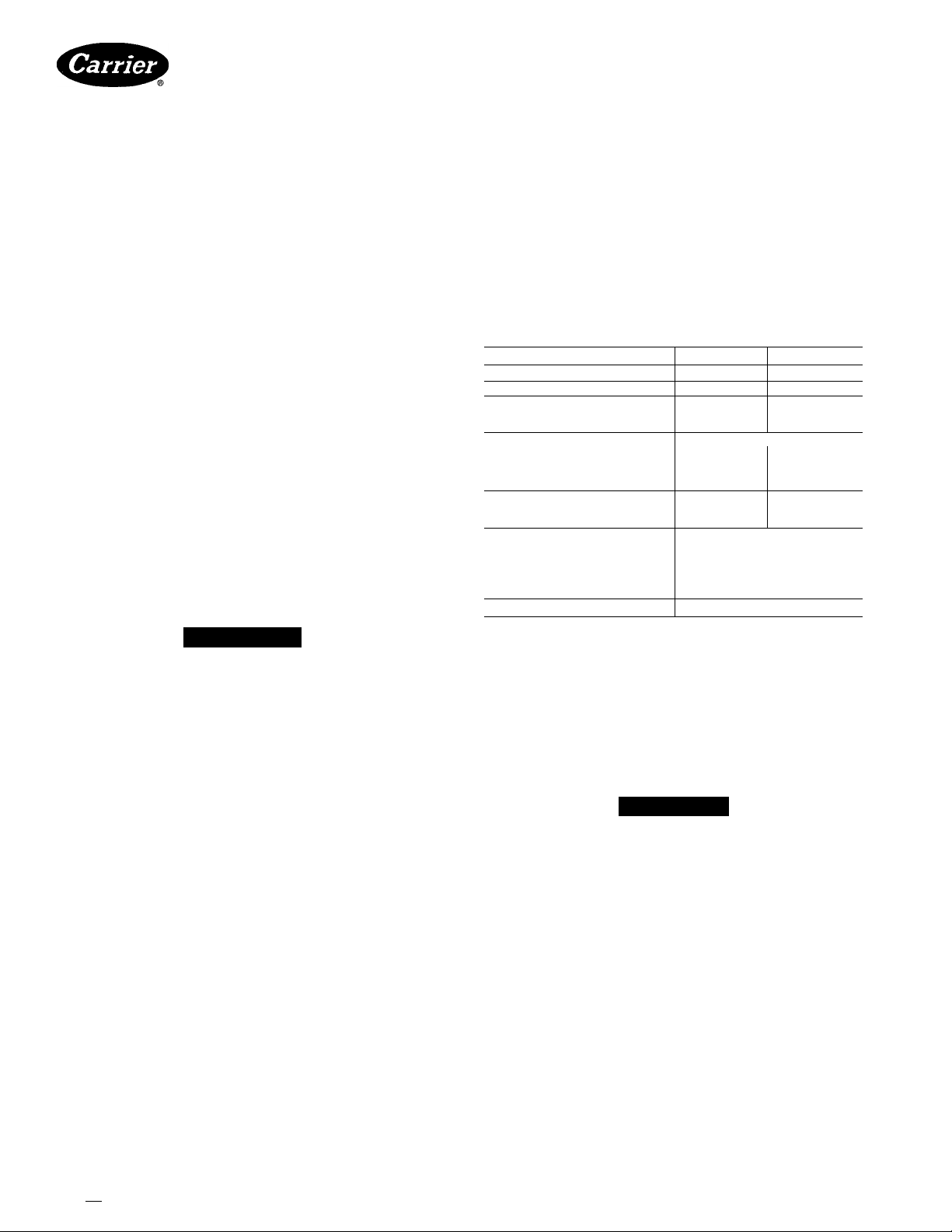
38AF
HEATING & COOLING
Air-Cooled Condensing Units
Installation, Start-Up and Service Instructions
SAFETY CONSIDERATIONS
Installing and servicing air conditioning equipment
can be hazardous due to system pressure and electrical
components. Only trained and qualified service personnel
should install or service air conditioning equipment.
Untrained personnel can perform basic maintenance,
such as cleaning and replacing filters. All other opera
tions should be performed by trained service personnel.
When working on air conditioning equipment, observe
precautions in literature and on tags and labels attached
to unit.
Follow all safety codes. Wear safety glasses and work
gloves. Use quenching cloth for brazing operations.
Have fire extinguisher available. Read these instruc
tions thoroughly. Consult local building codes and
National Electrical Code (NEC) for special installation
requirements.
A WARNING
Before installing or servicing system, always turn off
main power to system. There may be more than one
disconnect switch. Turn off accessory heater power if
applicable. Electrical shock can cause personal injury.
UNIT 38AF
OPER WEIGHT (lb)
REFRIGERANT*
COMPRESSOR
Oil (pts)
Crankcase Heater Watts
CONDENSER AIR FAN
Number...Rpm
Diameter (in.)
Motor Hp (NEMA)
Nominal Cfm Total
CONDENSER COIL
Face Area (sq tt)
Storage Capacity (lb)f
CONTROLS
Pressurestat Settings
FUSIBLE PLUG
*Unit is factory supplied with holding charge only.
tStorage capacity of condenser coil with coil 80% full of liquid R-22
at 124 F
Table 1 — Physical Data
007 008
300 400
22 22
46 8 0
40
Propeller; Direct Drive
1 1075 1 1075
22 22
'/2 v?
3500 4300
108
168 18 0
High Cutout
Cut-in
Low Cutout
Cut-In
426 ± 7 psig
320 ± 20 psig
27 ± 4 psig
67 ± 7 psig
200 F
40
17 7
INSTALLATION
Step 1 — Complete Pre-Installation Checks
UNCRATE UNIT — Remove unit packaging except for
the top skid assembly and wood bumpers, which should
be left in place until after unit is rigged into place.
INSPECT SHIPMENT — File claim with shipping com
pany if shipment is damaged or incomplete.
CONSIDER SYSTEM REQUIREMENTS
• Consult local building codes and National Electrical
Code (NEC) for special installation requirements.
• Allow sufficient space for airflow clearance, wiring,
refrigerant piping, and servicing unit. See Fig. 1.
• Locate unit so that condenser airflow is unrestricted
on all sides and above. Refer to Fig. 1.
• Unit may be mounted on a level pad directly on base
channels or mounted on raised pads at support points.
See Table 2 for weight distribution based on recom
mended support points.
NOTE: If vibration isolators are required for a parti
cular installation, use data in Table 2 to make proper
selection.
Manufacturer reserves the right to discontinue, or change at any time, specifications or designs without notice and without Incurring obligations.
BookM |4 PC111 Catalog No 563-852 PrintedinUSA Form38AF-1SI Pg 1 4-85 Replaces: New
Tab I3al2a
For replacement items use Carrier Specified Parts
Step 2 — Rig and Mount the Unit
A CAUTION
Be sure unit panels are securely in place prior to
rigging.
RIGGING — These units are designed for overhead
rigging only. Traverse base channels are provided with
1 -1 / 2 in. rigging holes that are located 1 -3/ 4 in. from each
end. Rig with top skid packaging assembly and wood
bumper strips in place to prevent unit damage by rigging
cable. As further protection for coil faces, plywood sheets
may be placed against sides of unit, behind cables. Run
cables to a central suspension point so that angle from the
horizontal is not less than 45 degrees. Raise and set unit
down carefully.
If it is necessary to roll unit into position, mount unit
on longitudinal rails, using a minimum of 3 rollers. Apply
force to rails, not unit. If unit is to be skidded into posi
tion, place it on a large pad and drag it by the pad. Do not
apply any force to unit.
Raise from above to lift unit from rails or pad when
unit is in final position.
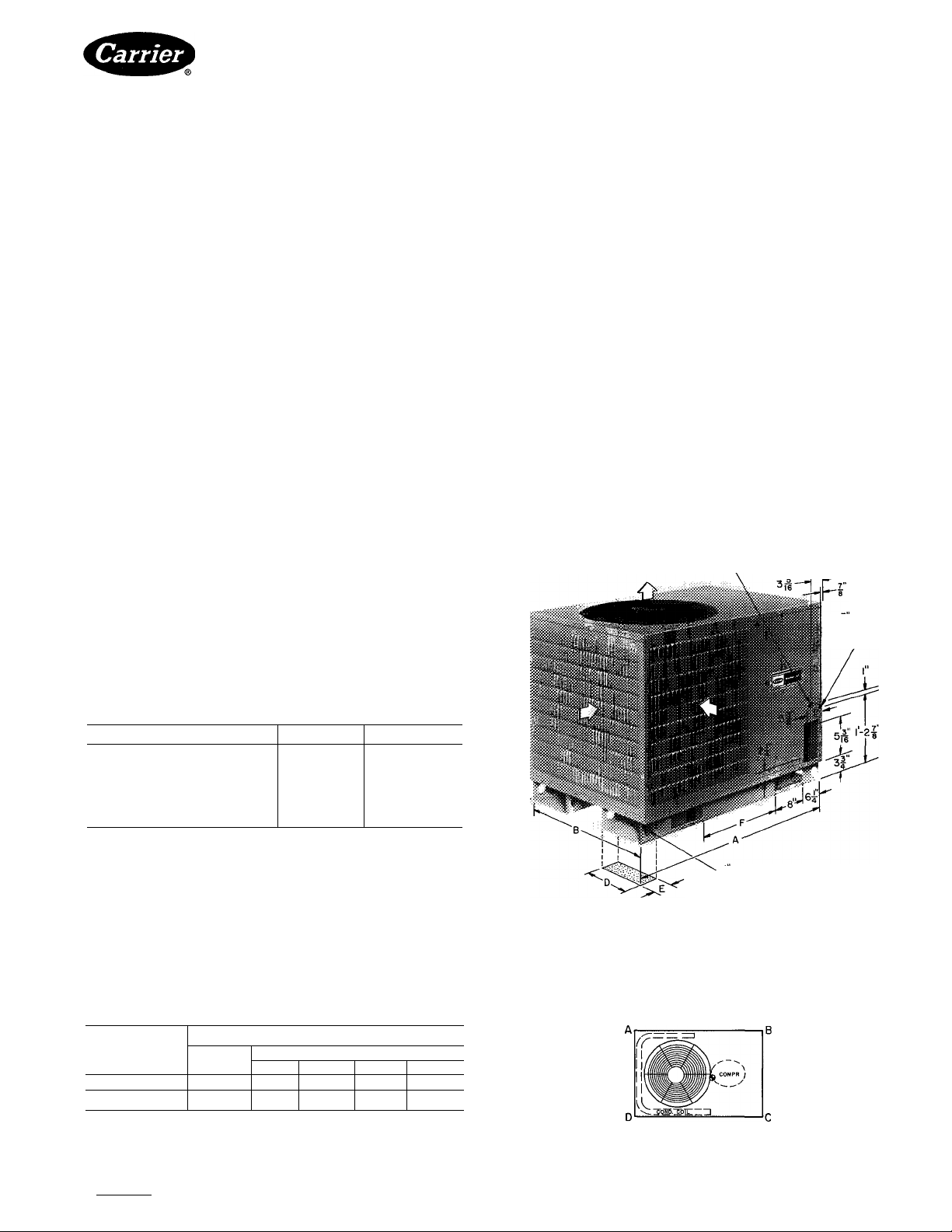
38AF
HEATING & COOLING
Step 3 — Complete Refrigerant Piping
Connections
SIZE REFRIGERANT LINES — Consider length of
piping required between condensing unit and evaporator,
amount of liquid lift, and compressor oil return. See
Table 3 and also refer to Part 3 of Carrier System Design
Manual for design details and line sizing. Refer to evap
orator installation instructions for additional information.
USE FILTER DRIER AND MOISTURE INDICATOR
— The filter drier is factory supplied. Moisture indicator
(sight glass) is a field-installed option and should be
installed just after liquid line shutoff valve. Do not use a
receiver; there is none provided with unit and one should
not be used.
MAKE PIPING CONNECTIONS — Remove block-off
in corner post and unsweat caps from liquid and suction
lines.
NOTE: Unit is shipped with R-22 holding charge. System
pre.ssure must be relieved before unsweating caps.
Pass nitrogen or other inert gas through piping while
brazing to prevent formation of copper oxide.
Install field-supplied thermostatic expansion valve(s)
to evaporator section. If 2 thermostatic expansion valves
are installed for 2-step cooling, install field-supplied
liquid line solenoid valve ahead of the second expansion
valve.
Air-Cooled Condensing Units
PROVIDE SAFETY RELIEF —A fusible plug is located
in unit liquid line. Do not cap this plug. If local code;
requires additional safety devices, install as directed.
Step 4 — Complete Electrical Connections
POWER WIRING — Unit is factory wired for voltage
shown on nameplate. Provide adequate fused disconnect
switch within sight of unit, readily accessible, but out of
reach of children. Provision for locking switch open (ofO
is advisable to prevent power from being turned on while
unit is being serviced. Disconnect switch, fuses, and field
wiring must comply with National Electrical Code and
local code requirements.
Route power wires through opening in unit side panel
and connect in unit control box as shown on unit label
diagram and Fig. 2. Unit must be grounded.
Affix crankcase heater warning sticker to unit dis
connect switch.
CONTROL CIRCUIT WIRING — Control voltage is
24 volts. See Fig. 3 and unit label diagram for fieldsupplied wiring details. Route control wires through
opening in unit side panel to connection in unit con
trol box.
if" HOLE FIELD POWER SUPPLY
DIMENSIONS (ft-in.)
UNIT 38AF 007 008
Length A 2-9
Width
Height
Base Rail Width D 0-10'/2
Minimum Support
Lift opening
separation
NOTE Units may be installed with any one side, except compressor access
side, within one ft of wall or other airflow obstruction as long as remaining
sides have at least 3 ft clearance Compressor side access is always 3 feet
Units may be located side by side with a minimum of 3ft between units
Allow at least a 5-ft clearance above the unit
B 2-9 2- 8Va
c 2-8
E 0-4 0- 4
F
1- 0’/4
4- 0%
2-11 '/s
O-IO'/j
1-10
Fig. 1 — Dimensions (ft-in.)
Table 2 — Weight Distribution
WEIGHT (lb)
UNIT 38AF
007 300
008 410
Oper
Wt
A B C
54
75
Support Point
78 100
116
D
68
133 86
LEFT
l-b rigging HOLE (8)
REAR
RIGHT
i HOLE
CONTROL
POWER
FRONT
TOP VIEW
Manufacturer reserves the right to discontinue, or change at any time, specifications or designs without notice and without incurring obligations.
Book 11 14 PC111 Catalog No 563-852 PrintedInUSA Form38AF-1SI Pg2 4-85 Replaces: New
Tab |3al2a
For replacement items use Carrier Specified Parts