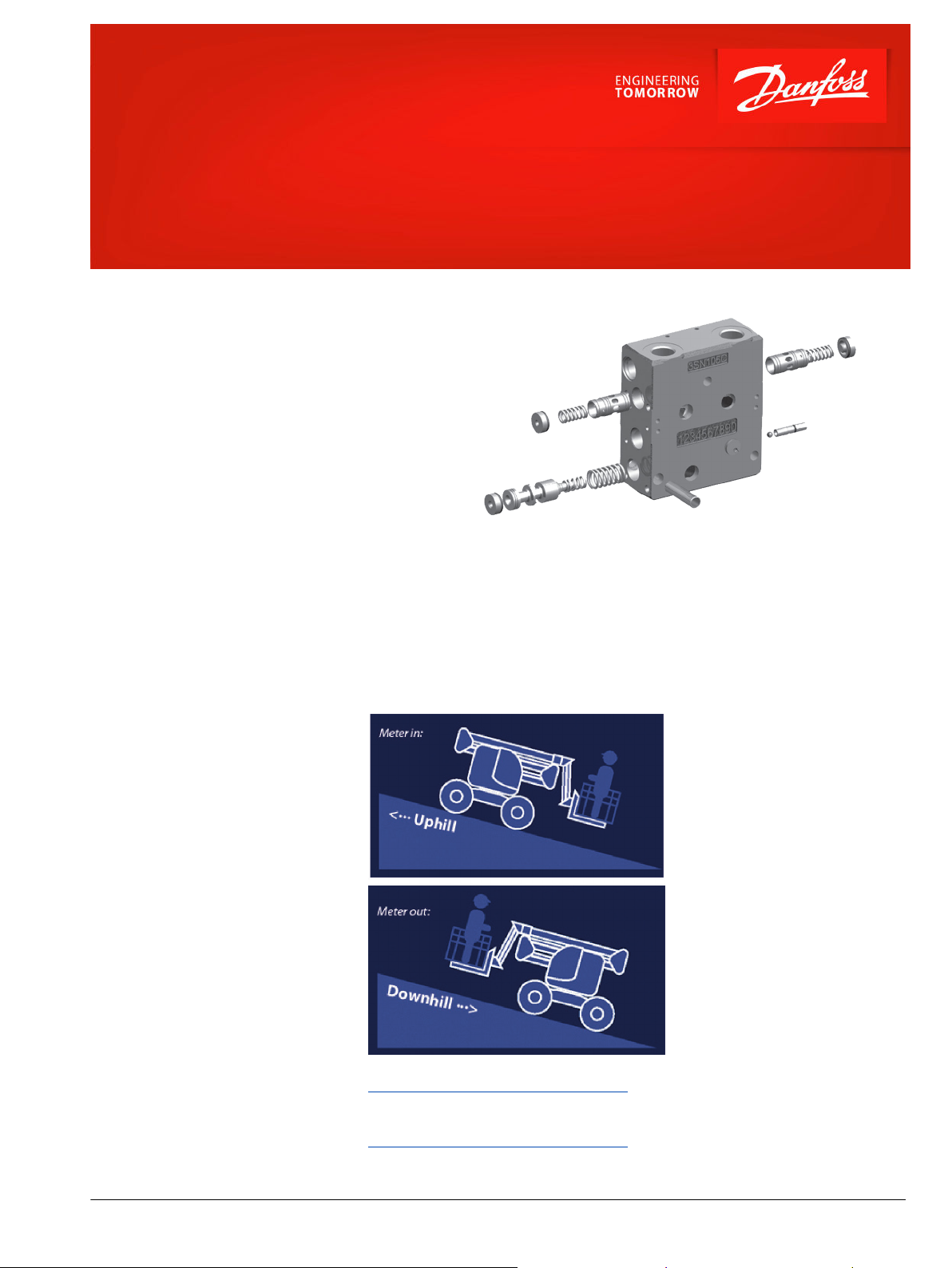
Data Sheet
Transmission Module
PVBM
Meter-In Meter-Out – Open Circuit Transmission
The Meter-in Meter-out module is designed primarily
for use with transmission hydraulic motors in e.q.
manlifts or demanding winch applications. The terms
Meter-In and Meter- Out relates to the oil flow being
metered into (Meter-In) and out from (Meter-Out) the
transmission motor by the PVG valve.
With the Meter-in Meter-out module both flows in
and out of the transmission motors are controlled at
the same time.
The Meter-in Meter-out module will ensure a stable,
well controlled movement of application when motor
is pushing (i.e. upwards hill) or motor being pulled
(i.e. downward hill) or horizontal movement.
Features
•
Integrated shock/anti-cavitation valve
(A- and B- port)
•
T0 connection
•
BSP/UNF
•
Meter-In compensator
•
Meter-Out compensator on A- and Bport
•
Increased control of negative loads
Comprehensive technical literature online
at powersolutions.danfoss.com
©
Danfoss | Mar 2017 L1117392 | AI00000124en-US0303 | 1
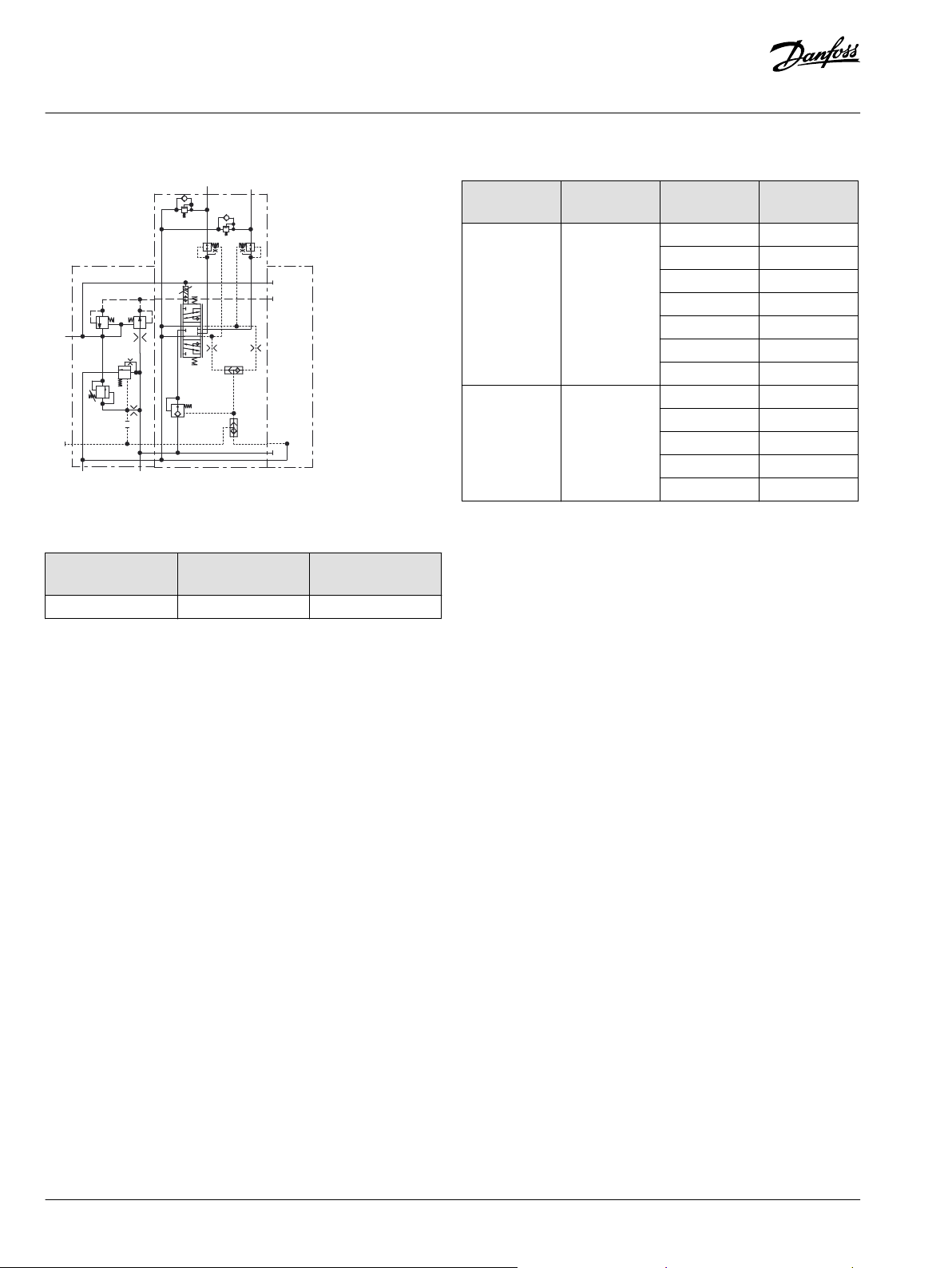
Data Sheet
Transmission Module PVBM
Schematic
Available spools
Flow
Characteristic
Progressive Closed neutral 5 11187198
Linear Closed neutral 10 11187177
Function in
Neutral
Flow l/min
(Symmetrical)
10 11185988
25 11186235
40 11186436
65 11186450
100 11156265
130 11156268
25 11187390
40 11187500
65 11187659
100 11156300
Part Number
Available modules
Description BSP G1/2 ports Code
No.
PVBM module 157B6268 11018399
SAE 7/8-14 ports
Code No.
Application Awareness
•
With the Meter-In Meter-Out module, stability is determined by ensuring that oil flow into the system is always lower than oil flow out
of the system. This is achieved by means of different spring settings in the Meter-In Meter-Out compensators. As an example, this
means that a motor will run faster in Meter-Out mode than in Meter-In mode.
•
Due to the Meter-out compensators, a backpressure valve is needed to avoid cavitations when running in meter-out situations. The
back pressure setting would be application dependent but typical values are between 5-10 bar. Increased back pressure setting
ensures better protection against cavitations but also decrease energy efficiencies. The hydraulic system would be leaking in neutral
when external forces acts on the working ports. To avoid unwanted movements of the applied motors, therefore external brakes are
needed.
•
Dependent on the application type smooth movement could be requested. PVE’s in combination with a controller and joystick could
be useful to add ramps on the spool and delay on the motor brakes so it doesn’t hit the brakes too hard when returning to neutral.
2 | © Danfoss | Mar 2017 L1117392 | AI00000124en-US0303

Data Sheet
Transmission Module PVBM
Technical specifications
Max. pressure Port P continuous, Port A/B 350 bar [5076 psi]
Port T static/dynamic 25/40 bar [362/580 psi]
Port A/B and P 130 l/min [34 US gal/min]
Oil flow, rated Port A/B and P 130 l/min [34 US gal/min]
Spool travel ±7 mm [±0.28 in]
Max. internal leakage A/B→T at 100 bar [1450 psi] and 21 mm2/s 1 l/min [61 in3/min]
Max. internal leakage A/B→T at 200 bar [2900 psi] and 21 mm2/s 1.5 l/min [92 in3/min]
Oil temperature (inlet) Recommended 30 → 60 °C [86 → 140°F]
Minimum -30 °C [-22 °F]
Maximum 90 °C [194 °F]
Ambient temperature -30 → 60 °C [-22 → 140 °F]
Oil viscosity Operating range 12-75 mm2/s [65-347 SUS]
Minimum 4 mm2/s [39 SUS]
Maximum 460 mm2/s [2128 SUS]
Filtration, max. contamination (ISO 4406) 18/16/13
©
Danfoss | Mar 2017 L1117392 | AI00000124en-US0303 | 3

Danfoss can accept no responsibility for possible errors in catalogues, brochures and other printed material. Danfoss reserves the right to alter its products without notice. This also applies to products
already on order provided that such alterations can be made without changes being necessary in specifications already agreed.
All trademarks in this material are property of the respective companies. Danfoss and the Danfoss logotype are trademarks of Danfoss A/S. All rights reserved.
4 | © Danfoss | Mar 2017 L1117392 | AI00000124en-US0303