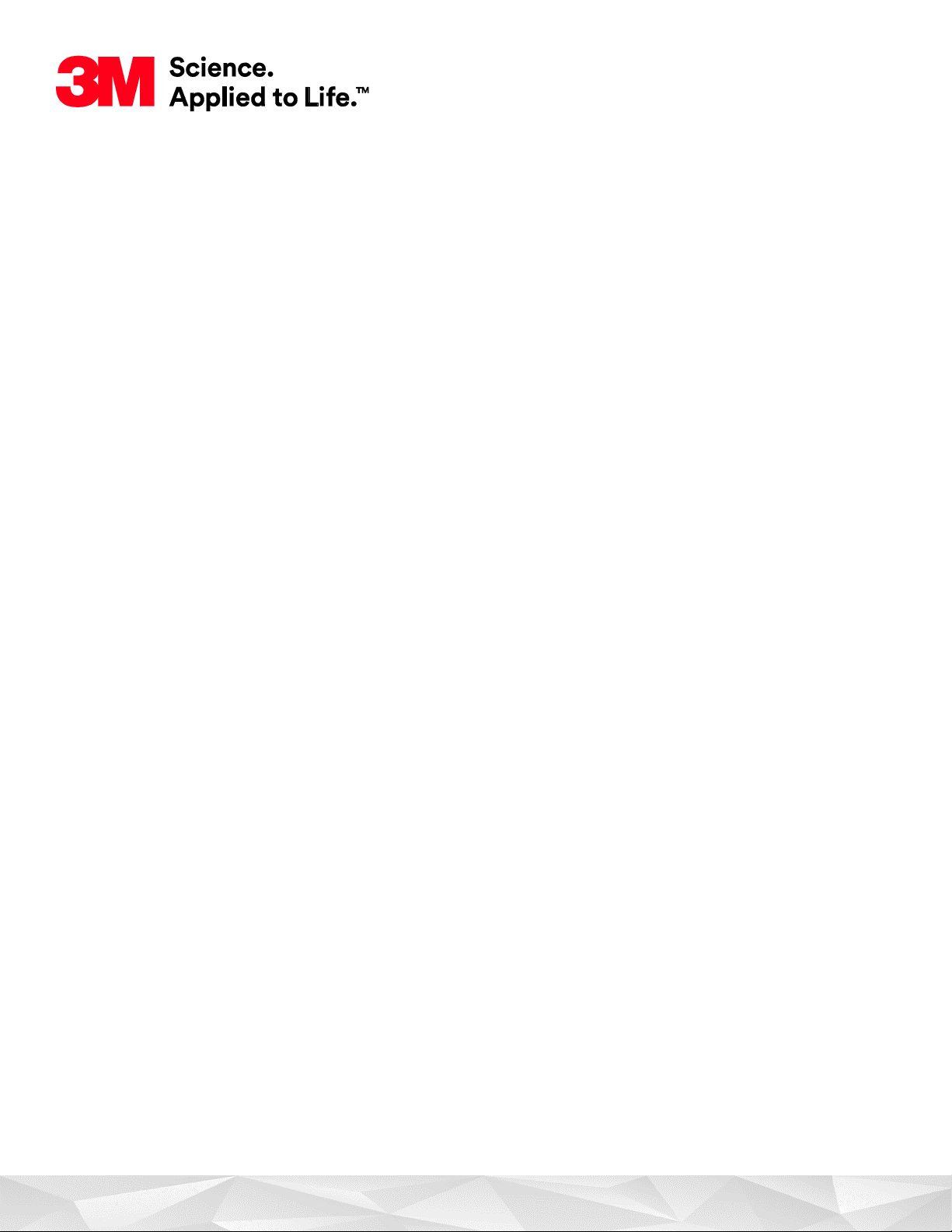
Transportation Safety Division
3M™ Reflective License Plate
Sheeting Recommended
Manufacturing Procedures
Information Folder 9.8
February 2021
Replaces Information Folder 9.8 Dated March 2020
1 Description
3M Reflective License Plate Sheeting Series 3750, 4770, 4780, 4790, 6700, 6750, and 9250 are durable, allweather sheetings designed for use in the fabrication of multi-year retroreflective license plates. They are used to
produce attractive license plates which function 24 hours a day to enhance nighttime safety and the legibility of
the vehicle identification system. The backsides of these sheetings are pre-coated with a pressure sensitive
adhesive, protected by a removable liner, for application to license plate substrates. Plates can be embossed and
roll coated with either transparent or opaque roll coating inks, or dry roll coating foils. Plates made with digitally
printed variable plate message sheeting need no roll coating.
2 Substrates
Metal cleanliness, pretreatment, and surface temperature are the most important factors for ensuring good
adhesion of the sheeting to the metal substrate. For instructions on checking metal cleanliness, see Section 4.1,
Quality Checklist: Metal Cleaning.
After metal straightening, aluminum entering the sheeting laminator should be in the temperature range of
105 ± 10 °F for optimal adhesion.
A minimum temperature of 70 °F is recommended.
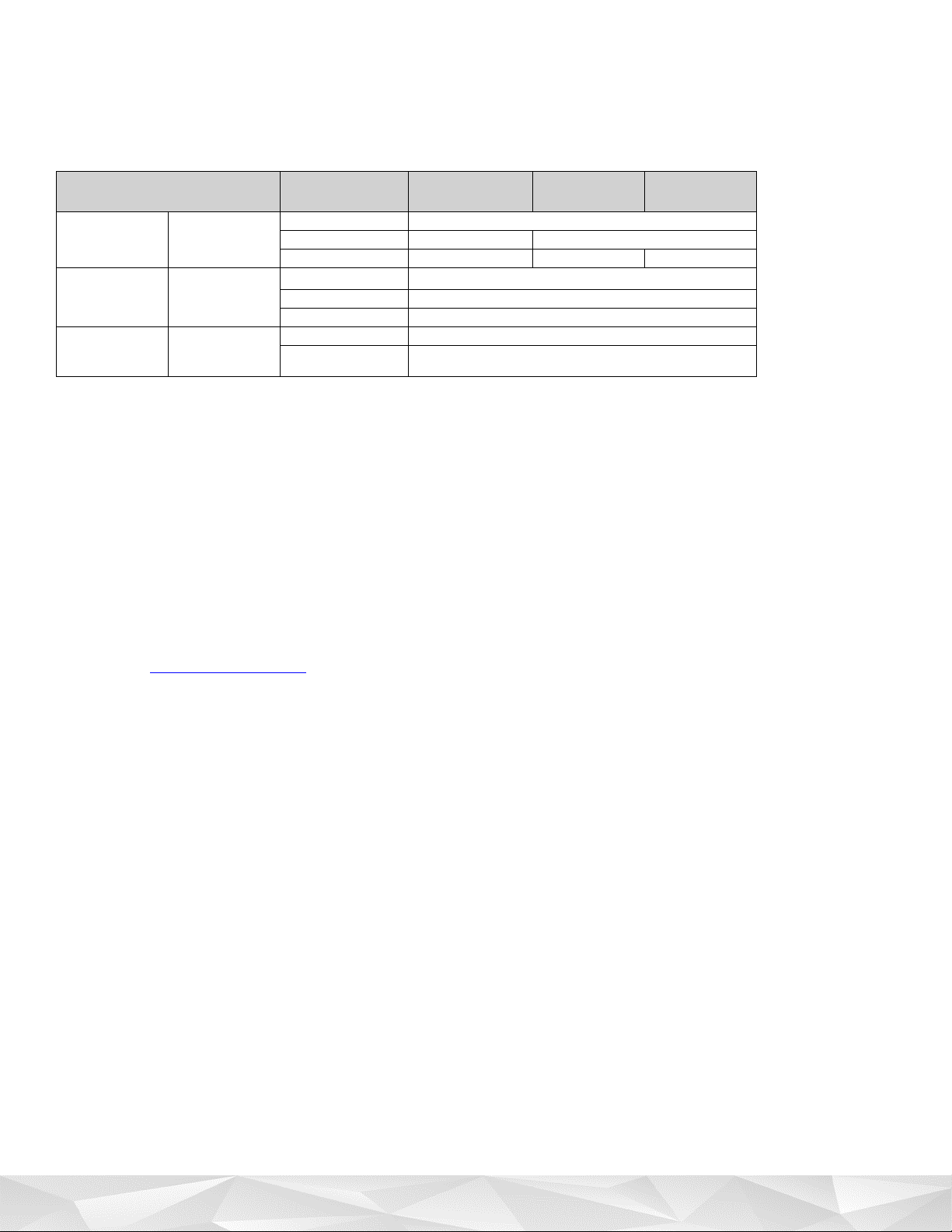
2 3M™ Reflective License Plate Sheeting Recommended Manufacturing Procedures February 2021
Table 1 presents the desired characteristics of recommended aluminum stock materials.
Table 1. Typical aluminum stock characteristics
Material Property
Alloy 3105
Al coil base Base metal
Front surface Pretreatment
Pretreatment
Back surface
a. 3M has experimented extensively with license plate pretreatments and concluded:
License plate manufacturers should consult with their aluminum stock supplier to discuss best options.
or polyester
washcoat
Aluminum pretreated with Bonderite 1455SF is no longer recommended for use.
Aluminum pretreated with Bonderite M-CR 1430C is recommended as a suitable replacement.
Temper H-18 or H-28 H-12 or H-22
Gauge (in.) 0.022 0.027 0.032
Formulation
Powdery residue None
Appearance No change in coating pattern
Powdery residue None
Appearance No change in coating pattern
DLP
(non-embossed)
Chemically treated or conversion coated
DLP &
Embossed
Embossed
a
3 Procedure
3.1 Retroreflective Sheeting Application
Applicator operators must maintain proper side to side alignment of the sheeting on the metal by adjusting the
steering on the 3M Squeeze Roll Applicator (16 inches) as needed.
For graphic printed sheeting, the 16 inch squeeze roll applicator adjustment must be set and monitored to
maintain the correct repeat pattern measurement on the sheeting after it is applied to the metal substrate. On
3M applicators, this adjustment is set by the thumb-wheel switches on the applicator electronic control panel
(refer to Information Folder 9.4
).
3.2 Cut Blanks
Cut blanks must be stored on edge after being removed from the blanking press. Avoid packing blanks too
tightly to minimize sticking of blanks and scuffing or scraping of sheeting.
The cut blanks must be stored for a minimum of 48 hours prior to embossing to allow the sheeting to reach
maximum adhesion to the metal substrate. Check the adhesion of the sheeting to the metal after the 48 hour
rest period (see Section 4.2 Quality Checklist: metal cleaning).
The surface of the license plate sheeting scratches easily. Care must be taken when handling cut blanks to
prevent the sheeting surfaces from getting scratched.
Blanking dies must be kept sharpened as any burrs on the bolt holes or along the edges of the plate can
scratch the surface of the sheeting.
3.3 Embossing
Embossing height must be uniform and maintained at a height sufficient to avoid smudging the background
during roll coating.
1 Satisfactory embossing heights are usually in the range of 0.070–0.080 inches (1.8–2.0 mm).
2 If registration characters and fixed copy cannot be maintained at a uniform height, registration
characters may be slightly higher, however, the difference between the registration character and
fixed copy heights should not exceed 0.003 inches (0.076 mm).
Dies causing scuffing and cutting should be removed from production, polished, adjusted, and/or repaired
before being put back into use.