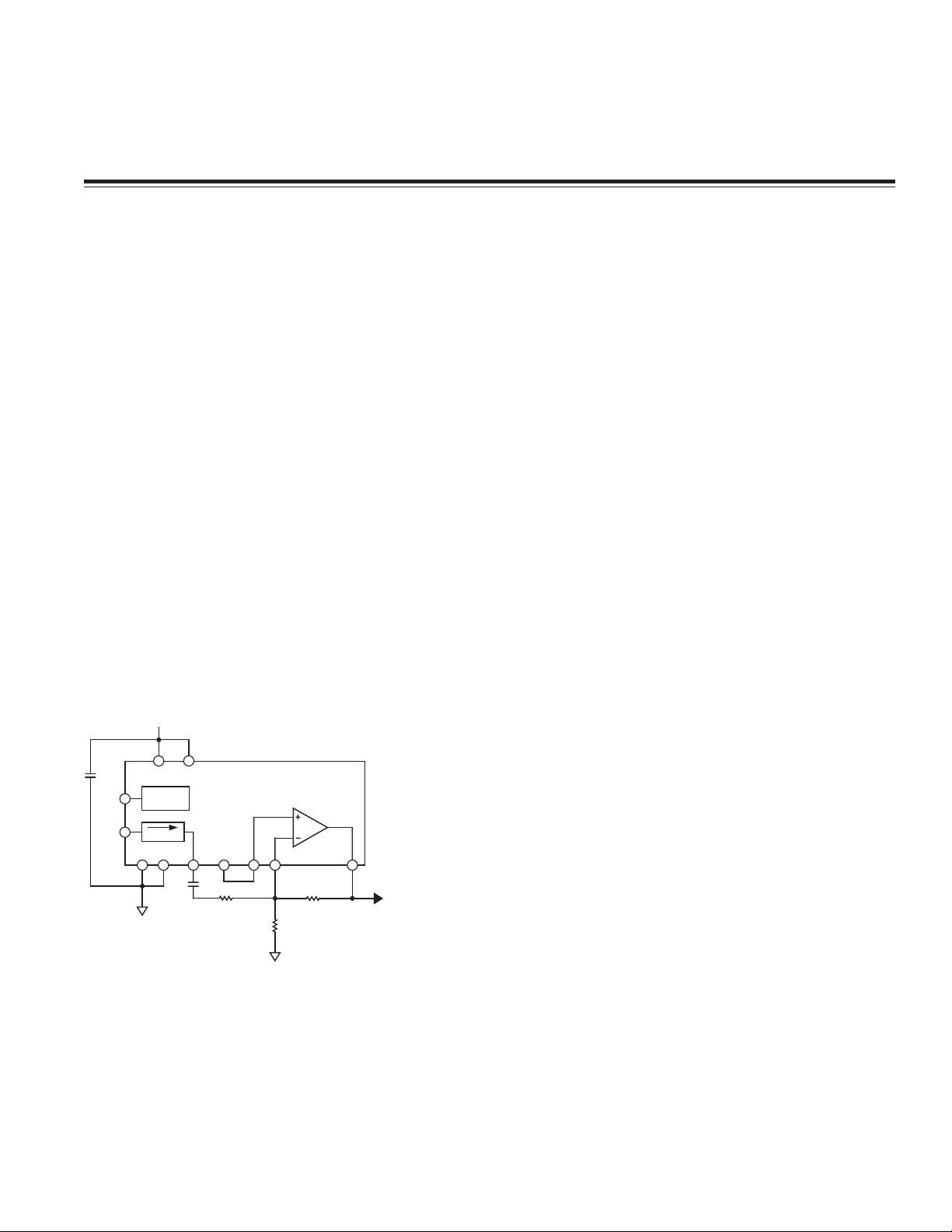
AN-598
a
APPLICATION NOTE
One Technology Way • P.O. Box 9106 • Norwood, MA 02062-9106 • Tel: 781/329-4700 • Fax: 781/326-8703 • www.analog.com
Temperature Compensation Techniques
for Low
Introduction
Analog Devices’ iMEMS accelerometers’ ability to sense
static acceleration make them uniquely suited for high
performance tilt measurement systems. However, the
0
g
stability over temperature performance of these sensors may, initially, lead one to believe that they would
be unusable over wide temperature ranges. This application note describes several techniques to compensate
for 0
g
drift over temperature.
Analyze the Application
Each temperature compensation strategy is suitable for
only certain applications. In order to find a practical temperature compensation technique, the first step must be an
evaluation of the application. The most effective technique will usually be one where the static acceleration
(dc) component can be ignored, and the accelerometer
ac-coupled. The simplest manifestation of this is shown in
Figure 1.
g
iMEMS® Accelerometers
by Harvey Weinberg
Digital Trickery
Often, simple ac-coupling is not practical. In applications where the input stimulus frequency range is under
0.5 Hz, the coupling capacitor may become rather large.
Fortunately, similar results can be achieved by resorting
to a clever algorithm.
In applications where small, infrequent changes in inclination must be detected, the following technique is very
effective: maintain a long-term average (several minutes)
of the accelerometer output in memory and subtract the
actual accelerometer measurement from the long-term
average. As temperature changes rather slowly in the
real world (rarely faster than 1∞C per minute), the longterm average will slowly change as temperature causes
the accelerometer output to drift. The actual stimulus will
have a negligible effect on the long-term average as it
rarely occurs, compared to the large number of samples
taken to make the average.
+5V
TEMP
SENSOR
SENSOR
47
0.1F
1314
8
ADXL105
9
249k
1110
402k
634k
12
OUTPUT
2.5V 400mV/g
0.1F
1
6
Figure 1. AC-Coupling the ADXL105
Simple ac-coupling is most effective in applications
where one is most interested in sensing shock, vibration,
or fairly high speed changes in inclination (e.g., checking
if something has fallen over or been picked up).
Another method of measuring small changes in inclination while rejecting 0
for a certain acceleration rate of change (⌬ angle/⌬ time).
The apparent acceleration rate of change due to temperature drift will be very slow (less than 80 m
1∞C per minute rate of change of temperature) because
temperature is a slowly changing parameter, whereas
actual tilt angle changes are usually much faster. This
technique is commonly used in automobile tilt alarms
where two-degree inclination changes (35 m
detected in an environment where the temperature can
change as much as 50∞C in an hour. See the Car Alarm
Reference Design on the Analog Devices website at:
www.analog.com/technology/mems/markets/auto-
motive/ref_design.html for more information.
Brute Force Techniques
If none of the above-mentioned techniques is compatible
with the application, some form of hardware temperature compensation may be required.
g
drift due to temperature is to look
g
per second for a
g
) must be
REV. 0
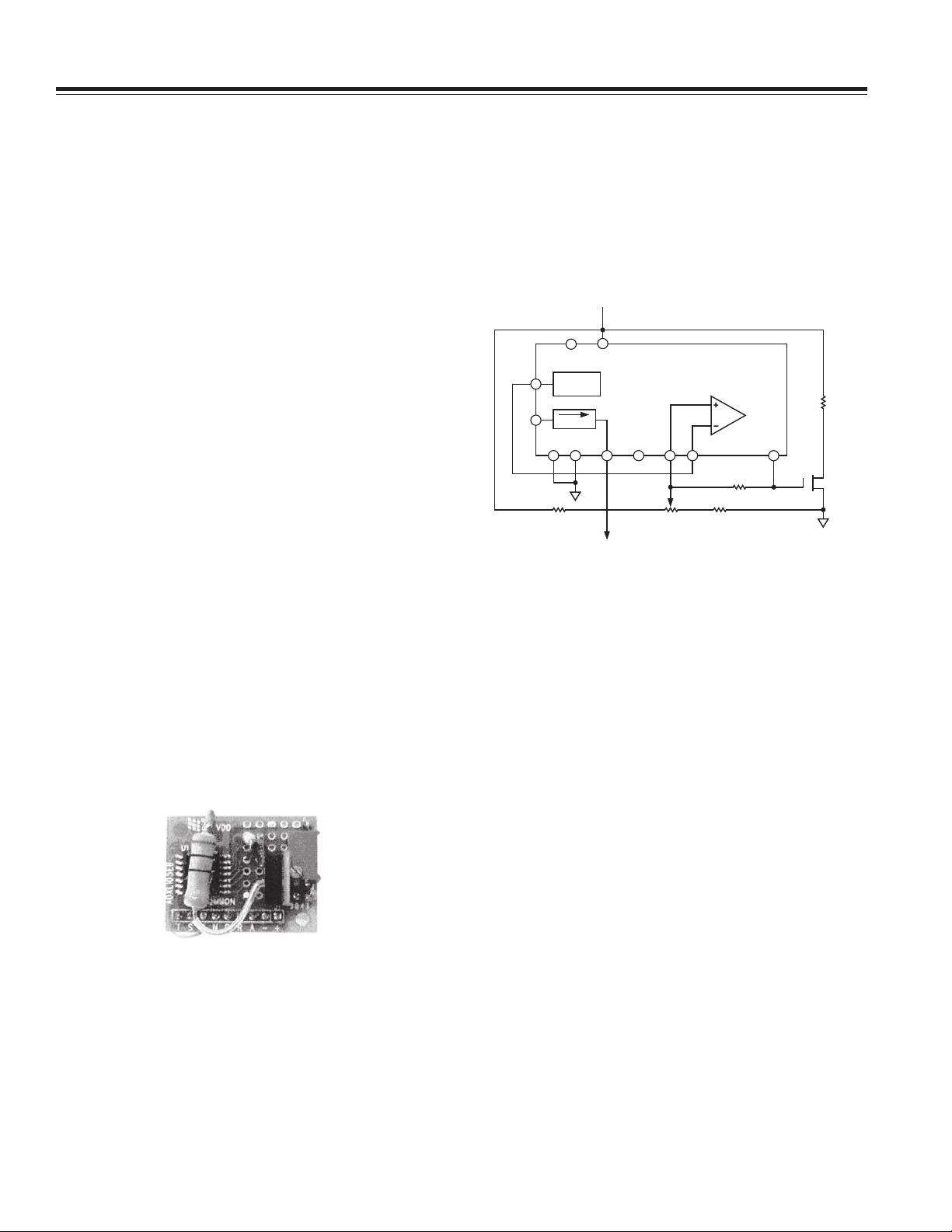
AN-598
Each accelerometer is “born” with a given temperature
characteristic that does not change over its life. Since
both the magnitude and sign of the temperature coefficient are variable from unit to unit, the temperature
compensation technique cannot simply consist of a temperature sensor in the feedback loop of an amplifier.
There are two basic techniques that can be used:
temperature mapping or ovenization. Temperature mapping is fairly straightforward in concept. A temperature
sensor is added to the circuit and the temperature is varied
while there is no stimulus (other than gravity) to the
accelerometer. The accelerometer output is read and used
to construct a compensation table or a formula that is
later used for temperature compensation. Since the
temperature characteristic of iMEMS accelerometers is
fairly linear, usually only two or three temperature points
are needed.
Normally the software used to construct the compensation table or formula is resident in the system
microcontroller and the temperature sweeps are performed during system level test or burn-in. In some
systems, there is even no need to perform a temperature
sweep, since the system can be made self-learning. For
example, an earthquake monitor can be built and then
warehoused in an unheated space for a few days. As the
temperature changes, the system learns how the temperature changes affect the acceleration signals. As long
as the systems do not experience any movement during
the “learn time,” the compensation table will be correct.
Ovenization solves the temperature drift problem by fixing
the temperature to some value at or higher than the maximum ambient temperature. This technique is most easily
and accurately realized with accelerometers that have an
on-chip temperature sensor such as the ADXL105. The
simplest manifestation is shown in Figure 2.
Here a power resistor is mounted on top of an ADXL105.
The on-chip temperature sensor is connected to the
inverting input of the ADXL105’s uncommitted op amp
while the noninverting input is connected to a fixed voltage chosen to correspond with the on-chip temperature
sensor’s output voltage at the desired temperature set
point. The uncommitted op amp output controls a small
MOSFET that switches power to the resistor. The schematic is shown in Figure 3.
+5V
13
14
8
OUTPUT
ADXL105
9
1k
TEMPERATURE
ADJUST
4
2W
HEATER
RESISTOR
1110
2k
750k
12
IRF530
1
6
TEMP
SENSOR
SENSOR
47
2k
ACCELERATION
Figure 3. Schematic for ADXL105 Ovenization Circuit
Using the values shown in Figure 3, the 0 g drift due to
temperature went from 216 m
g
to 44 mg over a 0∞C to
70∞C range (3.1 mg/∞C without ovenization to 0.44 mg/∞C
with ovenization).
The main disadvantage of ovenization is the relatively
high power consumption (approximately 6 W) which
makes it impractical for battery-powered systems.
Conclusion
There are a variety of methods that can be used for
temperature compensation. In order to choose one effectively, one must examine the application carefully and
capitalize on its particular requirements and possibilities.
The most effective methods of temperature compensation often use no hardware at all, only clever algorithms.
E03043–0–10/02(0)
Figure 2. Using a Power Resistor as a Heating Element
to Ovenize an ADXL105
©2002 Analog Devices, Inc. All rights reserved. Trademarks and
registered trademarks are the property of their respective companies.
–2–
PRINTED IN U.S.A.
REV. 0