord and
3-prong grounding type plug to fit the proper grounding type
receptacle. The green (or green and yellow) conductor in the cord is
the grounding wire. Never connect the green (or green and yellow)
wire to a live terminal. If your unit is intended for use on less than 150
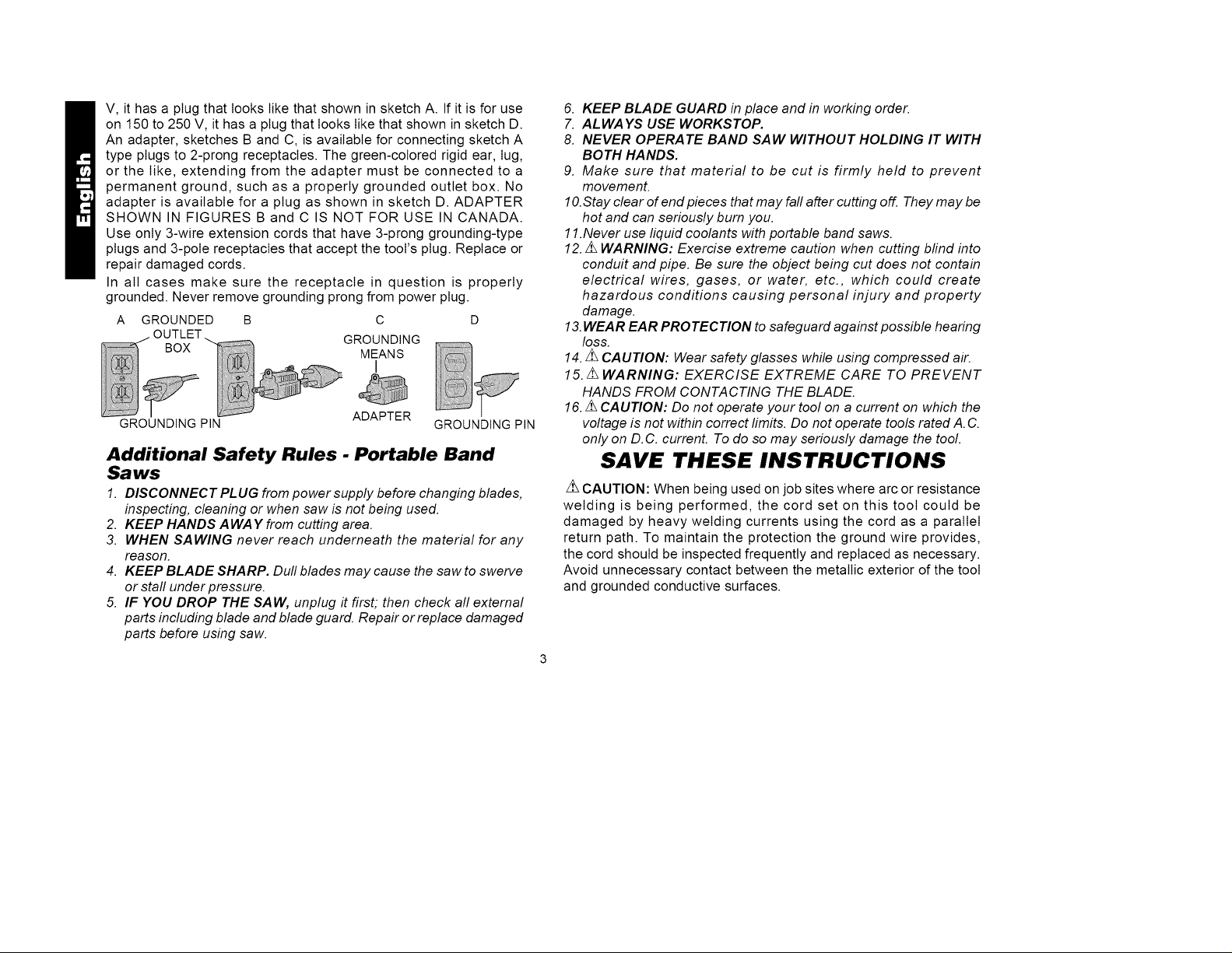
V,ithasaplugthatlookslikethatshowninsketchA.Ifitisforuse
on150to250V,ithasaplugthatlookslikethatshowninsketchD.
Anadapter,sketchesBandC,isavailableforconnectingsketchA
typeplugsto2-prongreceptacles.Thegreen-coloredrigidear,lug,
orthelike,extendingfromtheadaptermustbeconnectedtoa
permanentground,suchasa properlygroundedoutletbox.No
adapterisavailableforaplugasshowninsketchD.ADAPTER
SHOWNINFIGURESBandCISNOTFORUSEINCANADA.
Useonly3-wireextensioncordsthathave3-pronggrounding-type
plugsand3-polereceptaclesthatacceptthetool'splug.Replaceor
repairdamagedcords.
Inallcasesmakesurethereceptacleinquestionisproperly
grounded.Neverremovegroundingprongfrompowerplug.
A GROUNDEDB C D
GROUNDING
BOX MEANS
I
GROUNDING PIN
Additional Safety Rules - Portable Band
Saws
1. DISCONNECT PLUG from power supply before changing blades,
inspecting, cleaning or when saw is not being used.
2. KEEP HANDS AWAY from cutting area.
3. WHEN SAWING never reach underneath the material for any
reason.
4. KEEP BLADE SHARP. Dull blades may cause the saw to swerve
or staff under pressure.
5. IF YOU DROP THE SAW, unplug it first; then check aft external
parts including blade and blade guard. Repair or replace damaged
parts before using saw.
ADAPTER
GROUNDING PIN
6. KEEP BLADE GUARD in place and in working order.
7. ALWAYS USE WORKSTOP.
8. NEVER OPERATE BAND SAW WITHOUT HOLDING IT WITH
BOTH HANDS.
9. Make sure that material to be cut is firmly held to prevent
movement.
10.Stay clear of end pieces that may fall after cutting off. They may be
hot and can seriously bum you.
11.Never use liquid coolants with portable band saws.
12. z_ WARNING: Exercise extreme caution when cutting blind into
conduit and pipe. Be sure the object being cut does not contain
electrical wires, gases, or water, etc., which could create
hazardous conditions causing personal injury and property
damage.
13.WEAR EAR PROTECTION to safeguard against possible hearing
loss.
14. z_ CAUTION: Wear safety glasses while using compressed air.
15. z_WARNING: EXERCISE EXTREME CARE TO PREVENT
HANDS FROM CONTACTING THE BLADE.
16. z_CAUTION: Do not operate your tool on a current on which the
voltage is not within correct limits. Do not operate tools rated A. C.
only on D.C. current. To do so may seriously damage the tool.
SAVE THESE INSTRUCTIONS
CAUTION: When being used on job sites where arc or resistance
welding is being performed, the cord set on this tool could be
damaged by heavy welding currents using the cord as a parallel
return path. To maintain the protection the ground wire provides,
the cord should be inspected frequently and replaced as necessary.
Avoid unnecessary contact between the metallic exterior of the tool
and grounded conductive surfaces.
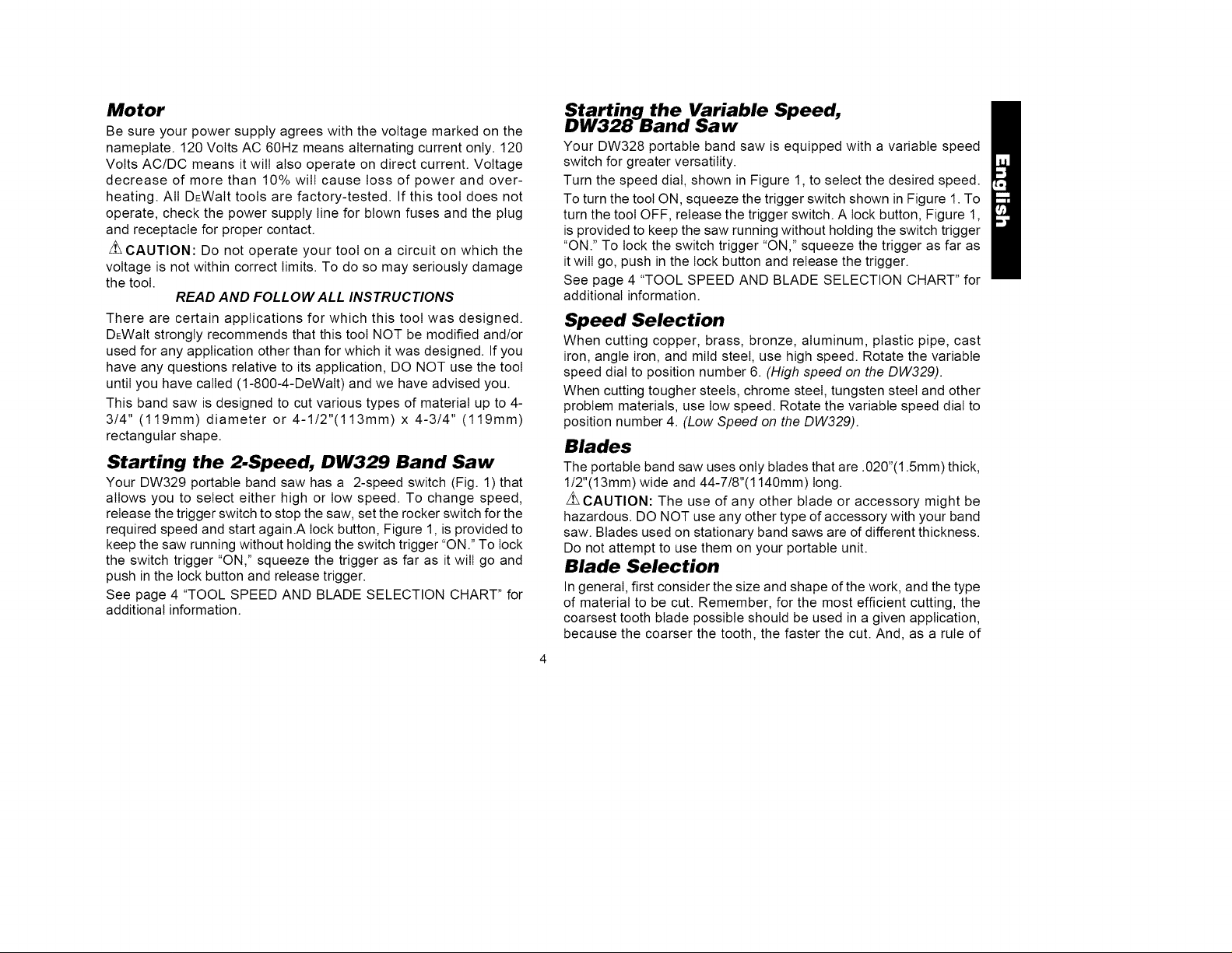
Motor
Be sure your power supply agrees with the voltage marked on the
nameplate. 120 Volts AC 60Hz means alternating current only. 120
Volts AC/DC means it will also operate on direct current. Voltage
decrease of more than 10% will cause loss of power and over-
heating. All DEWaIt tools are factory-tested. If this tool does not
operate, check the power supply line for blown fuses and the plug
and receptacle for proper contact.
Z_CAUTION: Do not operate your tool on a circuit on which the
voltage is not within correct limits. To do so may seriously damage
the tool.
READ AND FOLLOW ALL INSTRUCTIONS
There are certain applications for which this tool was designed.
DEWaIt strongly recommends that this tool NOT be modified and/or
used for any application other than for which it was designed. If you
have any questions relative to its application, DO NOT use the tool
until you have called (1-800-4-DeWaIt) and we have advised you.
This band saw is designed to cut various types of material up to 4-
3/4" (119mm) diameter or 4-1/2"(113mm) x 4-3/4" (119mm)
rectangular shape.
Starting the 2-Speed, DW329 Band Saw
Your DW329 portable band saw has a 2-speed switch (Fig. 1) that
allows you to select either high or low speed. To change speed,
release the trigger switch to stop the saw, set the rocker switch for the
required speed and start again.A lock button, Figure 1, is provided to
keep the saw running without holding the switch trigger "ON." To lock
the switch trigger "ON," squeeze the trigger as far as it will go and
push in the lock button and release trigger.
See page 4 "TOOL SPEED AND BLADE SELECTION CHART" for
additional information.
Starting the Variable Speed,
DW328 Band Saw
Your DW328 portable band saw is equipped with a variable speed
switch for greater versatility.
Turn the speed dial, shown in Figure 1, to select the desired speed.
To turn the tool ON, squeeze the trigger switch shown in Figure 1. To
turn the tool OFF, release the trigger switch. A lock button, Figure 1,
is provided to keep the saw running without holding the switch trigger
"ON." To lock the switch trigger "ON," squeeze the trigger as far as
it will go, push in the lock button and release the trigger.
See page 4 "TOOL SPEED AND BLADE SELECTION CHART" for
additional information.
Speed Selection
When cutting copper, brass, bronze, aluminum, plastic pipe, cast
iron, angle iron, and mild steel, use high speed. Rotate the variable
speed dial to position number 6. (High speed on the DW329).
When cutting tougher steels, chrome steel, tungsten steel and other
problem materials, use low speed. Rotate the variable speed dial to
position number 4. (Low Speed on the DW329).
Blades
The portable band saw uses only blades that are .020"(1.5mm) thick,
1/2"(13mm) wide and 44-7/8"(1140mm)long.
Z_CAUTION: The use of any other blade or accessory might be
hazardous. DO NOT use any other type of accessory with your band
saw. Blades used on stationary band saws are of different thickness.
Do not attempt to use them on your portable unit.
Blade Selection
In general, first consider the size and shape of the work, and the type
of material to be cut. Remember, for the most efficient cutting, the
coarsest tooth blade possible should be used in a given application,
because the coarser the tooth, the faster the cut. And, as a rule of
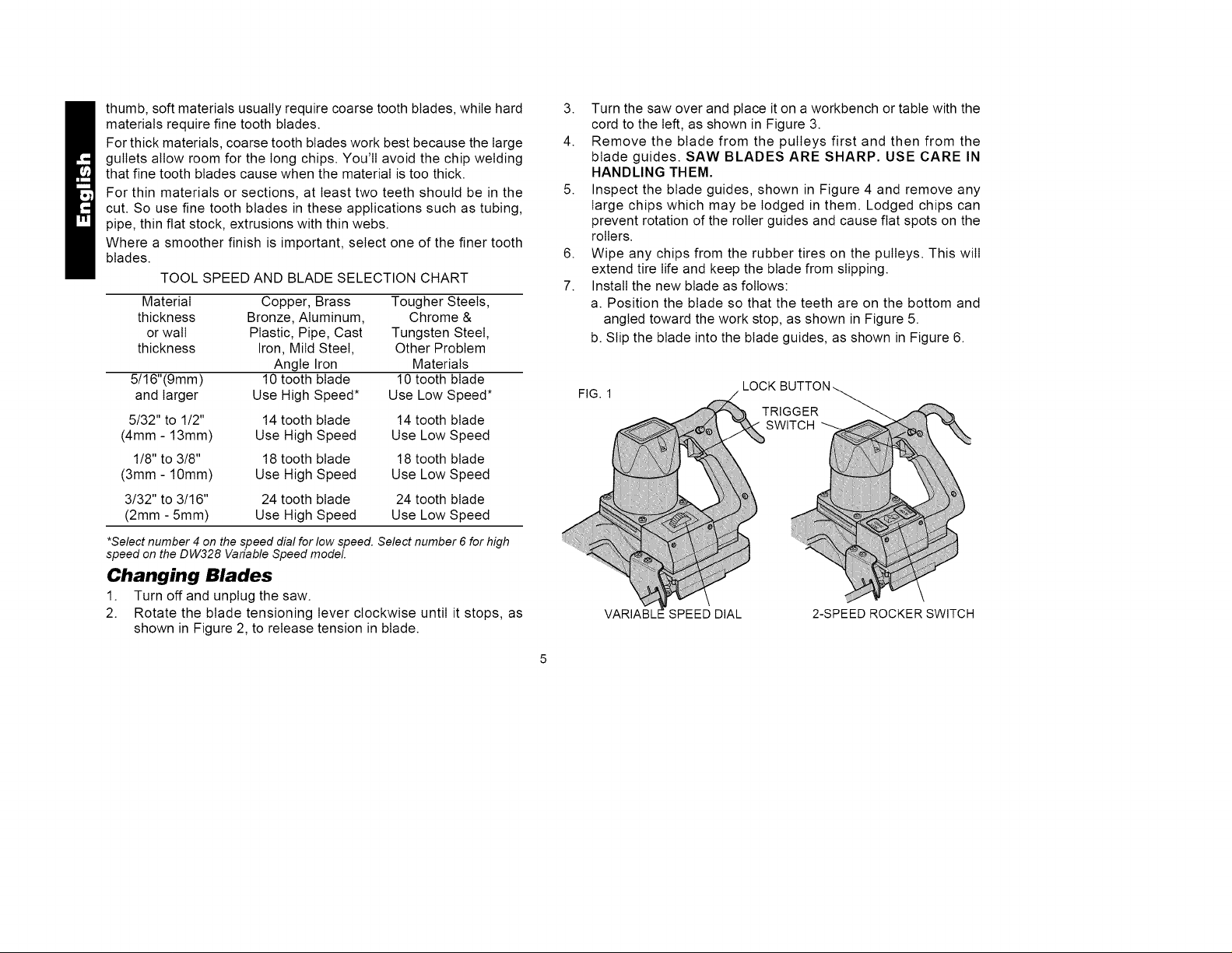
thumb,softmaterialsusuallyrequirecoarsetoothblades,whilehard
materialsrequirefinetoothblades.
Forthickmaterials,coarsetoothbladesworkbestbecausethelarge
gulletsallowroomforthelongchips.You'llavoidthechipwelding
thatfinetoothbladescausewhenthematerialistoothick.
Forthinmaterialsorsections,atleasttwoteethshouldbeinthe
cut.Sousefinetoothbladesintheseapplicationssuchastubing,
pipe,thinflatstock,extrusionswiththinwebs.
Whereasmootherfinishisimportant,selectoneofthefinertooth
blades.
TOOLSPEEDANDBLADESELECTIONCHART
Material Copper,Brass TougherSteels,
thickness Bronze,Aluminum, Chrome&
orwall Plastic,Pipe,Cast TungstenSteel,
thickness Iron,MildSteel, OtherProblem
AngleIron Materials
5/16"(9mm) 10toothblade 10toothblade
andlarger UseHighSpeed* UseLowSpeed*
5/32"to1/2" 14toothblade 14toothblade
(4mm-13mm) UseHighSpeed UseLowSpeed
1/8"to3/8" 18toothblade 18toothblade
(3mm-10mm) UseHighSpeed UseLowSpeed
3/32"to3/16" 24toothblade 24toothblade
(2mm-5mm) UseHighSpeed UseLowSpeed
*Selectnumber 4on the speeddial for lowspeed. Selectnumber 6for high
speedon the DW328 Variable Speedmodel.
Changing Blades
1. Turn off and unplug the saw.
2. Rotate the blade tensioning lever clockwise until it stops, as
shown in Figure 2, to release tension in blade.
3. Turnthesawoverandplaceitonaworkbenchortablewiththe
cordtotheleft,asshowninFigure3.
4. Removethebladefromthepulleysfirstandthenfromthe
bladeguides.SAWBLADES ARE SHARP. USE CARE IN
HANDLING THEM.
5. Inspect the blade guides, shown in Figure 4 and remove any
large chips which may be lodged in them. Lodged chips can
prevent rotation of the roller guides and cause flat spots on the
rollers.
6. Wipe any chips from the rubber tires on the pulleys. This will
extend tire life and keep the blade from slipping.
7. Install the new blade as follows:
a. Position the blade so that the teeth are on the bottom and
angled toward the work stop, as shown in Figure 5.
b. Slip the blade into the blade guides, as shown in Figure 6.
FIG. 1
VARIABLE SPEED DIAL 2-SPEED ROCKER SWITCH
LOCK
TRIGGER
SWITCH
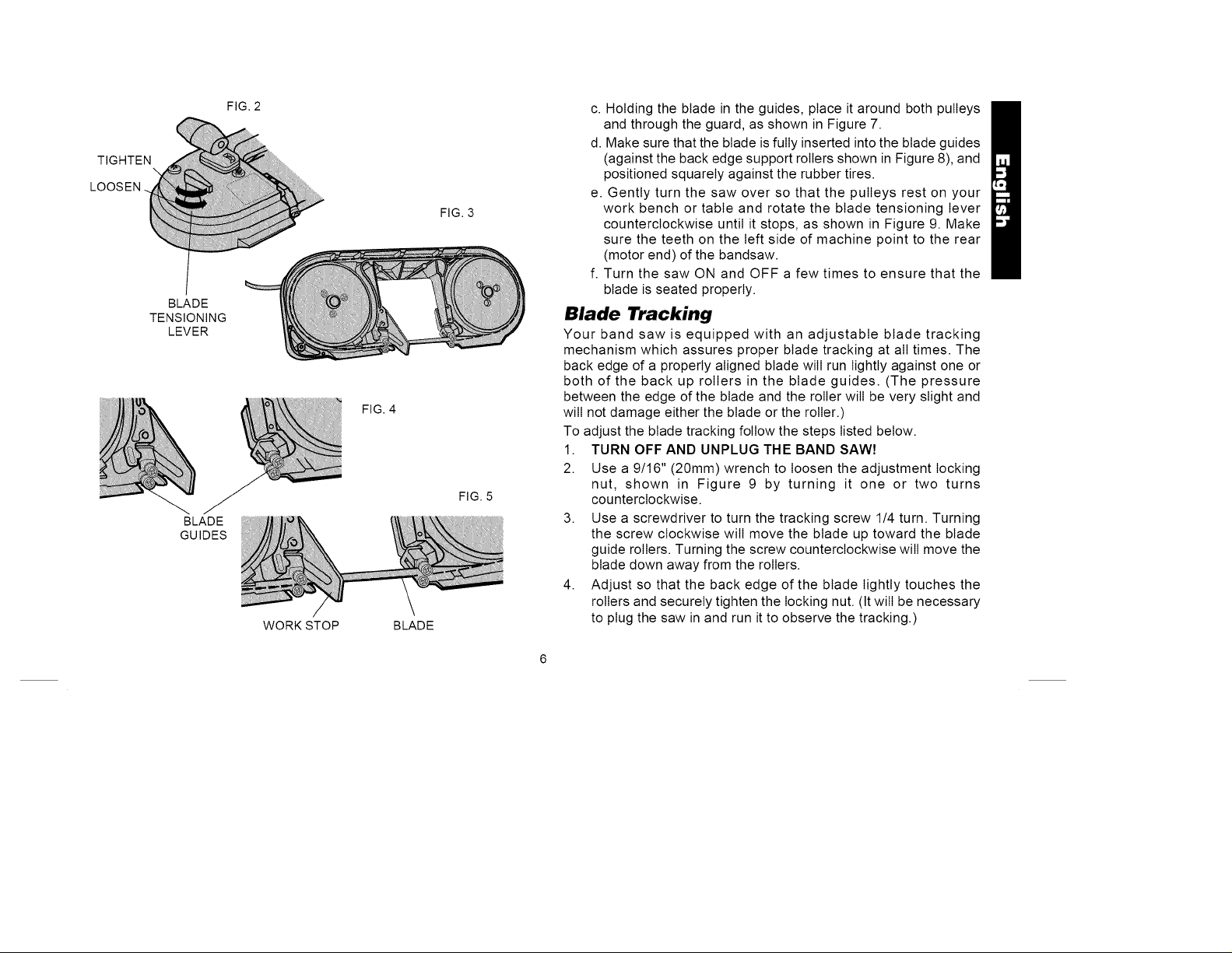
TIGHTEN
LOOSEN
TENSIONING
BLADE
LEVER
BLADE
GUIDES
FIG.2
WORKSTOP
FIG.4
FIG.3
BLADE
FIG.5
c. Holding the blade in the guides, place it around both pulleys
and through the guard, as shown in Figure 7.
d. Make sure that the blade is fully inserted into the blade guides
(against the back edge support rollers shown in Figure 8), and
positioned squarely against the rubber tires.
e. Gently turn the saw over so that the pulleys rest on your
work bench or table and rotate the blade tensioning lever
counterclockwise until it stops, as shown in Figure 9. Make
sure the teeth on the left side of machine point to the rear
(motor end) of the bandsaw.
f. Turn the saw ON and OFF a few times to ensure that the
blade is seated properly.
Blade Tracking
Your band saw is equipped with an adjustable blade tracking
mechanism which assures proper blade tracking at all times. The
back edge of a properly aligned blade will run lightly against one or
both of the back up rollers in the blade guides. (The pressure
between the edge of the blade and the roller will be very slight and
will not damage either the blade or the roller.)
To adjust the blade tracking follow the steps listed below.
1. TURN OFF AND UNPLUG THE BAND SAW!
2. Use a 9/16" (20mm) wrench to loosen the adjustment locking
nut, shown in Figure 9 by turning it one or two turns
counterclockwise.
3. Use a screwdriver to turn the tracking screw 1/4 turn. Turning
the screw clockwise will move the blade up toward the blade
guide rollers. Turning the screw counterclockwise will move the
blade down away from the rollers.
4. Adjust so that the back edge of the blade lightly touches the
rollers and securely tighten the locking nut. (It will be necessary
to plug the saw in and run it to observe the tracking.)
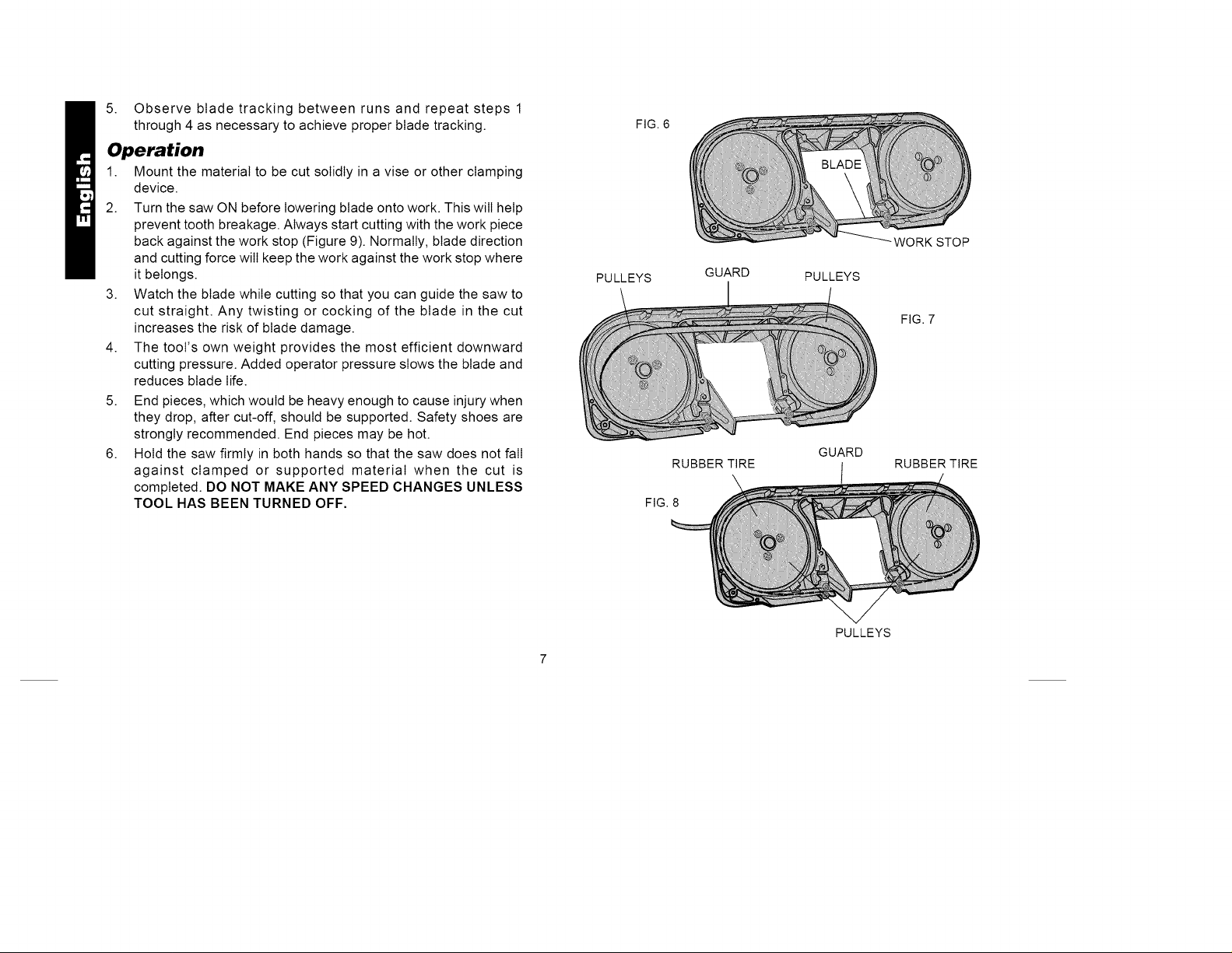
5. Observebladetrackingbetweenrunsandrepeatsteps1
through4asnecessarytoachieveproperbladetracking.
Operation
1. Mount the material to be cut solidly in a vise or other clamping
device.
2. Turn the saw ON before lowering blade onto work. This will help
prevent tooth breakage. Always start cutting with the work piece
back against the work stop (Figure 9). Normally, blade direction
and cutting force will keep the work against the work stop where
it belongs.
3. Watch the blade while cutting so that you can guide the saw to
cut straight. Any twisting or cocking of the blade in the cut
increases the risk of blade damage.
4. The tool's own weight provides the most efficient downward
cutting pressure. Added operator pressure slows the blade and
reduces blade life.
5. End pieces, which would be heavy enough to cause injury when
they drop, after cut-off, should be supported. Safety shoes are
strongly recommended. End pieces may be hot.
6. Hold the saw firmly in both hands so that the saw does not fail
against clamped or supported material when the cut is
completed. DO NOT MAKE ANY SPEED CHANGES UNLESS
TOOL HAS BEEN TURNED OFF.
PULLEYS
FIG. 6
FIG. 8
GUARD
RUBBERTIRE
\
-WORK STOP
PULLEYS
FIG. 7
GUARD
RUBBER TIRE
l
PULLEYS
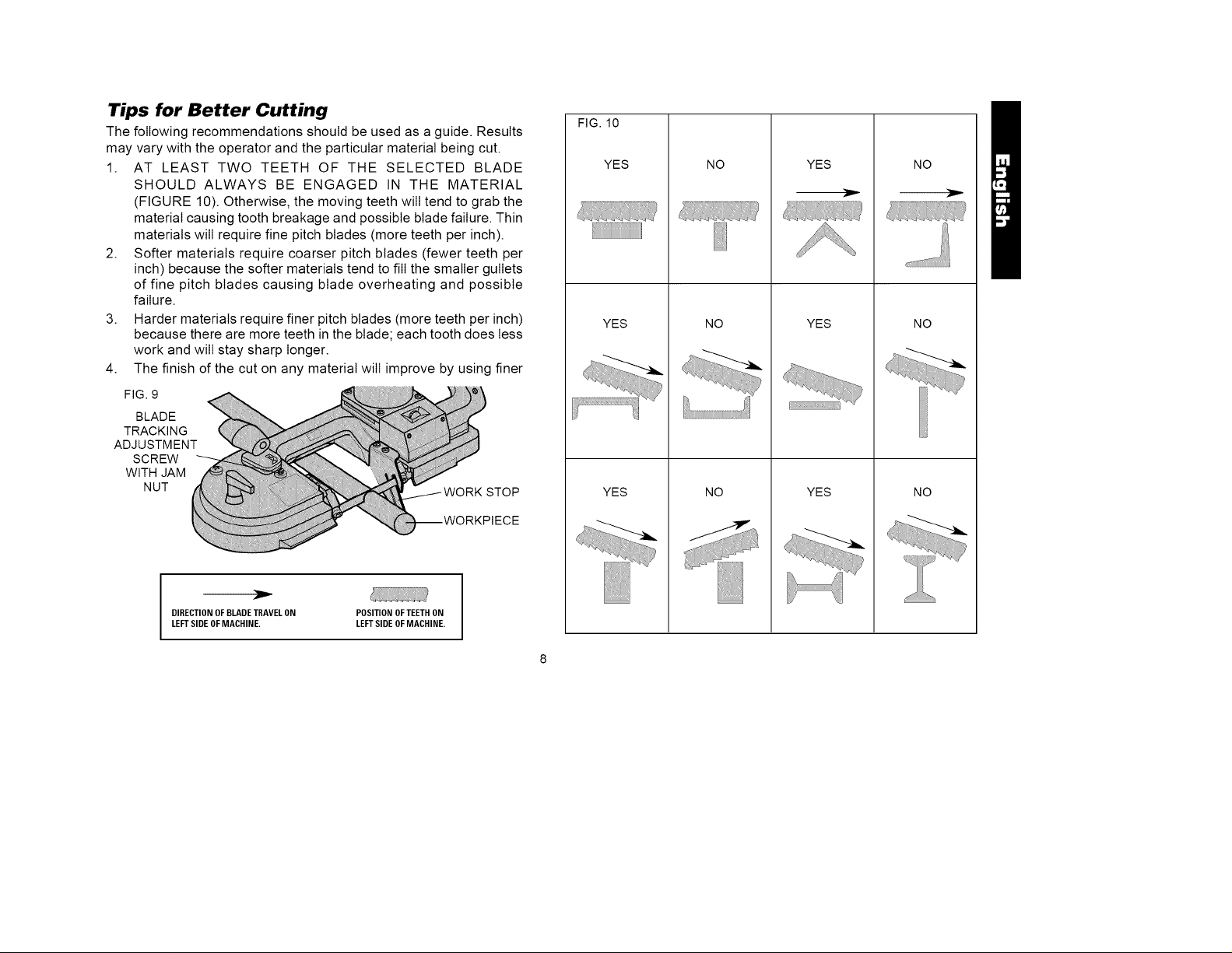
Tips for Better Cutting
The following recommendations should be used as a guide. Results
may vary with the operator and the particular material being cut.
1. AT LEAST TWO TEETH OF THE SELECTED BLADE
SHOULD ALWAYS BE ENGAGED IN THE MATERIAL
(FIGURE 10). Otherwise, the moving teeth will tend to grab the
material causing tooth breakage and possible blade failure. Thin
materials will require fine pitch blades (more teeth per inch).
2. Softer materials require coarser pitch blades (fewer teeth per
inch) because the softer materials tend to fill the smaller gullets
of fine pitch blades causing blade overheating and possible
failure.
3. Harder materials require finer pitch blades (more teeth per inch)
because there are more teeth in the blade; each tooth does less
work and will stay sharp longer.
4. The finish of the cut on any material will improve by using finer
FIG. 9
BLADE
TRACKING
ADJUSTMENT
SCREW
WITH JAM
NUT
FIG. 10
YES
YES
YES
NO
NO
NO
YES
YES
YES
NO
NO
NO
r
DIRECTIONOFBLADETRAVELON
LEFTSIDEOFMACHINE.
POSITION OFTEETHON
LEFTSIDEOFMACHINE.
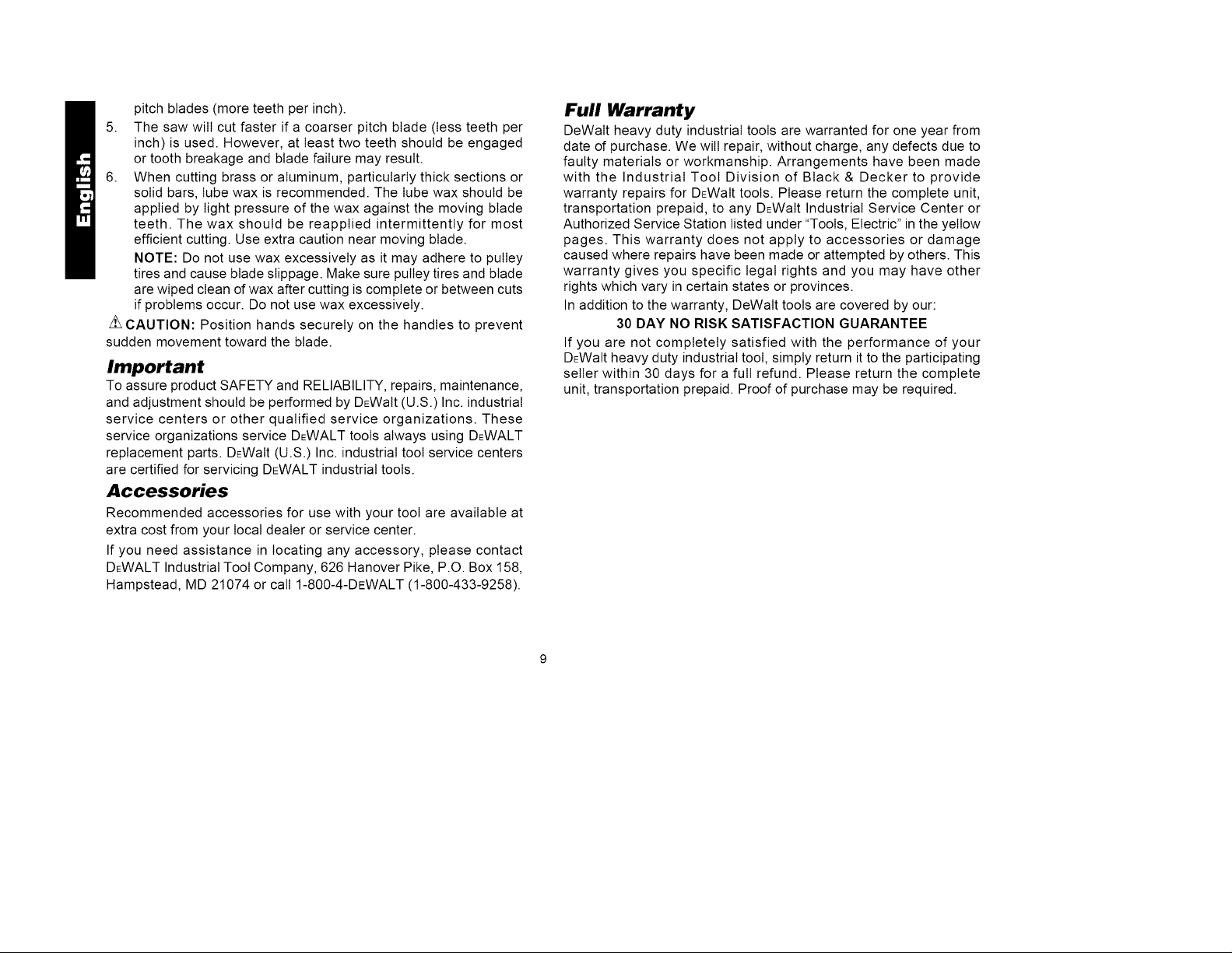
pitch blades (more teeth per inch).
5. The saw will cut faster if a coarser pitch blade (less teeth per
inch) is used. However, at least two teeth should be engaged
or tooth breakage and blade failure may result.
6. When cutting brass or aluminum, particularly thick sections or
solid bars, Iube wax is recommended. The Iube wax should be
applied by light pressure of the wax against the moving blade
teeth. The wax should be reapplied intermittently for most
efficient cutting. Use extra caution near moving blade.
NOTE: Do not use wax excessively as it may adhere to pulley
tires and cause blade slippage. Make sure pulley tires and blade
are wiped clean of wax after cutting is complete or between cuts
if problems occur. Do not use wax excessively.
Z_CAUTION: Position hands securely on the handles to prevent
sudden movement toward the blade.
Important
To assure product SAFETY and RELIABILITY, repairs, maintenance,
and adjustment should be performed by DEWalt (U.S.) Inc. industrial
service centers or other qualified service organizations. These
service organizations service DEWALT tools always using DEWALT
replacement parts. DEWalt (U.S.) Inc. industrial tool service centers
are certified for servicing DEWALT industrial tools.
Accessories
Recommended accessories for use with your tool are available at
extra cost from your local dealer or service center.
If you need assistance in locating any accessory, please contact
DEWALT Industrial Tool Company, 626 Hanover Pike, P.O. Box 158,
Hampstead, MD 21074 or call 1-800-4-DEWALT (1-800-433-9258).
Full Warranty
DeWalt heavy duty industrial tools are warranted for one year from
date of purchase. We will repair, without charge, any defects due to
faulty materials or workmanship. Arrangements have been made
with the Industrial Tool Division of Black & Decker to provide
warranty repairs for DEWalt tools. Please return the complete unit,
transportation prepaid, to any DEWalt Industrial Service Center or
Authorized Service Station listed under "Tools, Electric" inthe yellow
pages. This warranty does not apply to accessories or damage
caused where repairs have been made or attempted by others. This
warranty gives you specific legal rights and you may have other
rights which vary in certain states or provinces.
In addition to the warranty, DeWalt tools are covered by our:
30 DAY NO RISK SATISFACTION GUARANTEE
If you are not completely satisfied with the performance of your
DEWalt heavy duty industrial tool, simply return it to the participating
seller within 30 days for a full refund. Please return the complete
unit, transportation prepaid. Proof of purchase may be required.