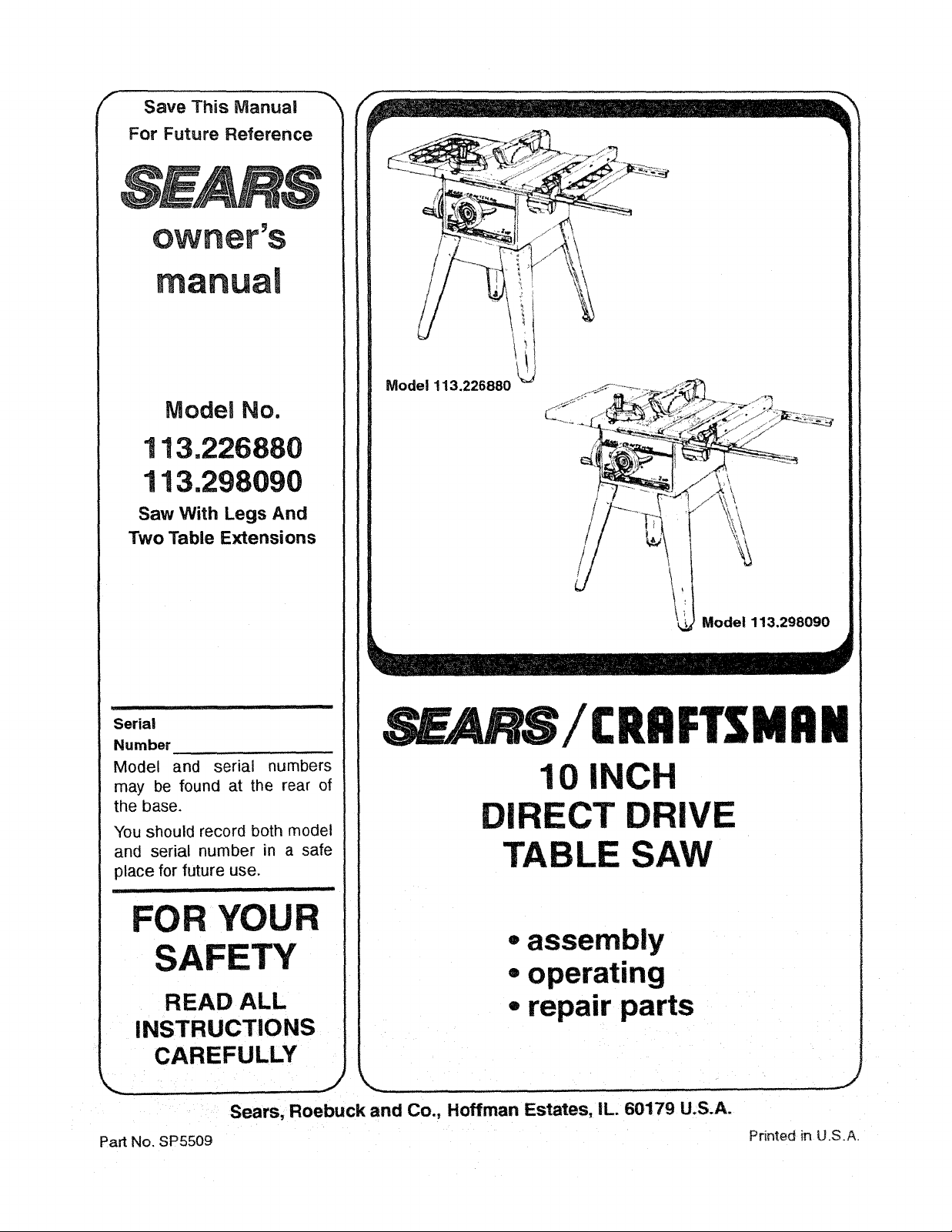
f
Save This lVlanuai
For Future Reference
Model No.
113,226880
Model 113.226880
1!3.298090
Saw With Legs And
Two Table Extensions
L L I
Serial
Number
Model and serial numbers
may be found at the rear of
the base.
You should record both model
and serial number in a safe
place for future use.
JJ
YOUR
SAFETY
READ ALL
INSTRUCTIONS
CAREFULLY
l
/
/
!
Model 113,298090
. . 6/CRRFTSMRN
10 INCH
DIRECT DRIVE
TABLE SAW
• assembly
=operating
- repair parts
%_,=,
Sears, Roebuck and Co., Hoffman Estates, iL. 60179 U.S.A.
Part No, SP 5509 Printed in U.S.A.
.J _.
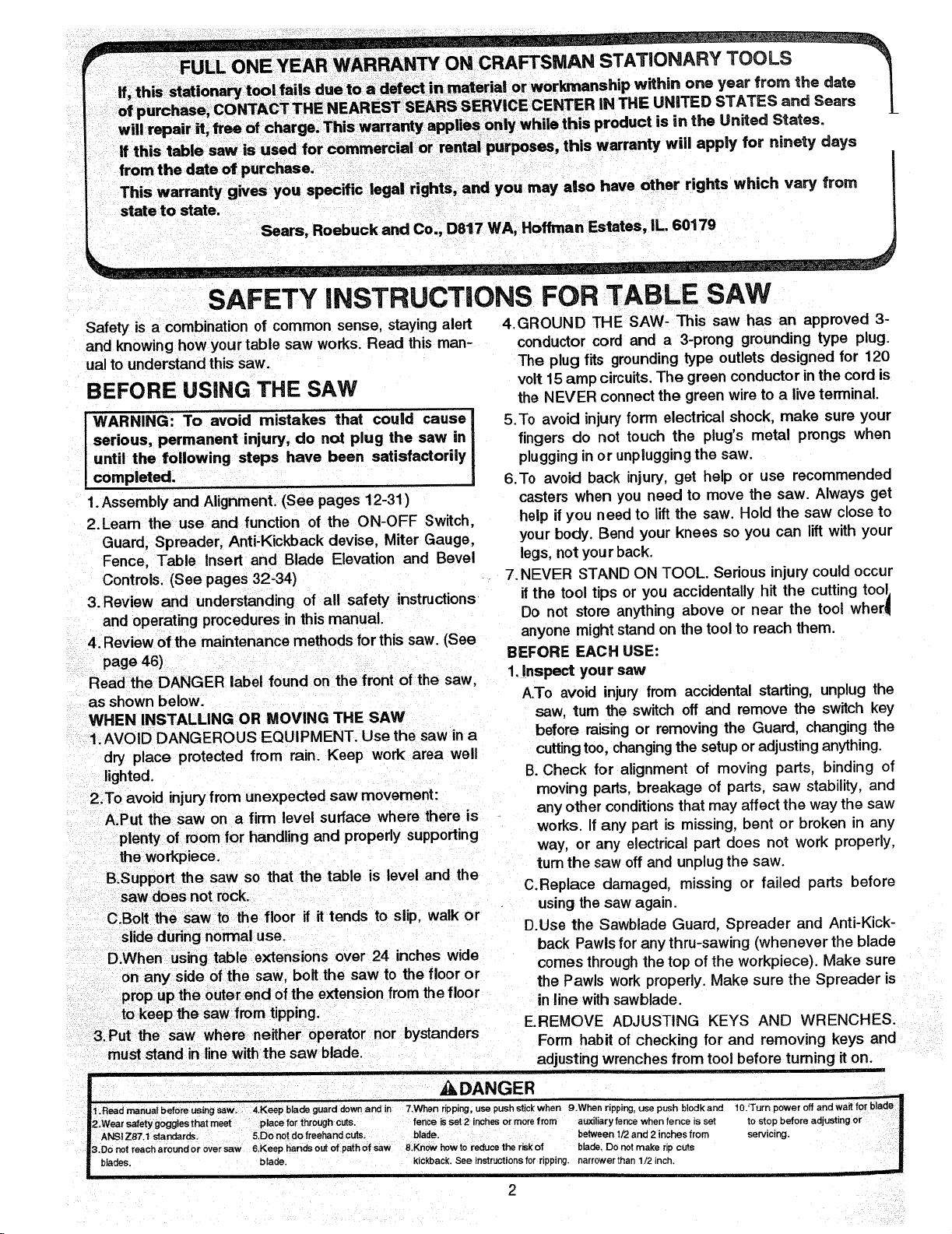
will repair it, free of charge. This warranty appUesonly while this product is in the United States.
If this table saw is used for commercial or rental purposes, this warranty wig apply for ninety days
from the date of purchase. |
This warranty gives you specific legal rights, and you may also have other rights which vary from
state to state.
Sears, Roebuck and Co., D817 WA, Hoffman Estates, IL. 60179
/
J
SAFETY INSTRUCT|ONS FOR TABLE SAW
Safety is a combination of common sense, staying alert 4.GROUND THE SAW- This saw has an approved 3-
and knowing how your table saw works. Read this man- conductor cord and a 3-prong grounding type plug.
ual to understand this saw. The plug fits grounding type outlets designed for 120
volt 15amp circuits.The green conductor in the cord is
BEFORE USING THE SAW the NEVER connect the green wire to a live terminal.
WARNING: To avoid mistakes that could cause_
serious, permanent injury, do not plug the saw in
until the following steps have been satisfactorily
completed.
1.Assembly and Alignment. (See pages 12-31 )
2.Learn the use and function of the ON-OFF Switch,
Guard, Spreader, Anti-Kickback devise, Miter Gauge,
Fence, Table Insert and Blade Elevation and Bevel
Controls. (See pages 32-34)
3. Review and understanding of all safety instructions
and operating procedures in this manual.
4. Review ofthe maintenance methods for this saw. (See
page 46)
Read the DANGER label found on the front of the saw,
as shown below.
WHEN INSTALLING OR MOVING THE SAW
1.AVOID DANGEROUS EQUIPMENT. Use the saw in a before raising or removing the Guard, changing the
dry place protected from rain. Keep work area well cuttingtoo, changingthe setupor adjustinganything.
lighted.
2.To avoid injuryfrom unexpected saw movement:
A.Put the saw on a firm level surface where there is
plenty of room for handling and properly supporting
the workpiece.
B.Support the saw so that the table is level and the
saw does not rock.
C.Bolt the saw to the floor it it tends to slip, walk or
slideduring nomnaluse.
D.When using table extensions over 24 inches wide
on any side of the saw, bolt the saw to the floor or
prop up the outer end ofthe extension from the floor in line with sawblade.
to keepthe saw from tipping. E.REMOVE ADJUSTING KEYS AND WRENCHES.
3.Put the saw where neither Operator nor bystanders Form habit of checking for and removing keys and
muststand in line with the saw blade, adjusting wrenches from tool before turning it on.
5.To avoid injury form electrical shock, make sure your
fingers do not touch the plug's metal prongs when
I
plugging in or unpluggingthe saw.
6.To avoid back injury, get help or use recommended
casters when you need to move the saw. Always get
help if you need to lift the saw. Hold the saw close to
your body. Bend your knees so you can lift with your
legs, not your back.
7. NEVER STAND ON TOOL. Serious injurycould occur
if the tool tips or you accidentally hit the cutting toolj
Do not store anything above or near the tool wher4
anyone might stand on the tool to reach them.
BEFORE EACH USE:
1.inspect your saw
A.To avoid injury from accidental starting, unplug the
saw, turn the switch off and remove the switch key
B. Check for alignment of moving parts, binding of
moving parts, breakage of parts, saw stability, and
any other conditions that may affect the way the saw
works. If any part is missing, bent or broken in any
way, or any electrical part does not work properly,
turn the saw off and unplug the saw.
C.Reptace damaged, missing or failed parts before
using the saw again.
D.Use the Sawblade Guard, Spreader and Anti-Kick-
back Pawls for any thru-sawing (whenever the blade
comes through the top of the workpiece). Make sure
the Pawls work properly. Make sure the Spreader is
I _DANGER
1 Read manual before using saw. 4.Keep bade guard down and in 7.When tipping, use push stick when 9.When ripping, use push blodk and 10.'Turn power off and wait for blade |
|2,Wear safety goggles that meat place for through cuts. fence is set 2 inches or more from auxiliary fence when fence is set to stop before adjusting or !
| ANSI Z87.1 standerds. 5,Do not do freshand cuts. blade, between l/2 and 2 inches from servicing, /
3.Do not reach around or over saw 6,Kesp hands out of path of saw 8.Kncw how to reduce the risk of blade. Do not make rip cuts
blades, blade, kickback, See instrustions for ripping, narrower than 1/2 inch.
2
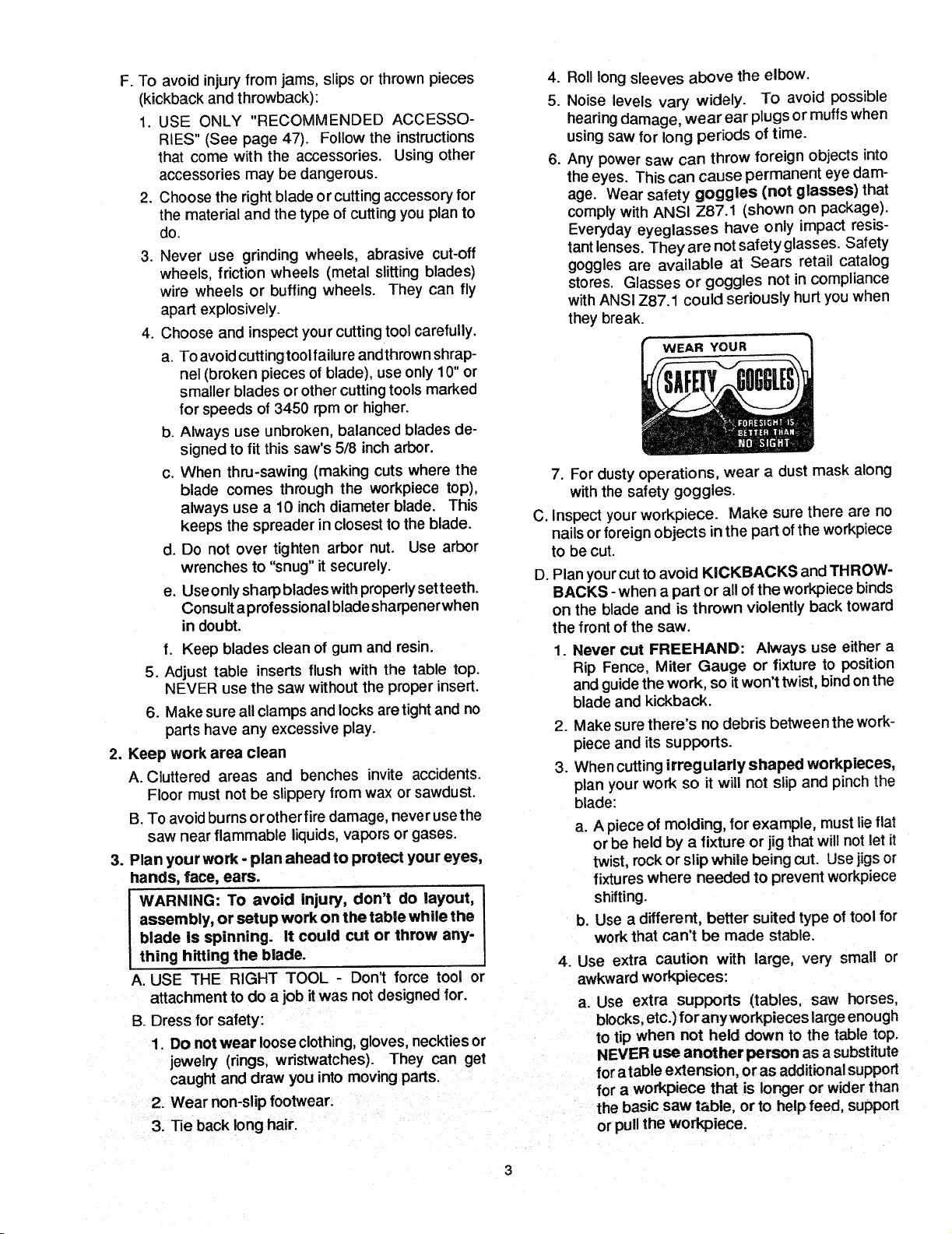
F.Toavoidinjuryfromjams,slipsorthrownpieces
(kickbackandthrowback):
1.USEONLY"RECOMMENDEDACCESSO-
RIES"(Seepage47). Followtheinstructions
thatcomewiththeaccessories.Usingother
accessoriesmaybedangerous.
2. Choosetherightbladeorcuttingaccessoryfor
thematerialandthetypeofcuttingyouplanto
do.
3. Neverusegrindingwheels, abrasive cut-off
wheels, friction wheels (metal slitting blades)
wire wheels or buffing wheels. They can fly
apart explosively.
4. Choose and inspect your cutting tool carefully.
a. To avoid cutting tool failure and thrown shrap-
nel (broken pieces of blade), use only 10" or
smaller blades or other cutting tools marked
for speeds of 3450 rpm or higher.
b. Always use unbroken, balanced blades de-
signed to fit this saw's 5/8 inch arbor.
c. When thru-sawing (making cuts where the
blade comes through the workpiece top),
always use a 10 inch diameter blade. This
keeps the spreader in closest to the blade.
d. Do not over tighten arbor nut. Use arbor
wrenches to "snug" it securely.
e. Use only sharp blades with properly setteeth.
Consult a professional blade sharpenerwhen
in doubt.
f. Keep blades clean of gum and resin.
5. Adjust table inserts flush with the table top.
NEVER use the saw without the proper insert.
6. Make sure all clamps and locks are tight and no
parts have any excessive play.
2. Keep work area clean
A. Cluttered areas and benches invite accidents.
Floor must not be slippery from wax or sawdust.
B. To avoid burns or other fire damage, never use the
saw near flammable liquids, vapors or gases.
3. Plan your work - plan ahead to protect your eyes,
hands, face, ears.
WARNING: To avoid injury, don't do layout,
assembly, or setup work on the table while the
blade is spinning. It could cut or throw any-
thing hitting the blade.
A. USE THE RIGHT TOOL - Don't force tool or
attachment to do a job it was not designed for.
B. Dress for safety:
1. Do not wear loose clothing,gloves, neckties or
jewelry (rings, wristwatches). They can get
caught and draw you into moving parts.
2. Wear non-slip footwear.
3. Tie back long hair.
.
Roll long sleeves above the elbow.
5.
Noise levels vary widely. To avoid possible
hearing damage, wear ear plugs or muffs when
using saw for long periods of time.
.
Any power saw can throw foreign objects into
the eyes. This can cause permanent eye dam-
age. Wear safety goggles (not glasses) that
comply with ANSI Z87.1 (shown on package).
Everyday eyeglasses have only impact resis-
tant lenses. They are not safety glasses. Safety
goggles are available at Sears retail catalog
stores. Glasses or goggles not in compliance
with ANSI Z87.1 could seriously hurt you when
they break.
WEAR YOUR
7. For dusty operations, wear a dust mask along
with the safety goggles.
C. Inspect your workpiece. Make sure there are no
nails or foreign objects in the part of the workpiece
to be cut.
D. Plan your cut to avoid KICKBACKS and THROW-
BACKS -when a part or all of the workpiece binds
on the blade and is thrown violently back toward
the front of the saw.
.
Never cut FREEHAND: Always use either a
Rip Fence, Miter Gauge or fixture to position
and guidethe work, so itwon't twist, bind onthe
blade and kickback.
2. Make sure there's no debris between the work-
piece and its supports.
3. When cutting irregularlyshaped workpieces,
plan your work so it will not slip and pinch the
blade:
a. A piece of molding, for example, must lieflat
or be held by a fixture or jigthat will not let it
twist, rock or slip while being cut. Use jigs or
fixtures where needed to prevent workpiece
shifting.
b. Use a different, better suited type of tool for
work that can't be made stable.
4. Use extra caution with large, very small or
awkward workpieces:
a.
Use extra supports (tables, saw horses,
blocks, etc.) for anyworkpieces large enough
to tip when not held down to the table top.
NEVER use another person as a substitute
for atable extension, oras additional support
for a workpiece that is longer or wider than
the basic saw table, or to help feed, support
or pullthe workpiece.
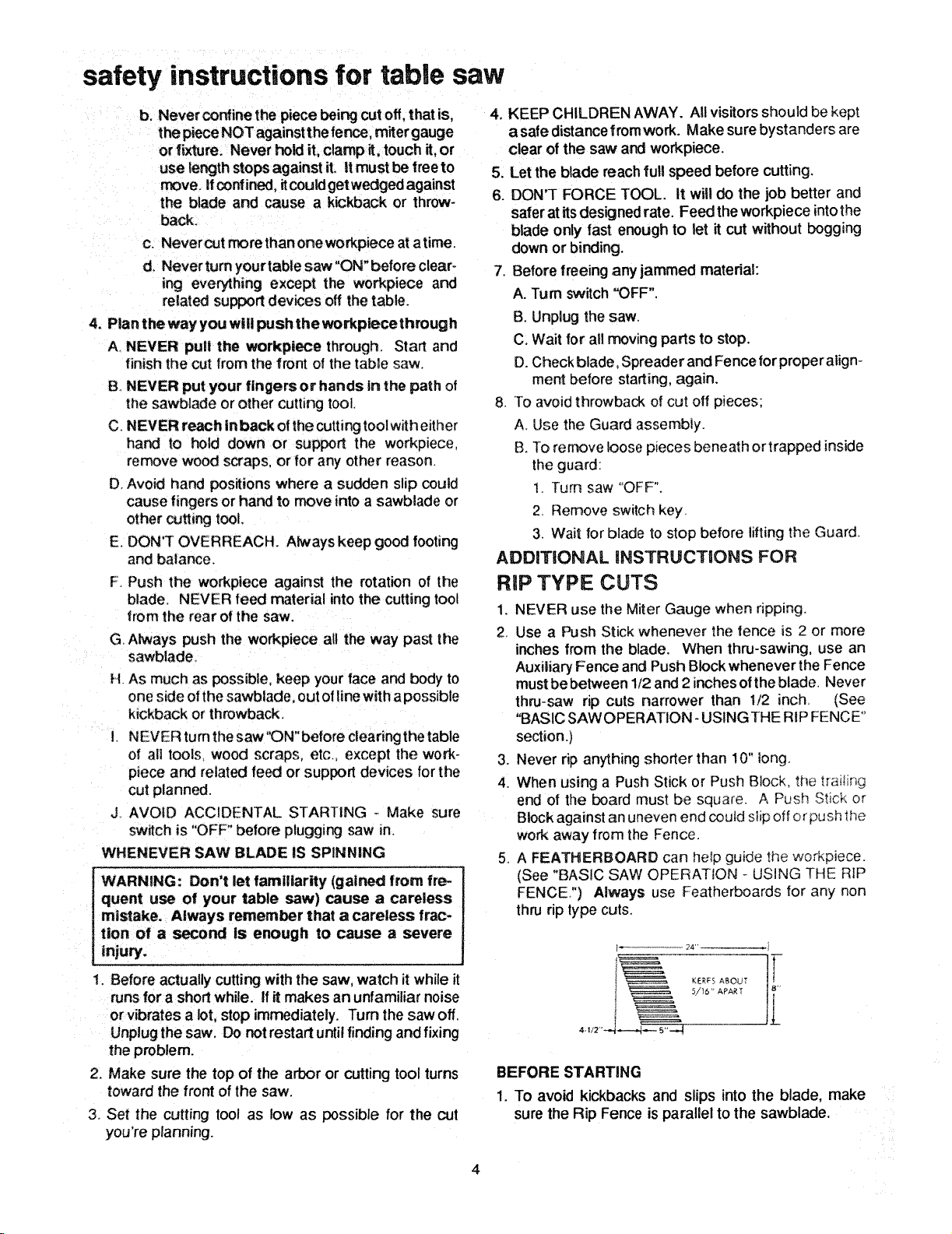
safety instructions for table saw
b. Never confine the piece being cut off, that is,
the pieceNOT against the fence, mitergauge
or fixture. Never hold it, clamp it. touch it, or
use length stops against it. itmust be free to
move. Ifconfined, itcouldgetwedged against
the blade and cause a kickback or throw-
back.
c. Never cut more than one workpiece at a time.
d. Never turn your table saw"ON" before clear°
ing everything except the workpiece and
related support devices off the table.
4. Plan the way you wil! push the workplece throug h
A NEVER pull the workpiece through. Start and
finish the cut from the front of the tabb saw.
B. NEVER putyour fingers or hands in the path of
the sawblade or other cuthng tool.
C. NEVER reach inback of the cutting toolwith either
hand to hold down or support the workpiece,
remove wood scraps, or for any other reason.
D Avoid hand positions where a sudden slip could
cause fingers or hand to move into a sawblade or
other oJtting tool,
E. DON'T OVERREACH. Always keep good footing
and balance.
F. Push the workpiece against the rotation of the
blade, NEVER feed material intothe cutting tool
from the rear of the saw.
G Always push the workpiece all the way past the
sawblade.
H. As much as possible, keep your face and body to
one side ofthe sawblade, out of linewith a possible
kickback or throwback.
I NEVER turn the saw"ON"before clearingthetabte
of al! tools wood scraps, etc., except the work-
piece and related feed or support devices for the
cut planned.
J, AVOID ACCIDENTAL STARTING - Make sure
switch is "OFF" before plugging saw in.
WHENEVER SAW BLADE iS SPINNING
WARNING: Don't let familiarity (gained from fre-
quent use of your table saw) cause a careless
mistake. Always remember that a careless frac-
tion of a second is enough to cause a severe
injury.
4. KEEP CHILDREN AWAY. All visitors should be kept
asafe distance fromwork. Make sure bystanders are
clear of the saw and workpiece.
5, Let the blade reach full speed before cutting.
6. DON'T FORCE TOOL. It will do the job better and
safer atits designed rate. Feedthe workpiece intothe
blade only fast enough to let it cut without bogging
down or binding.
7. Before freeing any jammed materiah
A. Turn switch "OFF".
B. Unplug the saw.
C. Wait for all moving parts to stop.
D. Check blade, Spreader and Fence for proper align-
ment before starting, again.
8. To avoid throwback of cut off p_eces:
A Use the Guard assembly.
B. To remove loose pieces beneath or trapped inside
the guard:
1. Turn saw "OFF".
2. Remove switch key
3. Wait for blade to stop before liftingthe Guard.
ADDITIONAL _NSTRUCTIONS FOR
RiP TYPE CUTS
1. NEVER use the Miter Gauge when ripping.
2 Use a Push Stick whenever the fence is 2 or more
inches from the blade. When thru-sawing, use an
Auxiliary Fence and Push Block whenever the Fence
must bebelween 1/2 and 2 inchesof the blade. Never
thru-saw rip cuts narrower than t/2 inch (See
'_ASIC SAW OPERATION -USING THE RIP FENCE"
section.)
3. Never rip anything shorter than 10" long.
4. When using a Push Stick or Push Btock, the traiting
end ot the board must be square. A Push Stick or
Block against an uneven end coutd stip off or push the
work away from the Fence.
5, A FEATHERBOARD can help guide the workpiece.
(See "BASIC SAW OPERATION - USING THE RIP
FENCE.") Always use Featherboards for any non
thru rip type cuts.
24 _i
1. Before actually cutting with the saw, watch itwhile it
runs for a short while. If it makes an unfamiliar noise
or vibrates a lot, stop immediately. Turn the saw off,
Unplug the saw. Do not restart until finding and fixing
the problem.
2. Make sure the top of the arbor or cutting tool turns
toward the front of the saw.
3. Set the cutting tool as low as possible for the cut
you're planning.
S/16" APART
BEFORE STARTING
1. To avoid kickbacks and slips into the blade, make
sure the Rip Fence is parallel to the sawblade.
4
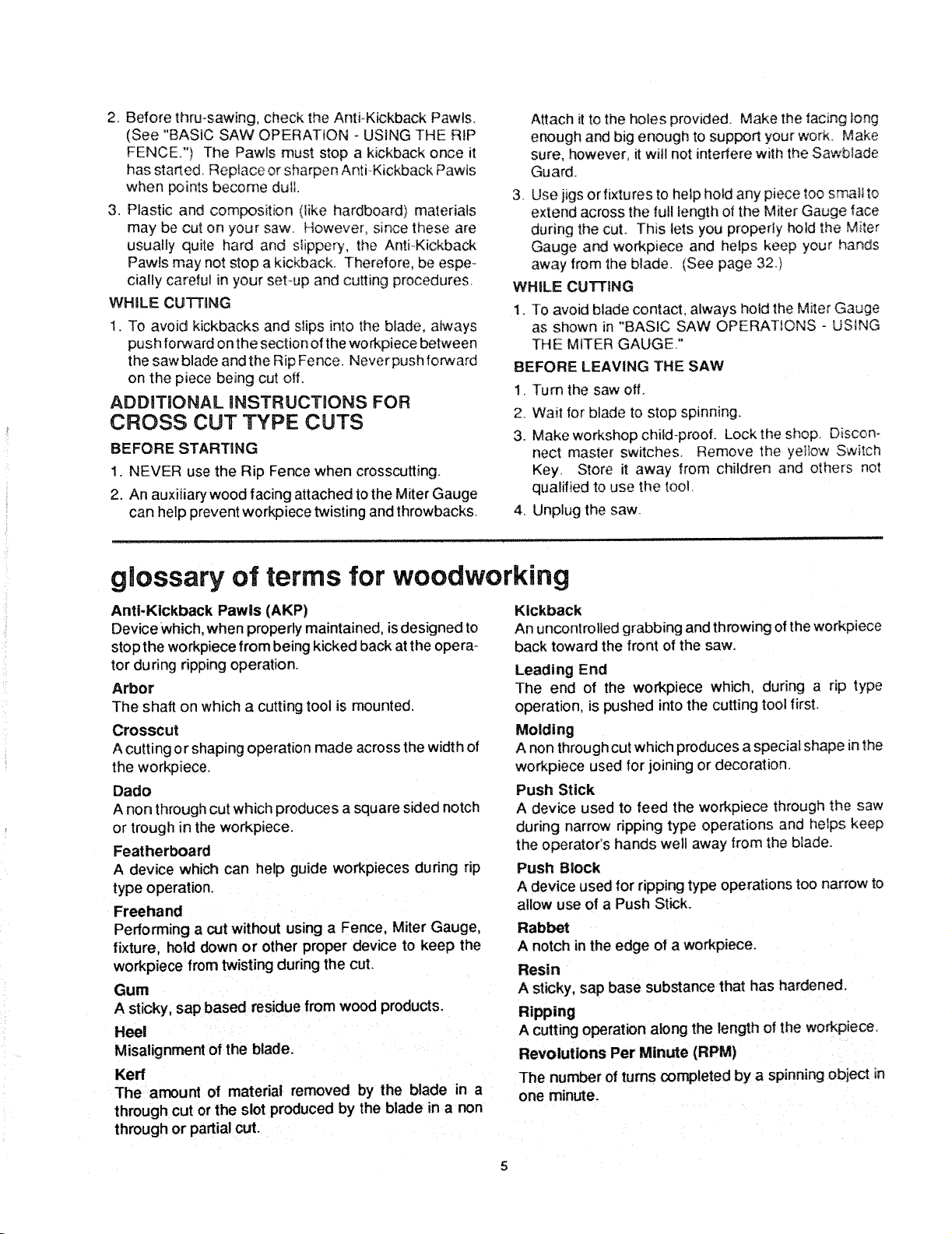
2_ Before thru-sawing, check the AntioKickback Pawls.
(See "BASIC SAW OPERATION - USING THE RIP
FENCE.") The Pawls must stop a kickback once it
has started Replace or stlarpen Anti-Kickback Pawls
when points become duti.
3. Plastic and composition (like hardboard) materials
may be cut on your saw However, since these are
usually quite hard and slippery, the Anti-Kickback
Pawls may not stop a kickback. Therefore, be espe-
cially careful in your set-up and cutting procedures
WHILE CUTTING
1. To avoid kickbacks and slips into the blade, always
push forward on the section of the workpiece between
the saw blade andthe Rip Fence. Never push forward
on the piece being cut off.
ADDITIONAL INSTRUCTOONS FOR
CROSS CUT TYPE CUTS
BEFORE STARTING
1. NEVER use the Rip Fence when crosscutting.
2. An auxiliary wood facing attached [o the Miter Gauge
can help prevent workpiece twisting and throwbacks
Attach it to the holes provided. Make the facing iong
enough and big enough to support your work. Make
sure, however, it witl not interfere with the Sawbfade
Guard..
3. Use jigs or fixtures to help hold any piece too sina!! to
extend across the full length of the Miter Gauge face
during the cut. This lets you properly hold the Miter
Gauge and workpiece and helps keep your hands
away from the blade. (See page 32,)
WHILE CUTTING
1. To avoid blade contact, always hold the Miter Gauge
as shown in "BASIC SAW OPERATIONS - USING
THE MITER GAUGE,"
BEFORE LEAVING THE SAW
1_ Turn the saw off.
2. Wait for blade to stop spinning.
3. Make workshop child-proof. Lockthe shop Discon-
nect master switches. Remove the yetlow Switch
Key. Store it away from children and others not
qualified to use the too!.
4 Unplug the saw
glossary of terms for woodworking
Anti-Kickback Pawls (AKP)
Device which, when properly maintained, is designed to
stop the workpiece from being kicked back at the opera-
tor during ripping operation.
Arbor
The shaft on which a cutting tool is mounted,
Crosscut
A cuttingor shaping operation made across the width of
the workpiece.
Dado
A non through cut which produces a square sided notch
or trough in the workpiece.
Featherboard
A device which can help guide workpieces during rip
type operation.
Freehand
Performing a cut without using a Fence, Miter Gauge,
fixture, hold down or other proper device to keep the
workpiece from twisting during the cut.
Gum
A sticky, sap based residue from wood products.
Heel
Misalignment of the blade.
Kerr
The amount of material removed by the blade in a
through cut orthe slotproduced by the blade in a non
through or partialcut.
Kickback
An uncontrolled grabbing and throwing of the workpiece
back toward the front of the saw.
Leading End
The end of the workpiece which, during a rip type
operation, ispushed into the cutting tool first.
Molding
A non throughcut which produces a special shape in the
workpiece used for joining or decoration.
Push Stick
A device used to feed the workpiece through the saw
during narrow ripping type operations and helps keep
the operator's hands well away trom the blade.
Push Block
A device used for ripping type operations too narrow to
allow use of a Push Stick.
Rabbet
A notch in the edge of a workpiece.
Resin
A sticky, sap base substance that has hardened.
Ripping
A cutting operation along the length of the workpiece.
Revolutions Per Minute (RPM)
The number of turns completed by a spinning object in
one minute.
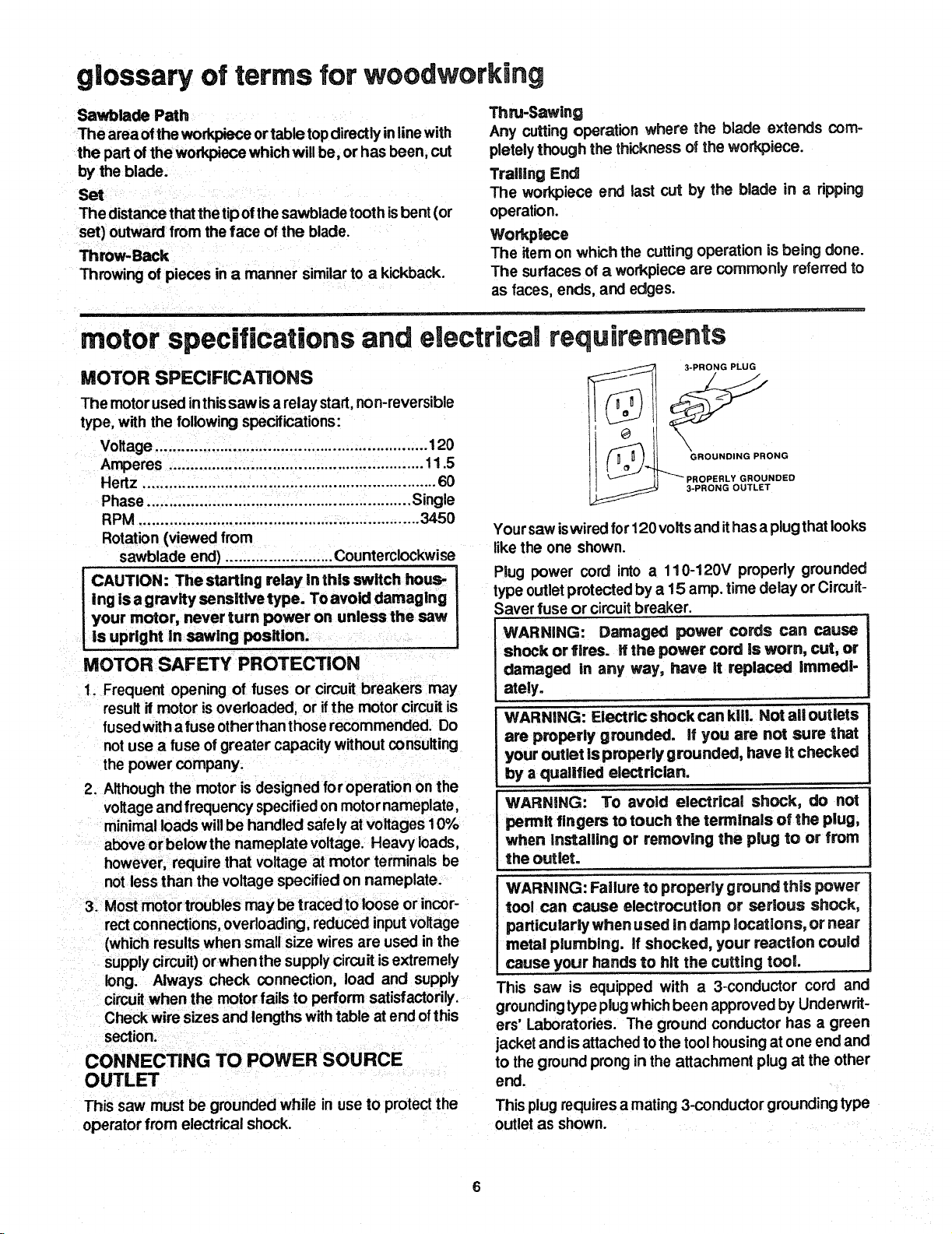
glossary of terms for woodworking
Sawblade Path
The area ofthe workpiece ortable topdirectly inline with
the part of the workpiece which will be, or has been, cut
by the blade.
Set
The distance thatthe tip ofthe sawblade toothisbent (or
set) outward from the face of the blade.
Throw-Back
Throwing of pieces in a manner similarto a kickback.
i
Thru-Sawing
Any cutting operation where the blade extends com-
pletelythough the thickness of the workpiece.
Trailing End
The workpiece end last cut by the blade in a ripping
operation.
Workplece
The item on which the cutting operation is being done.
The surfaces of a workpiece are commonly referred to
as faces, ends, and edges.
motor specifications and electrical requirements
MOTOR SPECiFICATiONS
The motorused inthissaw is arelay start,non-reversible
type, with the following specifications:
Voltage ............................................................... 120
Amperes ........................................................... 11.5
Hertz .................................................................... 60
Phase ................................................... Single
RPM ................................................................. 3450
Rotation (viewed from
sawblade end) ......................... Counterclockwise
CAUTION: The staring relay in this switch hous-
Ing is a gravity sensitive type. To avoid damaging
your motor, never turn power on unless the saw
is upright in sawing position,
MOTOR SAFETY PROTECTION
1. Frequent opening of fuses or circuit breakers may
result ifmotor is overloaded, or if the motor circuit is
fusedwith afuse other than those recommended. Do
notuse a fuse of greater capacity without consulting
the power company.
2. Although the motor is designed for operation on the
voltage and frequency specified on motor nameplate,
minimal loads will be handled safely at voltages 10%
aboveor below the nameplate voltage. Heavy loads,
however, require that voltage at motor terminals be
not less than the voltage specified on nameplate.
3- Most motor troubles may betraced to loose or incor-
rectconnections, overloading, reduced input voltage
(which results when small size wires are used inthe
supply circuit)orwhen the supply circuit isextremely
long. Always check connection, load and supply
circuitwhen the motor fails to perform satisfactorily.
Check wire sizes and lengths with table atend ofthis
section.
CONNECTING TO POWER SOURCE
OUTLET
This saw must be grounded while in use to protect the
operator from electrical shock.
Your saw iswired for 120 volts and ithas a plugthat looks
likethe one shown.
Plug power cord into a 110-120V properly grounded
type outlet protected by a 15 amp. time delay or Circuit-
Saver fuse or circuit breaker.
WARNING: Damaged power cords can cause
shock or fires, if the power cord is worn, cut, or
damaged in any way, have it replaced immedi-
ately.
WARNING: Electric shock can kill. Not all outlets
are properly grounded. If you are not sure that
your outlet is properly grounded, have itchecked
by a qualified electrician.
WARNING: To avoid electrical shock, do not J
permit fingers to touch the tenninals of the plug,
when InstalIlng or removing the plug to or from
the outlet.
WARNING: Failure to properly ground this power
tool can cause electrocution or serious shock,
particularly when used in damp locations, or near
metal plumbing, if shocked, your reaction could
cause your hands to hit the cutting tooL
This saw is equipped with a 3-conductor cord and
groundingtype plugwhichbeen approved by Underwrit-
ers' Laboratories. The ground conductor has a green
jacketand is attached to the tool housing at one endand
to theground prong in the attachment plug at the other
end.
This plug requires a mating 3-conductor grounding type
outlet as shown.
/t0)
\
¢-
3oPRONG PLUG
GROUNDING PRONG
PROPERLY GROUNDED
3-PRONG OUTLET
I
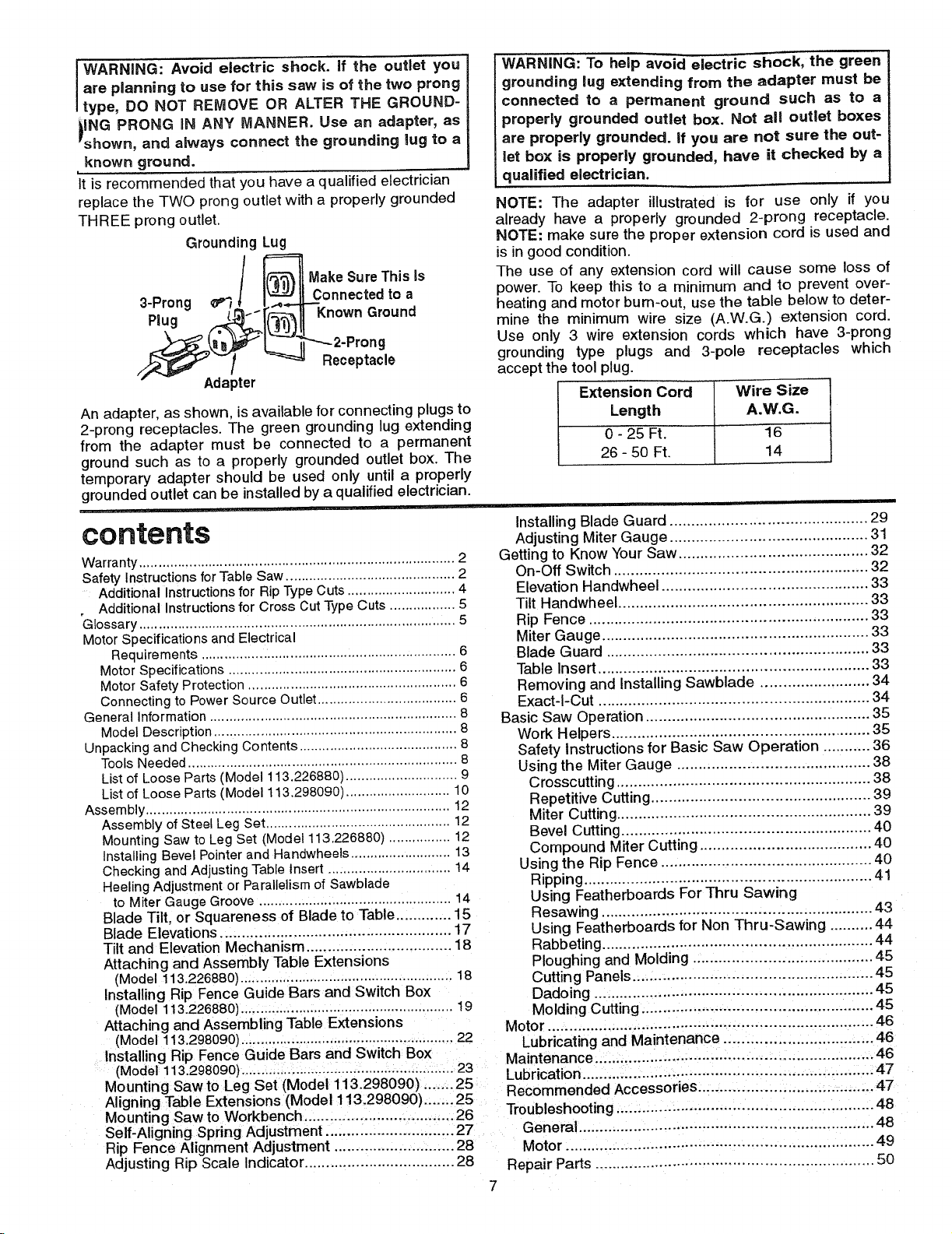
are planning to use for this saw is of the two prong
j WARNING: Avoid electric shock, if the outlet you
type, DO NOT REMOVE OR ALTER THE GROUND-
ING PRONG IN ANY MANNER. Use an adapter, as
shown, and always connect the grounding iug to a
known ground.
It is recommended that you have a qualified electrician
replace the TWO prong outlet with a properly grounded
THREE prong outlet.
Grounding Lug
/ _==_MakeSureThisis
3-Pron- _ _ I_11 Connectedto a
P,o ' ",o,,.,'
_--I -'=====_Receptacle
An adapter, as shown, is available for connecting plugs to
2-prong receptacles. The green grounding lug extending
from the adapter must be connected to a permanent
ground such as to a properly grounded outlet box. The
temporary adapter should be used only until a properly
grounded outlet can be installed by a qualified electrician.
......... I'll I'1
contents
Warranty .................................................................................. 2
Safety Instructions for Table Saw ............................................ 2
Additional Instructionsfor Rip Type Cuts ............................ 4
Additional Instructions for Cross Cut Type Cuts ................. 5
"Glossary .................................................................................. 5
Motor Specifications and Electrical
Requirements .................................................................. 6
Motor Specifications ........................................................... 6
Motor Safety Protection ...................................................... 6
Connecting to Power Source Outlet .................................... 6
General Information ................................................................ 8
Model Description ............................................................... 8
Unpacking and Checking Contents ......................................... 8
Tools Needed ...................................................................... 8
List of Loose Parts (Model 113.226880) ............................. 9
List of Loose Parts (Model 113.298090) ........................... 10
Assembly ............................................................................... 12
Assembly of Steel Leg Set ................................................ 12
Mounting Saw to Leg Set (Model 113.226880) ................ 12
Installing Bevel Pointer and Handwheels ......................... 13
Checking and Adjusting Table insert ............................... 14
Heeling Adjustment or Parallelism of Sawblade
to Miter Gauge Groove ................................................. 14
Blade Tilt, or Squareness of Blade to Table ............. 15
Blade Elevations ...................................................... 17
Tilt and Elevation Mechanism .................................. 18
Attaching and Assembly Table Extensions
(Model 113.226880) ....................................................... 18
Installing Rip Fence Guide Bars and Switch Box
(Model 113.2268801 ....................................................... 19
Attaching and Assembling Table Extensions
('Model 113.298090} ....................................................... 22
Installing Rip Fence Guide Bars and Switch Box
(Model 113.298090)...................................................... 23
Mounting Saw to Leg Set (Model 113.298090) ....... 25
Aligning Table Extensions (Model 113.298090) ....... 25
Mounting Saw to Workbench ................................... 26
Self-Aligning Spring Adjustment .............................. 27
Rip Fence Alignment Adjustment ............................ 28
Adjusting Rip Scale Indicator ................................... 28
Adapter
WARNING: To help avoid electric shock, the green
grounding lug extending from the adapter must be
connected to a permanent ground such as to a
properly grounded outlet box. Not all outlet boxes
are properly grounded, if you are not sure the out-
let box is properly grounded, have it checked by a
qualified electrician.
NOTE: The adapter illustrated is for use only if you
already have a properly grounded 2-prong receptacle.
NOTE: make sure the proper extension cord is used and
is in good condition.
The use of any extension cord will cause some loss of
power. To keep this to a minimum and to prevent over-
heating and motor burn-out, use the table below to deter-
mine the minimum wire size (A.W.G.) extension cord.
Use only 3 wire extension cords which have 3-prong
grounding type plugs and 3-pole receptacles which
accept the tool plug.
Extension Cord Wire Size
Length A.W.G.
0 - 25 Ft. 16
26 - 5O Ft. 14
ii
Installing Blade Guard ............................................. 29
Adjusting Miter Gauge ............................................. 31
Getting to Know Your Saw ........................................... 32
On-Off Switch .......................................................... 32
Elevation Handwheel ............................................... 33
Tilt Handwheel ......................................................... 33
Rip Fence ................................................................ 33
Miter Gauge ............................................................. 33
Blade Guard ............................................................ 33
Table Insert .............................................................. 33
Removing and Installing Sawblade ......................... 34
Exact-I-Cut .............................................................. 34
Basic Saw Operation ................................................... 35
Work Helpers ........................................................... 35
Safety Instructions for Basic Saw Operation ........... 36
Using the Miter Gauge ............................................ 38
Crosscutting .......................................................... 38
Repetitive Cutting .................................................. 39
Miter Cutting .......................................................... 39
Bevel Cutting ......................................................... 40
Compound Miter Cutting ....................................... 40
Using the Rip Fence ................................................ 40
Ripping .................................................................. 41
Using Featherboards For Thru Sawing
Resawing .............................................................. 43
Using Featherboards for Non Thru-Sawing .......... 44
Rabbeting .............................................................. 44
Ploughing and Molding ......................................... 45
Cutting Panels ....................................................... 45
Dadoing ................................................................ 45
Molding Cutting ..................................................... 45
Motor ........................................................................... 46
Lubricating and Maintenance .................................. 46
Maintenance ................................................................ 46
Lubrication ................................................................... 47
Recommended Accessories ........................................ 47
Troubleshooting ........................................................... 48
General .................................................................... 48
Motor ....................................................................... 49
Repair Parts ................................................................ 50
7
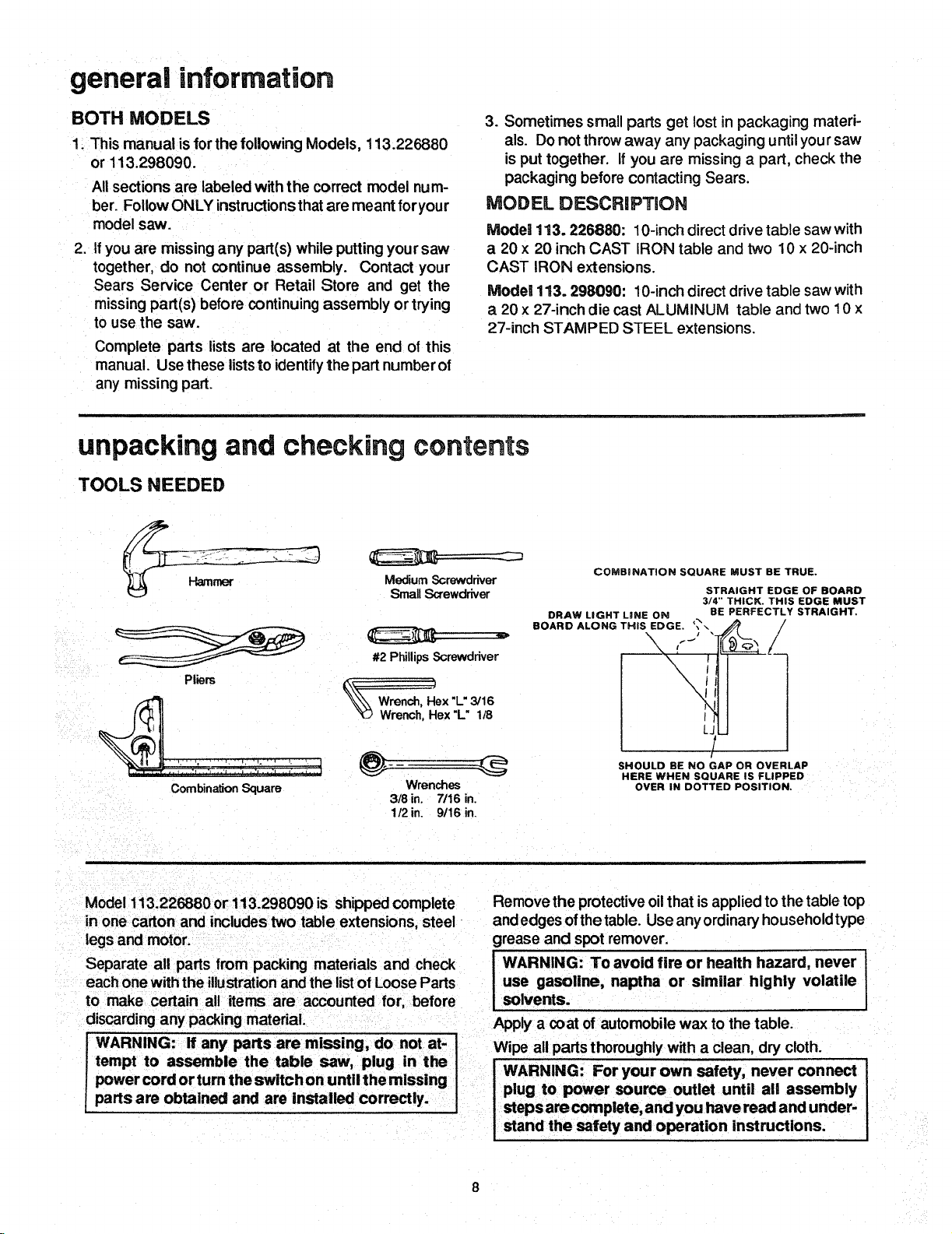
general information
BOTH MODELS
3. Sometimes small parts get lost in packaging materi-
1. This manual is for the following Models, 113.226880
or 113.298090.
All sections are labeled with the correct model num-
ber. Follow ONLY instructionsthat are meant foryour
model saw.
2. If you are missing any part(s) while putting your saw
together, do not continue assembly. Contact your
Sears Service Center or Retail Store and get the
missing part(s) before continuing assembly or trying
to use the saw.
MODEL DESCRIPTUON
Model 113. 226880:10-inch direct drive table saw with
a 20 x 20 inch CAST IRON table and two 10 x 20-inch
CAST IRON extensions.
Model 113. 298090: 10-inch direct drive table saw with
a 20 x 27-inch die cast ALUMINUM table and two 10 x
27-inch STAMPED STEEL extensions,
Complete parts lists are located at the end of this
manual. Use these liststo identify the part number of
any missing part.
unpacking and checking contents
TOOLS NEEDED
als. Do not throw away any packaging until your saw
is put together. If you are missing a part, check the
packaging before contacting Sears.
MediumScrewdriver
SmallScrewdriver
#2 Phillips Screwdriver
Pliers
_ Wrench, Hex "L" 3/16
"K_ Wrench, Hex'L" 1/8
Combination Square
Wrenches
3/8 in. 7/16 in.
1/2 in. 9/16 in.
Model 113.226880 or 113.298090 is shipped complete
in one carton and includes two table extensions, steel
legs and motor.
Separate all parts from packing materials and check
each one with the illustration and the list of Loose Parts
to make certain all items are accounted for, before
discarding any packing material.
WARNING: If any parts are missing, do not at-
tempt to assemble the table saw, plug in the
power cord or turn the switch on until the missing
parts are obtained and are installed correctly.
COMBINATION SQUARE MUST BE TRUE.
STRAIGHT EDGE OF BOARD
3/4" THICK. THIS EDGE MUST
DRAW LIGHT LINE ON
BOARD ALONG THIS EDGE. '3",
SHOULD BE NO GAP OR OVERLAP
HERE WHEN SQUARE IS FLIPPED
OVER IN DOTTED POSITION.
BE PERFECTLY STRAIGHT,
i •
I
L_
I
Remove the protective oil that is applied to the table top
and edgesofthetable. Use anyordinary household type
grease and spot remover.
use gasoline, naptha or similar highly volatile
WARNING: To avoid fire or health hazard, never I
solvents.
Apply a coat of automobile wax to the table.
Wipe all parts thoroughly with a clean, dry cloth.
WARNING: For your own safety, never connect
plug to power source outlet until all assembly
steps are complete, and you have read and under-
stand the safety and operation instructions.
I
8
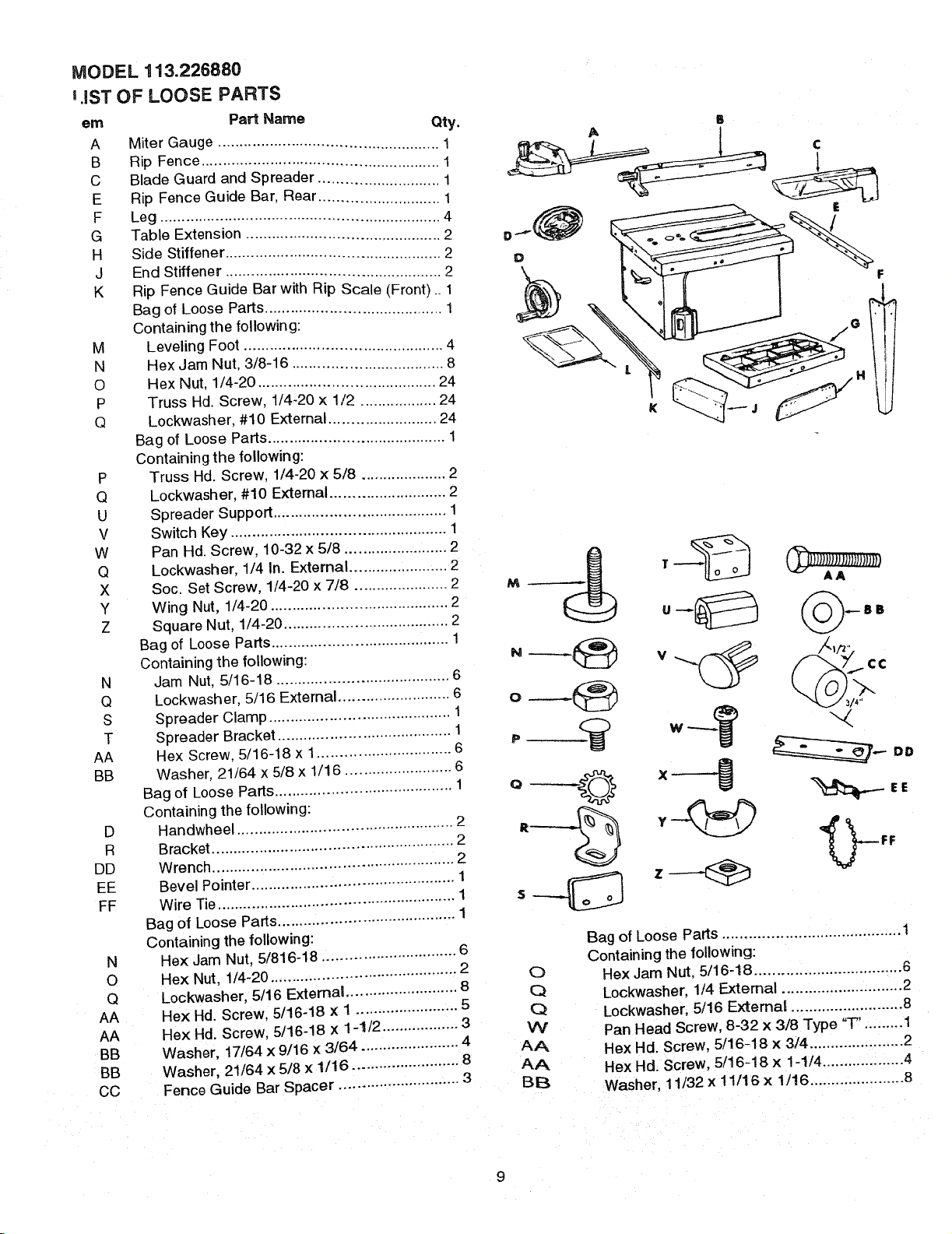
MODEL 113.226880
I.IST OF LOOSE PARTS
em Part Name Qty.
A Miter Gauge ................................................... 1
B Rip Fence ....................................................... 1
C Blade Guard and Spreader ............................ 1
E Rip Fence Guide Bar, Rear ............................ 1
F Leg ................................................................. 4
G Table Extension ............................................. 2
H Side Stiffener .................................................. 2
J End Stiffener .................................................. 2
K Rip Fence Guide Bar with Rip Scale (Front) .. 1
Bag of Loose Parts......................................... !
Containing the following:
M Leveling Foot .............................................. 4
N Hex Jam Nut, 3/8-16 ................................... 8
O Hex Nut, 1/4-20 ......................................... 24
P Truss Hd. Screw, 1/4-20 x 1/2 .................. 24
Q Lockwasher, #10 External ......................... 24
Bag of Loose Parts ......................................... 1
Containing the following:
P Truss Hd. Screw, 1/4-20 x 5/8 .................... 2
Q Lockwasher, #10 External ........................... 2
U Spreader Support ........................................ 1
V Switch Key .................................................. 1
W Pan Hd. Screw, 10-32 x 5/8 ........................ 2
Q Lockwasher, 1/4 In. External ....................... 2
X Soc. Set Screw, 1/4-20 x 7/8 ...................... 2
Y Wing Nut, 1/4-20 ......................................... 2
Z Square Nut, 1/4-20 ...................................... 2
Bag of Loose Parts ......................................... 1
Containing the following:
N Jam Nut, 5/16-18 ........................................ 6
Q Lockwasher, 5/16 External .......................... 6
S Spreader Clamp .......................................... 1
T Spreader Bracket ........................................ 1
AA Hex Screw, 5/16-18 x 1............................... 6
BB Washer, 21/64 x 5/8 x 1/16 ......................... 6
Bag of Loose Parts ......................................... 1
Containing the following:
D Handwheel .................................................. 2
R Bracket ........................................................ 2
DD Wrench ........................................................ 2
EE Bevel Pointer ............................................... 1
FF Wire Tie....................................................... 1
Bag of Loose Parts ......................................... 1
Containing the following:
N Hex Jam Nut, 5/816-18 ............................... 6
O
Q
AA
AA
BB
BB
CC
Hex Nut, 1/4-20 ...........................................
Lockwasher, 5/16 External .......................... 8
Hex Hd. Screw, 5/16-18 x 1 ........................ 5
Hex Hd. Screw, 5/16-18 x 1-1/2 .................. 3
Washer, 17/64 x 9/16 x 3/64 ....................... 4
Washer, 21/64 x 5/8 x 1/16 ......................... 8
Fence Guide Bar Spacer ............................ 3
D
F
1
_SB
o
.,<
_-,-- DD
o
Bag of Loose Parts ......................................... 1
2
0
Q
Q
W
AA
AA
BB
Containing the following:
Hex Jam Nut. 5/16-18 ................................. 6
Lockwasher, 1/4 External ............................ 2
Lockwasher, 5/16 Extemat .......................... 8
Pan Head Screw, 8-32 x 3/8 Type "T". ........ 1
Hex Hal. Screw, 5/16-18 x 3/4 ...................... 2
Hex Hd. Screw, 5/16-18 x 1-1/4 ................... 4
Washer, 11/32 x 11/16 x 1/!6 ...................... 8
9
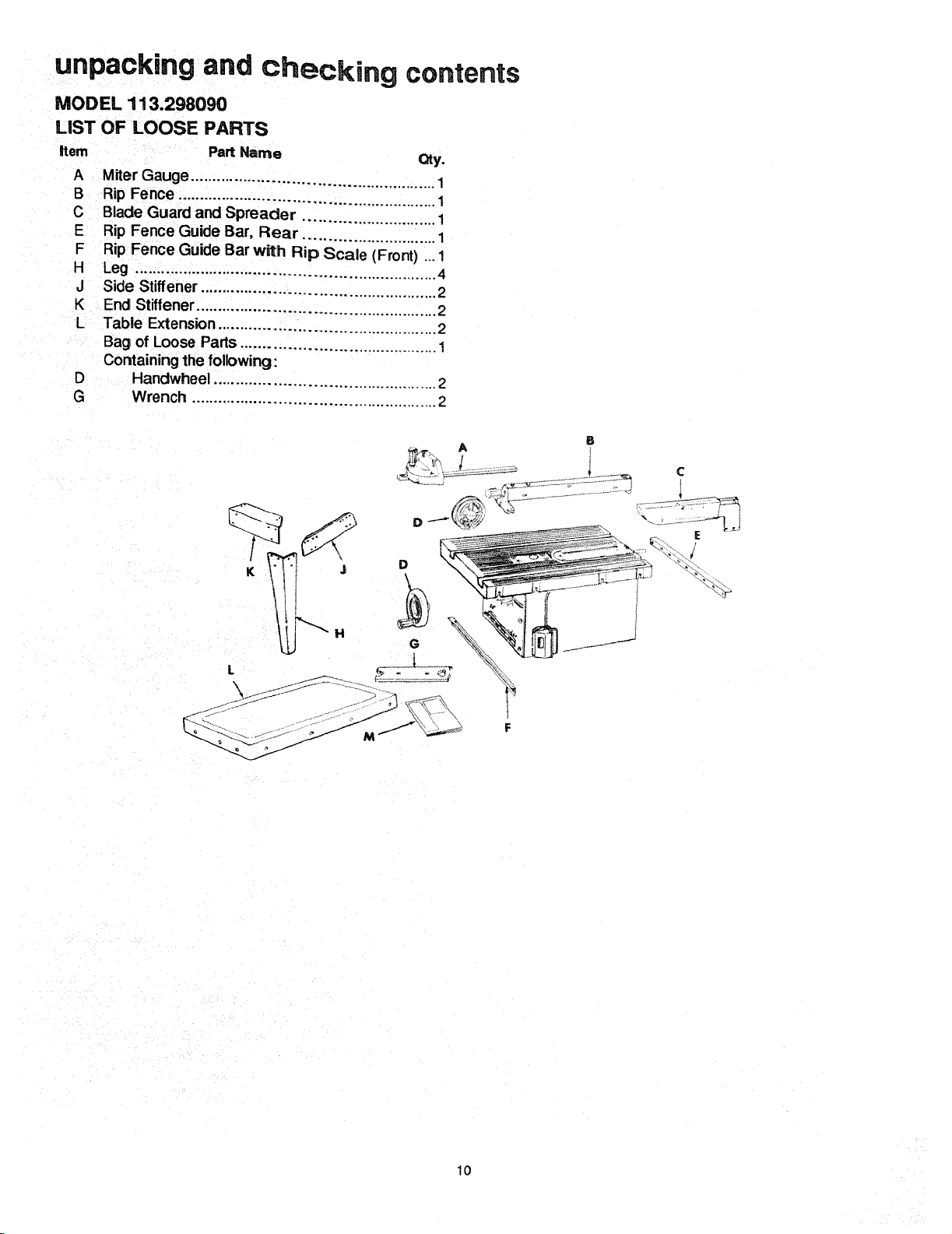
unpacking and checking contents
MODEL 113.298090
LIST OF LOOSE PARTS
item Part Name Qty.
A Miter Gauge ..................................................... 1
B Rip Fence ........................................................ 1
C Blade Guard and Spreader ............................. 1
E Rip Fence Guide Bar, Rear ............................. 1
F Rip Fence Guide Bar with Rip Scale (Front) ... 1
H Leg .................................................................. 4
J Side Stiffener ................................................... 2
K End Stiffener .................................................... 2
L Table Extension ............................................... 2
Bag of Loose Parts .......................................... 1
Containing the following:
D Handwheel ................................................ 2
G Wrench ..................................................... 2
B
L
lO

Bag of Loose Parts ............................................ 1
Containing the following:
N Spreader Support ............................................ 1
O Spreader Clamp .............................................. 1
P Spreader Bracket ............................................ 1
Bag of Loose Parts ............................................ 1
Containing the following:
Q Switch Key ...................................................... 1
U Soc. Hd. Setscrew 1/4-20x7/8 ......................... 2
T Square Nut, 1/4-20 .......................... 2
X Lockwasher, #10 External Type ...................... 2
X Lockwasher, 1/4 External Type ....................... 2
Y Wing Nut, 1/4-20 ............................................. 2
AA Pan Hd. Screw, 10-32x5/8 .............................. 2
BB Truss Head Screw, 1/4-20x5/8 ........................ 2
Bag of Loose Parts ............................................ 1
Containing the following:
R Flat Washer 17/64x9/16x3!64 ......................... 4
R Flat Washer 21/64x5/8x1/16 ........................... 4
V Guide Bar Spacer ............................................ 3
W Hex Nut, 1/4-20 ............................................... 2
W Hex Jam Nut, 5/16-18 ................................... 10
X Lockwasher, 1/4 in. External Type .................. 2
X Lockwasher, 5/16 in. External Type .............. 10
Z Hex Hd. Screw, 5/16-18xl .............................. 3
Z Hex Hd. Screw, 5/16-18x1-1/2 ........................ 3
Z Hex Hd. Screw, 5/16-18x1-1/4 ........................ 4
Bag of Loose Parts ............................................ 1
Containing the following:
W Hex Nut, 1/4-20 ............................................. 24
W Hex Jam Nut, 3/8-16 ....................................... 8
X Lockwasher, 1/4 Extemal Type .................... 24
BB Truss Head Screw, 1/4-20xl/2 ..................... 24
CC Leveling Foot .................................................. 4
Bag of Loose Parts ............................................ 2
Containing the following:
R Flat Washer 17/64x3/4x1/16 ........................... 4
R Flat Washer 11/32xl 1/16xl/16 ....................... 8
R Flat Washer 21/64x5/8x1/16 ........................... 8
W Hex Nut, 1/4-20 ............................................. 16
W Hex Jam Nut, 5/16-18 ..................................... 8
X Lockwasher, 1/4 Extemal Type .................... 16
X Lockwasher, 5/16 External Type .................... 8
Z Hex Head Screw, 5/16-18x1-1/4 ..................... 8
BB Truss Head Screw, 1/4-20xl ........................ 16
Bag of Loose Parts ............................................ 1
Containing the following:
DD Comer Stiffener Bracket ................................. 4
EE Comer Support Bracket .................................. 4
Bag of Loose Parts ............................................ 1
Containing the following:
W Hex Jam Nut, 5/16-18 ....... :............................. 2
X Lockwasher, External 5/16 ............................. 4
Z Hex Hd. Screw. 5/16-18x3/4 ........................... 2
AA Pan Cross Screw, Ty "-F', 8-32x3/8 ................ 1
FF Tie Wire .......................................................... 1
GG Bracket ............................................................ 2
HH Bevel Pointer .................................................. 1
11
DD
EE
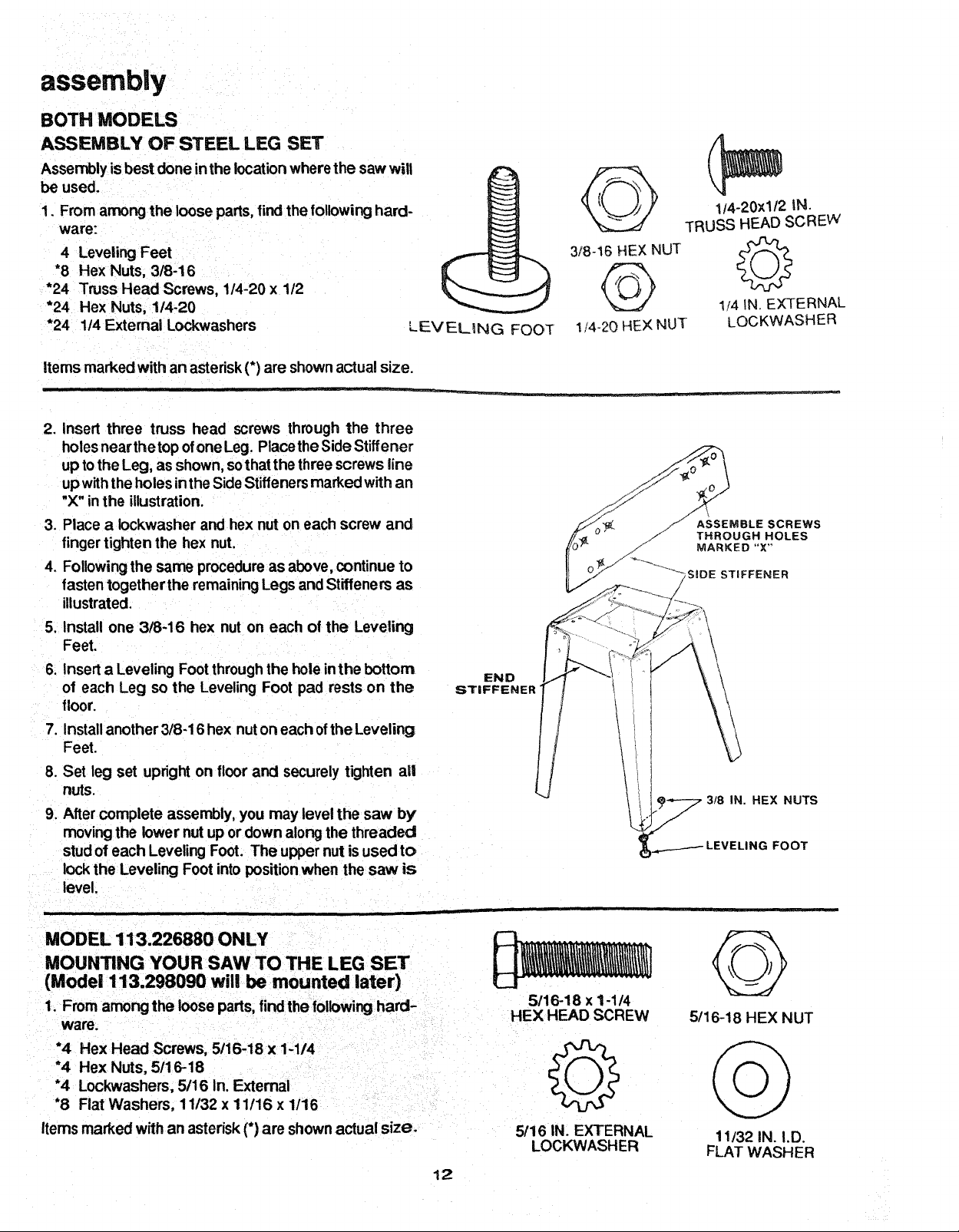
assembly
BOTH MODELS
ASSEMBLY OF STEEL LEG SET
Assembly isbest done in the location where the saw will
be used.
1. From among the loose parts,find the following hard-
ware:
4 Leveling Feet
*8 Hex Nuts, 3/8-16
*24 Truss Head Screws, 1/4-20 x 1/2
*24 Hex Nuts, 1/4-20
*24 1/4 Externa| Lockwashers
items marked with an asterisk (*) are shown actual size.
R_v
2. Insert three truss head screws through the three
holesnear the top ofone Leg. Placethe Side Stiffener
upto the Leg, as shown, sothat the three screws line
upwiththe holes inthe SideStiffeners marked with an
"X" inthe illustration.
3. Place a Iockwasher and hex nut on each screw and
finger tighten the hex nut.
4. Following the same procedure as above, continue to
fasten together the remaining Legs andStiffeners as
illustrated.
5. Install one 3/8-16 hex nut on each of the Leveling
Feet.
6. Insert a Leveling Footthroughthe hole inthe bottom
of each Leg so the Leveling Foot pad rests on the
floor.
7. Install another 3/8-16 hex nut on each ofthe Leveling
Feet.
8. Set leg set upright on floor and securely tighten all
nuts.
9. After complete assembly, you may level the saw by
moving the lower nut up or down along the threaded
stud of each Leveling Foot. The upper nut is used to
lock the Leveling Foot into positionwhen the saw is
level.
, , IL i
LEVELING FOOT
END
STIFFENER
3/8-16 HEY,NUT
@
114-20 HEX NUT
114-20X1/2 IN.
TRUSS HEAD SCREW
1/4 IN. EXTERNAL
LOCKWASHER
3/8 IN. HEX NUTS
LEVELING FOOT
MODEL 113.226880 ONLY
MOUNTING YOUR SAW TO THE LEG SET
(Model 113.298090 will be mounted later)
1. From among the loose parts, findthe following hard-
ware.
*4 Hex Head Screws, 5/16-18 x 1-1/4
*4 Hex Nuts, 5/16-18
*4 Lockwashers, 5/16 In. External
*8 Fiat Washers, 11/32 x 11/16 x 1/16
Items marked with an asterisk (*) are shownactual size.
12
5116-18 x 1-1/4
HEX HEAD SCREW
5/16 IN. EXTERNAL
LOCKWASHER
5/16-18 HEX NUT
11132 IN. I.D.
FLAT WASHER
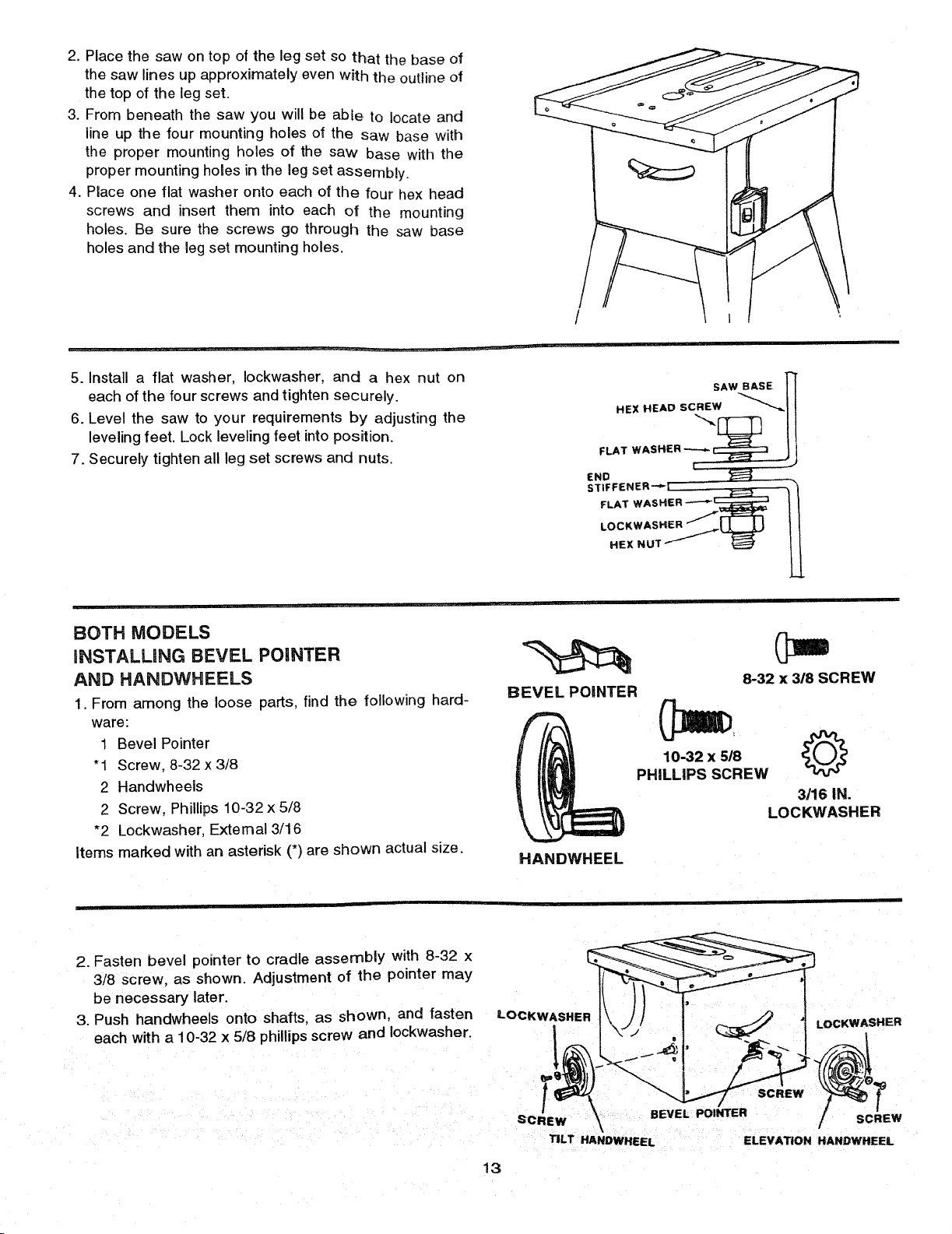
2.Placethesawontopofthelegsetsothatthebaseof
thesawlinesupapproximatelyevenwiththeoutlineof
thetopofthelegset.
3.Frombeneaththesawyouwillbeabteto locateand
lineupthe fourmountingholesofthesawbasewith
thepropermountingholesofthesaw basewiththe
propermountingholesintheleg set assembly.
4. Place one flat washer onto each of the four hex head
screws and insert them into each of the mounting
holes. Be sure the screws go through the saw base
holes and the leg set mounting holes.
5. Install a flat washer, Iockwasher, and a hex nut on
each of the four screws and tighten securely.
6. Level the saw to your requirements by adjusting the
leveling feet. Lock leveling feet into position.
7. Securely tighten all leg set screws and nuts.
BOTH MODELS
INSTALLING BEVEL POINTER
AND HANDWHEELS
1. From among the loose parts, find the following hard-
ware:
1 Bevel Pointer
*1 Screw, 8-32 x 3/8
2 Handwheels
2 Screw, Phillips 10-32 x 5/8
*2 Lockwasher, External 3/16
Items marked with an asterisk (*) are shown actual size.
HEX HEAD SCREW ""_._|
FLAT WAS HER --""_c_ 1
END
LOCKWAS"E"17 L
BEVEL POINTER
HANDWHEEL
SAW BASE [
8-32 x 3/8 SCREW
10-32 x 5/8
PHILLIPS SCREW
©
3/16 IN.
LO CKWASHER
2. Fasten bevel pointer to cradle assembly with 8-32 x
3/8 screw, as shown. Adjustment of the pointer may
be necessary later.
3. Push handwheels onto shafts, as shown, and fasten
each with a 10-32 x 5/8 phillips screw and Iockwasher.
LOCKWiSHE i ER
TILT HANDWHEEL ELEVATION HANDWHEEL
!3
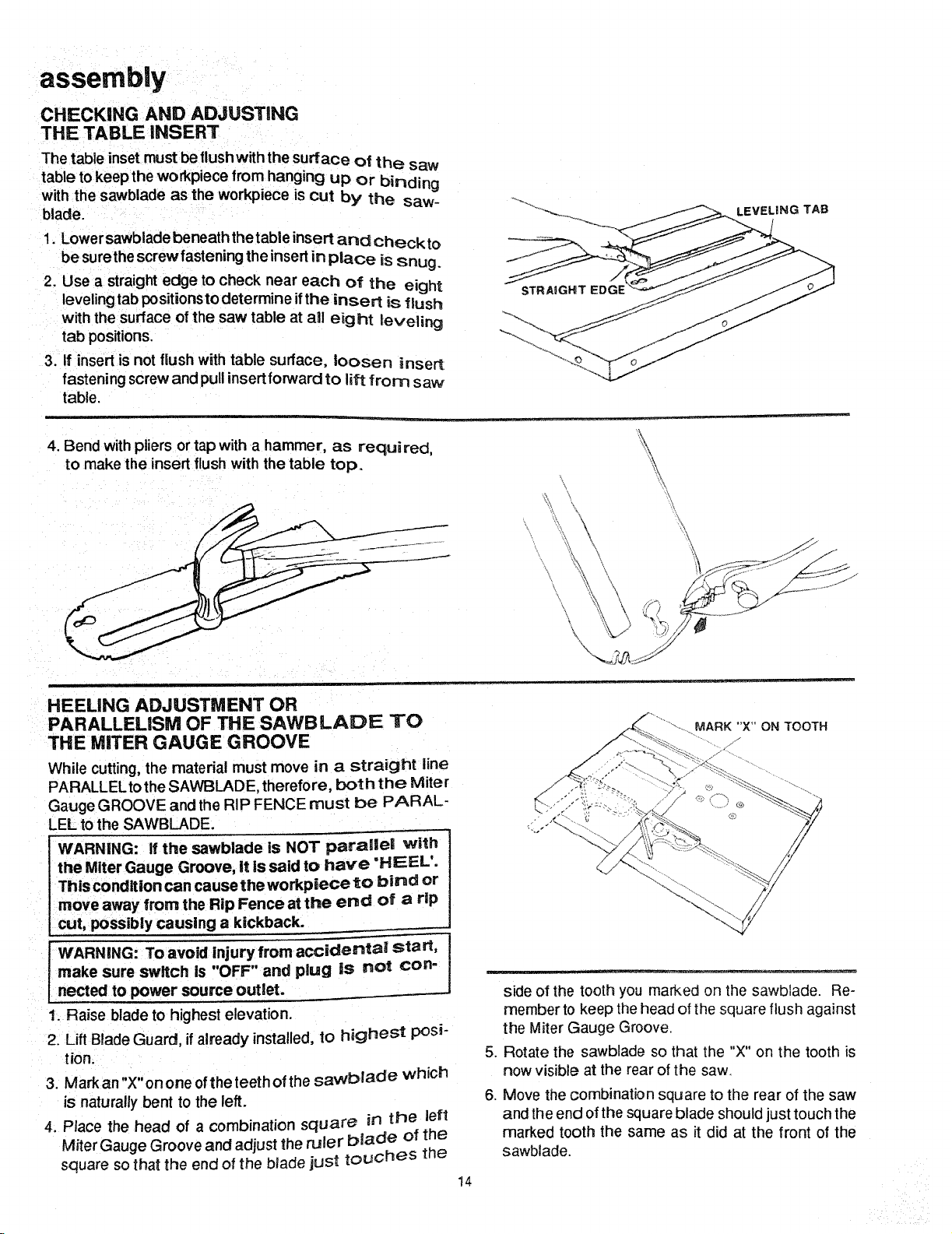
assembly
CHECKING AND ADJUSTING
THE TABLE INSERT
The table inset must be llushwith the surface of the saw
table to keep the workpiece from hanging up or binding
with the sawblade as the workpiece is cut by the saw-
blade.
1. Lower sawblade beneath the table insert and checkto
be surethe screw fastening the insert in Place is snug.
2. Use a straight edge to check near each of the eight
leveling tab positionsto determine if the insert is flush
with the surface of the saw table at all eight leveling
tab positions.
3. If insert is not flush with table surface, loosen inser_
fastening screw and pull insert forward to lift from saw
table.
4. Bend with pliers or tap with a hammer, as required,
to make the insert flush with the table top.
r
HEELING ADJUSTMENT OR
PARALLELISM OF THE SAWBLAOE TO
THE MITER GAUGE GROOVE
While cutting, the material must move in a straight line
PARALLELto the SAWBLADE, therefore, both the Miter
Gauge GROOVE and the RIP FENCE must be PARAL-
LEL to the SAWBLADE.
WARNING: if the sawblade is NOT parallel with
the Miter Gauge Groove, it is said to have "HEEL'.
This condition can cause the workpiece to bind or
move away from the Rip Fence at the end of a rip
cut, possibly causing a kickback.
make sure switch is "OFF" and plug is not con-
I WARNING: To avoid injury from accide ntai stall,
nected to power source outlet.
1. Raise blade to highest elevation.
2. Lift Blade Guard, if already installed, to highest posi-
tion.
3. Mark an "X" on one ofthe teeth of the sawbiade which
is naturally bent to the left.
4. Place the head of a combination square in the left
Miter Gauge Groove and adjust the ruler blade of the
square so that the end of the blade just touches the
side of the tooth you marked on the sawblade. Re-
member to keep the head of the square flush against
the Miter Gauge Groove.
5. Rotate the sawblade so that the "X" on the tooth is
now visible at the rear of the saw.
6. Move the combination square to the rear of the saw
and the end of the square blade should just touch the
marked tooth the same as it did at the front of the
sawblade.
14
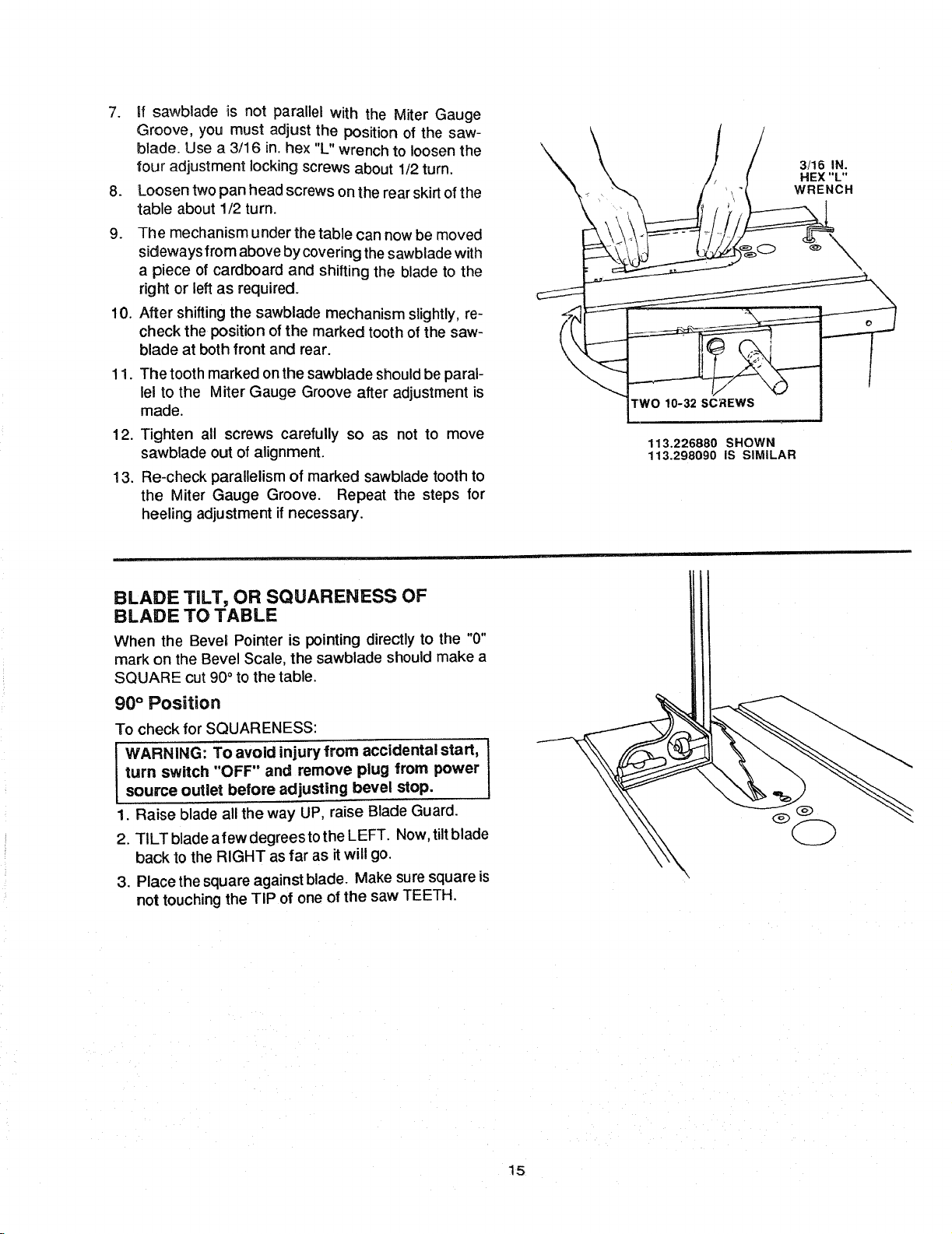
.
If sawblade is not parallel with the Miter Gauge
Groove, you must adjust the position of the saw-
blade. Use a 3/16 in. hex "L" wrench to loosen the
four adjustment locking screws about 1/2 turn.
.
Loosen two pan head screws on the rear skirt of the
table about 1/2 turn.
9_
The mechanism under the table can now be moved
sideways from above by covering the sawblade with
a piece of cardboard and shifting the blade to the
right or left as required.
10. After shifting the sawblade mechanism slightly, re-
check the position of the marked tooth of the saw-
blade at both front and rear.
11. The tooth marked on the sawblade should be paral-
lel to the Miter Gauge Groove after adjustment is
made.
12. Tighten all screws carefully so as not to move
sawblade out of alignment.
13. Re-check parallelism of marked sawblade tooth to
the Miter Gauge Groove. Repeat the steps for
heeling adjustment if necessary.
3/16 IN.
HEX "L"
WRENCH
°°\
113.226880 SHOWN
113.298090 IS SIMILAR
BLADE TILT, OR SQUARENESS OF
BLADE TO TABLE
When the Bevel Pointer is pointing directly to the "0"
mark on the Bevel Scale, the sawblade should make a
SQUARE cut 90° to the table.
90 ° Position
To check for SQUAR ENESS:
turn switch "OFF" and remove plug from power
I WARNING: To avoid injury from accidental start, I
source outlet before adjusting bevel stop.
1. Raise blade all the way UP, raise Blade Guard.
2. TILT blade a few degrees to the LEFT. Now, tiltblade
back to the RIGHT as far as it will go.
3. Place the square against blade. Make sure square is
not touching the TIP of one of the saw TEETH.
15

assembly
4. If blade is SQUARE to table; check pointer.
A. IfPointer DOES NOTpoint to"0" markon the Bevel
Scale, bend pointer to read "0".
5. If blade is NOT SQUARE to table, the 900 Limit Stop
mustbe adjusted.
]CAUTION: Cover blade with p,ece of card- i
board to protect your hand.
A. Usinga small size screwdriver, reach underneath
saw and loosen BOTH setscrews in 90° Stop
Collar.
NOTE: Ifyou can't reach the setscrews turn the
Tilt Handwheel slightly.
B. Rotate the Stop Collar moving itaway from pivot
nut.
C. Tilt blade RIGHT or LEFT, checking with your
square until blade is square to table.
D. Rotate Stop Collar toward Pivot Nut until it
TOUCH ES the Pivot Nut. Tightenthe setscrews.
E. Check Pointer, if it DOES NOT point to the "0"
mark onthe bevel scale, bend Pointer to read "0".
POINTER
ADJUSTING SCREW
r
o / Q
_/CP_FTgN_N
"O" POSITION\ _F_ / k .,
s il _.l'I/l"111'*_J_',lll'_llI"_\
,o 2# 2s 30 3_ 40 _
10"
Direct Drive .......... _ HP
G[ _..NGER I
............-F
BLADE COVERED
WITH P!ECE OF
CARDBOARD
/
1
/
/
\,h
SETSCREWS (2)
6. Tilt blade to LEFT as far as itwill go. Itwill stop when
the Pivot Nut is against the 45° Stop Collar.
7. Place an ACCURATE square against blade. Make
sure square is nottouching the TIP of one of the saw
teeth.
PIVOT NUT
90° STOP COLLAR
16
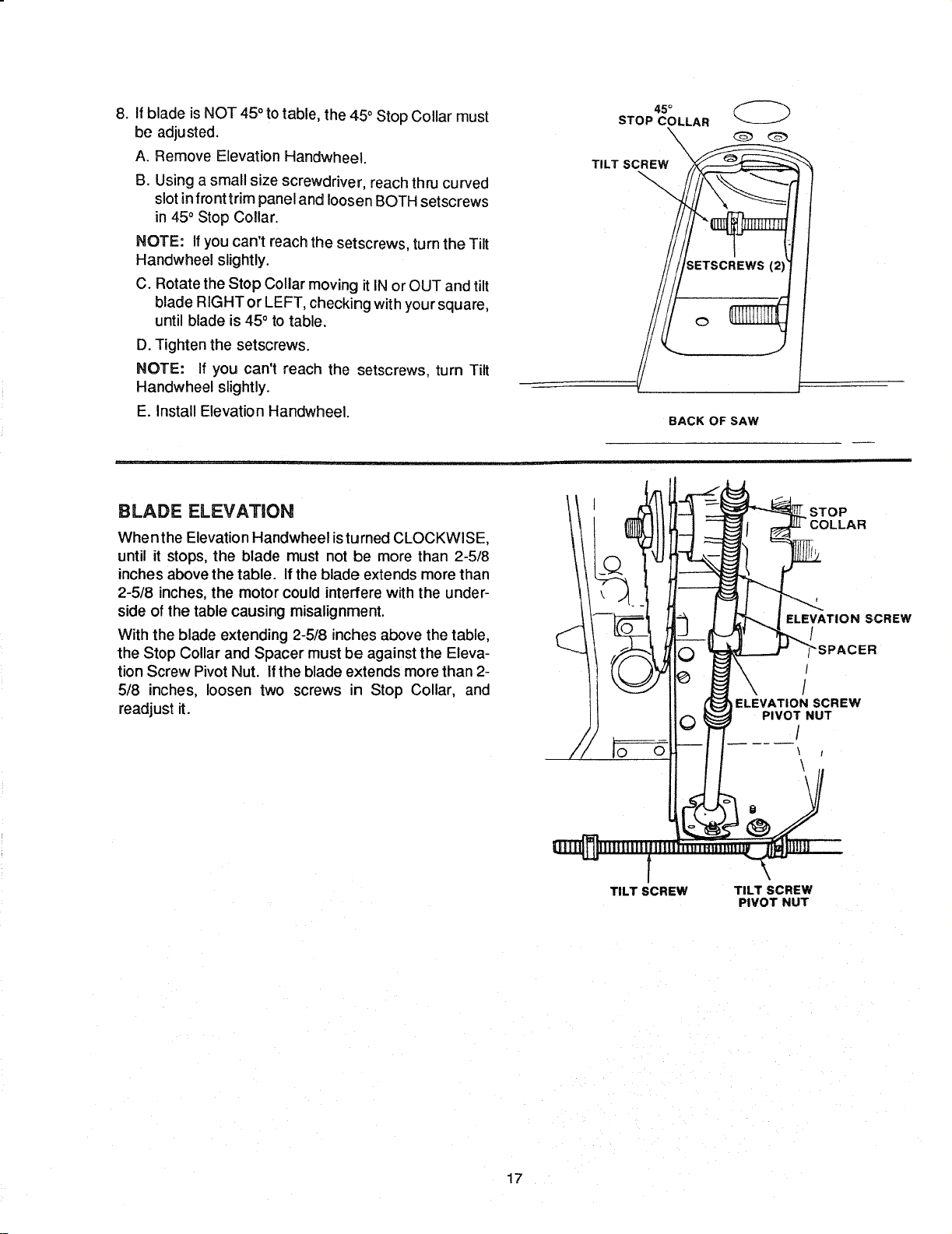
8. If blade isNOT 45 ° to table, the 45 ° Stop Collar must
be adjusted.
A. Remove Elevation HandwheeL
B. Using a small size screwdriver, reach thru curved
slot infront trim panel and loosen BOTH setscrews
in 45° Stop Collar.
NOTE: If you can't reach the setscrews, turn the Tilt
Handwheel slightly.
C. Rotate the Stop Collar moving it IN or OUT and tilt
blade RIGHT or LEFT, checking with your square,
until blade is 45° to table.
D. Tighten the setscrews.
NOTE: If you can't reach the setscrews, turn Tilt
Handwheel slightly.
E. Install Elevation Handwheel.
45°
STOP COLLAR
TILT SCREW
BACK OF SAW
BLADE ELEVATION
Whenthe Elevation Handwheel isturned CLOCKWISE,
until it stops, the blade must not be more than 2-5/8
inches above the table. If the blade extends more than
2-5/8 inches, the motor could interfere with the under-
side of the table causing misalignment.
With the blade extending 2-5/8 inches above the table,
the Stop Collar and Spacer must be against the Eleva-
tion Screw Pivot Nut. Ifthe blade extends more than 2-
5/8 inches, loosen two screws in Stop Collar, and
readjust it.
TILT SCREW
;TOP
_LLAR
ELEVATION SCREW
/
;PACER
/
/
ELEVATION SCREW
PIVOT NUT
TILT SCREW
PIVOT NUT
17
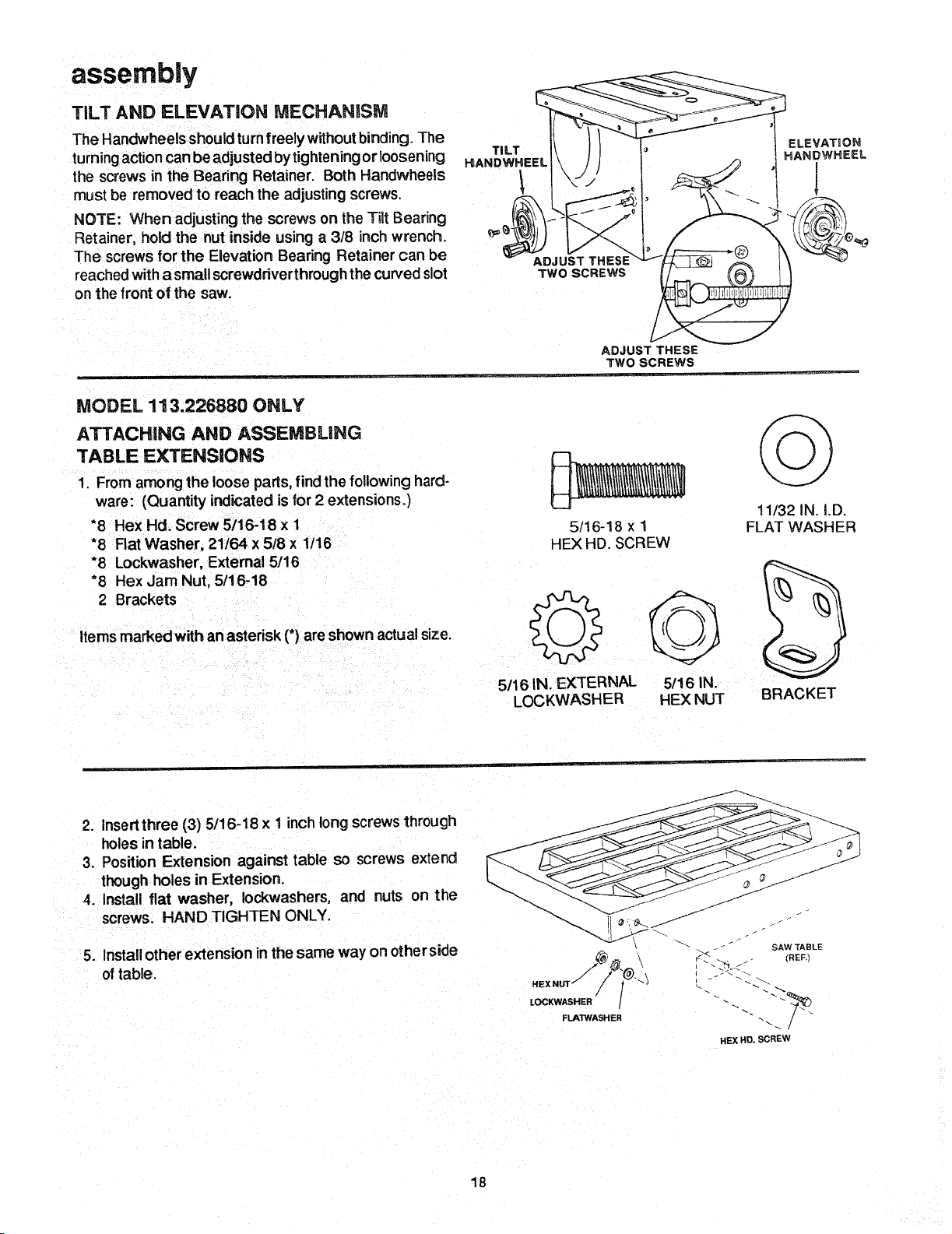
assembly
TiLT AND ELEVATION MECHANISM
The Handwheels should turnfreely withoutbinding. The
turningactioncanbe adjusted bytighteningor loosening
the screws in the Bearing Retainer. Both Handwheels
must be removed to reach the adjusting screws.
NOTE: When adjusting the screws on the Tilt Bearing
Retainer, hold the nut inside using a 3/8 inch wrench.
The screwsfor the Elevation Bearing Retainer can be
reachedwith a small screwdriver through the curved slot
on the front of the saw.
MODEL 113.226880 ONLY
ATTACHING AND ASSEMBLING
TABLE EXTENSIONS
1. From among the loose parts,find the following hard-
ware: (Quantity indicated is for 2 extensions.)
*8 Hex Hal. Screw 5/16-18 x 1
*8 Flat Washer, 21/64 x 5/8 x 1/16
*8 Lockwasher, External 5/16
*8 Hex Jam Nut, 5/16-18
2 Brackets
TILT
HANDWi_EEL
_ELEVATaON
ADJUST THESE
TWO SCREWS
ADJUST THESE
TWO SCREWS
5/16-18 x 1
HEX HD. SCREW
11/32 IN. I.D.
FLAT WASH ER
Items rnarkedwith an asterisk (*) are shown actual size.
2. Insert three (3) 5/16-18 x 1 inchlong screws through
holes in table.
3. Position Extension against table so screws extend
though holes in Extension.
4. Install flat washer, Iockwashers, and nuts on the
screws. HAND TIGHTEN ONLY.
5. Installother extension in the same way on other side
oftable.
5/16 IN. EXTERNAL 5tl 6 IN.
LOCKWASHER HEX NUT BRACKET
\
LOCKWASHER
FLATWASHER
18