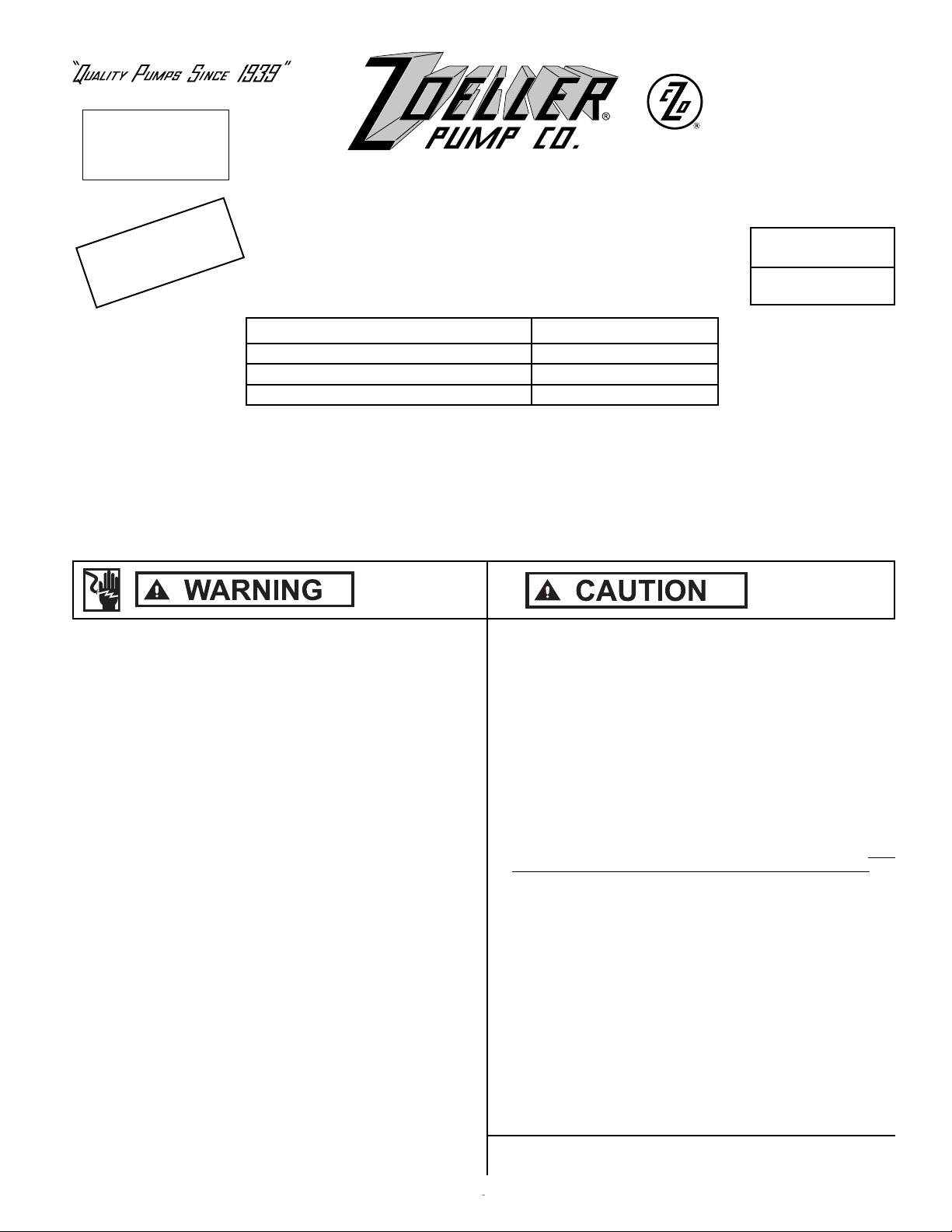
Notice to installing contractor: Instructions must remain with installation.
Product information presented
here re fl ects con di tions at time
of publication. Consult factory
re gard ing dis crep an cies or
in con sis ten cies.
MAIL TO: P.O. BOX 16347 • Louisville, KY 40256-0347
SHIP TO: 3649 Cane Run Road • Louisville, KY 40211-1961
(502) 778-2731 • 1 (800) 928-PUMP • FAX (502) 774-3624
SECTION: 6.10.001
FM0447
Rev. A
1009
Supersedes
0809
visit our web site:
www.zoeller.com
NOTICE: VENT HOLE FOR
CHECK VALVE
SEE #3 IN CAUTION SECTION
BELOW AND #4 ON PAGE 3
INSTALLATION INSTRUCTIONS
RECOMMENDED MODELS
MODEL NUMBER:
EFFLUENT*/SUMP/DEWATERING SEWAGE
DATE INSTALLED:
49, 50 Series, 70 Series, 98 Series 211 Series, 264 Series
130 Series, 140/4140, 145/4145 Series, 150 Series, 160/4160 Series 260 Series, 270/4270 Series
180/4180 Series, 191, 371, 372, 373 280/4280 Series, 290/4290 Series
*Effl uent systems should specify that pumps should not handle solids exceeding three fourths inch (¾") in order to prevent large solids from entering leeching fi elds, mound systems etc.
(Model 49 and 70 Series have 3/8" solids capability, 50, 90, 140, 145/4145, 151, 371 and 372 Series have ½", 130 Series has 5/8", 152,153, and 160/4160/180/4180, 373 Series have
¾".) Where codes permit, sewage pumps can be used for effl uent systems. Nonautomatic pump(s) with external level control recommended for septic tank effl uent applications.
PREINSTALLATION CHECKLIST - ALL IN STAL LA TIONS
1. Inspect your pump. Occasionally, products are damaged during shipment. If the unit is damaged, contact your dealer before using. DO NOT remove the test plugs in the cover nor the motor housing.
2. Carefully read the literature provided to familiarize yourself with specifi c details regarding in stal la tion and use. These materials should be retained for future reference.
SEE BELOW FOR
LIST OF WARNINGS
1. Make certain that the receptacle is within the reach of the pump’s pow er supply cord. DO NOT
USE AN EXTENSION CORD. Extension cords that are too long or too light do not deliver suffi cient
voltage to the pump motor. But, more important, they could present a safety haz ard if the insulation
were to become damaged or the con nec tion end were to fall into the sump.
2. Make sure the pump electrical supply circuit is equipped with fuses or circuit breakers of
proper capacity. A separate branch circuit is rec om mended, sized ac cord ing to the “National
Elec tri cal Code” for the current shown on the pump nameplate.
3. Testing for ground. As a safety measure, each electrical outlet should be checked for ground
using an Underwriters Laboratory Listed circuit analyzer which will indicate if the power, neutral
and ground wires are correctly connected to your outlet. If they are not, call a qualifi ed licensed
electrician.
4. For Added Safety. Pumping and other equipment with a 3-prong grounded plug must be connected
to a 3-prong grounded receptacle. For added safety the receptacle may be protected with a groundfault circuit interrupter. When a pump needs to be connected in a watertight junction box, the plug
can be removed and spliced to the supply cable with proper grounding. For added safety this circuit
may be protected by a ground-fault circuit in ter rupt er. The complete in stal la tion must comply with
the National Electrical Code and all applicable local codes and ordinances.
5. FOR YOUR PROTECTION, ALW AYS DISCONNECT PUMP FROM ITS POW ER SOURCE BE FORE
HANDLING. Single phase pumps are sup plied with a 3-prong ground ed plug to help protect you
against the possibility of electrical shock. DO NOT UNDER ANY CIRCUM STANCES RE MOVE
THE GROUND PIN. The 3-prong plug must be inserted into a mating 3-prong grounded receptacle.
If the in stal la tion does not have such a receptacle, it must be changed to the prop er type, wired
and ground ed in ac cor dance with the National Elec tri cal Code and all applicable local codes and
or di nanc es. Three phase pumps require motor starting devices with motor overload pro tec tion. See
FM0486 for duplex in stal la tions.
6. The tank is to be vented in accordance with local plumbing code. Pumps must be in stalled in ac cor dance with the National Electrical Code and all ap pli cable local codes and ordinances. Pumps
are not to be installed in locations clas si fi ed as hazardous in accordance with National Electrical
Code, ANSI/NFPA 70.
7. “Risk of electrical shock” Do not remove power supply cord and strain relief or connect conduit
directly to the pump.
8. Installation and servicing of electrical circuits and hardware should be performed by a qualifi ed
li censed electrician.
9. Pump installation and servicing should be performed by a qualifi ed person.
10. Risk of electric shock - These pumps have not been investigated for use in swimming pool and
marine areas.
11. According to the state of California (Prop 65), this product contains chemicals known to the state
of California to cause cancer and birth defects or other reproductive harm.
1. Check to be sure your power source is capable of handling the voltage re quire ments of the motor,
as indicated on the pump name plate.
2. The installation of automatic pumps with variable level fl oat switch es or nonautomatic pumps using
auxiliary variable level fl oat switches is the re spon si bil i ty of the in stall ing party and care should be
tak en that the tethered fl oat switch will not hang up on the pump apparatus or pit peculiarities and
is secured so that the pump will shut off. It is recommended to use rigid piping and fi ttings and the
pit be 18" or larger in diameter.
3. Information - vent hole purpose. It is necessary that all sub mers ible sump, effl uent, and sewage
pumps capable of handling various sizes of solid waste be of the bottom intake design to reduce
clog ging and seal failures. If a check valve is incorporated in the installation, a vent hole (approx.
3/16") must be drilled in the discharge pipe below the check valve and pit cover to purge the unit
of trapped air. Trapped air is caused by agitation and/or a dry basin. Vent hole should be checked
periodically for clogging. The 50 or 90 Series pumps have a vent lo cated in the pump housing
opposite the fl oat, ad ja cent to a housing lug, but an additional vent hole is recommended. The
vent hole on a High Head application may cause too much turbulence. You may not want to drill
one. If you choose not to drill a vent hole, be sure the pump case and impeller is covered with liquid
before connecting the pipe to the check valve and no inlet carries air to the pump intake. NOTE:
THE HOLE MUST ALSO BE BELOW THE BASIN COVER AND CLEANED PERIODICALL Y. Water
stream will be visible from this hole during pump run periods.
4. Pump should be checked frequently for debris and/or build up which may interfere with the fl oat “on”
or “off” position. Repair and service should be performed by Zoeller Pump Company Authorized
Service Station only.
5. Dewatering and effl uent sump pumps are not designed for use in pits handling raw sewage.
6. Maximum operating temperature for standard model pumps must not ex ceed 130°F (54°C). Model
49 max. temperature must not exceed 104ºF (40ºC). The 70 and 211 Series max. temperature must
not exceed 110ºF (43ºC).
7. Pump models 188/4188, 189/4189, and 295/4295 nonautomatic pump must run totally submerged
and CSA certifi ed pumps must be operated submerged with “off - on” level controls.
8. Pump models 266, 267, 268, 137 and 139 must be operated in an upright position. Do not attempt
to start pump when tilted or laying on its side.
9. Do not operate a pump in an ap pli ca tion where the Total Dynamic Head is less than the minimum
Total Dynamic Head listed on the Pump Performance Curves.
10. Model 49 is for indoor use only.
NOTE: Pumps with the “UL” mark and pumps with the “US” mark are tested to UL Standard UL778.
CSA Certifi ed pumps are certifi ed to CSA Standard C22.2 No. 108.
REFER TO WARRANTY ON PAGE 2.
SEE BELOW FOR
LIST OF CAUTIONS
P/N 006355
© Copyright 2009 Zoeller Co. All rights reserved.
1
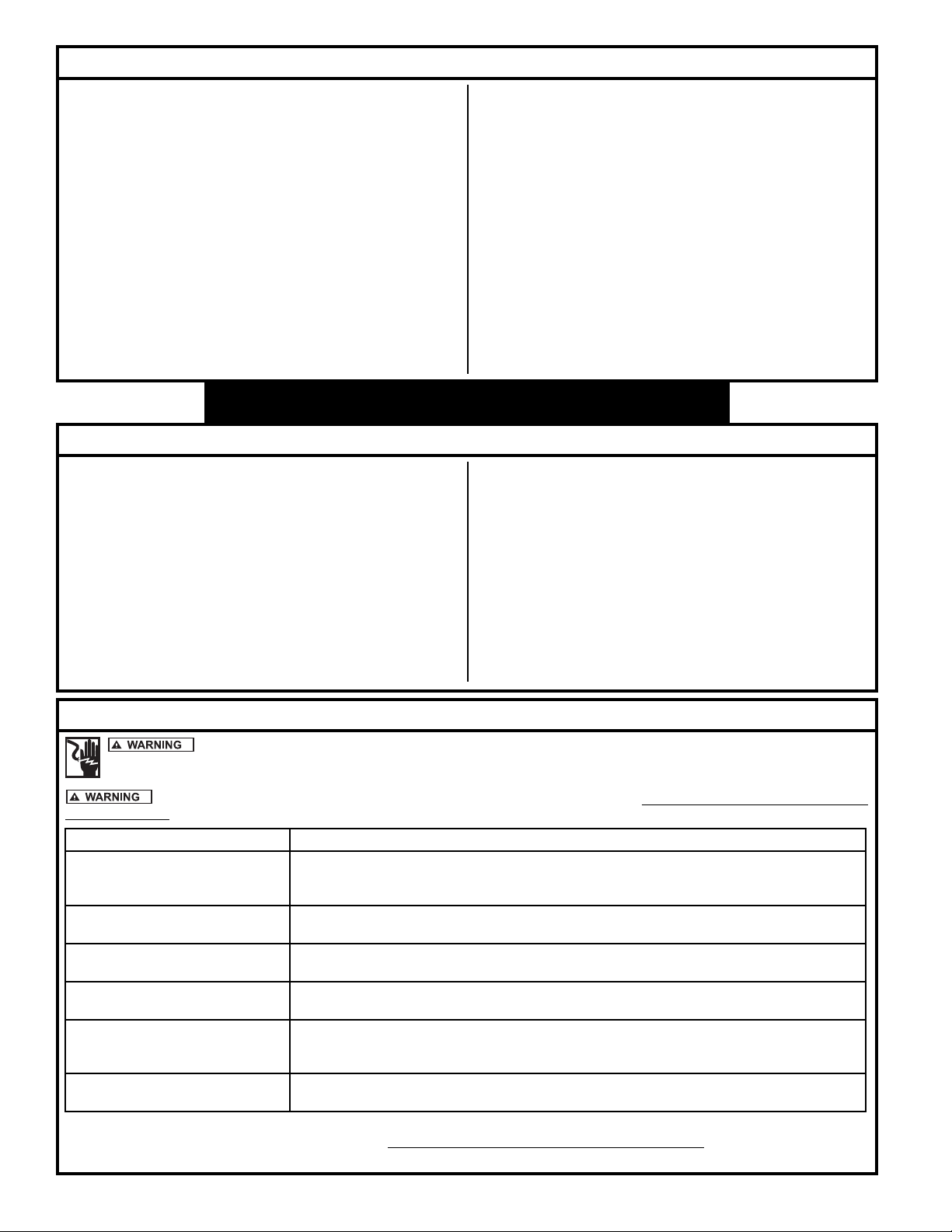
Limited Warranty
Manufacturer warrants, to the purchaser and subsequent owner during the warranty
period, every new product to be free from defects in material and workmanship under
normal use and service, when properly used and maintained, for a period of one year
from date of purchase by the end user, or 18 months from date of original manufacture
of the product, whichever comes fi rst. Parts that fail within the warranty period, one
year from date of purchase by the end user, or 18 months from the date of original
manufacture of the product, whichever comes fi rst, that inspections determine to be
defective in material or workmanship, will be repaired, replaced or remanufactured at
Manufacturer's option, provided however, that by so doing we will not be obligated to
replace an entire assembly, the entire mechanism or the complete unit. No allowance
will be made for shipping charges, damages, labor or other charges that may occur
due to product failure, repair or replacement.
This warranty does not apply to and there shall be no warranty for any material or
product that has been disassembled without prior approval of Manufacturer, subjected
to misuse, misapplication, neglect, alteration, accident or act of God; that has not
been installed, operated or maintained in accordance with Manufacturer's installation
instructions; that has been exposed to outside substances including but not limited to
the following: sand, gravel, cement, mud, tar, hydrocarbons, hydrocarbon derivatives
(oil, gasoline, solvents, etc.), or other abrasive or corrosive substances, wash towels
or feminine sanitary products, etc. in all pumping applications. The warranty set out
In those instances where damages are incurred as a result of an alleged pump failure,
the Homeowner must retain possession of the pump for investigation purposes.
EASY DO’S & DON'T’S FOR INSTALLING A SUMP PUMP
1. DO read thoroughly all installation material provided with the pump.
2. DO inspect pump for any visible damage caused by shipping. Contact
dealer if pump appears to be damaged.
3. DO clean all debris from the sump. Be sure that the pump will have a hard,
fl at surface beneath it. DO NOT install on sand, gravel or dirt.
4. DO be sure that the sump is large enough to allow proper clearance for the
level control switch(es) to operate properly.
5. DO Always Disconnect Pump From Power Source Before Handling.
DO always connect to a separately protected and properly grounded
circuit.
DO NOT ever cut, splice, or damage power cord (Only splice in a watertight
junction box).
DO NOT carry or lift pump by its power cord.
DO NOT use an extension cord with a sump pump.
6. DO install a check valve and a union in the discharge line.
DO NOT use a discharge pipe smaller than the pump discharge.
in the paragraph above is in lieu of all other warranties expressed or implied; and
we do not authorize any representative or other person to assume for us any other
liability in connection with our products.
Contact Manufacturer at, 3649 Cane Run Road, Lou is ville, Ken tucky 40211, Attention:
Cus tom er Ser vice De part ment to obtain any need ed repair or re place ment of part(s)
or additional in for ma tion pertaining to our warranty.
MANUFACTURER EXPRESSLY DIS CLAIMS LI A BIL I TY FOR SPE CIAL,
CON SE QUEN TIAL OR IN CI DEN TAL DAM AG ES OR BREACH OF EX PRESSED
OR IMPLIED WARRANTY; AND ANY IMPLIED WAR RAN TY OF FIT NESS FOR A
PAR TIC U LAR PUR POSE AND OF MER CHANT ABIL I TY SHALL BE LIM IT ED TO
THE DU RA TION OF THE EX PRESSED WAR RAN TY.
Some states do not allow limitations on the duration of an implied warranty, so the
above limitation may not apply to you. Some states do not allow the exclusion or
limitation of incidental or con se quen tial dam ag es, so the above lim i ta tion or exclusion
may not apply to you.
This warranty gives you specifi c legal rights and you may also have other rights
which vary from state to state.
7. DO NOT use a sump pump as a trench or excavation pump, or for pumping
sewage, gasoline, or other hazardous liquids.
8. DO test pump immediately after installation to be sure that the system is
working properly.
9. DO cover sump with an adequate sump cover.
10. DO review all applicable local and national codes and verify that the installation
conforms to each of them.
11. DO consult manufacturer for clarifi cations or questions.
12. DO
consider a two pump system with an alarm where an installation may become
overloaded or primary pump failure would result in property damages.
13. DO consider a D.C. Backup System where a sump or de w a ter ing pump
is necessary for the prevention of property damages from fl ooding due
to A.C. power disruptions, mechanical or electrical problems or system
over load ing.
14. DO inspect and test system for proper operations at least every three
months.
SERVICE CHECKLIST
sure you are wearing insulated protective sole shoes and not standing in water. Under fl ooded conditions, contact your local electric company or a
qualifi ed licensed electrician for disconnecting electrical service prior to pump removal.
at tempt ing service.
CONDITION COMMON CAUSES
A. Pump will not start or run. Check fuse, low voltage, over load open, open or incorrect wiring, open switch, impeller or seal bound me chan i cal ly,
B. Motor overheats and trips over load
or blows fuse.
C. Pump starts and stops too often. Float tight on rod, check valve stuck or none installed in long distance line, over load open, level switch(s) defec-
D. Pump will not shut off. Debris under fl oat assembly, fl oat or fl oat rod bound by pit sides or other, switch de fec tive, damaged or out of
E. Pump operates but delivers little or
no wa ter.
F. Drop in head and/or capacity after
a period of use.
If the above checklist does not uncover the problem, consult the factory - Do not attempt to service or otherwise disassemble pump. Service must
be performed by Zoeller Authorized Service Stations. Go to www.zoeller.com/zcopump/TechSupport/authsslisting.htm to fi nd the Authorized Service
Station in your area.
ELECTRICAL PRECAUTIONS- Before servicing a pump, always shut off the main power breaker and then unplug the pump - making
Submersible pumps contain oils which becomes pressurized and hot under operating conditions - allow 2½ hours after disconnecting before
defective capacitor or relay when used, motor or wiring shorted. Float assembly held down. Switch defective,
dam aged, or out of adjustment.
Incorrect voltage, negative head (discharge open lower than normal) impeller or seal bound mechanically, defective capacitor or relay, motor shorted.
tive, sump pit too small.
adjustment.
Check strainer housing, discharge pipe, or if check valve is used vent hole must be clear. Dis charge head
ex ceeds pump capacity. Low or incorrect voltage. Incorrect motor rotation. Ca pac i tor defective. Incoming water
con tain ing air or causing air to enter pump ing chamber.
Increased pipe friction, clogged line or check valve. Abrasive material and ad verse chem i cals could possibly
deteriorate impeller and pump housing. Check line. Remove base and inspect.
© Copyright 2009 Zoeller Co. All rights reserved.
2