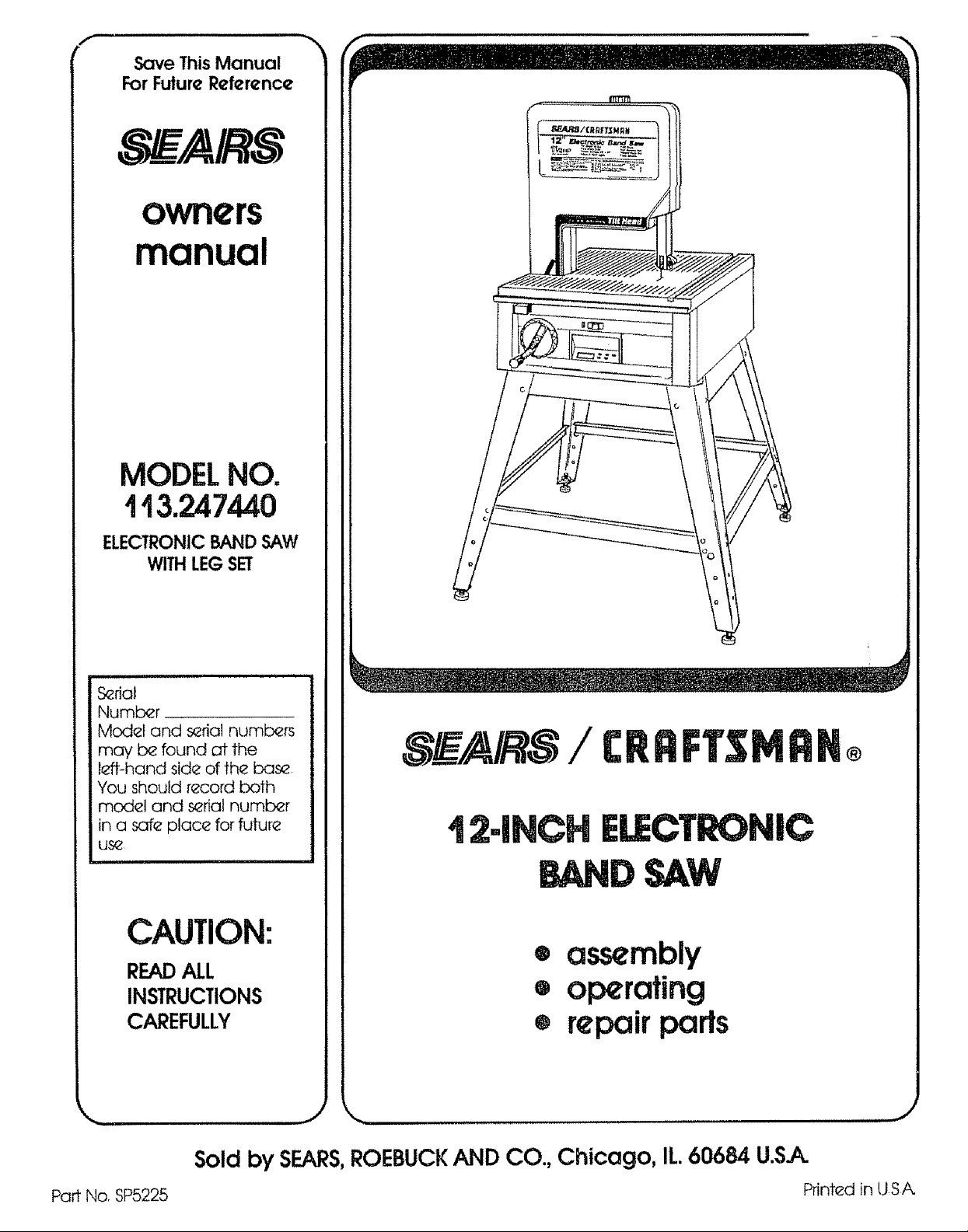
Save This Manual
For Future Reference
owners
manual
MODEL NO.
113.247440
ELECTRONIC BAND SAW
WITH LEG SET
S_dal
Number
Model and s_rial numbers
may b_ found at the
left-hand side of the bas_.
You should record both
model and s_rial number
in a safe place for future
US¢
CAUTION:
READ ALL
INSTRUCTIONS
CAREFULLY
8EAIRS / CRRFTSMRN®
!2-|NCH ELECTRONIC
BAND SAW
® assembly
® operating
o repair parts
k_
Part No SP5225
j k,.. j
Sold by SEARS,ROEBUCKAND CO., Chicago, IL.60684 U.S.A.
Printed in USA.
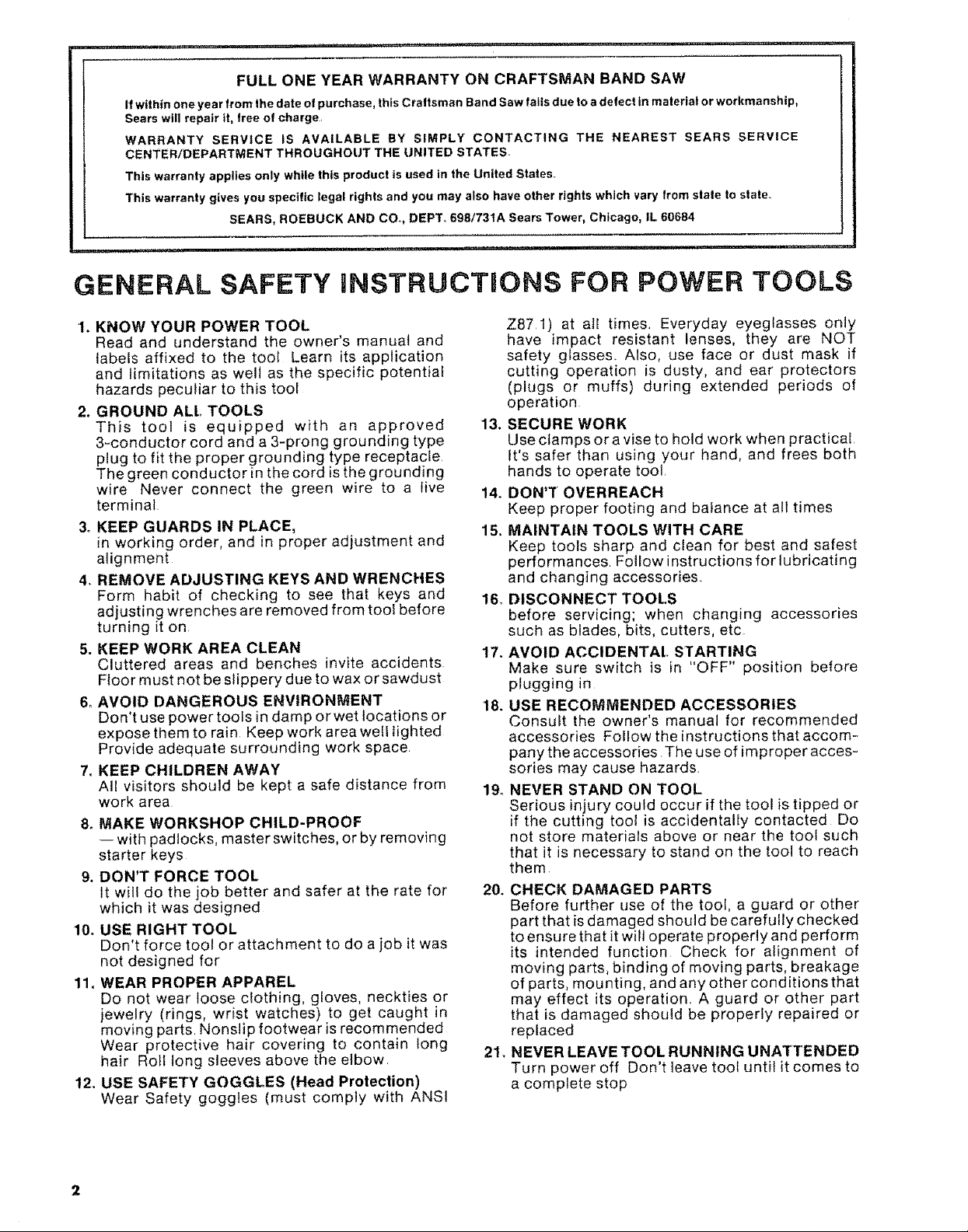
FULL ONE YEAR WARRANTY ON CRAFTSMAN BAND SAW
If within one year from the date of purchase, this Craftsman Band Saw fails due to a defect in material or workmanship,
Sears will repair ft, free of charge.
WARRANTY SERVtCE IS AVAILABLE BY SIMPLY CONTACTING THE NEAREST SEARS SERVICE
CENTER/DEPARTMENT THROUGHOUT THE UNITED STATES.
This warranty applies only while this product is used in the United States.
This warranty gives you specific legal rights and you may also have other rights which vary from stale to state.
SEARS, ROEBUCK AND CO., DEPT_ 698/731A Sears Tower, Chicago, IL 60684
GENERAL SAFETY INSTRUCTnONS FOR POWER TOOLS
'1.KNOW YOUR POWER TOOL
Read and understand the owner's manual and
labels affixed to the tool Learn its application
and limitations as well as the specific potential
hazards peculiar to this tool
2. GROUND ALL, TOOLS
This tool is equipped with an approved
3-conductor cord and a 3-prong grounding type
plug to fit the proper grounding type receptacle
The green conductor in the cord is the grounding
wire Never connect the green wire to a live
terminal
3. KEEP GUARDS IN PLACE,
in working order, and in proper adjustment and
alignment
4_ REMOVE ADJUSTING KEYS AND WRENCHES
Form habit of checking to see that keys and
adjusting wrenches are removed from tool before
turning it on
5. KEEP WORK AREA CLEAN
Cluttered areas and benches invite accidents
Floor must not be slippery due to wax or sawdust
6. AVOID DANGEROUS ENVIRONMENT
Don't use power tools in damp or wet locations or
expose them to rain Keep work area well lighted
Provide adequate surrounding work space,
7. KEEP CHILDREN AWAY
All visitors should be kept a safe distance from
work area
8oMAKE WORKSHOP CHILD-PROOF
-- with padlocks, master switches, or by removing
starter keys
9. DON'T FORCE TOOL
tt will do the job better and safer at the rate for
which it was designed
10. USE RIGHT TOOL
Don't force tool or attachment to do a job it was
not designed for
11. WEAR PROPER APPAREL
Do not wear loose clothing, gloves, neckties or
jewelry (rings, wrist watches) to get caught in
moving parts, Nonslip footwear is recommended
Wear protective hair covering to contain tong
hair Roll tong sleeves above the elbow
12, USE SAFETY GOGGLES (Head Protection)
Wear Safety goggles (must comply with ANSI
Z871) at all times, Everyday eyeglasses only
have impact resistant lenses, they are NOT
safety glasses, Also, use face or dust mask if
cutting operation is dusty, and ear protectors
(plugs or muffs) during extended periods of
operation
13. SECURE WORK
Use clamps or a vise to hold work when practical
It's safer than using your hand, and frees both
hands to operate tool
14. DON'T OVERREACH
Keep proper footing and balance at all times
15. MAINTAIN TOOLS WITH CARE
Keep tools sharp and clean for best and safest
performances Follow instructions for lubricating
and changing accessories
16, DISCONNECT TOOLS
before servicing; when changing accessories
such as blades, bits, cutters, etc
17. AVOID ACCIDENTAL STARTING
Make sure switch is in "OFF" position before
plugging in
18. USE RECOMMENDED ACCESSORIES
Consult the owner's manual for recommended
accessories Follow the instructions that accom-
pany the accessories The use of improper acces-
sories may cause hazards
19. NEVER STAND ON TOOL
Serious injury could occur if the tool is tipped or
if the cutting tool is accidentalfy contacted Do
not store materials above or near the toot such
that it is necessary to stand on the tool to reach
them,
20. CHECK DAMAGED PARTS
Before further use of the tool, a guard or other
part that is damaged should be carefully checked
to ensure that it will operate properly and perform
its intended function Check for alignment of
moving parts, binding of moving parts, breakage
of parts, mounting, and any other conditions that
may effect its operation, A guard or other part
that is damaged should be properly repaired or
replaced
21, NEVER LEAVE TOOL RUNNING UNATTENDED
Turn power off Don't leave tool until it comes to
a complete stop
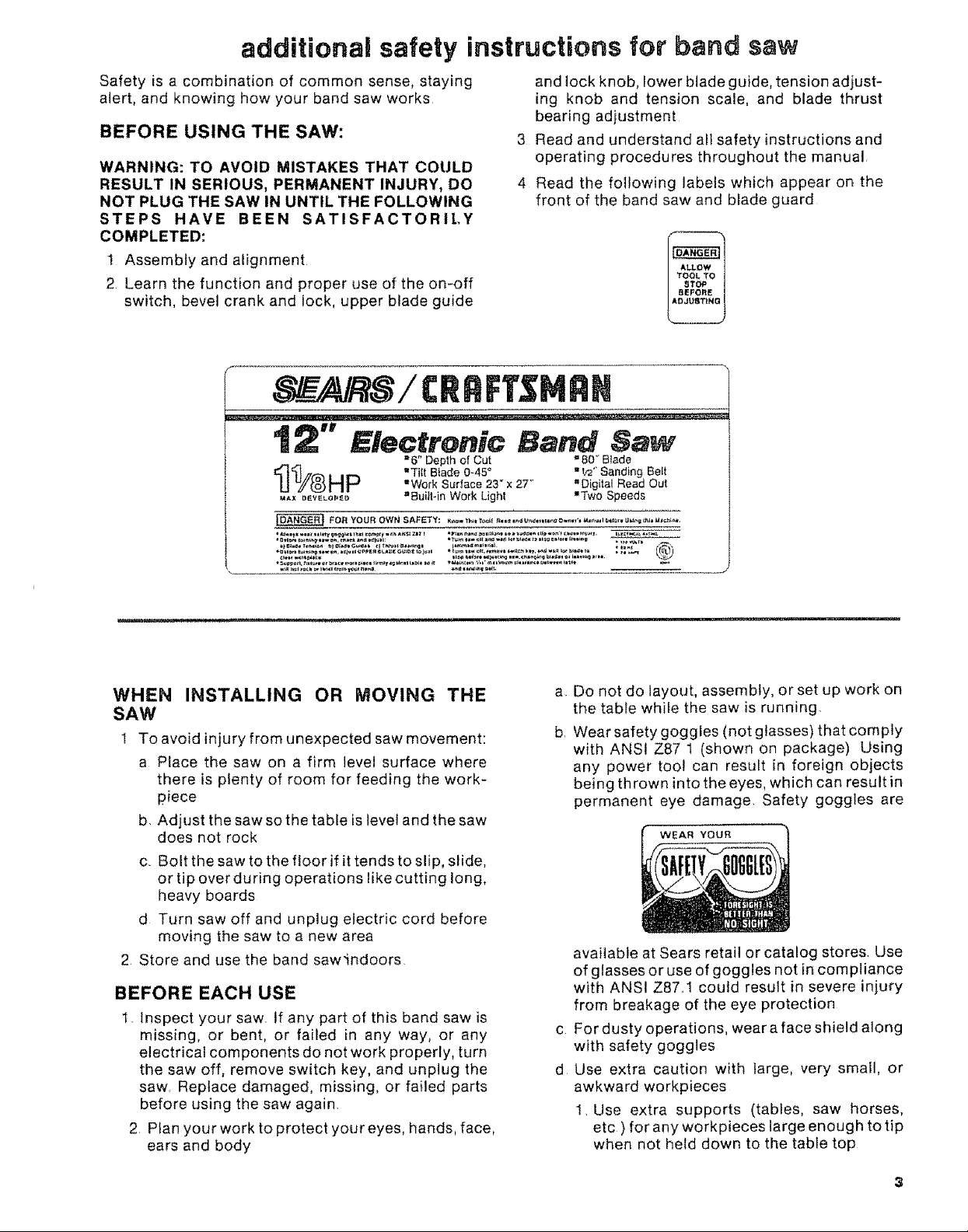
additional safety instructions for band saw
Safety is a combination of common sense, staying
alert, and knowing how your band saw works
BEFORE USING THE SAW:
WARNING: TO AVOID MISTAKES THAT COULD
RESULT IN SERIOUS, PERMANENT INJURY, DO
NOT PLUG THE SAW IN UNTIL THE FOLLOWING
STEPS HAVE BEEN SATISFACTORILY
COMPLETED:
1 Assembly and alignment
2, Learn the function and proper use of the on-off
switch, bevel crank and lock, upper blade guide
Electronic Band Saw
"6" Depth of Cut _'80n B_ade
.*.x D_v_.o._r_ =Built-in Work Light _Two Speeds
HP .T,,,,,adeo-,,,° S od,ngBe,,
=Work Surface 23"x 2T" '=Digital Read Out
and lock knob, lower blade guide, tension adjust-
ing knob and tension scale, and blade thrust
bearing adjustment
3 Read and understand aHsafety instructions and
operating procedures throughout the manual,
4 Read the following labels which appear on the
front of the band saw and blade guard
WHEN INSTALLING OR MOVING THE
SAW
To avoid injury from unexpected saw movement:
a Place the saw on a firm level surface where
there is plenty of room for feeding the work-
piece
b. Adjust the saw so the table is level and the saw
does not rock
c. Bolt the saw to the floor if it tends to slip, slide,
ortip over during operations like cutting long,
heavy boards
d Turn saw off and unplug electric cord before
moving the saw to a new area
2. Store and use the band sawindoors
BEFORE EACH USE
I. Inspect your saw. If any part of this band saw is
missing, or bent, or failed in any way, or any
electrical components do not work properly, turn
the saw off, remove switch key, and unplug the
saw Replace damaged, missing, or failed parts
before using the saw again.
2 Plan yourwork to protect youreyes, hands, face,
ears and body
a Do not do layout, assembly, or set up work on
the tame while the saw is running,
b, Wear safety goggles (not glasses) that comply
with ANSI Z87 1 (shown on package) Using
any power tool can result in foreign objects
being thrown into the eyes, which can result in
permanent eye damage Safety goggles are
WEAR YOUR
available at Sears retail or catalog stores, Use
of glasses or use of goggles not in compliance
with ANSI Z87A could result in severe injury
from breakage of the eye protection
C.
For dusty operations, weara face shield along
with safety goggles
d
Use extra caution with large, very small, or
awkward workpieces
1 Use extra supports (tables, saw horses,
etc ) for any workpieces large enough to tip
when not held down to the table top
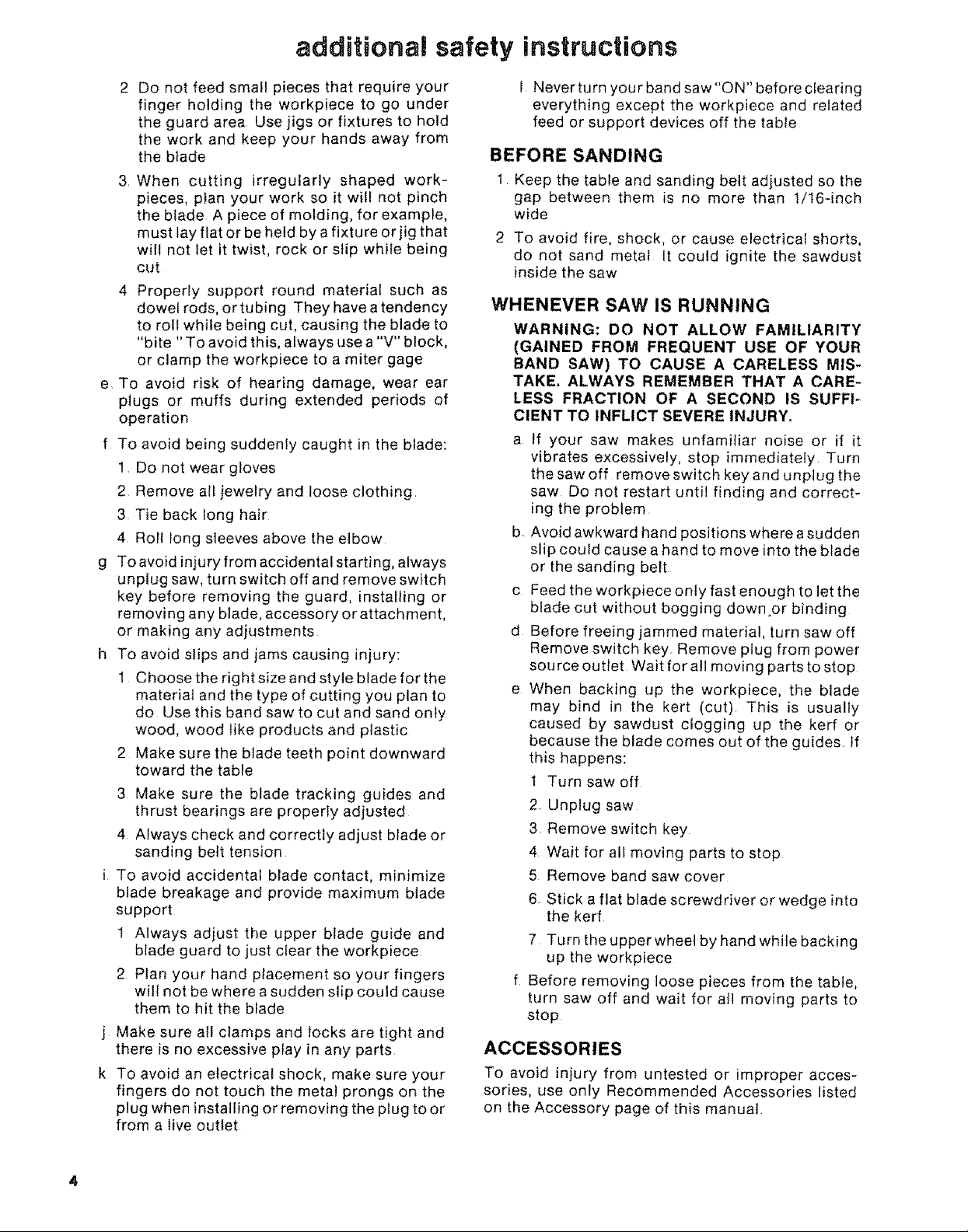
addffional safety instructions
2
Do not feed small pieces that require your
finger holding the workpiece to go under
the guard area Use jigs or fixtures to hold
the work and keep your hands away from
the blade
When cutting irregularly shaped work-
pieces, plan your work so it will not pinch
the blade A piece of molding, for example,
must lay flat or be held by a fixture or jig that
wil! not let it twist, rock or slip while being
cut
4 Properly support round material such as
dowel rods, or tubing They have a tendency
to roll while being cut, causing the blade to
"bite "To avoid this, always use a"V" block,
or clamp the workpiece to a miter gage
e
To avoid risk of hearing damage, wear ear
plugs or muffs during extended periods of
operation
f To avoid being suddenly caught in the blade:
1, Do not wear gloves
2 Remove all jewelry and loose clothing,
3 Tie back long hair
4 Roll tong sleeves above the elbow
g To avoid injury from accidental starting, always
unplug saw, turn switch off and remove switch
key before removing the guard, installing or
removing any blade, accessory or attachment,
or making any adjustments
h To avoid slips and jams causing injury:
1 Choose the right size and style blade for the
material and the type of cutting you plan to
do Use this band saw to cut and sand only
wood, wood like products and plastic
2 Make sure the blade teeth point downward
toward the table
3 Make sure the blade tracking guides and
thrust bearings are properly adjusted
4 Always check and correctly adjust blade or
sanding belt tension
i To avoid accidental blade contact, minimize
blade breakage and provide maximum blade
support
1 Always adjust the upper blade guide and
blade guard to just clear the workpiece
2 Plan your hand placement so your fingers
will not be where a sudden slip could cause
them to hit the blade
j Make sure all clamps and locks are tight and
there is no excessive play in any parts
k To avoid an electrical shock, make sure your
fingers do not touch the metal prongs on the
plug when installing or removing the plug to or
from a live outlet
I Never turn your band saw "ON" before clearing
everything except the workpiece and related
feed or support devices off the table
BEFORE SANDING
1 Keep the table and sanding belt adjusted so the
gap between them is no more than 1/16-inch
wide
2 To avoid fire, shock, or cause electrical shorts,
do not sand metal It could ignite the sawdust
inside the saw
WHENEVER SAW IS RUNNING
WARNING: DO NOT ALLOW FAMILIARITY
(GAINED FROM FREQUENT USE OF YOUR
BAND SAW) TO CAUSE A CARELESS MIS-
TAKE, ALWAYS REMEMBER THAT A CARE-
LESS FRACTION OF A SECOND IS SUFFIo
CIENT TO INFLICT SEVERE INJURY.
a tf your saw makes unfamiliar noise or if it
vibrates excessively, stop immediately Turn
the saw off remove switch key and unptug the
saw Do not restart until finding and correct-
ing the problem
b, Avoid awkward hand positions where a sudden
slip could cause a hand to move into the blade
or the sanding belt
c Feed the workpiece only fast enough to let the
blade cut without bogging down or binding
d Before freeing jammed material, turn saw off
Remove switch key, Remove plug from power
source outlet Wait for all moving parts to stop
e When backing up the workpiece, the blade
may bind in the kert (cut) This is usually
caused by sawdust clogging up the kerf or
because the blade comes out of the guides= If
this happens:
1 Turn saw off
2. Unplug saw
3 Remove switch key
4 Wait for all moving parts to stop
5 Remove band saw cover
6 Stick a flat blade screwdriver or wedge into
the kerf
7 Turn the upper wheel by hand while backing
up the workpiece
Before removing loose pieces from the table,
turn saw off and wait for atl moving parts to
stop
ACCESSORIES
To avoid injury from untested or improper acces-
sories, use only Recommended Accessories listed
on the Accessory page of this manual.
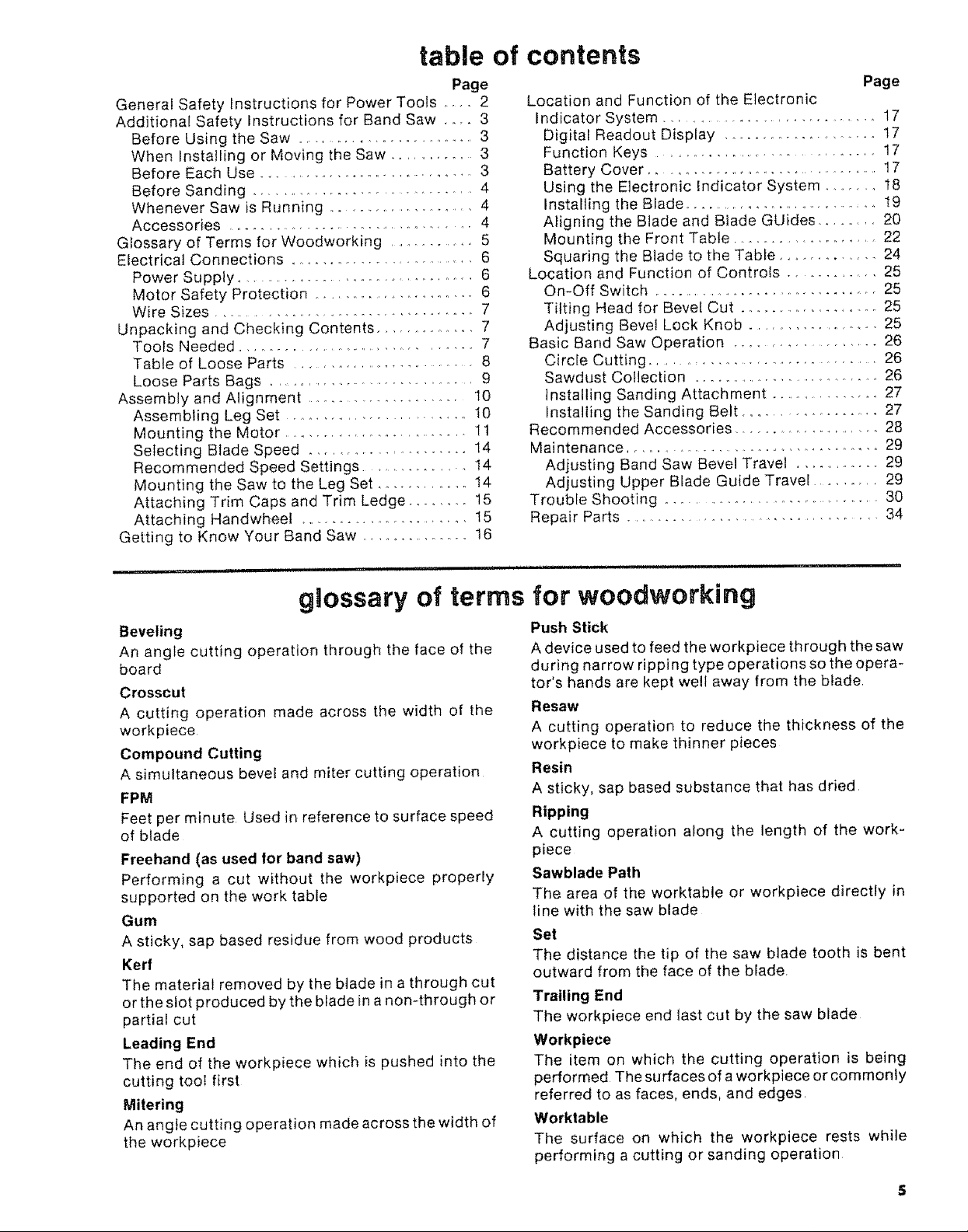
table of contents
Page
General Safety tnstructions for Power Tools .... 2
Additional Safety Instructions for Band Saw ..... 3
Before Using the Saw ............................ 3
When Installing or Moving the Saw ............. 3
Before Each Use .................................. 3
Before Sanding .......................... 4
Whenever Saw is Running ...................... 4
Accessories .................................. 4
Glossary of Terms for Woodworking ........... 5
Electrical Connections ............................ 6
Power Supply .............................. 6
Motor Safety Protection ........................... 6
Wire Sizes ................................... 7
Unpacking and Checking Contents ............. 7
Tools Needed ................................. 7
Table of Loose Parts .......................... 8
Loose Parts Bags ............................ 9
Assembly and Alignment ....................... 10
Assembling Leg Set ........................ 10
Mounting the Motor ........................... 11
Selecting Blade Speed ..................... 14
Recommended Speed Settings ................ t4
Mounting the Saw to the Leg Set .............. 14
Attaching Trim Caps and Trim Ledge ........ 15
Attaching Handwheel ...................... 15
Getting to Know Your Band Saw ............... 16
Page
Location and Function of the Electronic
Indicator System ............................... 17
Digital Readout Display ................... t7
Function Keys ............................... 17
Battery Cover ................................... 17
Using the Electronic indicator System ...... 18
Installing the Blade .............................. I9
Aligning the Blade and Biade GUides ........ 20
Mounting the Front Table ................ 22
Squaring the Blade to the Table ................ 24
Location and Function of Controls ........... 25
On-Off Switch .................................. 25
Tilting Head for Bevel Cut ................... 25
Adjusting Bevel Lock Knob ................ 25
Basic Band Saw Operation .................... 26
Circle Cutting ........................................ 26
Sawdust Collection ............................ 26
Installing Sanding Attachment ................ 27
Installing the Sanding Belt ................... 27
Recommended Accessories ....................... 28
Maintenance ....................................... 29
Adjusting Band Saw Bevel Travel ........... 29
Adjusting Upper Blade Guide Travel ......... 29
Trouble Shooting ............................. 30
Repair Parts ..................................... 34
glossary of terms
Beveling
An angle cutting operation through the face of the
board
Crosscut
A cutting operation made across the width of the
workpiece
Compound Cutting
A simultaneous bevel and miter cutting operation
FPM
Feet per minute Used in reference to surface speed
of blade
Freehand (as used for band saw)
Performing a cut without the workpiece properly
supported on the work table
Gum
A sticky, sap based residue from wood products
Kerf
The material removed by the blade in a through cut
or the slot produced by the blade in a non-through or
partial cut
Leading End
The end of the workpiece which is pushed into the
cutting tool first
Mitering
An angle cutting operation made across the width of
the workpiece
for woodworking
Push Stick
A device used to feed the workpiece through the saw
during narrow ripping type operations so the opera-
tor's hands are kept well away from the blade
Resaw
A cutting operation to reduce the thickness of the
workpiece to make thinner pieces
Resin
A sticky, sap based substance that has dried
Ripping
A cutting operation along the length of the work-
piece
Sawblade Path
The area of the worktable or workpiece directly in
line with the saw blade
Set
The distance the tip of the saw blade tooth is bent
outward from the face of the blade
Trailing End
The workpiece end tast cut by the saw blade
Workpiece
The item on which the cutting operation is being
performed The surfaces of a workpiece or commonly
referred to as faces, ends, and edges,
Worktable
The surface on which the workpiece rests while
performing a cutting or sanding operation
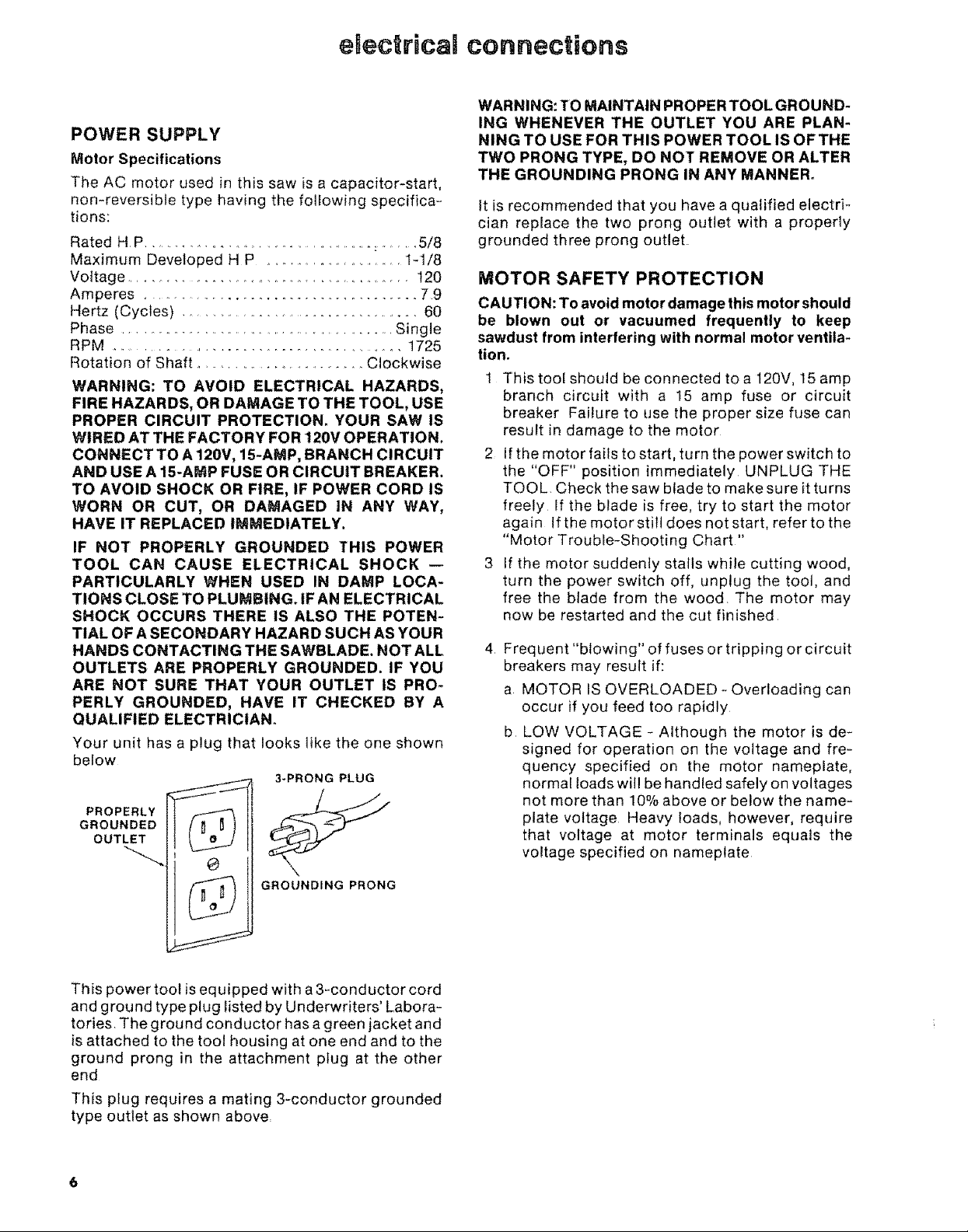
electrical connections
POWER SUPPLY
Motor Specifications
The AC motor used in this saw is a capacitor-start,
non-reversible type having the following specifica-
tions:
Rated H P..................................... _...... 5/8
Maximum Developed H P ................... t-1/8
Voltage ......................................... 120
Amperes ..................................... 7 9
Hertz (Cycles) ................................ 60
Phase ........................................... Single
RPM ....................................... 1725
Rotation of Shaft ........................ Clockwise
WARNING: TO AVOID ELECTRICAL HAZARDS,
FIRE HAZARDS, OR DAMAGE TO THE TOOL, USE
PROPER CIRCUIT PROTECTION. YOUR SAW IS
WIRED AT THE FACTORY FOR 120V OPERATION.
CONNECT TO A 120V, 15-AMP, BRANCH CIRCUIT
AND USE A 15-AMP FUSE OR CIRCUIT BREAKER.
TO AVOID SHOCK OR FIRE, IF POWER CORD tS
WORN OR CUT, OR DAMAGED IN ANY WAY,
HAVE IT REPLACED IMMEDIATELY.
IF NOT PROPERLY GROUNDED THIS POWER
TOOL CAN CAUSE ELECTRICAL SHOCK
PARTICULARLY WHEN USED IN DAMP LOCA-
TIONS CLOSE TO PLUMBING. IF AN ELECTRICAL
SHOCK OCCURS THERE IS ALSO THE POTEN-
TIAL OF A SECONDARY HAZARD SUCH AS YOUR
HANDS CONTACTING THE SAWBLADE. NOT ALL
OUTLETS ARE PROPERLY GROUNDED. IF YOU
ARE NOT SURE THAT YOUR OUTLET IS PRO-
PERLY GROUNDED, HAVE IT CHECKED BY A
QUALIFIED ELECTRICIAN.
Your unit has a plug that looks like the one shown
below
3-PRONG PLUG
GROUNDED
OUTLET
PROPERLY _
WARNING: TO MAINTAIN PROPER TOOL GROUND-
ING WHENEVER THE OUTLET YOU ARE PLAN-
NING TO USE FOR THIS POWER TOOL IS OFTHE
TWO PRONG TYPE, DO NOT REMOVE OR ALTER
THE GROUNDING PRONG IN ANY MANNER=
It is recommended that you have a qualified electri--
clan replace the two prong outlet with a properly
grounded three prong outlet.
MOTOR SAFETY PROTECTION
CAUTION: To avoid motor damage this motor should
be blown out or vacuumed frequently to keep
sawdust from interfering with normal motor ventila-
tion.
1 This tool should be connected to a 120V, t5 amp
branch circuit with a 15 amp fuse or circuit
breaker Failure to use the proper size fuse can
result in damage to the motor
2 If the motor fails to start, turn the power switch to
the "OFF" position immediately UNPLUG THE
TOOL, Check the saw blade to make sure it turns
freely If the blade is free, try to start the motor
again If the motor still does not start, refer to the
"Motor Trouble-Shooting Chart"
3 If the motor suddenly stafls while cutting wood,
turn the power switch off, unplug the tool, and
free the blade from the wood The motor may
now be restarted and the cut finished
,
Frequent "blowing" of fuses or tripping or circuit
breakers may result if:
a MOTOR IS OVERLOADED - Overloading can
occur if you feed too rapidly
b LOW VOLTAGE - Although the motor is de-
signed for operation on the voltage and fre-
quency specified on the motor nameplate,
normal loads will be handled safely on voltages
not more than 10% above or below the name-
plate voltage Heavy loads, however, require
that voltage at motor terminals equals the
voltage specified on nameplate
GROUNDING PRONG
This power tool is equipped with a 3*conductor cord
and ground type plug listed by Underwriters' Labora-
tories, The ground conductor has a green jacket and
is attached to the tool housing at one end and to the
ground prong in the attachment plug at the other
end
This plug requires a mating 3-conductor grounded
type outlet as shown above,
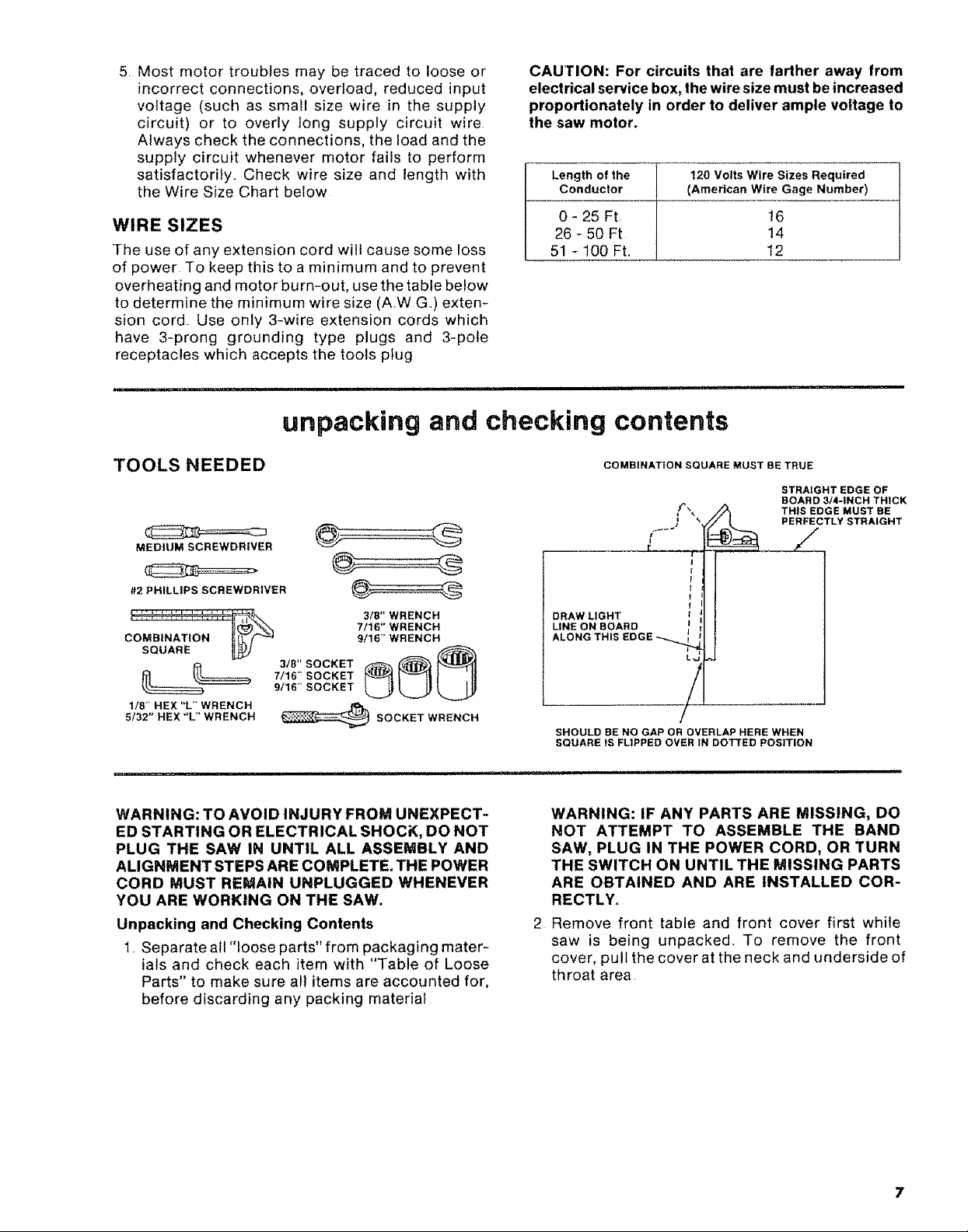
5 Mostmotortroublesmaybetracedto looseor
incorrectconnections,overload,reducedinput
vottage(suchassmallsizewire in thesupply
circuit) or to overlylong supplycircuit wire
Alwayschecktheconnections,theloadandthe
supplycircuit whenevermotorfails to perform
satisfactorily_Checkwiresizeandlengthwith
theWireSizeChartbelow
WIRE SIZES
The use of any extension cord will cause some loss
of power To keep this to a minimum and to prevent
overheating and motor burn-out, use the table below
to determine the minimum wire size (A.W G.) exten-
sion cord. Use only 3-wire extension cords which
have 3-prong grounding type plugs and 3-pole
receptacles which accepts the tools ptug
unpacking and checking contents
CAUTION: For circuits that are farther away from
electrical service box, the wire size must be increased
proportionately in order to deliver ample voltage to
the saw motor.
Length of the 120 Volts Wire Sizes Required
Conductor (American Wire Gage Number)
0 - 25 Ft 16
26 _ 50 Ft 14
51 - t00 Ft. 12
TOOLS NEEDED
MEDIUM SCREWDRIVER
@
.2PHILLIPSSCR WOR,VER@ @
3/8" WRENCH
COMBINATION _("_
SQUARE .i_'
7/16- SOCKET
9/16" SOCKET
118"' HEX "L'" WRENCH
5/32" HEX "L'" WRENCH
WARNING: TO AVOID INJURY FROM UNEXPECT-
ED STARTING OR ELECTRICAL SHOCK, DO NOT
PLUG THE SAW IN UNTIL ALL ASSEMBLY AND
ALIGNMENT STEPS ARE COMPLETE. THE POWER
CORD MUST REMAIN UNPLUGGED WHENEVER
YOU ARE WORKING ON THE SAW.
Unpacking and Checking Contents
t. Separate all "loose parts" from packaging mater-
ials and check each item with "Table of Loose
Parts" to make sure all items are accounted for,
before discarding any packing material
_ SOCKET WRENCH
7/16" WRENCH
9/16'" WRENCH
COMBINATION SQUARE MUST BE TRUE
STRAIGHT EDGE OF
BOARD 3/4=INCH THICK
THIS EDGE MUST BE
PERFECTLY STRAIGHT
DRAW LIGHT
LINE ON BOARD
ALONG THIS EDGE "_._,_
LJ
S
SHOULD BE NO GAP OR OVERLAP HERE WHEN
SQUARE tS FLIPPED OVER IN DOTTED POSITION
WARNING: IF ANY PARTS ARE MISSING, DO
NOT ATTEMPT TO ASSEMBLE THE BAND
SAW, PLUG IN THE POWER CORD, OR TURN
THE SWITCH ON UNTIL THE MISSING PARTS
ARE OBTAINED AND ARE INSTALLED COR-
RECTLY.
Remove front table and front cover first while
saw is being unpacked,. To remove the front
cover, pull the cover at the neck and underside of
throat area
7
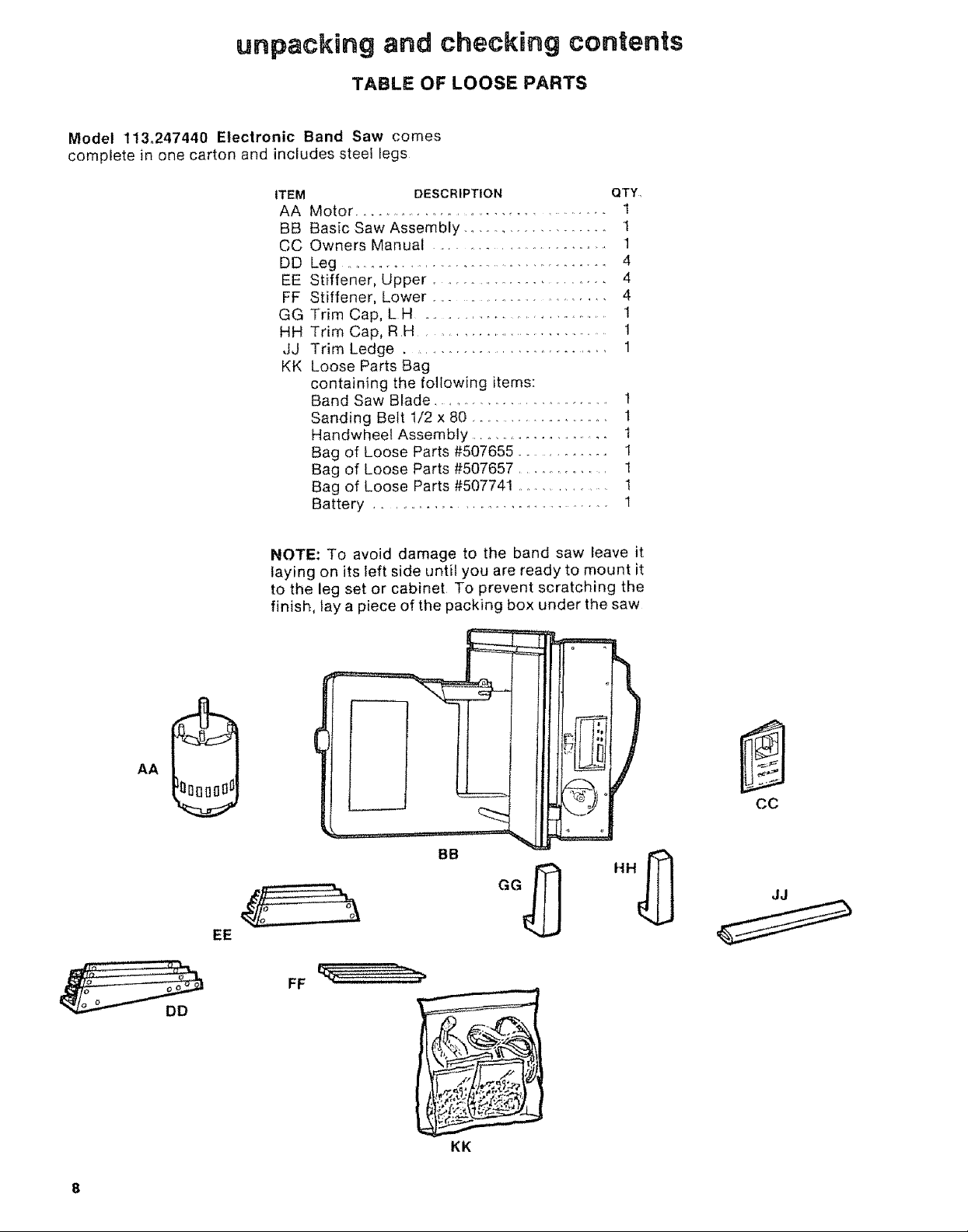
unpacking and checking contents
TABLE OF LOOSE PARTS
Model 113o247440 Electronic Band Saw comes
complete in one carton and includes steel legs
ITEM DESCRIPTION QTY,
AA Motor ................................... t
BB Basic Saw Assembly .................... 1
CC Owners Manual ......................... 1
DD Leg ....................................... 4
EE Stiffener, Upper ......................... 4
FF Stiffener, Lower ........................... 4
GG Trim Cap, LH ......................... 1
HH Trim Cap, RH .......................... 1
JJ Trim Ledge ........................ 1
KK Loose Parts Bag
containing the following items:
Band Saw Blade ....................... 1
Sanding Belt t/2 x 80 .................... t
Handwheet Assembly ....................... I
Bag of Loose Parts #507655 .............. 1
Bag of Loose Parts #507657 .......... 1
Bag of Loose Parts #507741 ................ 1
Battery ................................... 1
DD
NOTE: To avoid damage to the band saw leave it
Saying on its left side until you are ready to mount it
to the leg set or cabinet To prevent scratching the
finish, lay a piece of the packing box under the saw
1
CC
BB
JJ
EE
FF
KK
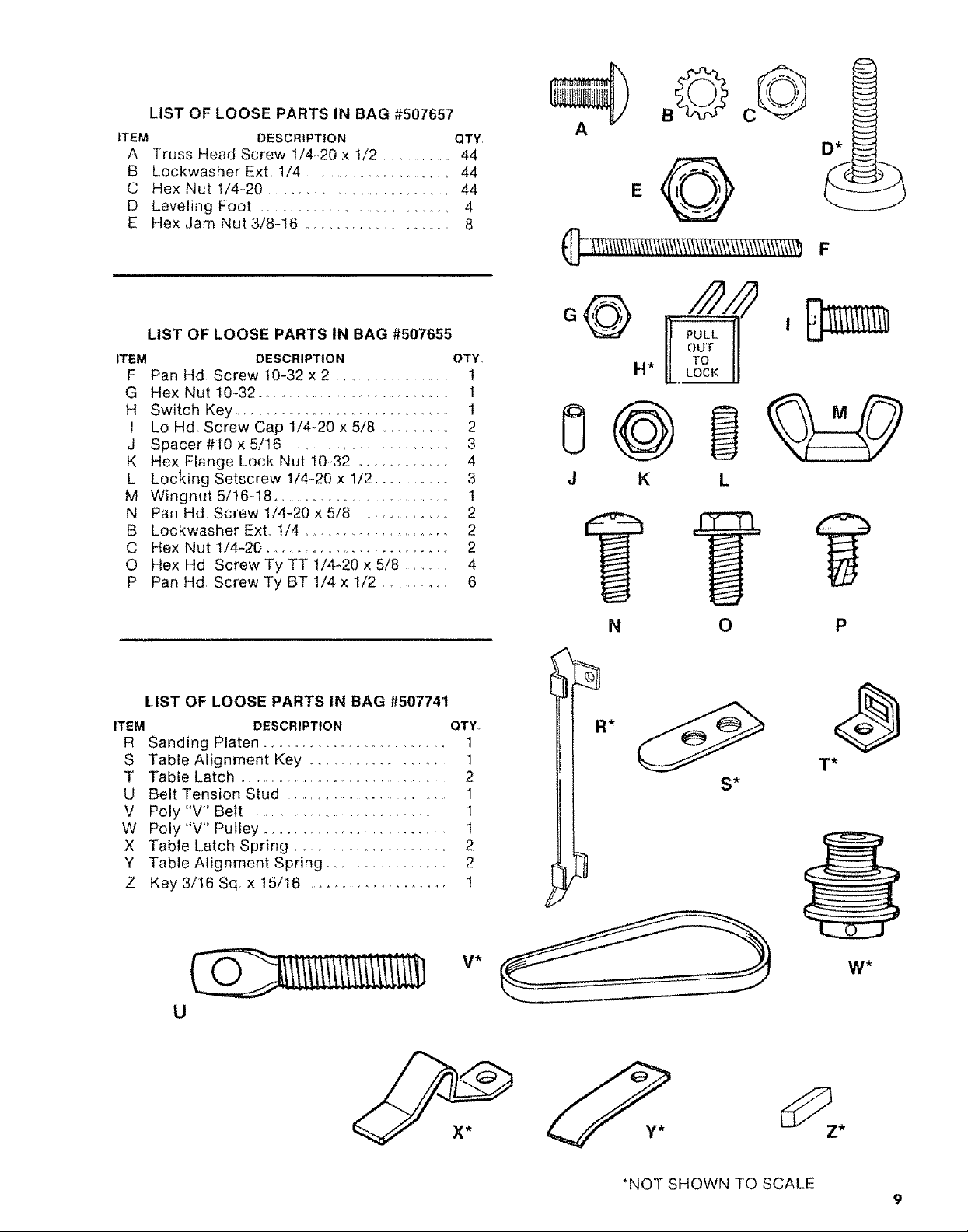
LIST OF LOOSE PARTS IN BAG #507657
ITEM DESCRIPTION QTY
A Truss Head Screw 1/4-20 x 1/2 ........... 44
B Lockwasher Ext, 1/4 .................. 44
C Hex Nut 1/4-20 ........................... 44
D Leveling Foot ........................... 4
E Hex ,Jam Nut 3/8-16 .................... 8
°©c©
@
_t_'_t_,',\\\\\\\',\\\\\\\\\\\_
F
LIST OF LOOSE PARTS IN BAG #507655
ITEM DESCRIPTION OTY,
F Pan Hd Screw I0-32 x 2 ................ 1
G Hex Nut 10-32 ........................ 1
H Switch Key ............................. 1
I Lo Hd, Screw Cap 1/4-20 x 5/8 .......... 2
J Spacer #10 x 5/t6 ........................ 3
K Hex Flange Lock Nut 10-32 ............ 4
L Locking Setscrew 1/4-20 x I/2 ........... 3
M Wingnut 5/!6-18 ..................... 1
N Pan Hd. Screw 1/4-20 x 5/8 .............. 2
B Lockwasher ExL 1/4 ....................... 2
C Hex Nut 1/4-20 ......................... 2
O Hex Hd Screw Ty TT I/4-20 x 5/8 ...... 4
P PanHd ScrewTyBT1/4xl/2 ......... 6
I.iST OF LOOSE PARTS IN BAG #507741
ITEM DESCRIPTION QTY,
R Sanding Platen .......................... 1
S Table Alignment Key ..................... 1
T Table Latch .................................... 2
U Belt Tension Stud ..................... 1
V Poly "V" Belt ........................... 1
W Poly"V" Pulley ......................... 1
X Table Latch Spring ........................... 2
Y Table Alignment Spring ................ 2
Z Key 3/16 Sq, x 15/16 .................. 1
o@
H*
0@
J K
N O P
LOCK
L
S_t
V _
U
*NOT SHOWN TO SCALE
W_
9
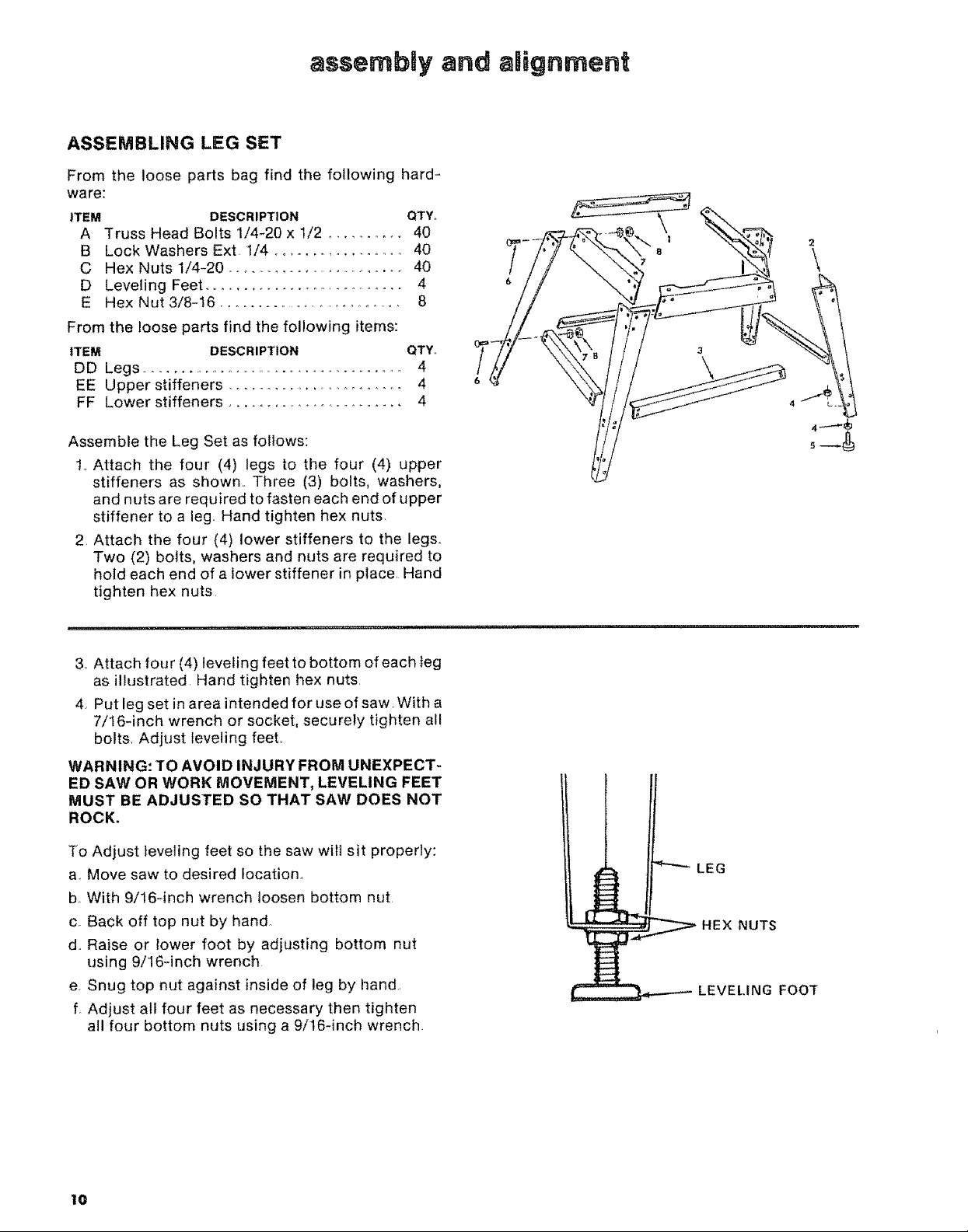
assembly and amignment
ASSEMBLING LEG SET
From the loose parts bag find the following hard-
ware:
ITEM DESCRIPTION QTY_
A Truss Head Bolts 1/4-20 x 1/2 ........... 40
B Lock Washers Ext 1/4 ................. 40
C Hex Nuts 1/4-20 .......................... 40
D Leveling Feet ......................... 4
E Hex Nut 3/8-16 ............................... 8
From the loose parts find the following items:
ITEM DESCRIPTION QTYo
DD Legs ...................................... 4
EE Upper stiffeners ........................... 4
FF Lower stiffeners ..................... 4
Assemble the Leg Set as follows:
1..Attach the four (4) legs to the four (4) upper
stiffeners as shown.. Three (3) bolts, washers,
and nuts are required to fasten each end of upper
stiffener to a leg. Hand tighten hex nuts,
2 Attach the four (4) lower stiffeners to the legs..
Two (2) bolts, washers and nuts are required to
hold each end of a lower stiffener in place. Hand
tighten hex nuts
3. Attach four (4) leveling feet to bottom of each leg
as illustrated Hand tighten hex nuts
4, Put leg set in area intended for use of saw With a
7/16-inch wrench or socket, securely tighten all
bolts. Adjust leveling feet.
WARNING: TO AVOID INJURY FROM UNEXPECT-
ED SAW OR WORK MOVEMENT, LEVELING FEET
MUST BE ADJUSTED SO THAT SAW DOES NOT
ROCK.
To Adjust leveling feet so the saw will sit properly:
a_ Move saw to desired location.
b. With 9/16-inch wrench loosen bottom nut
co Back off top nut by hand
d.. Raise or lower foot by adjusting bottom nut
using 9/16-inch wrench
e. Snug top nut against inside of leg by hand..
foAdjust all four feet as necessary then tighten
all four bottom nuts using a 9/16-inch wrench
LEG
NUTS
LEVELING FOOT
]0
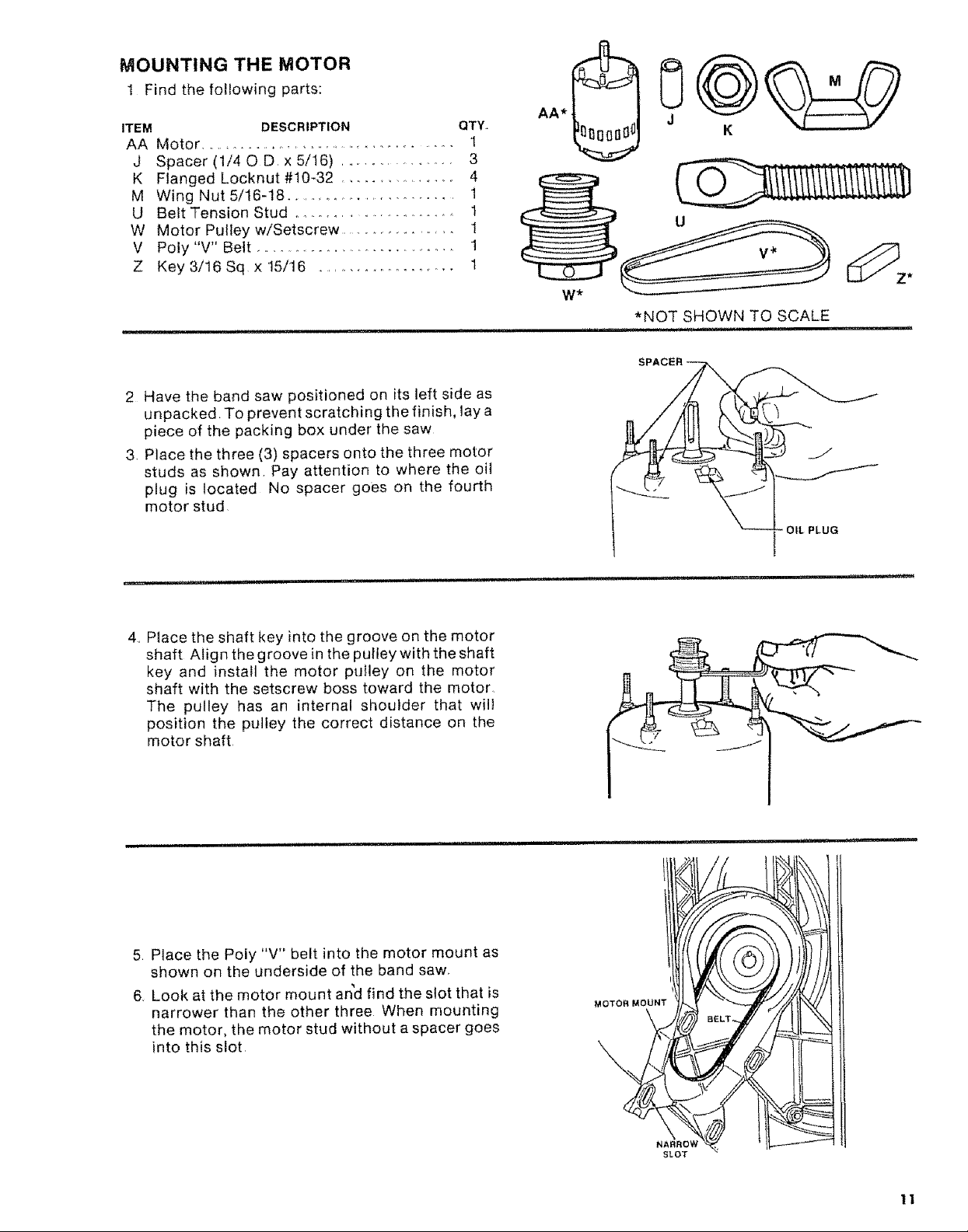
MOUNTING THE MOTOR
1 Find the following parts:
ITEM DESCRIPTION QTY_
AA Motor ..................................... 1
J Spacer (1/40 D x 5/16) ................ 3
K Flanged Locknut #10-32 .................. 4
M Wing Nut 5/16-18 ........................ 1
U Belt Tension Stud ........................... 1
W Motor Pulley w/Setscrew .................. 1
V Poly"V" Belt .................................... 1
Z Key3/16Sq x15/16 ..................... 1
2 Have the band saw positioned on its left side as
unpacked. To prevent scratching the finish, lay a
piece of the packing box under the saw
3, Place the three (3) spacers onto the three motor
studs as shown Pay attention to where the oil
plug is located No spacer goes on the fourth
motor stud
AA*
J K
U
*NOT SHOWN TO SCALE
\
_r_ O|L PLUG
4,, Place the shaft key into the groove on the motor
shaft Align the groove in the pulley with the shaft
key and install the motor pulley on the motor
shaft with the setscrew boss toward the motor
The pulley has an internal shoutder that wil_
position the pulley the correct distance on the
motor shaft
5, Place the Poly "V" belt into the motor mount as
shown on the underside of the band saw,
6. Look at the motor mount and find the slot that is
narrower than the other three When mounting
the motor, the motor stud without a spacer goes
into this slot
I
MOTOR MOUNT
NARROW
,SLOT
I]
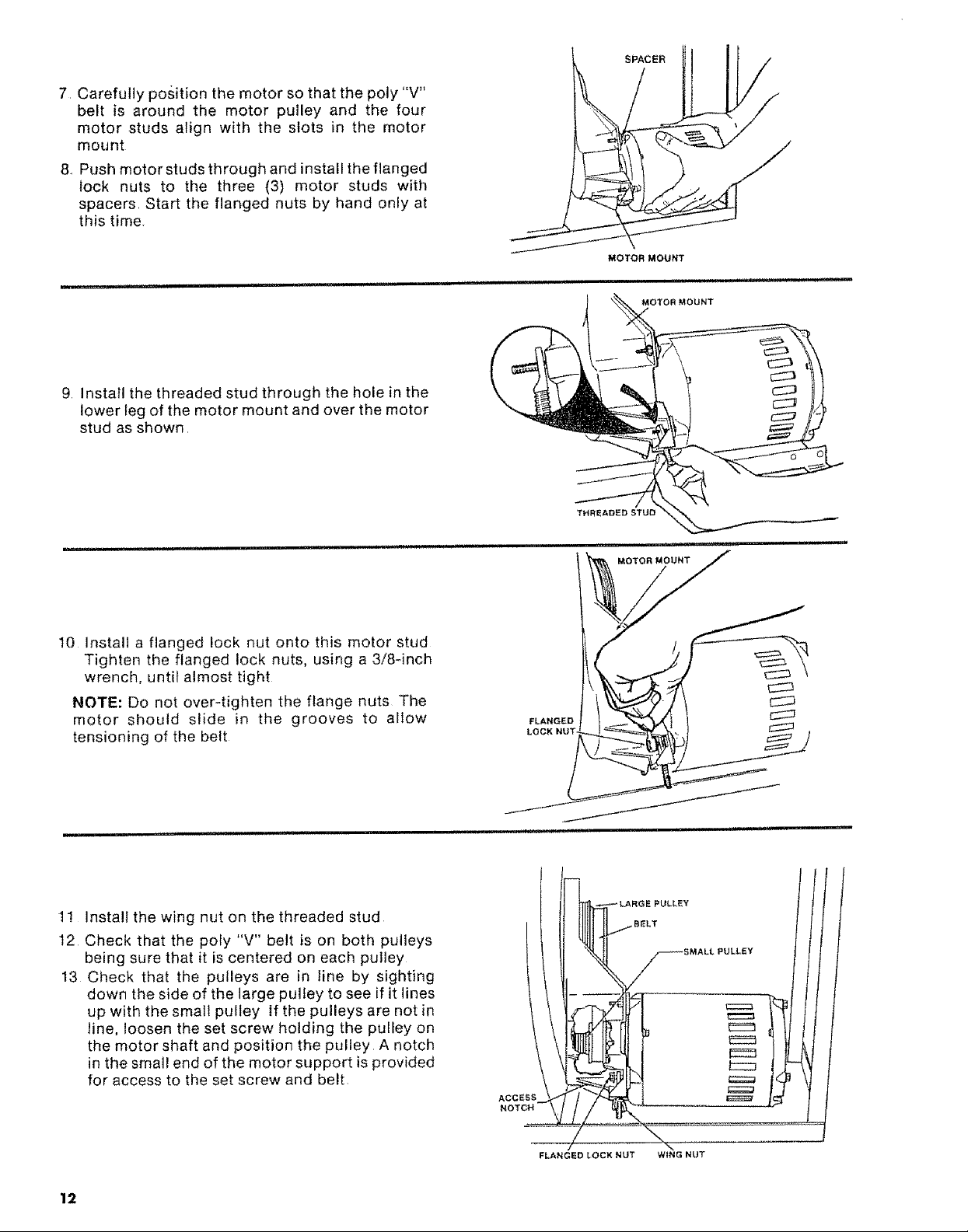
7 Carefully position the motor so that the poly "V"
belt is around the motor pulley and the four
motor studs align with the slots in the motor
mount
8, Push motor studs through and install theflanged
lock nuts to the three (3) motor studs with
spacers, Start the flanged nuts by hand only at
this time,
9, Install the threaded stud through the hole in the
lower teg of the motor mount and over the motor
stud as shown
SPACER
10 Install a flanged lock nut onto this motor stud
Tighten the flanged lock nuts, using a 3/8qnch
wrench, until almost tight
NOTE: Do not over-tighten the flange nuts The
motor should slide in the grooves to allow
tensioning of the belt
1! Install the wing nut on the threaded stud
12 Check that the poly "V" belt is on both pulleys
being sure that it is centered on each pulley
13 Check that the pulleys are in fine by sighting
down the side of the large pulley to see if it lines
up with the small pulley If the pulleys are not in
line, loosen the set screw holding the pulfey on
the motor shaft and position the pulley A notch
in the small end of the motor support is provided
for access to the set screw and belt,
THREADED STUD
\.oTo.MouNTf
1,,,, im
• SMALL PULLEY
N
12
/ -.,
FLANGED LOCK NUT WING NUT
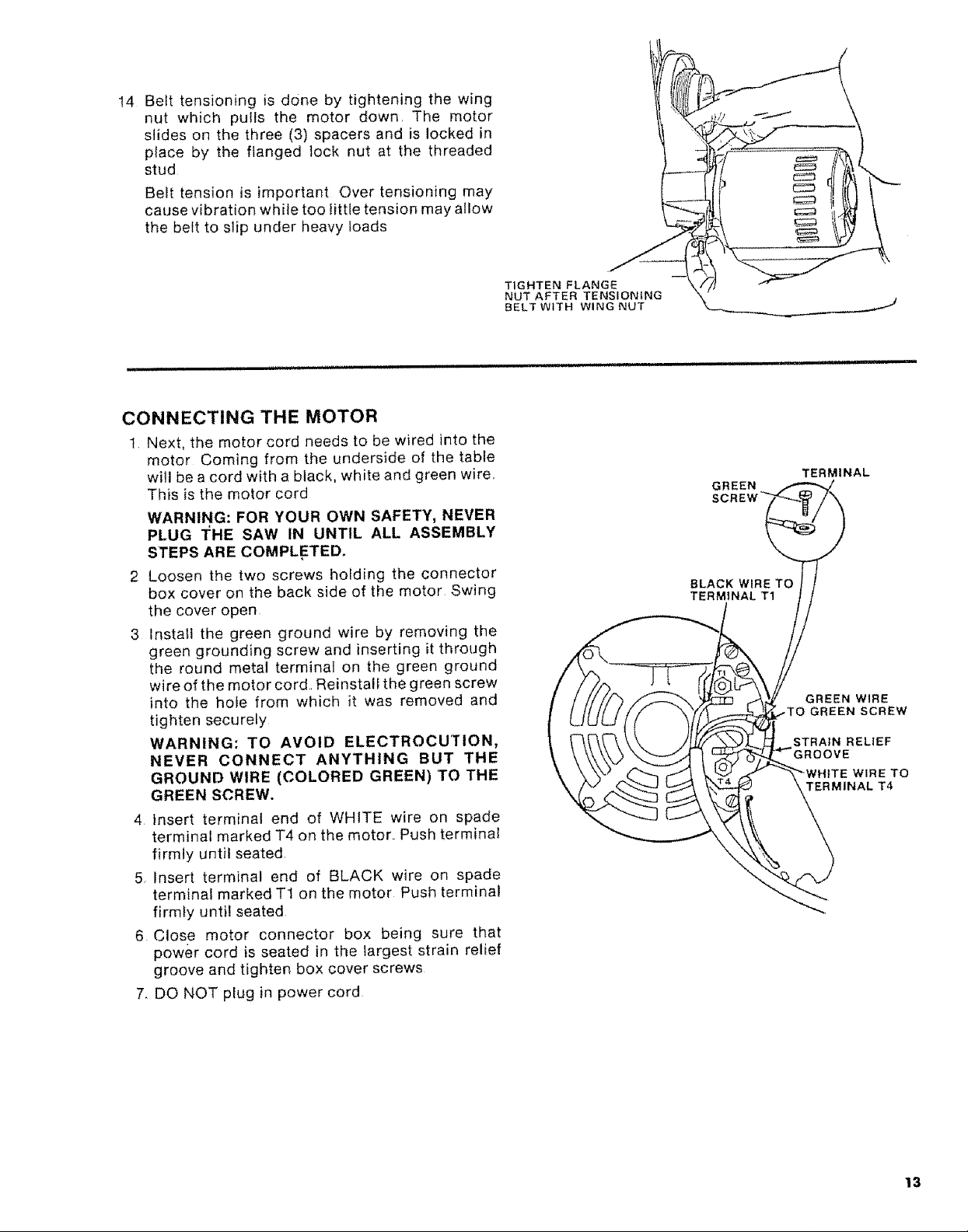
14 Belttensioningisdoneby tighteningthewing
nut which pulls the motor down, The motor
slideson thethree(3}spacersandislockedin
place by the flanged lock nut at the threaded
stud
Belt tension is important Over tensioning may
cause vibration while too little tension may allow
the belt to slip under heavy loads
CONNECTING THE MOTOR
1, Next, the motor cord needs to be wired into the
motor Coming from the underside of the table
will be a cord with a black, white and green wire,
This is the motor cord
WARNING: FOR YOUR OWN SAFETY, NEVER
PLUG "FHE SAW IN UNTIL ALL ASSEMBLY
STEPS ARE COMPL,ETEDo
2 Loosen the two screws holding the connector
box cover on the back side of the motor Swing
the cover open
3 Install the green ground wire by removing the
green grounding screw and inserting it through
the round metal terminal on the green ground
wire of the motor cord,, Reinstall the green screw
into the hole from which it was removed and
tighten securely
WARNING: TO AVOID ELECTROCUTION,
NEVER CONNECT ANYTHING BUT THE
GROUND WIRE (COLORED GREEN) TO THE
GREEN SCREW.
4 Insert terminal end of WHITE wire on spade
terminal marked T4 on the motor Push terminal
firmly until seated,
5 Insert terminal end of BLACK wire on spade
terminal marked T1 on the motor Push terminal
firmly until seated
6 Close motor connector box being sure that
power cord is seated in the largest strain relief
groove and tighten box cover screws
7, DO NOT plug in power cord
TIGHTEN FLANGE
NUT AFTER TENSIONING
BELT WITH WING NUT
GREEN
BLACK WIRE T(
TERMINAL T1
TERMINAL
GREEN WIRE
STRAIN RELIEF
WIRE TO
TERMINAL T4
]3
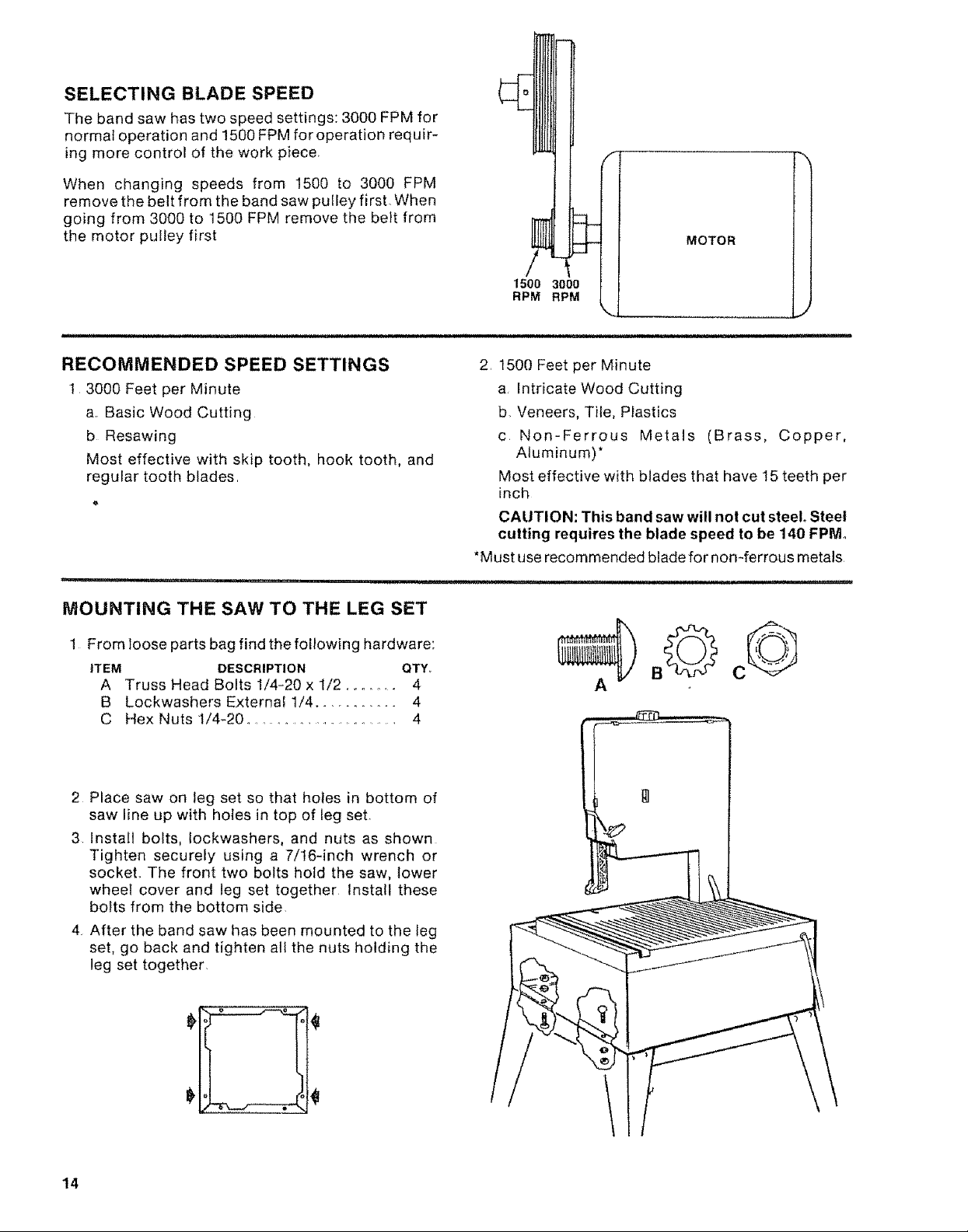
SELECTING BLADE SPEED
The band saw has two speed settings: 3000 FPM for
normal operation and 1500 FPM for operation requir-
ing more control of the work piece.
When changing speeds from 1500 to 3000 FPM
remove the belt from the band saw pulley first. When
going from 3000 to 1500 FPM remove the belt from
the motor pulley first
F
MOTOR
1500 3000
RPM RPM
RECOMMENDED SPEED SETTINGS
1 3000 Feet per Minute
a. Basic Wood Cutting
b Resawing
Most effective with skip tooth, hook tooth, and
regular tooth blades.
,, , =,, = =,, , =
MOUNTING THE SAW TO THE LEG SET
1 From loose parts bag find the following hardware:
ITEM DESCRIPTION QTY,
A Truss Head Bolts 1/4-20 x t/2 ........ 4
B Lockwashers External 1/4 ........... 4
C Hex Nuts 1/4-20 ........................ 4
2 Place saw on leg set so that holes in bottom of
saw line up with holes in top of feg set.
3 Install bolts, lockwashers, and nuts as shown
Tighten securely using a 7/16-inch wrench or
socket.. The front two bolts hold the saw, lower
wheel cover and leg set together Install these
bolts from the bottom side,
4. After the band saw has been mounted to the leg
set, go back and tighten all the nuts holding the
leg set together.
2. t500 Feet per Minute
a Intricate Wood Cutting
b. Veneers, Tile, Plastics
c. Non-Ferrous Metals (Brass, Copper,
Aluminum)*
Most effective with blades that have 15 teeth per
inch
CAUTION: This band saw will not cut steel. Steel
cutting requires the blade speed to be 140 FPM
*Must use recommended blade for nomferrous metals
14