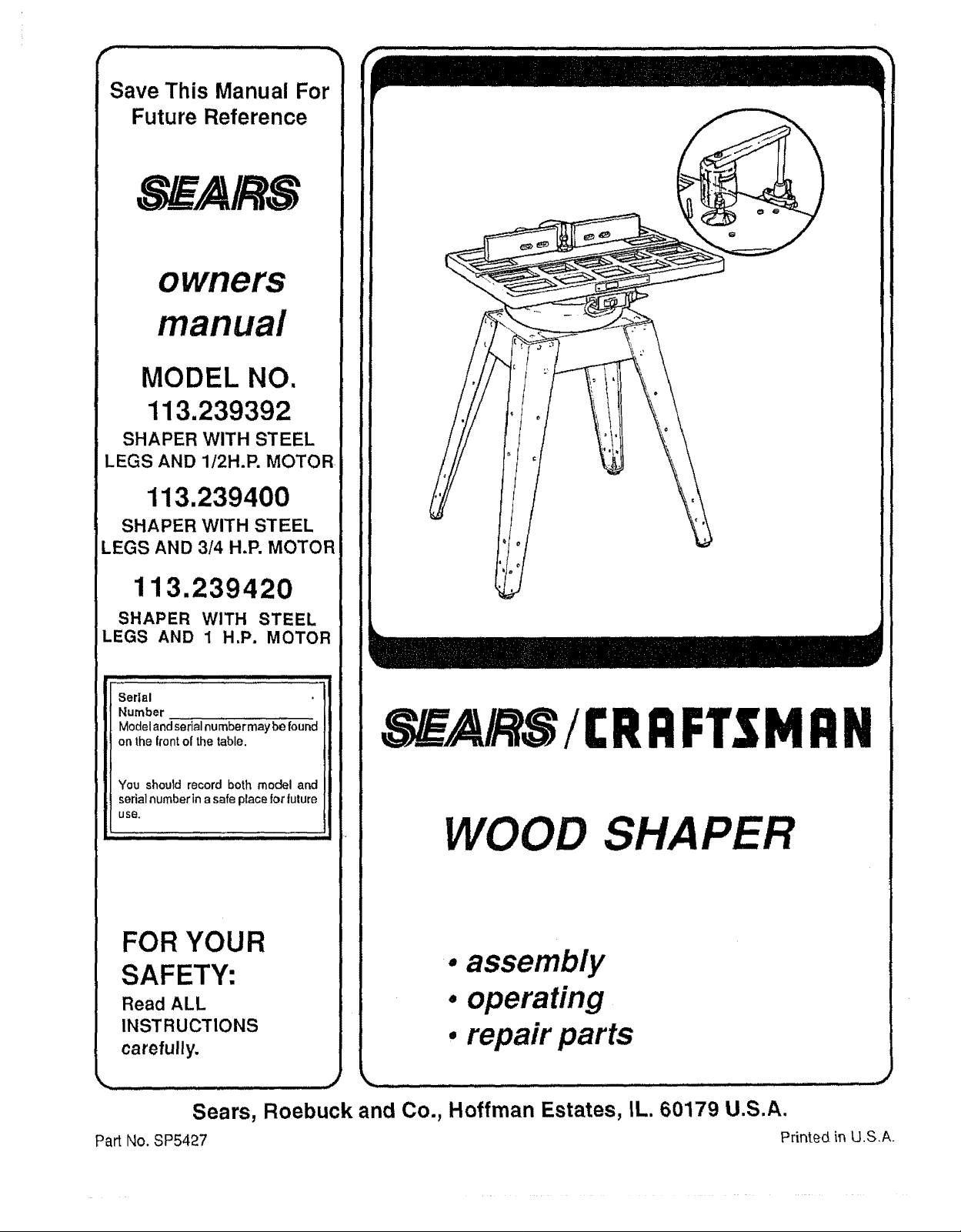
ILUUIII, I lllllm I,IllLILll,III IL
Save This Manual For
Future Reference
A/RS
owners
manual
MODEL NO.
113.239392
SHAPER WITH STEEL
LEGS AND I/2H.P. MOTOR
113.239400
SHAPER WITH STEEL
LEGS AND 3/4 H.P. MOTOR
113.239420
SHAPER WITH STEEL
LEGS AND 1 H,P. MOTOR
Serial
Number
Model and serial numbermaybe found
on the tront of the table.
You should record both model and
serial numberin a safe place for future
use,
FOR YOUR
SAFETY:
Read ALL
INSTRUCTIONS
carefully.
/I:RRFTSMRN
WOOD SHA
• assembly
• operating
, repair parts
Part No. SP5427
Sears, Roebuck and Co., Hoffman Estates, IL. 60179 U.S.A.
Printed in U.S,A.
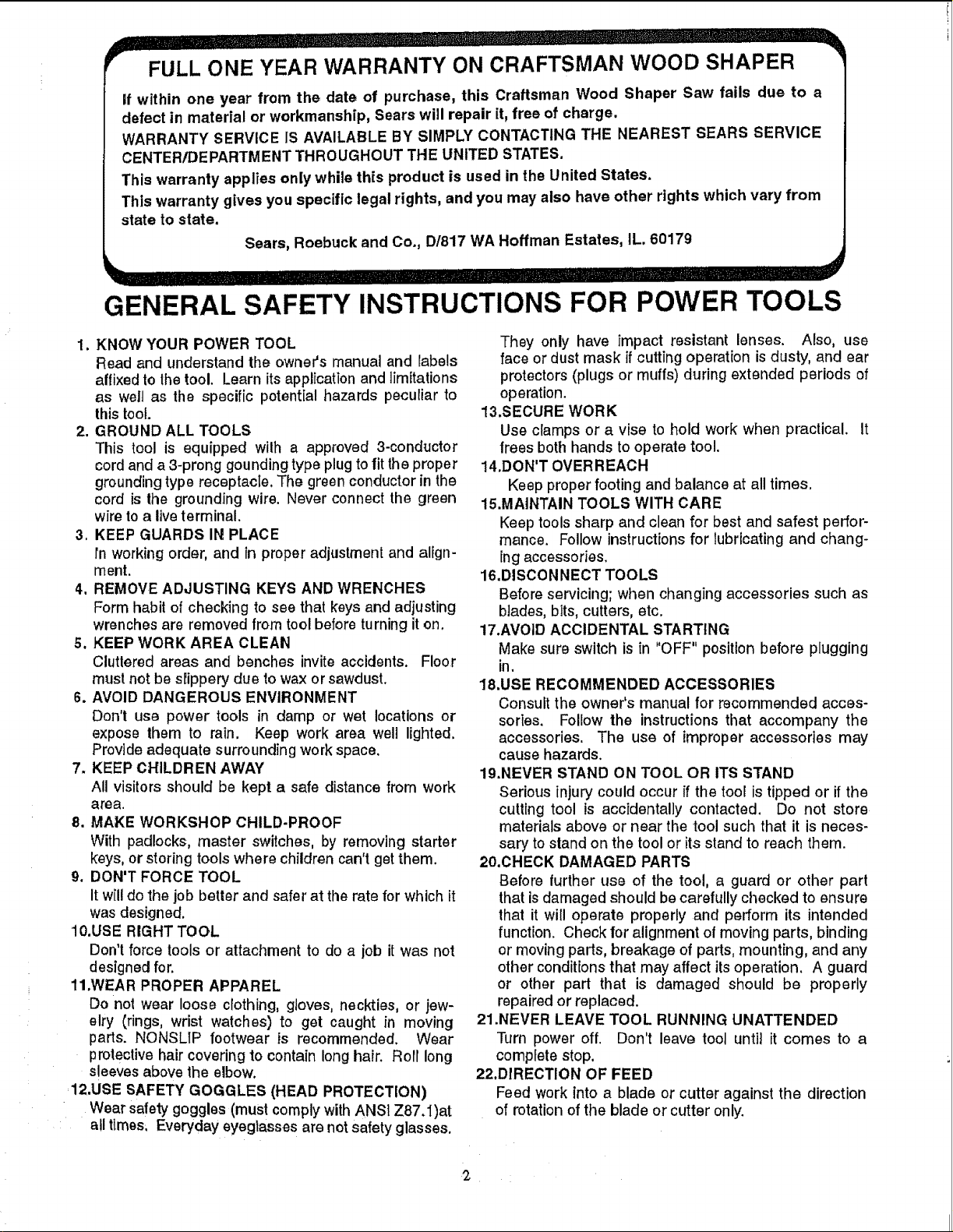
ii'_ ...... I ii I IFI
FULL ONE YEAR WARRANTY ON CRAFTSMAN WOOD SHAPER
If within one year from the date of purchase, this Craftsman Wood Shaper Saw fails due to a
defect in material or workmanship, Sears will repair it, free of charge.
WARRANTY SERVICE IS AVAILABLE BY SIMPLY CONTACTING THE NEAREST SEARS SERVICE
CENTER/DEPARTMENT THROUGHOUT THE UNITED STATES.
This warranty applies only while thEsproduct is used in the United States.
This warranty gives you specific legal rights, and you may also have other rights which vary from
state to state.
Sears, Roebuck and Co., D1817WA Hoffman Estates, IL. 60179
='- ............................... ....... IIMrl
GENERAL SAFETY INSTRUCTIONS FOR POWER TOOLS
.4
1. KNOW YOUR POWER TOOL
Read and understand the owner's manual and labels
affixed to lhe tool. Learn its application and limitations
as welt as the specific potential hazards peculiar to
this tool.
2. GROUND ALL TOOLS
This tool is equipped wilh a approved 3-conductor
cord and a 3-prong gounding type plug to fit the proper
grounding type receptacle. The green conductor in the
cord is the grounding wire. Never connect the green
wire to a live terminal.
3. KEEP GUARDS IN PLACE
rn working order, and in proper adjustment and align-
ment.
4. REMOVE ADJUSTING KEYS AND WRENCHES
Form habit of checking to see that keys and adjusting
wrenches are removed from tool before turning it on.
5. KEEP WORK AREA CLEAN
Ciutlered areas and benches invite accidents. Floor
must not be sfippery due to wax or sawdust.
6. AVOID DANGEROUS ENVIRONMENT
Don't use power tools in damp or wet locations or
expose them to rain. Keep work area well lighted.
Provide adequate surrounding work space.
7. KEEP CHILDREN AWAY
All visitors should be kept a safe distance from work
area.
8, MAKE WORKSHOP CHILD-PROOF
With padlocks, master switches, by removing starter
keys, or storing tools where children can't get them.
9. DON'T FORCE TOOL
It willdo the job better and safer at the rate for which it
was designed.
10.USE RIGHT TOOL
Don't force tools or attachment to do a job it was not
designed for.
11.WEAR PROPER APPAREL
Do not wear loose clothing, gJoves, neckties, or jew-
elry (rings, wrist watches) to get caught in moving
parts. NONSLIP footwear is recommended. Wear
protective hair covering to contain longhair. Floil long
sleeves above the elbow.
:12.USE SAFETY GOGGLES (HEAD PROTECTION)
Wear safety goggles (must comply with ANSI Z87.1)at
all times, Everyday eyeglasses are not safety glasses.
They only have impact resistant lenses. Also, use
face or dust mask if cutting operation is dusty, and ear
protectors (plugs or muffs) during extended periods of
operation.
13.SECURE WORK
Use clamps or a vise to hold work when practical. It
frees both hands to operate tool.
14,DON'T OVERREACH
Keep proper footing and balance at all times.
15.MAINTAIN TOOLS WITH CARE
Keep tools sharp and clean for best and safest perfor-
mance. Follow instructions for lubricating and chang-
ing accessories.
16.DISCONNECT TOOLS
Before servicing; when changing accessories such as
blades, bits, cutters, etc.
17.AVOtD ACCIDENTAL STARTING
Make sure switch is in "OFF" position before plugging
in.
18.USE RECOMMENDED ACCESSORIES
Consult the owner's manual for recommended acces-
sories. Follow the instructions that accompany the
accessories. The use of improper accessories may
cause hazards.
19.NEVER STAND ON TOOL OR ITS STAND
Serious injury could occur if the tool is tipped or if the
cutting tool is accidentally contacted. Do not store
materials above or near the tool such that it is neces-
sary to stand on the tool or its stand to reach them.
20.CHECK DAMAGED PARTS
Before further use of the tool, a guard or other part
that is damaged should be carefully checked to ensure
thai it will operate properly and perform its intended
function. Check for alignment of moving parts, binding
or moving parts, breakage of parts, mounting, and any
other conditions that may affect its operation. A guard
or other part that is damaged should be properly
repaired or replaced.
21.NEVER LEAVE TOOL RUNNING UNATTENDED
Turn power off. Don't leave tool until it comes to a
complete stop,
22.DIRECTION OF FEED
Feed work into a blade or cutter against the direction
of rotation of the blade or cutter only.
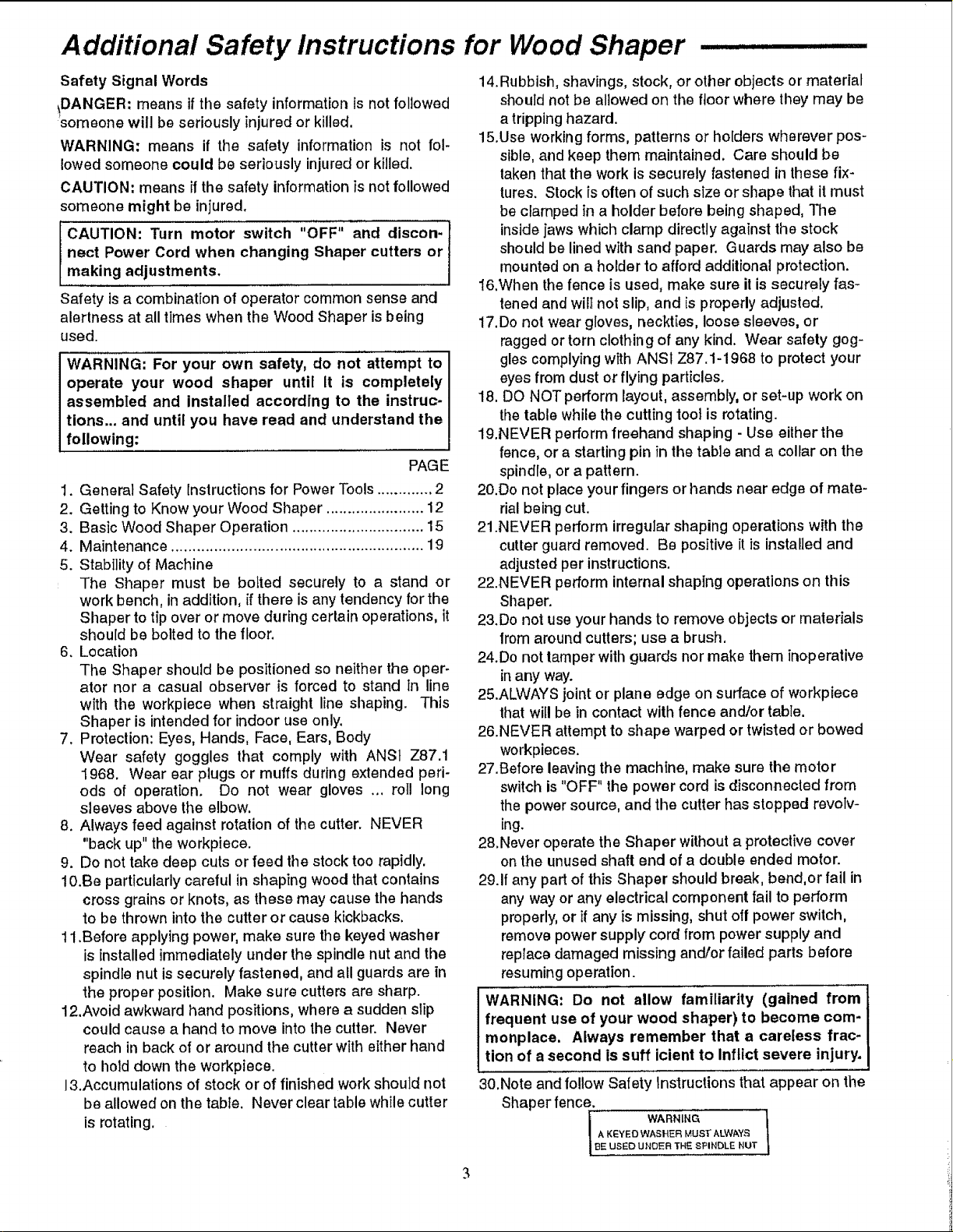
Additional Safety Instructions for Wood Shaper
Safety Signal Words
iDANGER: means if the safety information is not followed
someone will be seriously injured or killed.
WARNING: means if the safety information is not fol-
lowed someone could be seriously injured or killed.
CAUTION: means if the safety informationis not followed
someone might be injured.
CAUTION: Turn motor switch "OFF" and discon-
nect Power Cord when changing Shaper cutters or
making adjustments.
Safety is a combination of operator common sense and
alertness at all times when the Wood Shaper isbeing
used.
WARNING: For your own safety, do not attempt to
operate your wood shaper until It is completely
assembled and installed according to the instruc-
tions.., and until you have read and understand the
following:
PAGE
1. General Safety Instructionsfor Power Tools ............. 2
2. Getting to Know your Wood Shaper ....................... 12
3. Basic Wood Shaper Operation ............................... 15
4. Maintenance ........................................................... 19
5. Stability of Machine
The Shaper must be bolted securely to a stand or
work bench, in addition, if there is any tendency for the
Shaper to tip over or move during certain operations, it
should be bolted to the floor.
6. Location
The Shaper should be positioned so neither the oper-
ator nor a casual observer is forced to stand in line
with the workpiece when straight line shaping. This
Shaper is intended for indoor use only.
7. Protection: Eyes, Hands, Face, Ears, Body
Wear safety goggles that comply with ANSI Z87.1
1968. Wear ear plugs or muffs during extended peri-
ods of operation. Do not wear gloves ... roll long
sleeves above the elbow.
8. Always feed against rotation of the cutter. NEVER
"back up" the workpiece.
9. Do not take deep cuts or feed the stock too rapidly.
10.Be particularly careful in shaping wood that contains
cross grains or knots, as these may cause the hands
to be thrown into the cutter or cause kickbacks.
11.Before applying power, make sure the keyed washer
is installed immediately under the spindle nut and the
spindle nut is securely fastened, and all guards are in
the proper position. Make sure cutters are sharp.
12.Avoid awkward hand positions, where a sudden siip
could cause a hand to move intothe cutter. Never
reach in back of or around the cutter with either hand
to hold down the workpiece.
13.Accumulationsof stock or of finished work should not
be allowed on the table. Never clear table while cutter
is rotating.
14.Rubbish, shavings, stock, or other objects or material
should not be allowed on the floor where they may be
a tripping hazard.
15.Use working forms, patterns or ho[ders wherever pos-
sible, and keep them maintained, Care should be
taken that the work is securely fastened in these fix-
tures. Stock is often of such size or shape that it must
be clamped in a holder before being shaped, The
insidejaws which clamp directly against the stock
should be lined with sand paper. Guards may also be
mounted on a holder to afford additional protection.
16.When the fence is used, make sure il is securely fas-
tened and wilt not slip, and is properly adjusted.
17.Do not wear gloves, neckties, loose sleeves, or
ragged or torn clothing of any kind. Wear safety gog-
gles complying with ANSI Z87.1-1968 to protect your
eyes from dust o_'flying particles.
18. DO NOT perform layout, assembly, or set-up work on
the table while the cutting tool is rotating.
19.NEVER perform freehand shaping - Use either the
fence, or a starting pin in the table and a collar on the
spindle, or a pattern.
20.Oo not place your fingers or hands near edge of mate-
rial being cut.
21.NEVER perform irregular shaping operations with the
cutter guard removed. Be positive it is installed and
adjusted per instructions.
22.NEVER perform internal shaping operations on this
Shaper.
23.Do not use your hands to remove objects or materials
from around cutters; use a brush.
24.Do not tamper with guards nor make them inoperative
in any way.
25.ALWAYS joint or plane edge on surface of workpiece
that will be in contact with fence and/or table.
26.NEVER attempt to shape warped or twisted or bowed
workpieces.
27.Before leaving the machine, make sure the motor
switch is "OFF" the power cord is disconnected from
the power source, and the cutter has stopped revolv-
ing.
28.Never operate the Shaper without a protective cover
on the unused shaft end of a double ended motor.
29.1fany part of this Shaper should break, bend,or fail in
any way or any electrical component fail to perform
properly, or if any is missing, shut off power switch,
remove power supply cord from power supply and
replace damaged missing and/or failed parts before
resuming operation.
WARNING: Do not allow familiarity (gained from
frequent use of your wood shaper) to become com-
monplace. Always remember that a careless frac-
tion of a second is surf icient to Inflict severe injury.
30.Note and follow Safety instructions that appear on the
Shaper fence.
A KEYED WASHER MUST ALWAYS
I WARNING /
BE USED UNDER THE SPINDLE NUT
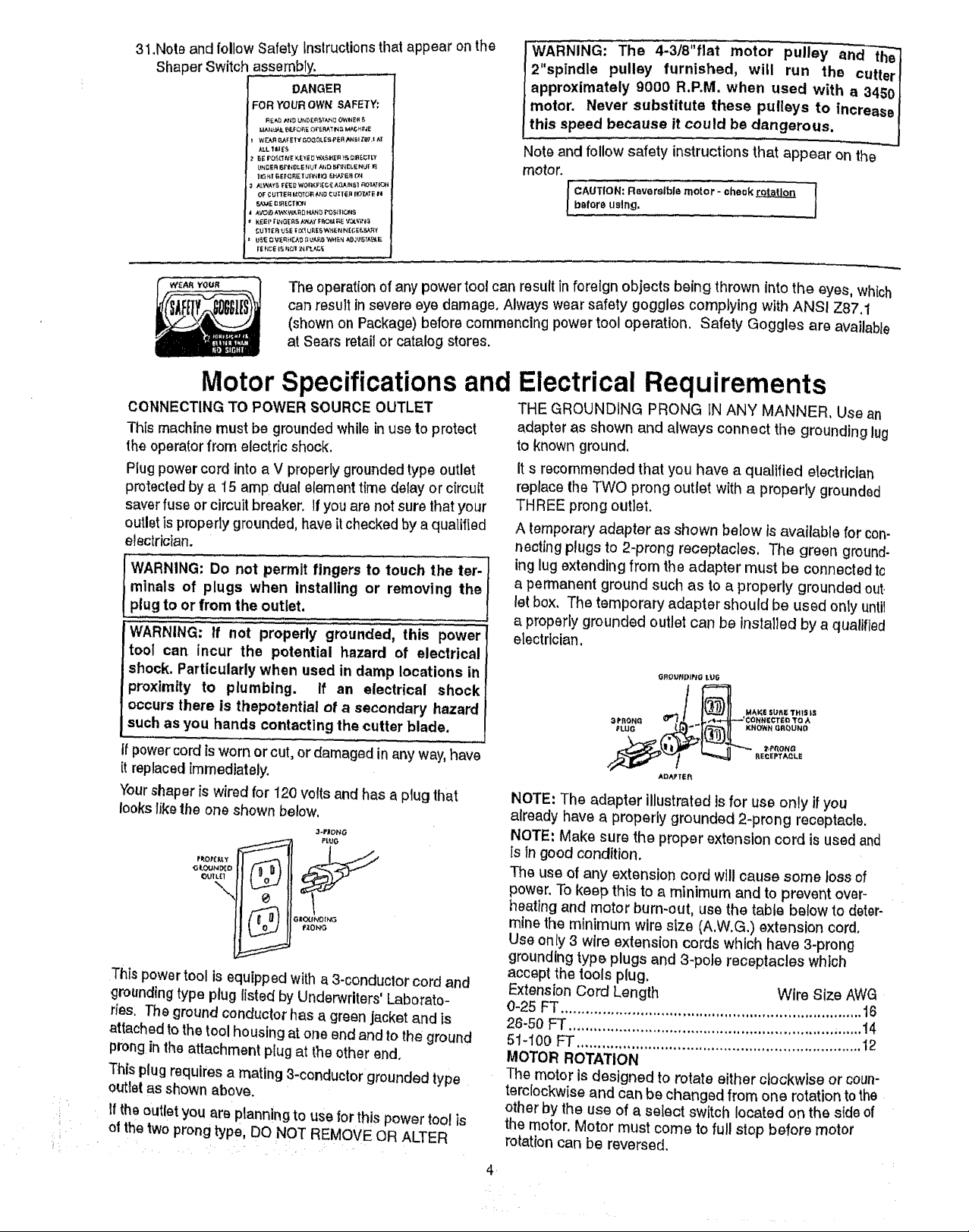
31.Note and follow Safety tnslructions that appear on the
Shaper Switch asse.mbly.'......
DANGER
-'OR YOUR OWK SAFETY:
READ ,t_tD LIN0 EFI_TM'I00_=_lE f4 _"
_VJ_L _3E_E _3PE_TFI_ _HI_JE
_E POSLTNEKE¥__WA_,Ht'FI_£CTLY
LINOE FI6rt_or-E pJUT _dD BPIPIIgLE N_]
T_l GEFGFIE T_llOi &I'+J_-P£F1121
OF ¢UFI'EI_ |.(r_TO;R,_g _O=T_+FIFIOTAtE El
F.d_ME__ EC_'IOt4
K_P F_GEES f_" FFICU RE '#_3+.VPI_
C U31£ _ 'JSE T _'_ Ur{E5 W_{E tt NE_E F-_f
U_ I_Vt_ _+f_AO13_-'_0_f_IEN AOJg_,TA_LE
The operation of anypower toolcan result inforelgn objects being thrown into the eyes, which
can result in severe eye damage, Always wear safety goggles comp_ying with ANSI Z87.1
(shown on Package) before commencing power tool operation. Safety Goggles are available
at Sears retail or catalog steres.
WARNING: The 4-3/8"flat motor pulley and th-_
2"spindle pulley furnished, will run the cutterl
approximately 9000 R.P.M. when used with a 34_0 t
motor. Never substitute these pulleys to increase l
this speed because it could be dangerous, j
Note and follow safety instructionsthat appear on the
motor.
|I-CAUTION:re+or+uslng.Reverslblemotor-cheok_ I
Motor Specifications and
CONNECTING TO POWER SOURCE OUTLET
Thismachine must be grounded 'while inuse to protect
the operator from electric shock,
Plug power cord into a V properly grounded type outlet
protected by a 15 amp dual element time delay or circuit
saver fuse or circuit breaker. If you are not sure that your
outletis properly grounded, have itchecked by a qualMed
electrician.
WARNING: Do not permit fingers to touch the ter-
minals of plugs when installing or removing the
plug to or from the outlet.
WARNING: If not properly grounded, this power
Electrical Requirements
THE GROUNDING PRONG iN ANY MANNER, Use an
adapter as shown and always connect the grounding lug
to known ground,
It s recommended that you have a qualified electrician
replace the TWO prong outlet with a properly grounded
THREE prong outlet,
A temporary adapter as shown below is available for con-
necting plugs to 2-prong receptacles. The green ground-
ing lug extending from the adapter must be connected tc
a permanent ground such as to a properly grounded out
let box, The temporary adapter should be used only until
proper_ygrounded outlet can be installed by a qualified
electrician.
tool can incur the potential hazard of electrical
shock. Particularly when used in damp locations in
proximity to plumbing. If an electrical shock
occurs there is thepotential of a secondary hazard
such as you hands contacting the cutter blade.
If power cord is worn orcut, or damaged in any way,have
It replaced immediately,
Yourshaper is wired for 120 volts and has a plug that
looks like the one shown below,
3J_ONO
NOTE: The adapter illustrated is for use only if you
already have a properly grounded 2-prong receptacle.
NOTE: Make sure the proper extension cord is used and
ADAPTER
is in good condition,
G_OUNtJ_D
OU1L_t
The use of any extension cord will cause some loss of
power. To keep this to a minimum and to prevent over-
heating and motor burn-out, use the table below to deter-
_ PLUO
P_OV?3
mine the minimum wire size (A,W,G,) extension cord,
Use only 3 wire extension cords which have 3-prong
grounding type plugs and 3-pole receptacles which
This power tool is equipped with a3-conductorcord and
grounding type plug listed by Underwriters' Labotate-
ties. fine ground conductorhas a green jacket and is
attached to the tool housing at one end and to the ground
prong in the attachment plug at the other end.
Tihisplug requires a mating 3'conductor grounded type
outlet as shown above.
i
i
If the outlet you are planning to use for this power tool is
ofthe two prong type, DO NOT REMOVE OR ALTER
accept the tools plug,
Extension Cord Length Wire Size AWG
0-25 FT ........................................................................ 16
28-50 FT ............................................................... .......14
51-100 FT .................................................................... 12
MOTOR ROTATION
The motor is designed to rotate either clockwise or coun-
terclockwise and can be changed from one rotation tothe
other by the use of a select switch located on the side of
the motor, Motor must come to full stop before motor
rotation can be reversed,
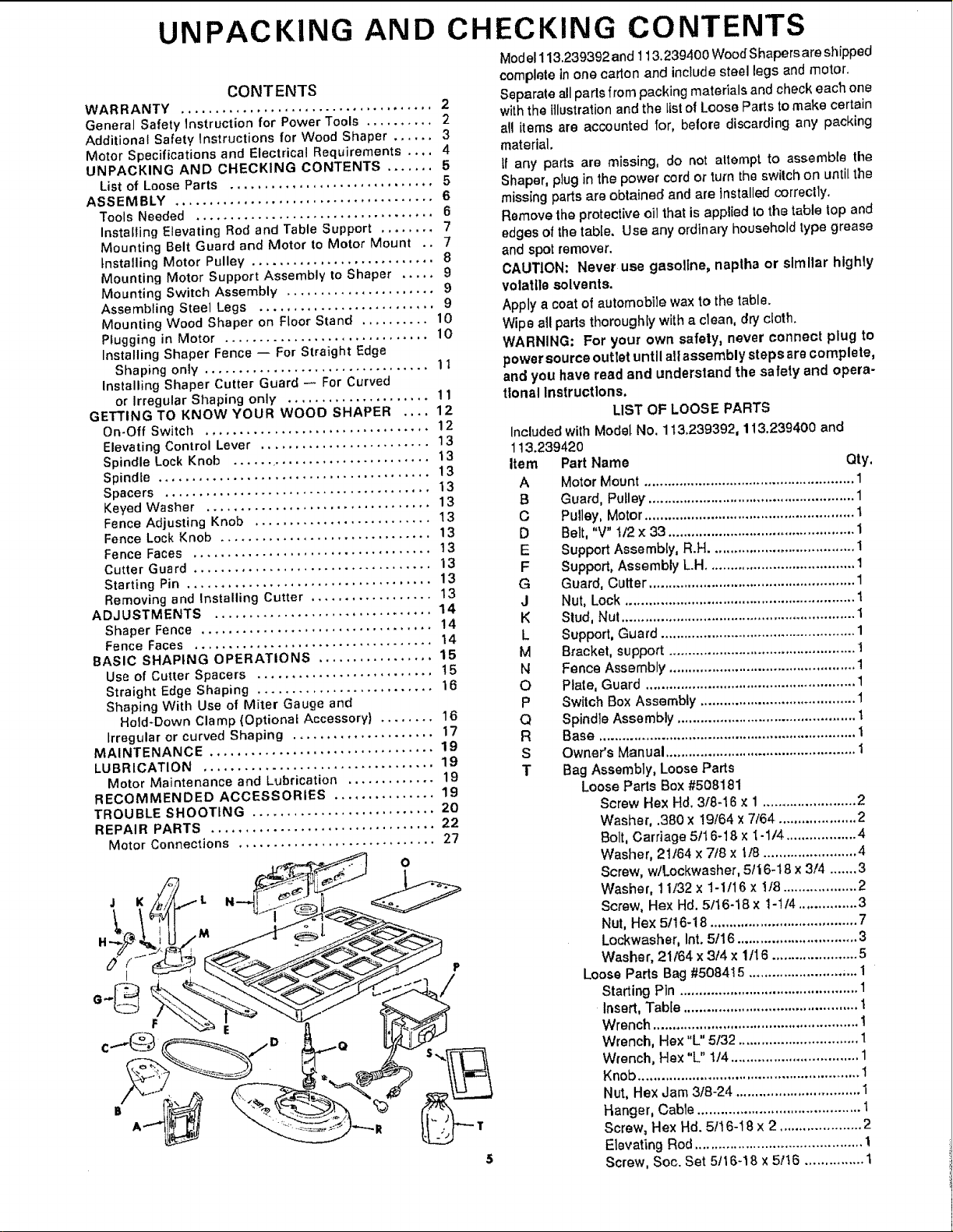
UNPACKING AND CHECKING CONTENTS
CONTENTS
WARRANTY ..................................... 2
General Safety Instruction for Power Tools .......... 2
Additional Safety Instructions for Wood Shaper ...... 3
Motor Specifications and Electrical Requirements .... 4
UNPACKING AND CHECKING CONTENTS ....... 5;
List of Loose Parts .............................. 5
ASSEMBLY ...................................... 6
Tools Needed ................................... 6
Installing Elevating Rod and Table Support ........ 7
Mounting Belt Guard and Motor to Motor Mount .. 7
_nstalling Motor Pulley ........................... 8
Mounting Motor Support Assembly to Shaper ..... 9
Mounting Switch Assembly ...................... 9
Assembling Steel Legs .......................... 9
Mounting Wood Shaper on Floor Stand .......... 10
Pfugging in Motor .............................. 10
Installing Shaper Fence -- For Straight Edge
Shaping only ................................. 11
Installing Shaper Cutter Guard -- For Curved
or Irregular Shaping only ..................... 11
GETTING TO KNOW YOUR WOOD SHAPER .... 12
On-Off Switch ................................. 12
Elevating Control Lever ......................... 13
Spindle Lock Knob .............................. 13
Spindle ........................................ 13
Spacers ....................................... 13
Keyed Washer ................................. 13
Fence Adjusting Knob .......................... 13
Fence Lock Knob ............................... 13
Fence Faces ................................... t 3
Cutter Guard ................................... 13
Starting Pin .................................... 13
Removing and Installing Cutter .................. 13
ADJUSTMENTS ................................ 14
Shaper Fence .................................. !4
Fence Faces ................................... 14
BASIC SHAPING OPERATIONS ................. 15
Use of Cutter Spacers .......................... 15
Straight Edge Shaping .......................... 16
Shaping With Use of Miter Gauge and
Hold-Down Clamp (Optional Accessory) ........ 16
Irregular or curved Shaping ..................... 17
MAINTENANCE ................................. 19
LUBRICATION .................................. 19
Motor Maintenance and Lubrication ............. 19
RECOMMENDED ACCESSORIES ............... 19
TROUBLE SHOOTING ........................... 20
REPAIR PARTS ................................. 22
Motor Connections ............................. 27
Model 113.239392and t 13.239400 Wood Shapers are shipped
complete in one carton and include steel legs and motor.
Separate all parts from packing materials and check each one
with the illustration and the list of Loose Parts to make certain
all items are accounted for, before discarding any packing
material.
_fany parts are missing, do not attempt to assembte the
Shaper, plug in the power cord or turn the swilch on until t_qe
missing parts are obtained and are installed correclly,
Remove the protective oil that is applied to the table lop and
edges of the table. Use any ordinary household type grease
and spot remover.
CAUTION: Never use gasoline, naplha or similar highly
volatile solvents.
Apply a coat of automobile wax to the table.
Wipe all partsthoroughly with a clean, dry cloth.
WARNING: For your own safety, never connect plug to
power source outlet until allassembly steps are comple re,
and you have read and understand the safety and opera-
tional Instructions.
LIST OF LOOSE PARTS
Included with Model No. 113.239392, 113.239400 and
113.239420
Item Part Name Qty,
A Motor Mount ...................................................... 1
B Guard, Pulley ..................................................... 1
O Pulley, Motor ...................................................... 1
D Belt, "V" 112x 33 ................................................ 1
E Support Assembly, R.H ..................................... 1
F Support, Assembly L.H ....................................... 1
G Guard, Cutter ..................................................... 1
J Nut, Lock ........................................................... 1
K Stud, Nut ............................................................ 1
L Support, Guard .................................................. 1
M Bracket, support ................................................ 1
N Fence Assembly ................................................ 1
O Plate, Guard ...................................................... 1
P Switch Box Assembly ........................................ 1
Q Spindle Assembly .............................................. t
R Base .................................................................. 1
S Owner's Manual ................................................. 1
T Bag Assembly, Loose Parts
Loose Parts Box #508181
Screw Hex Hd. 3!8-16 x 1 ........................ 2
Washer, .380 x !9/64 x 7/64 .................... 2
Bolt, Carriage 5tl 6-18 x 1-1/4 .................. 4
Washer, 2t/64 x 7t8 x 1t8 ........................ 4
Screw, w/Lockwasher, 5t16-18 x 3/4 ....... 3
Washer, 11/32 x 1-1/16 x 1t8 ................... 2
Screw, Hex Hd. 5/16-18 x 1-1/4 ............... 3
Nut, Hex 5116-!8 ...................................... 7
Lockwasher, Int. 5/16 ............................... 3
Washa r, 21f64 x 314 x 1/16 ...................... 5
Loose Parts Bag #508415 ........................ _...1
Starting Pin .............................................. 1
Insert, Table ............................................. 1
Wrench ..................................................... I
Wrench, He× "L" 5/32 ............................... 1
Wrench, He× "L" 1/4 ................................. 1
Knob ......................................................... 1
Nut, Hex Jam 318-24 ................................ 1
P,anger, Cable .......................................... 1
Screw, Hex Hd. 5f16-18 x 2 ..................... 2
Elevating Rod ........................................... !
Screw, Soc. Set 5t16-18 x 5/t6 ............... 1
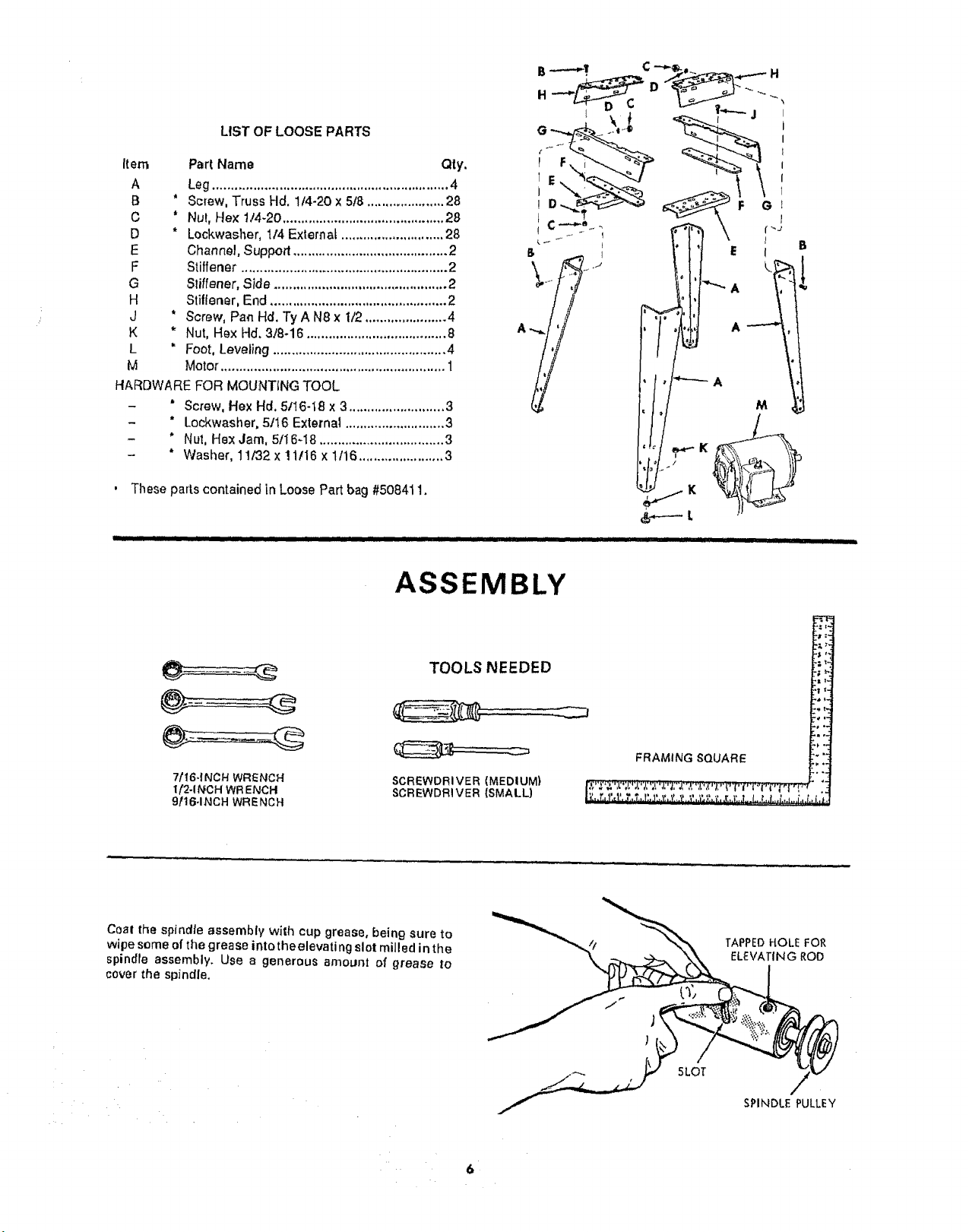
LIST OF LOOSE PARTS
Item Part Name Qty.
A Leg................................................................4
B ' Screw, Truss Hd. 1t4-20 x 5t8 ..................... 28
C * Nut, Hex 1./4-20............................................ 28
D * Lockwasher, 1/4 External ............................ 28
E Channel, Support .......................................... 2
F Stiffener ........................................................ 2
G Stiffener, Side ............................................... 2
H Stitloner, End ................................................ 2
J * Screw, Pan Hd. Ty A N8 x I/2 ....................... 4
K * Nut, Hex Hd. 3/8-16 ...................................... 8
L " Foot, Leveling ............................................... 4
M Motor ............................................................. 1
HARDWARE FOR MOUNTING TOOL
- " Screw, Hex Hd, 5116-18 x 3 .......................... 3
- * Lockwasher, 5,/t6 External ........................... 3
- * Nut, Hex Jam, 5/16_18 .................................. 3
- " Washe{, 11/32 x 11/16 x 1/16 ....................... 3
, These parts contained in Loose Part bag #508411.
,,,,,
ASSEMBLY
TOOLS NEEDED !!i
7/'16-_NCH WRSNCH
1/2-INCH WRENCH
9t16-1NCH WRENCH
Coal the spindte assembly with cup grease, being sure to
wipe same of the grease intothe elevating slot milled in the
spindle assembly. Use a generous amount of grease to
cover the spindle.
t,=.
TAPPEO HOLE FOP-,
ELEVATING ROD
SLOT
/
SPINDLEPULLEY
6
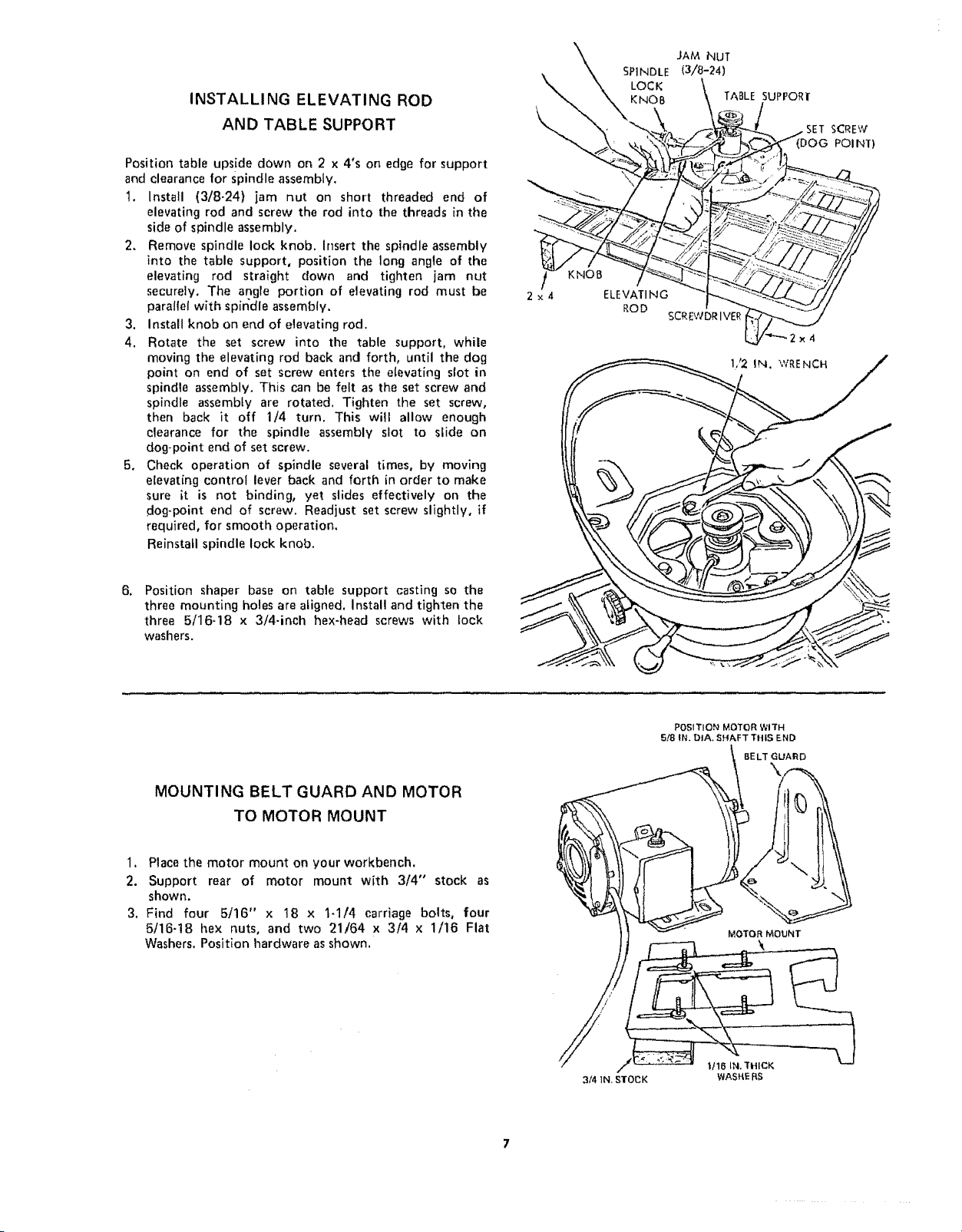
INSTALLING ELEVATING ROD
AND TABLE SUPPORT
Position table upside down on 2 x 4's on edge for support
and clearance for Spindle assembly.
1. Install (3/8-24) jam nut on short threaded end of
elevating rod and screw the rod into the threads in the
side of spindle assembly.
2, Remove spindle lock knob, Insert the spindle assembly
into the table support, position the long angle of the
elevating rod straight down and tighten jam nut
securely, The angle portion of elevating rod must be
parallel with spindle assembly.
3. Install knob on end of elevating rod,
4. Rotate the set screw into the table support, while
moving the elevating rod back and forth, until the dog
point on end of set screw enters the elevating slot in
spindle assembly, This can be felt as the set screw and
spindle assembly are rotated. Tighten the set screw,
then back it off 1/4 turn. This witl allow enough
clearance for the spindle assembly slot to slide on
dog-point end of set screw.
5, Check operation of spindle several times, by moving
elevating control lever back and forth in order to make
sure it is not binding, yet slides effectively on the
dog-point end of screw. Readjust set screw slightly, if
required, for smooth operation.
Reinstall spindle lock knob.
2x4
JAM NUT
SPINDLE
LOCK
KNOB
KNOB
/
ELEVATI NG
ROD
(3/8-24)
TABLE SUPPORT
SCRE_M
(DOG POINT)
£CREWDR IVER
"_2 × 4
J
6,
Position shaper base on table support casting so the
three mounting holes are aligned. Install and tighten the
three 5/16-18 x 3/4-inch hex-head screws with lock
washers.
MOUNTING BELT GUARD AND MOTOR
TO MOTOR MOUNT
1. Place the motor mount on your workbench.
2. Support rear of motor mount with 3/4" stock as
shown,
3. Find four 5/16" x 18 x 1-1/4 carriage bolts, four
5/16-18 hex nuts, and two 21/64 x 3/4 x 1/16 Flat
Washers, Position hardware as shown,
POSITION MOTOR WITH
5/8 IN. DIA, SHAFT THIS END
BE LT GUARD
MOTOR MOUNT
3_IN. STOCK
1/16 IN. THICK
WASHE RS
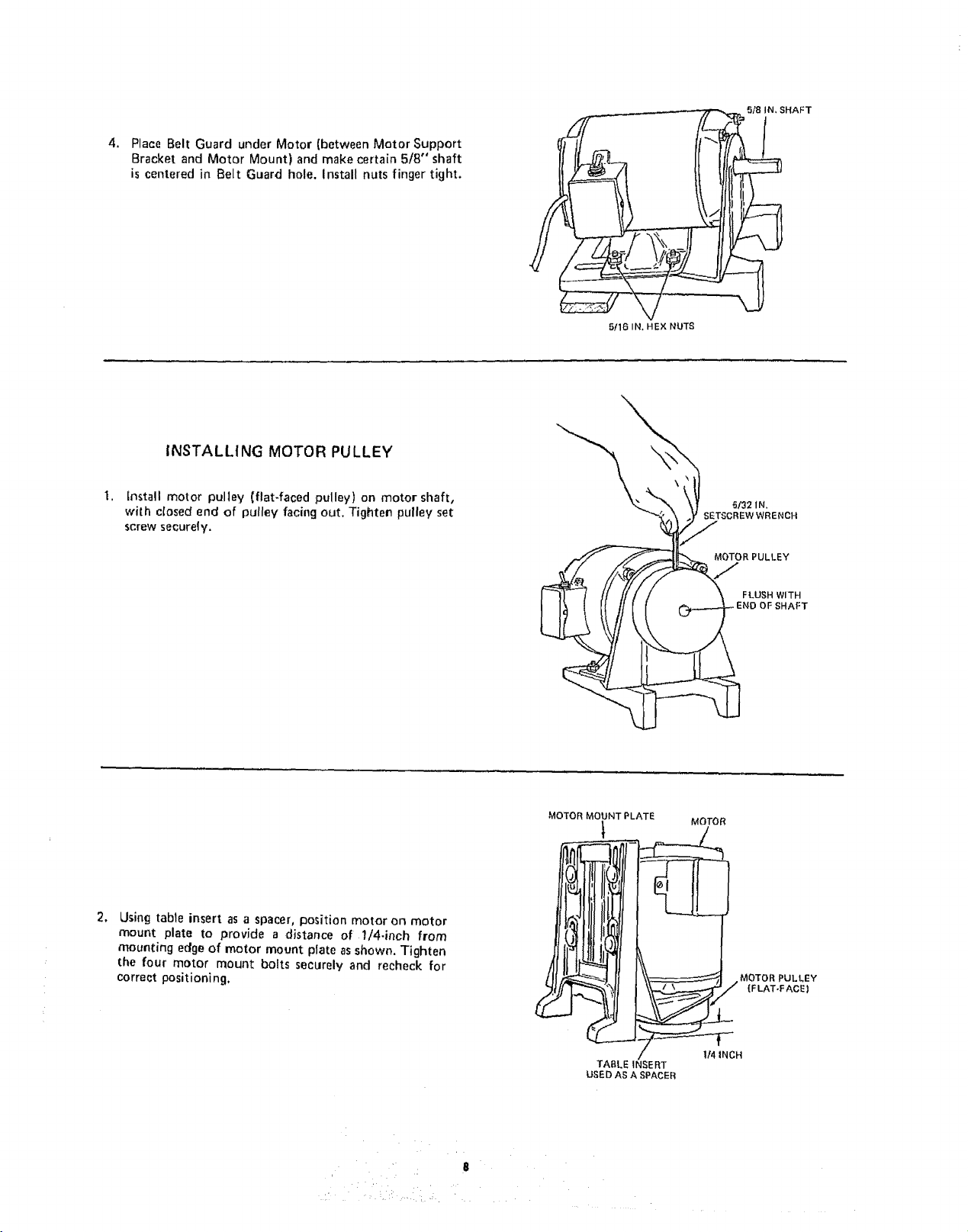
4. Place Belt Guard under Motor [between Motor Support
Bracket and Motor Mount) and make certain 5/8" shaft
is centered in Belt Guard hole. Install nuts finger tight.
INSTALLING MOTOR PULLEY
5!16 IN. HEX NUTS
install motor pulley (flat-faced pulley) on motor shaft,
with closed end of pulley facing out, Tighten pulley set
screw securely.
2,
Using table insert as a spacer,position motor on motor
mount plate to provide a distance of 1/4-inch from
mounting edge of motor mount plate as shown. Tighten
the four motor mount bolts securely and recheck for
correct positioning,
SETSCREW WRENCH
MOTOR MOUNT PLATE MOTOR
5_21N,
MOTOR PULLEY
J
FLUSH WITH
SHAFT
_IN'-CH
TABLE IN_ERT
USED AS A SPACER
•8

MOUNTING MOTOR SUPPORT ASSEMBLY
TO SHAPER
1.
Place V-belt on motor pulley and attach motor mount
plate to shaper base with two bolts 13/8-18 x t-inch}
and washers, Leave bolts finger tight.
2, Roll the belt onto spindle pulley, pull motor mount
plate toward end of base until bett is tight enough to
prevent slipping and tighten the two bolts, Each bolt
should be in approximately the same position in the
base slots.
3. Position elevating rod in approximate mid position and
turn spindle pulley by hand several times to see that the
belt rides in the approximate mid position of motor
pulley. If not, recheck assembly. The belt should
change positions on motor pulley as the lever position is
changed (while the spindle pulley is rotated by hand}.
MOUNTING SWITCH ASSEMBLY
MOTOR MOUNT PLATE
ELEVATI NG
ROD
SPINDLE
PU LL EY
MOTOR
BASE
I.
Attach the switch assembly to the underside of the
Shaper table using the two screws and lockwashers
packed with the switch.
ASSEMBLING STEEL LEGS
1. Assemble the two (2) End Stiffeners and the two (2)
Side Stiffeners using four (4) 1/4-20 Truss head screws.
The End Stiffeners are placed on top of each Side
Stiffener as shown. Insert screws through the 9/32 inch
diameter holes and finger tighten 1/4-20 nuts.
2. Attach the four (4) legs to the side and End Stiffener
using 1/4-20 screws, lockwashers and nuts as shown.
3. Remove the four (4) Truss head screws whict_ were
assembled in Paragraph No, One, Place the two (2)
Support Channels as shown, in position, align holes in
supports with holes in the side Stiffeners, replace
Iockwashers and nuts. Tighten all nuts using 7/16"
wrench.
/
%
I
4, The two (2) Stiffeners, (F} are fastened to the top side
of each side stiffener using N8 x t/2 self-threading
screws. The guard plate is mounted as shown using same
screws,
5. Install leveling feet as shown. To level Leg Set, loosen
nut on inside of leg and turn nut on outside to raise or
lower feet. Adjust all four levelers, if necessary, and then
tighten nuts on inside of leg.
NOTE: These levelers are not intended for I_eight
adjust ment.