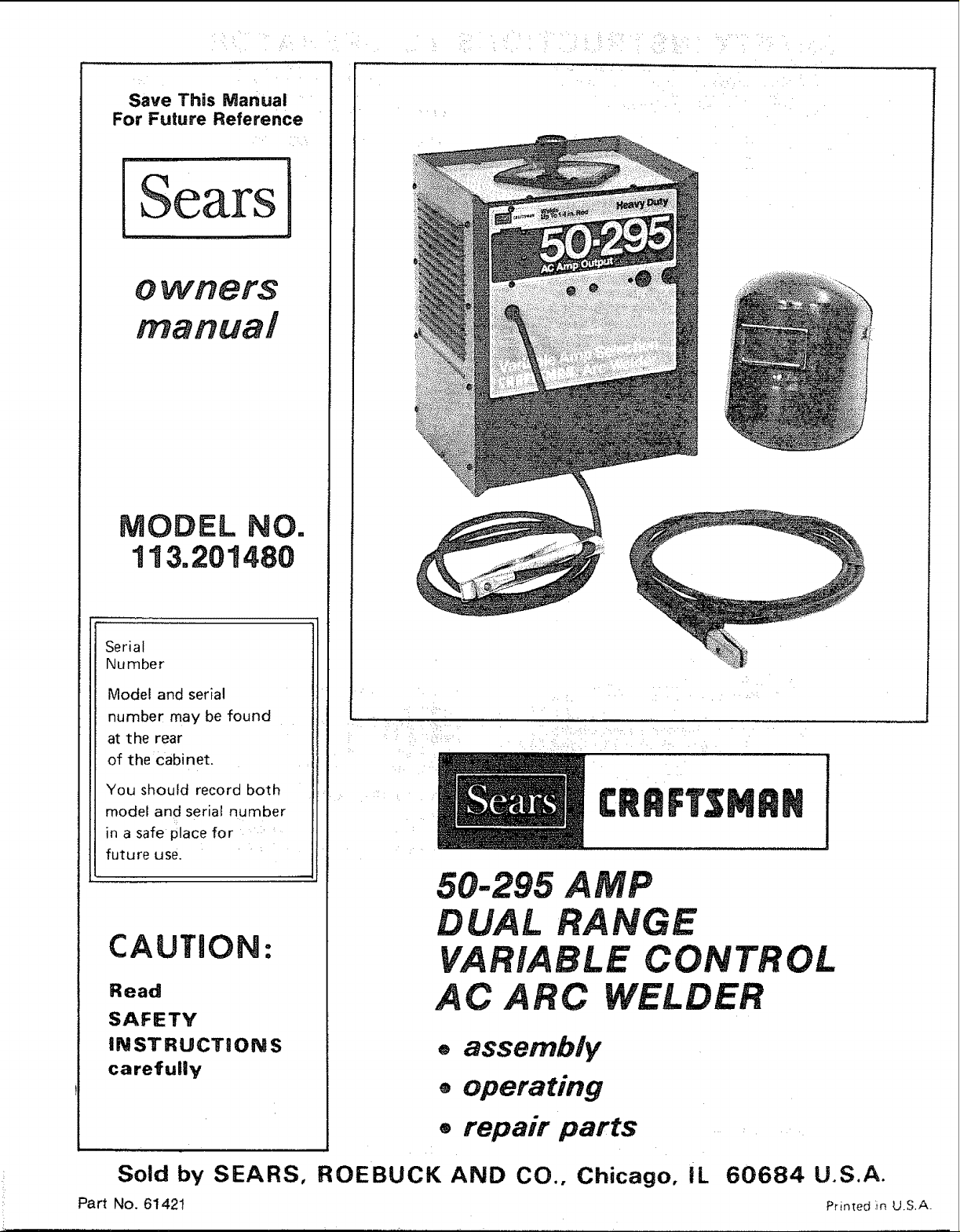
Save This Manual
For Future Reference
MODEL NO.
113.201480
Serial
Number
Model and serial
number may be found
at the rear
of the cabinet.
You should record both
model and serial number
in a safe place for
future use.
CAUTION:
Read
SAFETY
INSTRUCTIONS
carefully
• •i•: i•i::¸:_:::: : ; :• :; :
50-295 AMP
DUAL RANGE
VARIABLE CONTROL
ACARC
e assembly
® operating
Sold by SEARS,
Part No. 61421
® repair parts
ROEBUCK AND CO., Chicago, IL
60684 U.S.A.
Printed ;inU.S.A_
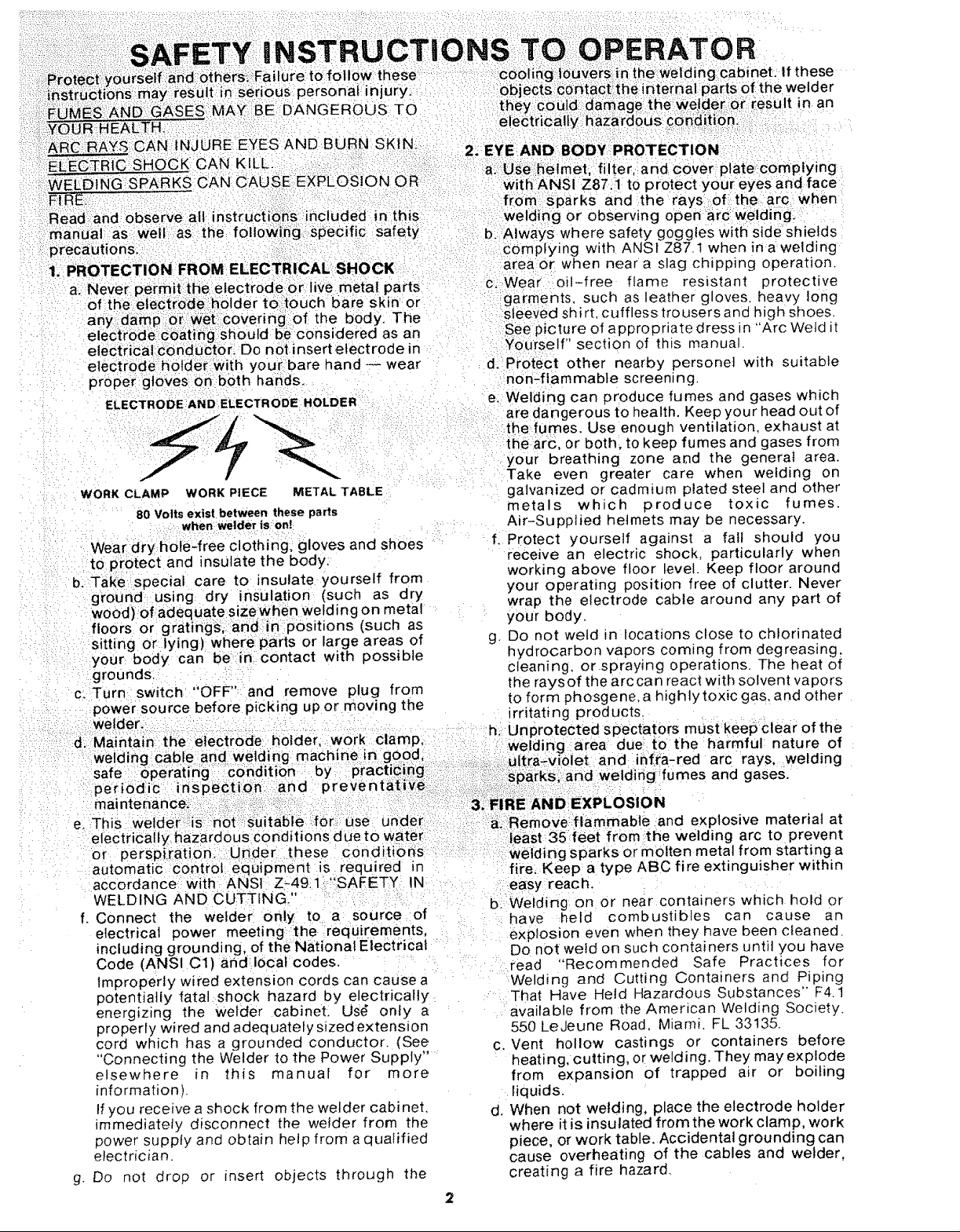
a:. Never permit the electrode or live metal parts
of:the eiectrodeholder t0_t0uch bare sk nor
any: damp:o_ W_eti::covering of the body. The
electrede:cbating slioutd be considered as an
electrical conducltor_ Do n0t insert electrode in
electrode hotde_iWith your bare hand -- wear
pr0pergloVes on both hands.
ELECTRODE AND ELECTRODE HOLDER
WORK CLAMP WORK PIECE METAL TABLE
80 Volts exist between these parts
when welder ison!
Weardry hole_free clothing, gloves and shoes
to protect and insulate the body:
b. Take special care to insulate yourself from
ground using dry insulation (such as dry
wood) of adequate sizewhen welding on metal
floors or gratings, and in:Positions (such as
sitting or lying) where parts or fargo areas of
your body can be in contact with possible
grounds:
c: Turn switch "OFF", and remove plug from
power source before picking up or moving the
welder.
:d. Maintain the electrode: holder, work clamp,
welding cable arid welding machine in good; :i i:
safe Operating i €onditior_ :by : Practii_i_g:!!i: :i:::':
per io d!ic in S pect ion ::=and p r e ve n tat ive i!,:_i,:__!.il
area or when near a slag chipping operation.
c, Wear oil-free flame resistant protective
garments, such as leather gloves heavy long
sleeved shirt, cuffless trousers and high shoes.
See picture of appropriate dress in "Arc Weld it
YOurself" section of this manual.
d. Protect other nearby persone] with suitable
nOn-flammable screening.
e. Welding can produce fumes and gases which
are dangerous to health. Keep your head out of
the fumes. Use enough ventilation, exhaust at
the arc, or both, to keep fumes and gases from
your breathing zone aod the general area.
Take even greater care when welding on
galvanized or cadmium plated steel and other
metals which produce toxic fumes.
Air-Supplied helmets may be necessary.
f. Protect yourself against a fall should you
recewe an electric shock, particularly when
working above floor level. Keep floor around
your operating position free of clutter. Never
wrap the electrode cable around any part of
your body.
g. Do not weld in locations close to chlorinated
hydrocarbon vapors coming from degreasing.
cleaning, orspraying operations. The heat of
the rays of the arc can react with solvent vapors
to form phosgene, a highlytoxic gas. and other
irritating products.
h. nprotected spectators must keepclear of the
area due to the harmful nature of
et and infra-red arc rays, welding
and weldirig fumes and gases.
e. This Welder':_iis ':not;}:::i_uitable i:iori:_:use
electrically hazardous conditions due to
or persph;atiom Under these c0ndil
automatic control equipment iS required in
accordance: with ANSI Z-49.1:.";SAFETY IN
WELDING AND CUTTING_"
f. Connect the welder on!y to a source of
electrical power meeting the requirements,
including grounding, of the National Electrical
Code (ANSI C1) and local codes,
Improperly wired extension cords can cause a
potentially fatal shock hazard by electrically
energizing the Welder cabinet. Us_ only a
properly wired and adequately sized extension
cord which has a grounded conductor. (See
"Connecting the WeJder to the Power Supply ....
elsewhere in this manual for more
information).
If you receive a shock from the welder cabinet.
immediately disconnect the welder from the
power supply and obtain help from a qualified
electrician.
g. Do not drop or insert objects through the
a::Remove:flammable and explosive material at
ieast 35 feet from the welding arc to prevent
welding sparks or molten metal from starting a
fire. Keep a type ABC fire extinguisher within
.easy reach.
b. Welding on or near containers which hold or
have held combustibles can cause an
explosion even when they have been cleaned.
Do not weld on such containers until you have
read "Recommended Safe Practices for
Welding and Cutting Containers and Piping
That Have Heid Hazardous Substances" F4.1
available from the American Welding Society.
550 LeJeune Road, Miami. FL 33135.
c. Vent hollow castings or containers before
heating, cutting, or welding. They may explode
from expansion of trapped air or boiling
liquids.
d. When not welding, place the electrode holder
where it is insulated from the work clamp, work
piece, or work table. Accidental grounding can
cause overheating of the cables and welder,
creating a fire hazard.

e.Neverconnecttheworkcableorclamptoany
objectbuttheworkpieceormeta_worktable.
Connectingto otherobjectssuchasbuilding
ground can cause stray currents to flow,
resultinginoverheatingorfire.
4. PREVENTATIVE MAINTENANCE
a. Never apply power to the welder with any part
of the ,cabinet" removed. Position on-off
switch in "off" position and disconnect welder
from the power supply before doing
maintenance work inside the machine.
Removal of the welder cabinet should be done
onty by a qualified service technician.
b. Before connecting the welder power cord to
the receptacle, check the following:
1. Inspect the power cord and welding cables
for cuts or burns and make sure blades and
ground pin on the plug are straight.
2. Inspect "ON-OFF" switch leverfor cracks or
broken parts.
3, Inspect electrode holder jaw insulators for
cracks or broken parts.
c. Never weld anything on or to the welder
cabinet, as a burn through may cause
transformer failure.
d. If any part of your welder is malfunctioning or
has been damaged or broken, such as switch,
cables, helmet, electrode holder, cease
operation immediately and disconnect welder
from the power source and turn switch "OFF"
until the particular part is properly repaired or
replaced.
5. ADDITIONAL SAFETY INFORMATION
a. For additional safety information, purchase
copies of "Practice for Occupational and
Educational Eye and Face Protection" (ANSI
Z87.1), "Safety in Welding and Cutting" (ANSI
Z49.1), and "Fire Prevention in Use of Cutting
.... , and ,Welding Processes" (ANSIiNFPA No.
518) from the American National Standards
Institute, 1430 Broadway, New York, New
York, 10018. Purchase copiesof"OSHA Safety
and Health Standard" 29 CFR 1910 from the
U.S. Government Printing Office, Washington,
D.C. 20402.
SPECiFICATiONS
INPUT
Volts AC.. ............................ ..... 230
Hertz (Cycles) .;..... ...................... 60
Rated Input Amps .......................... 60
Delay Action Type Circuit Breaker or Fuse 60Amp
Short Circuit Amps ....................... 100
Power Cord Length ................ wire direct
OUTPUT
AC Low Range Amps .................. 50-185
AC High Range Amps .................. 65-295
DC Range Amps ............................ *
Arc Voltage ................................ 30
AC Open Circuit Volts (max) ............... 80
DC Open Circuit Volts (Max) ................ *
Kilo-Volt-Amps .......................... 16,8
Kilo-Watts ............................... 11.0
Power Factor % ............................ 65
Duty Cycle % .......................... 20-100
GENERAL
Electrode Capacity ................... 1/16-1/4
Low Hydrogen ...................... 1/16-3/16
Stainless Steel ...................... 1/16-3/16
Aluminum .................................. *
Electrode Cable Length ................... 12'
Work Cable Length ....................... 10'
Dimensions .................... 15" x 12" x 21"
" Does not apply to this welder
READ AND OBSERVE THE INSTRUCTIONS
APPEARING ON THE WARNING INFORMA-
TION FOUND ON THE CABINET,
ELECTRODE HOLDER AND ON THE INSIDE
OF THE WELDING HELMET.
TURNING WELDE R ON, CHECK THE ELECTRODE HOLDER TO
t .,_ WARNING ELECTR,CSHOCKCA.BEFATAL!BeFOa_I
BE SURE THAT THERE ARE NO PROTRUDING SCRE W HEADS
_1_ AND THAT ALL INSULATION iS SECURE _ _ :" '_
WARNING! ARC WELDING CAN BE iN3URIOUS TO OPERATOi_ AND PERSONS
_N THE WORK AREA -- CONSULT OWNERS MANUAL BEFORE OPERATING
To get the most from your welder we suggest you read the manual carefully--
even if you're an accomplished welder, and keep it available to serve as a
handy reference, or in the event that repair parts would be required.
FULL ONE YEAR WARRANTY ON CRAFTSMAN ELECTRIC WELDER
if thisCraftsman Etectric Welder fails to perform properly, dueto adefect inmateriaJor workmanship,within oneyear
from thedate of purchase, Sears will repair it free of charge. This warranty applies only whilethis product isinuseinthe
United States.
WARRANTY SERVICE IS AVAILABLE BY SIMPLY RETURNING THE WELDERTO THE NEAREST SEARS SERVICE
CENTER/DEPARTMENT THROUGHOUT THE UNITED STATES.
This warranty gives you specific legal rights, and you may have other rights wtiich vary from state to state_
SEARS, ROEBUCK AND CO., Dept, 698/731Ai Sears Tower, Chicago, IL 60684
i
1
LENS (_
SHADE NO.
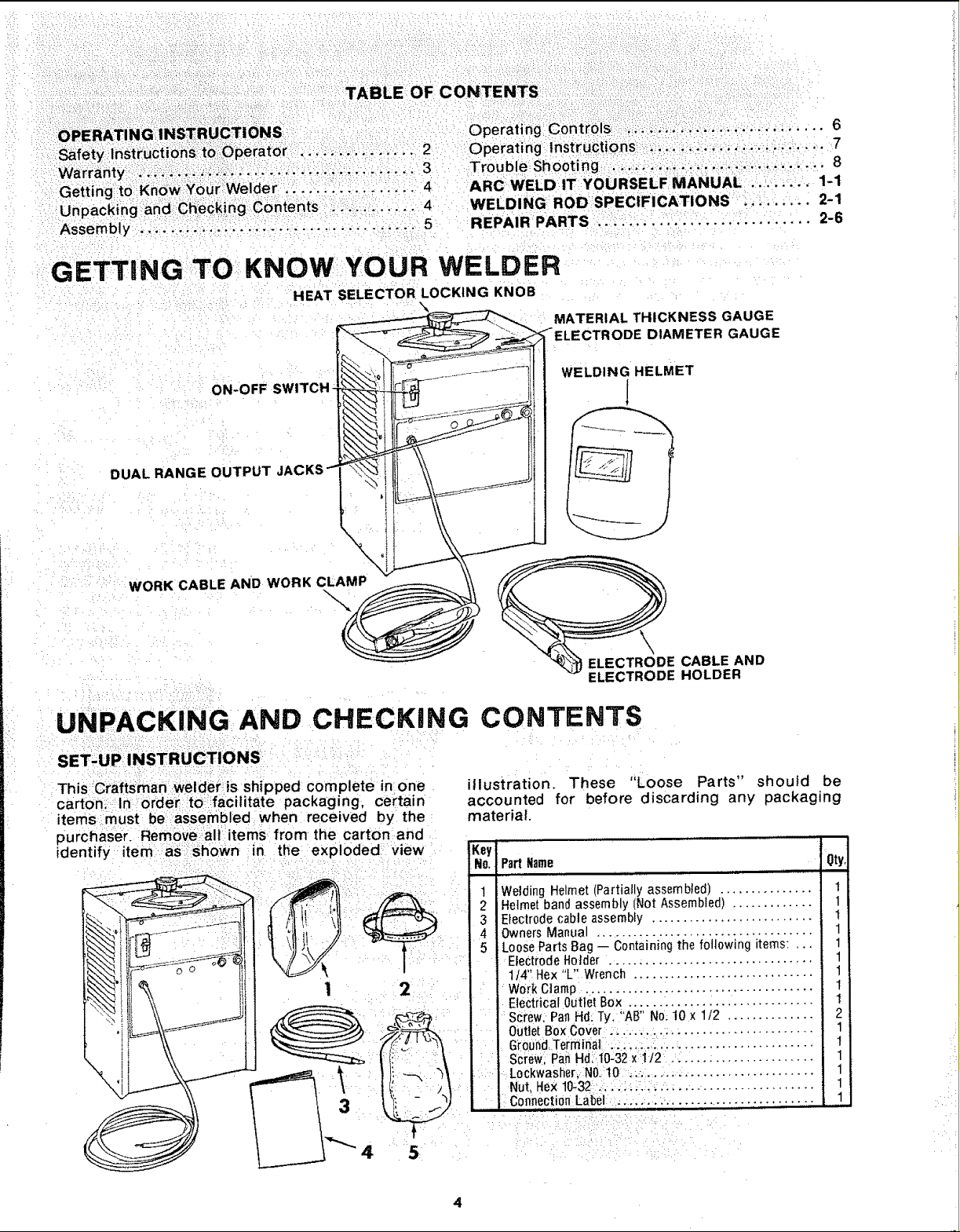
OPERATING!I_INSTR_CTI ONS
Operating ContrOls ................. 6
0 ........................ 7
Warranty _ : ii !:.! :i _.:_i:::.:... :.:;_:.:. _.i _. !., _i 3
Getting tO ::'.. :,:_:i. :. 4
Unpacking and C_cki"gGontents :;: .!;;...... 4
T ................. 8
ARC ..... 1-1
WELDING ROD SPECIFICATIONS ......... 2-1
REPAIR PARTS ............................ 2-6
GETTING TO: KNOW YOUR WELDER
HEAT SELECTOR LOCKING KNOB
MATERIAL THICKNESS GAUGE
_ELECTRODE DIAMETER GAUGE
ON-OFF SWITCH
DUAL RANGE OUTPUT _"
WORK CABLE AND WORK CLAMP
-%
\
\
\
WELDING HELMET
ELECTRODE CABLE AND
ELECTRODE HOLDER
UNPACKING AND CHECKING CONTENTS
SET-UP INSTRUCTIONS _
This Craftsmanwelder:is shipped complete in one
carton_ 'In order to:facilitate packaging; ce_'tain
items must be assembled when received by the
purchaser. Remove:all items from the carton and
identify item as _shown in the exploded view
_:__ _i 1 WeidingHetmet(Partia,lyassembted) ...............
--__ ii 1 "_ 2 E,ectrodeHoJder ..............................
illustration. These "Loose Parts" should be
accounted for before discarding any packaging
material.
Key
No. PartName ' Oty
2 Helmet band assembly (NotAssembled) .............
3 Electrode cable assembly ..........................
4 OwnersManual ...................................
5 LooseParts Bag -- Containing the following items: ,..
1/4" Hex"L" Wrench .............................
WorkClamp .:....................................
Screw. Pan Hd: Ty, "AB" No. 10 x 1/2 ..............
i OutletBoxCover. ...... ..: ....................... '
• G_oundTerminal ...... ; .-:...........................
i ] Screw PahHdi10-32 x'_t2 .. .... , ................
J Nut, Hex10:32 ..... ::..:_..: .... ..................
, ConnectionLabel ;... :.. .........
!
1
1
t
1
1
1
1
I
I
2
t
t
1
1
1
1
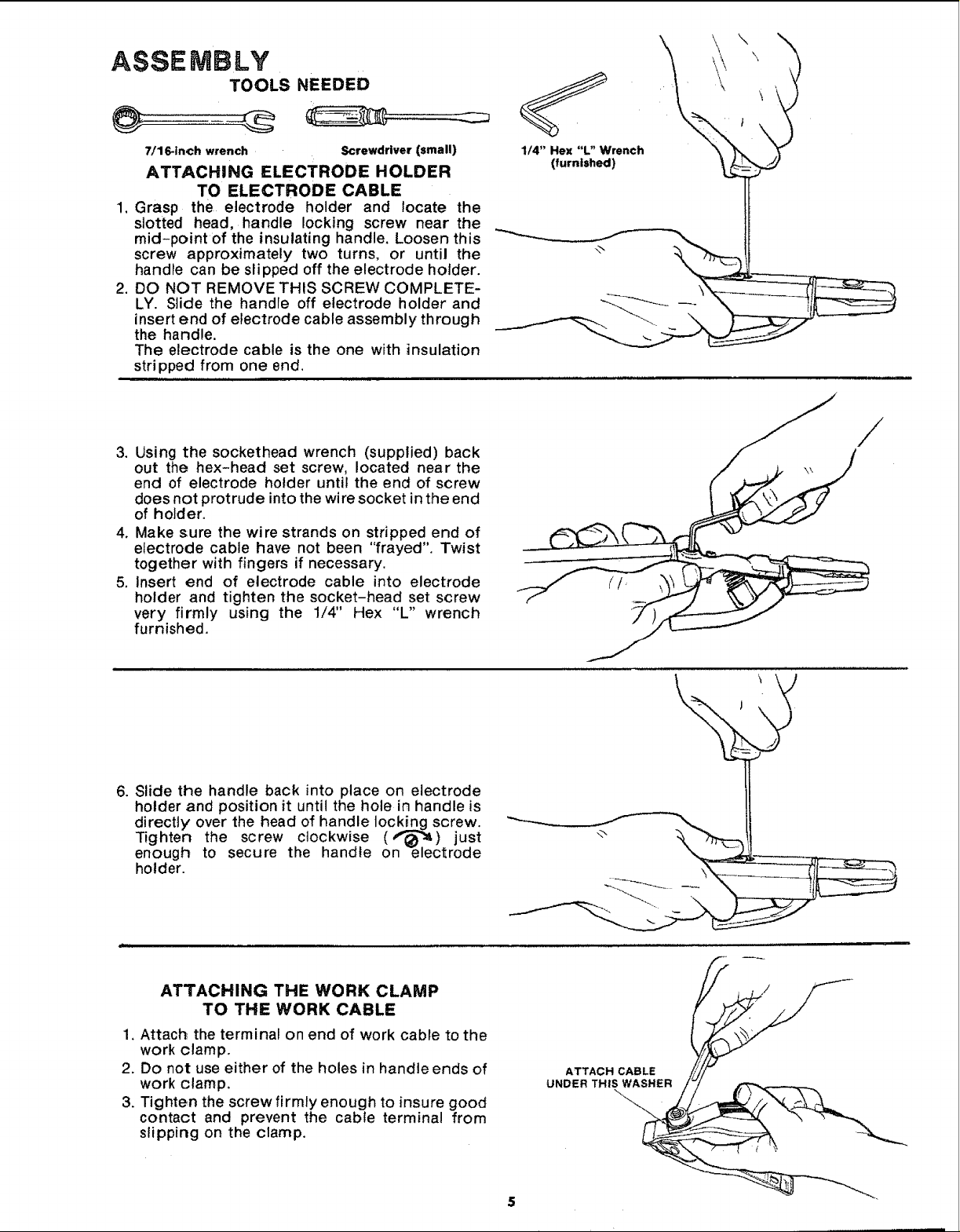
ASSEMBLY
TOOLS NEEDED
@
7/16-inch wrench Screwdriver (small)
ATTACHING ELECTRODE HOLDER
TO ELECTRODE CABLE
,
Grasp the electrode holder and locate the
slotted head, handle locking screw near the
mid-point of the insulating handle. Loosen this
screw approximately two turns, or until the
handle can be slipped off the electrode holder.
,
DO NOT REMOVE THIS SCREW COMPLETE-
LY. Slide the handle off electrode holder and
insert end of electrode cable assembly through
the handle.
The electrode cable is the one with insulation
stripped from one end.
3. Using the sockethead wrench (supplied) back
out the hex-head set screw, located near the
end of electrode holder until the end of screw
does not protrude into the wire socket inthe end
of holder.
4. Make sure the wire strands on stripped end of
electrode cable have not been "frayed". Twist
together with fingers if necessary.
5. Insert end of electrode cable into electrode
holder and tighten the socket-head set screw
very firmly using the 1/4" Hex "L" wrench
furnished.
1/4" Hex "L" Wrench
(furnished)
6. Slide the handle back into place on electrode
holder and position it until the hole in handle is
directly' over the head of handle Iock__nngscrew.
Tighten the screw clockwise (,"_.) just
enough to secure the handle on e_ectrode
holder.
ATTACHING THE WORK CLAMP
TO THE WORK CABLE
1. Attach the terminal on end of work cable to the
work clamp.
2. Do not use either of the holes in handle ends of
work clamp.
3. Tighten the screw firmly enough to insure good
contact and prevent the cable terminal from
slipping on the clamp.
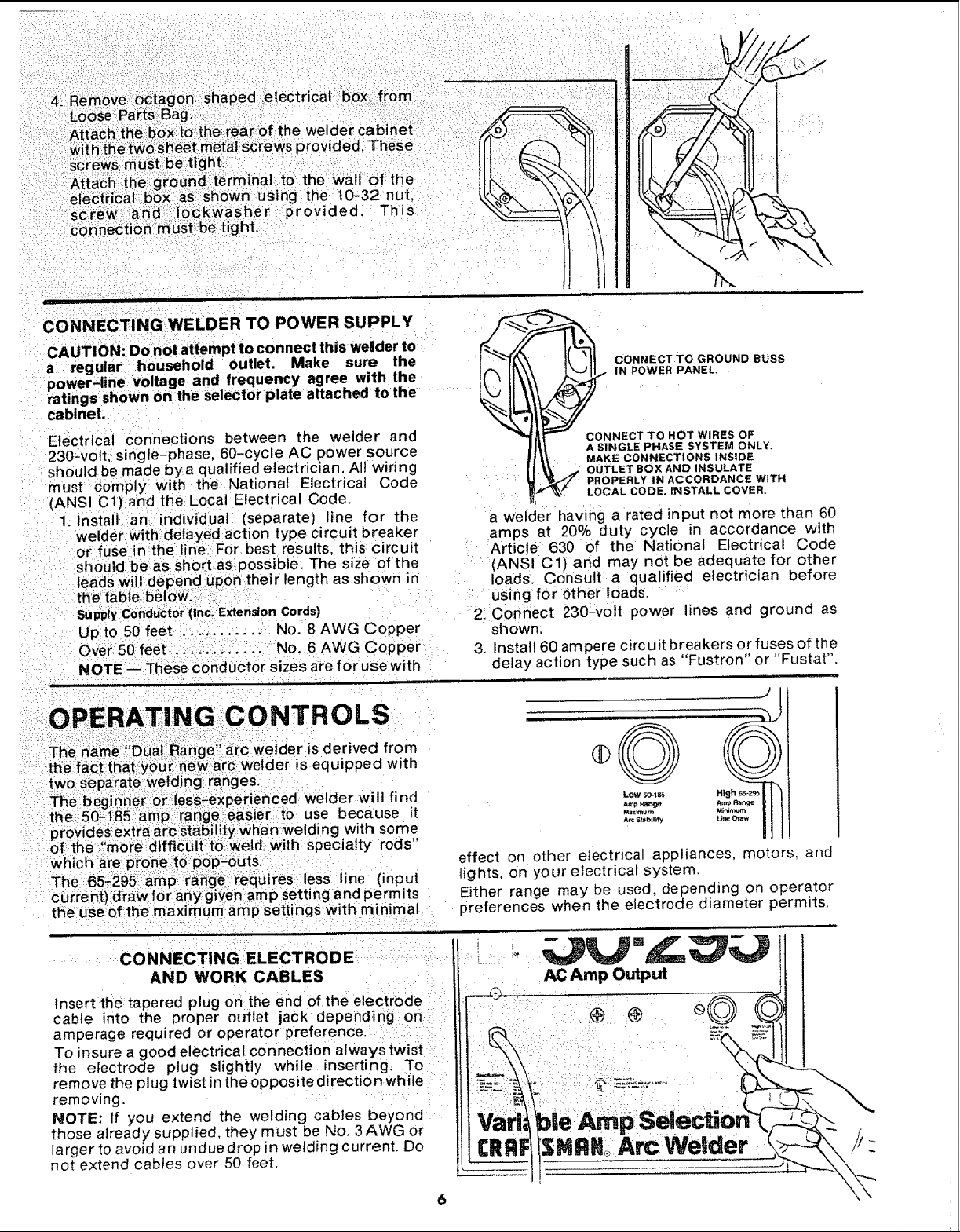
CONNECTING WELDER TO POWER SUPPLY
CAUTION: Do not attempt to connect this welder to
a regular household outlet. Make sure the
power-line voltage and frequency agree with the
ratings shown on the selector plate attached tothe
cabinet_
Electrical connections between the welder and
230-volt, single-phase, 60-cycle AC power source
should be made by a qualified electrician. All wiring
must comply With the National Electrical Code
(ANSI Ct)a'nd theLocal Electrical Code.
1. Install an individual (separate)line for the
welder With;delayed action type circuit breaker
or fuse in the line:: For best results, this circuit
should: boas shortas possible. The size of the
leads:will depend Upon:their length as shown in
the: table belOW_:i:::_
Suppty C0nduCtor (i.c. Exteriston Cords)
Up to 50 feet ._- ........ No. 8 AWG Copper
Over 50:feet .._ .......... No. 6 AWG Copper
NOTE .-These conductor sizes are for use with
i ............ ,.,, , , . , ,
CONNECT TO GROUND BUSS
IN POWER PANEL,
CONNECT TO HOT WIRES OF
A SINGLE PHASE SYSTEM ONLY.
OUTLET BOX AND INSULATE
_ _ MAKE CONNECTIONS INSIDE
PROPERLY IN ACCORDANCE WITH
LOCAL CODE. INSTALL. COVER,
a welder having a rated input not more than 60
amps at 20% dutY cycle in accordance with
Article 630 of the National Electrical Code
(ANSI C1) and may not be adequate for other
loads. Consult a qualified electrician before
using for other loads.
2_
Connect 230-vott power lines and ground as
shown.
3.
Install 60 am pete circuit breakers or fuses of the
delay action type such as "Fustron" or "Fustat".
H
L ,
CON NECTING ELECTRODE
AND WORK CABLES
Insert the tapered plug on the end of the electrode
cable into the proper outlet jack depending on
amperage required or operator preference.
To insure a good electrical connection always twist
the electrode plug slightly while inserting. To
remove the Dlug twist in theoppositedirection while
removing.
NOTE: If you extend the welding cables beyond
those already supplied, they must be No. 3 AWG or
larger to avoidan unduedrop in welding current. Do
not extend cables over 50 feet.
LOW r_O-18,_
Am_ Rar_ge
M=xLmum
Arc $_I_#_v
effect on other electrical appliances, motors, and
lights, on your electrical system.
Either range may be used, depending on operator
preferences when the electrode diameter permits.
L
AC Amp Output
leArnp se
$MRN Arc Welder
__J
6
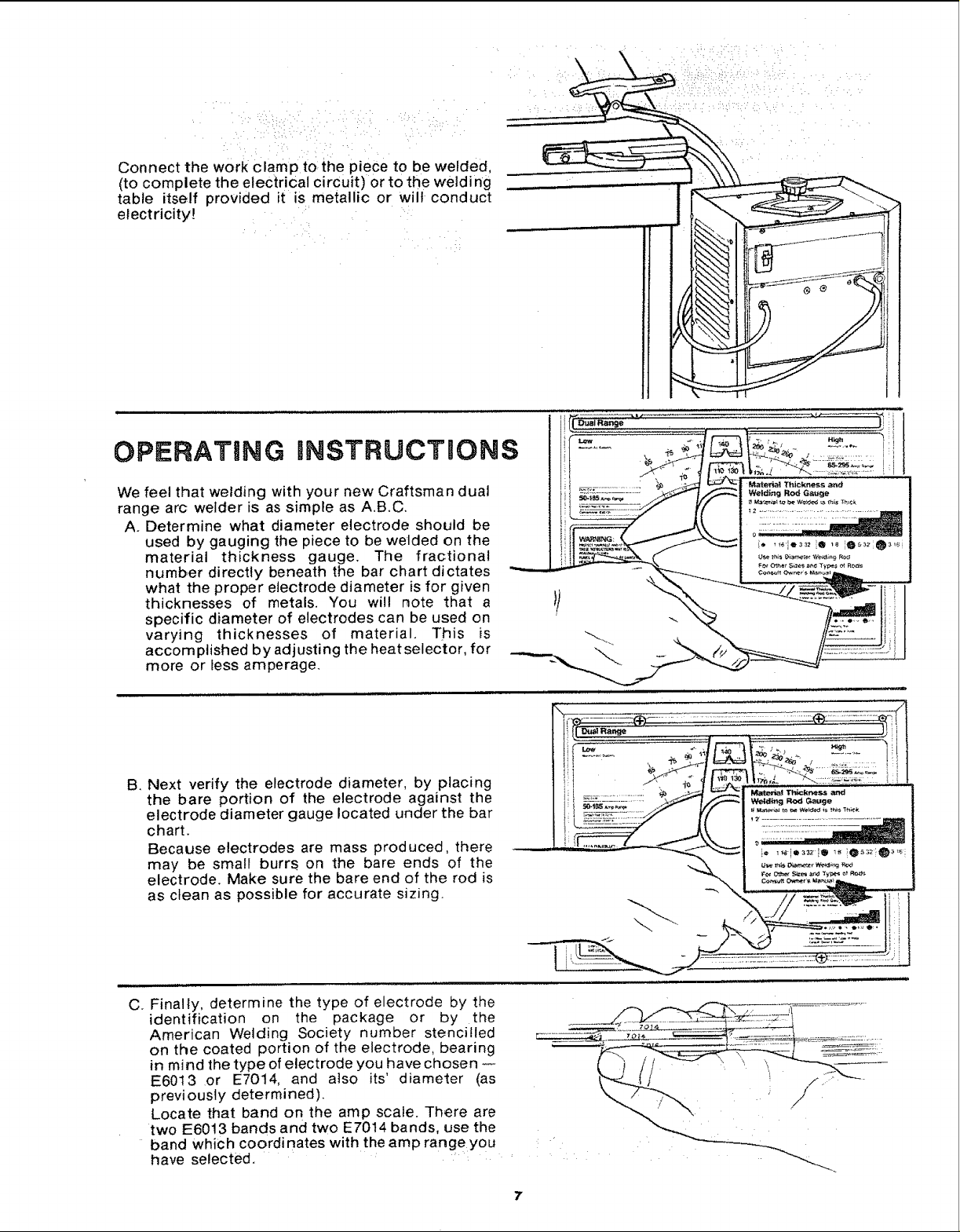
Connectthework clamp to the piece to be welded,
(to complete the electrical circuit) or to the welding
table itself provided it is metallic or wilt conduct
electricity!
OPERATING INSTRUCTIONS
We feel that welding with your new Craftsman dual
range arc welder is as simple as A.B.C.
A. Determine what diameter electrode should be
used by gauging the piece to be welded on the
material thickness gauge. The fractional
number directly beneath the bar chart dictates
what the proper electrode diameter is for given
thicknesses of metals. You will note that a
specific diameter of electrodes can be used on
varying thicknesses of material. This is
accomplished by adjusting the heat selector, for
more or less amperage.
B. Next verify the electrode diameter, by placing
the bare portion of the electrode against the
electrode diameter gauge located under the bar
chart.
Because electrodes are mass produced, there
may be small burrs on the bare ends of the
electrode. Make sure the bare end of the rod is
as clean as possible for accurate sizing.
C. Finally, determine the type of electrode by the
identification on the package or by the
American Welding Society number stencilled
on the coated portion of the electrode, bearing
in mind the type of electrode you have chosen
E6013 or E7014, and also its' diameter (as
previously determined).
Locate that band on the amp scale. There are
two E6013 bands and two E7014 bands, use the
band which coordinates with the amp rangeyou
have selected.
7
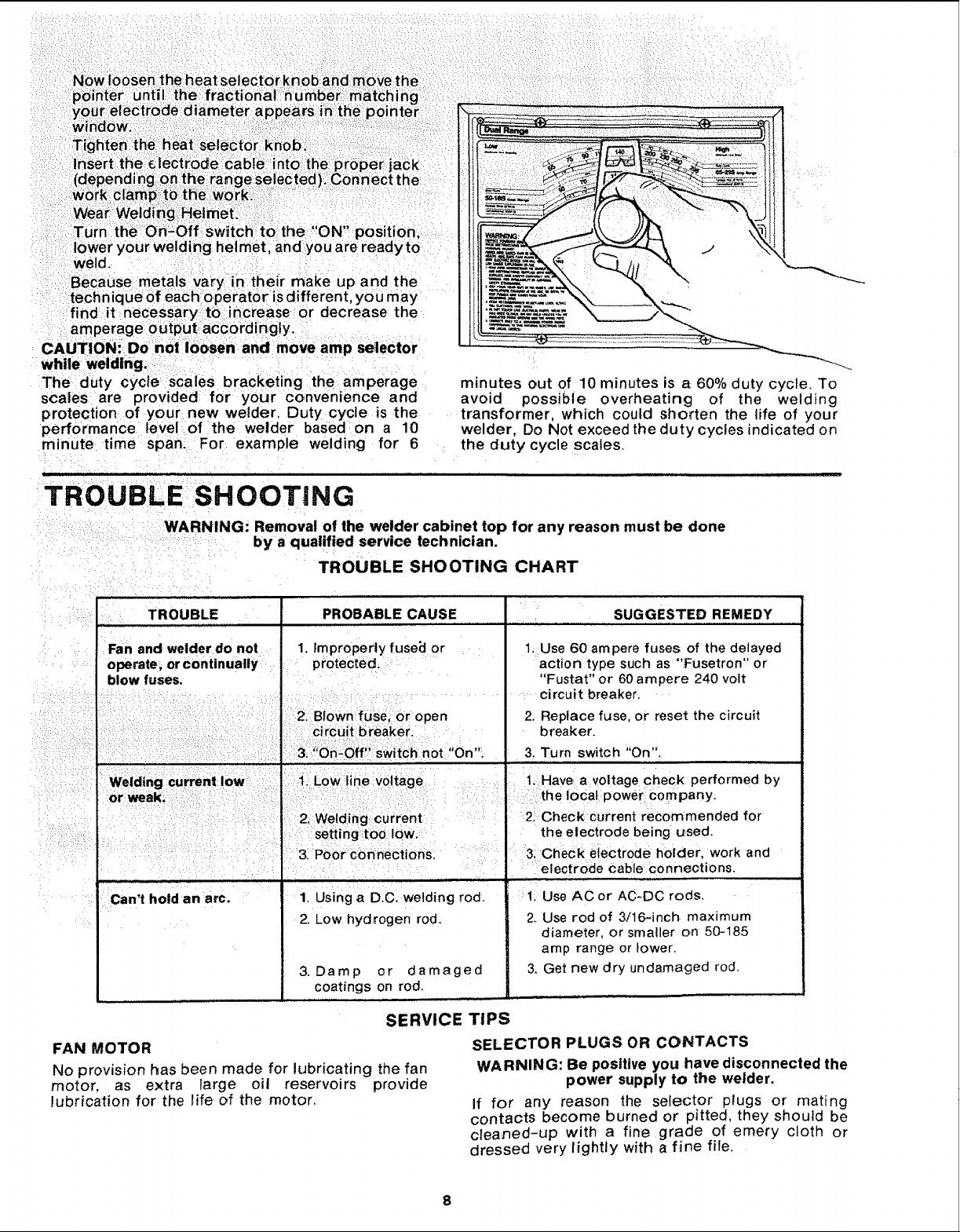
weld.
Because metals vary {n their make up and the
technique of each operat0r is different, you may
find it necessary to: increase: or decrease the
amperage output accord!ngly.
CAUTION: Donol loosen and move amp se|ector
while welding..
The duty cycle scales bracketing the amperage
sca':les are provided for your convenience and
protection of your new weGder. Duty cycle is the
performance level of the welder based on a 10
minute time span. For example welding for 6
TROUBLE SHOOTING
minutes out of 10 minutes is a 60% duty cycle. To
avoid possible overheating of the welding
transformer, which could shorten the life of your
welder, Do Not exceed the duty cycles indicated on
the duty cycle scales.
WARNING: Removal of the welder cabinet top for any reason must be done
TROUBLE , SUGGESTED REMEDY
Fan and welder do not 1. Improperly fuse_l or 1. Use 60 ampere fuses of the delayed
operate; orcontinually : protected, action type such as "Fusetron" or
blow fuses. ' : "Fustat" or 60 ampere 240 volt
i; Welding current low: !i:i i'::':_ilLow ine voi'tage , "t. Have a voltage 'c'heck performed by
or:weak; : ! ; :/ : :the local powerl Company.
.... : I: Welding current I 2! Check current recommended for
: : : ! : setting:too Iowl I the electrode being used.
...... :- : : iI 3 P0or:c0nnect ons I 3: Check eiectrode holder work and
Can't hold an arc.
by a q ualified service technician.
TROUBLE SHOOTING CHART
PROBABLE CAUSE
I ................ circuit breaker.
i 2, Blown:fuse,; or open 2. Replace fuse, or reset the circuit
Circuitbreaker. breaker.
.3,?"OPi:-0ff":switch not "On". 3. Turn switch _'On".
; I : ..... .... : electrode Cable Connections.
1. Using a D.C. welding rod.
2. Low hydrogen rod.
3. Damp or damaged
coatings on rod.
i 1: Use ACor AC-DC rods.
2. Use rod of 3/16-inch maximum
diameter, or smaller on 50-185
amp range or lower.
3. Get new dry undamaged rod.
SERVICE TIPS
FAN MOTOR
No provision has been made for lubricating the fan
motor, as extra large oil reservoirs provide
lubrication for the life of the motor.
SELECTOR PLUGS OR CONTACTS
WARNING: Be positive you :have disconnected the
power supply to the welder.
If for any reason the selector plugs or mating
contacts become burned or pitted, they should be
cleaned-up with a fine grade of emery cloth or
dressed very lightly with a fine fife.
8
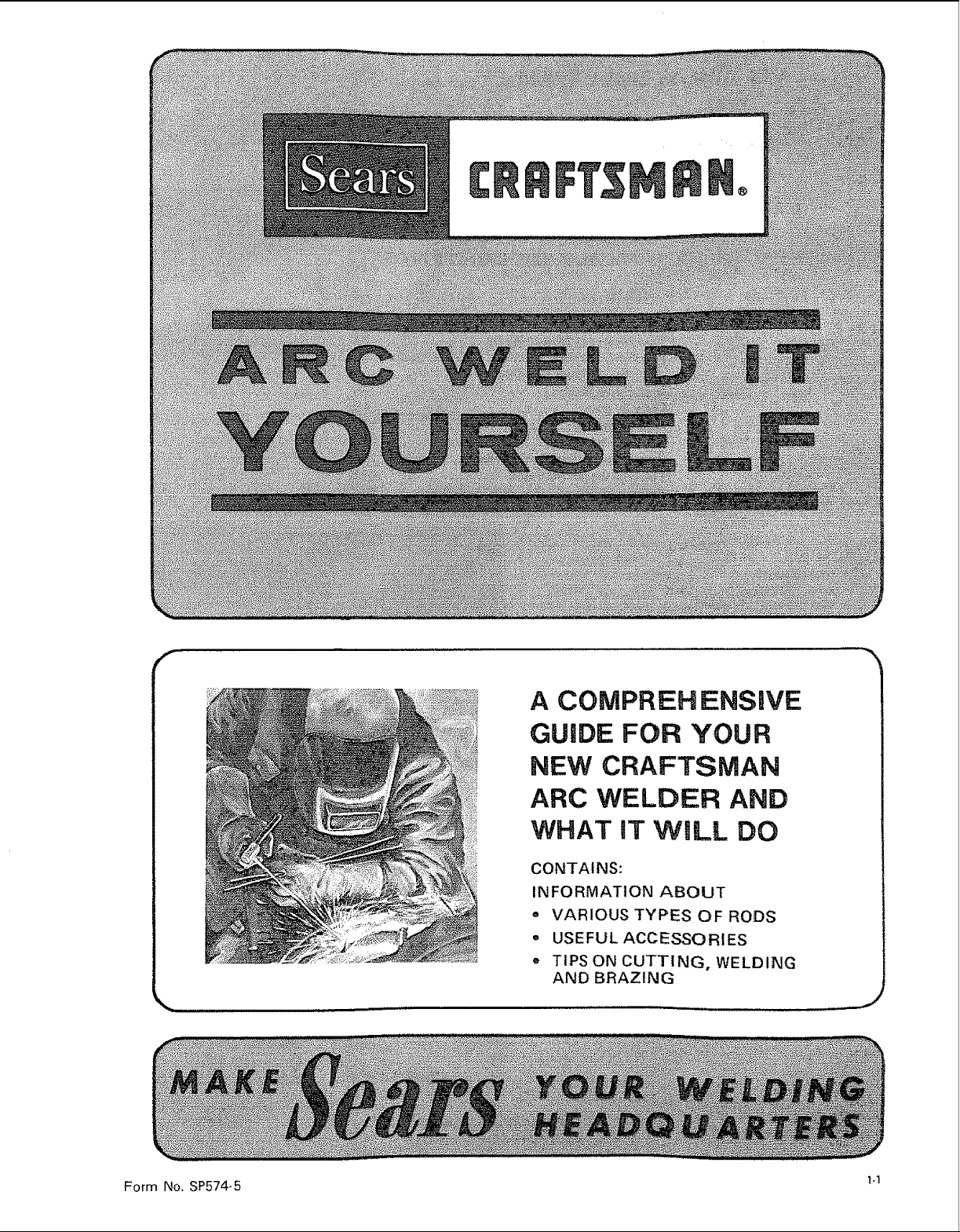
fl
%_
A COMPREH ENSIVE
GUIDE FOR YOUR
NEW CRAFTSMAN
ARC WELDER AND
WHAT iT W=ILL DO
CONTAt NS:
INFORMATION ABOUT
o VARIOUS TYPES OF RODS
o USEFUL ACCESSORIES
e TIPS ON CUTTING, WELDING
AND BRAZING
,,J
Form No. SP574+5 t.1
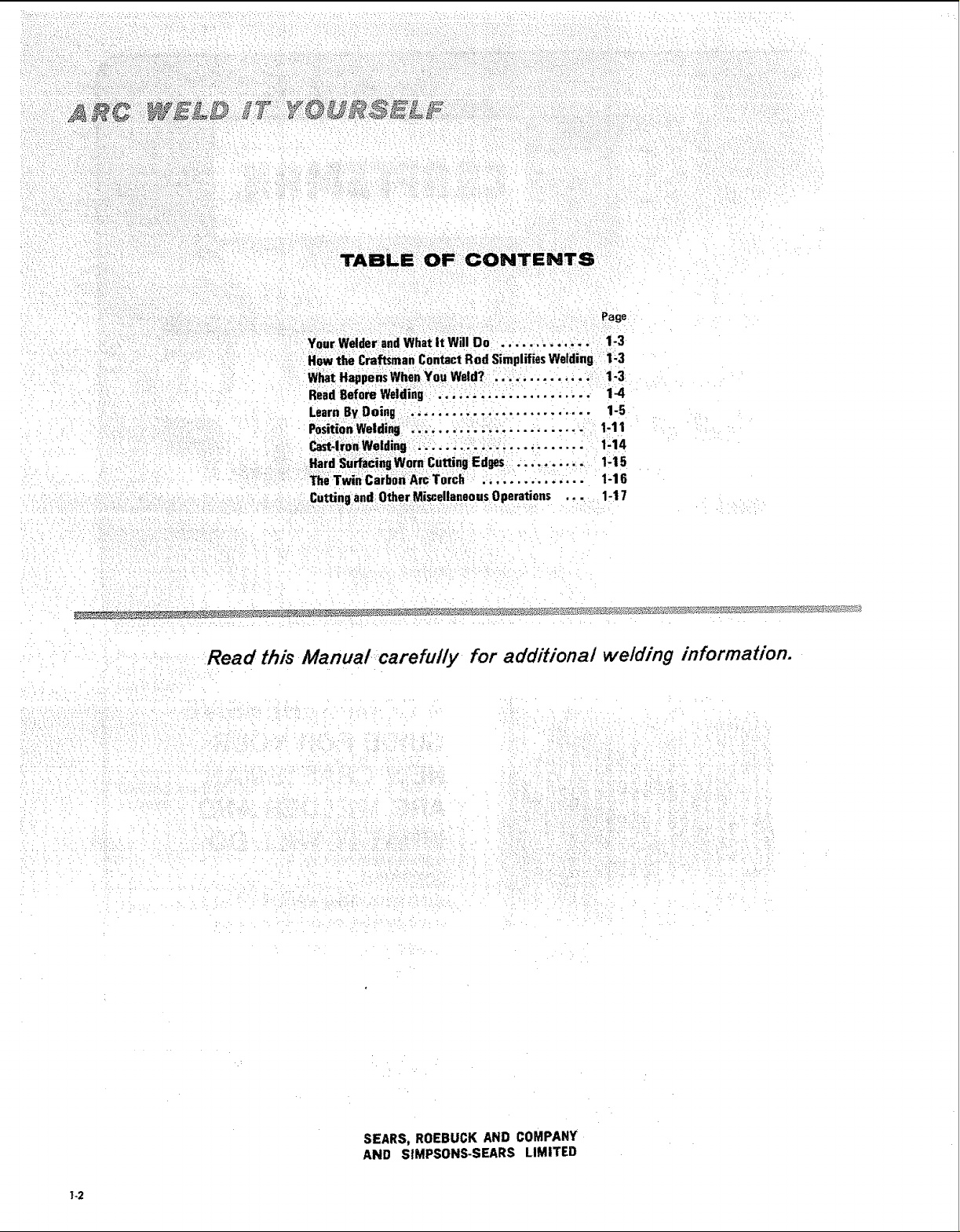
_i_?/:-: ¸ _:!. ......
TABLE OF _cONTENTs
_iii_!i.i___
Page
Your WelderandWhatit Will Do ............. 1-3
Howthe CraftSmanCOntactRod SimplifiesWelding 1-3
WhatHappensWhenYou Weld? .. .......... 1-3
RoadeefareWeiding .:i._._,.!..:,....i.,.... 1-4
LearnBy Doing ........................... 1-5
PositionWelding ......................... 1-11
Cast4ronWelding....; .... ...... . 1-14
.a,dSu ,,=jn.Wor,,C. .gEd,-IIZ 1-15
TheTwin CarbonArc Torch ............... 1-16
CuttingandOtherMiscellaneousOperations ... 1-17
Read this Manual carefully for additional welding information.
1.2
. _ ••• H• •••• H•¸
SEARS, ROEBUCK AND COMPANY
AND S|MPSONS-SEARS LIMITED
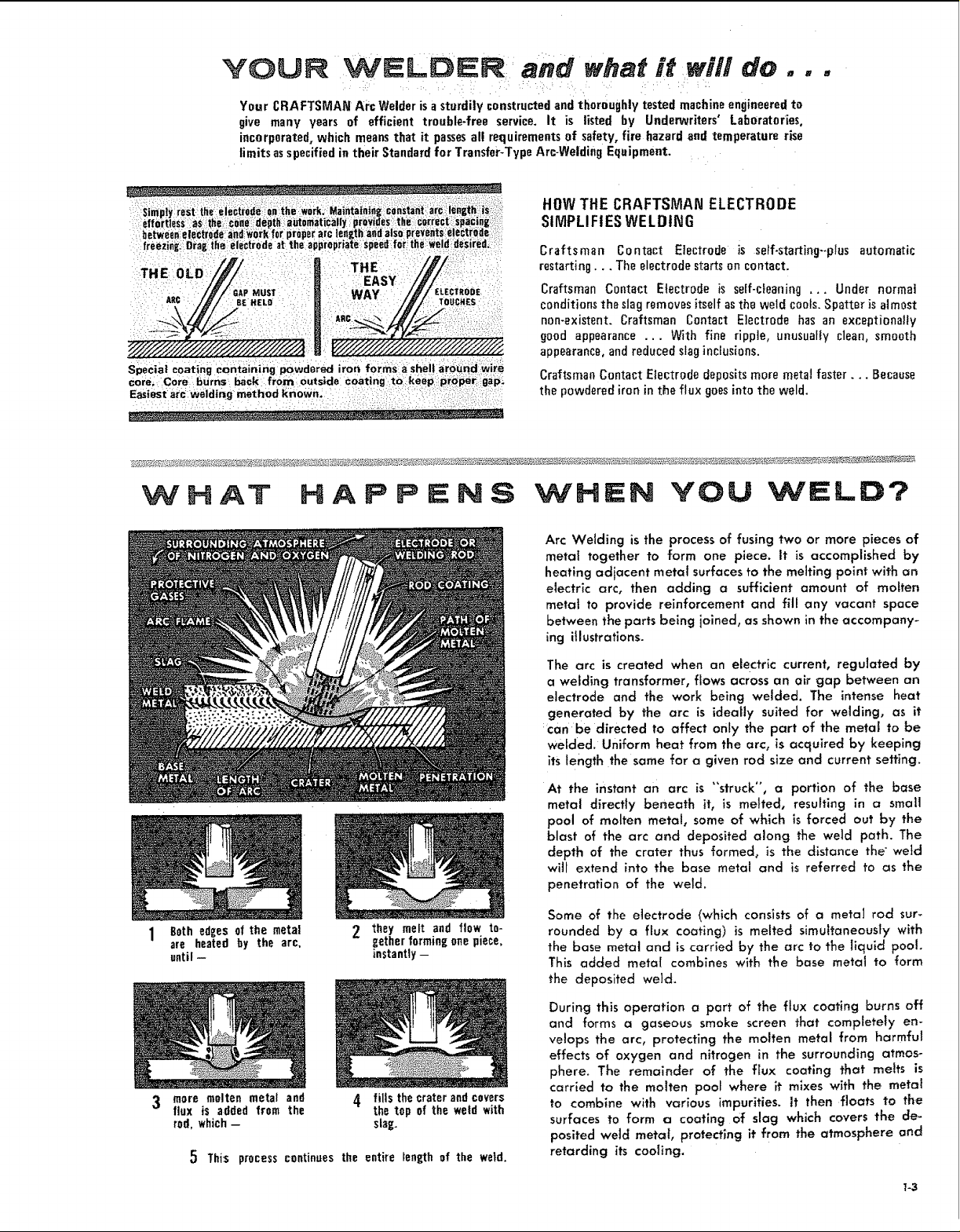
YOUR WELDER and what H wil/ do . .
Your CRAFTSMAN ArcWelderisa sturdilyconstructedandthoroughlytestedmachineengineeredto
give many years of efficient trouble-freeservice. It is listed by Underwriters' Laboratories,
incorporated,whichmeansthat it passesal! requirementsof safety, fire hazardand temperaturerise
limitsasspecifiedin their Standardfor Transfer-TypeArc-WeldingEquipment.
S reply rest the electrode :an the iwork, Maintaining consta_nt:arcilength::is _
effortless as the cOne_:depth aOtomatiCaly pt+oydes the correct! spacin[i
betweenelectr#de:a:ndlw0rkfor properarc length andals0 p{ev _ht_,e ei_trede
freezinj Drag the electrode at the appropriate speed f0r the Weld:desired_:
E
,ec/_'/_# MUSe' WAY /Ji''LoEC_OOe
HOWTHE CRAFTSMAN ELECTRODE
SIMPLIFIES WELDING
Craftsman Contact Electrode is se/f-starting--p{usautomatic
restarting... The electrode startson contact.
Craftsman Contact Electrode is self-cleaning... Under normal
conditionstheslagremovesitselfastheweld cools.Spatter is almost
non-exiszent. Craftsman Contact Electrode has an exceptionally
good appearance... With fine ripple, unusuafiyclean, smooth
appearance,andreducedslaginclusions.
Special coating containing powdered iron forms a shell around wire
Core, Core burns back from outside coating to keep proper: go:p;
Easiest arc_welding method known.
CraftsmanContact Electrodedepositsmoremetal faster... Because
the powderedironin the flux goesintothe weld.
W H AT H A P P N S WHEN YOU WELD?
Arc Welding isthe processof fusing two or more pieces of
metal together to form one piece. It is accomplished by
heating adjacent metal surfaces to the melting point with an
electric arc, then adding a sufficient amount of molten
metat to provide reinforcement and fill any vacant space
between the parts being ioined, asshown in the accompany-
ing itlustrations.
The arc is created when an electric current, regulated by
a welding transformer, flows across an air gap between an
electrode and the work being welded. The intense heat
generated by the arc is ideally suited for welding, as it
:can be directed to affect only the part of the metal to be
welded, uniform heat from the arc, is acquired by keeping
its length the same for a given rod size and current setting.
1 Bath edges of the metal
are heated by the arc,
until --
mare molten metal and
flux is added from the
rod, which-
5 This process continues the entire length of the weld.
2 _hey melt and flow to-
gether forming onepiece,
instantly -
4 fills thecrater andcovers
the top of the weld with
sing.
At the instant an arc is "struck", a portion of the base
metal directly beneath it, is melted, resulting in a small
pool of molten metal, some of which is forced out by the
blast of the arc a_d deposited along the weld path. The
depth of the crater thus formed, is the distance the" weld
will extend into the base metal and is referred to as the
penetration of the weld.
Some of the electrode (which consists of a metal rod sur-
rounded by a flux coating) is melted simuhaneousty with
the base metal and is carried by the arc to the liquid pool
This added mete! combines with the base metal to form
the deposited we}.d.
During this operation a part of the flux coating burns off
and forms a gaseous smoke screen that completely en-
ve!ops the arc, protecting the molten metal from harmful
effects of oxygen and nitrogen in the surrounding atmos-
phere. The remainder of the flux coating that melts is
carried to the molten pool where it mixes with th_ metal
to combine with various impurities. It then floats to the
surfaces to form a coating Of slag which covers the de-
posited weld metc_{,protecting it from the atmosphere and
retarding its coollng.