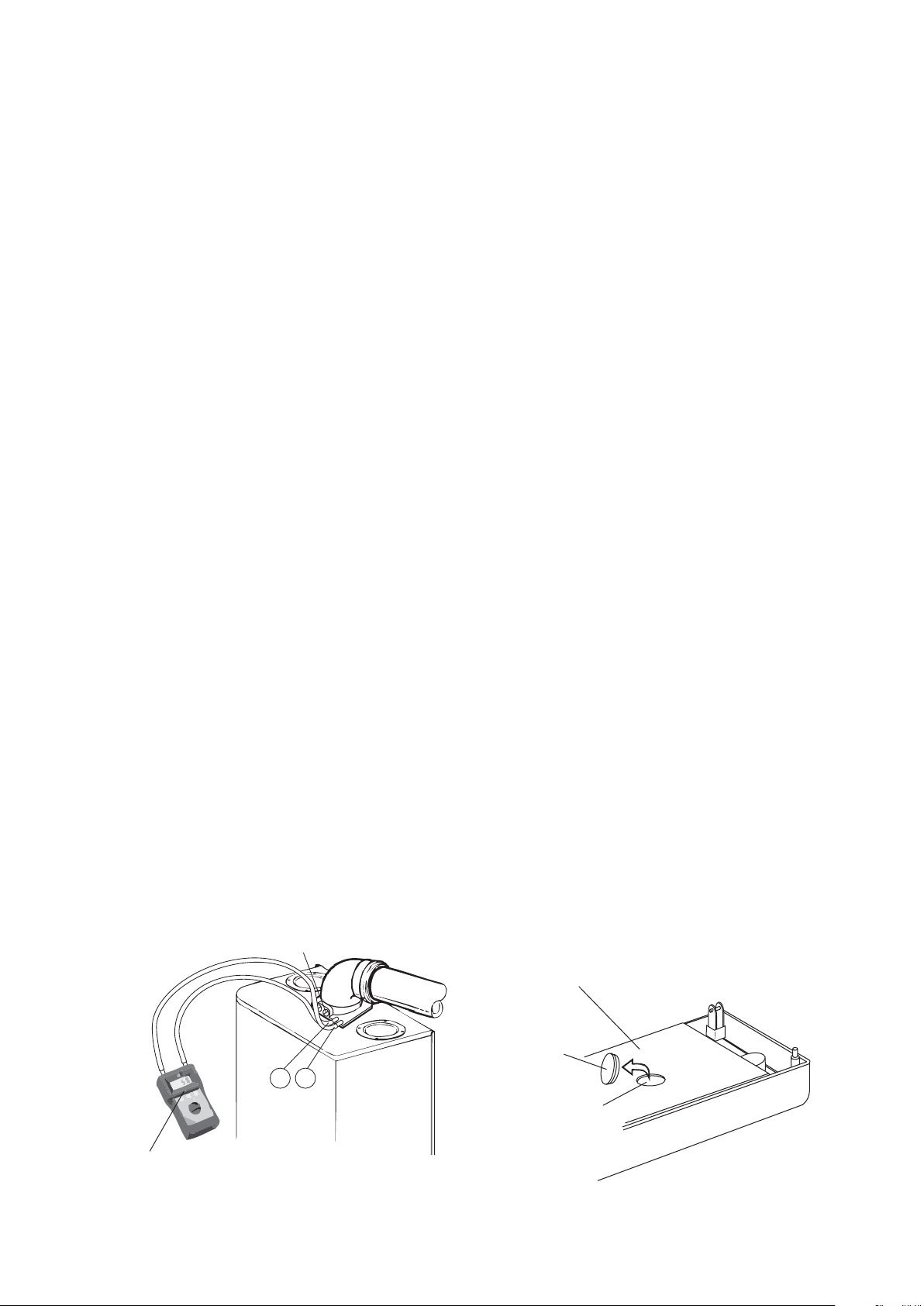
Instructions for adjusting the PCB and
Dungs gas valve
Alpha CD25X, 28X and CD12S, 20S, 28S
Boiler Ranges
1. GENERAL
When the printed circuit board (PCB) or Dungs gas valve have been replaced or require adjustment, the following
must be carried out:-
a. Check and adjust (if necessary) the CO2 content of the exhaust flue gases.
Note: A flue gas combustion analyser is required for these measurements. Also a 2 mm Allen key will be
required to adjust the gas valve.
b. Check and adjust (if necessary) the burner pressures.
Note: A differential pressure gauge will be required to enable the pressure to be correctly set.
c. Set the maximum output.
d. Ensure that all electrical plugs and connectors are pushed fully home and soundly connected.
Note: Before fitting a new PCB ensure the polarity of the electrical supply is correct by testing the supply, using a
suitable multimeter, as follows:
Live to Neutral 240 Volts AC
Live to Earth 240 Volts AC
Neutral to Earth zero Volts AC
2. FIT THE REPLACEMENT PCB AND/OR GAS VALVE
Refer to the Installation and Servicing instructions to gain access to and replacement of the PCB and/or gas valve.
3. ADJUST THE PCB AND GAS V AL VE TO THE CORRECT SETTINGS
a. Remove the screws from the pressure test points P1 and P2 and connect a differential pressure gauge to the test
points as shown in Fig. 1. Remove the screw securing the flue sampling cover and remove the cover. Place the
flue gas analyser probe into the flue sampling point (marked 'F').
b. Remove the grommet in the rear of the control panel (see Fig. 2) to gain access to the PCB. Using a small
screwdriver turn the 'CH CAP' potentiometer fully clockwise to maximum output, see Fig. 3.
c. Turn the selector switch to the reset position until the neon 'A' (red) is illuminated. This will operate the boiler at
maximum output for 10 minutes.
Flue sample
point (marked 'F')
Rear of control panel
-
+
-
Remove
grommet
+
Access to
potentiometer
CH CAP and
MAX CAP
Differential
Burner
pressure
-
+
Fig. 1 Fig. 2
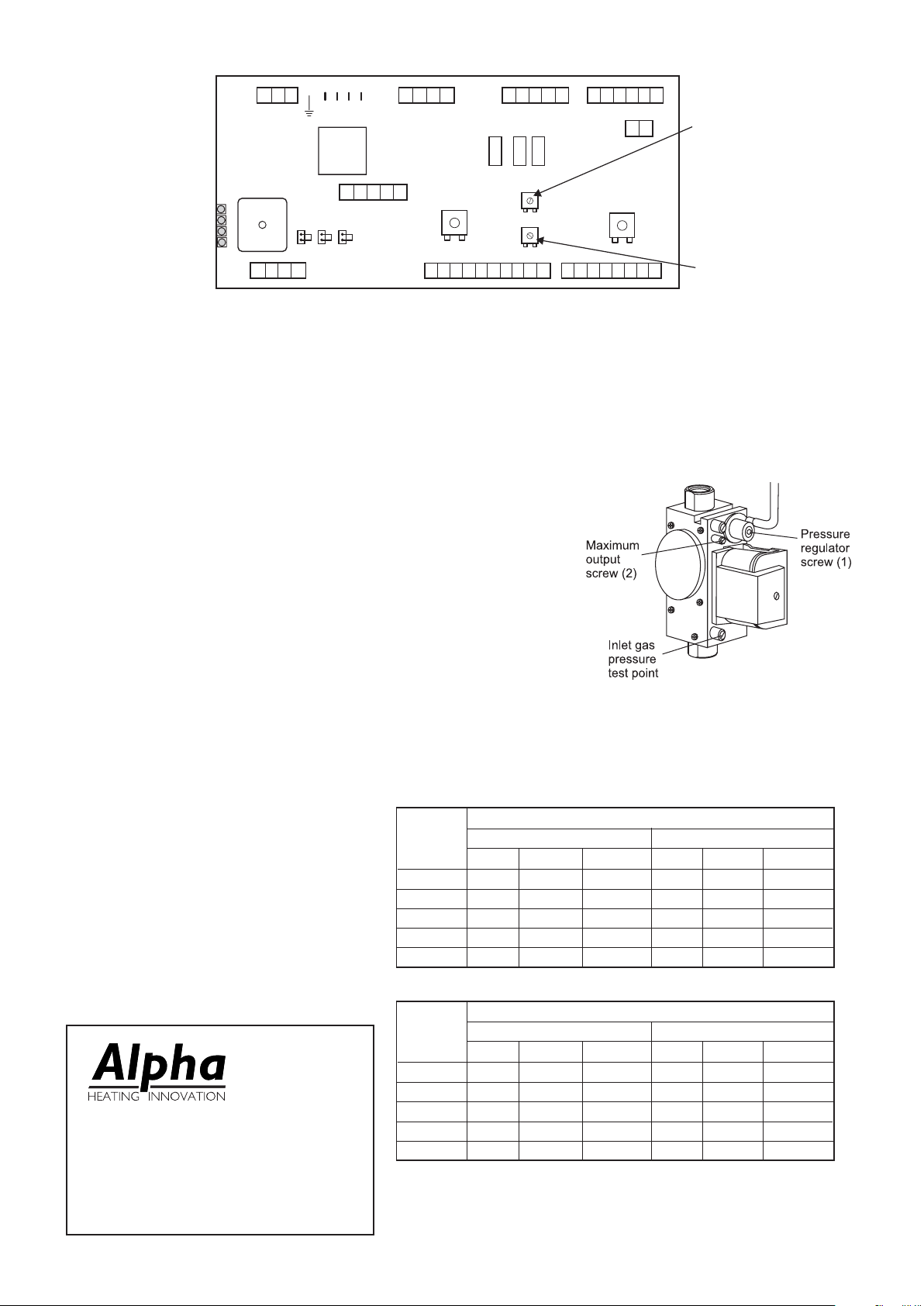
5
X15
4
12
6
6
5
CH CAP
X3
X11
8
71
MAX CAP
Green LED
Yellow LED
Red LED
Red LED
3
Main
PCB
1
21
X8
2
S3 S1 S2
4
3
X4
2
4
1
32
X13
1
X6
315 mAT max
1
X9
Fuse F1
250 V
DHW SET
3
2
4
X7
5
4
32
453
X12
F1 F2 F3
958
6
7
Fuse F2 and F3
CH CAP
MAX CAP
10
1
2.5 AF
250 V
2
3
231
CH SET
4
Fig. 3
d. Allow the boiler to operate for 5 minutes to stabilise, then using a small screwdriver turn the 'MAX CAP'
potentiometer (clockwise to increase) until the maximum pressure is obtained on the differential pressure gauge
(refer to table 1 for the correct pressure).
e. Adjust the 'CH CAP' potentiometer by turning screw fully anticlockwise to the minimum output position.
f. Measure the CO
the CO2% given in table 2 at the minimum output, then the gas valve must be adjusted. To gain access remove the
front casing by releasing the four screws and lifting off.
g. Using a 'hexagonal' 2 mm allen key, turn the pressure regulator screw (1), see
Fig. 4 clockwise to increase CO2 and anticlockwise to reduce CO2 until the
correct value given in table 2 is obtained.
h. Adjust the 'CH CAP' potentiometer to give the maximum output (fully clockwise),
i.e. set the burner pressure to the Max stated in table 1.
i. At the maximum output check that the CO
is that stated in table 2. If not, adjust the maximum output screw (2) on the
gas valve (see Fig. 4) using a suitable screwdriver until the CO2 content is
correct. Then recheck the CO2 content when the 'CH CAP' potentiometer is
at minimum output. Repeat the previous procedures 'e to i' until the
correct values are obtained.
When the adjustment procedure has been completed, set the 'CH CAP' to
give the maximum differential pressure for central heating (CH)
Note: This must be done when the boiler is operating in the condition
described in Section 3 paragraph c overleaf.
j. Remove the analyser and pressure gauge and re-assemble in the reverse order, ensuring that all the pressure test points
and flue sampling points have been refitted with the screws/caps previously removed and been tested for tightness.
content of the exhaust flue gas at the minimum output with the analyser. If the reading is not within
2
content of the exhaust flue gas
2
Fig. 4
Alpha Therm Limited.
Nepicar House, London Road, Wrotham Heath,
Sevenoaks, Kent TN15 7RS
Tel: 0870 3001964
email: info@alphatherm.co.uk
website: www.alpha-innovation.co.uk
Table 1
Differential burner pressure (mbar)
Boiler
model
CD25X
CD28X
CD12S
CD20S
CD28S
Natural gas LPG (propane)
Min
0.40
0.24
0.20
0.33
0.25
CH Max
3.32
6.60
6.60
6.65
6.30
DHW Max
5.20
8.83
-
-
-
Min
0.54
0.30
0.18
0.35
0.40
CH Max
4.39
7.61
7.57
8.17
7.50
DHW Max
7.00
10.18
-
-
-
Table 2
%CO2 content (± 0.2%)
Boiler
model
CD25X
CD28X
CD12S
CD20S
CD28S
These instructions have been carefully prepared but we reserve the right to
alter the specification at any time in the interest of product improvement.
© Alpha Therm Limited 2007.
Natural gas LPG (propane)
Min
9.0
8.9
8.9
8.9
9.1
CH Max
9.4
9.4
9.4
9.4
9.4
DHW Max
9.40
9.44
-
-
-
Min
10.0
10.1
10.2
10.2
10.3
CH Max
10.6
10.7
10.6
10.6
10.6
DHW Max
10.6
10.7
-
-
-
Instructions compiled and designed by Publications 2000 - Tel: (01670) 356211 0707/D211