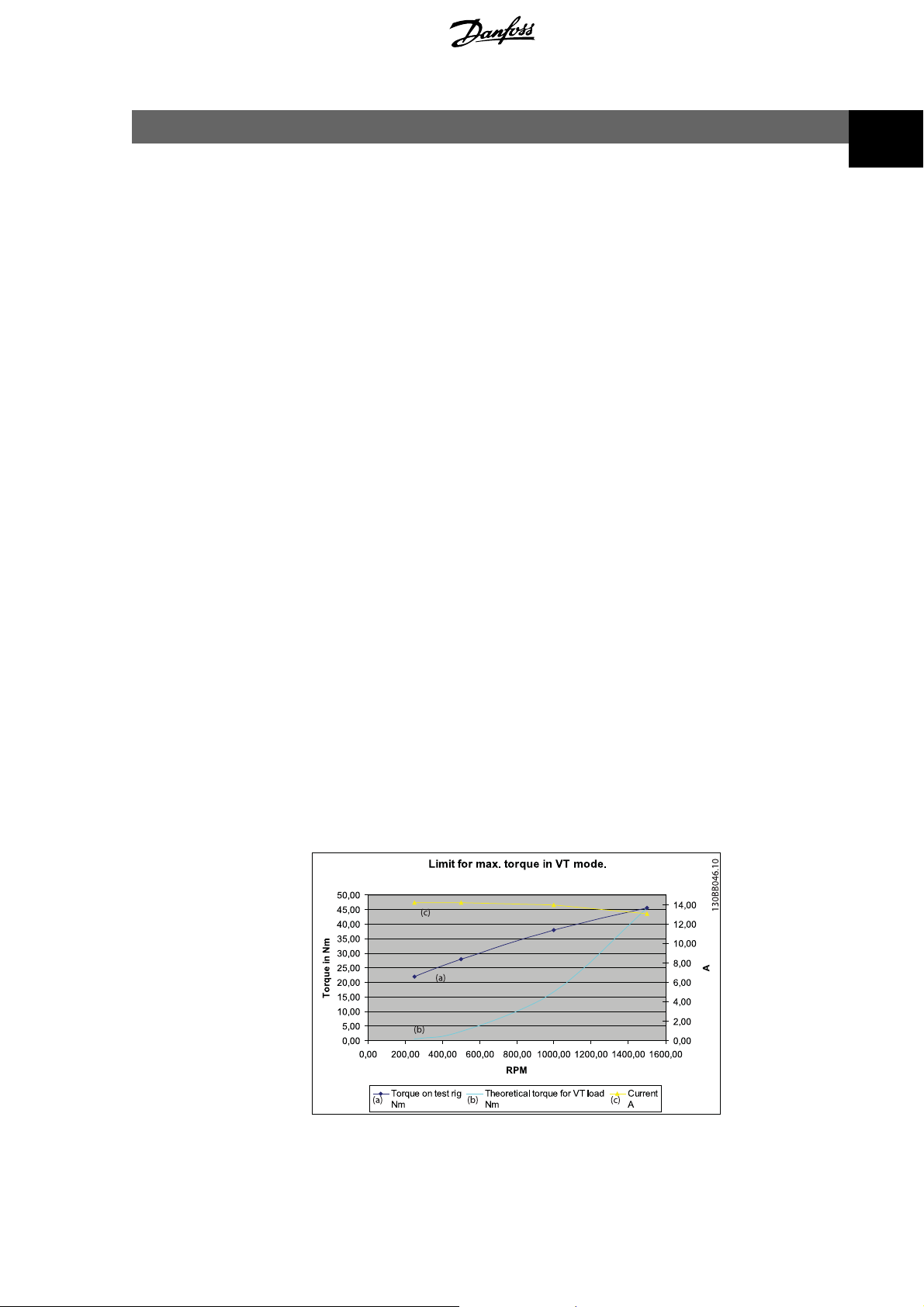
VLT® FC 100, FC 200 & FC 300 Drives
Application Note
1 Motor Protection
1 Motor Protection
1.1.1 Abstract
This Application Note describes how the VLT® FC 100, FC 200 and FC 300 Drives protects the
motor from being overloaded.
1.1.2
How Danfoss VLT
When using a Danfoss VLT® the application is protected in the following way.
First of all the drive contains several measurements and features to protect it self for overload,
over voltage and over temperature. The protecting features can keep the application running by
controlling the reason for the over load etc.
When for instance a pump is overloaded the drive will default give a warning in the display and
derate the speed of the pump in order to reduce the current and in that way keep the pump in
operation. If it is preferred to make the drive give a trip alarm and stop the application is configurable by parameter settings.
When the drive temperature is too high it will automatically reduce the switching frequency in
order to lower the heat dissipation.
®
AQUA protects the application
1
The motor is protected by a current or torque limit feature, which again can derate the speed,
give a warning or trip the drive if chosen.
Further more the drive contains an ETR timer which is estimating the motor temperature based
on motor current and speed. This is exactly the same way of protecting the motor as using a TI16
contactor with a motor protective switch attached. (Bimetal)
The torque limit feature is protecting the system for being overloaded no matter the speed. When
the drive is operating in VT mode the torque limit is reached at a lower level than if the system is
operating at nominal speed.
The following test results show that the torque limit is different at different speed. The curve
marked (a) shows the torque where the warning is triggered.
MN.90.01.02 - VLT® is a registered Danfoss trademark
1
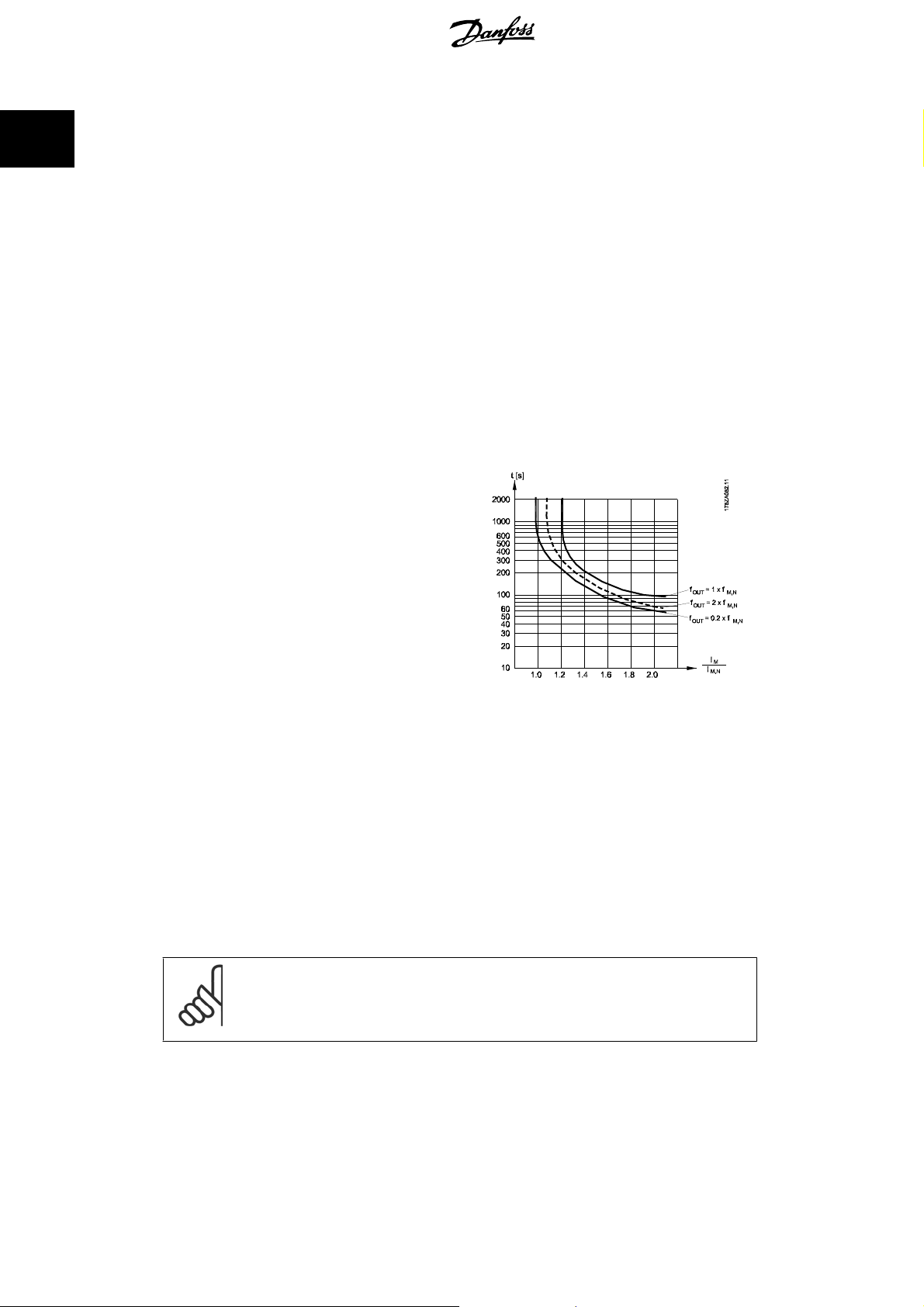
1
1 Motor Protection
When the speed is decreased the current is increased due to lower motor impedance at reduced
frequency.
Zm = 2*pi*f*L
Tm = C*Flux*I (Tm is torque, C is a constant, I is current)
At lower speed the flux is reduced (lower voltage), hence the current I is increased at the same
torque.
1.1.3 ETR (Electronic Thermal relay)
This is the way Danfoss protect the motor from being overheated. It is an electr onic f eature that
simulates a bimetal relay based on internal measurements.
The characteristic is shown in the following figure.
VLT® FC 100, FC 200 & FC 300 Drives
Application Note
Figure ETR: The X-axis is showing the ratio
between Imotor and Imotor nominal. The Yaxis is showing the time in seconds before the
ETR cut of and trip the drive. The curves are
showing the characteristic nominal speed, at
twice the nominal speed and at 0,2*the nominal speed.
It is clear that at lower speed the ETR cuts of
at lower heat due to less cooling of the motor.
In that way the motor are protected from being over heated even at low speed.
The ETR feature is calculating the motor temperature based on actual current and speed. The
calculated temperature is visible as a read out parameter in P16-18 in the FC202.
1.1.4 Summary
With the Torque limit feature the motor is protected for being overloaded independent of the
speed. With the ETR the motor is protected for being over heated and there is no need for any
further motor protection. That means when the motor is heated up the ETR timer controls for how
long time the motor can be running at the high temperature before it is stopped in order to prevent
over heating. If the motor is overloaded without reaching the temperature where the ETR shuts
of the motor, the torque limit is protecting the motor and application for being overloaded.
NB!
ETR is activated in P1-90
Torque limit is controlled in P4-16 and the timer before the torque limit warning shall
trip is controlled in P14-25.
2
MN.90.01.02 - VLT® is a registered Danfoss trademark