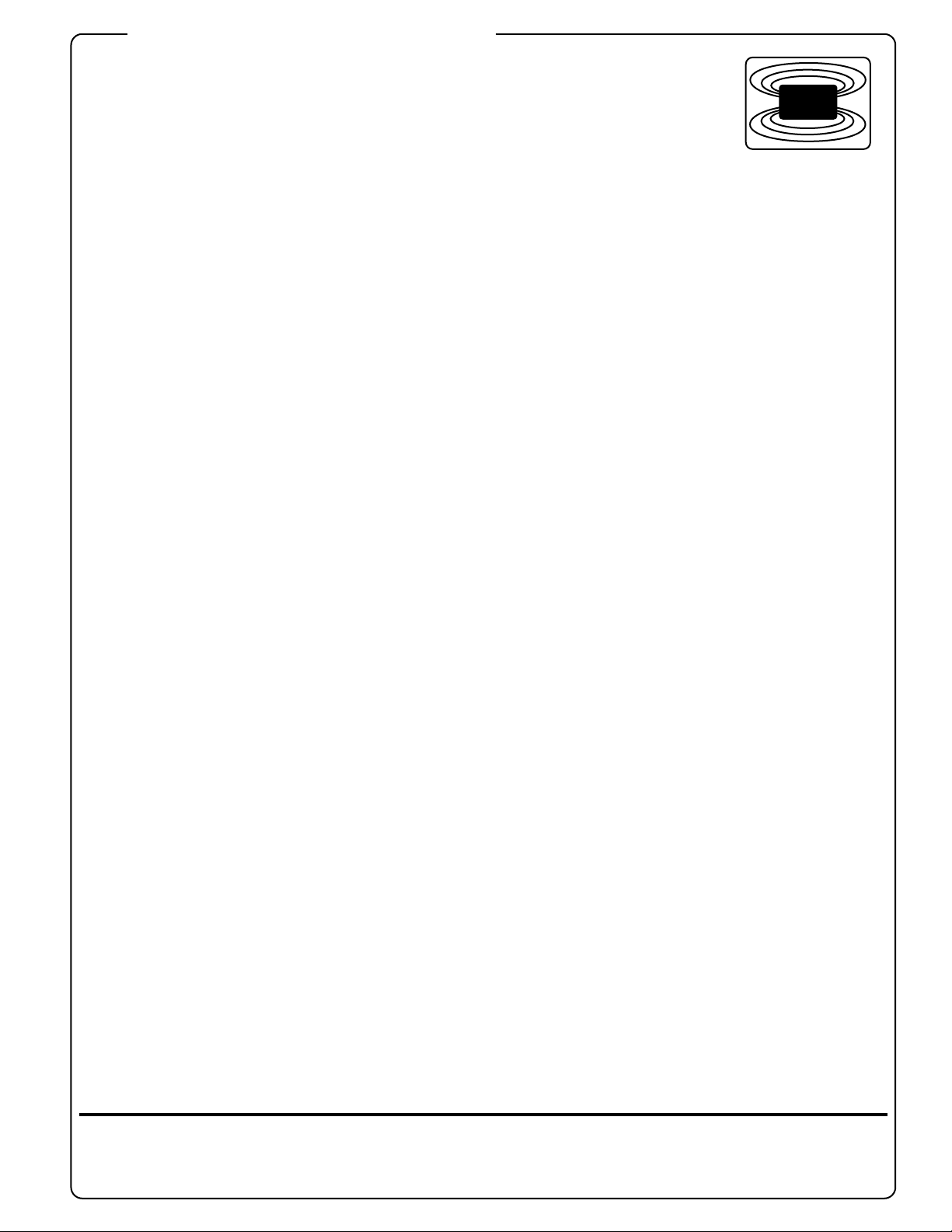
EXCELLENCE IN MAGNETICS AND CRYOGENICS
AMI
MODEL 187 LIQUID LEVEL
CONTROLLER
INSTALLATION, OPERATION, AND
MAINTENANCE INSTRUCTIONS
American Magnetics, Inc.
PO Box 2509, 112 Flint Road, Oak Ridge, TN 37831-2509, Tel: 865 482-1056, Fax: 865 482-5472
March 1998
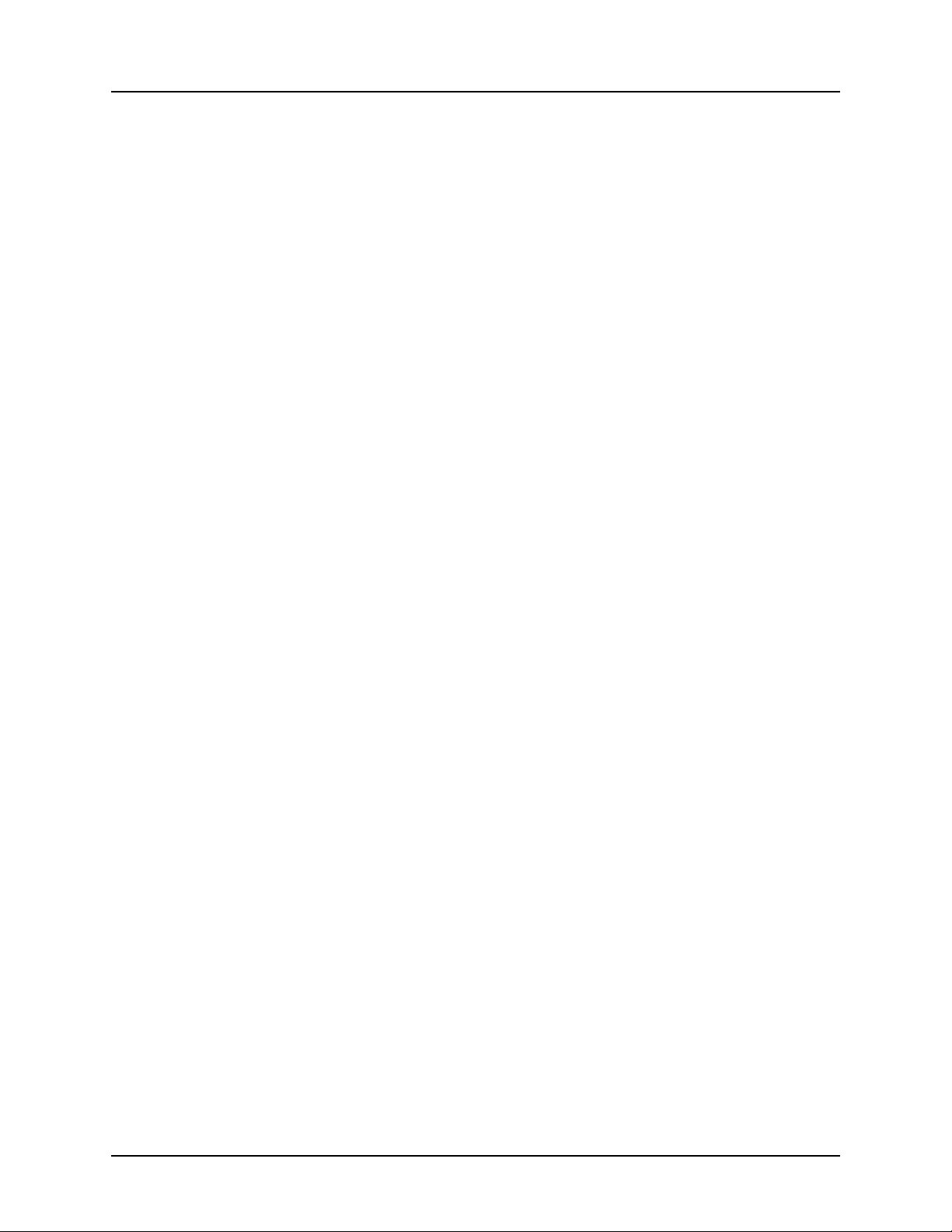
Model 187 Liquid Level Controller
AMI Order Number:_____________________
Shipping Date:_________________________
Model 187 Serial #:______________________
Firmware Revision:_____________________
Input Power Requirements:___________________________________________________________
Sensor Length (mm):_____________________________________________________________
Calibration Passcode:____________________
Maximum Dielectric: _________________
_____________________________________________________________________________________
_____________________________________________________________________________________
_____________________________________________________________________________________
_____________________________________________________________________________________
_____________________________________________________________________________________
_____________________________________________________________________________________
_____________________________________________________________________________________
_____________________________________________________________________________________
All products manufactured by AMI are warranted to be free of defects in materials and
workmanship and to perform as specified for a period of one year from date of shipment. In
the event of failure occurring during normal use, AMI, at it s opt ion, will r epair o r repla ce a ll
products or components that fail under warranty, and such repair or replacement shall
constitute a fulfillment of all AMI liabilities with respect to its products. Since, however,
AMI does not have control over the installation conditions or the use to which its products
are put, no warranty can be made of fitness for a particular purpose, and AMI cannot be
liable for special or consequential damages. All warranty repairs are F.O.B. Oak Ridge,
Copyright © 1998 by American Magnetics, Inc., Oak Ridge, Tennessee, USA
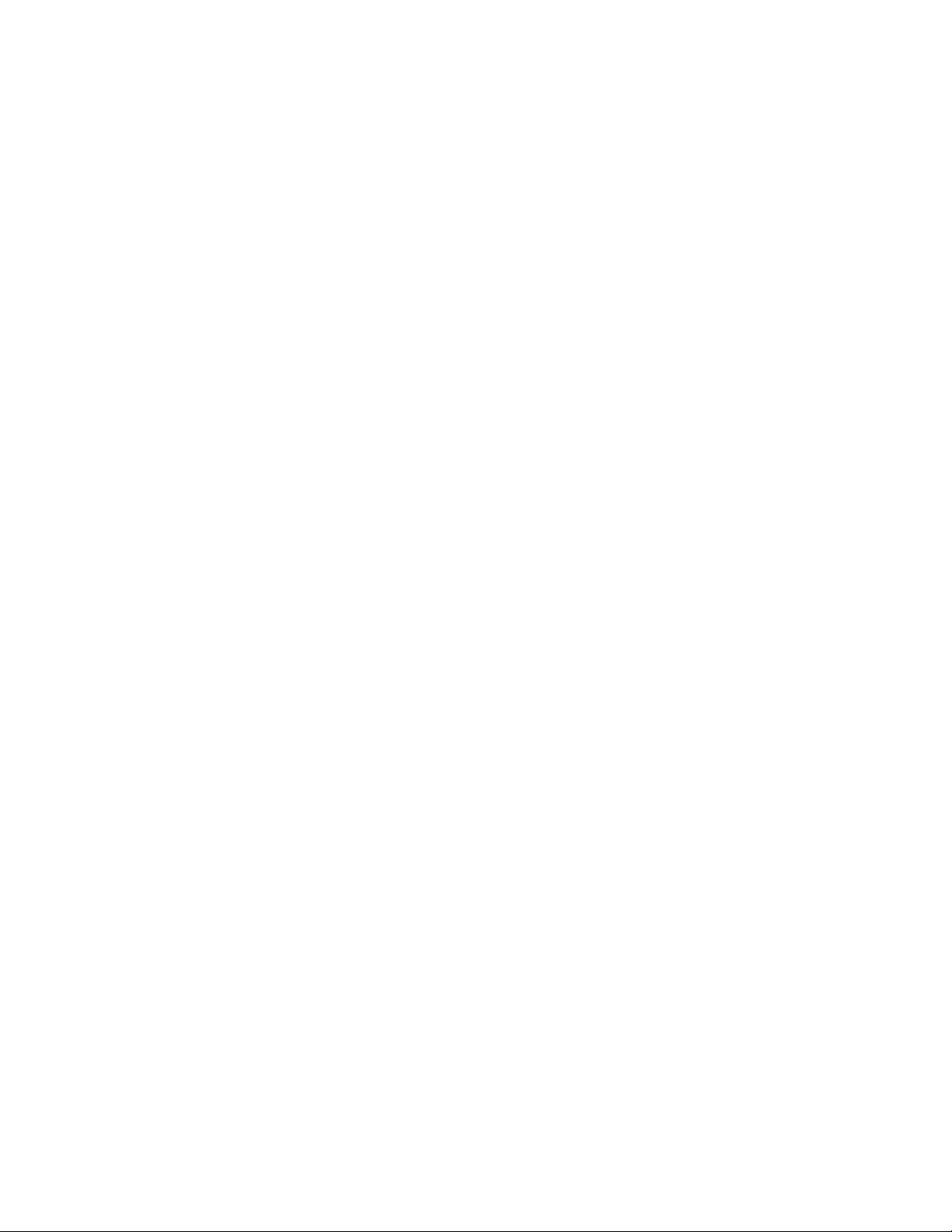
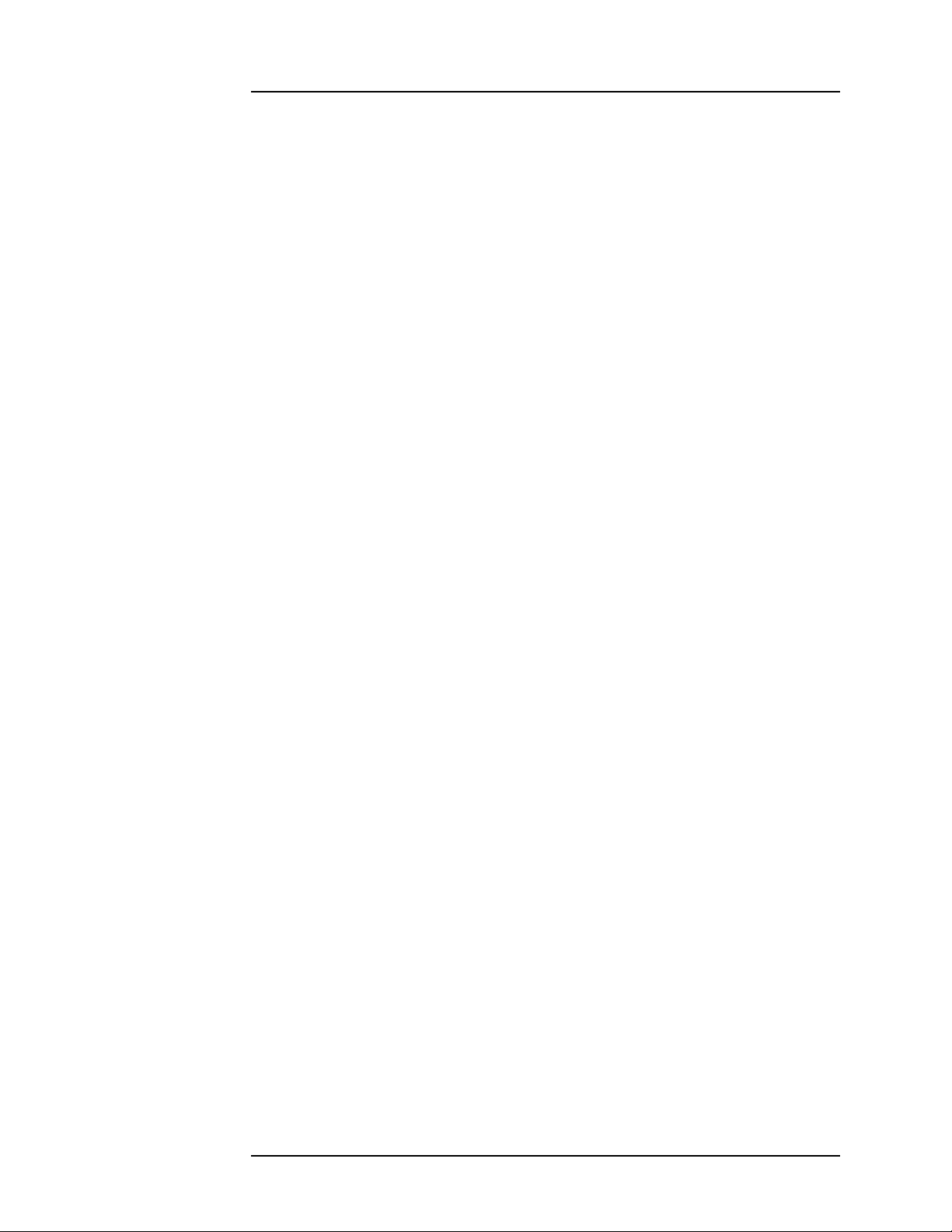
Table of Contents
.....................................................................
..........................................................
...............................................................
.................................................................
..............................................................
......................................................................
Recommended Safety Equipment
..............................
.............................................................
...................................................................
Compensated capacitance-based level sensing
........................................................
Convenient display and direct keypad entry
.................................................
Remote computer monitoring or controlled operation
..................................................................
.....................................................................
.......................................................................
Model 187 Specifications @ 25
°C.............................................
.......................................................
Rack Mounting the Instrument
................................................
.................................................................
Connecting the Model 187 to the Sensor
.................................
Installing the Optional Solenoid-Operated Fill Valve
Connecting the Instrument to Power
.....................................
...........................................................
Energizing the instrument
..........................................
Selecting the Appropriate Units
.................................
Configuring the Length Settings
................................
Configuring the HI and LO Alarms
............................
Configuring the A and B Setpoints
.............................
................................................
Configuring the Fill Timer
..........................................
Foreword................................................................................... v
1 Introduction.............................................................................. 1
2 Installation................................................................................ 7
3 Operation................................................................................ 13
i
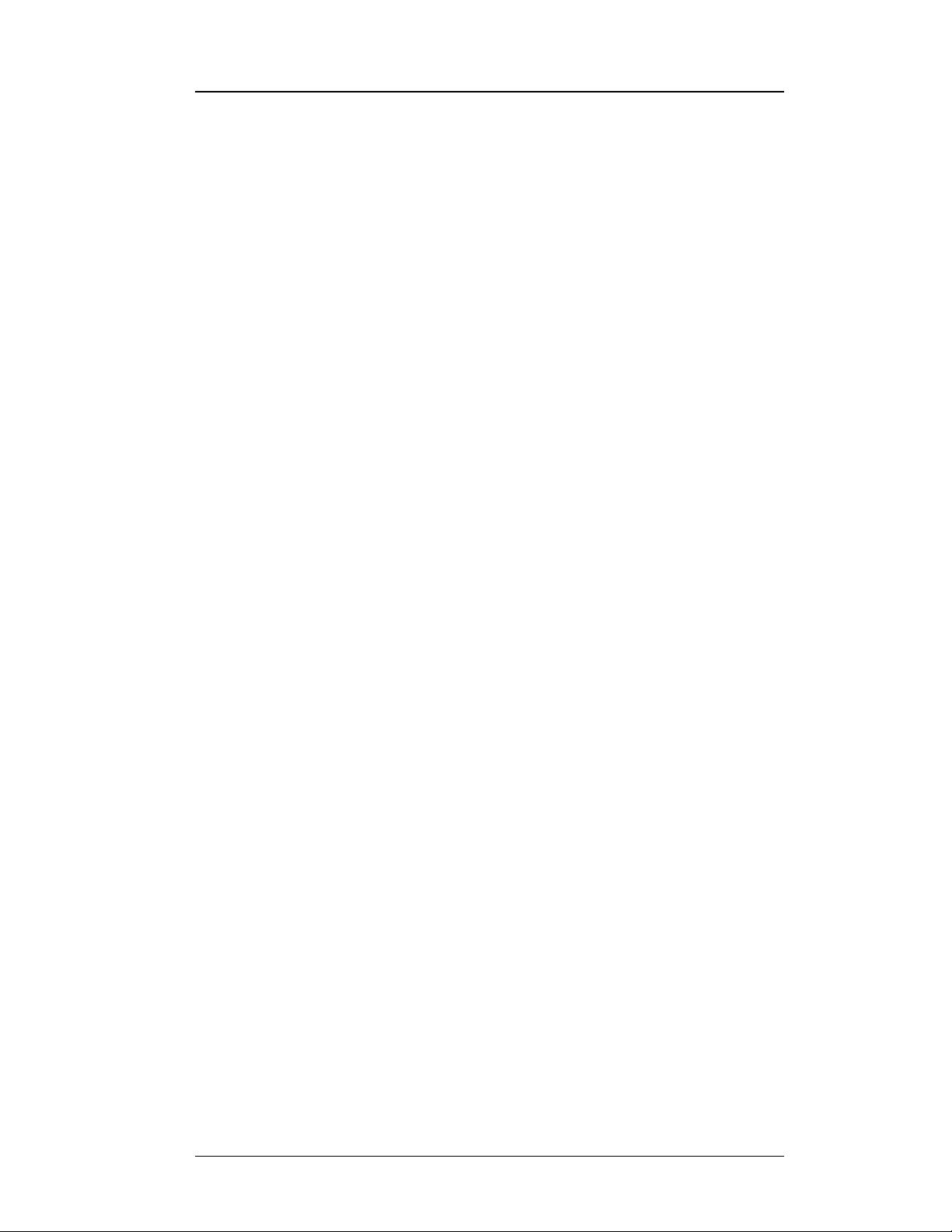
Table of Contents
..............................................................
........................................................................
..........................................................
Entering Numerical Values
.............................
.....................................
..................................................
........................................................................
.......................................................................
..........................................................................
..........................................................................
..................................................................
.....................................................
.........................................................
.................................................
....................................................................
...........................................................
......................................................
.................................................................
................................................................
.............................................
...........................................
.............................................
...................................
................................................
........................................
.....................................................................
......................................................
...........................................................
SCPI Language Introduction
.......................................
.....................................................
.......................................
Serial Polling and the Service Request (SRQ)
Reading the Status Byte using *STB?
Using the Message Available Bit(s)
............................................
............................................................
..............................................
...............................
....................................
................................................................
.......................................................
...................................................
...............................................
4 Remote Interface Reference..................................................27
*OPC
*OPC?
ii
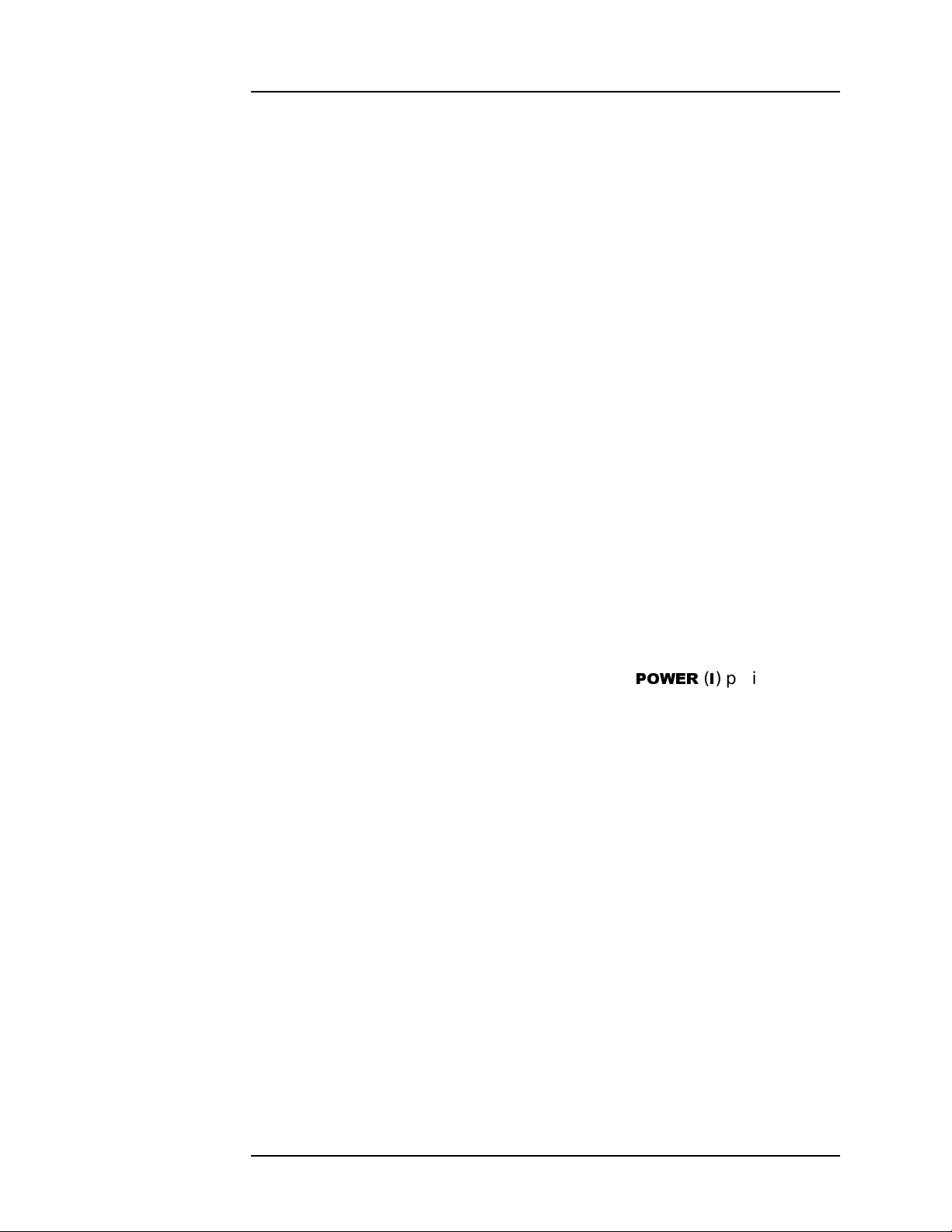
Table of Contents
.....................................................
.........................................................
..............................................
.................................................................
...............................................................
........................................
..........................................
Alarm Configuration Commands and Queries
............................................
Length Configuration Commands and Queries
Fill Mode Control and Queries
...................................
Calibration Commands and Queries
..........................
Remote Units Commands and Queries
........................................................................
.........................................................
................................................................
..........................................................
...............................................................
..........................................................
Model 187 Troubleshooting Hints
..........................................
The Model 187 does not appear to be energized
with the power switch in the
The Model 187 does not remember the alarm
setpoints after power is remov ed.
...............................
The Model 187 displays “Over/Under Flow”.
The Model 187 displays “Max Diel Exceeded”.
The liquid level unexpectedly drops rapidly as
the tank level approaches 100%.
................................
The liquid level unexpectedly rises rapidly as
the tank level approaches 0%.
....................................
The USER and FACTORY calibrations do not
yield the same liquid level.
.........................................
The Model 187 is not responding to remote
.......................................
Additional Technical Support
.................................................
..............................................................
5 Service .................................................................................... 51
32:(5 (,
iii
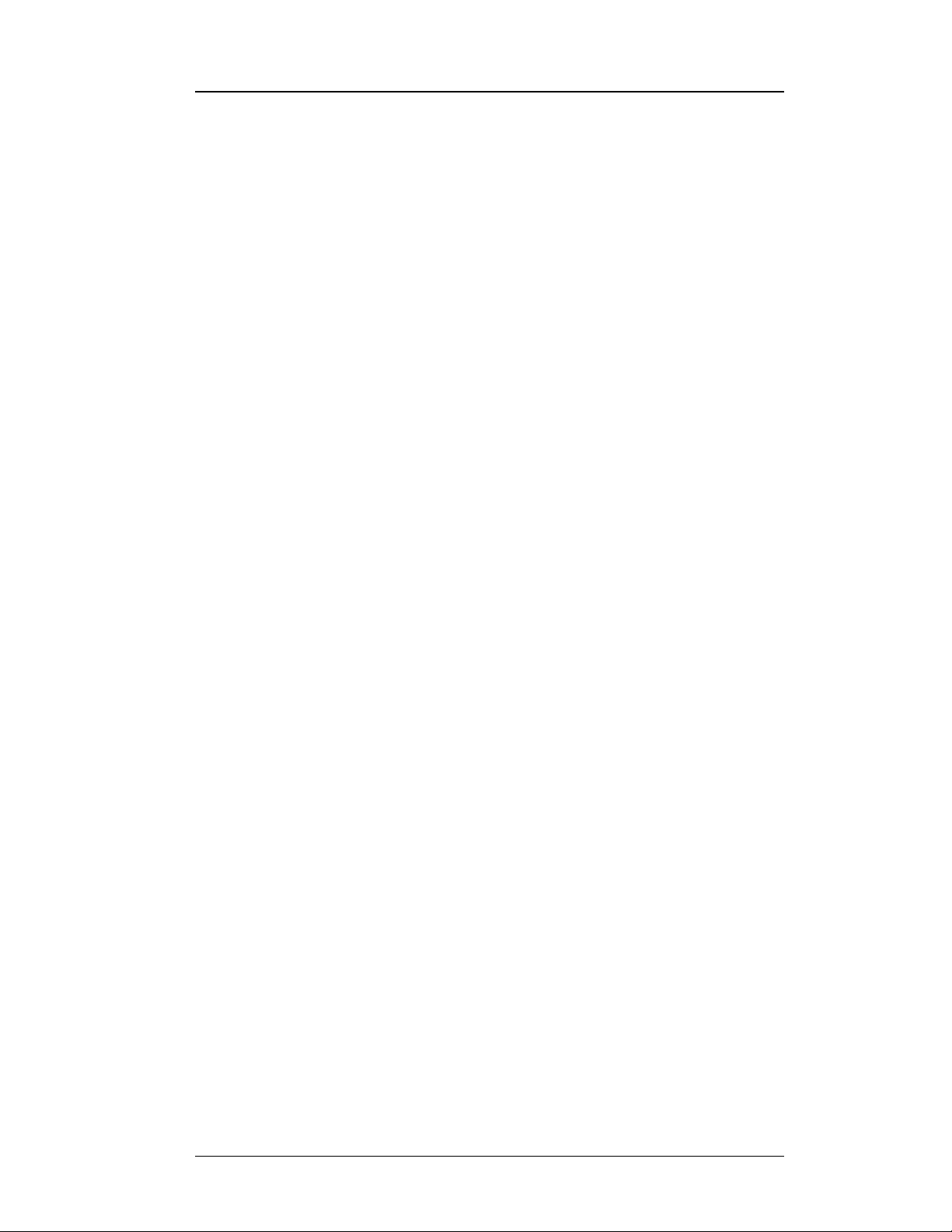
Table of Contents
4-20 mA Current Loop Option
.................................................
Auxiliary Connector J8 Pinout
................................................
................................................................
..............................................................
Appendix..................................................................................57
Index.........................................................................................63
iv
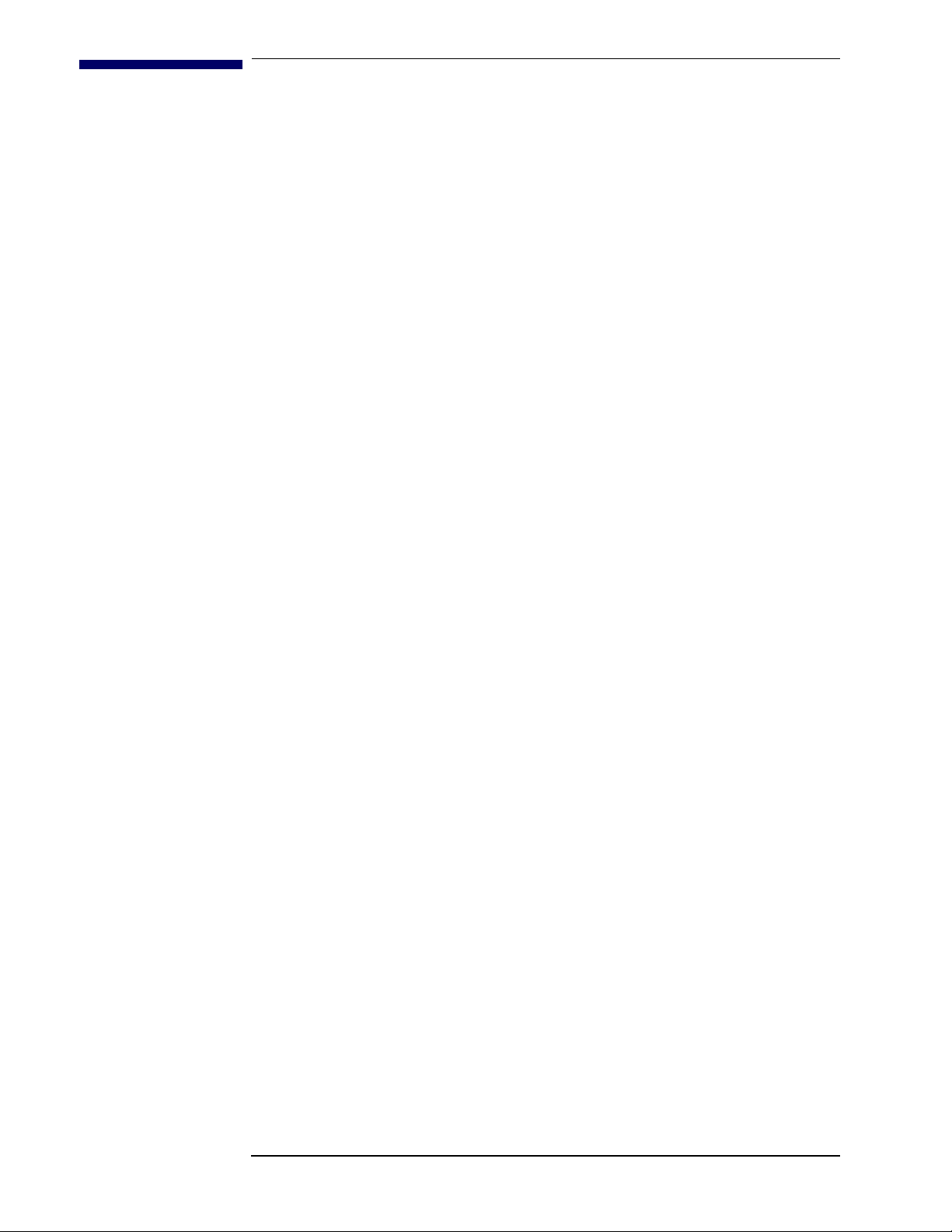
Foreword
This manual contains the operation and maintenance instructions for the
American Magnetics, Inc. Model 187 Liquid Level Controller. The manual
outlines the instructions for instrument use in various system designs.
Since it is impossible to cover all possible system/sensor designs, the most
common configuration is discussed and the user is encouraged to contact
an authorized AMI Technical Support Representative for infor mat i on
regarding specific configurations not explicitly covered in this manual.
introduces the reader to the functions and char acteristics of
the instrument. It provides the primary illustrations of the front and rear
panel layouts as well as documenting the performance specifications.
describes how the instrument is unpacked and installed in
conjunction with ancillary equipment in a typical cryogenic system.
describes how the instrument is used to measure and control
instrument displays and controls are documented.
Remote Interface Reference
documents all remote commands and
queries available through the RS-232 and IEEE-488 interfaces. A quick-
reference summary of commands is provided as well as a detailed
provides guidelines to assist the user in troubleshooting possible
system and instrument malfunctions. Information for contacting AMI
Technical Support personnel is also provided.
documents the rear panel co n n e ct o rs.
Purpose and Scope
Contents of This Manual
v
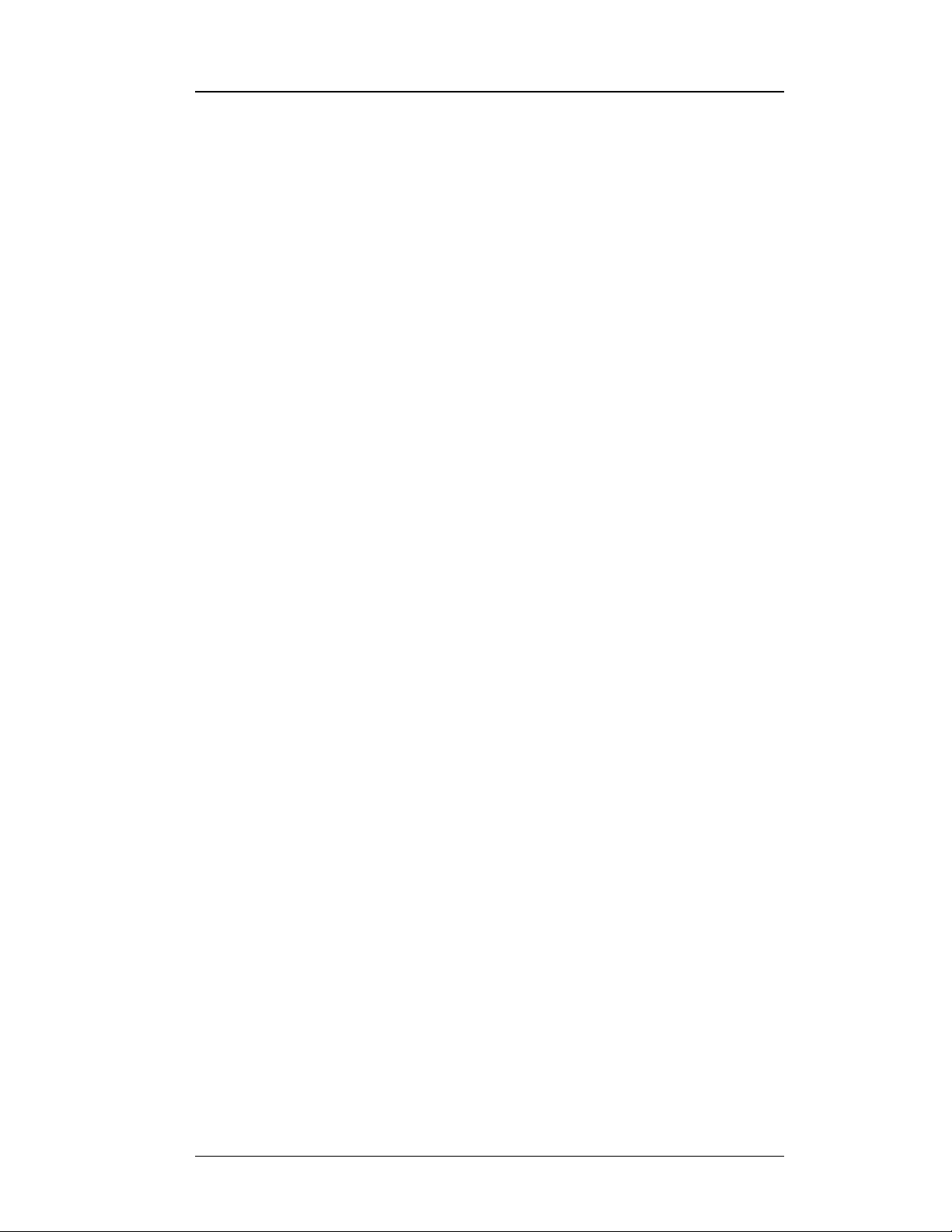
Foreword
The Model 187 has been designed to operate with an AMI Liquid Level
Sensor. Operation with other equipment is not recommended and may
Personnel handling cryogenic liquids should be thoroughly instructed and
trained as to the nature of the liquids. Training is essential to minimize
accidental spilling. Due to the coldness of these materials, a cryogen
spilled on many objects or surfaces may damage the surface or cause the
object to shatter, often in an explosive manner.
Inert gases released into a confined or inadequately ventilated space can
displace sufficient oxygen to make the local atmosphere incapable of
sustaining life. Cryogenic liquefied gases are potentially extreme
suffocation hazards since a small amount of liquid will vaporize and yield
a very large volume of oxygen-displacing gas. Always ensure the location
where the cryogen is used is well ventilated. Breathing air with
insufficient oxygen content may cause unconsciousness without warning.
If a space is suspect, purge the space completely with air and test before
entry. If this is not possible, wear a forced-air respirator and enter only
with a co-worker standing by wearing a forced-air respirator.
Cryogenic liquids, due to their extremely low temperatures, will burn the
skin in a similar manner as would hot liquids. Never permit cryogenic
liquids to come into contact with the skin or allow liquid nitrogen to soak
clothing. Serious burns may result from careless handling. Never touch
uninsulated pipes or vessels containing cryogenic liquids. Flesh will stick
to extremely cold materials. Even nonmetallic materials are dangerous to
touch at low temperatures. The vapors expelled during the venting process
are sufficiently cold to burn flesh or freeze optic tissues. Insulated gloves
should be used to prevent frost-bite when operating valves on cryogenic
tanks. Be suspicious of valves on cryogenic systems; the extremes of
temperature they undergo causes seals to fail frequently.
In the event a person is burned by a cryogen or material cooled to
cryogenic temperatures, the following first aid treatment should be given
pending the arrival and treatment of a physician or other medical care
If any cryogenic liquid contacts the skin or eyes, immediately flush
the affected area gently with tepid water (102°F
40.5°C) and then apply cold compresses.
Applicable Hardware
Applicable Hardware
General Precautions
Cryogen Safety
vi
−
−
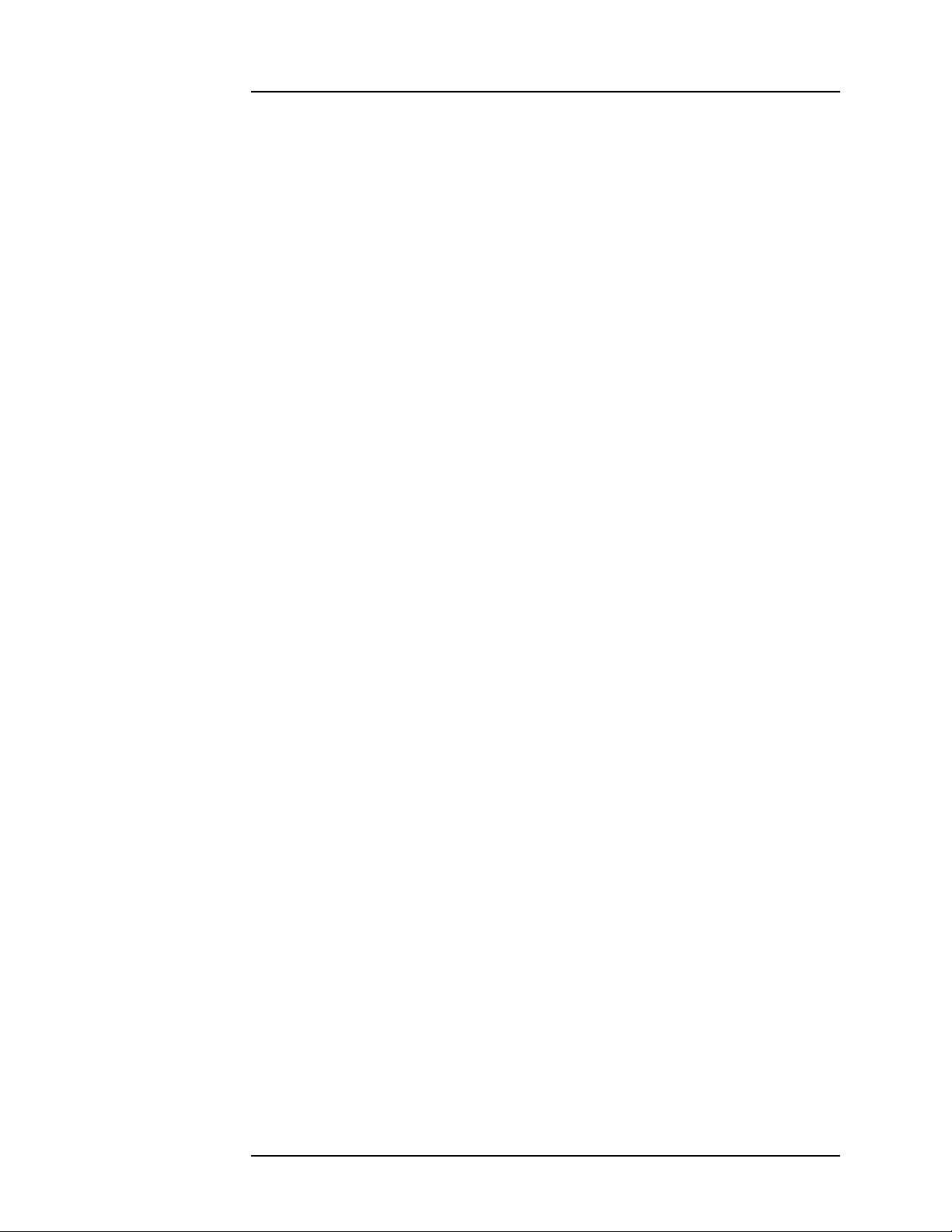
Foreword
Do not apply heat. Loosen any clothing that may restrict
circulation. Apply a sterile protective dressing to the affected area.
If the skin is blistered or there is any chance that the eyes have
been affected, get the patient immediately to a physici an for
Containers of cryogenic liquids are self pressurizing (a s the liquid boils off,
vapor pressure increases). Hoses or lines used to transfer these liquids
should never be sealed at both ends (i.e. by closing valves at both ends).
When pouring cryogenic liquids from one container to another, the
receiving container should be cooled gradually to prevent damage by
thermal shock. The liquid should be poured slowly to avoid spattering due
to rapid boil off. The receiving vessel should be vent ed during the transfer.
Introduction of a substance at or near room temperature into a cryogenic
liquid should be done with great caution. There may be a violent gas boil
off and a considerable amount of splashing as a r esult of this rapid boi ling.
There is also a chance that the material may crack or catastrophically fail
due to forces caused by large diffe rences in ther mal contrac tion of differe nt
regions of the material. Personnel engaged in this type of activity should
be instructed concerning this hazard and should always wear a full face
shield and protective clothing. If severe spraying or splashing could occur,
safety glasses or chemical goggles along with body length protective
aprons will provide additional protection.
The properties of many materials at extremely low temperatures may be
quite different from the properties that these same materials exhibit at
room temperatures. Exercise extreme care when handling materials cooled
to cryogenic temperatures until the properties of these materials under
these conditions are known.
Metals to be used for use in cryogenic equipment application must posses
sufficient physical properties at these low temperatures. Since ordinary
carbon steels, and to somewhat a lesser extent, alloy steels, lose much of
their ductility at low temperature s, they are considered unsatisfactory and
sometimes unsafe for these applications. The austinetic Ni-Cr alloys
exhibit good ductility at these low temperatures and the most widely used
is 18-8 stainless steel. Copper, Monel
, brass and aluminum are also
considered satisfactory materials for cryogenic service .
Cryogenic storage systems are complex systems with the potential to
seriously injure personnel or equipment if not operated according to
procedures. Proper use of safety mechanisms (pressure relief valves,
Safety Summary
Safety Summary
vii
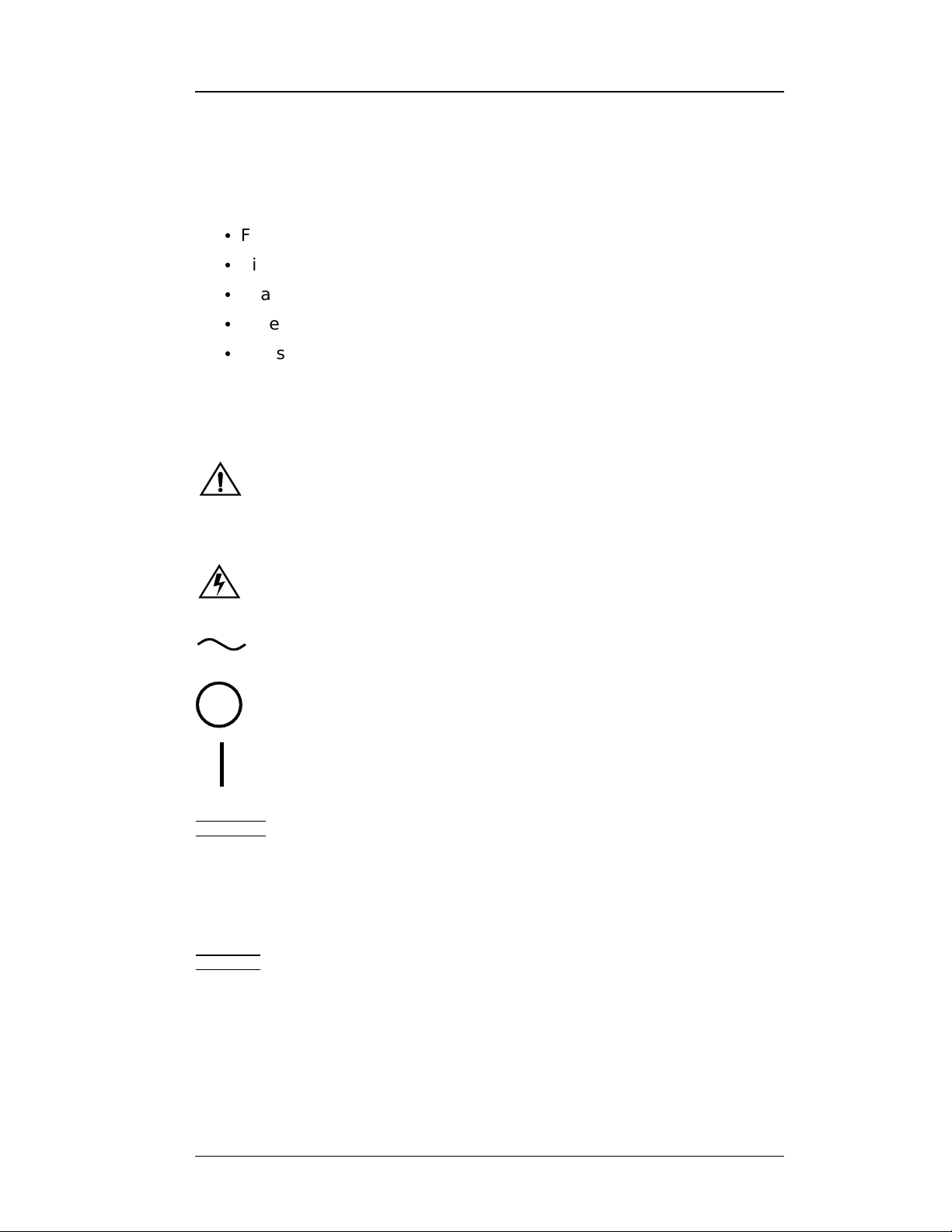
Foreword
rupture disks, etc.) included in the cryostat and top plate assembly are
Fire extinguisher rated for class C fires
Signs to indicate that there are potentially dangerous cryogens in
Instruction manual symbol: the product is marked with this
symbol when it is necessary for you to refer to the instruction
manual in order to protect against damage to the product or
Hazardous voltage symbol.
Alternating Current (Refer to IEC 417, No. 5032).
Off (Supply) (Refer to IEC 417, No. 5008).
On (Supply) (Refer to IEC 417, No. 5007).
The Warning sign denotes a hazard. It calls attention to a procedure or
practice, which if not correctly adhered to, could result in personal injury.
Do not proceed beyond a Warning sign until the indicated conditions are
fully understood and met.
The Caution sign denotes a hazard. It calls attention to an operating
procedure or practice, which if not adhered to, could cause damage or
destruction of a part or all of the product. Do not proceed beyond a Caution
sign until the indicated conditions are fully understood and met.
Safety Summary
Recommended Safety Equipment
Safety Legend
Warning
Caution
viii
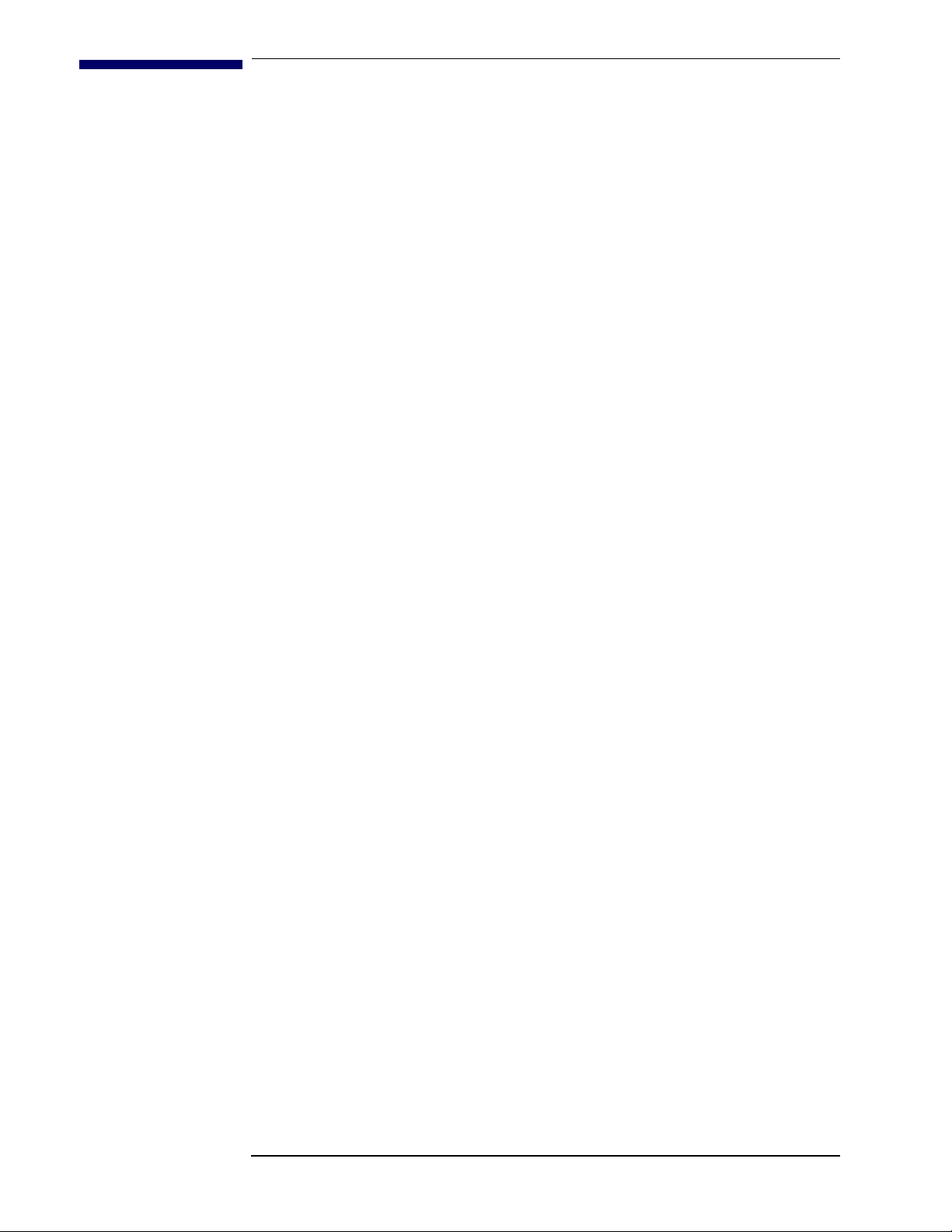
1 Introduction
The American Magnetics, Inc. (AMI) Model 187 Liquid Level Controller
system (patent-pending) is an advanced, microprocessor-based solution
designed to provide compensated, capacitance-based level monitoring and
control of virtually any cryogenic liquid over a
pressures and temperature s
The system consists of a Model 187 Liquid Level Controller, sensor,
connecting coaxial cables pairs, and an optional solenoid-oper ated fill
valve. The primary instrument sensing element is typically a 3/8 inch (9.5
mm) OD cylindrical capacitor constr ucted of stainless steel which allows a
non-conducting fluid to become the dielectric between the concentric
In addition to the primary cylindrical sensing element, circular-shaped
parallel plate capacitors are mounted on the sensing element in order to
provide “reference” data to compensate the primary capacitance
measurement. The instrument measures the primary sensing element
capacitance, compensates for any dielectric variations with respect to the
calibration conditions using the “reference” plates, and displays a level
reading. The sensors are nor mally constructed in o ne-piece lengths o f up to
The Model 187 is designed to be factory calibrated by AMI for a matched
sensor and is ready for immediate use upon delivery. The capacitance-
based primary and reference sensors provide f eedback to the instrument to
measure liquid level for any non-conducting liquid and compensate fo r a
wide range of operating conditions — therefore,
, but the Model 187 provides the option of a user
All calibration data is password protected to prevent unauthorized
modification and is stored in non-volatile memory. The instrument also
provides a function to select between the user calibration and the AMI
1.1 Model 187 Features
1.1.1 Compensated capacitance-based level sensing
1.1.2 Factory calibration
1
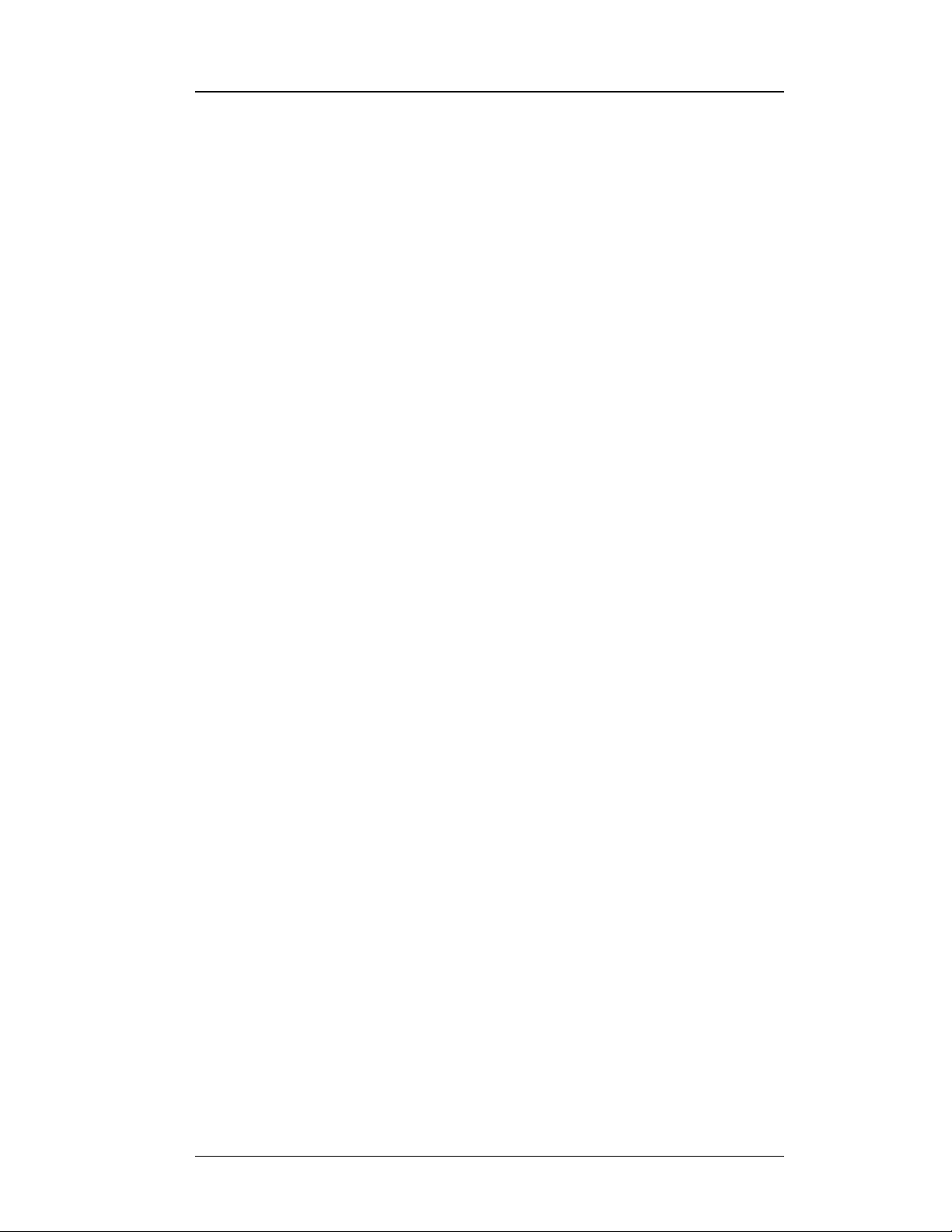
Introduction
The instrument is equipped with a 16 x 2 backlit character-mode LCD
display which provides liquid level and setpoint indication in inches,
centimeters, or percent as selected by the user. A front panel keypad
interface allows the user to easily view and modify the instrument
settings. The default display indicates liquid level and fill/loss rate. The
current liquid level is updated and visible in many of the display modes
used in configuring various settings of the instrument.
The 4 x 4 keypad is provided for d irect entry of values f or se tpoints, sensor
lengths, and other functions. The keyp ad also provide s a con ve nient me nu-
type interface for configuring various instrument se ttings that require
selection from a list of options.
The Model 187 provides four level setpoints, two of which (A & B) are
control setpoints used to control liquid level through use of a solenoid-
operated fill valve. The remaining setpoi nts (HI & LO) are ala rm setpoints
and can be set for other control or alarm functions.
The HI and LO setpoints operate relay contacts in addition to the front
panel LED indications. LED indication is also provided for the A setpoint,
B setpoint, and automatic contro ller (FILL) f unction of t he instrument. All
setpoints are accessible via the keypad. The automatic controller (FILL)
function can also be manually overridden or disabled using the keypad.
A timeout feature is also provided with the automatic controller (FILL)
function. The timeout specifies the maximum amount of time necessary for
the Model 187 to fill the target vessel to the A setpoint. If fill is not
achieved within the timeout period, the Model 187 ends the fill operation
(de-energizes the rear panel controller output) and indicates expiration of
the timeout feature by blinking t he FILL LED and set ting the approp riate
flags accessible through the serial or GPIB remote interfaces.
The Model 187 can be configured to provide an optional analog 0-10 volt
DC signal accessible from the rear panel of the instrument for use with a
recorder. A 4-20 mA current loop option is available in lieu of the voltage
RS-232 is provided as a standard digital interface for the Model 187.
Additional digital interface options, including RS-422 or GPIB (IEEE
488.2 compliant), are available. The serial and GPIB remote interfaces
provide a comprehensive command set for monitoring and configuring all
functions of the instrument.
Model 187 Features
1.1.3 Convenient display and direct keypad entry
1.1.4 Automatic level control
1.1.5 Remote computer monitoring or controlled operation
2
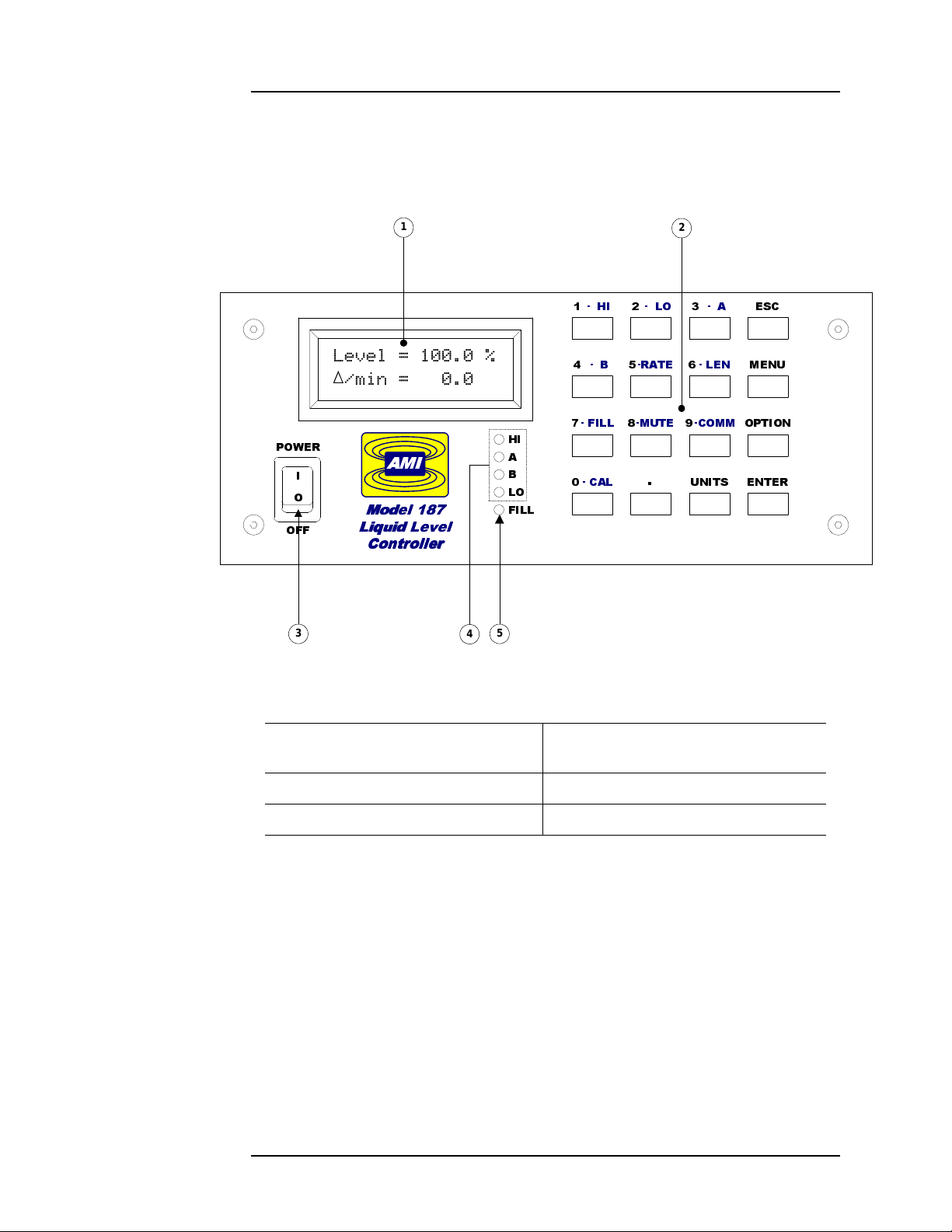
Introduction
Front Panel Layout
1.2 Front Panel Layout
/HYHO
PLQ
32:(5
$0,
O
2
2))
16 character x 2 line LCD display
1
with backlight
$0,
0RGHO
0RGHO
/LTXLG /HYHO
/LTXLG /HYHO
&RQWUROOHU
&RQWUROOHU
+,
$
%
/2
),//
Ã+, Ã/2
Ã% Ã5$7( Ã /(1
à ),// Ã087( Ã&200
à &$/
HI, A, B, and LO alarm LEDs
4
Ã$
81,76 (17(5
(6&
0(18
4 x 4 keypad
2
Powe r switc h
3
FILL Indicator LED
5
3
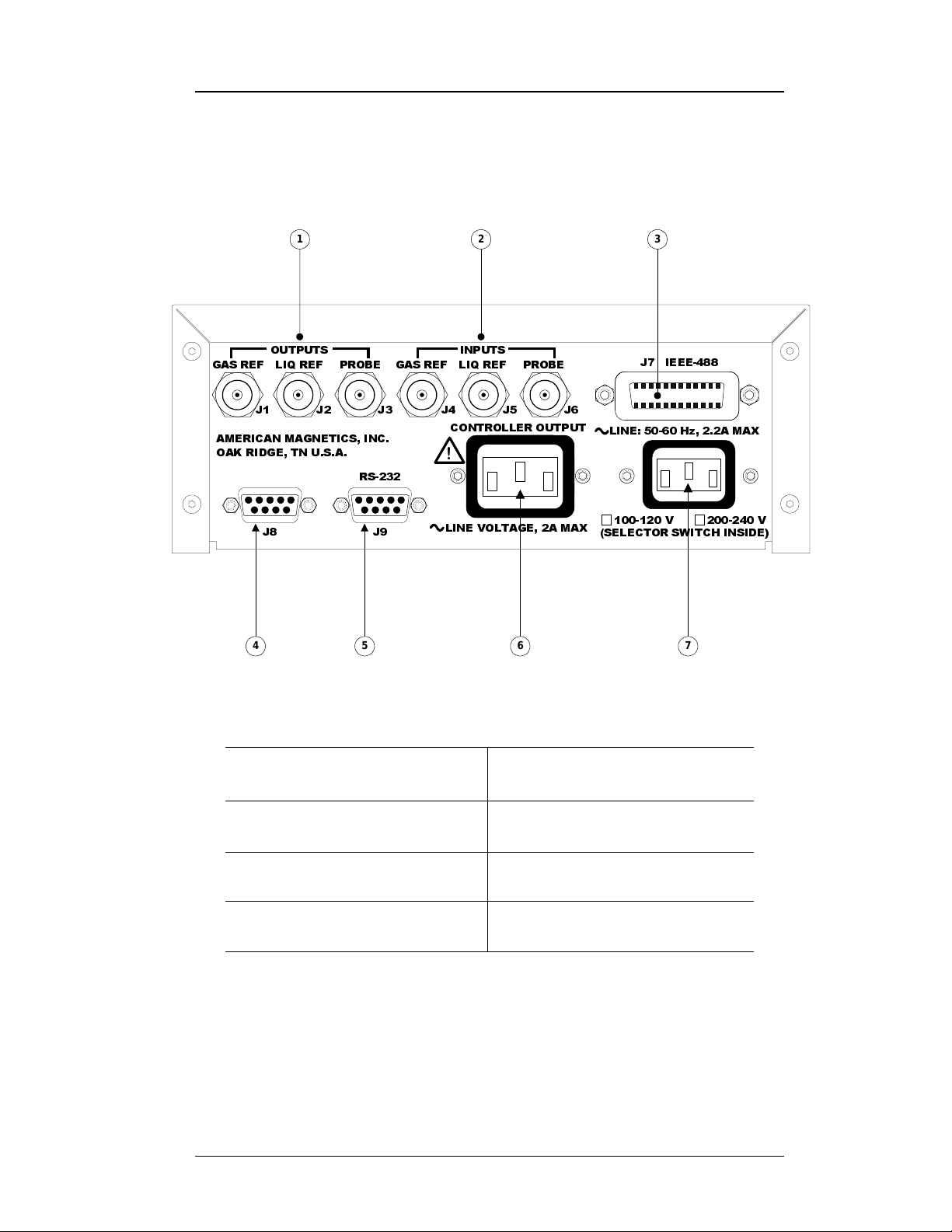
Introduction
Rear Panel Layout
1.3 Rear Panel Layout
1 3
*$6 5() /,4 5() 352%( *$6 5() /,4 5() 352%(
$0(5,&$1 0$*1(7,&6 ,1&
2$. 5,'*( 71 86$
2873876 ,13876
- - - - - -
56
- -
4 6
5 7
2
&21752//(5 287387
/,1( 92/7$*( $ 0$;
- ,(((
/,1( +] $ 0$;
9 9
6(/(&725 6:,7&+ ,16,'(
BNC
1
coaxial connector outputs
to sensor
BNC
2
coaxial connector inputs
from sensor
IEEE-488 communications port
3
RS-232 (standard) or RS-422
5
DB-9 female connector
Controller output receptacle
6
(reverse IEC-320)
IEC-320 Power cord connector
7
(IEC-320)
Auxiliary DB-9 male connector
4
(see
Appendix
for pinout)
4
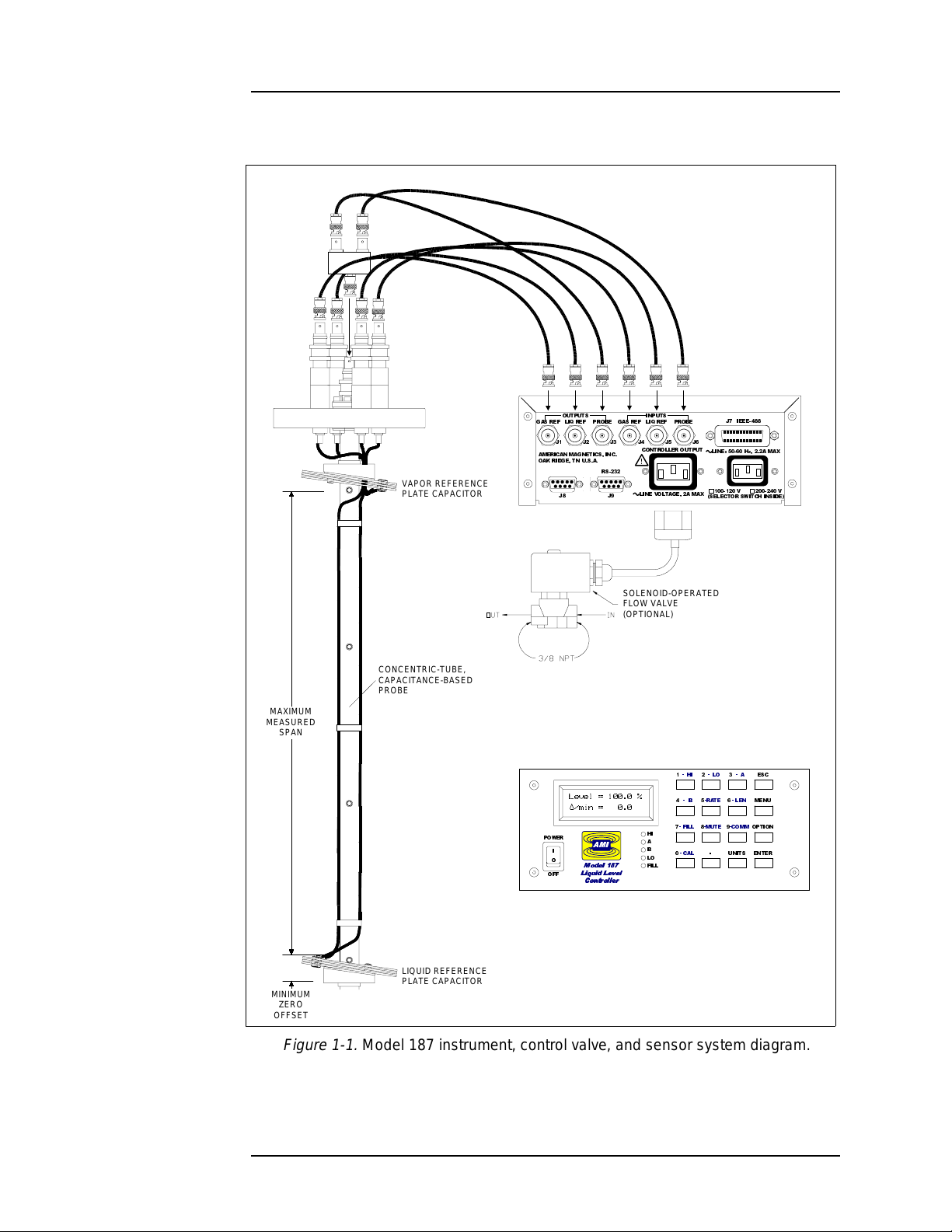
Introduction
Instrument/Sensor System Diagram
1.4 System Diagram
SENSOR CABLES
RG-59/U COAXIAL
150 FEET MAXIMUM LENGTH
MAXIMUM
MEASURED
SPAN
VAPOR REFERENCE
PLATE CAPACITOR
CONCENTRIC-TUBE,
CAPACITANCE-BASED
PROBE
2873876 ,13876
*$6 5() /,4 5() 352%( *$6 5() /,4 5() 352%(
- - - - - -
$0(5,&$1 0$*1(7,&6 ,1&
2$. 5,'*( 7186$
- -
56
&21752//(5 287387
/,1( 92/7$*( $0$;
REAR PANEL
SOLENOID-OPERATED
FLOW VALVE
(OPTIONAL)
/HYHO
PLQ
32:(5
$0,
$0,
O
2
0RGHO
0RGHO
/LTXLG /HYHO
/LTXLG /HYHO
2))
&RQWUROOHU
&RQWUROOHU
FRONT PANEL
LIQUID LEVEL
CONTROLLER
Ã+, Ã/2
Ã% Ã5$7( Ã /(1
à ),// Ã087( Ã&200
+,
$
%
à &$/
/2
),//
MODEL 187
- ,(((
/,1( +]$ 0$;
9 9
6(/(&725 6:,7&+ ,16,'(
(6&
Ã$
0(18
237,21
81,76 (17(5
MINIMUM
ZERO
OFFSET
Figure 1-1.
LIQUID REFERENCE
PLATE CAPACITOR
Model 187 instrument, control valve, and sensor system diagram.
5
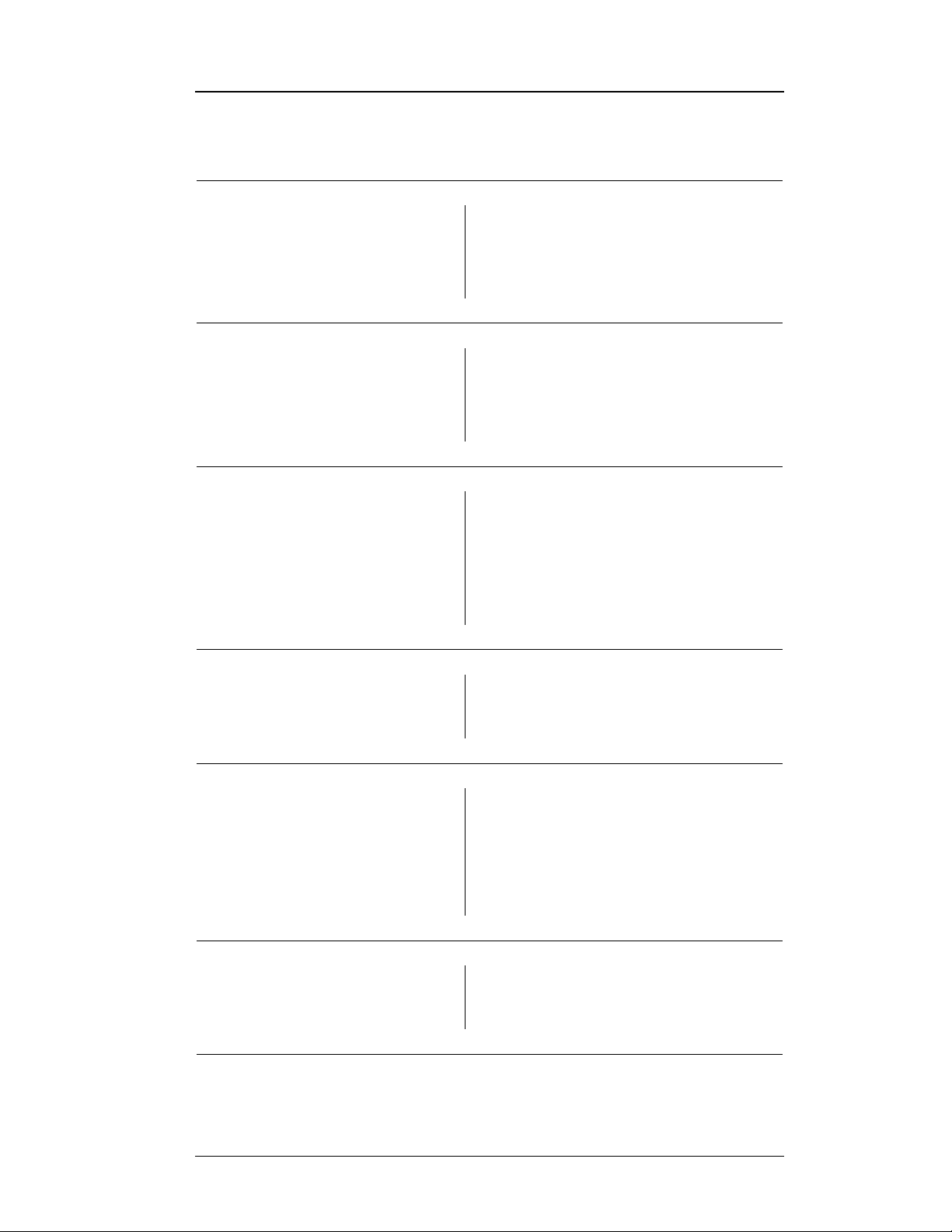
Introduction
Specifications
1.5 Model 187 Specifications @ 25 °C
Level Measurements
Resolution: 0.1 %, 0.1 cm, or 0.1 in
Accuracy:
Linearity:
Temperature Coefficient: 0.1% / °C
Operating Parameters
HI, A, B, and LO Alarms:
HI/LO Alarm Relay Contact Ratings: 10 V at 0.5 A (normally open, closed on alarm)
Controller Output: AC line voltage @ 2A max current
Fill Timer: 0.1 to 9,999.9 minutes
Analog Output
Integral Non-linearit y:
Resolution: 16 bits
Total Error:
Current Drift (4-20 mA): 75 ppm / °C
Voltage Drift (0-10 V): 100 ppm / °C
0.5%
±
0.2%
±
% to 100% adjustable
0
0.012%
±
0.25% for 4-20 mA output
±
0.5% for 0-10 V output
±
Power Requirements
Memory Backup Battery: 3.6 Volt AA Lithium Cell
Physical
Dimensions (Standard): 97 mm H x 213 mm W x 290 mm D
Weight (Standard): 2.0 kg (5.4 lbs.)
Dimensions (Rack Mount): 89 mm H x 483 mm W x 290 mm D
Weight (Rack Mount): 2.3 kg (6.1 lbs.)
Environmental
Ambient Temperature: Operating: 0 °C to 50 °C (32 °F to 122 °F)
Relative Humidity: 0% to 95%; non-condensing
Primary: 100-120 or 200-240 VAC ±10%
50 - 60 Hz, 2.2 A max
(3.8" H x 8.4" W x 11.4" D)
(3.5" H x 19" W x 11.4" D)
Nonoperating: −20 °C to 60 °C (−4 °F to 140 °F)
6
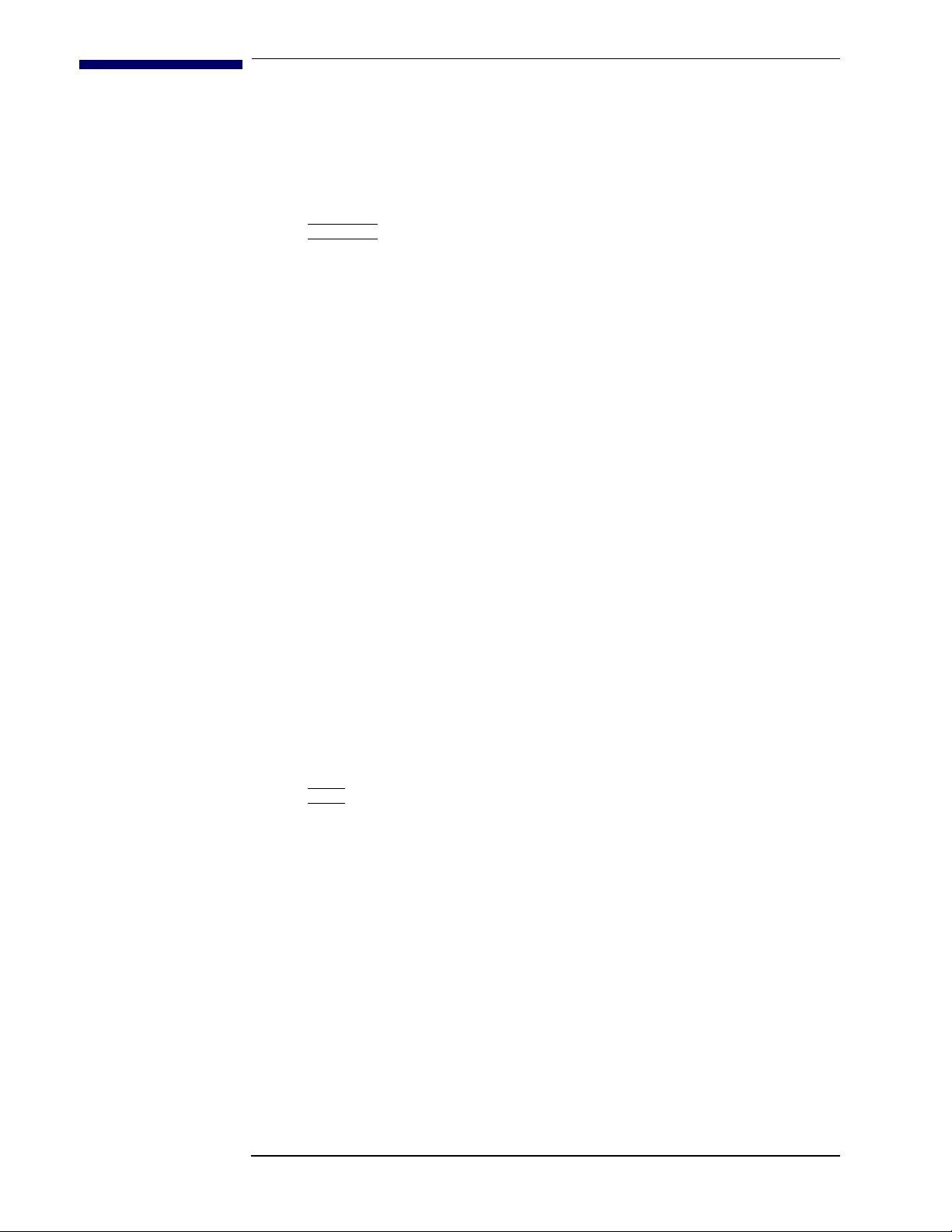
2 Installation
Before energizing the instrument, the earth ground of the power
receptacle must be verified to be at earth potential and able to carry
the rated current of the power circuit. Using extension cords should
be avoided; however, if one must be used, ensure the ground
conductor is intact and capable of carrying the rated current.
In the event that the ground path of the instrument becomes less
than sufficient to ca r ry th e ra te d curr e n t of the po w e r ci r cu i t, th e
instrument should be disconnected from power, labeled as unsafe,
and removed from place of operation.
Do not operate this instrument in the presence of flammable gases.
Doing so could result in a life-threatening explosion.
Do not modify this instrument in any way. If component
replacement is required, return the instrument to AMI facilities as
described in the Troubleshooting section of this manual.
Carefully remove the instrument, sensor, and interconnecting coaxial
cables from the shipping carto n and remove al l packaging material . A rack
mounting kit is supplied if the instrument was purchased with the rack
If there is any shipping damage, save all packing material and
contact the shipping representative to file a damage claim. Do not
return the instrument to AMI unless prior authorization has been
If the chassis is a table top model, place the instrument on a flat, secure
Warning
2.1 Unpacking the Instrument
Note
7
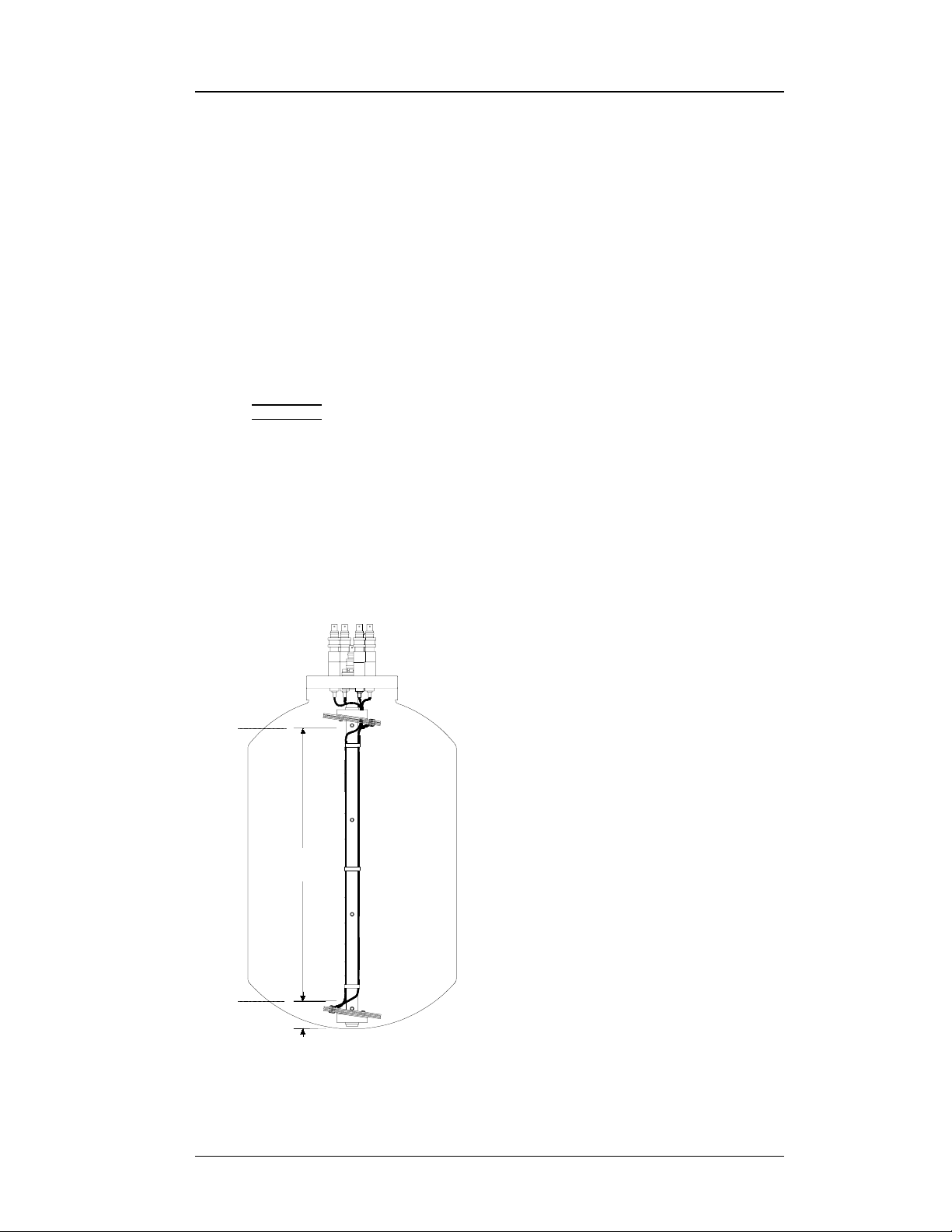
Installation
instrument has a rack mount chassis, follow the following procedure:
Attach the rack mount adapter pieces to the inst rument by fir st
removing the four screws on the side of the instrument that
attach the cover to the chassis. Attach the rack mount adapter
pieces to the sides of the instrument by reinstalling the screws.
Install the instrument in a 19" rack by securing the front panel
to the rail in each of the four corners with mounting hardware
supplied by the cabinet manufacturer.
Do not remove the cabinet feet and then rei n sert the origi n al screws.
Doing so could present a severe life-threatening electrical hazard. If
removal of the cabinet feet is desired, replace the original screws
with screws not to exceed 1/4" in length. Screws longer than 1/4"
will contact and damage the printed circuit board inside the unit.
sensor since dents, crimps, bends or
other physical distortions in the
cylindrical and plate sensors will
change electrical characteristics
and possibly cause calibration
errors and/or disruption of proper
instrument operation. It is also
important to ensure that the sensor
is installed in a vertical orientation
for optimal operation of the sensors.
Make a note of the 0% and 100%
points of the target vessel per
diagram at left. Before installing
the sensor and before filling the
target vessel, the user may first
section—especially the zero offset
and measured span length settings
Drawings will be provided for
custom sensor or mounting flange
Installing the sensor
2.2 Rack Mounting the Instrument
Warning
2.3 Installing the Sensor
100%
MAXIMUM
MEASURED
SPAN
0%
MINIMUM
ZERO
OFFSET
8
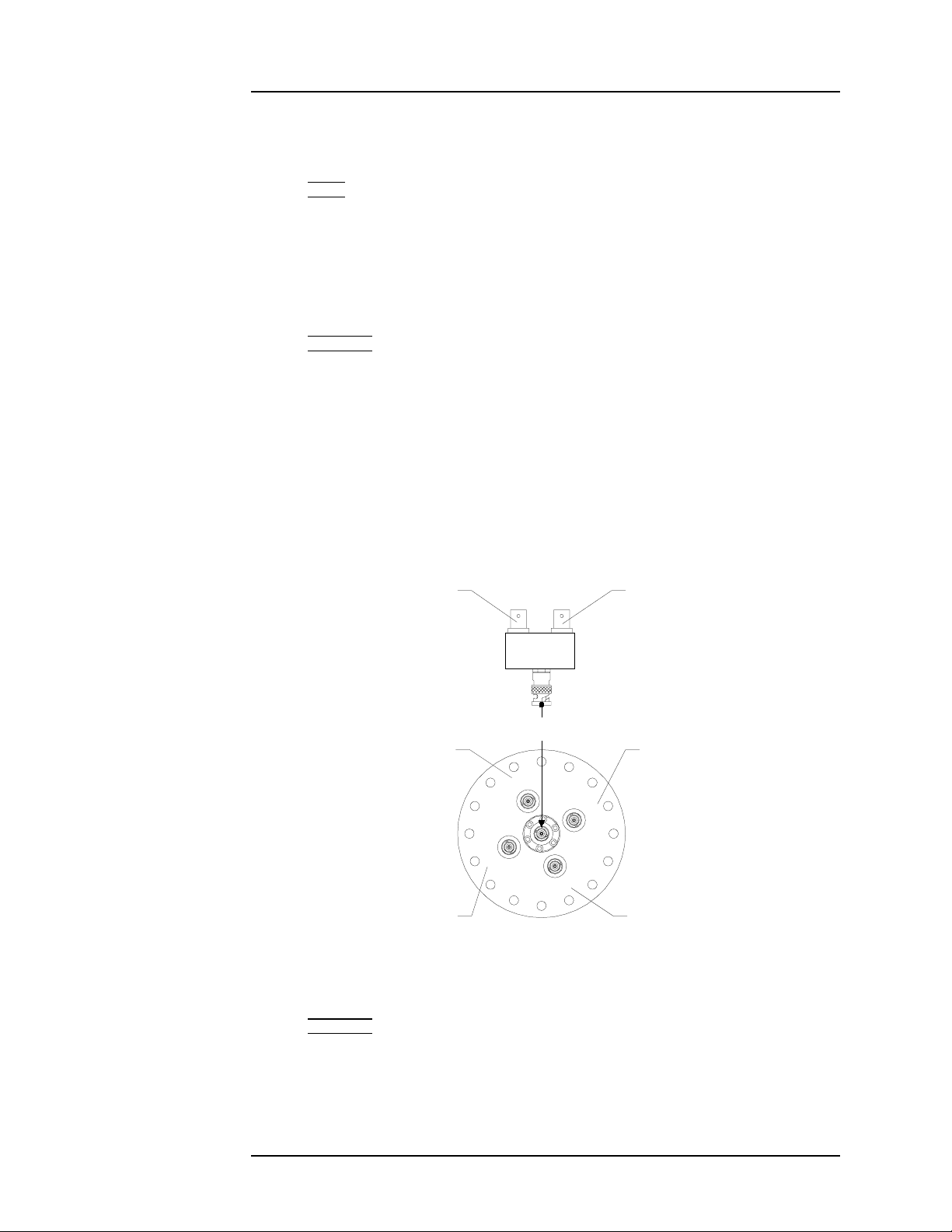
Installation
The electrical char acteristics of the interconnecting coaxial cables
are temperature dependent over extreme ranges and the cables may
become brittle at cryo genic temperatures. The ca bles should be
mounted in such a manner as to avoid large temperature gradients
such as those encountered in the pa th of dewar vents.
Operation of the AMI Model 187 Liquid Level Instrument with a
device other than an AMI Liquid Level Sensor may void the
the Model 187 to the sensor using the six supplied RG-59/U
coaxial cables. Ensure the cables are connected to the correct sensor and
r (see Figure 2-1 below and page 5 for a system
diagram). The numbers shown in Figure 2-1 will be metal-stamped on the
sensor top-plate and probe cable adapter.
Moisture or contaminants in any of the BNC coaxial connectors can
short the measu r ement and cause er roneous read in gs . A pack of
non-conductive electrical connection lubricant (ECL) has been
Connecting the sensor cables
2.4 Connecting the Model 187 to the Sensor
Note
Caution
CONNECT 3 TO OUTPUTS: PROBE (J3) CONNECT 6 TO INPUTS: PROBE (J6)
3 6
CONNECT TO
CENTER BNC CONNECTOR
CONNECT 5 TO INPUTS: LIQ REF (J5)
Figure 2-1.
Diagram of sensor top-plate and cable connections.
5
2
4
CONNECT 1 TO OUTPUTS: GAS REF (J1)
1
CONNECT 4 TO INPUTS: GAS REF (J4)CONNECT 2 TO OUTPUTS: LIQ REF (J2)
Caution
9
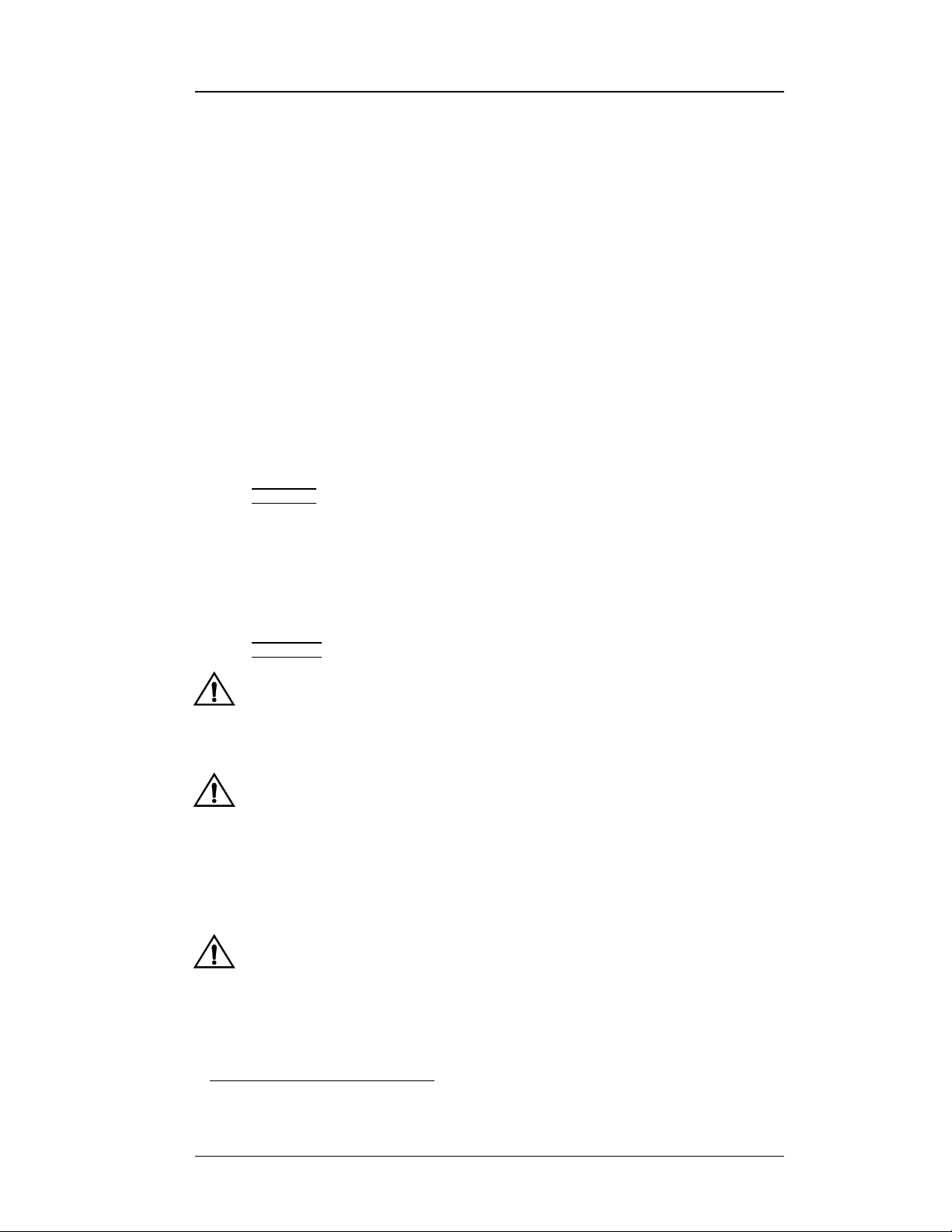
Installation
included with the liquid level sensor packaging to reduce the
possibility of this occurring. If the sensor is operated in an
environment where it will be exposed to moisture or other
contaminants, AMI recommends applying a small amount of ECL to
any of the BNC connectors that may be exposed. Mate the doped
connectors and then remove any ex cess ECL from the outside of the
connector. Added protection can be achieved by coveri ng the doped
connections with a short section of heat-shrink tubing.
solenoid-operated fill valve by connecti ng the valve power cable
to the AC controller output rec ept acle on the rear pan el of t he ins tru ment.
The standard AMI supplied valve has a 9/32 inch orifice and the input and
output are tapped for 3/8 NPT.
When using a solenoid-operated control valve with the Model 187,
ensure the valve is configured for the opera ting voltage of the Model
187. Failure to do so will result in faulty operation and may al so
result in valve dam age .
Before touching any of the controller output receptacle terminals or
touching the wiring connected to these terminals, remove power to
the instrument by unplugging it or turning the power switch to the
The controller output recep tacle conduc ts hazardous AC line volta ge
potentials. It is for use with equipment which has no live parts
which are accessible. Conductors connected to its terminals must be
insulated from user contact by reinforced or double insulation
capable of withstanding 4250 V (impulse) for a 230 VAC Category II
installation, or 2550 V (impulse) for a 120 VAC Category II
This instrument is designed for opera tion from a single-ph ase powe r
source for maximum safety. The controller output receptacle
circuitry only switches the “line” (“ hot”) connection to the AC mains.
If two-phase power is applied, any equipment connected to the
controller output receptacle conducts hazardous AC voltage even
when the controller output receptacle is not energized.
Connecting the sensor cables
2.5 Installing the Optional Solenoid-Operated Fill Valve
Caution
Warning
1. MSDS sheets for the ECL are available upon request.
10
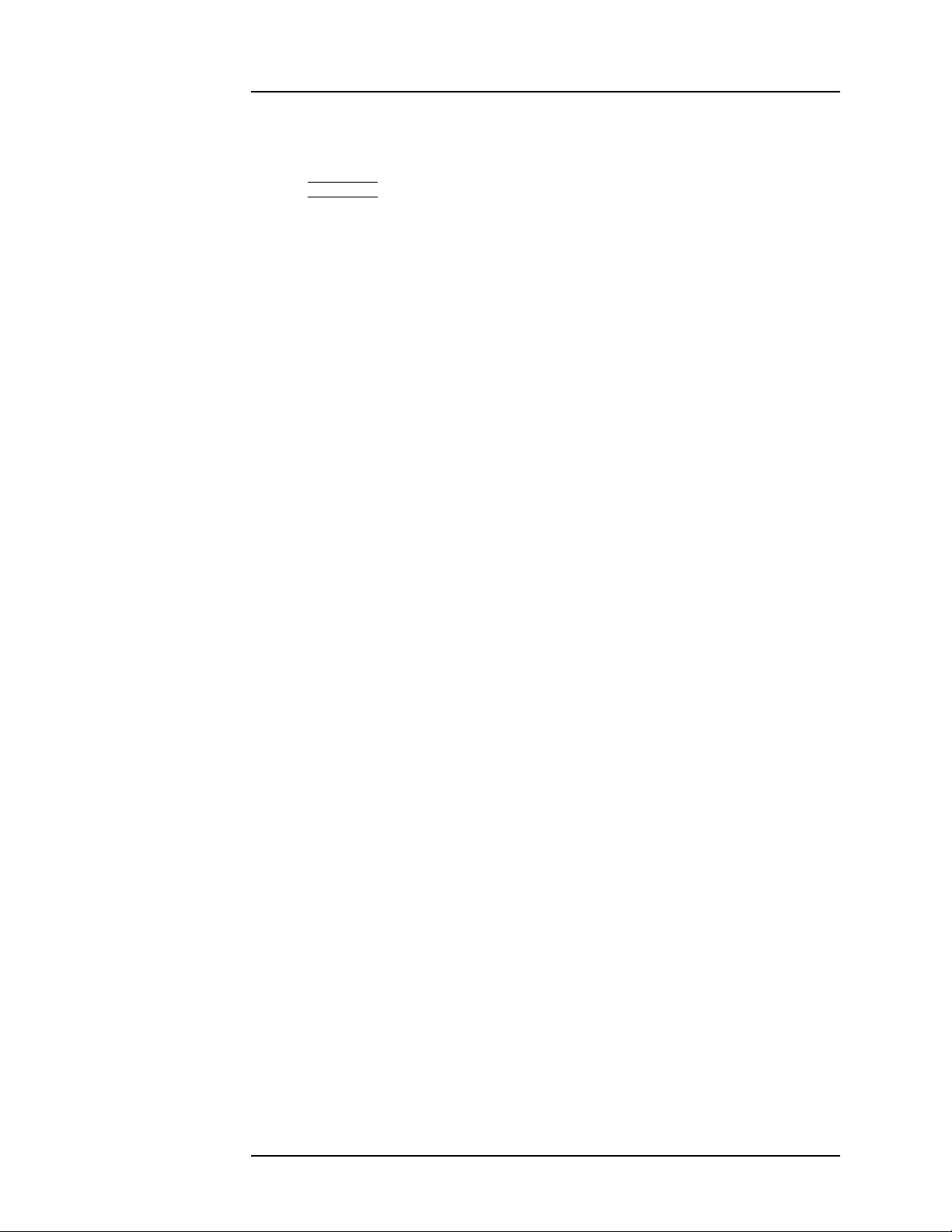
Installation
operates on 50-60 Hz power and may be configured
for 100-120 or 200-240 VAC ±10 %. The power requirements fo r each
instrument is marked on the calibration sticker on the bottom of the
instrument. Verify that your instrument is configured for your
power source prior to pl ugging in the li ne cord. Do not f ail to connect
the input ground terminal securely to an external earth ground.
instrument is configured for the proper operating voltage
by referring to the calibration sticker affixed to the bott om of the
instrument. If the operating voltage is correct, plug the line cord into the
appropriate power receptacle.
If the instrument operating voltage needs to be changed, ensure the
instrument is de-energized by disconnecting the power cord from the
power source. Remove the instrum ent cover and slide the voltage selector
switch on the main printed circuit board to the proper volt age. Replace the
Verifying power requirements
2.6 Connecting the Instrument to Power
Warning
11
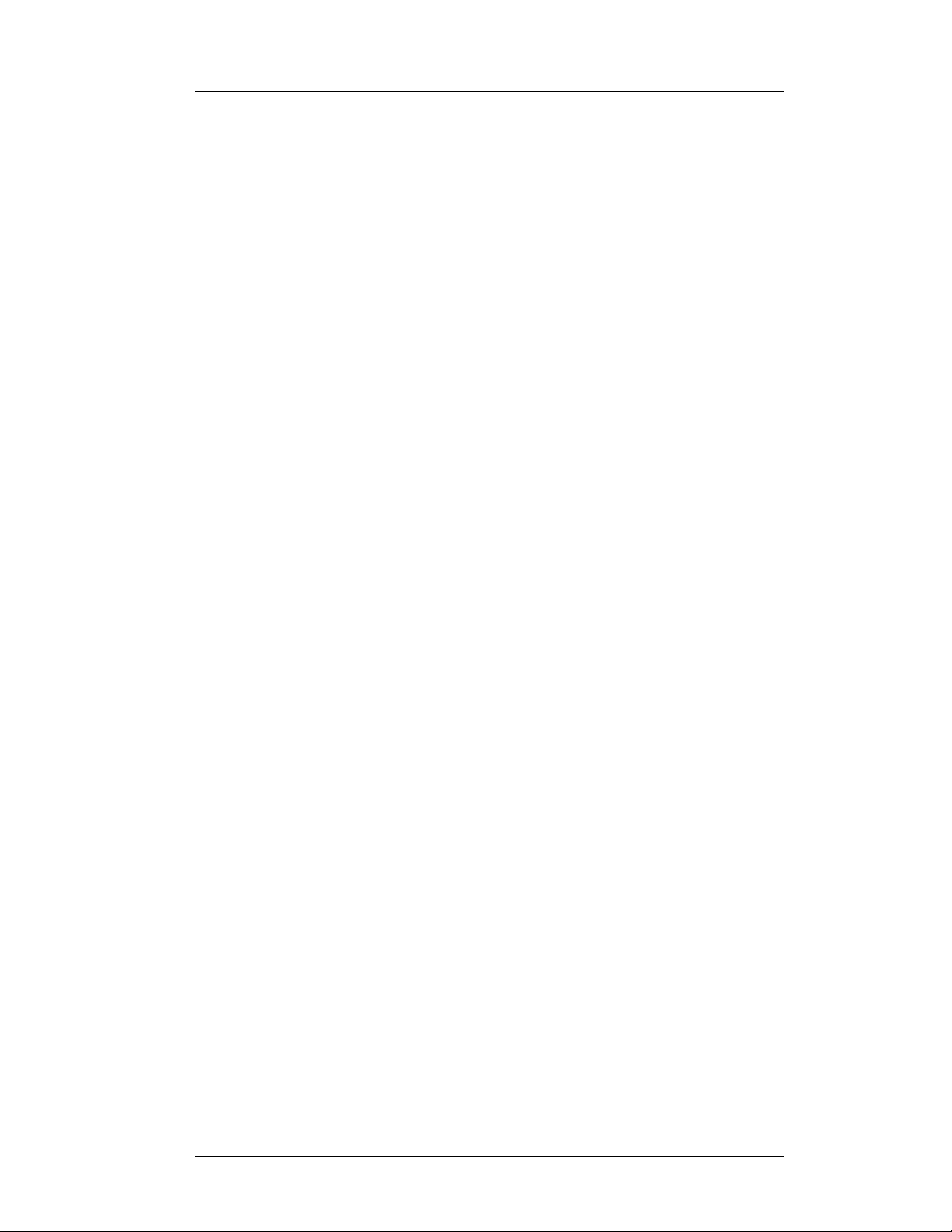
Installation
Verifying power requirements
12