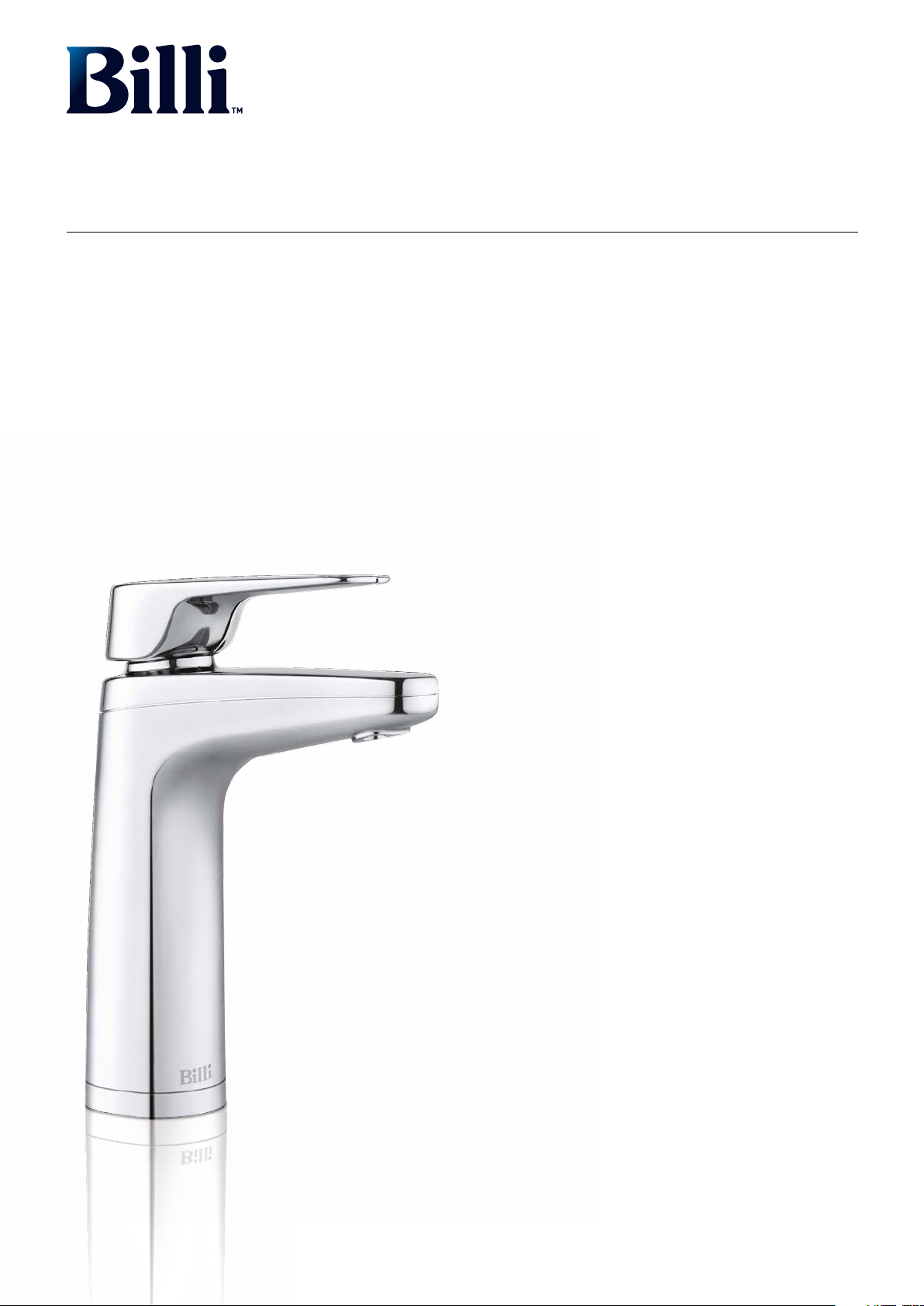
Installation guide
Billi B-5000
Tap options XL, XT, XR
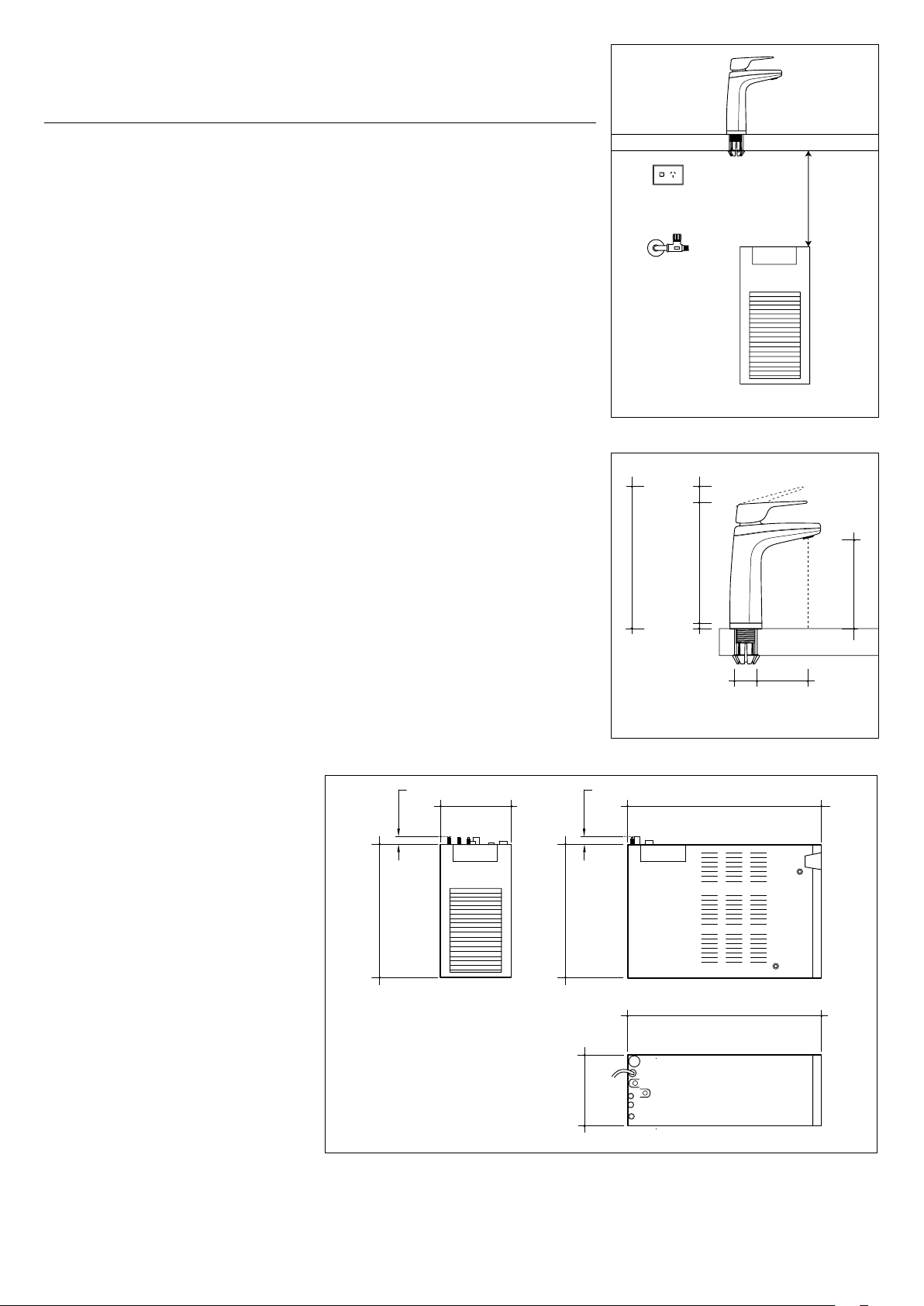
Installation requirements
XL, XT, XR.
Components for Billi B-5000
Before commencing installation,
ensure you have identified the following.
1. Underbench module
2. Dispenser upper with tubing
3. Dispenser base & mount
4. Barb locking bush
5. 4mm chrome screw & allen key
6. Large washer
7. Tube spring clamps x 3
8. 600mm flexible braided hose
9. Filter Cartridge (installed)
10. User guide
11. Warranty Registration Card
12. Warning label
Additional Components – XR
13. Remote panel kit
Determine Unit Location
Plan the installation. Dispenser tube lengths,
position of power and water outlets, required
air space around the underbench module and
access for service must be considered before
cutting tube lengths. Refer to Diagrams 1,2
and 3 for clearances around the dispenser
and unit. Unit must be installed horizontally
with plastic vent panel facing to front of
cupboard. The B-5000 is designed for internal
installation only.
Water Supply
The B-5000 must only be connected to a cold
water supply. A ½” BSP stop tap (not supplied)
is to be installed in an easily accessible
position within 600mm from the B-5000
water supply inlet. The B-5000 incorporates
a certified pressure limiting and backflow
prevention device. Do not fit an additional
pressure limiting valve.
Dynamic inlet supply pressure:
Min. 250 kPa, max. 1000 kPa
Supply Temperature: min. 5°C max. 30°C.
Power Requirements
A single 10 amp standard power
outlet is required. All B-5000 units supplied
with 1 metre flex cord and plug.
20mm
180mm
Cupboard Dimensions:
220mm Minimum Width
365mm Minimum Depth
Stop Tap
(Installed by Plumber)
Max 450mm from Unit
205mm
bench
thickness
1mm-48mm
20mm
20mm
175mm
10mm
Tubing
removed
for clarity
Power
Outlet
Tubing
removed
for clarity
Tubing
removed
for clarity
35mm 70mm
498mm
800mm
Tube Length
Supplied
Diagram 1
130mm
Diagram 2
Do not install with water that is
microbiologically unsafe or with water
of unknown quality without adequate
disinfection before or after the system.
Systems certified for cyst reduction may
be used on disinfected water that may
contain filterable cysts.
Ventilation
The B-5000 requires some cupboard
ventilation and adequate air space as well
as an unobstructed clearance of at least
100mm on each side of the underbench unit
is necessary.
IMPORTANT: Insufficient ventilation will cause
inefficient refrigeration system operation,
increasing power usage.
2
340mm 340mm
FRONT SIDE
180mm
498mm
TOP
Diagram 3
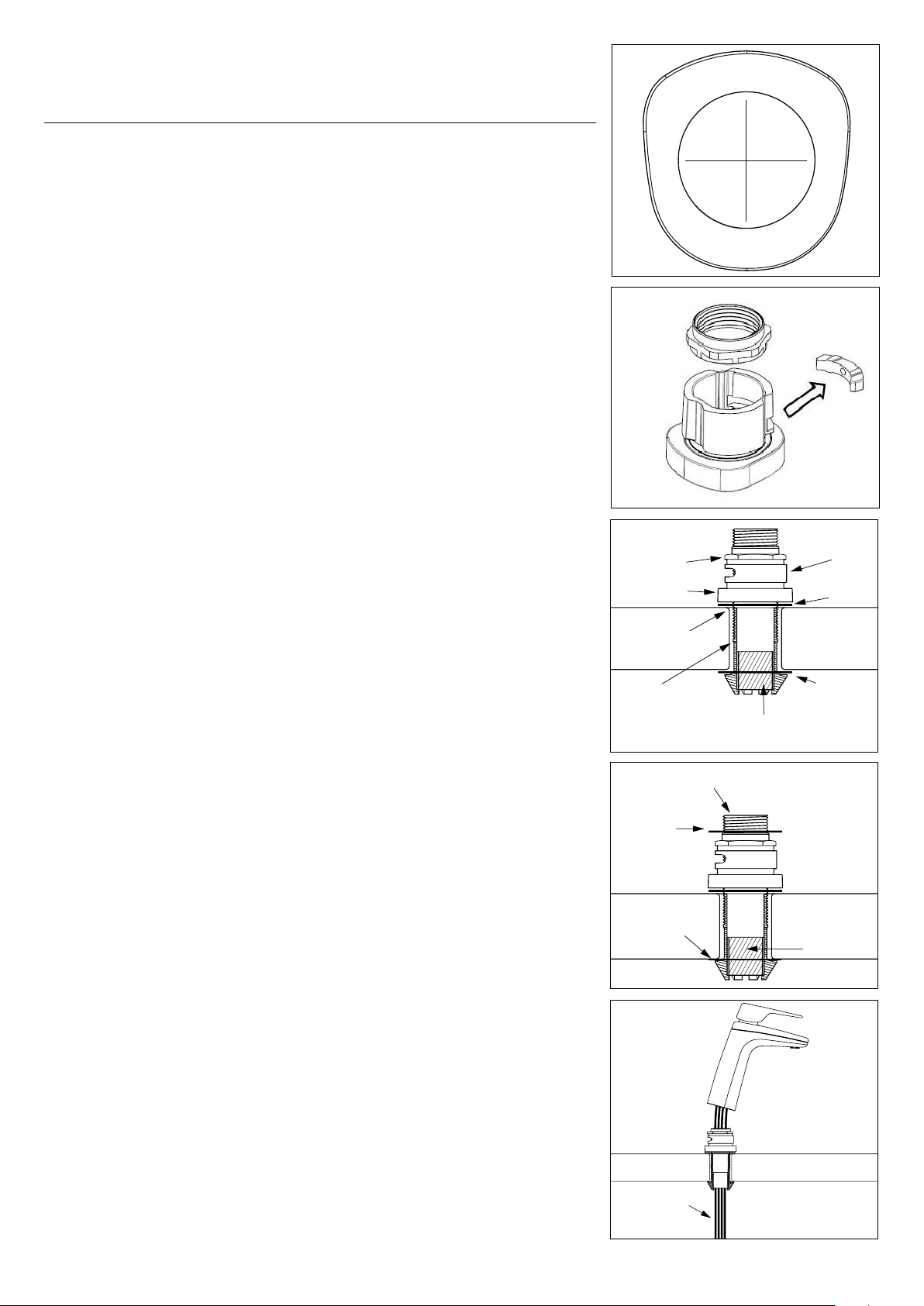
Installing the dispenser
XL, XT, XR.
IMPORTANT: This Billi appliance is to be installed by a licensed trades person in accordance with
AS/NZS 3500.1 and AS/NZ 3500.2 and in compliance with applicable state regulatory requirements.
For correct operation of this appliance, it is essential to observe the manufacturer’s instructions.
1. Install Dispenser Assembly
Determine position of dispenser mounting
hole in sinktop or benchtop.
Dispenser base
template (Diagram 4) may be cut out and
used to assist in correct positioning. Refer to
Diagram 2 for clearances allowed. Hole size
required is ø32mm.
Stainless Steel Sinktop
A suitable 35mm hole punch (Part no:
857901) is available as an accessory from Billi
Australia Pty Ltd. If possible, cut hole with die
mounted below the sinktop surface so that
burr is pulled downwards. Alternatively,
remove burr and radius edge of hole with fine
file. This allows barbed dispenser
mount to slide smoothly into mounting hole.
Timber/Laminate Benchtop
Maximum benchtop thickness is 50mm.
Cut 32mm hole in appropriate position*.
When drilling through a particle board
bench top, take care to avoid a large chip
breaking away as drill breaks through
underside surface. We recommend drilling
a small pilot hole through benchtop, partially
drilling the 32mm hole from underneath and
then completing drilling the hole from above.
The large 30mm washer supplied may be
used to secure barb where underside particle
board bench top has chipped away.
* For stone or granite bench tops you
will require a certified stone mason
to pre-drill the hole.
2. Activate Dispenser Swivel Feature
To activate the swivel feature of your
dispenser, you will need to remove the
locking piece from the dispenser base.
Simply push out the piece as show in
Diagram 5. This will allow the tap to
move 45 degrees to the left and right.
IMPORTANT: Remove burrs and check internal
bore is completely smooth.
4. Fit Dispenser Head Assembly
a. Feed dispenser tubing and loom through
centre hole in the following order:
i. Dispenser power cord.
ii. Silicone tubes.
b. Gently pull hoses from under the
bench top, do not attempt to force tubing
through with a pointed object as silicone
tube is easily punctured. Check tubing
is not kinked or twisted.
c. Turn dispenser head assembly to
approximately 60° from the straight
ahead position of dispenser base.
Slide head assembly onto base assembly
whilst gently pulling tubing downwards
from underneath to prevent tubing
bunching and kinking. Mounting lugs
will pass nut and slide down the 3
grooves on the swivel bearing.
d. Once fully down, turn dispenser to
straight ahead position. Fit chrome
plated M4 retaining screw to lower rear
threaded hole and tighten using the allen
key supplied. If swivel feature activated
check dispenser now swivels smoothly
45° in each direction.
dispenser base
Locking Nut
Base Casting
Ensure burr
is removed
& edge has
a radius
Barbed
Mounting
Shaft
Barb locking bush in position
Remove burrs after cutting and
ensure internal bore is smooth
Cut o
excess
thread
template
Diagram 4
Diagram 5
Swivel
Bearing
Gasket
D Washer
required
Diagram 6
3. Fit Dispenser Base
a. Cut a 32mm hole in sinktop or benchtop.
Remove burr if protruding upwards.
b. Push barbed mounting shaft through
mount hole.
c. Insert barb locking bush as shown in
Diagram 6. Finger tighten nut.
d. Ensure barb is centred in mount hole
before tightening. Check position of base
ring and gasket.
e. Moderately tighten locking nut using
multigrips or spanner. Take care to avoid
overtightening nut which may break the
plastic threaded shaft.
f. Place large D washer over thread as
shown in Diagram 7.
g. Cut off excess threaded shaft with a
hacksaw, using washer as a cutting guide.
(Diagram 7)
D washer
Silicone
tubing
Alloy locking
bush
Diagram 7
Diagram 8
3