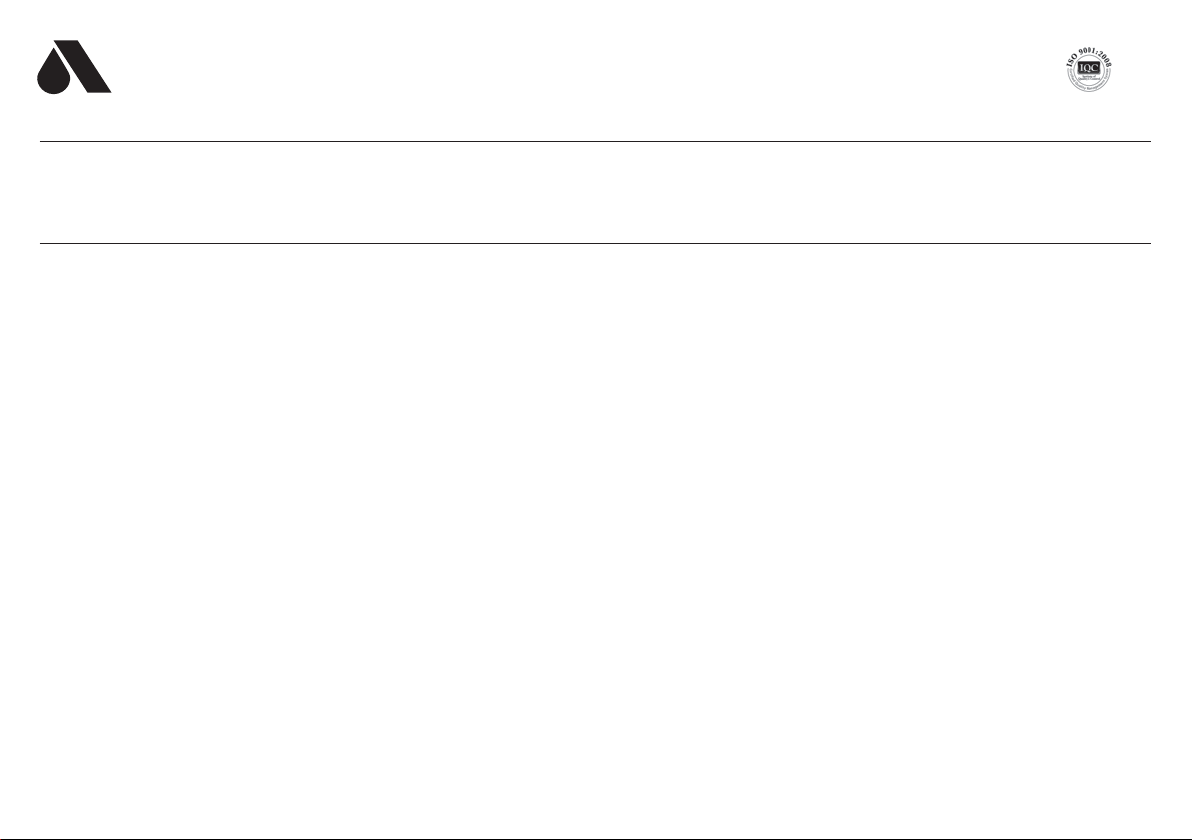
A.R.I.
A.R.I.
Flow Control Accessories Ltd.
Kfar-Charuv 12932 Israel
Tel. 972-4-6761988 Fax. 972-4-6763402 www.arivalves.com
Backflow Preventer RP-500 - Reduced Pressure Zone
Approved under : USA : NSF61 (Drinking water), ASSE 1013, AWWA C511, Approved by the Foundation for Cross Connection Control and Hydraulic Research at the
University of Southern California, Listed for Uniform Plumbing Code. Australia : AS4020 (Drinking water), Watermark AS2845.1. France : ACS.
0302AusM-RP500-10
Installation
(a) The RPZ device must be installed in an accessible
location for periodic field-testing and maintenance.
(b) The location selected should have adequate drainage
for relief valve discharge. Drainage may be piped away,
a funnel RPZ is provided (See figure). The RPZ should
never be placed where it may become submerged in
standing water.
(c) Flush all upstream piping thoroughly to remove
debris prior to installing the RPZ.
(d) Assemble the components before positioning into
permanent pipe installation.
(e) Install the RPZ in a horizontal position with
adequate clearance from walls and/or obstructions, for
testing and maintenance.
A 305 mm to 338 mm clearance between the lower
most portion of the RPZ and floor should be provided.
(f) It is recommended that a “Y” strainer be installed
just upstream of the RPZ assembly to eliminate any
debris from entering the device and fouling the check
and/or relief valve.
(g) After installing the assembly and with the outlet
shut-off valve (#2), pressurize the RPZ device and
bleed air through test cock #3 Then open the outlet
shut-off valve (#2).
Note: If water continues to drain from the relief valve,
check the Trouble Shooting section for probable
causes and solutions.
Installation Tips
(a) Recommendation: Do not install in areas subjected
to freezing for a long period of time.
(b) The product must be protected from excessive
pressure increases. Pressure increases can be caused by
thermal expansion or water hammer. These excessive
pressure situations must be eliminated to protect the
valve and system from possible damage.
(c) Do not use any pipe glue, oil grease or solvent on
any parts unless instructed to do so.
(d) Do not force parts. Parts should fit together freely.
Maintenance Instructions
A. Disassembly - RP 500.
1. Close the outlet shut-off valve (#2), then close the
inlet shut-off valve (#1).
2. Bleed pressure from the assembly by opening test
cock #1, #2, #3.
3. Caution The cover is spring-loaded and should be
removed carefully to avoid personal injury.
3.1. Remove the relief valve cover bolts while holding
the cover down.
3.2. Lift the cover straight up.
3.3. Remove the relief valve kit.
3.4. Remove the spring.
3.5. Remove the retainer.
3.6. Extract the check valves.
Note: All the disassembled parts may now be cleaned
and reassembled or, depending on their condition,
discarded and replaced with a new assembly from the
repair kit. O-rings should be cleaned or replaced as
necessary and lightly greased with the NSF approved
silicon based grease.
B. Assembly - RP 500.
1. Install the check valves. The valves must be securely
in place.
2. Install the retainer.
3. Put the spring to its place.
4. Install the relief valve kit.
5. Put on the cover, hold it down and close the bolts.
Caution The bolts have to be secured with a
recommended torque of:
2.5 Kg/m. for models DN 15/20/25
9 Kg/m. for models DN 32/40/50
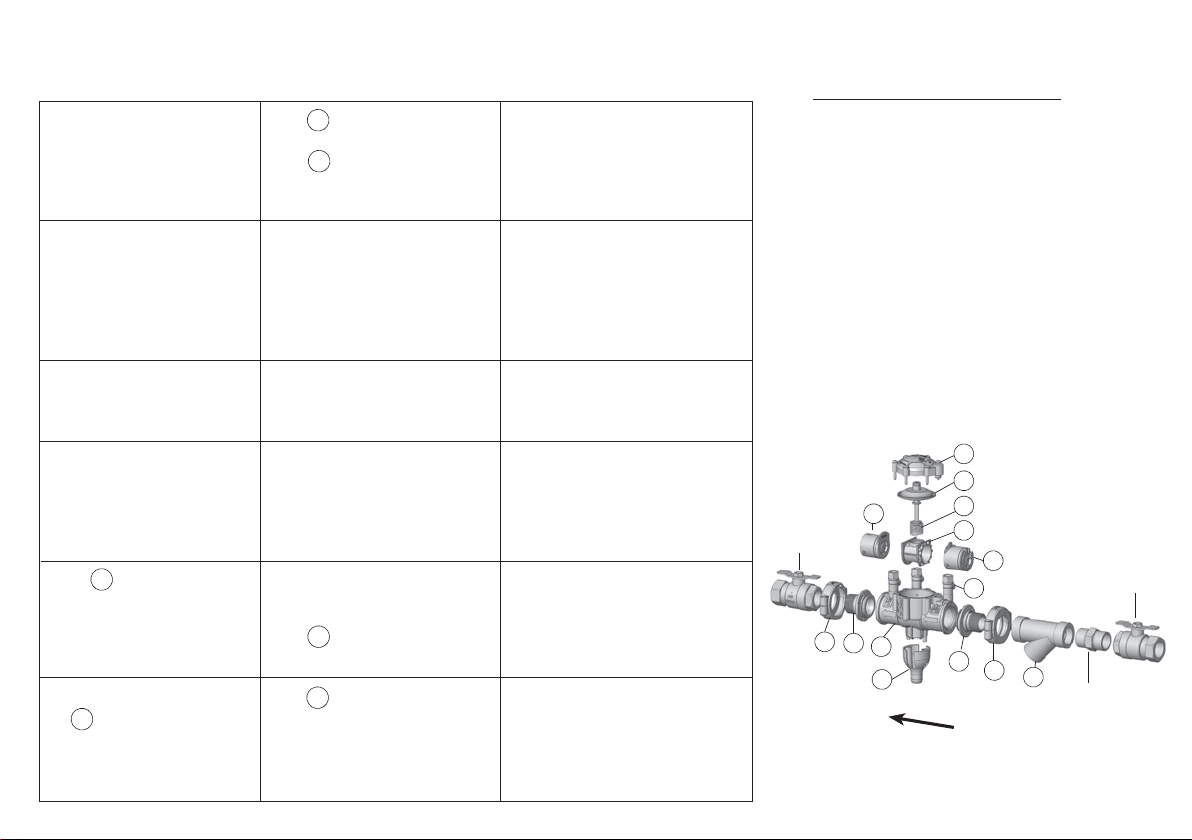
PARTS LIST TROUBLE SHOOTING GUIDE
Symptom Cause
1. Relief valve continuously
discharges during no-flow
conditions.
2. Relief valves discharges
continuously during flow and
no-flow conditions.
3. Relief valve discharges
intermittently in a "spitting"
action during no-flow condition.
4. Relief valve does not open
during field test no.1
5. No. 6 check valve fails to
hold backpressure.
6. Pressure differential across
no. 5 check valve is low during
field test no. 3 a (does not meet
0.2 bar minimum)
a. No. 5 check valve fouled with
debris.
b. No. 6 check valve fouled with
debris coupled with a backpressure
condition.
a. Relief valve fouled with debris.
b. Damaged diaphragm (allows water
to pass through, from inlet to zone).
c. The passage to inlet side of
diaphragm plugged.
Pressure fluctuations (water hammer)
from supply.
a. Outlet shut-off valve (#2) not
closed completely.
b. Test equipment improperly
installed.
a. Outlet shut-off valve (#2) not
closed completely.
b. No. 6 check valve fouled with
debris.
a. No. 6 check valve fouled with
debris.
b. Upstream pressure fluctuations
causing inaccurate gauge reading.
Corrective Action
a. Inspect and clean the seat and seal.
b. Inspect and clean the seat and seal.
a. Inspect and clean relief valve seat
disk and seat.
b. Replace the relief valve kit.
c. Inspect and clean passage in cover
and body.
Eliminate or reduce pressure
fluctuations.
a. Close outlet shut-off valve (#2) or
inspect for possible through leakage.
b. Recheck test procedure.
a. Close shut-off valve #2 or inspect
for possible through leakage.
b. Inspect and clean the seat and seal.
a. Inspect and clean the seat and seal.
b. Eliminiate pressure fluctuation.
No. Part
1. Cover Assembly
2. Relief Valve Assembly
3. Relief Valve Spring
4. Retainer
5. Inlet Check valve Assembly
6. Outlet Check valve Assembly
7. Body Assembly
8. Test Cocks (#1, #2, #3)
9. Adaptor Assembly
10. Clamp Assembly
11. Funnel
12. Strainer
10
6
9
7
11
Outlet Shut-off
Valve (#2)
1
2
3
4
5
8
9
10
12
Inlet Shut-off
Valve (#1)
Adaptor