
GENERAL
The unit is manufactured, checked and supplied in
accordance with our published specification, and when
installed and used in normal or prescribed
applications, with the lid in place and within the
parameters set for mechanical and electrical
performance, will not cause danger or hazard to life or
limb.
HEALTH AND SAFETY AT WORK ACT 1974
WARNINGS
1. THE USERS ATTENTION IS DRAWN TO THE
FACT THAT, WHEN THE UNIT IS ‘LIVE’ WITH
RESPECT TO ELECTRICAL OR PRESSURE
SUPPLIES, A HAZARD MAY EXIST IF THE
UNIT IS OPENED OR DISMANTLED.
2. UNITS MUST BE SELECTED AND INSTALLED
BY SUITABLY TRAINED AND QUALIFIED
PERSONNEL IN ACCORDANCE WITH
APPROPRIATE CODES OF PRACTICE SO
THAT THE POSSIBILITY OF FAILURE
RESULTING IN INJURY OR DAMAGE
CAUSED BY MISUSE OR MISAPPLICATION IS
AVOIDED.
OPERATING PRINCIPLES
A closed system containing the equilibrium of liquid
and vapour is used to sense the process temperature.
The pressure within the system is proportional to the
applied temperature. This pressure is applied to a
diaphragm sealed piston, which in turn, operates a
push rod. The rod is restrained by an adjustable
spring. When the force on the rod overcomes the
spring pressure the rod moves and operates a switch
or switches. When the temperature falls the rod is
restored to its original position and the switch or
switches reset.
INSTALLATION
The instruments are designed to be mounted vertically
(refer to figs 3 & 4) however mounting up to 45° in any
plane is acceptable although a small calibration shift
may occur. They can be mounted either direct to
process or to a wall or panel using the back plate
provided. Select the mounting point so as to avoid
excessive shock, vibration or temperature fluctuation.
Instruments should be mounted to avoid excessive
heat transfer from the process lines or adjacent plant.
Capillary Version
Mount the sensing bulb so that the base of the
instrument is above the tip of the bulb and the bulb is
level with, or no more than 250 mm below, the base of
the instrument. The bulb extension is fitted with a
sliding compression gland to accommodate different
thermowells.
Fig 2
SCREW DRIVER
LOCATION SLOTS
LOWEST SET POINT
HIGHEST SET POINT
ADJUST RIGHT TO
LEFT TO INCREASE
SET POINT
INSTALLATION, OPERATING AND
MAINTENANCE INSTRUCTIONS FOR
VAPOUR PRESSURE GR SERIES
TEMPERATURE SWITCHES
(MODEL GR7)
ISSUE E 03/10
PRODUCT CODE
CAUTION
Though the design is of rugged construction, do not
apply excessive torque to the conduit nipple. Support
should be given to the end fittings using a 40 mm (1.9 /
16”) spanner. For the rigid stem version it is
recommended that a portion of flexible conduit be
used to prevent undue stresses being applied to the
unit.
WARNING: CHECK THE CONNECTION THREAD
SIZE AND SPECIFICATION OF THE UNIT TO AVOID
MISMATCHING WITH THE PROCESS
CONNECTION ADAPTOR. SEE DIGIT 11 OF THE
PRODUCT CODE.
WIRING (Fig 1)
Terminal Enclosure Version (Fig 4)
Wire in accordance with local and national codes. Use
cables no larger than 2.5 mm2 (14 AWG). Deliver
electrical connection through a suitable cable gland
which will maintain the IP rating of the instrument.
Insert bare wires fully into the terminal block and
tighten securely. Keep wiring tails to a minimum.
Flying Lead Version (Fig 1)
The leads are factory sealed so it is unnecessary to
seal the conduit to the conduit nipple. However flying
leads must be terminated in accordance with local and
national codes. Each conductor is provided with an
identity tag. If these become detached refer to the
colour code in the wiring diagram.
WIRING DIAGRAM
CERTIFIED ENCLOSURES
All Series GR Switches can be supplied with
BASEEFA certified enclosures to the following
ENCLOSURE
MODEL
ELECTRICAL ENTRY
MATERIAL OF WETTED PARTS
RANGE
SWITCHING OPTIONS
standards:
Zone 1 (Div 1) IEC 79-1
BS 5501: Parts 1 and 5: EN50 014 and EN50 018
CENELEC. Codes ‘H’ for aluminium and ‘R’ for
stainless steel EExd IIC T6.
All enclosures are suitable for outdoor use and the
majority of products are rated IP66. Refer to the
product label and / or leaflet. Only operation,
maintenance or repair procedures either contained
herein or approved by Delta Controls may be used, to
avoid rendering the equipment unsafe in operation and
/ or nullifying the Certification. NO MODIFICATIONS
PROCESS CONNECTION
OPTIONS AND TREATMENTS
SPECIAL ENGINEERING
Rigid Stem
Assemble the unit either direct, or indirect via a
thermowell, using the spanner facility provided,
ensuring that the full length of the sensing bulb is:
a) fully immersed in the process temperature;
b) the bulb does not ‘bottom, in the thermowell to
prevent damage.
In the interest of development and improvement Delta Controls Ltd, reserve the right to amend without notice,
details contained in this publication. No legal liability will be accepted by Delta Controls Ltd, for any errors,
T +44 (0) 208 939 3511 F +44 (0) 208 783 1163 E sales@delta-controls.com W www.delta-controls.com
Fig 3 FLYING LEADS CODE ‘A’
YOUR TRUSTED PARTNER IN PROCESS INSTRUMENTATION
DELTA CONTROLS LIMITED, ISLAND FARM AVENUE, WEST MOLESEY, SURREY KT8 2UZ
Registered Office Registered in England No 5369683
ARE PERMITTED.
Electrical Adaptors
Zone 1. Use only certified adaptors for Zone 1.
EExe for increased safety installations and EExd for
Flameproof installations.
References for Selection and Installation
BSEN60079-14 Part4 for all Enclosure Codes (Intrinsic
Safety)
BSEN 50014 Part 1 for Enclosure Codes H,R
BSEN60529 IP RATING (Ingress Protection)
omissions or amendments.
½” NPT
GROUND
SCREW ‘H’
OR ‘R’
111
4.3
.0
7
MOUNTING
HOLES FOR
M5 SCREWS
(WHEN FITTED) ‘H’
OR ‘R’
MAINTENANCE
Inspections should be carried out at quarterly to yearly
intervals depending upon operating conditions.
Where a terminal enclosure is fitted, isolate the unit
from process and power and remove the lid. Check all
terminals for tightness. Check that cable tails are not
fouled or chafed. Check for internal condensation.
Rectify as necessary.
It is recommended that instruments used to provide an
alarm are operated periodically to ensure they are
functioning correctly.
If further maintenance is required seek advice from
DELTA CONTROLS before attempting repair or
replacement of parts.
Note: Should the diaphragm fail the process will vent
to atmosphere via a control orifice without pressurising
the switch enclosure.
Periodically ensure the vent area does not
Become blocked and the vent plug has not degraded.
Ensure that the vent area is not obstructed.
OPERATION
Temperature switches are supplied calibrated against
falling temperature unless otherwise specified. Set
Point adjustment refers to falling temperature.
Switching differential is the difference between the set
point and the operating value on rising temperature.
Set Point Adjustment: Models GR7 (Fig 2)
1. Isolate the instrument from the process.
2. Adjustment may be carried out with the unit live.
3. Loosen both cover screws.
4. Rotate cover anti-clockwise to allow access.
5. Using a screwdriver rotate the adjuster to obtain the
desired setting. Turn right to left to increase the
setting. An appropriate setting is shown by pointer
against reference scale.
6. Rotate cover clockwise to close and tighten screws.
TERMINAL ENCLOSURE CODE K (fig 5 & 6) INSTALLATION
Terminal enclosure is rated IP65 for outdoor use.
This is a certified enclosure Zone 1 (Div 1) IEC 79-1
BS 5501: Parts 1 and 5: EN50 014 and EN50 018
EExd IIC T6.
Instrument enclosure is certified to Zone 1 (Div 1) IEC
79-1 BS 5501: Parts 1 and 5: EN50 014 and EN50
018 Cenelec.
WARNING: Lid and adaptors. It is a safety
requirement that at least 5 full threads are engaged
when the unit is in operation. Never operate the unit
unless this condition is met. Do not use greases or
lubricants not compatible with the environment,
process or aluminium.
REPLACEMENT PARTS
Use only factory authorised parts and procedures.
The only parts normally recommended for site
replacement are microswitches. However, in some
circumstances other spares kits are available. Apply
for details quoting the serial number and full product
code.
WARRANTIES – SEE CONDITIONS OF SALE
Fig 4
CODES ‘C’ & ‘D’
2.24
57
171.0
HOLES 4.5
mm DIA
SUITABLE
FOR M4
SCREWS
MAX HEAD
DIA 7.5 mm
Stock No: 002522/GR7
1.57
40
3.15
15.0
0.59
45.0
1.77
80
2.70
68.5
M20 x 1.5
0.79
20
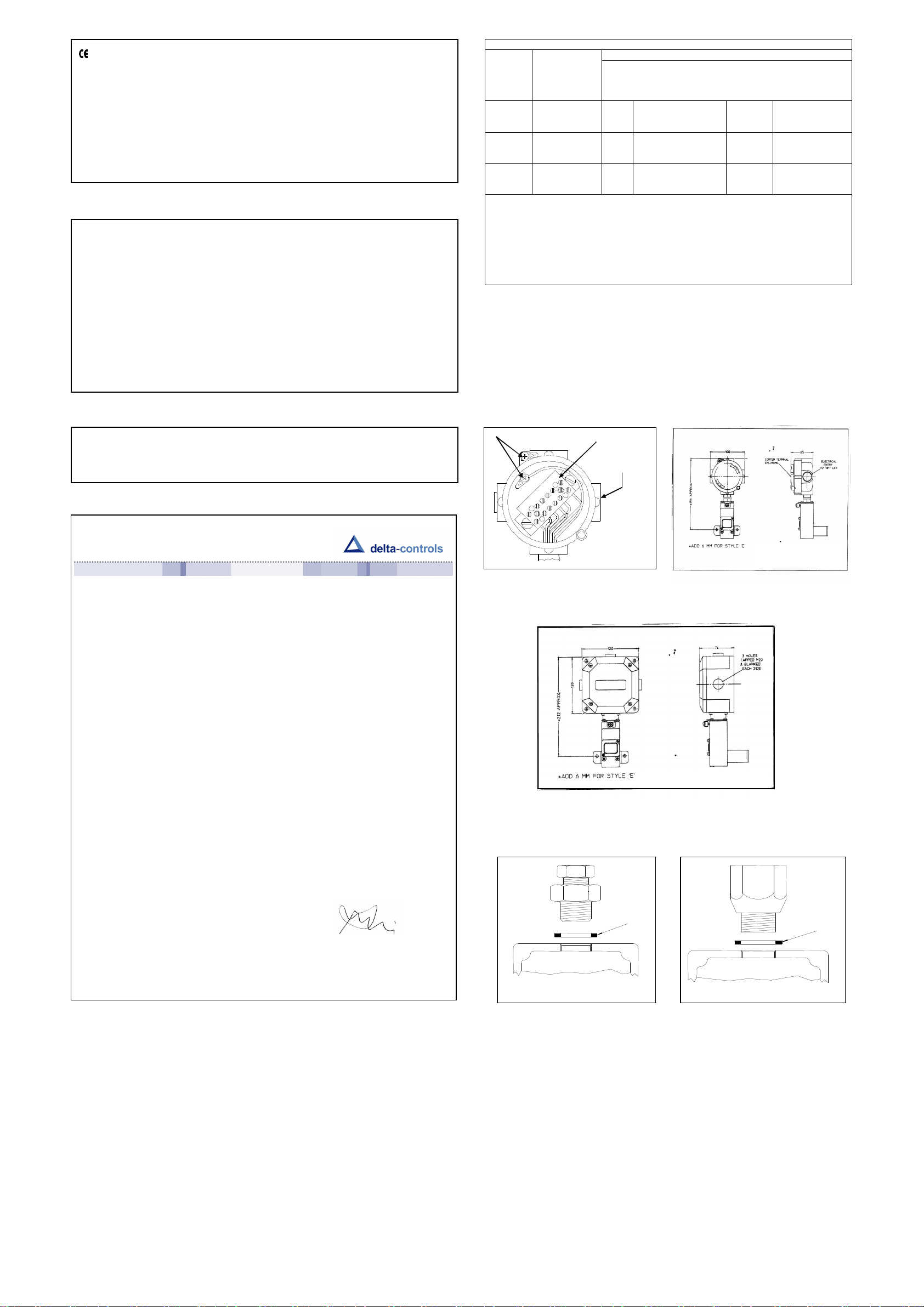
Low Voltage Directive (LVD) – 2006/95/AC. Switch products with enclosure codes ‘W’ and
‘A’ supplied CE-marked must be installed and used in accordance with the main instructions
and this addendum supplied with each product. Products rated lower than 50V ac and 75 V dc
are outside the scope of the LVD, and therefore, do not require CE-marking under this
directive. The LVD does not apply to products with enclosure codes ‘H’, ‘K’, ‘R’, ‘M’, ‘N’ for use
in hazardous areas. Switch products with enclosure codes ‘H’, ‘K’, ‘R’, ‘M’, ‘N’, are covered by
the Explosive Atmospheres Directive ATEX – 94/9/EC and when CE-marked will indicate
compliance with this directive alone. The following directives do not apply to switch products
manufactured by Delta Controls:
Electromagnetic Compatibility EMC – 2004/108/EC
Machinery Safety Directive MSD – 2006/42/EC
WIRING
Junction box cable glands and adaptors. Optional Junction box code ‘C’ is supplied with an
M20 x 1.5 tapped hole blanked with a red plug. Discard the red plug and fit a suitable
proprietary brass or nylon M20 cable gland with thread length of 10 mm. Fit a fibre washer to
the outside. See diagram 1.
Alternately the junction box may be supplied from the factory with a threaded adaptor ready to
accept the customer’s gland or conduit system.
Alternatives:
1) a metal or nylon adaptor may be used to accommodate other sizes of gland eg NPT, or
conduit system. See diagram 2.
Earthing / grounding – Use earthing point provided inside the junction box (when fitted). The
user must make suitable local earthing arrangement, if required, to ensure that metal glands /
adaptors are earthed.
SWITCH
CODE
(type)
HS, HD,
HR
HP, HQ,
HT
HV, HW,
HY
UL/CSA
RATING
(Resistive)
*See Note
11A @ 110/250 VAC
5/0.5 @ 30/125 VDC
5A @ 250 VAC
2A @ 30 VDC
1A @ 125 VAC
*1A @ 30 VDC
Uimp
Ui RATING (Ie/Ue)
0.8kV
250V
0.5kV 250V
0.5kV 120V
IEC 947-5-1/EN 60947-5-1 RATING
0.6/0.3A @ 120/240 VAC
0.22/0.1A @ 125/250VDC
0.6/0.3A @ 120/240 VAC
0.22/0.1A @ 125/250VDC
0.3A @ 120 VAC
Designation
&
Utilization
Category
AC14/D300
DC13/R300
AC14/D300
DC13/R300
AC14/E150
MAKE
AC
DC
AC
DC
AC
432 72
432 72
216 36
VA
28 28
28 28
The electrical rating is dependent on the microswitch fitted to the switch. The electrical
rating is defined by each approval that the microswitch complies with and is shown on the
product nameplate, ie UL/CSA or IEC. It should be noted that the switch must be used
within the electrical rating specified from the approval you require. Table A lists the
actual IEC ratings against the Designation and Utilisation Category marked on the
nameplate. If in doubt, seek guidance from factory.
TABLE A – MICROSWITCH RATINGS
BREAK
Pollution degree – all products are suitable for use in pollution degree 3.Ref EN60947-5-1
Electrical Isolation – these products are not suitable for electrical isolation. Always isolate
circuit separately to carry out any electrical work.
Declaration of Conformity
We: Delta Controls Ltd
Island Farm Avenue
West Molesey
Surrey, UK
KT8 2UZ
As the manufacturers of the apparatus listed, declare under our sole
responsibility that the products listed below:
Pressure, Pressure Difference, Temperature & Flow switches series “W” or “A”:
201, 202, 203, 281, 204, 207, 208, 209, 231, 232, 233, 234, S21, S22, S24, GR2, GR4, VM2, VM4.
301, 303, 304, 381, 384, 306, 386, 310, 316, S31, S34, GR3, GR6.
721, 731, 771, 722, 732, 772, 723, 733, 773, 781, 734, 774, 741, 742, 743, 744, S71, GR7.
131.
To which this declaration relates are in conformity with the following
relevant standards or parts thereof:
EN 60947-1 :1992 Low voltage switch gear and control-gear-general rules.
EN 60947-5-1:1992 Low voltage switch gear and control-gear-control circuit devices and switching
elements.
EN 60529: 1991 Specification for classification of degrees of protection provided by enclosures.
EN 60950:1992 Safety of information technology equipment including electrical business equipment:
section 2.5.
BS 6134:1991 Specification for pressure and vacuum switches.
And thereby conforms to the requirements of the Low Voltage Directive
73/23/EC amended by 93/68/EEC.
………………….
R. Harrison
Managing Director
Original dated 22nd June 2000
Rev. B dated 12
th
August 2009
Signed:
NO
COM
NC
COM
NC
Fig 7
DIAG 1
JUNCTION BOX
CABLE GLAND ASSEMBLY
NORMAL R H
ELECTRICAL ENTRY
MODEL GR7 WITH TERMINAL ENCLOSURE CODE J
DIAG 2
WASHER
MODEL GR7 W ITH TER MINAL
ENCLOSURE CODE K
FIBRE
JUNCTION BOX
ADAPTOR ASSEMBLY