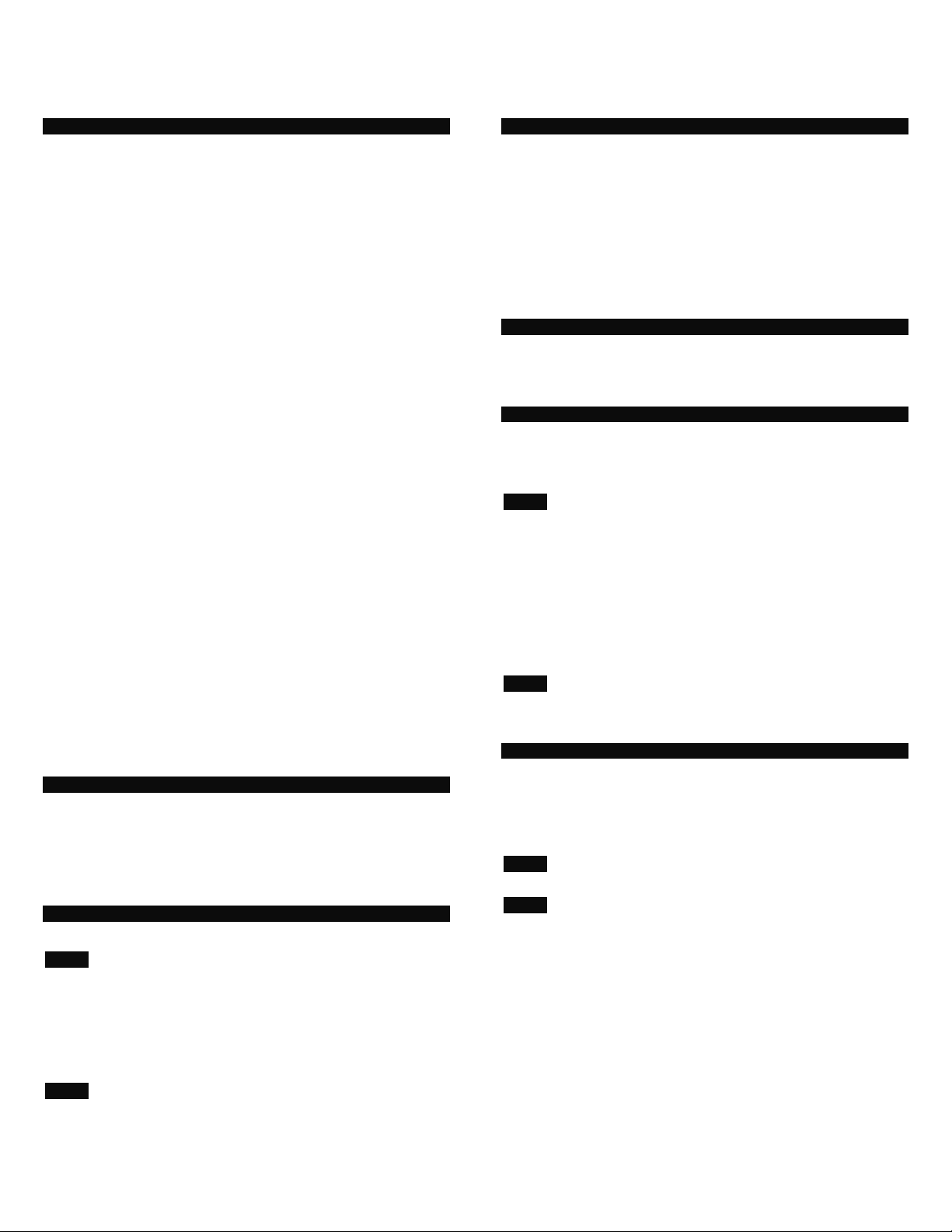
PosiTest
®
Pull-Off Adhesion Tester
Instruction Manual v1.0
Introduction
The portable, hand-operated PosiTest Pull-Off Adhesion Tester
measures the force required to pull a specified test diameter of
coating away from its substrate using hydraulic pressure. The
pressure is displayed in both MPa and PSI on a precision dial
indicator and can be related to the coating’s strength of adhesion
to the substrate.
In accordance with ASTM D4541-95 and ISO 4624, the PosiTest
Pull-Off Adhesion Tester evaluates the adhesion (pull-off
strength) of a coating by determining the greatest tensile pull off
force that it can bear before detaching. Breaking points,
demonstrated by fractured surfaces, occur along the weakest
plane within the system consisting of the dolly, adhesive, coating
layers and substrate.
There are a few basic steps for testing coating adhesion with a
PosiTest Adhesion Tester:
1. Dolly & Coating Preparation
o The dolly and the coating are cleaned and abraded.
2. Adhesive & Dolly Application
o The adhesive is prepared and applied to the dolly. The
dolly is then adhered to the coated surface and
adhesive is allowed to cure.
3. Test Area Separation
o The test area of the coating is separated from the area
surrounding the dolly by cutting or drilling. Drilling
(50mm or 20mm dollies) must be done before dolly is
adhered to the surface – cutting with hole-saw (20mm
dollies only) should be done after dolly is adhered and
adhesive is cured.
4. Pull-off Test
o After connecting actuator’s quick-coupling to the dolly,
pressure is pumped into the system and the dolly pulls
the coating(s) away.
5. Analysis of Test Results
o The dolly and the coating are examined and evaluated
to determine the nature of the coating failure.
Dolly Preparation
1. To remove oxidation and contaminants, place the included
abrasive pad on a flat surface and rub the base of the dolly
across the pad 4-5 times.
2. As required, remove residue left from the abrading process
using a dry cloth or paper towel.
Coating Surface Preparation
1. Lightly roughen the coating using the included abrasive pad
Note: As coating abrasion may introduce flaws, it should only
be used when necessary to remove surface contaminants,
or when the bond strength between the adhesive and the
coating is insufficient for pull testing.
2. To promote the bond between the dolly and the coating,
degrease the area of the coating to be tested using alcohol
or acetone to remove any oil, moisture or dust.
Note: Ensure that any alternative abrasion techniques,
degreasers or adhesives do not alter the properties of the
coating. Test by applying a small amount of degreaser or
adhesive to a sample area and observing effects.
Adhesive Selection
The adhesive included in the PosiTest Adhesion Tester kit has
been chosen as the recommended adhesive due to its versatility.
This adhesive has minimal impact on a variety of coatings and a
tensile strength exceeding the maximum performance
capabilities of the pressure system under ideal conditions. Other
adhesives may be preferred based on requirements such as
cure time, coating type, working temperature and pull off
strength, e.g., quick curing one-part cyanoacrylates (superglues)
may be sufficient for painted surfaces, but two-part epoxies are
preferred for porous or rough coatings.
Araldite® Adhesive* Preparation
Using a wooden stir stick (included), mix equal parts of the
2011/A and 2011/B adhesive on one of the included cardboard
mixing palettes until the compound appears homogenous.
Adhering Dollies to Coating
1. Apply a uniform film of adhesive on the base of the dolly
(approximately 2-4 mils thick for best results)
2. Attach the dolly to the prepared coating test area.
Note: If the coated surface to be tested is overhead or vertical,
a means to hold the dolly in place during the cure time may
be required, i.e. removable tape.
3. Gently push down on the dolly to squeeze out excess
adhesive. Do not twist or slide the dolly back and forth on
the coating as air bubbles may be generated.
4. Carefully remove excess adhesive from around the edges of
the dolly.
5. Allow to cure per the adhesive manufacturer’s instructions
Note: Many adhesives cure faster and provide a stronger bond
when cured with heat. Similarly, cold environments may
cause a longer cure time and weaker bond strength.
Final Dolly Preparation
Cutting Instructions:
1. Cut through the coating around the edges of the dolly with
the 20 mm cutting tool, removing any excess adhesive.
2. Clear away any debris from the cutting process.
Note: Cutting may induce coating surface flaws such as
microcracking that may alter test results.
Note: For coatings with strong lateral bonding it is
recommended to cut completely through the coating down to
the substrate.
Drilling Instructions:
1. Place template on the coating to be tested. With a hand-drill
(using a 5/32” / 4.0 mm drill bit) drill the first positioning hole
into the coating through the hole marked No.1. While drilling,
always hold template firmly against the coating. After drilling,
remove the template and remove debris from surface.
2. Reposition the template and insert one of the two attached
pins through the template hole marked No.1 and into the
first drilled positioning hole.
3. Drill the second positioning hole into the coating through the
template hole marked No.2. After drilling, remove the
template and remove debris from surface.
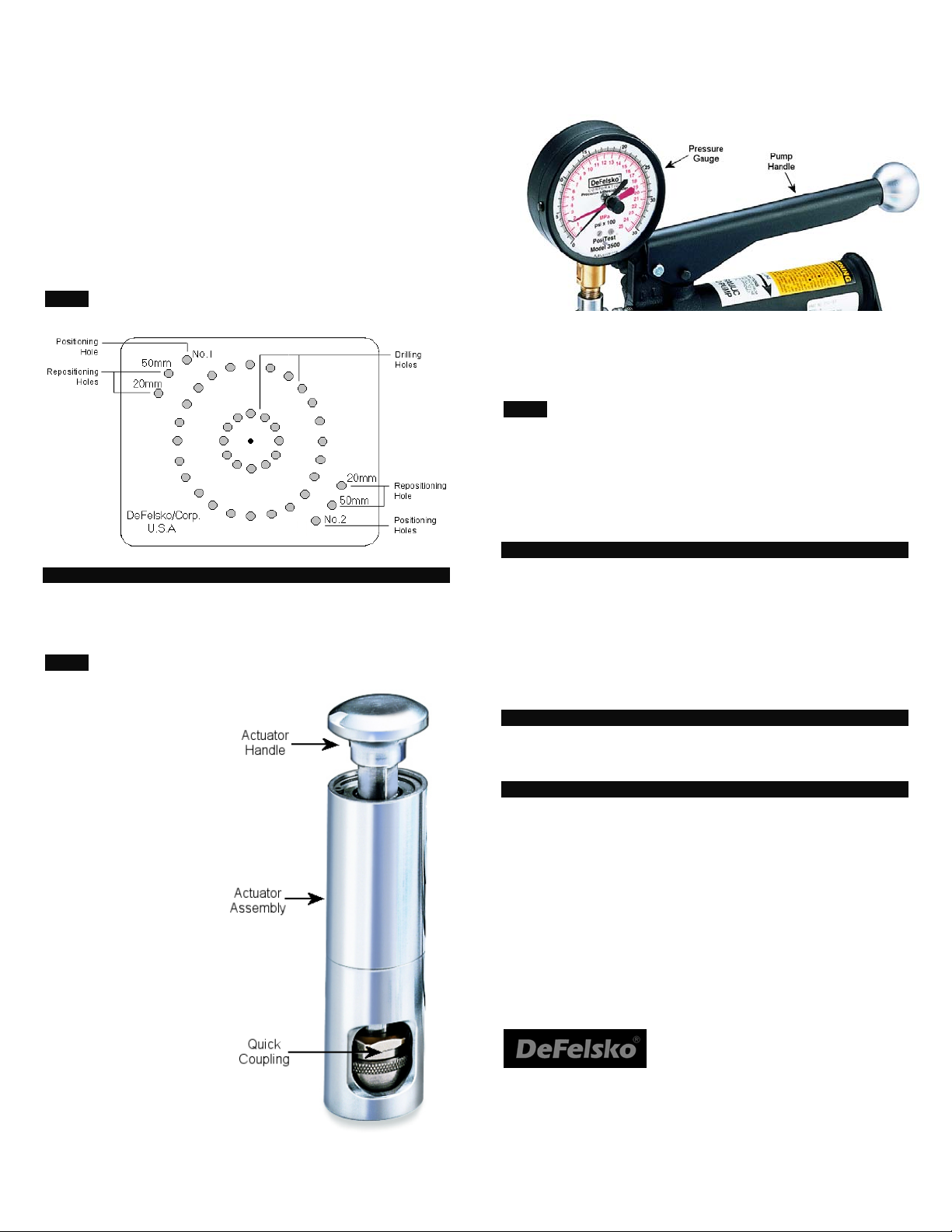
4. Reposition the template and insert the two attached pins
through the template holes marked No.1 and No.2 and into
the two drilled positioning holes.
5. The template is now positioned to drill either the 20mm or
50mm circle of holes (depending on dolly size) into t he coating.
6. After all holes have been drilled into the coating for the
chosen circle size, remove the template and clean debris
from the surface.
7. To complete the drilling process and remove all material
between existing holes, place the template back onto the
surface but rotate so the drilled positioning holes line up with
the template repositioning holes labeled 20mm or 50mm, as
appropriate. Replace positioning pins and repeat steps 5 & 6.
Note: Make sure all holes for the chosen circle size are drilled
completely through the coating to the substrate surface.
7. Begin pumping the pump handle until the black indicator on
the pressure gauge starts to move. Continue pumping at a
uniform rate of no more than 1 MPa (150 psi) per second
until the actuator pulls the dolly from the coating.
8. Immediately following the pull, open the pressure relief valve
on the pump to release the pressure. The red “drag”
indicator on the pressure gauge will maintain the maximum
pressure reading.
Note: An imprecise return of the black indicator to zero does
not necessarily mean the gauge is out of calibration. If all
pressure has been relieved but indicator still does not return
to zero, simply tap the gauge on its case with a finger or
elevate pressure and release again.
9. Record the pull off pressure and mark the dolly for future
qualitative analysis.
Pull Testing
1. Ensure the pressure relief valve on the pump is completely
open
2. Turn the red “drag” indicator on the pressure gauge to zero.
Note: If the black indicator will not return to zero, check to be
sure that pressure has been completely relieved from the
system.
3. Push the actuator
handle completely
down into the actuator
assembly.
4. Place the actuator
assembly over the
dolly head and attach
the quick coupling to
the dolly by reaching
through the holes in
the actuator assembly
and lifting the quick
coupling. Release the
quick coupling when
the dolly head is
completely engaged.
5. Close the pressure
relief valve on the
pump tightly.
6. Ensure the pump is on
a well-supported
horizontal surface. If it
is necessary to place
the pump on a vertical
surface, position the
unit so the pump hose outlet is in the down position to
prevent air from being pumped into the actuator.
Analyzing Results
Test results can be considered 100% valid when the coating is
completely removed from the substrate and remains adhered to
the adhesive on the dolly. When only a portion of the coating is
removed, specific results should be analyzed including the
fracture pattern to determine the cohesive properties of the
coating and adhesion properties between the dolly and adhesive,
adhesive and coating, distinct coating layers, and coating and
substrate.
Maintenance
Refer to the Pump Operating Instructions (included) for
maintenance information.
Warranty
The manufacturer fully warrants its products against defects in
workmanship or materials for a period of one year from date of
purchase. In the event that a tester is found to be defective,
return the product with proof of purchase to your dealer, and the
defective product will be repaired or replaced at the
manufacturer’s option.
No responsibility is assumed for incidental or consequential
damages.
The warranty is voided if the tester or its components have been
disassembled or tampered with.
Data subject to change without notice
DeFelsko Corporation
802 Proctor Avenue, PO Box 676
Ogdensburg, NY 13669 USA
The Measure of Qualit
© DeFelsko Corporation USA 2000 • All Rights Reserved • Patents applied for • Printed in USA
This manual is copyrighted with all rights reserved and may not be reproduced or transmitted, in
whole or part, by any means, without written permission from DeFelsko Corporation.
DeFelsko and PosiTest are trademarks of DeFelsko Corporation registered in the U.S. and in
other countries.
Every effort has been made to ensure that the information in the manual is accurate. DeFelsko is
not responsible for printing or clerical errors.
Tel: 315-393-4450 – Fax: 315-393-8471
Email: techsale@defelsko.com – web: www.defelsko.com