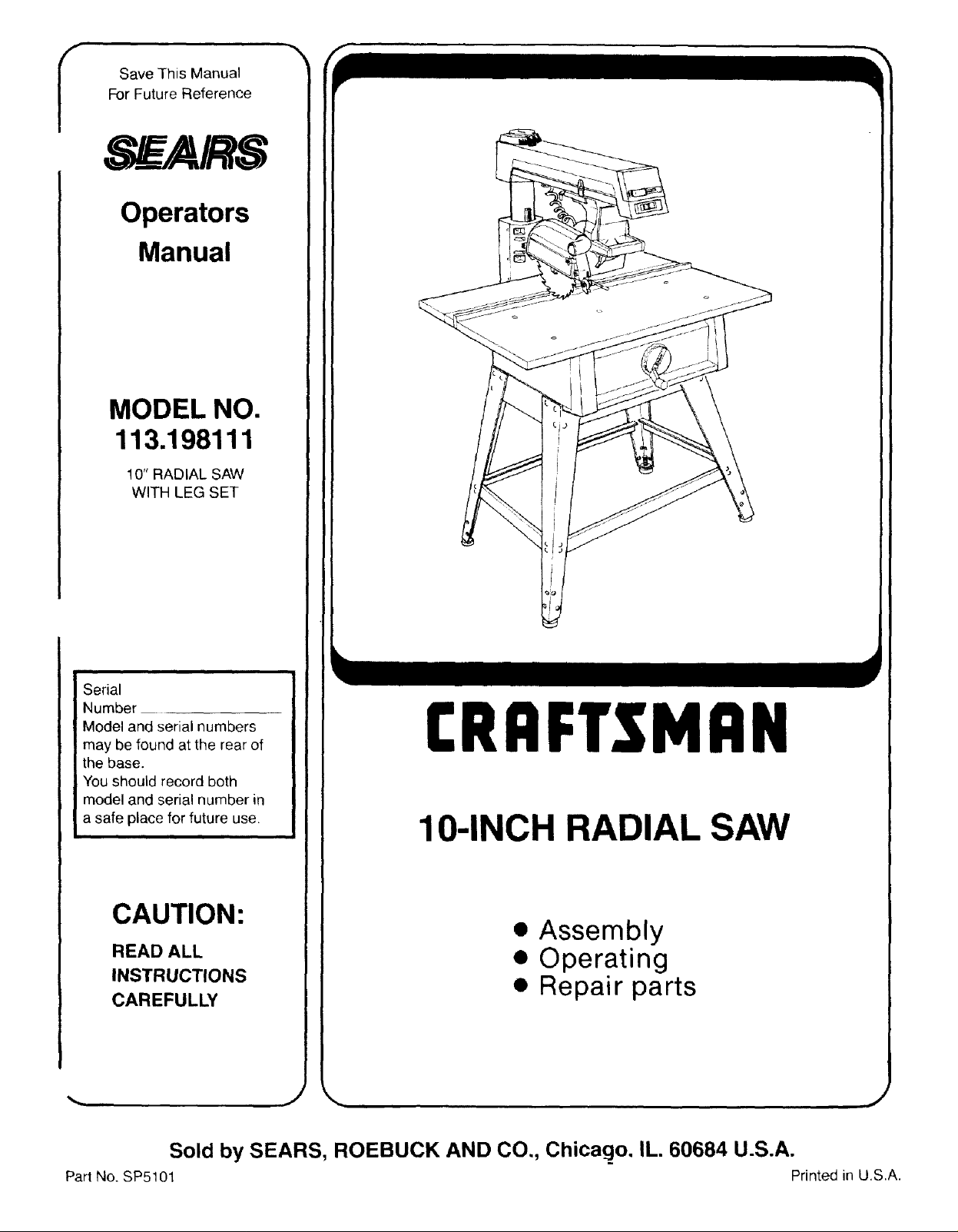
Save This Manual
For Future Reference
_AIRS
Operators
Manual
MODEL NO.
113.198111
10" RADIAL SAW
WITH LEG SET
,,,,,,,,,,,,,,,,
Serial
Number
Model and serial numbers
may be found at the rear of
the base.
You should record both
model and serial number in
a safe place for future use.
CAUTION:
READ ALL
INSTRUCTIONS
CAREFULLY
I:RRFTSMRN
10-INCH RADIAL SAW
• Assembly
• Operating
• Repair parts
Sold by SEARS, ROEBUCK AND CO., Chicag_o. IL. 60684 U.S.A.
Part No. SP5101 Printed in U.S.A.
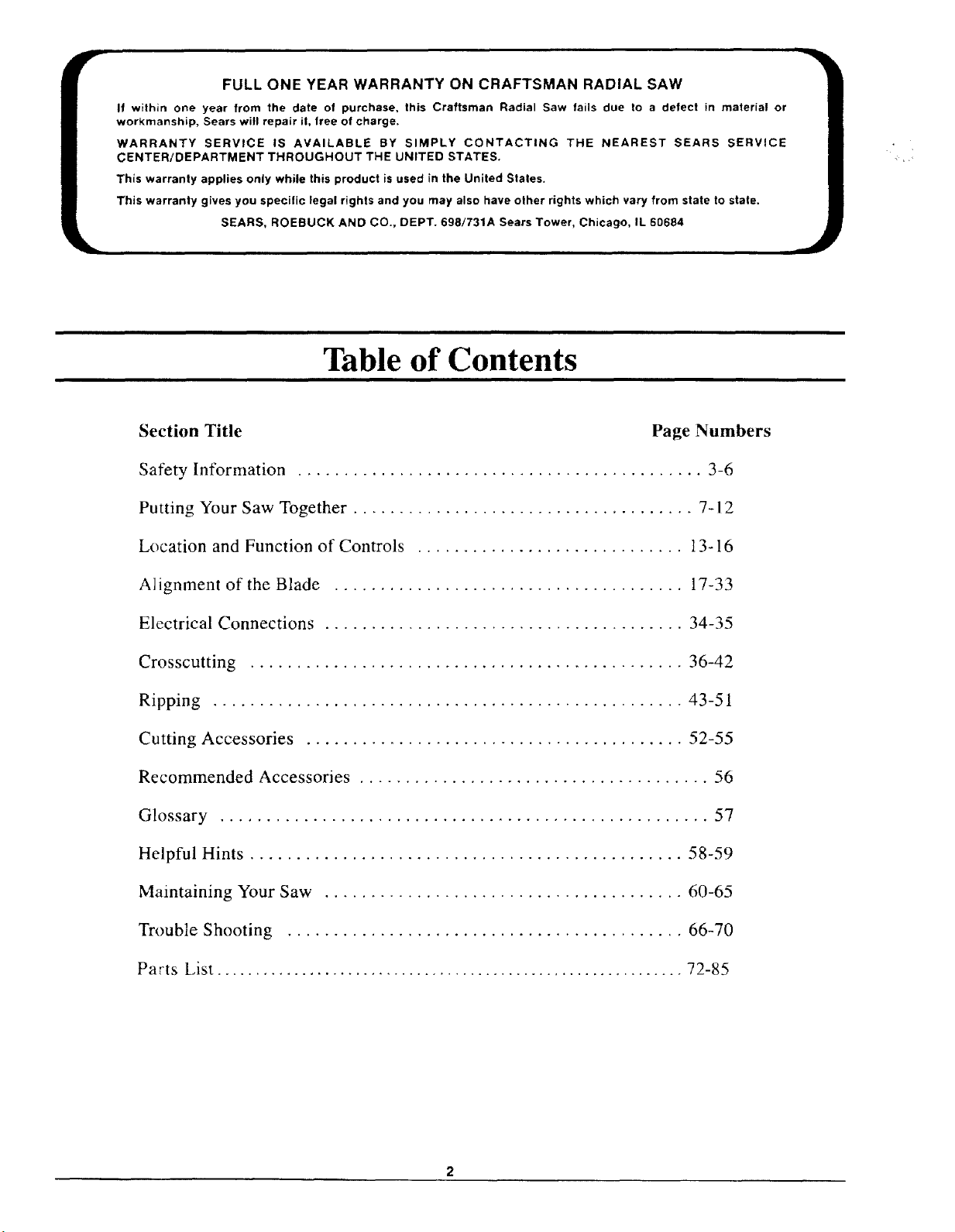
FULL ONE YEAR WARRANTY ON CRAFTSMAN RADIAL SAW
If within one year from the date of purchase, this Craftsman Radial Saw fails due to a defect in material or
workmanship, Sears will repair il, tree of charge.
WARRANTY SERVICE IS AVAILABLE BY SIMPLY CONTACTING THE NEAREST SEARS SERVICE
CENTER/DEPARTMENT THROUGHOUT THE UNITED STATES.
This warranty applies only while this product is used in the United States.
This warranty gives you specilic legal rights and you may also have other rights which vary from state to stale.
SEARS, ROEBUCK AND CO., DEPT. 698/731A Sears Tower, Chicago, IL 60684
Table of Contents
Section Title Page Numbers
Safety Information ............................................ 3-6
ii
Putting Your Saw Together ..................................... 7-12
Location and Function of Controls ............................. 13-16
Alignment of the Blade ...................................... 1%33
Electrical Connections ....................................... 34-35
Crosscutting ............................................... 36-42
Ripping ................................................... 43-51
Cutting Accessories ......................................... 52-55
Recommended Accessories ...................................... 56
Glossary ..................................................... 57
Helpful Hints ............................................... 58-59
Maintaining Your Saw ....................................... 60-65
Trouble Shooting ........................................... 66-70
Parts List ............................................................. 72-85
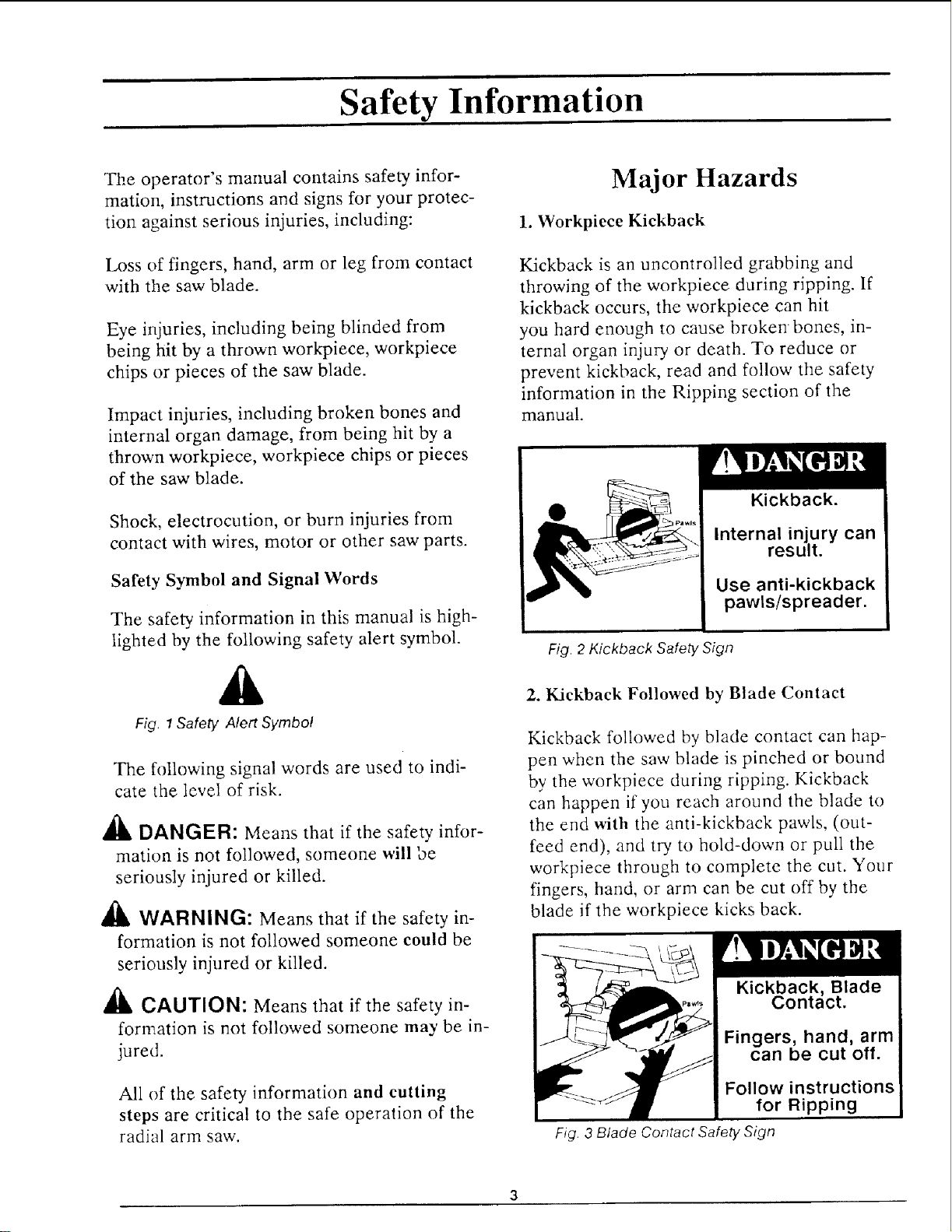
Safety Information
The operator's manual contains safety infor-
mation, instructions and signs for your protec-
tion against serious injuries, including:
Loss of fingers, hand, arm or leg from contact
with the saw blade.
Eye injuries, including being blinded from
being hit by a thrown workpiece, workpiece
chips or pieces of the saw blade.
Impact injuries, including broken bones and
internal organ damage, from being hit by a
thrown workpiece, workpiece chips or pieces
of the saw blade.
Shock, electrocution, or burn injuries from
contact with wires, motor or other saw parts.
Safety Symbol and Signal Words
The safety information in this manual is high-
lighted by the following safety alert symbol.
Major Hazards
1. Workpiece Kickback
Kickback is an uncontrolled grabbing and
throwing of the workpiece during ripping. If
kickback occurs, the workpiece can hit
you hard enough to cause broken bones, in-
ternal organ injury or death. To reduce or
prevent kickback, read and follow the safety
information in the Ripping section of the
manual.
Kickback.
Internal injury can
result.
Use anti-kickback
pawls/spreader.
Fig, 2 Kickback Safety Sign
Fig. 1Safety Alert Symbol
The following signal words are used to indi-
cate the level of risk.
DANGER: Means that if the safety infor-
mation is not followed, someone will be
seriously injured or killed.
WARNING: Means that if the safety in-
formation is not followed someone could be
seriously injured or killed.
CAUTION: Means that if the safety in-
formation is not followed someone may be in-
jured.
All of the safety information and cutting
steps are critical to the safe operation of the
radial arm saw.
2. Kickback Followed by Blade Contact
Kickback followed by blade contact can hap-
pen when the saw blade is pinched or bound
by the workpiece during ripping. Kickback
can happen if you reach around the blade to
the end with the anti-kickback pawls, (out-
feed end), and try to hold-down or pull the
workpiece through to complete the cut. Your
fingers, hand, or arm can be cut off by the
blade if the workpiece kicks back.
Kickback, Blade
Contact.
Fingers, hand, arm
can be cut off.
Follow instructions
for Ripping
Fig. 3 Blade Contact Safety Sign
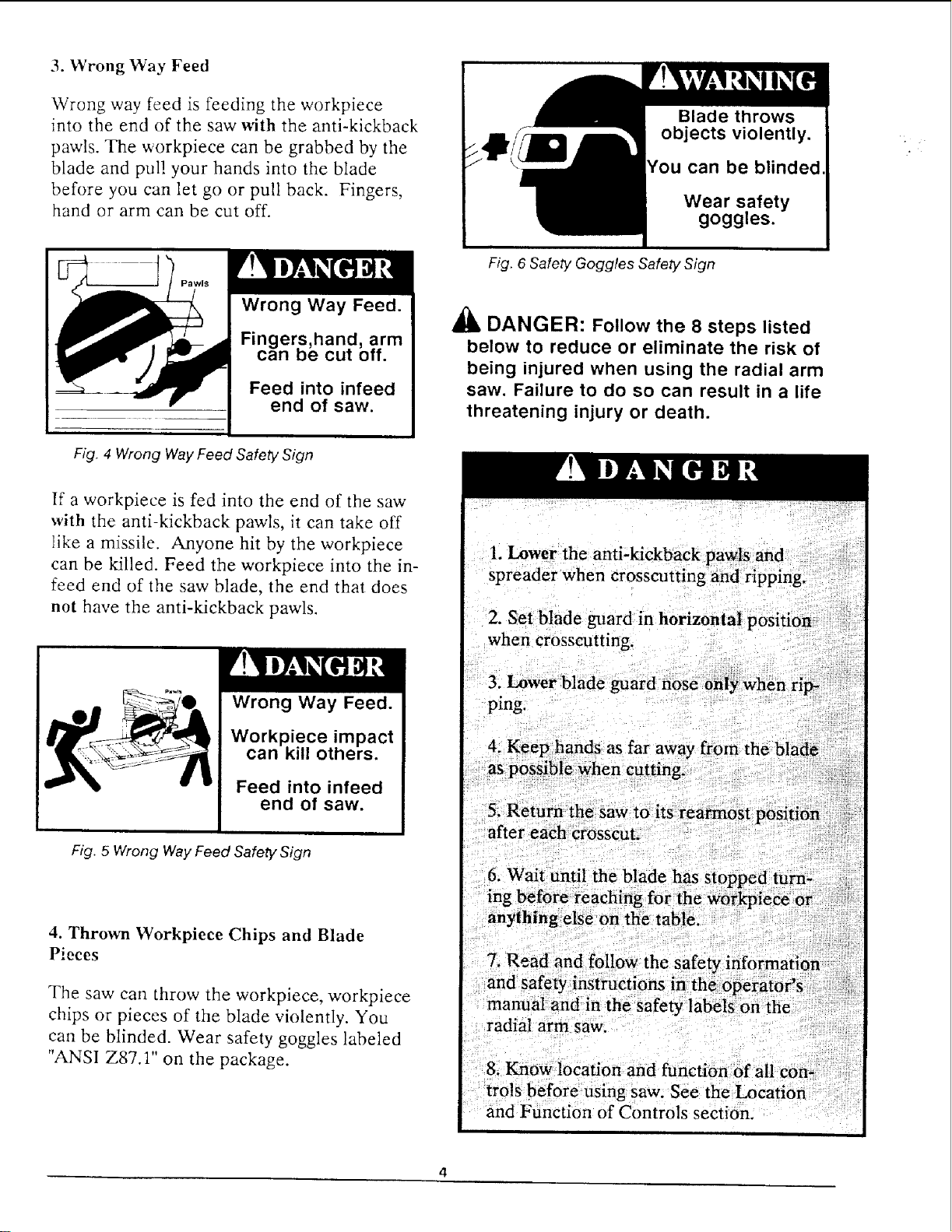
3. Wrong Way Feed
Wrong way feed is feeding the workpiece
into the end of the saw ,Mth the anti-kickback
pawls. The workpiece can be grabbed by the
blade and pul! your hands into the blade
before you can let go or pull back. Fingers,
hand or arm can be cut off.
Wrong Way Feed.
Fingers,hand, arm
can De cut off.
Feed into infeed
end of saw.
Fig, 4 Wrong WayFeed Safety Sign
If a workpiece is fed into the end of the saw
with the anti-kickback pawls, it can take off
like a missile. Anyone hit by the workpiece
can be killed. Feed the workpiece into the in-
feed end of the saw blade, the end that does
not have the anti-kickback pawls.
can be blinded
Wear safety
goggles.
Fig. 6 Safety Goggles Safety Sign
_k DANGER: Follow the 8 steps listed
below to reduce or eliminate the risk of
being injured when using the radial arm
saw. Failure to do so can result in a life
threatening injury or death.
can kill others.
__, _ Workpiece impact
Fig. 5 Wrong Way Feed Safety Sign
4. Thrown Workpiece Chips and Blade
Pieces
The saw can throw the workpiece, workpiece
chips or pieces of the blade violently. You
can be blinded. Wear safety goggles labeled
"ANSI Z87.1" on the package.
_ fli Feed into infeed
iWr°n Wa e "I
end of saw.
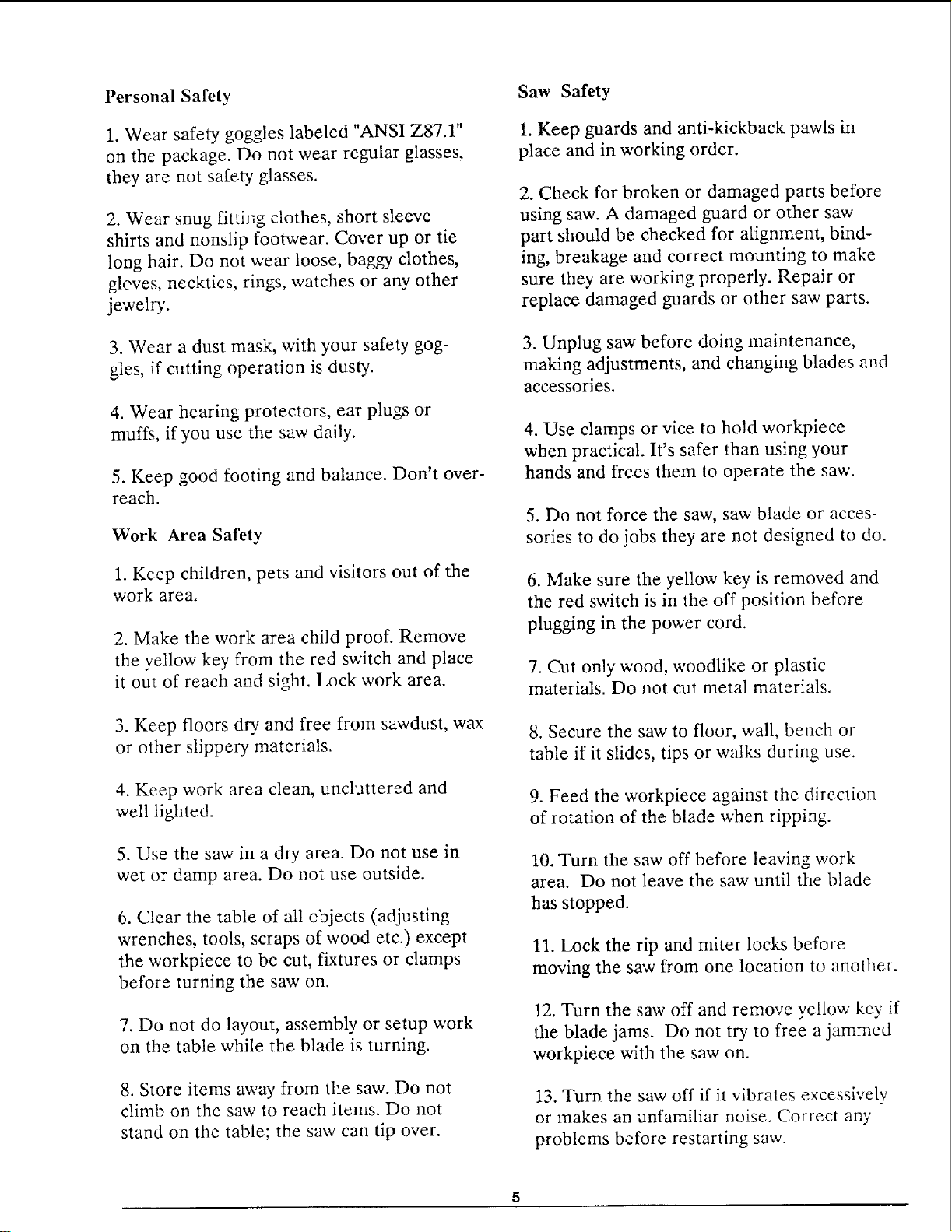
Personal Safety
Saw Safety
1. Wear safety goggles labeled "ANSI Z87.1"
on the package. Do not wear regular glasses,
they are not safety glasses.
2. Wear snug fitting clothes, short sleeve
shirts and nonslip footwear. Cover up or tie
long hair. Do not wear loose, bag_ clothes,
gloves, neckties, rings, watches or any other
jewelry.
3. Wear a dust mask, with your safety gog-
gles, if cutting operation is dusty.
4. Wear hearing protectors, ear plugs or
muffs, if you use the saw daily.
5. Keep good footing and balance. Don't over-
reach.
Work Area Safety
1. Keep children, pets and visitors out of the
work area.
2. Make the work area child proof. Remove
the yellow key from the red switch and place
it out of reach and sight. [x)ck work area.
1. Keep guards and anti-kickback pawls in
place and in working order.
2. Check for broken or damaged parts before
using saw. A damaged guard or other saw
part should be checked for alignment, bind-
ing, breakage and correct mounting to make
sure they are working properly. Repair or
replace damaged guards or other saw parts.
3. Unplug saw before doing maintenance,
making adjustments, and changing blades and
accessories.
4. Use clamps or vice to hold workpiece
when practical. It's safer than using your
hands and frees them to operate the saw.
5. Do not force the saw, saw blade or acces-
sories to do jobs they are not designed to do.
6. Make sure the yellow key is removed and
the red switch is in the off position before
plugging in the power cord.
7. Cut only wood, woodlike or plastic
materials. Do not cut metal materials.
3. Keep floors dry and free from sawdust, wax
or other slippery materials.
4. Keep work area clean, uncluttered and
well lighted.
5. Use the saw in a dry area. Do not use in
wet or damp area. Do not use outside.
6. Clear the table of all objects (adjusting
wrenches, tools, scraps of wood etc.) except
the workpiece to be cut, fixtures or clamps
before turning the saw on.
7. Do not do layout, assembly or setup work
on the table while the blade is turning.
8. Store items away from the saw. Do not
climb on the saw to reach items. Do not
stand on the table; the saw can tip over.
8. Secure the saw to floor, wall, bench or
table if it slides, tips or walks during use.
9. Feed the workpiece against the direction
of rotation of the blade when ripping.
10. Turn the saw off before leaving work
area. Do not leave the saw until the blade
has stopped.
11. Lock the rip and miter locks before
moving the saw from one location to another.
12. Turn the saw off and remove yellow key if
the blade jams. Do not try to free a jammed
workpiece with the saw on.
13. Turn the saw off if it vibrates excessively
or makes an unfamiliar noise. Correct any
problems before restarting saw.
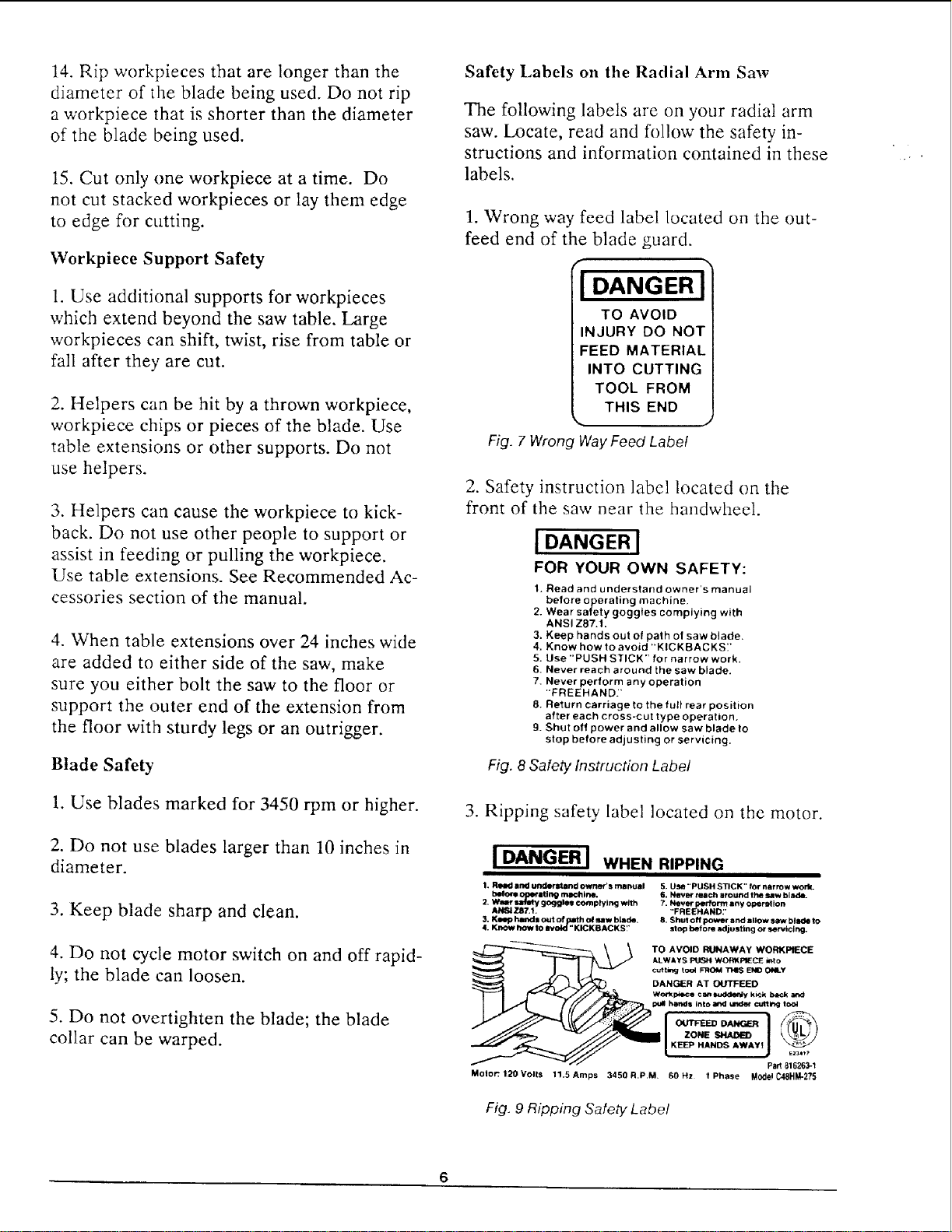
14.Rip workpiecesthat arelonger thanthe
diameter of the blade being used.Do not rip
aworkpiece that isshorter than thediameter
of the blade beingused.
15.Cut only oneworkpiece at a time. Do
not cut stackedworkpiecesor lay themedge
to edgefor cutting.
Workpiece Support Safety
Safety Labels on the Radial Arm Saw
The following labels are on your radial arm
saw. Locate, read and follow the safety in-
structions and information contained in these
labels.
1. Wrong way feed label located on the out-
feed end of the blade guard.
f
1. Use additional supports for workpieces
which extend beyond the saw table. Large
workpieces can shift, twist, rise from table or
fall after they are cut.
2. Helpers can be hit by a thrown workpiece,
workpiece chips or pieces of the blade. Use
table extensions or other supports. Do not
use helpers.
3. Helpers can cause the workpiece to kick-
back. Do not use other people to support or
assist in feeding or pulling the workpiece.
Use table extensions. See Recommended Ac-
cessories section of the manual.
4. When table extensions over 24 inches wide
are added to either side of the saw, make
sure you either bolt the saw to the floor or
support the outer end of the extension from
the floor with sturdy legs or an outrigger.
Blade Safety
[ DANGER
TO AVOID
INJURY DO NOT
FEED MATERIAL
INTO CUTTING
TOOL FROM
THIS END
Fig. 7 Wrong Way Feed Label
2. Safety instruction label located on the
front of the saw near the hai_dwheel.
I DANGERI
FOR YOUR OWN SAFETY:
1. Read and understand owner's manual
before operating machine,
2. Wear safety goggles complying with
ANSI Z87.1.
3. Keep hands out of path of saw blade,
4, Know how to avoid "KICKBACKS:
5. Use "'PUSH STICK" for narrow work.
6. Never reach around the saw blade.
7. Never perform any operation
"FREEHAND:'
8. Return carriage to the full rear position
after each cross-cut type operation.
9. Shut off power and allow saw blade to
stop before adjusting or servicing,
Fig. 8 Safety Instruction Label
1. Use blades marked for 3450 rpm or higher.
2. Do not use blades larger than 10 inches in
diameter.
3. Keep blade sharp and clean.
4. Do not cycle motor switch on and off rapid-
ly; the blade can loosen.
5. Do not overtighten the blade; the blade
collar can be warped.
3. Ripping safety label located on the motor.
I DANGER I WHEN RIPPING
1. Read and understand owner's manual 5. Use "PUSH STICK" tor narrow work.
belore atln9 machine.
Wirer IOper'safetygoggles c_mptyin_J with 6. Nevs.r reach aroulld the saw blade_2.
ANS_ Z87.1. "FREEHAND;'
4.3'Keep hlmdl out OfKnow row to h ol saw blade, st op before adjusting or servlclr'_g.
Motor: 120 Volts 11.5 Amps 3450 RP.M. 60 Hz 1 Phase Mode! C48HM-275
Fig. 9 Ripping Safety Labe!
Iv_" KICKBACKS" 8. Shut off power and allow saw bl_ to
7. Never perform any opermllon
cuttkng tool FROM "fTIIS END ONLY
TO AVOID F_INAWAY WORKPIECE
AI.W&YS _ W_PIECIE into
DANGER AT OUTFEED
hands into _'_:l under cui'llr_ to,_l
OU'rFEI_ D,_K?,ER
ZONE SHADED k
KEEP HANDS AWAY!
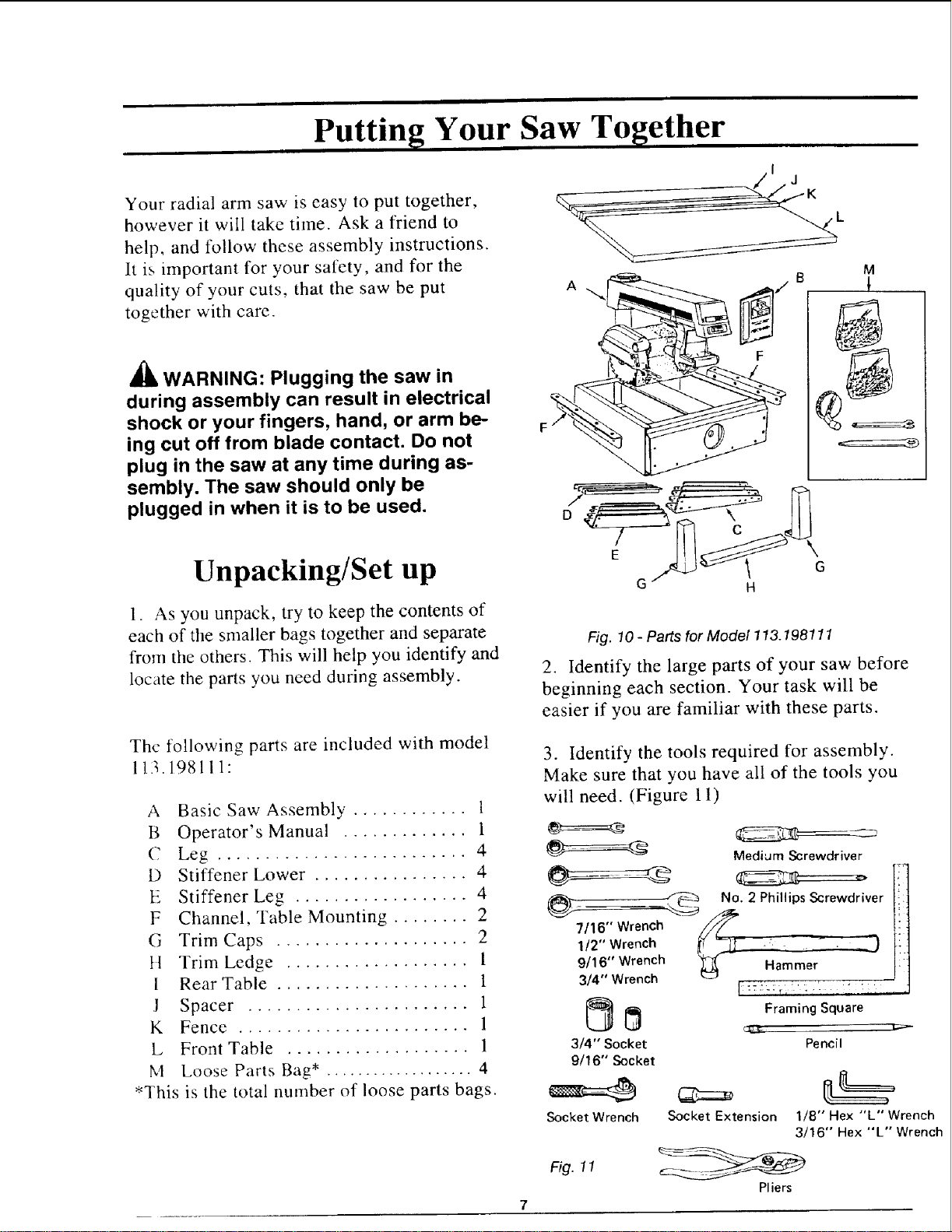
Putting Your Saw Together
Your radial arm saw is easy to put together,
however it will take time. Ask a friend to
help, and follow these assembly instructions.
It is important for your safety, and for the
quality of your cuts, that the saw be put
together with care.
WARNING: Plugging the saw in
during assembly can result in electrical
shock or your fingers, hand, or arm be-
ing cut off from blade contact. Do not
plug in the saw at any time during as-
sembly. The saw should only be
plugged in when it is to be used.
Unpacking/Set up
F
1. As you unpack, try to keep the contents of
each of the smaller bags together and separate
from the others. This will help you identify and
locate the parts you need during assembly.
The following parts are included with model
11_.1981 l l:
A Basic Saw Assembly ............ 1
B Operator's Manual ............. 1
C Leg .......................... 4
D Stiffener Lower ................ 4
E Stiffener Leg .................. 4
F Channel, Table Mounting ........ 2
G Trim Caps .................... 2
tf Trim Ledge ................... l
I Rear Table .................... 1
.I Spacer ....................... 1
K Fence ........................ 1
L Front Table ................... 1
M Loose Parts Bag* ................... 4
*This is the total number of loose parts bags.
Fig. 10 - Parts for Model 113.198111
2. Identify the large parts of your saw before
beginning each section. Your task will be
easier if you are familiar with these parts.
3. Identify the tools required for assembly.
Make sure that you have all of the tools you
will need, (Figure 11)
____
...... -_ Medium Screwdriver
7116" Wrench '///_
1/2" Wrench. _( _] . -, ., ._..)
9//16'_NWr::::h t_ Hammer
3/4'" Socket Pencil
9/16" Socket
Socket Wrench
Socket Extension 1/8" Hex "'L" Wrench
No. 2 Phillips Screwdriver 11
Framing Square
3/16" Hex "'L" Wrenct
7
Fig. 11
Pliers
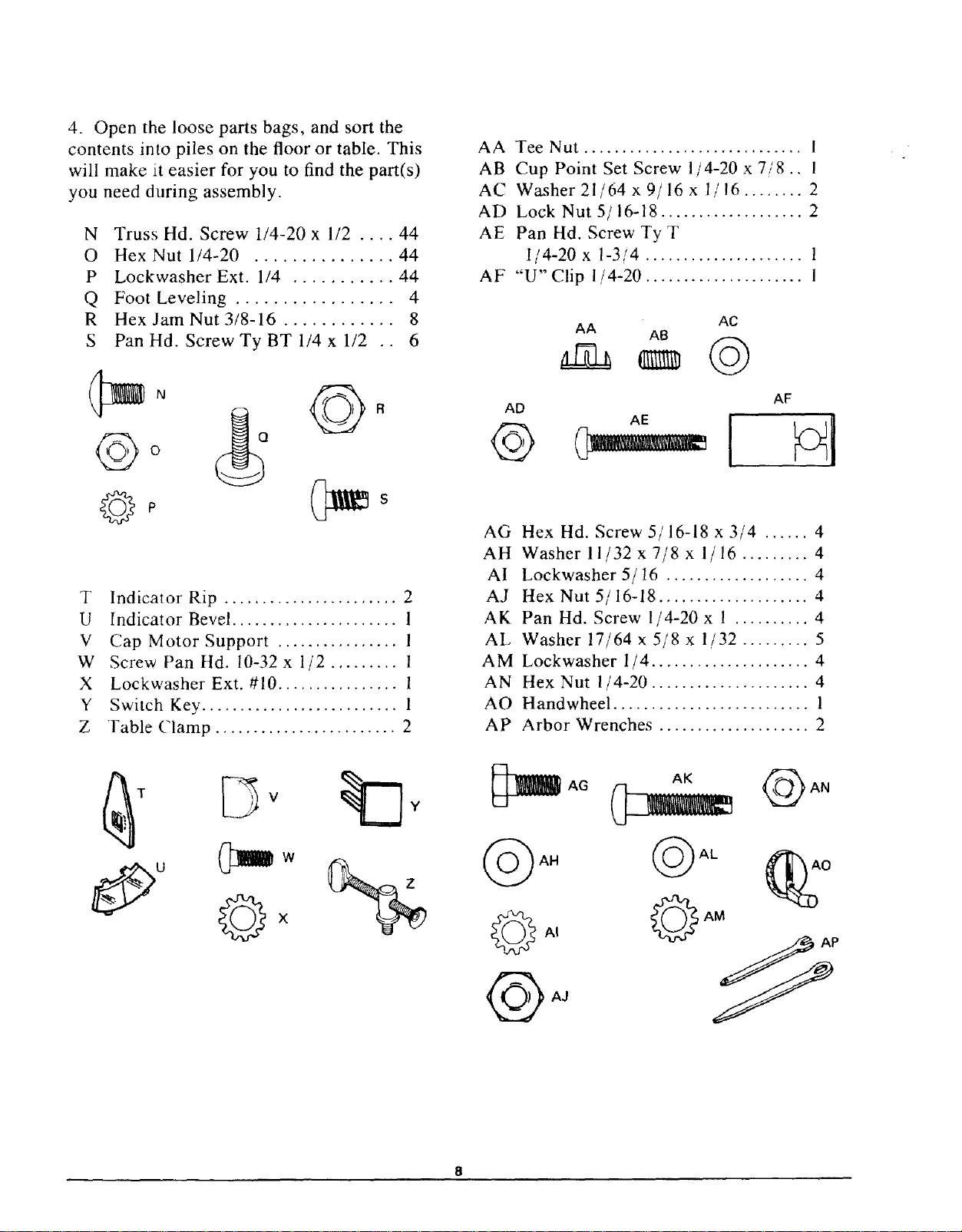
4. Open the loose parts bags, and sort the
contents into piles on the floor or table. This
will make it easier for you to find the part(s)
you need during assembly.
N Truss Hd. Screw 1/4-20 x 1/2 .... 44
O Hex Nut 1/4-20 ............... 44
P Lockwasher Ext. 1/4 ........... 44
Q Foot Leveling ................. 4
R Hex Jam Nut 3/8-16 ............ 8
S Pan Hd. Screw Ty BT 1/4 x 1/2 .. 6
AA Tee Nut ............................. 1
AB Cup Point Set Screw 1/4-20 x 7/8 .. 1
AC Washer21/64x9/16xl/16 ........ 2
AD Lock Nut 5/16-18 ................... 2
AE Pan Hd. Screw Ty T
I/4-20 x 1-3/4 ..................... !
AF "U" Clip 1/4-20 ..................... I
AC
AA AB
©
©
©
T Indicator Rip ....................... 2
U Indicator Bevel ...................... l
V Cap Motor Support ................ 1
W Screw Pan Hd. 10-32 x 1/2 ......... 1
X Lockwasher Ext. #10 ................ 1
Y Switch Key .......................... 1
Z Fable ('lamp ........................ 2
O
AD AF
AG Hex Hd. Screw 5/16-18 x 3/4 ...... 4
AH Washerll!32xT/Sxli16 ......... 4
AI Lockwasher 5/16 ................... 4
AJ Hex Nut 5/16-18 .................... 4
AK Pan Hd. Screw 1/4-20 x I .......... 4
AL Washer 17/64 x 5/8 x 1/32 ......... 5
AM Lockwasher I/4 ..................... 4
AN Hex Nut l/4-20 ..................... 4
AO Handwheel .......................... 1
AP Arbor Wrenches .................... 2
AG _ @ AN
AI 0 AM
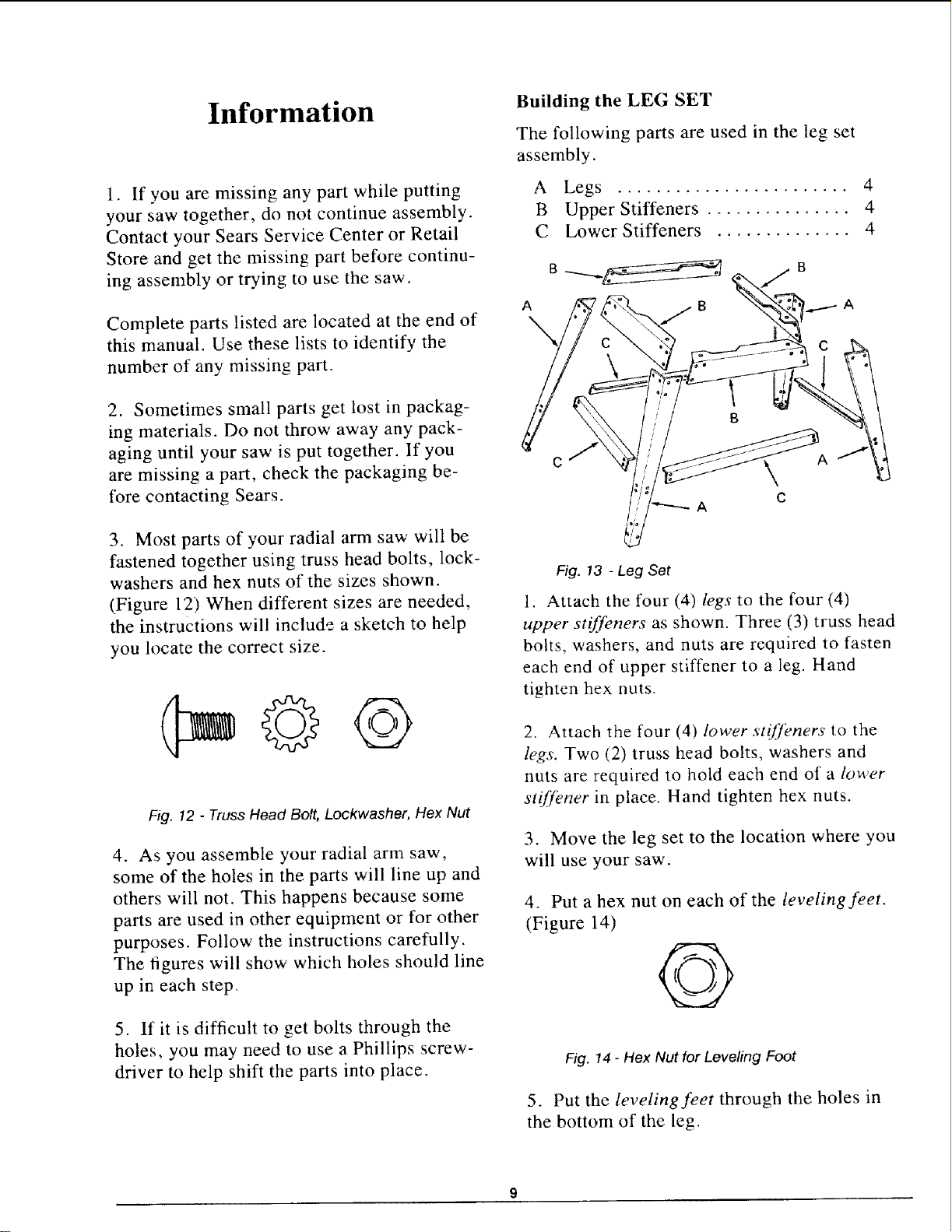
Information
Building the LEG SET
The following parts are used in the leg set
assembly.
1. If you are missing any part while putting
your saw together, do not continue assembly.
Contact your Sears Service Center or Retail
Store and get the missing part before continu-
ing assembly or trying to use the saw.
Complete parts listed are located at the end of
this manual. Use these lists to identify the
number of any missing part.
2. Sometimes small parts get lost in packag-
ing materials. Do not throw away any pack-
aging until your saw is put together. If you
are missing a part, check the packaging be-
fore contacting Sears.
3. Most parts of your radial arm saw will be
fastened together using truss head bolts, lock-
washers and hex nuts of the sizes shown.
(Figure 12) When different sizes are needed,
the instructions will include a sketch to help
you locate the correct size.
A Legs ........................ 4
B Upper Stiffeners ............... 4
C Lower Stiffeners .............. 4
A
/8 A
\
C
Fig. 13 -Leg Set
1. Attach the four (4) legs to the four (4)
upper st_['eners as shown. Three (3) truss head
bolts, washers, and nuts are required to fasten
each end of upper stiffener to a leg. Hand
tighten hex nuts.
Fig. 12 - Truss Head Bolt, Lockwasher, Hex Nut
4. As you assemble your radial arm saw,
some of the holes in the parts will line up and
others will not. This happens because some
parts are used in other equipment or for other
purposes. Follow the instructions carefully.
The figures will show which holes should line
up in each step.
5. If it is difficult to get bolts through the
holes, you may need to use a Phillips screw-
driver to help shift the parts into place.
2. Attach the four (4) lower st(/Jbners to the
legs, Two (2) truss head bolts, washers and
nuts are required to hold each end of a lower
st_['ener in place. Hand tighten hex nuts.
3. Move the leg set to the location where you
will use your saw.
4. Put a hex nut on each of the leveling feet.
(Figure 14)
Fig. 14 - Hex Nut for Leveling Foot
5. Put the leveling feet through the holes in
the bottom of the leg.
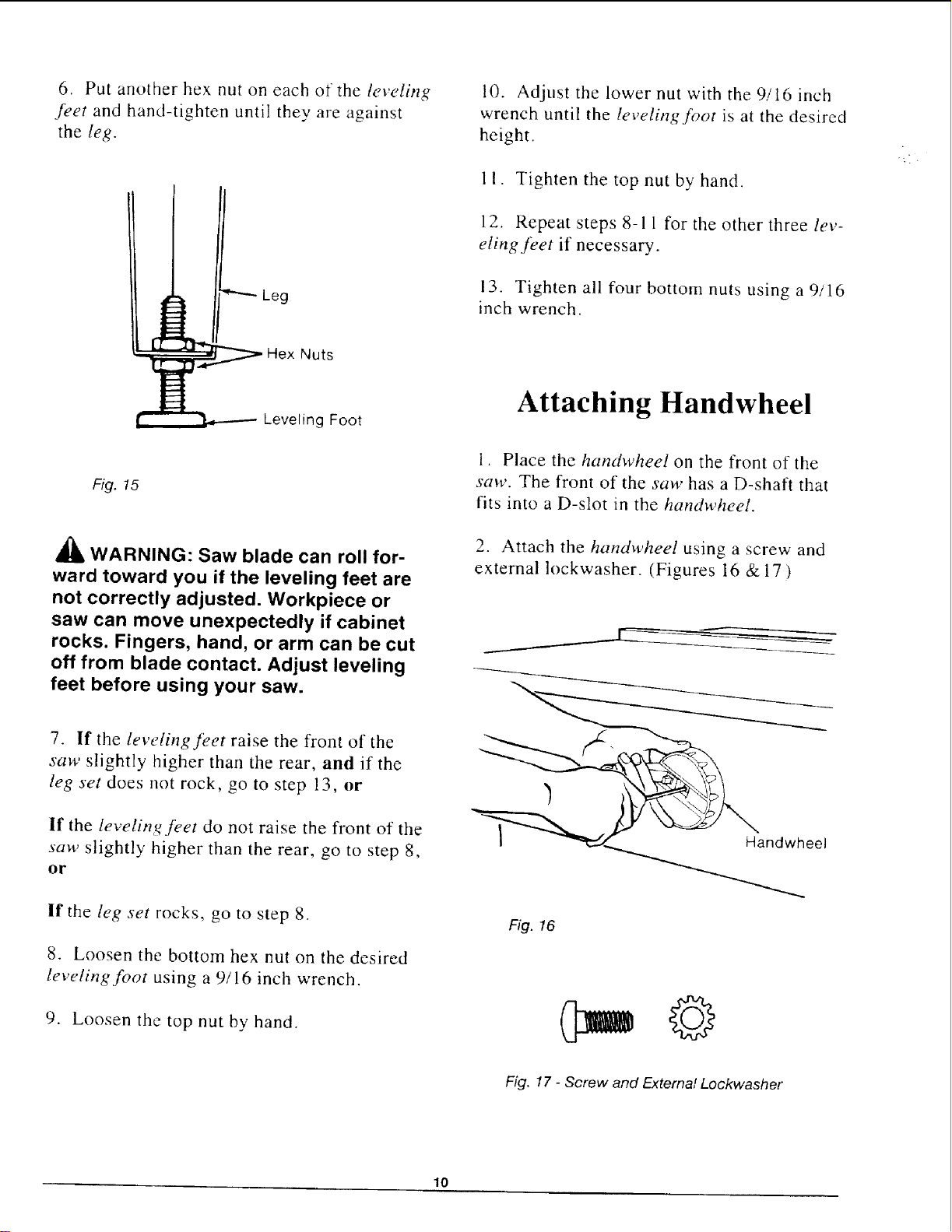
6. Put another hex nut on each of the leveling
,feet and hand-tighten until they are against
the leg.
10. Adjust the lower nut with the 9/16 inch
wrench until the leveling jbot is at the desired
height.
11. Tighten the top nut by hand.
12. Repeat steps 8-11 for the other three lev-
eling feet if necessary.
Leg
Nuts
Leveling Foot
Fig. 15
_lb WARNING: Saw blade can roll for-
ward toward you if the leveling feet are
not correctly adjusted. Workpiece or
saw can move unexpectedly if cabinet
rocks. Fingers, hand, or arm can be cut
off from blade contact. Adjust leveling
feet before using your saw.
13. Tighten all four bottom nuts using a 9/16
inch wrench.
Attaching Handwheel
1. Place the handwheel on the front of the
saw. The front of the saw has a D-shaft that
fits into a D-slot in the handwheel.
2. Attach the handwheet using a screw and
external lockwasher. (Figures 16 & 17 )
7. If the leveling feet raise the front of the
saw slightly higher than the rear, and if the
leg set does not rock, go to step 13, or
If the leveling feet do not raise the front of the
saw slightly higher than the rear, go to step 8,
or
If the leg set rocks, go to step 8.
8. Loosen the bottom hex nut on the desired
leveling foot using a 9/16 inch wrench.
9. Loosen the top nut by hand.
Handwheel
Fig. 16
©
Fig. 17 - Screw and External Lockwasher
10
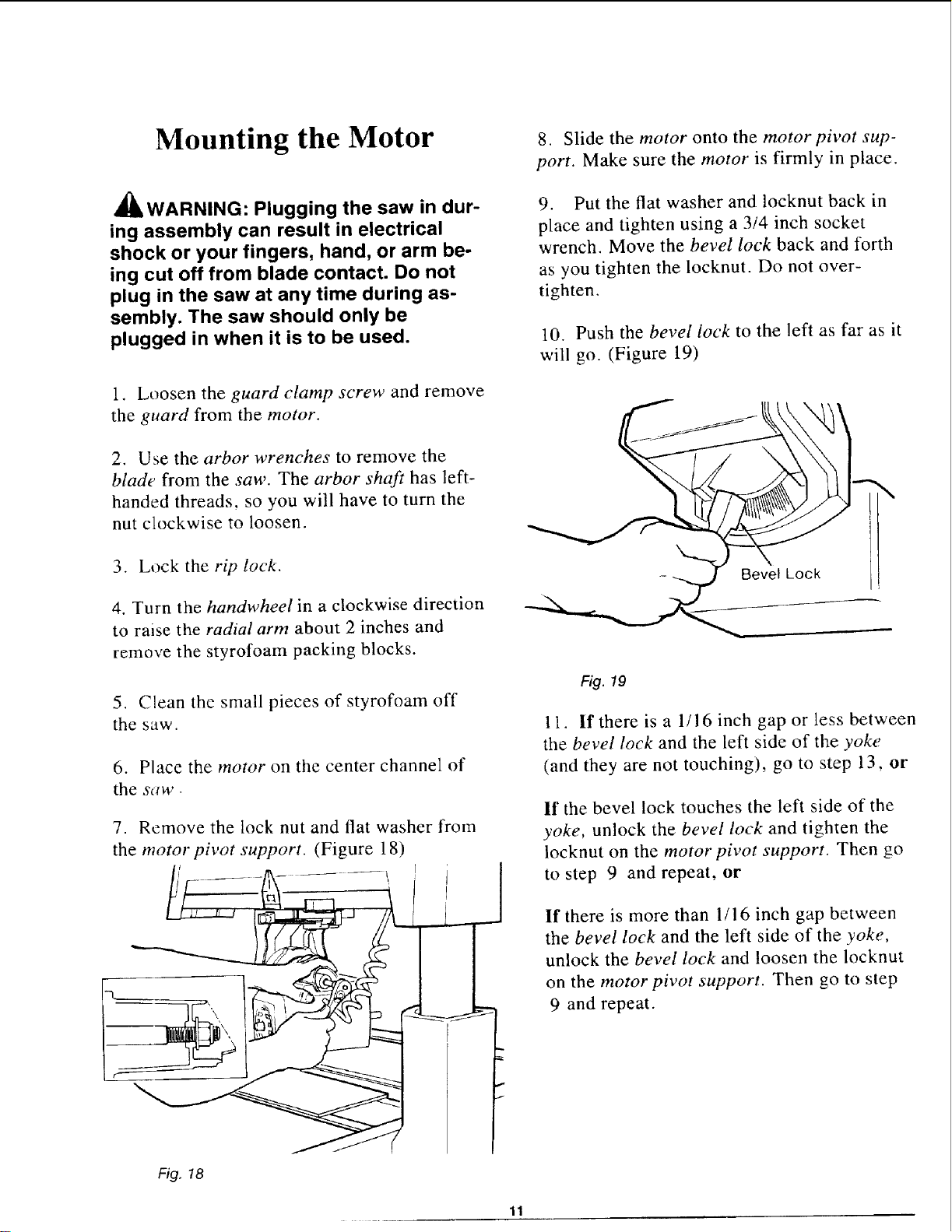
Mounting the Motor
8. Slide the motor onto the motor pivot sup-
port. Make sure the motor is firmly in place.
_kWARNING: Plugging the saw in dur-
ing assembly can result in electrical
shock or your fingers, hand, or arm be-
ing cut off from blade contact. Do not
plug in the saw at any time during as-
sembly. The saw should only be
plugged in when it is to be used.
1, Loosen the guard clamp screw and remove
the guard from the motor.
2. Use the arbor wrenches to remove the
blade from the saw. The arbor shaft has left-
handed threads, so you will have to turn the
nut clockwise to loosen.
3. Lock the rip lock.
4. Turn the handwheeI in a clockwise direction
to raise the radial arm about 2 inches and
remove the styrofoam packing blocks.
9. Put the flat washer and locknut back in
place and tighten using a 3/4 inch socket
wrench. Move the bevel lock back and forth
as you tighten the locknut. Do not over-
tighten.
10. Push the bevel lock to the left as far as it
will go. (Figure 19)
5. Clean the small pieces of styrofoam off
the saw.
6. Place the motor on the center channel of
the saw.
7. Remove the lock nut and fiat washer t'rol]]
the motor pivot support. (Figure 18)
-k_..__ ;t,
Fig. 19
11. If there is a 1/16 inch gap or less between
the bevel lock and the left side of the yoke
(and they are not touching), go to step 13, or
If the bevel lock touches the left side of the
yoke, unlock the bevel lock and tighten the
locknut on the motor pivot support. Then go
to step 9 and repeat, or
If there is more than 1/16 inch gap between
the bevel lock and the left side of the yoke,
unlock the bevel lock and loosen the locknut
on the motor pivot support. Then go to step
9 and repeat.
Fig. 18
11
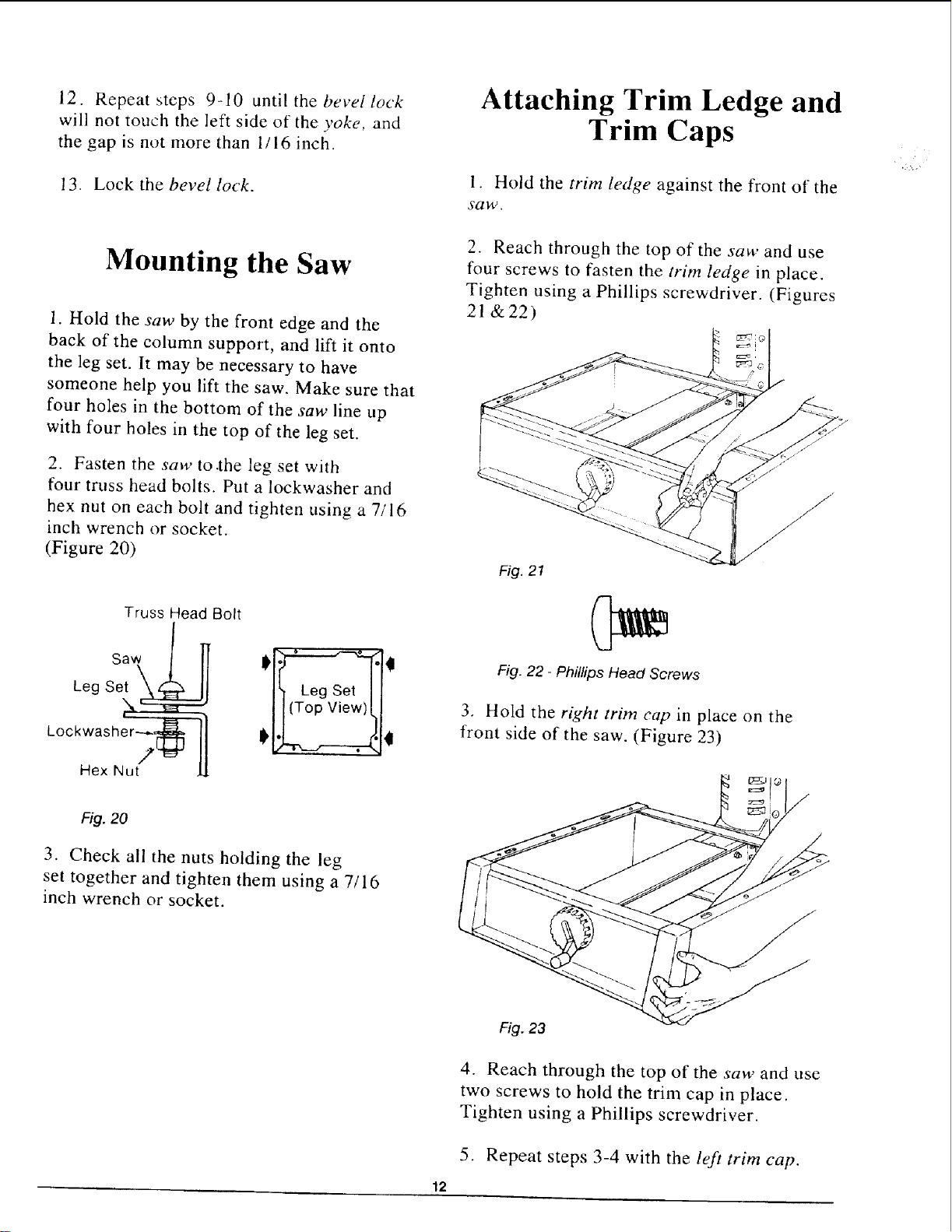
12. Repeat steps 9-10 until the bevel lock
will not touch the left side of the yoke, and
the gap is not more than 1/16 inch.
Attaching Trim Ledge and
Trim Caps
13. Lock the bevel lock.
Mounting the Saw
1. Hold the saw by the front edge and the
back of the column support, and lift it onto
the leg set. It may be necessary to have
someone help you lift the saw. Make sure that
four holes in the bottom of the saw line up
with four holes in the top of the leg set.
2. Fasten the saw to .the leg set with
four truss head bolts. Put a lockwasher and
hex nut on each bolt and tighten using a 7/16
inch wrench or socket.
(Figure 20)
Truss Head Bolt
Saw] 1]
l. Hold the trim ledge against the front of the
saw.
2. Reach through the top of the saw and use
four screws to fasten the trim ledge in place.
Tighten using a Phillips screwdriver. (Figures
21 &22)
Fi9.21
O=
Fig. 22- Phillips Head Screws
Leg Set
kockwasher---_ ]/
Hex Nut _'1_ Lit
Fig. 20
3. Check all the nuts holding the leg
set together and tighten them using a 7/16
inch wrench or socket.
3. Hold the right trim cap in place on the
front side of the saw. (Figure 23)
4. Reach through the top of the saw and use
two screws to hold the trim cap in place.
Tighten using a Phillips screwdriver.
5. Repeat steps 3-4 with the left trim cap.
12
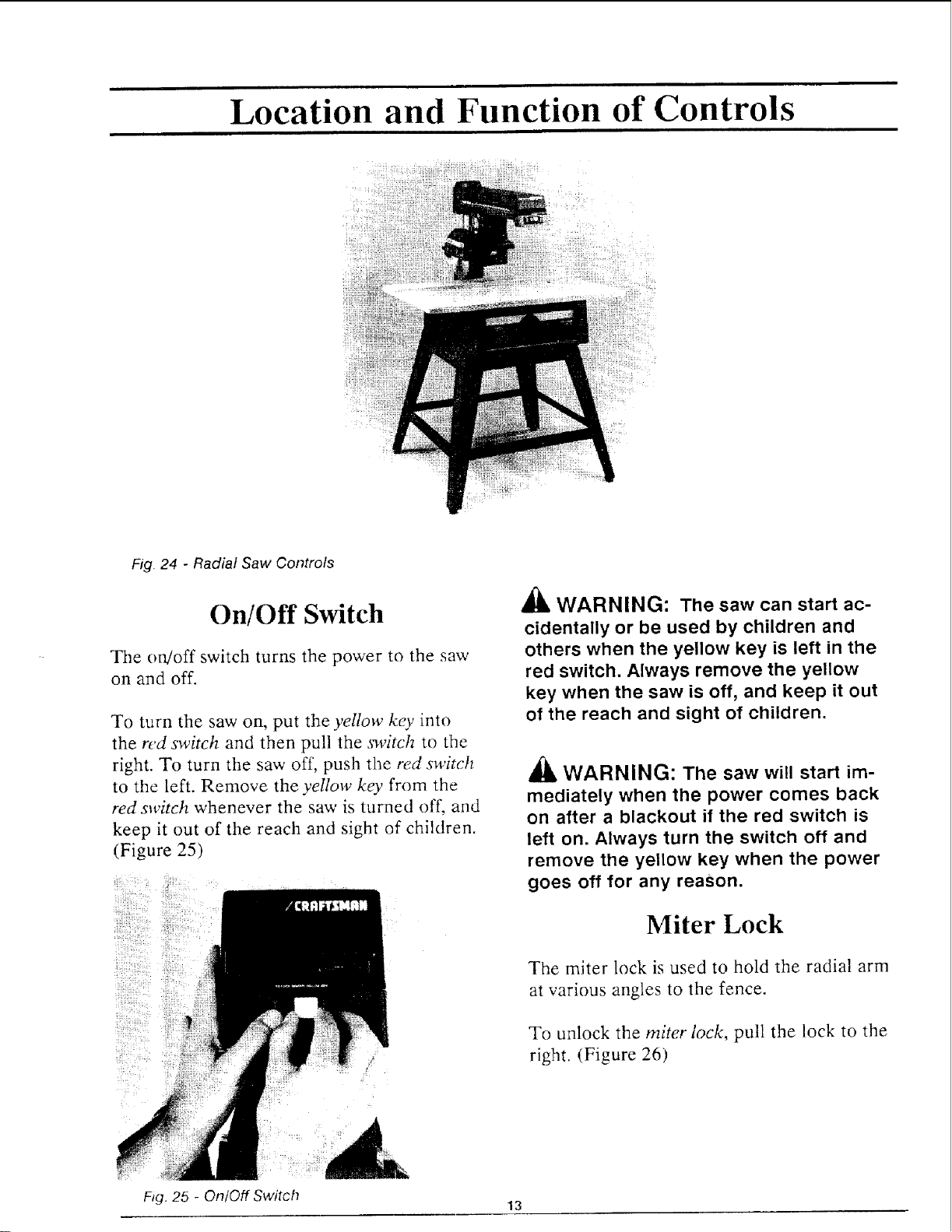
Location and Function of Controls
Fig 24 - Radial Saw Controls
On/Off Switch
The on!off switch turns the power to the saw
on and off.
To turn the saw on, put the yellow key into
the nd switch and then pull the switch to the
right. To turn the saw off, push the md switch
to the left. Remove the yellow key from the
red switch whenever the saw is turned of L and
keep it out of the reach and sight of children.
(Figure 25)
WARNING: The saw can start ac-
cidentally or be used by children and
others when the yellow key is left in the
red switch. Always remove the yellow
key when the saw is off, and keep it out
of the reach and sight of children.
Z&
WARNING: The saw will start im-
mediately when the power comes back
on after a blackout if the red switch is
left on. Always turn the switch off and
remove the yellow key when the power
goes off for any reason.
Miter Lock
The miter lock is used to hold the radial arm
at various angles to the fence.
To unlock the miter lock, pull the lock to the
right. (Figure 26)
Fig. 25 - On/Off Switch
13
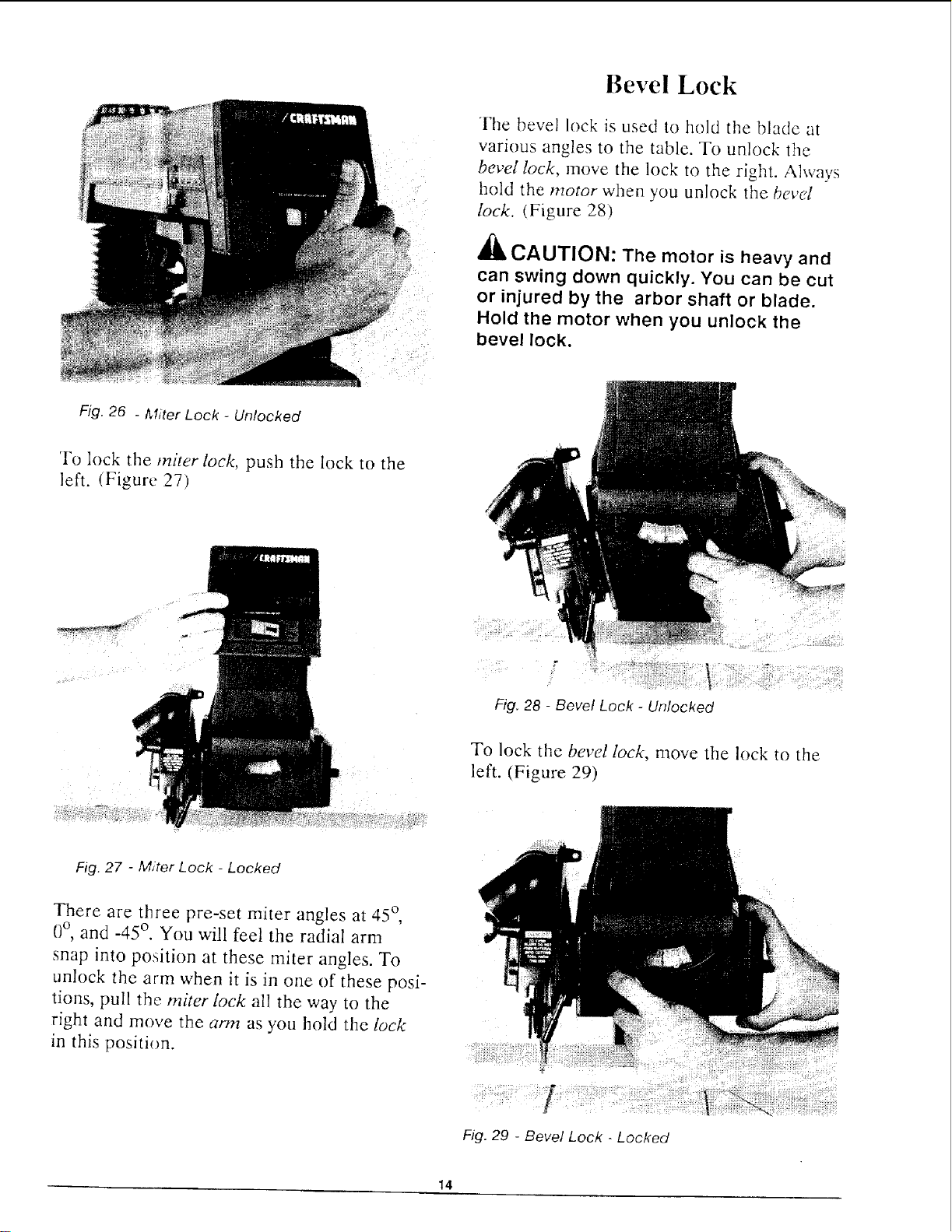
Fig. 26 - Miter Lock - Unlocked
To lock the miter lock, push the lock to the
left. (Figure 27)
Bevel Lock
l-he bevel lock is used to hold the blade at
various angles to the table. To unlock the
bevel lock, move the lock to the right. Always
hold the motor when you unlock the bevd
lock. (Figure 28)
,CAUTION: The motor is heavy and
can swing down quickly. You can be cut
or injured by the arbor shaft or blade.
Hold the motor when you unlock the
bevel lock.
Fig. 27 - Miter Lock - Locked
There are three pre-set miter angles at 45 °,
0°, and -45 °. You will feel the radial arm
snap into position at these miter angles. To
unlock the arm when it is in one of these pos>
tions, pull the miter lock all the way to the
right and move the ann as you hold the lock
in this position.
Fig. 28 - Bevel Lock - Unlocked
To lock the bevel lock, move the lock to the
left. (Figure 29)
14
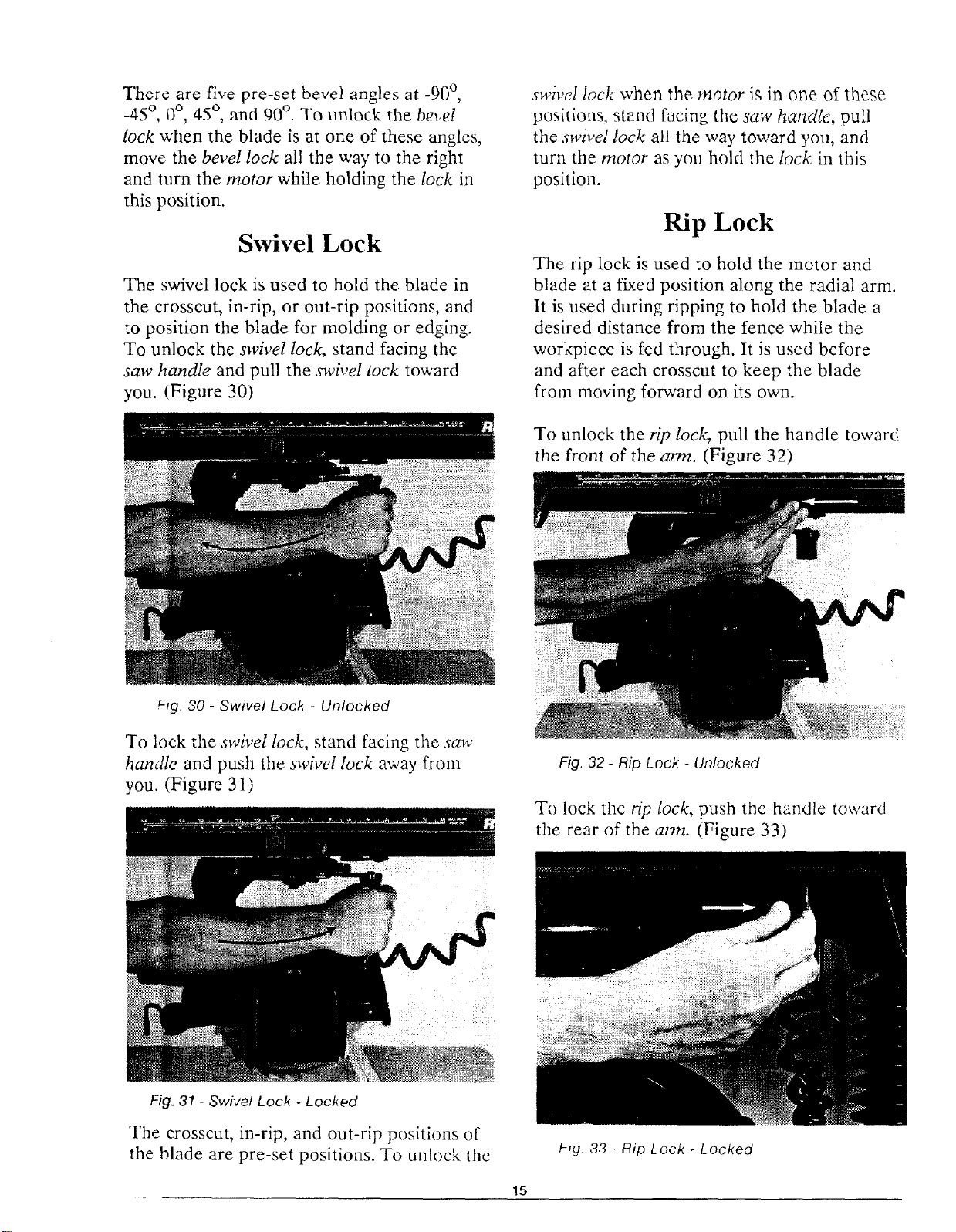
There are flve pre-set bevel angles at -90 °,
-45 °, 0°, 45 °, nnd 90 °. To unlock the bgvel
lock when the blade is at one of these angles,
move the bevel lock all the way to the right
and turn the motor while holding the lock in
this position.
Swivel Lock
The swivel lock is used to hold the blade in
the crosscut, in-rip, or out-rip positions, and
to position the blade for molding or edging.
To unlock the swivel lock, stand facing the
saw handle and pull the swivel lock toward
you. (Figure 30)
s_d_,el lock when the motor ig in one o[ these
positions, stand facing the saw handle, pull
the swivel lock all the way toward you, and
turn the motor as yon hold the lock in this
position.
Rip Lock
The rip lock is used to hold the motor and
blade at a fixed position along the radial arm.
It is used during ripping to hold the blade a
desired distance from the fence while the
workpiece is fed through. It is used before
and after each crosscut to keep the blade
from moving forward on its own.
To unlock the rip lock, pull the handle toward
the front of the arm. (Figure 32)
Frg. 30 - Swivel Lock - Unlocked
To lock the swivel lock, stand facing the saw
handle and push the swivel lock away from
you. (Figure 31)
Fig. 31 - Swivel Lock - Locked
The crosscut, in-rip, and out-rip positions of
the blade are pre-set positions. To unlock the
Fig, 32- Rip Lock - Unlocked
To lock the rip lock, push the handle toward
the rear of the ann. (Figure 33)
Fig. 33 - Rip Lock - Locked
15
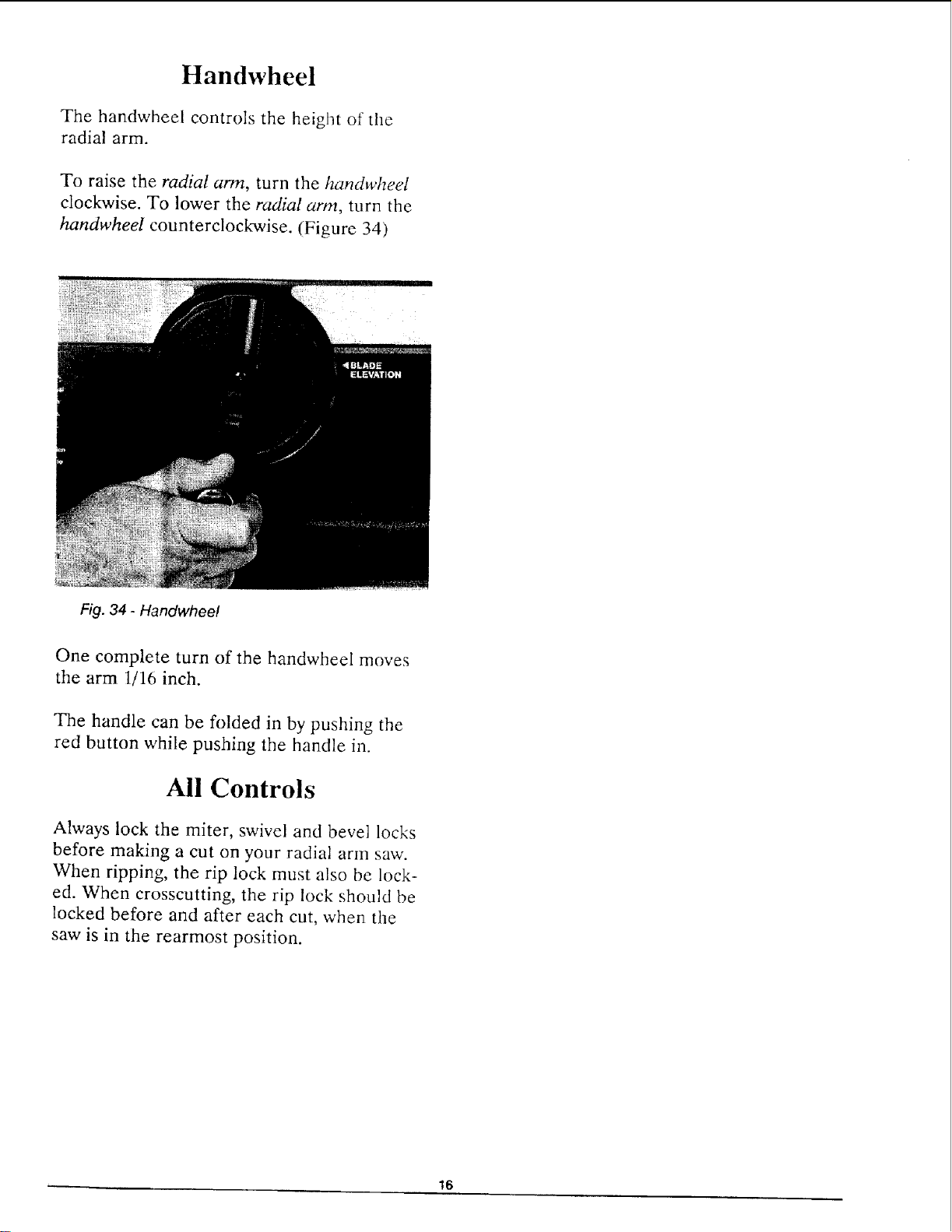
Handwheel
The handwheel controls the height of the
radial arm.
To raise the radial arm, turn the handwheel
clockwise. To lower the radial arm, turn the
handwheel counterclockwise. (Figure 34)
Fig. 34 - Handwhee!
One complete turn of the handwheel moves
the arm 1/16 inch.
The handle can be folded in by pushing the
red button while pushing the handle in.
All Controls
Always lock the miter, swivel and bevel locks
before making a cut on your radial arm saw.
When ripping, the rip lock must also be lock-
ed. When crosscutting, the rip lock should be
locked before and after each cut, when the
saw is in the rearmost position.
16
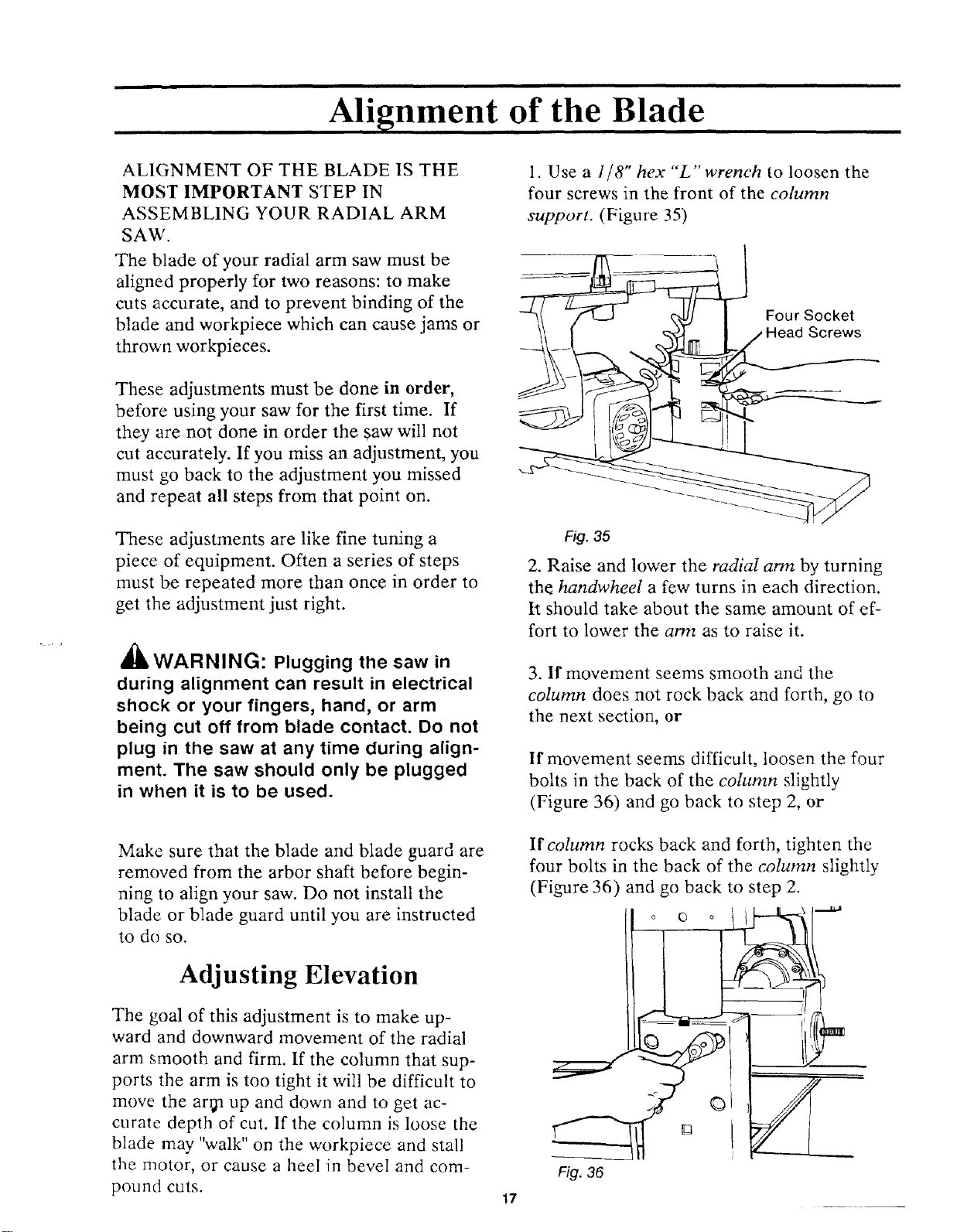
, Alignment of the Blade
ALIGNMENT OF THE BLADE IS THE
MOST IMPORTANT STEP IN
ASSEMBLING YOUR RADIAL ARM
SAW.
The blade of your radial arm saw must be
aligned properly for two reasons: to make
cuts accurate, and to prevent binding of the
Made and workpiece which can cause jams or
thrown workpieces.
These adjustments must be done in order,
before using your saw for the first time. If
they are not done in order the saw will not
cut accurately. If you miss an adjustment, you
must go back to the adjustment you missed
and repeat all steps from that point on.
These adjustments are like fine tuning a
piece of equipment. Often a series of steps
must be repeated more than once in order to
get the adjustment just right.
A
4UkWARNING: Plugging the saw in
during alignment can result in electrical
shock or your fingers, hand, or arm
being cut off from blade contact. Do not
plug in the saw at any time during align-
ment. The saw should only be plugged
in when it is to be used.
1. Use a 1/8" hex "'L" wrench to loosen the
four screws in the front of the column
support. (Figure 35)
Four Socket
Screws
Fig. 35
2. Raise and lower the radial ann by turning
the handwheel a few turns in each direction.
tt should take about the same amount of ef-
fort to lower the arm as to raise it.
3. If movement seems smooth and the
column does not rock back and forth, go to
the next section, or
If movement seems difficult, loosen the four
bolts in the back of the column slightly
(Figure 36) and go back to step 2, or
Make sure that the blade and blade guard are
removed from the arbor shaft before begin-
ning to align your saw. Do not install the
blade or blade guard until you are instructed
to do so.
Adjusting Elevation
The goal of this adjustment is to make up-
ward and downward movement of the radial
arm smooth and firm. If the column that sup-
ports the arm is too tight it will be difficult to
move the ar_a up and down and to get ac-
curate depth of cut. If the column is loose the
blade may "walk" on the workpiece and stall
the motor, or cause a heel in bevel and com-
pound cuts.
If column rocks back and forth, tighten the
four bolts in the back of the column slightly
(Figure 36) and go back to step 2.
Fig. 36
17
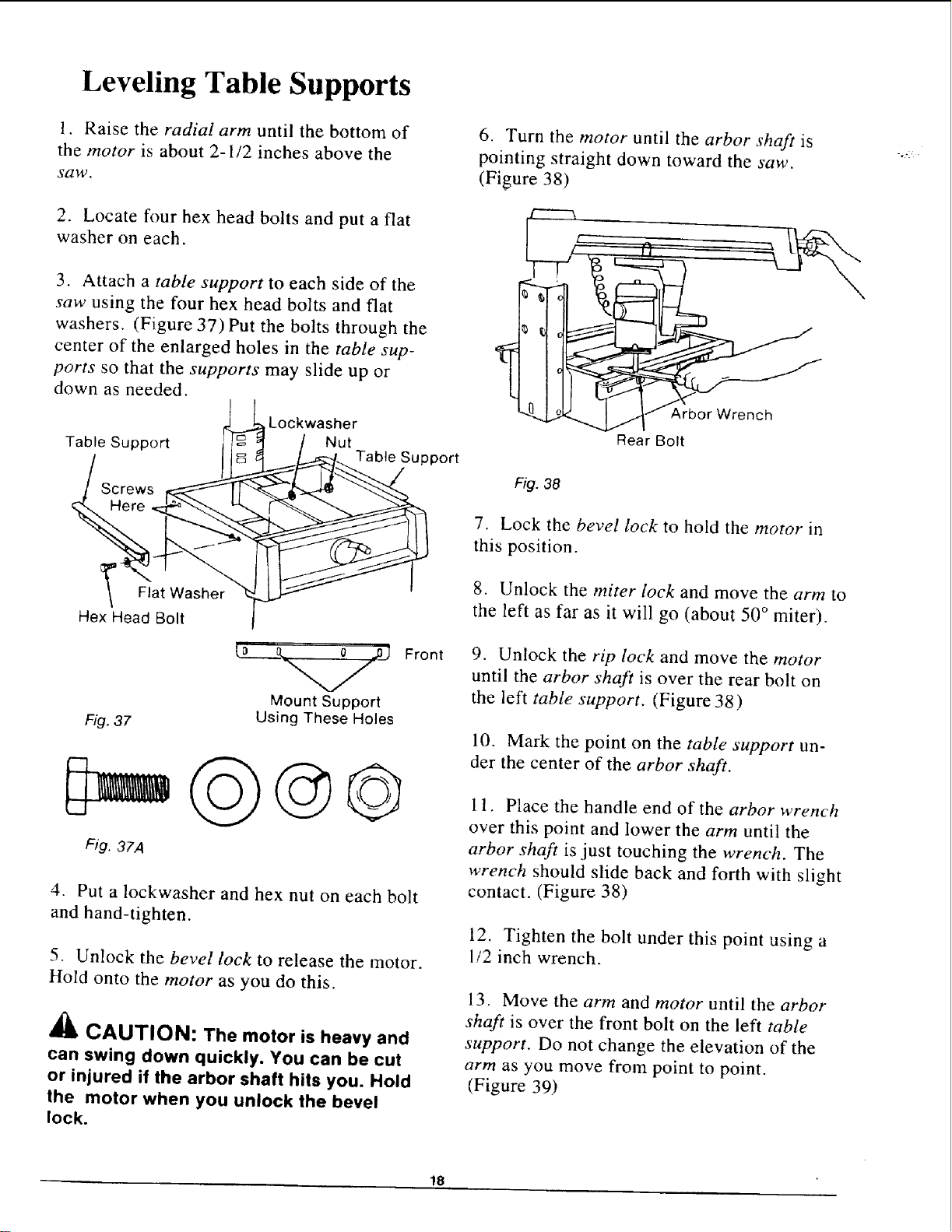
Leveling Table Supports
1. Raise the radial arm until the bottom of
the motor is about 2-1/2 inches above the
saw.
2. Locate fl)ur hex head bolts and put a flat
washer on each.
3. Attach a table support to each side of the
saw using the four hex head bolts and flat
washers. (Figure 37) Put the bolts through the
center of the enlarged holes in the table sup-
ports so that the supports may slide up or
down as needed.
Lockwasher
Table Support
Screws
Here
Nut
Table Support
6. Turn the motor until the arbor shaft is
pointing straight down toward the saw.
(Figure 38)
Arbor Wrench
Rear Bolt
Fig. 38
7. Lock the bevel lock to hold the motor in
this position.
Flat Washer
Hex Head Bolt
t0 ___j
Mount Support
Fig. 37
Using These Holes
©©
Fig. 37A
4. Put a lockwasher and hex nut on each bolt
and hand-tighten.
5. Unlock the bevel lock to release the motor.
Hold onto the motor as you do this,
,fk
CAUTION: The motor is heavy and
can swing down quickly. You can be cut
or injured if the arbor shaft hits you. Hold
the motor when you unlock the bevel
lock.
Front
8. Unlock the miter lock and move the arm to
the left as far as it will go (about 50 ° miter).
9. Unlock the rip lock and move the motor
until the arbor shaft is over the rear bolt on
the left table support. (Figure 38)
10. Mark the point on the table support un-
der the center of the arbor shaft.
I 1. Place the handle end of the arbor wrench
over this point and lower the arm until the
arbor shaft is just touching the wrench. The
wrench should slide back and forth with slight
contact. (Figure 38)
12. Tighten the bolt under this point using a
1/2 inch wrench.
13. Move the arm and motor until the arbor
shaft is over the front bolt on the left table
support. Do not change the elevation of the
arm as you move from point to point.
(Figure 39)
18
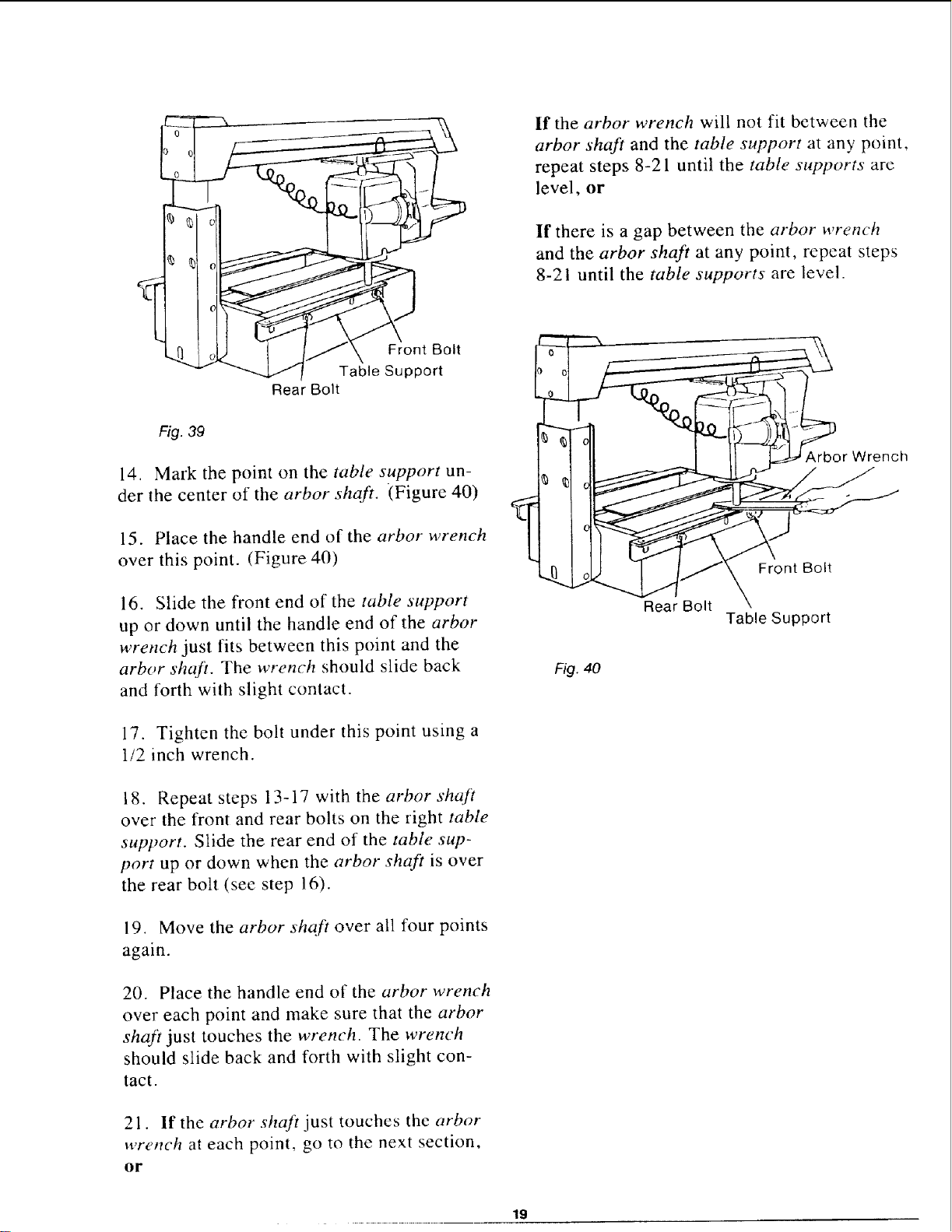
0
r) 0 0
_L._]_,_ j . _ Front Bolt
- _ Table Support
Rear Bolt
Fig. 39
14. Mark the point on the table support un-
der the center of the arbor shaft. (Figure 40)
15. Place the handle end of the arbor wrench
over this point. (Figure 40)
I[ the arbor wrench will not fit between the
arbor shaft and the table support at any point,
repeat steps 8-21 until the table supports are
level, or
If there is a gap between the arbor wrench
and the arbor shaft at any point, repeat steps
8-21 until the table supports are level.
I orWrench
16. Slide the front end of the table support
up or down until the handle end of the arbor
wrench just fits between this point and the
arbor shaft. The wrench should slide back
and forth with slight contact.
17. Tighten the bolt under this point using a
1/2 inch wrench.
18. Repeat steps 13-17 with the arbor shaft
over the front and rear bolts on the right table
support. Slide the rear end of the table sup-
port up or down when the arbor shaft is over
the rear bolt (see step 16).
19. Move the arbor shaft over all four points
again.
20. Place the handle end of the arbor wrench
over each point and make sure that the arbor
shaft just touches the wrench. The wrench
should slide back and forth with slight con-
tact.
Rear Bolt
Table Support
Fig. 40
21. If the arbor shaft just touches the arbor
wre_tch at each point, go to the next section,
or
19
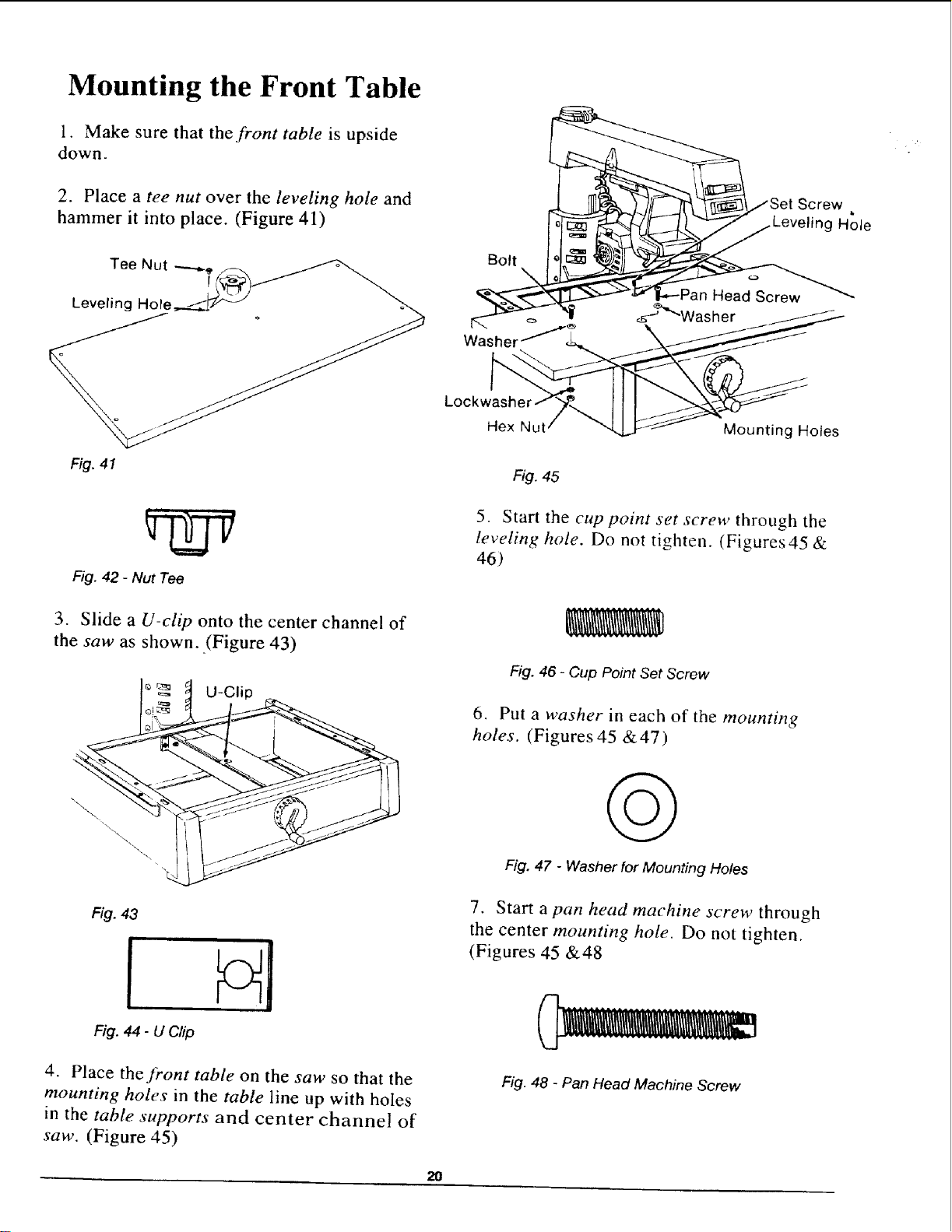
Mounting the Front Table
1. Make sure that the front table is upside
down.
2. Place a tee nut over the leveling hole and
hammer it into place. (Figure 41)
Tee Nut --.--_/_..
[
Leveling Ho,e_ .F_-
Fig. 41
Fig. 42 - Nut Tee
3. Slide a U-clip onto the center channel of
the saw as shown. (Figure 43)
:rew
g Hole
Bolt
Head Screw
Loc
Hex Nut Mounting Holes
Fig. 45
5. Start the cup point set screw through the
leveling hole. Do not tighten. (Figures 45 &
46)
Fig. 46 - Cup Point Set Screw
Fig.4a
Fig. 44 - u Clip
4. Place the front table on the saw so that the
mounting holes in the table line up with holes
in the table supports and center channel o[
saw, (Figure 45)
6. Put a washer in each of the mounting
holes, (Figures 45 &47)
G
Fig. 47 - Washer for Mounting Holes
7. Start a pan head machine screw through
the center mounting hole. Do not tighten.
(Figures 45 &48
Fig. 48 - Pan Head Machine Screw
20
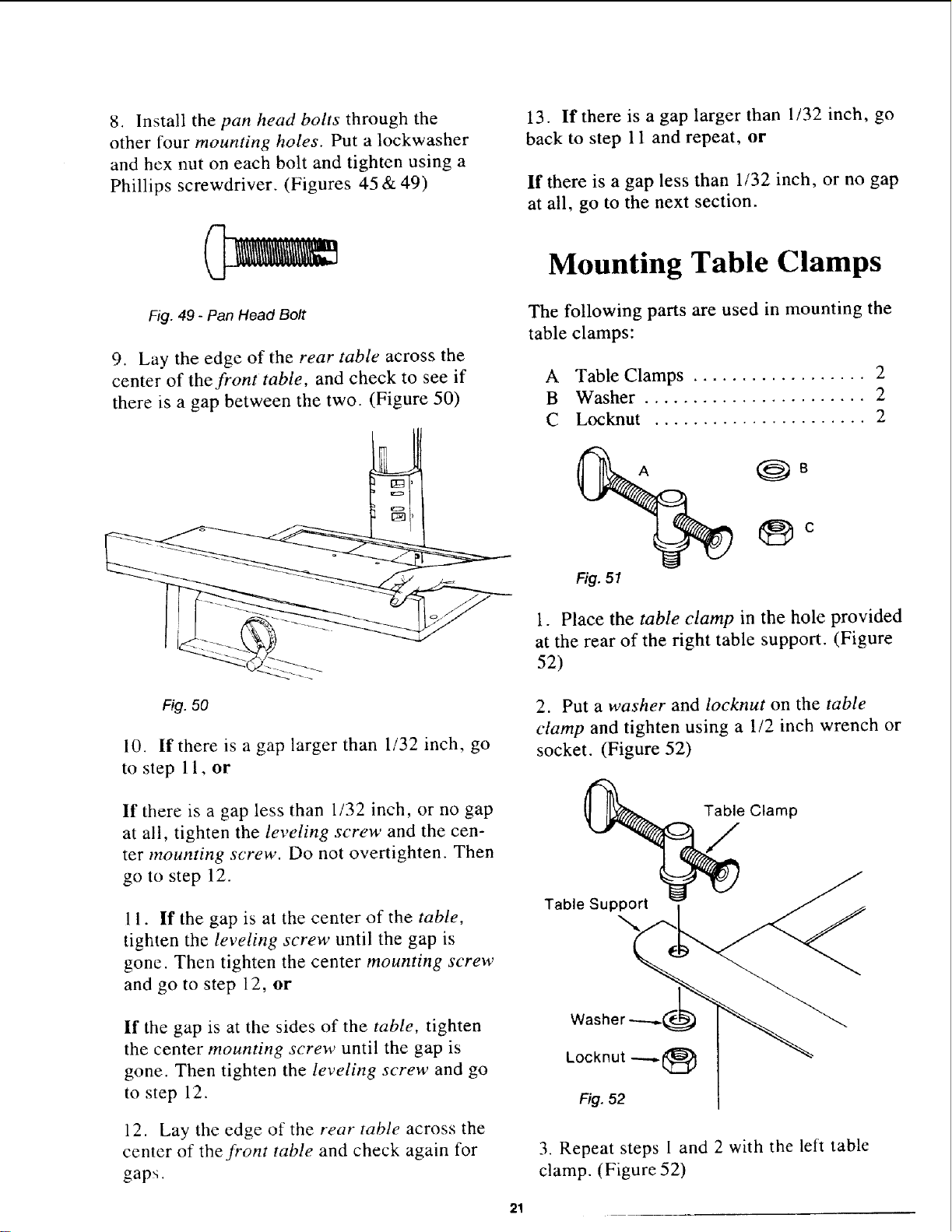
8. Install the pan head bolts through the
other four mounting holes. Put a lockwasher
and hex nut on each bolt and tighten using a
Phillips screwdriver. (Figures 45 & 49)
13. If there is a gap larger than 1/32 inch, go
back to step 11 and repeat, or
If there is a gap less than 1/32 inch, or no gap
at all, go to the next section.
Mounting Table Clamps
Fig. 49 - Pan Head Bolt
9. Lay the edge of the rear table across the
center of the front table, and check to see if
there is a gap between the two. (Figure 50)
Fig. 50
10. If there is a gap larger than 1/32 inch, go
to step 11, or
The following parts are used in mounting the
table clamps:
A Table Clamps .................. 2
B Washer ....................... 2
C Locknut ...................... 2
Fig.51
1. Place the table clamp in the hole provided
at the rear of the right table support. (Figure
52)
2. Put a washer and locknut on the table
clamp and tighten using a 1/2 inch wrench or
socket. (Figure 52)
If there is a gap less than 1/32 inch, or no gap
at all, tighten the leveling screw and the cen-
ter mounting screw. Do not overtighten. Then
go to step 12.
l 1. If the gap is at the center of the table,
tighten the leveling screw until the gap is
gone. Then tighten the center mounting screw
and go to step 12, or
If the gap is at the sides of the table, tighten
the center mounting screw until the gap is
gone. Then tighten the leveling screw and go
to step 12.
12. Lay the edge of the rear table across the
center of the front table and check again for
gaps.
Table Clamp
Table Support
3. Repeat steps l and 2 with the left table
clamp. (Figure 52)
21
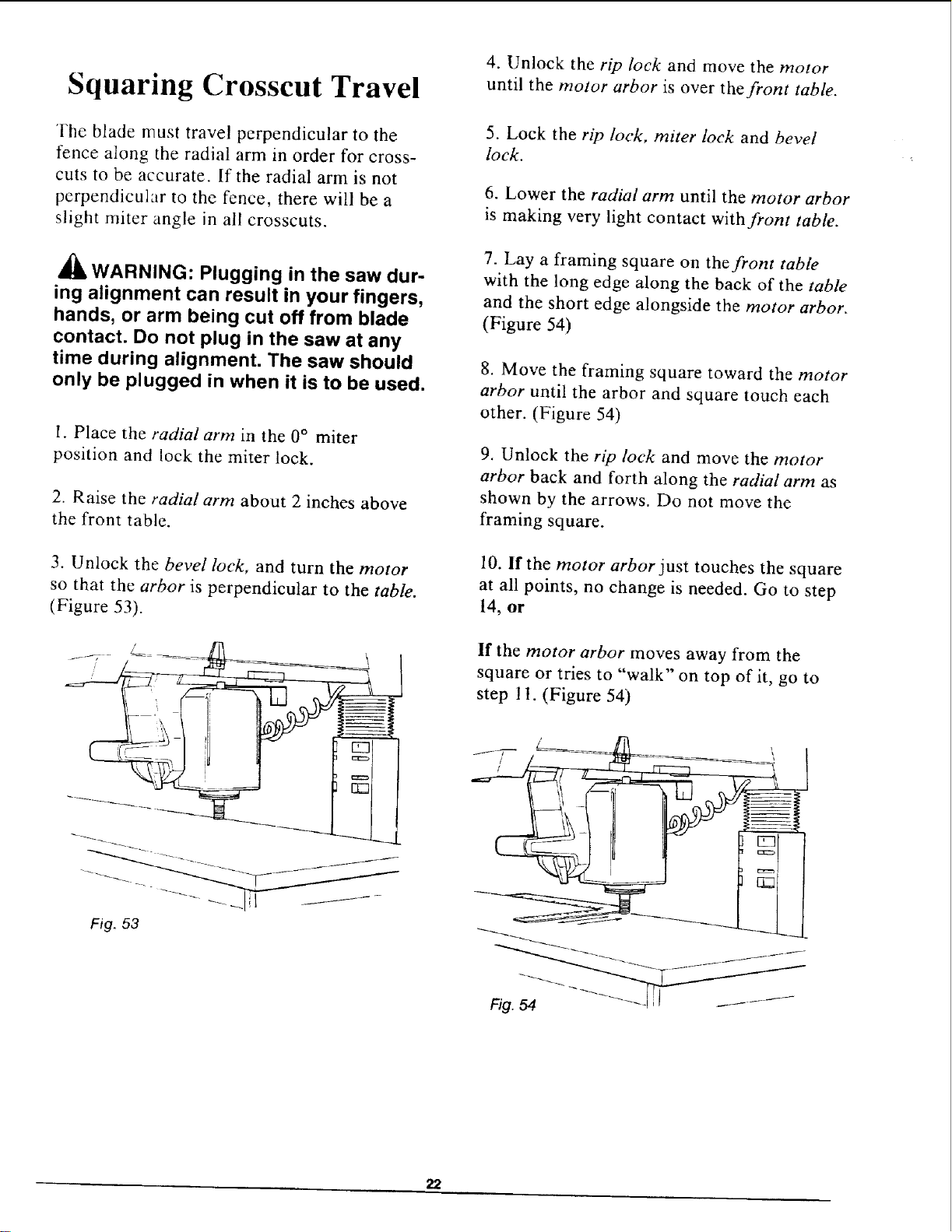
Squaring Crosscut Travel
4. Unlock the rip lock and move the motor
until the motor arbor is over the front table.
The blade must travel perpendicular to the
fence along the radial arm in order for cross-
cuts to be accurate. If the radial arm is not
perpendicular to the fence, there will be a
slight miter angle in all crosscuts.
_IbWARNING: Plugging in the saw dur-
ing alignment can result in your fingers,
hands, or arm being cut off from blade
contact. Do not plug in the saw at any
time during alignment. The saw should
only be plugged in when it is to be used.
I. Place the radial arm in the 0 ° miter
position and lock the miter lock.
2. Raise the radial arm about 2 inches above
the front table.
3. Unlock the bevel lock, and turn the motor
so that the arbor is perpendicular to the table.
(Figure 53).
5. Lock the rip lock, miter lock and bevel
lock.
6. Lower the radial arm until the motor arbor
is making very light contact with front table.
7. Lay a framing square on the front table
with the long edge along the back of the table
and the short edge alongside the motor arbor.
(Figure 54)
8. Move the framing square toward the motor
arbor until the arbor and square touch each
other. (Figure 54)
9. Unlock the rip lock and move the motor
arbor back and forth along the radial arm as
shown by the arrows. Do not move the
framing square.
10. If the motor arbor just touches the square
at all points, no change is needed. Go to step
14, or
Fig. 53
If the motor arbor moves away from the
square or tries to "walk" on top of it, go to
step l 1. (Figure 54)
Fig. 54
22
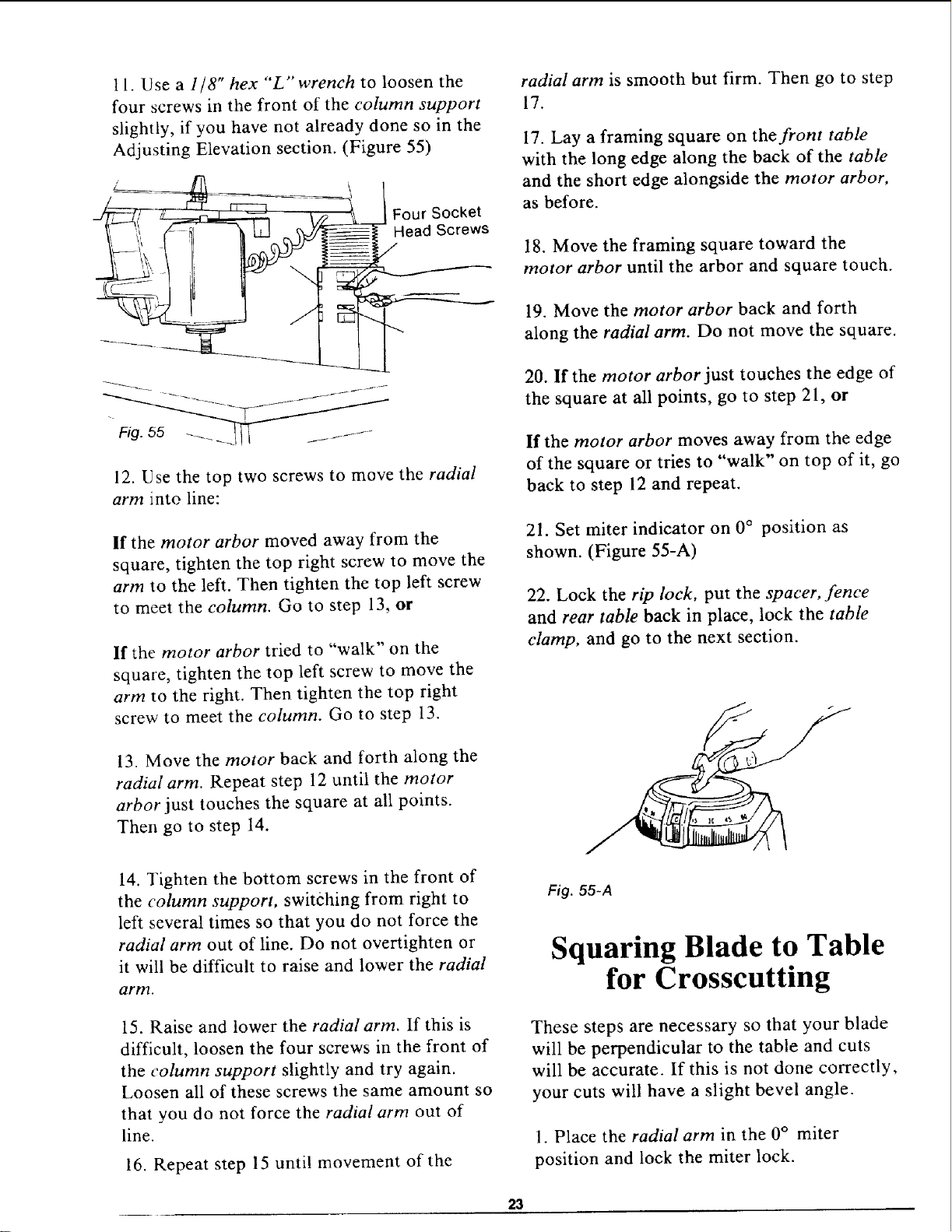
11. Use a 1/8" hex "L" wrench to loosen the
four screws in the front of the column support
slightly, if you have not already done so in the
Adjusting Elevation section. (Figure 55)
Four Socket
Head Screws
J
12. Use the top two screws to move the radial
arm into line:
radial arm is smooth but firm. Then go to step
17.
17. Lay a framing square on the front table
with the long edge along the back of the table
and the short edge alongside the motor arbor,
as before.
18. Move the framing square toward the
motor arbor until the arbor and square touch.
19. Move the motor arbor back and forth
along the radial arm. Do not move the square.
20. If the motor arbor just touches the edge of
the square at all points, go to step 21, or
If the motor arbor moves away from the edge
of the square or tries to "walk" on top of it, go
back to step 12 and repeat.
If the motor arbor moved away from the
square, tighten the top right screw to move the
arm to the left. Then tighten the top left screw
to meet the column. Go to step 13, or
If the motor arbor tried to "walk" on the
square, tighten the top left screw to move the
arm to the right. Then tighten the top right
screw to meet the column. Go to step 13.
13. Move the motor back and forth along the
radial arm. Repeat step 12 until the motor
arbor just touches the square at all points.
Then go to step 14.
14. Tighten the bottom screws in the front of
the column support, switching from right to
left several times so that you do not force the
radial arm out of line. Do not overtighten or
it will be difficult to raise and lower the radial
arm.
21. Set miter indicator on 0 ° position as
shown. (Figure 55-A)
22. Lock the rip lock, put the spacer, fence
and rear table back in place, lock the table
clamp, and go to the next section.
Fig. 55-A
Squaring Blade to Table
for Crosscutting
15. Raise and lower the radial arm. If this is
difficult, loosen the four screws in the front of
the column support slightly and try again.
Loosen all of these screws the same amount so
that you do not force the radial arm out of
line.
16. Repeat step 15 until movement of the
These steps are necessary so that your blade
will be perpendicular to the table and cuts
will be accurate. If this is not done correctly,
your cuts will have a slight bevel angle.
I. Place the radial arm in the 0 ° miter
position and lock the miter lock.
23
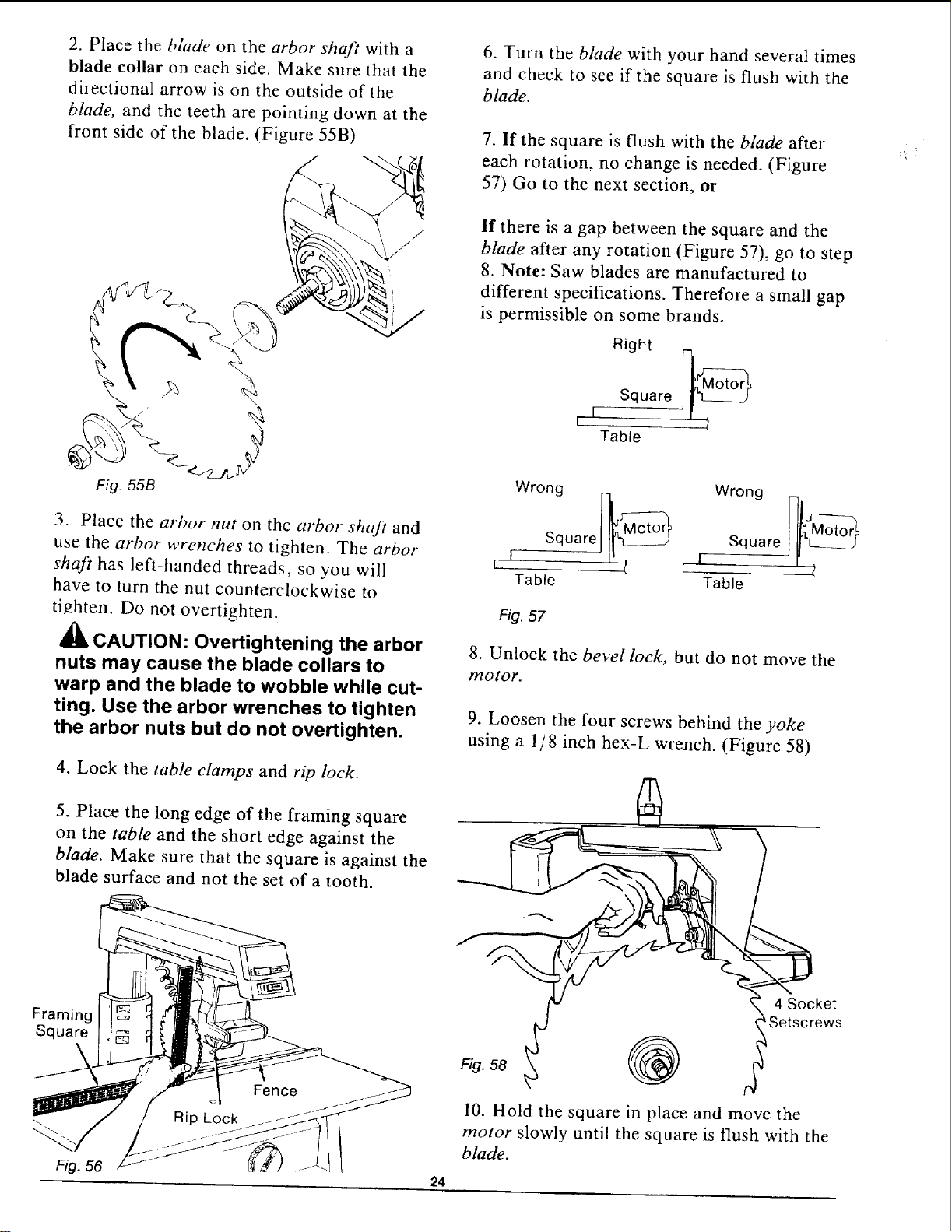
2. Place the blade on the arbor shaft with a
blade collar on each side. Make sure that the
directional arrow is on the outside of the
blade, and the teeth are pointing down at the
front side of the blade. (Figure 55B)
6. Turn the blade with your hand several times
and check to see if the square is flush with the
blade.
7. If the square is flush with the blade after
each rotation, no change is needed. (Figure
57) Go to the next section, or
Fig. 5513
3. Place the arbor nut on the arbor shaft and
use the arbor wrenches to tighten. The arbor
shaft has left-handed threads, so you will
have to turn the nut counterclockwise to
tizhten. Do not overtighten.
CAUTION: Overtightening the arbor
nuts may cause the blade collars to
warp and the blade to wobble while cut-
ting. Use the arbor wrenches to tighten
the arbor nuts but do not overtighten.
/
If there is a gap between the square and the
blade after any rotation (Figure 57), go to step
8. Note: Saw blades are manufactured to
different specifications. Therefore a small gap
is permissible on some brands.
Right _j_
"Fable
Wrong _ Wrong
Squarel_ F_u__U _
J ,_
Table Table
Fig, 57
8. Unlock the bevel lock, but do not move the
motor.
9. Loosen the four screws behind the yoke
using a 1/8 inch hex-L wrench. (Figure 58)
4. Lock the table clamps and rip lock.
5. Place the long edge of the framing square
on the table and the short edge against the
blade. Make sure that the square is against the
blade surface and not the set of a tooth.
Framin
Square
Fence
Rip Lock
Fig. 56
Fig. 58 _
10. Hold the square in place and move the
motor slowly until the square is flush with the
blade.
24
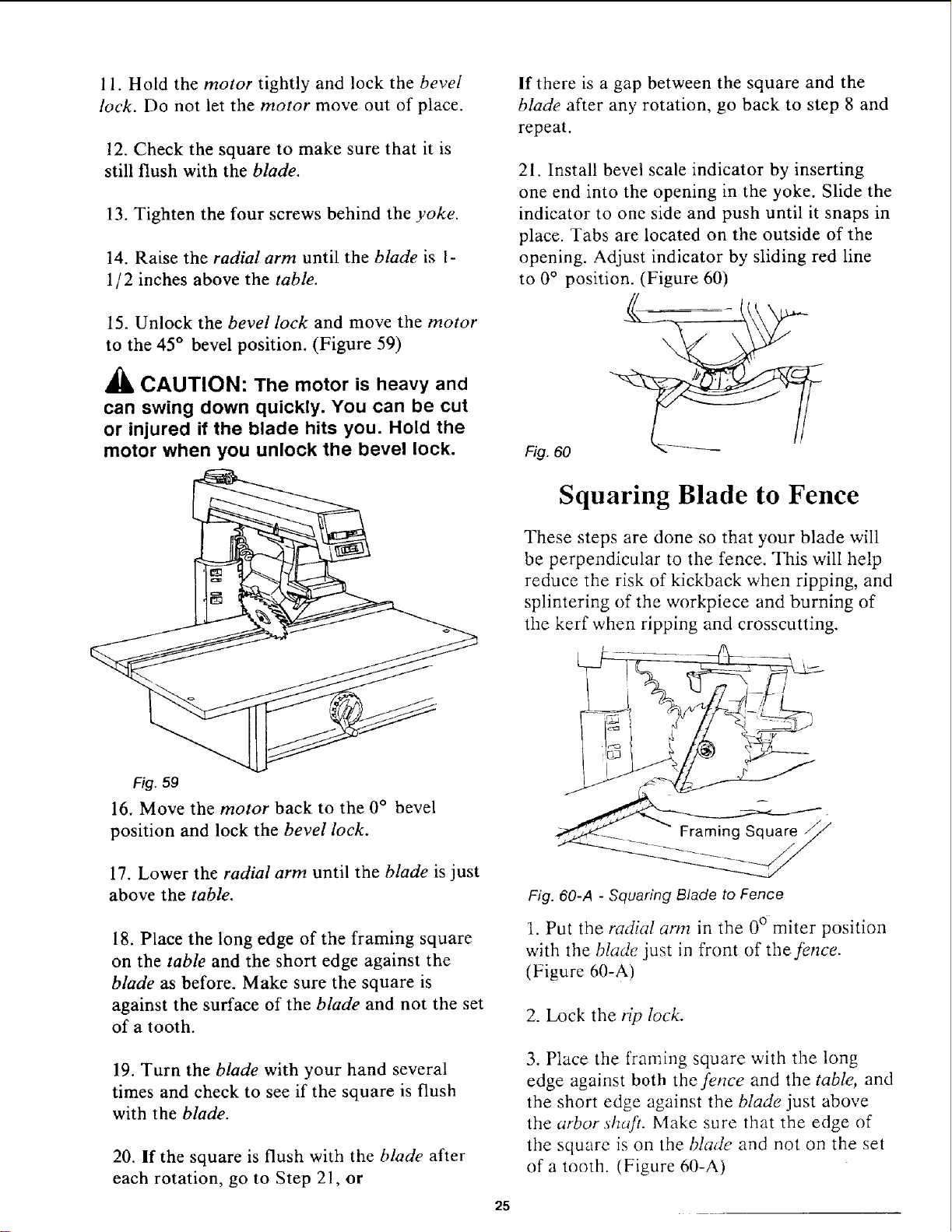
11. Hold the motor tightly and lock the bevel
lock. Do not let the motor move out of place.
12. Check the square to make sure that it is
still flush with the blade.
13. Tighten the four screws behind the yoke.
14. Raise the radial arm until the blade is I-
1/2 inches above the table.
15. Unlock the bevel lock and move the motor
to the 45 ° bevel position. (Figure 59)
CAUTION: The motor is heavy and
can swing down quickly. You can be cut
or injured if the blade hits you. Hold the
motor when you unlock the bevel lock.
If there is a gap between the square and the
blade after any rotation, go back to step 8 and
repeat.
21. Install bevel scale indicator by inserting
one end into the opening in the yoke. Slide the
indicator to one side and push until it snaps in
place. Tabs are located on the outside of the
opening. Adjust indicator by sliding red line
to 0 ° position. (Figure 60)
Fig. 60
Squaring Blade to Fence
Fig. 59
16. Move the motor back to the 0 ° bevel
position and lock the bevel lock.
17. Lower the radial arm until the blade is just
above the table.
18. Place the long edge of the flaming square
on the table and the short edge against the
blade as before. Make sure the square is
against the surface of the blade and not the set
of a tooth.
These steps are done so that your blade will
be perpendicular to the fence. This will help
reduce the risk of kickback when ripping, and
splintering of the workpiece and burning of
the kerf when ripping and crosscutting.
Fig. 60-A - Squaring Blade to Fence
1. Put the radial ann in the 0 ° miter position
with the blade just in front of the fence.
(Figure 60-A)
2. Lock the @ lock.
19. Turn the blade with your hand several
times and check to see if the square is flush
with the blade.
20. If the square is flush with the blade after
each rotation, go to Step 21, or
3. Place the framing square with the long
edge against both the fence and the table, and
the short edge against the blade just above
the arbor sh@. Make sure that tlne edge of
the square is on the blade and not on the set
of a tooth. (Figure 60-A)
25
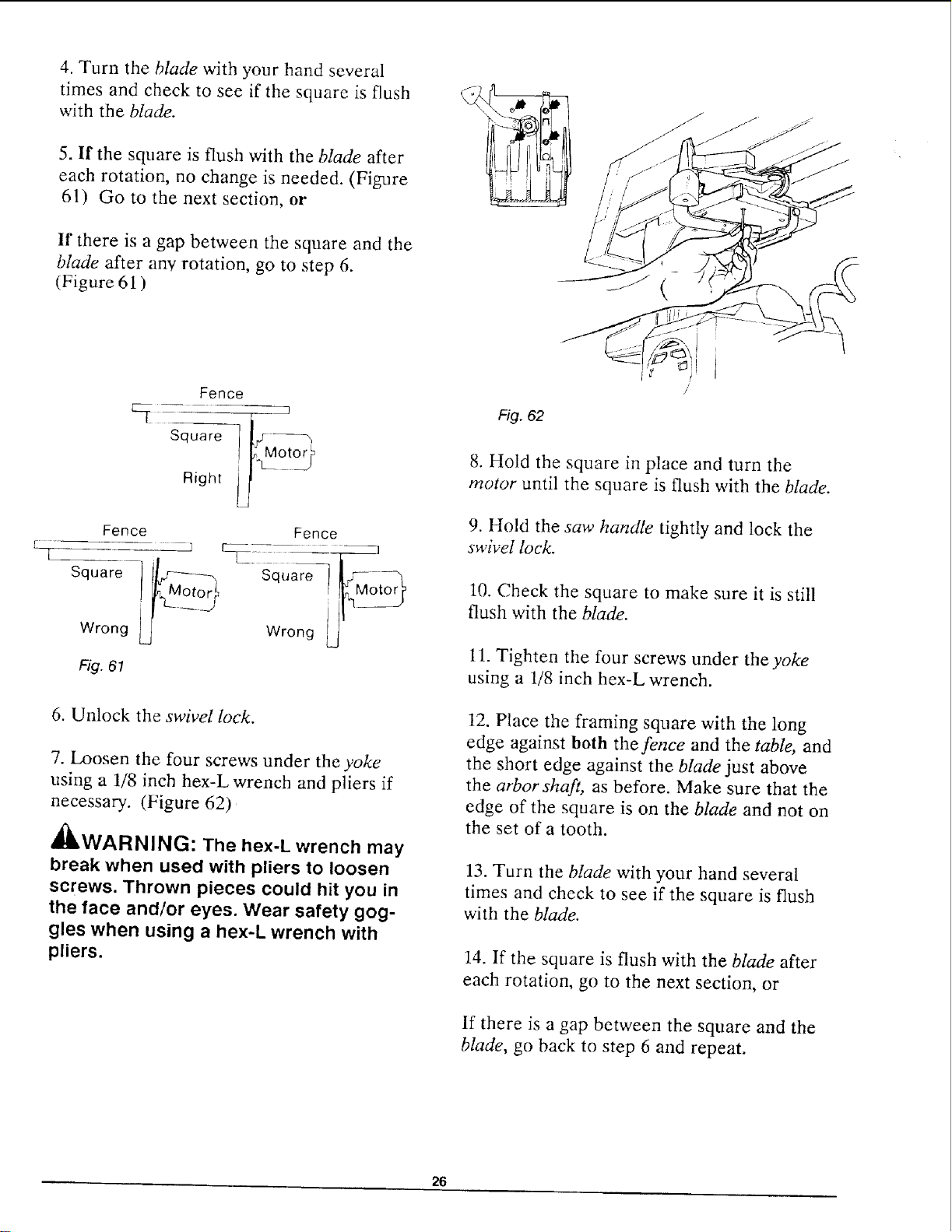
4. Turn the blade with your hand several
times and check to see if the square is flush
with the blade.
5. If the square is flush with the blade after
each rotation, no change is needed. (Figure
61) Go to the next section, or
If there is a gap between the square and the
blade after any rotation, go to step 6.
(Figure 61 )
Fence
I
Right il 'L- _)
Fig. 62
8. Hold the square in place and turn the
motor until the square is flush with the blade.
Fence Fence
i! i{l'--
Wron0 Wron0
Fig. 61
6. Unlock the swivel lock.
7. Loosen the four screws under the yoke
using a 1/8 inch hex-L wrench and pliers if
necessary. (Figure 62)
_I_WARNING: The hex-L wrench may
break when used with pliers to loosen
screws. Thrown pieces could hit you in
the face and/or eyes. Wear safety gog-
gles when using a hex-L wrench with
pliers.
9. Hold the saw handle tightly and lock the
swivel lock.
10. Check the square to make sure it is still
flush with the blade.
11. Tighten the four screws under the yoke
using a 1/8 inch hex-L wrench.
12. Place the framing square with the long
edge against both the fence and the table, and
the short edge against the blade just above
the arbor shaft, as before. Make sure that the
edge of the square is on the blade and not on
the set of a tooth.
13. Turn the blade with your hand several
times and check to see if the square is flush
with the blade.
14. If the square is flush with. the blade after
each rotation, go to the next section, or
If there is a gap between the square and the
blade, go back to step 6 and repeat.
26
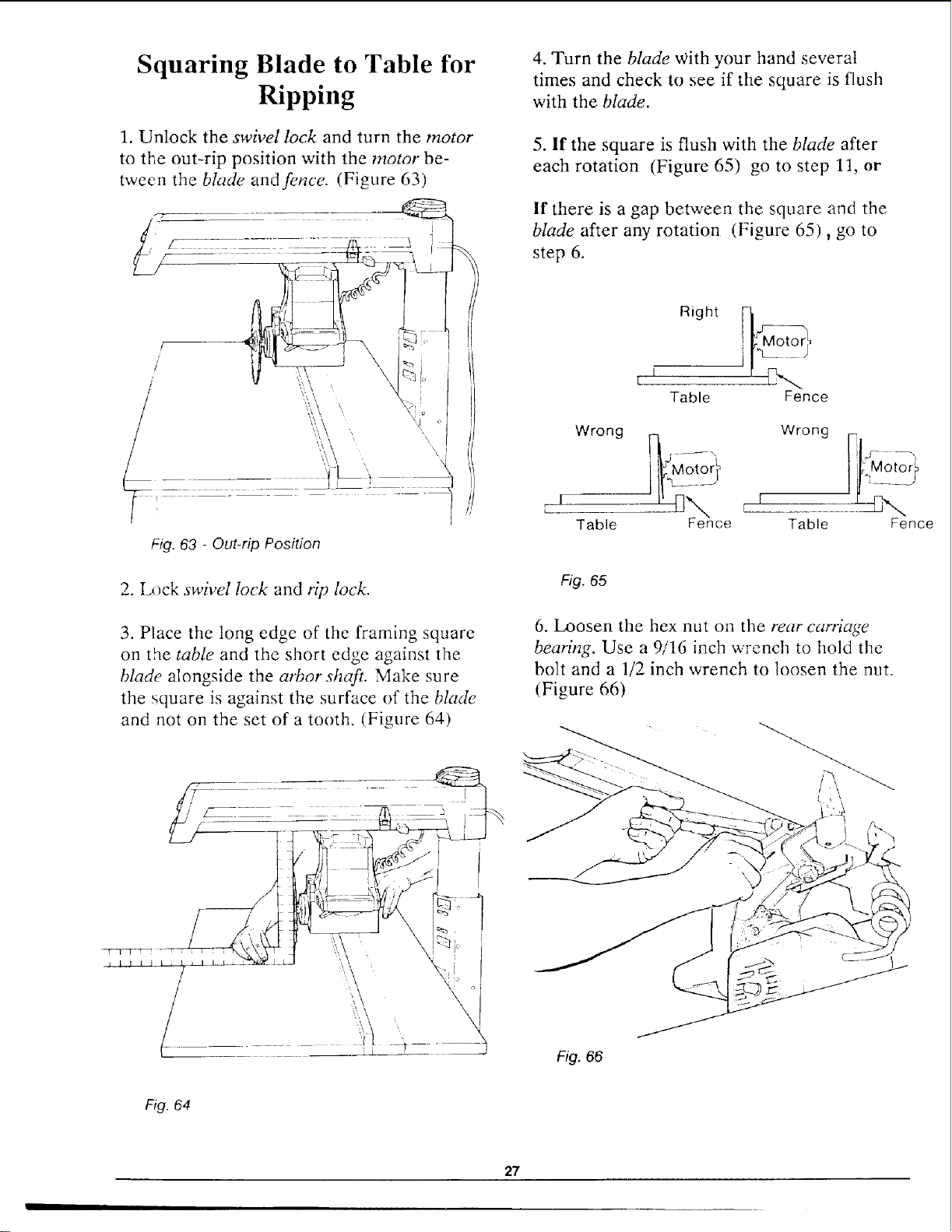
Squaring Blade to Table for
Ripping
4. Turn the blade v_ith your hand several
times and check to see if the square is flush
with the blade.
1. Unlock the swivel lock and turn the motor
to the out-rip position with the motor be-
tween the blade and fence. (Figure 63)
Fig. 63 - Out-rip Position
2. Lock swivel lock and rip lock.
5. If the square is flush with the blade after
each rotation (Figure 65) go to step 11, or
If there is a gap between the square and the
blade after any rotation (Figure 65), go to
step 6.
i Right
Table Fence
<rrM°t% r_t' If
Wrong )_.__F_ 1 Wrong _lu--<_
Table ence Table Fence
Fig. 65
3. Place the long edge of the framing square
on the table and the short edge against the
blade alongside the arbor sh@. Make sure
the square is against the surface of the blade
and not on the set of a tooth. (Figure 64)
6. Loosen the hex nut on the rear carriage
bearing. Use a 9116 inch wrench to hold the
bolt and a 1/2 inch wrench to loosen the nut.
(Figure 66)
Fig. 66
Illlllllll
Fig. 64
27