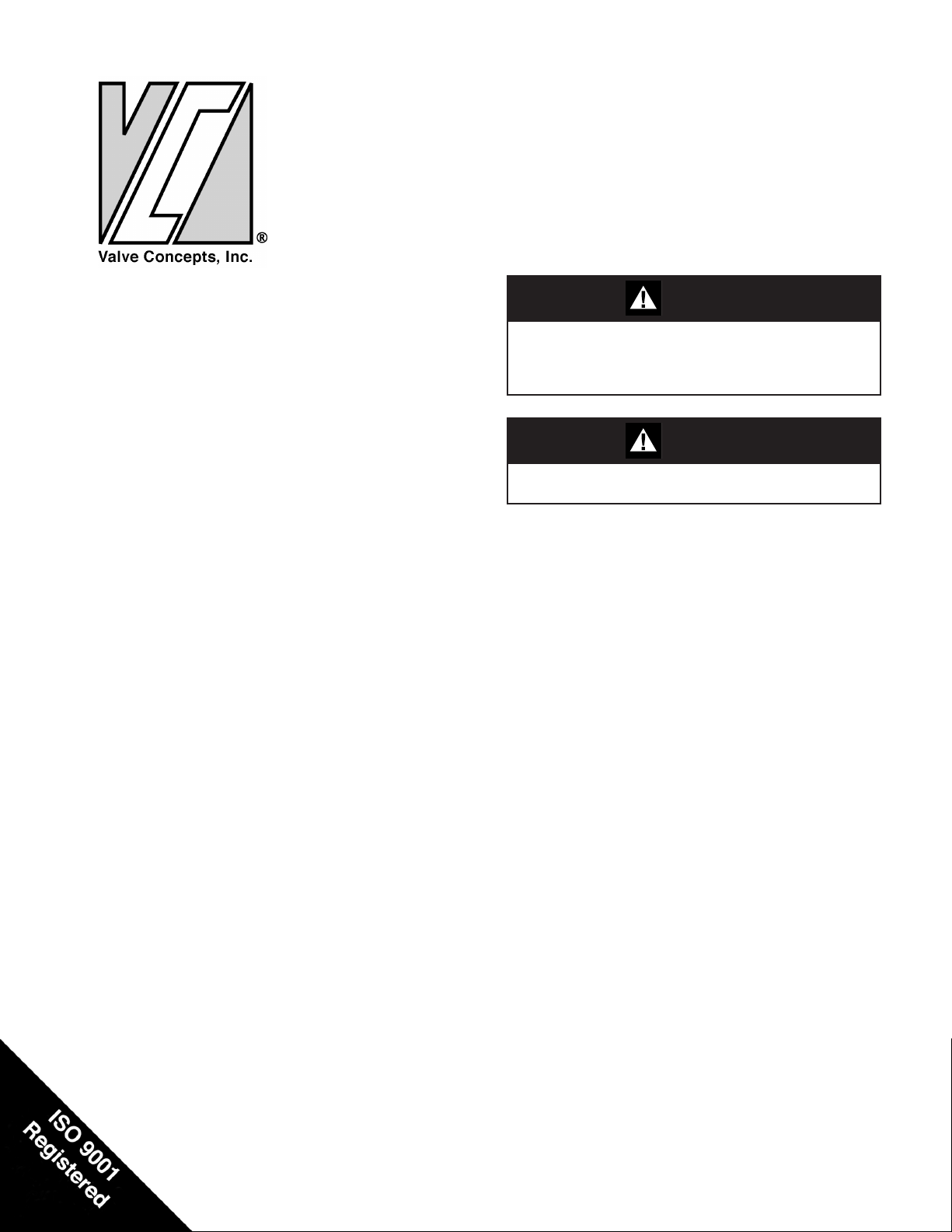
INSTALLATION, OPERATION AND MAINTENANCE MANUAL (IOM)
Model 1049
Secure-Gard Pilot Operated Vent Valve
IOM - 1049
07-05
SECTION I
WARNING
I. DESCRIPTION AND SCOPE
The Model 1049 Secure-Gard is a pilot operated vent
valve intended for installation on atmospheric and low
pressure storage tanks, vapor recovery systems, and
process systems.
The Model 1049 is a low pressure pilot operated valve.
In as such, does not supply vacuum relief. If vacuum
relief is required, it should be provided by a separate
device.
CAUTION
Follow your company’s safety procedures to avoid injury to personnel or damage to equipment.
SECTION II
II. PRIOR TO INSTALLATION
Remove all packing material inside and outside of the valve prior to installation.
SAFETY WARNING: In addition to your company’s safety procedures, this section includes guidelines that should
be followed during the installation, operation, and maintenance of Valve Concepts, Inc’s Pilot Operated Vent Valve.
It is necessary to completely read and understand these guidelines.
Tank or system over pressure protection is the primary function of pilot operated vent valves. It must be selected to
meet the total pressure ow requirements within the Maximum Allowable Working Pressure of the system on which
it is installed. Consult API Standard 2000 for tank protection sizing procedures. Improperly specied vent valves
may result in structural damage to the tank or system, and may cause severe personal injury or death.
Valves are pre-set at the factory per customer purchase specications. DO NOT change the set pressure without
consulting the factory or your local VCI representative. Improper adjustment may cause teh valve to malfunction.
DO NOT attempt to remove the valve from the tank or process vessel without rst bleeding all pressure from the
system. ALTERNATIVE MEANS OF PRESSURE VENTING MUST BE PROVIDED WHEN THE VALVE IS OUT
OF SERVICE.
The valve has been exposed to process while in service. Observe all plant procedures and Material Safety Data
Sheets (MSDS) for the products in the system while inspecting, adjusting, or servicing the valve. Take approriate
safety precautions regarding eye protection, respiration and skin contact.
SECTION III
III. INSTALLATION
The inlet and outlet anges are normally standard ANSI 150 lbs. class anges unless otherwise indicated and
should be connected following accepted piping practices.
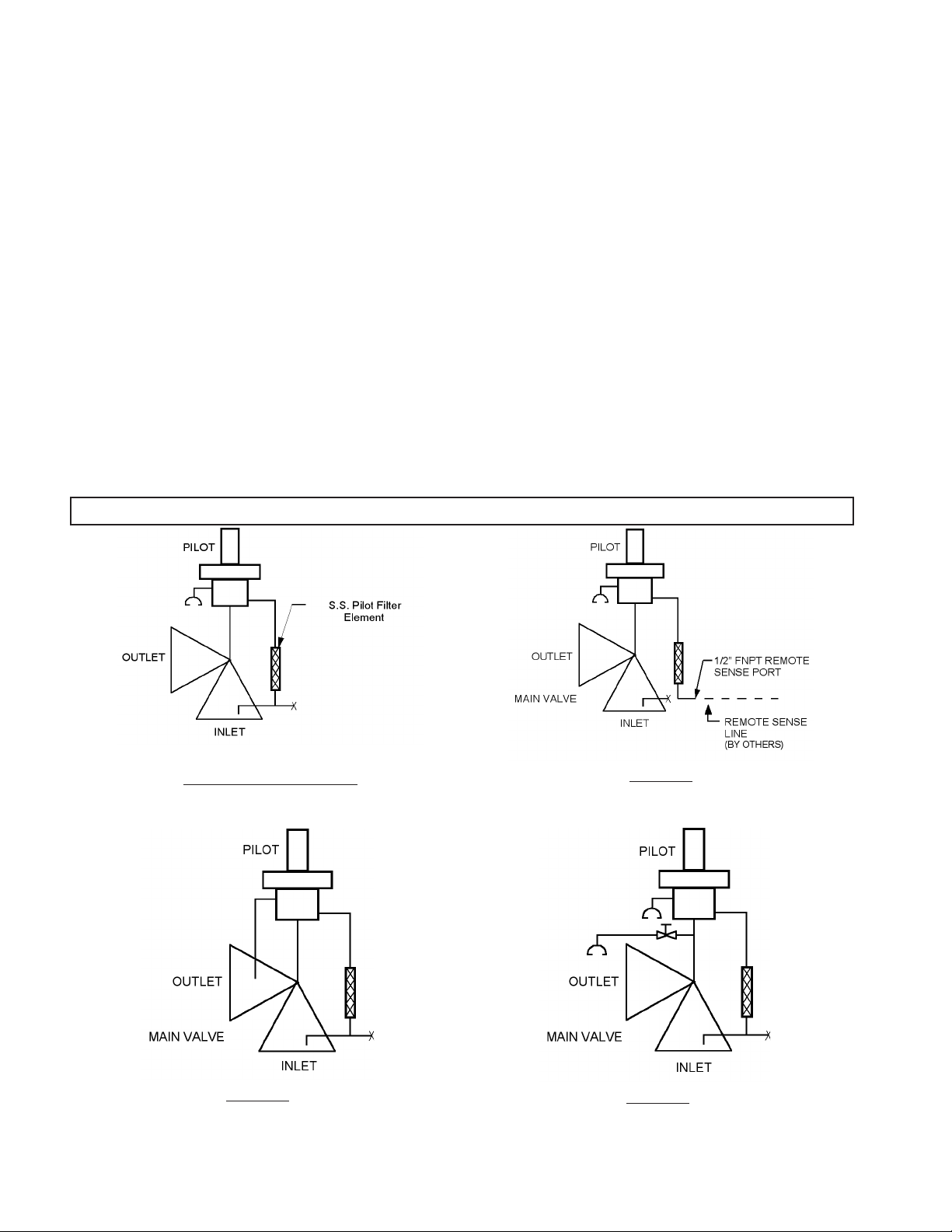
The inlet is vertical and the outlet is horizontal. The
valve should be installed in the normal upright position
with the cap at the top of the valve and the valve inlet at
the bottom. The outlet is to the side.
For valves using the remote sensing port connection,
sense lines should be a 1/2” O.D. tube or larger and the
length should not exceed fteen feet. Longer lengths
may be used with larger diameter sense lines. The
sense line should slope downward from the sense port
to the tank to allow condensate, if any, to drain back
into the tank and not block the sensing capability.
rotameter. (Standard rotameter supplied by Valve Con-
cepts is rated to 250 psig.) Once the gas source is con-
nected, the purge ow can be adjusted by turning the
knob at the top of the rotameter and observing the ow
indicator. The purge mechanism is designed not to affect the set pressure of the vent valve.
When the tank pressure is below set pressure, the main
valve seat will be closed. If the rotameter is mounted
to purge both the pilot sense and discharge lines, there
will be a very small ow to the valve outlet from the
purge mechanism.
VALVES WITH PURGE ROTAMETER
VALVE WITH AIR OR N2 ASSIST:
For valves with a rotameter mounted for purging either
the pilot sense line only or both pilot sense and dis-
charge lines, connect the purge gas source, usually dry
nitrogen, to the 1/4” FNPT connection at the bottom of
the rotameter. The pressure of the purge gas source
must be higher than the set pressure of the vent valve,
but not to exceed the maximum pressure rating of the
For valves with air or nitrogen assist pilot, connect the
gas source to the 1/4” FNPT connection at the inlet of
the lter regulator. The pressure must be a minimum of
5 psig, but not to exceed the maximum pressure rating
of the lter regulator. (The standard lter regulator sup-
plied by Valve Concepts is rated at 300 psig.)
INSTALLATION DIAGRAMS FOR STANDARD ACCESSORIES & CONFIGURATIONS
Standard Conguration
Internal Sensing, SS Pilot Filter Element and
Pilot Exhaust to Atmosphere
Option 1
With Pilot Exhaust Tubed to Main Valve Outlet
With Manual Blowdown Valve
Option 2
With Remote Sensing
Option 3
2 IOM-1049
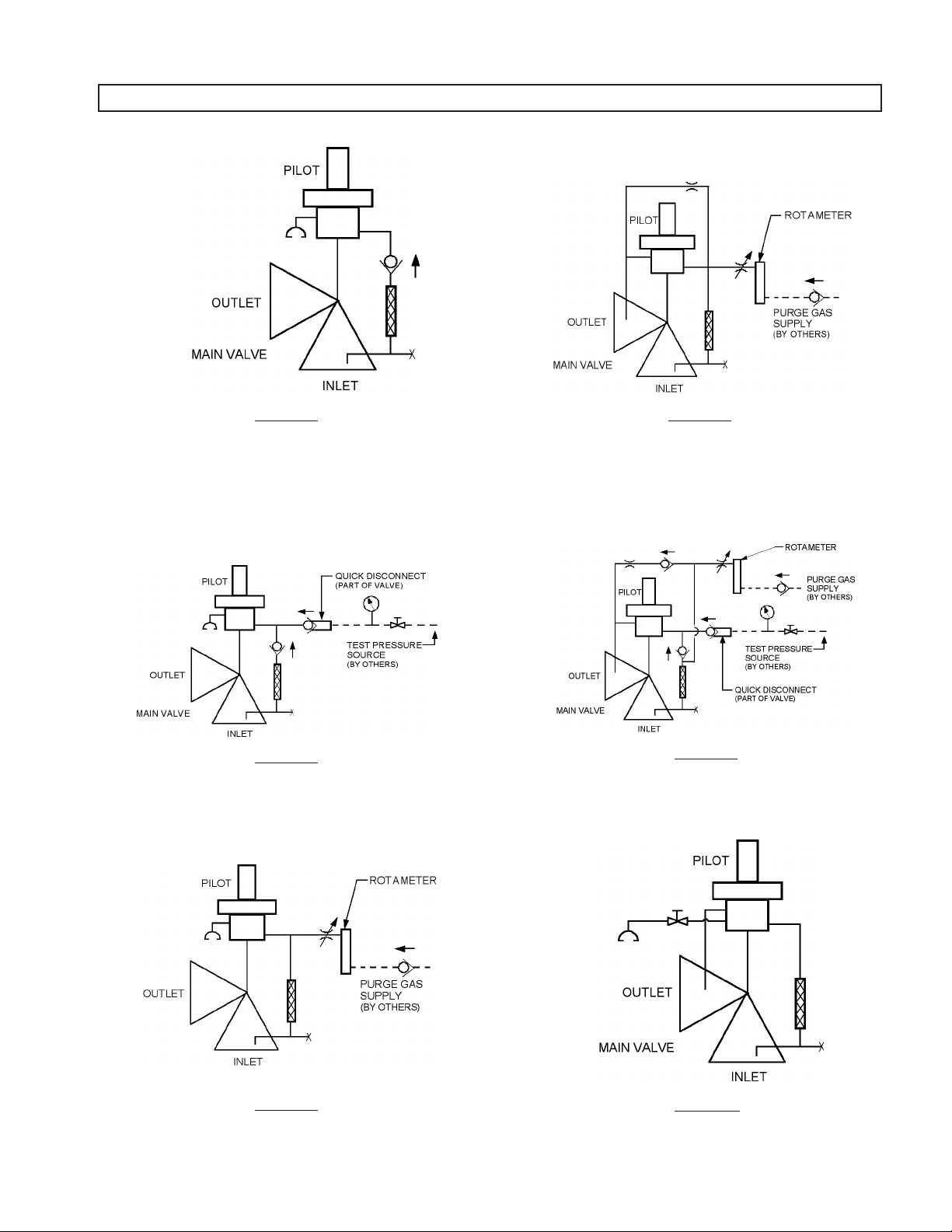
INSTALLATION DIAGRAMS FOR STANDARD ACCESSORIES & CONFIGURATIONS
Option 4
With Back Flow Preventer to Prevent Back Flow
through Main Valve and Pilot
Option 5
With Field Test Connection
(Back Flow Preventer Included)
Option 7
With Rotameter to Purge Pilot Sense
and Discharge Lines
Option 8
With Field Test Connection, Back Flow Preventer and
Rotameter to Purge Pilot Sense and Discharge Lines
Option 6
With Rotameter to Purge Pilot Sense
Option A
Internal Sensing, SS Pilot Filter Element, Pilot Exhaust
to Main Valve Outlet with Manual Blowdown Valve
3IOM-1049