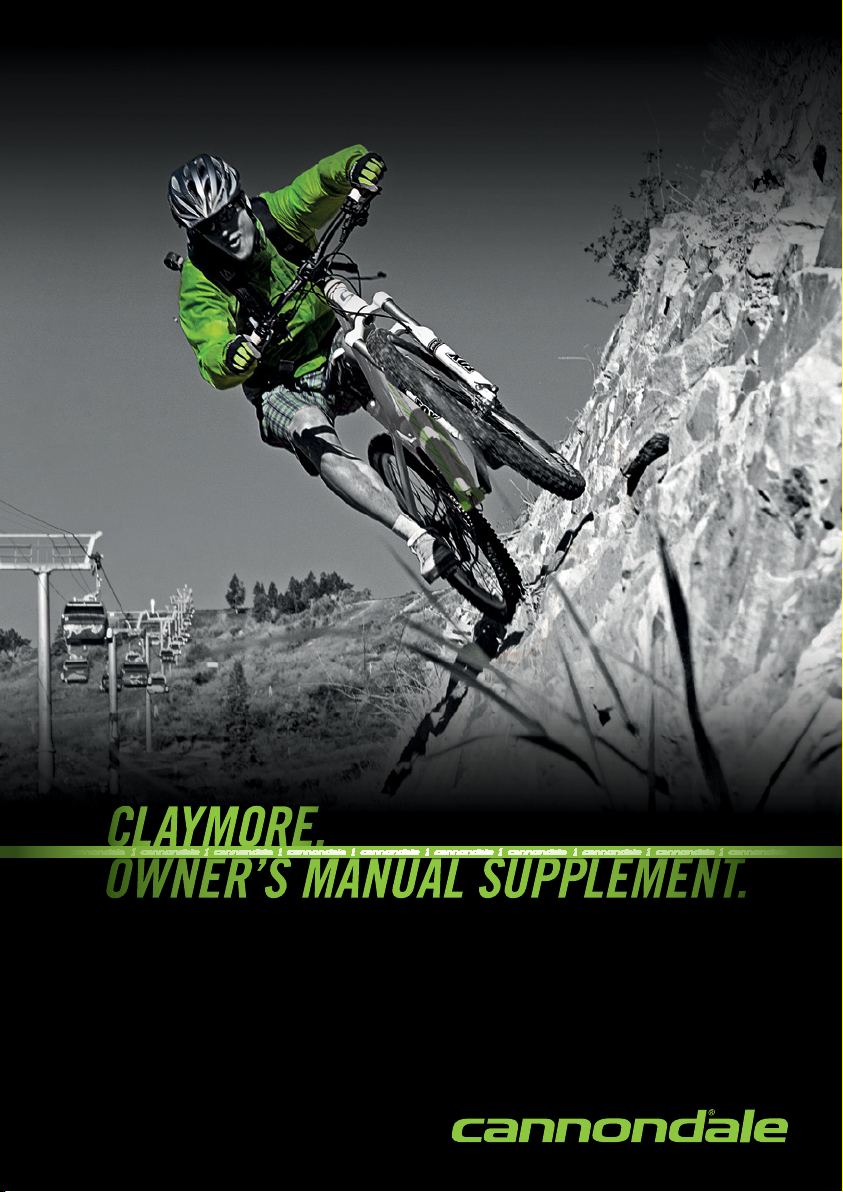
126585
OWNER’S MANUAL SUPPLEMENT.
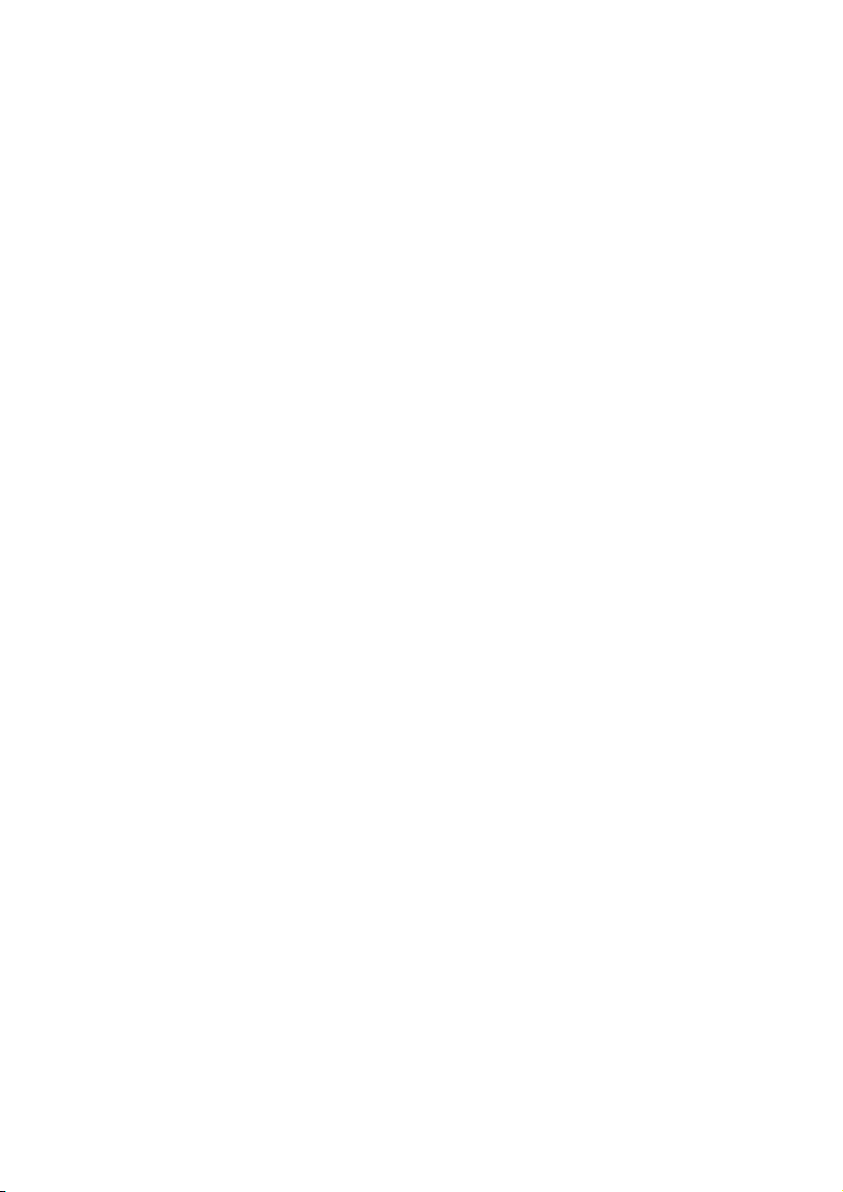
CLAYMORE
OWNER’S MANUAL SUPPLEMENT
ENGLISH
126585.PDF
EN - 03/11
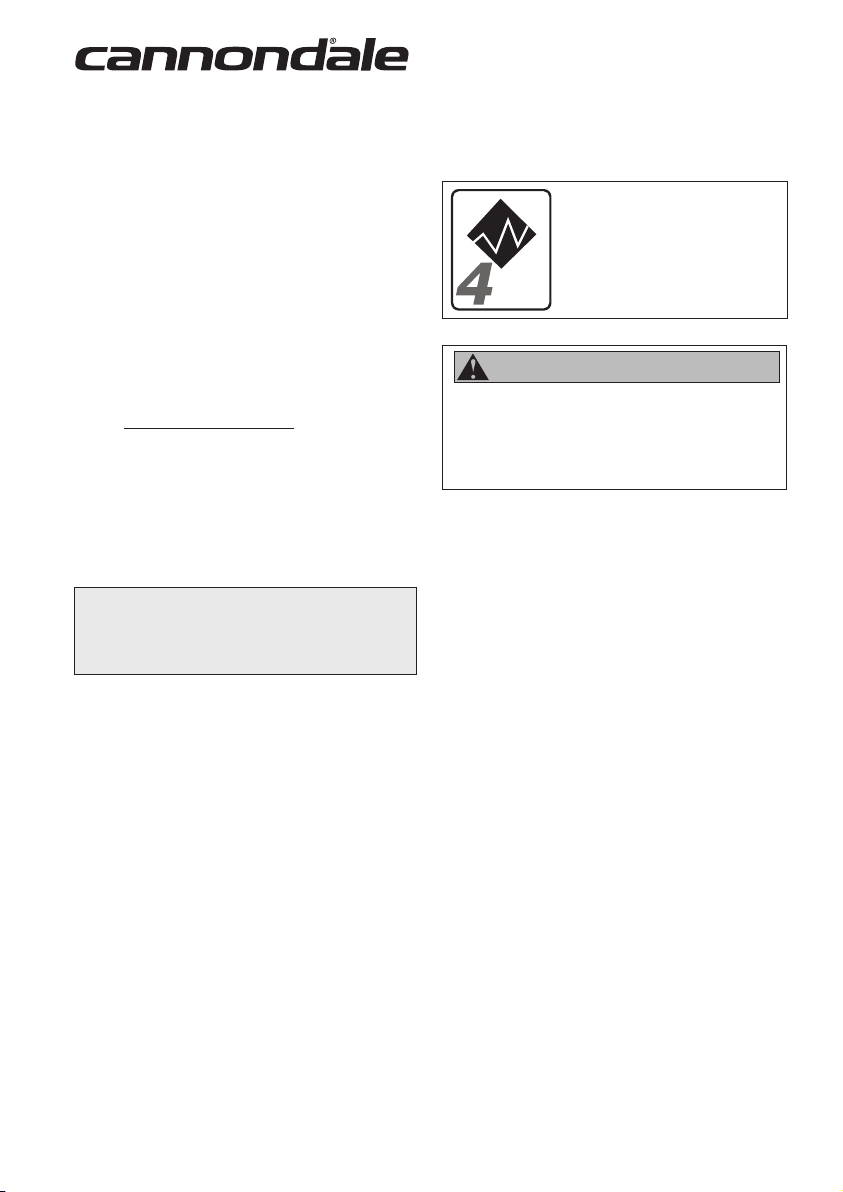
ABOUT THIS SUPPLEMENT
Cannondale Owner’s Manual Supplements provide important
model specic safety, maintenance, and technical information.
They are not replacements for your Cannondale Bicycle Owner’s
Manual.
This supplement may be one of several for your bike. Be sure to
obtain and read all of them.
If you need a manual or supplement, or have a question about
your bike, please contact your Cannondale Dealer immediately,
or call us at one of the telephone numbers listed on the back
cover of this manual.
You can download Adobe Acrobat PDF versions of any
Cannondale Owner’s Manuals or Supplements from our
website: http://www.cannondale.com/.
YOUR CANNONDALE DEALER
To make sure your bike is ser viced and maintained correctly, and
that you protect applicable warranties, please coordinate all
service and maintenance through your authorized Cannondale
Dealer.
NOTICE
Unauthorized service, maintenance, or repair par ts can
result in serious damage and void your warranty.
SAFETY INFORMATION
INTENDED USE
ASTM F2043
The intended use of all models is
ASTM CONDITION 4, OverMountain.
For extreme
o-road riding
WARNING
UNDERSTAND YOUR BIKE AND ITS INTENDED USE. USING
YOUR BIKE THE WRONG WAY IS DANGEROUS.
Please read your Cannondale Bicycle Owner’s Manual for
more information about Intended Use and Conditions 1-5.
2
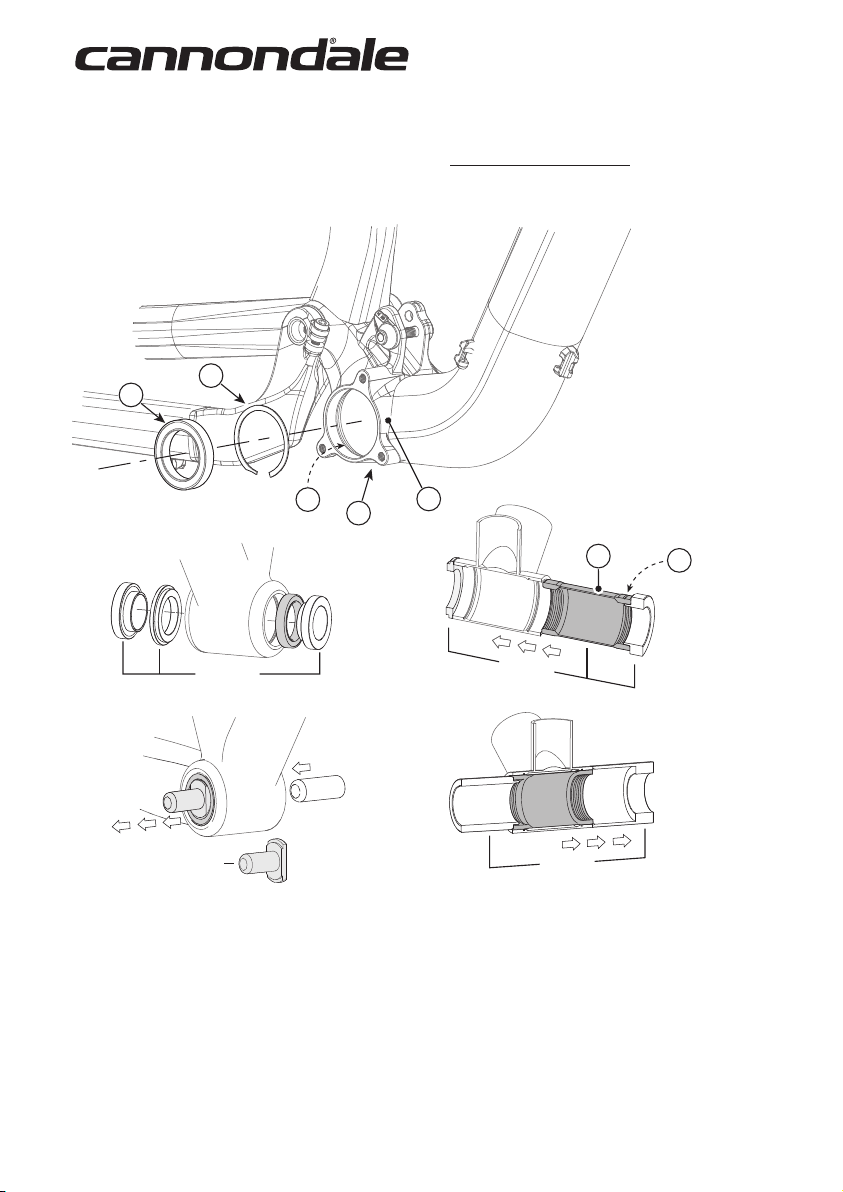
BOTTOM BRACKET
The bottom bracket shell is compatible with the BB30 Standard. See http://www.bb30standard.com/.
The SI bottom bracket adapter enables the use of standard English/73mm bottom bracket cranksets.
KT011/
3
KT010/
a
2
1
KF368/
4
Identication
1. Bottom Bracket Shell a. Bb Circlip Groove
2. ISCG03 Mount b. Adapter Drive-Side Groove
3. Circlip
4. Bearing
5. 73mm Adapter
Loctite™ 609
73mm
KF366/
73mm
5
b
4
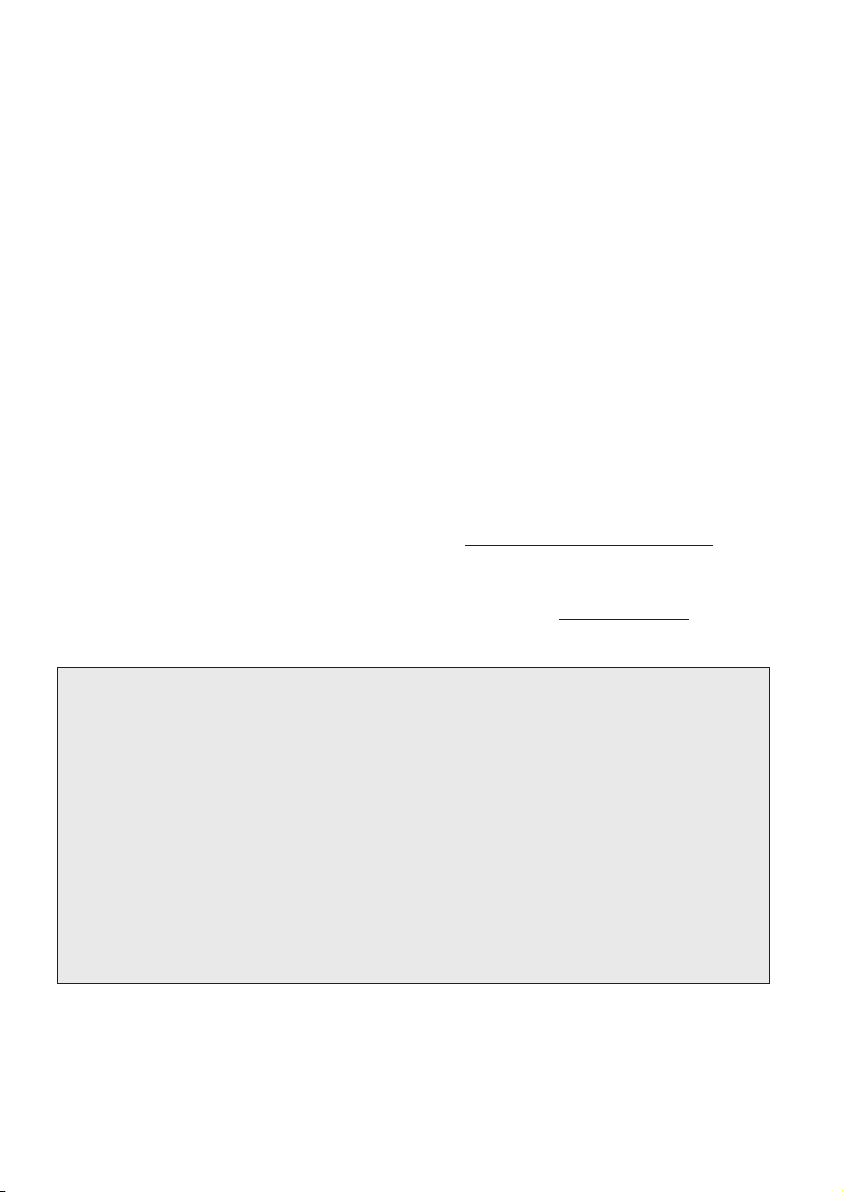
126585.PDF
Bearing Maintenance
Inspect bearing condition annually (at a minimum) and anytime the crankset assembly is disassembled or serviced. With the
crankset removed, rotate the inner bearing race of both bearings; rotation should be smooth. No play or movement inside the
shell. If the bearing is damaged, replace both bearings with new ones.
Bearing Removal/Installation (Professional Bike Mechanic Only)
Remove the old bearings with the bearing removal tool KT011/.
Reinstall bearings with a headset press and tool KT010/. Clean inside of shell apply a high-quality bicycle bearing grease to the
inside surface. Press bearing one at a time. Press each bearing until seated against the circlip. Following installation, apply a light
coating of a high-quality bicycle bearing grease to both sides of each bearing to help repel moisture.
TIP: Unless a circlip is damaged, removal is unnecessary during bearing removal. Use a small thin-blade screw driver or pick to lift the
hooked end up out of the groove and then pushing the circlip out counter-clockwise.
Adapter Removal/Installation (Professional Bike Mechanic Only)
To install, rst remove the bearings and circlips and clean the inside of the BB shell and adapter. Use a clean lint-free shop towel
dampened with alcohol. Apply Loctite™ 609 carefully to the bearing seat positions to both shell and adapter. Install the adapter
with a headset press and the installation tool KF368/. Adapter groove must be located on the BB drive side. Press until the
groove side face is ush with the drive side face of shell. Allow at least 12 hours (at 72°F) for the Loctite to cure before installing
the standard bottom bracket crankset. Follow Loctite Technical Data Sheet http://tds.loctite.com/tds5/docs/609-EN.PDF
To remove, use tool KF366/ with a headset bearing press with tool arrangement as shown. Following removal, it will be
necessary to clean all remaining Loctite residue with a before reinstalling the Si circlips and bearings. Use Loctite 768. Use a
dental pick to remove any adhesive from the grooves. For Loctite clean-up instructions : http://tds.loctite.com/
NOTICE
BEARINGS - Frequent or routine renewal of undamaged bearings is not recommended. Repeated removal and reinstallation
can damage the inside BB shell surfaces resulting in poor bearing t. Do not face, mill or machine the bottom bracket shell for
any reason. Doing so can result in serious damage and possibly a ruined bike frame.
ADAPTERS - Use only adapters/tool recommended by Cannondale. Other available adapters /tools may cause damage.
See Replacement Parts. An adapter isn’t a “repair” part, so the BB shell must be in good condition. Repeated removal and
reinstallation of an adapter, or improper tools can cause damage. Therefore it is not recommended.
Loctite 609 - Prolonged contact with the frame nish may result in discoloration or damage. Be sure to immediately wipe up
any spills and remove any compound in contact with the painted surfaces.
Do not cut, face, or use abrasives to clean the inside if the BB shell.
We strongly recommend that these procedures be performed by an Authorized Cannondale Dealer. Damage caused by
improper installation/removal is not covered under your warranty.
5
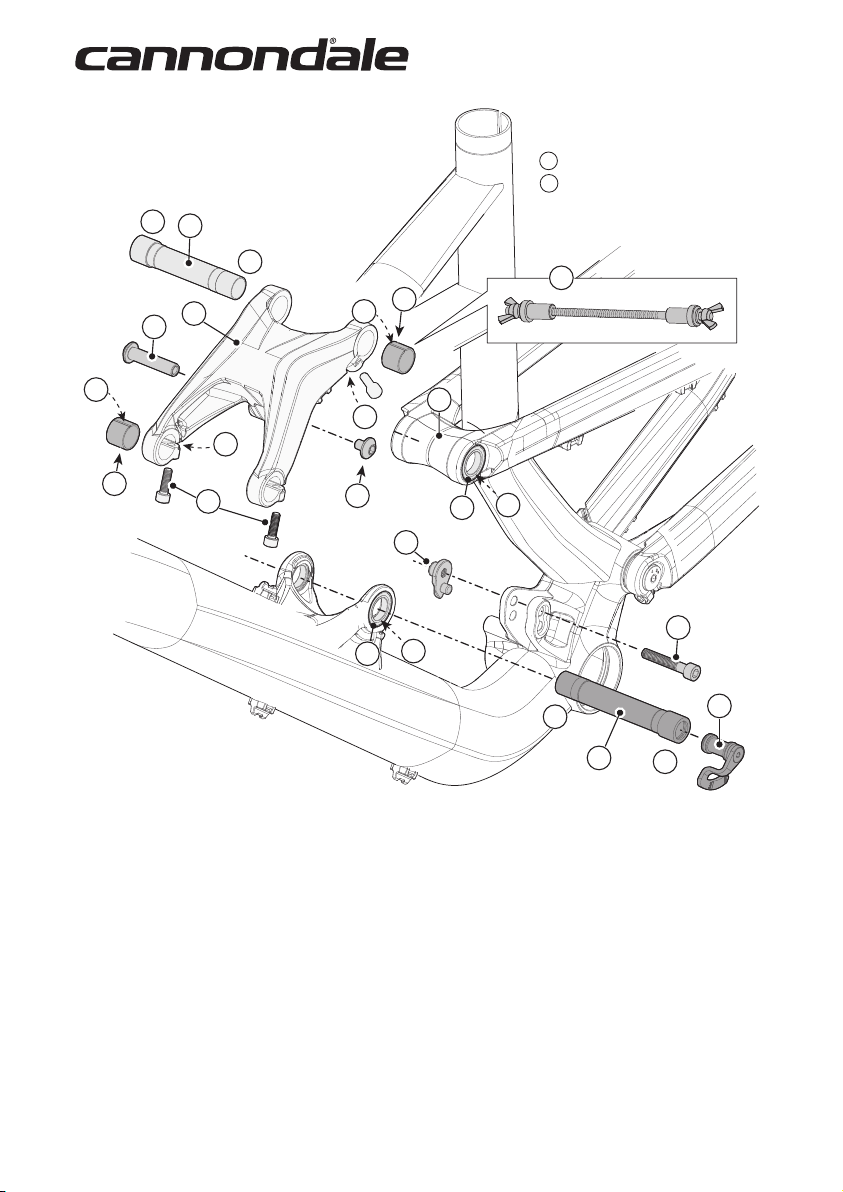
SHOCK LINK
c
2
= 5.0 Nm, 44.0 InLbs - Loctite™ 242 (blue)
8
= 8.0 Nm, 71.0 InLbs - Loctite™ 242 (blue)
9
1
9
M8X35
a
a
4
8
M5X16 (4X)
Identication
1. Shock Link
2. SS Lever Axle
3. DT Link Axle
4. Main Shim
5. Link Tool (inc. KP169/)
6. Bearing (61802-2RS, 15X24X5)
7. Seat Stay
8. Pinch bolts
9. Shock Mounting Bolt
10. Gemini Nut
11. SAG Indicator
a. gap
b. bearing inner race
c. large end
d. small end
d
4
a
a
9
6
7
6
10
b
KP169/
b
5
9
M6X35
d
3
11
c
Be sure to loosen the pinch bolts of link before assembly.
Before assembly, inspect all bearings for good condition. Replace if necessary.
Clean and apply Loctite 242 (blue) to the pinch bolt threads.
Tighten to 5 Nm, 44 InLbs.
Clean and apply light grease to pivot axles and main shims.
Insert DT Link Axle and SS Lever axles from opposites side of the link as shown.
Route cables correctly around pivot. See Cable Routing.
6
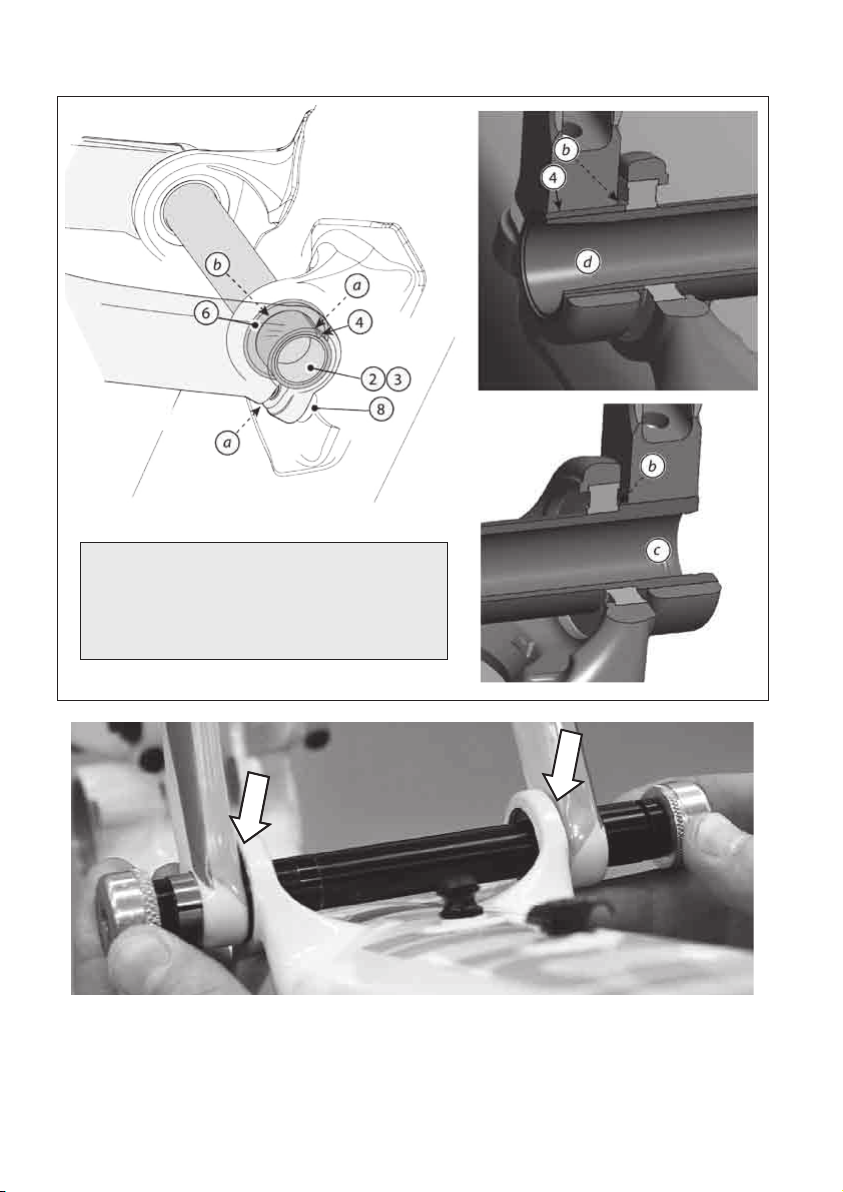
NOTICE
Incorrect assembly (pivot/shim) can result in linkage play,
accelerated wear, or damage.
Do not over-tighten. Use a torque wrench.
126585.PDF
Use KP169/ to press link pivot axles and main shim together as shown. Before tightening pinch bolts, make sure both the
shim and axle are seated against the bearing inner race (upper), and the gaps (arrows) between bearing and link arm should
be the same on each side. You can center the link easily shifting it left or right to do it before the bolts are tightened.
7