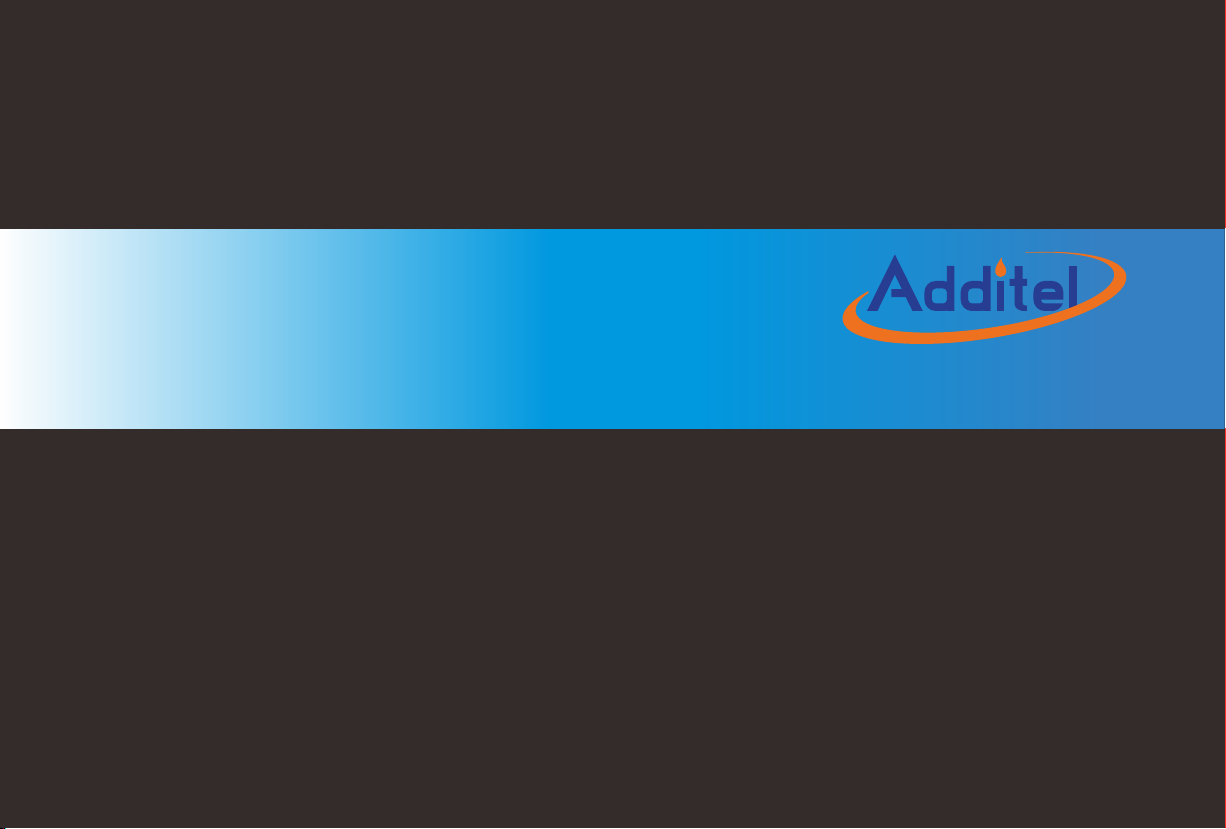
ADT780 Pressure Controller

ADT780 Pressure Controller
User Manual
(Version No.: 201902V02)
(Please download the latest version via www.additel.com)
Additel Corporation.
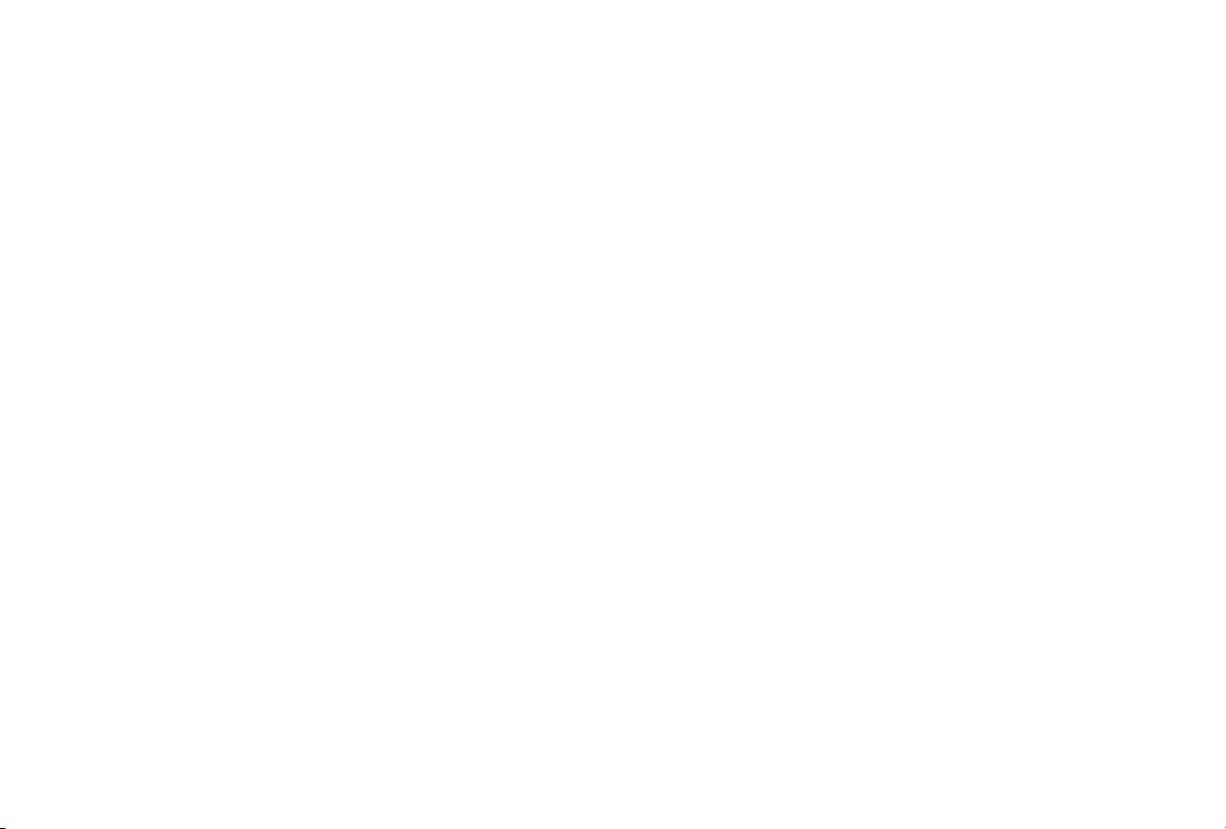
Statement
This manual applies to ADT780 pressure controller series designed and produced by Additel Corporation.
This manual is subject to change without notice.

I. SAFETY NOTES 1
1.1 SAFETY AND CAUTION 1
1.2 LIABILITY 1
1.3 GENERAL SAFETY 1
1.4 WARNING
II. INTRODUCTION
2.1 OVERVIEW 2
2.2 FUNCTIONS 4
2.3 TECHNICAL SPECIFICATION 4
III. INSTALLATION 7
3.1 INSTALLATION 7
3.2 PRESSURE CONNECTION 7
3.3 ELECTRICAL MENU 9
3.4 COMMUNICATION MENU 10
3.5 PRESSURE MODULE CONNECTION 11
3.6 ELECTRIC SIGNAL MEASUREMENT AND BUS COMMUNICATION CONNECTION 12
IV. POWER-ON 14
4.1 POWER-ON SEQUENCE 14
4.2 LANGUAGE SETUP 14
4.3 DATE AND TIME SETUP 14
4.4 PRESSURE OUTPUT OF SETUP 15
V. OPERATION 15
I
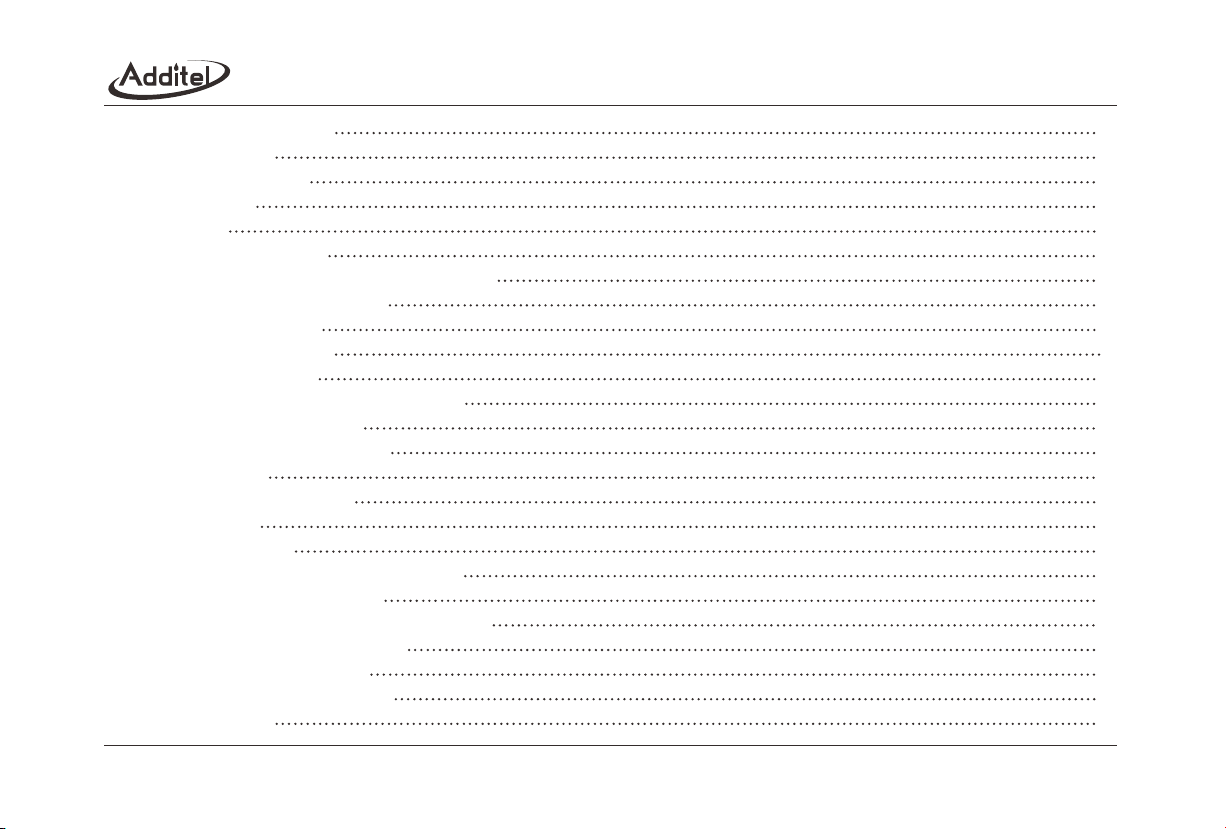
5.1 PRESSURE SETUP 15
5.2 UNIT SETUP 15
5.3 MEASUREMENT 15
5.4 CONTROL 16
5.5 EMPTY 16
5.6 PROGRAM SETUP 17
5.7 CURRENT/VOLTAGE MEASUREMENT 17
5.8 SWITCH MEASUREMENT 17
5.9 CONTROL SETUP 17
5.10 PRESSURE ZERO 19
5.11 DISPLAY SETUP 19
5.12 PRESSURE HEAD CORRECTION 19
5.13 DO CONFIGURATION 20
5.14 HART COMMUNICATION 20
5.14.1 Polling 20
5.14.2 Process Quantity 21
5.14.3 Setup 21
5.14.4 Diagnosis 21
5.15 PROFIBUS PA COMMUNICATION 23
5.15.1 Function Description 23
5.15.2 Equipment Description Document 23
5.15.3 Connection and Search 24
5.15.4 Process Quantities 24
5.15.5 Transmitter Operation 24
5.16 LEAK TEST 25
II
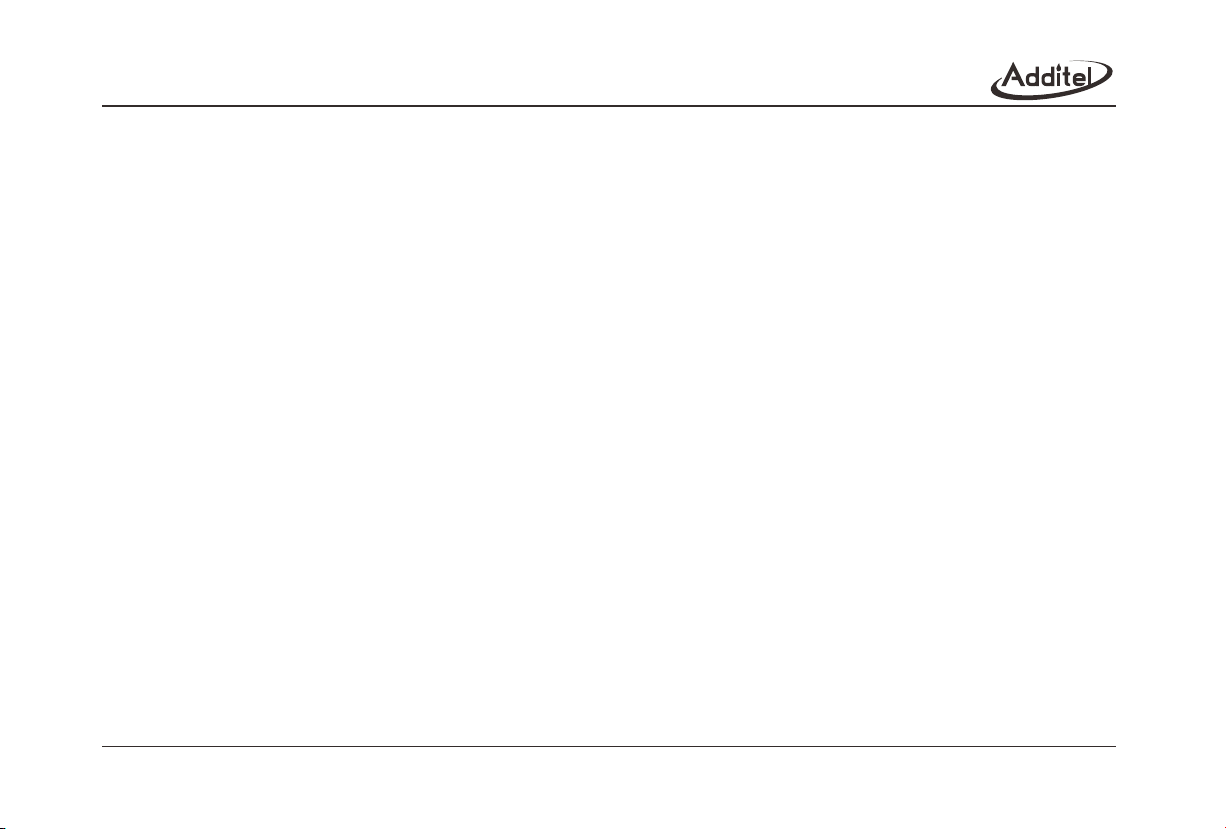
5.16.1 Setup ……………………………………………………………………………………………………………………… 25
5.16.2 Execution ………………………………………………………………………………………………………………… 25
5.17 SWITCH TEST ………………………………………………………………………………………………………………… 25
5.17.1 Setup ……………………………………………………………………………………………………………………… 25
5.17.2 Execution ………………………………………………………………………………………………………………… 26
5.18 AUTOMATIC STEPPING …………………………………………………………………………………………………… 26
5.18.1 Setting …………………………………………………………………………………………………………………… 26
5.18.2 Execution ………………………………………………………………………………………………………………… 26
5.19 DECOMPRESSOR …………………………………………………………………………………………………………… 27
5.19.1 Setup ……………………………………………………………………………………………………………………… 27
5.19.2 Execution ………………………………………………………………………………………………………………… 27
VI. REMOTE COMMUNICATION ……… … … … … ……… … … … … ………… … … … … ……… … … … … … ……… 28
6.1 COMMUNICATION SETTING ………………………………………………………………………………………………… 28
6.1.1 Communication Setting –RS232 ………………………………………………………………………………………… 28
6.1.2 Communication Setting –WIFI …………………………………………………………………………………………… 28
6.1.3 Communication Setting – LAN …………………………………………………………………………………………… 28
6.2 COMMUNICATION COMMANDS …………………………………………………………………………………………… 29
VII. MAINTENANCE … … … … … … … … … … … … … … … … … … … … … … … … … … … … … … … … … … … … … … 2 9
7.1 SYSTEM AND PRODUCT INFORMATION ………………………………………………………………………………… 29
7.2 FIRMWARE UPDATES ………………………………………………………………………………………………………… 29
7.3 CALIBRATION ………………………………………………………………………………………………………………… 29
7.3.1 Internal pressure module and external pressure module calibration ……………………………………………… 30
7.3.2 Atmospheric pressure module and vacuum module calibration …………………………………………………… 33
7.3.3 Electrical signals measurement standards …………………………………………………………………………… 34
7.3.4 Atmospheric pressure module calibration ……………………………………………………………………………… 34
II I
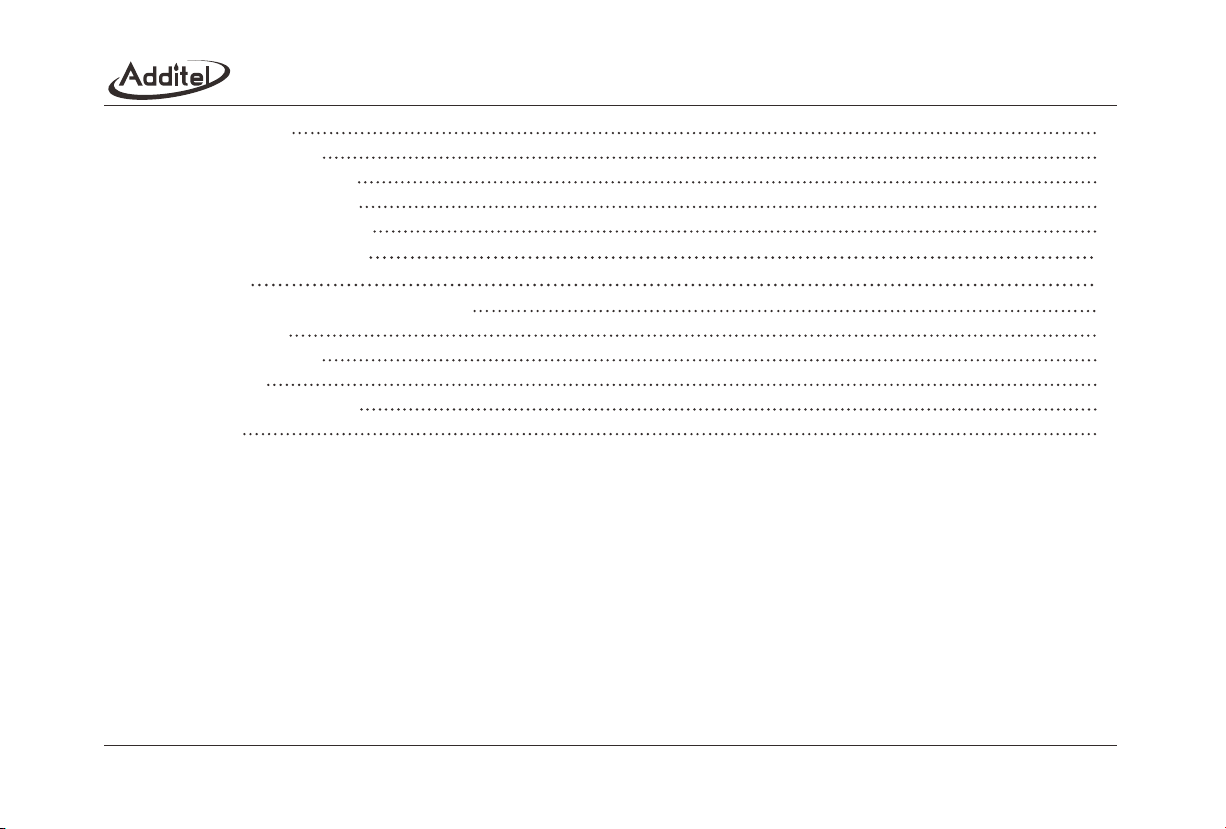
7.3.5 Self-tuning 35
7.4 UNINSTALLATION 35
7.5 CHANGEABLE PARTS 36
7.6 FUSE REPLACEMENT 36
7.7 FILTER REPLACEMENT 37
VIII. TROUBLESHOOTING 38
IX. APPENDIX 40
9.1 TRANSPORTATION AND STORAGE 40
9.1.2 Packaging 40
9.1.3 Transportation 40
9.1.4 Storage 40
9.2 PRESSURE UNIT LIST 40
9.3 SCPI List 41
IV
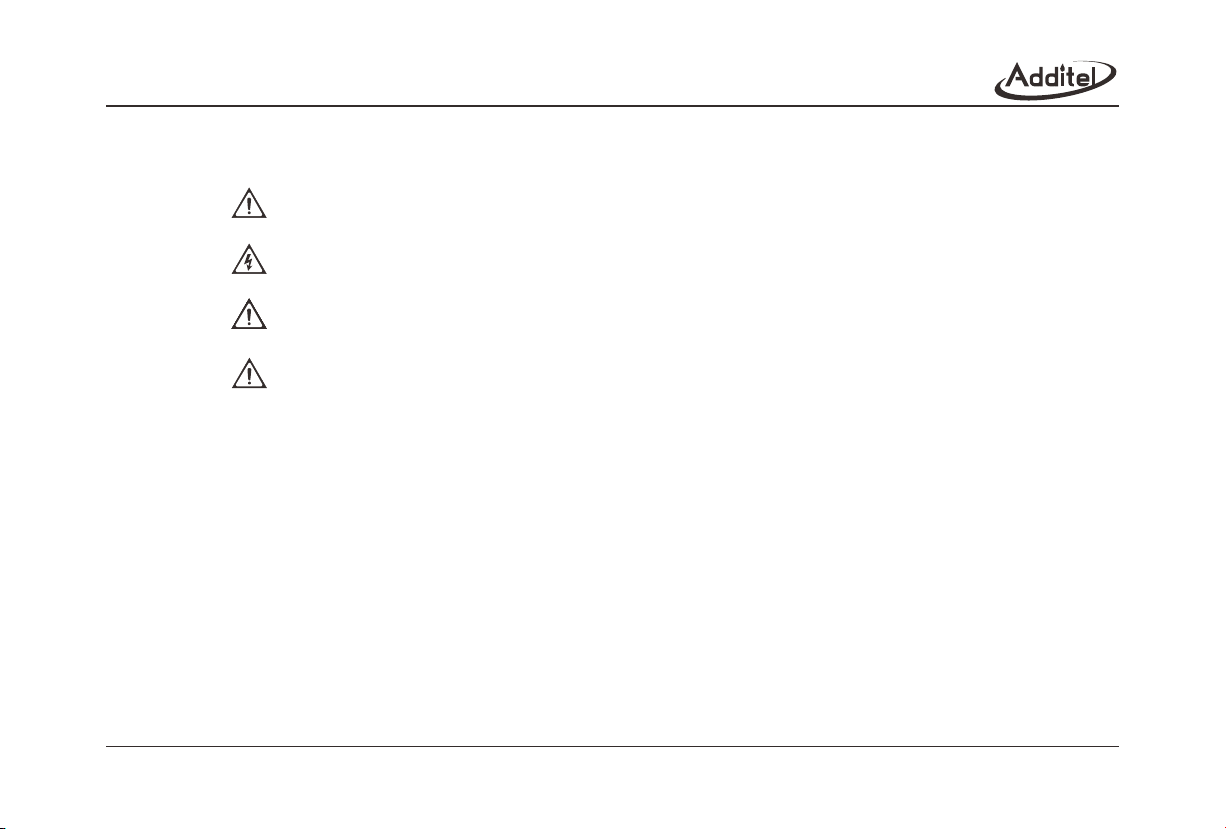
I. Safety Notes
1.1 Safety and Caution
The mark on the controller means that the user must pay attention to operation instructions in the manual before
operation.
The mark on the controller means that high voltage may exist at the terminal or jack. Direct contact should be
avoided.
The mark in the manual refers to high voltage or high pressure where injury could occur.
Warning
The mark in the manual Indicates product damage may occur if operation instructions are not closely followed. Any
Caution
damage resulting in incorrect use of the product is not covered under the product warranty.
1.2 Liability
◆ Please note the following safety instructions;
◆ Please read the user manual before operation;
◆ Only operate with recommended media;
◆ Do not use the controller if damage is suspected;
◆ This product should be maintained by Additel or an authorized agent;
◆ Ensure the ground is connected with the AC power.
1.3 General Safety
◆ The controller should not be subject to strong vibration, impact, high temperature, high humidity or strong magnetic
influence;
1
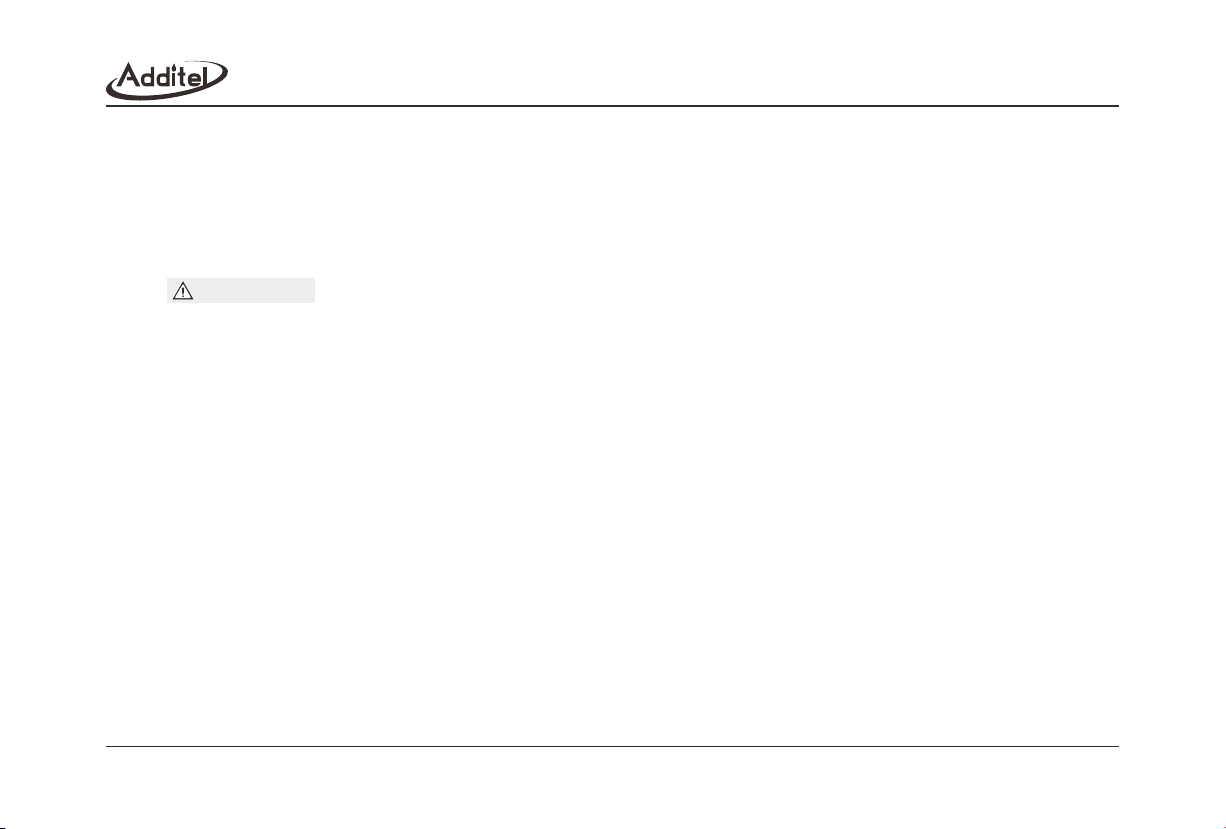
Do not use objects to clean or maintenance the controller that are not warranted;
The power voltage of the controller could cause physical injury. Even if the power supply is off, power could be
temporarily stored;
Ensure the controller is completely dry of any condensation that may have occurred.
1.4 Warning
High Pressure means the potential risk of high pressure air exist. The high pressure system can be installed and
operated by professionals only;
Pipes, valves and other facilities connected with the controller must be rated to the maximum pressure and the
sufficient safety redundancy considered;
Clean, dry and noncorrosive air shall be used. Oxygen should not be used as the control media;
Do not use in dusty, steamy or corrosive gas circumstances;
Do not use in explosive or dangerous environments;
Ensure the controller is not used under overvoltage condition;
When using nitrogen or inert gas as the media, the sufficient ventilation shall be ensured in the operation area.
II. Introduction
2.1 Overview
ADT780 Pressure Controller series can be used for a wide variety of application tests, calibrations and verifications.
ADT780 Pressure Controller has two range-dependent base units that determine the maximum pressures listed below.
Each base requires an external gas supply or Additel Electric Pump to control pressure.
● -0.1MPa ~ 7MPa; one pressure module with the range of 7MPa is embedded;
2
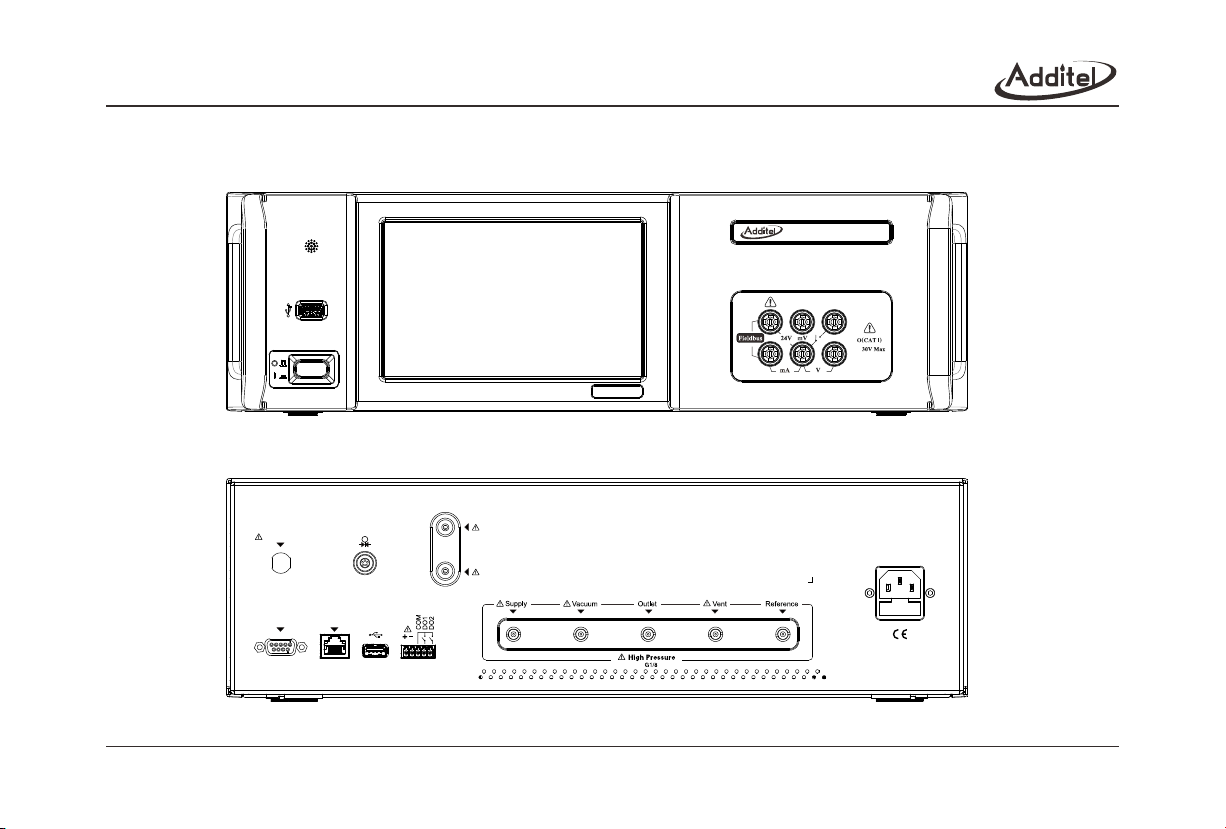
● -0.1MPa ~ 21MPa; one pressure module with the range of 21MPa is embedded;
ADT780 can be equipped externally or internally with Additel 160A series of pressure modules.
780 Pressure Controller
DC
Fig. 2-1 Basic Structure of ADT780 front panel
Logic Output
RS-232
Barometer
Exhaust
LAN
75W Max
(100-240) V
(50-60) Hz
Fuse T3.15A 250V
Fig. 2-2 Basic Structure of ADT780 rear panel
3
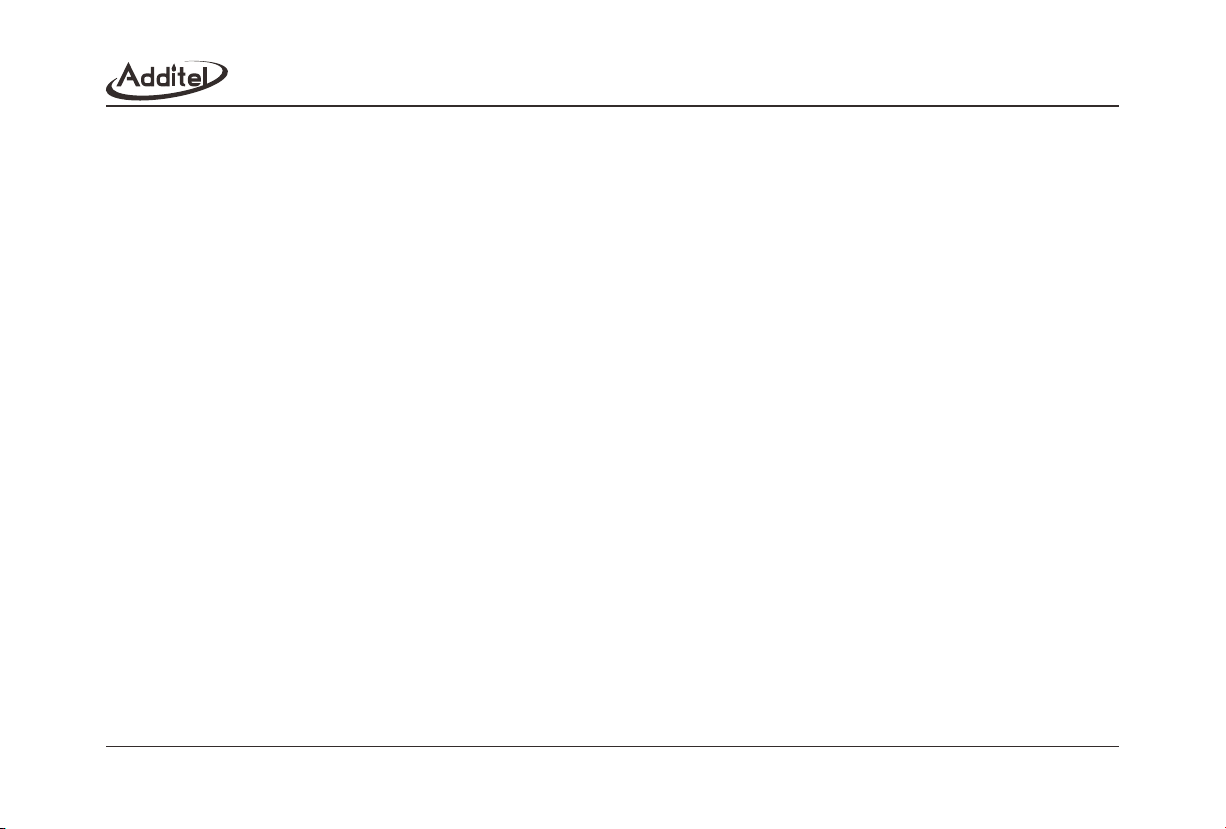
2.2 Functions
Full auto control output pressure;
Can either be connected with pressure modules externally for control output ;
ADT780 output control defaults to the internal sensor when an external sensor is not connected;
ADT780 is embedded with 40Pa barometric pressure sensor (optional 11Pa) and can realize the absolute pressure and
gage pressure;
DC24V power output;
2-way DO digital output;
DC±30mA current measurement or voltage measurement (±30V, ±300mV);
Pressure switch capability;
800x480 color touch-screen display control operation and good HMI;
Two modes: controller mode and calibrator mode;
Main USB menu and configurable with a USB flash disk externally;
RS232, LAN and WiFi menus;
HART Profibus protocol calibrates HART equipment;
Profibus PA protocols;
WINCE operation system.
2.3 Technical Specification
Technical indexes:
4
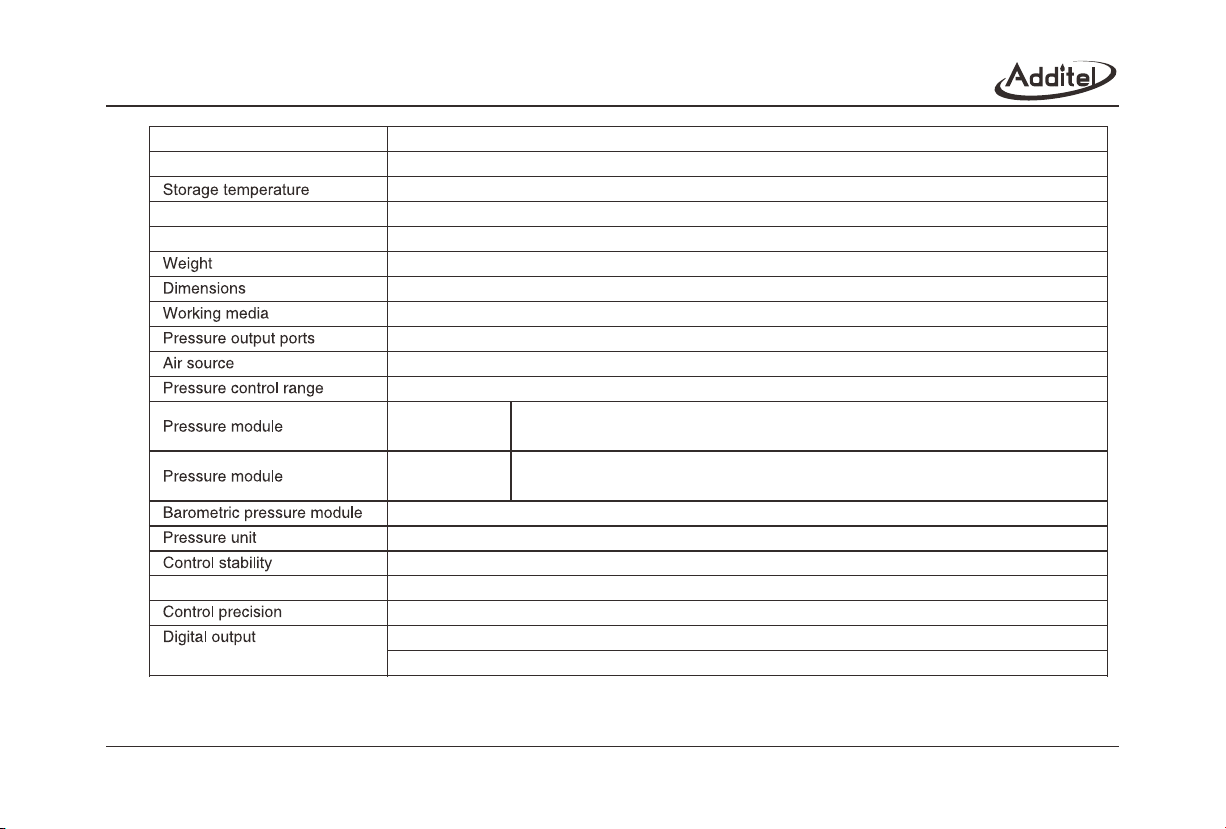
Power supply
Operation temperature
Working environment humidity
Display panel
Internal capacity
(100~240)VAC 50/60 Hz, maximum power consumption: 75 W
(0~50)
(-20~70)
<90%, non-condensed
7” color display, resolution: 800×480
15kg
3U cabinet (L×W×H = 419×440×132)mm
Nitrogen or dry and clean compressed air
Supply and outlet port: G1/8 female thread
110% ~120% of the pressure range
(-0.095~7) MPa or (-0.095~21) MPa
(-0.1~7)MPa
(-0.1~21)MPa
See ordering information for options and performance specifications. Control
sensor can be based on internal or external sensors.
See ordering information for options and performance specifications. Control
sensor can be based on internal or external sensors.
①
①
(60~110)kPa, accuracuy is 40Pa (11Pa is optional)
See Annex 9.2 for the pressure unit list
0.003% FS (stability based on % FS of control sensor)
500cc
Depending on the selected pressure control module
Two-way digital output (DO), programmable, source-less output, load-carrying capacity, 1A/DC24V
One-way source output, programmable, load-carrying capacity DC24V@200mA
Table 2-1 Technical Indexes
5

The pressure range and control is determinant of the pressure module selected. Beyond its range, the measurement
value can be displayed only. 0.01%FS or 0.05% FS external connection modules can be selected.
The control stability is correspondenting with pressure range.
Barometer Measurement Uncertainty
Sensor/Mode
ADT160-02-CPXX
ADT160-01-APXXQ
Table 2-2 Technical indexes of electric signal measurement technology
Gauge
N/A
3 Pa ②
Absolute
40 Pa ①
N/A
40 Pa uncertainty (K=2) includes calibration uncertainty, linearity, and long term stability (<30 Pa per year). Barometer
range of 60 to 110 kPa.
Combined linearity, hysteresis, and repeatability. Add 3 Pa when used in gauge mode. When the absolute pressure type
of ADT160-01-APXXQ is switched to the gauge pressure type, the zeroing must be implemented by user. The ADT780
controller will clear the value difference between ADT160-01-APXXQ module and barometer module automatically.
Technical indexes of electrical signal measurement (ambient temperature 20 ±5 , yearly accuracy)
Measurement Range
(-30.0000~30.0000)V
(-300.000~300.000) mV
(-30.0000~30.0000) mA
If the switch has the tour inspection voltage, the voltage scope shall be DC 3V DC 24V.
Table 2-3 Technical indexes of electric signal measurement technology
Resolution
0.1mV
1µV
0.1µA
Accuracy
±(0.01%RD+1.5mV)
±(0.01%RD+15µV)
±(0.01%RD+1.5µA)
Note 1: When the ambient temperature exceeds the range from 15-25 , the temperature coefficient for voltage &
current measurement range: ±0.0005FS / .
6
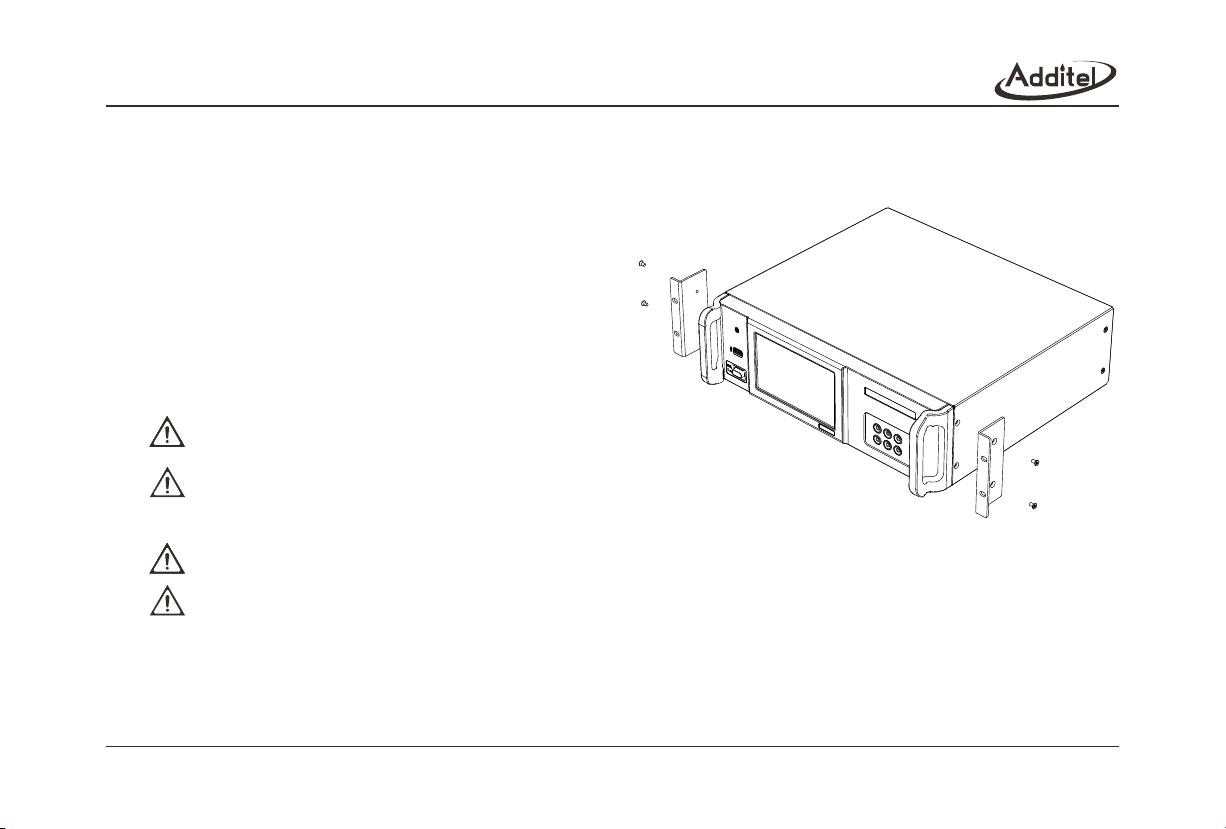
Note 2: Input characteristics:
(1) Voltage measurement range: input impedance >1MΩ,max. input voltage at the port: ±300VDC;
(2) Current measurement range: input impedance <10Ω, maximum input current at the port: ±1A DC.
◆ DC24V output, accuracy: ±0.24V, 50mA;
III. Installation
3.1 Installation
ADT780 pressure controller can used on a bench or rack
mounted. A rack mount kit may also be used to install the
controller on 19” (3U) cabinet. The rack mount kit includes
two fins and four installation screws. See Fig. 3-1:
When in operation gas may escape from “Vent” or
“Exhaust” ports and close contact should be avoided.
Warning
Ensure ventalation space near the bottom and rear
Caution
of the controller for heat dissipation.
3.2 Pressure Connection
Appropriate cautions and safety regulations should be observed when using gas supplies.
Warning
All pressure output is G1/8 and O-rings shall be used for sealing during connection.
Caution
See Fig. 2-3 for ADT780 pressure menu.
◆ Supply:
The Supply port is to connect a positive pressure supply to the controller. The supply should meet the following
requirements:
Fig. 3-1 Rack enclosure installation diagram
7
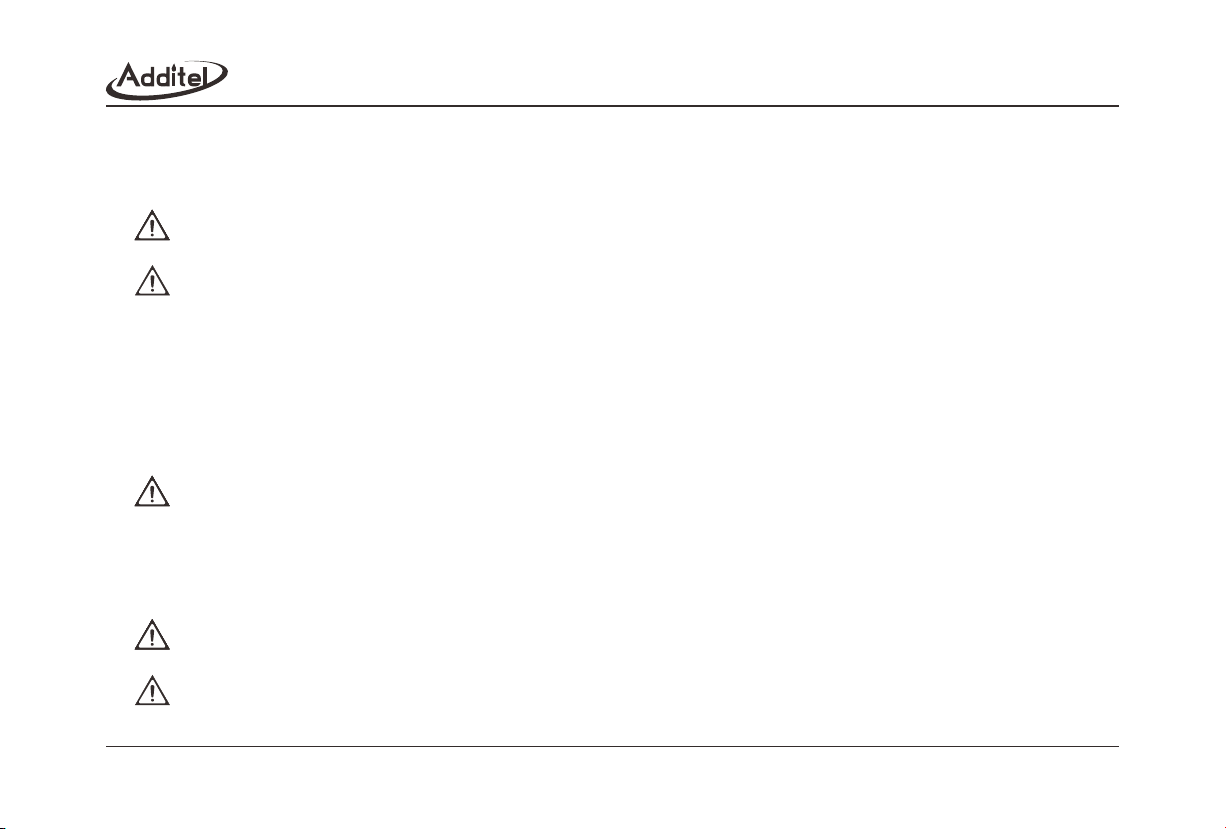
1) Air or nitrogen must be clean and dry;
2) The air supply source pressure scope shall be 110-120% of the range of the pressure module connected with the
controller;
The maximum air source pressure shall be 120%FS of the upper limit of the range of the pressure module connected
Warning
with the controller. Otherwise, injury or equipment damage may occur.
It is suggested that the positive pressure air source shall be connected to “Supply” after passing through the air-liquid
Caution
separator.
◆Vacuum:
“Vacuum” is the port which provides vacuum source for the controller. If no vacuum source is required, the port should be
open to atmosphere.
The controller is embedded with a vacuum switch solenoid valve. When the valve releases pressure from the higher
pressure to the lower pressure, gas will be exhausted from “Exhaust”. The controller can control the solenoid valve to
choose “Vacuum” only if the vacuum pressure is required.
Positive pressure applied to the vaccum port may result in injury or equipment damage.
Warning
◆Outlet:
Outlet" is the pressure output /measurement menuport. Under the measurement mode, the outlet can be connected
with external pressure (please execute the empty function before connection). Under the control mode, the controller
outputs an adjustable pressure at the set point.
The “Outlet” pressure should not exceed the pressure module range. Otherwise, injury or equipment damage may occur.
Warning
When the controller is set to measure mode and the external pressure control exceeds 2MPa, the release valve
should be tightly screwed in the “Supply” port (As Fig 7-1). If there is a need to remove this release valve, please
Caution
loosen it firstly to relief the residual gas out.
8