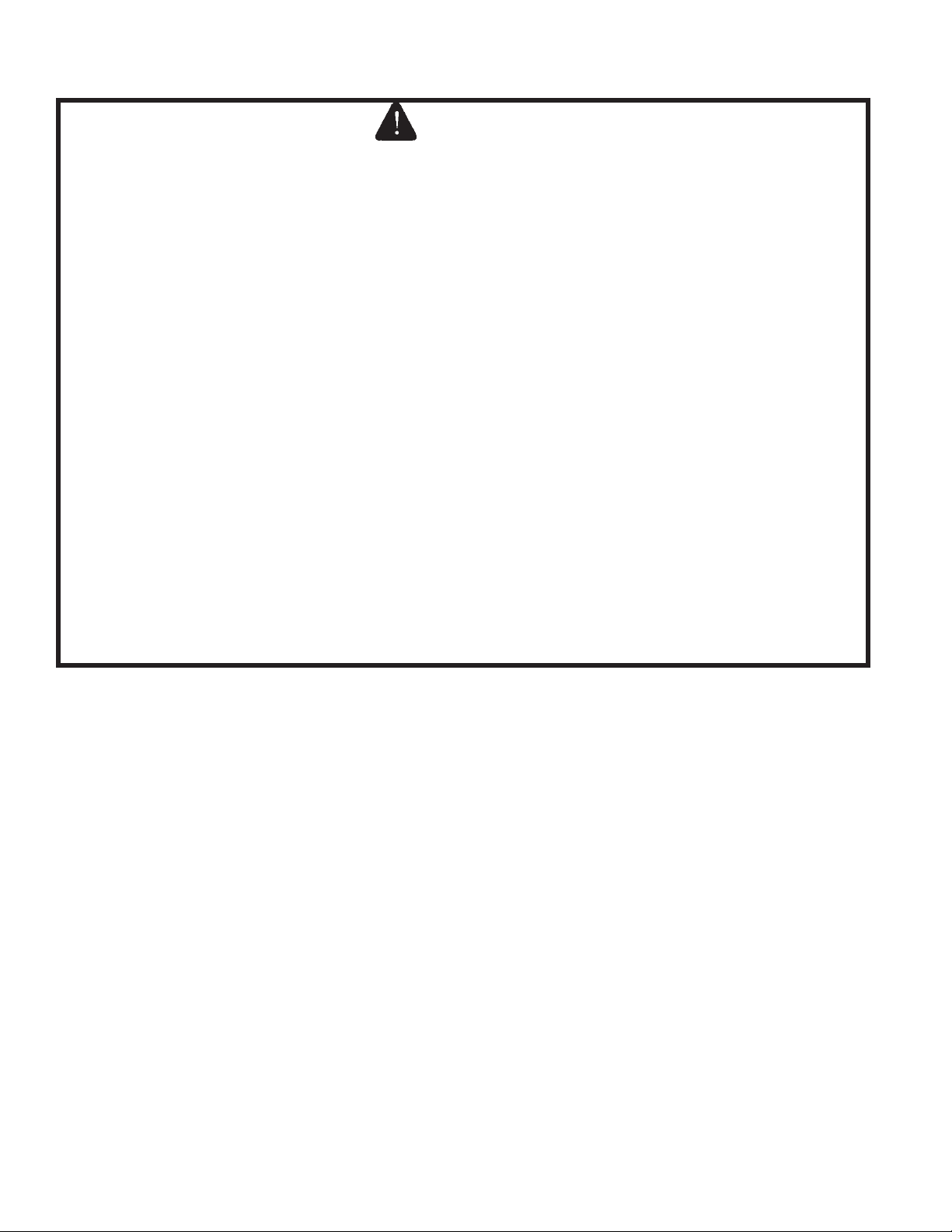
XII Service and Maintenance
WARNING
• THE BOILER CONTAINS REFRACTORY CERAMIC FIBER, A POSSIBLE HUMAN
CARCINOGEN. USE A NIOSH APPROVED RESPIRATOR WHEN SERVICING
HIGH-TEMPERATURE INSULATION AND GASKET MATERIALS. WASH EXPOSED
SKIN GENTLY WITH SOAP AND WATER AFTER CONTACT. WASH EXPOSED
CLOTHING SEPERATE FROM NORMAL LAUNDRY.
• LABEL ALL WIRES PRIOR TO DISCONNECTION WHEN SERVICING CONTROLS.
WIRING ERRORS CAN CAUSE IMPROPER AND DANGEROUS OPERATION.
VERIFY PROPER OPERATION AFTER SERVICING.
• FAILURE TO MAINTAIN THE BOILER IN PROPER WORKING CONDITION MAY
LEAD TO FIRE, EXPLOSION, PERSONAL INJURY OR DEATH AND EXTENSIVE
PROPERTY DAMAGE.
• TURN OFF ALL GAS AND ELECTRIC POWER SUPPLIES TO THE BOILER BEFORE
SERVICING. CONTACT WITH OR RELEASE OF DANGEROUS FLAMMABLE
GAS, ELECTRICAL VOLTAGE, MOVING PARTS AND VERY HOT WATER UNDER
PRESSURE MAY CAUSE SERIOUS PERSONAL INJURY, PROPERTY DAMAGE OR
DEATH.
• LOCK ELECTRICAL BOXES AND GAS VALVES CLOSED TO PREVENT SOMEONE
FROM INADVERTENTLY RESTORING POWER OF GAS BEFORE THE HEATING
SYSTEM IS SAFE TO OPERATE.
• WATER LEAKS CAN CAUSE SEVERE CORROSION DAMAGE TO THE BOILER OR
OTHER SYSTEM COMPONENTS. REPAIR ANY LEAKS FOUND IMMEDIATELY.
The following routine maintenance should be performed on an annual basis:
1) Turn off electrical power and gas supply to the boiler
2) Inspect the ue passages for signs of blockage. If there is any carbon in the combustion chamber or the ue passages,
clean the heat exchanger before proceeding further. See the cleaning procedure below.
3) Remove all burners, noting the location of the pilot main burner. If burners show signs of deterioration, they should be
replaced (some discoloration around the burner ports is normal). Clean the burners by rst brushing the ports with a soft
bristle brush and then vacuuming out any debris through the venturi opening.
4) Remove any debris found in the combustion chamber, being careful not to disturb combustion chamber insulation.
5) Inspect the pilot assembly. Clean any deposits found on the electrode and grounding strap. The ideal gap between the
electrode and the ground strap is 1/8”. Inspect the porcelain for cracks or other deterioration. Replace pilot assembly if
deterioration is found.
6) Inspect the combustion chamber insulation for deterioration.
7) Inspect the ignition cable insulation for cracks or other deterioration. If deterioration is found, replace cable.
8) Reinstall burners, being careful to put the pilot main burner in its original location.
9) Inspect all boiler wiring for loose connections or deterioration.
10) Inspect the vent system:
• Make sure that the vent system is free of obstructions.
• Make sure that all vent system supports are intact.
• Inspect joints for signs of condensate or ue gas leakage.
• Inspect venting components for corrosion or other deterioration. Replace any defective vent components.
36
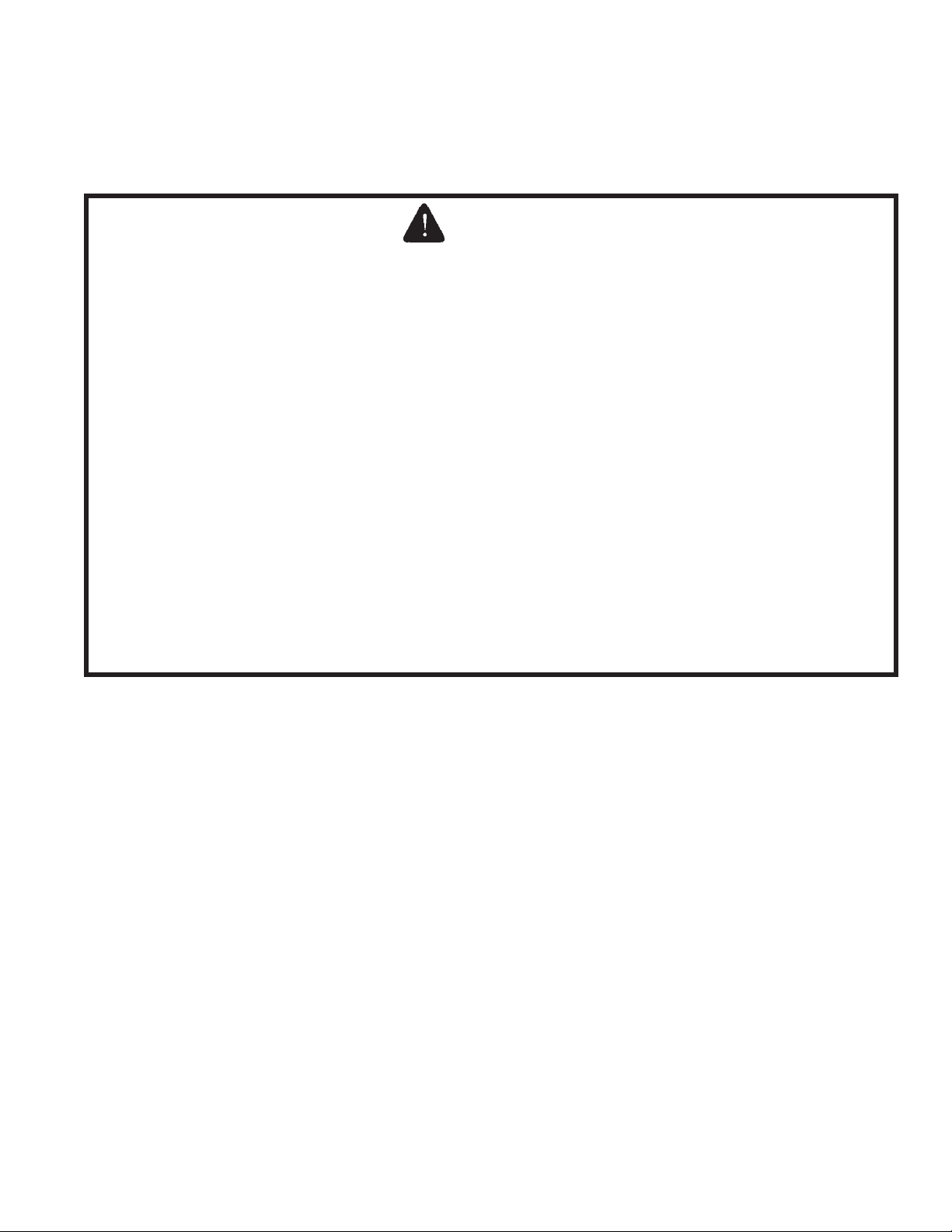
11) Inspect the boiler and hydronic system for leaks.
12) Place the boiler back in operation using the procedure outlined in “Start-up”. Check the pilot line and any other gas pip
ing disturbed during the inspection process for leaks.
Heat Exchanger Cleaning Procedure
WARNING
SOOT DEPOSITS IN THE FLUE PASSAGES ARE A SIGN THAT THE BOILER MAY BE
OPERATING AT HIGH CARBON MONOXIDE (CO) LEVELS. AFTER CLEANING THE
BOILER OF SOOT DEPOSITS, CHECK THE CO LEVEL IN THE FLUE GAS TO INSURE
THAT THE BOILER IS OPERATING PROPERLY.
If it is necessary to check CO, use a combustion analyzer, or other instrument which is designed to measure
CO in flue gas. A CO “sniffer” designed for testing CO levels in ambient air cannot be used to check boiler combustion. Take a flue gas sample by inserting a sample probe through the draft diverter opening and into the flue
collector so that the sample is taken in the area directly over the heat exchanger. Do not take a sample until
the boiler has been firing for at least five minutes. A normal CO reading for an AWR series boiler is less than
50ppm (0.005%). A reading of more than 100ppm (0.01%) is indicative of a combustion problem.
Some causes of excessive CO include:
• Incorrectly sized main burner orifice for the altitude at which boiler is installed
• Crooked or out-of-round orifice holes (never attempt to drill orifice for this boiler in the field)
• Partially plugged flue passages
• Improper manifold pressure
• Foreign material in burner venturis or burner ports
• Leak in seal between flue collector and heat exchanger
• Inadequate supply of combustion air
1) Turn off electrical power and gas supply to the boiler.
2) Disconnect the damper and vent connector from the boiler.
3) Remove the top jacket panel. If possible, remove the rear and left side jacket panels
4) Remove the burners.
5) Disconnect the wiring at the blocked vent switch.
6) Remove the four #10 sheet metal screws holding the ue collector onto the block. Also remove the two #10 sheet metal
screws securing the ue collector to the rear jacket panel.
7) Remove the ue collector from the heat exchanger.
8) Carefully remove the ue collector gasket strips and set them aside.
9) Clean the ue passageways using a stiff bristle brush. Be certain that all foreign material is removed from the gaps
between the pins.
10) Clean the bottom surfaces of the heat exchanger.
11) Put a light in the combustion chamber and look through the ue passages from the top to verify that they have been
thoroughly cleaned.
12) Replace the ue collector gasket strips. If desired, RTV-732 silicone sealant with a 500F intermittent duty temperature
rating may be substituted for this rope gasket. The ue collector must be thoroughly sealed to the heat exchanger.
13) Reattach the ue collector.
14) Reattach all the jacket components.
15) Reinstall burners, being careful to put the pilot main burner in its original location.
16) Replace the blocked vent switch.
17) Reconnect the damper and vent system.
37