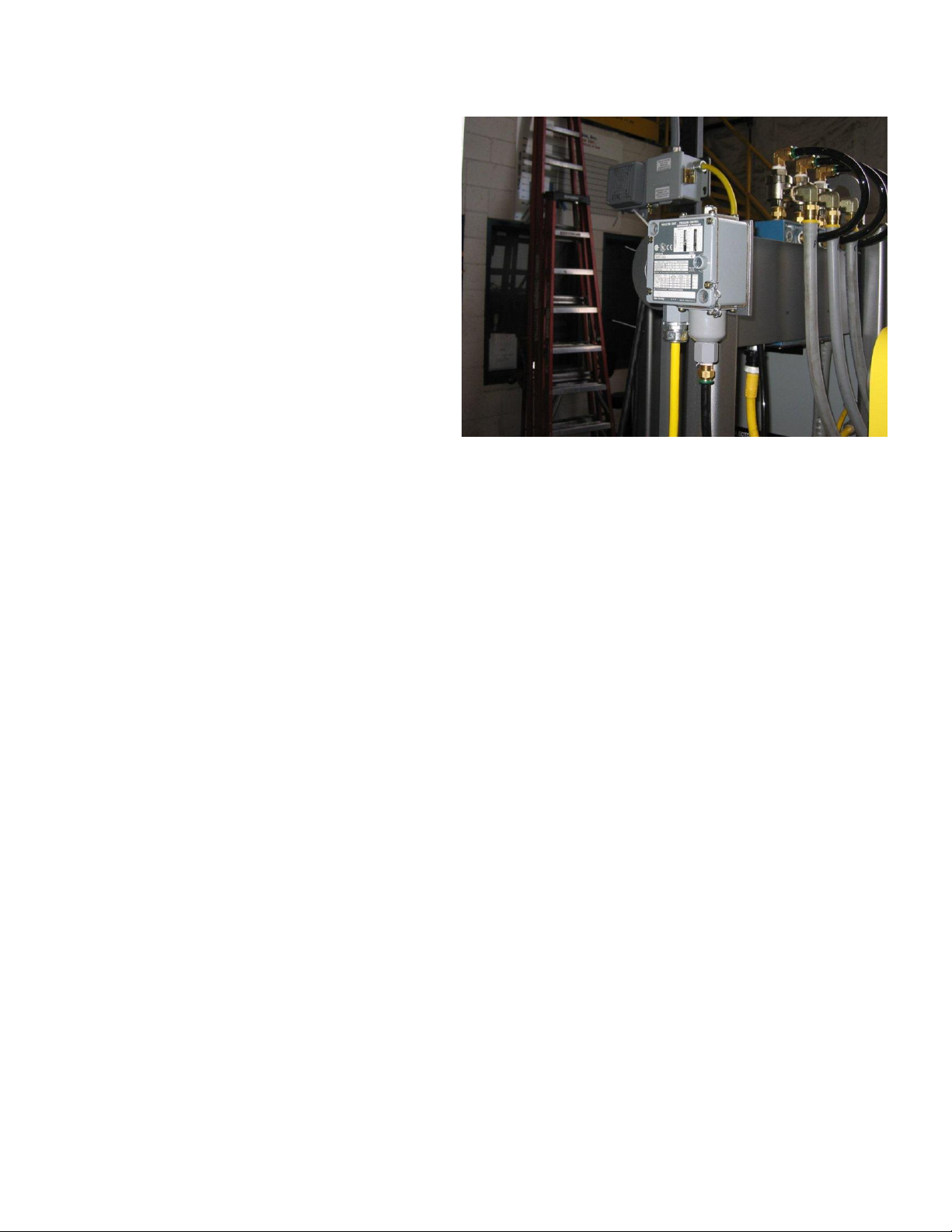
Pressure Switch 836T – Allen Bradley
Technical Data
Technical Terms
Adjustable operating range — Total span
within which the contacts can be adjusted to
trip and reset.
Trip setting — Higher pressure setting at
which value the contacts transfer from their
normal state to a change state.
Reset setting — Lower pressure setting at
which value the contacts return to their
normal state.
Adjustable differential — Difference between the trip and reset values
Minimum differential — When the differential is set to the lowest possible difference between trip and
reset.
Maximum differential — When the differential is set to the highest possible difference between trip
and reset.
Max. occasional surge pressure — Maximum surge pressure that can be applied to the actuator. Surges
or transients can occur during start-up and shut-down of a machine or system. Expressed in
milliseconds, complex electronic instrumentation is required to measure the varying amplitude,
frequency, and duration of this wave form. Extreme surges that occur approximately 8 times in a 24-
hour period are negligible.
Maximum line pressure — Maximum sustained pressure that can be applied to the actuator without
permanent damage. The control should not be cycled at this pressure. Note: Does not apply to piston
type controls.
psi — Pounds per square inch gauge (positive pressure). Devices listed are in gauge pressure units which
use atmospheric pressure as a reference. Atmospheric pressure at sea level is approximately 14.7 psi or
30 in. Hg.
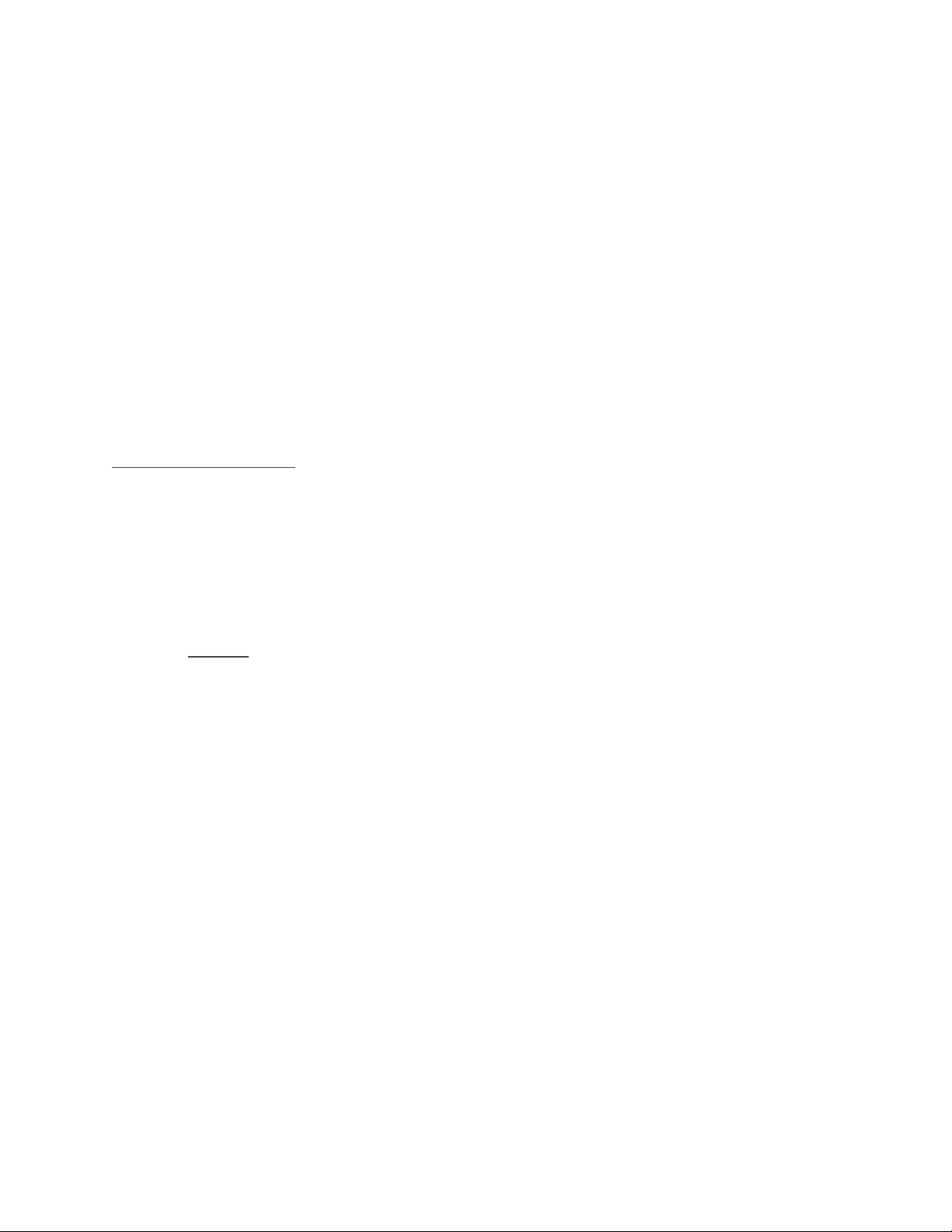
Pressure Switch 836T – Allen Bradley
Vacuum — Inches of mercury (in. Hg) vacuum (negative pressure).
Operating range adjustment screw — This screw is used to adjust the trip setting by varying the force
of the main spring.
Differential adjustment screw — This screw is used to adjust reset setting by varying the force of the
differential blade spring.
Pressure media — There are many types of pressure media that can be controlled. Examples include
air, water, hydraulic fluids, and other types of gases and liquids. The type of media and the maximum
system pressure will determine the type of actuator used for the pressure control application. See
Pressure Control Selection.
Pressure connection — Common standard types of pressure connections used in control systems are
1/4 in. and 3/8 in. N.P.T. female pipe threads. SAE 7/16 and SAE 9/16 O-ring boss seals are also
available (piston versions only).
Contact configuration — Bulletin 836T controls are available with either a 2-circuit or 4-circuit contact
block. See Contacts.
Style D
Style D — pressure difference controls adjustable system difference range — The adjustable
operating range for a pressure difference control.
System difference pressure bushing — This bushing is used to adjust the trip setting by varying the
force on the main spring.
Trip setting — Desired difference in pressure between the two bellows at which value the contacts
transfer from their normal state to a changed state. This occurs in one of the following conditions:
The pressure in the bottom bellows is higher than the pressure in the top bellows by a value equal to
the trip setting.
The pressure in the bottom bellows remains constant and the pressure in the top bellows decreases
by a value equal to the trip setting.
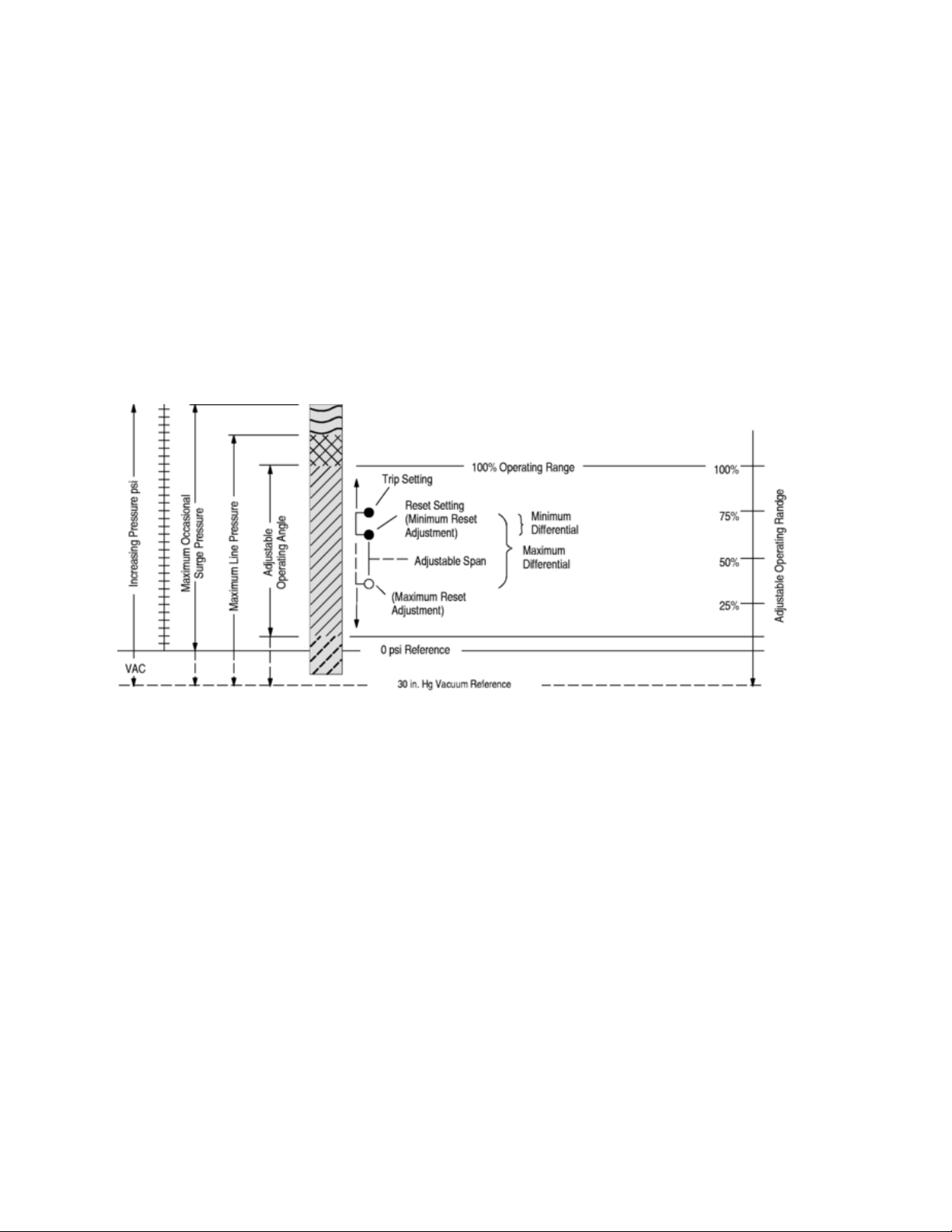
Pressure Switch 836T – Allen Bradley
Reset setting — Pre-determined normal difference in pressure between the two bellows, at which
value the contacts return to their normal state. This occurs in one of the following conditions:
The pressure in the bottom bellows is lower than the top bellows.
The pressure in the bottom bellows remains constant and the pressure in the top bellows increases.
Figure 1
Graphics to Illustrate Technical Terms
Theory of Operation
Bulletin 836T Pressure Controls are designed to open or close electrical circuits in response to changes
in pneumatic (air or gas) or hydraulic (oil or non-corrosive liquids) pressure. Piston controls are not
intended for use with air or water. (Figure 2) shows the basic operating mechanism.
Pressure is applied to the actuator which can be either a bellows or piston type. As pressure rises, the
actuator exerts force on the main spring. When the threshold force of the main spring is overcome,
levers transfer the motion to the contact block, displacing the contacts — this is referred to as the trip
setting. The unique lever design amplifies the actuator motion, providing shorter stroke, which results
in maximizing bellows life.

Pressure Switch 836T – Allen Bradley
The lever assembly also includes a virtually friction-free over-center toggle arrangement, providing
positive snap action to the contact block for long contact life. As pressure falls, force on the
differential spring increases and contacts return to their normal state — this is referred to as reset
setting. Varying the force of the main spring (by turning the operating range adjustment screw)
determines when the contacts will trip. Varying the force of the differential spring (by turning the
differential adjustment screw) determines when the contacts will reset. Setting trip and reset values
determines the operating parameters of the application.
Figure 2
Basic Mechanical Structure

Pressure Switch 836T – Allen Bradley
Applications for Control
Pressure controls can be used to either control or monitor a machine or process. (Figure 3) shows a
typical control application. Here, pressure is controlled within predetermined high and low values.
(Figure 4) shows a typical monitoring application. Here, pressure is monitored between a high and low
value, signaling when a preset limit has been exceeded.
Figure 3
Typical Control Application
Figure 4
Typical Monitoring Application

Pressure Switch 836T – Allen Bradley
Control Setting — Style T Pressure Controls
Allen-Bradley controls are designed for ease of setting to help minimize installation time. Standard
pressure controls shipped from the factory are set at the maximum operating range and minimum
differential. By using a pressure gauge and following these simple directions, the control can be set to
the specific requirements for each application. See (Figure 5).
Step 1 — Adjust trip setting
The trip setting is controlled by the operating range adjustment screw and is adjusted externally. After
loosening the lock nut, the trip setting is set by turning the operating range adjustment screw
counterclockwise to lower the trip setting or clockwise to raise the trip setting. The approximate trip
setting is shown on the indicating scale. When the proper setting is reached, simply tighten the lock
nut.
Note: Turning the operating range adjustment screw will cause both the trip and reset settings to
change in virtually equal increments.
Step 2 — Adjust reset setting
The reset setting is controlled by an external differential adjustment screw. The reset setting is set by
turning the differential adjustment screw clockwise to increase the differential or counterclockwise to
decrease the differential.
Note: Adjusting the differential has little or no affect on the trip setting.

Pressure Switch 836T – Allen Bradley
Figure 5
Trip and reset adjustment for pressure controls
Mounting without Removing Cover
Bulletin 836T controls can be mounted without removing the front cover. This helps prevent foreign
materials from entering the opened enclosure during the interval between mounting and wiring of the
control.