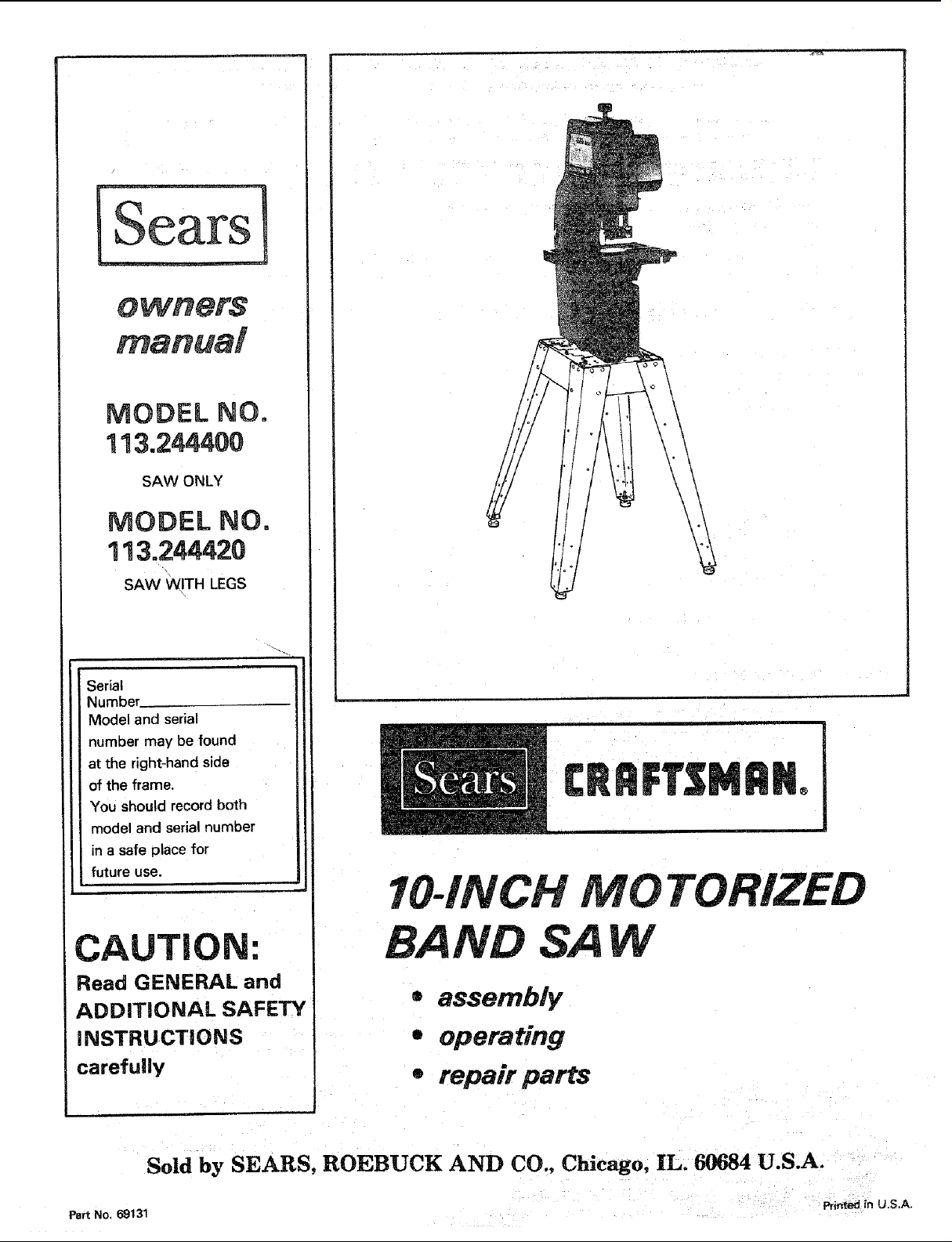
MODEL NO.
113.244400
SAW ONLY
, ,,,,,j,,,,r,,,,,,,,
MODEL NO.
113.244420
SAW WITH LEGS
Serial
Number
Model and serial
number may be found
at the right-hand side
of the frame.
You should record both
model and serial number
in a safe place for
future use.
CAUTION:
IO-/NCH MOTORIZED
Read GENERAL and
ADDITIONAL SAFETY
iNSTRUCTIONS
carefully
Sold by SEARS, ROEBUCK AND CO., Ch cage, IL. 60684 U.S.A.
Part No. 69131 Printed in U.S,A.
® assembly
= operating
® repairparts
i
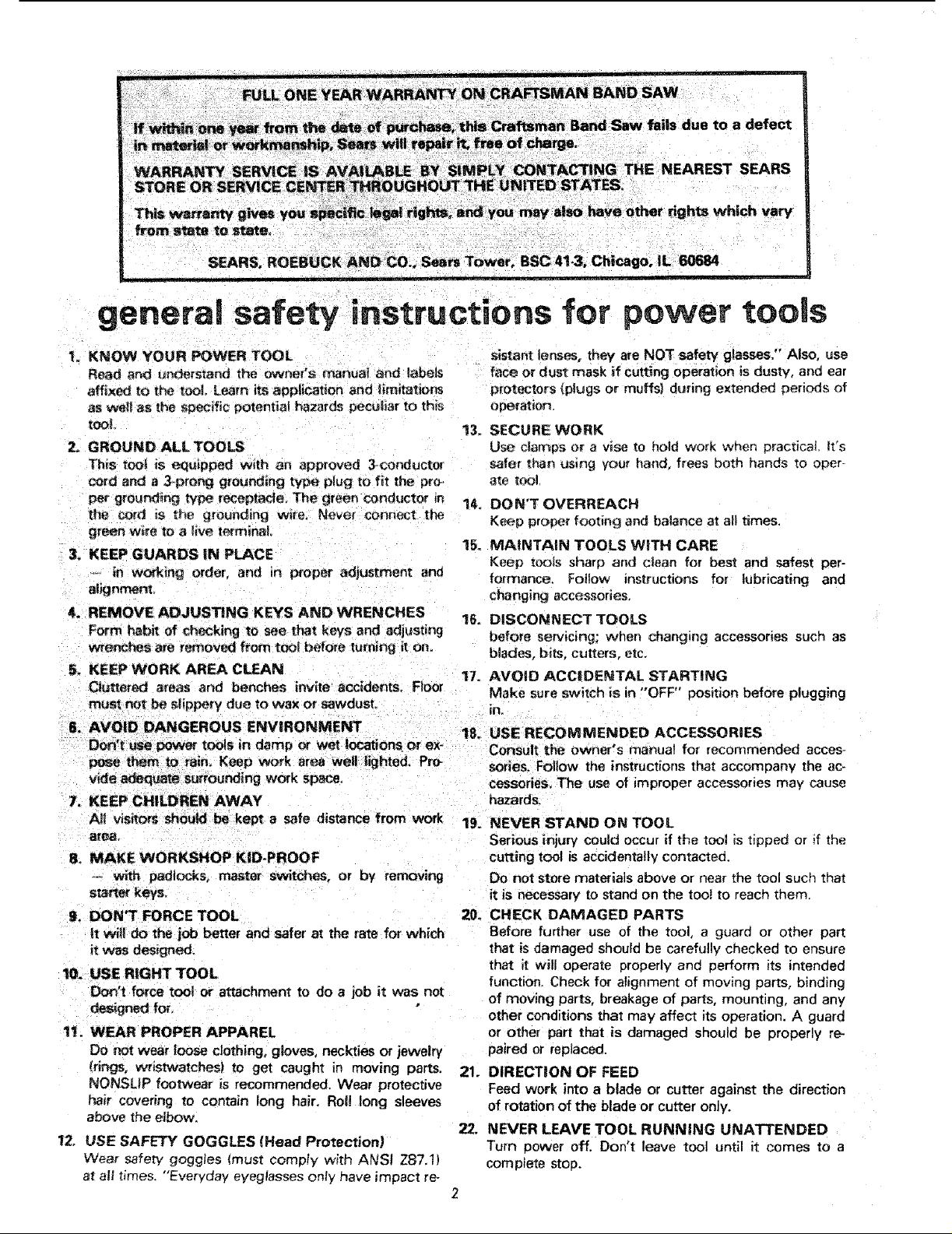
_due to a defect
SEARS
you rr_y also have otherdghts which vary
, SEARS0 ROEBUCK AND C0.. Sea_ Tower. BSC 41.3. Chicago. IL 60684
genera! safetyinstructions for power tools
1. KNOW YOUR POWER TOOL
Read and =_nderstand the owner's manual and labels
affixed to the tool Learn its app|ication and thnita[ions
as we_! as the s_ecific potential hazards peculiar to this
tool
2. GROUND ALL TOOLS
This toot is _quipped with an approved 3-conductor
_,x_rdand a 3_prong grounding type plug to fit the prc_.
per grounding type receptacle. The green conductor _n
the _rd is the grounding wire, Neverconnect the
green w_re to a |ire terminal.
3. KEEP GUARDS iN PLACE
in working order, and =n proper adjustment and
eBignrnent,
4. REMOVE ADJUSTING KEYS ANDWRENCHES
Form habit of checking to see that keys and adjusting
wrenches are r_noved frorr too! before turning _ton,
5, KEEP WORK AREA CLEAN
Ctu_ered areas and benches invite accidents. Floor
must r_t be slipperydue to wax or sawdust.
6_ AVOID DANGEROUS ENVIRONMENT 18. USERECOMMENDED ACCESSORIES
Do_'t use power tools in damp ot wet b-._.ationsor ex- Cortsult the owner's manual for recommended acces-
ted. Pr_ ..........s°ries-F°ll°WTheuse,the instructi°nsofimproperthatacceseoriesaCC°mpanYmaythecauseaC"
7. KEEP CHILDRENAWAY
AJt visitors should be kept a safe distance from work
8r_,
8. MAKE WORKSHOP KID-PROOF
-_ with padlocks, master switd-_es, or by removing
s_rter keys.
g. DON'T FORCE TOOL
It wifl do the job better and safer at the rate for which
it was des_ned.
10. USE RIGHT TOOL
Don't force tool or attachment to do a job it was not
deigned for.
1!. WEAR PROPER APPAREL
Do not wear loose clothing, giovea, neckties of jewelry
(rings, wristwatches) to get caugh_ in moving parts.
NONSUP footwear is recommended. Wear protective
hair covering to contain long hair. Rol! long sleeves
above the elbow.
12. USE SAFETY GOGGLES (Head Protection_
Wear safety goggles (must comply with ANSI Z87.1)
at all dines. "Everyday eyeglasses onty have impact re-
sistant lenses, they are NOT safety glasses:' Also. use
face or dust mask if cutting operation is dusty, and ear
protectors (ptugs or muffs} dudng extended periods of
operatior_.
33. SECURE WORK
Use ¢|a_ps or a vise to hold work wr_en practical It's
_ier than using your hand. frees both hands to oper
ate tool
14. DON'T OVERREACH
Keep proper footing and balance at al! times
15. MAINTAIN TOOLS WITH CARE
Keep tools sharp and dean for best and safest per-
formance. Follow instructions for lubricating and
changing accessories,
16. DISCONNECT TOOLS
before servicing; when changing accessories such as
blades, bits, cutters, etc.
17. AVOID ACCIDENTAL STARTING
Make sure switch is in "OFF" _osition before plugging
in=
hazards,
19. NEVER STAND ON TOOL
Serious inlury could occur if the tool is tipped or }f the
cutting tool is accidentally contacted.
Donor store materials above or near the tool such that
it is necessary to stand on the tooJ to reach them.
20. CHECK DAMAGED PARTS
Before, further use of the tool, a guard or other part
that is damaged should be carefully checked to ensure
that it will operate properly anc_ perform its intended
function, Check for alignment of moving parts, binding
of moving ;)arts, breakage of parts, mounting, and any
other conditions that may affect its operation. A guard
or other part that is damaged should be properly r_
paired or replaced.
21. DIRECTION OF FEED
Feed work into a blade or cutter against the direction
of rotation of the blade or cutter only.
22. NEVER LEAVE TOOL RUNNING UNATTENDED
Turn power off. Don't leave tool until it comes to a
complete stop.
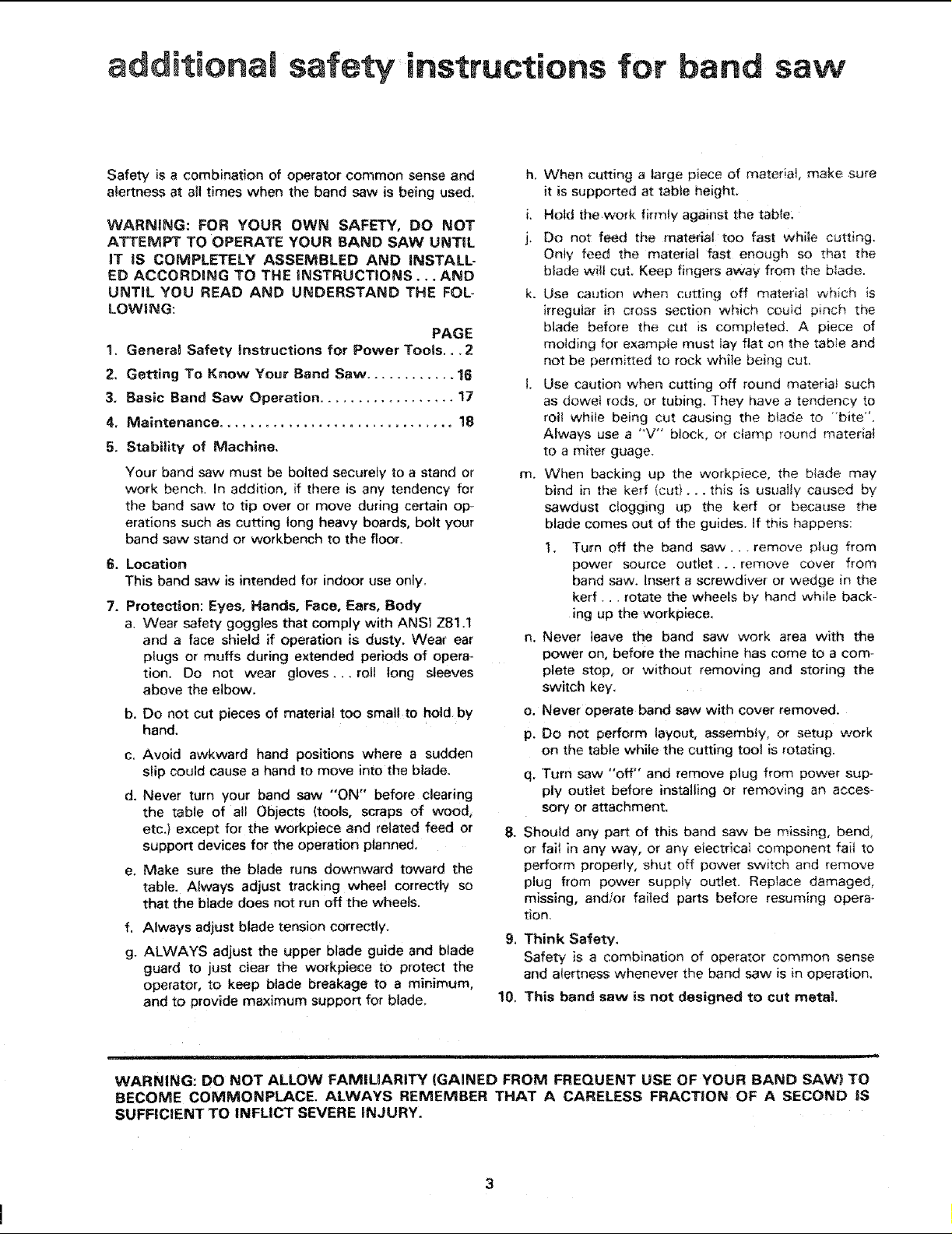
additional safety instructions for band saw
Safety is a combination of operator common sense and
alertness at all times when the band saw is being used.
WARNING: FOR YOUR OWN SAFETY, DO NOT
ATTEMPT TO OPERATE YOUR BAND SAW UNTIL
IT iS COMPLETELY ASSEMBLED AND INSTALL-
ED ACCORDING TO THE INSTRUCTIONS.. _AND
UNTIL YOU READ AND UNDERSTAND THE FOb
LOWING:
PAGE
1. General Safety Instructions for Power Toots.,. 2
2. Getting To Know Your Band Saw ............ 16
3. Basic Band Saw Operation .................. 17
4. Maintenance ............................... 18
5. Stability of Machine,
Your band saw must be bolted secureiy to a stand or
work bench. In addition, if there is any tendency for
the band saw to tip over or move during certain op
erations such as cutting long heavy boards, bolt your
band saw stand or workbench to the floor.
,
Location
This band saw is intended for indoor use only.
7.
Protection: Eyes, Hands, Face, Ears, Body
a Wear safety goggles that comply with ANSI Z81.1
and a face shield if operation is dusty. Wear ear
plugs or muffs during extended periods of opera-
tion. Do not wear gloves,., roll long sleeves
above the elbow.
b,
Do not cut pieces of materia! too small to hold by
hand.
C.
Avoid awkward hand positions where a sudden
slip could cause a hand to move into the blade,
d.
Never turn your band saw "ON" before clearing
the table of all Objects (tools, scraps of wood,
etc.) except for the workpiece and related feed or
support devices for the operation planned.
Make sure the blade runs downward toward the
e_
table. Always adjust tracking wheel correctly so
that the blade does not run off the wheels.
f,
Always adjust blade tension correctly.
ALWAYS adjust the upper blade guide and blade
g-
guard to just clear the workpiece to protect the
operator, to keep btade breakage to a minimum,
and to provide maximum support for blade,
h. When cutting a large piece of material, make sure
it is supported at table height,
i, Hold the work firmiy against the table:
j. Do not feed the matedal too fast while cutting.
Only feed the material fast enough so thaz the
blade witl cut, Keep fingers away from the blade.
k, Use citation when cutting off materia_ vvh;ch is
irregular in cross section ,which couid pinch the
blade before the cut is completed. A piece of
motding for exampte must lay fiat on the tab!e and
not be permitted to rock while being cut.
t. Use caution when cutting off round rnateria_ such
as dowel rods, or tubing. They have a tendency/ _o
rol_ whiie being cut causing the b_ade to 'bite".
Always use a "V" block, o_ ctamp round materia!
to a miter guage.
m,
When backing up the workpiece, the btade may
bind in the kerf (cut),.. this is usually caused by
sawdust clogging up the kerr or because the
blade comes out of the guides. If this happens:
1° Turn off the band saw.._ remove ptug from
power source outlet.,, remove cover from
band saw. Insert a screwdive_ or wedge in the
kerr _.. rotate the wheels by hand while back-
ing up the workpiece,
n. Never leave the band saw work area with the
power on, before the machine has come to a com-
plete stop, or without removing and storing the
switch key,
o, Never operate band saw with cover removed.
p. Do not perform layout, assembly, or setup work
on the table while the cutting tool is rotating.
q, Turn saw "off" and remove plug from power sup-
ply outlet before installing or removing an acces=
sory or attachment,
°
Should any part of this band saw be missing, bend,
or fail in any way, or any electrica_ component fail to
perform properly, shut off power switch and remove
plug from power supply outlet. Replace damaged,
missing, andJor failed parts before resuming opera-
rich.
9,
Think Safety,
Safety is a combination of operator common sense
and alertness whenever the band saw is in operation.
10, This band saw _s not designed to cut metal
i i ii, i i, , i ii ii i _1,
WARNING: DO NOT ALLOW FAMIUARITY (GAINED FROM FREQUENT USE OF YOUR BAND SAW} TO
BECOME COMMONPLACE. ALWAYS REMEMBER THAT A CARELESS FRACTION OF A SECOND IS
SUFFICIENT TO iNFLICT SEVERE INJURY.
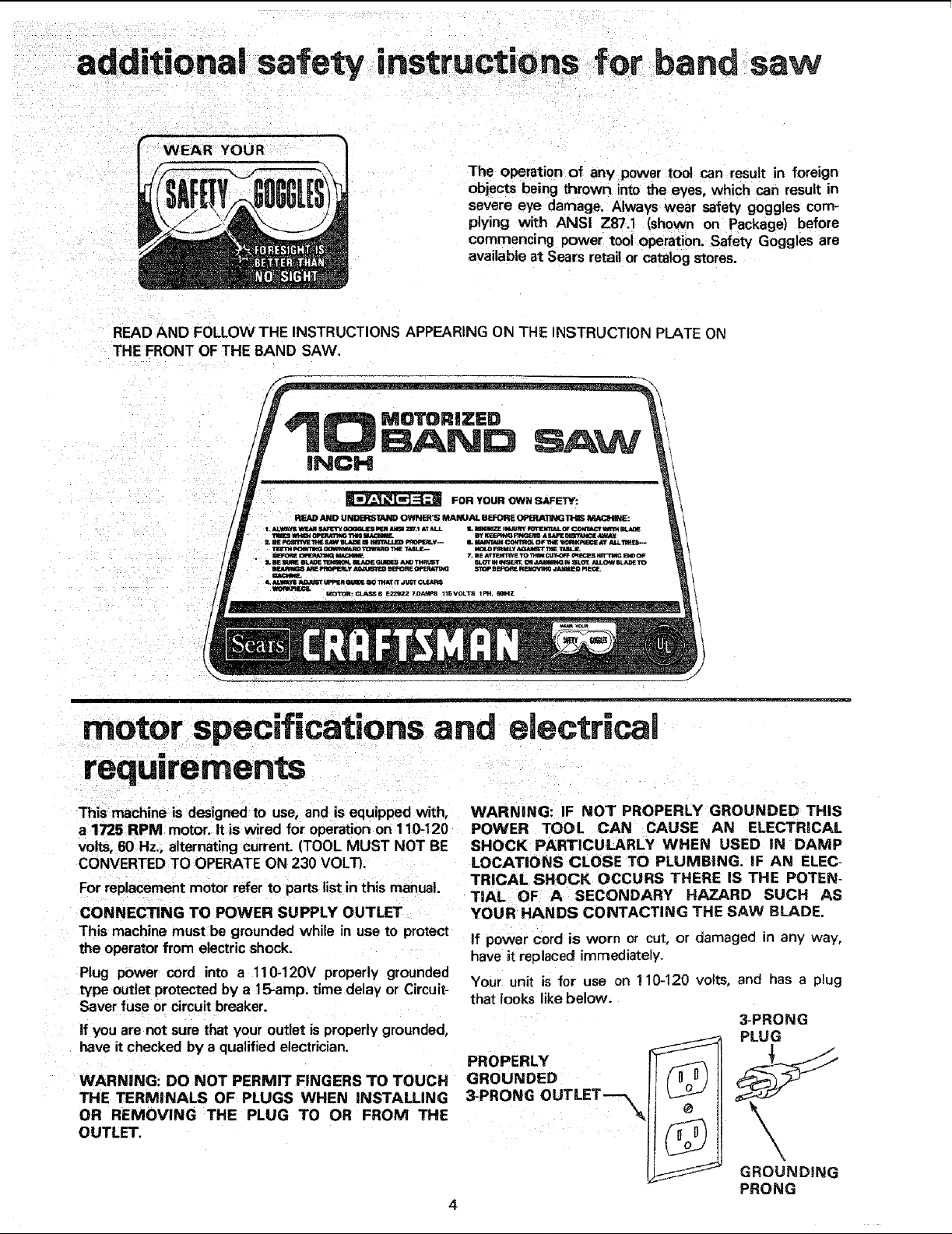
safety instructions for band saw
The operation of any power tool can result in foreign
objects being throwr; into the eyes, which can resultin
severe eye damage, Always wear safety goggles com-
plying with ANSI Z87.1 (shown on Package) before
commencing power t0oloperation. Safety Goggles are
available at Sears retail or catalog stores.
READ AND FOLLOW THE INSTRUCTIONS APPEARING ON THE INSTRUCTION PLATE ON
THE FRONT OF THE BAND SAW.
MOTORIZED
BAND SAW
INCH
motor specifications and
requirements
This machine is designed to use, and is equipped with,
a 1725 RPM motor. It is wired for operation on 110-120
volts, 60 Hz., alternating current. (TOOL MUST NOT BE
CONVERTED TO OPERATE ON 230 VOLT).
For replacement motor refer to parts list in this manual.
CONNECTING TO POWER SUPPLY OUTLET
This machine must be grounded while in use to protect
the operator from electric shock.
Plug power cord into a 110-120V properly grounded
type outlet protected by a 15-amp. time delay or Circuit-
Saver fuse or circuit breaker.
If you are not sure that your outlet is properly grounded,
have it checked by a qualified electrician.
WARNING: DO NOT PERMIT FINGERS TO TOUCH
THE TERMINALS OF PLUGS WHEN INSTALLING
OR REMOVING THE PLUG TO OR FROM THE
OUTLET.
GROUNDED
_PRONG OUTLET--_
........... _L J
eJectrJcaJ
WARNING: IF NOT PROPERLY GROUNDED THIS
POWER TOOL CAN CAUSE AN ELECTRICAL
SHOCK PARTICULARLY WHEN USED iN DAMP
LOCATIONS CLOSE TO PLUMBING. IF AN ELEC-
TRICAL SHOCK OCCURS THERE IS THE POTEN-
TIAL OF A SECONDARY HAZARD SUCH AS
YOUR HANDS CONTACTING THE SAW BLADE.
If power cord is worn or cut, or damaged in any way,
have Jtreplaced immediately.
Your unit is for use on 110-120 volts, and has a plug
that looks likebelow.
3-PRONG
PLUG
PROPERLY
GROUNDING
PRONG
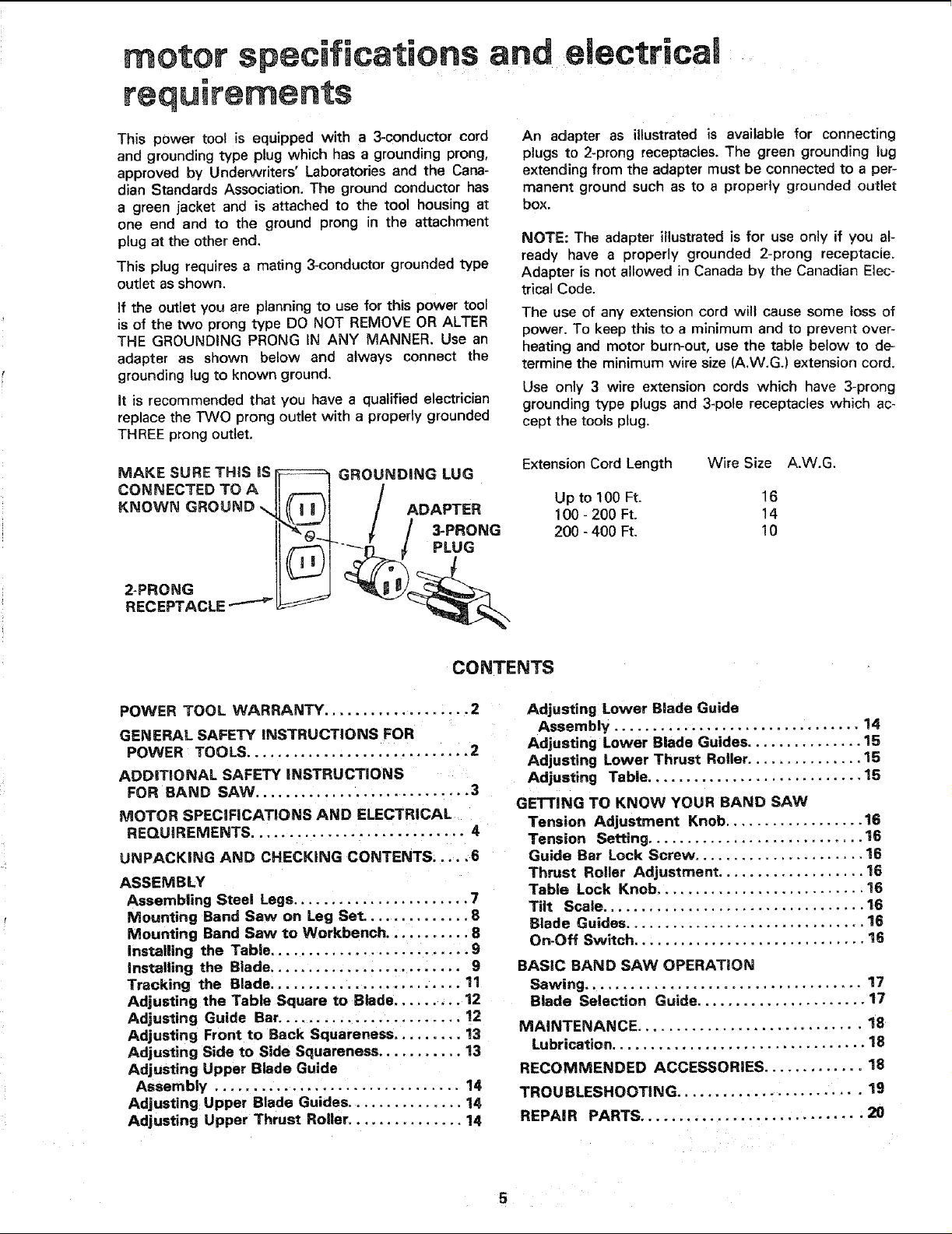
motor specifications and electrical
requirements
This power toot is equipped with a 3-conductor cord
and grounding type plug which has a grounding prong,
approved by Underwriters' Laboratories and the Cana-
dian Standards Association. The ground conductor has
a green jacket and is attached to the tool housing at
one end and to the ground prong in the attachment
plug at the other end.
This plug requires a mating 3-conductor grounded type
outlet as shown.
ff the outlet you are planning to use for this power tool
is of the two prong type DO NOT REMOVE OR ALTER
THE GROUNDING PRONG IN ANY MANNER. Use an
adapter as shown below and always connect the
grounding lug to known ground.
It is recommended that you have a qualified electrician
replace the TWO prong outlet with a properly grounded
THREE prong outlet.
MAKE SURE THIS IS -_ GROUNDING LUG
KNOWN GROUND \ ADAPTER
CONNECTED TO A .@ 1 /
I / 3PRONG
An adapter as illustrated is available for connecting
plugs to 2-prong receptacles. The green grounding tug
extending from the adapter must be connected to a per-
manent ground such as to a properly grounded outlet
box.
NOTE: The adapter illustrated is for use only if you al-
ready have a properly grounded 2-prong receptacle.
Adapter is not allowed in Canada by the Canadian Elec-
trical Code.
The use of any extension cord will cause some loss of
power. To keep this to a minimum and to prevent over-
heating and motor burn-out, use the table below to de-
termine the minimum wire size (A.W.G.) extension cord.
Use only 3 wire extension cords which have 3-prong
grounding type plugs and 3-pole receptacles which ac-
cept the tools plug.
Extension Cord Length
Up to 100 Ft. 16
100 - 200 Ft. 14
200 - 400 Ft. 10
Wire Size A.W.G.
RECEPTACLE /
CONTENTS
POWER TOOL WARRANTY ...................2
GENERAL SAFETY INSTRUCTIONS FOR
POWER TOOLS .............................2
ADDITIONAL SAFETY iNSTRUCTIONS
FOR BAND SAW ............................ 3
MOTOR SPECIFICATIONS AND ELECTRICAL
REQU IREMENTS ............................ 4
UNPACKING AND CHECKING CONTENTS ..... 6
ASSEMBLY
Assembling Steel Legs ....................... 7
Mounting Band Saw on Leg Set .............. 8
Mounting Band Saw to Workbench ........... 8
Installing the Table .......................... 9
Installing the Blade ......................... 9
Tracking the Blade ......................... 11
Adjusting the Table Square to Blade ......... 12
Adjusting Guide Bar ........................ !2
Adjusting Front to Back Squareness ......... 13
Adjusting Side to Side Squareness ........... 13
Adjusting Upper Blade Guide
Assembly ................................ 14
Adjusting Upper Blade Guides ............... 14
Adjusting Upper Thrust Roller ............... 14
Adjusting Lower Blade Guide
Assembly ................................ 14
Adjusting Lower Blade Guides ............... 15
Adjusting Lower Thrust Roller ............... 15
Adjusting Table ............................ 15
GETTING TO KNOW YOUR BAND SAW
Tension Adjustment Knob .................. 16
Tension Setting ............................ 16
Guide Bar Lock Screw ...................... 16
Thrust Roller Adjustment ................... 16
Table Lock Knob ........................... 16
Tilt Scale .................................. 16
Blade Guides ............................... 16
On-Off Switch .............................. 16
BASIC BAND SAW OPERATION
Sawing .................................... 17
Blade Selection Guide ...................... 17
MAINTENANCE ............................. 18
Lubrication ................................. 18
RECOMMENDED ACCESSORIES ............. 18
TROUBLESHOOTING ........................ 19
REPAIR PARTS ............................. 20
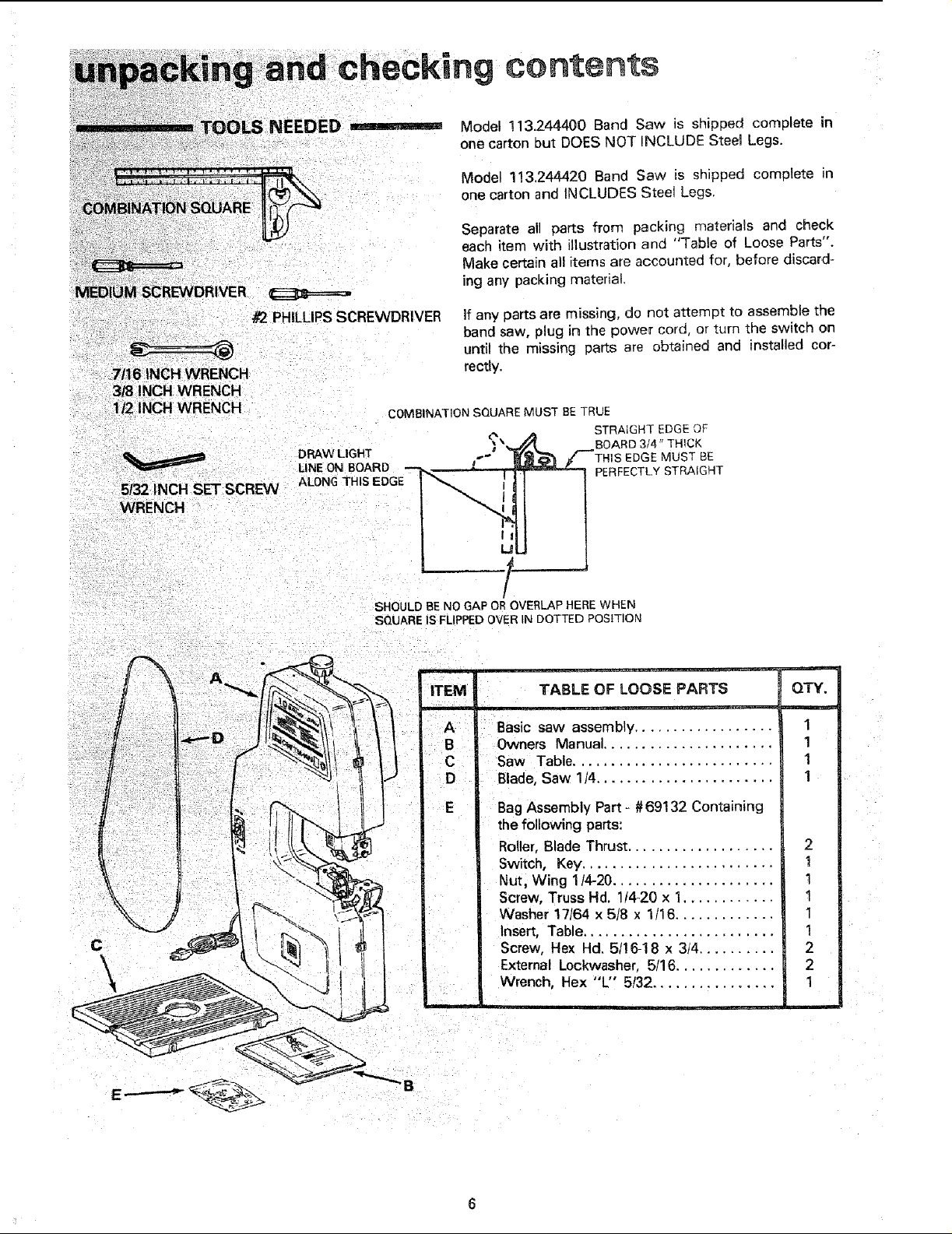
and checking contents
Model 113.244400 Band Saw is shipped complete in
one carton 10ut DOES NOT INCLUDE Steel Legs.
Model 113.244420 Band Saw is shipped complete in
one carton and iNCLUDES Steel Legs,
Separate all oarts from packing materials and check
each item with illustration and "Table of Loose Parts".
Make certain atl items are accounted for, before discard-
ing any packing material.
INCH WRENCH
#2 PHILLIPSSCREWDRIVER
COMBINATION SQUARE MUST BE TRUE
DRAW LIGHT EDGE MUST BE
LINE ON BOARD PERFECTLY STRAIGHT
ALONG
SHOULD BE NO GAP OR OVERLAP HERE WHEN
SQUARE IS FLIPPED OVER IN DOTTED POS|TION
If any parts are missing, do not attempt to assemble the
band saw, plug in the power cord, or turn the switch on
until the missing parts are obtained and installed cor-
rectly.
STRAIGHT EDGE OF
BOARD 3/4" TH1CK
I!
LJ
!
TABLE OF LOOSE PARTS
J
A Basic saw assembly .................. 1
B Owners Manual ...................... 1
C Saw Table .......................... 1
D Blade, Saw 1t4 ....................... 1
,=
QTY.
E Bag Assembly Part - #69132 Containing
the following parts:
Roller, Blade Thrust ................... 2
Switch, Key ......................... 1
Nut, Wing 1/4-20 ..................... I
Screw, Truss Hd. 1/420 x 1............ t
Washer 17/64 x 5/8 x 1/16 ............. 1
C
Insert, Table .......................... 1
Screw, Hex Hd, 5I! 6-18 x 3/4 .......... 2
External Lockwasher, 5/16 ............. 2
Wrench, Hex "L" 5!32 ................. 1
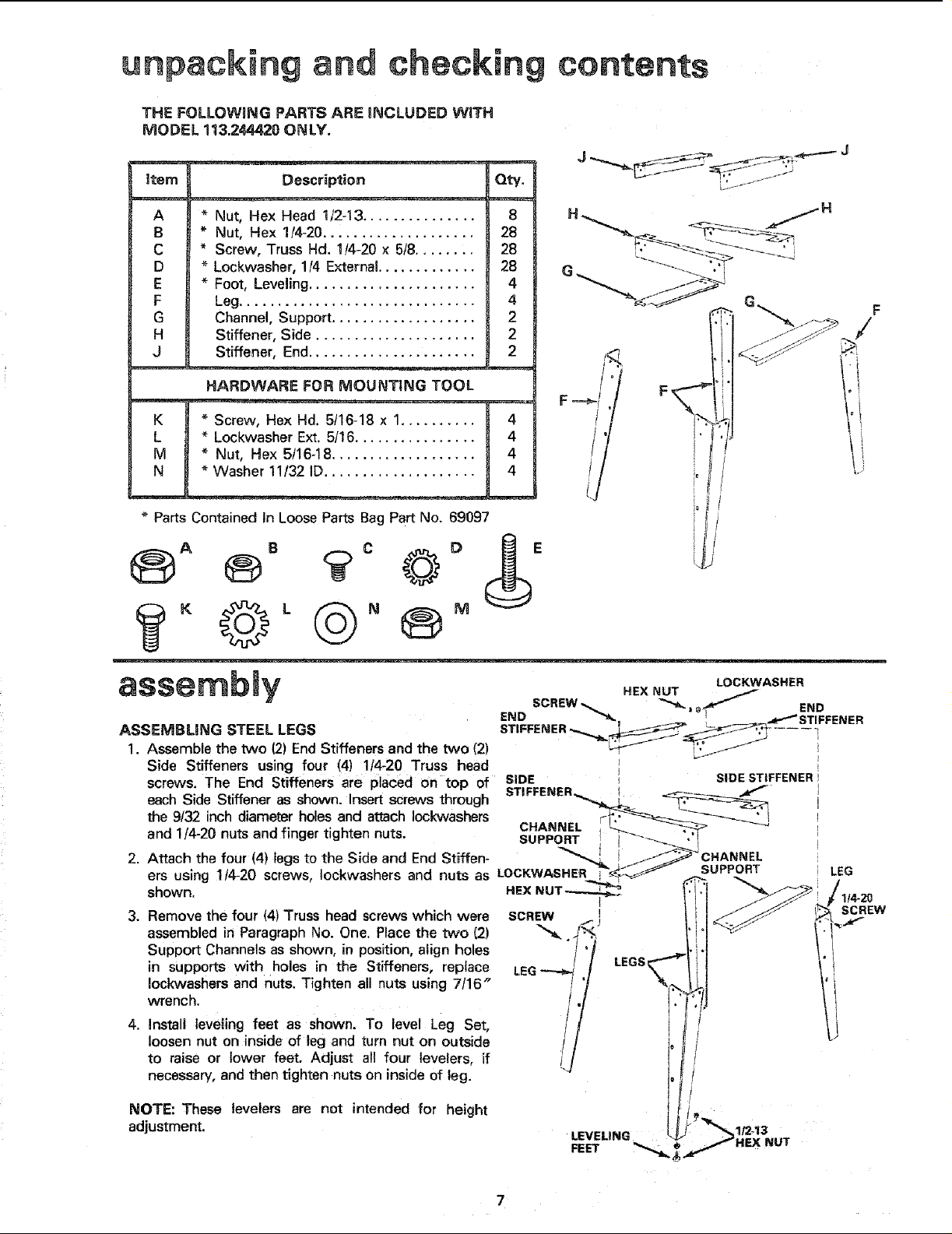
THE FOLLOWING PARTS ARE iNCLUDED WITH
MODEL 113.244420 ONLY.
_tem
Description
J _ _ _._---- J
QW.
A
B
C
D
E
F
G
H
J
Nut, Hex Head 112-t3 ............... 8
Nut, Hex 1/4-20 .................... 28
Screw, Truss Hd. 1/4-20 x 518........ 28
€$
Lockwasher, 1/4 External ............. 28
Fore, Levering ...................... 4
Leg............................... 4
Channel, Support ................... 2
Stiffener, Side ..................... 2
Stiffener, End ...................... 2
HARDWARE FOR MOUNTING TOOL
K
L
M
N
Parts Contained in Loose Parts Beg Part No. 69097
Screw, Hex Hd. 5/16-18 x 1.......... 4
* Lockwasher Ext. 5/16 ................ 4
Nut, Hex 5/16-18 ................... 4
Washer 11/32 ID.................... 4
F
/
assembly .EX.OT
ASSEMELi NG STEEL LEGS .......... "--.,.,__ ______...... _j -----
1. Assemble the two (2) End Stiffeners and the two (2) _ ___J
Side Stiffeners using four (4) 1t4-20 Truss head t
screws. The End Stiffeners are placed on top of SiDE _ SIDE STIFFENER!
each Side Stiffener as shown. Insert screws through STIFFENER_ _,__
the 9/32 inch diameter holes and attach Iockwashers CHA"NEL r'___'_-_._
and 114-20nuts and finger tighten nuts. SUPPOR:r" ', _"-'_---_ _
2. Attach the four (4) legs to the Side and End Stiffen- _[ i _/_CHANNEL
ers using 1t4-20 screws, Iockwashers and nuts as LOCKWASHER __'_-_ SUPPORT LEG
shown. HEX NUT_
3. Remove the four (4) Truss head screws which were SCREW ! SCREW
assembled in Paragraph No. One. Place the two (2) _,. !._..; "_
Support Channels as shown, in position, align holes "/ LEGS_
in supports with holes in the Stiffeners, replace LEG
Iockwashers and nuts. Tighten all nuts using 7/16"
wrench. !
4. Install teveling feet as shown. To level Leg Set,
loosen nut on inside of leg and turn nut on outside /
to raise or lower feet. Adjust all four levelers, if
necessary, and then tighten nuts on inside of leg.
NOTE: These levelers are not intended for height
adjustment.
SCREW%= _. _l END
l
/
LOCKWASHER
7
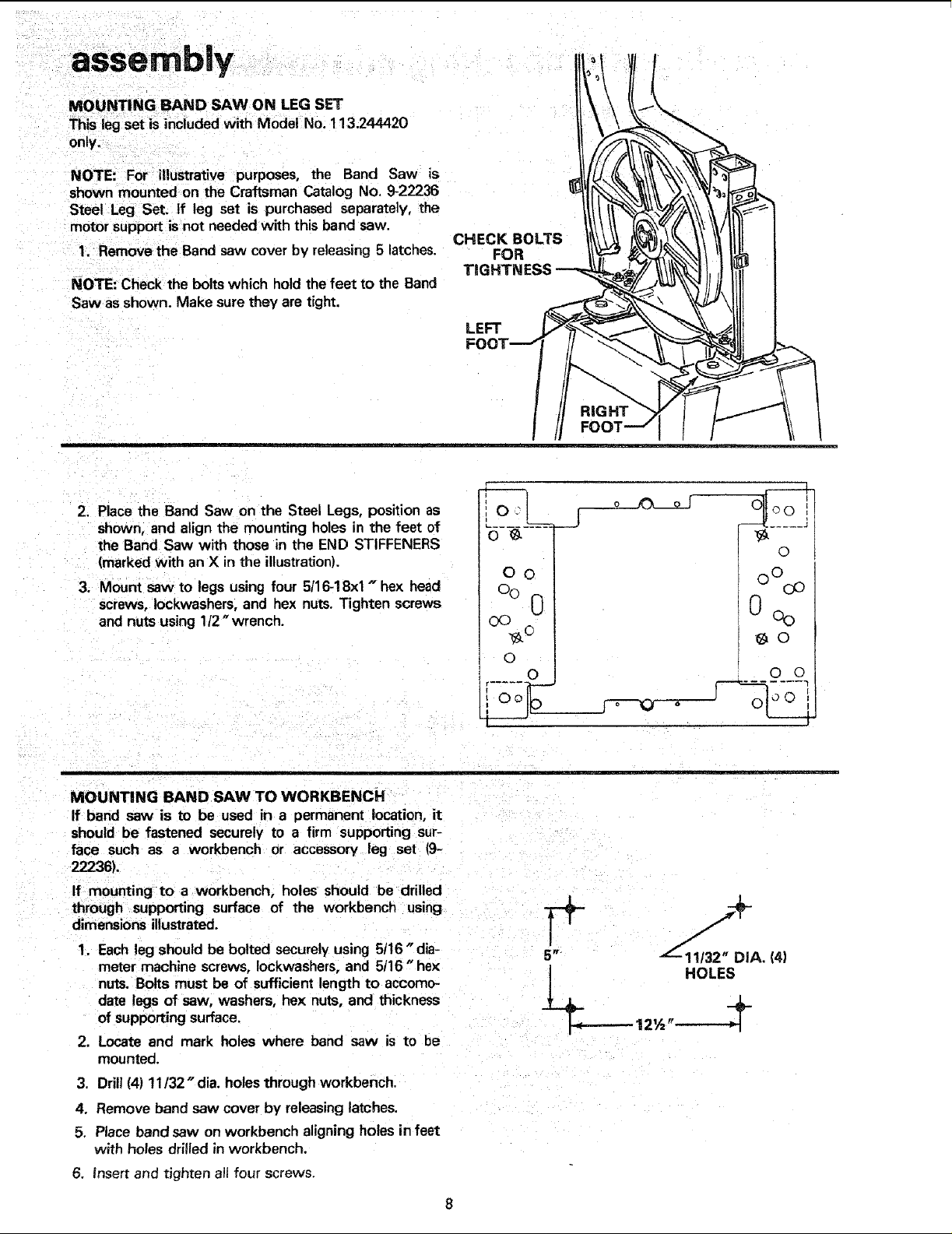
assembly
MOUNTING BAND SAW ON LEG SET
This leg set is includedwith Model No. 113.244420
only.
NOTE: For illustrative purposes, the Band Saw is
shown mounted on the Craftsman Catalog No. 9-22236
Steel Leg Set. If leg set is purchased separately, the
motor support is not needed with this band saw.
1. Remove the Band saw cover by releasing 5 latches.
NOTE: Check the bolts which hold the feet to the Band
Saw as shown. Make sure they are tight.
2. Place the Band Saw on the Steel Legs, position as
shown, and align the mounting holes in the feet of
the Band Saw with those in the END STIFFENERS
(marked with an X in the illustration).
3. Mount saw to legs using four 5/16-18xl u hex head
screws, Iockwashers, and hex nuts. Tighten screws
and nuts using 1/2 " wrench.
CHECK BOLTS
FOR
TIGHTr
LEFT
O
OO
©
O
©
© Ooo
_O
O ©
MOUNTING BAND SAW TO WORKBENCH
If band saw is to be used in a permanent location, it
should be fastened securely to a firm supporting sur-
face such as a workbench or accessory leg set (9-
22236).
If mounting to a workbench, holes should be drilled
through supporting surface of the workbench using
dimensionsillustrated.
1. Each leg should be bolted securelyusing 5/16 " dia-
meter machine screws, Iockwashers,and 5/16" hex
nuts.Bolts must be of sufficientlength to accomo-
date legs of saw, washers, hex nuts, and thickness
of supportingsurface.
2. Locate and mark holes where band saw is to be
mounted.
3. Drill (4) 11t32"dia. holesthrough workbench,
4. Remove band saw cover by releasinglatches.
5, Place bandsaw on workbench aligningholes in feet
with holes drilled in workbench.
6. Insert and tighten all four screws.
5" DIA, (4)
__ , HOLES
12½ _