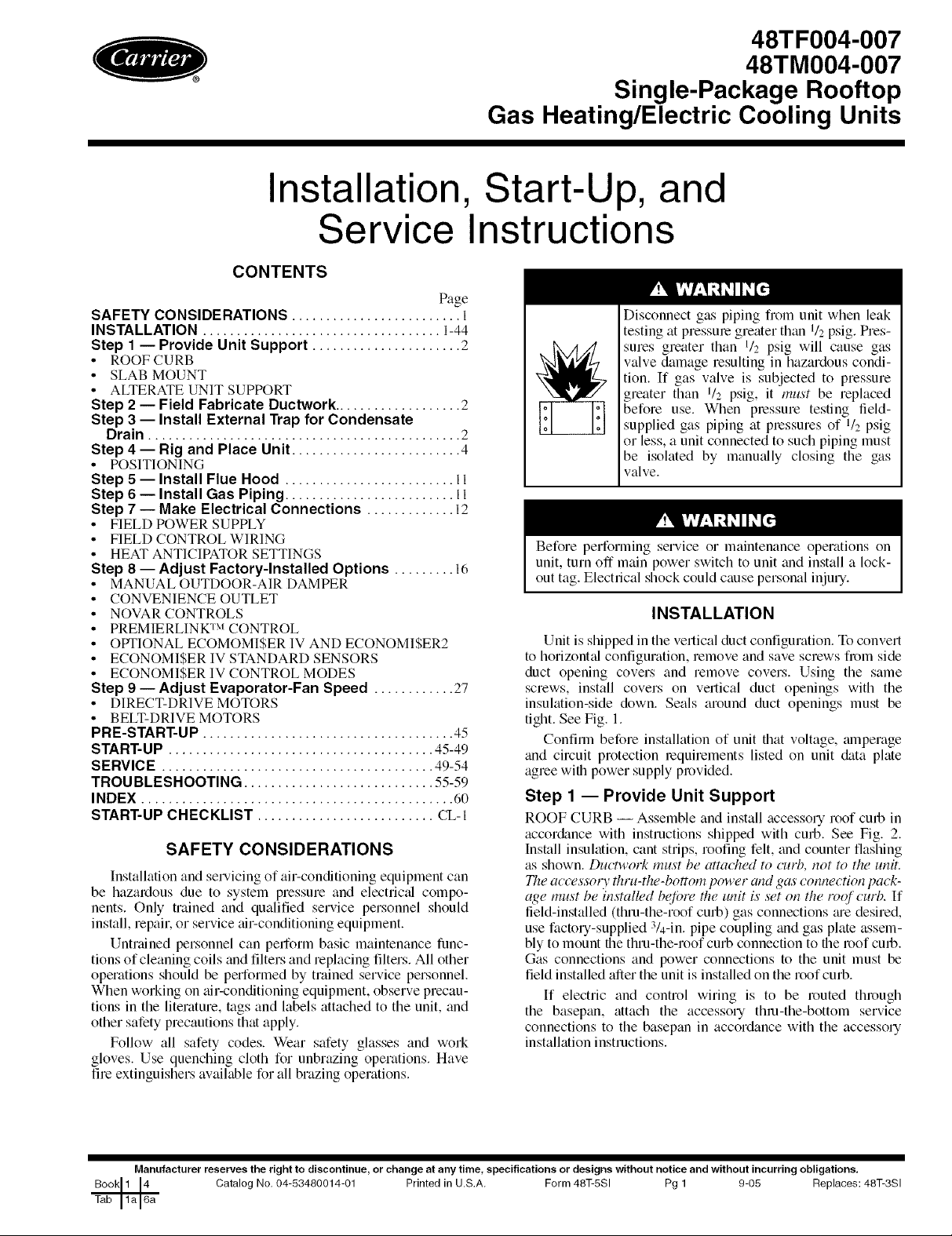
Single-Package Rooftop
Gas Heating/Electric Cooling Units
Installation, Start-Up, and
Service Instructions
CONTENTS
48TF004-007
48TM004-007
SAFETY CONSIDERATIONS ......................... 1
Page
INSTALLATION ................................... 1-44
Step 1-- Provide Unit Support ...................... 2
• ROOF CURB
• SLAB MOUNT
• ALTERATE UNIT SUPPORT
Step 2 -- Field Fabricate Ductwork ................... 2
Step 3 -- Install External Trap for Condensate
Drain .............................................. 2
Step 4 -- Rig and Place Unit ......................... 4
• POSITIONING
Step 5 -- Install Flue Hood ......................... 11
Step 6 -- Install Gas Piping ......................... 11
Step 7 -- Make Electrical Connections ............. 12
• FIELD POWER SUPPLY
• FIELD CONTROL WIRING
• HEAT ANTICIPATOR SETTINGS
Step 8- Adjust Factory-Installed Options ......... 16
• MANUAL OUTDOOR-AIR DAMPER
• CONVENIENCE OUTLET
• NOVAR CONTROLS
• PREMIERLINK TM CONTROL
• OPTIONAL ECOMOMISER IV AND ECONOMI$ER2
• ECONOMI$ER IVSTANDARD SENSORS
• ECONOMISER IV CONTROL MODES
Step 9 -- Adjust Evaporator-Fan Speed ............ 27
• DIRECT-DRIVE MOTORS
• BELT-DRIVE MOTORS
PRE-START-UP ..................................... 45
START-UP ....................................... 45-49
SERVICE ........................................ 49-54
TROUBLESHOOTING ............................ 55-59
INDEX .............................................. 60
START-UP CHECKLIST .......................... CL-I
SAFETY CONSIDERATIONS
Installation and servicing of air-conditioning equipment can
be hazardous due to system pressure and electric_d compo-
nents. Only trained and qualified service personnel should
install, repair, or service at>conditioning equipment.
Untrained personnel can perform basic maintenance func-
tions of cleaning coils and filters and replacing filters. All other
operations should be performed by trained service personnel.
When working on at>conditioning equipment, observe precau-
tions in the literature, tags and labels attached to the unit, and
other safety precautions that apply.
Follow all safety codes. Wear safety glasses and work
gloves. Use quenching cloth for unbrazing operations. Have
fire extinguishers available for all brazing operations.
Disconnect gas piping from unit when leak
testing at pressure greater than 1/2 psig. Pres-
sures greater than 1/2 psig will cause gas
valve damage resulting in hazardous condi-
tion. If gas valve is subjected to pressure
greater than 1/2 psig, it must be replaced
before use. When pressure testing field-
supplied gas piping at pressures of 1/2 psig
or less, a unit connected to such piping must
be isolated by manually closing the gas
valve.
Before performing service or maintenance operations on
unit, turn off main power switch to unit and install a lock-
out tag. Electrical shock could c_mse personal injury.
INSTALLATION
Unit is shipped in the vertical duct configuration. To convert
to horizont_d configuration, remove and save screws fi_m side
duct opening covers and remove covers. Using the same
screws, install covers on veriical duct openings with the
insulation-side down. Seals around duct openings must be
tight. See Fig. 1.
Confimt before installation of unit that voltage, mnperage
and circuit protection requirements listed on unit &tta plate
agree with power supply provided.
Step 1 -- Provide Unit Support
ROOF CURB -- Assemble and install accesso U roof curb in
accor&mce with instructions shipped with curb. See Fig. 2.
Install insulation, cant strips, roofing felt, and counter flashing
as shown. Ductwork must be attached to curb, not to the unit.
The accesso O"thru-the-boltom power and gas connection pack-
age must be installed b@re the unit is ,wt on the roo/ curb. If
field-installed (thin-the-roof curb) gas connections tue desired,
use factory-supplied 3/4-in. pipe coupling and gas plate assem-
bly to mount the thin-the-roof curb connection to the roof crag.
Gas connections and power connections to the unit must be
field installed after the unit is installed on the roof curb.
If electric and control wiring is to be routed through
the basepan, attach the accessory thru-the-bottom service
connections to the basepan in accordance with the accessory
installation instructions.
Manufacturer reserves the right to discontinue, or change at any time, specifications or designs without notice and without incurring obligations.
Catalog No. 04-53480014-01 Printed in U.S.A, Form 48T-5SI Pg 1 9-05 Replaces: 48T-3SI
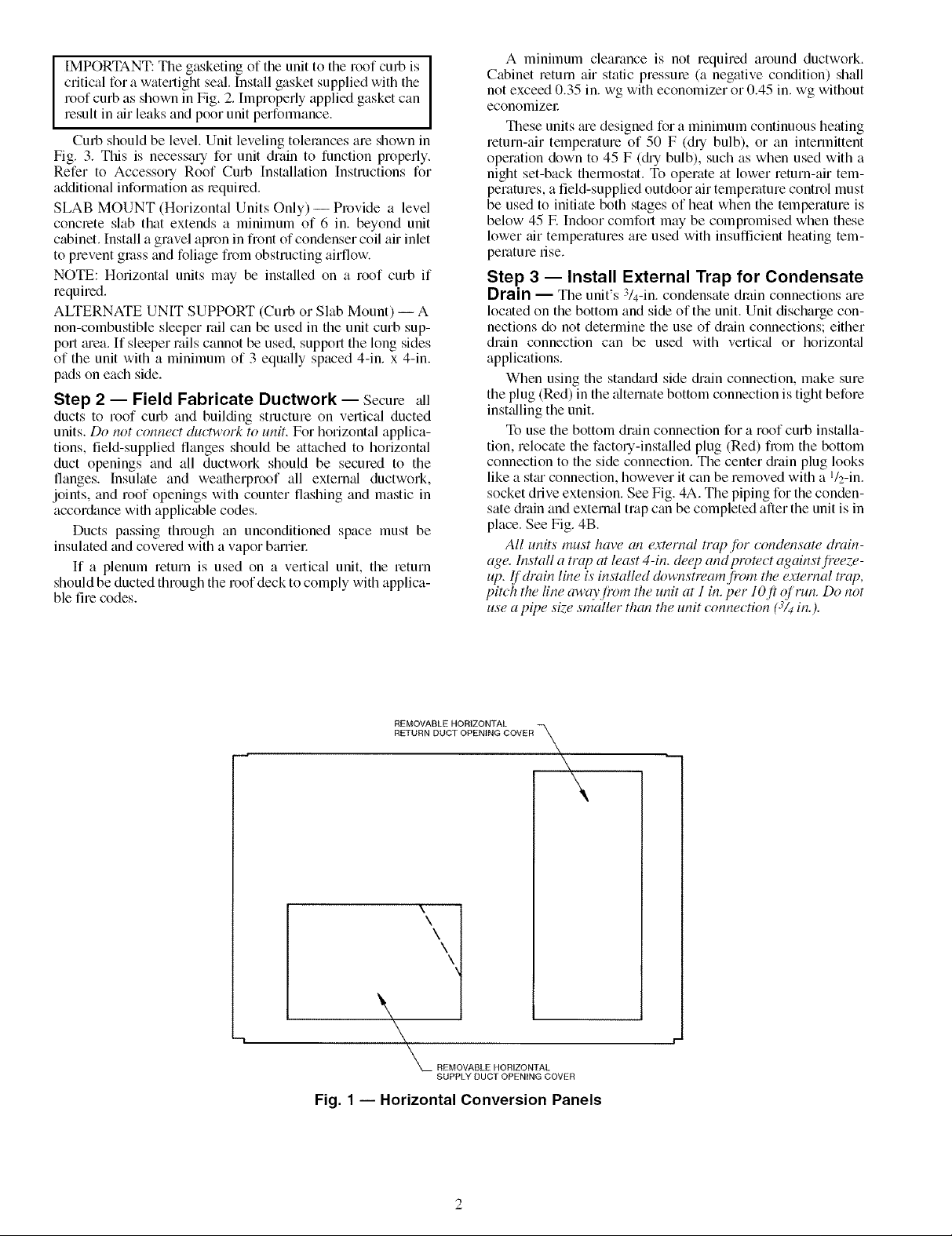
IMPORTANT: Tile gasketing of tile unit to tile roof curb is ]
critical for a watertight seal. Install gasket supplied with the
roof curb as shown in Fig. 2. hnproperly applied gasket can
result in tdr leaks and pool unit performance.
Curb should be level. Unit leveling tolerances are shown in
Fig. 3. This is necessary for unit drain to function properly.
Refer to Accessory Roof Curb Installation Instructions for
additional information as lequiled.
SLAB MOUNT (Horizontal Units Only) -- Provide a level
conclete slab that extends a minimum of 6 in. beyond unit
cabinet. Install a gravel apron in front of condenser coil air inlet
to prevent gross and foliage from obstructing airflow.
NOTE: Horizontal units may be installed on a roof curb if
required.
ALTERNATE UNIT SUPPORT (Curb or Slab Mount) -- A
non-combustible sleeper rail can be used in the unit curb sup-
port tuea. If sleeper rails cannot be used, support the long sides
of the unit with a minimum of 3 equally spaced 4-in. x 4-in.
pads on each side.
Step 2 -- Field Fabricate Ductwork -- Secure all
ducts to roof curb and building structure on vertical ducted
units. Do not connect du(_'ork to unit. For horizontal applica-
tions, field-supplied flanges should be attached to horizontal
duct openings and all ductwork should be secured to the
flanges. Insulate and weatherproof all external ductwork,
joints, and roof openings with counter flashing and mastic in
accor&mce with applicable codes.
Ducts passing through an unconditioned space must be
insulated and covered with a vapor b_uriel:
If a plenum return is used on a vertical unit, the return
should be ducted through the roof deck to comply with applica-
ble fire codes.
I
A minimum clearance is not required around ductwork.
Cabinet return air static pressme (a negative condition) shall
not exceed 0.35 in. wg with economizer or 0.45 in. wg without
economizeE
These units tue designed for a minimum continuous heating
return-air temperature of 50 F (dry bulb), or an intermittent
operation down to 45 F (@ bulb), such as when used with a
night set-back thermostat. To operate at lower return-air tem-
peratures, a field-supplied outdoor air temperature control must
be used to initiate both stages of heat when the temperature is
below 45 E Indoor comfort may be compromised when these
lower air temperatures are used with insufficient heating tem-
perature rise.
Step 3 -- Install External Trap for Condensate
Drain -- The unit's 3/4-in. condensate drain connections are
located on the bottom and side of the unit. Unit discharge con-
nections do not deterraine the use of drain connections; either
dnun connection can be used with vertic;d or horizont;d
applications.
When using the standard side &'ain connection, make sure
the plug (Red) in the ;alternate bottom connection is tight before
inst;dling the unit.
To use the bottom drain connection for a roof curb installa-
tion, relocate the factory-installed plug (Red) from the bottom
connection to the side connection. The center &'ain plug looks
like a stm"connection, however it can be removed with a l/2-in.
socket drive extension. See Fig. 4A. The piping for the conden-
sate &'ain and external trap can be completed after the unit is in
place. See Fig. 4B.
All units must have an exWrnal trap./(_r condensaW druin-
age. Instull a tru l) at least 4-in. deep and prowct against fi'eeze-
Ul).I/ drain line is installed downstmam /?om the exWrlml trap,
pitch the fine awayfl'om the unit at 1 in. per lOft q/run. Do not
use a pipe s£e smaller than the unit connection (J/4 in.).
\
\
\
\
\
\
\L__REMOVAOLENOOIZONTAL
SUPPLY DUCT OPENING COVER
Fig. 1 -- Horizontal Conversion Panels
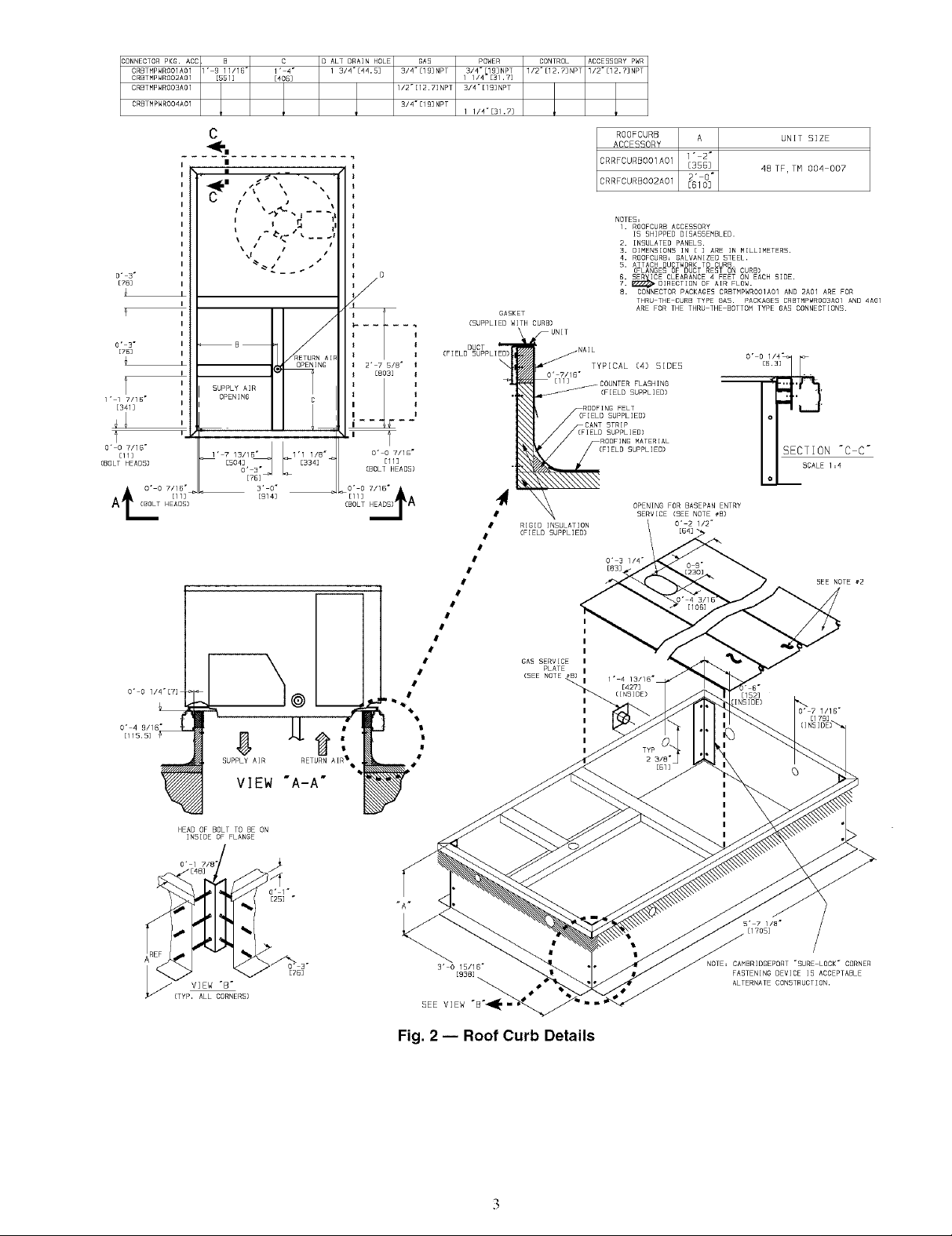
CRBTMPWROO2A01 [5513
CRBTMPWROO4A01
CRBTMPWROO3AOI 1
O" 3"
[763
,l
O" 3"
[75]
k
1' 1 7115" i
[341] I
_l ,
T _"
O" 0 7/16"
[II]
(BOLT HEADS)
O" 0 7/16"
At_ ....
I
HEADS)
c
SUPPLY AIR
OPENING
[5043
_' 7 13/15B_._
o'
[75]
[406] 1 1/4"[3117]
1/2"[12.7]NPT
3/4"[19]NPT
/
(FIELD
3" O"
[914]
POWER CONTROL
3/4"[1B]NPT 1/2"[12IT]NPT
3/4"[18]NPT
1 1/4"[31.7]
GASKET
(SUPPLIED WITH CURB)
DUCT
\
O" 7/16"
/((FIELD SUPPLIED)
ROOFCURB A UNIT SIZE
ACCESSORY
CRRFCURBOO1AO1 1" 2"
CRRFCURBOO2AO1 [S1 O]
NOTES:
II ROOFCURB ACCESSORY
IS 5HIPPED DISASSEMBLED.
2. INSULATED PANELS.
31 DIMENSIONS iN [ ] ARE IN MILLiMETERSI
I ROOFCURB: GALVANIZED £TEELI
I ATTACH DUCTWORK TO CURBI
(FLANGES OF DUCT REST ON CURB)
SER ICE CLEARANCE 4 FEET ON EACH
_] _OlRECTION OF AIR FLOW. S[DEI
81 CONNECTOR PACKAGES CRBTMPWROO1AO1 AND 2AO1 ARE FOR
TBRU THE CURB TYPE GAS, PACKAGES CRBTMPWROO3AOI AND 4AOI
ARE FOR THE THRU THE BOTTOM TYPE GAB CONNECTIONS.
TYPICAL (4) SIDES
CANT STRIP
SERVICE (SEE NOTE #8)
[358] 48 TF, TM 004 DO7
2" 0 °
o,oLsy
_oNZc c"
O" 2 1/2"
SCALE 1:4
O" 0 1/4"[7]
O0 145.95116_
SUPPLY AIR ET AI
VIEW "A-A"
HEAD OF BOLT TO BE ON
INSIDE OF FLANGE
0/
O" 3 1/4"
NOTE: CAMBRIDGEPORT "SURE LOCK" CORNER
FASTENING DEVICE IS ACCEPTABLE
Fig. 2 -- Roof Curb Details
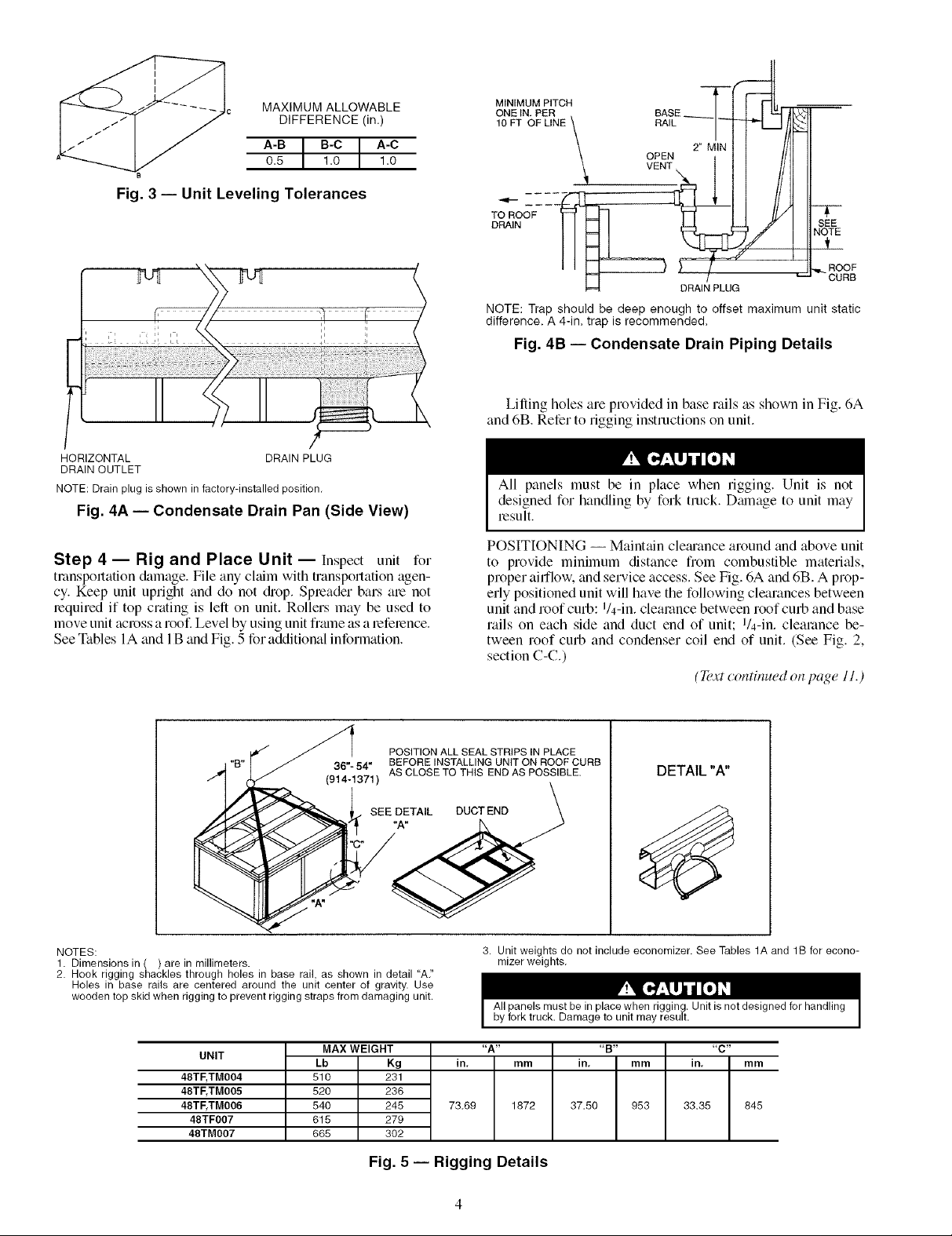
MAXIMUM ALLOWABLE
DIFFERENCE (in.)
A-B B-C
0.5 1.0
B
A-C
1.0
Fig. 3 -- Unit Leveling Tolerances
HORIZONTAL DRAIN PLUG
DRAIN OUTLET
NOTE: Drain plug is shown in factory-installed position.
Fig. 4A -- Condensate Drain Pan (Side View)
Step 4 -- Rig and Place Unit -- inspect unit for
tmnspottation &mmge. File any cltdtn with transportation agen-
cy. Keep unit uptight and do not &'op. Spteader bars ate not
required if top crating is left on unit, Rollers may be used to
move unit across a roof. Level by using unit flame as a tefetence.
See Tables IA and 1B and Fig, 5 for additional information,
MINIMUM PITCH
°°%NgL%\
TO ROOF
DRAIN
DRAIN PLUG
NOTE: Trap should be deep enough to offset maximum unit static
difference.A 4-in. trap is recommended.
Fig. 4B -- Condensate Drain Piping Details
Lifting holes are provided in base rails as shown inFig. 6A
and 6B. Refer to rigging instructions on unit.
All panels must be in place when rigging. Unit is not
designed for handling by fork truck. Dmnage to unit may
result.
POSITIONING -- Maintain clemance around and above unit
to provide minimum distance fiom combustible materials,
proper airflow, and service access. See Fig. 6A and 6B. A prop-
erly positioned unit will have the following cleatances between
unit and roof curb: I/4-in. clearance between roof curb and base
rails on each side and duct end of unit; I/4-in. clearance be-
tween roof curb and condenser coil end of unit. (See Fig. 2,
section C-C.)
(Text continued on page 11.)
--T--
SEE
NOTE
ROOF
CURB
POSITION ALL SEAL STRIPS IN PLACE
36"- 54"
(914-1371)
NOTES:
1. Dimensions in ( ) are in millimeters.
2. Hook rigging shackles through holes in base rail, as shown in detail "A."
Holes in base rails are centered around the unit center of gravity. Use
wooden top skid when rigging to prevent rigging straps from damaging unit.
UNIT
48TF, TM004
48TF, TM005
48TF, TM006
48TF007
48TM007
MAX WEIGHT
Lb Kg
510 231
520 236
540 245
615 279
665 302
BEFORE INSTALLING UNIT ON ROOF CURB
AS CLOSE TO THIS END AS POSSIBLE.
Fig. 5 -- Rigging Details
DETAIL "A"
DUCTEND
3. Unit weights do not include economizer. See Tables 1A and 1B for econo-
mizer weights.
All panels must be in place when rigging. Unit is not designed for handling
by fork truck. Damage to unit may result.
"A .... B.... C"
in, mm in. mm in, mm
73.69 1872 37.50 953 33.35 845
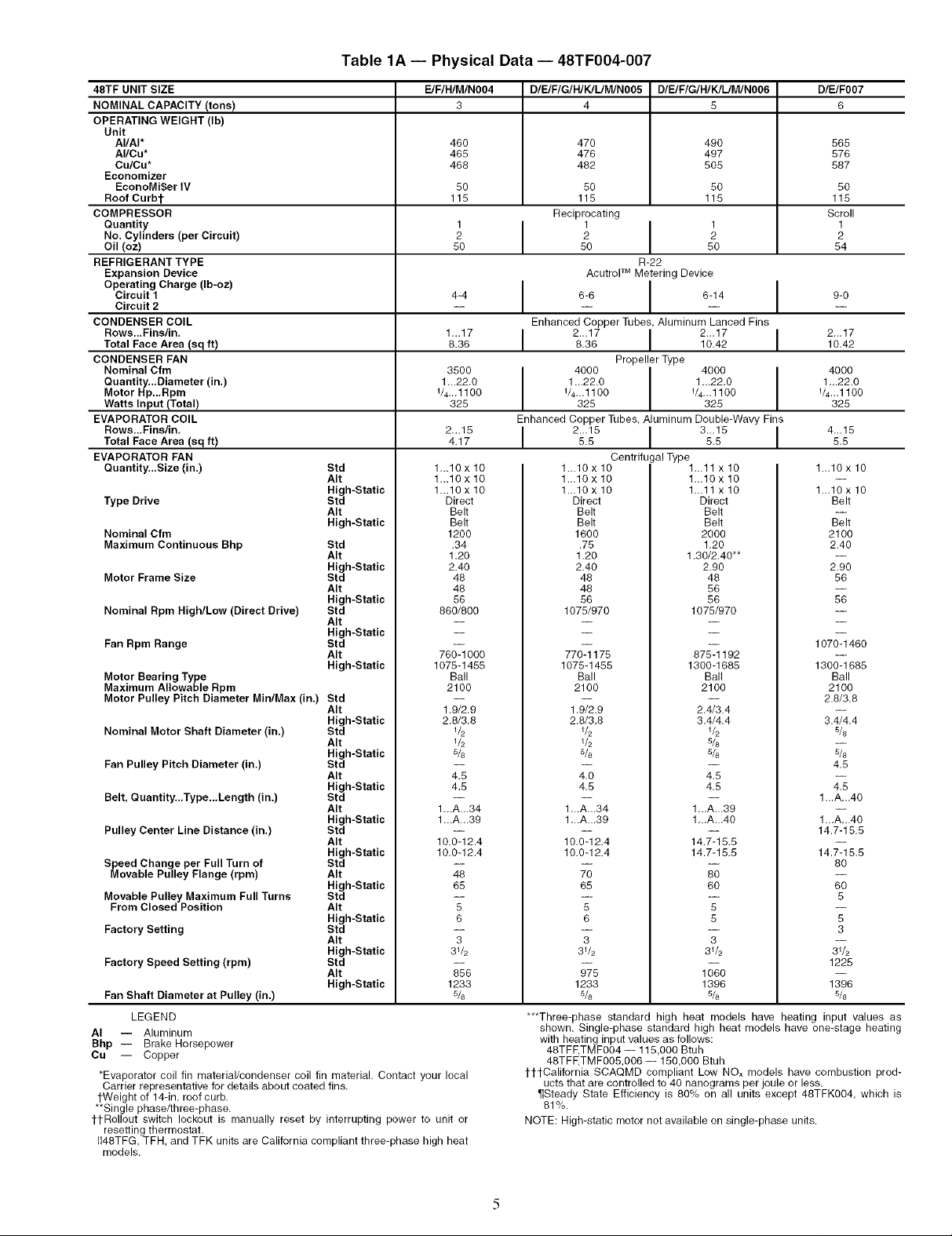
Table1A- Physical Data- 48TF004-007
48TF UNIT SIZE E/F/H/M/N004 D/E/FIG/HIK/L/M/NO05 D/E/F/G/H/K]LIM/NO06 D/E/F007
NOMINAL CAPACITY (tone) 3 4 5 6
OPERATING WEIGHT (Ib)
Unit
AI/AI* 460 470 490 565
AI/Cu* 465 476 497 576
Cu/Cu* 466 482 505 587
Economizer
EconoMi$er IV 50 50 50 50
Roof Curbt 115 115 115 115
COMPRESSOR Reciprocating Scroll
Quantity 1 1 I 1 1
No. Cylinders (per Circuit) 2 2 I 2 2
Oil (oz) 50 50 50 54
REFRIGERANT TYPE R-22
Expansion Device AcutroF MMetering Device
Circuit I 4-4 6-6 6-14 9-0
Operating Charge (Ib-oz) I I
Circuit 2 ....
CONDENSER COIL Enhanced Copper Tubes, Aluminum Lanced Fins
Rows...Finslin, 1,..17 I 2_.17 I 2._17 I 2_,17
Total Face Area (sq ft) 8.36 8.36 10,42 10,42
CONDENSER FAN Propeller Type
Nominal Cfm 3500 4000 I 4000 I 4000
Motor Hp..,Rpm 1/4.,,1100 1/4,..1100 V4-. 1100 V4.-1100
Quantity...Diameter (in.) 1,..22,0 1.,.22.0 I 1 ,..22,0 I 1,,.22.0
Watts Input (Total) 325 325 325 325
EVAPORATOR COIL Enhanced Copper Tubes, Aluminum Double-Wavy Fins
Rows..,Fins/in, 2_.15 I 2._15 I 3_,15 I 4_,15
Total Face Area (sq ft) 4.17 5.5 5,5 5,5
EVAPORATOR FAN Centrifugal Type
Quantity..,Size (in.)
Type Drive
Nominal Cfm
Maximum Continuous Bhp
Motor Frame Size
Nominal Rpm High/Low (Direct Drive)
Fan Rpm Range
Motor Bearing Type
Maximum Allowable Rpm
Motor Pulley Pitch Diameter MiniMax (in.) Std
Nominal Motor Shaft Diameter (in.) Std
Fan Pulley Pitch Diameter (in.) Std
Belt, Quantity..,Type..,Length (in.) Std
Pulley Center Line Distance (in.) Std
Speed Change per Full Turn of Std
Movable Pulley Flange (rpm) AIt
Movable Pulley Maximum Full Turns Std
From Closed Position Air
Factory Setting Std
Factory Speed Setting (rpm) Std
Fan Shaft Diameter at Pulley (in.)
LEGEND
AI -- Aluminum
Bhp -- Brake Horsepower
Cu -- Copper
*Evaporator coil fin material/condenser coil fin material, Contact your local
Carrier representative for details about coated fins,
l-Weight of 14-in. roof curb,
**Single phase/three-phase.
ttRollout switch lockout is manually reset by interrupting power to unit or
resetting thermostat.
1148TFG, TFH, and TFK units are California compliant three-phase high heat
models.
Std
AIt
High-Static
Std
AIt
High-Static
Std
AIt
High-Static
Std
AIt
High-Static
Std
AIt
High-Static
Std
AIt
High-Static
Air
High-Static
Air
High-Static
Air
High-Static
Air
High-Static
Air
High-Static
High-Static
High-Static
Air
High-Static
Air
High-Static
1_.10 x 10
1_.10 x 10
1_.10x 10
Direct
Belt
Belt
1200
.34
1.20
2.40
48
48
56
860/800
760-1000
1075-1455
Ball
2100
1,9/2,9
2,8/3,8
1/2
1/2
%
4.5
4.5
1...A.,.34
1...A_.39
10,0-12.4
10,0-12.4
48
65
5
6
3
31/2
856
1233
%
1.,.10 x 10
1.,.10 x 10
1.,.10 x 10
Direct
Belt
Belt
1600
.75
1,20
2,40
46
46
56
1075/970
770-1175
1075-1455
Ball
2100
1,9/2.9
2,8/3,6
s/8
4.0
4.5
1,..A..,34
1,..A..,39
10,0-12.4
10,0-12.4
7O
65
5
6
3
31/2
975
1233
s&
***Three-phase standard high heat models have heating input values as
shown. Single-phase standard high heat models have one-stage heating
with heating input values as follows:
48TFF, TMF004- 115,000 Btuh
48TFF, TMF005,006- 150,000 Btuh
tl-l-California SCAQMD compliant Low NOx models have combustion prod-
ucts that are controlled to 40 nanograms per joule or less.
¶Steady State Efficiency is 80% on all units except 48TFK004, which is
81%.
NOTE: High-static motor not available on single-phase units,
1,..11x 10
1,..10 x 10
1-.11x 10
Direct
Belt
Belt
2000
1,20
1.30/2.40"*
2,90
48
56
56
1075/970
875-1192
1300-1685
Ball
2100
2,4/3.4
3.4/4.4
V2
5/8
5/8
4,5
4,5
1,.,A,.,39
1,.,A,.,40
14,7-15,5
14.7-15,5
80
60
5
5
3
3V2
1060
1396
5/8
1._10x 10
1._10 x 10
Belt
Belt
2100
2.40
2.90
56
56
1070-1460
1300-1685
Ball
2100
2.8/3.8
3.4/4.4
5/s
5/8
4.5
4.5
1...A_.40
1...A_.40
14.7-15.5
14.7-15.5
8O
6O
5
5
3
31/2
1225
1396
5/8
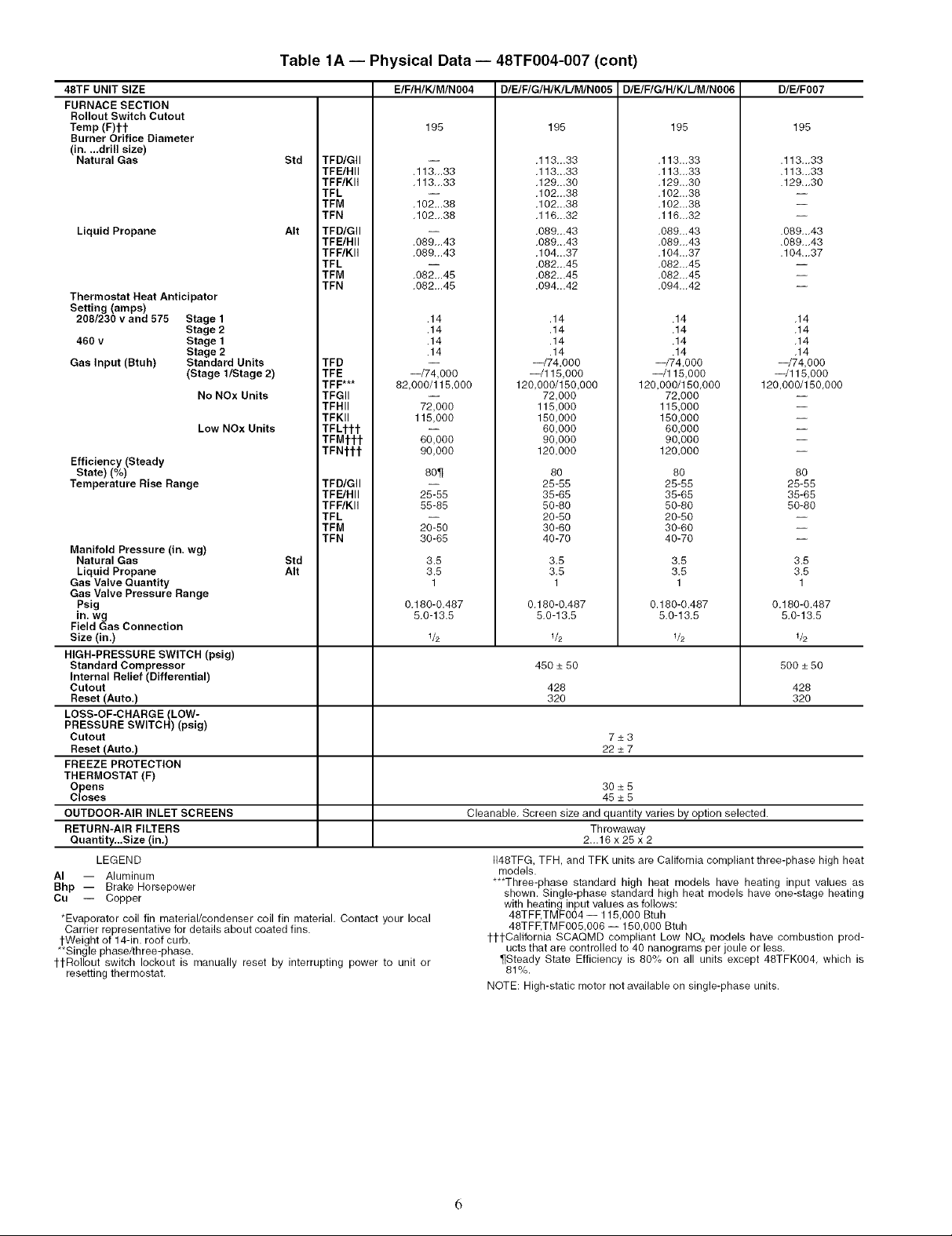
Table 1A -- Physical Data- 48TF004-007 (cent)
48TF UNIT SIZE
FURNACE SECTION
Rollout Switch Cutout
Temp (F)tt
Burner Orifice Diameter
(in...,drill size)
Natural Gas
Liquid Propane
Thermostat Heat Anticipator
Setting (amps)
208/230 v and 575 Stage 1
460 v Stage 1
Gas Input (Btuh)
Stage 2
Stage 2
Standard Units
(Stage l/Stage 2)
No NOx Units
Low NOx Units
Efficiency (Steady
State) (%)
Temperature Rise Range
Manifold Pressure (in. wg)
Natural Gas Std
Liquid Propane AIt
Gas Valve Quantity
Gas Valve Pressure Range
Psig
in. wg
Field Gas Connection
Std TFD/GII
TFE/HII .113...33
TFF/KII ,113_.33
TFL
TFM ,102.38
TFN ,102.,.38
AIt TFD/GII
TFE/HII .089-.43
TFF/KII ,089,,.43
TFL
TFM ,082-.45
TFN ,082.,.45
TFD
TFE --/74,000
TFF*** 82,000/115,000
TFGII
TFHII 72,000
TFKII 115,000
TFLttt
TFMttt 80,000
TFNttt 90,000
TFD/GII
TFE/HII 25-55
TFF/KII 55-85
TFL
TFM 20-50
TFN 30-65
Size (in.)
HIGH-PRESSURE SWITCH (psig)
Standard Compressor
Internal Relief (Differential)
Cutout
Reset (Auto.)
LOSS-OF-CHARGE (LOW-
PRESSURE SWITCH) (psig)
Cutout
Reset (Auto.)
FREEZE PROTECTION
THERMOSTAT (F)
Opens
Closes
OUTDOOR-AIR INLET SCREENS
RETURN-AIR FILTERS
Quantity..,Size (in,)
LEGEND
AI -- Aluminum
Bhp -- Brake Horsepower
Cu -- Copper
*Evaporator coil fin material/condenser coil fin material. Contact your local
Carrier representative for details about coated fins.
tWeight of 14-in. roof curb.
**Single phase/three-phase.
l-tRollout switch lockout is manually reset by interrupting power to unit or
resetting thermostat.
E/F/H/K/M/N004
0.180-0.487
5.0-13.5
D/EIF/GIHIK]LIMINO05 D/E/F/GIH/K]L/M/NO06 D/E/F007
195
.14
.14
.14
.14
80¶
3.5
3.5
1/2
1
195
,113-.33
,113,..33
.129,..30
.102-.38
,102...38
,116,..32
,089.,.43
,089,..43
,104-.37
,082-.45
,082,..45
,094,..42
.14
.14
.14
.14
--/74,000
--/115,000
120,000/150,000
72,000
115,000
150,000
60,000
90,000
120,000
8O
25-85
35-65
50-80
20-80
30-60
40-70
3,5
3,5
1
0.180-0.487
5.0-13.5
1/2
.113...33
.113...33
.129...30
.102...38
.102...38
,116,.,32
.089,..43
.089.-43
.104...37
.082...45
.082...48
.094...42
--/74,000
--/115,000
120,000/150,000
72,000
115,000
150,000
60,000
90,000
120,000
28-55
35-65
50-80
20-50
30-60
40-70
0.180-0.487
5.0-13.5
450 -+50
428
320
7-+3
22-+7
3O-+5
45-+5
Cleanable. Screen size and quantity varies by option selected.
Throwaway
2...16 x 28 x 2
1148TFG, TFH, and TFK units are California compliant three-phase high heat
models.
***Three-phase standard high heat models have heating input values as
shown. Single-phase standard high heat models have one-stage heating
with heating input values as follows:
48TFF, TMF004 -- 115,000 Btuh
48TFF, TMF005,006 -- 150,000 Btuh
tttCalifornia SCAQMD compliant Low NO× models have combustion prod-
ucts that are controlled to 40 nanograms per joule or less.
¶Steady State Efficiency is 80% on all units except 48TFK004, which is
81%.
NOTE: High-static motor not available on single-phase units.
195
.14
.14
.14
.14
80
3.5
3.5
1/2
195
.113,.,33
.113..,33
.129.-30
.089.-43
.089..,43
.104..,37
,14
,14
,14
,14
--/74,000
--/115,000
120,000/150,000
8O
25-55
35-68
50-80
3.5
1
3.5
1
0.180-0.487
5.0-13.5
V2
500 -+50
428
320
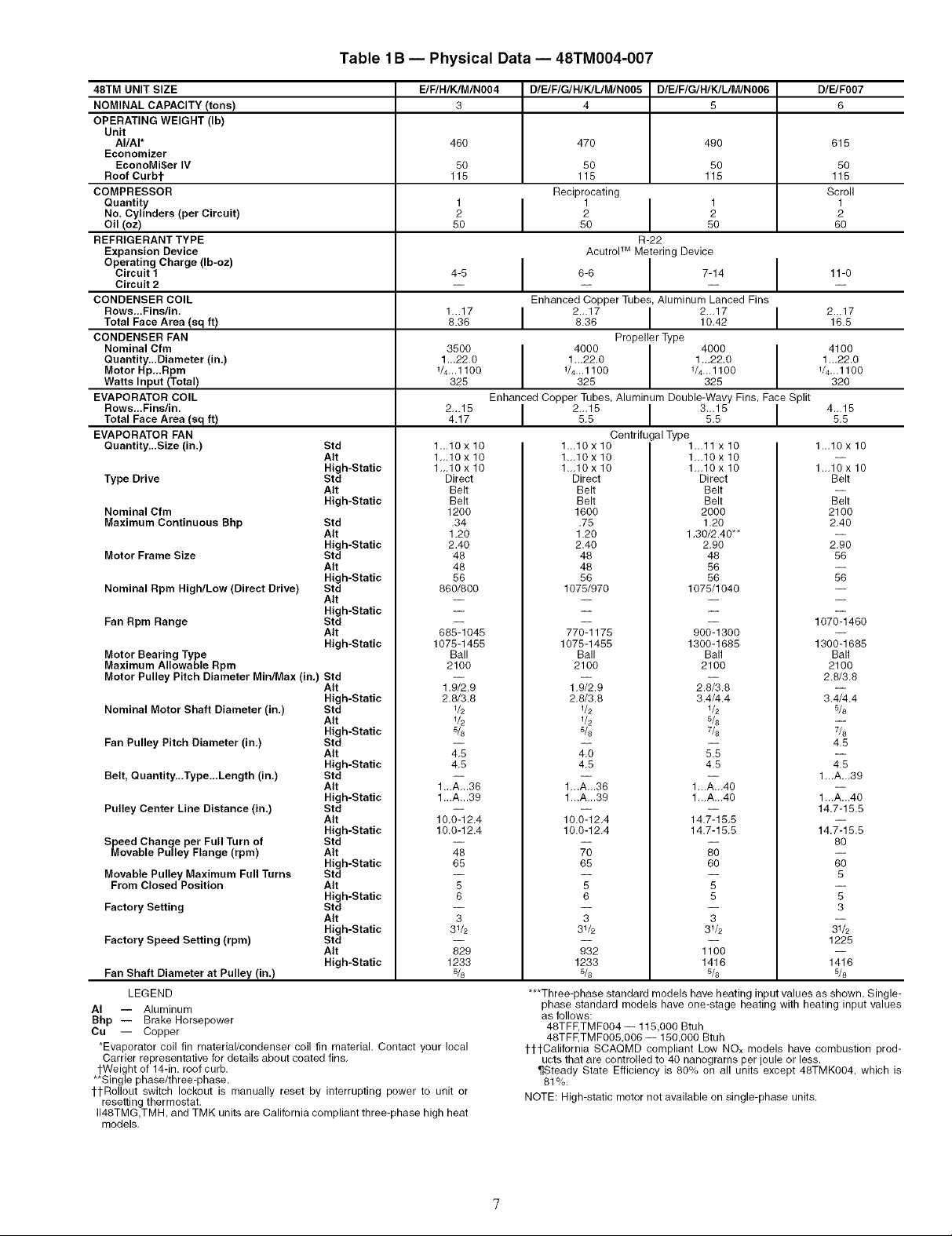
Table 1B -- Physical Data -- 48TM004-007
48TM UNIT SIZE E/F/H/K]M/N004 D/E/F/G/H/K]L/M/N005 D/E/F/G/H/K]L/M/NO06 D/F-/F007
NOMINAL CAPACITY (tons) 3 4 5 6
OPERATING WEIGHT (Ib)
Unit
AI/AI* 460 470 490 615
Economizer
EconoMi$er IV 50 50 50 50
Roof Curbt 115 115 115 115
COMPRESSOR Reciprocating Scroll
Quantity 1 I 1 1 1
No. Cylinders (per Circuit) 2 I 2 2 2
Oil (oz) 50 50 80 60
REFRIGERANT TYPE R-22
Expansion Device Acutrol TM Metering Device
Operating Charge (Ib-oz) I
Circuit 1 4-8 I 6-6 7-14 11-0Circuit 2 ....
CONDENSER COIL Enhanced Copper Tubes, Aluminum Lanced Fins
Rows,.,Fins/in. 1,..17 I 2_.17 I 2.,,17 I 2...17
Total Face Area (sq ft) 8.36 8.36 10,42 16.5
CONDENSER FAN Propeller Type
Nominal Cfm 3500 4000 4000 4100
Quantity...Diameter (in.) 1._22.0 1,_22.0 1_,22.0 1_.22.0
Motor Hp,,.Rpm V4-. 1100 1/4._1100 1/4._1100 V4-. 1100
Watts Input (Total) 325 325 325 320
EVAPORATOR COIL Enhanced Copper Tubes, Aluminum Double-Wavy Fins, Face Split
Rows.,.Finslin. 2_.15 I 2._15 I 3._15 I 4_.15
Total Face Area (eq ft) 4.17 5,5 5.5 5.5
EVAPORATOR FAN Centrifugal Type
Quantity...Size (in.)
Type Drive
Nominal Cfm
Maximum Continuous Bhp
Motor Frame Size
Nominal Rpm High/Low (Direct Drive)
Fan Rpm Range
Motor Bearing Type
Maximum Allowable Rpm
Motor Pulley Pitch Diameter Min/Max (in.) Std
Nominal Motor Shaft Diameter (in,)
Fan Pulley Pitch Diameter (in.)
Belt, Quantity..,Type..,Length (in,)
Pulley Center Line Distance (in.)
Speed Change per Full Turn of
Movable Pulley Flange (rpm)
Movable Pulley Maximum Full Turns
From Closed Position
Factory Setting
Factory Speed Setting (rpm)
Fan Shaft Diameter at Pulley (in.)
LEGEND
AI -- Aluminum
Bhp -- Brake Horsepower
Cu -- Copper
*Evaporator coil fin material/condenser coil fin material, Contact your local
Carrier representative for details about coated fins,
tWeight of 14-in. roof curb.
**Single phase/three-phase.
ttRollout switch lockout is manually reset by interrupting power to unit or
resetting thermostat,
IN8TMG,TMH, and TMK units are California compliant three-phase high heat
models,
Std
AIt
High-Static
Std
AIt
High-Static
Std
AIt
High-Static
Std
AIt
High=Static
Std
AIt
High-Static
Std
AIt
High-Static
AIt
High-Static
Std
AIt
High-Static
Std
AIt
High-Static
Std
AIt
High-Static
Std
AIt
High-Static
Std
AIt
High-Static
Std
AIt
High-Static
Std
AIt
High-Static
Std
AIt
High-Static
1.,.10 x 10
1,,.10 x 10
1_.10x 10
Direct
Belt
Belt
1200
.34
1.20
2.40
48
48
56
860/800
685-1045
1075-1455
Ball
2100
1,9/2.9
2,8/3.8
V2
V2
5/8
4,5
4,5
1...A,..36
1...A,..39
10,0-12.4
10,0-12.4
48
65
5
6
3
31/2
829
1233
s/8
1._10x 10
1._10x 10
1._10x 10
Direct
Belt
Belt
1600
,75
1.20
2.40
48
48
56
1075/970
770-1175
1075-1455
Ball
2100
1,9/2.9
2,8/3.8
1/2
1/2
5/s
4,0
4,5
1...A-.36
1...A-.39
10.0-12,4
10.0-12,4
7O
65
5
6
3
31/2
932
1233
s/8
***Three-phase standard models have heating input values as shown. Single-
phase standard models have one-stage heating with heating input values
as follows:
48TFF, TMF004- 115,000 Btuh
48TFF, TMF005,006- 150,000 Btuh
ttl-California SCAQMD compliant Low NOx models have combustion prod-
ucts that are controlled to 40 nanograms per joule or less.
']]Steady State Efficiency is 80% on all units except 48TMK004, which is
81%.
NOTE: High-static motor not available on single-phase units,
1_.11x 10
1,..10 x 10
1_.10x 10
Direct
Belt
Belt
2000
1,20
1.30/2.40"*
2,90
48
56
56
1075/1040
900-1300
1300-1685
Ball
2100
2.8/3.8
3.4/4,4
1/2
s/8
7/s
5.5
4.5
1...A.-40
1...A.-40
14.7-15,5
14.7-15,5
80
60
5
5
3
31/2
1100
1416
s/s
1._10x 10
1._10x 10
Belt
Belt
2100
2,40
2,90
56
56
1070-1460
1300-1685
Ball
2100
2.8/3,8
3.4/4,4
s/8
7/8
4.5
4.5
1,.,A._39
1,.,A..,40
14,7-15.5
14,7-15.5
8O
6O
5
5
3
3d2
1225
1416
s&
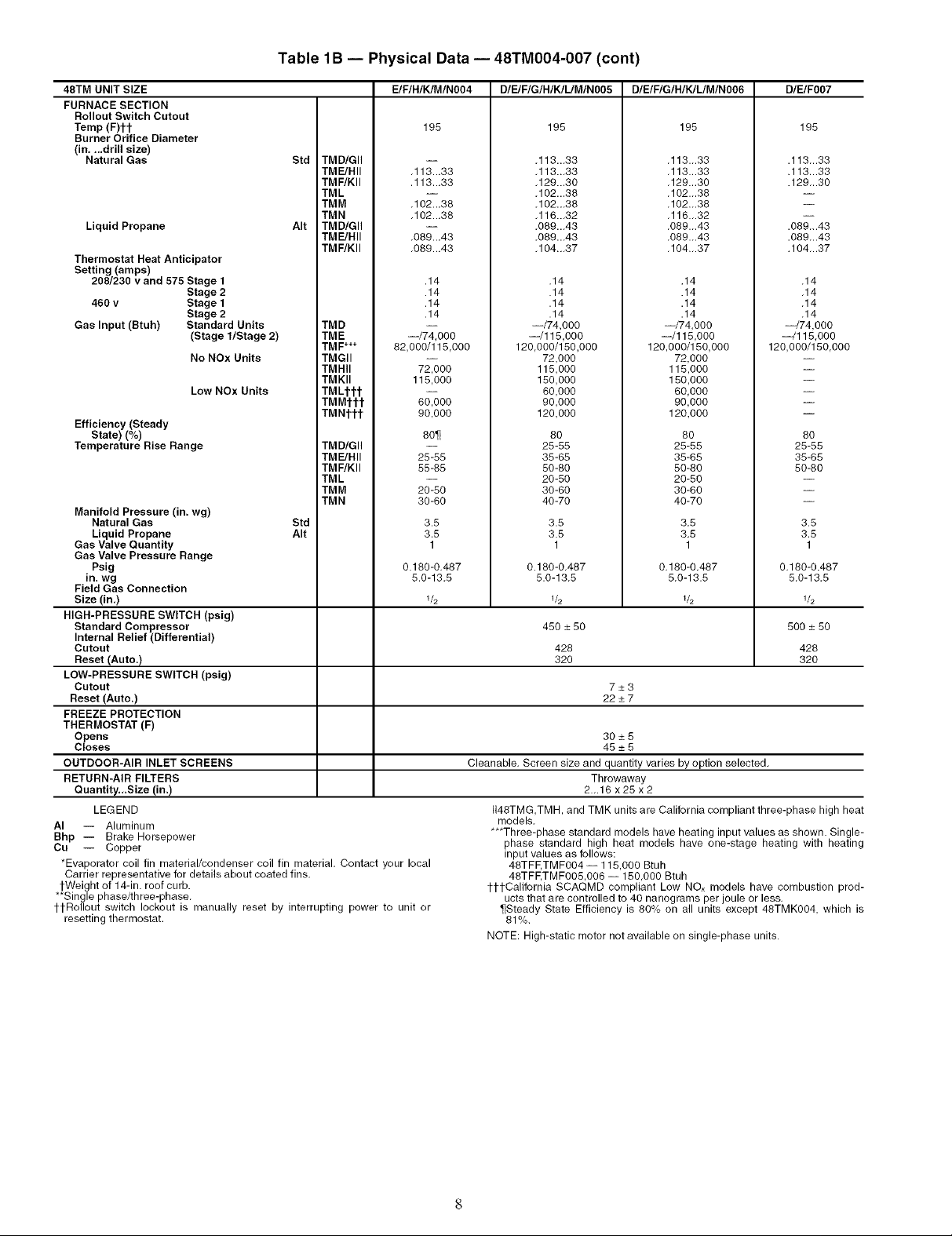
Table 1B -- Physical Data -- 48TM004-007 (cent)
48TM UNIT SIZE
FURNACE SECTION
Rollout Switch Cutout
Temp (F)tt
Burner Orifice Diameter
(in, ...drill size)
Natural Gas
Liquid Propane
Thermostat Heat Anticipator
Setting (amps)
208/230 v and 575 Stage 1
460 v Stage 1
Gas Input (Btuh) Standard Units
Stage 2
Stage 2
(Stage l/Stage 2)
No NOx Units
Low NOx Units
Efficiency (Steady
State) (%)
Temperature Rise Range
Manifold Pressure (in. wg)
Natural Gas Std
Liquid Propane AIt
Gas Valve Quantity
Gas Valve Pressure Range
Psig
in. wg
Field Gas Connection
Std TMD/GII
TME/HII .113...33
TM F/KII .113...33
TML
TMM .102.-38
TMN .102...38
AIt TMD/GII
TME/HII .089...43
TMF/KII .089.-43
TMD
TME --/74,000
TMF*** 82,000/115,000
TMGII
TMHII 72,000
TMKII 115,000
TMLttt
TMMttt 60,000
TMNttt 90.000
TMD/GII
TME/HII 25-55
TMF/KII 55-85
TML
TMM 20-50
TMN 30-60
EIWHIK/M/NO04
0.180-0.487
5.0-13.5
Size (in,)
HIGH-PRESSURE SWITCH (psig)
Standard Compressor
Internal Relief (Differential)
Cutout
Reset (Auto.)
LOW-PRESSURE SWITCH (psig)
Cutout
Reset (Auto.)
FREEZE PROTECTION
THERMOSTAT (F)
Opens
Closes
OUTDOOR-AIR INLET SCREENS
RETURN-AIR FILTERS
Quantity.,.Size (in.)
LEGEND
AI -- Aluminum
Bhp -- Brake Horsepower
Cu -- Copper
*Evaporator coil fin material/condenser coil fin material. Contact your local
Carrier representative for details about coated fins.
tWeight of 14-in. roof curb.
**Single phase/three-phase.
ttRollout switch lockout is manually reset by interrupting power to unit or
resetting thermostat.
D/E/FIGIHIK/L/M/NO05 D/EIFIG/H/K]LIM/NO06
195
.14
.14
.14
.14
80¶
3.5
3.5
1
195
.113...33
.113.-33
.129...30
.102...38
.102.-38
.116...32
.089...43
.089...43
.104.-37
.14
.14
.14
.14
--_4,000
--/115,000
120,000/150,000
72,000
115,000
150,000
60,000
90,000
120,000
80
25-55
35-65
50-80
20-50
30-60
40-70
3.5
3.5
1
0.180-0.487
5.0-13.5
120,000/150,000
0.180-0.487
450 _+50
428
320
7_+3
22_+7
30_+5
45_+5
Cleanable. Screen size and quantity varies by option selected.
Throwaway
2...16 x 25 x 2
1148TMG,TMH, and TMK units are California compliant three-phase high heat
models.
***Three-phase standard models have heating input values as shown. Single-
phase standard high heat models have one-stage heating with heating
input values as follows:
48TFF, TMFO04 -- 115,000 Btuh
48TFF, TMFO05,006 -- 150,000 Btuh
tttCalifornia SCAQMD compliant Low NO× models have combustion prod-
ucts that are controlled to 40 nanograms per joule or less.
¶Steady State Efficiency is 80% on all units except 48TMKO04, which is
81%.
NOTE: High-static motor not available on single-phase units.
195
.113...33
.113...33
.129.-30
.102.-38
.102-.38
.116...32
.089...43
.089...43
.104-.37
.14
.14
.14
.14
--/74,000
--/115,000
72,000
115,000
150,000
60,000
90,000
120,000
8O
25-55
35-85
50-80
20-50
30-60
40-70
3.5
3.5
1
5.0-13.5
V2
D/E/F007
195
.113-.33
.113...33
.129-.30
.089...43
.089...43
.104...37
.14
.14
.14
.14
--/74,000
--/115,000
120,000/150,000
8O
28-55
35-65
50-80
3.5
3.5
1
0.180-0.487
5.0-13.5
500 _+50
428
320
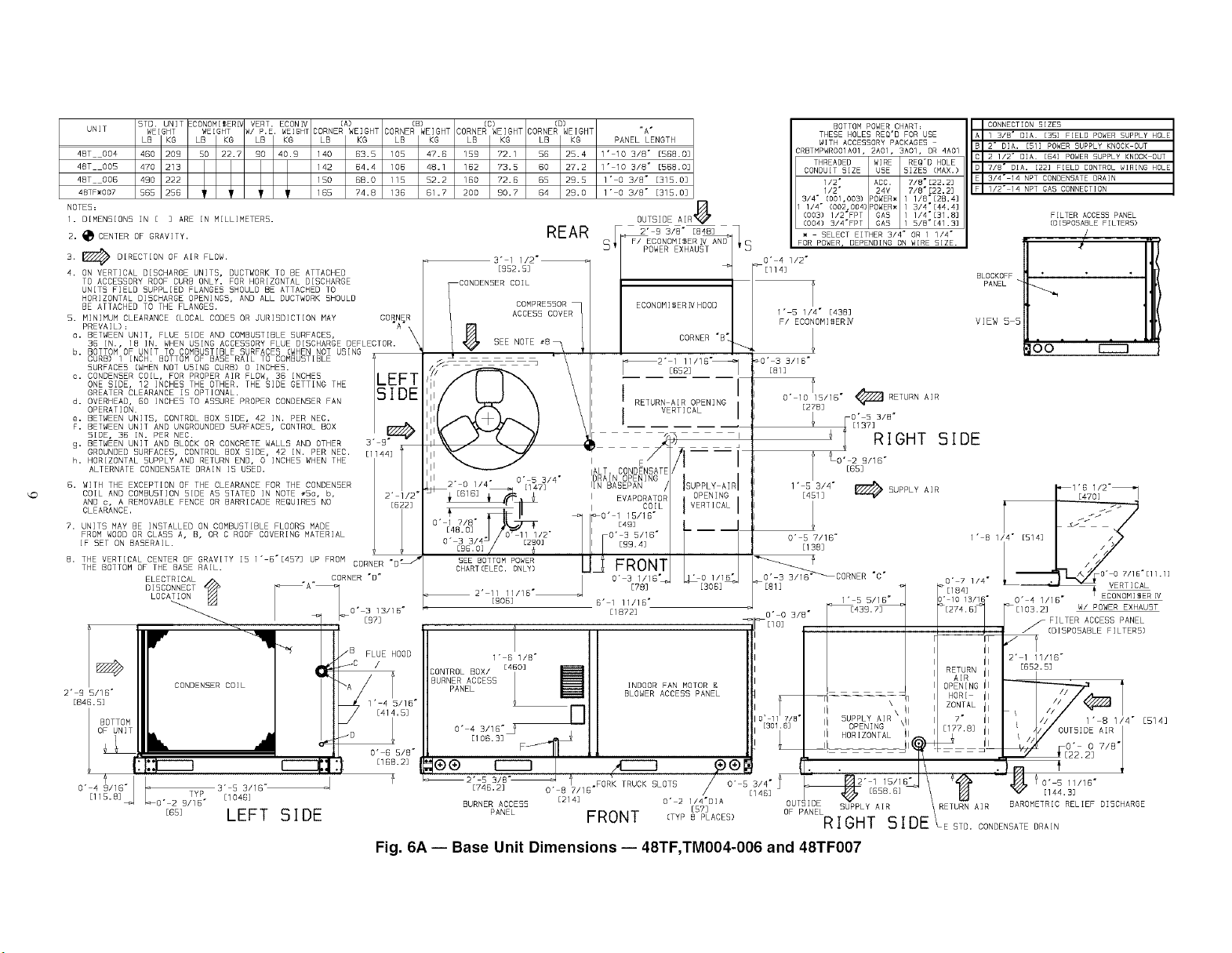
UNIT WEIGHT WEIGHT W/ P.E. WEIGH1 CORNER WEIGHT CORNER WEIGHT CORNER WEIGHT CORNER WEIGHT
48T 004 460 209 BO 22.7 BO 40.9 140 63.5 105 47. B 15B 72.1 56 25.4
48T 005 470 213 142 84.4 106 48.1 162 73.5 60 27.2
48T BOB 490 222 lSO 58.0 ll5 52.2 1CO 72.5 55 29.5
4BTF_O07 565 258 185 74.8 138 81 . 7 200 90.7 84 29.0
NOTES=
1. DIMENSIONS iN [ ] ARE IN MILLIMETERS.
2. _CENTER OF GRAVITY.
3. _ D[RECT[QN OF AIR FLOW.
4. ON VERTICAL DISCHARGE UNITS, DUCTWORK TO BE ATTACHED
TO ACCESSORY ROOF CURB ONLY. FOR HORIZONTAL DISCHARGE
UNITS FIELD SUPPLIED FLANGES 5WQULD BE ATTACHED TO
HORIZONTAL DISCHARGE OPENINGS, AND ALL DUCTWORK SHOULD
BE ATTACHED TO THE FLANGES.
5. MINIMUM CLEARANCE (LOCAL CODES OR JURISDICTION MAY CORNER
PREVAIL)= "A"
o. BETWEEN UNIT, FLUE SIDE AND COMBUSTIBLE SURFACES, \
38 IN., 18 iN. WHEN USING ACCESSORY FLUE DISCHARGE DEFLECTOR.
b. BOTTOM OF UNIT TO COMBUSTIBLE SURFACES (WHEN NOT USING
CURB) ] INCH. BOTTOM OF BASE RAIL TO COMBUSTIBLE
SURFACES (WHEN NOT USING CURB) 0 INCHES.
c. CONDENSER COIL, FOR PROPER AiR FLOW, 35 INCHES
ONE SIDE, 12 INCHES THE OTHER, THE SIDE GETTING THE
GREATER CLEARANCE [5 OPTIONAL. ISIDE
d. OVERHEAD, BO INCHES TO ASSURE PROPER CONDENSER FAN
OPERATION.
e. BETWEEN UNITS, CONTROL BOX SIDE, 42 iN. PER NEC.
F. BETWEEN UNiT AND UNGROUNDED SURFACES, CONTROL BOX
BIDE, BB IN. PER NEC.
3" BETWEEN UNIT AND BLOCK OR CONCRETE WALLS AND OTHER
GROUNDED SURFACES, CONTROL BOX SIDE, 42 IN. PER NEC.
h. HORIZONTAL SUPPLY AND RETURN END, 0 INCHES WHEN THE
ALTERNATE CONDENSATE DRAIN IS USED.
5. WITH THE EXCEPTION OF THE CLEARANCE FOR THE CONDENSER
<.o
COIL AND COMBU5TION 5IDE A5 5TATEO IN NOTE _5a, b,
AND c, A REMOVABLE FENCE OR BARRICADE REQUIRES NO
CLEARANCE.
7. UNITS MAY BE INSTALLED ON COMBUSTIBLE FLOORS MADE
FROM WOOD OR CLASS A, B, OR C ROOF COVERING MATERIAL
IF SET ON BASERAIL.
THE VERTICAL CENTER OF GRAVITY [5 1" B'[457] UP FROM CORNER "O "/_-
THE BOTTOM QF THE BASE RAIL.
2' B 5/18"
EB4B. 5]
O" 4 8/16 1 0_2"2 3' S 3/18"[115.8] TYP [1046]
5TD. UNit ECONOMHGERI_ VERT. ECONN (A) (B) (C) (D)
LB KG LB KG LB KG LB KG LB KG LB KG LB KG
ELECTRICAL CORNER "D"
DISCONNECT _LOCATION
9/15"
[G5] LEFT SIDE
TLEFT
I
3" B"
FLUE HOOD
/
1' 4 5116"
[414.5]
O" 6 5/8"
[18812]
"A" THESE HOLES RED'D FOR USE
PANEL LENGTH
• ]O 3/8" EBBS.Q3
• 10 3/8" [568.03
I' O 3/8" [315.03
1' 0 3/8" [315.03
OUTSIDE A[R_ FILTER ACCESS PANEL
BOTTOM POWER CHART: SIZES
DIA, [51] POWER SUPPLY KNOCK OUT
REAR
3" 1 1/2"_ O" 4 1/2"
[952.5] _ ECONOMISER_HOOD _ /FEl 14] l BLOCKOFF
COMPRESSOR
k
N
CONDENSER COIL PANEL
_8 SEE NOTE _8, CORNER "B'. _(_)0 " " p._i} -
f- " _O' 3 3/15"
/ _ _ [B1 ]
II I RETURN AIR OPEN;N G 1B/IS" <_1 RETURN A;R
IIK _ ?J /) I _ {E137_RIGHT SIDE
II O" 5 3X4" DRAIN OPENING
2" O 1/4" [147] IIN BASEPAN / ISUPPLYAIRI 1" 5 3/4" _ SUPPLY 1'6 1/2"
_ _18] _ L_ I EVAPORATOR , OPENING I [451] rd!'Zd!/_Y AIR rl [470]
_I I COIL VERTICAL IP 7_F_ J1_
o _<Z_o__ I _ (_B_ L__
O" B 3/4" [2901 I [BBI4] 38
EBSIO]
BEE BOTTOM POWER I If _D_MT I I I_"-"--_ _ /_/'
CHART (ELEC. ONLY) I1_ IRWIn/ /16,[llIl]
CONTROL BOX/ E4BO] It U --T _ EgS2.S]
PANEL BLOWER ACCESS PANEL i_ HORI
O' 4 B/1B" 30' 6 III OPENING KII
BURNER ACCESS _l_l INDOOR FAN MOTOR _" I __I
_2 ._5 3_8" t FOR) TRUCK SLOTS /0" S 3/4" _" 1 15/1
oo
BURNER ACCESS [214] O" 2 IW4"DIA OUT_]DE 5_PPLY AIR RETURN AIR BAROMETRIC RELIEF DISCHARGE
ACCE55 COVER l" S 1/4" [438]
\ , 0.,o,
ALT CONDENSATE
2" 11 11w15" _ [78] [306] IE3_] _ ,' VERTICAL
[BOB] 6" 1 11116" ] 1' 5 5118" D' 10 13/16" O" 4 1/1G"
, II:I I
1" 5 liB" 2' 1 11/1@"
(lO8s_J _ II II ol I HORIZONTAL_ (_,4_
• 11 lJ
....... o-B_x,_- / ,,4B_ 4_ ,BBB.B, "-G11144.BX,G"
I 0"3 I/IG'_ LI" 0 IWlG_ LO" 3 3/18°--/_'6-"-_CORNER "C" 0" 7 IX4"
nil II _l Kh ZBNTAL
I II I II o' _ 7/a'l 5UPPLYAIR L 7" 4"
PANEL FRONT (TYP8PLACES) R IGHT S IDE ESTD.CONDENSATEDRAIN
POWER EXHAUST
F/ ECOiOMI_ERN VIEW 5
I VEBTICALI (27B O'BBZB"
E I o'2Bw'B'(GS
_[184] _ ECONOMISER IV
[1872] _ 0" 0 3/8" r [43B'7_ _[103.2] W/ POWER EXHAUBT
_ ElI
[57] OF PANEL
I I
Fig. 6A -- Base Unit Dimensions -- 48TF,TM004-006 and 48TF007
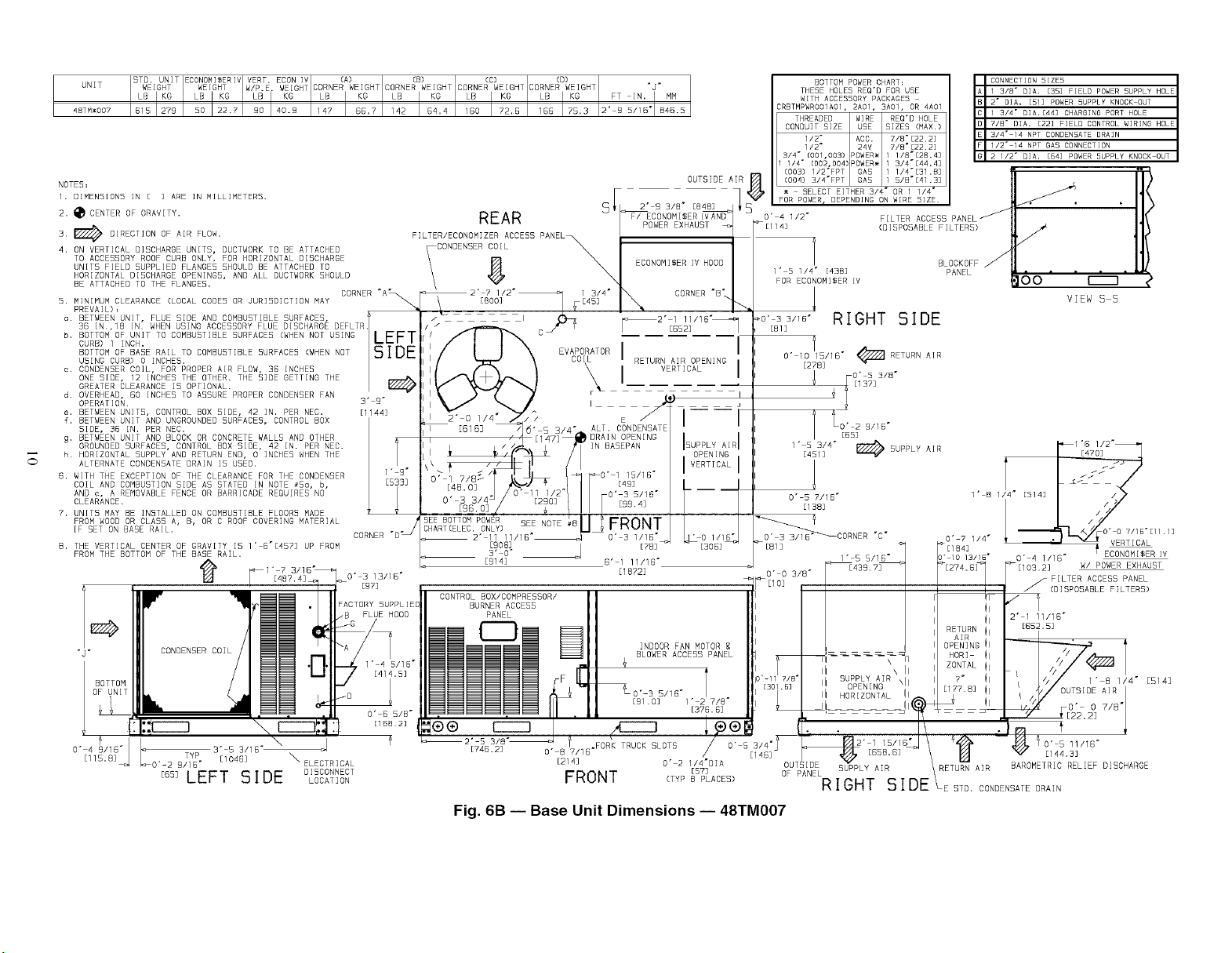
UNIT
48TM_007
NOTES=
1.
DIMENSIONS IN [ ] ARE IN MILLIMETERS.
2.
_CENTER OF GRAVITY.
DIRECTION OF AIR FLOW.
ON VERTICAL DISCHARGE UNITS, DUCTWORK TO BE ATTACHED
TO ACCESSORY ROOF CURB ONLY. FOR HORIZONTAL DISCHARGE
UNITS FIELD SUPPLIED FLANGES SHOULD BE ATTACHED TO
HORIZONTAL DISCHARGE OPENINGS, AND ALL OUCTWORK SHOULD
BE ATTACHED TO THE FLANGES.
5. MINIMUM CLEARANCE (LOCAL CODE5 OR JURI5DICTION MAY
PREVAIL) :
o. BETWEEN UNIT, FLUE SIDE AND COMBUSTIBLE SURFACES, l
38 [N.,18 IN. WHEN USING ACCESSORY FLUE DISCHARGE DEFLTR.
b. BOTTOM OF UNIT TO COMBUSTIBLE SURFACES [WHEN NOT USING
CURB) I INCH.
BOTTOM OF BASE RAIL TO COMBUSTIBLE SURFACES (WHEN NOT
USING CURB) 0 INCHES.
e. CONDENSER C8]L, F8R PROPER AIR FLOW, 38 INCHES
ONE 5[DE, 12 INCHES THE OTHER. THE SIDE GETTING THE
CREATER CLEARANCE I5 OPTIONAL.
d. OVERHEAD, SO INCHES TO ASSURE PROPER CONDENSER FAN
OPERATION. 3" B"
e. BETWEEN UNITS, CONTROL BOX SIDE, 42 IN. PER NEC. [1144]
£. BETWEEN UNIT AND UNGROUNDED SURFACES, CONTROL BOX
SIDE, 36 IN. PER NEC.
g' BETWEEN UNIT AND BLOCK OR CONCRETE WALLS AND OTHER
GROUNDED SURFACES, CONTROL 80X SIDE, 42 IN. PER NEC.
h. HORIZONTAL SUPPLY AND RETURN END, O INCHES WHEN THE
ALTERNATE CONDENSATE DRAIN IS USED.
G. WITH THE EXCEPTION OF THE CLEARANCE FOR THE CONDENSER
COIL AND COMBUSTION SIDE AS STATED IN NOTE #5o, b,
AND c, A REMOVABLE FENCE OR BARRICADE REQUIRES NO
CLEARANCE.
7. UNITS MAY BE INSTALLED ON COMBUSTIBLE FLOORS MADE
FROM WOOD OR CLASS A, B, OR C ROOF COVERING MATERIAL
[F SET ON BASE RAIL.
8. THE VERTICAL CENTER OF GRAVITY IS 1" 5"[457] UP FROM
FROM THE BOTTOM OF THE BASE RAIL.
CORNER
CORNER
r o 43z,8
FACTORY 5UPPLIED
[115.83 TYP 3" 5 3/15"_
0'49/161 0_0- 2" 2
8/18" [1045] _ ELECTRICAL
EE5)LEFT SIDE OIBCONNECTLocATION
FLUE HOOD
1" 4 5/16"
[414.5]
O" 5 5/8"
[158.2]
REAR
FILTER/ECBNOMIZERIcoNDENSER8CoILACCESS PANEL_
cf_
EVAPORATOR I
COIL RETURN AIR OPENING
VERTICAL
' E) I----i
ALT. CONDENSATE
_DRAIN OPENING
IN BASEPAN
15/18"
[48]
O" 3 5/18"
E98.4]
2"11
[BOB]
3" O"
[814]
CONTROL BOX/COMPRESSOR/
BURNER ACCESS
PANEL
2' 5 3/8
[74G.2]
O" 8
[214] O" 2 1/4"D]A
FRONT
O" 3 1/15"
G" 1 ll/1G"
[1872]
BLOWER ACCESS PANEL
, [378. G]
7/18.FORK TRUCK SLOTS O" 5 3/4"
[81.0] I" 2 7/8"
FRONT (TYPB PLACES)
Fig. 6B -- Base Unit Dimensions -- 48TM007
SUPPLY AIRI
I VERTICAL I
j" 0 1/
[78]
INDOOR FAN MOTOR
8s/ s-
OPENING
[305]
l eC
[57]
BOTTOM POWER CHART:
THE5E HOLE5 REQ'D FOR U5E
WITH ACCESSORY PACKAGES
CRBTMPWROO1A01, 2AOl, 3A01, OR 4AOl
THREADED WIRE REQ'D HOLE
CONDUIT SIZE USE SIZES (MAX.)
1/2" ACC. 7/8"[22.2]
1/2" 24V 7/8"[22.2]
3/4" (001,003) _OWER_ 1/8"E28.43
1/4" (O02,004)_OWER_ 3/4"[44,43
(003) 1/2"FPT GAS 1/4"[31183
(DISPOSABLE FILTERS)
I BLOCKOFF
l" S l/4" [438] PANEL
FOR ECSNOMISER IV
_0,33z_- RIGHT SIDE
[81]
O" I0 IS/IB" _._____ RETURN AIR
[278]
I
l" 5 3/4"
[4Sl]
O' S 7/15"
[138]
_EB1]
O' 0 3/8"
O' 5 3/8"
_ F[137]
_O' 2 8Z15"
[85]
"C"
1" 5 5/15"
[438.7]
IIi \ h ZONTAL
III SUPPLY AIR Nil 7"
III HORIZONTAL lh
\ 1 HOR]
OPENING
II! lh(
El 46]
OUT SUPPLY AIR
OF PANEL
RIGHT SIDE
CONNECTION SIZES
1 3/8" DIA. [35] FIELD POWER SUPPLY HOLE
O0
VIEW S S
SUPPLY AIR _, [470]
1/4" [514] /
1' 8 l_ A
O' 7 1/4" L
[IB4] _ ECONOMISER IV
13/IE" O' 4 1/18"
2' 1 11/15"
[552.5]
RETURN AIR
E STD. CONDENSATE DRAIN
BAROMETRIC RELIEF DISCHARGE
_ Z O" 0 7/16"[11.1]
W/ POWER EXHAUST
O" 0 7/8"
OUTSIDE AIR v
t
O" S 11/18"
044.33
_1'81/2"
1' 8 1/4" [514]
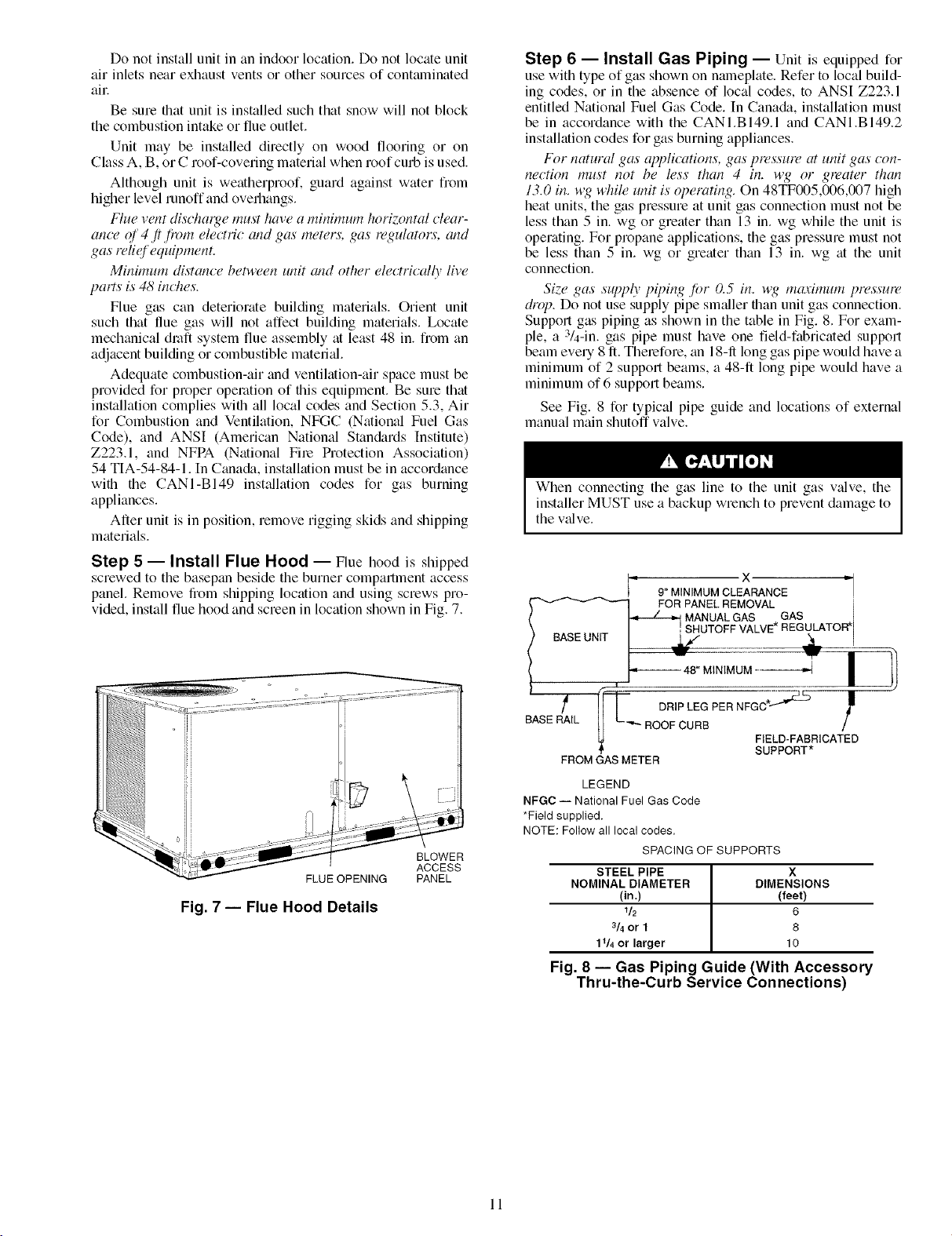
Do not install unit in an indoor location. Do not locate unit
air inlets near exhaust vents or other sources of contalninated
all:
Be sure that unit is installed such that snow will not block
the combustion intake or flue outlet.
Unit may be installed directly on wood flooring or on
Class A, B, or C roof-covering material when roof curb is used.
Although unit is weatherproof, guard against water fiom
higher level runoff and overhangs.
Flue vent dischaqq, e must have a minimum hoH;ontul clear-
ance qf4 fi,fmm elecTHc and gas mewrs, gas mgulawt:_, and
gas milerequipment.
Minimum distance between unit and other electrically live
parts is 48 inches.
Flue gas can deteriorate building materials. Orient unit
such that flue gas will not affect building materials. Locate
mechanical draft system flue assembly at least 48 in. fiom an
adjacent building or combustible materi_d.
Adequate combustion-air and ventilation-air space must be
provided for proper operation of this equipment. Be sure that
installation complies with all local codes and Section 5.3, Air
for Combustion and Ventilation, NFGC (National Fuel Gas
Code), and ANSI (American National Stan&rds Institute)
Z223.1, and NFPA (National File Protection Association)
54 TIA-54-84-1. In Cana&t, installation must be in accordance
with the CANI-BI49 inst_dlation codes for gas burning
appliances.
After unit is in position, remove rigging skids and shipping
materials.
Step 6 -- Install Gas Piping -- Unit is equipped for
use with type of gas shown on nameplate. Refer to local build-
ing codes, or in the absence of local codes, to ANSI Z223.1
entitled National Fuel Gas Code. In Cana&t, installation must
be in accordance with the CANI.BI49A and CANI.BI49.2
installation codes for gas burning appliances.
For natural gas applications, gas pressuw at unit gas con-
nection must not be less titan 4 in. wg or greaWr than
13.0 in. wg while unit is operating. On 48TF005,006,007 high
heat units, the gas pressure at unit gas connection must not be
less than 5 in. wg or greater than 13 in. wg while the unit is
operating. For propane applications, the gas pressure must not
be less than 5 in. wg or greater than 13 in. wg at the unit
connection.
Size gas supply piping .fbr 0.5 in. wg maximum pressure
drop. Do not use supply pipe smNler titan unit gas connection.
Support gas piping as shown in the table in Fig. 8. For exam-
ple, a 3h-in. gas pipe must have one field-fabricated support
beam every 8 ft. Therefore, an 18-1l long gas pipe would have a
minimum of 2 support beams, a 48-ft long pipe would have a
minimum of 6 support beams.
See Fig. 8 for typical pipe guide and locations of external
manual main shutoff valve.
When connecting the gas line to the unit gas valve, the
installer MUST use a backup wrench to prevent damage to
the v_flve.
Step 5 -- Install Flue Hood -- Flue hood is shipped
screwed to the basepan beside the burner compmlment access
panel. Remove from shipping location and using screws pro-
vide& install flue hood and screen in location shown in Fig. 7.
BLOWER
FLUE OPENING
Fig. 7 -- Flue Hood Details
ACCESS
PANEL
,-, X
9" MINIMUM CLEARANCE
,i SHUTOFF VALVE REGULATOR*]
BASE UNIT =o=================o==o==
l_ FOR PANEL REMOVAL
/ DRIP LEG PER NFGC!
BASE RAIL -'*'" ROOF CURB
FROM GAS METER
NFGC -- National Fuel Gas Code
*Field supplied.
NOTE: Follow all local codes.
NOMINAL DIAMETER DIMENSIONS
-._--_ 48" MINIM UM Illll li
LEGEND
STEEL PIPE X
(in.) (feet)
V2 6
314or 1 8
1V4 or larger 10
MANUALGAS.GAS I
FIELD-FABRICATED
SUPPORT*
SPACING OF SUPPORTS
Fig. 8 -- Gas Piping Guide (With Accessory
Thru-the-Curb Service Connections)
11
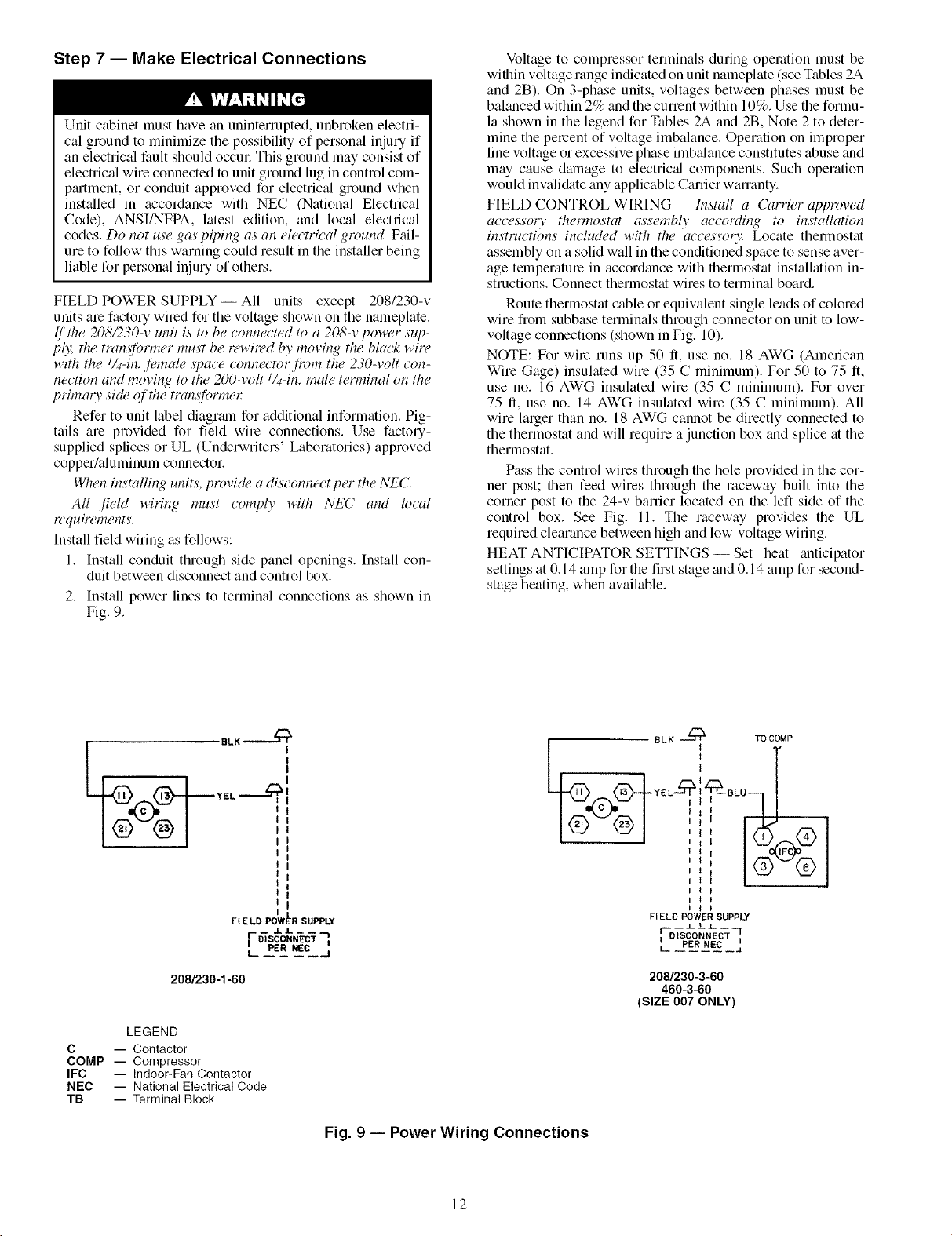
Step 7 -- Make Electrical Connections
Unit cabinet must have tin uninterrupted, unbroken electri-
cal ground to minimize the possibility of persomd injury if
an electrical fault should occm: This ground may consist of
electrical wire connected to unit ground lug in control com-
ptu-tment, or conduit approved for electrical ground when
insttdled in accordance with NEC (National Electrical
Code), ANSI/NFPA, latest edition, and local electrical
codes. Do not use gas piping as an electrical ground. Fail-
ure to follow this warning could result in the installer being
liable for personal injury of others.
FIELD POWER SUPPLY -- All units except 208/230-v
units are factory wired for the voltage shown on the nameplate.
If the 208/230-v unit is to be connected to a 208-v power sup-
p13; the tran_fin'mer must be rewired by moving the black wire
with the//4-in, fi, male .s)ga_e connecwr fi'om the 230-volt _on-
nection and moving to the 200-volt l/4-in, mule terminal on the
prima 0" sMe of the tran@n'mel:
Refer to unit label diagrmn for additional information. Pig-
tails are provided for field wire connections. Use factory-
supplied splices or UL (Underwriters' Laboratories) approved
copper/aluminum connector
When installing units, proffde a dis_ onnect per the NEC.
All .field wiring must comply with NEC and lotzd
requirements.
Install field wiring as follows:
1. Install conduit through side panel openings. Install con-
duit between disconnect and control box.
2. Install power lines to terminal connections as shown in
Fig. 9.
Voltage to compressor terminals during operation must be
within voltage range indicated on unit nameplate (see Tables 2A
and 2B). On 3-phase units, voltages between phases must be
bahmced within 2% and the currant within 10%. Use the formu-
la shown in the legend for Tables 2A and 2B, Note 2 to deter-
mine the percent of voltage imbalance. Operation on improper
line voltage or excessive phase imbalance constitutes abuse and
may cause dmnage to electrictd components. Such operation
would invali&tte any applicable Carrier wammty.
FIELD CONTROL WIRING -- Install a Carrier-apl)roved
acc'essoiw thermostat assembly according to installation
instructions included w#h the accessolw Locate thermostat
assembly on a solid wall in the conditione_l space to sense aver-
age temperature in accor&mce with thermostat installation in-
structions. Connect thermostat wires to terminal board.
Route thermostat cable or equivalent single leads of colored
wire from subbase terminals through connector on unit to low-
voltage connections (shown in Fig. 10).
NOTE: For wire runs up 50 ft, use no. 18 AWG (American
Wire Gage) insulated wire (35 C minimum). For 50 to 75 ft,
use no. 16 AWG insulated wire (35 C minimum). For over
75 It, use no. 14 AWG insulated wire (35 C minimum). All
wire larger than no. 18 AWG cannot be directly connected to
the thermostat and will require a junction box and splice tit the
thermostat.
Pass the control wires through the hole provided in the cor-
ner post; then feed wires through the raceway built into the
corner post to the 24-v barrier located on the left side of the
control box. See Fig. 11. The raceway provides the UL
required clearance between high and low-voltage wiring.
HEAT ANTICIPATOR SETTINGS -- Set heat anticipator
settings tit 0.14 amp for the first stage and 0.14 amp for second-
stage heating, when available.
FIELD_W_'.suPP,_
r'DISCONNECT I
I PER NEC j
208/230-1-60
LEGEND
C -- Contactor
COMP -- Compressor
IFC -- Indoor-Fan Contactor
NEC -- National Electrical Code
TB -- Terminal Block
Fig. 9 -- Power Wiring Connections
BLK TO COMP
FI ELD POWER SUPPLY
__ .LJ.,L.__
Ir-'DISCONN ECT-I
t PER NECC__J
208/230-3-60
460-3-60
(SIZE 007 ONLY)
12
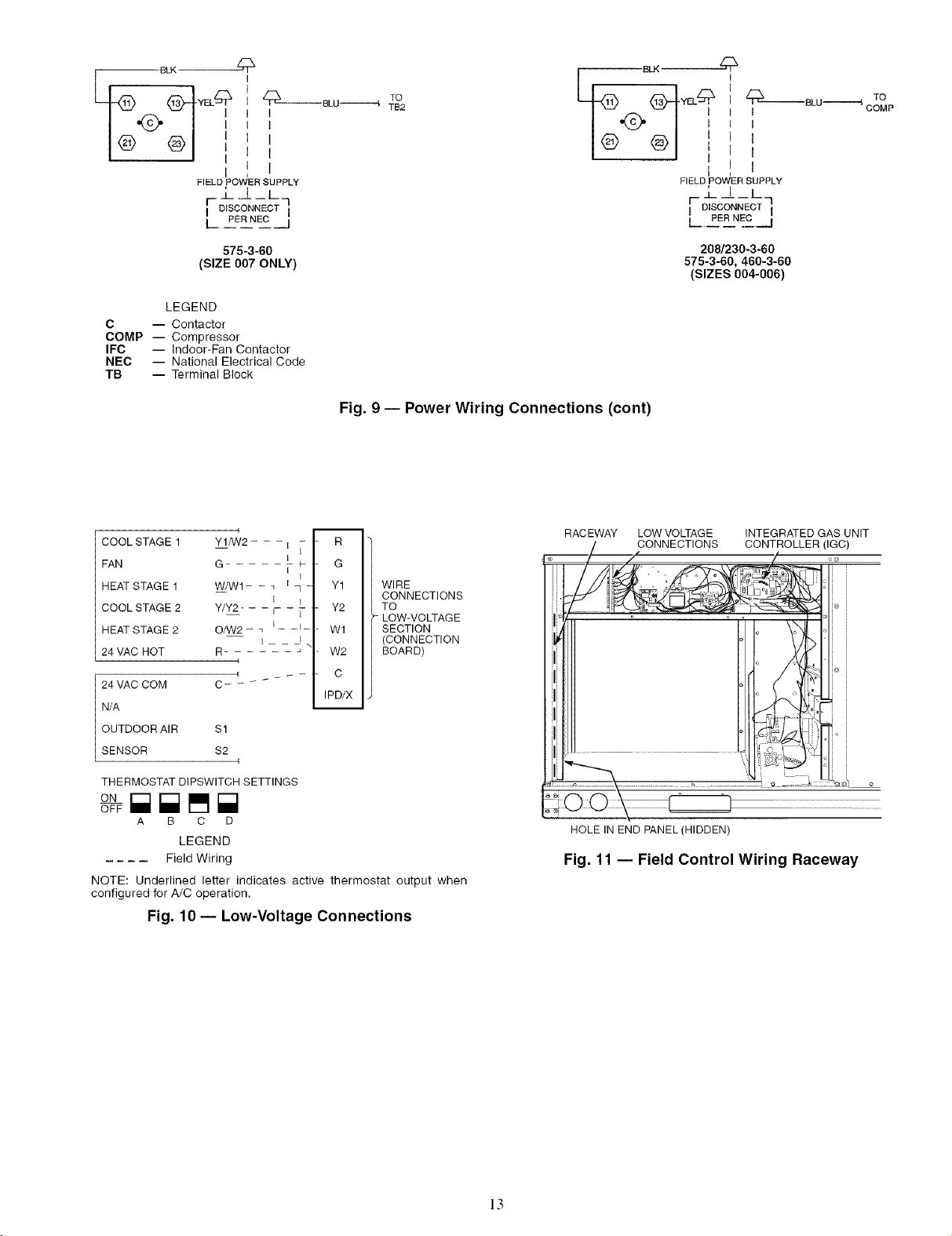
z_--_BLU'--------_ TO
I
!
I
I
I
FIELD POWER SUPPLY
-L- ____L
F DISCONNECT ]
[ PER NEC j
575-3-60
(SIZE 007 ONLY)
LEGEND
C -- Contactor
COMP -- Compressor
IFC -- Indoor-Fan Contactor
NEC -- National Electrical Code
TB -- Terminal Block
TB2
Fig. 9 -- Power Wiring Connections (cont)
-BLK--
FIELD POWER SUPPLY
575-3-60, 460-3-60
I
I
I
I
I
..L.. __L_
r I
I DISCONNECT I
PER NEC I
208/230-3-60
(SIZES 004-006)
BLU-------4 cTOMp
COOL STAGE 1
FAN
HEAT STAGE 1
COOL STAGE 2
HEAT STAGE 2
24 VAC HOT
24 VAC COM
N/A
OUTDOOR AIR Sl
SENSOR S2
THERMOSTAT DIPSWITCH SETTINGS
ON
A B C D
Field Wiring
NOTE: Underlined letter indicates active thermostat output when
configured for A/C operation.
Y1/W2- - -I [- - R
W/W1- - _ I q _ Y1 WIRE
Y/Y2- - - F - _- - Y2 TO
O/W2- _ I_ _1_ _ Wl SECTION
-- i _ I (CONNECTION
R= -_3 _ , W2 BOARD)
LEGEND
m
i _ CONNECTIONS
/
LOW-VOLTAGE
IPD/X
Fig. 10- Low-Voltage Connections
RACEWAY LOW VOLTAGE
CONNECTIONS
INTEGRATED GAS UNIT
CONTROLLER (IGC)
il
_"--m
HOLE IN END PANEL (HIDDEN)
Fig. 11 -- Field Control Wiring Raceway
13
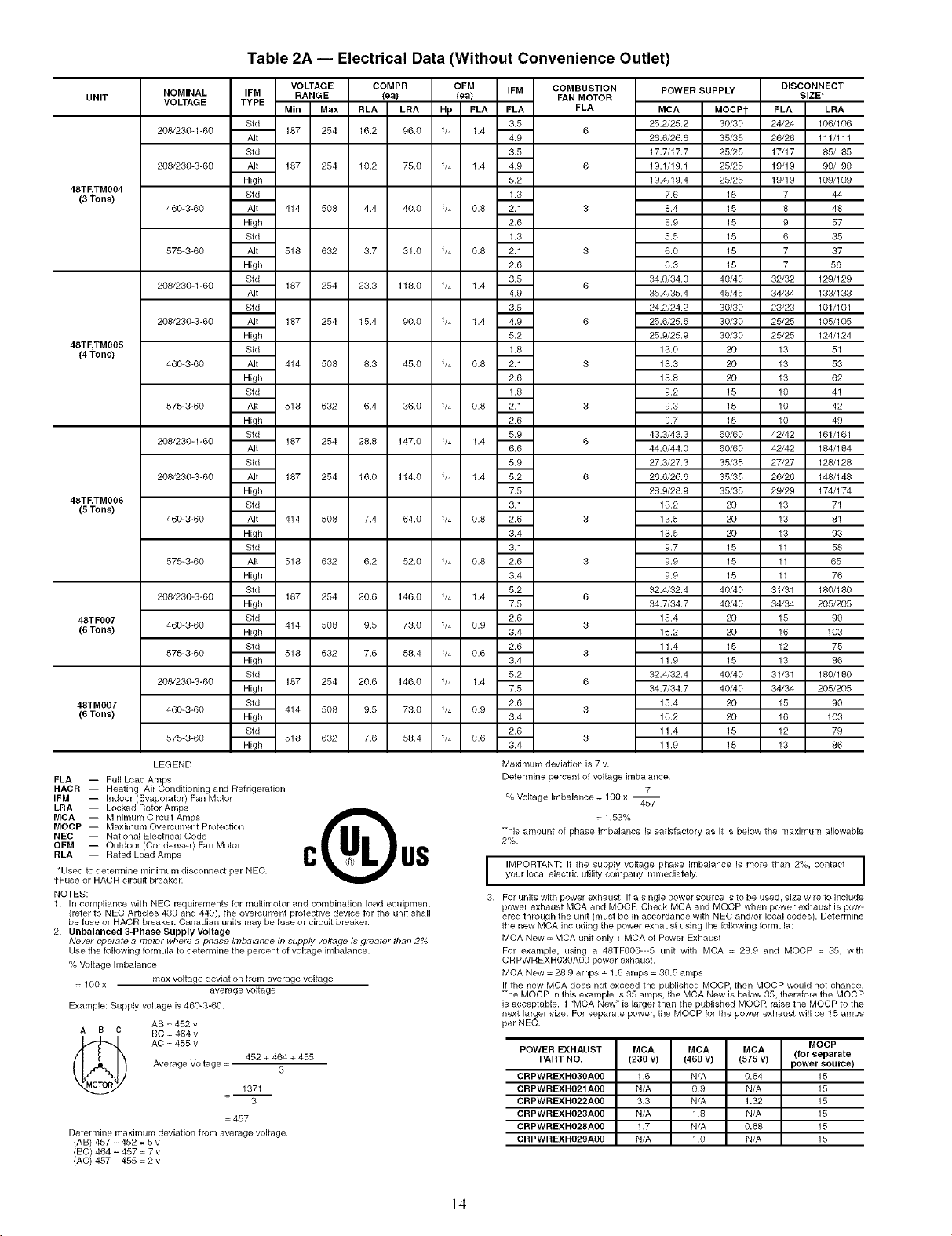
Table 2A -- Electrical Data (Without Convenience Outlet)
UNIT
48TF,TM004
(3 Tons)
48TF,TM005
(4 Tons)
48TF,TM006
(5 Tons)
48TF007
(0 Tons)
48TM007
(6 Tons)
FLA -- Full Load Amps
HACR -- Heating, Air Conditioning and Refrigeration
IFM -- Indoor (Evaporator) Fan Motor
MCA -- Minir'aum Circuit Amps
MOCP -- Maxir'aum Overcurrent Protection
NEC -- National Electrical Code
OFM -- Outdoor (Cond ...... ) Far, Motor ..__
RLA -- Rated Load Amps
LRA -- Locked Rotor Amps C @
*Used to determine minimur'a disconnect per NEC.
tFuse or HAOR circuit breaker.
NOTES:
1. In compliance with NEC requirements for multimotor and combination load equipment
(refer to NEC Articles 430 and 440), the overcurrent protective device k)r the unit shall
be fuse or HAOR breaker. Canadian units may be fuse or circuit breaker.
2. Unbalanced 3-Phase Supply Voltage
Never operate a motor w6ere a phase imbalance in supply voltage is greater than 2%.
Use the following formula to determine the percent of voltage imbalance.
% Voltage Imbalance
= 100 x max voltage deviation from average voltage
Example: Supply voltage is 460-3-60.
A B C BC = 464v
Determine r'aaximum deviation from average voltage.
(AB) 457 - 452 = 5 v
(BC) 464 - 457 = 7 v
(AC) 457 - 455 = 2 v
NOMINAL
VOLTAGE
208/230-1-60
208/230-3-60
460-3-60
575-3-60
208/230-1-60
208/230=3-60
460-3-60
575-3-60
208/230-1-60
208/230-3-60
460-3-60
575-3-60
208/230=3-60
460-3-60
575-3-60
208/230-3-60
460-8-60
575-8-60
LEGEND
AB = 452 v
Average Voltage = 462 + 464 + 455
AC = 455 v
TYPE FAN MOTOR
average voltage
1371
= 457
VOLTAGE COMPR OFM COMBUSTION
IFM RANGE (ea) (ea) IFM
MIn Max RLA LRA Hp FLA FLA FLA
Std 3.5
187 254 16.2 96.0 V4 1.4 .6
AIt 4.9
Std 3.6
AIt 187 264 10.2 75.0 V4 1.4 4.9 .6
High 5.2
Std 1.3
AIt 414 508 4.4 40.0 V4 0.8 2.1 .3
High 2.6
Std 1.3
AIt 518 632 8.7 31.0 V4 0.8 2.1 .3
High 2.6
Std 3.6
187 264 23.3 118,0 V4 1.4 .6
AIt 4.9
Std 3.6
AIt 187 264 15.4 90.0 V4 1.4 4.9 .6
High 5.2
Std 1.8
AIt 414 508 8.3 45.0 V4 0.8 2.1 .3
High 2.6
Std 1.8
AIt 518 632 6.4 86.0 V4 0.8 2.1 .3
High 2.6
Std 5.9
187 264 28.8 147,0 V4 1.4 .6
AIt 6.6
Std 5.9
AIt 187 264 16.0 114,0 V4 1.4 5.2 .6
High 7.6
Std 3.1
AIt 414 508 7.4 64.0 V4 0.8 2.6 .3
High 3.4
Std 3.1
AIt 518 632 6.2 52.0 V4 0.8 2.6 .3
High 3.4
Std 5.2
187 254 20.6 146.0 V4 1.4 .6
High 7.5
S'td 2.6
414 508 9.5 73.0 V4 0.9 .3
High 3.4
Std 2.6
518 632 7.6 58.4 V4 0.6 .3
High 3.4
Std 5.2
187 254 20.6 146.0 V4 1.4 .6
High 7.5
Std 2.6
414 508 9.5 73.0 V4 0.9 .3
High 3.4
Std 2.6
518 632 7.6 58.4 V4 0.6 .3
High 3.4
3
3
POWER SUPPLY DISCONNECT
MCA MOCPt FLA LRA
25.2/25.2 30/80 24/24 106/106
26.6/26.6 35/85 26/26 111/111
17.7/17.7 25/25 17/17 85/ 85
19.1/19.1 25/25 19/19 90/ 90
19.4/19.4 25/25 19/19 109/109
7.6 15 7 44
8.4 15 8 48
8.9 15 9 57
5.5 15 6 35
6.0 15 7 37
6.3 15 7 56
34.0/34.0 40/40 32/32 129/129
35.4/35.4 45/45 34/34 133/133
24.2/24.2 30/30 23/23 101/101
25.6/25.6 30/30 25/25 105/105
25.9/25.9 30/30 25/25 124/124
13.0 20 13 51
13.3 20 13 53
13.8 20 13 62
9.2 15 10 41
9.3 15 10 42
9.7 15 10 49
43.3/43.3 60/60 42/42 161/161
44.0/44.0 60/60 42/42 184/184
27.3/27.3 35/35 27/27 128/128
26.6/26.6 35/35 26/26 148/148
28.9/28.9 35/35 29/29 174/174
13.2 20 13 71
13.5 20 13 81
13.5 20 13 93
9.7 15 11 58
9.9 15 11 65
9.9 15 11 76
32.4/32.4 40/40 31/31 180/180
34.7/34.7 40/40 34/34 205/205
15.4 20 15 90
16.2 20 16 103
11.4 15 12 75
11.9 15 13 86
32.4/32.4 40/40 31/31 180/180
34.7/34.7 40/40 34/34 205/205
15.4 20 15 90
16.2 20 16 103
11.4 15 12 79
11.9 15 13 86
Maxir'aum deviation is 7 v.
Detemline percent of voltage imbalance.
% Voltage Imbalance = 100 x --
This amount of phase imbalance is satisfactory as it is below the maximum alk)wable
2%.
your local electric utility company immediately.
I IMPORTANT: If the supply voltage phase imbalance is more than 2%, contact I
3. For units with power exhaust: If a single power source is to be used, size wire to include
power exhaust MCA and MOOR Check MCA and MOCP when power exhaust is pow-
ered through the unit (must be in accordance with NED and/or local codes). Determine
the new MCA including the power exhaust using the following formula:
MCA New = MCA unit only + MCA of Power Exhaust
For example, using a 48TF006---5 unit with MCA = 28.9 and MOCP = 35, with
CRPWREXH080A00 power exhaust.
MCA New = 28.9 amps + 1.6 amps = 30.5 amps
If the new MCA does not exceed the published MOCP, then MOCP would not change.
The MOOP in this example is 35 amps, the MCA New is below 35, therefore the MOCP
is acceptable. If "MCA New" is larger than the published MOOP, raise the MOCP to the
next larger size. For separate power, the MOCP for the power exhaust will be 15 amps
per NEC.
POWER EXHAUST MCA MCA MCA (for separate
PART NO. (230 v) (460 v) (575 v) power source)
CRPWREXH030AO0 1.6 N/A 0.64 15
CRPWBEXH021AO0 N/A 0.9 N/A 15
CRPWREXH022A00 3.3 N/A 1.32 15
CRPWREXH023A00 N/A 1.8 N/A 15
CRPWREXH028A00 1.7 N/A 0.08 15
CRPWREXH029A00 N/A 1.0 N/A 15
= 1.53%
7
457
SIZE*
MOCP
I
14
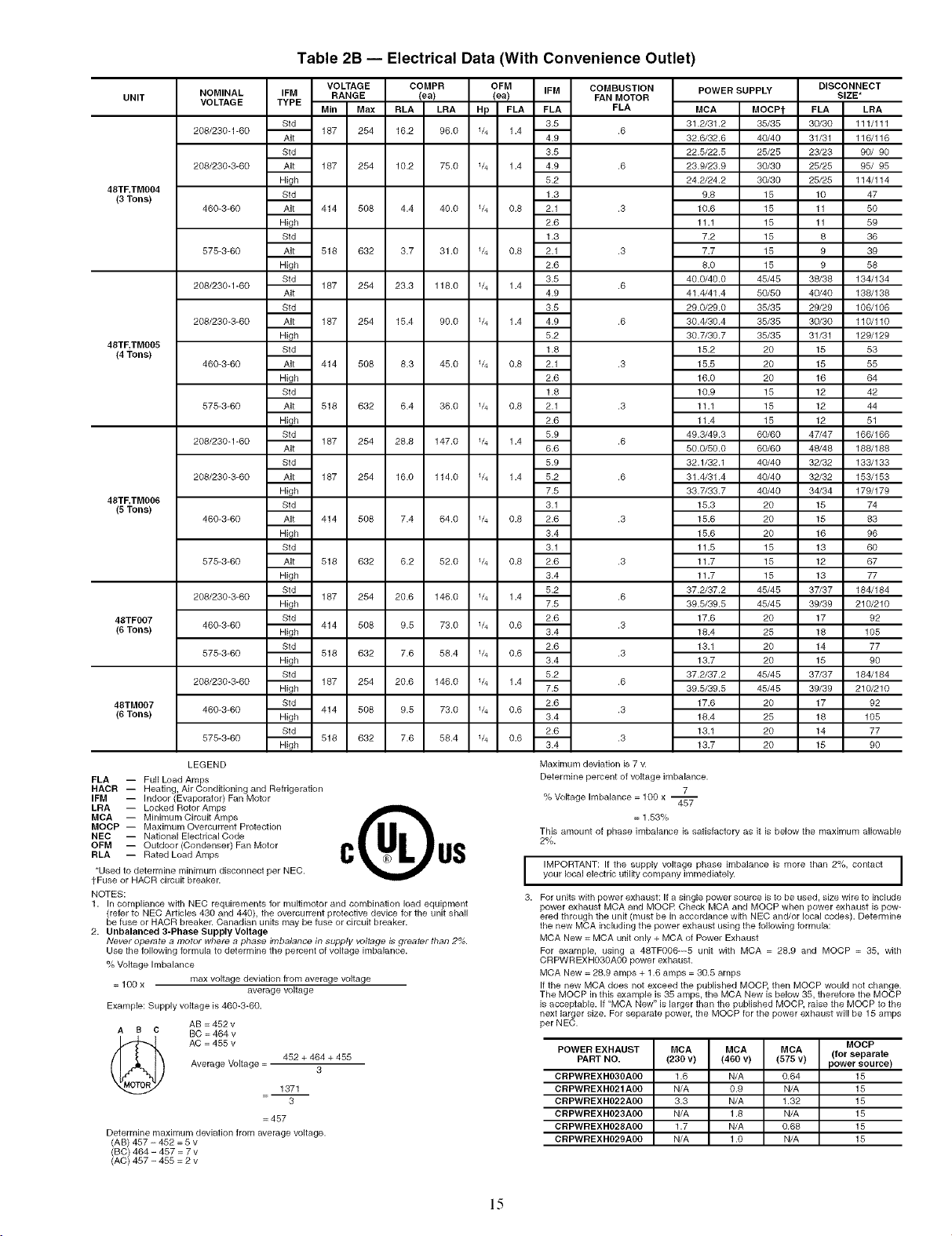
Table 2B -- Electrical Data (With Convenience Outlet)
UNIT
48TF, TM004
(3 Tons)
48TF, TM005
(4 Tons)
48TF, TM006
(5 Tons)
48TF007
(6 Tons)
46TM007
(6 Tons)
FLA -- Full Load Amps
HACR -- Heating, AirConditionb_gandRefrigeratk)n
IFM -- Indoor (Evaporator) Fan Mok)r
MCA -- Minimum Circuit Amps
MOCP -- Maximum Overcurrent Protection
NEC -- National ElectricaICode
OFM -- Outdoor (Cond ...... ) Fan Motor II II1[=1,
RLA -- Rated Load Amps
LRA -- Locked Rotor Amps C @
*Used to detemline minimum disconnect per NEC.
tFuse or HACR circuit breaker.
NOTES:
1. In compliance with NEC requirements for mugimotor and combination load equipment
(refer to NEC Articles 430 and 440), the overcurrent protective device for the unit shall
be fuse or HACR breaker. Canadian units may be fuse or circuit breaker.
2. Unbalanced 3-Phase Supply Voltage
Never operate a motor where a phase imbalance in supply voltage is greater than 2%.
Use the following formula to determine the percent of vogage imbalance.
% Voltage Imbalance
= 100 x max vogage deviation from average vogage
Example: Supply vogage is 480-3-60.
A 8 C BC =464 v
Determine maximum deviation from average w)gage.
(AB) 457 - 452 = 5 v
(BC) 464 - 457 = 7 v
(AC) 457 - 455 = 2 v
NOMINAL
VOLTAGE
208/230-1-60
208/230-3-60
460-3-60
575-3-60
208/230-1-60
208/230-3=60
460-3-60
575-3-60
208/230-1-60
208/230-3=60
460-3-80
575-3-60
208/230-3-60 187 254 20.6 146.0 l& 1.4
460-3-60 414 508 9.5 73.0 l& 0.6
575-3-60 518 632 7.6 58.4 l& 0.6
208/230-3-60 187 254 20.6 146.0 l& 1.4
460-3-60 414 508 9.5 73.0 l& 0.6
575-3-60 518 632 7.6 58.4 l& 0.6
LEGEND
AB = 452 v
Average Voltage = 452 + 464 + 456
AC = 456 v
TYPE FAN MOTOR
average voltage
= 457
VOLTAGE COMPR OFM COMBUSTION
IFM RANGE (ea) (ea) IFM
MIn Max RLA LRA Hp FLA FLA FLA
Std 3.5
187 254 16.2 96.0 1/4 1.4 .6
AIt 4.9
Std 3.5
AIt 187 254 10.2 75.0 1/4 1.4 4.9 .6
High 5.2
Std 1.3
AIt 414 508 4.4 40.0 1/4 0.8 2.1 .3
High 2.6
Std 1.3
AIt 518 632 3.7 31.0 1/4 0.8 2.1 .3
High 2.6
Std 3.5
187 254 23.3 118.0 1/4 1.4 .6
A9 4.9
Std 3.5
AIt 187 254 15.4 90.0 1/4 1.4 4.9 .6
High 5.2
Std 1.8
AIt 414 508 8.3 45.0 1/4 0.8 2.1 .3
High 2.6
Std 1.8
AIt 518 632 6.4 36.0 1/4 0.8 2.1 .3
Hitch 2.6
Std 5.9
187 254 28.8 147.0 1/4 1.4 .6
A9 6.6
Std 5.9
AIt 187 254 16.0 114.0 1/4 1.4 5.2 .6
High 7.5
Std 3.1
AIt 414 508 7.4 64.0 1/4 0.8 2.6 .3
Hitch 3.4
Std 3.1
AIt 518 632 6.2 52.0 1/4 0.8 2.6 .3
High
Std
High
Std
High
Std
High
Std
High
Std
High
Std
High
UO
3
1371
3
POWER SUPPLY DISCONNECT
MCA MOCPt FLA LRA
31.2/31.2 35/35 30/30 111/111
32.6/32.8 40/40 31/31 116/116
22.5/22.5 25/25 23/23 90/ 90
23.9/23.9 30/30 25/25 95/ 95
24.2/24.2 30/30 25/25 114/114
9.8 15 10 47
10.6 15 11 50
11.1 15 11 59
7.2 15 8 36
7.7 15 9 39
8.0 15 9 58
40.0/40.0 45/45 38/38 134/134
41.4/41.4 50/50 40/40 138/138
29.0/29.0 35/35 29/29 106/106
30.4/30.4 35/35 30/30 110/110
30.7/30.7 35/35 31/31 129/129
15.2 20 15 53
15.5 20 15 55
16.0 20 16 64
10.9 15 12 42
11.1 15 12 44
11.4 15 12 51
49.3/49.3 60/60 47/47 166/166
50.0/50.0 60/60 48/48 188/188
32.1/32.1 40/40 32/32 133/133
31.4/31.4 40/40 32/32 153/153
33.7/33.7 40/40 34/34 179/179
15.3 20 15 74
15.6 20 15 83
15.6 20 16 96
11.5 15 13 60
3.4
5.2
7.5
2.6
3.4
2.6
3.4
5.2
7.5
2.6
3.4
2.6
3.4
Maximum deviation is7 v.
Determine percent of voltage imbalance.
% Voltage Imbalance = 100 x 45"_"
This amount o1 phase imbalance is satisfactory as it is below the maximum allowable
2%.
your local electric utility company immediately.
I IMPORTANT: If the supply voltage phase imbalance is more than 2%, contact I
3. For units with power exhaust: If a single power source isto be used, size wire to include
power exhaust MCA and MOOR Check MCA and MOCP when power exhaust is pow-
ered through the unit (must be in accordance with NEC and/or local codes). Determine
the new MCA including the power exhaust using the foflowing formula:
MCA New = MCA unit only + MCA of Power Exhaust
For example, using a 48TF006-=-5 unit with MCA = 28.9 and MOCP = 35, with
CRPWREXH030A00 power exhaust.
MCA New = 28.9 amps + 1.6 amps = 30.5 amps
If the new MCA does not exceed the published MOOP, then MOCP would not change.
The MOCP in this example is 35 amps, the MCA New is below 35, therefore the MOCP
is acceptable. If "MCA New" is larger than the published MOCP, raise the MOCP to the
next larger size. For separate power, the MOCP for the power exhaust will be 15 amps
per NEC.
POWER EXHAUST MCA MCA MCA (for separate
CRPWREXH030A00 1.6 N/A 0.64 15
CRPWREXH021A00 N/A 0.9 N/A 15
CRPWREXH022A00 8.3 N/A 1.32 15
CRPWREXH023A00 N/A 1.8 N/A 15
CRPWREXH028A00 1.7 N/A 0.68 15
CRPWREXH029A00 N/A 1.0 N/A 15
.6
.3
.3
.6
.3
.3
= 1.53%
PART NO. (230 v) (480 v) (575 v) power source)
11.7 15 12 67
11.7 15 13 77
37.2/37.2 45/45 37/37 184/184
39.5/39.5 45/45 39/39 210/210
17.6 20 17 92
18.4 25 18 105
13.1 20 14 77
13.7 20 15 90
37.2/37.2 45/45 37/37 184/184
39.5/39.5 45/45 39/39 210/210
17.6 20 17 92
18.4 25 18 105
13.1 20 14 77
13.7 20 15 90
7
SIZE*
MOCP
I
1.5
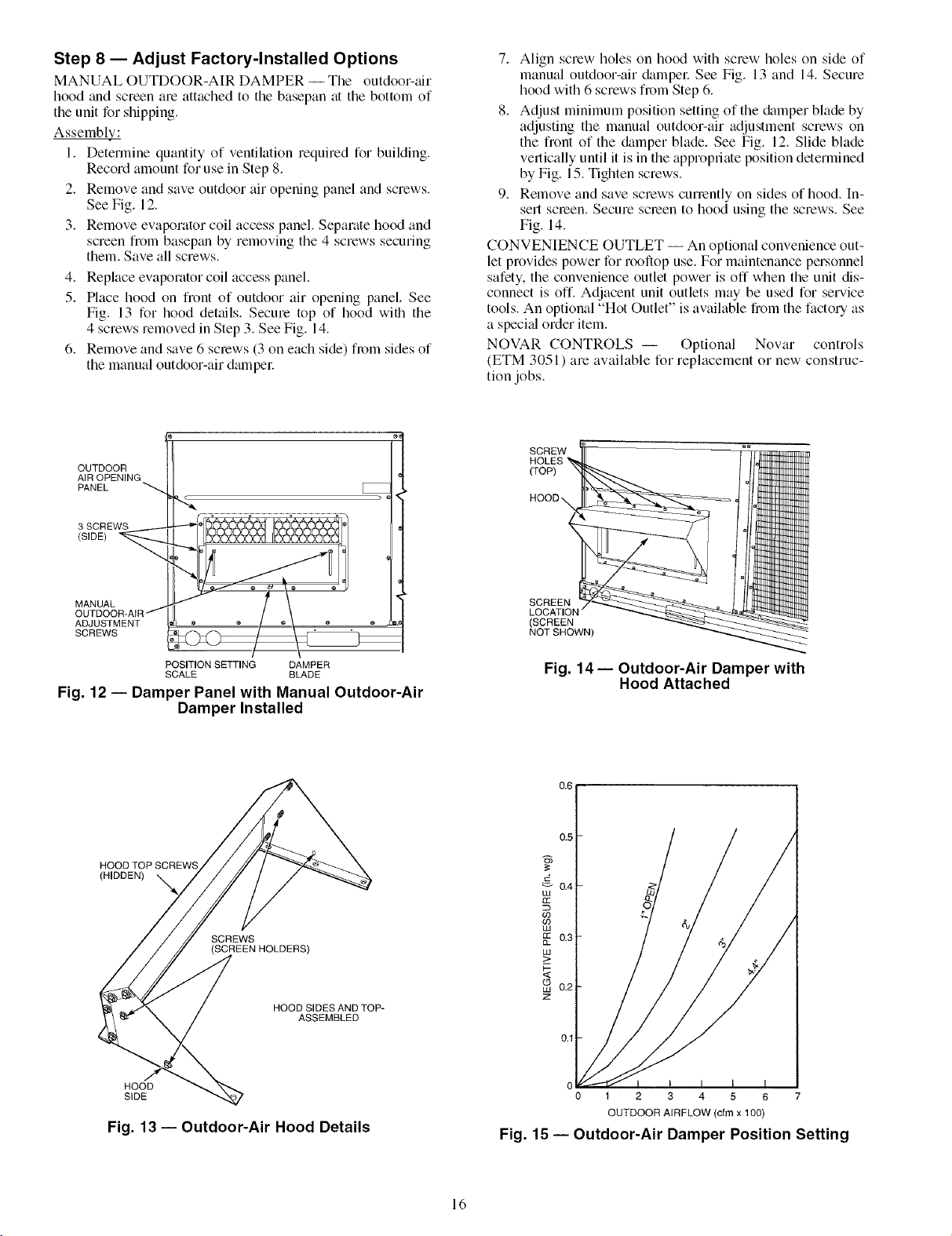
Step 8 -- Adjust Factory-Installed Options
MANUAL OUTDOOR-AIR DAMPER -- The outdoor-air
hood and screen are attached to the basepan at the bottom of
the unit for shipping.
Assembly5.:
1. Determine quantity of ventilation required for building.
Record amount for use in Step 8.
2. Remove and save outdoor air opening panel and screws.
See Fig. 12.
3. Remove evaporator coil access panel. Separate hood and
screen from basepan by removing the 4 screws securing
them. Save all screws.
4. Replace evaporator coil access panel.
5. Place hood on fiont of outdoor air opening panel. See
Fig. 13 for hood details. Secure top of hood with the
4 screws removed in Step 3. See Fig. 14.
6. Remove and save 6 screws (3 on each side) from sides of
the manual outdoor-air dmnpel:
OUTDOOR
AIR OPENING
PANEL
H
7. Align screw holes on hood with screw holes on side of
manual outdoor-air dampel: See Fig. 13 and 14. Secure
hood with 6 screws from Step 6.
8. Adjust minimum position setting of the &_mper blade by
adjusting the manual outdoor-air adjustment screws on
the front of the &tmper blade. See Fig. 12. Slide blade
vertically until it is in the appropriate position determined
by Fig. 15. Tighten screws.
9. Remove and save screws cunently on sides of hood. In-
sert scleen. Secure scleen to hood using the screws. See
Fig. 14.
CONVENIENCE OUTLET -- An optional convenience out-
let provides power for rooftop use. For maintenance personnel
safety, the convenience outlet power is off when the unit dis-
connect is off. Adjacent unit outlets may be used for service
tools. An optional "Hot Outlet" is available from the factory as
a special order item.
NOVAR CONTROLS -- Optional Novar controls
(ETM 3051) are available for replacement or new construc-
tion jobs.
SCREW
_op)
HOOD_
MANUAL
OUTDOOR-AIR J
ADJUSTMENT =
SCREWS
POSITION SETTING DAMPER
SCALE BLADE
Fig. 12 -- Damper Panel with Manual Outdoor-Air
Damper Installed
HOOD TOP SCREWS
(HIDDEN) -_
SCREWS
SCREEN HOLDERS)
HOOD SIDESAND TOP-
ASSEMBLED
SCREEN
LOCATION
(SCREEN
NOT SHOWN)
Fig. 14 -- Outdoor-Air Damper with
Hood Attached
0.6
0.5
_-_ 0.4
W
CC
w
0.3
t.tl
_>
0.2
z
0.1
HOOD
SIDE
Fig. 13 -- Outdoor-Air Hood Details
0
0 1 2 3 4 5 6 7
OUTDOOR AIRFLOW (cfm x 100)
Fig. 15 -- Outdoor-Air Damper Position Setting
16
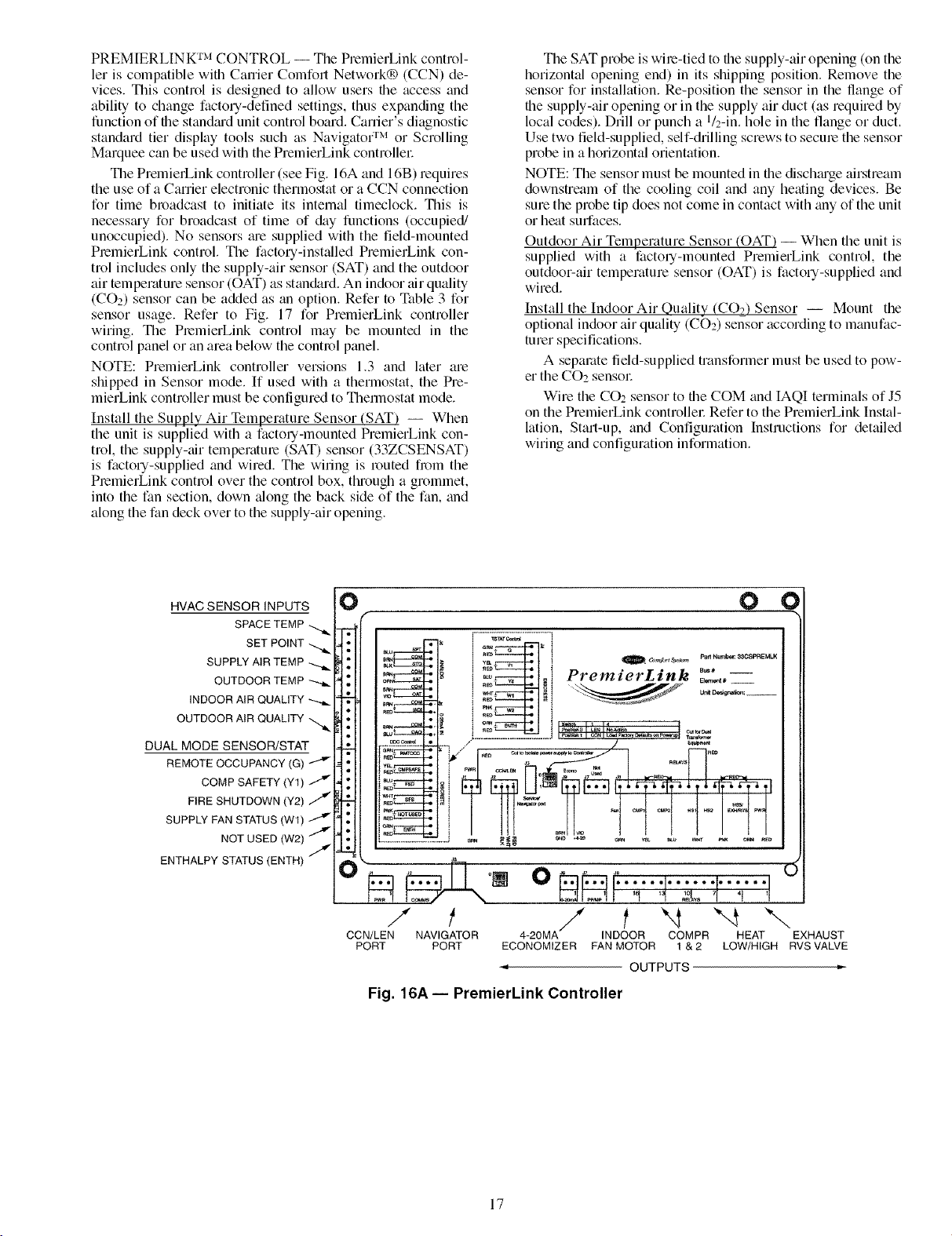
PREMIERLINK TM CONTROL -- The PremierLink control-
let is compatible with Carrier Comfo]l Network® (CCN) de-
vices. This control is designed to allow users file access and
ability to change factory-defined settings, thus expanding the
function of file standm'd unit control board. Career's diagnostic
standard tier display tools such as Navigator TM or Scrolling
Marquee can be used wifll the PremierLink controlle]:
The PremielLink controller (see Fig. 16A and 16B) requires
the use of a Carrier electronic thermostat or a CCN connection
for time broadcast to initiate its internal timeclock. This is
necessmy for broadcast of time of &ty functions (occupied/
unoccupied). No sensors me supplied with the field-mounted
PremierLink control. The factory-installed PremierLink con-
trol includes only the supply-air sensor (SAT) and the outdoor
air temperature sensor ((-)AT) as stan&trd. An indoor air quality
(CO2) sensor can be added as tin option. Refer to Table 3 for
sensor usage. Refer to Fig. 17 for PremierLink controller
wiring. The PmmierLink control may be mounted in file
control panel or an area below the control panel.
NOTE: PmmierLink controller versions 1.3 and later am
shipped in Sensor mode. If used with a fllermostat, the Pre-
mierLink controller must be configured to Themiostat mode.
Install the Supply Air Temperature Sensor (SAT) -- When
the unit is supplied with a factory-mounted PremierLink con-
trol, the supply-air temperature (SAT) sensor (33ZCSENSAT)
is factory-supplied and wimdi The wiring is routed from the
PmmierLink control over the control box, through a grommet,
into the fan section, down _flong the back side of the fan, and
along the fan deck over to the supply-air opening.
The SAT probe is wire-tied to the supply-air opening (on the
horizontal opening end) in its shipping position. Remove the
sensor for installation. Re-position the sensor in the flange of
the supply-air opening or in the supply air duct (as required by
local codes). Drill or punch a l/2-in, hole in the flange or duct.
Use two field-supplied, self-drilling screws to secure the sensor
probe in a horizontal orientation.
NOTE: The sensor must be mounted in the dischmge airstream
downstream of the cooling coil and any heating devices. Be
sure the probe tip does not come in contact with tiny of the unit
or heat surfaces.
Outdoor Air Temperature Sensor (OAT) -- When the unit is
supplied with a factoq-mounted PremierLink control, the
outdoor-air temperature sensor (OAT) is factory-supplied and
wired.
Install the Indoor Air Quality (COp) Sensor -- Mount the
optional indoor air quality (CO2) sensor according to manufac-
turer specifications.
A separate field-supplied transformer must be used to pow-
er the CO2 sensor
Wire the CO2 sensor to the COM and IAQI terminals of J5
on the PremierLink controflel: Refer to the PremierLink Instal-
lation, Start-up, and Configuration Instructions for detailed
wiring and configuration information.
HVAC SENSOR INPUTS O
SPACETEMP _ h'_
SET POINT _ El"]
SUPPLYAIR TEMP _ _i]
OUTDOOR TEMP _ ]lil
INDOOR AIR QUALITY _ LT_
OUTDOOR AIRQUALITY _ _!1
DUAL MODE SENSOR/STAT ]+_,11
REMOTEOCCUPANCY (G) "_v H " I
COMP SAFETY (Y1) ""'_ H ; I
FIRE SHUTDOWN (Y2) _ r_
suPPLY FAN STATUS(Wl) ""_ H i ]
ENTHALPY STATUS(ENTH) "_]_ _" _
NOTUSED (W2) ""_ Iq • I
/
CCN/LEN
PORT
OUTPUTS
Fig. 16A -- PremierLink Controller
17
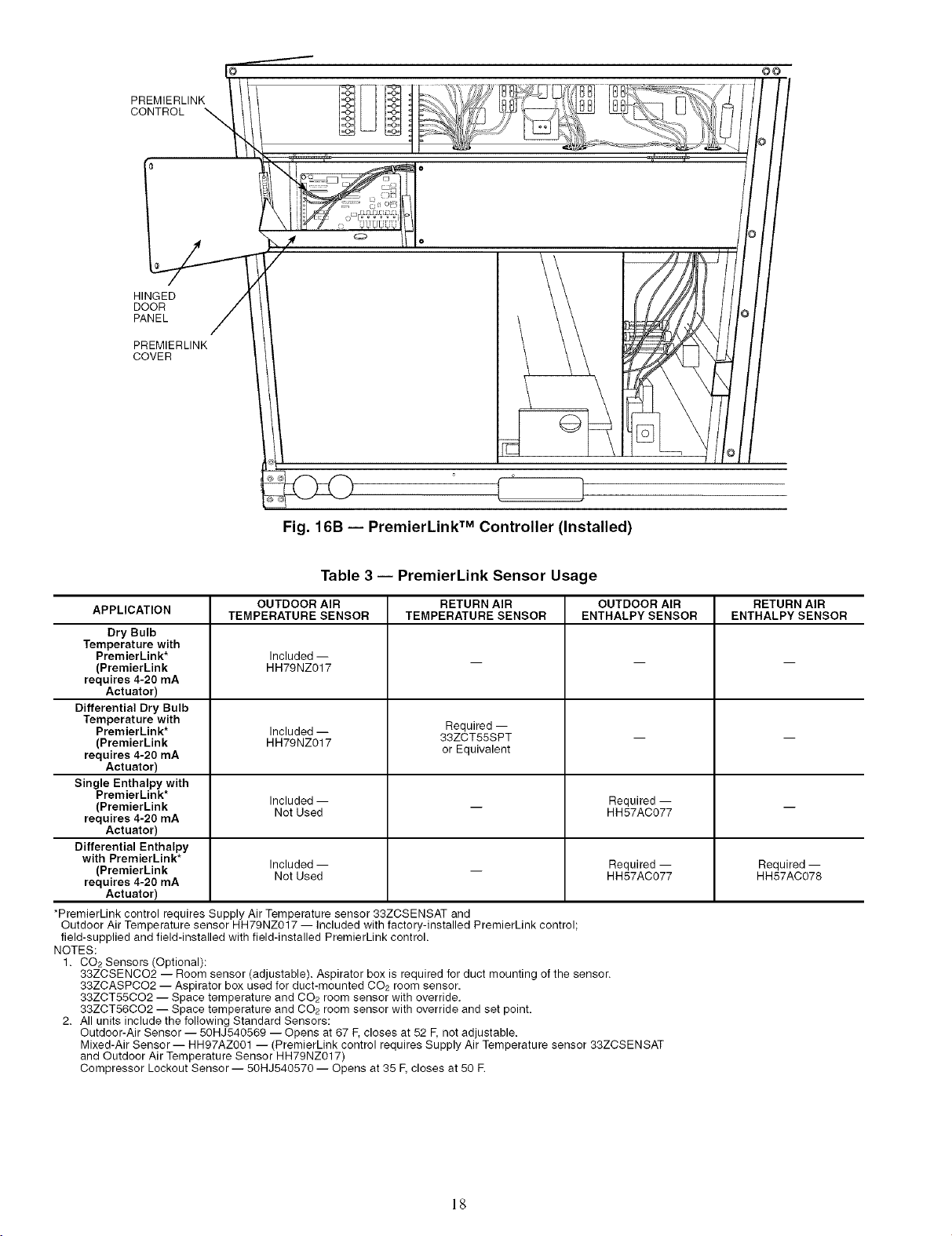
PREMIERLINK
CONTROL
HINGED
DOOR
PANEL
PREMIERLINK
COVER
©©
J
Fig. 16B -- PremierLink TM Controller (Installed)
Table 3 -- PremierLink Sensor Usage
APPLICATION TEMPERATURE SENSOR TEMPERATURE SENSOR ENTHALPY SENSOR ENTHALPY SENSOR
Dry Bulb
Temperature with
PremierLink* Included --
(PremierLink HH79NZ017
requires 4-20 mA
Actuator)
Differential Dry Bulb
Temperature with
PremierLink* Included -- Required --
(PremierLink HH79NZ017 33ZCT55SPT -- --
requires 4-20 mA or Equivalent
Actuator)
Single Enthalpy with
PremierLink*
(PremierLink Included -- __ Required -- _
requires 4-20 mA
Actuator)
Differential Enthalpy
with PremierLink*
(PremierLink Included -- __ Required -- Required --
requires 4-20 mA
Actuator)
*PremierLink control requires Supply Air Temperature sensor 33ZCSENSAT and
Outdoor Air Temperature sensor HH79NZ017 -- included with factory-installed PremierLink control;
field-supplied and field-installed with field-installed PremierLink control.
NOTES:
1. CO2 Sensors (Optional):
33ZCSENCO2 -- Room sensor (adjustable). Aspirator box is required for duct mounting of the sensor.
33ZCASPCO2 -- Aspirator box used for duct-mounted CO2 room sensor.
33ZCT55CO2 -- Space temperature and CO2 room sensor with override.
33ZCT56CO2 -- Space temperature and CO2 room sensor with override and set point.
2. All units include the following Standard Sensors:
Outdoor-Air Sensor -- 50HJ540569 -- Opens at 67 F, closes at 52 F,not adjustable.
Mixed-Air Sensor -- HH97AZ001 -- (PremierLink control requires Supply Air Temperature sensor 33ZCSENSAT
and Outdoor Air Temperature Sensor HH79NZ017)
Compressor Lockout Sensor -- 50HJ540570 -- Opens at 35 E closes at 50 R
OUTDOOR AIR RETURN AIR OUTDOOR AIR RETURN AIR
Not Used HH57AC077
Not Used HH57AC077 HH57AC078
18
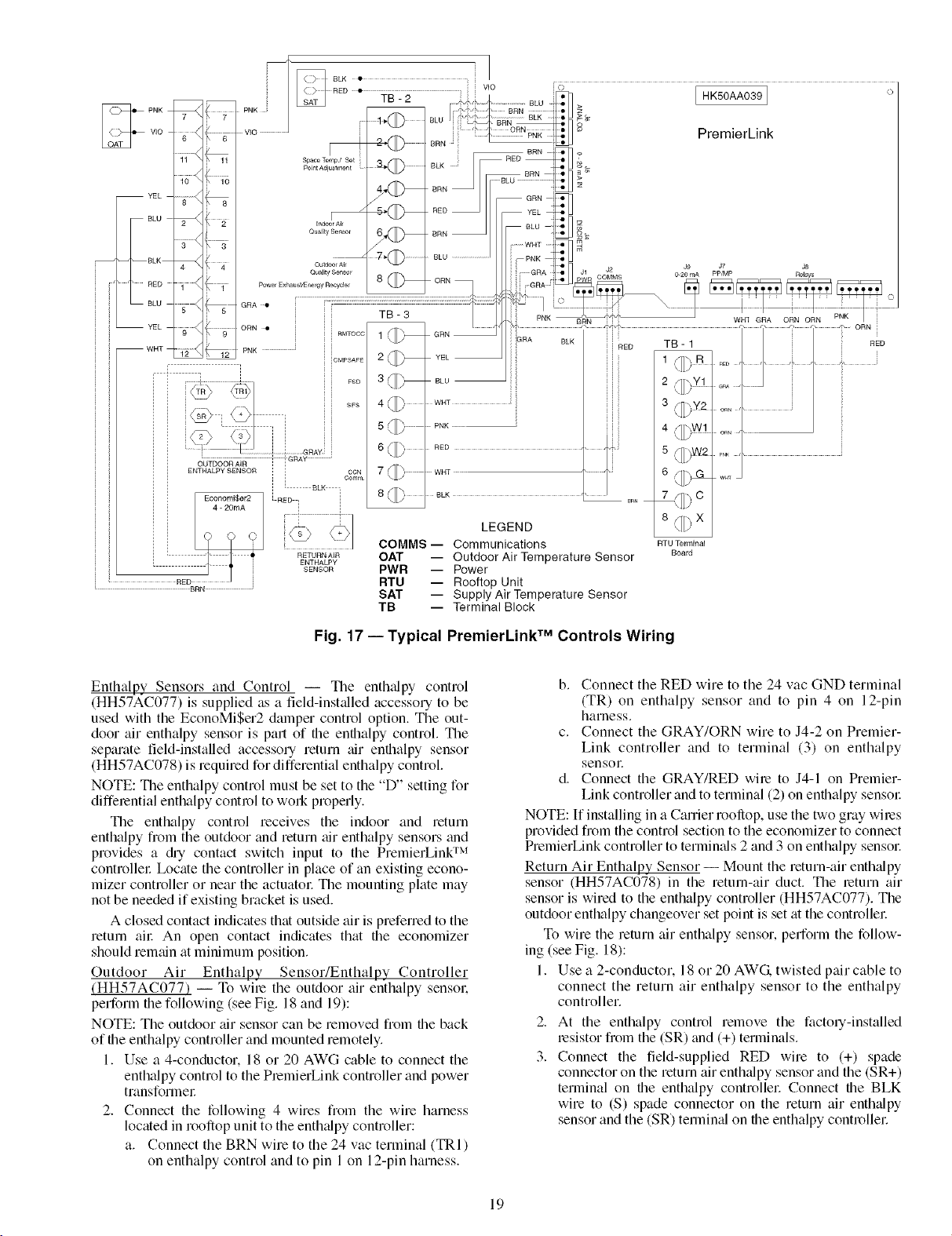
PNK
VIO
.....................................................................BRN...................................
SAT -- Supply Air Temperature Sensor
TB -- Terminal Block
Fig. 17 -- Typical PremierLink TM Controls Wiring
Enthalpy Sensors and Control i The enthalpy control
(HH57AC077) is supplied as a t]eld-inst_dled accessory to be
used with the EconoMi$er2 damper control option. The out-
door air enthalpy sensor is pall of die enthalpy control. The
separate field-installed accessory return tdr enthalpy sensor
(HH57AC078) is required for differential enthalpy control.
NOTE: The enthalpy control must be set to the "D" setting for
diffelential enthalpy control to won properly.
The enthalpy control receives the indoor and return
enthalpy from the outdoor and return air enthalpy sensors and
provides a &y contact switch input to the PremierLinld '_'_
controllel: Ix_cate the controller in place of an existing econo-
mizer controller or near the actuator The mounting plate may
not be needed if existing bracket is used.
A closed contact indicates that outside air is preferred to the
return all: An open contact indicates that die economizer
should remain at minimum position.
Outdoor Air Enthalpy Sensor/Enthalpy Controller
(HH57AC077) i To wile the outdoor air enthalpy sensoit
perform the following (see Fig. 18 and 19):
NOTE: The outdoor air sensor can be removed from die back
of die enthalpy controller and mounted remotely.
1. Use a 4-conductor. 18 or 20 AWG cable to connect the
enthalpy control to the PlemierLink controller and power
transforme_:
2. Connect the following 4 wires from the wire harness
located in rooftop unit to the enth_dpy controller:
a. Connect the BRN wire to the 24 vac terminal (TRI)
on enthalpy control and to pin 1 on 12-pin harness.
b. Connect the RED wire to the 24 vac GND terminal
(TR) on enthalpy sensor and to pin 4 on 12-pin
harness.
c. Connect the GRAY/ORN wire to J4-2 on Premier-
Link controller and to terminal (3) on enthalpy
sensoE
d. Connect the GRAY/RED wire to J4-1 on Premier-
Link controller and to terminal (2) on enthalpy sensol:
NOTE: If installing in a Carrier roollop, use the two gray wires
provided from the control section to the economizer to connect
PremierLink controller to termimds 2 and 3 on enthalpy sensol:
Return Air Enthalpy Sensor i Mount the return-air enth_dpy
sensor (HH57AC078) in the return-air duct. The return air
sensor is wired to the enthalpy controller (HH57AC077). The
outdoor enthalpy changeover set point is set at the controllel:
To wire the return air enthalpy sensor, perform the follow-
ing (see Fig. 18):
1. Use a 2-conductor, 18 or 20 AWC_ twisted pair cable to
connect the return air enthalpy sensor to the enthalpy
controller.
2. At the enthalpy control remove the factory-installed
resistor from the (SR) and (+) terminals.
3. Connect the field-supplied RED wire to (+) spade
connector on the return air enth_dpy sensor and the (SR+)
terminal on die enthalpy controller Connect the BLK
wire to (S) spade connector on the return air enth_dpy
sensor and the (SR) termimd on die enthalpy controlle_:
19