
Installation Instructions
NOTE: Read the entire instruction manual before starting the
installation.
NOTE: Installer: Make sure the Owner's Manual and Service
Instructions are left with the unit after installation,
TABLE OF CONTENTS
PAGE
SAFETY CONSIDERATIONS ......................... 1
INTRODUCTION ................................... 2
RECEIVING AND INSTALLATION ................. 2-16
Check Equipment .................................. 2
Identify Unit .................................... 2
Inspect Shipment ................................. 2
Provide Unit Support ............................... 2
Roof Curb ...................................... 2
Slab Mount ..................................... 2
Ground Mount .................................. 2
Provide Clearances ................................. 2
Rig and Place Unit ................................. 2
Inspection ...................................... 2
Installation ...................................... 2
Select and Install Ductwork ........................... 5
Converting Horizontal Discharge Units to Downflow
(Vertical) Discharge Units .......................... 7
Provide for Condensate Disposal ...................... 7
Install Electrical Connections ......................... 7
High-Voltage Connections ......................... 8
Routing Power Leads into Unit ...................... 8
Connecting Ground lead to Ground Lug ............... 8
Routing Control Power Wires (24-v) ................. 8
Easy Select _ . ................................... 9
50XZ Sequence of Operation ...................... 15
Special Procedures for 208-V Operation .............. 16
PRE-START-UP ................................... 16
START-UP ..................................... 16-19
50XZ Start-Up ................................... 16
Check for Refrigerant Leaks ......................... 17
Start-Up Adjustments ............................. 17
Check Cooling & Heating Operation ................. 17
Checking & Adjusting Refrigerant Charge ............ 18
Refrigerant Charge .............................. 18
No Charge ..................................... 18
Low Charge Cooling ............................. 18
To Use Cooling Charging Charts .................... 18
Indoor Airflow & Airflow Adjustments .............. 18
Defrost Control ................................... 19
Quiet Shift ..................................... 19
Defrost ....................................... 19
MAINTENANCE ................................ 20-25
Air Filter ........................................ 20
Indoor Blower and Motor ........................... 20
Outdoor Coil, Indoor Coil, & Condensate Drain Pan ...... 20
Outdoor Fan ..................................... 23
Electrical Controls and Wiring ....................... 23
Refrigerant Circuit ................................. 23
®
Turn to the Expertg
C99088
Fig. 1 - Unit 50XZ
Indoor Airflow ................................... 23
Metering Devices- TXV &AccuRater TM Piston .......... 23
Pressure Switches ................................. 24
Loss of Charge Switch ............................. 24
High Pressure Switch .............................. 24
Copeland Scroll compressor (Puron Refrigerant) ......... 24
Refrigerant System ................................ 24
Refrigerant .................................... 24
Compressor Oil ................................. 24
Servicing Systems on Roofs with Synthetic Materials .... 24
Liquid Line Filter Drier ........................... 25
Puron® (R-410A) Refrigerant Charging ............. 25
System Information ................................ 25
Loss of Charge Switch ............................ 25
Check Defrost Thermostat ......................... 25
TROUBLESHOOTING .............................. 25
START-UP CHECKLIST ............................ 25
SAFETY CONSIDERATIONS
Improper installation adjustment, alteration, service, maintenance,
or use can cause explosion, fire, electrical shock, or other
conditions which may cause death, personal injury, or property
damage. Consult a qualified installer, service agency, or your
distributor or branch for information or assistance. The qualified
installer or agency must use factory-authorized kits or accessories
when modifying this product Refer to the individual instructions
packaged with the kits or accessories when installing.
Follow all safety codes. Wear safety glasses, protective clothing,
and work gloves. Use quenching cloth for brazing operations.
Have a fire extinguisher available. Read these instructions
thoroughly and follow all warnings or cautions included in
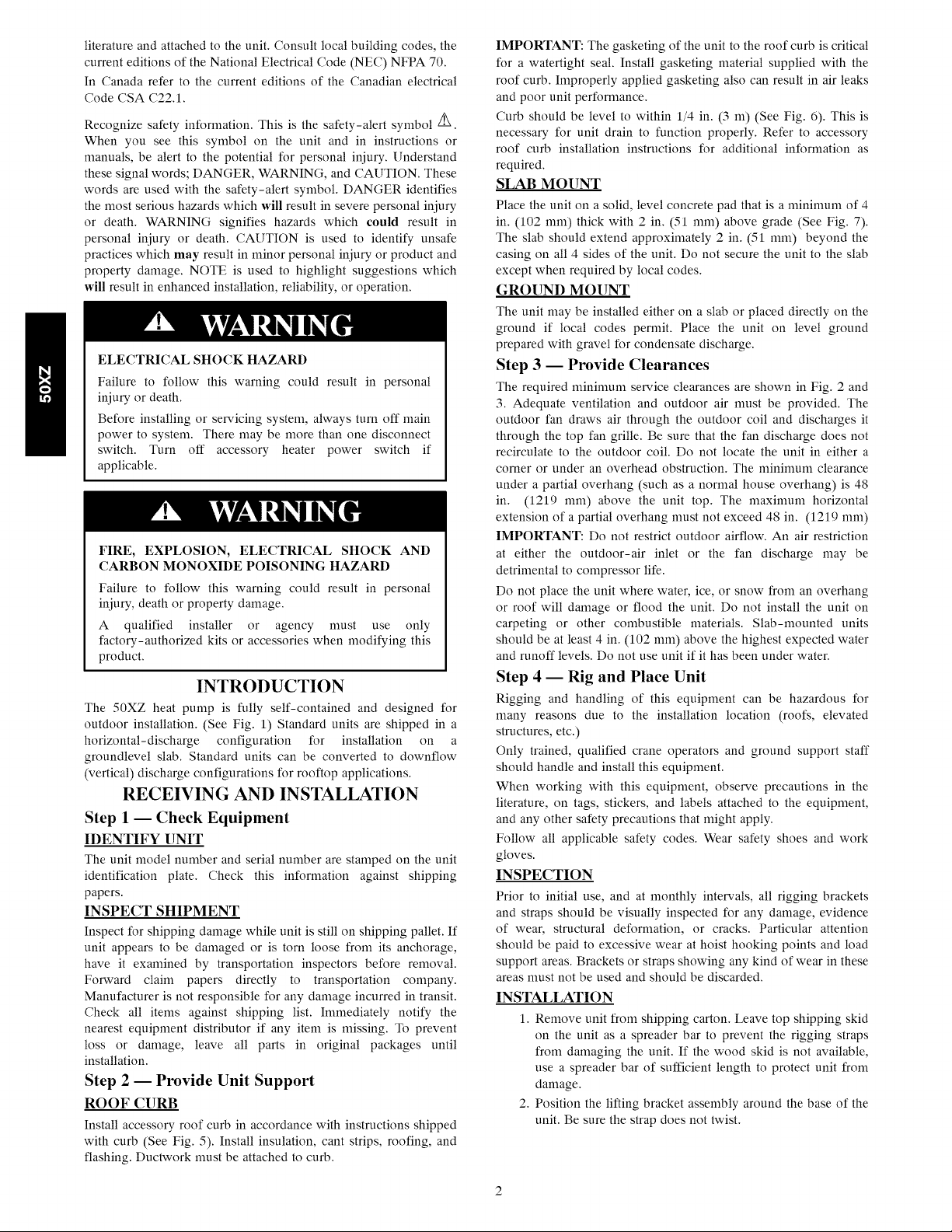
literatureandattachedto the unit. Consult local building codes, the
current editions of the National Electrical Code (NEC) NFPA 70.
In Canada refer to the current editions of the Canadian electrical
Code CSA C22A.
Recognize safety information. This is the safety-alert symbol /_.
When you see this symbol on the unit and in instructions or
manuals, be alert to the potential for personal injury. Understand
these signal words; DANGER, WARNING, and CAUTION. These
words are used with the safety-alert symbol. DANGER identifies
the most serious hazards which will result in severe personal injury
or death. WARNING signifies hazards which could result in
personal injury or death. CAUTION is used to identify unsafe
practices which may result in minor personal injury or product and
property damage. NOTE is used to highlight suggestions which
will result in enhanced installation, reliability, or operation.
ELECTRICALSHOCK HAZARD
Failure to follow this warning could result in personal
injury or death.
Before installing or servicing system, always turn off main
power to system. There may be more than one disconnect
switch. Turn off accessory heater power switch if
applicable.
FIRE, EXPLOSION, ELECTRICAL SHOCK AND
CARBON MONOXIDE POISONING HAZARD
Failure to follow this warning could result in personal
injury, death or property damage.
A qualified installer or agency must use only
factory-authorized kits or accessories when modifying this
product.
INTRODUCTION
The 50XZ heat pump is fully self-contained and designed for
outdoor installation. (See Fig. 1) Standard units are shipped in a
horizontal-discharge configuration for installation on a
groundlevel slab. Standard units can be converted to downflow
(vertical) discharge configurations for rooftop applications.
RECEIVING AND INSTALLATION
Step 1 -- Check Equipment
IDENTIFY UNIT
The unit model number and serial number are stamped on the unit
identification plate. Check this information against shipping
papers.
INSPECT SHIPMENT
Inspect for shipping damage while unit is still on shipping pallet. If
unit appears to be damaged or is torn loose from its anchorage,
have it examined by transportation inspectors before removal.
Forward claim papers directly to transportation company.
Manufacturer is not responsible for any damage incurred in transit.
Check all items against shipping list. Immediately notify the
nearest equipment distributor if any item is missing. To prevent
loss or damage, leave all parts in original packages until
installation.
Step 2 -- Provide Unit Support
ROOF CURB
Install accessory roof curb in accordance with instructions shipped
with curb (See Fig. 5). Install insulation, cant strips, roofing, and
flashing. Ductwork must be attached to curb.
IMPORTANT: The gasketing of the unit to the roof curb is critical
for a watertight seal. Install gasketing material supplied with the
roof curb. Improperly applied gasketing also can result in air leaks
and poor unit performance.
Curb should be level to within 1/4 in. (3 m) (See Fig. 6). This is
necessary for unit drain to function properly. Refer to accessory
roof curb installation instructions for additional information as
required.
SLAB MOUNT
Place the unit on a solid, level concrete pad that is a minimum of 4
in. (102 mm) thick with 2 in. (51 mm) above grade (See Fig. 7).
The slab should extend approximately 2 in. (51 mm) beyond the
casing on all 4 sides of the unit. Do not secure the unit to the slab
except when required by local codes.
GROUND MOUNT
The unit may be installed either on a slab or placed directly on the
ground if local codes permit. Place the unit on level ground
prepared with gravel for condensate discharge.
Step 3 -- Provide Clearances
The required minimum service clearances are shown in Fig. 2 and
3. Adequate ventilation and outdoor air must be provided. The
outdoor fan draws air through the outdoor coil and discharges it
through the top fan grille. Be sure that the fan discharge does not
recirculate to the outdoor coil. Do not locate the unit in either a
corner or under an overhead obstruction. The minimum clearance
under a partial overhang (such as a normal house overhang) is 48
in. (1219 mm) above the unit top. The maximum horizontal
extension of a partial overhang must not exceed 48 in. (1219 mm)
IMPORTANT: Do not restrict outdoor airflow. An air restriction
at either the outdoor-air inlet or the fan discharge may be
detrimental to compressor life.
Do not place the unit where water, ice, or snow from an overhang
or roof will damage or flood the unit. Do not install the unit on
carpeting or other combustible materials. Slab-mounted units
should be at least 4 in. (102 mm) above the highest expected water
and runoff levels. Do not use unit if it has been under water.
Step 4 -- Rig and Place Unit
Rigging and handling of this equipment can be hazardous for
many reasons due to the installation location (roofs, elevated
structures, etc.)
Only trained, qualified crane operators and ground support staff
should handle and install this equipment.
When working with this equipment, observe precautions in the
literature, on tags, stickers, and labels attached to the equipment,
and any other safety precautions that might apply.
Follow all applicable safety codes. Wear safety shoes and work
gloves.
INSPECTION
Prior to initial use, and at monthly intervals, all rigging brackets
and straps should be visually inspected for any damage, evidence
of wear, structural deformation, or cracks. Particular attention
should be paid to excessive wear at hoist hooking points and load
support areas. Brackets or straps showing any kind of wear in these
areas must not be used and should be discarded.
INSTALLATION
1. Remove unit from shipping carton. Leave top shipping skid
on the unit as a spreader bar to prevent the rigging straps
from damaging the unit. If the wood skid is not available,
use a spreader bar of sufficient length to protect unit from
damage.
2. Position the lifting bracket assembly around the base of the
unit. Be sure the strap does not twist.
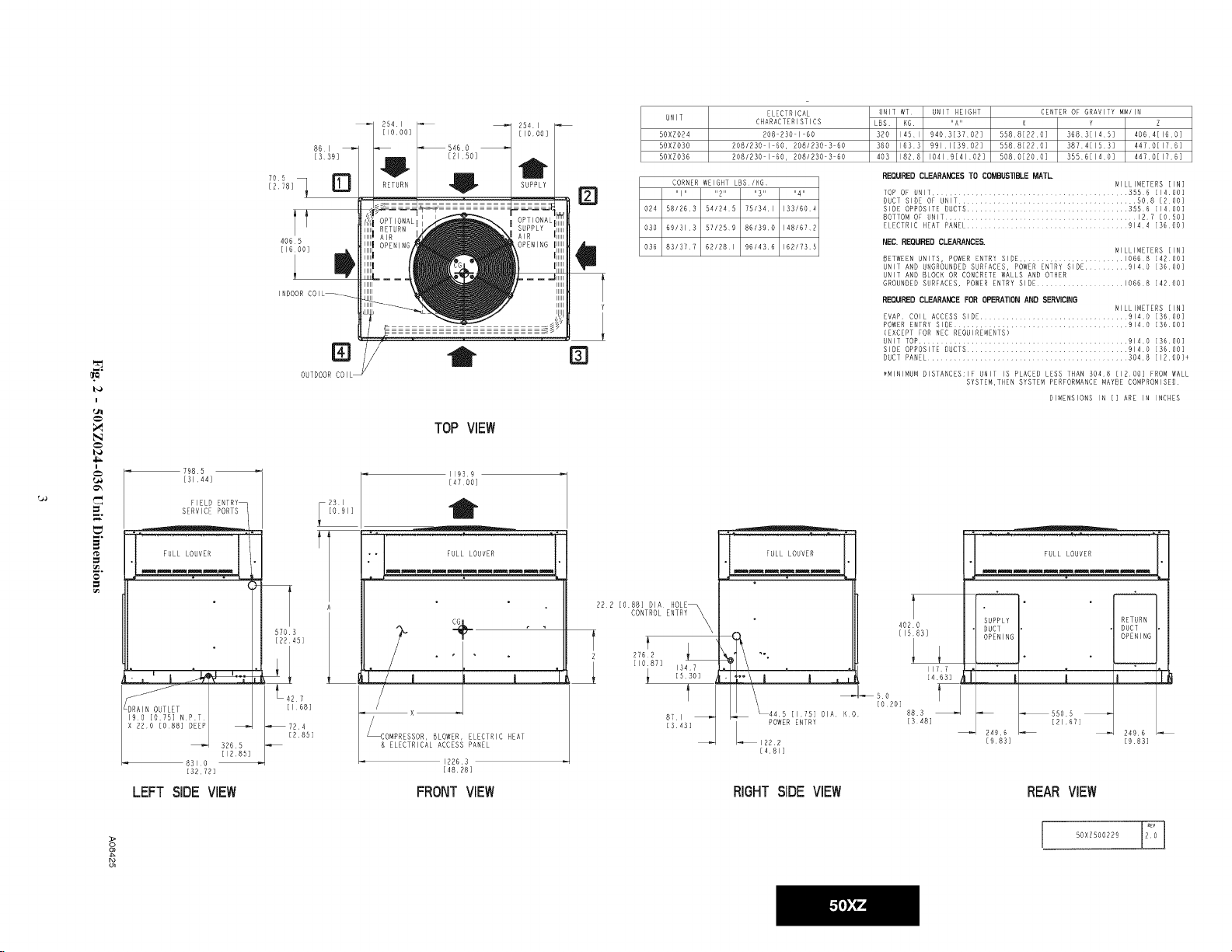
UNIT
3OXZOR4
5460
705
[878]
861
[359]
It
,t06 5
[16 DO]
INDOOR
ml
I
@
OUTDOOR COIL
T
Y
53XZO30
50XZO38
CORNER WEIGHT LBS/HG
III .... 2 .... 3 .... 4.
024 581263 34/243 731341 133/604
030 89/313 37/259 86/390 1481672
036 83/377 62/281 96/436 162/735
ELECTRICAL
CHARACTERISTICS
208 230 I 60
2031230 I 60, 2031230 3 60
208/230 I 60, 2031230 3 60
UNIT WT UNIT HEIGHT
LBS KG IIAII
320 1451 940313702]
360 1633 991113902]
403 1828 1041R[4102]
REO_RED CLEARANCES TO COMBUSTIBLE MATL.
TOP OF UNIT ............................. 355 6 [1400]
DUCT SIDE OF UNIT ............................ 508 [2 00]
SIDE OPPOSITE DUSTS ........................ 355 6 [14 O0]
BOTTOM OF UNIT ................................... 127 [OBO]
ELECTRIC HEAT PANEL ................................ 9144 [3600]
NEC. REQUIRED CLEARANCES
BETWEEN UNITS, POWER ENTRY SIDE ................. I066 8 [42 00]
UNIT AND UNGROUNDED SURFACES, POWER ENTRY SIDE ........ 9140 [3600]
UNIT AND BLOCK OR CONCRETE WALLS AND OTHER
GROUNDED SURFACES, POWER ENTRY SIDE .................. 10668 [4200]
REG_RED CLEARANCE FOR OPERATION AND SERVICING
EVAP COIL ACCESS SIDE ..................... 91_0 [36 OO]
POWER ENTRY SIDE ............................ 91_0 [3600]
(EXCEPT FOR NEC REQUIREMENTS)
UNIT TOP ........................................... 91_0 [3600]
SIDE OPPOSITE DUCTS .................................... 9140 [3600]
DUCT PANEL.............................................. 3048 [12DO]+
_MINIMUM DISTANCES:IF UNIT IS PLACED LESS THAN 3048 [1200] FROM WALL
SYSTEM,THEN SYSTEM PERFORMANCE MAYBE COMPROMISED
CENTER OF GRAVITY MMIIN
5588[220] 3874[153] 4470[176]
50801200] 3556[140] 4470[176]
Y Z
3683[145] 4064[160]
MILLIMETERS [IN]
MILLIMETERS [IN]
MILLIMETERS [IN]
DIMENSIONS IN [] ARE IN INCHES
TOP VIEW
I
_7985
[31 44]
FIELD ENTRY_
SERVICE PORTS I
11939
[4700]
t
=
_°
LEFT SIDE VIEW
>
o
FULL LOUVER
8310
[3272]
[1285]
5703
[2245]
427
[I 68]
[285]
o, FULL LOUVER
A
, /
I
n m _
_COMPRESSOR, BLOWER, ELECTRIC HEAT
& ELECTRICAL ACCESS PANEL
FRONTVIEW
12263
[4828]
,_FULL LOUVER
[088] DIA HOLE
222 CONTROL ENTRY_
Z 2762 X
t
[1087] 13
[530]
871 _
[343]
N
\
_BO
5 [I 75] DIA KO
POWER ENTRY
1222
[481]
[O2O]
4020
[1583]
88 3 _
[3 48]
t
_ii _'-_-_ .... _ •° mm_ FULL_O_LOUVER
SUPPLY
• DUCT
OPENING
117 !
[463]
°
PaR6 2496
[983] [985]
_5505
[2167]
RETURN
DUCT
OPENING
1
RIGHTSIDEVIEW REARVIEW
3DXZBDO22R/%

UNIT
50XZO42
50XZO48
SOXZO6O
CORNER WEIGHT LBS/KG
III .... 2 .... 3 .... 411
042 961436 591268 124/563 175/795
[16 01]
INDOOR COIL
[_ /
OUTDOOR COIL _VI
I
Q D
048 1021463 651295 131/595 1811822
000 107/486 70/318 136/617 186/844
ELECTRICAL
CHARACTERISTICS
208 230 I 60, 208/230 3 60
208 230 I 60, 208/230 3 60
208 230 I 60, 208/230 3 60
REQUIRED CLEARANCES TO COMBUSTIBLE MATL.
TOP OF UNIT ........................................ 3556 [1400]
DUCT SIDE OF UNIT .............................. 508 [200]
SIDE OPPOSITE DUCTS ....................... 355 6 [14 003
BOTTOM OF UNIT ........................... 127 [0 50]
ELECTRIC HEAT _ANEL ..................................... 9144 [3600]
NEC. REQUIRED CLEARANCES.
BETWEEN UNITS, POWER ENTRY SIDE ....................... 10658 [4200]
UNIT AND UNGROUNDED SURFACES, POWER ENTRY SIDE ........ 9140 [3600]
UNIT AND _LOCK OR CONCRETE WALLS AND OTHER
GROUNDED SURFACES, POWER ENTRY SIDE ........... 10668 [4200]
REQUIRED CLEARANCE FOR OPERATION AND SERVICING
EVAP COIL ACCESS SIDE .................................. 9140 [3600]
°OWER ENTRY SlOE ........................................ 9140 [3000]
(EXCEPT FOR NEC REQUIREMENTS)
UNIT TOP.................................. 9140 [3600]
SIDE OPPOSITE DUCTS ...................... 9140 [3600]
DUCT PANEL ............................ 3048 [1200]_
_MINIMUM DISTANCES:IF UNIT IS PLACED LESS THAN 3048 [1200] FROM WALL
UNIT WT UNIT HEIGHT CENTER OF GRAVITv MM/IN
LBS HG "A" Y Z
4Sa 206 10917[4298] 4476[176] _572[180]
479 217 11425[4_983 4953[1953 4476[1763 4572[1803
499 226 1193 3[4698] 5334[21 O] 5080[20 O] 4_20[17,6]
MILLIMETERS [IN]
MILLIMETERS [IN]
MILLIMETERS [IN]
SYSTEM,THEN SYSTEM PERFORMANCE MAYBE COMPROMISED
DIMENSIONS IN [] ARE IN INCHES
TOP VIEW
11939
&
r_
10906
[4294]
SERVICE FORTS i
FIELD ENTRY_
230
I E091]
[4700]
/
FULL LOUVER
_°
75] DIA HO
445 [I POWER ENTRY_
5292
o>
2
2
427 •
[168] DRAIN OUTLET
190 [075] NPT
X 220 [088] DP [1295]
11231
[4422]
LEFT SIDE VIEW
:2442]
_x I
COMPRESSOR, BLOWER, ELECTRIC HEAT
& ELECTRICAL ACCESS PANEL
12263
[4828]
FRONT VIEW
T t
326 I
[1284]
869
[481]
[342]
IR20
FULL LOUVER
[088] OlA HOLE
CONTROL ENTRY
RIGHT SIDE VIEW
_4 I
[0 16]
402 0
[15 83]
t
1177
[4 63]
.,_j FULL LOUVER m
SUPPLY RETURN
DUCT • DUCT .
OPENING
.___J__ I 1 --4.
_872 _3413
[343] E1367]
_3512 _ _B51 2 '_
[1383] [1383]
REAR VIEW
50XZSOO183
[ D
rev
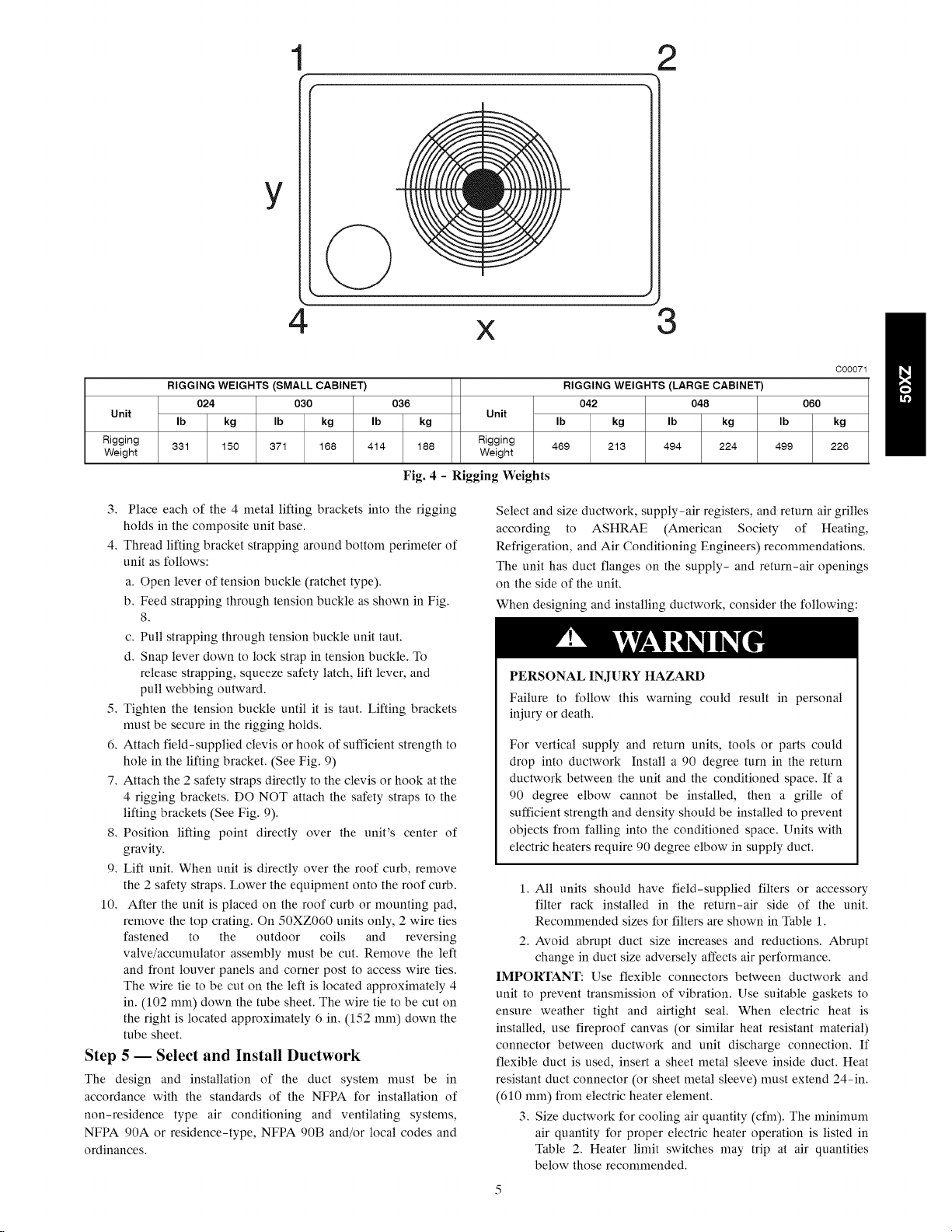
Unit
Rigging
Weight
1 2
Y
RIGGING WEIGHTS (SMALL CABINET)
024 030 036
Ib kg Ib kg Ib kg Unit
331 150 371 168 414 188 RiggingWeight
Fig. 4 - Rigging Weights
C00071
RIGGING WEIGHTS (LARGE CABINET)
042 048 060
3. Place each of the 4 metal lifting brackets into the rigging
holds in the composite unit base.
4. Thread lifting bracket strapping around bottom perimeter of
unit as follows:
a. Open lever of tension buckle (ratchet type).
b. Feed strapping through tension buckle as shown in Fig.
8.
c. Pull strapping through tension buckle unit taut.
d. Snap lever down to lock strap in tension buckle. To
release strapping, squeeze safety latch, lift lever, and
pull webbing outward.
5. Tighten the tension buckle until it is taut. Lifting brackets
must be secure in the rigging holds.
6. Attach field-supplied clevis or hook of sufficient strength to
hole in the lifting bracket. (See Fig. 9)
7. Attach the 2 safety straps directly to the clevis or hook at the
4 rigging brackets. DO NOT attach the safety straps to the
lifting brackets (See Fig. 9).
8. Position lifting point directly over the unit's center of
gravity.
9. Lift unit. When unit is directly over the roof curb, remove
the 2 safety straps. Lower the equipment onto the roof curb.
10. After the unit is placed on the roof curb or mounting pad,
remove the top crating. On 50XZ060 units only, 2 wire ties
fastened to the outdoor coils and reversing
valve/accumulator assembly must be cut. Remove the left
and front louver panels and corner post to access wire ties.
The wire tie to be cut on the left is located approximately 4
in. (102 mm) down the tube sheet. The wire tie to be cut on
the right is located approximately 6 in. (152 mm) down the
tube sheet.
Step 5 -- Select and Install Ductwork
The design and installation of the duct system must be in
accordance with the standards of the NFPA for installation of
non-residence type air conditioning and ventilating systems,
NFPA 90A or residence-type, NFPA 90B and/or local codes and
ordinances.
Select and size ductwork, supply-air registers, and return air grilles
according to ASHRAE (American Society of Heating,
Refrigeration, and Air Conditioning Engineers) recommendations.
The unit has duct flanges on the supply- and return-air openings
on the side of the unit.
When designing and installing ductwork, consider the following:
PERSONAL INJURY HAZARD
Failure to follow this warning could result in personal
injury or death.
For vertical supply and return units, tools or parts could
drop into ductwork Install a 90 degree turn in the return
ductwork between the unit and the conditioned space. If a
90 degree elbow cannot be installed, then a grille of
sufficient strength and density should be installed to prevent
objects from falling into the conditioned space. Units with
electric heaters require 90 degree elbow in supply duct.
1. All units should have field-supplied filters or accessory
filter rack installed in the return-air side of the unit.
Recommended sizes for filters are shown in Table 1.
2. Avoid abrupt duct size increases and reductions. Abrupt
change in duct size adversely affects air performance.
IMPORTANT: Use flexible connectors between ductwork and
unit to prevent transmission of vibration. Use suitable gaskets to
ensure weather tight and airtight seal. When electric heat is
installed, use fireproof canvas (or similar heat resistant material)
connector between ductwork and unit discharge connection. If
flexible duct is used, insert a sheet metal sleeve inside duct. Heat
resistant duct connector (or sheet metal sleeve) must extend 24-in.
(610 mm) from electric heater element.
3. Size ductwork for cooling air quantity (cfm). The minimum
air quantity for proper electric heater operation is listed in
Table 2. Heater limit switches may trip at air quantities
below those recommended.
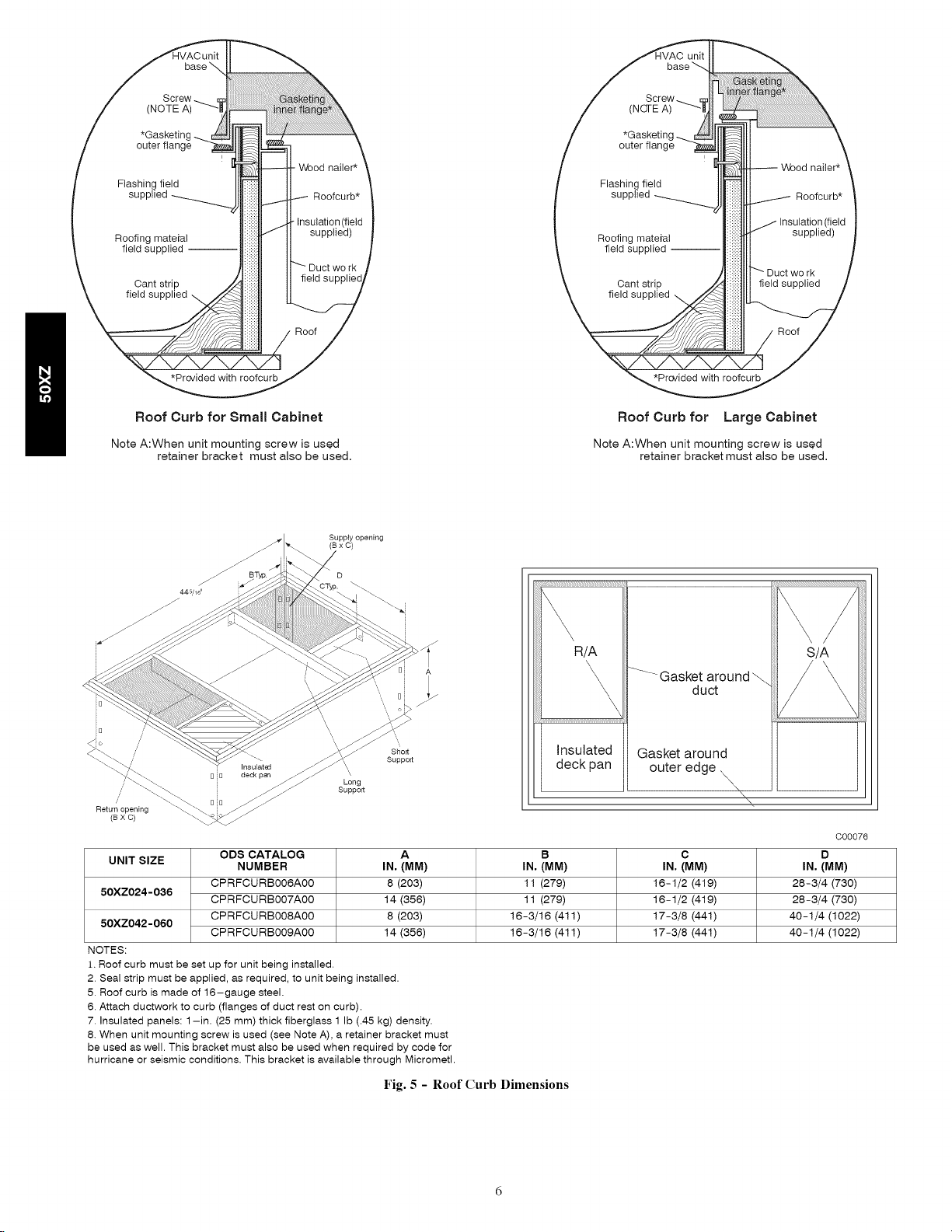
field supplied
/ base
/ ,,,_crew'_._
/ (NOTEA) _
/ *Gasketin;...__
I Flashing field II1_11t
I supplied _ _n_il_ Roofcurb*
II_i;llltJ Insulation(field
Roofing matei'at II ii l" supplied)
\
_, /l_!i:llll _ Duct we rk j
\ c__tllt field supplied /
Roof Curb for Small Cabinet
Note A:When unit mounting screw is used
retainer bracket must also be used.
Supply opening
(BxC)
Roof Curb for Large Cabinet
Note A:When unit mounting screw is used
retainer bracket must also be used.
R/A
_ Gasket around \.
Insulated Gasket around
deck pan outer edge \
ODS CATALOG
UNIT SIZE IN. (MM) IN. (MM) IN. (MM)
50XZ024-036 14 (356) 11 (279) 16-1/2 (419)
50XZ042-060 8 (203) 16-3/16 (411 ) 17-3/8 (441)
NOTES:
1. Roof curb must be set up for unit being installed,
2. Seal strip must be applied, as required, to unit being installed.
5. Roof curb is made of 16-gauge steel,
6. Attach ductwork to curb (flanges of duct rest on curb).
7. Insulated panels: 1-in. (25 mm) thick fiberglass 1 Ib (.45 kg) density.
8, When unit mounting screw is used (see Note A), a retainer bracket must
be used as well. This bracket must also be used when required by code for
hurricane or seismic conditions. This bracket is available through Micrometl.
NUMBER
CPRFCURB006A00
CPRFCURB007A00
CPRFCURB008A00
CPRFCURB009A00
A B C
8 (203) 11 (279) 16-1/2 (419)
14 (356) 16-3/16 (411) 17-3/8 (441)
Fig. 5 - Roof Curb Dimensions
duct
\/
S/A
/2
/ \
\\
\
C00076
D
IN. (MM)
28-3/4 (730)
28-3/4 (730)
40-1/4 (1022)
40-1/4 (1022)
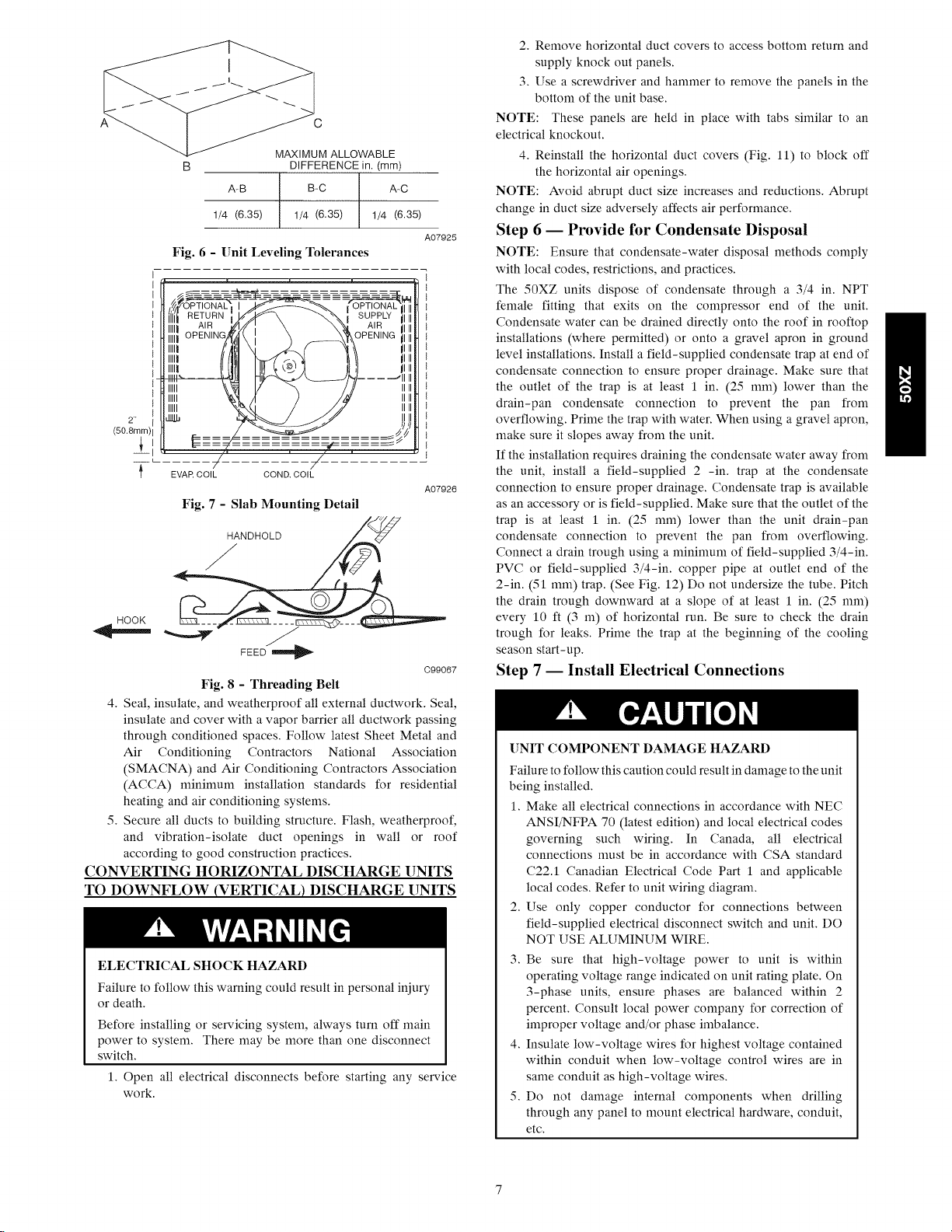
B
A-B
1/4 (6.35)
Fig. 6 - Unit Leveling Tolerances
ill_RETURN
AIR
MAXIMUM ALLOWABLE
DIFFERENCE in. (mm)
B-C ArC
1/4 (6.35) 1/4 (6.35)
A07925
IIIIIOPEN'NGt
IIIII /'
IIII| [[[
III1! I_l
IIIII....
IIIII \
IIIII
IIIII IIII
2"
(50.8ram)
±
EVAR COIL COND. COIL
A07926
Fig. 7 - Slab Mounting Detail
oo
FEED
C99067
Fig. 8 - Threading Belt
4. Seal, insulate, and weatherproof all external ductwork. Seal,
insulate and cover with avapor barrier all ductwork passing
through conditioned spaces. Follow latest Sheet Metal and
Air Conditioning Contractors National Association
(SMACNA) and Air Conditioning Contractors Association
(ACCA) minimum installation standards for residential
heating and air conditioning systems.
5. Secure all ducts to building structure. Flash, weatherproof,
and vibration-isolate duct openings in wall or roof
according to good construction practices.
CONVERTING HORIZONTAL DISCHARGE UNITS
TO DOWNFLOW (VERTICAL) DISCHARGE UNITS
ELECTRICAL SHOCK HAZARD
Failure to follow this warning could result in personal iniury
or death.
Before installing or servicing system, always turn off main
power to system. There may be more than one disconnect
switch.
1. Open all electrical disconnects before starting any servace
work.
2. Remove horizontal duct covers to access bottom return and
supply knock out panels.
3. Use a screwdriver and hammer to remove the panels in the
bottom of the unit base.
NOTE: These panels are held in place with tabs similar to an
electrical knockout.
4. Reinstall the horizontal duct covers (Fig. 11) to block off
the horizontal air openings.
NOTE: Avoid abrupt duct size increases and reductions. Abrupt
change in duct size adversely affects air performance.
Step 6 -- Provide for Condensate Disposal
NOTE: Ensure that condensate-water disposal methods comply
with local codes, restrictions, and practices.
The 50XZ units dispose of condensate through a 3/4 in. NPT
female fitting that exits on the compressor end of the unit.
Condensate water can be drained directly onto the roof in rooftop
installations (where permitted) or onto a gravel apron in ground
level installations. Install a field-supplied condensate trap at end of
condensate connection to ensure proper drainage. Make sure that
the outlet of the trap is at least 1 in. (25 mm) lower than the
drain-pan condensate connection to prevent the pan from
overflowing. Prime the trap with water. When using a gravel apron,
make sure it slopes away from the unit.
If the installation requires draining the condensate water away from
the unit, install a field-supplied 2 -in. trap at the condensate
connection to ensure proper drainage. Condensate trap is available
as an accessory or is field-supplied. Make sure that the outlet of the
trap is at least 1 in. (25 mm) lower than the unit drain-pan
condensate connection to prevent the pan from overflowing.
Connect a drain trough using a minimum of field-supplied 3/4-in.
PVC or field-supplied 3/4-in. copper pipe at outlet end of the
2-in. (51 mm) trap. (See Fig. 12) Do not undersize the tube. Pitch
the drain trough downward at a slope of at least 1 in. (25 mm)
every 10 ft (3 m) of horizontal run. Be sure to check the drain
trough for leaks. Prime the trap at the beginning of the cooling
season start-up.
Step 7 -- Install Electrical Connections
UNIT COMPONENT DAMAGE HAZARD
Failure to follow this caution could result in damage to the unit
being installed.
1. Make all electrical connections in accordance with NEC
ANSI/NFPA 70 (latest edition) and local electrical codes
governing such wiring. In Canada, all electrical
connections must be in accordance with CSA standard
C22.1 Canadian Electrical Code Part 1 and applicable
local codes. Refer to unit wiring diagram.
2. Use only copper conductor for connections between
field-supplied electrical disconnect switch and unit. DO
NOT USE ALUMINUM WIRE.
3. Be sure that high-voltage power to unit is within
operating voltage range indicated on unit rating plate. On
3-phase units, ensure phases are balanced within 2
percent. Consult local power company for correction of
improper voltage and/or phase imbalance.
4. Insulate low-voltage wires for highest voltage contained
within conduit when low-voltage control wires are in
same conduit as high-voltage wires.
5. Do not damage internal components when drilling
through any panel to mount electrical hardware, conduit,
etc.

PLACE RIGGING BRACKET ASSEMBLY IN 4
HAND HOLES AND INSTALL TIE DOWN STRAP
AROUND PERIMETER OF UNIT AND THROUGH
SEE DETAIL A
U NIT 50XZ A B
024 19.0 18.25 463.6
030 19.0 18.25 463.6
036 20.0 19.0 482.6
042 20.0 2t .25 539.8
048 20.0 2t .25 539.8
060 2t .0 20.0 508.0
in, in, mm
SPACE IN BRACKET ASSEMBLY
Fig. 9 - Suggested Rigging
ELECTRICAL SHOCK HAZARD
Failure to follow this warning could result in personal injury
or death.
The unit cabinet must have an uninterrupted, unbroken
electrical ground. This ground may consist of an electrical
wire connected to the unit ground screw in the control
compartment, or conduit approved for electrical ground when
installed in accordance with NEC, ANSI/NFPA 70 American
National Standards Institute/National Fire Protection
Association (latest edition) (in Canada, Canadian Electrical
Code CSA C22.1) and local electrical codes.
HIGH-VOLTAGE CONNECTIONS
The unit must have a separate electrical service with a
field-supplied, waterproof disconnect switch mounted at, or within
sight from the unit. Refer to the unit rating plate, NEC and local
codes for maximum fuse/circuit breaker size and minimum circuit
amps (ampacity) for wire sizing.
The field-supplied disconnect may be mounted on the unit over
the high-voltage inlet hole (See Fig. 2 and 3).
If the unit has an electric heater, a second disconnect may be
required. Consult the Installation, Start-Up, and Service
Instructions provided with the accessory for electrical service
connections.
Operation of unit on improper line voltage constitutes abuse and
may cause unit damage that could affect warranty.
DETAIL A
SCALE 0.250
TIGHTEN STRAPPING SECURELY
WITH TENSION BUCKLE
INSTALL SAFETY STRAPS TO
RIGGING CLEVIS AT 4 RIGGING BRACKETS
mm
482.6
482.6
508.0
508.0
508.0
533.4
ROUTING POWER LEADS INTO UNIT
Use only copper wire between disconnect and unit. The
highvoltage leads should be in a conduit until they enter the duct
panel; conduit termination at the duct panel must be watertight.
Run the high-voltage leads through the power entry knockout on
the power entry side panel. (See Fig. 2 and 3 for location and size)
When the leads are inside the unit, run leads up the high-voltage
raceway to the line wiring splice box (See Fig. 13 through 17). For
singlephase units, connect leads to the black and yellow wires; for
3-phase units, connect the leads to the black, yellow, and blue
wires.
CONNECTING GROUND LEAD TO GROUND LUG
Refer to Fig. 15 and 16. Connect the ground lead to the chassis
using the ground lug in the wiring splice box.
ROUTING CONTROL POWER WIRES (24-V)
Form a drip-loop with the thermostat leads before routing them
into the unit. Route the thermostat leads through grommeted,
low-voltage hole provided in unit into unit control power splice
box. (See Fig. 2 and 3) Connect thermostat leads to unit control
power leads as shown in Fig. 15.
The unit transformer supplies 24-v power for complete system
including accessory electrical heater. An automatic-reset circuit
breaker (See Fig. 17) is provided in the 24-v circuit; see the
caution label on the transformer or Fig. 18. Transformer is factory
wired for 230-v operation. If supply voltage is 208-v, rewire
transformer primary as described in Special Procedures for 208-v
Operation section.
C99075
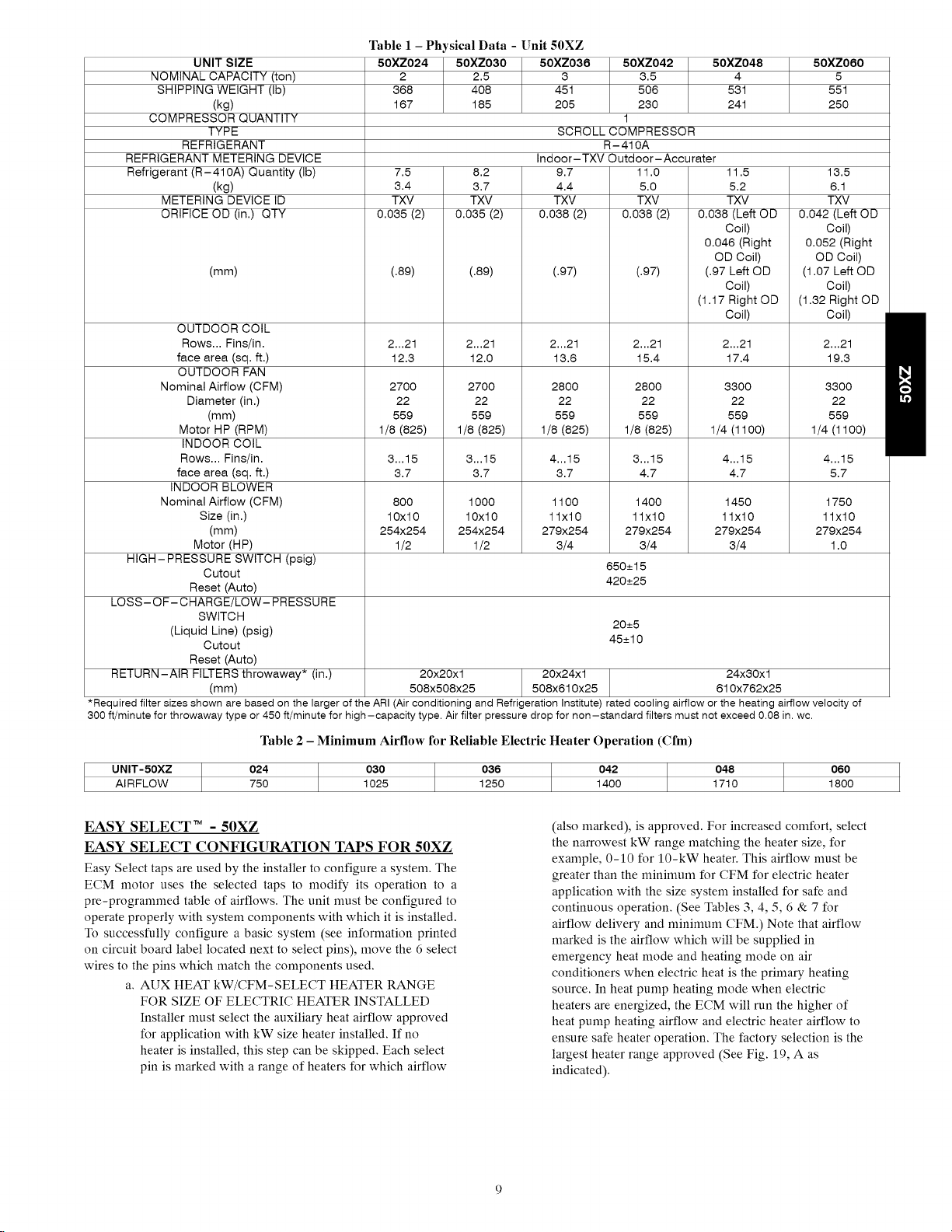
Table I - Physical Data - Unit 50XZ
UNIT SIZE
NOMINAL CAPACITY (ton)
SHIPPING WEIGHT (Ib)
(kg)
COMPRESSOR QUANTITY
TYPE
REFRIGERANT
REFRIGERANT METERING DEVICE
Refrigerant (R-410A) Quantity (Ib)
METERING DEVICE ID
(kg)
ORIFICE OD (in.) QTY
(mm)
Rows... Fins/in. 2...21 2...21 2...21 2...21 2...21 2...21
face area (sq. ft.) 12.3 12.0 13.6 15.4 17.4 19.3
OUTDOOR FAN
Nominal Airflow (CFM) 2700 2700 2800 2800 3300 3300
Diameter (in.) 22 22 22 22 22 22
OUTDOOR COIL l
(mm) 559 559 559 559 559 559
Motor HP (RPM) 1/8 (825) 1/8 (825) 1/8 (825) 1/8 (825) 1/4 (1100) 1/4 (1100)
INDOOR COIL
Rows... Fins/in. 3...15 3...15 4...15 3...15 4...15 4...15
face area (sq. ft.) 3.7 3.7 3.7 4.7 4.7 5.7
INDOOR BLOWER
Nominal Airflow (CFM) 800 1000 11 O0 1400 1450 1750
Size (in.) 10x10 10x10 1lx10 1 lx10 1lx10 1lx10
(mm) 254x254 254x254 279x254 279x254 279x254 279x254
Motor (H P) 1/2 1/2 3/4 3/4 3/4 1.0
HIGH- PRESSURE SWITCH (psig) 650_+15
LOSS- OF- CHARGE/LOW- PRESSURE
RETURN-AIR FILTERS throwaway* (in.) 20x20x1 20x24x1 24x30x1
*Required filter sizes shown are based on the larger of the ARI (Air conditioning and Refrigeration Institute) rated cooling airflow or the heating airflow velocity of
300 ft/minute for throwaway type or 450 ft/minute for high-capacity type. Air filter pressure drop for non-standard filters must not exceed 0.08 in. wc.
UNIT-5OXZ 024 030 036 042 048 060
AIRFLOW 750 1025 1250 1400 1710 1800
Cutout
Reset (Auto) 420_+25
SWITCH 20_+5
(Liquid Line) (psig) 45_+10
Cutout
Reset (Auto)
(mm) 508x508x25 508x610x25 610x762x25
Table 2 - Minimum Airflow for Reliable Electric Heater Operation (Cfm)
50XZ024 50XZ030 50XZ036 50XZ042 50XZ048 50XZ080
2 2.5 3 3.5 4 5
388 408 451 508 531 551
167 185 205 230 241 250
SCROLL COMPRESSOR
7.5
3.4
TXV
0.035 (2)
(.89)
8.2
3.7
TXV
0.035 (2)
(.89)
Indoor-TXV Outdoor-Accurater
9.7
4.4
TXV
0.038 (2)
(.97)
1
R- 410A
0.038 (2)
11.0
5.0
TXV
(.97)
11.5
5.2
TXV
0.038 (Left OD
Coil)
0.046 (Right
OD Coil)
(.97 Left OD
Coil)
(1.17 Right OD
Coil)
13.5
6.1
TXV
0.042 (Left OD
Coil)
0.052 (Right
OD Coil)
(1.07 Left OD
Coil)
(1.32 Right OD
Coil)
EASY SELECT TM - 50XZ
EASY SELECT CONFIGURATION TAPS FOR 50XZ
Easy Select taps are used by the installer to configure a system. The
ECM motor uses the selected taps to modify its operation to a
pre-programmed table of airflows. The unit must be configured to
operate properly with system components with which it is installed.
To successfully configure a basic system (see information printed
on circuit board label located next to select pins), move the 6 select
wires to the pins which match the components used.
a. AUX HEAT kW/CFM-SELECT HEATER RANGE
FOR SIZE OF ELECTRIC HEATER INSTALLED
Installer must select the auxiliary heat airflow approved
for application with kW size heater installed. If no
heater is installed, this step can be skipped. Each select
pin is marked with a range of heaters for which airflow
(also marked), is approved. For increased comfort, select
the narrowest kW range matching the heater size, for
example, 0-10 for 10-kW heater. This airflow must be
greater than the minimum for CFM for electric heater
application with the size system installed for safe and
continuous operation. (See Tables 3, 4, 5, 6 & 7 for
airflow delivery and n_ininmm CFM.) Note that airflow
marked is the airflow which will be supplied in
emergency heat mode and heating mode on air
conditioners when electric heat is the primary heating
source. In heat pump heating mode when electric
heaters are energized, the ECM will run the higher of
heat pump heating airflow and electric heater airflow to
ensure safe heater operation. The factory selection is the
largest heater range approved (See Fig. 19, A as
indicated).