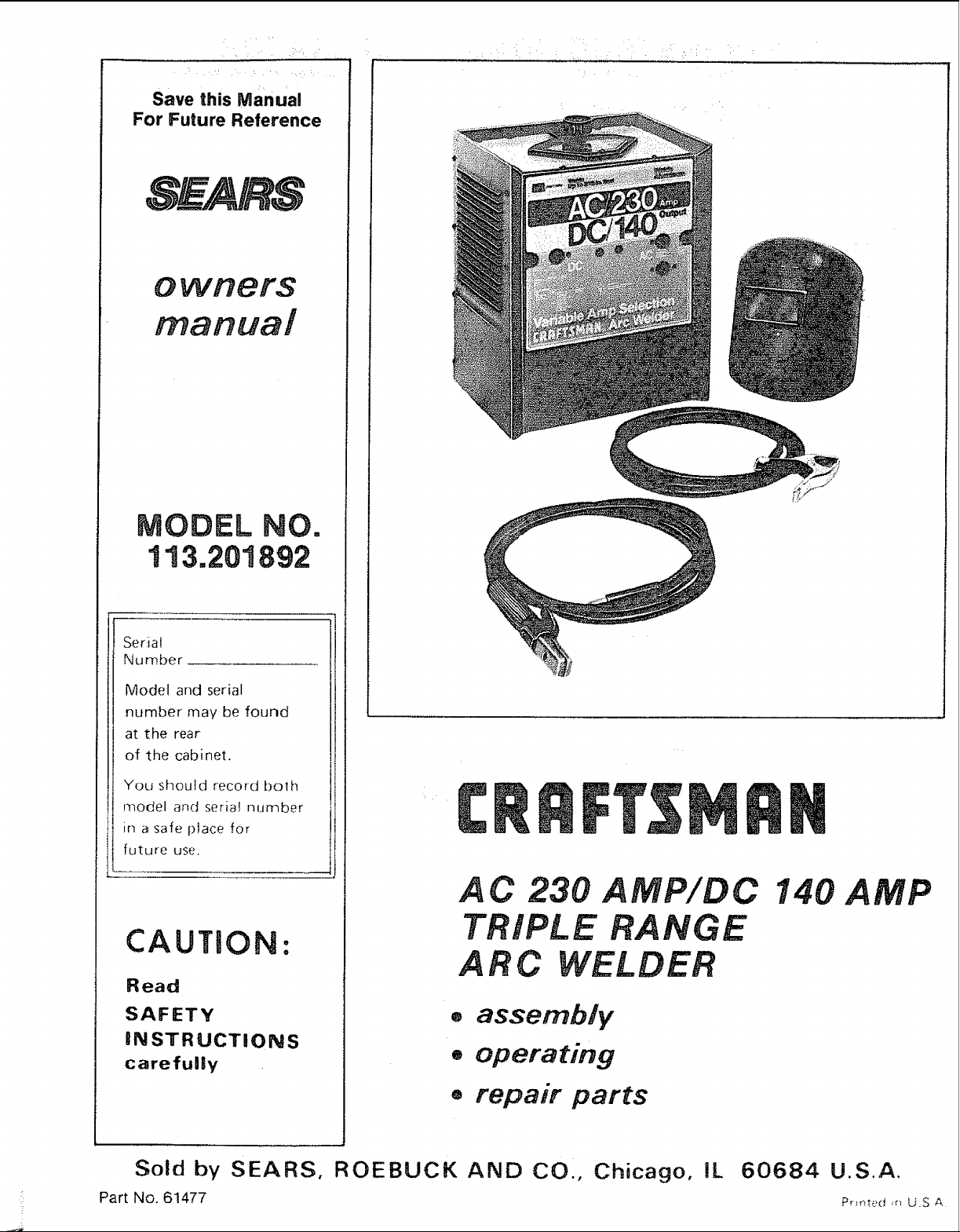
Save this Manual
For Future Reference
S_ AJRS
MODEL NO.
113.201892
Serial
Number
Model and serial
number may be found
at the rear
of the cabinet.
You should record both
model and seriaI number
in a safe place for
future use.
CAUTION:
Read
SAFETY
iNSTRUCTIONS
carefully
A C 230 AMP/DC
TRIPLE RANGE
ARC WELDER
® assembly
• operating
140 AMP
= repair parts
Sold by
Part No. 61477
,i
SEARS,
ROEBUCK AND COl,
Chicago, iL
60684 U.S.A.
P_nted _rl USA
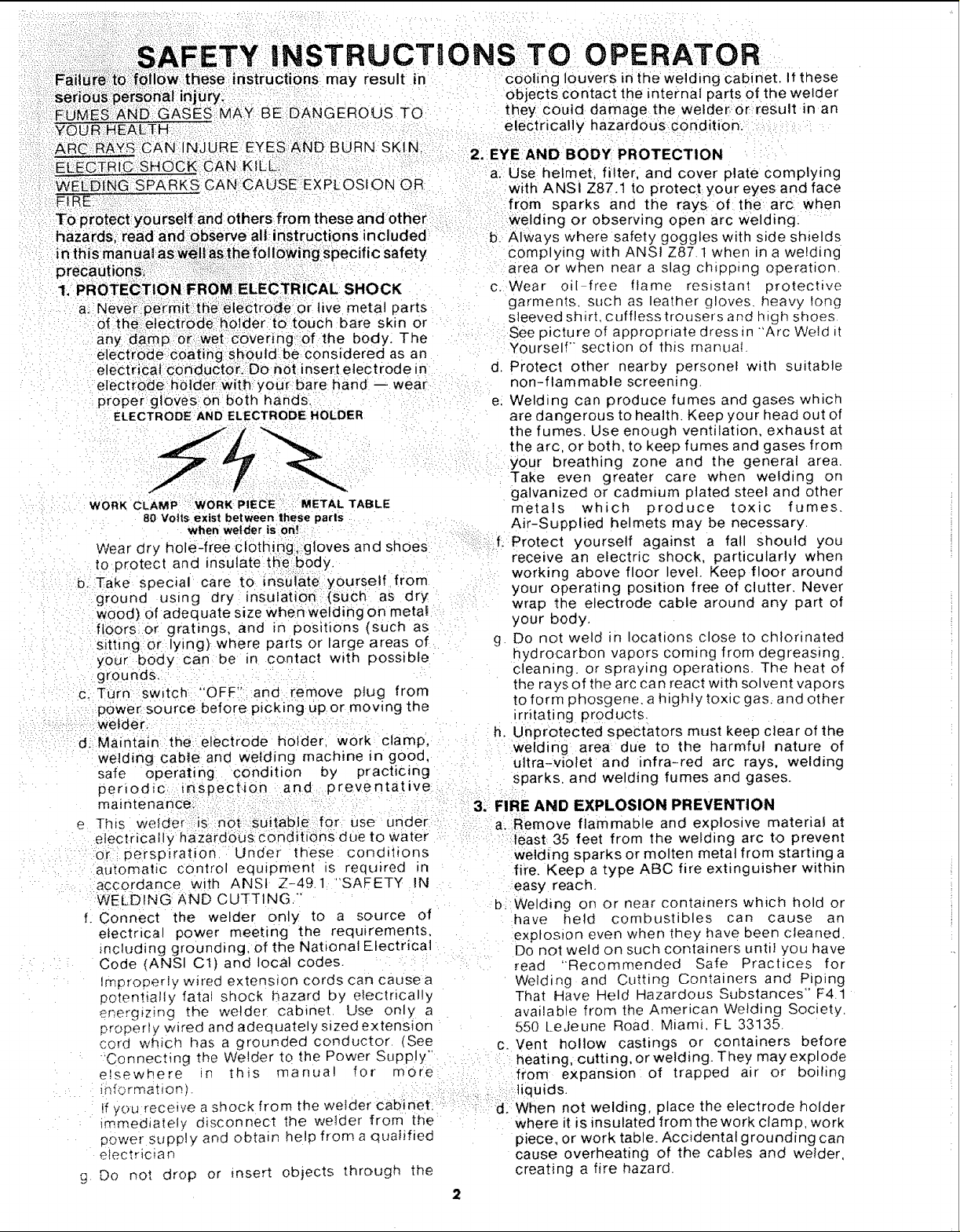
.... -:%. :.
': SAFET INST.UCT
: i Fail_re:i!t_:;:!f0i 0w these ::instructions may result in
sedods personat!njury_ :. :::i;i::: :
FIJME'S ND G A S ES :iMAY BEl :D AN G E ROU S TO
_O'U R :NEAETH::: ::: ,' :i:'i
::iN:_iIjR E:::EYE S :A:ND :BElRN S KIN.:
SH O : ::::i::::
wEL:B:tNG SPARKS cAN: CAOSE_:E:XP_OSfON O R:
MRE:": :: ::
To pt0i_ectlyourself: and others fforn these and othei _
hazard:s; read and 0bServe all instructions included:
in tfiis rnanl_at asW_i!as!:the f01ibwing specific safety
precautionS:_ !: i :::::::!: !
1: SHOCK
ai: or live metal parts
0fi:the :electrode:holder to touch bare skin Or
any ii:lara p::0(: wet id6ve ring:of the body. The
electri6dec0atiiig Should be €0nsidered as an
electrlCat COndu(_toiL Do not:insert electrode in
electrode holder with your:bare hand wear
proper gloves on both hands:.
ELECTRODE AND ELECTRODE HOLDER
WORK CLAMP :WORK PIECE METAL TABLE
to protect and insulate tfie bodY.
b.-Fake special care to insuiate "yourself from
c: Turn sw_tch "OFF" and remove plug from
::- wefdeL
d: Maintain the:electrode holder work clamp,
electricaiiy hazardoi]S:c0nd t _ns due to water least 35 feet from the welding arc t,o prevent
f_ Connect the welder only to a source of
g Do not drop or insert objects through the
80 Volts exist between these paris
when welder is 0n!
Wear dry hole-free ctothing:,::gtoves and shoes
ground using dry insulation {such as dry_
wood) ol adequate size when welding on meta_
floors:or gratings, and in positions (such as
sitting 0r lying ) where parts or large areas of
y0ur:body can be in contact with possible
grounds.
power source before picking upor moving the
wetdin9 cable and welding machine in good,
safe operating condition by practicing
periodic inSpect.ion and preventative
maintenance; ......... 3. FIRE AND EXPLOSION PREVENTION
This 0se under .... a Remove flammable and explosive material at
or perspiration Under these conditions
automahc control equipment _s required in
accordance with ANSI Z-491 "SAFETY IN
WELDING AND CUTTING "
electrical power meeting the requirements.
including grounding, of the National Electrical
Code (ANSI C1) and local codes.
Improper!y wired extensfon cords can cause a
potentially fatal shock hazard by electrically
energ z ng the welder cabinet Use only a
proper!y wired and adequately sized extension
cord which has a grounded conductor (See
'Connecting the Welder to the Power Supply
elsewhere in this manual for more
information}
f you recewe a shock from the welder cabinetl
_mmediately disconnect the we_der from the
[_ower supply and obtain help from a qualified
electrician
IONS:TO: OPERATOR
cooling louvers in the welding cabinet. If these
objects contact the internal parts of the welder
they couid damage the welder or result in an
electrically hazardous condition.
2. EYE AND BODY PROTECTION
a. Use helmet filter, and cover plate complying
with ANSI Z87.1 to protect your eyes and face
from sparks and the rays of the arc when
Welding or observing open arc welding.
b_ Always where safety goggles with side shields
complying with ANSI Z87.1 when in a welding
area or when near a slag chipping operation
c. Wear oil free flame resistant protechve
garments, such as leather gloves, heavy long
sleeved shirt cufflesstrousers and h pgh shoes
See picture of appropriate dress=n "'Arc Weld _t
YOurself" section of this manual
d. Protect other nearby personel with suitable
non-flammable screening.
e. Welding can produce fumes and gases which
are dangerous to health. Keep your head out of
the fumes. Use enough ventilation, exhaust at
the arc. or both. to keep fumes and gases from
your breathing zone and the general area.
Take even greater care when welding on
galvanized or cadmium plated steel and other
metals which produce toxic fumes.
Air-Supplied helmets may be necessary.
" f. Protect yourself against a fall should you
receive an electric shock, particularly when
working above floor level. Keep floor around
your operating position free of clutter. Never
wrap the electrode cable around any part of
your body.
g Do not weld in locations close to chlorinated
hydrocarbon vapors coming from degreasmg.
cleaning, or spraying operations. The heat of
the rays of the arc can react with solvent vapors
to form phosgene, a highly toxic gas. and other
irritating products.
h. Unprotected spectators must keep clear of the
welding area due to the harmful nature of
ultra-violet and infra-red arc rays, welding
sparks, and welding fumes and gases.
welding sparks or molten metal from starting a
fire. Keep a type ABC fire extinguisher within
easy reach.
b: Welding on or near containers which hold or
have held combustibles can cause an
exDtos_on even when they have been cleaned.
Do not weld on such containers until you have
read "Recommended Safe Practices for
Welding and Cutting Containers and Pping
That Have Held Hazardous Substances" F4.1
available from the American Welding Society,
550 LeJeune Road Miami. FL 33135.
c. Vent hollow castings or containers before
heating, cutting, or welding. They may explode
from expansion of trapped air or boiling
liquids.
d. When not welding, place the electrode holder
where it is insulated from thework clamp work
piece, or work table. Accidental grounding can
cause overheating of the cables and welder,
creating a fire hazard.
2
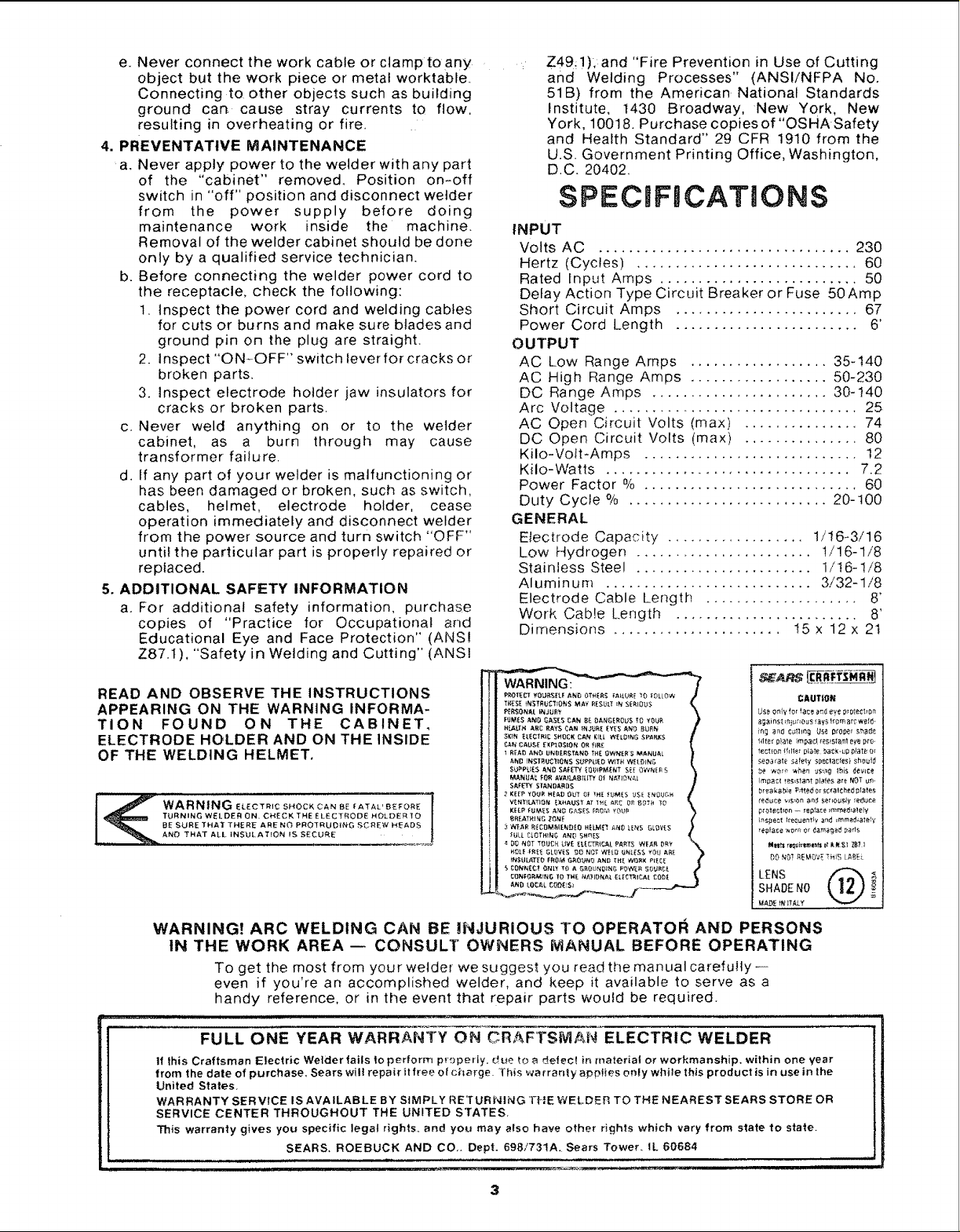
e.Neverconnecttheworkcableorclamptoany
objectbuttheworkpieceormetalworktable_
Connectingto otherobjectssuchasbuilding
ground can cause stray currentsto flow,
resultingin overheatingor fire.
4. PREVENTATIVE MAINTENANCE
'a. Never apply power to the welder with any part
of the "cabinet" removed. Position on-off
switch in "off" position and disconnect welder
from the power supply before doing
maintenance work inside the machine.
Removal of the welder cabinet should be done
only by a qualified service technician.
b. Before connecting the welder power cord to
the receptacle, check the following:
1. Inspect the power cord and welding cables
for cuts or burns and make sure blades and
ground pin on the plug are straighL
2. Inspect "ON-OFF" switch Iever for cracks or
broken parts.
3. inspect electrode holder jaw insulators for
cracks or broken parts.
c. Never weld anything on or to the welder
cabinet, as a burn through may cause
transformer failu re.
d. If any part of your welder is malfunctioning or
has been damaged or broken, such as switch,
cables, helmet, electrode holder, cease
operation immediately and disconnect welder
from the power source and turn switch "OFF"
until the particular part is properly repaired or
replaced.
5. ADDITIONAL SAFETY INFORMATION
a. For additional safety information, purchase
copies of "Practice for Occupational and
Educational Eye and Face Protection" (ANS!
Z87.I), "Safety in Welding and Cutting" (ANSI
Z49_!);_and "Fire Prevention in Use of Cutting
and Welding Processes" (ANSI/NFPA No.
51B) from the American National Standards
Institute, t430 Broadway, New York, New
York, 10018. Purchase copies of "OSHA Safety
and Health Standard" 29 CFR 1910 from the
U.S. Government Printing Office, Washington,
D.C. 20402.
SPECmFgCATIONS
INPUT
Volts AC ................................. 230
Hertz (Cycles) ............................. 60
Rated Input Amps .......................... 50
Delay Action Type Circuit Breaker or Fuse 50Amp
Short Circuit Amps ........................ 67
Power Cord Length ........................ 6'
OUTPUT
AC Low Range Amps .................. 35-140
AC High Range Amps .................. 50-230
DC Range Amps ....................... 30-140
Arc Voltage ................................ 25
AC Open Circuit Volts (max) ............... 74
DC Open Circuit Volts (max) ............... 80
Kilo-Volt-Amps ............................ t2
Kilo-Watts ................................ 7.2
Power Factor % ............................ 60
Duty Cycle % .......................... 20-100
GENERAL
E_ectrode Capacity .................. 1/!6_3/16
Low Hydrogen ....................... !/!6-1/8
Stainless Steel ....................... 1/!6-1/8
Aluminum ........................... 3/32-1/8
Electrode Cable Length .................... 8'
Work Cable Length ........................ 8'
Dimensions ...................... t5 x 12 x 2t
READ AND OBSERVE THE INSTRUCTIONS
APPEARING ON THE WARNING INFORMA-
TION FOUND ON THE CABINET,
ELECTRODE HOLDER AND ON THE INSIDE
OF THE WELDING HELMET,
TURNING WELDER ON. CHECK THE ELEC]ROOE HOLDER TO
I ..,_ WARNING E_ECTR,CSHOCKCANBEfATAl'BEfOREI
BE SURE I'HA_ THERE ARE NO PROTRUDING ,SCREW H_:ADS
ANO THAT ALL INSULATION IS SiECURE
WARNING! ARC WELDING CAN BE iNJURIOUS TO OPERATOI_ AND PERSONS
IN THE WORK AREA _ CONSULT OWNERS MANUAL BEFORE OPERATING
To get the most from your welder we suggest you read the manual carefully --
even if you're an accomplished welder, and keep it available to serve as a
handy reference, or in the event that repair parts would be required.
FULL ONE YEAR WARRANTY ON CRAFTSMAN ELECTRIC WELDER
If this Craftsman Electric Welder fails to perform properly, due to a delecI in material or workmanship, within one year
from the date of purchase, Sears will repair it free o{ charge. this warranly applies only while this product is in use in the
United States
WARRANTY SERVICE IS AVAILABLE BY SIMPLY RE[URNING THE WELDER TO THE NEAREST SEARS STORE OR
SERVICE CENTER THROUGHOUT THE UNITED STATES.
This warranty gives you specific legal rights, and you may also have other rights which vary from state to state.
SEARS. ROEBUCK AND CO,. Dept. 698/731A. Sears Tower. IL 60684
CAUTIg_
U_ 0rdy for!a_ a_d eye p_D_e_b0n
a,_ams_ _dun0u_ _y_ _0m ar_ we_d-
h1_erp!ale Impac__e_stantey_ p_9-
tect_o_!hll_ p_a_ ba_k-up p!atR o_
Separate _a!e_y _p_la_es_ should
Impact Tes_sIant plple$ _ t_0T u_'_-
'I
br_akPbi_ P_'t$_0rsc_'alchedpla_e_
_-r_lechon-- ;_pface_mme_a_I¥
_s_ect _ouen_v and _mmed_a_e_v
I
SHADEN0
LENS @ "_
MADE f# _TALY
3
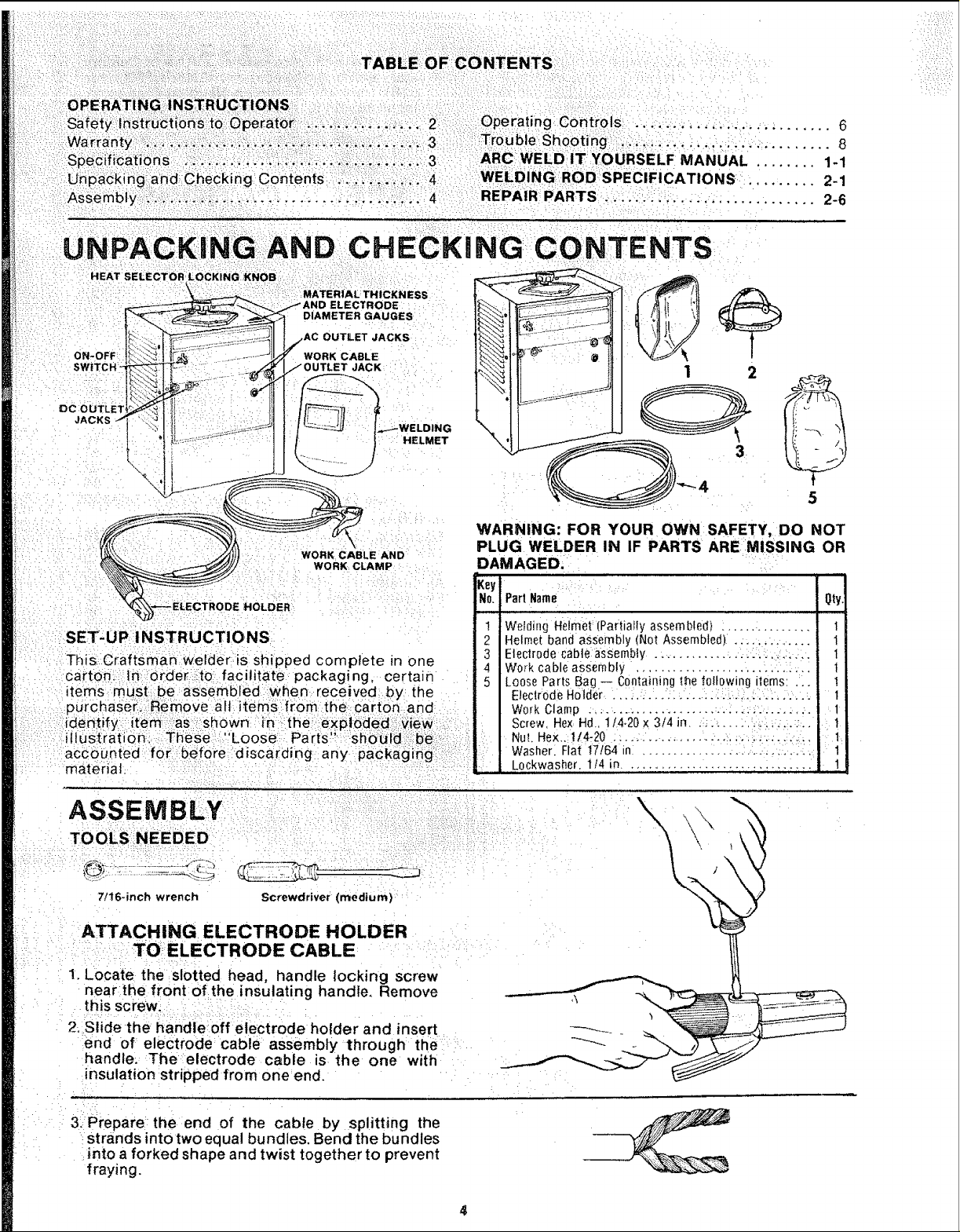
-TABLE OF CONTENTS
:i-....... ,,:. ::2 Operating: Coriti;o s: .,. _............... 6
Warrantv Troube:Sh0oting:i:i.:::.: : 8
..... ......... 2-1
'::i_:::::. ,...:.......... ::.i i:::i !:::. 4 REPAIR PARTS :... ::.:i:i i, ..... ..... 2-6
AND CHECKING CONTENTS
ELECTRODE
DIAMETER GAUGES
OUTLET JACKS
ON-OFF
DO OUTLET4
WORK CABLE
;K
WELDING
HELMET
/
/
WORK CABLE AND
WORK CLAM P
SET-UP INSTRUCTIONS
This Craftsman welder.is shipped complete in one
carton: in :order:;_to facilitate packaging, certain
itemslmust:i be assembled when received by the
purchaSei;:2BemoVe afl items.from the carton and .
ident fy item : as :;shOwn in::,:the! e:,x,ptOded::!iview _
iilUSt:ration: These ::"Loose i Parts" :sho:ul:d i:_!:be _-_:
accounted for before discarding: any packag rig: ....
material.
ASSEMBLY
TOOLS NEEDED
7/16-inch wrench
ATTACHING ELECTRODE HOLDER
TO ELECTRODE CABLE
1. Locate the slotted head, handle locking screw
near the front of the insulating handle. Remove
this screw.
Z Slide the handleoff electrode holder and insert
end of electrode cable assembly through the
handle: The electrode cable is the one with
insulation stripped from one end.
Screwdriver (medium)
WARNING: FOR YOUR OWN SAFETY, DO NOT
PLUG WELDER IN IF PARTS ARE MISSING OR
DAMAGED.
Key_ .
N0.
PartName Qty
1
Welding HElmet:(Partially assembled) 1
2
Helmetband assembly (Not Assembled) .. .... ....... 1
3
Electrode cable assembly .............. .::: ..... :.... 1
4
Work cableassembly ,.................... .,.,:.., t
5
Loose Parts Bag -- Coetainingt;qefollowing items: ... 1
,,, = ._
ElectrodeHolder ..... . .... : ...... :...:, 1
Work Clamp ........ .............. ..:..:....- .... . 1
Screw Hex Hd. 1/4-20x 3/4in..:;.....:,:,._,...:.. !
NuL Hex. !14-20 ::,..... ....... .-..::,.,,i..... ....
Washer: Flat 17164in............ :. .... ...:..,...., _ 1
L0ckwasher, 1t4 in......................... !
/
3. Prepare=the end of the cable by splitting the
strands into two equal bundles. Bend the bundles
into a forked shape and twist together to prevent
fraying.
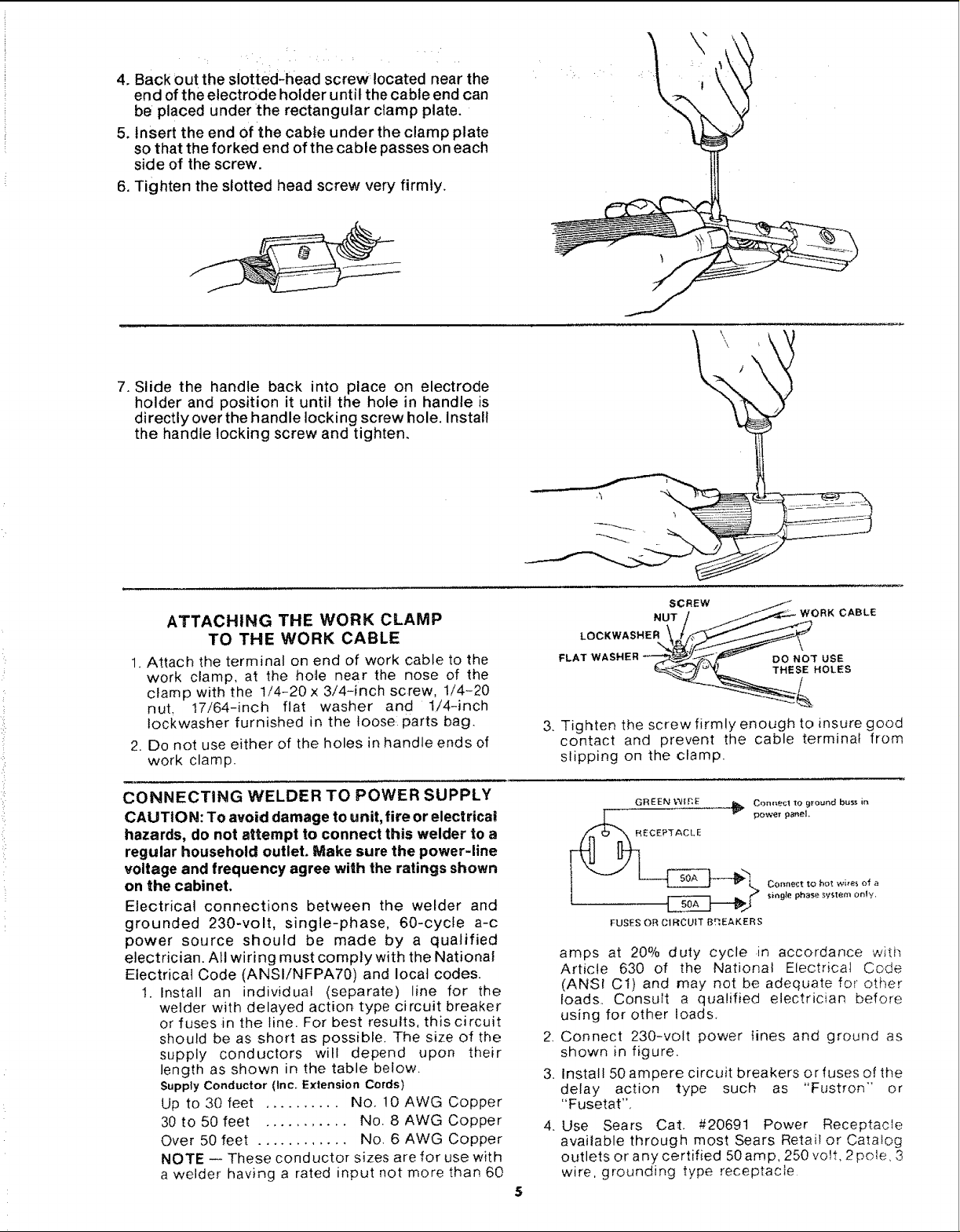
4. Back out the slotted-head screwtocated near the
end of the electrode holder until the cable end can
be placed under the rectangular clamp plate.
5. Insert the end of the cable under the clamp plate
so that the forked end of the cable passes on each
side of the screw.
6. Tighten the slotted head screw very firmly.
7. Slide the handle back into place on electrode
holder and position it until the hole in handle is
directly over the handle locking screw hole. Install
the handle locking screw and tighten.
ATTACHING THE WORK CLAMP
TO THE WORK CABLE
1. Attach the terminal on end of work cable to the
work clamp, at the ho_e near the nose of the
clamp with the 1/4-20 x 3/4-inch screw, 1/4-20
nut, 17/64-inch flat washer and 1/4-inch
tockwasher furnished in the loose: parts bag.
2. Do not use either of the holes in handle ends of
work clamp.
CONNECTING WELDER TO POWER SUPPLY
CAUTION: To avoid damage to unit, fire or electrical
hazards, do not attempt to connect this welder to a
regular household outlet. Make sure the power-line
voltage and frequency agree with the ratings shown
on the cabinet.
Electrical connections between the welder and
grounded 230-volt, single-phase, 60-cycfe a-c
power source should be made by a qualified
electrician. All wiring must comply with the National
Electrical Code (ANSl/NFPA70) and local codes.
1. Install an individual (separate) line for the
welder with delayed action_ type circuit breaker
or fuses in the line. For best results, this circuit
should be as short as possible. The size of the
supply conductors wilt depend upon their
length as shown in the table below.
Supply Conductor (Inc. Extension Cords)
Up to 30 feet .......... No. !0 AWG Copper
30 to 50 feet ........... No. 8 AWG Copper
Over 50 feet ............ No. 6 AWG Copper
NOTE -- These conductor sizes are for use with
a welder having a rated input not more than 60
SCREW
3. Tighten the screw firmly enough to insure good
contact and prevent the cable terminal from
slipping on the clamp.
GREEN W{RE
ECEPTACLE
FUSESOR C{F{CUtT BnEAKERS
Con_ecl Io g_ound buss in
power panel.
CoP_nect !:o hot ',vires of a
$ingte phase system only,
amps at 20% duty cycle in accordance with
Article 630 of the National Electrical Code
(ANSI Ct) and may not be adequate for other
loads. Consult a qualified electrician before
using for other loads.
,
Connect 230-volt power lines and ground as
shown in figure.
3.
Install 50 ampere circuit breakers or fuses of the
delay action type such as "Fustron" or
"Fusetat",
4.
Use Sears Cat. #20691 Power Receptacle
available through most Sears Retail or Cata}og
outlets or any certified 50 amp, 250 volt. 2 pole, 3
wire, grounding type receptacle.
5
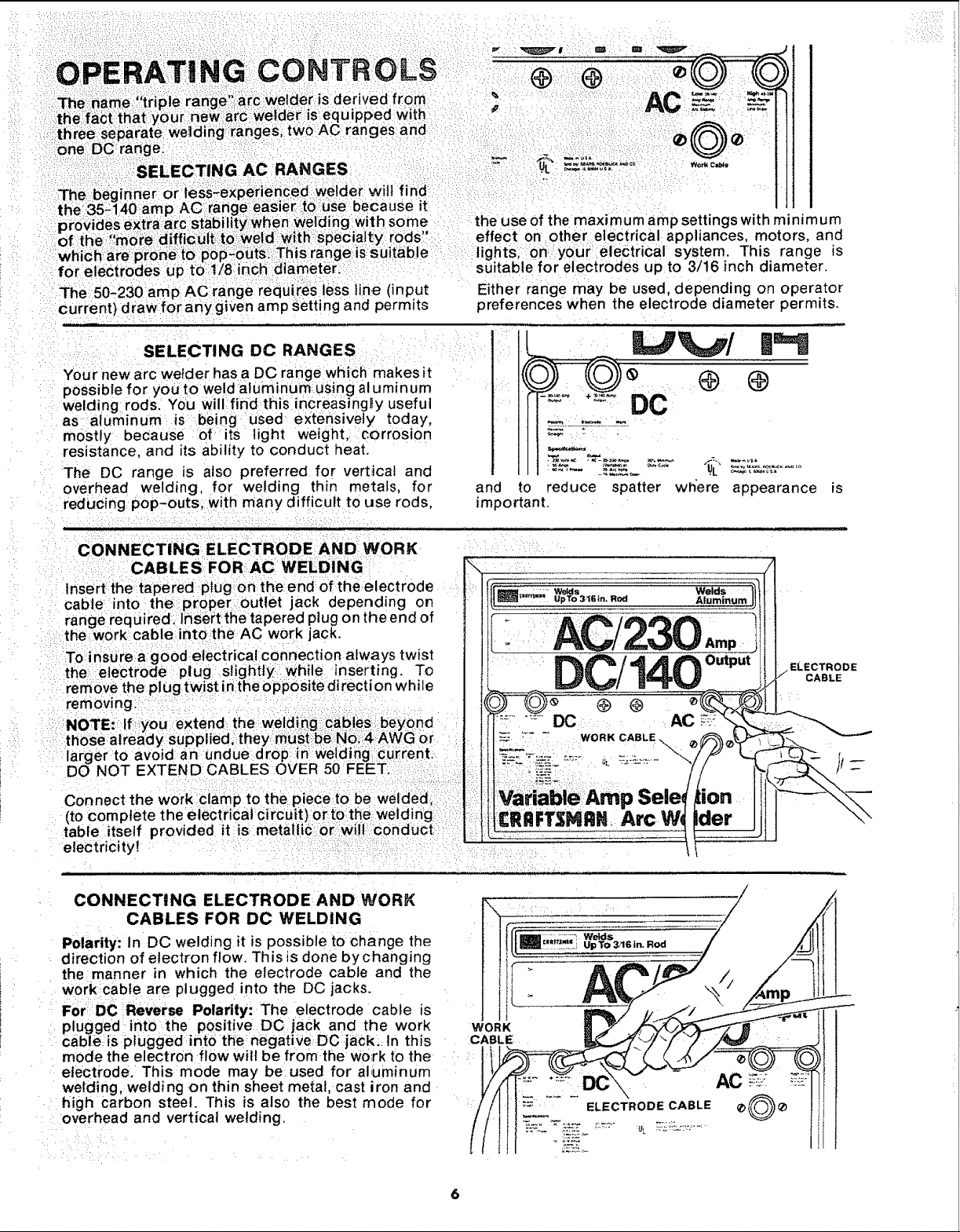
!::O
our
::tt
one
The 50-230amp AC range requi_:es less line (input
current) draw for any given amp setting and permits
SELECTING DC RANGES
Your new arc welder has a DC range which makes it
possible for youto weld aluminum using al uminum
welding rods. You will find this increasing_.y useful
as aluminum is be ngused eXtensively today,
mostly because o_ its light weight,: corrosion
resistance, and its ability to conduct heat.
The DC range is also preferred for verticat and
overhead welding, for welding thin metals, for
reducing pop-outs; with many difficult to use rods,
ranges two :AC ranges and
JNTRO:L:S @
welder: is derived from
is equipped with P
== v j
suitable for electrodes up to 3/!6 inch diameter.
Either range may be used, depending on operator
preferences when the electrode diameter permits.
and to reduce spatter where appearance
important.
ii:!:i::i:_:i::_i:i:
is
CONNECTING ELECTRODE AND WORK
CABLES FORAC WELDING
Insert the tapered plug on the:end of the electrode
cable into theproper Outlet jack depending on
range required, insert the tapered plug on the end of
the:work cable into_the AC work jack.
:To insure a good electrical connection always twist
the: electrode plug _slightty: while inserting. To
rem0ve the plug twist in theopposite directi on while
remowng:
NOTE:: If_you extend the welding:iilCables:beyond
those already supplied, they:must be No: 4 AWG or
larger to avoid an undue drop:in:weiding:currenL
DO NOT EXTEND CABLES OVER 50 FEET.
Connect the work c amp to the: piece to be welded,
(to complete the etectdcai circuit) or to the weiding
table itself provided it is metailic orwill conductl
electricity!
CONNECTING ELECTRODE AND WORK
CABLES FOR DC WELDING
Polarity: In DC welding it is possible to change the
direction of electron flow. This is done by changing
the manner in which the electrode cable and the
workcable are plugged into the DC jacks.
ForDC Reverse Polarity: The electrode cable is
plugged into the positive DC jack and the work
cable is plugged into the negative DC jack._ In this
mode the electron flow wilt be from the wo_rk to the
electrode. This mode may be used for ahJminum
welding, weldi ng .on thi n sheet metal, cast iron and
high carbon steel. This is also the best mode for
overhead and vertical welding.
WORK
CABLE
l
6
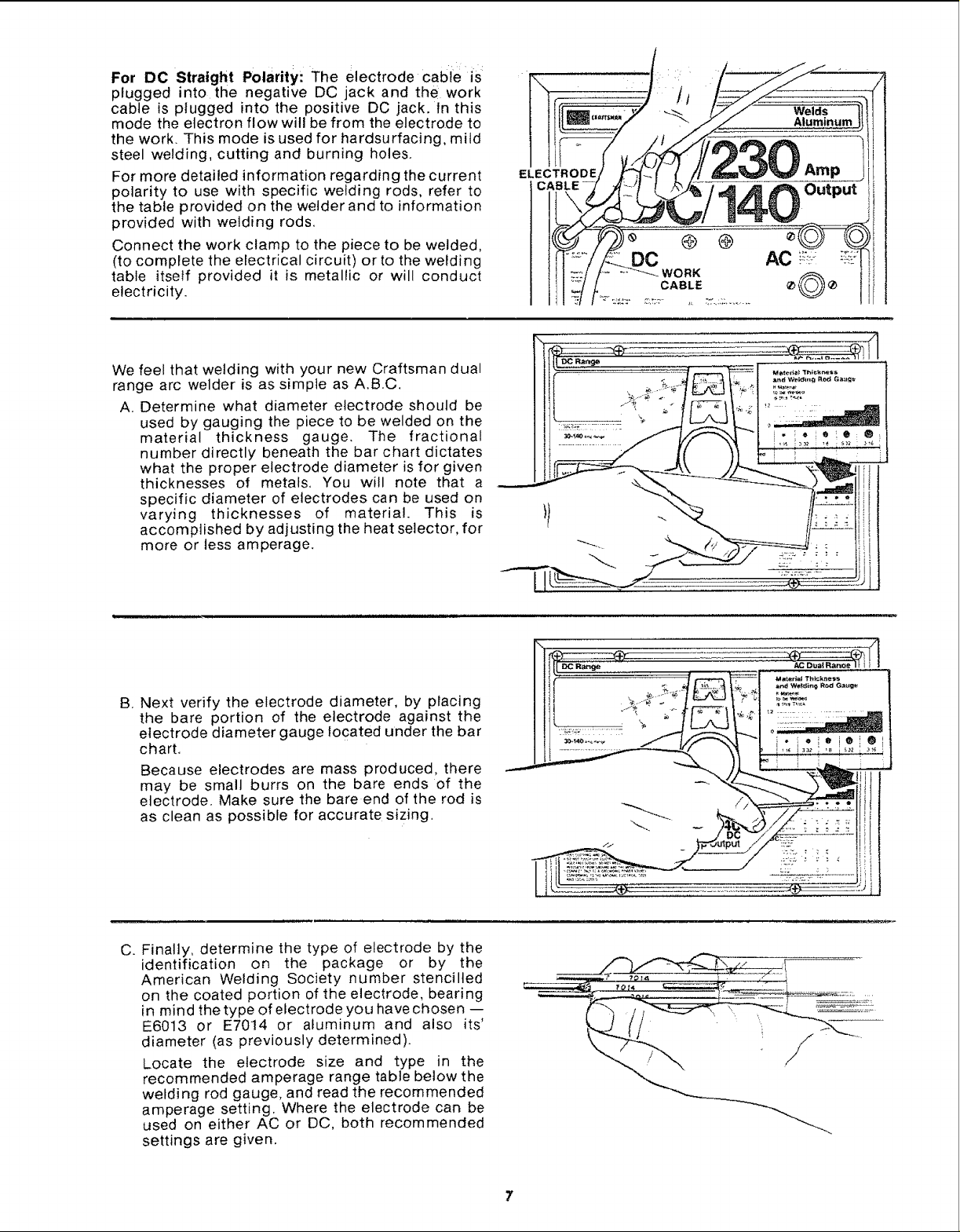
For DC Straight Polarity: The electrode cable is:
plugged into the negative DC jack and the work
cable is plugged into the positive DC jack. In this
mode the electron flowwill be from the electrode to
the work. This mode is used for hardsurfacing, mild
steel welding, cutting and burning holes.
For more detailed information regarding the current
polarity to use with specific welding rods, refer to
the table provided on the welder and to information
provided with welding rods.
Connect the work clamp to the piece to be welded,
(to complete the electrical circuit) orto the welding
table itself provided it is metallic or will conduct
electricity.
We feel that welding with your new Craftsman dual
range arc welder is as simple as A.B.C.
A. Determine what diameter electrode should be
used by gauging the piece to be welded on the
material thickness gauge. The fractional
number directly beneath the bar chart dictates
what the proper electrode diameter is for given
thicknesses of metals, You will note that a
specific diameter of electrodes can be used on
varying thicknesses of material. This is
accomplished by adjusting the heat selector, for
more or tess amperage.
ELECTRODE
C
DC
_/ORK
CABLE
Welds
Aluminum
140ou,.u,
@
o
B, Next verify the electrode diameter, by placing
the bare portion of the electrode against the
electrode diameter gauge located under the bar
chart.
Because electrodes are mass produced, there
may be small burrs on the bare ends of the
electrode. Make sure the bare end of the rod is
as clean as possible for accurate sizing.
C. Finally, determine the type of electrode by the
identification on the package or by the
American Welding Society number stencilled
on the coated portion of the electrode, bearing
in mind the type of electrode you have chosen --
E6013 or E7014 or aluminum and also its'
diameter (as previously determined).
Locate the electrode size and type in the
recommended amperage range table below the
welding rod gauge, and read the recommended
amperage setting, Where the electrode can be
used on either AC or DC, both recommended
settings are given,
f
/
7
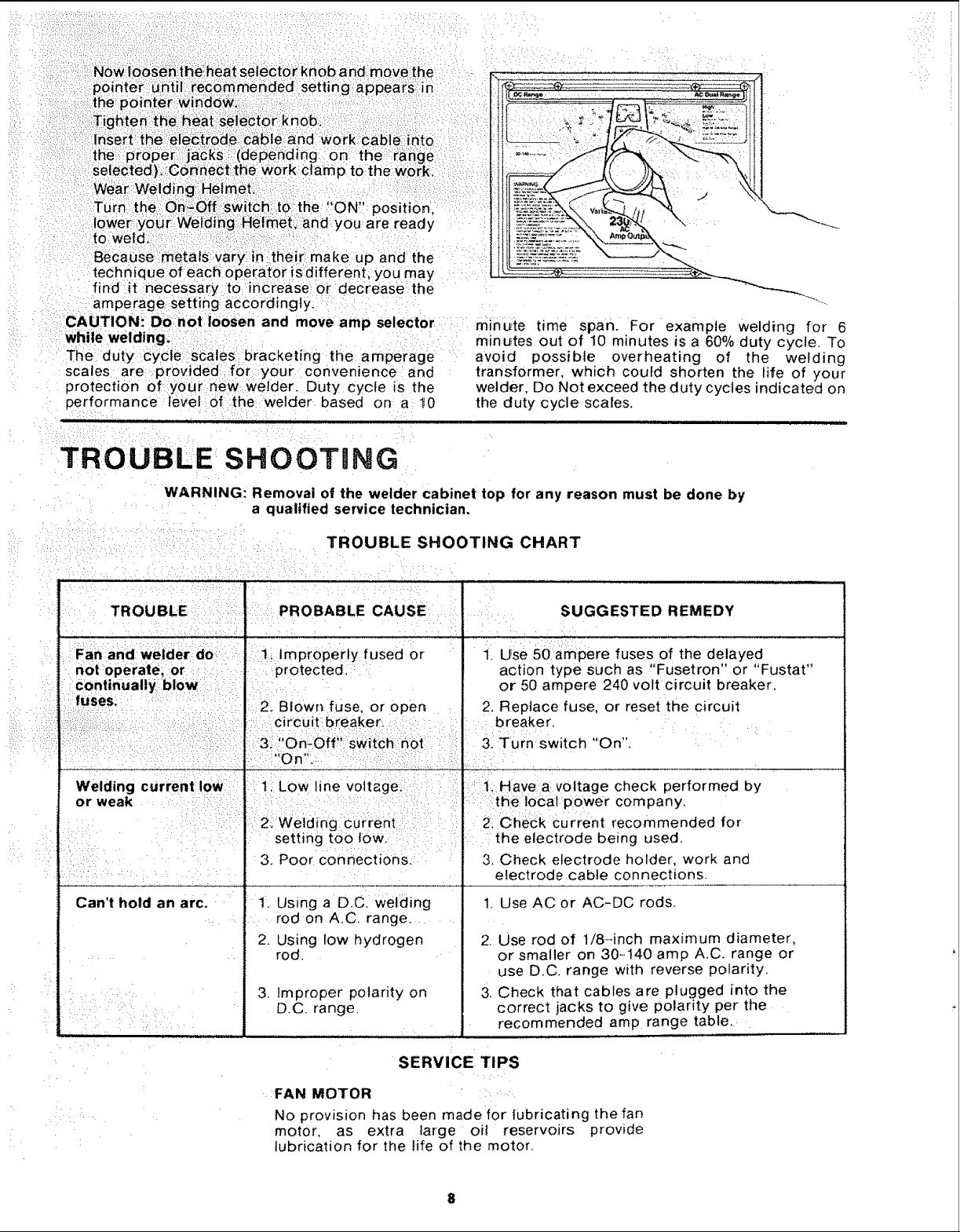
..:Now !oosen tlie heat selector knob and move the
: pointer urtti/_i_ecommehded Setting: appears_:: in
:: thep0i ::i _i:!: .:::i: ,:i i: :
i: i :' .nob: ::
selected)::_ Connect.the Work Clam p to the w6rk
Wear ! .
Turn:the 'ON" position,
• lower your:Welding: He!meL, and you are ready
to:weld,:- ....
up and the
technique of each operator fsdifferent, you may
find it necessary to increase or decrease the
amperage setting; accordingly.
CAUTION: Donot loosen and move amp selector
while welding.
The duty cycle scales: bracketing the amperage
scales are provided for :your convenience and
protection ofly0ur new welder. Duty cycle is the
performance level of the welder based on a t0
TROUBLE SHOOTmNG
: i/: :
minute time span, For example welding for 6
minutes oul of 10 minutes is a 60% duty cycle. To
avoid possible overheating of the welding
transformer, which could shorten the fife of your
welder, Do Not exceed the duty cycles indicated on
the duty cycle scales.
WARNING: Removal of the welder cabinet top for any reason must be done by
a qualified service technician.
TROUBLE SHOOTING CHART
TROUBLE : ::: i PROBABLE CAUSE ! SUGGESTED REMEDY
Fan and welder do:i Improperly fused or 1 Use 50 ampere fuses of the delayed
: r " tr n" r
not operate, or :-:: ....... i _P otected, achon type such as Fuse o o Fustat
: Continually blow _ :i I or 50 ampere 240 volt circuit breaker.
:fuses: i : 112. Blown fuse, or open 2, Replace fuse, or reset the circuit
.... breaker,
: ::: i:i;;; "OmOif:" :switch 3: Turn:switch "On". :
Welding currentlow t Low line v01tage_ iti:,111 Haven voltage check performed by
or weak ! " the local power company,
2, Welding Cur:rent i:! 2. Check Current recommended for
Setting too low. : ! the electrode being used.
: 3, Poor connections: 3, Check electrode holder, work and
" .:_L_ _ electrode cable connections.
Can't hold an arc. ,
3.
Using a D.C. welding
rod on A,C, range.
2.
Using low hydrogen
rod,
Improper polarity on
D.C. range,
1. Use AC or AC-DC rods,
2. Use rod of 1/8-inch maximum diameter,
or smaller on 30-140 amp A.C. range or
use D.C. range with reverse polarity.
3, Check that cables are plugged into the
correct jacks to give polarity per the
recommended amp range table.
SERVICE TIPS
FAN MOTOR
No provision has been made for lubricating the fan
motor, as extra large oil reservoirs provide
lubrication for the life of the motor,
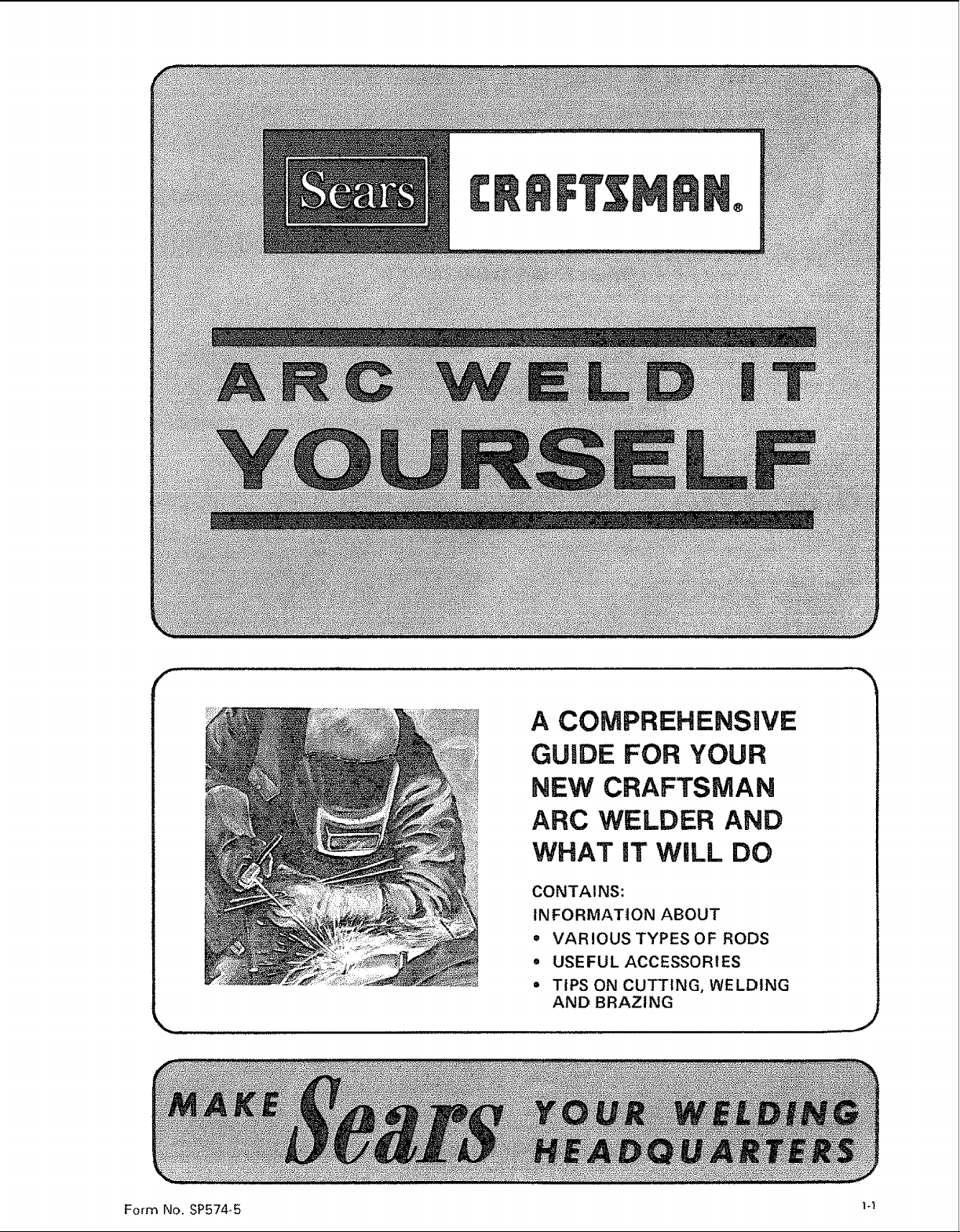
f
A COMPREHENSIVE
GUIDE FOR YOUR
NEW CRAFTSMAN
ARC WELDER AND
WHAT iT WiLL DO
CONTAINS:
INFORMATION ABOUT
= VARIOUS TYPES OF RODS
= USEFUL ACCESSORIES
° TIPS ON CUTTING, WELDING
AND BRAZING
J
Form No. SP574_5 14
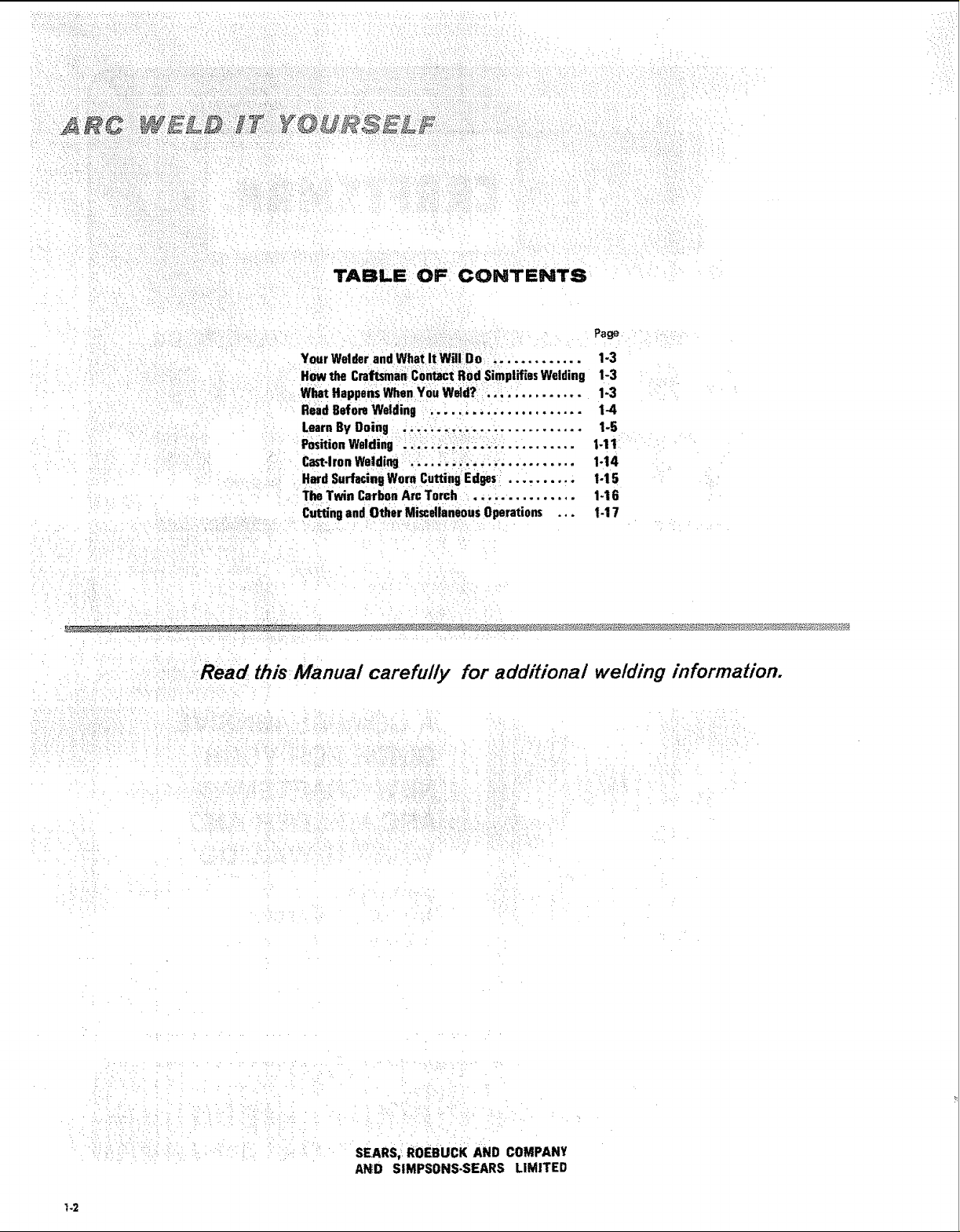
TABLE OF CONTENTS
Page
YourWelderandWhatIt Will Do ............. 1-3
Howthe CraftsmanContactRodSimplifiesWelding 1-3
WhatHappensWhenYouWeld? .............. 1-3
ReadBeforeWelding ...................... 14
LearnBy Doing............................ 1-5
PositionWelding ......................... 1-11
Cast-IronWelding ........................ 1-14
HardSurfacingWoreCuttingEdges .......... 1-15
TheTwin CarbonArc Torch ............... 1-16
Cuttingand OtherMiscellaneousOperations .,. 1-17
•ii:i•I;••••
Read this Manual carefully for additional welding information.
1-2
SEARS,' ROEBUCK AND COMPANY
AND SIMPSONS-SEARS LIMITED
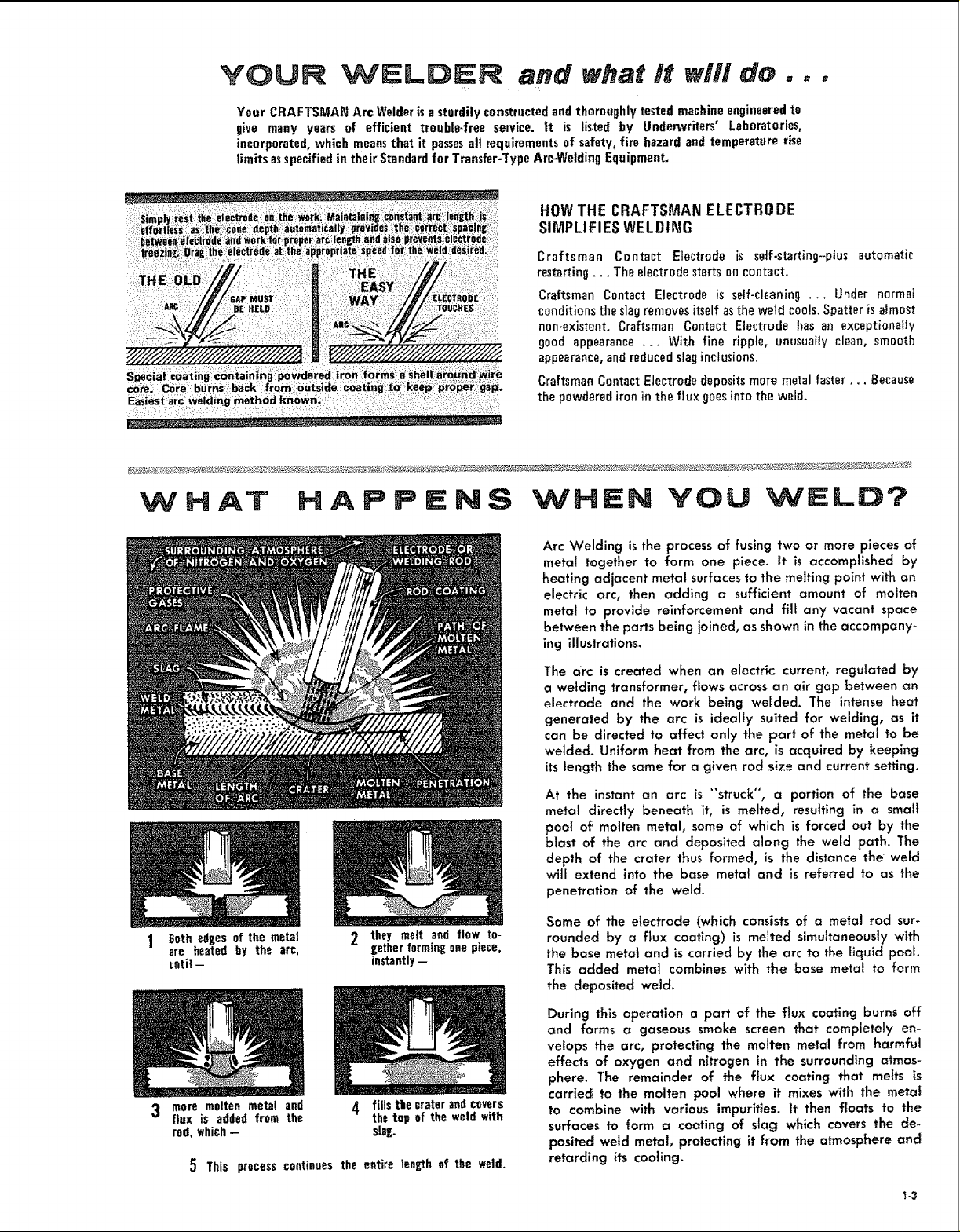
YOUR WELDER and what it will do..,
Your CRAFTSMAN Arc Welder is a sturdily constructed and thoroughly tested machine engineered to
give many years of efficient trouble-free service. It is listed by Underwriters' Laboratories,
incorporated, which meansthat it passesall requirements of safety, fire hazard and temperature rise
limits asspecified in their Standard for Transfer-Type Arc-Welding Equipment.
HOWTHE CRAFTSMAN ELECTRODE
SIMPLIFIES WELDING
Craftsman Contact Electrode is self-starting-plus automatic
restarting... The electrode starts on contact.
Craftsman Contact Electrode is self-cleaning ... Under normal
conditions the slag removes itself asthe weld cools. Spatter is almost
non-existent. Craftsman Contact Electrode has an exceptionally
good appearance .., With fine ripple, unusually clean, smooth
appearance, and reduced slaginclusions,
Craftsman Contact Electrode deposits more metal faster,,. Because
the powdered iron in the flux goes into the weld.
W' H AT H A P P E N S WHEN YOU WELD?
| Seth edges of the metal
are heated by the arc,
until-
2 they meft and flew to-
gether formingone piece,
instantly--
Arc Welding is the process of fusing two or more pieces of
metal together to form one piece. It is accomplished by
heating adjacent metal surfaces to the melting point with an
electric arc, then adding a sufficient amount of molten
metal to provide reinforcement and fill any vacant space
between the parts being ioined, as shown in the accompany-
ing illustrations.
The arc is created when an electric current, regulated by
a welding transformer, flows across an air gap between an
electrode and the work being we_ded. The intense heat
generated by the arc is ic{eally suited for welding, as it
can be directed to affect only the part of the metal to be
welded. Uniform heat from the arc, is acquired by keeping
its length the same for a given rod size and current setting.
At the instant an arc is "struck", a portion of the base
metal directly beneath it, is melted, resulting in a small
poot of molten metal, some of which is forced out by the
blast of the arc and deposited along the weld path. The
depth of the crater thus formed, is the distance the weld
wit[ extend into the base metal and is referred to as the
penetration of the weld.
Some of the electrode (which consists of a metal rod sur-
rounded by a flux coating) is melted simultaneously with
the base metal and is carried by the arc to the liquid pool.
This added metal combines with t_e base metal to form
the deposited weld.
more molten metal and
flux is added from the
rod, which-
5 This process continues the entire length of the weld.
4 fills the craterand covers
the top of the weld with
slag.
During this operation a part of the flux coating burns off
and forms a gaseous smoke screen that completely en-
velops the arc, protecting the molten metal from harmful
effects of oxygen and nitrogen in the surrounding atmos-
phere. The remainder of the flux coating that melts is
carriec_ to the molten pool where it mixes with the metal
to combine with various impurities. It then floats to the
surfaces to form a coating of slag which covers the de-
posited weld metal, protecting it from the atmosphere and
retarding its cooling.