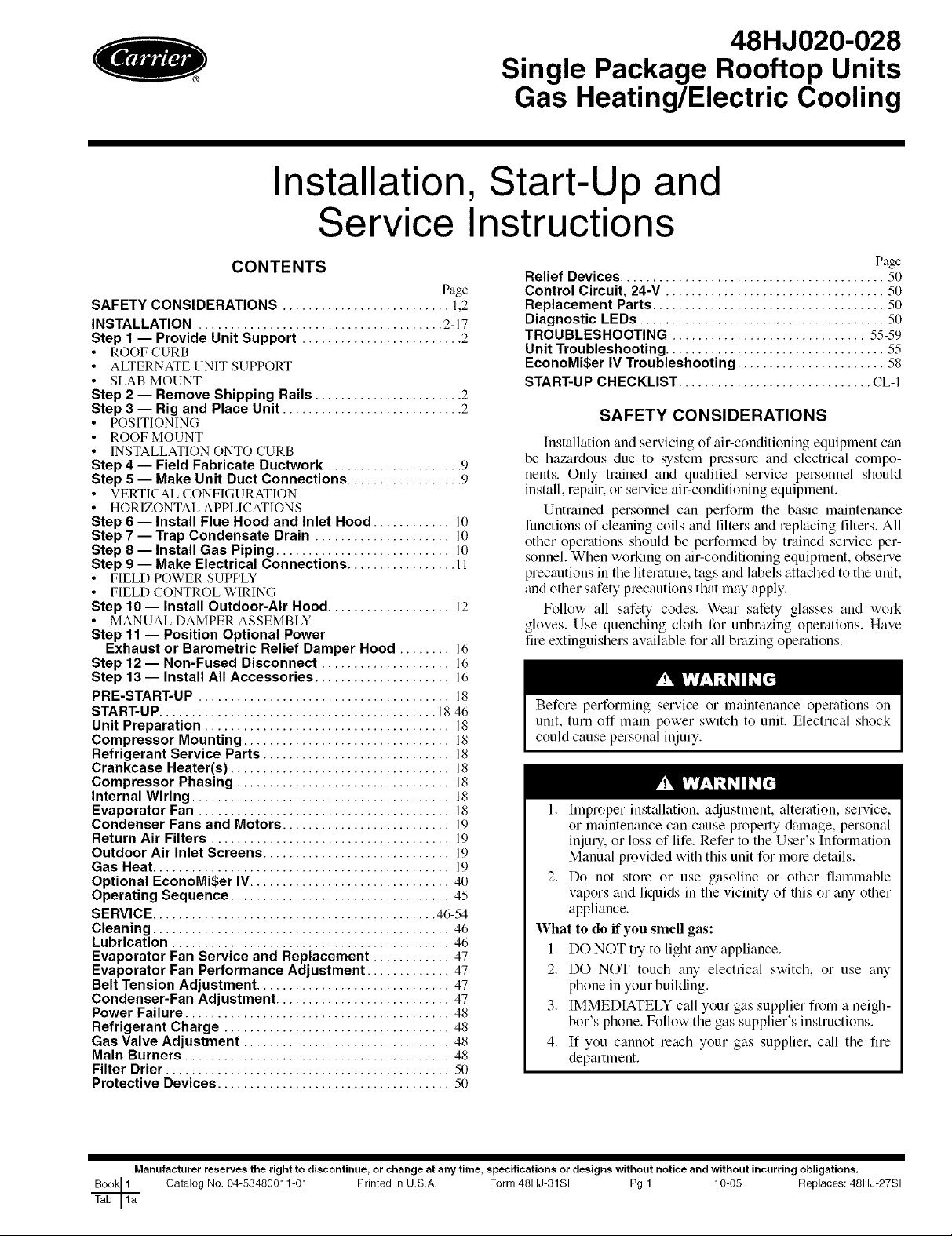
Single Package Rooftop Units
Gas Heating/Electric Cooling
Installation, Start-Up and
Service Instructions
48HJ020-028
CONTENTS
Page
SAFETY CONSIDERATIONS .......................... 1,2
INSTALLATION ...................................... 2-17
Step 1 -- Provide Unit Support ......................... 2
• ROOF CURB
• ALTERNATE UNIT SUPPORT
• SLAB MOUNT
Step 2 -- Remove Shipping Rails ....................... 2
Step 3 -- Rig and Place Unit ............................ 2
• POSITIONING
• ROOF MOUNT
• INSTALLATION ONTO CURB
Step 4 -- Field Fabricate Ductwork ..................... 9
Step 5 -- Make Unit Duct Connections .................. 9
• VERTICAL CONFIGURATION
• HORIZONTAL APPLICATIONS
Step 6 -- Install Flue Hood and Inlet Hood ............ 10
Step 7 -- Trap Condensate Drain ..................... 10
Step 8 -- Install Gas Piping ........................... 10
Step 9 -- Make Electrical Connections ................. 11
• FIELD POWER SUPPLY
• FIELD CONTROL WIRING
Step 10 -- Install Outdoor-Air Hood ................... 12
• MANUAL DAMPER ASSEMBLY
Step 11 -- Position Optional Power
Exhaust or Barometric Relief Damper Hood ........ 16
Step 12 -- Non-Fused Disconnect .................... 16
Step 13 -- Install All Accessories ..................... 16
PRE-START-UP ....................................... 18
START-UP ........................................... !8-46
Unit Preparation ...................................... 18
Compressor Mounting ................................ 18
Refrigerant Service Parts ............................. !8
Crankcase Heater(s) .................................. !8
Compressor Phasing ................................. 18
Internal Wiring ........................................ 18
Evaporator Fan ....................................... 18
Condenser Fans and Motors .......................... 19
Return Air Filters ..................................... 19
Outdoor Air Inlet Screens ............................. 19
Gas Heat .............................................. 19
Optional EconoMi$er IV............................... 40
Operating Sequence .................................. 45
SERVICE ............................................ 4(,-54
Cleaning .............................................. 46
Lubrication ........................................... 46
Evaporator Fan Service and Replacement ............ 47
Evaporator Fan Performance Adjustment ............. 47
Belt Tension Adjustment .............................. 47
Condenser-Fan Adjustment ........................... 47
Power Failure ......................................... 48
Refrigerant Charge ................................... 48
Gas Valve Adjustment ................................ 48
Main Burners ......................................... 48
Filter Drier ............................................ 50
Protective Devices .................................... 50
Relief Devices ......................................... 50
Page
Control Circuit, 24-V .................................. 50
Replacement Parts .................................... 50
Diagnostic LEDs ...................................... 50
TROUBLESHOOTING .............................. 55-59
Unit Troubleshooting .................................. 55
EconoMi$er IV Troubleshooting ....................... 58
START-UP CHECKLIST .............................. CL-!
SAFETY CONSIDERATIONS
Installation and servicing of air-conditioning equipment can
be hazardous due to system plessure and electrical compo-
nents. Only trained and qualified service personnel should
install, repair, or service air-conditioning equipment.
Untrained personnel can perform the basic maintenance
functions of cleaning coils and filters and replacing filters. All
other operations should be performed by trained service per-
sonnel. When working on _fir-conditioning equipment, observe
precautions in the literature, tags and labels attached to the unit,
and other safety precautions that may apply.
Follow all safety codes. Wear safety glasses and work
gloves. Use quenching cloth for unbrazing operations. Have
fire extinguishers available for fill brazing operations.
Before perforlning service or maintenance operations on
unit, turn off main power switch to unit. Electrical shock
could cause personal injury.
1. Improper inst_fllation, adjustment, alteration, service,
or maintenance can cause property &Lmage, personal
injury, or loss of life. Refer to the User's Information
Manual provided with this unit for mole details.
2. Do not stole or use gasoline or other flammable
vapors and liquids in the vicinity of this or any other
appliance.
What to do if you smell gas:
1. DO NOT try to light any appliance.
2. DO NOT touch any electrical switch, or use any
phone in your building.
3. IMMEDIATELY call your gas supplier from a neigh-
bor's phone. Follow the gas supplier's instructions.
4. If you cannot reach your gas supplier, c_dl the fire
department.
Manufacturer reserves the right to discontinue, or change at any time, specifications or designs without notice and without incurring obligations.
Bookl 1 Catalog No. 04-53480011-01 Printed in U.S,A. Form 48HJ-31SI Pg 1 10-05 Replaces: 48HJ-27SI
Tab Ila
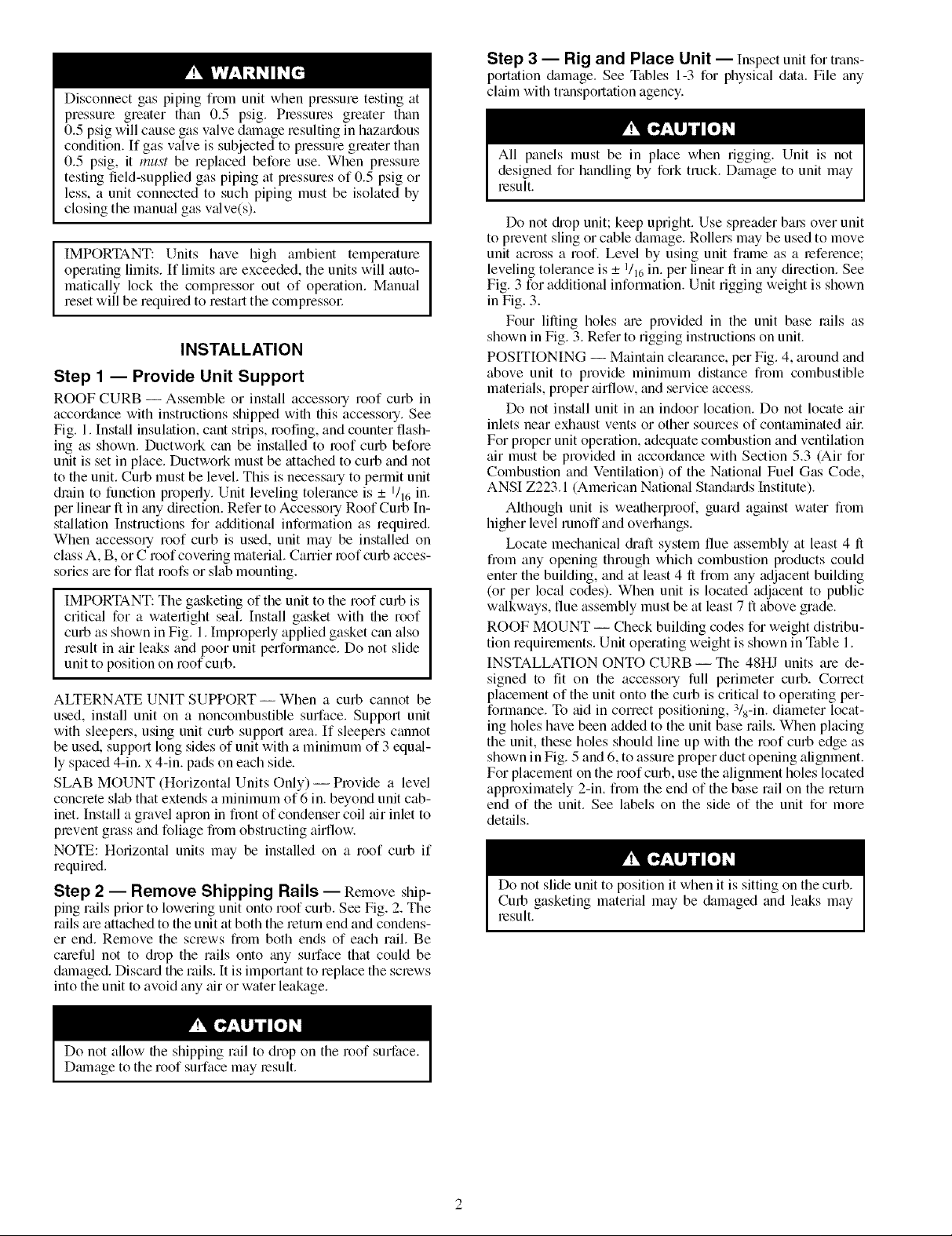
Disconnect gas piping from unit when pressure testing at
pressure greater than 0.5 psig. Plessmes greater than
0.5 psig will cause gas valve damage resulting in hazardous
condition. If gas valve is subjected to pressure greater than
0.5 psig, it must be replaced before use. When pressme
testing field-supplied gas piping at pressures of 0.5 psig or
less, a unit connected to such piping must be isolated by
closing the manual gas v_dve(s).
IMPORTANT: Units have high ambient temperature]
operating limits. If limits are exceeded, the units will auto-
matically lock the compressor out of operation. Manual
reset will be required to restart the compressol:
INSTALLATION
Step 1 -- Provide Unit Support
ROOF CURB -- Assemble or install accessory roof curb in
accor&mce with instructions shipped with this accessory. See
Fig. 1. Install insulation, cant strips, roofing, and counter flash-
ing as shown. Ductwork can be installed to roof curb before
unit is set in place. Ductwork must be attached to curb and not
to the unit. Curb must be level. This is necessary to permit unit
drain to function properly. Unit leveling tolerance is _+J/l(_in.
per line,u ft in any direction. Refer to Accessory Roof Curb In-
st',_lation Instructions for additional information as required.
When accessory roof curb is used, unit may be installed on
class A, B, or C roof covering materi_d. Carrier roof curb acces-
sories are for flat roofs or slab mounting.
IMPORTANT: The gasketing of the unit to the roof curb is
critical for a watertight seal. Install gasket with the roof
curb as shown in Fig. 1. Improperly applied gasket can also
result in air leaks and poor unit performance. Do not slide
unit to position on roof curb.
ALTERNATE UNIT SUPPORT- When a curb cannot be
used, install unit on a noncombustible surface. Support unit
with sleepeLs, using unit curb support area. If sleepers cannot
be used, support long sides of unit with a minimum of 3 eqmfl-
ly spaced 4-in. x 4-in. pads on each side.
SLAB MOUNT (Horizontal Units Only) -- Provide a level
concrete slab that extends a minimum of 6 in. beyond unit cab-
inet. Install a gravel apron in fi_mt of condenser coil air inlet to
plevent gross and foliage from obstructing airflow.
NOTE: Horizontal units may be installed on a roof curb if
required.
Step 2 -- Remove Shipping Rails -- Remove ship-
ping rails prior to lowering unit onto roof curb. See Fig. 2. The
rails are attached to the unit at both the return end and condens-
er end. Remove the sclews from both ends of each rail. Be
c_u'eful not to drop the rails onto gray surface that could be
dmnaged. Disc_ud the rails. It is important to replace the sclews
into the unit to avoid any air or water leakage.
I
Step 3 -- Rig and Place Unit -- Inspect unit for trans-
portation &image. See Tables 1-3 for physical data. File any
claim with transportation agency.
All panels must be in place when rigging. Unit is not
designed for handling by fork truck. Dmnage to unit may
result.
Do not diop unit; keep upright. Use spreader baLs over unit
to prevent sling or cable damage. Rollers may be used to move
unit across a roof. Level by using unit fralne as a leference;
leveling tolerance is _+1/1(_in. per linetu ft in any direction. See
Fig. 3 for additional information. Unit rigging weight is shown
in Fig. 3.
Four lifting holes tue provided in the unit base mils as
shown in Fig. 3. Refer to rigging instructions on unit.
POSITIONING -- Maintain clearance, per Fig. 4, around and
above unit to provide minimum distance from combustible
materials, proper airflow, and service access.
Do not inst_dl unit in an indoor location. Do not locate air
inlets near exhaust vents or other sources of contaminated ai_:
For proper unit operation, adequate combustion and ventilation
air must be provided in accordance with Section 5.3 (Air for
Combustion and Ventilation) of the Natiomd Fuel Gas Code,
ANSI Z223.1 (American National Standmds Institute).
Although unit is weatherproof, guard against water from
higher level runoff and overhangs.
Ix)cate mechanical diaft system flue assembly at least 4 ft
from any opening through which combustion products could
enter the building, and at least 4 ft from any adjacent building
(or per local codes). When unit is located adjacent to public
w_dkways, flue assembly must be at least 7 ft above grade.
ROOF MOUNT -- Check building codes for weight distribu-
tion requirements. Unit operating weight is shown in Table 1.
INSTALLATION ONTO CURB- The 48HJ units are de-
signed to fit on the accessory full perimeter curb. Correct
placement of the unit onto the curb is critical to operating per-
formance. To aid in correct positioning, 3/s-in. diameter locat-
ing holes have been added to the unit base rails. When placing
the unit, these holes should line up with the roof curb edge as
shown in Fig. 5 and 6, to assure proper duct opening alignment.
For placement on the roof curb, use the alignment holes located
approximately 2-in. fiom the end of the base rail on the return
end of the unit. See labels on the side of the unit for more
details.
Do not slide unit to position it when it is sitting on the curb.
Curb gasketing material may be &_maged and leaks may
result.
Do not allow the shipping rail to drop on the roof surface.
Dmnage to the roof surface may result.
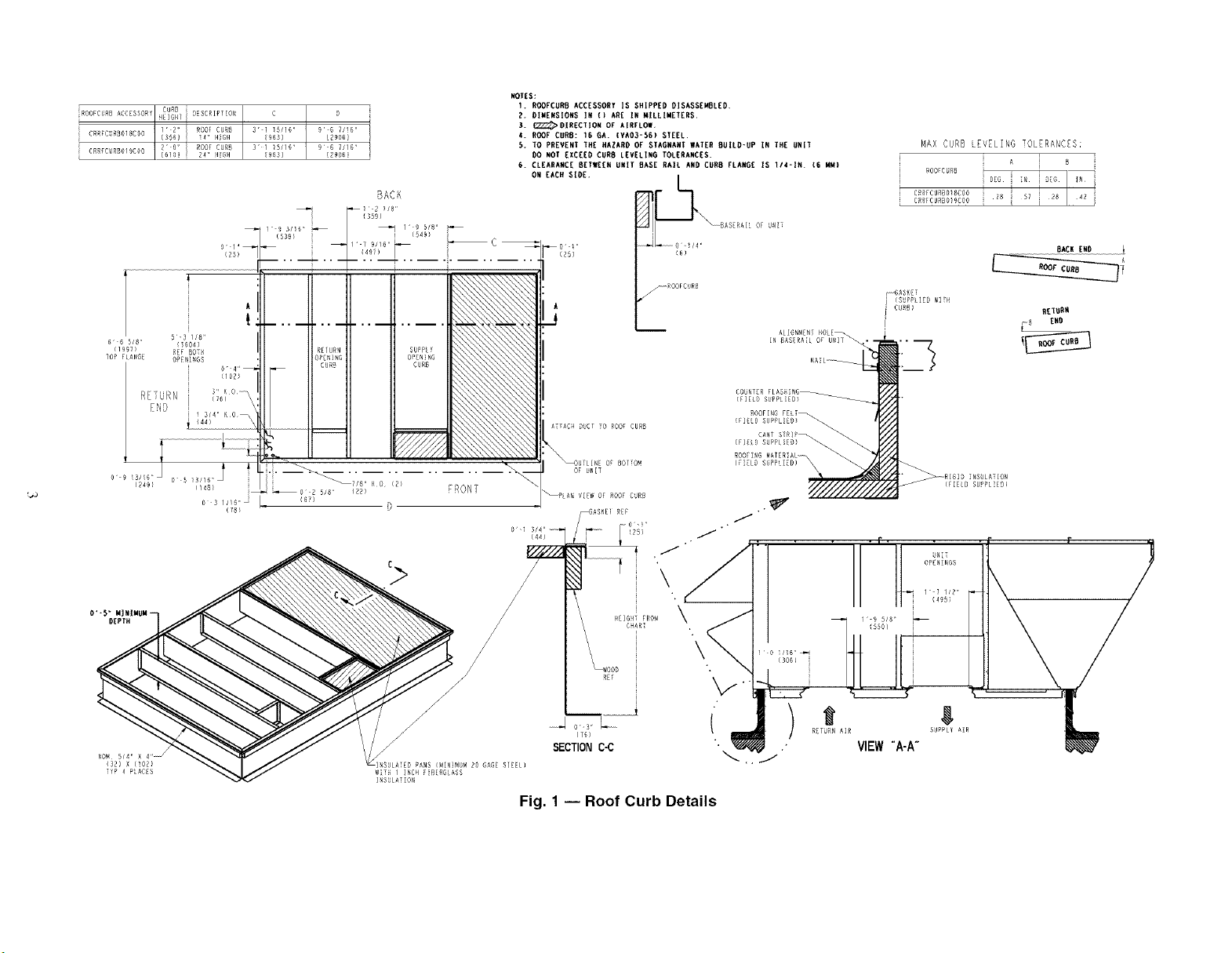
RONT
ATTACfl DUCT TO ROOF CURB
_OU}L/_I OF BOTiOM
8F UNIT
_PLAN VI{_ OF ROOF CUR8
\
MAX CURB LEVELING TOLERANCES:
R08FCDR5 DES _ 88 [N
CRIFCUIBO_BCOQ ii iCRRFCURS0! 9C05 28 57 28 _
,--GASKET
i {SSPPL][D _l_t
i _URB_
]
_NSULATION
(FIELD SUPPL_EO!
UNiT
OPENINGS
A B
RE_URN
m5 [1tl
BACKEN_
FROM
CHARi
(T£)
SECTIONCiC
Fig. 1 -- Roof Curb Details
SUPPLY AIR
VIEW"A-A"
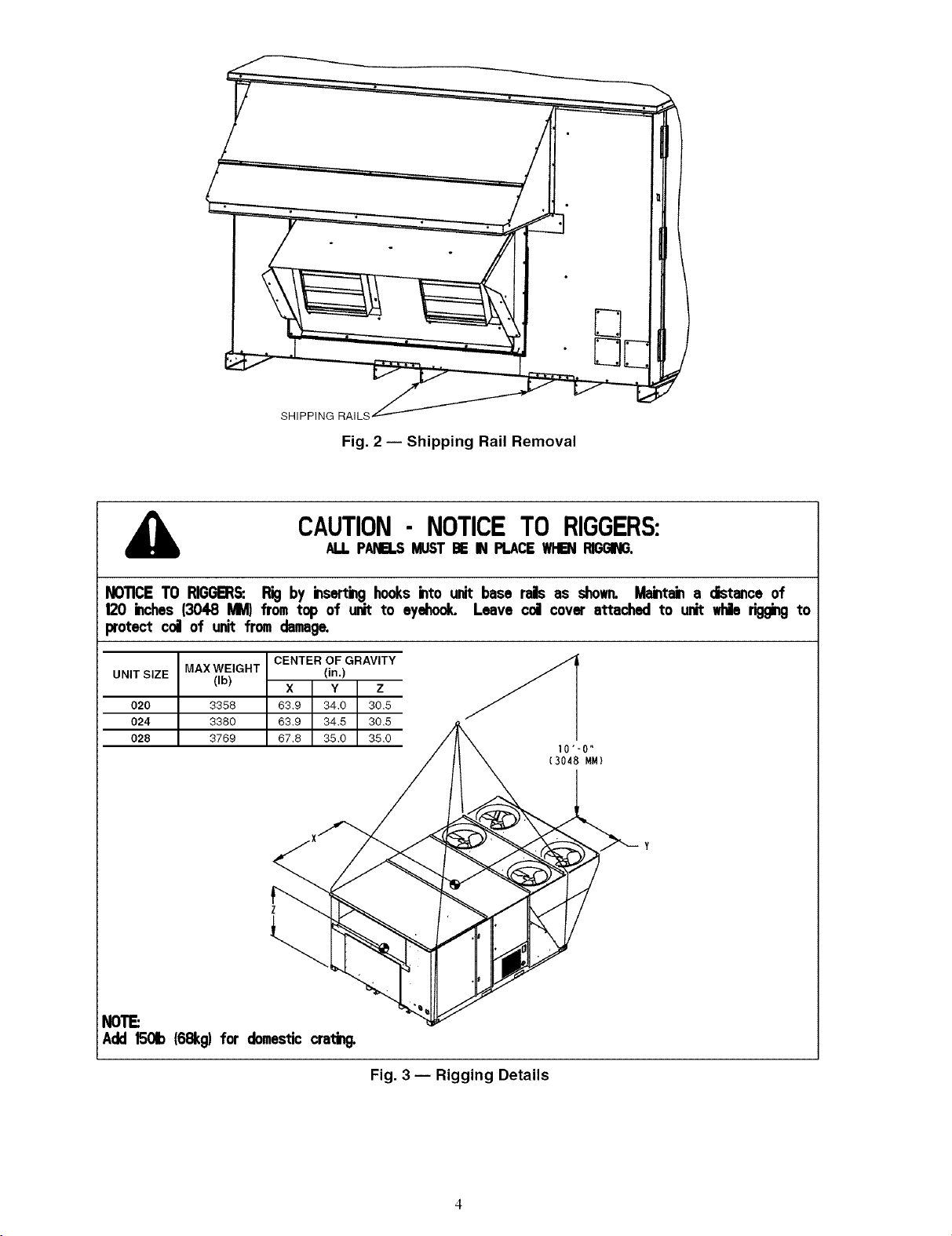
Fig. 2 -- Shipping Rail Removal
CAUTION NOTICETO RIGGERS:
ALL PAI_,.S MUSTBEIN PLACE_ RIGGING.
NOTICETO RIGC-B_& Rig by insertinghooksinto unit base rais as shown. Maintaina cistance of
120 inches (3048 MM) from top of unit to eyehook. Leave co] cover attached to unit _ riggbg to
protect coil of unit from damage.
UNIT SIZE MAXWEIGHT
020 3358
024 3380
028 3769
(Ib)
CENTER OF GRAVITY
(in.)
X Y Z
63.9 34.0 30.5
63.9 34.5 30.5
67.8 35.0 35.0
NOTE:
Add 1501b(68kg) for domesticoratb9.
10"-0"
(3048 MM)
Fig. 3-- Rigging Details
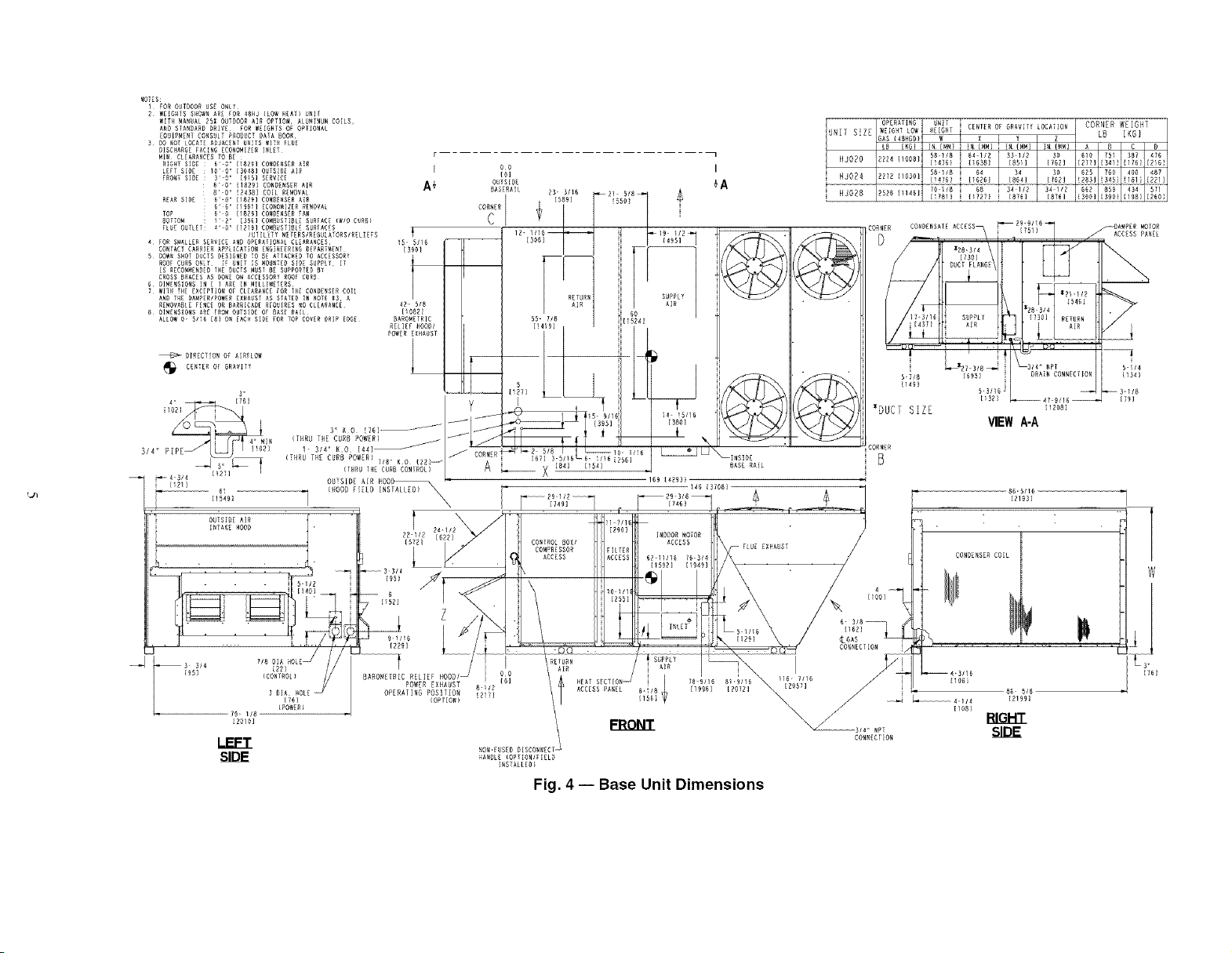
F ..........................
I
,_A
UNIT SiZE
HJO20
HJ024
HJO88
OPZRATIRG N_T CORNER WEIGHT
WEIGHT LOW HEI6_T CENT[R OF GRAVITY LOCATION L_ [NGI
j x i _ z
58 118 54 112 33 1/2 30 610 751 387 4762224 11008} [1476} (1538} [851] 1752] 1277] [_41 [1761 (2!6
[476 116251 I ] i ] 283] 345 1181i 221
2526 [t14_] 70 /8 58 34112 34-1/Z 652 859 434 571
[7811 (t727] [876] [B76] i300] 390 [1981 [2601
_OIRECTiON OF AIRFLOW
CENTER OF GRAVITY
[121]
[15491
OUfSI_E AIR " "
I_TA_E aOOD *
= _ _ = = , _
_ _;5_/° _ol
79- 1/8
12010]
(PO_ER)
LEFT
S_E
O0
_OR-FUSED DISCO_R[C__
_AROLE (OPTIONIFIZLO
IRSTALLEO)
Fig. 4 -- Base Unit Dimensions
_t9 1/2
SUPPLY
EXHAUST
149_
'DUCT SIZE
[)321 1791
11208]
VIEWA-A
86-5/1G
[21931
CONDENSERCOIL
!1
8_ 5/8
[2199]
RIGHT
SIDE
/" ACCESS PANEL
/
W
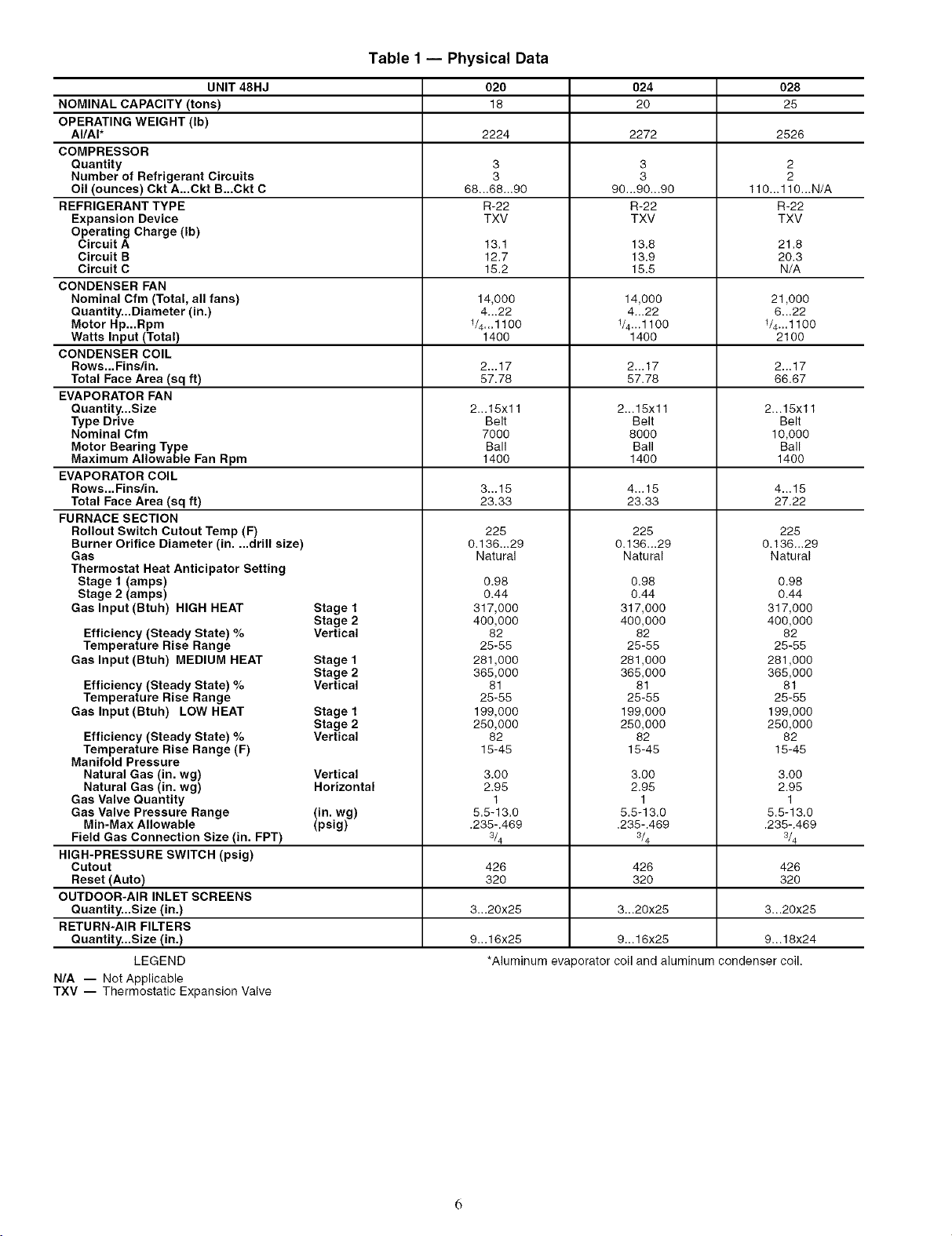
UNIT 48HJ
NOMINAL CAPACITY (tons)
OPERATING WEIGHT (Ib)
AI/AI*
COMPRESSOR
Quantity
Number of Refrigerant Circuits
Oil (ounces) Ckt A...Ckt B...Ckt C
REFRIGERANT TYPE
Expansion Device
Operating Charge (Ib)
Circuit A
Circuit B
Circuit C
CONDENSER FAN
Nominal Cfm (Total, all fans)
Quantity...Diameter (in.)
Motor Hp...Rpm
Watts Input (Total)
CONDENSER COIL
Rows... Fins/in.
Total Face Area (sq ft)
EVAPORATOR FAN
Quantity...Size
Type Drive
Nominal Cfm
Motor Bearing Type
Maximum Allowable Fan Rpm
EVAPORATOR COIL
Rows... Fins/in.
Total Face Area (sq ft)
FURNACE SECTION
Rollout Switch Cutout Temp (F)
Burner Orifice Diameter (in....drill size)
Gas
Thermostat Heat Anticipator Setting
Stage 1 (amps)
Stage 2 (amps)
Gas Input (Btuh) HIGH HEAT
Efficiency (Steady State) %
Temperature Rise Range
Gas Input (Btuh) MEDIUM HEAT
Efficiency (Steady State) %
Temperature Rise Range
Gas Input (Btuh) LOW HEAT
Efficiency (Steady State) %
Temperature Rise Range (F)
Manifold Pressure
Natural Gas (in. wg)
Natural Gas (in. wg)
Gas Valve Quantity
Gas Valve Pressure Range
Min-Max Allowable
Field Gas Connection Size (in. FPT)
HIGH-PRESSURE SWITCH (psig)
Cutout
Reset (Auto)
OUTDOOR-AIR INLET SCREENS
Quantity...Size (in.)
RETURN-AIR FILTERS
Quantity...Size (in.)
LEGEND
N/A -- Not Applicable
TXV -- Thermostatic Expansion Valve
Stage 1
Stage 2
Vertical
Stage 1
Stage 2
Vertical
Stage 1
Stage 2
Vertical
Vertical
Horizontal
(in. wg)
(psig)
Table 1-- Physical Data
020 024 028
18 20 25
2224 2272 2526
3 3 2
3 3 2
68...68...90 90...90...90 110... 110...N/A
R-22 R-22 R-22
TXV TXV TXV
13.1 13.8 21.8
12.7 13.9 20.3
15.2 15.5 N/A
14,000 14,000 21,OOO
4...22 4...22 6...22
1/4...110O 1/4...11O0 1/4._1100
1400 1400 2100
2...17 2...17 2...17
57.78 57.78 66.67
2...15xl 1 2...15xl 1 2...15xl 1
Belt Belt Belt
7000 8000 10,000
Ball Ball Ball
1400 1400 1400
3...15 4...15 4...15
23.33 23.33 27.22
225
0.136...29
Natural
0.98
0.44
317,000
400,000
82
25-55
281,000
365,000
81
25-55
199,000
250,000
82
15-45
3.00
2.95
1
5.5-13.0
.235-.469
s/4
426 426 426
320 320 320
3...20x25 3...20x25 3...20x25
9...16x25 9...16x25 9...18x24
*Aluminum ew _oratorcoiland aluminum condensercoil.
225
0.136...29
Natural
0.98
0.44
317,000
400,000
82
25-55
281,000
365,000
81
25-55
199,000
250,000
82
15-45
3.00
2.95
1
5.5-13.0
.235-.469
s/4
225
0.136._29
Natural
0.98
0.44
317,000
400,000
82
25-55
281,000
365,000
81
25-55
199,000
250,000
82
15-45
3.00
2.95
1
5.5-13.0
.235-.469
sh
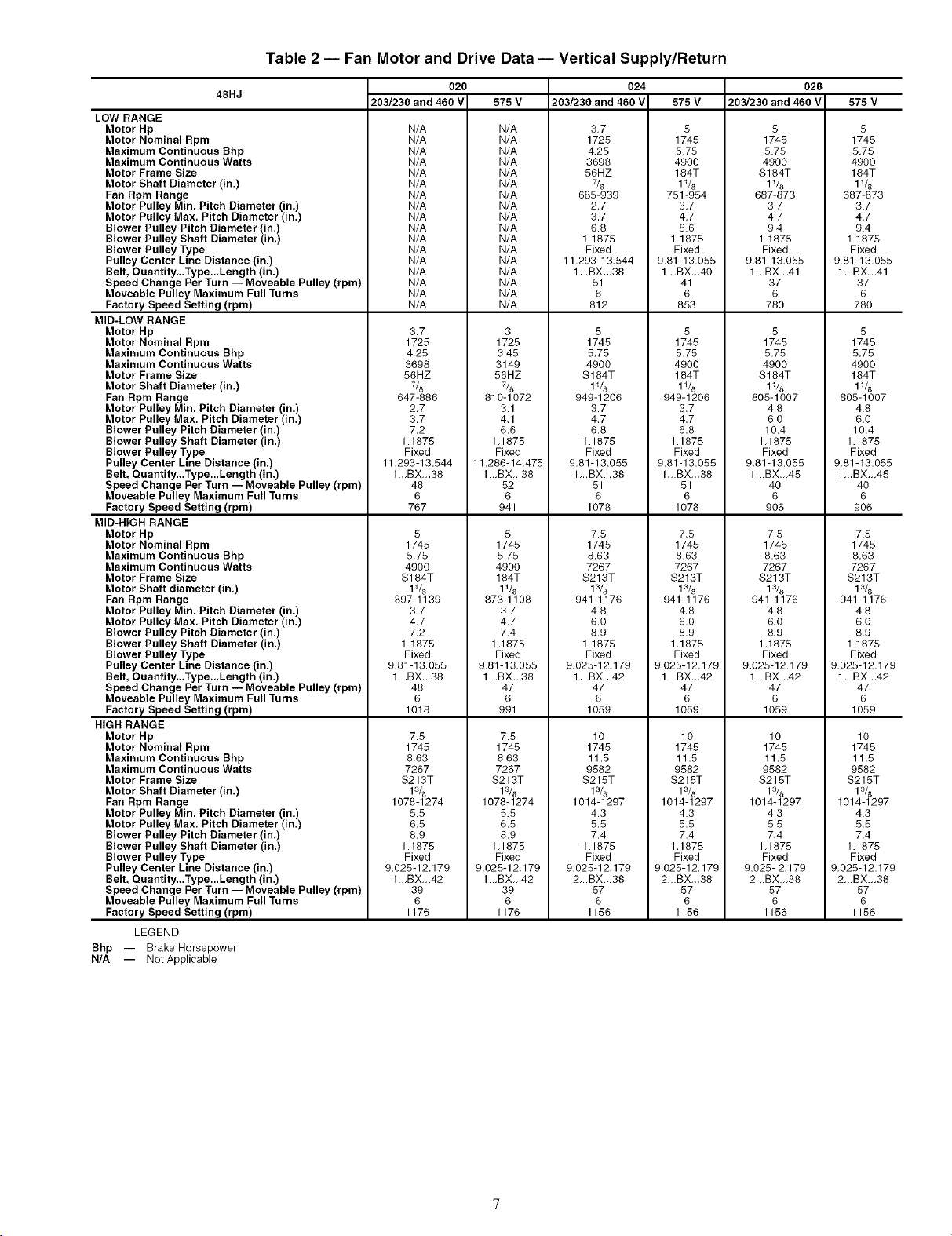
Table 2 -- Fan Motor and Drive Data -- Vertical Supply/Return
48HJ
LOW RANGE
Motor Hp
Motor Nominal Rpm
Maximum Continuous Bhp
Maximum Continuous Watts
Motor Frame Size
Motor Shaft Diameter (in.)
Fan Rpm Range
Motor Pulley Min, Pitch Diameter (in.)
Motor Pulley Max, Pitch Diameter (in,)
Blower Pulley Pitch Diameter (in.)
Blower Pulley Shaft Diameter (in.)
Blower Pulley Type
Pulley Center Line Distance (in.)
Belt, Quantity,.,Type..,Length (in.)
Speed Change Per Turn -- Moveable Pulley (rpm)
Moveable Pulley Maximum Full Turns
Factory Speed Setting (rpm)
MID-LOW RANGE
Motor Hp
Motor Nominal Rpm
Maximum Continuous Bhp
Maximum Continuous Watts
Motor Frame Size
Motor Shaft Diameter (in.)
Fan Rpm Range
Motor Pulley Min, Pitch Diameter (in.)
Motor Pulley Max, Pitch Diameter (in,)
Blower Pulley Pitch Diameter (in.)
Blower Pulley Shaft Diameter (in.)
Blower Pulley Type
Pulley Center Line Distance (in.)
Belt, Quantity,.,Type..,Length (in.)
Speed Change Per Turn -- Moveable Pulley (rpm)
Moveable Pulley Maximum Full Turns
Factory Speed Setting (rpm)
MID-HIGH RANGE
Motor Hp
Motor Nominal Rpm
Maximum Continuous Bhp
Maximum Continuous Watts
Motor Frame Size
Motor Shaft diameter (in.)
Fan Rpm Range
Motor Pulley Min, Pitch Diameter (in.)
Motor Pulley Max. Pitch Diameter (in,)
Blower Pulley Pitch Diameter (in.)
Blower Pulley Shaft Diameter (in.)
Blower Pulley Type
Pulley Center Line Distance (in.)
Belt, Quantity...Type..,Length (in.)
Speed Change Per Turn -- Moveable Pulley (rpm)
Moveable Pulley Maximum Full Turns
Factory Speed Setting (rpm)
HIGH RANGE
Motor Hp
Motor Nominal Rpm
Maximum Continuous Bhp
Maximum Continuous Watts
Motor Frame Size
Motor Shaft Diameter (in.)
Fan Rpm Range
Motor Pulley Min. Pitch Diameter (in.)
Motor Pulley Max. Pitch Diameter (in,)
Blower Pulley Pitch Diameter (in.)
Blower Pulley Shaft Diameter (in.)
Blower Pulley Type
Pulley Center Line Distance (in.)
Belt, Quantity...Type..,Length (in.)
Speed Change Per Turn -- Moveable Pulley (rpm)
Moveable Pulley Maximum Full Turns
Factory Speed Setting (rpm)
LEGEND
Bhp -- Brake Horsepower
N/A -- Not Applicable
020
203/230 and 460 V
N/A
N/A
N/A
N/A
N/A
N/A
N/A
N/A
N/A
N/A
N/A
N/A
N/A
N/A
N/A
N/A
N/A
3.7
1725
4.25
3698
56HZ
7&
647-886
2.7
3.7
7.2
1.1875
Fixed
11.293-13.544
1._BX_.38
48
6
767
5
1745
5.75
4900
$184T
l_&
897-1139
3.7
4.7
7.2
1.1875
Fixed
9,81-13.055
1..,BX-.38
48
6
1018
7.5
1745
8.63
7267
$213T
13&
1078-1274
5.5
6.5
8.9
1.1875
Fixed
9.025-12.179
1..,BX_.42
39
6
1176
575 V
N/A
N/A
N/A
N/A
N/A
N/A
N/A
N/A
N/A
N/A
N/A
N/A
N/A
N/A
N/A
N/A
N/A
3
1725
3.45
3149
56HZ
7&
810-1072
3.1
4.1
6.6
1,1875
Fixed
11.286-14.475
1..,BX,..38
52
6
941
5
1745
5.75
4900
184T
11/8
873-1108
3.7
4.7
7.4
1,1875
Fixed
9.81-13.055
1..,BX_.38
47
6
991
7.5
1745
8.63
7267
$213T
13&
1078-1274
5.5
6.5
8.9
1.1875
Fixed
9.025-12.179
1...BX_.42
39
6
1176
024
203/230 and 460 V
3.7
1725
4.25
3698
56HZ
7/8
685-939
2.7
3.7
6.8
1.1875
Fixed
11.293-13.544
1,..BX_.38
51
6
812
5
1745
5,75
4900
$184T
11&
949-1206
3.7
4.7
6.8
1.1875
Fixed
9.81-13.055
1_.BX...38
51
6
1078
7.5
1745
8.63
7267
$213T
13/8
941-1176
4.8
6.0
8.9
1.1875
Fixed
9.025-12,179
1,.BX.-42
47
6
1059
10
1745
11.5
9582
$215T
1%
1014-1297
4.3
5.5
7.4
1.1875
Fixed
9.025-12.179
2_.BX._38
57
6
1156
575 V
5
1745
5.75
4900
184T
751-954
3,7
4.7
8.6
1.1875
Fixed
9.81-13.055
1...BX_.40
41
6
853
5
1745
5.75
4900
184T
l_&
949-1206
3.7
4.7
6.8
1.1875
Fixed
9.81-13.055
1..BX._38
51
6
1078
7.5
1745
8.63
7267
$213T
13/8
941-1176
4.8
6.0
8.9
1.1875
Fixed
9.025-12,179
1...BX-,42
47
6
1059
lO
1745
11.5
9582
$215T
1%
1014-1297
4.3
5.5
7.4
1.1875
Fixed
9.025-12.179
2..BX_,38
57
6
1156
O28
203/230 and 460 V
5
1745
5.75
4900
$184T
1%
687-873
3.7
4.7
9.4
1.1875
Fixed
9.81-13.055
1..BX._41
37
6
78O
5
1745
5.75
4900
$184T
l_&
805-1007
4.8
6.0
10.4
1.1875
Fixed
9.81-13.055
1_.BX_,45
4O
6
906
7.5
1745
8.63
7267
$213T
1%
941-1176
4.8
6.0
8.9
1.1875
Fixed
9.025-12.179
1.,BX.-42
47
6
1059
10
1745
11.5
9582
$215T
1%
1014-1297
4.3
5.5
7.4
1.1875
Fixed
9.025- 2.179
2._BX._38
57
6
1156
575 V
5
1745
5.75
4900
184T
11&
687-873
3.7
4.7
9.4
1.1875
Fixed
9.81-13.055
1_.BX_.41
37
6
78O
5
1745
5.75
4900
184T
l_&
805-1007
4.8
6.0
10.4
1.1875
Fixed
9.81-13.055
1_.BX._45
4O
6
906
7.5
1745
8.63
7267
S213T
13&
941-1176
4.8
6.0
8.9
1.1875
Fixed
9.025-12.179
1_.BX._42
47
6
1059
lO
1745
11.5
9582
S215T
13&
1014-1297
4.3
5.5
7.4
1.1875
Fixed
9.025-12.179
2_.BX._38
57
6
1156
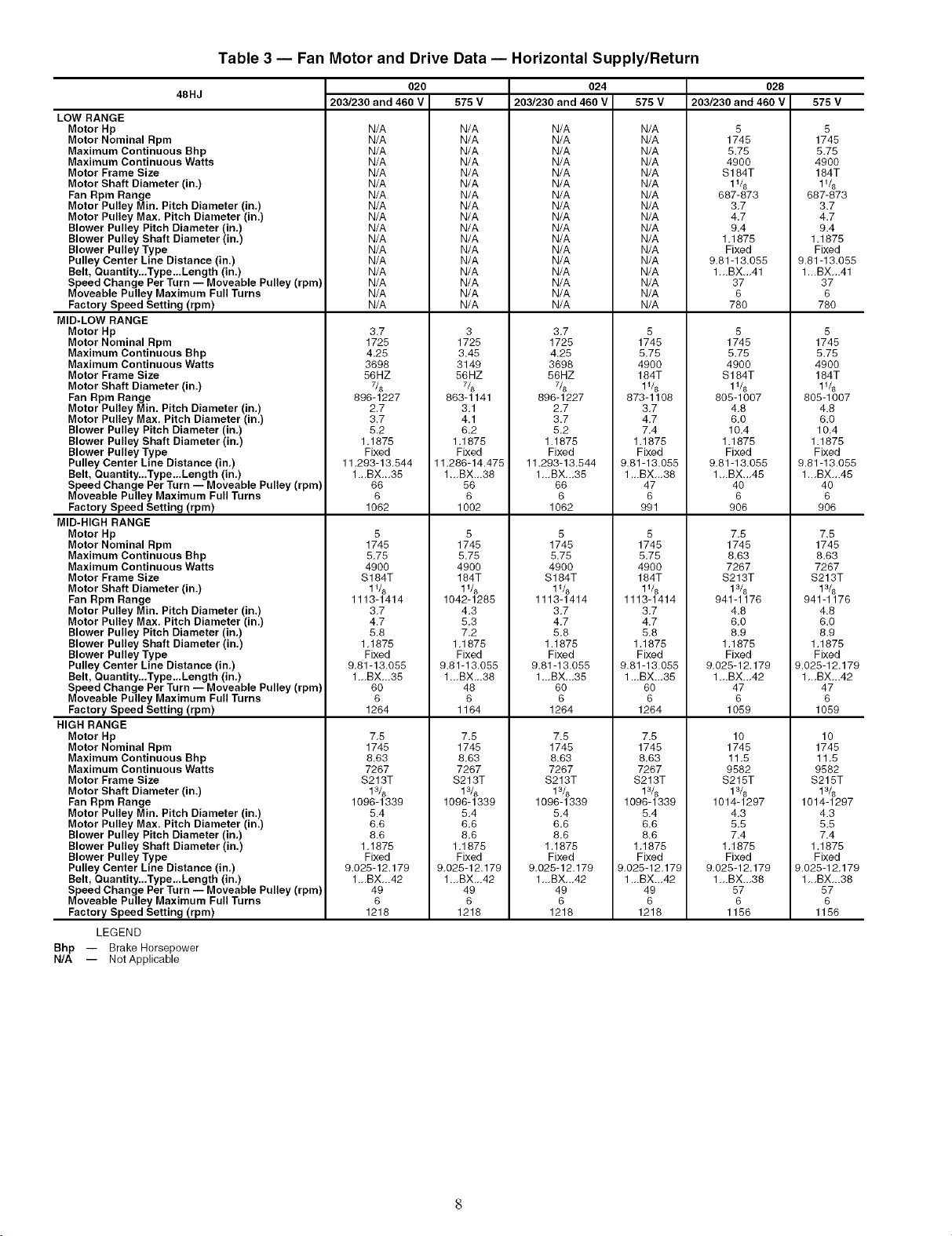
Table 3 -- Fan Motor and Drive Data -- Horizontal Supply/Return
48HJ
LOW RANGE
Motor Hp
Motor Nominal Rpm
Maximum Continuous Bhp
Maximum Continuous Watts
Motor Frame Size
Motor Shaft Diameter (in.)
Fan Rpm Range
Motor Pulley Min. Pitch Diameter (in,)
Motor Pulley Max, Pitch Diameter (in.)
Blower Pulley Pitch Diameter (in.)
Blower Pulley Shaft Diameter (in,)
Blower Pulley Type
Pulley Center Line Distance (in.)
Belt, Quantity..,Type...Length (in,)
Speed Change Per Turn -- Moveable Pulley (rpm)
Moveable Pulley Maximum Full Turns
Factory Speed Setting (rpm)
MID-LOW RANGE
Motor Hp
Motor Nominal Rpm
Maximum Continuous Bhp
Maximum Continuous Watts
Motor Frame Size
Motor Shaft Diameter (in.)
Fan Rpm Range
Motor Pulley Min. Pitch Diameter (in,)
Motor Pulley Max, Pitch Diameter (in.)
Blower Pulley Pitch Diameter (in,)
Blower Pulley Shaft Diameter (in,)
Blower Pulley Type
Pulley Center Line Distance (in.)
Belt, Quantity..,Type...Length (in,)
Speed Change Per Turn -- Moveable Pulley (rpm)
Moveable Pulley Maximum Full Turns
Factory Speed Setting (rpm)
MID-HIGH RANGE
Motor Hp
Motor Nominal Rpm
Maximum Continuous Bhp
Maximum Continuous Watts
Motor Frame Size
Motor Shaft Diameter (in.)
Fan Rpm Range
Motor Pulley Min. Pitch Diameter (in,)
Motor Pulley Max. Pitch Diameter (in.)
Blower Pulley Pitch Diameter (in.)
Blower Pulley Shaft Diameter (in,)
Blower Pulley Type
Pulley Center Line Distance (in,)
Belt, Quantity.,.Type.,.Length (in,)
Speed Change Per Turn -- Moveable Pulley (rpm)
Moveable Pulley Maximum Full Turns
Factory Speed Setting (rpm)
HIGH RANGE
Motor Hp
Motor Nominal Rpm
Maximum Continuous Bhp
Maximum Continuous Watts
Motor Frame Size
Motor Shaft Diameter (in.)
Fan Rpm Range
Motor Pulley Min. Pitch Diameter (in.)
Motor Pulley Max. Pitch Diameter (in.)
Blower Pulley Pitch Diameter (in.)
Blower Pulley Shaft Diameter (in,)
Blower Pulley Type
Pulley Center Line Distance (in,)
Belt, Quantity.,.Type.,.Length (in,)
Speed Change Per Turn -- Moveable Pulley (rpm)
Moveable Pulley Maximum Full Turns
Factory Speed Setting (rpm)
LEGEND
Bhp -- Brake Horsepower
N/A -- Not Applicable
020
203/230 and 460 V
N/A
N/A
N/A
N/A
N/A
N/A
N/A
N/A
N/A
N/A
N/A
N/A
N/A
N/A
N/A
N/A
N/A
3.7
1725
4.25
3698
56HZ
7/s
896-1227
2.7
3.7
5.2
1.1875
Fixed
11.293-13.544
1..,BX,..35
66
6
1062
5
1745
5,75
4900
$184T
l_&
1113-1414
3.7
4.7
5.8
1.1875
Fixed
9.81-13.055
1 .-BX,..35
60
6
1264
7.5
1745
8.63
7267
$213T
13&
1096-1339
5.4
6,6
8.6
1.1875
Fixed
9.025-12.179
1._BX...42
49
6
1218
575 V
N/A
N/A
N/A
N/A
N/A
N/A
N/A
N/A
N/A
N/A
N/A
N/A
N/A
N/A
N/A
N/A
N/A
3
1725
3.45
3149
56HZ
7&
863-1141
3.1
4.1
6.2
1.1875
Fixed
11.286-14.475
1._BX...38
56
6
1002
5
1745
5.75
4900
184T
1042-1285
4.3
5.3
7.2
1.1875
Fixed
9.81-13.055
1..,BX.,.38
48
6
1164
7.5
1745
8.63
7267
$213T
13/8
1096-1339
5.4
6.6
8.6
1.1875
Fixed
9.025-12.179
1._BX_.42
49
6
1218
024
203/230 and 460 V
N/A
N/A
N/A
N/A
N/A
N/A
N/A
N/A
N/A
N/A
N/A
N/A
N/A
N/A
N/A
N/A
N/A
3.7
1725
4.25
3698
56HZ
7&
896-1227
2.7
3.7
5.2
1.1875
Fixed
11.293-13.544
1._BX..,35
66
6
1062
5
1745
5.75
4900
$184T
11&
1113-1414
3.7
4.7
5.8
1.1875
Fixed
9,81-13.055
1,.,BX,.,35
60
6
1264
7.5
1745
8.63
7267
S213T
1%
1096-1339
5.4
6.6
8.6
1.1875
Fixed
9.025-12.179
1,.,BX_,42
49
6
1218
575 V
N/A
N/A
N/A
N/A
N/A
N/A
N/A
N/A
N/A
N/A
N/A
N/A
N/A
N/A
N/A
N/A
N/A
5
1745
5.75
4900
184T
11/s
873-1108
3.7
4.7
7.4
1.1875
Fixed
9.81-13.055
1.,.BX,_38
47
6
991
5
1745
5.75
4900
184T
11/s
1113-1414
3.7
4.7
5.8
1.1875
Fixed
9.81-13.055
1.,.BX..,35
60
6
1264
7.5
1745
8.63
7267
S213T
13/s
1096-1339
5.4
6.6
8.6
1.1875
Fixed
9.025-12.179
1.,.BX..,42
49
6
1218
028
203/230 and 460 V
5
1745
5.75
4900
S184T
11/8
687-873
3,7
4,7
9,4
1.1875
Fixed
9.81-13.055
1-BX.-41
37
6
78O
5
1745
5.75
4900
S184T
11/8
605-1007
4.6
6.0
10,4
1.1875
Fixed
9.81-13.055
1.,.BX..,45
4O
6
906
7.5
1745
8.63
7267
S213T
13/8
941-1176
4.8
6,0
8,9
1.1875
Fixed
9.025-12.179
1-.BX...42
47
6
1059
lO
1745
11,5
9582
S215T
13/s
1014-1297
4,3
5,5
7,4
1.1875
Fixed
9,025-12,179
1.,BX..,38
57
6
1156
575 V
5
1745
5.75
4900
184T
l_&
687-873
3.7
4.7
9.4
1.1875
Fixed
9.81-13.055
1...BX_.41
37
6
78O
5
1745
5.75
4900
184T
l_&
805-1007
4.8
6.0
10.4
1.1875
Fixed
9.81-13.055
1..,BX,..45
4O
6
906
7.5
1745
8.63
7267
S213T
13&
941-1176
4.8
6.0
8.9
1.1875
Fixed
9.025-12.179
1,.,BX,..42
47
6
1059
lO
1745
11.5
9582
S215T
13&
1014-1297
4.3
5.5
7.4
1.1875
Fixed
9.025-12.179
1,.,BX,..38
57
6
1156
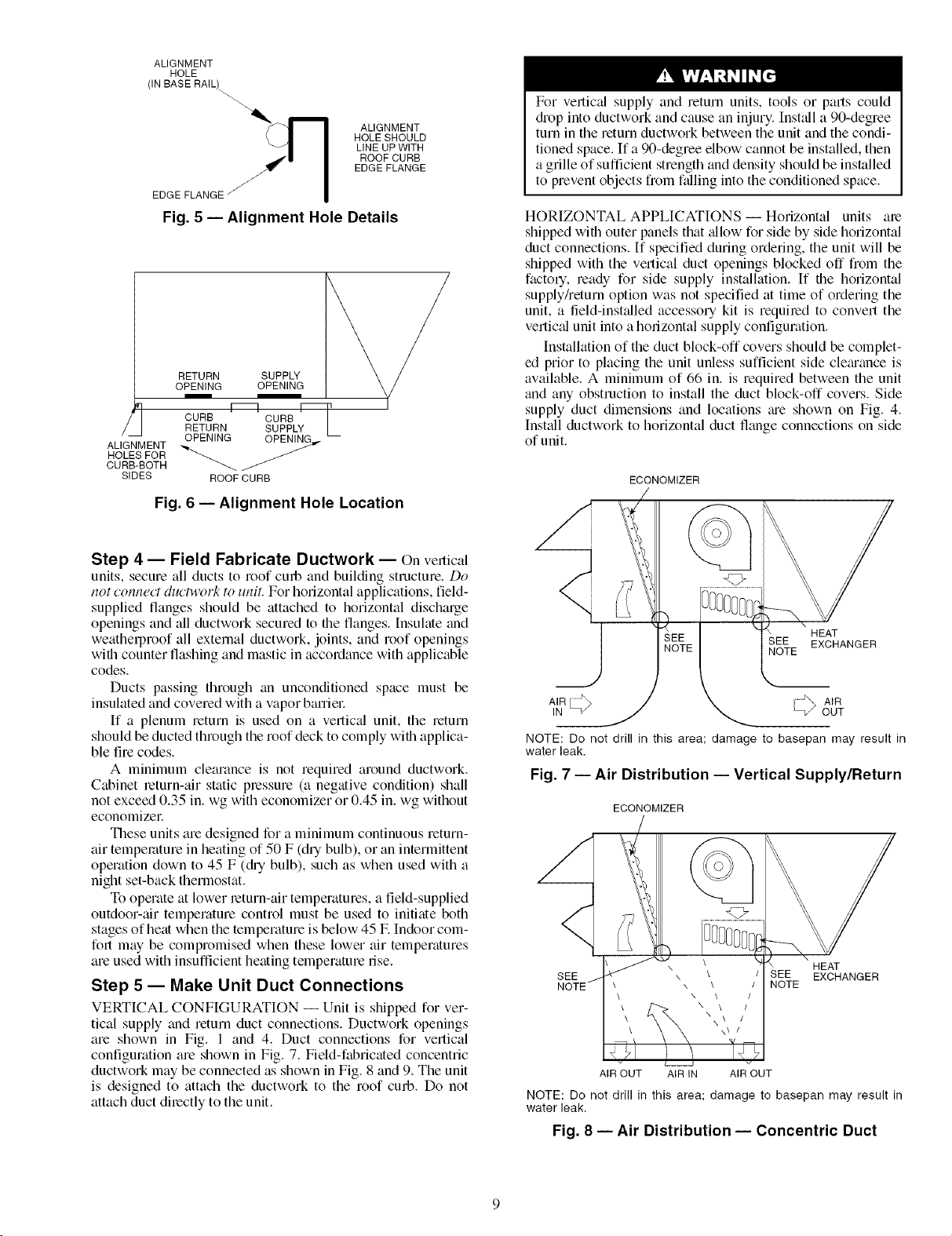
ALIGNMENT
HOLES FOR
CURB-BOTH
SIDES
ALIGNMENT
HOLE
(IN BASE RAIL)_
HOLE SHOULD
LINE UP WITH
ROOF CURB
_q ALIGNMENT
EDGE FLANGE
EDGE FLANGE
Fig. 5 -- Alignment Hole Details
RETURN SUPPLY I_/
OPENING OPENING
CURB CURB_F
RETURN SUPPLY L
OPENING OPENINg.
ROOF CURB
Fig. 6 -- Alignment Hole Location
For vertical supply and return units, tools or pmls could
diop into ductwork and cause an injury. [nst_dl a 90-degree
turn in the return ductwork between the unit and the condi-
tioned space. If a 90-degree elbow cannot be installed, then
a grille of sufficient strength and density should be installed
to prevent objects from f_dling into the conditioned space.
HORIZONTAL APPLICATIONS-- Horizontal units are
shipped with outer panels that allow for side by side horizontal
duct connections. If specified during ordering, the unit will be
shipped with the vertical duct openings blocked off from the
factory, ready for side supply installation. If the horizontal
supply#eturn option was not specified at time of ordering the
unit, a field-installed accessory kit is requiled to convert the
vertical unit into a horizontal supply configuration.
Installation of the duct block-off covers should be complet-
ed prior to placing the unit unless sufficient side cle_u'ance is
available. A minimum of 66 in. is required between the unit
and any obstruction to install the duct block-off covers. Side
supply duct dimensions and locations tue shown on Fig. 4.
Install ductwork to horizontal duct flange connections on side
of unit.
ECONOMIZER
Step 4 -- Field Fabricate Ductwork -- On vertical
units, secure all ducts to roof curb and building structure. Do
not connect ductwork to unit. For horizontal applications, field-
supplied flanges should be attached to horizontal discharge
openings and all ductwork secured to the flanges. Insulate and
weatherproof all external ductwork, joints, and roof openings
with counter flashing and mastic in accordance with applicable
codes.
Ducts passing through an unconditioned space must be
insulated and covered with a vapor barriel:
if a plenum return is used on a vertic_fl unit, the return
should be ducted through the roof deck to comply with applica-
ble fire codes.
A minimum clearance is not required around ductwork.
Cabinet leturn-air static plessure (a negative condition) shall
not exceed 0.35 in. wg with economizer or 0.45 in. wg without
economizel:
These units are designed for a minimum continuous return-
air temperature in heating of 50 F (dry bulb), or an intermittent
operation down to 45 F (di_ bulb), such as when used with a
night set-back thermostat.
To operate at lower return-air temperatures, a field-supplied
outdoor-air temperature control must be used to initiate both
stages of heat when the temperature is below 45 R Indoor com-
fort may be compromised when these lower air temperatures
are used with insufficient heating temperature rise.
Step 5 -- Make Unit Duct Connections
VERTICAL CONFIGURATION -- Unit is shipped for ver-
tical supply and return duct connections. Ductwork openings
are shown in Fig. 1 and 4. Duct connections for vertical
configuration are shown in Fig. 7. Field-fabricated concentric
ductwork may be connected as shown in Fig. 8 and 9. The unit
is designed to attach the ductwork to the roof curb. Do not
attach duct directly to the unit.
\ HEAT
SEE EXCHANGER
NOTE
@AIR
OUT
NOTE: Do not drill in this area; damage to basepan may result in
water leak,
Fig. 7 -- Air Distribution -- Vertical Supply/Return
ECONOMIZER
SEE
AIR OUT AIR IN AIR OUT
NOTE: Do not drill in this area; damage to basepan may result in
water leak.
SEE HEAT
EXCHANGER
NOTE
Fig. 8 -- Air Distribution -- Concentric Duct
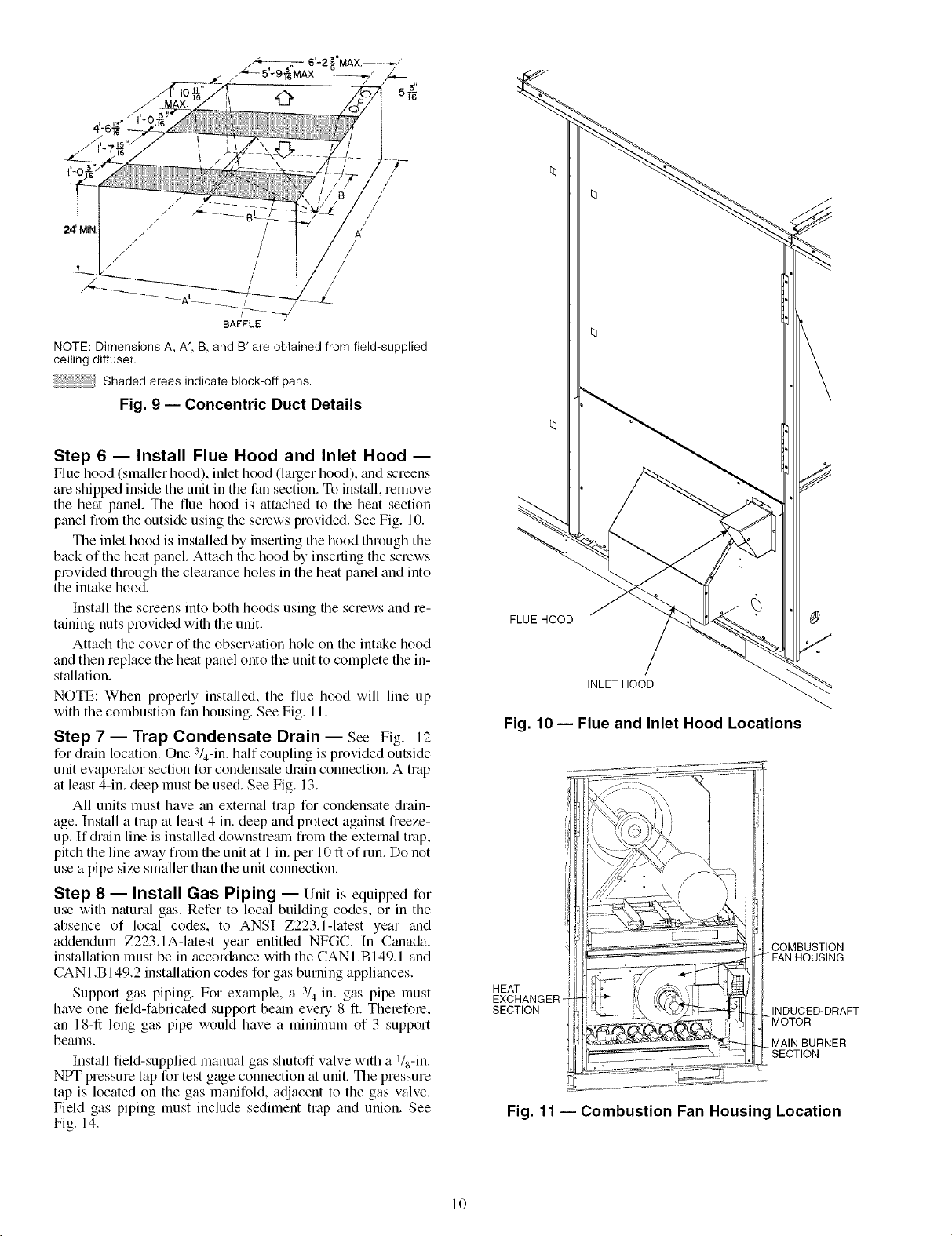
/
BAFFLE
NOTE: DimensionsA, A', B,and B' are obtained fromfield-supplied
ceiling diffuser.
;_ Shaded areas indicate block-offpans.
Fig. 9 -- Concentric Duct Details
Step 6 -- Install Flue Hood and Inlet Hood --
Flue hood (smaller hood), inlet hood (larger hood), and screens
are shipped inside the unit in the fan section. To install, remove
the heat panel. Tile flue hood is attached to the heat section
panel from the outside using tile sclews provided. See Fig. 10.
Tile inlet hood is installed by inselling the hood through the
back of the heat panel. Attach the hood by inserting the screws
provided through the clearance holes in the heat panel and into
the intake hood.
Install the screens into both hoods using file screws and re-
taining nuts provided with the unit.
Attach the cover of the observation hole on the intake hood
and then replace the heat panel onto the unit to complete the in-
stfdlation.
NOTE: When properly installed, the flue hood will line up
with the combustion fan housing. See Fig. 11.
Step 7 -- Trap Condensate Drain -- See Fig. 12
for drain location. One 3/4-in. half coupling is provided outside
unit evaporator section for condensate drain connection. A trap
fit least 4-in. deep must be used. See Fig. 13.
All units must have an external trap for condensate drain-
age. Install a trap fit least 4 in. deep and protect against freeze-
up. If drain line is installed downstremn from the external trap,
pitch the line away from the unit fit 1 in. per 10 11of run. Do not
use a pipe size smaller than the unit connection.
Step 8 -- Install Gas Piping -- Unit is equipped for
use with natural gas. Refer to local building codes, or in the
absence of local codes, to ANSI Z223.1-1atest year and
addendum Z223.1A-latest year entitled NFGC. [n Canada,
installation must be in accordance with the CANI .B149.1 and
CAN 1.B 149.2 installation codes for gas burning appliances.
Support gas piping. For exanlple, a 3/4-in. gas pipe must
have one field-fabricated support bemn every 8 11.Thelefore,
an 18-1l long gas pipe would have a minimum of 3 support
beams.
Instfdl field-supplied manual gas shutoff valve with a 1/8-in.
NPT pressure tap for test gage connection fit unit. Tile pressure
tap is located on the gas manifold, adjacent to the gas valve.
Field gas piping must include sediment trap and union. See
Fig. 14.
FLUE HOOD
INLET HOOD
Fig. 10 -- Flue and Inlet Hood Locations
COMBUSTION
FAN HOUSING
HEAT
EXCHANGER-
SECTION
INDUCED-DRAFT
-MOTOR
MAIN BURNER
-SECTION
Fig. 11 -- Combustion Fan Housing Location
10
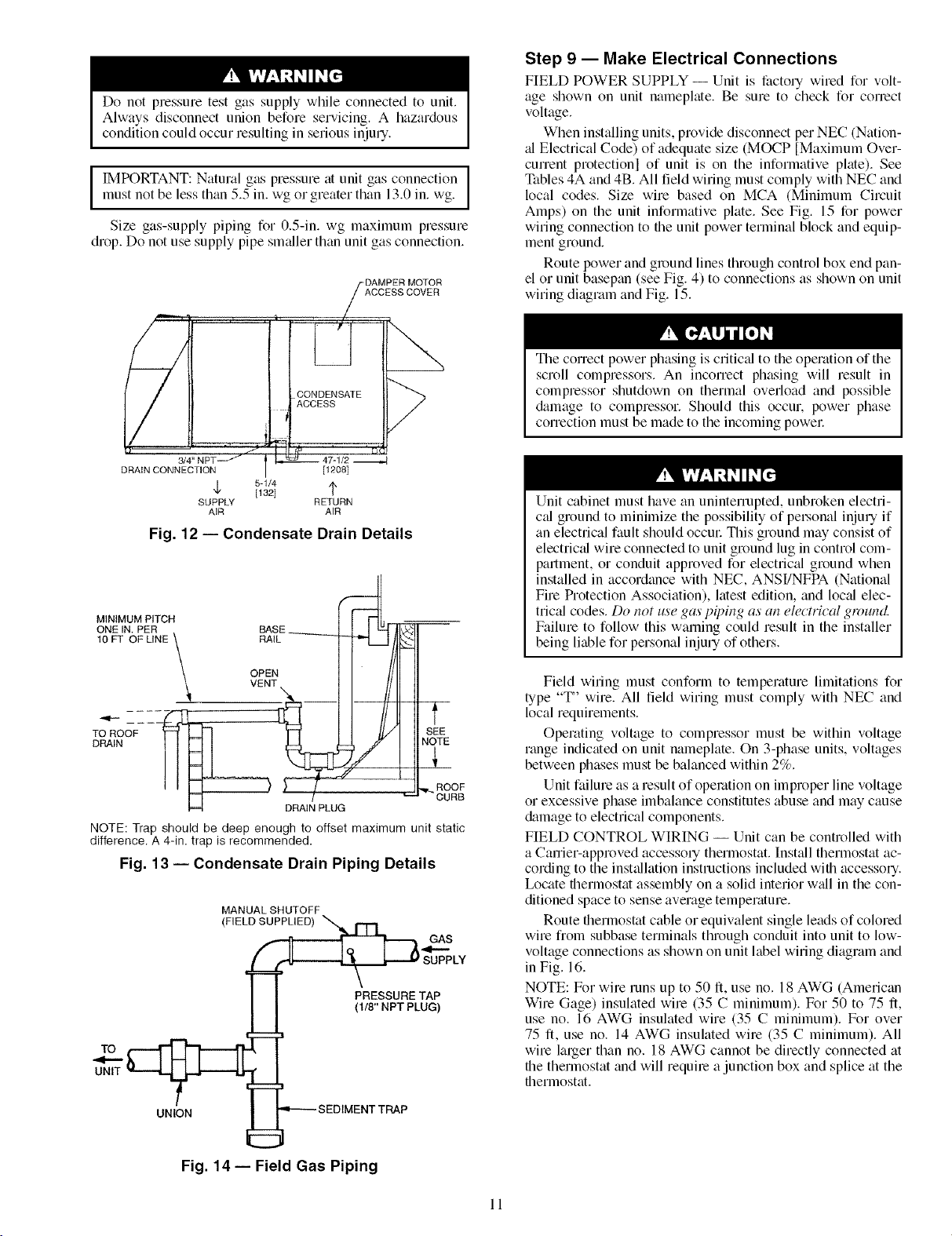
Do not pressure test gas supply while connected to unit.
Always disconnect union before servicing. A hazardous
condition could occur resulting in serious injury.
I MPORTANT: Natural gas pressure at unit gas connectionmust not be less than 5.5 in. wg or greater than 13.0 in. wg.
Size gas-supply piping for 0.5-in. wg maximum pressure
drop. Do not use supply pipe smaller than unit gas connection.
•DAMPER MOTOR
Og#gSA,E
D_
DRAIN CONNECTION [12081
/ 5-1/4
[132]
AiR AIR
Fig. 12- Condensate Drain Details
MINIMUM PITCH
ONE IN PER
SUPPLY RETURN
Step 9 -- Make Electrical Connections
FIELD POWER SUPPLY- Unit is factory wired for volt-
age shown on unit nameplate. Be sure to check for conect
voltage.
When installing units, provide disconnect per NEC (Nation-
al Electrical Code) of adequate size (MOCP [Maximum Over-
current protectionl of unit is on the informative plate). See
Tables 4A and 4B. All field wiring must comply with NEC and
local codes. Size wire based on MCA (Minimum Circuit
Amps) on the unit informative plate. See Fig. 15 for power
wiring connection to the unit power terminal block and equip-
ment ground.
Route power and ground lines through control box end pan-
el or unit basepan (see Fig. 4) to connections as shown on unit
wiring diagram and Fig. 15.
The correct power phasing is critical to the operation of the
scroll compressors. An incorrect phasing will result in
compressor shutdown on thermal overload and possible
&_mage to compressor. Should this occur, power phase
correction must be made to the incoming powel:
Unit cabinet must have an uninterrupted, unbroken electri-
c_fl ground to minimize the possibility of peLsonal injury if
an electrical fault should occur This ground may consist of
electric_d wire connected to unit ground lug in control com-
partment, or conduit approved for electrical ground when
installed in accordance with NEC, ANSI/NFPA (National
Fire Protection Association), latest edition, and loc_d elec-
triced codes. Do not use gas piping as an electrical ground
Failure to follow this warning could result in the installer
being liable for personal injury of others.
10 FT ()F LINE
t
TO ROOF
DRAIN
DRAIN PLUG
NOTE: Trap should be deep enough to offset maximum unit static
difference.A 4-in. trap is recommended•
Fig. 13- Condensate Drain Piping Details
MANUAL SHUTOFF
(FIELD SUPPLIED)
TO
UNIT
i _-"--- SEDIMENT TRAP
FT'I
PRESSURE TAP
(1/8" NPT PLUG)
SEE
NOTE
A_
ROOF
CURB
SUPPLY
Field wiring must conform to temperature limitations for
type "T' wire. All field wiring must comply with NEC and
local requirements.
Operating voltage to compressor must be within voltage
range indicated on unit nameplate. On 3-phase units, voltages
between phases must be balanced within 2%.
Unit failure as a result of operation on improper line voltage
or excessive phase imbalance constitutes abuse and may cause
&_mage to electrical components.
FIELD CONTROL WIRING -- Unit can be controlled with
a Carrier-approved accesso q thermostat. Install thermostat ac-
cording to the installation instructions included with accessory.
Ix)cate thermostat assembly on a solid interior w_dl in the con-
ditioned space to sense average temperature.
Route thermostat cable or equivalent single leads of colored
wire from subbase terminals through conduit into unit to low-
voltage connections as shown on unit label wiring diagram and
in Fig. 16.
NOTE: For wire runs up to 50 ft, use no. 18 AWG (Americ_m
Wire Gage) insulated wire (35 C minimum). For 50 to 75 fl,
use no. 16 AWG insulated wire (35 C minimum). For over
75 fl, use no. 14 AWG insulated wire (35 C minimum). All
wire larger than no. 18 AWG cannot be directly connected at
the thermostat and will requile a junction box and splice at the
thermostat.
Fig. 14- Field Gas Piping
11
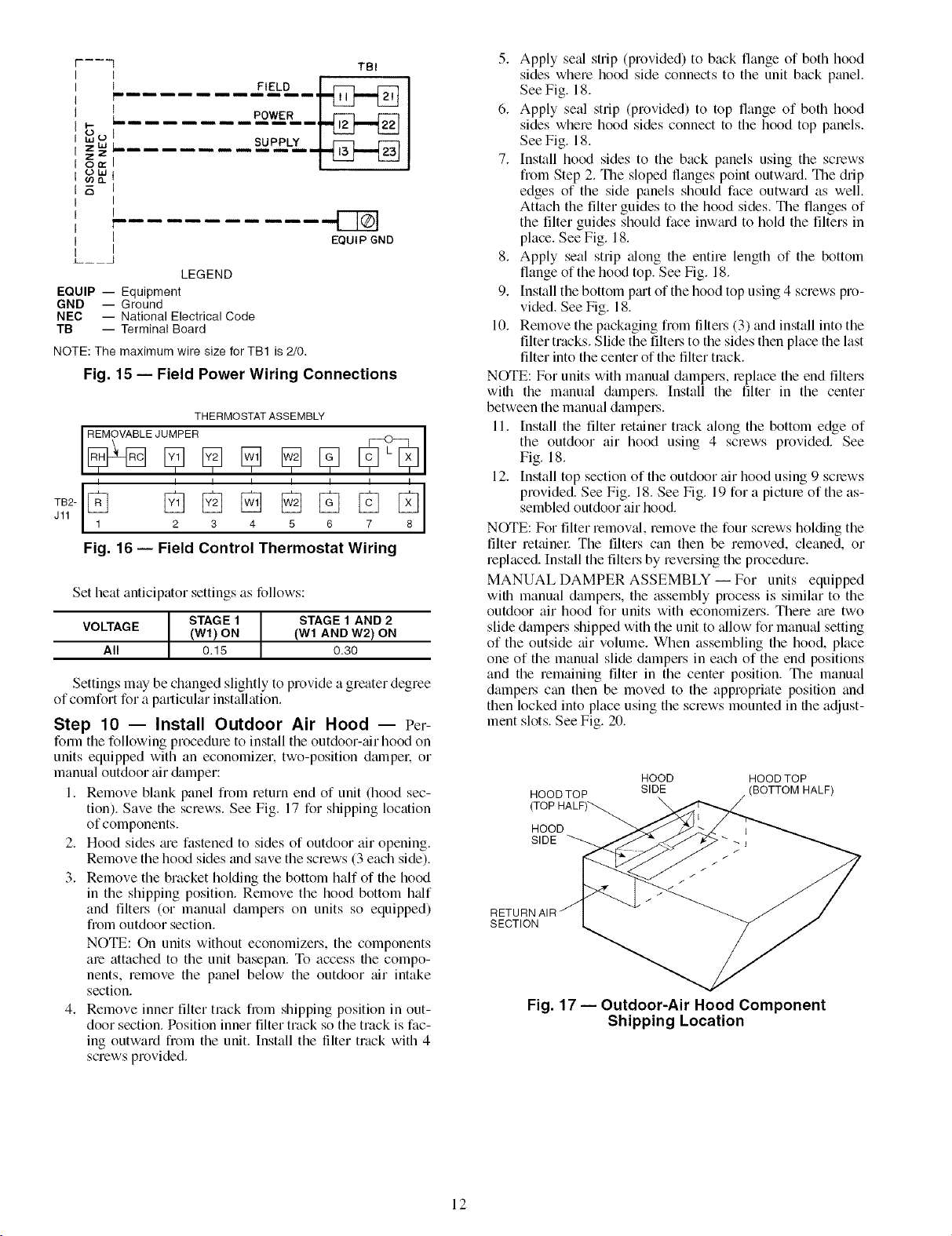
.... I TBI
II FIELD [ r---I
L.......
Z_U_ SUPPLY , F_!
o=;-..........
I
I
!
r
I
i
LEGEND
EQUIP --
GND --
NEC --
TB --
NOTE: The maximum wire size for TB1 is 2/0.
Equipment
Ground
National ElectricalCode
Terminal Board
Fig. 15- Field Power Wiring Connections
THERMOSTAT ASSEMBLY
I I I I I I I I
TB2- []
Jll 1 [_ [_ [_ _ [_ [] [_
2 3 4 5 6 7 8
Fig. 16- Field Control Thermostat Wiring
Set heat anticipator settings as follows:
VOLTAGE
All
STAGE 1 STAGE 1 AND 2
(Wl) ON (W1 AND W2) ON
0.15 0.30
Settings may be changed slightly to provide a greater degree
of comfort for a particular installation.
Step 10 -- Install Outdoor Air Hood -- Per-
fonn the following procedure to install the outdoor-_dr hood on
units equipped with an economizer, two-position dmnpeL or
manual outdoor air &+mper:
1. Remove blank panel from return end of unit (hood sec-
tion). Save the screws. See Fig. 17 for shipping location
of components.
2. Hood sides me fastened to sides of outdoor air opening.
Remove the hood sides and save the screws (3 each side).
3. Remove the bracket holding the bottom half of the hood
in the shipping position. Remove the hood bottom half
and filters (or manual dampers on units so equipped)
from outdoor section.
NOTE: On units without economizers, the components
are attached to the unit basepan. To access the compo-
nents, remove the panel below the outdoor air intake
section.
4. Remove inner filter track from shipping position in out-
door section. Position inner filter track so the track is fac-
ing outward from the unit. Install the tilter track with 4
screws provided.
EQUIP GND
5. Apply seal strip (provided) to back flange of both hood
sides where hood side connects to the unit back panel.
See Fig. 18.
6. Apply seal strip (provided) to top flange of both hood
sides where hood sides connect to the hood top panels.
See Fig. 18.
7. Install hood sides to the back panels using the screws
from Step 2. The sloped flanges point outwtud. The drip
edges of the side panels should face outwmd as well.
Attach the filter guides to the hood sides. The flanges of
the filter guides should face inwm'd to hold the filters in
place. See Fig. 18.
8. Apply seal strip along the entire length of the bottom
flange of the hood top. See Fig. 18.
9. Install the bottom pmt of the hood top using 4 screws pro-
videdi See Fig. 18.
10. Remove the packaging from tilters (3) and install into the
filter tracks. Slide the filtel.'s to the sides then place the last
filter into the center of the tilter track.
NOTE: For units with manu;d dampers, replace the end filters
with the manual ck_mpers. Install the filter in the center
between the manual dampel.s.
11. Install the filter retainer track along the bottom edge of
the outdoor air hood using 4 screws provided. See
Fig. 18.
12. Install top section of the outdoor air hood using 9 screws
provided. See Fig. 18. See Fig. 19 for a pictme of the as-
sembled outdoor air hood.
NOTE: For filter remov_fl, remove the four screws holding the
filter retainel: The filters can then be removed, cleaned, or
replaced. Install the filters by reversing the procedure.
MANUAL DAMPER ASSEMBLY-- For units equipped
with manual dampers, the assembly process is similar to the
outdoor air hood for units with economizers. There me two
slide dampers shipped with the unit to _fllow for manual setting
of the outside air volume. When assembling the hood, place
one of the manual slide dampers in each of the end positions
and the remaining filter in the center position. The manual
dampel.s can then be moved to the appropriate position and
then locked into place using the screws mounted in the adjust-
ment slots. See Fig. 20.
HOOD HOOD TOP
SIDE (BOTTOM HALF)
SECTION
HOOD TOP
(TOP HALF)_
HOOD
SIDE
Fig. 17 -- Outdoor-Air Hood Component
Shipping Location
12
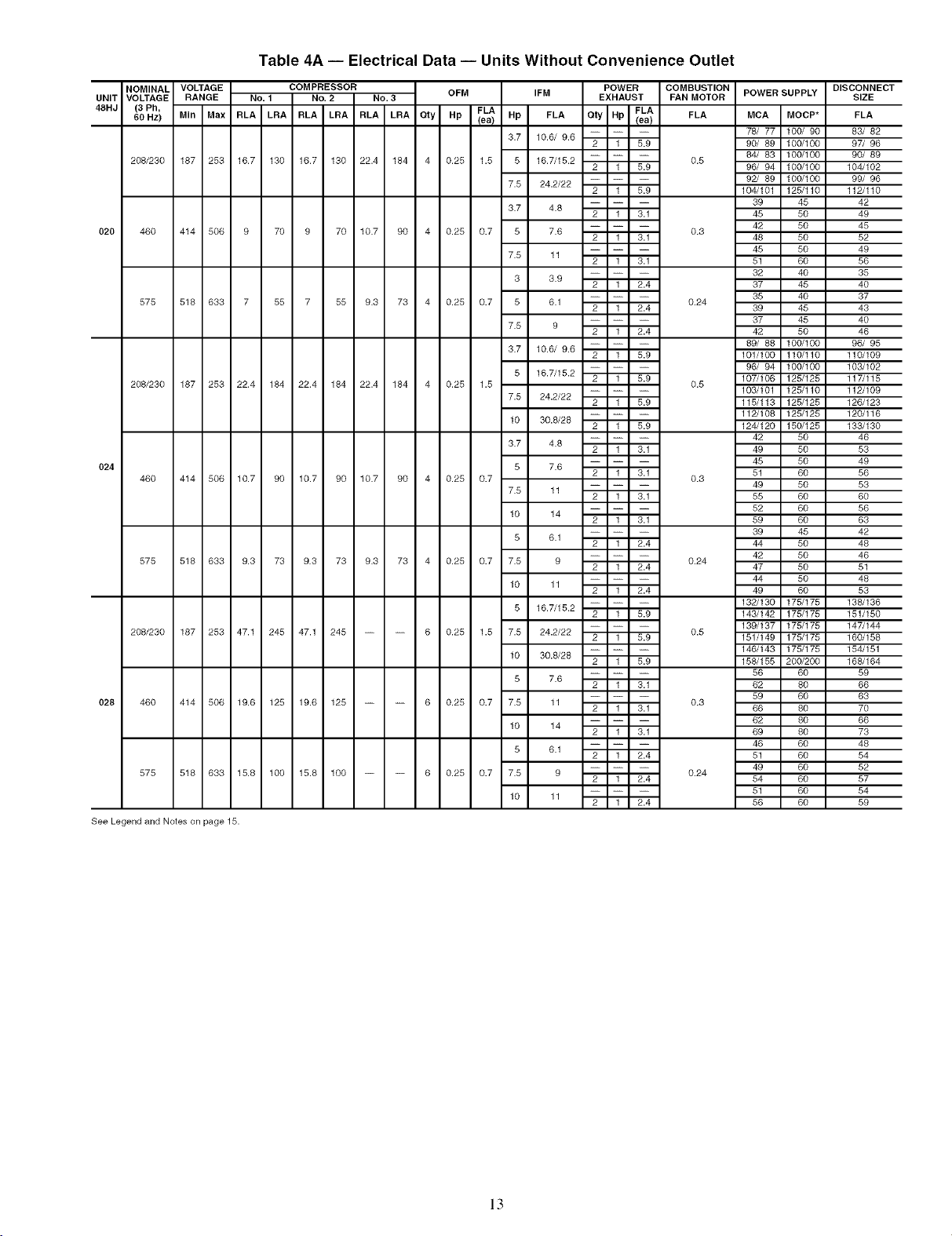
Table 4A -- Electrical Data -- Units Without Convenience Outlet
NOMINAL VOLTAGE COMPRESSOR OFM IFM POWER
UNIT VOLTAGE RANGE NO. 1 NO. 2 NO. 3 EXHAUST
48HJ (3 Ph,
60Hz)
MIn Max RLA LRA RLA LRA RLA LRA Oty Hp iea} Hp FLA Qty Hp _L/_
208/230 187 253 16.7 130 16.7 130 22.4 184 4 0.25 1.5 5 16.7/15.2
020 460 414 506 9 70 9 70 10.7 90 4 0.25 0.7 5 7.6
575 518 633 7 55 7 55 9.3 73 4 0.25 0.7 5 6.1
208/230 187 253 22.4 184 22.4 184 22.4 184 4 0.25 1.5
024
460 414 506 10.7 90 10.7 90 10.7 90 4 0.25 0.7
575 518 633 9.3 73 9.3 73 9.3 73 4 0.25 0.7 7.5 9
208/230 187 253 47.1 245 47.1 245 6 0.25 1.5 7.5 24.2/22
028 460 414 506 19.6 125 19.6 125 6 0.25 0.7 7.5 11
575 518 633 15.8 100 15.8 100 6 0.25 0.7 7.5 9
See Legend and Notes on page 15.
FLA
3.7 10.6/ 9.6
7.5 24.2/22
3.7 4.8
7.5 11
3 3.9
7.5 9
3.7 10.6/ 9.6
5 16.7/15.2
7.5 24.2/22
10 30.8/28
3.7 4.8
5 7.6
7.5 11
10 14
5 6.1
10 11
5 16.7/15.2
10 30.8/28
5 7.6
10 14
5 6.1
10 11
2 1 5.9
2 1 5.9
2 1 5.9
2 1 3.1
2 1 3.1
2 1 3.1
2 1 2.4
2 1 2.4
2 1 2.4
2 1 5.9
2 1 5.9
2 1 5.9
2 1 5.9
2 1 3.1
2 1 3.1
2 1 3.1
2 1 3.1
2 1 2.4
2 1 2.4
2 1 2.4
2 1 5.9
2 1 5.9
2 1 5.9
2 1 3.1
2 1 3.1
2 1 3.1
2 1 2.4
2 1 2.4
2 1 2.4
COMBUSTION DISCONNECT
FAN MOTOR POWER SUPPLY SIZE
FLA MCA MOCP* FLA
7_ 77 10_ 90 8_ 82
9_ 89 10&100 9_ 96
0.5
0.3
0.24
0.5
0.3
0.24
0.5
0.3
0.24
6_ 83 10&100 9_ 89
9_ 94 10_100 10_102
9_ 89 10_100 99/ 96
104/101 12_110 112/110
39 45 42
45 50 49
42 50 45
48 50 52
45 50 49
51 60 56
32 40 35
37 45 40
35 40 37
39 45 43
37 45 40
42 50 46
6_ 88 10&100 9& 95
101/100 11_110 11_109
9_ 94 10_100 10_102
10_106 12_125 11_115
10_101 12_110 112/109
11_113 12_125 12&123
11_108 12_125 12_116
12_120 15_125 13_130
42 50 46
49 50 53
45 50 49
51 60 56
49 50 53
55 60 60
52 60 56
59 60 63
39 45 42
44 50 48
42 50 46
47 50 51
44 50 46
49 60 53
132/130 17_175 13_136
14_142 17_175 151/150
13_137 17_175 14_144
151/149 17_175 16_158
14_143 17_175 15_151
15_155 20_200 16_164
56 60 59
62 60 66
59 60 63
66 60 70
62 60 66
69 60 73
46 60 48
51 60 54
49 60 52
54 60 57
51 60 54
56 60 59
13
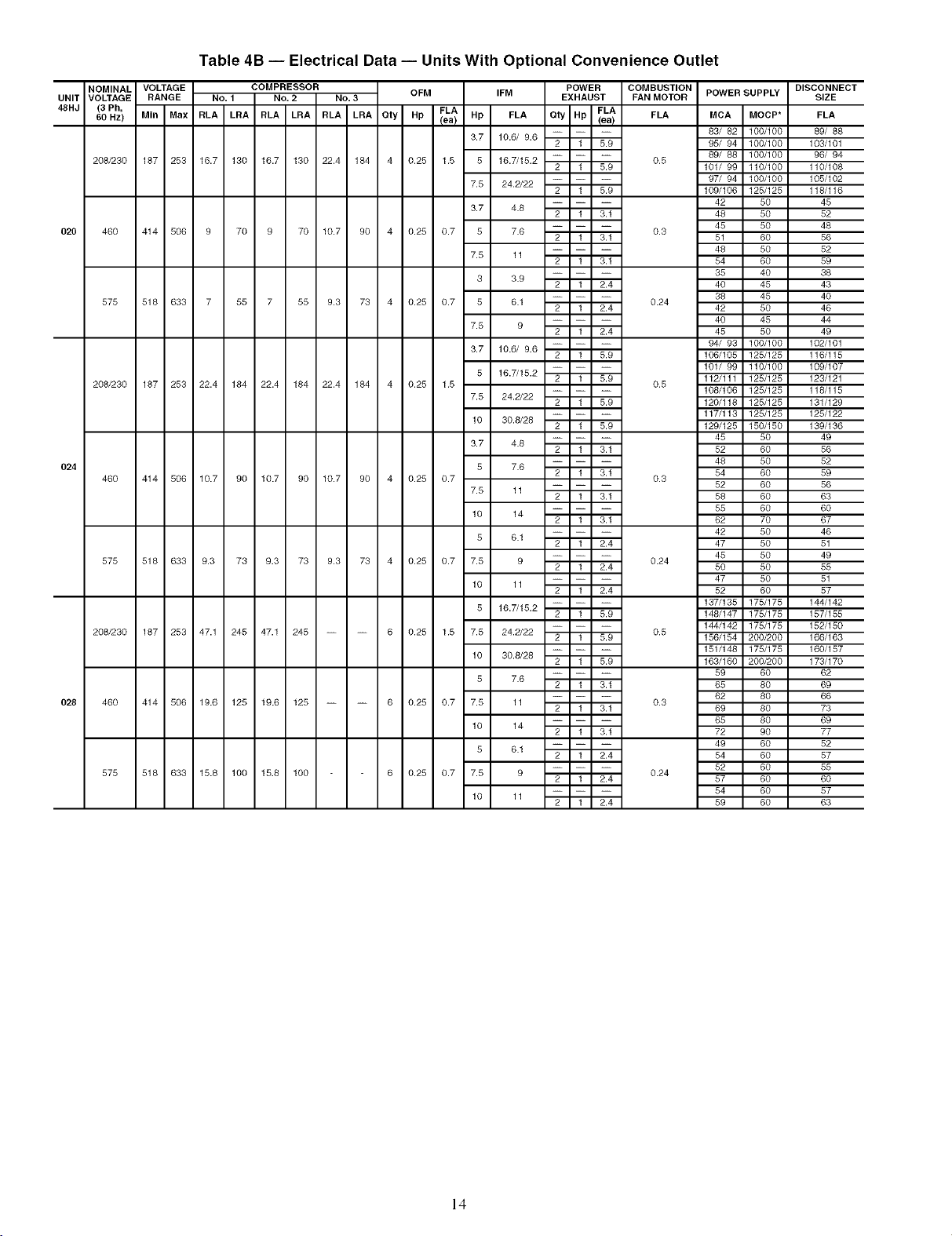
Table 4B -- Electrical Data -- Units With Optional Convenience Outlet
NOMINAL VOLTAGE
UNIT VOLTAGE RANGE
48HJ (3 Ph,
80 Hz) MIn Max RLA LRA RLA LRA RLA LRA Oty Hp Hp FLA O_ Hp {ea}
208/230 187 253 16.7 130 16.7 130 22.4 184 4 0.25 1.5 5 16.7/15.2
020 480 414 506 9 70 9 70 10.7 90 4 0.25 0.7 5 7.6
575 518 633 7 55 7 55 9.3 73 4 8.25 0.7 5 6.1
208/230 187 253 22.4 184 22.4 184 22.4 184 4 0.25 1.5
024 5 7.6
460 414 506 10.7 90 10.7 98 10.7 90 4 0.25 0.7
575 518 633 9.3 73 9.3 73 9.3 73 4 0.25 0.7 7.5 9
208/230 187 253 47.1 245 47.1 245 6 0.25 1.5 7.5 24.2/22
028 460 414 506 19.6 125 19.6 125 6 0.25 0.7 7.5 11
575 518 633 15.8 100 15.8 100 6 0.25 0.7 7.5 9
COMPRESSOR POWER
NO. 1 NO. 2 NO. 3 OFM IFM EXHAUST
_a_ FLA
3.7 10._ 9.6
7.5 24.2/22
3.7 4.8
7.5 11
3 3.9
7.5 9
3.7 10.6/ 9.6
5 16.7/15.2
7.5 24.2/22
10 30.8/28
3.7 4.8
7.5 11
10 14
5 6.1
10 11
5 16.7/15.2
10 30.8/28
5 7.6
10 14
5 6.1
10 11
COMBUSTION DISCONNECT
FAN MOTOR POWER SUPPLY SIZE
FLA MCA MOCP* FLA
2 1 5.9 95/ 94 100/100 103/101
2 1 5.9 101/ 99 110/100 110/108
2 1 5.9 109/106 125/125 118/116
2 1 3.1 48 50 52
2 1 3.1 51 60 56
2 1 3.1 54 60 59
2 1 2.4 40 45 43
2 1 2.4 42 50 46
2 1 2.4 45 50 49
2 1 5.9 106/105 125/125 116/115
2 1 5.9 112/111 125/125 123/121
2 1 5.9 128/118 125/125 131/129
2 1 5.9 129/125 150/150 139/136
2 1 3.1 52 60 56
2 1 3.1 54 60 59
2 1 3.1 58 60 63
2 1 3.1 62 70 67
2 1 2.4 47 50 51
2 1 2.4 50 50 55
2 1 2.4 52 60 57
2 1 5.9 148/147 175/175 157/155
2 1 5.9 156/154 208G00 166/163
2 1 5.9 163/160 200G00 173/170
2 1 3.1 65 80 69
2 1 3.1 69 80 73
2 1 3.1 72 90 77
2 1 2.4 54 60 57
2 1 2.4 57 60 60
2 1 2.4 59 60 63
0.5
0.3
0.24
0.5
0.3
0.24
0.5
0.3
0.24
83/ 82 108/100 89/ 88
89/ 88 100/100 96/ 94
97/ 94 108/100 105/102
42 50 45
45 50 48
48 50 52
35 40 38
38 45 40
40 45 44
94/ 93 108/100 102/101
101/ 99 110/100 109/107
108/106 125/125 118/115
117/113 125/125 125/122
45 50 49
48 50 52
52 60 56
55 60 60
42 50 46
45 50 49
47 50 51
137/135 175/175 144/142
144/142 175/175 152/150
151/148 175/175 160/157
59 60 62
62 80 66
65 80 69
49 60 52
52 60 55
54 60 57
14
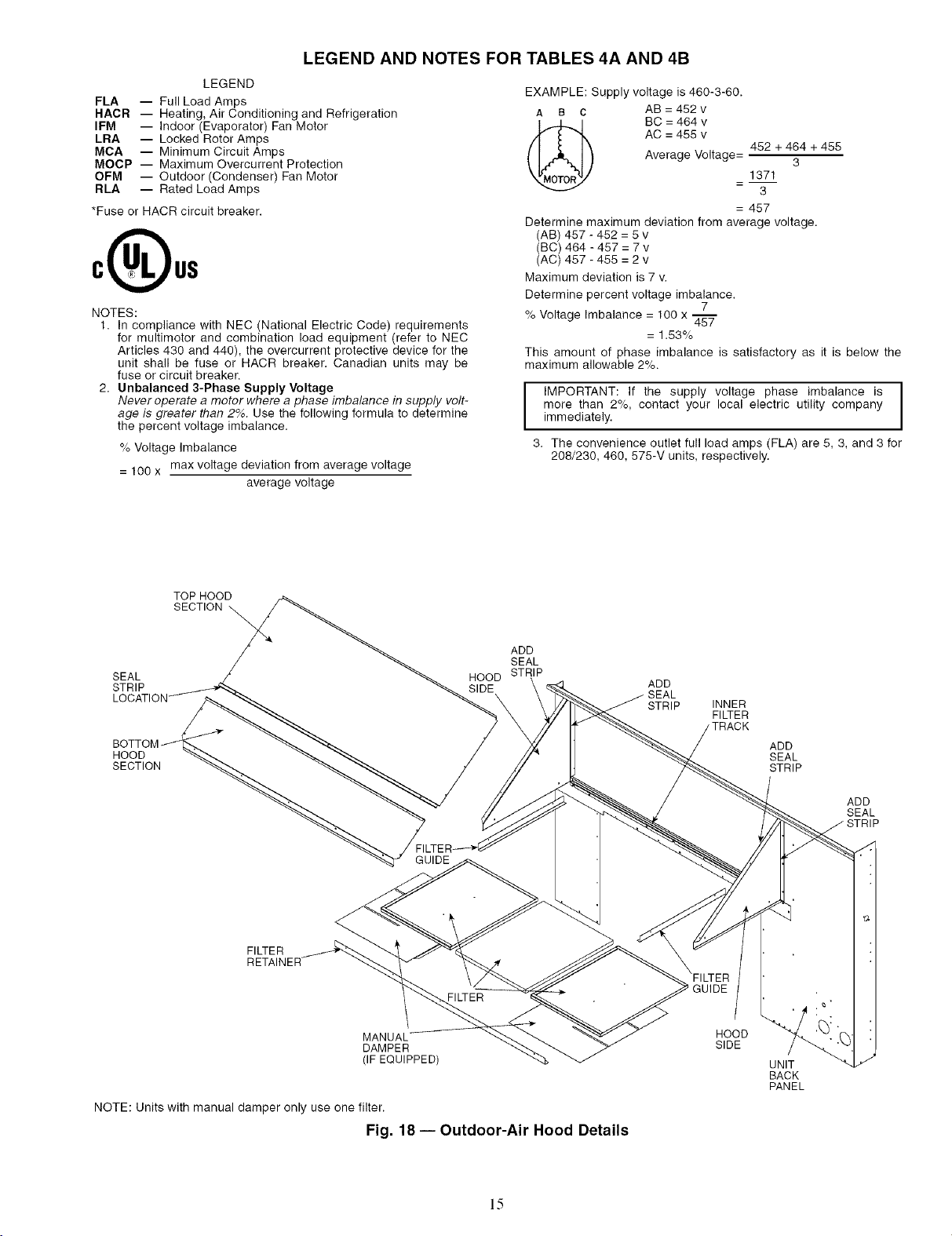
LEGEND AND NOTES FOR TABLES 4A AND 4B
LEGEND
FLA -- Full Load Amps
HACR -- Heating, Air Conditioning and Refrigeration
IFM -- Indoor (Evaporator) Fan Motor
LRA -- Locked Rotor Amps
MCA -- Minimum Circuit Amps
MOCP -- Maximum Overcurrent Protection
OFM -- Outdoor (Condenser) Fan Motor
RLA -- Rated Load Amps
*Fuse or HACR circuit breaker.
NOTES:
1. In compliance with NEC (National Electric Code) requirements
for multimotor and combination load equipment (refer to NEC
Articles 430 and 440), the overcurrent protective device for the
unit shall be fuse or HACR breaker. Canadian units may be
fuse or circuit breaker.
2. Unbalanced 3-Phase Supply Voltage
Never operate a motor where a phase imbalance in supply volt-
age is greater than 2%. Use the following formula to determine
the percent voltage imbalance.
% Voltage Imbalance
= 100 x max voltage deviation from average voltage
average voltage
EXAMPLE: Supply voltage is 460-3-60.
A B C AB = 452 v
AC = 456 v
Average Voltage= 452 + 464 + 456
(_ BC = 464 v
3
1371
3
= 457
Determine maximum deviation from average voltage.
(AB) 467 - 462 = 5 v
(BC) 464 - 457 = 7 v
(AC) 457 - 456 = 2 v
Maximum deviation is 7 v.
Determine percent voltage imbalance.
7
% Voltage Imbalance = 100 x 45"_-
= 1.53%
This amount of phase imbalance is satisfactory as it is below the
maximum allowable 2%.
more than 2%, contact your local electric utility company
I IMPORTANT: If the supply voltage phase imbalance is I
immediately.
3. The convenience outlet full load amps (FLA) are 5, 3, and 3 for
208/230,460, 575-V units, respectively.
I
TOP HOOD
SECTION
SEAL
STRIP
HOOD
SECTION
FILTER
RETAINER
MANUAL
DAMPER
(IF EQUIPPED)
NOTE: Units with manual damper only use one filter.
Fig. 18 -- Outdoor-Air Hood Details
GUIDE
HOOD STRIP
SIDE
FILTER
ADD
SEAL
ADD
SEAL
STRIP
INNER
FINER
TRACK
HOOD
SIDE
ADD
SEAL
STRIP
UNIT
BACK
PANEL
ADD
SEAL
STRIP
]5
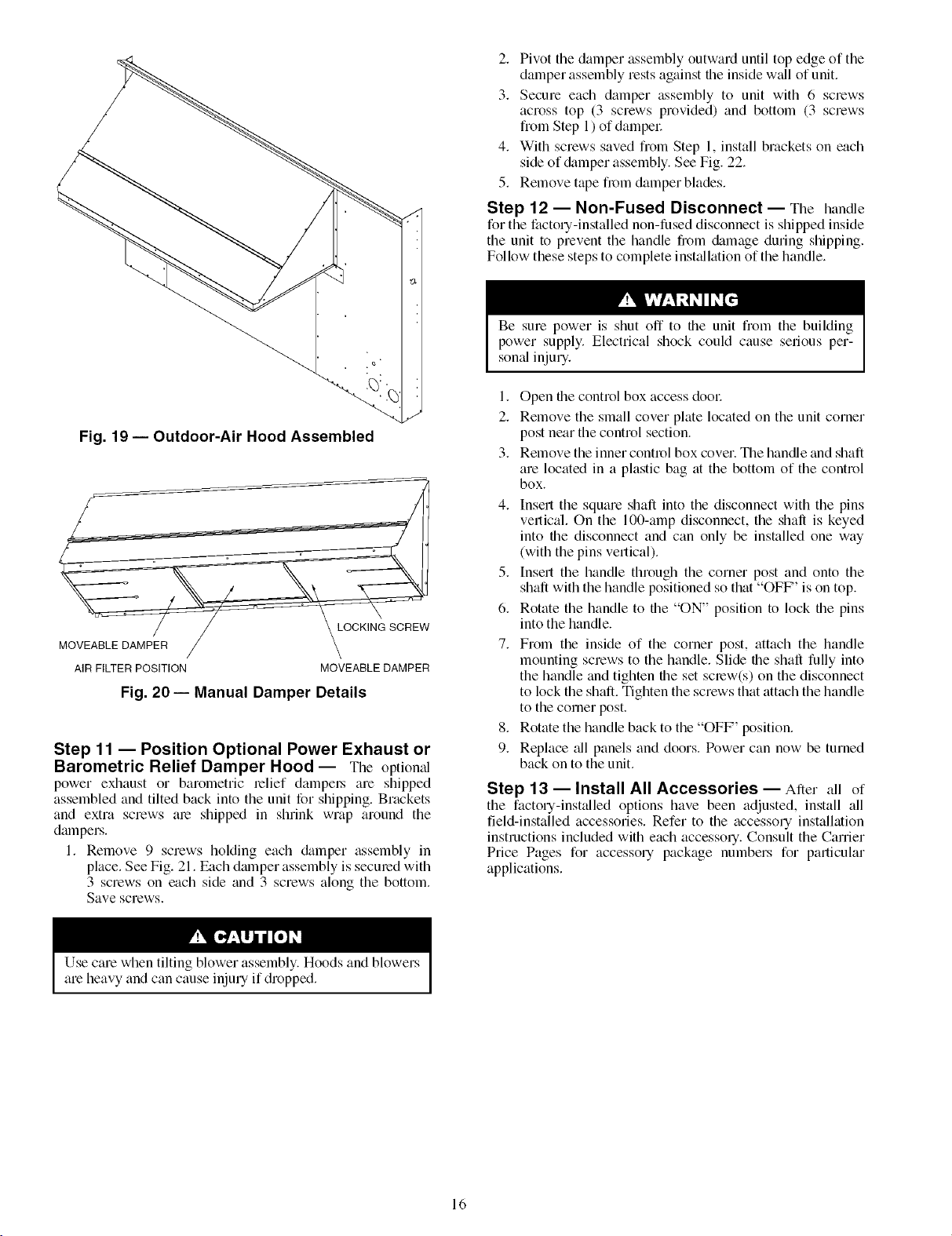
/4.
/
Fig. 19- Outdoor-Air Hood Assembled
MOVEABLEDAMPER/ \
AIR FILTER POSITION MOVEABLE DAMPER
Fig. 20- Manual Damper Details
Step 11 -- Position Optional Power Exhaust or
Barometric Relief Damper Hood -- The optiomfl
power exhaust or barolnetric relief dampel_ are shipped
assembled and tilted back into the unit for shipping. Brackets
and extra screws ale shipped in shrink wrap around the
dmnpers.
1. Remove 9 screws holding each &tmper assembly in
place. See Fig. 21. Each dmnper assembly is secured with
3 screws on each side and 3 screws along the bottom.
Save screws.
2. Pivot the damper assembly outward until top edge of the
damper assembly rests against file inside w_dl of unit.
3. Secure each damper assembly to unit with 6 screws
across top (3 screws provided) and bottom (3 screws
from Step 1) of dampel:
4. With screws saved from Step 1, install brackets on each
side of &tmper assembly. See Fig. 22.
5. Remove tape from damper blades.
Step 12 -- Non-Fused Disconnect -- The handle
for the factory-installed non-fused disconnect is shipped inside
the unit to prevent the handle from &image during shipping.
Follow these steps to complete inst_dlation of the handle.
Be sure power is shut off to the unit from the building
power supply. Electrical shock could cause serious per-
somd injury.
1. Open the control box access dool:
2. Remove the small cover plate located on the unit corner
post near the control section.
3. Remove the inner control box cover. The handle and shall
are located in a plastic bag at the bottom of the control
box.
4. Insert the square shall into the disconnect with the pins
vertical. On the 100-amp disconnect, the shall is keyed
into the disconnect and can only be installed one way
(with the pins vertical).
5. Insert the handle through the corner post and onto the
shall with the handle positioned so that "OFF' is on top.
6. Rotate the handle to the "ON" position to lock the pins
into the handle.
7. From the inside of the corner post, attach the handle
mounting screws to the handle. Slide the shall fully into
the handle and tighten the set screw(s) on the disconnect
to lock the shall. Tighten the screws that attach the handle
to the corner post.
8. Rotate the handle back to the "OFF" position.
9. Replace _fll panels and doors. Power can now be turned
back on to the unit.
Step 13 --Install All Accessories--After all of
the factory-installed options have been adjusted, install all
field-installed accessories. Refer to the accessory installation
instructions included with each accessory. Consult the CaMer
Price Pages for accessory package numbers for particular
applications.
Use care when tilting blower assembly. Hoods and blowers
are heavy and can cause injury if dropped.
16
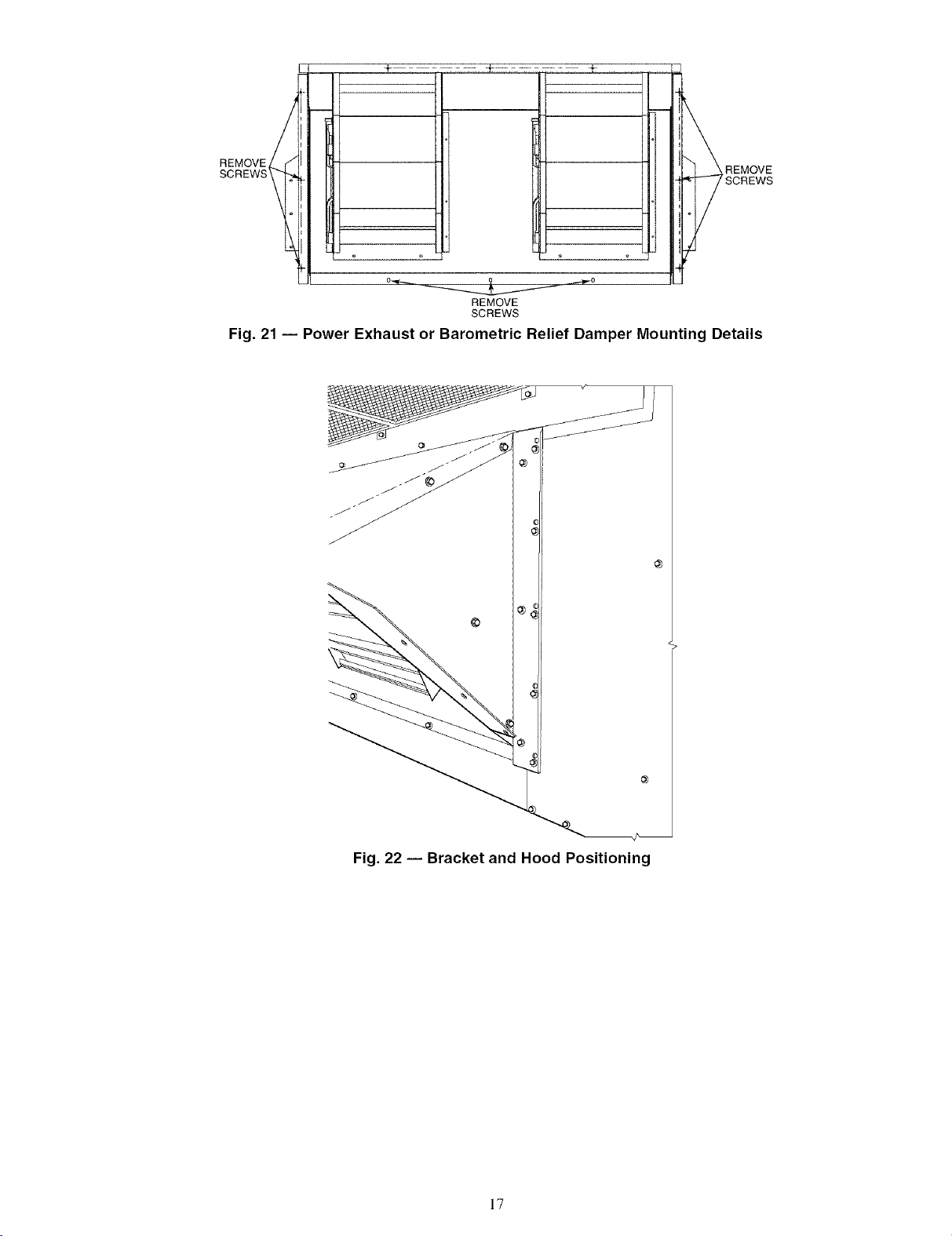
REMOVE
SCREWS_
REMOVE
SCREWS
Fig. 21 -- Power Exhaust or Barometric Relief Damper Mounting Details
®_
,REMOVE
SCREWS
Fig. 22 -- Bracket and Hood Positioning
]7
@
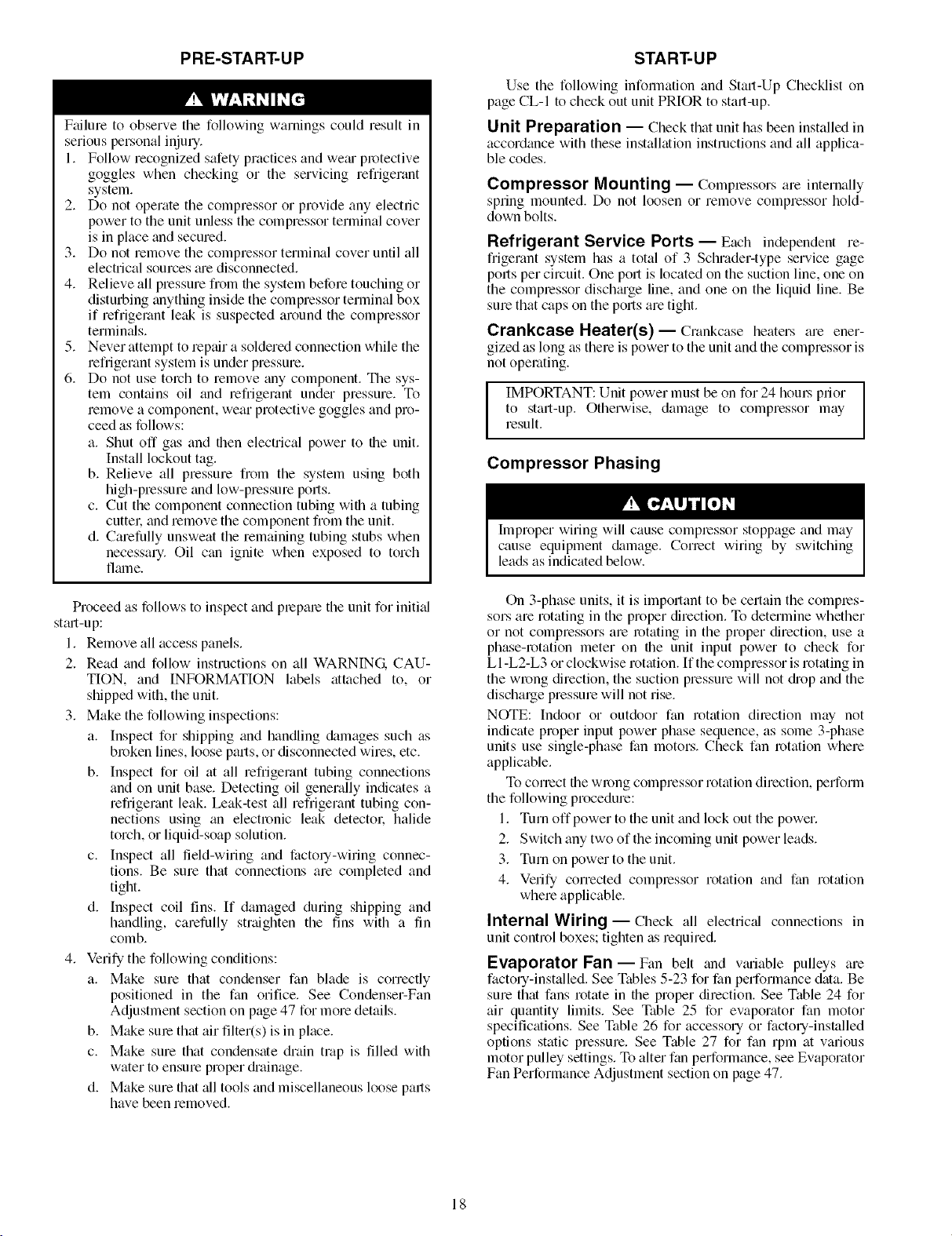
PRE-START-UP
F;filure to observe the following warnings could result in
serious personal injury.
1. Follow recognized safety practices and we;u protective
goggles when checking or the servicing refrigerant
system.
2. Do not operate the compressor or provide any electric
power to the unit unless the compressor terminal cover
is in place and secured.
3. Do not remove the compressor terminal cover until all
electrical sources _ue disconnected.
4. Relieve all pressure from file system before touching or
disturbing anything inside the compressor terminal box
if refrigerant leak is suspected around the compressor
terminals.
5. Never attempt to repair a soldered connection while the
refrigerant system is under pressure.
6. Do not use torch to remove any component. The sys-
tem contains oil and refrigerant under pressure. To
remove a component, wear protective goggles and pro-
ceed as follows:
a. Shut off gas and then electrical power to the unit.
Install lockout tag.
b. Relieve all pressure from the system using both
high-pressure and low-pressure ports.
c. Cut the component connection tubing with a tubing
cuttek and remove the component from the unit.
d. Carefully unsweat the remaining tubing stubs when
necessary. Oil can ignite when exposed to torch
flalne.
START-UP
Use the following inforlnation and Start-Up Checklist on
page CL-I to check out unit PRIOR to start-up.
Unit Preparation -- Check that unit l'msbeen installed in
accordance with these installation instructions and all applica-
ble codes.
Compressor Mounting- Compressorsare internally
spring mounted. Do not loosen or remove compressor hold-
down bolts.
Refrigerant Service Ports-- Each independent re-
frigerant system has a total of 3 Schmder-type service gage
ports per circuit. One port is located on the suction line, one on
the compressor dischmge line, and one on the liquid line. Be
sure that caps on the ports are tight.
Crankcase Heater(s)- Crankcase heaters are ener-
gized as long as there is power to the unit and the compressor is
not operating.
IMPORTANT: Unit power must be on for 24 hom.'sprior
to start-up. Otherwise, damage to compressor may
result.
Compressor Phasing
hnproper wiring will cause compressor stoppage and may
cause equipment damage. Correct wiring by switching
leads as indicated below.
Proceed as follows to inspect and prepare the unit for initial
st_ut-up:
1. Remove all access panels.
2. Read and follow instructions on all WARNING CAU-
TION, and INFORMATION labels attached to, or
shipped with, the unit.
3. Make the following inspections:
a. Inspect for shipping and handling damages such as
broken lines, loose parts, or disconnected wires, etc.
b. Inspect for oil at all refrigerant tubing connections
and on unit base. Detecting oil generally indicates a
refrigerant leak. Leak-test all refiigemnt tubing con-
nections using an electronic leak detectok halide
torch, or liquid-soap solution.
c. Inspect all tield-wiring and factou-wiring connec-
tions. Be sure that connections are completed and
tight.
d. Inspect coil fins. If damaged during shipping and
handling, carefully straighten the fins with a tin
comb.
4. Verify the following conditions:
a. Make sure that condenser fan blade is correctly
positioned in the fan orifice. See Condenser-Fan
Adjustment section on page 47 for more details.
b. Make sure that air filter(s) is in place.
c. Make sure that condensate drain trap is filled with
water to ensure proper di'ainage.
d. Make sure that all tools and miscellaneous loose parts
have been removed.
On 3-phase units, it is important to be certain the compres-
sors are rotating in the proper direction. To determine whether
or not compressors are rotating in the proper direction, use a
phase-rotation meter on the unit input power to check for
L I-L2-L3 or clockwise rotation. If the compressor is rotating in
the wrong direction, the suction pressure will not diop and the
discharge pressure will not rise.
NOTE: Indoor or outdoor fan rotation direction may not
indicate proper input power phase sequence, as some 3-phase
units use single-phase fan motors. Check fan rotation where
applicable.
To correct the wrong compressor rotation direction, perform
the following procedure:
1. Turn offpower to the unit and lock out the power.
2. Switch any two of the incoming unit power leads.
3. Turn on power to the unit.
4. Verify corrected compressor rotation and fan rotation
where applicable.
Internal Wiring- Check all electrical connections in
unit control boxes; tighten as required.
Evaporator Fan- Fan belt and v_uiable pulleys are
factory-installed. See Tables 5-23 for fan performance data. Be
sure that fans rotate in the proper direction. See Table 24 for
air quantity limits. See Table 25 for evaporator fan motor
specifications. See Table 26 for accessory or factory-installed
options static pressure. See Table 27 for fan rpm at various
motor pulley settings. To alter fan performance, see Evaporator
Fan Performance Adjustment section on page 47.
18
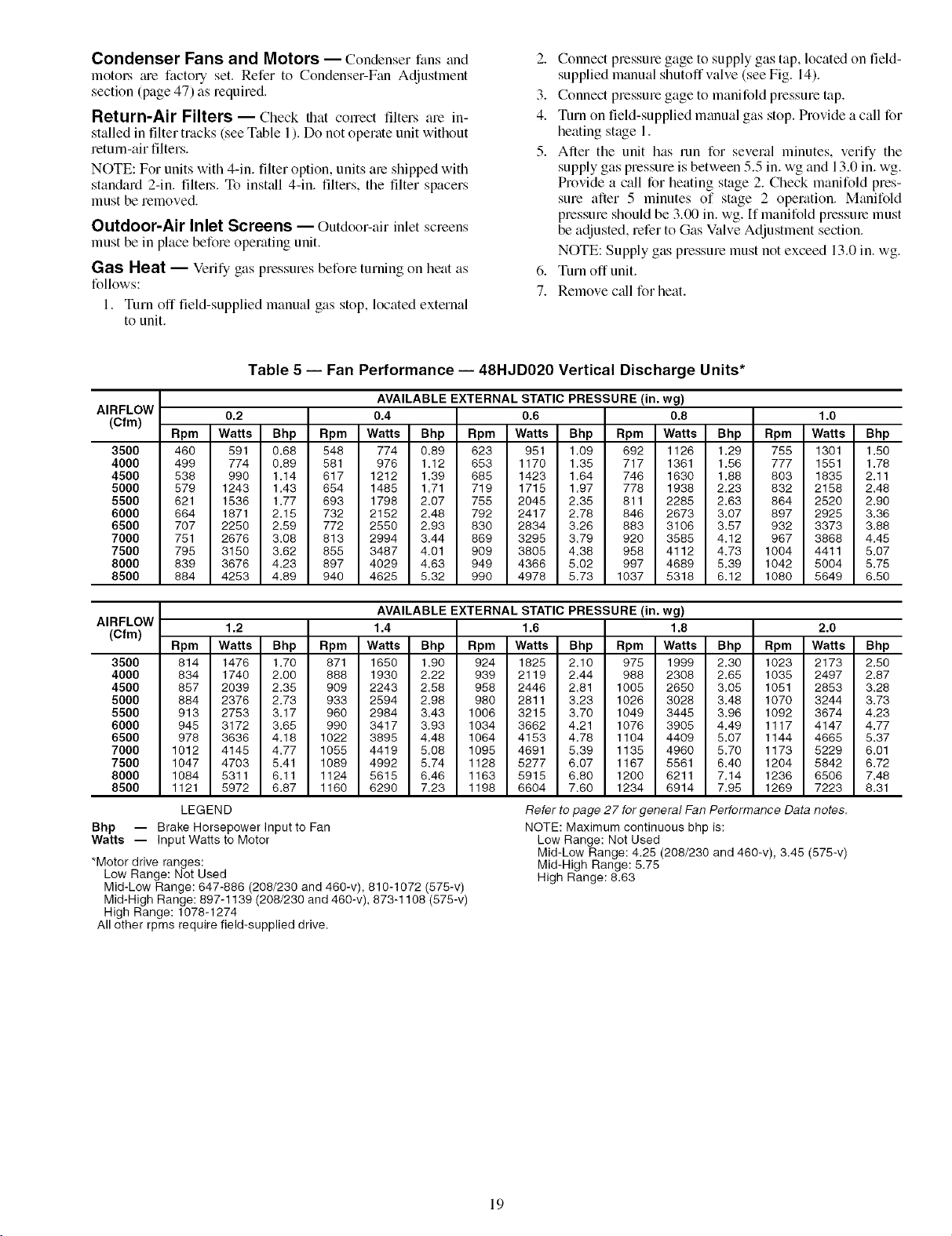
Condenser Fans and Motors -- Condenser fans and
motols ;ue factory set. Refer to Condensel;Fan Adjustment
section (page 47) as required.
Return-Air Filters- Check that correct flters are in-
stalled in filter tracks (see Table 1). Do not operate unit without
return-air filters.
NOTE: For units with 4-in. filter option, units ale shipped with
standard 2-in. filtel_. To inst_fll 4-in. filters, tile filter spacers
must be removed.
Outdoor-Air Inlet Screens -- Outdoor-air inlet screens
must be in place before operating unit.
Gas Heat -- Verify gas pressures before turning on heat as
follows:
1. Turn off field-supplied manual gas stop, located external
to unit.
Table 5 -- Fan Performance -- 48HJD020 Vertical Discharge Units*
AIRFLOW
(Cfm)
3500
4000
4500
5000
5500
6000
6500
7000
7500
8000
8500
0.2 0.4 0.6 0.8 1.0
Rpm Watts Bhp Rpm Watts Bhp Rpm Watts Bhp Rpm Watts Bhp Rpm Watts Bhp
460 591 0.68 548 774 0.89 623 951 1.09 692 1126 1.29 755 1301 1.50
499 774 0.89 581 976 1.12 653 1170 1.35 717 1361 1.56 777 1551 1.78
538 990 1.14 617 1212 1.39 685 1423 1.64 746 1630 1.88 803 1835 2.11
579 1243 1.43 654 1485 1.71 719 1715 1.97 778 1938 2.23 832 2158 2.48
621 1536 1.77 693 1798 2.07 755 2045 2.35 811 2285 2.63 864 2520 2.90
664 1871 2.15 732 2152 2.48 792 2417 2.78 846 2673 3.07 897 2925 3.36
707 2250 2.59 772 2550 2.93 830 2834 3.26 883 3106 3.57 932 3373 3.88
751 2676 3.08 813 2994 3.44 869 3295 3.79 920 3585 4.12 967 3868 4.45
795 3150 3.62 855 3487 4.01 909 3805 4.38 958 4112 4.73 1004 4411 5.07
839 3676 4.23 897 4029 4.63 949 4366 5.02 997 4689 5.39 1042 5004 5.75
884 4253 4.89 940 4625 5.32 990 4978 5.73 1037 5318 6.12 1080 5649 6.50
AVAILABLE EXTERNAL STATIC PRESSURE (in. wg)
2. Connect pressure gage to supply gas tap, located on field-
supplied manual shutoff valve (see Fig. 14).
3. Connect pressure gage to manifold pressure tap.
4. Turn on feld-supplied manual gas stop. Provide a call for
heating stage 1.
5. After the unit has run for several minutes, verify tile
supply gas pressure is between 5.5 in. wg and 13.0 in. wg.
Provide a call for heating stage 2. Check manifold pres-
sure after 5 minutes of stage 2 operation. Manifold
pressure should be 3.00 in. wg. If manifold pressure must
be adjusted, refer to Gas Valve Adjustment section.
NOTE: Supply gas pressure must not exceed 13.0 in. wg.
6. Turn off unit.
7. Remove c_dl for heat.
AIRFLOW
(Cfm)
3500
4000
4500
5000
5500
6000
6500
7000
7500
8000
8500
Bhp -- Brake Horsepower Input to Fan
Watts -- Input Watts to Motor
*Motor drive ranges:
Low Range: Not Used
Mid-Low Range: 647-886 (208/230 and 460-v), 810-1072 (575-v)
Mid-High Range: 897-1139 (208/230 and 460-v), 873-1108 (575-v)
High Range: 1078-1274
All other rpms require field-supplied drive.
Rpm Watts Bhp Rpm Watts Bhp Rpm Watts Bhp Rpm Watts Bhp Rpm Watts Bhp
814 1476 1.70 871 1650 1.90 924 1825 2.10 975 1999 2.30 1023 2173 2.50
834 1740 2.00 888 1930 2.22 939 2119 2.44 988 2308 2.65 1035 2497 2.87
857 2039 2.35 909 2243 2.58 958 2446 2.81 1005 2650 3.05 1051 2853 3.28
884 2376 2.73 933 2594 2.98 980 2811 3.23 1026 3028 3.48 1070 3244 3.73
913 2753 3.17 960 2984 3.43 1006 3215 3.70 1049 3445 3.96 1092 3674 4.23
945 3172 3.65 990 3417 3.93 1034 3662 4.21 1076 3905 4.49 1117 4147 4.77
978 3636 4.18 1022 3895 4.48 1064 4153 4.78 1104 4409 5.07 1144 4665 5.37
1012 4145 4.77 1055 4419 5.08 1095 4691 5.39 1135 4960 5.70 1173 5229 6.01
1047 4703 5.41 1089 4992 5.74 1128 5277 6.07 1167 5561 6.40 1204 5842 6.72
1084 5311 6.11 1124 5615 6.46 1163 5915 6.80 1200 6211 7.14 1236 6506 7.48
1121 5972 6.87 1160 6290 7.23 1198 6604 7.60 1234 6914 7.95 1269 7223 8.31
1.2 1.4 1.6 1.8 2.0
LEGEND Refer to page 27 for general Fan Performance Data notes.
AVAILABLE EXTERNAL STATIC PRESSURE (in. wg)
NOTE: Maximum continuous bhp is:
Low Range: Not Used
Mid-Low Range: 4.25 (208/230 and 460-v), 3.45 (575-v)
Mid-High Range: 5.75
High Range: 8.63
19

Table 6 -- Fan Performance -- 48HJE020 Vertical Discharge Units*
AIRFLOW
(Cfm)
350O
4000
4500
5000
5500
6000
6500
7000
7500
8000
8500
AIRFLOW
(Cfm)
3500
4000
4500
5000
5500
6000
6500
7000
7500
8000
8500
0.2 0.4 0.6 0.8 1.0
Rpm Watts Bhp Rpm Watts Bhp Rpm Watts Bhp Rpm Watts Bhp Rpm Watts Bhp
470 611 0.70 556 791 0.91 630 967 1.11 697 1141 1.31 760 1314 1.51
511 802 0.92 691 1001 1.16 661 1194 1.37 725 1383 1.59 784 1572 1.81
553 1029 1.18 629 1248 1.44 695 1458 1.68 756 1663 1.91 812 1866 2.16
597 1297 1.49 669 1534 1.76 732 1761 2.03 789 1982 2.28 843 2201 2.53
641 1606 1.85 709 1862 2.14 770 2106 2.42 825 2343 2.70 876 2577 2.96
686 1961 2.26 751 2234 2.57 809 2495 2.87 862 2749 3.16 911 2997 3.45
732 2363 2.72 794 2653 3.05 849 2931 3.37 900 3201 3.68 948 3465 3.99
779 2816 3.24 837 3122 3.59 891 3416 3.93 940 3702 4.26 986 3981 4.58
826 3320 3.82 882 3642 4.19 933 3953 4.66 980 4254 4.89 1025 4549 6.23
873 3879 4.46 926 4217 4.86 976 4542 5.22 1021 4860 5.59 1065 5169 6.96
921 4496 6.17 972 4847 6.57 1019 5189 5.97 1063 6621 6.35 1106 5846 6.72
1.2 1.4 1.6 1.8 2.0
Rpm Watts Bhp Rpm Watts Bhp Rpm Watts Bhp Rpm Watts Bhp Rpm Watts Bhp
818 1488 1.71 874 1661 1.91 927 1835 2.11 978 2008 2.31 1026 2182 2.51
840 1760 2.02 893 1948 2.24 943 2136 2.46 992 2324 2.67 1039 2512 2.89
865 2068 2.38 915 2270 2.61 964 2472 2.84 1011 2673 3.07 1056 2876 3.31
893 2417 2.78 942 2632 3.03 988 2848 3.28 1033 3063 3.52 1076 3278 3.77
925 2808 3.23 971 3037 3.49 1016 3266 3.76 1059 3494 4.02 1100 3721 4.28
958 3243 3.73 1003 3486 4.01 1045 3728 4.29 1087 3970 4.57 1127 4210 4.84
993 3725 4.28 1036 3982 4.58 1077 4238 4.87 1117 4492 5.17 1156 4745 6.46
1029 4256 4.90 1071 4528 6.21 1111 4797 5.52 1150 5064 5.82 1187 5330 6.13
1067 4838 6.56 1107 5124 6.89 1146 5407 6.22 1184 5688 6.54 1220 5967 6.86
1106 5474 6.30 1145 5774 6.64 1182 6071 6.98 1219 6365 7.32 1254 6657 7.66
1145 6165 7.09 1183 6479 7.45 1220 6790 7.81 1255 7098 8.16 1290 7403 8.51
AVAILABLE EXTERNAL STATIC PRESSURE (in. wg)
AVAILABLE EXTERNAL STATIC PRESSURE (in. wg)
LEGEND Refer to page 27 for general Fan Performance Data notes.
Bhp -- Brake Horsepower Input to Fan
Watts -- Input Watts to Motor
*Motor drive ranges:
Low Range: Not Used
Mid-Low Range: 647-886 (208/230 and 460-v), 810-1072 (575-v)
Mid-High Range: 897-1139 (206/230 and 480-v), 673-1108 (575-v)
High Range: 1078-1274
All other rpms require field-supplied drive.
NOTE: Maximum continuous bhp is:
Low Range: Not Used
Mid-Low Range: 4.25 (208/230 and 460-v), 3.45 (575-v)
Mid-High Range: 5.76
High Range: 8.63
2O

Table 7 -- Fan Performance -- 48HJF020 Vertical Discharge Units*
AIRFLOW
(Cfm)
3500
4000
4500
5000
5500
6000
6500
7000
7500
8000
8500
AIRFLOW
(Cfm)
3500
4000
4500
5000
5500
6000
6500
7000
7500
8000
8500
0.2 0.4 0.6 0.8 1.0
Rpm Watts Bhp Rpm Watts Bhp Rpm Watts Bhp Rpm Watts Bhp Rpm Watts Bhp
470 611 0.70 556 791 0.91 630 967 1.11 697 1141 1.31 760 1314 1.51
511 802 0.92 591 1001 1.15 661 1194 1.37 725 1383 1.59 784 1572 1.81
553 1029 1.18 629 1248 1.44 695 1458 1.68 756 1663 1.91 812 1866 2.15
597 1297 1.49 669 1534 1.76 732 1761 2.03 789 1982 2.28 843 2201 2.53
641 1606 1.85 709 1862 2.14 770 2106 2.42 828 2343 2.70 876 2577 2.96
686 1961 2.26 751 2234 2.57 809 2495 2.87 862 2749 3.16 911 2997 3.45
732 2363 2.72 794 2653 3.05 849 2931 3.37 900 3201 3.68 948 3465 3.99
779 2815 3.24 837 3122 3.59 891 3416 3.93 940 3702 4.26 986 3981 4.58
826 3320 3.82 882 3642 4.19 933 3953 4.55 980 4254 4.89 1025 4549 5.23
873 3879 4.46 926 4217 4.85 975 4542 5.22 1021 4860 5.59 1065 5169 5.95
921 4495 5.17 972 4847 5.57 1019 5189 5.97 1063 5521 6.35 1105 5846 6.72
1.2 1.4 1.6
Rpm Watts Bhp Rpm Watts Bhp Rpm Watts Bhp Rpm
818 1488 1.71 874 1661 1.91 927 1835 2.11 978
840 1760 2.02 893 1948 2.24 943 2136 2.46 992
865 2068 2.38 915 2270 2.61 964 2472 2.84 1011
893 2417 2.78 942 2632 3.03 988 2848 3.28 1033
925 2808 3.23 971 3037 3.49 1016 3266 3.76 1059
958 3243 3.73 1003 3486 4.01 1045 3728 4.29 1087
993 3725 4.28 1036 3982 4.58 1077 4238 4.87 1117
1029 4256 4.90 1071 4528 5.21 1111 4797 5.52 1150
1067 4838 5.56 1107 5124 5.89 1146 5407 6.22 1184
1106 5474 6.30 1145 5774 6.64 1182 6071 6.98 1219
1145 6165 7.09 1183 6479 7.45 1220 6790 7.81 1255
AVAILABLE EXTERNAL STATIC PRESSURE (in. wg)
AVAILABLE EXTERNAL STATIC PRESSURE (in.
LEGEND
Bhp -- Brake Horsepower Input to Fan
Watts -- Input Watts to Motor
*Motor drive ranges:
Low Range: Not Used
Mid-Low Range: 647-886 (208/230 and 460-v), 810-1072 (575-v)
Mid-High Range: 897-1139 (208/230 and 460-v), 873-1108 (575-v)
High Range: 1078-1274
All other rpms require field-supplied drive.
wg)
1.8 2.0
Watts Bhp Rpm Watts Bhp
2008 2.31 1026 2182 2.51
2324 2,67 1039 2512 2,89
2673 3,07 1056 2876 3,31
3063 3,52 1076 3278 3,77
3494 4.02 1100 3721 4.28
3970 4.57 1127 4210 4.84
4492 5.17 1156 4745 5.46
5064 5,82 1187 5330 6,13
5688 6.54 1220 5967 6.86
6365 7,32 1254 6657 7.66
7098 8.16 1290 7403 8.51
Refer to page 27 for general Fan Performance Data notes.
NOTE: Maximum continuous bhp is:
Low Range: Not Used
Mid-Low Range: 4.25 (208/230 and 460-v), 3.45 (575-v)
Mid-High Range: 5.75
High Range: 8.63
21

Table 8 -- Fan Performance -- 48HJD024 Vertical Discharge Units*
AIRFLOW
(Cfm)
5,000
5,500
6,000
6,500
7,000
7,500
8,000
8,500
9,000
9,500
10,000
AIRFLOW
(Cfm)
5,000
5,500
6,000
6,500
7,000
7,500
8,000
8,500
9,000
9,500
10,000
0.2 0.4 0.6 0.8 1.0
Rpm Watts Bhp Rpm Watts Bhp Rpm Watts Bhp Rpm Watts Bhp Rpm Watts Bhp
590 1276 1.47 683 1516 1.74 727 1745 2.01 788 1968 2.26 840 2189 2.52
633 1579 1.82 703 1838 2.11 764 2084 2.40 820 2324 2.67 872 2560 2.94
677 1925 2.21 744 2203 2.53 803 2467 2.84 857 2723 3.13 907 2974 3.42
722 2317 2.67 786 2614 3.01 842 2896 3.33 894 3167 3.64 942 3434 3.95
767 2758 3.17 828 3073 3.53 883 3371 3.88 933 3660 4.21 979 3942 4.53
813 3250 3.74 871 3582 4.12 924 3897 4.48 972 4202 4.83 1017 4500 5.18
859 3795 4.36 915 4143 4.77 966 4475 5.15 1012 4797 5.52 1056 5110 5.88
906 4394 5.05 959 4759 5.47 1008 5107 5.87 1053 5445 6.26 1096 5774 6.64
952 5051 5.81 1004 5432 6.25 1051 5797 6.67 1095 6150 7.07 1136 6494 7.47
999 5767 6.63 1049 6163 7.09 1094 6544 7.53 1137 6913 7.95 1177 7272 8.36
1047 6544 7.53 1094 6956 8.00 1138 7352 8.46 1180 7736 8.90 1219 8111 9.33
1.2 1.4 1.6 1.8 2.0
Rpm Watts Bhp Rpm Watts Bhp Rpm Watts Bhp Rpm Watts Bhp Rpm Watts Bhp
891 2408 2,77 940 2625 3,02 987 2843 3,27 1032 3060 3,52 1076 3277 3.77
921 2792 3.21 968 3024 3.48 1014 3255 3.74 1057 3485 4.01 1099 3716 4.27
954 3221 3.70 999 3467 3.99 1042 3711 4.27 1084 3955 4.55 1125 4198 4.83
988 3696 4.25 1032 3956 4.55 1073 4214 4.85 1114 4470 5.14 1153 4726 5.44
1024 4219 4.85 1066 4493 5.17 1106 4764 5.48 1145 5034 5.79 1183 5303 6.10
1060 4792 5.51 1101 5080 5.84 1140 5365 6.17 1178 5649 6.50 1215 5930 6.82
1098 5417 6.23 1138 5719 6.58 1176 6018 6.92 1213 6315 7.26 1249 6610 7.60
1137 6096 7.01 1175 6413 7.38 1212 6726 7.74 1248 7036 8.09 1283 7344 8.45
1176 6831 7.86 1214 7163 8.24 1250 7490 8.61 1285 7814 8.99 1319 8135 9.36
1216 7624 8.77 1253 7970 9.17 1288 8312 9.56 1322 8649 9.95 1355 8984 10.33
1256 8478 9.75 1292 8838 10.16 1327 9193 10.57 1360 9545 10.98 1393 9893 11.38
AVAILABLE EXTERNAL STATIC PRESSURE (in. wg)
AVAILABLE EXTERNAL STATIC PRESSURE (in. wg)
LEGEND
Bhp -- Brake Horsepower Input to Fan
Watts -- Input Watts to Motor
*Motor drive ranges:
Low Range: 685-939 (208/230 and 460-v), 751-954 (575-v)
Mid-Low Range: 949-1206
Mid-High Range: 941-1176
High Range: 1014-1297
All other rpms require field-supplied drive.
Refer to page 27 for general Fan Performance Data notes.
NOTE: Maximum continuous bhp is:
Low Range: 4.25 (208/230 and 460-v), 5.75 (575-v)
Mid-Low Range: 5.75
Mid-High Range: 8.63
High Range: 11.50
22

Table 9 -- Fan Performance -- 48HJE024 Vertical Discharge Units*
AIRFLOW
(Cfm)
5,000
5,500
6,000
6,500
7,000
7,500
8,000
8,500
9,000
9,500
10,000
AIRFLOW
(Cfm)
5,000
5,500
6,000
6,500
7,000
7,500
8,000
8,500
9,000
9,500
10,000
0.2 0.4 0.6 0.8 1.0
Rpm Watts Bhp Rpm Watts Bhp Rpm Watts Bhp Rpm Watts Bhp Rpm Watts Bhp
607 1329 1.53 677 1565 1.80 740 1791 2.06 797 2013 2.31 850 2231 2.57
652 1648 1.90 719 1902 2.19 779 2145 2.47 833 2382 2.74 884 2616 3.01
699 2013 2,32 763 2285 2.63 819 2545 2.93 872 2798 3,22 921 3046 3.50
746 2428 2,79 807 2716 3.12 861 2993 3.44 911 3262 3,75 958 3525 4.05
794 2895 3,33 851 3198 3.68 904 3491 4.02 952 3776 4,34 998 4055 4.66
842 3415 3,93 897 3735 4.30 947 4043 4.65 994 4343 5.00 1038 4637 5.33
891 3992 4,59 943 4327 4.98 991 4650 5.35 1036 4966 5,71 1079 5274 6.07
940 4628 5,32 990 4977 5.72 1036 5316 6.11 1080 5646 6.49 1121 5970 6.87
990 5325 6.12 1037 5688 6.54 1082 6042 6.95 1124 6386 7,35 1163 6724 7.73
1039 6085 7.00 1085 6462 7.43 1128 6829 7.85 1168 7188 8.27 1207 7541 8.67
1089 6911 7.95 1133 7301 8.40 1174 7682 8.83 1213 8055 9.26 1251 8421 9.69
1.2 1.4 1.6 1.8 2.0
Rpm Watts Bhp Rpm Watts Bhp Rpm Watts Bhp Rpm Watts Bhp Rpm Watts Bhp
900 2448 2,82 949 2664 3,06 995 2879 3.31 1040 3095 3.56 1083 3310 3.81
933 2847 3.27 979 3077 3.54 1023 3305 3.80 1066 3534 4.06 1108 3762 4.33
967 3292 3.79 1011 3535 4.07 1054 3778 4.35 1095 4019 4.62 1135 4260 4.90
1003 3785 4.35 1046 4043 4.65 1087 4298 4.94 1127 4553 5.24 1165 4806 5.53
1041 4330 4.98 1082 4601 5.29 1122 4870 5.60 1160 5138 5.91 1197 5404 6.22
1079 4926 5.67 1119 5212 5.99 1158 5495 6.32 1195 5776 6.64 1231 6055 6.96
1119 5578 6.42 1158 5878 6.76 1195 6174 7.10 1231 6468 7.44 1267 6761 7.78
1160 6288 7.23 1198 6601 7.59 1234 6912 7.95 1269 7219 8.30 1303 7524 8.65
1202 7056 8.12 1238 7384 8.49 1273 7708 8.87 1308 8029 9.23 1341 8347 9.60
1244 7887 9.07 1279 8228 9.46 1314 8566 9.85 1347 8900 10.24 1379 9231 10.62
1287 8781 10.10 1321 9137 10.51 1355 9488 10.91 1387 9836 11.31 -- -- --
AVAILABLE EXTERNAL STATIC PRESSURE (in. wg)
AVAILABLE EXTERNAL STATIC PRESSURE (in. wg)
LEGEND
Bhp -- Brake Horsepower Input to Fan
Watts -- Input Watts to Motor
*Motor drive ranges:
Low Range: 685-939 (208/230 and 460-v), 751-954 (575-v)
Mid-Low Range: 949-1206
Mid-High Range: 941-1176
High Range: 1014-1297
All other rpms require field-supplied drive.
Refer to page 27 for general Fan Performance Data notes.
NOTE: Maximum continuous bhp is:
Low Range: 4.25 (208/230 and 460-v), 5.75 (575-v)
Mid-Low Range: 5.75
Mid-High Range: 8.63
High Range: 11.50
23

Table 10 -- Fan Performance -- 48HJF024 Vertical Discharge Units*
AIRFLOW
(Cfm)
5,000
5,500
6,000
6,500
7,000
7,500
8,000
8,500
9,000
9,500
10,000
AIRFLOW
(Cfm)
5,000
5,500
6,000
6,500
7,000
7,500
8,000
8,500
9,000
9,500
10,000
0.2 0.4 0.6 0.8 1.0
Rpm Watts Bhp Rpm Watts Bhp Rpm Watts Bhp Rpm Watts Bhp Rpm Watts
607 1329 1.53 677 1565 1.80 740 1791 2.06 797 2013 2.31 850 2231
652 1648 1,90 719 1902 2.19 779 2145 2,47 833 2382 2.74 884 2616
699 2013 2,32 763 2285 2.63 819 2545 2,93 872 2798 3.22 921 3046
746 2428 2,79 807 2716 3.12 861 2993 3,44 911 3262 3.75 958 3525
794 2895 3,33 851 3198 3.68 904 3491 4,02 952 3776 4.34 998 4055
842 3415 3,93 897 3735 4.30 947 4043 4,65 994 4343 5.00 1038 4637
891 3992 4,59 943 4327 4.98 991 4650 5.35 1036 4966 5.71 1079 5274
940 4628 5.32 990 4977 5.72 1036 5316 6,11 1080 5646 6.49 1121 5970
990 5325 6,12 1037 5688 6,54 1082 6042 6.95 1124 6386 7.35 1163 6724
1039 6085 7.00 1085 6462 7.43 1128 6829 7.85 1168 7188 8.27 1207 7541
1089 6911 7.95 1133 7301 8.40 1174 7682 8.83 1213 8055 9.26 1251 8421
1.2 1.4 1.6 1.8 2.0
Rpm Watts Bhp Rpm Watts Bhp Rpm Watts Bhp Rpm Watts Bhp Rpm Watts
900 2448 2.82 949 2664 3.06 995 2879 3.31 1040 3095 3.56 1083 3310
933 2847 3.27 979 3077 3.54 1023 3305 3.80 1066 3534 4.06 1108 3762
967 3292 3.79 1011 3535 4.07 1054 3778 4.35 1095 4019 4.62 1135 4260
1003 3785 4.35 1046 4043 4.65 1087 4298 4.94 1127 4553 5.24 1165 4806
1041 4330 4.98 1082 4601 5.29 1122 4870 5.60 1160 5138 5.91 1197 5404
1079 4926 5.67 1119 5212 5.99 1158 5495 6.32 1195 5776 6.64 1231 6055
1119 5578 6.42 1158 5878 6.76 1195 6174 7.10 1231 6468 7.44 1267 6761
1160 6288 7.23 1198 6601 7.59 1234 6912 7.95 1269 7219 8.30 1303 7524
1202 7056 8.12 1238 7384 8.49 1273 7708 8.87 1308 8029 9.23 1341 8347
1244 7887 9.07 1279 8228 9.46 1314 8566 9.85 1347 8900 10.24 1379 9231
1287 8781 10.10 1321 9137 10.51 1355 9488 10.91 1387 9836 11.31 -- --
AVAILABLE EXTERNAL STATIC PRESSURE (in. wg)
AVAILABLE EXTERNAL STATIC PRESSURE (in. wg)
LEGEND
Bhp -- Brake Horsepower Input to Fan
Watts -- Input Watts to Motor
*Motor drive ranges:
Low Range: 685-939 (208/230 and 460-v), 751-954 (575-v)
Mid-Low Range: 949-1206
Mid-High Range: 941-1176
High Range: 1014-1297
All other rpms require field-supplied drive.
Bhp
2.57
3.01
3.50
4.05
4.66
5.33
6.07
6.87
7.73
8.67
9.69
Bhp
3.81
4.33
4.90
5.53
6.22
6.96
7.78
8.65
9.60
10.62
Refer to page 27 for general Fan Performance Data notes.
NOTE: Maximum continuous bhp is:
Low Range: 4.25 (208/230 and 460-v), 5.75 (575-v)
Mid-Low Range: 5.75
Mid-High Range: 8.63
High Range: 11.50
24

Table 11 -- Fan Performance -- 48HJD028 Vertical Discharge Units*
AIRFLOW
(Cfm)
6,500
7,000
7,500
8,000
8,500
9,000
9,500
10,000
10,500
11,000
11,500
12,000
12,500
AIRFLOW
(Cfm)
6,500
7,000
7,500
8,000
8,500
9,000
9,500
10,000
10,500
11,000
Rpm Watts Bhp Rpm Watts Bhp Rpm Watts Bhp Rpm Watts Bhp Rpm Watts Bhp
1033 6,108 7.03 1090 6,684 7.69 1132 7,105 8.17 1169 7,470 8.59 1203 7,813 8.99
1079 6,911 7.95 1137 7,550 8.68 1180 8,007 9.21 1216 8,399 9.66 1249 8,761 10.08
1126 7,773 8.94 1184 8,480 9.75 1227 8,978 10.33 1263 9,399 10.81 1296 9,782 11.25
1172 8,696 10.00 1232 9,475 10.90 1274 10,017 11.52 1310 10,468 12.04 1342 10,876 12.81
1219 9,681 11.13 1279 10,539 12.12 1322 11,127 12.80 1357 11,611 13.35 -- -- --
1268 10,732 12.34 1326 11,669 13.42 .........
1311 11,848 13.63 ............
Rpm Watts Bhp Rpm Watts Bhp Rpm Watts Bhp Rpm Watts Bhp Rpm Watts Bhp
1024 4,426 5.09 1066 4,760 5.48 1109 5,126 5.90 1153 5,524 6.35 1197 5,953 6.85
1063 5,026 5.78 1101 5,351 6.15 1141 5,702 6.56 1181 6,081 6.99 1222 6,490 7.46
1104 5,698 6.55 1140 6,020 6.92 1176 6,361 7.32 1213 6,727 7.74 1251 7,118 8.19
1146 6,443 7.41 1180 6,765 7.78 1214 7,103 8.17 1249 7,489 8.58 1283 7,837 9.01
1190 7,289 8.35 1222 7,886 8.73 1255 7,925 9.11 1287 8,276 9.52 1319 8,645 9.94
1235 8,148 9.37 1266 8,483 9.76 1296 8,824 10.15 1327 9,176 10.55 1357 9,541 10.97
1280 9,111 10.48 1310 9,456 10.88 1340 9,804 11.28 1369 10,158 11.68 1398 10,822 12.10
1326 10,147 11.67 1355 10,505 12.08 1384 10,862 12.49 ......
1372 11,259 12.95 ............
0.2 0.4 0.6 0.8 1.0
750 2,468 2.84 806 2,767 3.18 854 3,031 3.49 898 3,298 3.79 943 3,584 4.12
797 2,942 3.38 853 3,276 3.77 899 3,587 4.09 941 3,832 4.41 982 4,118 4.74
845 3,468 3.99 900 3,840 4.42 945 4,142 4.76 985 4,430 5.09 1024 4,721 5.43
892 4,045 4.65 948 4,462 5.13 991 4,789 5.51 1030 5,092 5.86 1067 5,391 6.20
939 4,677 5.38 995 5,141 5.91 1038 5,497 6.32 1076 5,818 6.69 1112 6,129 7.05
986 5,364 6.17 1042 5,882 6.76 1085 6,269 7.21 1122 6,611 7.60 1157 6,936 7.98
1.2 1.4 1.6 1.8 2.0
988 3,900 4.49 1035 4,250 4.89 1082 4,634 5.33 1130 5,053 5.81 1177 5,499 6.32
11,500
12,000
12,500
LEGEND
Bhp -- Brake Horsepower Input to Fan
Watts -- Input Watts to Motor
*Motor drive ranges:
Low Range: 687-873
Mid-Low Range: 805-1007
Mid-High Range: 941-1176
High Range: 1014-1297
All other rpms require field-supplied drive.
AVAILABLE EXTERNAL STATIC PRESSURE (in. wg)
AVAILABLE EXTERNAL STATIC PRESSURE (in. wg)
Refer to page 27 for general Fan Performance Data notes.
NOTE: Maximum continuous bhp is:
Low Range: 5.75
Mid-Low Range: 5.75
Mid-High Range: 8.63
High Range: 11.80
2.5

Table 12 -- Fan Performance -- 48HJE028 Vertical Discharge Units*
AIRFLOW
(Cfm)
6,500
7,000
7,500
8,000
8,500
9,000
9,500
10,000
10,500
11,000
11,500
12,000
Rpm Watts Bhp
1033 5,799 6.67 1076 6,191 7.12 1114 6,533 7.51 1148 6,856 7.89 1181 7,173 8.25
1085 6,640 7.64 1128 7,058 8.12 1164 7,421 8.54 1198 7,761 8.93 1229 8,091 9.31
1137 7,553 8.69 1179 8,000 9.20 1214 8,385 9.64 1247 8,741 10.05 1278 9,086 10.45
1190 8,542 9.82 1230 9,016 10.37 1265 9,424 10.84 1297 9,799 11.27 1327 10,158 11.68
1242 9,609 11.05 1282 10,111 11.63 1316 10,542 12.12 1347 10,937 12.58 1376 11,311 13.01
1294 10,756 12.37 1333 11,287 12.98 1367 11,741 13.50 ......
1347 11,985 13.78 ............
0.2
775 2,600 2.99
826 3,115 3.58
878 3,690 4.24
929 4,326 4.98
981 5,029 5.78 1026 5,395 6.20 1064 5,717 6.58 1100 6,025 6.93 1134 6,332 7.28
12,500
AIRFLOW
(Cfm)
6,500
7,000
7,500
8,000
8,500
9,000
9,500
10,000
10,500
Rpm Watts Bhp Rpm Watts Bhp Rpm Watts Bhp Rpm Watts Bhp Rpm Watts Bhp
1004 4,016 4.62 1050 4,374 5.03 1098 4,769 5.48 1145 5,195 5.97 1192 5646 6.49
1041 4,559 5.24 1083 4,902 5.64 1126 5,277 6.07 1170 5,685 6.54 1214 6122 7.04
1081 5,179 5.96 1120 5,512 6.34 1159 5,872 6.75 1199 6,261 7.20 1240 6680 7.68
1124 5,875 6.76 1160 6,203 7.13 1196 6,553 7.54 1233 6,928 7.97 1270 7329 8.43
1168 6,647 7.64 1202 6,974 8.02 1235 7,318 8.42 1269 7,684 8.84 1304 8071 9.28
1214 7,495 8.62 1245 7,825 9.00 1277 8,168 9.39 1309 8,527 9.81 1341 8905 10.24
1260 8,421 9.69 1290 8,756 10.07 1320 9,100 10.47 1351 9,457 10.88 1381 9830 11.31
1308 9,425 10.84 1337 9,768 11.23 1365 10,116 11.63 1394 10,474 12.05 -- -- --
1356 10,510 12.09 1384 10,862 12.49 .........
1.2 1.4 1.6 1.8 2.0
11,000
11,500
12,000
12,500
LEGEND
Bhp -- Brake Horsepower Input to Fan
Watts -- Input Watts to Motor
*Motor drive ranges:
Low Range: 687-873
Mid-Low Range: 805-1007
Mid-High Range: 941-1176
High Range: 1014-1297
All other rpms require field-supplied drive.
AVAILABLE EXTERNAL STATIC PRESSURE (in. wg)
0.4 0.6 0.8 1.0
Rpm Watts Bhp Rpm Watts Bhp Rpm Watts Bhp Rpm Watts Bhp
825 2,872 3.30 871 3,130 3.60 915 3,400 3.91 959 3,692 4.25
875 3,408 3.92 918 3,679 4.23 959 3,954 4.55 1000 4,245 4.88
925 4,006 4.61 966 4,292 4.94 1005 4,575 5.26 1043 4,868 5.60
975 4,667 5.37 1015 4,970 5.72 1052 5,265 6.06 1088 5,564 6.40
AVAILABLE EXTERNAL STATIC PRESSURE (in. wg)
Refer to page 27 for general Fan Performance Data notes.
NOTE: Maximum continuous bhp is:
Low Range: 5.75
Mid-Low Range: 5.75
Mid-High Range: 8.63
High Range: 11.50
26

Table 13 -- Fan Performance -- 48HJF028 Vertical Discharge Units*
AIRFLOW
(Cfm)
6,500
7,000
7,500
8,000
8,500
9,000
9,500
10,000
10,500
11,000
11,500
12,000
12,500
AIRFLOW
(Cfm)
6,500
7,000
7,500
8,000
8,500
9,000
9,500
10,000
10,500
11,000
11,500
12,000
12,500
Bhp -- Brake Horsepower Input to Fan
Watts -- Input Watts to Motor
*Motor drive ranges:
Low Range: 687-873
Mid-Low Range: 805-1007
Mid-High Range: 941-1176
High Range: 1014-1297
All other rpms require field-supplied drive.
Rpm Watts Bhp Rpm Watts Bhp Rpm Watts Bhp Rpm Watts Bhp Rpm Watts Bhp
1033 5,799 6.67 1076 6,191 7.12 1114 6,533 7.51 1148 6,856 7.89 1181 7,173 8.25
1085 6,640 7.64 1128 7,058 8.12 1164 7,421 8.54 1198 7,761 8.93 1229 8,091 9.31
1137 7,563 8.69 1179 8,000 9.20 1214 8,385 9.64 1247 8,741 10.06 1278 9,086 10.45
1190 8,542 9.82 1230 9,016 10.37 1265 9,424 10.84 1297 9,799 11.27 1327 10,158 11.68
1242 9,609 11.05 1282 10,111 11.63 1316 10,542 12.12 1347 10,937 12.68 1376 11,311 13.01
1294 10,756 12.37 1333 11,287 12.98 1367 11,741 13.50 ......
1347 11,985 13.78 ............
Rpm Watts Bhp Rpm Watts Bhp Rpm Watts Bhp Rpm Watts Bhp Rpm Watts Bhp
1004 4,016 4.62 1050 4,374 5.03 1098 4,769 5.48 1145 5,195 5.97 1192 5646 6.49
1041 4,559 5.24 1083 4,902 5.64 1126 5,277 6.07 1170 5,685 6.54 1214 6122 7.04
1081 5,179 5.96 1120 5,512 6.34 1159 5,872 6.75 1199 6,261 7.20 1240 6680 7.68
1124 5,875 6.76 1160 6,203 7.13 1196 6,553 7.54 1233 6,928 7.97 1270 7329 8.43
1168 6,647 7.64 1202 6,974 8.02 1235 7,318 8.42 1269 7,684 8.84 1304 8071 9.28
1214 7,495 8.62 1245 7,825 9.00 1277 8,168 9.39 1309 8,527 9.81 1341 8905 10.24
1260 8,421 9.69 1290 8,756 10.07 1320 9,100 10.47 1351 9,457 10.88 1381 9830 11.31
1308 9,425 10.84 1337 9,768 11.23 1365 10,116 11.63 1394 10,474 12.05 -- -- --
1356 10,510 12.09 1384 10,862 12.49 .........
0.2 0.4 0.6 0.8 1.0
775 2,600 2.99 825 2,872 3.30 871 3,130 3.60 915 3,400 3.91 959 3,692 4.25
826 3,115 3.58 875 3,408 3.92 918 3,679 4.23 959 3,954 4.55 1000 4,245 4.88
878 3,690 4.24 925 4,006 4.61 966 4,292 4.94 1005 4,575 5.26 1043 4,868 5.60
929 4,326 4.98 975 4,667 5.37 1015 4,970 5.72 1052 5,265 6.06 1088 5,664 6.40
981 5,029 5.78 1026 5,395 6.20 1064 5,717 6.58 1100 6,025 6.93 1134 6,332 7.28
1.2 1.4 1.6 1.8 2.0
LEGEND
AVAILABLE EXTERNAL STATIC PRESSURE (in. wg)
AVAILABLE EXTERNAL STATIC PRESSURE (in. wg)
Refer to this page for general Fan Performance Data notes.
NOTE: Maximum continuous bhp is:
Low Range: 5.75
Mid-Low Range: 5.75
Mid-High Range: 8.63
High Range: 11.60
GENERAL NOTES FOR TABLES 5-22
1. Static pressure losses (i.e., EconoMi$er IV) from Table 26 must
be added to external static pressure before entering Fan Per-
formance table.
2. Interpolation is permissible. Do not extrapolate.
3. Fan performance is based on wet coils, clean filters, and casing
losses. See Table 26 on page 39.
4. Extensive motor and drive testing on these units ensures that
the full horsepower and watts range of the motor can be utilized
with confidence. Using the fan motors up to the watts or bhp
rating shown will not result in nuisance tripping or premature
motor failure. Unit warranty will not be affected.
5. Use of a field-supplied motor may affect wire size. Contact your
Carrier representative for details.
27

AIRFLOW
(Cfm)
3,500
4,000
4,500
5,000
5,500
6,000
6,500
7,000
7,500
8,000
8,500
9,000
9,500
10,000
Table 14- Fan Performance- 48HJD020 Horizontal Discharge Units _'
EXTERNAL STATIC PRESSURE(in. wg)
0.2 0.4 0.6 0.8 1.0
Rpm Bhp Watts Rpm Bhp Watts Rpm Bhp Watts Rpm Bhp Watts Rpm Bhp Watts
635 1064 1.22 709 1278 1.47 776 1492 1.72 838 1708 1.96 896 1924 2.21
707 1402 1.61 773 1627 1.87 835 1853 2.13 892 2080 2.39 947 2307 2.65
780 1802 2.07 840 2037 2.34 897 2273 2.61 950 2510 2.89 1001 2465 2.84
853 2264 2.60 909 2510 2.89 961 2756 3.17 1011 2710 3.12 1059 3015 3.47
928 2794 3.21 979 3049 3.51 1028 3012 3.46 1075 3333 3.83 1120 3661 4.21
1003 3047 3.50 1051 3376 3.88 1096 3714 4.27 1140 4059 4.67 1182 4411 5.07
1079 3812 4.38 1123 4166 4.79 1166 4529 5.21 1207 4898 5.63 1247 5274 6.07
1155 4697 5.40 1196 5078 5.84 1236 5465 6.29 1275 5859 6.74 1313 6260 7.20
1231 5714 6.57 1270 6120 7.04 1308 6533 7.51 1345 6952 8.00 1381 7378 8.49
1308 6871 7.90 1344 7303 8.40 1380 7741 8.90 ......
1385 8177 9.40 ............
AIRFLOW
(Cfm)
3,500
4,000
4,500
5,000
5,500
6,000
6,500
7,000
7,500
8,000
8,500
9,000
9,500
10,000
Bhp -- Brake Horsepower Input to Fan
Watts -- Input Watts to Motor
*Motor drive ranges:
Low Range: Net Used
Mid-Low Range: 896-1227 (208/230 and 460-v), 863-1141 (575-v)
Mid-High Range: 1113-1414 (208/230 and 460-v), 1042-1285
(575-v)
High Range: 1096-1339
All other rpms require field-supplied drive.
Rpm Bhp Watts Rpm Bhp Watts Rpm Bhp Watts Rpm Bhp Watts Rpm Bhp Watts
951 2143 2.46 1003 2120 2.44 1052 2387 2.75 1100 2662 3.06 1148 2944 3.39
998 2535 2.92 1048 2548 2.93 1095 2835 3.26 1141 3129 3.60 1184 3432 3.95
1050 2756 3.17 1097 3055 3.51 1142 3363 3.87 1185 3878 4.23 1227 4001 4.60
1105 3329 3.83 1150 3651 4.20 1192 3979 4.58 1234 4315 4.96 1274 4658 5.36
1163 3997 4.60 1205 4342 4.99 1246 4692 5.40 1288 5051 5.81 1324 5415 6.23
1224 4771 5.49 1263 5138 5.91 1302 5511 6.34 1340 5892 6.78 1377 6278 7.22
1286 5658 6.51 1324 6048 6.96 1361 6445 7.41 1397 6847 7.87 -- -- --
1350 6668 7.67 1386 7081 8.14 .........
LEGEND
1.2 1.4 1.6 1.8 2.0
EXTERNAL STATIC PRESSURE (in. wg)
Refer to page 27 for general Fan Performance Data notes.
NOTE: Maximum continuous bhp is:
Low Range: Not Used
Mid-Low Range: 4.25 (208/230 and 460-v), 3.45 (575-v)
Mid-High Range: 5.75
High Range: 8.63
28

AIRFLOW
(Cfm)
3,500
4,000
4,500
5,000
5,500
6,000
6,500
7,000
7,500
8,000
8,500
9,000
9,500
10,000
Table 15- Fan Performance- 48HJE020 Horizontal Discharge Units*
EXTERNAL STATIC PRESSURE(in. wg)
0.2 0.4 0.6 0.8 1.0
Rpm Bhp Watts Rpm Bhp Watts Rpm Bhp Watts Rpm Bhp Watts Rpm Bhp Watts
645 1105 1.27 720 1329 1.53 788 1549 1.78 851 1767 2.03 910 1982 2.28
718 1454 1.67 785 1692 1.95 848 1926 2.22 906 2158 2.48 962 2388 2.75
792 1866 2.15 853 2117 2.43 911 2364 2.72 985 2609 3.00 1017 2583 2.97
887 2343 2.69 923 2605 3.00 977 2865 3.30 1027 2845 3.27 1078 3163 3.64
943 2889 3.32 995 3162 3.64 1044 3158 3.63 1092 3497 4.02 1138 3843 4.42
1019 3177 3.85 1067 3532 4.06 1113 3892 4.48 1158 4259 4.90 1201 4631 5.33
1096 3973 4.57 1141 4354 5.01 1184 4742 5.45 1226 5136 5.91 1267 5535 6.37
1173 4894 5.63 1215 5304 6.10 1256 5719 6.58 1295 6140 7.06 1334 6567 7.55
1250 5952 6.85 1290 6389 7.35 1328 6832 7.86 1366 7281 8.37 -- -- --
1328 7153 8.23 1365 7620 8.76 .........
AIRFLOW
(Cfm)
3,500
4,000
4,500
5,000
5,500
6,000
6,500
7,000
7,500
8,000
8,500
9,000
9,500
10,000
Bhp -- Brake Horsepower Input to Fan
Watts -- Input Watts to Motor
*Motor drive ranges:
Low Range: Not Used
Mid-Low Range: 896-1227 (208/230 and 460-v), 863-1141 (575-v)
Mid-High Range: 1113-1414 (208/230 and 460-v), 1042-1285
(575-v)
High Range: 1096-1339
All other rpms require field-supplied drive.
Rpm Bhp Watts Rpm Bhp Watts Rpm Bhp Watts Rpm Bhp Watts Rpm Bhp Watts
985 2195 2.53 1018 2181 2.51 1068 2442 2.81 1116 2708 3.11 1162 2979 3.43
1014 2364 2.72 1064 2644 3.04 1112 2930 3.37 1158 3221 3.70 1202 3517 4.05
1067 2882 3.31 1114 3187 3.67 1160 3498 4.02 1204 3814 4.39 1248 4135 4.76
1123 3489 4.01 1168 3820 4.39 1211 4156 4.78 1253 4497 5.17 1294 4844 5.57
1182 4194 4.82 1224 4551 5.23 1266 4913 5.65 1306 5280 6.07 1345 5652 6.50
1243 5008 5.76 1283 5391 6.20 1323 5779 6.65 1361 6172 7.10 1398 6569 7.56
1306 5939 6.83 1345 6349 7.30 1382 6763 7.78 ......
1371 6997 8.05 ............
LEGEND
1.2 1,4 1,6 1,8 2.0
EXTERNAL STATIC PRESSURE (in. wg)
Refer to page 27 for general Fan Performance Data notes.
NOTE: Maximum continuous bhp is:
Low Range: Not Used
Mid-Low Range: 4.25 (208/230 and 460-v), 3.45 (575-v)
Mid-High Range: 5.75
High Range: 8.63
29

AIRFLOW
(Cfm)
3,500
4,000
4,500
5,000
5,500
6,000
6,500
7,000
7,500
8,000
8,500
0,000
9,500
10,000
Table 16- Fan Performance- 48HJF020 Horizontal Discharge Units*
EXTERNAL STATIC PRESSURE(in. wg)
0.2 0.4 0.6 0.8 1.0
Rpm Bhp Watts Rpm Bhp Watts Rpm Bhp Watts Rpm Bhp Watts Rpm Bhp Watts
645 1105 1.27 720 1329 1.53 788 1549 1.78 851 1767 2.03 910 1982 2.28
718 1454 1.67 785 1692 1.95 848 1926 2.22 906 2158 2.48 962 2388 2.75
792 1866 2.15 853 2117 2.43 911 2364 2.72 965 2609 3.00 1017 2583 2.97
867 2343 2.69 923 2605 3.00 977 2865 3.30 1027 2845 3.27 1076 3163 3.64
943 2889 3.32 995 3162 3.64 1044 3158 3.63 1092 3497 4.02 1138 3843 4.42
1019 3177 3.65 1067 3532 4.06 1113 3892 4.48 1158 4259 4.90 1201 4631 5.33
1096 3973 4.57 1141 4354 5.01 1184 4742 5.45 1226 5136 5.91 1267 5535 6.37
1173 4894 5.63 1215 5304 6.10 1256 5719 6.58 1295 6140 7.06 1334 6567 7.55
1250 5952 6.85 1290 6389 7.35 1328 6832 7.86 1366 7281 8.37 -- -- --
1328 7153 8.23 1365 7620 8.76 .........
AIRFLOW
(Cfm)
3,500
4,000
4,500
5,000
5,500
6,000
6,500
7,000
7,500
8,000
8,500
0,000
9,500
10,000
Bhp -- Brake Horsepower Input to Fan
Watts -- Input Watts to Motor
*Motor drive ranges:
Low Range: Net Used
Mid-Low Range: 896-1227 (208/230 and 460-v), 863-1141 (575-v)
Mid-High Range: 1113-1414 (208/230 and 460-v), 1042-1285
(575-v)
High Range: 1096-1339
All other rpms require field-supplied drive.
Rpm Bhp Watts Rpm Bhp Watts Rpm Bhp Watts Rpm Bhp Watts Rpm Bhp Watts
965 2195 2.53 1018 2181 2.51 1068 2442 2.81 1116 2708 3.11 1162 2979 3.43
1014 2364 2.72 1064 2644 3.04 1112 2930 3.37 1158 3221 3.70 1202 3517 4.05
1067 2882 3.31 1114 3187 3.67 1160 3498 4.02 1204 3814 4.39 1246 4135 4.76
1123 3489 4.01 1168 3820 4.39 1211 4156 4.78 1253 4497 5.17 1294 4844 5.57
1182 4194 4.82 1224 4551 5.23 1266 4913 5.65 1306 5280 6.07 1345 5652 6.50
1243 5008 5.76 1283 5391 6.20 1323 5779 6.65 1361 6172 7.10 1398 6569 7.56
1306 5939 6.83 1345 6349 7.30 1382 6763 7.78 ......
1371 6997 8.05 ............
LEGEND
1.2 1.4 1.6 1.8 2.0
EXTERNAL STATIC PRESSURE (in. wg)
Refer to page 27 for general Fan Performance Data notes.
NOTE: Maximum continuous bhp is:
Low Range: Not Used
Mid-Low Range: 4.25 (208/230 and 460-v), 3.45 (575-v)
Mid-High Range: 5.75
High Range: 8.63
30

AIRFLOW
(Cfm)
3,500
4,000
4,500
5,000
5,500
6,000
6,500
7,000
7,500
8,000
8,500
9,000
9,500
10,000
Table 17 -- Fan Performance -- 48HJD024 Horizontal Discharge Units*
EXTERNAL STATIC PRESSURE(in. wg)
0.2 0.4 0.6 0.8 1.0
Rpm Bhp Watts Rpm Bhp Watts Rpm Bhp Watts Rpm Bhp Watts Rpm Bhp Watts
642 1082 1.24 714 1296 1.49 781 1510 1.74 843 1726 1.98 901 1943 2.23
714 1426 1.64 780 1651 1.90 841 1877 2.16 898 2103 2.42 982 2330 2.68
787 1831 2.11 847 2067 2.38 904 2303 2.65 957 2540 2.92 1008 2501 2.88
862 2301 2.65 917 2547 2.93 969 2793 3.21 1019 2755 3.17 1066 3062 3.52
937 2838 3.26 988 3094 3.56 1036 3067 3.53 1083 3390 3.90 1127 3719 4.28
1013 3113 3.58 1060 3445 3.96 1106 3783 4.35 1149 4130 4.75 1191 4484 5.16
1089 3893 4.48 1133 4250 4.89 1175 4615 5.31 1216 4986 5.73 1256 5364 6.17
1166 4798 5.52 1207 5181 5.96 1247 5570 6.41 1285 8965 6.86 1323 6369 7.32
1243 5837 6.71 1282 6244 7.18 1319 6658 7.66 1356 7080 8.14 1391 7507 8.63
1320 7017 8.07 1356 7450 8.57 1392 7890 9.08 ......
1398 8350 9.60 ............
AIRFLOW
(Cfm)
3,500
4,000
4,500
5,000
5,500
6,000
6,500
7,000
Rpm Bhp Watts Rpm Bhp Watts Rpm Bhp Watts Rpm Bhp Watts Rpm Bhp Watts
955 2160 2.48 1007 2142 2.46 1056 2409 2.77 1104 2684 3.09 1149 2968 3.41
1004 2299 2.64 1053 2578 2.96 1100 2865 3.29 1145 3160 3.63 1189 3463 3.98
1056 2793 3.21 1103 3093 3.56 1147 3402 3.91 1191 3718 4.28 1233 4041 4.65
1112 3376 3.88 1156 3699 4.25 1199 4029 4.63 1240 4366 5.02 1280 4710 5.42
1171 4057 4.67 1212 4402 5.06 1253 4754 5.47 1292 8114 5.88 1331 5480 6.30
1232 4848 5.57 1271 5213 6.00 1310 5588 6.43 1348 8970 6.87 1384 6358 7.31
1295 5749 6.61 1333 6141 7.06 1369 6538 7.52 ......
1360 6778 7.80 1396 7193 8.27 .........
1.2 1.4 1.6 1.8 2,0
7,500
8,000
8,500
9,000
9,500
10,000
LEGEND
Bhp -- Brake Horsepower Input to Fan
Watts -- Input Watts to Motor
*Motor drive ranges:
Low Range: Not Used
Mid-Low Range: 896-1227 (208/230 and 460-v), 873-1108 (575-v)
Mid-High Range: 1113-1414
High Range: 1096-1339
All other rpms require field-supplied drive.
EXTERNAL STATIC PRESSURE (in. wg)
Refer to page 27 for general Fan Performance Data notes.
NOTE: Maximum continuous bhp is:
Low Range: Not Used
Mid-Low Range: 4.26 (208/230 and 460-v), 5.75 (575-v)
Mid-High Range: 5.78
High Range: 8.63
3!

Table 18 -- Fan Performance -- 48HJE024 Horizontal Discharge Units*
AIRFLOW
(Cfm)
3,500
4,000
4,500
5,000
5,500
6,000
6,500
7,000
7,500
8,000
8,500
9,000
9,500
10,000
AIRFLOW
(Cfm)
3,500
4,000
4,500
5,000
5,500
6,000
6,500
7,000
7,500
8,000
8,500
9,000
9,500
10,000
Bhp -- Brake Horsepower Input to Fan
Watts -- Input Watts to Motor
*Motor drive ranges:
Low Range: Not Used
Mid-Low Range: 896-1227 (208/230 and 460-v), 873-1108 (575-v)
Mid-High Range: 1113-1414
High Range: 1096-1339
All other rpms require field-supplied drive.
Rpm Bhp Watts Rpm Bhp Watts Rpm Bhp Watts Rpm Bhp Watts Rpm Bhp Watts
652 1123 1.29 726 1347 1.55 793 1567 1.80 856 1784 2.05 914 2000 2.30
725 1479 1.70 792 1716 1.97 854 1950 2.24 912 2182 2.51 967 2412 2.77
800 1897 2.18 861 2148 2.47 918 2395 2.75 972 2639 3.04 1024 2620 3.01
875 2383 2.74 931 2645 3.04 984 2904 3.34 1035 2892 3.33 1083 3212 3.69
952 2937 3.38 1003 2883 3.32 1053 3217 3.70 1100 3558 4.09 1145 3905 4.49
1029 3249 3.74 1077 3605 4.15 1123 3966 4.56 1167 4334 4.98 1210 4707 5.41
1106 4061 4.67 1151 4445 5.11 1194 4834 5.56 1236 5229 6.01 1276 5629 6.47
1184 5003 5.75 1226 5414 6.23 1266 5831 6.71 1306 6253 7.19 1344 6681 7.68
1262 6083 7.00 1302 6522 7.50 1340 6967 8.01 1377 7417 8.53 -- -- --
1341 7312 8.41 1378 7779 8.95 .........
Rpm Bhp Watts Rpm Bhp Watts Rpm Bhp Watts Rpm Bhp Watts Rpm Bhp Watts
970 2213 2.55 1022 2203 2.53 1072 2464 2.83 1120 2730 3.14 1166 3002 3.45
1019 2393 2.75 1069 2673 3.07 1117 2959 3.40 1163 3251 3.74 1207 3548 4.08
1073 2920 3.36 1120 3226 3.71 1165 3537 4.07 1209 3854 4.43 1252 4176 4.80
1130 3537 4.07 1174 3870 4.45 1218 4207 4.84 1259 4549 5.23 1300 4896 5.63
1189 4257 4.90 1232 4614 5.31 1273 4977 5.72 1313 5345 6.15 1352 5719 6.58
1251 5086 5.85 1292 5469 6.29 1331 5859 6.74 1369 6253 7.19 -- -- --
1315 6035 6.94 1354 6446 7.41 1391 6861 7.89 ......
1381 7114 8.18 ............
LEGEND
0.2 0.4 0.6 0.8 1.0
1.2 1.4 1.6 1.8 2.0
EXTERNAL STATIC PRESSURE (in. wg)
EXTERNAL STATIC PRESSURE (in. wg)
Refer to page 27 for general Fan Performance Data notes.
NOTE: Maximum continuous bhp is:
Low Range: Not Used
Mid-Low Range: 4.25 (208/230 and 460-v), 5.75 (575-v)
Mid-High Range: 5.75
High Range: 8.63
32

AIRFLOW
(Cfm)
3,500
4,000
4,500
5,000
5,500
6,000
6,500
7,000
7,500
8,000
8,500
9,000
9,500
10,000
Table 19 -- Fan Performance- 48HJF024 Horizontal Discharge Units*
EXTERNAL STATIC PRESSURE (in. wg)
0.2 0.4 0.6 0.8 1.0
Rpm Bhp Watts Rpm Bhp Watts Rpm Bhp Watts Rpm Bhp Watts Rpm Bhp Watts
652 1123 1.29 726 1347 1.55 793 1567 1.80 856 1784 2.05 914 2000 2.30
725 1479 1.70 792 1716 1.97 854 1950 2.24 912 2182 2.51 967 2412 2.77
800 1897 2.18 861 2148 2.47 918 2395 2.75 972 2639 3.04 1024 2620 3.01
875 2383 2.74 931 2645 3.04 984 2904 3.34 1035 2892 3.33 1083 3212 3.69
952 2937 3.36 1003 2883 3.32 1053 3217 3.70 1100 3558 4.09 1145 3905 4.49
1029 3249 3.74 1077 3605 4.15 1123 3966 4.56 1167 4334 4.96 1210 4707 5.41
1106 4061 4.67 1151 4445 5.11 1194 4834 5.56 1236 5229 6.01 1276 5629 6.47
1184 5003 5.75 1226 5414 6.23 1266 5831 6.71 1306 6253 7.19 1344 6681 7.68
1262 6083 7.00 1302 6522 7.50 1340 6967 8.01 1377 7417 8.53 -- -- --
1341 7312 8.41 1378 7779 8.95 .........
AIRFLOW
(Cfm)
3,500
4,000
4,500
5,000
5,500
6,000
6,500
7,000
7,500
8,000
8,500
9,000
9,500
10,000
Bhp -- Brake Horsepower Input to Fan
Watts -- Input Watts to Motor
*Motor drive ranges:
Low Range: Not Used
Mid-Low Range: 896-1227 (208/230 and 460-v), 873-1108 (575-v)
Mid-High Range: 1113-1414
High Range: 1096-1339
All other rpms require field-supplied drive.
Rpm Bhp Watts Rpm Bhp Watts Rpm Bhp Watts Rpm Bhp Watts Rpm Bhp Watts
970 2213 2.55 1022 2203 2.53 1072 2464 2.83 1120 2730 3.14 1166 3002 3.45
1019 2393 2.75 1069 2673 3.07 1117 2959 3.40 1163 3251 3.74 1207 3548 4.08
1073 2920 3.36 1120 3226 3.71 1165 3537 4.07 1209 3854 4.43 1252 4176 4.80
1130 3537 4.07 1174 3870 4.45 1218 4207 4.84 1259 4549 5.23 1300 4896 5.63
1189 4257 4.90 1232 4614 5.31 1273 4977 5.72 1313 5345 6.15 1352 5719 6.56
1251 5086 5.85 1292 5469 6.29 1331 5859 6.74 1369 6253 7.19 -- -- --
1315 6035 6.94 1354 6446 7.41 1391 6861 7.89 ......
1381 7114 8.18 ............
LEGEND
1.2 1,4 1,6 1,8 2.0
EXTERNAL STATIC PRESSURE (in. wg)
Refer to page 27 for general Fan Performance Data notes.
NOTE: Maximum continuous bhp is:
Low Range: Not Used
Mid-Low Range: 4.25 (208/230 and 460-v), 5.75 (575-v)
Mid-High Range: 5.75
High Range: 8.63
33

AIRFLOW
(Cfm)
6,500
7,000
7,500
8,000
8,500
9,000
9,500
10,000
10,500
11,000
11,500
12,000
12,500
Table 20 -- Fan Performance -- 48HJD028 Horizontal Discharge Units*
EXTERNAL STATIC PRESSURE (in. wg)
0.2 0.4 0.6 0.8 1.0
Rpm Bhp Watts Rpm Bhp Watts Rpm Bhp Watts Rpm Bhp Watts Rpm Bhp Watts
786 2,658 3.06 819 2,835 3.26 857 3,052 3.51 899 3,304 3.80 943 3,586 4.12
842 3,208 3.69 871 3,386 3.89 905 3,599 4.14 943 3,847 4.42 983 4,123 4.74
898 3,827 4.40 925 4,006 4.61 955 4,217 4.85 989 4,460 5.13 1026 4,733 5.44
955 4,518 5.20 979 4,699 5.40 1007 4,908 5.65 1037 5,148 5.92 1070 5,416 6.23
1012 5,284 6.08 1034 5,466 6.29 1059 5,675 6.53 1087 5,912 6.80 1117 6,176 7.10
1069 6,127 7.05 1090 6,312 7.26 1113 6,521 7.50 1138 6,757 7.77 1165 7,017 8.07
1127 7,050 8.11 1146 7,238 8.32 1167 7,448 8.57 1190 7,682 8.84 1215 7,940 9.13
1184 8,057 9.27 1202 8,247 9.49 1221 8,460 9.73 1243 8,693 10.00 1266 8,948 10.29
1242 9,149 10.52 1258 9,344 10.75 1276 9,557 10.99 1296 9,791 11.26 1318 10,046 11.55
1299 10,331 11.88 1315 10,529 12.11 1332 10,745 12.36 1350 10,979 12.63 1370 11,232 12.92
1357 11,604 13.35 1372 11,806 13.58 .........
AIRFLOW
(Cfm)
6,500
7,000
7,500
8,000
8,500
9,000
9,500
10,000
10,500
11,000
11,500
12,000
12,500
Bhp -- Brake Horsepower Input to Fan
Watts -- Input Watts to Motor
*Motor drive ranges:
Low Range: 687-873
Mid-Low Range: 805-1007
Mid-High Range: 941-1176
High Range: 1014-1297
All other rpms require field-supplied drive.
Rpm Bhp Watts Rpm Bhp Watts Rpm Bhp Watts Rpm Bhp Watts Rpm Bhp Watts
988 3,900 4.49 1035 4,248 4.89 1082 4,632 5.33 1129 5,050 5.81 1177 5,499 6.32
1024 4,428 5.09 1066 4,760 5.48 1109 5,124 5.89 1153 5,521 6.35 1197 5,950 6.84
1063 5,031 5.79 1102 5,354 6.16 1141 5,703 6.56 1181 6,081 6.99 1221 6,487 7.46
1105 5,709 6.57 1140 6,025 6.93 1176 6,364 7.32 1213 6,729 7.74 1250 7,116 8.18
1149 6,465 7.44 1181 6,777 7.79 1215 7,109 8.18 1249 7,463 8.58 1283 7,838 9.02
1194 7,302 8.40 1225 7,608 8.75 1256 7,935 9.13 1287 8,282 9.53 1319 8,649 9.95
1242 8,222 9.46 1270 8,524 9.80 1298 8,847 10.17 1328 9,189 10.57 1358 9,548 10.98
1290 9,227 10.61 1316 9,525 10.96 1343 9,845 11.32 1370 10,181 11.71 1399 10,536 12.12
1340 10,321 11.87 1364 10,617 12.21 1389 10,932 12.57 ......
1391 11,505 13.23 ............
LEGEND
1.2 1.4 1.6 1.8 2.0
EXTERNAL STATIC PRESSURE (in. wg)
Refer to page 27 for general Fan Performance Data notes.
NOTE: Maximum continuous bhp is:
Low Range: 5.75
Mid-Low Range: 5.75
Mid-High Range: 8.63
High Range: 11.50
.34

AIRFLOW
(Cfm)
6,500
7,000
7,500
8,000
8,500
9,000
9,500
10,000
10,500
11,000
11,500
12,000
12,500
Table 21 -- Fan Performance -- 48HJE028 Horizontal Discharge Units*
EXTERNAL STATIC PRESSURE (in. wg)
0.2 0.4 0.6 0.8 1.0
Rpm Bhp Watts Rpm Bhp Watts Rpm Bhp Watts Rpm Bhp Watts Rpm Bhp Watts
799 2,730 3.14 833 2,914 3.35 872 3,135 3.61 914 3,392 3.90 958 3,687 4.24
856 3,294 3.79 887 3,481 4.00 921 3,699 4.25 958 3,950 4.54 999 4,235 4.87
913 3,929 4.52 941 4,118 4.74 972 4,335 4.99 1006 4,582 5.27 1042 4,860 5.59
971 4,637 5.33 996 4,829 5.55 1024 5,046 5.80 1055 5,290 6.08 1088 5,562 6.40
1029 5,421 6.24 1052 5,617 6.46 1078 5,835 6.71 1106 6,077 6.99 1136 6,345 7.30
1087 6,285 7.23 1108 6,484 7.46 1132 6,703 7.71 1158 6,946 7.99 1185 7,211 8.29
1145 7,231 8.32 1165 7,433 8.55 1187 7,655 8.80 1211 7,898 9.08 1236 8,161 9.39
1203 8,262 9.50 1222 8,468 9.74 1243 8,693 10.00 1265 8,936 10.28 1288 9,199 10.58
1261 9,381 10.79 1279 9,592 11.03 1299 9,820 11.29 1319 10,065 11.58 1341 10,327 11.88
1320 10,592 12.18 1337 10,807 12.43 1355 11,038 12.70 1374 11,284 12.98 1394 11,547 13.28
1378 11,896 13.68 ............
AIRFLOW
(Cfm)
6,500
7,000
7,500
8,000
8,500
9,000
9,500
10,000
10,500
Rpm Bhp Watts Rpm Bhp Watts Rpm Bhp Watts Rpm Bhp Watts Rpm Bhp Watts
1005 4,020 4.62 1052 4,390 5.05 1100 4,791 5.51 1148 5,221 6.00 1195 5673 6.52
1041 4,555 5.24 1084 4,908 5.64 1128 5,294 6.09 1172 5,710 6.57 1217 6153 7.08
1080 5,168 5.94 1119 5,508 6.33 1160 5,878 6.76 1201 6,279 7.22 1242 6708 7.71
1122 5,862 6.74 1158 6,190 7.12 1195 6,548 7.53 1233 6,934 7.97 1272 7347 8.45
1167 6,638 7.63 1200 6,959 8.00 1234 7,305 8.40 1269 7,677 8.83 1304 8076 9.29
1214 7,499 8.63 1244 7,813 8.99 1275 8,149 9.37 1308 8,511 9.79 1340 8896 10.23
1262 8,447 9.72 1290 8,754 10.07 1319 9,084 10.45 1349 9,437 10.85 1379 9812 11.28
1312 9,482 10.91 1338 9,785 11.25 1365 10,110 11.63 1392 10,454 12.02 -- -- --
1363 10,608 12.20 1387 10,909 12.55 .........
1.2 1.4 1.6 1.8 2.0
11,000
11,500
12,000
12,500
LEGEND
Bhp -- Brake Horsepower Input to Fan
Watts -- Input Watts to Motor
*Motor drive ranges:
Low Range: 687-873
Mid-Low Range: 805-1007
Mid-High Range: 941-1176
High Range: 1014-1297
All other rpms require field-supplied drive.
EXTERNAL STATIC PRESSURE (in. wg)
Refer to page 27 for general Fan Performance Data notes.
NOTE: Maximum continuous bhp is:
Low Range: 5.75
Mid-Low Range: 5.75
Mid-High Range: 8.63
High Range: 11.50
.35

AIRFLOW
(Cfm)
6,500
7,000
7,500
8,000
8,500
9,000
9,500
10,000
10,500
11,000
11,500
12,000
12,500
Table 22 -- Fan Performance -- 48HJF028 Horizontal Discharge Units*
EXTERNAL STATIC PRESSURE (in. wg)
0.2 0.4 0.6 0.8 1.0
Rpm Bhp Watts Rpm Bhp Watts Rpm Bhp Watts Rpm Bhp Watts Rpm Bhp Watts
799 2,730 3.14 833 2,914 3.35 872 3,135 3.61 914 3,392 3.90 958 3,687 4.24
856 3,294 3.79 887 3,481 4.00 921 3,699 4.25 958 3,950 4.54 999 4,235 4.87
913 3,929 4.52 941 4,118 4.74 972 4,335 4.99 1006 4,582 5.27 1042 4,860 5.59
971 4,637 5.33 996 4,829 5.55 1024 5,046 5.80 1055 5,290 6.08 1088 5,562 6.40
1029 5,421 6.24 1052 5,617 6.46 1078 5,835 6.71 1106 6,077 6.99 1136 6,345 7.30
1087 6,285 7.23 1108 6,484 7.46 1132 6,703 7.71 1158 6,946 7.99 1185 7,211 8.29
1145 7,231 8.32 1165 7,433 8.55 1187 7,655 8.80 1211 7,898 9.08 1236 8,161 9.39
1203 8,262 9.50 1222 8,468 9.74 1243 8,693 10.00 1265 8,936 10.28 1288 9,199 10.58
1261 9,381 10.79 1279 9,592 11.03 1299 9,820 11.29 1319 10,065 11.58 1341 10,327 11.88
1320 10,592 12.18 1337 10,807 12.43 1355 11,038 12.70 1374 11,284 12.98 1394 11,547 13.28
1378 11,896 13.68 ............
AIRFLOW
(Cfm)
6,500
7,000
7,500
8,000
8,500
9,000
9,500
10,000
10,500
11,000
11,500
12,000
12,500
Bhp -- Brake Horsepower Input to Fan
Watts -- Input Watts to Motor
*Motor drive ranges:
Low Range: 687-873
Mid-Low Range: 805-1007
Mid-High Range: 941-1176
High Range: 1014-1297
All other rpms require field-supplied drive.
AIRFLOW
(Ofm)
3250
3350
3450
3550
3650
3750
3850
3950
4050
4250
4450
4650
4850
5050
5250
5450
5650
5850
Bhp -- Brake Horsepower
ESP -- External Static Pressure (in. wg)
Rpm Bhp Watts Rpm Bhp Watts Rpm Bhp Watts Rpm Bhp Watts Rpm Bhp Watts
1005 4,020 4.62 1052 4,390 5.05 1100 4,791 5.51 1148 5,221 6.00 1195 5673 6.52
1041 4,555 5.24 1084 4,908 5.64 1128 5,294 6.09 1172 5,710 6.57 1217 6153 7.08
1080 5,168 5.94 1119 5,508 6.33 1160 5,878 6.76 1201 6,279 7.22 1242 6708 7.71
1122 5,862 6.74 1156 6,190 7.12 1195 6,548 7.53 1233 6,934 7.97 1272 7347 8.45
1167 6,638 7.63 1200 6,959 6.00 1234 7,305 6.40 1269 7,677 6.83 1304 6076 9.29
1214 7,499 6.63 1244 7,813 6.99 1275 6,149 9.37 1308 6,511 9.79 1340 6896 10.23
1262 6,447 9.72 1290 6,754 10.07 1319 9,084 10.45 1349 9,437 10.85 1379 9812 11.28
1312 9,482 10.91 1338 9,785 11.25 1365 10,110 11.63 1392 10,454 12.02 -- -- --
1363 10,608 12.20 1387 10,909 12.55 .........
LEGEND
ESP Bhp Watts ESP Bhp Watts
0.32 1.41 1580 0.70 1.49 1670
0.23 1.44 1610 0.63 1.52 1700
0.17 1.46 1635 0.59 1.55 1730
0.13 1.47 1645 0.56 1.56 1745
0.09 1.49 1665 0.53 1.58 1765
1.2 1.4 1.6 1.8 2.0
LOW SPEED
208 V 230,460,575 V
0.51 1.60 1790
0.48 1.62 1810
0.45 1.64 1835
0.40 1.67 1865
LEGEND
EXTERNAL STATIC PRESSURE (in. wg)
Refer to page 27 for general Fan Performance Data notes.
NOTE: Maximum continuous bhp is:
Low Range: 5.75
Mid-Low Range: 5.75
Mid-High Range: 8.63
High Range: 11.50
Table 23 -- Power Exhaust Fan Performance
MEDIUM SPEED
208 V 230,460,575 V
ESP Bhp Watts ESP Bhp Watts
0.60 1.51 1690 0.82 1.62 1810
0.55 1.54 1720 0.78 1.64 1840
0.49 1.56 1750 0.73 1.67 1870
0.43 1.59 1780 0.68 1.70 1900
0.39 1.62 1815 0.64 1.72 1930
0.33 1.64 1835 0.59 1.74 1950
0.27 1.66 1860 0.54 1.76 1975
0.22 1.68 1885 0.49 1.79 2000
0.17 1.74 1945 0.40 1.84 2060
0.00 1.79 2005 0.30 1.89 2115
0.22 1.94 2170
0.16 1.98 2215
0.12 2.02 2260
HIGH SPEED
208 V 230,460,575 V
ESP Bhp Watts ESP Bhp Watts
0.60 1.85 2070 0.73 1.99 2230
0.56 1.87 2095 0.69 2.01 2255
0.51 1.89 2120 0.65 2.04 2280
0.41 1.92 2145 0.56 2.06 2310
0.31 1.97 2205 0.47 2.12 2370
0.20 2.04 2280 0.37 2.19 2450
0.11 2.09 2335 0.30 2.24 2505
0.04 2.13 2385 0.23 2.28 2555
-- 0.17 2.33 2610
-- 0.12 2.38 2665
-- 0.07 2.40 2690
-- 0.04 2.42 2710
36

Table 24 -- Operation Air Quantity Limits
48HJ
Minimum
Cfm
Maximum
Cfm
GAS HEAT
High Heat (8 Cell)
COOLING
020
5,400 9,000 Medium Heat (8Cell)
Low Heat (5 Cell)
High Heat (8 Cell)
024 5,500 10,000 Medium Heat (8Cell)
Low Heat (5 Cell)
High Heat (8 Cell)
028 6,000 11,500 Medium Heat (8Cell)
Low Heat (5 Cell)
*7000 cfm minimum recommended above 1.0 in. wg external static pressure.
HEATING
(Nat. Gas, Vertical)
MINIMUM CFM
5_522
4,977
4,218
5,522
4,977
4,218
5,522
4,977
4,218
Table 25 -- Evaporator Fan Motor Specifications
UNIT DRIVE
Low
Mid-Low
Mid-High
High
48HJ020
Low
Mid-Low
Mid-High
High
LEGEND
BHP -- Brake Horsepower
BkW -- Brake Kilowatts
ORIENTATION
Vertical
Vertical
Vertical
Vertical
Horizontal
Horizontal
Horizontal
Horizontal
MOTOR
PIN
N/A
N/A
N/A
N/A
HD60FK651
HD60FK651
HD60FK651
HD58DL575
HD60FL650
HD60FL650
HD60FL650
HD60FL575
HD62FL650
HD62FL650
HD62FL650
HD62FL575
N/A
N/A
N/A
N/A
HD60FK651
HD60FK651
HD60FK651
HD58DL575
HD60FL650
HD60FL650
HD60FL650
HD60FL575
HD62FL650
HD62FL650
HD62FL650
HD62FL575
NOMINAL
HP
N/A
N/A
N/A
N/A
3.7
3.7
3.7
3
5
5
5
5
7.5
7.5
7.5
7.5
N/A
N/A
N/A
N/A
3.7
3.7
3.7
3
5
5
5
5
7.5
7.5
7.5
7.5
HEATING
(Nat. Gas, Horizontal)
MINIMUM CFM
5,522
4,977
4,218
5,522
4,977
4,218
5,470*
4,977*
4,218
VOLTAGE WATTS % BHP BkW AMPS
208 N/A N/A N/A N/A N/A
230 N/A N/A N/A N/A N/A
460 N/A N/A N/A N/A N/A
575 N/A N/A N/A N/A N/A
208 3698 85.8 4.25 3.17 10.6
230 3698 85.8 4.25 3.17 9.6
460 3698 85.8 4.25 3.17 4.8
575 3149 81.7 3.45 2.57 3.9
208 4900 87.5 5.75 4.29 16.7
230 4900 87.5 5.75 4.29 15.2
460 4900 87.5 5.75 4.29 7.6
575 4900 87.5 5.75 4.29 6.1
208 7267 88.5 8.63 6.43 24.2
230 7267 88.5 8.63 6.43 22
460 7267 88.5 8.63 6.43 11
575 7267 88.5 8.63 6.43 9
208 N/A N/A N/A N/A N/A
230 N/A N/A N/A N/A N/A
460 N/A N/A N/A N/A N/A
575 N/A N/A N/A N/A N/A
208 3698 85.8 4.25 3.17 10.6
230 3698 85.8 4.25 3.17 9.6
460 3698 85.8 4.25 3.17 4.8
575 3149 81.7 3.45 2.57 3.9
208 4900 87.5 5.75 4.29 16.7
230 4900 87.5 5.75 4.29 15.2
460 4900 87.5 5.75 4.29 7.6
575 4900 87.5 5.75 4.29 6.1
208 7267 88.5 8.63 6.43 24.2
230 7267 88.5 8.63 6.43 22
460 7267 88.5 8.63 6.43 11
575 7267 88.5 8.63 6.43 9
MAX EFFICIENCY MAX MAX MAX
HEATING
(Propane, Vertical)
MINIMUM CFM
5,522
4,480
4,218
5,522
4,480
4,218
5,522
4,480
4,218
HEATING
(Propane, Horizontal)
MINIMUM CFM
4,920
4,480
3,796
4,920
4,480
3,796
4,920*
4,480*
3,796
37

UNIT
48HJ024
48HJ028
BHP --
BkW --
DRIVE
Low
Mid-Low
Mid-High
High
Low
Mid-Low
Mid-High
High
Low
Mid-Low
Mid-High
High
Low
Mid-Low
Mid-High
High
LEGEND
Brake Horsepower
Brake Kilowatts
Table 25 -- Evaporator Fan Motor Specifications (cont)
ORIENTATION
Vertical
Vertical
Vertical
Vertical
Horizontal
Horizontal
Horizontal
Horizontal
Vertical
Vertical
Vertical
Vertical
Horizontal
Horizontal
Horizontal
Horizontal
MOTOR
PIN
HD60FK651
HD60FK651
HD60FK651
HD60FL575
HD60FL650
HD60FL650
HD60FL650
HD60FL575
HD62FL650
HD62FL650
HD62FL650
HD62FL575
HD64FL650
HD64FL650
HD64FL650
HD64FL575
N/A
N/A
N/A
N/A
HD60FK651
HD60FK651
HD60FK651
HD60FL575
HD60FL650
HD60FL650
HD60FL650
HD60FL575
HD62FL650
HD62FL650
HD62FL650
HD62FL575
HD60FL650
HD60FL650
HD60FL650
HD60FL575
HD60FL650
HD60FL650
HD60FL650
HD60FL575
HD62FL650
HD62FL650
HD62FL650
HD62FL575
HD64FL650
HD64FL650
HD64FL650
HD64FL575
HD60FL650
HD60FL650
HD60FL650
HD60FL575
HD60FL650
HD60FL650
HD60FL650
HD60FL575
HD62FL650
HD62FL650
HD62FL650
HD62FL575
HD64FL650
HD64FL650
HD64FL650
HD64FL575
NOMINAL
HP
3.7
3.7
3.7
5
5
5
5
5
7.5
7.5
7.5
7.5
10
10
10
10
N/A
N/A
N/A
N/A
3.7
3.7
3.7
5
5
5
5
5
7.5
7.5
7.5
7.5
5
5
5
5
5
5
5
5
7.5
7.5
7.5
7.5
10
10
10
10
5
5
5
5
5
5
5
5
7.5
7.5
7.5
7.5
10
10
10
10
VOLTAGE WATTS % BHP BkW AMPS
208 3698 85.8 4.25 3.17 10.6
230 3698 85.8 4.25 3.17 9.6
460 3698 85.8 4.25 3.17 4.8
575 4900 87.5 5.75 4.29 6.1
208 4900 87.5 5.75 4.29 16.7
230 4900 87.5 5.75 4.29 15.2
460 4900 87.5 5.75 4.29 7.6
575 4900 87.5 5.75 4.29 6.1
208 7267 88.5 8.63 6.43 24.2
230 7267 88.5 8.63 6.43 22
460 7267 88.5 8.63 6.43 11
575 7267 88.5 8.63 6.43 9
208 9582 89.5 11.5 8.58 30.8
230 9582 89.5 11.5 8.58 28
460 9582 89.5 11.5 8.58 14
575 9582 89.5 11.5 8.58 11
208 N/A N/A N/A N/A N/A
230 N/A N/A N/A N/A N/A
460 N/A N/A N/A N/A N/A
575 N/A N/A N/A N/A N/A
208 3698 85.8 4.25 3.17 10.6
230 3698 85.8 4.25 3.17 9.6
460 3698 85.8 4.25 3.17 4.8
575 4900 87.5 5.75 4.29 6.1
208 4900 87.5 5.75 4.29 16.7
230 4900 87.5 5.75 4.29 15.2
460 4900 87.5 5.75 4.29 7.6
575 4900 87.5 5.75 4.29 6.1
208 7267 88.5 8.63 6.43 24.2
230 7267 88.5 8.63 6.43 22
460 7267 88.5 8.63 6.43 11
575 7267 88.5 8.63 6.43 9
208 4900 87.5 5.75 4.29 16.7
230 4900 87.5 5.75 4.29 15.2
460 4900 87.5 5.75 4.29 7.6
575 4900 87.5 5.75 4.29 6.1
208 4900 87.5 5.75 4.29 16.7
230 4900 87.5 5.75 4.29 15.2
460 4900 87.5 5.75 4.29 7.6
575 4900 87.5 5.75 4.29 6.1
208 7267 88.5 8.63 6.43 24.2
230 7267 88.5 8.63 6.43 22
460 7267 88.5 8.63 6.43 11
575 7267 88.5 8.63 6.43 9
208 9582 89.5 11.5 8.58 30.8
230 9582 89.5 11.5 8.58 28
460 9582 89.5 11.5 8.58 14
575 9582 89.5 11.5 8.58 11
208 4900 87.5 5.75 4.29 16.7
230 4900 87.5 5.75 4.29 15.2
460 4900 87.5 5.75 4.29 7.6
575 4900 87.5 5.75 4.29 6.1
208 4900 87.5 5.75 4.29 16.7
230 4900 87.5 5.75 4.29 15.2
460 4900 87.5 5.75 4.29 7.6
575 4900 87.5 5.75 4.29 6.1
208 7267 88.5 8.63 6.43 24.2
230 7267 88.5 8.63 6.43 22
460 7267 88.5 8.63 6.43 11
575 7267 88.5 8.63 6.43 9
208 9582 89.5 11.5 8.58 30.8
230 9582 89.5 11.5 8.58 28
460 9582 89.5 11.5 8.58 14
575 9582 89.5 11.5 8.58 11
MAX EFFICIENCY MAX MAX MAX
38

48HJ
Low Range Vertical
Mid-Low Range Vertical
020
(208/230 and
460 volt)
020
(575 volt)
024
(208/230 and
460 volt)
024
(575 volt)
028
(all voltages)
Mid-High Range Vertical
High Range Vertical
Low Range Horizontal
Mid-Low Range Horizontal
Mid-High Range Horizontal
High Range Horizontal
Low Range Vertical
Mid-Low Range Vertical
Mid-High Range Vertical
High Range Vertical
Low Range Horizontal
Mid-Low Range Horizontal
Mid-High Range Horizontal
High Range Horizontal
Low Range Vertical
Mid-Low Range Vertical
Mid-High Range Vertical
High Range Vertical
Low Range Horizontal
Mid-Low Range Horizontal
Mid-High Range Horizontal
High Range Horizontal
Low Range Vertical
Mid-Low Range Vertical
Mid-High Range Vertical
High Range Vertical
Low Range Horizontal
Mid-Low Range Horizontal
Mid-High Range Horizontal
High Range Horizontal
Low Range Vertical
Mid-Low Range Vertical
Mid-High Range Vertical
High Range Vertical
Low Range Horizontal
Mid-Low Range Horizontal
Mid-High Range Horizontal
High Range Horizontal
*Approximate fan rpm shown.
Table 26 -- Accessory/FlOP EconoMi$er IV Static Pressure (in. wg)*
COMPONENT 8,000
EconoMi$er IV 0.10
CFM
COMPONENT8,500i9,000i9,500it0,00C; ,0,500i,,,000i,,,5001,2,000
EconoMi$er IV 0.11 0.12 0.13 0.15 0.16 0.17 0.19 0.20
LEGEND
FlOP -- Factory-installed Option
*The static pressure must be added to the external static pressure. The sum and the evapora-
tor entering-air cfm should then be used in conjunction with the Fan Performance tables to
determine blower rpm and watts.
Table 27 -- Fan Rpm at Motor Pulley Settings*
DRIVE
0 1_ 1 11_ 2 21_ 3 31_ 4 41_ 5 51_ 6
N/A N/A N/A N/A N/A N/A N/A N/A N/A N/A N/A N/A N/A
647 667 687 707 727 747 767 786 806 826 846 866 886
897 917 937 958 978 998 1018 1038 1058 1079 1099 1119 1139
1078 1094 1111 1127 1143 1160 1176 1192 1209 1225 1241 1258 1274
N/A N/A N/A N/A N/A N/A N/A N/A N/A N/A N/A N/A N/A
896 924 951 979 1006 1034 1062 1089 1117 1144 1172 1199 1227
1113 1138 1163 1188 1213 1238 1264 1289 1314 1339 1364 1389 1414
1096 1116 1137 1157 1177 1197 1218 1238 1258 1278 1299 1319 1339
N/A N/A N/A N/A N/A N/A N/A N/A N/A N/A N/A N/A N/A
810 832 854 876 897 919 941 963 985 1007 1028 1050 1072
873 893 912 932 951 971 991 1010 1030 1049 1069 1088 1108
1078 1094 1111 1127 1143 1160 1176 1192 1209 1225 1241 1258 1274
N/A N/A N/A N/A N/A N/A N/A N/A N/A N/A N/A N/A N/A
863 886 909 933 956 979 1002 1025 1048 1072 1095 1118 1141
1042 1062 1083 1103 1123 1143 1164 1184 1204 1224 1245 1265 1285
1096 1116 1137 1157 1177 1197 1218 1238 1258 1278 1299 1319 1339
685 706 727 749 770 791 812 833 854 876 897 918 939
949 970 992 1013 1035 1056 1078 1099 1120 1142 1163 1185 1206
941 981 980 1000 1019 1039 1059 1078 1098 1117 1137 1156 1176
1014 1038 1061 1085 1108 1132 1156 1179 1203 1226 1250 1273 1297
N/A N/A N/A N/A N/A N/A N/A N/A N/A N/A N/A N/A N/A
896 924 951 979 1006 1034 1062 1089 1117 1144 1172 1199 1227
1113 1138 1163 1188 1213 1238 1264 1289 1314 1339 1364 1389 1414
1096 1116 1137 1157 1177 1197 1218 1238 1258 1278 1299 1319 1339
751 768 785 802 819 836 853 869 886 903 920 937 954
949 970 992 1013 1035 1056 1078 1099 1120 1142 1163 1185 1206
941 981 980 1000 1019 1039 1059 1078 1098 1117 1137 1156 1176
1014 1038 1061 1085 1108 1132 1156 1179 1203 1226 1250 1273 1297
N/A N/A N/A N/A N/A N/A N/A N/A N/A N/A N/A N/A N/A
873 893 912 932 951 971 991 1010 1030 1049 1069 1088 1108
1113 1138 1163 1188 1213 1238 1264 1289 1314 1339 1364 1389 1414
1096 1116 1137 1157 1177 1197 1218 1238 1258 1278 1299 1319 1339
687 703 718 734 749 765 780 796 811 827 842 858 873
805 822 839 856 872 889 906 923 940 957 973 990 1007
941 981 980 1000 1019 1039 1059 1078 1098 1117 1137 1156 1176
1014 1038 1061 1085 1108 1132 1156 1179 1203 1226 1250 1273 1297
687 703 718 734 749 765 780 796 811 827 842 858 873
805 822 839 856 872 889 906 923 940 957 973 990 1007
941 981 980 1000 1019 1039 1059 1078 1098 1117 1137 1156 1176
1014 1038 1061 1085 1108 1132 1156 1179 1203 1226 1250 1273 1297
MOTOR PULLEY TURNS OPEN
39

Optional EconoMi$er IV -- SeeFig. 23 for EconoMi$er
IV component locations. The optional EconoMiSer IV comes
fiom the factory fully wiled and assembled. No field wMng or
assembly is requiled for stand;u'd outdoor dly bulb changeover
operation. Field wiring of accessory sensors is lequiled for
diffelent operational modes.
ECONOMISER IV STANDARD SENSORS
Outdoor Air Temperature (OAT) Sensor -- The outdoor air
temperature sensor (HH57AC074) is a 10 to 20 mA device
used to measure file outdoor-air temperatme. The outdoor-_dr
temperature is used to determine when the EconoMi$er W can
be used for free cooling. The sensor is factory-installed on the
EconoMi$er IV in the outdoor airstremn. See Fig. 24. The op-
erating range of temperature measurement is 40 to 100 E
Supply-Air Temperature _SAT) Sensor -- The supply-_dr
temperature sensor is a 3 K thermistor located at the outlet of
the indoor fan. See Fig. 24. This sensor is factory installed. The
operating range of temperature measurement is 0 ° to 158 E
The temperature sensor is a short probe with blue wires
running to it.
Outdoor Air Lockout Sensor -- The EconoMi$er IV is
equipped with an ambient temperature lockout switch located
in the outdoor ailstream which is used to lock out the compres-
sors below a 42 F ambient temperature.
ECONOMI$ER IV CONTROLLER WIRING AND OPER-
ATIONAL MODES -- Determine file EconoMiSer IV control
mode befole set up of the control. Some modes of operation may
require diffelent sensors. Refer to Table 28. The EconoMi$er IV
is supplied from the factory with a supply-air temperature
sensor _md an outdoor air temperature sensoc This allows for
operation of file EconoMiSer IV with outdoor air dly bulb
changeover control. Additional accessories can be added to
allow for different types of changeover control and operation
of the EconoMiSer IV and unit.
Outdoor Dry Bulb Changeover -- The standmd controller is
shipped from the factory configured for outdoor chT bulb
changeover control. The outdoor air and supply-air temperature
sensors abe included as stan&ud. For this control mode, the out-
door temperature is compmed to an adjustable set point selected
on the control. If the outdoor-air temperature is above the set
point, the EconoMiSer IV will adjust the outdoor-air dmnpers to
minimum position. If the outdoor-air temperature is below the
set point, file position of the outdoor-air dampel.s will be con-
trolled to provide fiee cooling using outdoor ail: When in this
mode, the LED next to the free cooling set point potentiometer
will be on. The changeover temperatme set point is controlled
by file free cooling set point potentiometer located on the con-
trol. The sc_de on the potentiometer is A, B, C, and D. See
Fig. 25 for the conesponding temperatme changeover values.
DAMPER
DAMPER
ACTUATOR
ECONOMIZER
BLOCKOFF
ASSEMBLY
WIRE
HARNESS
Fig. 23 -- EconoMi$er IV Component Locations (Exploded View)
4O

J
Fig. 24 -- Supply Air
Temperature Sensor Location
19
LED ION
17
18
16- - LED OFF _ LEDON
<15 _
E14 LED OFF-
13
12
11
10
9
40 45 58 55 68 65
DEGREES FAHRENHEIT
Fig. 25 -- Outdoor Air Temperature
Changeover Set Points
Differential Dry Bulb Control -- For differentkd ch-y bulb
control the stan&"ud outdoor dU bulb sensor is used in conjunc-
tion with an additiomd accesso U c_h7 bulb sensor (part number
CRTEMPSN002A00). The accesso U sensor must be mounted
in the return ail_tream. Wiring is provided in the EconoMiSer
IV wiling htuness. See Fig. 26.
In this mode of operation, the outdoor-tilt temperature is
compared to the return-air temperature and the lower tempera-
ture tfirstream is used for cooling. When using this mode of
_LED ON
_,< LED ON---
LED OFF _'_%.
70 75 80 85 90 95 100
I
changeover control, turn the enthalpy set point potentiometer
fully clockwise to the D setting.
Outdoor Enthalpy Changeover -- For enthalpy control, acces-
soU enthalpy sensor (p_u-t number HH57AC078) is lequired.
Replace the standard outdoor dU bulb temperature sensor with
the accesso U enthalpy sensor in the same mounting location.
When the outdoor air enthalpy rises above the outdoor enth_dpy
changeover set point, the outdoor-tilt dmnper moves to its mini-
mum position. The outdoor enth_dpy changeover set point is set
with the outdoor enthalpy set point potentiometer on the
EconoMiSer [V controller The set points are A, B, C, and D.
See Fig. 27. The factou-installed 620-ohm jumper must be in
place across termimds SR and + on the EconoMiSer IV control-
len See Fig. 26.
Differential Enthalpy Control -- For differential enthalpy
control, the EconoMiSer [V controller uses two enth_dpy
sensors (HH57AC078 and CRENTDIF004A00), one in the
outside air and one in the return air duct. The EconoMi$er IV
controller compales the outdoor tfir enthalpy to the return air
enth_dpy to determine EconoMi$er IV use. The controller
selects the lower enthalpy air (return or outdoor) for cooling.
For example, when the outdoor air has a lower enth_dpy than
the return tfir. the EconoMiSer IV opens to bring in outdoor air
for free cooling.
Replace file standard outside tfir dU bulb temperature
sensor with the accesso U enthalpy sensor in the same mount-
ing location. Mount the return air enth_dpy sensor in the return
tfir duct. Wiring is provided in the EconoMiSer IV wiring
harness. See Fig. 26. The outdoor enth_dpy changeover set
point is set with the outdoor enthalpy set point potentiometer
on the EconoMiSer IV controllel: When using this mode of
changeover control, turn the enthalpy set point potentiometer
fully clockwise to the D setting. See Fig. 28.
Indoor Air Quality (IAQ) Sensor [nput -- The IAQ input
can be used for demand control ventilation control based on the
level of CO 2 measured in the space or return _firduct.
Mount the optional IAQ sensor according to manufacturer
specifications. The IAQ sensor should be wired to the AQ and
AQI terminals of the controllen Adjust the DCV (demand
controlled ventilation) potentiometel.s to correspond to the
DCV voltage output of the indoor _fir qu_dity sensor at the
user-determined set point. See Fig. 29.
If a separate field-supplied transformer is used to power the
IAQ sensor, the sensor must not be grounded or the
EconoMi$er IV control board will be damaged.
Table 28 -- EconoMi$er IV Sensor Usage
APPLICATION DRY BULB SENSOR ENTHALPY SENSOR
Outdoor Air Dry Bulb None. The outdoor air dry bulb sensor is factory installed. CRTEMPSN002A00*
Differential Dry Bulb CRTEMPSN002A00* (2) CRTEMPSN002A00*
Single Enthalpy HH57AC078 None. The single enthalpy sensor is factory installed.
Differential Enthalpy and CRENTDIF004A00*
CO2 for DCV Control using a
Wall-Mounted CO2 Sensor
CO2 for DCV Control using a
Duct-Mounted CO2 Sensor
*CRENTDIF004A00 and CRTEMPSN002A00 accessories are used on many different base units. As such, these kits may contain parts that will
not be needed for installation.
1-33ZCSENCO2 is an accessory CO2sensor.
**33ZCASPCO2 is aR accessory aspirator box required for duct-mounted applications.
1-1-CRCBDIOX005A00 is an accessory that contains both 33ZCSENCO2 and 33ZCASPCO2 accessories.
ECONOMI$ER IV WITH OUTDOOR AIR ECONOMI$ER IV WITH SINGLE
Accessories Required Accessories Required
HH57AC078
CRENTDIF004A00*
33ZCSENCO2
aRd CRCBDIOX005A00tt
33ZCSENCO2_
33ZCASPCO2**
and CRCBDIOX005A00tt
33ZCSENCO27 _
33ZCASPCO2**
33ZCSENCO2
41

Exhaust Set Point Adjustment -- The exhaust set point will
determine when the exhaust fan runs based on dmnper position
(if accessory power exhaust is installed). The set point is modi-
fied with the Exhaust Fan Set Point (EXH SET) potentiometer
See Fig. 28. The set point represents the damper position above
which the exhaust fans will be turned on. When there is a call
for exhaust, the EconoMiSer IV controller provides a 45 _+15
second delay before exhaust fan activation to allow the damp-
ers to open. This delay _fllows file damper to reach the appro-
priate position to avoid unnecessary fan overload.
Minimum Position Control -- There is a minimum damper
position potentiometer on the EconoMiSer [V controllel: See
Fig. 28. The minimum damper position maintains the mini-
mum aidlow into the building during the occupied period.
When using demand ventilation, the minimum damper posi-
tion represents the minimum ventilation position for VOC (vola-
tile organic compounds) ventilation requirements. The maximum
demand ventilation position is used for lhlly occupied ventilation.
When demand ventilation control is not being used, the
minimum position potentiometer should be used to set the oc-
cupied ventilation position. The maximum demand ventilation
position should be turned fully clockwise.
Adjust the minimum position potentiometer to allow the
minimum mnount of outdoor ail: as required by local codes, to
enter the building. Make minimum position adjustments with
at least 10° F temperature difference between the outdoor and
return-air temperatures. To determine the minimum position
setting, perform the following procedure:
1. Calculate the appropriate mixed-air temperature using the
following formula::
OA RA T
(TO x I--T-_T) + (TR x I-T-_ ) = M
To = Outdoor-Air Temperature
OA = Percent of Outdoor Air
TR= Return-Air Temperature
RA = Percent of Return Air
TM = Mixed-Air Temperature
As tin example, if local codes require 10% outdoor air
dunng occupied conditions, outdoor-air temperature is
60 IF.and return-air temperature is 75 IF.
(60 x. 10) + (75 x .90) = 73.5 F
2. Disconnect the supply air sensor from terminals T and TI.
3. Ensure that the factory-installed jumper is in place across
terminals P and PI. If remote damper positioning is being
used, make sure that the termimfls are wired according to
Fig. 26 and that the minimum position potentiometer is
turned fully clockwise.
4. Connect 24 vac across termin_ds TR and TRI.
5. Cmefully adjust the minimum position potentiometer
until file measured mixed-air temperatme matches the
c_dculated v_due.
6. Reconnect the supply-air sensor to terminals T and TI.
Remote control of the EconoMiSer IV damper is desirable
when requiring additional temporary ventilation. If a field-
supplied remote potentiometer (Honeywell part number
$963B1128) is wired to the EconoMiSer IV controllel: the
minimum position of file dmnper can be controlled from a re-
mote location.
To control the minimum damper position remotely, remove
the factory-installed jumper on the P and PI tenninals on the
EconoMiSer IV controllel: Wire the field-supplied potentiome-
ter to the P and PI termimfls on the EconoMiSer IV controllel:
See Fig. 2(>.
SAT
DA ENTIIA!_Y IS INSTALLED
Fig. 26 -- EconoMiSer IV Wiring
__/HEN INSTi_-LIN6 IA ENTHALPY
IS DISCONNECTEDWHEN ACCY
LEGEND
IA -- Indoor Air
IAQ -- Indoor Air Quality
OA -- Outdoor Air
OAS -- Outdoor Air Temperature Sensor
PL -- Plug
RAS -- Return Air Temperature Sensor
SAT -- Supply Air Temperature Sensor
RETURN AIR SENSOR IENO_ 6L'0_2
RESISTOR BETWEEN SR+ & SR ANB
CDNNECT BLU ZORN VIES
42

85 90 95 100 105 110
(29) (32) (35) (38) (41) (43)
CONTROL CONTROL POINT
CURVE APPROX. °F (°C)
AT 50% RH
A 73123)
B 70 (21)
C 67(19)
D 63(17)
N
\
X
\
\\
-\
_x
\
35 40 45 50 55 60 65 70 75 80 85 90 95 100 105 110
(2) (4) (7) (10) (13) (16) (18) (21) (24) (27) (29) (32) (35) (38) (41) (43)
APPROXIMATE DRY BULB TEMPERATURE i F (C)
Fig. 27 -- Enthalpy Changeover Set Points
FAN SET POINT
LED Lt_
WHEN EXHAUST
CONTACT IS MADE
POSITION SETTING
DEMAND CONTROL
VENTILATION SET POINT
DEMAND CONTROL
VENTILATION INPUT
IS ABOVE SET POINT
VENTILATION SET POINT
LED LIGHTS WHEN
OUTDOOR AIR IS
SUITABLE FOR
FREE COOLING
CHANGEOVER SET POINT
ENTHALPY
Fig. 28 -- EconoMi$er IV Controller Potentiometer
and LED Locations
HIGH LIMIT
+900 ppm
+1100 ppm
_1000 ppm
o o
z
_o
LT_
Z
8
LU
L_
z
<
cc
\ CURVE
CO2 SENSOR MAX RANGE SEqq-ING
6000
5000
4000
3000
____.__ +800 ppm
2000
1000
0
2 3 4 5 6 7 8
DAMPER VOLTAGE FOR MAX VENTILATION RATE
Fig. 29 -- CO2Sensor Maximum Range Setting
43

Damper Movement -- Damper movement fiom full open to
full closed (or vice vel_a) takes up to 21/2 minutes.
Thermostats -- Tile EconoMi$er IV control woNs with con-
ventional thermostats that have a YI (cool stage 1), Y2 (cool
stage 2), WI (heat stage 1), W2 (heat stage 2), trod G (fan). The
EconoMi$er IV control does not support space temperature
sensol_ like the T55 or T56. Connections me made at the ther-
mostat terminal connection board located in the main control
box.
Occupancy Control -- The factory default configuration for
the EconoMiSer IV control is occupied mode. Occupied status
is provided by the black jumper from termimfl TR to termintfl
N. When unoccupied mode is desired, install a field-supplied
timeclock function in place of the jumper between TR and N.
See Fig. 26. When the timeclock contacts ale closed, the
EconoMi$er IV control will be in occupied mode. When the
timeclock contacts are open 0emoving the 24-v signtfl from
terminal N), the EconoMiSer IV will be in unoccupied mode.
Demand Control Ventilation -- When using the Econo-
MiSer IV for demand control ventilation, there are some equip-
ment selection criteria which should be considered. When
selecting the heat capacity and cool capacity of the equipment,
the maximum ventilation rote must be evaluated for design
conditions. The maximum &lmper position must be calculated
to provide the desired fresh ail:
Typictflly the maximum ventilation rate will be about 5 to
10% more than the typical cfm required per person, using nor-
mal outside air design criteria.
A proportional anticipatory strategy should be taken with
the following conditions: a zone with a large area, varied
occupancy, trod equipment that cannot exceed the required
ventilation rate fit design conditions. Exceeding the required
ventilation rote means the equipment can condition air at a
maximum ventilation rate that is greater than the required
ventilation rate for maximum occupancy. A proportional-
anticipatory strategy will cause the fresh air supplied to
increase as the room CO 2 level increases even though the CO 2
set point has not been reached. By the time the CO 2 level
reaches the set point, the damper will be fit maximum ventila-
tion and should maintain the set point.
In order to have the CO_ sensor control the economizer
dmnper in this manner, firs[ determine the &unper voltage
output for minimum or base ventilation. Base ventilation is the
ventilation required to remove contaminants during unoccu-
pied periods. The following equation may be used to determine
the percent of outside-air entering the building for a given
dmnper position. For best results there should be fit least a
10 degree difference in outside and return-air temperatures.
OA RA T
(To x l--i--_-) + (TR x l--i.-_- ) = M
To = Outdoor-Air Tempeiature
OA = Percent of Outdoor Air
TR= Return-Air Temperature
RA = Percent of Return Air
TM = Mixed-Air Temperature
Once base ventilation has been detemfined, set the mini-
mum dmnper position potentiometer to the correct position.
The stone equation can be used to determine the occupied or
maximum ventilation rate to the building. For example, an
output of 3.6 volts to the actuator provides a base ventilation
rate of 5% and an output of 6.7 volts provides the maximum
ventilation rate of 20% (or base plus 15 cfm per pelion). Use
Fig. 29 to determine the maximum setting of the CO 2 sensol:
For example, a 1100 ppm set point relates to a 15 cfm per
person design. Use the 1100 ppm curve on Fig. 29 to find the
point when the CO 2 sensor output will be 6.7 volts. Line up the
point on the giaph with the left side of the chart to determine
that the range configuration for the CO 2 sensor should be 1800
ppm. The EconoMiSer IV controller will output the 6.7 volts
from the CO 2 sensor to the actuator when the CO 2 concentra-
tion in the space is fit 1100 ppm. The DCV set point may be left
fit 2 volts since the CO 2 sensor voltage will be ignored by the
EconoMiSer IV controller until it rises above the 3.6 volt
setting of the minimum position potentiometel:
Once the fully occupied dmnper position has been deter-
mined, set the maximum dmnper demand control ventilation
potentiometer to this position. Do not set to the maximum
position as this can result in over-ventilation to the space and
potential high-humidity levels.
CO_2 Sensor Configuration -- The CO2 sensor has preset
standard voltage settings that can be selected anytime after the
sensor is powered up. See Table 29.
Use setting 1 or 2 for Carrier equipment. See Table 29.
1. Press Clear and Mode buttons. Hold fit least 5 seconds
until the sensor enters the Edit mode.
2. Press Mode twice. The STDSET Menu will appeal:
3. Use the Up/Down button to select the preset numbel: See
Table 29.
4. Press Enter to lock in file selection.
5. Press Mode to exit and resume normtfl operation.
The custom settings of the CO2 sensor can be changed any-
time after the sensor is energized. Follow the steps below to
change file non-stan&ud settings:
1. Press Clear and Mode buttons. Hold tit least 5 seconds
until the sensor enters the Edit mode.
2. Press Mode twice. The STDSET Menu will appeal:
3. Use the Up/Down button to toggle to the NONSTD menu
and press Entel:
4. Use the Up/Down button to toggle through each of the
nine variables, starting with Altitude, until file desired
setting is reached.
5. Press Mode to move through the variables.
6. Press Enter to lock in the selection, then press Mode to
continue to the next vmiable.
Dehumidification of Fresh Air with DCV Control -- Infor-
mation from ASHRAE (American Society of Heating,
Refrigeration, and Air Conditioning Engineers) indicates that
the largest humidity load on tiny zone is the fresh air intro-
ducedi For some applications, a device such as a 62AQ energy
recovery unit is added to reduce the moisture content of the
fresh air being brought into the building when the enthalpy is
high. In most cases, the normal heating and cooling processes
are more than adequate to remove the humidity loads for most
commercM applications.
If normal rooftop heating and cooling operation is not ade-
quate for the outdoor humidity level, an energy recovery unit
and/or a dehumidification option should be considered.
44

SETTING
1
2
3
4
5
6
7
8
9 Parking/Air Intakes/
LEGEND
ppm -- Parts Per Million
EQUIPMENT
Interface w/Standard
Building Control System
Economizer
Health & Safety
Loading Docks
Table 29 -- 002 Sensor Standard Settings
OUTPUT
Proportional
Proportional
Exponential
Proportional
Proportional
Exponential
Exponential
Proportional
Proportional
VENTILATION
RATE
(cfm/Pereon)
Any
Any
Any
15
20
15
20
ANALOG
OUTPUT
0-10V
4-20 mA
2-10V
7-20 mA
0-10V
4-20 mA
0-10V
4-20 mA
0-10V
4-20 mA
0-10V
4-20 mA
0-10V
4-20 mA
0-10V
4-20 mA
0-10V
4-20 mA
002
CONTROLRANGE
(ppm)
0-2000
0-2000
0-2000
0-1100
O- 900
0-1100
O- 900
0-9999
0-2000
OPTIONAL
RELAY SETPOINT
(ppm)
1000
1000
1100
1100
900
1100
900
5000
7OO
RELAY
HYSTERESIS
(ppm)
50
50
50
50
50
50
50
50O
50
Operating Sequence
COOLING. UNITS WITHOUT ECONOMIZER -- When
the thermostat calls for one stage of cooling, YI and G are en-
ergized. The indoor-fan contactor (IFC) and compressor con-
tactor(s) (C.AI and C.BI on three-compressor units or C.AI
only on two-compressor units), and outdoor-fan contactors
(OFCI and OFC2 when outdoor temperature is above LTS set-
ting) ale energized and the indoor-fan motol: compressor(s)
(AI and BI on three compressor units or AI only on two-
compressor units), and outdoor fans controlled by OFCI are
stalled. If the outdoor temperature is above the setting of the
low temperature switch, the outdoor fans controlled by OFC2
are _dso stmted.
If more cooling is required, the thermostat will call for a
second stage of cooling, energizing Y2. This will allow relay
CRI to energize, which in turn energizes the compressor
contactor (C.CI on three-compressor units or C.BI on
two-compressor units). The second stage compressor (CI on
three-compressor units or B I on two-compressor units is then
started.
HEATING, UNITS WITHOUT ECONOMIZER
NOTE: The 48HJ020-028 units have 2 stages of heat.
When the thermostat calls for heating, power is sent to W
on the [GC (integrated gas unit controller) board. An LED
(light-emitting diode) on the IGC bo_ud will be on during nor-
mal operation. A check is made to ensure that the rollout
switch and limit switch are closed and the induced-draft motor
is running. The induced-draft motor is then energized, and
when speed is proven with the hall effect sensor on the motor.
the ignition activation period begins. The burners will ignite
within 5 seconds.
If the burners do not light, there is a 22-second delay before
another 5-second attempt. If the burners still do not light, this
sequence is repeated for 15 minutes. After the 15 minutes have
elapsed, if the burners still have not lit, heating is locked out.
To reset the control, break 24-v power to the thermostat.
When ignition occurs the IGC board will continue to moni-
tor the condition of the rollout and limit switches, the hall effect
sensol: as well as the flame sensol: If the unit is controlled
through a room thermostat set for fan auto., 45 seconds after
ignition occurs, the indoor-fan motor will be energized (and the
outdoor-air dampers will open to their minimum position). If
for some reason the overtemperature limit opens prior to the
start of the indoor fan blower, on the next attempt, the
45-second delay will be shortened to 5 seconds less than the
time from initiation of heat to when the limit tripped. Gas will
not be interrupted to the burners and heating will continue.
Once modified, the fan on delay will not change back to
45 seconds unless power is reset to the control.
When additional heat is required, W2 closes and initiates
power to the second stage of the main gas valve. When the
thermostat is satisfied, WI and W2 open and the gas valve
closes, interrupting the flow of gas to the main burners. If the
call forWl lasted less than 1 minute, the heating cycle will not
terminate until 1 minute after WI became active. If the unit is
controlled through a room thermostat set for fan auto., the
indoor-fan motor will continue to operate for an additional
45 seconds then stop (and the outdoor-air dampers will close).
If the overtemperatme limit opens after the indoor motor is
stopped within 10 minutes of WI becoming inactive, on the
next cycle the time will be extended by 15 seconds. The
maximum delay is 3 minutes. Once modified, the fan off delay
will not change back to 45 seconds unless power is reset to
the control.
A LED indicator is provided on the IGC to monitor opera-
tion. The IGC is located by removing the side panel and view-
ing the [GC through the view port located in the control box
access panel. During norm;d operation, the LED is continuous-
ly on. For information on troubleshooting refer to page 56.
COOLING. UNITS WITH ECONOMISER IV -- When free
cooling is not available, the compressors will be controlled by
the zone thermostat. When free cooling is available, the
outdoor-air damper is modulated by the EconoMiSer IV con-
trol to provide a 50 to 55 F supply-air temperature into the
zone. As the supply-air temperature fluctuates above 55 or
below 50 E the dampers will be modulated (open or close) to
bring the supply-air temperature back within the set point
limits.
For EconoMi$er IV operation, there must be a thermostat
call for the fan (G). This will move the &{mper to its minimum
position during the occupied mode.
Above 50 F supply-air temperature, the dampers will modu-
late from 100% open to the minimum open position. From 50 F
to 45 F supply-tdr temperature, the dampers will maintain at
the minimum open position. Below 45 F the &tmpers will be
completely shut. As the supply-air temperature rises, the &{top-
ers will come back open to the minimum open position once
the supply air temperature rises to 48 E
45

If optionalpowerexhaustisinstalled,astheoutdoor-air
damperopensandcloses,thepowerexhaustfanswillbeener-
gizedanddeenergized.
Iffield-inst_dledaccessoryCO2sensorsaleconnectedtothe
EconoMi$erIVcontrol,ademandcontrolledventilationstlate-
gywillbegintooperate.AstheCO2levelinthezoneincreases
abovetheCO2setpoint,fileminimumpositionofthedamper
willbeincreasedproportionally.AsfileCO2leveldecreases
becauseoftheincreaseinfleshair.theoutdoor-airdamperwill
beproportionallyclosed.Damperpositionwillfollowthehigh-
erdemandconditionfromDCVmodeorfreecoolingmode.
Dampermovementfromfullclosedtofullopen(orvice
versa)willtakebetween1112and2112minutes.
Iffieecoolingcanbe used as determined fiom file appropri-
ate changeover command (switch, dry bulb, enthalpy curve,
differential dry bulb, or differential enthalpy), a call for cooling
(YI closes at the thermostat) will cause the control to modulate
the dampers open to maintain the supply air temperature set
point at 50 to 55 E
As the supply-air temperature drops below the set point
range of 50 to 55 E the control will modulate the outdoor-air
dmnpers closed to maintain the proper supply-air temperature.
HEATING. UNITS WITH ECONOMI$ER IV -- When the
room temperature calls for heat, file heating controls am ene>
gized as described in the Heating, Units Without Economizer
section. The IFM (indoor fan motor) is energized and the
EconoMiSer IV damper modulates to the minimum position.
When the thermostat is satisfied and WI and W2 ale deener-
gized, the IFM continues to run, and file economizer damper
modulates to the minimum position.
SERVICE
Before performing service or maintenance operations on
unit, turn off main power switch to unit. Electrical shock
could cause personal injury.
Cleaning -- Inspect unit interior at beginning of each heat-
ing and cooling season and as operating conditions require. Re-
move unit top panel and/or side panels for access to unit interiol:
EVAPORATOR COIL -- Clean as required with commerci_d
coil cleanel:
CONDENSER COIL--Clean condenser coil annu_dly and
as required by location and outdoo>air conditions. Inspect coil
monflfly; clean as required.
CONDENSATE DRAIN -- Check and clean each year at the
st_u'tof the cooling season. In winter, keep drains and traps dry.
An access panel is located above the condensate connection to
allow easy clean out of the condensate pan. Tile first time the
panel is removed, file insulation behind the access panel will
need to be cut away. Carefully cut file insulation with a knife or
blade on three sides so the insulation can be folded out of the
way during cleaning. Be careful not to damage components be-
hind the insulation while cutting. Once cleaning is completed,
fold the insulation back into place and secure the access panel
in the original position.
FILTERS -- Clean or replace at stalt of each heating and cool-
ing season, or more often if operating conditions require. Refer
to Table 1 for type and size.
OUTDOOR-AIR INLET SCREENS -- Clean screens with
steam or hot water and a mild detergent. Do not use throwaway
filters in place of screens. See Table 1 for quantity and size.
MAIN BURNER -- At file beginning of each heating season,
inspect for deterioration or blockage due to corrosion or other
causes. Observe the main burner flames. Refer to Main Burn-
ers section on page 48.
FLUE GAS PASSAGEWAYS -- Tile flue collector box and
heat exchanger cells may be inspected by removing heat
section access panel (Fig. 4), flue box cover, and main burner
assembly (Fig. 30). Refer to Main Burners section on page 48
for burner removed sequence. If cleaning is required, clean
tubes with a wire brush.
Use c_mtion with ceramic heat exchanger baffles. When in-
stalling retaining clip, be sure file center leg of the clip extends
inward toward baffle. See Fig. 31.
COMBUSTION-AIR BLOWER -- Clean periodic_dly to as-
sure proper airflow and heating efficiency. Inspect blower
wheel every fgdland periodically during heating season. For the
first heating season, inspect blower wheel bi-monfllly to deter-
mine proper cleaning frequency.
To inspect blower wheel, remove heat section panel. Using
an inspection mirror and flashlight, look into the flue exhaust
duct to inspect file wheel. If cleaning is required, remove motor
and wheel assembly by removing the screws holding the flue
box cover to the flue box. See Fig. 30. Remove the screws
holding the inducer housing to the inlet plate. The wheel can
then be removed fiom the motor shaft and cleaned with a deter-
gent or solvent. Replace the wheel onto the motor shaft in the
correct position and reassemble the flue cover onto the flue
box.
Lubrication
COMPRESSORS- Each compressor is chguged with the
correct amount of oil al the factory. Conventional white oil
(Zerol 150T or Sontex SA32) is used. White oil is compatible
wifll 3GS oil, and 3GS oil may be used if the addition of oil is
required. See compressor nameplate for original oil charge. Oil
mchguge amount is shown in Table 1. When a compressor is
exchanged in the field it is possible that a major portion of the
oil fiom the replaced compressor may still be in the system.
While this will not affect the reliability of the replacement
compressor, tile extra oil will add rotor drag and increase pow-
er usage. To lemove this excess oil, an access valve may be
added to the lower portion of the suction line at the inlet of the
compmssoc The compressor should then be run for 10 min-
utes, shut down and the access valve opened until no oil flows.
This should be repeated twice to make sure the proper oil level
has been achieved.
FAN SHAFT BEARINGS -- Lubricate bearings at least ev-
ely 6 months with suitable bearing grease. Typical lubricants
are given below:
MANUFACTURER LUBRICANT
Texaco Regal AFB-2*
Mobil Mobilplex EP No. 1
Sunoco Prestige 42
Texaco Multifak 2
*Preferred lubricant because it contains rust and oxidation inhibitors.
CONDENSER AND EVAPORATOR-FAN MOTOR
BEARINGS- The condenser and evaporator-fan motors
have permanently sealed bearings, so no field lubrication is
necessary.
46

COMBUSTION
HEAT
EXCHANGER
SECTION
IGC BOARD
(HIDDEN)
/ :[_]
7
MAIN BURNER IGC -- Integrated Gas
SECTION Controller
-FAN HOUSING
INDUCED
DRAFT
MOTOR
MAIN GAS
VALVE
Fig. 30 -- Typical Gas Heating Section
CERAMIC
BAFFLE
CLIP x_
NOTE: One baffle and clip will be in each upper tube of the heat
exchanger.
Fig. 31 -- Removing Heat Exchanger Ceramic
Baffles and Clips
Evaporator Fan Service and Replacement-- The
48HJ units feature a slide-out fan deck for easy servicing of the
indoor-fan motol: pulleys, belt, and bearings. To service com-
ponents in this section, perform the following procedure:
1. Turnoffunit powel:
2. Open the fan section access panel.
3. Remove three no. 10 screws at fiont of slide-out fan deck.
Save screws. See Fig. 32.
4. Disconnect the electrical plugs and wires connected to the
slide-out fan deck (evaporator fan plug, supply air ther-
mistol: and fan status switch if installed). Wires may be
damaged if not disconnected.
5. Fan deck can now be slid out to access serviceable
components.
DO NOT SLIDE FAN DECK OUT PAST THE STOP
BRACKET. ff lurther access is required, the fan deck must
be suppolled. Make sure plugs and wiring are not pinched
between fan housing and unit center post. Damage to unit
may result.
6. To replace fan deck to operating position, slide fan deck
back into the unit. Secure with the three no. 10 screws
removed in Step 3.
7. Re-attach electric_d plugs and wires.
8. Close fan section access dooc
9. Restore power to unit.
Evaporator Fan Performance Adjustment
(Fig. 32 and 33) -- Fan motor pulleys are factory set
for speed shown in Table 1.
To change fan speeds:
1. Shut offunit power supply.
2. Ix_osen nuts on the 4 ctu'riage bolts in the mounting base.
Using adjusting bolts and plate, slide motor and remove
belt.
3. Ix_osen movable-pulley flange setscrew (see Fig. 33).
4. Screw movable flange towtud fixed flange to increase
speed and away fi_m fixed flange to decrease speed. In-
creasing fan speed increases load on motol: Do not ex-
ceed maximum speed specified in Table 1.
See Table 24 for air quantity limits.
5. Set movable flange at nearest keyway of pulley hub and
tighten setscrew. (See Table 1 for speed change for each
lull turn of pulley flange.)
6. Replace and tighten belts (see Belt Tension Adjustment
section below).
7. Restore power to unit.
To align fan and motor pulleys:
1. Ix_osen fan pulley setscrews.
2. Slide fan pulley along fan shaft.
3. Make angultu" alignment by loosening motor from
mounting plate.
Belt Tension Adjustment -- To adjust belt tension:
1. Turn off unit power
2. Slide out fan deck to service position as shown in Evapo-
rator Fan Service and Replacement section above.
3. Ix_osen fan motor bolts.
4. Move motor mounting plate to adjust to proper belt ten-
sion. See Table 30. Motor adjuster bolts may be used to
tighten belts. See Fig. 32.
5. Check for proper belt alignment. Adjust if necessary.
6. Tighten motor mounting plate bolts to lock motor in
proper position.
7. Return fan deck back into operating position.
8. Restore power to unit.
Table 30 -- Belt Tension Adjustment
BELT TENSION (Ib)
48HJ VOLTAGE
208/230
020 460
575
208/230 4.8
024 460 4.8
575 5.3
208/230 4.5
028 460 4.5
575 4.5
LEGEND
N/A -- Not Available
Unit Model Number Position 10
A,J B,K C,L D,M E,N F,P G,Q H,R
N/A 4.9 5.1 5.7 N/A 4.7 5.0 5.5
N/A 4.9 5.1 5.7 N/A 4.7 5.0 5.5
N/A 3.9 5.2 5.7 N/A 3.8 4.7 5.5
5.1 5.8 4.5 N/A 4.7 5.0 5.5
5.1 5.8 4.5 N/A 4.7 5.0 5.5
5.1 5.6 4.5 N/A 5.2 5.0 5.5
5.4 5.9 4.5 4.5 5.4 5.9 4.5
5.4 5.9 4.5 4.5 5.4 5.9 4.5
5.4 5.9 4.5 4.5 5.4 5.9 4.5
Condenser-Fan Adjustment (Fig. 34)
1. Shut off unit power supply.
2.
Remove condenser-fan assembly (grille, motor, motor
cover, and fan) and loosen fan hub setscrews.
3. Adjust fan height as shown in Fig. 34.
4. Tighten setscrews and replace condenser-fan assembly.
5. Turn on powerto unit.
47

MOTOR
FAN
PULLEY
- PULLEY
(HIDDEN)
- MOTOR
MOUNTING
- BASE
SLIDE-OUT
FAN DECK
Fig. 32 -- Evaporator-Fan Motor Adjustment
STRAIGHTEDGE MUST
WITH BELT
PULLEY
MOVABLE
FLANGES
PULLEY
MOTOR AND FAN
SHAFTS MUST BE
PARALLEL
SETSCREWS_
FIXED FLANGES
SINGLE-GROOVE
Fig. 33 -- Evaporator-Fan Alignment and
Adjustment
T , v ,
Fig. 34 -- Condenser-Fan Adjustment
Power Failure -- Dampers have a spring return. [n event
of power failure, dampers will return to fully closed position
until power is restored. Do not manually operate damt)er
I'IION)K
Refrigerant Charge -- Amount of refiigerant ch;uge is
listed on unit nameplate and in Table 1. Refer to Career GTAC
II; Module 5; Chmging, Recovery, Recycling, and Reclamation
section for charging methods and procedures. Unit panels must
be in place when unit is operating during charging procedure.
NOTE: Do not use recycled refrigerant as it may cont;fin
contaminants.
NO CHARGE -- Use standard evacuating techniques. After
evacuating system, weigh in the specified amount of refriger-
ant (refer to Table 1).
LOW CHARGE COOLING -- Using cooling charging chaff
(see Fig. 35-37), add or remove refrigerant until conditions of
the chaff are met. An accurate pressure gage and temperature-
sensing device is required. Charging is accomplished by ensur-
ing the proper amount of liquid subcooling. Measure liquid line
pressure at the liquid line service valve using pressure gage.
Connect temperature sensing device to the liquid line netu the
liquid line service valve and insulate it so that outdoor ambient
temperature does not affect reading.
TO USE THE COOLING CHARGING CHART -- Use the
above temperature and pressure readings, and find the intersec-
tion point on the cooling charging chart. If intersection point on
chmt is above line, add refrigerant. If intersection point on
chtut is below line, carefully recover some of the charge. Re-
check suction pressme as charge is adjusted.
NOTE: Indoor-air cfin must be within normal operating range
of unit. All outdoor fans must be operating.
The TXV (thermostatic expansion valve) is set to maintain
between 10 and 15 degrees of supeflleat at the compressors.
The valves are factory set and should not requile le-adjustment.
Gas Valve Adjustment
NATURAL GAS- The gas valve opens and closes in re-
sponse to the thermostat or limit control.
When power is supplied to valve terminals W2 (High Fire)
and C l, the main valve opens to its preset position.
The regular factory setting is stalnped on the valve body.
The setting is 3.00 in. wg for vertical supply/dischalge units.
The setting is 2.95 in. wg for horizont_d supply/discharge units.
To adjust regulator:
1. Set unit at setting for no call for heat.
2. Turn main gas valve to OFF position.
3. Remove l/a-in, pipe plug from manifold or gas valve
pressure tap connection. Install a suitable pressure-
measuring device.
4. Set main gas valve to ON position.
5. Set thennostat at setting to call for heat.
6. Remove screw cap covering regulator adjustment screw
(See Fig. 38).
7. Turn adjustment screw clockwise to increase pressure or
counterclockwise to decrease pressure.
8. Once desired pressure is established, set unit setting
for no call for heat, turn off main gas valve, remove
pressure-measuring device, and replace I/s-in. pipe
plug and screw cap.
Main Burners -- For most applications, main burners are
factory set and should require no adjustment.
For applications at altitudes above 2000 1l, refer to
Tables 31 and 32 for altitude compensation.
MAIN BURNER REMOVAL
1. Shut off (field-supplied) manual main gas v;dve.
2. Shut off power to unit.
3. Remove gas section access panel.
4. Disconnect gas piping from gas valve inlet.
5. Remove wires from gas valve.
6. Remove wires from rollout switch.
7. Remove sensor wire and ignitor cable from IGC board.
8. Remove 2 screws securing manifold bracket to basepan.
9. Remove 2 screws that hold the burner assembly to vesti-
bule plate.
10. Lift burner/manifold assembly out of unit.
48

CHARGING CHART fALLCIRCUITS)
ALL OUTDOOR FANS MUST BE OPERATING
LIOUIDPI_[SSIJI![[UTERINGTXV,[psi91
LEGEND
TXV --Thermostatic Expansion Valve
Fig. 35 -- Cooling Charging Chart-
48HJ020 Units
CHARGING CHART FALL CIRCUITS)
ALL OUTDOORFANS MUST BE OPERATING
2 LEADS, #18 WIRE 1/32 INSULATION, REGULATOR
600V. MAX., 105°C _ ADJUSTMENT SCREW
(REMOVE COVER)
//// \\\ / OUTLET PRESSURE
/u_u_ I}\\ / /TAP (PLUGGED)
I I1 I'='/A'TL_ _ _ln-t n_9[t:_l RECEPTACLE AND
I JII / ._9%\\ _LT--_JI I /TAB COMBINATION
_______ TERMINAL
\ [. _)/ " _'[ _/ [_) \PILOTCONNECTION
\ --, H / ' " FOR 1/4" O.D. TUBING
INLET PRESSURE TAP / (PLUGGED)
(PLUGGED) /
1/8 - 27 N.P.T. THDS. RECEPTACLE TERMINAL
/
Fig. 38 -- Gas Valve
Table 31 -- Altitude Compensation (Natural Gas)
ELEVATION
(ft) Low Medium High Heat High Heat
0-2,000 29 30 29 29
2,000 29 30 29 29
3,000 30 31 30 30
4,000 30 31 30 30
5,000 30 31 30 30
6,000 30 31 30 30
7,000 31 32 31 31
8,000 31 32 31 31
9,000 31 32 31 31
above 10,000 32 33 32 32
ORIFICE SIZE -- NATURAL GAS
Heat Heat (6 Cell) (8 Cell)
LIQUID PRESSURE ENTERING TXV, [psi 9]
LEGEND
TXV -- Thermostatic Expansion Valve
Fig. 36 -- Cooling Charging Chart --
48HJ024 Units
CHARGING CHART FALL CIRCUITS)
ALL OUTDOORFANS MUST BE OPEt?ATINC
_6o _'5o ;oo
LIQUID PRESSURE ENTZRING TXV, Ipsigl
LEGEND
TXV -- Thermostatic Expansion Valve
Fig. 37 -- Cooling Charging Chart --
48HJ028 Units
Table 32 -- Altitude Compensation (LP Gas)
ELEVATION
(ft) Low Medium High Heat High Heat
0-2,000 35 38 35 35
2,000 36 39 36 36
3,000 36 39 36 36
4,000 37 40 37 37
5,000 37 40 37 37
6,000 38 41 38 38
7,000 39 42 39 39
8,000 40 43 40 40
9,000 41 44 41 41
above 10,000 42 45 42 42
Heat Heat (6 Cell) (8 Cell)
CLEANING AND ADJUSTMENT
1. Remove burner rack from unit as described in Main
Burner Removed section above.
2. Inspect burners, and if dirty, remove burners from rack.
3. Using a soft brash, clean burneLs and crossover port as
required.
4. Adjust spark gap. See Fig. 39.
5. Reinstall burners on rack.
6. Reinstall burner rack as described above.
ORIFICE SIZE -- LP GAS
49

SPARK GAP.120"TO .140"
Fig. 39 -- Spark Gap Adjustment
DETAIL"C"
Filter Drier -- Replace whenever refiigerant system is ex-
posed to atmosphere.
Protective Devices
COMPRESSOR PROTECTION
Overcurrent -- Each compressor has internal line bleak motor
protection.
Overtemperature -- Each compressor has an internal protector
to protect it against excessively high dischmge gas temperatures.
Compressor Lockout -- If any of the safeties (high-pressure.
low-pressure, freeze protection thermostat, compressor intern¢fl
thermostat) trip, or if there is loss of power to the compressors,
the cooling lockout (CLO) will lock the compressot.s off. To
reset, manually move the thermostat setting.
HIGH-PRESSURE AND LOW-PRESSURE SWITCHES --
If either switch trips, or if the compressor overtempemture
switch activates, that refrigerant circuit will be automatically
locked out by the CLO. To reset, manually move the thermo-
stat setting.
FREEZE PROTECTION THERMOSTAT (FPT) -- An FPT
is located on the top and bottom of the evaporator coil. They
detect frost build-up and turn off the compressor, ¢fllowing the
coil to cleat: Once the frost has melted, the compressor can be
reenergized by resetting the compressor lockout.
EVAPORATOR FAN MOTOR PROTECTION -- A manu-
al teset, calibrated trip, magnetic circuit breaker protects
against overcurtent. Do not bypass connections or increase the
size of the breaker to correct trouble. Determine the cause and
correct it before resetting the breaker.
CONDENSER-FAN MOTOR PROTECTION -- Each
condenser-fan motor is internally protected against
overtemperature.
Fuses m'e also located in the control box and feed power to
the condenser fan motors. Always replace blown fuses with the
correct size fuse as indicated on the unit fuse label.
Relief Devices -- All units have relief devices to protect
against &_mage from excessive pressures (i.e., fire). These
devices protect the high and low side.
Control Circuit, 24-V- Each control circuit is pro-
tected against overcurrent by a 3.2 amp circuit breaket:
Breaker can be reset. If it trips, determine cause of trouble
before resetting. See Fig. 40-42 for wiring.
Replacement Parts -- A complete list of teplacement
parts may be obt_uned from any Canier distributor upon
request.
Diagnostic LEDs -- The IGC control board has a LED
for diagnostic purposes. The [GC error codes _ue shown in
Table 33.
Table 33 -- IGC LED Indications
ERROR CODE
Normal Operation
Hardware Failure
Fan On/Off Delay Modified
Limit Switch Fault
Flame Sense Fault
Five Consecutive Limit Switch Faults
Ignition Lockout Fault
Inducer Switch Fault
Rollout Switch Fault
Internal Control Fault
Software Lockout
LEGEND
IGC -- Integrated Gas Unit Controller
LED -- Light-Emitting Diode
NOTES:
1. There is a 3-second pause between error code displays,
2. If more than one error code exists, all applicable error codes will be dis-
played in numerical sequence,
3. Error codes on the IGC will be lost if power to the unit is interrupted.
LED INDICATION
On
Off
1 Flash
2 Flashes
3 Flashes
4 Flashes
5 Flashes
6 Flashes
7 Flashes
8 Flashes
9 Flashes
5O

LEGEND
Fig. 40 -- Low Voltage Control Schematic
Fig. 41 -- Power Schematic and Fig. 42 -- Component Arrangement
.A --
_,HA --
AL --
AUX --
.B --
.C --
CAP --
CB --
CC --
CCH --
CLO --
COMP --
CR --
CS --
DU --
FCS --
FlOP --
FPT --
FS --
FU --
GND --
GV --
GVR --
HACR --
HS --
HERM --
HPS --
I
IA
IAQ --
IDM =
IFC --
IFCB --
IFM --
IGC --
IRH --
LAFC --
Circuit A LPS = Low Pressure Switch
Adjustable Heat Anticipator LS -- Limit Switch
Ambient Limit MGV -- Main Gas Valve
Auxiliary Contact OA -- Outdoor Air
Circuit B OAS -- Outdoor Air Sensor
Circuit C OAT -- Outdoor-Air Temperature
Compressor, Contactor OFC -- Outdoor-Fan Contactor
Capacitor OFM -- Outdoor-Fan Motor
Circuit Breaker ORH -- Outdoor Relative Humidity
Compressor Contactor PEC -- Power Exhaust Contactor
Crankcase Heater PEM -- Power Exhaust Motor
Compressor Lockout PL -- Plug
Compressor OC -- Quadruple Contactor
Compressor Relay OT -- Quadruple Terminal
Current Sensor RAS -- Return Air Sensor
Dummy Terminal RAT -- Return Air Thermostat
Fan Cycling Switch RS -- Rollout Switch
Factory-Installed Option SAT -- Supply-Air Temperature
Female Pipe Thread TB -- Terminal Block
Flame Sensor TC -- Thermostat Cooling
Fuse TR -- Thermostat Heating
Ground TRAN -- Transformer
Gas Valve O Terminal (Marked)
Gas Valve Relay
Heating, Air Conditioning, and Refrigeration O Terminal (Unmarked)
Heat Sensor _ Terminal Block
Hermetic
L_
High-Pressure Switch • Splice
Ignitor _ Splice (Marked)
Indoor Air _ Splice (Field Supplied)
Indoor-Air Quality
Induced-Draft Motor -- Factory Wiring
Indoor-Fan Contactor Field Control Wiring
Indoor-Fan Circuit Breaker .... Field Power Wiring
Indoor-Fan Motor
Integrated Gas Controller .... Accessory or Optional Wiring
Indoor Relative Humidity ..=.=.=.= To Indicate Common Potential Only,
Low Ambient Fan Control Not To Represent Wiring
THERMOSTAT/IGC MARKINGS
BM -- Blower Motor RS -- Rollout Switch
C = Common RT -- Power Supply
CM = Inducer Motor SS = Speed Sensor
CS = Centrifugal Switch W = Thermostat Heat
G -- Fan Wl -- 1st Stage of Heating
GV -- Gas Valve W2 -- 2nd Stage of Heating
IFO -- Indoor Fan On X -- Alarm Output
LI -- Line I Y1 -- 1st Stage of Cooling
R -- Thermostat Power Y2 -- 2rid Stage of Cooling
NOTES:
1. Factory wiring is in accordance with the National Electrical Codes. Any field
modifications or additions must be in compliance with all applicable codes.
2. Use 75 C minimum wire for field power supply. Use copper wires for all units.
3. All circuit breakers "Must Trip Amps" are equal to or less than 156% RLA
(rated load amps).
4. Compressor and fan motors are thermally protected. Three-phase motors
protected against primary single phase conditions.
5. The CLO locks out the compressor to prevent short cycling on compressor
overload and safety devices; before replacing CLO, check these devices.
51

) trc
] fez
eL+.t
] fez
) e(c_
¢,¢1
_tnAU
_e/cl
Fig. 40 -- Low Voltage Control Schematic
52

MOVE WIRES l© OFCI
WHEN INSTALLING
A_BIENT FAN CONTROL
ACCESSORY
ONLY
C A! YEL
YEL
CLOCI
3 CIRI_JF
(3 CIRCU_
!FCg
BLK
............................BLK T£ANI
I
I
ADD WIRES WHEN !NSTA!LING
IOW AMBIENT FAN CONTROl
CONNECT _IRE TO
APPROPRIA?E UNll VOL?AGE
ACCESSORY
PI53 PL/0
1028/300ONLYI
I0281a00 ONLYI
PL56 P{IZ
vIo 208/230v
----- BLK 460V
Fig. 41 -- Power Schematic
53

L/1
AND AL
COMPRESSOR COBTACTORB
ALL UNITS EXCEPT OB8130O BOB/Z30V
10201210-024/240 ONLY}
EOUIP
GROUND
_ (D28/DDO ONLY}
CO_@RESSOR CONTACTORS
OD81SO0 2081B3DV ONLY
TBERM LOCATION
THER_ LOCATION
EVAPORATOR RETURN BEND END PLY
020/810 ONLY) (BUD/SOB ONLY: PLS
{O241240 ONLY) PL4
CKTB PLI4
-B_TC CKTB
[0201810 )NLY}
_CNTB PL9
(ODOIBIO ONLY)
PLIO
PLI]
PLIBI
PLID!
PL15
ONLY) PL]6
PL]7
PL]8
PL19
PLB1
PLUG LOCATION REFERENCE
:ORTROL BOX
CONTROL BOARD}
_EAT SECTIO_ PARTITION
HEAT CONTROLS)
:AN SECTION
I_DOOR FAN MOTOR}
:ORDENSER SECTION
PL5
OR_l, B, 3)
IORDE_BER SECTIO_
PLG
ICONOW[EZR SECTION
PLT
ECOnOmIZER MOTOR}
>OMEN EXHAUST SECTION
IPOWER EXHAUST MOTORS1
:ONDERSER SECTIO_
OF_I}
:ONDERSER SECTION
OE_2)
:ONDERSER SECTION
OF_S)
:ONDENSER SECT]O_
OF_4}
:ORDERSER SECTION
OF_S)
:ONDERBERSECTION
OF_6)
:AN SECTION
FAN STATUS ACCESSORY)
ECONOMIZER SECTION
B-POSITION DA_PERI
:OMPRESSOR SECTION
COB SENSOR)
:OMP_E_SO_SECTIOW
:ORDERSER SECTIO_
SPEED CONTROL)
CCH 81 CC_ AI
[VAP CIRCUIT CONFIGURATION
OUTLET TRAffSEOR_ERI
CIRCUIT CIRCUIT
A
rl_Y
THERMISTORS
SPEED CONTROL-
CO_"_E'_E
Fig. 42 -- Component Arrangement

TROUBLESHOOTING
Unit Troubleshooting- Refer to Tables 34-36 and
Fig. 43.
Table 34 -- Cooling Service Analysis
PROBLEM CAUSE REMEDY
Compressor and Condenser Power failure. Gall power company.
Fan Will Not Start, Fuse blown or circuit breaker tripped. Replace fuse or reset circuit breaker.
Defective thermostat, contactor, transformer, or control Replace component.
relay.
Insufficient line voltage. Determine cause and correct.
Incorrect or faulty wiring. Check wiring diagram and rewire correctly.
Thermostat setting too high. Lower thermostat setting below room temperature.
Compressor Will Not Start Faulty wiring or loose connections in compressor Check wiring and repair or replace.
but Condenser Fan Runs. circuit.
Compressor motor burned out, seized, or internal Determine cause. Replace compressor.
overload open.
Defective overload. Determine cause and replace.
Compressor locked out Determine cause for safety trip and reset lockout.
One leg of 3-phase power dead. Replace fuse or reset circuit breaker.
Compressor Cycles Refrigerant overcharge or undercharge. Recover refrigerant, evacuate system, and recharge to
(other than normally nameplate.
satisfying thermostat), Defective compressor. Replace and determine cause.
Insufficient line voltage. Determine cause and correct.
Blocked condenser. Determine cause and correct.
Defective overload. Determine cause and replace.
Defective thermostat. Replace thermostat.
Faulty condenser-fan motor. Replace.
Restriction in refrigerant system. Locate restriction and remove.
Compressor Operates Dirty air filter. Replace filter.
continuously. Unit undersized for load. Decrease load or increase unit size.
Thermostat set too low. Reset thermostat.
Low refrigerant charge. Locate leak, repair, and recharge.
Air in system. Recover refrigerant, evacuate system, and recharge.
Condenser coil dirty or restricted. Clean coil or remove restriction.
Excessive Head Pressure. Dirty air filter. Replace filter.
Dirty condenser coil. Clean coil.
Refrigerant overcharged. Recover excess refrigerant.
Faulty TXV. 1. Check TXV bulb mounting and secure tightly to suction line.
Air in system. Recover refrigerant, evacuate system, and recharge.
Condenser air restricted or air short-cycling. Determine cause and correct.
Head Pressure Too Low, Low refrigerant charge. Check for leaks, repair, and recharge.
Restriction in liquid tube. Remove restriction.
Excessive Suction Pressure. High heat load. Check for source and eliminate.
Faulty TXV. 1. Check TXV bulb mounting and secure tightly to suction line.
Refrigerant overcharged. Recover excess refrigerant.
Suction Pressure Too Low. Dirty air filter. Replace filter.
Low refrigerant charge. Check for leaks, repair, and recharge.
Metering device or low side restricted. Remove source of restriction.
Faulty TXV. 1. Check TXV bulb mounting and secure tightly to suction line.
Insufficient evaporator airflow. Increase air quantity. Check filter and replace if
Temperature too low in conditioned area. Reset thermostat.
Field-installed filter drier restricted. Replace.
LEGEND
TXV -- Thermostatic Expansion Valve
Determine cause.
2. Replace TXV if stuck open or closed.
2. Replace TXV if stuck open or closed.
2. Replace TXV if stuck open or closed.
necessary.
55

Table 35 -- Heating Service Analysis
PROBLEM
Burners Will Not Ignite.
Inadequate Heating.
Poor Flame Characteristics,
Burners Will Not Turn Off. Unit is locked into Heating mode for a one minute
Misaligned spark electrodes.
No gas at main burners,
Water in gas line,
No power to furnace.
No 24 v power supply to control circuit,
Miswired or loose connections.
Burned-out heat anticipator inthermostat.
Broken thermostat wires,
Dirty air filter.
Gas input to unit too low,
Unit undersized for application,
Restricted airflow.
Blower speed too low.
Limit switch cycles main burners.
Too much outdoor air.
Incomplete combustion (lack of combustion air)
results in:
Aldehyde odors, CO, sooting flame, or floating flame.
minimum.
CAUSE
REMEDY
Check flame ignition and sensor electrode positioning,
Adjust as needed.
Check gas line for air; purge as necessary. After purging gas line of
air, allow gas to dissipate for at least 5 minutes before attempting to
relight unit,
Check gas valve,
Drain water and install drip leg to trap water,
Check power supply, fuses, wiring, and circuit breaker.
Check transformer, Transformers with internal evercurrent protection
require a cool-down period before resetting, Check 24-v circuit
breaker; reset if necessary.
Check all wiring and wire nut connections,
Replace thermostat,
Run continuity check, Replace wires if necessary.
Clean or replace filter as necessary.
Check gas pressure at manifold, Clock gas meter for input, If too
low, increase manifold pressure or replace with correct orifices.
Replace with proper unit or add additional unit,
Clean filter, replace filter, or remove any restrictions.
Install alternate motor, if applicable, or adjust pulley to increase fan
speed.
Check rotation of blower, thermostat heat anticipator settings, and
temperature rise of unit. Adjust as needed.
Adjust minimum position.
Check economizer operation.
Check all screws around flue outlets and burner compartment.
Tighten as necessary.
Cracked heat exchanger. Replace heat exchanger,
Overfired unit -- reduce input, change orifices, or adjust gas line or
manifold pressure,
Check vent for restriction, Clean as necessary.
Check orifice to burner alignment,
Wait until mandatory one minute time period has elapsed or power
to unit.
Table 36 -- IGC Board LED Alarm Codes
LED FLASH ACTION TAKEN BY
CODE DESCRIPTION CONTROL RESET METHOD PROBABLE CAUSE
On Normal Operation -- -- --
Off Hardware Failure No gas heating. -- Loss of power to the IGC. Check 5 amp fuse on IGC,
1 Flash Indoor Fan On/Off Delay 5 seconds subtracted from On Power reset. High temperature limit switch opens during heat
2 Flashes Limit Switch Fault Gas valve and igniter Off. Limit switch closed, or heat High temperature limit switch is open. Check the operation
3 Flashes Flame Sense Fault Indoor fan and inducer On. Flame sense normal. The IGC sensed a flame when the gas valve should be
4 Flashes Four Consecutive Limit No gas heating. Heat call (W) Off. 4 consecutive limit switch faults within a single call for
5 Flashes Ignition Fault No gas heating. Heat call (W) Off. Unit unsuccessfully attempted ignition for 15 minutes.
6 Flashes Induced Draft Motor Fault If heat off: no gas heating. Inducer sense normal, or Inducer sense On when heat call Off, or inducer sense Off
7 Flashes Rollout Switch Lockout Gas valve and igniter Off. Power reset. Rollout switch has opened. Check gas valve operation.
8 Flashes Internal Control Lockout No gas heating. Power reset. IGC has sensed internal hardware or software error. If
9 Flashes Temporary Software Lockout No gas heating, hour auto reset, or power Electrical interference is disrupting the IGC software.
IGC -- Integrated Gas Unit Control
LED -- Light-Emitting Diode
Modified delay, exchanger warm-up period before fan-on delay expires.
Switch Fault Power reset for LED reset, heat. See Limit Switch Fault.
LEGEND
5 seconds added to Off delay High temperature limit switch opens within
(3 min max). 10 minutes of heat call (W) Off.
Indoor fan and inducer On. ,_all (W) Off. of the indoor (evaporator) fan motor. Ensure that the sup-
Power reset for LED reset, closed. Check wiring, flame sensor, and gas valve opera-
Power reset for LED reset. Check igniter and flame sensor electrode spacing, gaps,
If heat on: gas valve Off and heat call (W) Off. when heat call On. Check wiring, voltage, and operation of
inducer On. IGC motor. Check speed sensor wiring to IGC.
Indoor fan and inducer On. Check induced-draft blower wheel is properly secured to
reset.
NOTES:
1. There is a 3-second pause between alarm code displays.
2. If more than one alarm code exists, all applicable alarm codes will be dis-
played in numerical sequence.
3. Alarm codes on the IGC will be lost if power to the unit is interrupted.
)ower to unit, 24V circuit breaker, transformer, and wiring
to the IGC.
See Limit Switch Fault.
ply-air temperature rise is within the range on the unit
nameplate. Check wiring and limit switch
operation.
tion.
etc. Check flame sense and igniter wiring. Check gas valve
operation and gas supply.
motor shaft.
fault is not cleared by resetting 24 v power, replace the
IGC.
56

I I.-(HEATING) IGC BOARD
J 2 FLASHES - OPENING OF LtMfT
I 3 FLASHES - FLAME SENSOR
J 4 _ + LIM+TSV_TCH
5 FLASHE8 - IGNmON LOCKOUT(No _ _ 15 rr_u_5)
I 6 _ - INDUCED DRAFT
I 7 FLASHES - _ OF
I 9 FLASHES - SOFTWARE
9,/WrCH
I_TES FLAME WTfH
CLOSED GAS VALVE
CYCtED 4 TIMES ON SINGLE
CALL FOR HEAT
FAULT
8e_" fer ee _)
_ F_kT
LOCKOUT _"
F
I,
_&
F _ FAN MOTOR
_ _FAN
_ _ AND
START _VM_EDt&TELY
I I I_3_'_ ON DEt.AY
IMMeDiATELY
_F_
I
I i
I
I I
I COMSt,_'TIONRELAy_INDt.,_i_DR_'TMOTOR(ID_THROUGH I
4,
_ HIGH VOLTAGE I
10,000 VOLT _ARK FOR 5
_d3ONE6
1
2. DEF_ 24V TR,aNS.
3. _WIRE
I I, BLOWN 5 AMP FUSE
4, NO POWER TO LINIT
'WI' FROM BASE CONTROL BOARD ENERGIZES 'W'
ON IGC - 1 MINUTE LOCK-ON
_ 'Ct/t ON IGC
t,
IF IDM 18 TURNING AT CORRECT SPEED (AT LEAST 2400 RPM), H_L IE}=PT:CT 8_NSOR SENDS CORRr:CT 81GNAL TO _ *Jl' ON IGC
l
SWffCH ARE CLOSED, _C SAFETY
LOP-.4£V_LL INITIA'_E
IF IJM1T SWITCH AND ROLLOUT
SE_ENCE
i,
I
VALVE FOR 5 SECONDS
I
I
I
I
OFF GAS VALVE AND SPARK
I OC SA_ LOGtC V_ILLSHUT
(5 _8 OF L_)) i
LEGEND
IDM -- Induced-Draft Motor
IGC -- Integrated Gas Unit Controller
NOTE: Thermostat Fan Switch in the
"AUTO" position.
Yes
4,
HAS BEEN _ DUE TO LIMrr SWfTCH
I /If=FER 45 SECOh_D_ (ON LEDS F THE _ !
TRIPS) IGC WlLL 15kFjRGIZE BL(:7#ER RELAY
Yes
I
No
J H_NG_ _ I
I ,_ s.ro_,s,s,_=-rYLOaCSHUTSO_ C_._VALV_ J
(DBJW _ BY 5 8ECOND_ FOR _ UME SW/TCH TRP -
Fig. 43 -- IGC Control (Heating and Cooling)
45 SECOND BLOWER 8HLmOFF DELAY
MAXIMUM DELAY: 3 MINUTES)
ANOTHER 5SL::OONDS) FROM
SUBTRACT 5 SECONDS (OR J
INDOOR FAR ON TIME 13B_Y
57

EconoMiSer IV Troubleshooting -- See Table 37
for EconoMi$er IV input/output logic.
A functional view of the EconoMi$er [V is shown in
Fig. 43. Typic;d settings, sensor ranges, and jumper positions
are also shown. An EconoMi$er IV simulator program is avail-
able from Carrier to help with EconoMi$er IV tr;fining and
troubleshooting.
ECONOMI$ER IV PREPARATION-- This procedure is
used to prepare the EconoMi$er IV for troubleshooting. No
troubleshooting or testing is done by performing the following
procedure.
NOTE: This procedure requires a 9-v battery, 1.2 kilo-ohm
resistol: and a 5.6 kilo-ohm resistor which are not supplied
with the EconoMi$er IV.
tiometers before starting troubleshooting.
I IMPORTANT: Be sure to record the positions of all poten - ]
1. Disconnect power at TR and TRI. All LEDs should be
off. Exhaust fan contacts should be open.
2. Disconnect device at P and PI.
3. Jumper P to PI.
4. Disconnect wires at T and TI. Place 5.6 kilo-ohm resistor
across T and TI.
5. Jumper TR to 1.
6. Jumper TR to N.
7. If connected, remove sensor from termin_ds So and +.
Connect 1.2 kilo-ohm 4074EJM checkout resistor across
terminals So and +.
8. Put 620-ohln resistor across terminals SR and +.
9. Set minimum position, DCV set point, and exhaust
potentiometers fully CCW (counteMockwise).
10. Set DCV maximum position potentiometer fully CW
(clockwise).
11. Set enthalpy potentiometer to D.
12. Apply power (24 vac) to terminals TR and TRI.
DIFFERENTIAL ENTHALPY-- To check differential
enthalpy:
1. Make sure EconoMiSer IV preparation procedure has
been performed.
2. Place 620-ohm resistor across So and +.
3. Place 1.2 kilo-ohln resistor across S R and +. The Free
Cool LED should be lit.
4. Remove 620-ohm resistor across So and +. The Free
Cool LED should turn off.
5. Return EconoMiSer IV settings and wiring to normal
after completing troubleshooting.
SINGLE ENTHALPY -- To check single enthalpy:
1. Make sure EconoMiSer IV preparation procedure has
been performed.
2. Set the enthalpy potentiometer to A (fully CCW). The
Free Cool LED should be lit.
3. Set the enth_dpy potentiometer to D (fully CW). The Free
Cool LED should turn off.
4. Return EconoMiSer IV settings and wiring to norlnal
after completing troubleshooting.
DCV (Demand Controlled Ventilation) AND POWER
EXHAUST -- To check DCV and Power Exhaust:
1. Make sure EconoMiSer IV preparation procedure has
been performed.
2. Ensure terminals AQ and AQI tue open. The LED for
both DCV and Exhaust should be off. The actuator
should be lully closed.
3. Connect a 9-v battery to AQ (positive node) and AQl
(negative node). The LED for both DCV and Exhaust
should turn on. The actuator should (hive to between 90
and 95% open.
4. Turn the Exhaust potentiometer CW until the Exhaust
LED turns off. The LED should turn off when the
potentiometer is approximately 90%. The actuator should
remain in position.
5. Turn the DCV set point potentiometer CW until the DCV
LED turns off. The DCV LED should turn off when the
potentiometer is approximately 9 v. The actuator should
drive fully closed.
6. Turn the DCV and Exhaust potentiometers CCW until
the Exhaust LED turns on. The exhaust contacts will
close 30 to 120 seconds after the Exhaust LED turns on.
7. Return EconoMi$er IV settings and wiring to normal
after completing troubleshooting.
DCV MINIMUM AND MAXIMUM POSITION -- To check
the DCV minimum and maximum position:
1. Make sure EconoMiSer IV prepmation procedure has
been performed.
2. Connect a 9-v battery to AQ (positive node) and AQI
(negative node). The DCV LED should turn on. The
actuator should (hive to between 90 and 95% open.
3. Turn the DCV Maximum Position potentiometer to mid-
point. The actuator should drive to between 20 and 80%
open.
4. Turn the DCV Maximum Position potentiometer to lully
CCW. The actuator should drive fully closed.
5. Turn the Minimum Position potentiometer to midpoint.
The actuator should (hive to between 20 and 80% open.
6. Turn the Minimum Position Potentiometer lully CW. The
actuator should drive fully open.
7. Remove the jumper from TR and N. The actuator should
drive fully closed.
8. Return EconoMiSer IV settings and wiring to norm_d
after completing troubleshooting.
SUPPLY-AIR INPUT -- To check supply-air input:
1. Make sure EconoMi$er IV prepmation procedure has
been performed.
2. Set the Enthalpy potentiometer to A. The Free Cool LED
turns on. The actuator should drive to between 20 and
80% open.
3. Remove the 5.6 kilo-ohm lesistor and jumper T to TI.
The actuator should (hive lully open.
4. Remove the jumper across T and TI. The actuator should
drive fully closed.
5. Return EconoMiSer IV settings and wiring to norm_d
after completing troubleshooting.
ECONOMISER IV TROUBLESHOOTING COMPLE-
TION -- This procedure is used to return the EconoMiSer IV
to operation. No troubleshooting or testing is done by perform-
ing the following procedure.
1. Disconnect power at TR and TRI.
2. Set enthalpy potentiometer to previous setting.
3. Set DCV maximum position potentiometer to previous
setting.
4. Set minimum position, DCV set point, and exhaust
potentiometers to previous settings.
5. Remove 620-ohm resistor from terminals SRand +.
6. Remove 1.2 kilo-ohm checkout resistor from terminals
So and +. If used, reconnect sensor from terminals So and
+.
58

7. Remove jumper flom TR to N.
8. Remove jumper fiom TR to 1.
9. Remove 5.6 kilo-ohm resistor from T and TI. Reconnect
wiles tit T and TI.
Table 37 -- EconoMi$er IV Input/Output Logic
INPUTS
Demand Control
Ventilation (DCV)
Below set
(DCV LED Off)
Above set
(DCV LED On)
*For single enthalpy control, the module compares outdoor
enthalpy to the ABCD set point.
1-Power at N terminal determines Occupied/Unoccupied setting:
24 vac (Occupied), no power (Unoccupied).
**Modulation is based on the supply-air sensor signal.
1-1-Modulation is based on the DCV signal.
High
(Free
Low
(Free
High
(Free
Low
(Free
Enthalpy* Compressor
Outdoor Return Y1 Y2 Stage Stage
Low On On On On
Cooling LED Off) On Off On Off
Off Off Off Off
High On On On Off
Cooling LED On) On Off Off Off
Off Off Off Off
Low On On On On
Cooling LED Off) On Off On Off
Off Off Off Off
High On On On Off
Cooling LED On) On Off Off Off
Off Off Off Off
l 0. Remove jumper fiom P to Pl. Reconnect device a P and
PI.
11. Apply power (24 vac) to terminals TR and TRI.
OUTPUTS
N Terminal1-
1 2
Minimum position Closed
Modulating** (between min.
3osition and full-open)
Minimum position
Modulating1-1- (between min.
3osition and DCV maximum)
Modulating***
***Modulation is based on the greater of DCV and supply-air sen-
sor signals, between minimum position and either maximum
position (DCV) or fully open (supply-air signal).
I-I-I-Modulation is based on the greater of DCV and supply-air sen-
sor signals, between closed and either maximum position (DCV)
or fully open (supply-air signal).
Occupied Unoccupied
Damper
Modulating** (between
closed and full-open)
Closed
Modulating1-1- (between
closed and DCV
maximum)
Modulating1-1-1-
Fig. 43 -- EconoMi$er IV Functional View
59

Copyright 2005 Carrier Corporation
Manufacturer reserves the right to discontinue, or change at any time, specifications or designs without notice and without incurring obligations.
Bookll Catalog No. 04-53480011-01 Printed in U.S.A. Form 48HJ-31SI Pg 60 10-05 Replaces: 48HJ-27SI
Tab Ila

START-UP CHECKLIST
MODEL NO.: SERIAL NO.:
DATE: TECHNICIAN:
I. PRE-START-UP:
[] VERIFY THAT ALL PACKING MATERIALS HAVE BEEN REMOVED FROM UNIT
[] VERIFY INSTALLATION OF OUTDOOR AIR HOOD
[] VERIFY INSTALLATION OF FLUE EXHAUST AND INLET HOOD
[] VERIFY THAT CONDENSATE CONNECTION IS INSTALLED PER INSTRUCTIONS
[] VERIFY THAT ALL ELECTRICAL CONNECTIONS AND TERMINALS ARE TIGHT
[] VERIFY GAS PRESSURE TO UNIT GAS VALVE IS WITHIN SPECIFIED RANGE
[] CHECK GAS PIPING FOR LEAKS
[] CHECK THAT INDOOR-AIR FILTERS ARE CLEAN AND INPLACE
[] CHECK THAT OUTDOOR AIR INLET SCREENS ARE IN PLACE
[] VERIFY THAT UNIT IS LEVEL
[] CHECK FAN WHEEL AND PROPELLER FOR LOCATION IN HOUSING/ORIFICE, AND VERIFY SETSCREW
IS TIGHT
[] VERIFY THAT FAN SHEAVES ARE ALIGNED AND BELTS ARE PROPERLY TENSIONED
[] VERIFY THAT SCROLL COMPRESSORS ARE ROTATING IN THE CORRECT DIRECTION
[] VERIFY INSTALLATION OF THERMOSTAT/SPACE SENSOR
[] VERIFY THAT CRANKCASE HEATERS HAVE BEEN ENERGIZED FOR ATLEAST 24 HOURS
LU
2:
d3
LU
I--
rm
Z
o,
<
I-
o
II. START-UP
ELECTRICAL
SUPPLY VOLTAGE LI-L2 L2-L3 L3-LI
COMPRESSOR AMPS -- COMPRESSOR AI LI
-- COMPRESSOR B 1 LI
COMPRESSOR CI LI
(020,024 ONLY)
SUPPLY FAN AMPS
TEMPERATURES
OUTDOOR-AIR TEMPERATURE
RETURN-AIR TEMPERATURE
COOLING SUPPLY AIR
GAS HEAT SUPPLY AIR
PRESSURES
GAS INLET PRESSURE
GAS MANIFOLD PRESSURE STAGE NO. 1
REFRIGERANT SUCTION CIRCUIT A
CIRCUIT B
CIRCUIT C
REFRIGERANT DISCHARGE CIRCUIT A
CIRCUIT B
CIRCUIT C
[] VERIFY REFRIGERANT CHARGE USING CHARGING CHARTS ON PAGE 49
F DB (Dry Bulb)
FDB
F
F
IN. WG
IN. WG
PSIG
PSIG
PSIG(020,024ONLY)
PSIG
PSIG
PSIG(020,024ONLY)
L2 L3
L2 L3
L2 L3
F WB (Wet Bulb)
STAGE NO. 2 IN. WG
LU
2:
rm
LU
I--
d3
Z
o,
<
o
GENERAL
[] ECONOMIZERMINIMUMVENTANDCHANGEOVERSETTINGSTOJOB REQUIREMENTS
Copyright 2005 Carrier Corporation
Manufacturer reserves the right to discontinue, or change at any time, specifications or designs without notice and without incurring obligations.
Book 111 Catalog No, 04-53480011-01 Printed in U.S.A, Form 48HJ-31SI Pg CL-1 10-05 Replaces: 48HJ-2781
Tab
F