
Instructions for Drilling and Assembling Series C Rotary Handle
Mechanism for M-Frame Series C Circuit Breakers, Molded Case Switches
WARNING
DO NOT ATTEMPT TO INSTALL OR PERFORM
MAINTENANCE ON EQUIPMENT WHILE IT IS ENERGIZED. DEATH, SEVERE PERSONAL INJURY, OR
SUBSTANTIAL PROPERTY DAMAGE CAN RESULT
FROM CONTACT WITH ENERGIZED EQUIPMENT.
ALWAYS VERIFY THAT NO VOLTAGE IS PRESENT
BEFORE PROCEEDING WITH THE TASK, AND
ALWAYS FOLLOW GENERALLY ACCEPTED SAFETY
PROCEDURES.
THE CUTLER-HAMMER CORPORATION (WESTINGHOUSE PRODUCTS) IS NOT LIABLE FOR THE
MISAPPLICATION OR MISINSTALLATION OF ITS
PRODUCTS.
The user is cautioned to observe all recommendations,
warnings and cautions relating to the safety of personnel
and equipment as well as all general and local health and
safety laws, codes and procedures.
I.L. 15603D
The recommendations and information contained herein
are based on Cutler-Hammer’s experience and judgment,
but should not be considered to be all-inclusive or
covering every application of circumstance which may
arise. If any questions arise, contact Cutler-Hammer for
further information of instructions.
DESCRIPTION
The Cutler-Hammer general purpose Rotary handle
mechanism is suitable for use with NEMA 1, 3R, 12 and
4, 4x fabricated enclosures. For NEMA 4 and 4x enclosures the rotary handle is labeled and gasketed for these
applications. It is designed for use with Series C –
M-Frame Circuit Breakers and Molded Case Switches up
to 800 amps.
Required for a standard application are the operating
handle, shaft, and mechanism.
The operating handle has been designed to meet NFPA
79 requirements. It may be mounted in either the horizontal or vertical direction. The handle was ergonomically
designed with extra clearance for a “gloved hand” to
operate. It may be padlocked in the OFF position utilizing
3 padlocks (.312 Max).
The standard label in the operating handle indicates ON/
Tripped/OFF/Open/Reset. To fulfill international requirements, an alternate handle may be ordered which
indicates (l)/Tripped/(O) /Open/Reset.
To meet the various enclosure depths, four variable depth
shafts are offered (6", 12", 16", and 24"). Each shaft
includes a support brace to ensure proper alignment. In
addition, the 16" and 24" extra long shafts include an
adjustable support bracket.
The standard mechanism located on the breaker does
include means for internally locking the breaker in the
“OFF” position with up to 3 padlocks each with a maximum diameter of .312".
As an option, an auxiliary switch is offered so that the
control panel builder may electrically indicate the status
of the breaker. This accessory would be mounted on the
mechanism and comes with 24" pigtail leads.
Fig. 1-1 M Rotary Handle Mechanism Assembly
Effective August 2009 Supersedes I.L. 15603C February 2002
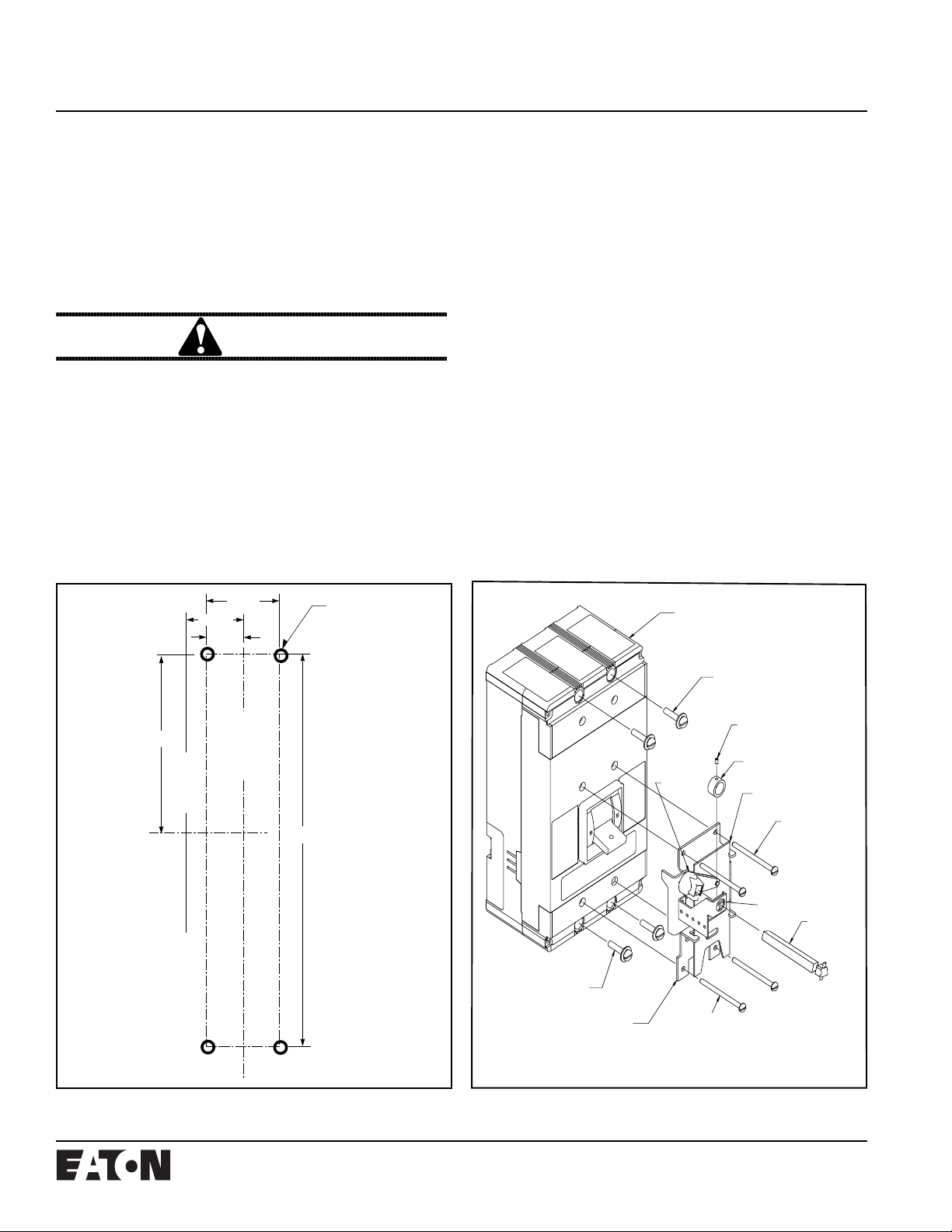
Page 2
I.L. 15603D
INSTALLATION INSTRUCTIONS:
The installation procedure consists of: drilling and modifying customer enclosure; installing the circuit breaker and
operating assembly; assembling the shaft to the operating assembly, and handle assembly to the enclosure
cover; testing function of installed handle mechanism. To
install the handle mechanism, perform the following
steps.
WARNING
WHEN INSTALLING A NEW HANDLE MECHANISM,
OR A NEW CIRCUIT BREAKER AND HANDLE
MECHANISM IN AN EXISTING ELECTRICAL SYSTEM, MAKE SURE THERE IS NO VOLTAGE
PRESENT WHERE WORK IS TO BE PERFORMED.
SPECIAL ATTENTION SHOULD BE PAID TO REVERSE FEED APPLICATIONS TO ENSURE NO
VOLTAGE IS PRESENT. THE VOLTAGES IN ENERGIZED EQUIPMENT CAN CAUSE DEATH OR SEVERE
PERSONAL INJURY.
2. 75
2.147
1.38
Ø .38
4 HOLES
or .31-18 TAP
Installation of Circuit Breaker and Operating
Assembly
1. Determine position for circuit breaker in enclosure.
Drill and/or tap circuit breaker mounting holes in
enclosure mounting surface as shown in Fig. 2-1.
2. Turn circuit breaker to “OFF” position.
3. Mount circuit breaker to enclosure using the four (4)
5/16-18x1.25" long screws in the hardware kit. Insert
screws and lockwashers into load and line end circuit
breaker mounting holes and tighten securely. (Fig. 2-
2.)
4. Mount mechanism onto circuit breaker, ensuring slide
plate is engaged with the circuit breaker handle.
Remove the (2) breaker cover screws and (2) load
cover screws as shown in Fig. 2-2 and discard. Insert
the (4) screws (.190-32 x 1.75) enclosed, along with
lockwashers from the hardware kit, through the
mounting holes of the mechanism and into the empty
cover screw holes of the circuit breaker, as shown on
Fig. 2-2.
M-FRAME
LINE
6.742
BREAKER
L
C
ROTARY
L
C
HANDLE
CL ROTARY
HANDLE
14.75
Fig. 2-1 Drill & Tapping Plan for M-Frame Breaker
5/16 -18 X1.25"
FOR ENCLOSURE MTG.
Torque 10-12 ft-lbs
(13.5-16.2 Nm)
SET SCREW
COLLAR - HOLDS
SHAFT IN PLACE
ROTARY
MD-MECH.
SLIDER
REMOVE (2)
COVER
SCREW AND
DISCARD.
USE THE (2)
.190-32 x 1.75"
Torque 24-25 in-lb
(2.7-2.8 Nm)
SHAFT
SUPPORT
LOAD
5/16 - 18 X 1.25"
FOR MTG TO
ENCLOSURE
Torque 10-12 ft-lbs
(13.5-16.2 Nm)
BASE
PLATE
PIVOT LINK
REMOVE (2)
LOAD END
COVER
SCREW AND
USE THE (2)
.190-32 x 1.75"
Torque 24-25 in-lb
(2.7-2.8 Nm)
Fig. 2-2 M-Frame Breaker/Mechanism Assembly
SHAFT
Eective August 2009
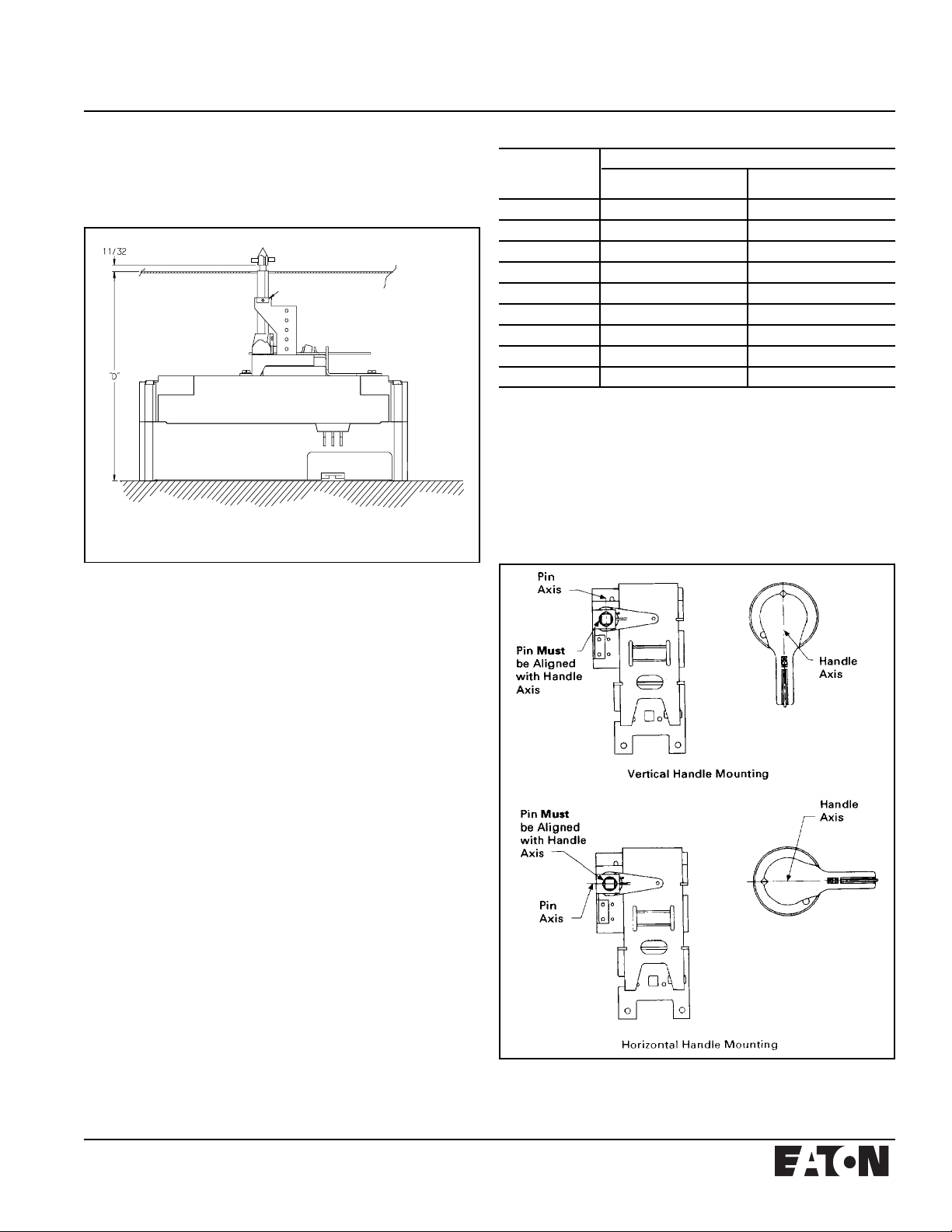
I.L. 15603D
Page 3
Installation of Shaft to Operating Assembly
1. Measure panel depth “D” to determine shaft length
by subtracting 4.50" from this dimension.
Collar With Set Screw
Shaft Length = "D" - 4.50
Fig. 3-1 Cutting Shaft to Length and Collar to Shaft
2. Mark shaft, measuring length beginning at the
pointed end and cut to correct length. (Fig. 3-1)
3. If adjustable support extension is being used (designed for 16" and 24" shaft lengths), install loosely
at this time. Remove screws from extension and use
to attach to shaft support bracket.
4. Place square end of shaft into square opening of die
cast pivot link on the operating mechanism to the
circuit breaker. Ensure pin is in shaft correctly
oriented with respect to anticipated handle position
(vertical or horizontal handle placement, see Fig. 3-
2).
5. Take set screw and shaft collar from hardware kit and
insert set screw into shaft collar. Place square end of
shaft through shaft support bracket then through
shaft collar and into square opening of die cast pivot
link on the operating mechanism attached to the
circuit breaker, as shown on Fig. 2-2. Position shaft
collar lightly against the underside of the shaft
support collar and torque set screw between 28-30
in-lbs.
6. For vertical or horizontal handle mounting orientation,
see Fig. 3-3.
7. If adjustable support extension is being used, tighten
securely at this time.
Distance Correction
from
Hinge
4 3/16" 9/16"
5 5/32” 7/16"
6 1/8" 11/32"
7 3/32" 9/32"
8 3/32" 1/4"
9 3/32" 7/32"
10 1/16" 3/16"
11 1/16" 3/16"
12 1/16" 5/32"
Flat Hinge Offset Hinge
Table 4.1 Correction Factor Table
Installation of Handle Assembly onto Enclosure
Cover
1. To determine where to drill the enclosure door cover,
close the cover with moderate force in order to cause
the point of the shaft to scratch/mark the paint on the
inside of the door.
Fig. 3-2 Handle Orientation
Eective August 2009